常用的内孔加工方法与特点解析修订稿
内孔加工方法

内孔加工方法
❖ 盲孔车削
车盲孔时内孔车刀的刀尖必须与工件中心线高度相同,否则孔底将不能 被车平。同时还必须保证盲孔车刀刀尖至刀柄外侧的距离a要小于内也 半径R,否则将无法车削到孔底中心,刀柄外侧就已与孔壁上部相碰。
控制车孔深度的方法通常采用粗车时在刀柄上刻线痕作记号或安放限位 铜片,以及利用床鞍刻度控制线来控制等,精车时需用小滑板刻度盘或 游标深度尺等来控制车孔的深度。
内孔加工方法
内孔加工方法
孔的车削基本上与车外圆相同,只是进刀和退刀的方向相反。下面我们 对通孔、盲孔与台阶孔的车削分别进行介绍。
❖ 通孔车削
启动车床,主轴正转,分别摇动大滑轮与中滑板,使刀尖接近并轻轻接 触工件内孔壁,以此作为确定切削深度的零点位置。
中滑板少量进刀,试车,纵向退刀,停车,对试车的内孔部分进行测量。 粗车,由于刀杆伸出较长所以,粗车时的切削用量要比车外圆时适当减
在粗车进行后,留有一些精车余量,测量,确定进刀量,精车。
内孔工方法
❖ 台阶孔车削
车直径较小的阶台孔时,由于观察困难而尺寸精度不宜掌握,所以常采 用粗、精车小孔,再粗精车大孔。
车大的台阶也时,在便测量小孔尺寸而视线又不受影响的情况下,一般 先粗车大孔和小孔,再精车小孔和大孔。
车削孔径尺寸相差较大的阶台孔时,最好采用主偏角Kr<90°(一般为 85°~88°)的车刀先粗车,然后再用主偏角Kr<90°刀精车。
内孔加工方法
❖ 车端面,钻中心孔。
钻孔,选择比孔径略小的钻头先钻出底孔。其钻孔深度从钻头顶尖量起, 并在钻头刻线作记号,以控制钻孔深度。然后用相同直径的平头钻将孔 底扩成平底,在孔底平面略留有精车余量。
内孔表面加工常用方法大汇总

内孔表面加工方法较多,常用的有钻孔、扩孔、铰孔、镗孔、磨孔、拉孔、研磨孔、珩磨孔、滚压孔等。
一、钻孔用钻头在工件实体部位加工孔称为钻孔。
钻孔属粗加工,可达到的尺寸公差等级为IT13~IT11,表面粗糙度值为Ra50~12.5μm。
钻孔有以下工艺特点:1.钻头容易偏斜。
在钻床上钻孔时,容易引起孔的轴线偏移和不直,但孔径无显著变化;在车床上钻孔时,容易引起孔径的变化,但孔的轴线仍然是直的。
因此,在钻孔前应先加工端面,并用钻头或中心钻预钻一个锥坑,以便钻头定心。
钻小孔和深孔时,为了避免孔的轴线偏移和不直,应尽可能采用工件回转方式进行钻孔。
2.孔径容易扩大。
钻削时钻头两切削刃径向力不等将引起孔径扩大;卧式车床钻孔时的切入引偏也是孔径扩大的重要原因;此外钻头的径向跳动等也是造成孔径扩大的原因。
3.孔的表面质量较差。
钻削切屑较宽,在孔内被迫卷为螺旋状,流出时与孔壁发生摩擦而刮伤已加工表面。
4.钻削时轴向力大。
这主要是由钻头的横刃引起的。
因此,当钻孔直径d﹥30mm时,一般分两次进行钻削。
第一次钻出(0.5~0.7)d,第二次钻到所需的孔径。
由于横刃第二次不参加切削,故可采用较大的进给量,使孔的表面质量和生产率均得到提高。
二、扩孔扩孔是用扩孔钻对已钻出的孔做进一步加工,以扩大孔径并提高精度和降低表面粗糙度值。
