柔性线路板工艺资料
fc板工艺
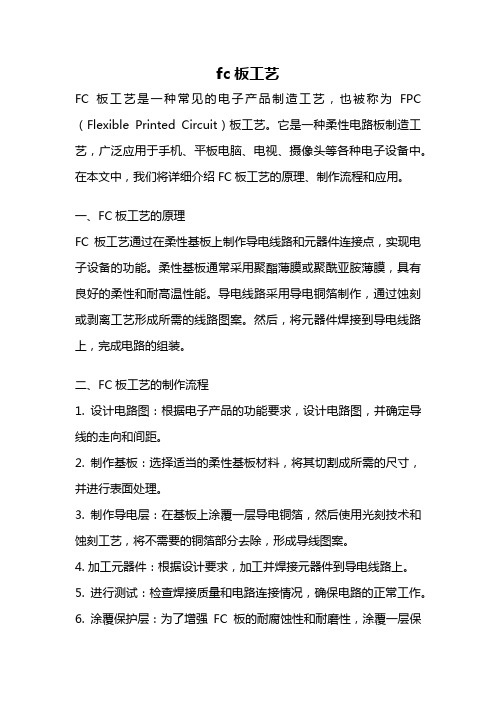
fc板工艺FC板工艺是一种常见的电子产品制造工艺,也被称为FPC (Flexible Printed Circuit)板工艺。
它是一种柔性电路板制造工艺,广泛应用于手机、平板电脑、电视、摄像头等各种电子设备中。
在本文中,我们将详细介绍FC板工艺的原理、制作流程和应用。
一、FC板工艺的原理FC板工艺通过在柔性基板上制作导电线路和元器件连接点,实现电子设备的功能。
柔性基板通常采用聚酯薄膜或聚酰亚胺薄膜,具有良好的柔性和耐高温性能。
导电线路采用导电铜箔制作,通过蚀刻或剥离工艺形成所需的线路图案。
然后,将元器件焊接到导电线路上,完成电路的组装。
二、FC板工艺的制作流程1. 设计电路图:根据电子产品的功能要求,设计电路图,并确定导线的走向和间距。
2. 制作基板:选择适当的柔性基板材料,将其切割成所需的尺寸,并进行表面处理。
3. 制作导电层:在基板上涂覆一层导电铜箔,然后使用光刻技术和蚀刻工艺,将不需要的铜箔部分去除,形成导线图案。
4. 加工元器件:根据设计要求,加工并焊接元器件到导电线路上。
5. 进行测试:检查焊接质量和电路连接情况,确保电路的正常工作。
6. 涂覆保护层:为了增强FC板的耐腐蚀性和耐磨性,涂覆一层保护层。
7. 切割成型:根据电子产品的尺寸要求,将FC板切割成所需的形状。
8. 进行最终测试:对制作好的FC板进行全面测试,确保其质量和性能符合要求。
三、FC板工艺的应用FC板工艺具有柔性、轻薄、可弯曲等特点,广泛应用于各种电子设备中。
以下是几个常见的应用领域:1. 手机和平板电脑:FC板工艺可用于连接手机和平板电脑的触摸屏、显示屏、摄像头等部件,实现它们之间的信号传输和功能控制。
2. 电视和显示器:FC板工艺可用于连接电视和显示器的背光模块、主板、按钮控制等部件,实现它们之间的信号传输和功能控制。
3. 汽车电子:FC板工艺可用于连接汽车电子设备,如导航仪、音响系统、仪表盘等,实现它们之间的信号传输和功能控制。
FPC工艺简介FPC基础知识

FPC发展
主要在四个方面: 1、厚度。FPC的厚度必须更加灵活,必须做
到更薄;
2、耐折性。可以弯折是FPC与生俱来的特性 ,未来的FPC耐折性必须更强,必须超过1万 次,当然,这就需要有更好的基材;
FPC发展
3、价格。现阶段,FPC的价格较PCB高很多 ,如果FPC价格下来了,市场必定又会宽广 很多。
FPC基础知识
FPC FPC结构 FPC FPC发展
FPC简介—定义
柔性电路板,简称软板或FPC,是以聚酰亚 胺或聚酯薄膜为基材制成的一种具有高度 可靠性,绝佳的可挠性印刷线路板,故又 称可挠性线路板。
FPC简介—特性
轻:重量比PCB(硬板)轻
可以减少最终产品的重量
薄:厚度比PCB薄
可以提高柔软度.加强再有限空间内在三度空间的组装
工程目的:双面板为使上下线路导通,先鑚孔以利后续镀铜。
工程目的:双面板为使上下线路导通,先鑚孔以利后续镀铜。
工程目的:使孔壁中不导电的部份导通,成为导体,使后续的电镀制程 得以进行。
工程目的:使双面板上铜面与下铜面导通。
工程目的:利用加温加热方式将干式感光薄膜与铜面黏合,配合曝光产 生化学反应以完成保护铜箔。
FPC结构—铜箔
分为压延铜和电解铜两种。压延铜强度高, 耐弯折,但价格较贵。电解铜价格便宜的多 ,但强度差,易折断,一般用在很少弯折的 场合。
铜箔厚度的选择要依据引线最小宽度和最 小间距而定。铜箔越薄,可达到的最小宽度 和间距越小。
FPC结构—PTH
PTH(Plating Through Hole)镀通孔 目的:
25um 厚的基材价格最便宜,应用也最普遍。如果需 要电路板硬一点,应选用50um 的基材。反之,如果需 要电路板柔软一点,则选用 13um 的基材。
FPCB工艺制造流程介绍
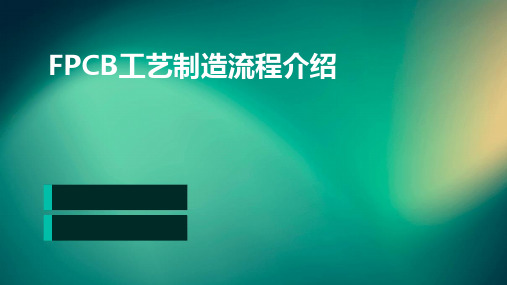
设备与环境控制
总结词
设备与环境是FPCB工艺制造过程中的重要影响因素, 必须对其进行有效控制以保证产品质量。
详细描述
定期对设备进行维护和保养,确保设备处于良好状态。 同时,对生产环境进行监控,包括温度、湿度、洁净度 等,确保满足工艺要求。对于有特殊要求的工艺环节, 还应配置相应的设备和环境设施。
工艺参数控制
在生产过程中,如果原材料供应不足 或中断,可能会导致生产停滞,影响 交货期和客户满意度。
供应商管理
加强供应商管理,与供应商建立长期 合作关系,确保原材料的稳定供应。 同时,应制定应急预案,以应对突发 情况。
工艺参数调整与优化
要点一
工艺参数优化
在FPCB工艺制造过程中,工艺参数的调整和优化对于提高 产品质量和生产效率至关重要。
电镀技术
总结词
电镀技术是在电路图形上覆盖一层金属镀层,以提高导 电性能和耐腐蚀性。
详细描述
电镀技术通过电解的方法,在电路图形上覆盖一层金属 镀层,如铜、镍等。这层金属镀层可以提高导电性能和 耐腐蚀性,保证FPCB在使用过程中的稳定性和可靠性。 同时,电镀技术还可以实现多层镀层和复合镀层的效果 ,满足B工艺制造过程的未 来展望
新材料的应用
高导热材料
随着电子设备性能的提升, 高导热材料在FPCB中的应 用将更加广泛,以提高散 热性能。