扩孔可达到的尺寸公差等级为IT11~IT10, 表面粗糙度值为Ra12.5~6.3μm,属于孔的半精加工方法,常作铰削前的预加工,也可作为精度不高的孔的终加工。
扩孔方法如图7-4所示,扩孔余量(D-d),可由表查阅。
扩孔钻的形式随直径不同而不同。
直径为Φ10~Φ32的为锥柄扩孔钻,如图7-5a所示。
直径Φ25~Φ80的为套式扩孔钻,如图7-5b所示。
扩孔钻的结构与麻花钻相比有以下特点:1.刚性较好。
由于扩孔的背吃刀量小,切屑少,扩孔钻的容屑槽浅而窄,钻芯直径较大,增加了扩孔钻工作部分的刚性。
2.导向性好。
内孔的加工讲解
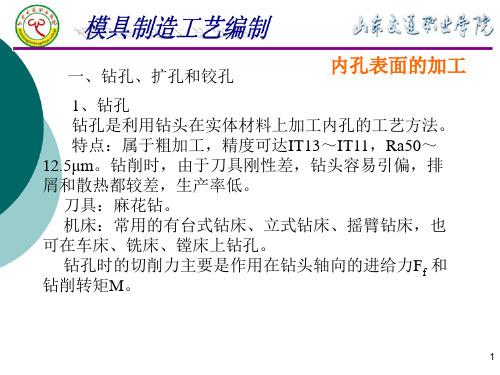
15
11
四、磨孔与孔的精密加工 1 磨孔工艺特点:属于孔的精加方法。精度可达IT7, Ra1.6~0.4 μm。 磨孔不仅能获得较高的尺寸精度和表面质量,而且 还可以提高孔的位置精度和孔的轴线的直线度。与外圆 磨削相比,工作条件较差:砂轮直径小,刚性差,排屑 和散热困难,生产率低。对于淬硬零件中的孔加工,磨 孔是主要的加工方法。 内孔为断续圆周表面(如有键槽或花键的孔)、阶 梯孔及盲孔时,常采用磨孔作为精加工。
研磨孔是一种光整加工方法。精度可达IT7~IT6, Ra0.4~0.025μm,形状精度也有相应的提高,但不能提 高位置精度。
16
珩磨头对孔施加一定压力,结构如图;切除极小的 加工余量。
17
②研磨孔是一种光整加工方法。精度可达IT7~IT6, Ra0.4~0.025μm,形状精度也有相应的提高,但不能提 高位置精度。需要在精镗、精铰或精磨之后进行。
18
固定式研磨棒多用于单件生产。带槽研磨棒便于存 贮研磨剂,用于粗研,光滑研磨棒,一般用于精研。如 图所示 。所有研具采用比工件软的材料制成,这些材料 为铸铁、铜、青铜、巴氏合金及硬木等。有时也可用钢 做研具。研磨时,部分磨粒悬浮于工件与研具之间,部 分磨粒则嵌入研具的表面层,工件与研具作相对运动, 磨料就在工件表面上切除很薄的一层金属 ( 主要是上工 序在工件表面上留下的凸峰 ) 。
12
磨孔时砂轮的尺寸受被加工孔径尺寸的限制,一般 砂轮直径为工件孔径的 0.5—0.9 倍,磨头轴的直径和 长度也取决于被加工孔的直径和深度。故磨削速度低, 磨头的刚度差,磨削质量和生产率均受到影响。
轴类零部件内孔加工方法

轴类零部件内孔加工是机械加工中常见的一项工艺,确保内孔的精度和表面质量对零部件的功能和性能至关重要。
以下是一些常见的轴类零部件内孔加工方法:
1. 钻削:
- 钻削是最基本的内孔加工方法之一。
通过使用钻头,可在工件上创建孔。
对于较小直径和较短深度的内孔,钻削是一种经济有效的方法。
2. 铰削:
- 铰削是通过使用铰刀,将内孔表面进行切削,以提高其精度和表面质量。
铰刀可以调整,使内孔具有所需的直径和形状。
3. 车削:
- 车削是通过使用车刀在工件上旋转的情况下,切削内孔的一种方法。
车削通常用于制作较大直径和较深的内孔,可以实现较高的加工效率。