轻量化材料
为了满足电子设备轻薄化 的需求,轻量化材料将在 FPCB制造中得到应用,降 低产品重量。
环保材料
随着环保意识的提高,无 卤素、无铅等环保材料将 在FPCB制造中得到推广, 减少对环境的污染。
FPCB工艺制造流程介绍
目 录
• FPCB工艺简介 • FPCB制造流程 • FPCB工艺制造过程中的关键技术 • FPCB工艺制造过程中的质量控制 • FPCB工艺制造过程的挑战与解决方案 • FPCB工艺制造过程的未来展望
柔性线路板制作工艺流程及PCB设计软件应用
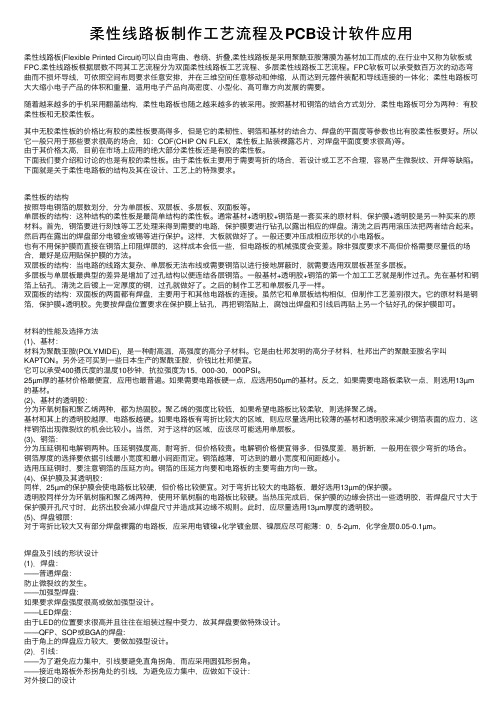
柔性线路板制作⼯艺流程及PCB设计软件应⽤柔性线路板(Flexible Printed Circuit)可以⾃由弯曲、卷绕、折叠,柔性线路板是采⽤聚酰亚胺薄膜为基材加⼯⽽成的,在⾏业中⼜称为软板或FPC.柔性线路板根据层数不同其⼯艺流程分为双⾯柔性线路板⼯艺流程、多层柔性线路板⼯艺流程。
FPC软板可以承受数百万次的动态弯曲⽽不损坏导线,可依照空间布局要求任意安排,并在三维空间任意移动和伸缩,从⽽达到元器件装配和导线连接的⼀体化;柔性电路板可⼤⼤缩⼩电⼦产品的体积和重量,适⽤电⼦产品向⾼密度、⼩型化、⾼可靠⽅向发展的需要。
随着越来越多的⼿机采⽤翻盖结构,柔性电路板也随之越来越多的被采⽤。
按照基材和铜箔的结合⽅式划分,柔性电路板可分为两种:有胶柔性板和⽆胶柔性板。
其中⽆胶柔性板的价格⽐有胶的柔性板要⾼得多,但是它的柔韧性、铜箔和基材的结合⼒、焊盘的平⾯度等参数也⽐有胶柔性板要好。
所以它⼀般只⽤于那些要求很⾼的场合,如:COF(CHIP ON FLEX,柔性板上贴装裸露芯⽚,对焊盘平⾯度要求很⾼)等。
由于其价格太⾼,⽬前在市场上应⽤的绝⼤部分柔性板还是有胶的柔性板。
下⾯我们要介绍和讨论的也是有胶的柔性板。
由于柔性板主要⽤于需要弯折的场合,若设计或⼯艺不合理,容易产⽣微裂纹、开焊等缺陷。
下⾯就是关于柔性电路板的结构及其在设计、⼯艺上的特殊要求。
柔性板的结构按照导电铜箔的层数划分,分为单层板、双层板、多层板、双⾯板等。
单层板的结构:这种结构的柔性板是最简单结构的柔性板。
通常基材+透明胶+铜箔是⼀套买来的原材料,保护膜+透明胶是另⼀种买来的原材料。
⾸先,铜箔要进⾏刻蚀等⼯艺处理来得到需要的电路,保护膜要进⾏钻孔以露出相应的焊盘。
清洗之后再⽤滚压法把两者结合起来。
然后再在露出的焊盘部分电镀⾦或锡等进⾏保护。
这样,⼤板就做好了。
⼀般还要冲压成相应形状的⼩电路板。
也有不⽤保护膜⽽直接在铜箔上印阻焊层的,这样成本会低⼀些,但电路板的机械强度会变差。
FPC生产方式及工艺流程

FPC生产方式及工艺流程FPC,即柔性印刷电路板(Flexible Printed Circuit Board),是一种以聚酰亚胺薄膜为基材,经过电子线路制作工艺加工而成的柔性电路板。
相比传统的刚性电路板,FPC具有体积小、重量轻、可折迭、可弯曲等优点,广泛应用于汽车电子、消费电子、医疗设备等领域。
FPC的生产方式包括单面贴片、双面贴片和多层贴片三种,下面将详细介绍每种生产方式的工艺流程。
1.单面贴片生产方式:(1)刷膜:将聚酰亚胺薄膜放在滚筒上,通过刷涂胶水的方式将胶水均匀地涂布在薄膜上。
(2)固化:将刷涂胶水的聚酰亚胺薄膜放入固化炉中,经过高温固化,使胶水变为固态。
(3)表面处理:使用化学方法将聚酰亚胺薄膜表面进行粗糙化处理,增加与线路层的粘附力。
(4)印刷:将图纸上的线路图案通过丝网印刷的方式印制到聚酰亚胺薄膜上。
(5)电镀:将印制好的线路薄膜浸入电镀槽中,进行金属电镀,使线路形成导电层。
(6)固定:将电镀好的线路薄膜放在模具中,通过热压或胶合的方式将导线固定在聚酰亚胺薄膜上。
(7)加工:对固定好的线路薄膜进行裁剪、穿孔等加工工艺,使其符合设计要求。
(8)测试:对加工好的FPC进行电气测试,确保各个线路连接正常。
(9)质检:对测试合格的FPC进行外观检查,确保产品质量。
(10)包装:将质检合格的FPC进行包装,以便运输和销售。
2.双面贴片生产方式:双面贴片生产方式在单面贴片的基础上增加了第二层线路,使FPC具有更高的线路密度和更复杂的功能。
(1)刷膜:同单面贴片生产方式。
(2)固化:同单面贴片生产方式。
(3)表面处理:同单面贴片生产方式。
(4)印刷:同单面贴片生产方式。
(5)电镀:同单面贴片生产方式。
(6)固定:将第一个线路薄膜和第二个线路薄膜按照设计要求进行层间定位和胶合,固定在一起。
(7)加工:同单面贴片生产方式。
(8)测试:同单面贴片生产方式。
(9)质检:同单面贴片生产方式。
(10)包装:同单面贴片生产方式。
FPC生产工艺流程
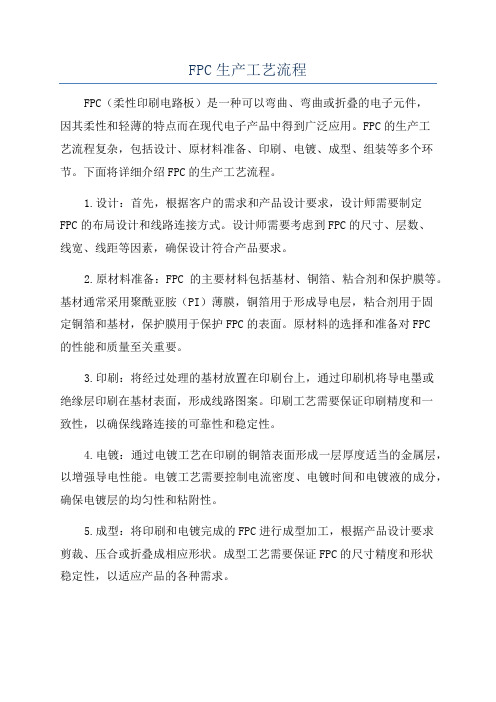
FPC生产工艺流程FPC(柔性印刷电路板)是一种可以弯曲、弯曲或折叠的电子元件,因其柔性和轻薄的特点而在现代电子产品中得到广泛应用。
FPC的生产工艺流程复杂,包括设计、原材料准备、印刷、电镀、成型、组装等多个环节。
下面将详细介绍FPC的生产工艺流程。
1.设计:首先,根据客户的需求和产品设计要求,设计师需要制定FPC的布局设计和线路连接方式。
设计师需要考虑到FPC的尺寸、层数、线宽、线距等因素,确保设计符合产品要求。
2.原材料准备:FPC的主要材料包括基材、铜箔、粘合剂和保护膜等。
基材通常采用聚酰亚胺(PI)薄膜,铜箔用于形成导电层,粘合剂用于固定铜箔和基材,保护膜用于保护FPC的表面。
原材料的选择和准备对FPC的性能和质量至关重要。
3.印刷:将经过处理的基材放置在印刷台上,通过印刷机将导电墨或绝缘层印刷在基材表面,形成线路图案。
印刷工艺需要保证印刷精度和一致性,以确保线路连接的可靠性和稳定性。
4.电镀:通过电镀工艺在印刷的铜箔表面形成一层厚度适当的金属层,以增强导电性能。
电镀工艺需要控制电流密度、电镀时间和电镀液的成分,确保电镀层的均匀性和粘附性。
5.成型:将印刷和电镀完成的FPC进行成型加工,根据产品设计要求剪裁、压合或折叠成相应形状。
成型工艺需要保证FPC的尺寸精度和形状稳定性,以适应产品的各种需求。
6.组装:对成型的FPC进行元件焊接、封装和测试等工艺,最终形成成品FPC。
组装工艺需要保证焊接质量和可靠性,确保FPC在产品组装和使用过程中正常运行。
综上所述,FPC的生产工艺流程包括设计、原材料准备、印刷、电镀、成型、组装等多个环节。
每个环节都需要严格控制工艺参数和质量要求,以确保FPC的性能和质量达到客户的要求。
随着电子产品的不断发展和更新换代,FPC的生产工艺也将不断改进和优化,以满足市场对于柔性电子产品的需求。
fpc rtr生产工艺

fpc rtr生产工艺FPC(柔性印刷电路板)RTR(卷对卷)生产工艺是一种用于生产柔性电路板的先进生产工艺。
这种工艺可以大大提高生产效率和产品质量。
本文将介绍FPC RTR生产工艺的流程和优势。
首先,FPC RTR生产工艺的流程如下:设计电路板原图-制作印刷板材-嵌孔-贴合-切割成型-质检-包装。
设计电路板原图是整个工艺的第一步。
设计师根据产品的需求和要求绘制电路原图,包括电路线路和组件位置。
这个原图会被转化为制作印刷板材的数据。
制作印刷板材是制造电路板的关键步骤。
这个过程通过将电路原图转化为印刷板的图片。
制造商将暴露光在印刷板上,然后通过化学腐蚀和镀铜等方法制作电路线路图。
嵌孔是将电路板上的引脚连接到电路板下方的器件的过程。
生产商使用钻孔机将孔钻到电路板上,并确保孔尺寸准确无误。
这样,电路板和器件之间可以通过这些孔连接。
贴合是将硬质电路板(如PCB)与柔性电路板(FPC)相结合的过程。
贴合是使用特殊的胶黏剂将硬电路板和柔性电路板粘合在一起。
这样就可以为柔性电路板提供稳定的支撑,并保护电路线路不被损坏。
切割成型意味着将贴合后的电路板切成所需的形状和尺寸。
这通常通过机械切割或激光切割完成。
切割成型的过程需要非常精确,以确保产品符合规格。
质检是生产中至关重要的环节。
产品的质量检查包括检查电路线路的连接性、孔的位置和尺寸、切割成型的精度等。
只有通过了质检的产品才能被认为是合格的。
最后,经过包装后的产品可以出厂销售。
包装是将产品放入适当的容器或包装中,以确保其在运输和使用过程中不受损坏。
FPC RTR生产工艺的优势有以下几点:首先,该工艺大大提高了生产效率。
由于该工艺采用卷对卷的生产方式,无需进行人工操作和人工翻板,生产速度更快。
减少了因人工操作引起的工时损失及生产效率低下的问题。
其次,该工艺减少了产品的损坏率。
相比传统的切割板型生产工艺,FPC RTR生产工艺在切割成型环节中采用了机械或激光切割,减少了人工操作的不准确性,从而大大降低了产品的损坏率。
FPC基础知识解析

FPC基础知识解析目录一、FPC概述 (2)1.1 FPC的定义 (2)1.2 FPC的发展历程 (3)1.3 FPC的应用领域 (5)二、FPC的基本结构 (6)2.1 FPC的组成结构 (6)2.2 FPC的类型 (8)2.2.1 按照层数分类 (9)2.2.2 按照导电介质分类 (10)2.3 FPC的规格 (11)2.3.1 按照尺寸分类 (13)2.3.2 按照厚度分类 (13)三、FPC的制作工艺 (14)3.1 印刷电路板(PCB)的制作工艺 (15)3.2 电子元件的制造工艺 (16)3.3 FPC的组装工艺 (17)四、FPC的性能要求 (19)4.1 导电性 (20)4.2 结构强度 (22)4.3 抗干扰能力 (23)4.4 可焊性 (24)五、FPC的设计与制造 (25)5.1 设计原则与方法 (26)5.2 制造工艺与流程 (28)六、FPC的应用与选购 (29)6.1 应用领域 (30)6.2 质量判断与选购指南 (31)七、FPC的发展趋势与挑战 (33)7.1 发展趋势 (34)7.2 面临的挑战 (36)一、FPC概述FPC,即柔性印刷电路板,是电子行业中的重要组成部分。
它是一种具有高密度、高可靠性的柔性电子组件,具有多种功能,并在多个领域得到广泛应用。
FPC的主要特点在于其可弯曲、可折叠的特性,这使得它在各种紧凑且复杂的设计中表现出色。
FPC还具有轻薄、薄型化、短小、轻量以及良好的散热性和可焊性等优点。
FPC的制造过程涉及多个步骤,包括基板材料的选择、导电层和绝缘层的制作、覆盖层的涂布以及最终的固化处理等。
这些步骤需要精确控制,以确保FPC的质量和性能。