4. 镗削:
- 镗削是通过使用镗刀,以旋转或振动的方式切削内孔。
这种方法可以实现较高的精度和表面质量,特别适用于对内孔直径和圆度有严格要求的情况。
5. 滚压:
- 滚压是通过使用滚轮或滚动刀具,将内孔材料进行塑性变形,从而形成所需的内孔形状。
这种方法可以提高内孔的表面质量和硬度。
6. 磨削:
- 磨削是通过使用磨石或磨削刀具,对内孔进行精细磨削,以获得高精度和高表面质量。
磨削通常用于对内孔直径和形状有极高要求的情况。
7. 激光加工:
- 激光加工是通过激光束将内孔材料切割或蒸发,以实现对内孔进行精确加工的方法。
这种方法适用于一些特殊材料或需要非常高精度的内孔加工。
在选择合适的轴类零部件内孔加工方法时,需要考虑材料特性、加工精度、生产效率和成本等因素。
通常,工程师会根据具体的要求和工件特点选择最合适的加工方法。
内孔研磨方法

内孔研磨方法1. 概述内孔研磨是一种常见的表面处理技术,主要应用于金属制品的加工过程中。
通过内孔研磨方法,可以改善金属件的表面粗糙度、形状误差,提高其加工精度和使用寿命。
本文将介绍内孔研磨的基本原理、常用研磨方法以及注意事项。
2. 内孔研磨的原理内孔研磨是利用磨削工具对孔壁进行磨削,使其表面达到一定的精度和光洁度。
其基本原理包括以下几个方面:2.1 磨削力学原理内孔研磨时,磨削工具施加在孔壁上的力会使磨粒与孔壁之间发生相对运动,从而产生磨削作用。
在磨削过程中,磨粒会不断切削孔壁上的金属,使其表面达到预期的精度。
2.2 磨削液的作用磨削液在内孔研磨中起到冷却、润滑和清洁的作用。
它可以降低磨削过程中的摩擦热和摩擦力,减少磨削工具与孔壁的磨损,同时还可以冲洗掉产生的切屑和磨粒,保持磨削的稳定性和效果。
3. 常用内孔研磨方法内孔研磨方法主要包括以下几种:3.1 钻孔研磨法钻孔研磨法是一种常见的内孔研磨方法。
它通过将研磨工具安装在钻孔机上,利用旋转运动对孔壁进行磨削。
这种方法适用于直径较小且长度较短的孔壁。
钻孔研磨法具有操作简单、成本低廉的特点,但对于孔壁的形状精度和表面粗糙度要求较高的情况下,效果可能不理想。
3.2 磨削棒研磨法磨削棒研磨法是一种较为常用的内孔研磨方法。
它采用磨棒作为研磨工具,通过旋转和推进的方式对孔壁进行磨削。
这种方法适用于直径较大的孔壁,可以满足一定的加工精度和表面要求。
磨削棒研磨法的优点是操作简单、成本低廉,但对于孔壁的圆度和直线度要求较高的情况下,可能存在一定的局限性。
3.3 内圆磨砂研磨法内圆磨砂研磨法是一种高精度的内孔研磨方法。
它采用内圆磨轮作为研磨工具,通过旋转和推进的方式对孔壁进行磨削。
这种方法适用于直径较小、形状要求较高的孔壁,可以达到较高的加工精度和表面质量。
内圆磨砂研磨法的缺点是设备价格较高,操作要求较为复杂。
4. 内孔研磨的注意事项在进行内孔研磨时,需要注意以下几个方面:4.1 研磨工具的选择根据孔壁的直径、长度和形状要求,选择合适的研磨工具。
孔的加工方法有哪些

孔的加工方法有哪些孔的加工方法有很多种,下面将逐一介绍其中一些较为常见和常用的方法。