随着科技的不断发展,FPC的应用领域也在不断扩大。
在智能手机、平板电脑、笔记本电脑等消费电子产品中,FPC被广泛应用于触控面板、摄像头模组、电池管理系统等方面。
在汽车电子、医疗设备、工业控制等领域,FPC也发挥着重要作用。
SMT(FPC)工艺流程

优化焊接工艺
通过调整焊接温度、时间等工艺参数,提高 焊接质量稳定性。
提高生产效率
通过加强设备维护、优化工艺参数等方式, 提高生产效率。
THANKS FOR WATCHING
感谢您的观看
对焊接温度、时间、压力等工艺参数进行 精确控制,确保焊接质量可靠,防止工艺参数
根据实际生产情况,对工艺参数进行 优化调整,提高生产效率和产品质量。
改进设备与工具
不断改进和更新设备与工具,提高生 产自动化程度和精度,降低人为因素 对产品质量的影响。
加强员工培训
陷和故障。
材料
电子元件
包括电阻、电容、电感、二极管等,是构成电子产品的基本元件。
PCB板
是电子元件的载体,提供电路连接和支撑作用。
焊膏和胶水
用于将电子元件固定在PCB板上,是焊接和粘接过程中必不可少的材料。
辅助材料
包括防护材料、包装材料等,用于保护和运输PCB板和电子元件。
04 SMT(FPC)工艺流程中的 质量控制与优化
03 SMT(FPC)工艺流程中使 用的设备与材料
设备
贴片机
用于将电子元件贴装到PCB板 上,是SMT工艺流程中的核心
设备。
印刷机
用于将焊膏或胶水印刷到PCB 板上,以确保电子元件能够准 确贴装。
回流焊炉
用于将贴装好的PCB板加热, 使焊膏熔化并完成电子元件的 焊接。
检测设备
包括光学检测设备和功能检测 设备,用于检测PCB板上的缺
定期对员工进行培训和考核,提高员 工的技能水平和质量意识,确保生产 过程中的质量控制。
持续改进与创新
鼓励员工提出改进意见和创新方案, 不断优化生产工艺和流程,提高生产 效率和产品质量。
柔性电路板(FPC)工艺介绍

FPC压合工艺介绍1.层压工艺流程:叠层→开模→上料→闭模→预压→成型→冷却→开模→下料→检查→下工序2.叠层操作指示:A.生产前准备好离型膜\钢板\硅胶并用粘尘布或粘尘纸清洁钢板\硅胶\离型膜表面灰尘,杂物等.B.将离型膜尺寸开好(500m*500m),放臵在叠层区备用,且每叠层完一个周期的软板,需备用钢板400块,使生产延续不至于断料.C.叠层操作时,需双手戴手套或5指戴手指套,严禁裸手接触软板.D.叠板时先放钢板硅胶离型膜FPC 离型膜硅胶钢板.一直按此叠10层(特殊要求除外)每一层摆放FPC数量以每1PNL板尺寸大小确定一层可摆FPC的数量是多少(板到硅胶四边的距离需保持7cm以上)摆板时应尽量将FPC摆放于硅胶中央部位,且每块板间距为2cm.每一层里面摆放FPC的厚度要一致(例如:单面板不可与多层板混放)每一开口,每一层摆放FPC的图形要一样,且摆放图形的位臵和顺序大致相同.摆放时应将FPC覆膜面或贴补强面朝上.离型膜要平整覆盖于软板上,不能有折皱和折叠现象.操作完毕,将叠层好的FPC平放在运输带上,送至下工序.3.注意事项:叠层时操作必须戴手套或手指套叠层前检查钢板是否有凹凸不平,硅胶是否有破损\裂痕\蜂眼.离型膜是否粘有垃圾.无以上不良现象的钢板\硅胶\离型膜方能使用于生产叠层时摆放FPC的位臵及图形需一致放离型膜时,必须先确认离型膜正反面.确认方法:1.用油性笔在离型膜一角落划一下,如果笔迹很清楚定为反面,不清晰为正面.2.戴白手套触摸离型膜,有一面很光滑可以逻劲的那一面为正面,反之为反面.4.层压操作指示:A.流程: 生产流程:退膜前处理贴合压合电镀层压流程:钻孔→贴BS膜→过塑→压基材→沉镀Cu→干膜→蚀刻→前处理→贴膜→叠层→压合→检查→下工序生产材料配置:名称规格钢板550*500mm硅胶500*500mm离型膜500*500mm5.工艺说明:A.叠层:在叠层台面上放一块钢板\硅胶\离型膜\软板\离型膜\硅胶\钢板\按此顺序以此类推.叠+层为一个开口B.上料:由两人站在两侧,前后一起抓住叠好的10层(一个开口)的板,轻轻慢慢地抬起放到压合机前每一个开口的边缘,慢慢地推到模板的正中间.不允许只抓一层钢板或只推一块钢板,防止钢板\硅胶\软板\离型膜错位及滑动.叠层结构:钢板------------------------------------------硅胶**************************离型膜------------------------------------------软板++++++++++++++++++++++++++离型膜------------------------------------------硅胶**************************钢板------------------------------------------C.压合:将叠层好的板逐个开口放好后,在机台控制面板上按“闭模”键,模板上开到顶部时,会自动停止并进入预压状态.预压10-15分钟后,须将压力调到所压之型号的工艺参数,详见<压制参数一览表>,此时进入成型压合状态.D.冷却:当成型压合时间到了之后,就将控制面板上的冷却水开关打开,进水管的四个阀门也打开,以及加热开关关闭.将温度降至80℃以下后方可下料.并将冷却水开关及进水开关全部关闭.加热开关打开升温为下次作好准备.E.下料:冷却时间足够后,按开模键.压机开始卸压,模板下降到底部时,戴好厚手套,两个人侧分开站好,分别抬出各个开口的10层板.将钢板\硅胶\离型膜一层层掀开,且把钢板\硅胶摆放齐.废离型膜扔到垃圾桶里.压好的软板用PP膠片隔放好.6.工艺控制:A.压合机在压合之前须检查机器台面是否干净,钢板有无变形,硅胶有无破损,离型膜有无皱折.确认好之后方可生产.B.参数设定:温度时间压力175±10℃传压30-60min 10-15MP固化温度时间150±10℃1-2h7.工艺维护、开关机操作和设备维护A.快压\传压开关机a.合上电源总开关,将开关拨到“ON”位臵.电气柜上电源指示灯亮b. 选择手动操作,按下闭模按钮.油泵电机运转,闭模指示灯亮.柱塞在液压作用下带动热板上开\合模,继而升压.当液压缸内的液压力升至表下限时,油泵开始工作.至最上限时泵止.从而完成闭模动作.B.成型结束后,按下开模按钮,电机运转指示灯亮,既开模.当柱塞下降时,撞到触动行开关时,泵停止.C.加热控制系统温度控制是数字温度调节器来实现自动检测.目板的温度可以在电气柜上的调节气器读出,下排是设定温度,上排是实际温度显示.面板上的“OUT/ON键控制加热温度的启动与停止.D.烘箱\开关机a.设定温度及时间,然后按下“启动”键加热器开始加热.b.待加热到设定温度,带上防高温手套,打开烘箱门,把软板放入烘箱内,将烘箱门关上.c.当设定时间到达时,警报器响.这时只需将“电热”键关上,待温度降到50℃以下,方可将软板取出.d.如需重新工作,只要将“电热”键开启即可.8.检验:A.压不实:即包封膜压不结实,紧密.1.线路导体须有0.13mm以上的间距.2.导体之间的压不实面积超过线距的20%时作返压处理.3.压不实区域长度超过0.13mm时作返工处理.B.气泡:即包封与铜箔之间充有空气,形状凸起.1.气泡长度≥10mm时判定为NG2.气泡横跨两导体时判定为NG3.气泡接触处形时判定为NGC.线路扭曲1.线路扭曲,扭折现象不允许D.溢胶:包封膜的胶溢出Cu面1.溢胶面积≤0.2mm时判定为OK.带孔的焊盘溢胶量≤1/4焊盘面积判定OK.孔边焊盘最小可焊量不小于0.1mm.E.孔内残胶:不允许孔内有残胶F.折痕\压痕\压伤(压断线,造成线路受损作报废处理)a.FPC表面伤痕长度L≥20mm,且深度明显,不允许其它轻微的可通过U A I处理.G.可靠性能测试:a.剥离程度测试b.热冲击性能测试。
柔性线路板制程解释
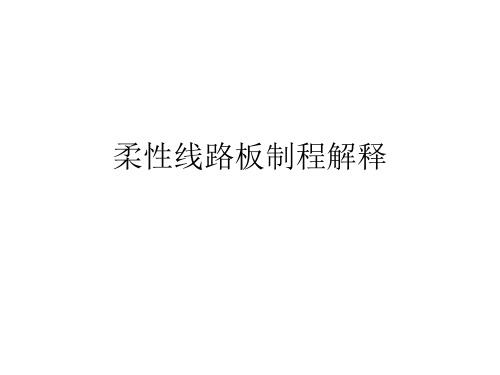
注意事项:
温度 前后风刀角度
电镀锡铅(Tin/Lead plating)
目的:
通过电镀形式在铜面 上镀上 一层光亮的锡铅, 主 要 目 的 为 提 供 Soldering Interface。
流程:
化学清洗→微蚀(酸洗) →水洗→预浸→电镀 → 水 洗 → 中 和 (防氧化)→水洗→ 烘干
印刷(solder mask)
表面划伤
• *导电图形上不应有划伤、裂缝。导 体边缘不应有各种凹凸不平、缺口、针 孔及擦伤而暴露基底。
*导体宽度减少不能大于设计图纸中 规定的最小导体宽度的20%
•
线 宽
(1)成品板上的最小线 宽应符合客户图纸 (2)允许线宽上个别变 窄段长度不大于25mm,但 最小要保留生产底片上导 线宽度的60% (3)缺损、针眼至少 保留生产底片上线宽的 30%,并且缺口的长度不 大于所留下线宽的3倍
目的:
以蚀刻液来咬 蚀未被干膜覆盖的裸铜, 使不需要的铜层被除去, 仅留下必需的线路。
常见缺陷:
蚀刻不足、(形成梯 型铜)、蚀刻过量、 开路、短路、缺损、
线宽、线距不准等
注意事项:
1.速度(依据药液浓度) 2.温度 3.喷嘴压力
去膜(Strip)
目的;
以NaOH将留在线路上之干膜完 全去除,线路即成型。
线路变细
针眼
缺损
露
线
露线
• 保护膜移位引起的 露线拒收
PCB常用专业术语中英文对照
项 目 英文 A/W(Art Work) Coupon DWG(Drawi ng) ZIF LAY-UP 中文 底片 试样条 工程图 焊脚 贴保护膜 等 项 目 英文 A/R(Annular Ring) Clearance G/F(Gold Finger) GND/VCC L/S(Line Spacing) L/W(Line Width) 中文 环宽 空环 金手指 接地层、接 电压层 线距 线宽
柔性电路板生产工艺
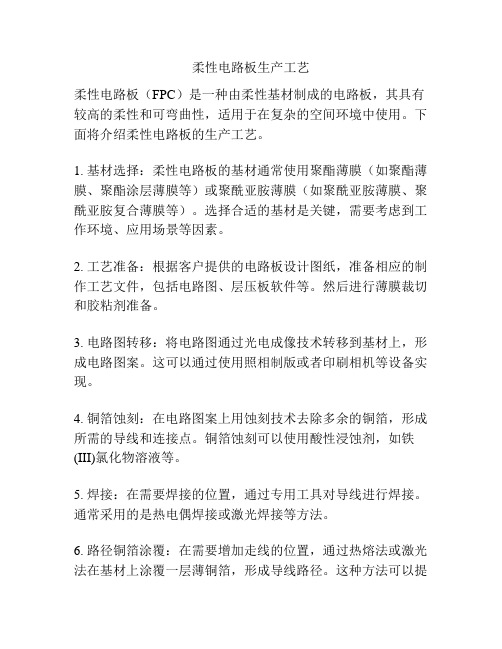
柔性电路板生产工艺柔性电路板(FPC)是一种由柔性基材制成的电路板,其具有较高的柔性和可弯曲性,适用于在复杂的空间环境中使用。
下面将介绍柔性电路板的生产工艺。
1. 基材选择:柔性电路板的基材通常使用聚酯薄膜(如聚酯薄膜、聚酯涂层薄膜等)或聚酰亚胺薄膜(如聚酰亚胺薄膜、聚酰亚胺复合薄膜等)。
选择合适的基材是关键,需要考虑到工作环境、应用场景等因素。
2. 工艺准备:根据客户提供的电路板设计图纸,准备相应的制作工艺文件,包括电路图、层压板软件等。
然后进行薄膜裁切和胶粘剂准备。
3. 电路图转移:将电路图通过光电成像技术转移到基材上,形成电路图案。
这可以通过使用照相制版或者印刷相机等设备实现。