一、钻孔。
钻孔是最基本、最常见的孔加工方法之一。
钻孔的主要工具是钻,通常是使用手动或机械钻来实现。
钻孔可以用于加工各种材料,如金属、木材和塑料等。
钻孔可分为常规钻孔和深孔钻孔。
常规钻孔主要用于加工孔径较小的孔洞,而深孔钻孔则用于加工深孔孔洞。
二、镗孔。
镗孔是一种通过旋转刀具来加工孔洞的方法。
这种方法主要用于加工较大直径或较大长度的孔洞。
镗孔的刀具称为镗刀,它与被加工的孔洞有几乎相同的形状和尺寸。
镗孔通常分为手动镗孔和机械镗孔两种方式,在机械镗孔中,有进给镗孔和振动镗孔等不同的方式。
三、铰孔。
铰孔是一种用于加工内螺纹孔和螺旋槽孔的方法。
这种方法主要通过铰刀进行加工,铰孔可以将孔洞加工成不同规格的螺纹或槽。
铰孔的方式有手动铰孔和机械铰孔两种。
四、扩孔。
扩孔是通过专用的工具对已经存在的孔洞进行加工,使其直径变大的方法。
这种方法通常用于调整孔洞的尺寸或加工锥形孔洞。
扩孔的工具有扩孔钻、扩孔机等。
五、插孔。
插孔是通过插削和切削来加工孔洞的方法。
这种方法通常用于加工较大直径和深度的孔洞。
插孔使用的刀具通常为铣刀或孔镗刀。
插孔可分为轮廓插孔和径向插孔两种方式。
六、滚花孔。
滚花孔是通过滚花刀具沿孔壁进行旋转来加工出带有滚花形状的孔洞。
这种方法主要用于装饰和美化材料表面。
七、激光孔加工。
激光孔加工是一种利用激光器对材料进行烧蚀来加工孔洞的方法。
这种方法通常用于加工高硬度和高耐磨材料,如金属合金和陶瓷等。
八、放电加工。
放电加工是一种利用电火花放电的方式加工孔洞的方法。
这种方法通常用于加工硬度较高的材料,如工具钢和硬质合金等。
九、冲孔。
冲孔是一种利用冲压机械对材料进行冲压,形成孔洞的方法。
这种加工方法通常适用于薄板材料,如金属板和塑料片等。
总之,孔的加工方法有很多种,每种方法都有其适用的材料和特定的加工需求。
在实际应用中,可以根据具体情况选择合适的孔加工方法来进行加工。
常用的内孔加工方法与特点解析

常用的内孔加工方法与特点解析The manuscript was revised on the evening of 2021一、钻孔在模具零件上用钻头主要有两种方式:一种是钻头回转,零件固定不回转,如在普通台式钻床、摇臂钻、镗床上钻孔;另外一种方式零件回转而钻头不回转,如在车床上钻孔,这两种不同的钻孔方式所产生的误差不一样,在钻床或镗床上钻孔,由于钻头回转,使刚性不强的钻头易引偏,被加工孔的中心线偏移,但孔径不会发生变化。
钻头的直径一般不超过75mm,若钻孔大于30mm以上,通过采用两次钻销,即先用直径较小的钻头(被要求加工孔径尺寸的~倍)先钻孔,再用孔径合适的钻头进行第二次钻孔直到加工到所要求的直径。
以减小进给力。
钻头钻孔的加工精度,一般可以达到IT11~IT13级,表面粗糙度Ra为~。
二、扩孔用扩孔钻扩大零件孔径的加工方法,既可以作为精加工(铰孔、镗孔)前的预加工,也可以作为要求不高的孔径最终加工。
孔径的加工精度,一般可以达到IT10~IT13级,表面粗糙度Ra为~。