4. 铜箔蚀刻:在电路图案上用蚀刻技术去除多余的铜箔,形成所需的导线和连接点。
铜箔蚀刻可以使用酸性浸蚀剂,如铁(III)氯化物溶液等。
5. 焊接:在需要焊接的位置,通过专用工具对导线进行焊接。
通常采用的是热电偶焊接或激光焊接等方法。
6. 路径铜箔涂覆:在需要增加走线的位置,通过热熔法或激光法在基材上涂覆一层薄铜箔,形成导线路径。
这种方法可以提高电路板的导电性能。
7. 背胶压合:将背胶预先涂覆在基材上,然后通过热压法将背胶和导线固定在一起,形成柔性电路板的整体结构。
8. 焊盘覆铜:在柔性电路板上需要焊接元件的位置,使用化学镀铜或真空沉积等方法在导线上涂覆一层铜箔,形成焊盘。
9. 表面保护:为了保护电路板不受外界环境的影响,可以在导线上涂覆一层保护剂,如聚酯涂层或聚酰亚胺涂层等。
这可以增加电路板的耐用性和可靠性。
10.切割和成品检测:根据客户要求,将刚完成的柔性电路板切割成所需的尺寸和形状,并进行成品检测,包括电阻、绝缘等指标的测试。
以上是柔性电路板的生产工艺,其具有较高的可靠性和灵活性,广泛应用于电子产品、通信设备和汽车等领域。
随着新材料和新工艺的引入,柔性电路板的生产工艺也在不断发展和改进,以满足不同应用的需求。
柔性电路板(FPC)工艺介绍

FPC压合工艺介绍1.层压工艺流程:叠层→开模→上料→闭模→预压→成型→冷却→开模→下料→检查→下工序2.叠层操作指示:A.生产前准备好离型膜\钢板\硅胶并用粘尘布或粘尘纸清洁钢板\硅胶\离型膜表面灰尘,杂物等.B.将离型膜尺寸开好(500m*500m),放臵在叠层区备用,且每叠层完一个周期的软板,需备用钢板400块,使生产延续不至于断料.C.叠层操作时,需双手戴手套或5指戴手指套,严禁裸手接触软板.D.叠板时先放钢板硅胶离型膜FPC 离型膜硅胶钢板.一直按此叠10层(特殊要求除外)每一层摆放FPC数量以每1PNL板尺寸大小确定一层可摆FPC的数量是多少(板到硅胶四边的距离需保持7cm以上)摆板时应尽量将FPC摆放于硅胶中央部位,且每块板间距为2cm.每一层里面摆放FPC的厚度要一致(例如:单面板不可与多层板混放)每一开口,每一层摆放FPC的图形要一样,且摆放图形的位臵和顺序大致相同.摆放时应将FPC覆膜面或贴补强面朝上.离型膜要平整覆盖于软板上,不能有折皱和折叠现象.操作完毕,将叠层好的FPC平放在运输带上,送至下工序.3.注意事项:叠层时操作必须戴手套或手指套叠层前检查钢板是否有凹凸不平,硅胶是否有破损\裂痕\蜂眼.离型膜是否粘有垃圾.无以上不良现象的钢板\硅胶\离型膜方能使用于生产叠层时摆放FPC的位臵及图形需一致放离型膜时,必须先确认离型膜正反面.确认方法:1.用油性笔在离型膜一角落划一下,如果笔迹很清楚定为反面,不清晰为正面.2.戴白手套触摸离型膜,有一面很光滑可以逻劲的那一面为正面,反之为反面.4.层压操作指示:A.流程: 生产流程:退膜前处理贴合压合电镀层压流程:钻孔→贴BS膜→过塑→压基材→沉镀Cu→干膜→蚀刻→前处理→贴膜→叠层→压合→检查→下工序生产材料配置:名称规格钢板550*500mm硅胶500*500mm离型膜500*500mm5.工艺说明:A.叠层:在叠层台面上放一块钢板\硅胶\离型膜\软板\离型膜\硅胶\钢板\按此顺序以此类推.叠+层为一个开口B.上料:由两人站在两侧,前后一起抓住叠好的10层(一个开口)的板,轻轻慢慢地抬起放到压合机前每一个开口的边缘,慢慢地推到模板的正中间.不允许只抓一层钢板或只推一块钢板,防止钢板\硅胶\软板\离型膜错位及滑动.叠层结构:钢板------------------------------------------硅胶**************************离型膜------------------------------------------软板++++++++++++++++++++++++++离型膜------------------------------------------硅胶**************************钢板------------------------------------------C.压合:将叠层好的板逐个开口放好后,在机台控制面板上按“闭模”键,模板上开到顶部时,会自动停止并进入预压状态.预压10-15分钟后,须将压力调到所压之型号的工艺参数,详见<压制参数一览表>,此时进入成型压合状态.D.冷却:当成型压合时间到了之后,就将控制面板上的冷却水开关打开,进水管的四个阀门也打开,以及加热开关关闭.将温度降至80℃以下后方可下料.并将冷却水开关及进水开关全部关闭.加热开关打开升温为下次作好准备.E.下料:冷却时间足够后,按开模键.压机开始卸压,模板下降到底部时,戴好厚手套,两个人侧分开站好,分别抬出各个开口的10层板.将钢板\硅胶\离型膜一层层掀开,且把钢板\硅胶摆放齐.废离型膜扔到垃圾桶里.压好的软板用PP膠片隔放好.6.工艺控制:A.压合机在压合之前须检查机器台面是否干净,钢板有无变形,硅胶有无破损,离型膜有无皱折.确认好之后方可生产.B.参数设定:温度时间压力175±10℃传压30-60min 10-15MP固化温度时间150±10℃1-2h7.工艺维护、开关机操作和设备维护A.快压\传压开关机a.合上电源总开关,将开关拨到“ON”位臵.电气柜上电源指示灯亮b. 选择手动操作,按下闭模按钮.油泵电机运转,闭模指示灯亮.柱塞在液压作用下带动热板上开\合模,继而升压.当液压缸内的液压力升至表下限时,油泵开始工作.至最上限时泵止.从而完成闭模动作.B.成型结束后,按下开模按钮,电机运转指示灯亮,既开模.当柱塞下降时,撞到触动行开关时,泵停止.C.加热控制系统温度控制是数字温度调节器来实现自动检测.目板的温度可以在电气柜上的调节气器读出,下排是设定温度,上排是实际温度显示.面板上的“OUT/ON键控制加热温度的启动与停止.D.烘箱\开关机a.设定温度及时间,然后按下“启动”键加热器开始加热.b.待加热到设定温度,带上防高温手套,打开烘箱门,把软板放入烘箱内,将烘箱门关上.c.当设定时间到达时,警报器响.这时只需将“电热”键关上,待温度降到50℃以下,方可将软板取出.d.如需重新工作,只要将“电热”键开启即可.8.检验:A.压不实:即包封膜压不结实,紧密.1.线路导体须有0.13mm以上的间距.2.导体之间的压不实面积超过线距的20%时作返压处理.3.压不实区域长度超过0.13mm时作返工处理.B.气泡:即包封与铜箔之间充有空气,形状凸起.1.气泡长度≥10mm时判定为NG2.气泡横跨两导体时判定为NG3.气泡接触处形时判定为NGC.线路扭曲1.线路扭曲,扭折现象不允许D.溢胶:包封膜的胶溢出Cu面1.溢胶面积≤0.2mm时判定为OK.带孔的焊盘溢胶量≤1/4焊盘面积判定OK.孔边焊盘最小可焊量不小于0.1mm.E.孔内残胶:不允许孔内有残胶F.折痕\压痕\压伤(压断线,造成线路受损作报废处理)a.FPC表面伤痕长度L≥20mm,且深度明显,不允许其它轻微的可通过U A I处理.G.可靠性能测试:a.剥离程度测试b.热冲击性能测试。
- 1、下载文档前请自行甄别文档内容的完整性,平台不提供额外的编辑、内容补充、找答案等附加服务。
- 2、"仅部分预览"的文档,不可在线预览部分如存在完整性等问题,可反馈申请退款(可完整预览的文档不适用该条件!)。
- 3、如文档侵犯您的权益,请联系客服反馈,我们会尽快为您处理(人工客服工作时间:9:00-18:30)。
收藏天地 电邮 killmai@
资料提供 timor Page:5 of 11
整孔
黑孔
微蝕
鍍銅
4.3.1. 4.3.2.
黑孔注意事項 微蝕是否清潔 鍍銅注意事項 夾板是否夾緊 鍍銅面銅厚度 孔銅切片檢查
無滾輪痕 不可孔破
水痕
壓折痕
收藏天地 电邮 killmai@
收藏天地 电邮 killmai@
资料提供 timor
軟性印刷電路板簡介
Introduction to FLEXIBLE PRINTED CIRCUIT
收藏天地 电邮 killmai@
目
錄
资料提供 timor
1. 軟板簡介 ................................. 1 2. 基本材料 ................................. 1 3. 常用單位 ................................. 2 4. 軟板製程 ................................. 2
4.3.黑孔/鍍銅 Black Hole/Cu Plating 於鑽孔後 以黑孔方式於孔壁絕緣位置以碳粉附著而能導電 再以鍍 銅方式於孔壁上形成孔銅達到上 下線路導通之目的 其大致方式為 先以整孔劑使孔壁帶正電荷 經黑孔使帶負電微粒之碳粉附著於表 面 再以微蝕將銅面上之碳粉剝離 僅留孔壁絕緣位置上有一層碳粉 經鍍銅後形成孔銅
# 離型紙方向
0-無, 1-上, 2-下, 3-雙面
A 加強片 A
4.2.2. 鑽孔程式版面設計
對位孔 位於版面四角 其中左下角為 2 孔(方向孔) 其餘 3 個角
均為 1 孔 共 5 孔 此五孔為鑽孔時尋邊用 亦為曝光及
AOI 之套 Pin 孔以及方向辨別用
斷針檢查孔 位於左下角之方向孔上方 為每一孔徑鑽針所鑽之最
2.5.2. 鍚鉛印刷 於裸銅面上以鍚膏印刷方式再過迴焊爐
Байду номын сангаас
2.5.3. 電鍍 電鍍錫/鉛(Sn/Pb) 鎳/金(Ni/Au)
2.5.4. 化學沈積 以化學藥液沈積方式進行錫/鉛 鎳/金表面處理
2.6. 背膠(雙面膠)
膠系一般有 Acrylic 膠及 Silicone 膠等 而雙面膠又區分為有基材
(Substrate)膠及無基材膠
RR
40T(30B)
覆蓋膜
品料號末三碼 版別 40/30 程式格式
T 上 CVL B 下 CVL
加強片鑽孔程式
B46
NNN
RR
4#A
加強片
品料號末三碼 版別 4 程式格式
# 離型紙方向
0-無, 1-上, 2-下, 3-雙面
A 加強片 A
背膠鑽孔程式
B47
NNN
RR
4#A
背膠
品料號末三碼 版別 4 程式格式
底片編號標記 做為底片複本之管制 為以 8888 數字標記
最小線寬/線距標記 W/G 供蝕刻條件設定
品 DateCode 標記 做為生 週期之控制 以 8888 數字標記
順序為週/年
工單編號標示框 W/N[
] 做為工單編號填寫用
備註 8888 數字表示方式如下
4.4.6. 4.4.7.
壓膜注意事項 乾膜不可皺折 壓膜須平整 不可有氣泡 壓膜滾輪須平整及清潔 壓膜不可偏位 雙面板裁切乾膜時須切 不可殘留乾膜屑 曝光注意事項 底片藥膜面須正確(接觸乾膜方向) 底片須清潔 不可有刮傷 物 缺口 凸出 針 等情形 底片壽命是否在使用期限內 底片工令號是否正確 曝光對位須準確 不可有孔破 偏位之情形 曝光能量 21 階測試 須在 7~9 階間 吸真空是否足夠 時間 牛頓 是否出 曝光台面之清潔
=底片版別
NNNNN= 品料號
TRA 線路底片
T=正面線路 B=背面線路
C01=底片代碼
4.4.4. 底片版面設計 Tooling Hole
曝光套 Pin 孔(D) 底片經沖孔後供曝光套 Pin 用
沖孔輔助孔(H) 供底片或線路沖孔之準備孔
AOI 套 Pin 孔(D) 線路上同曝光套 Pin 孔供 AOI 套 Pin 用
收藏天地 电邮 killmai@
资料提供 timor Page:2 of 11
2.3.2. FR4 為 Expoxy 材質
2.3.3. 樹脂板 一般稱尿素板
補強材料一般均以感壓膠 PRESSURE SENSITIVE ADHESIVE 與軟板貼合
但 PI 補強膠片則均使用熱熔膠(Thermosetting)壓合
曝光
顯影
蝕刻
剝膜
4.5.1. D.E.S.注意事項 放板方向 位置 單面板收料速度 左右不可偏擺 顯影是否完全 剝膜是否完全 是否有烘乾 線寬量測 線路檢驗
收藏天地 电邮 killmai@
资料提供 timor Page:1 of 11
1. 軟板(FLEXIBLE PRINTED CIRCUIT)簡介 以俱撓性之基材製成之印刷電路板 裝及動態撓曲等優
具有體積小
重量輕
可做 3D 立體組
2. 基本材料
2.1.銅箔基材 COPPER CLAD LAMINATE
2.4. 印刷油墨
印刷油墨一般區分為防焊油墨(Solder Mask 色) 文字油墨
(Legen 白色 黑色) 銀漿油墨(Silver Ink 銀色)三種 而油墨種
類又分為 UV 硬化型(UV Cure)及熱烘烤型(Thermal Post Cure)二種
2.5. 表面處理
2.5.1. 防銹處理 於裸銅面上抗氧化劑
资料提供 timor Page:6 of 11
4.4.壓膜/曝光 Dry Film Lamination/Exposure
4.4.1. 乾膜 Dry Film
為一抵抗蝕刻藥液之介質 藉由曝光將影像轉移 顯影後有曝光之
位置將留下而於蝕刻時可保護銅面不被蝕刻液侵蝕形成線路
4.4.2. 底片
底片為一透明膠片 我們所使用之曝光底片為一負片 看得到黑色
3. 常用單位 : 線寬/距之量測單位 1mil= 10-3 inch= 25.4x10-3 mm= 0.0254 mm 3.2. : 鍍層厚度之量測單位 =10-6 inch
4. 軟板製程 4.1. 一般流程
Double Sided
NC Drilling
Black Hole
Cu Plating
由銅箔+膠+基材組合而成 亦有無膠基材 亦即僅銅箔+基材 其價
格較高 在目前應用上較少 除非特殊需求
2.1.1. 銅箔 Copper Foil
在材料上區分為壓延銅(ROLLED ANNEAL
Copper Foil)及電解銅(ELECTRO DEPOSITED
Copper Foil)兩種 在特性上來說 壓延銅 之機械特性較佳 有撓折性要求時大部分均
部分為我們所不要之位置 透明部分為我們要留下之位置 底片
有藥膜面及非藥膜面 藥膜面錯誤會造成曝光時光散射而造成影像
轉移時無法達到我們所要之線寬尺寸造成良率降低
底片
藥膜 乾膜 曝光之乾膜
基材
4.4.3. 底片編碼原則
C01 –T TRA - NNNNN REV.
MM/DD/YY
MM/DD/YY=月/日/年
高 但其耐燃性較佳 PET 價格較低 但不
Adhesive
耐熱 因此若有焊接需求時 大部分均選用
Coverlay
PI 材質
厚度上則區分為 1mil 2mil 兩種
2.1.3. 膠 Adhesive
膠一般有 Acrylic 膠及 Expoxy 膠兩種 最常使用 Expoxy 膠
厚度上由 0.4~1mil 均有 一般使用 1mil 膠厚
4.2.鑽孔 NC Drilling 雙面板為使上 下線路導通 以鍍通孔方式
资料提供 timor Page:3 of 11
先鑽孔以利後續鍍銅
4.2.1. 鑽孔程式編碼
銅箔基材鑽孔程式
B40
NNN
RR
400(300)
銅箔基材 品料號末三碼 版別 程式格式(4000/3000)
覆蓋膜鑽孔程式
B45
NNN
4.1.一般流程 ............................. 2 4.2.鑽孔 ................................. 3 4.3.黑孔/鍍銅 ............................ 4 4.4.壓膜/曝光 ............................ 6 4.5.顯影/蝕刻/剝膜 ....................... 8 4.6.微蝕 ................................. 8 4.7.CVL 假接著/壓合....................... 9 4.8.沖孔 ................................. 9 4.9.鍍錫鉛 ............................... 9 4.10. .................................... 水平噴錫9 4.11. .................................... 印刷 10 4.12. .................................... 沖型 10 4.13. .................................... 電測 10
Coverlay Adhesive
選用壓延銅 厚度上則區分為 1/2oz (0.7mil) 1oz 2oz 等三種 一般均使用 1oz 2.1.2. 基材 Substrate 在材料上區分為 PI (Polymide ) Film 及 PET (Polyester) Pilm 兩種 PI 之價格較