三、铰孔是用铰刀对未淬火孔进行精加工的一种孔径的加工方法。
铰孔的加工精度,一般可以达到IT6~IT10级,表面粗糙度Ra为~。
在模具制造加工中,一般用手工铰孔,其优点是切削速度慢,不易升温和产生积屑瘤,切削时无振动,容易控制刀具中心位置,因此当孔的精度要求很高时,主要用手工铰孔,或机床粗铰再用手工精铰。
在铰孔时应主要以下几点:a. 合理选择铰孔销孔余量及切削和规范;b. 铰孔刃口平整,能提高刃磨质量;c. 铰销钢材时,要用乳化液作为切削液。
四、车孔在车床上车孔,主要特征是零件随主轴回转,而刀具做进给运动,其加工后的孔轴心线与零件的回转轴线同轴。
孔的圆度主要取决于机床主轴的回转精度,孔的纵向几何形状误差主要取决于刀具的进给方向。
这种车孔方式适用于加工外圆表面与孔要求有同轴度的零件。
五、镗孔在镗床上镗孔,主要靠刀具回转,而零件做进给运动。
孔加工方法的工艺特点
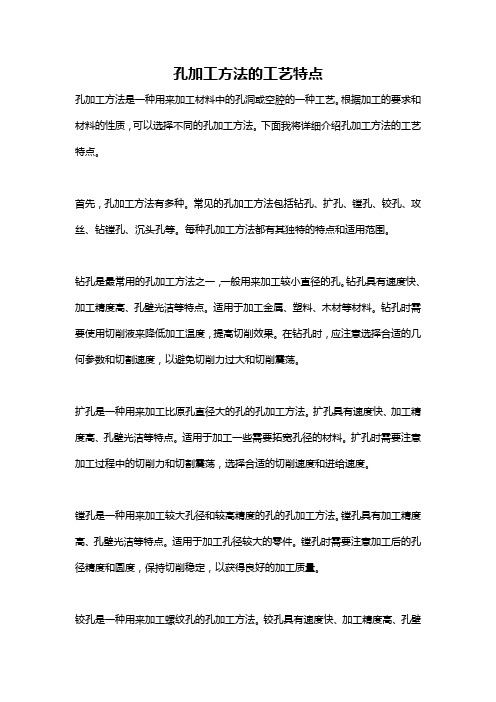
孔加工方法的工艺特点孔加工方法是一种用来加工材料中的孔洞或空腔的一种工艺。
根据加工的要求和材料的性质,可以选择不同的孔加工方法。
下面我将详细介绍孔加工方法的工艺特点。
首先,孔加工方法有多种。
常见的孔加工方法包括钻孔、扩孔、镗孔、铰孔、攻丝、钻镗孔、沉头孔等。
每种孔加工方法都有其独特的特点和适用范围。
钻孔是最常用的孔加工方法之一,一般用来加工较小直径的孔。
钻孔具有速度快、加工精度高、孔壁光洁等特点。
适用于加工金属、塑料、木材等材料。
钻孔时需要使用切削液来降低加工温度,提高切削效果。
在钻孔时,应注意选择合适的几何参数和切割速度,以避免切削力过大和切削震荡。
扩孔是一种用来加工比原孔直径大的孔的孔加工方法。
扩孔具有速度快、加工精度高、孔壁光洁等特点。
适用于加工一些需要拓宽孔径的材料。
扩孔时需要注意加工过程中的切削力和切割震荡,选择合适的切削速度和进给速度。
镗孔是一种用来加工较大孔径和较高精度的孔的孔加工方法。
镗孔具有加工精度高、孔壁光洁等特点。
适用于加工孔径较大的零件。
镗孔时需要注意加工后的孔径精度和圆度,保持切削稳定,以获得良好的加工质量。
铰孔是一种用来加工螺纹孔的孔加工方法。
铰孔具有速度快、加工精度高、孔壁光洁等特点。
适用于加工螺纹孔。
铰孔时需要注意选择合适的铰孔工具,并使用适当的切削液,以降低切削温度,提高切削效果。
攻丝是一种用来加工内螺纹的孔加工方法。
攻丝具有速度快、加工精度高、孔壁光洁等特点。
适用于加工内螺纹。
攻丝时需要选择合适的攻丝工具,并使用适当的切削液,以降低切削温度,提高切削效果。
钻镗孔是一种用来加工孔径较大和孔深较大的孔的孔加工方法。
钻镗孔具有加工精度高、孔壁光洁等特点。
适用于加工孔径较大的孔。
钻镗孔时需要注意切削过程中的切削力和切割震荡,选择合适的切削速度和进给速度。
沉头孔是一种用来加工带有沉头的孔的孔加工方法。
沉头孔具有孔底平整、孔口光洁等特点。
适用于加工需要孔底平整的材料。
沉头孔时需要注意沉头的深度和尺寸,以获得良好的孔底质量。
孔加工工艺解析大全
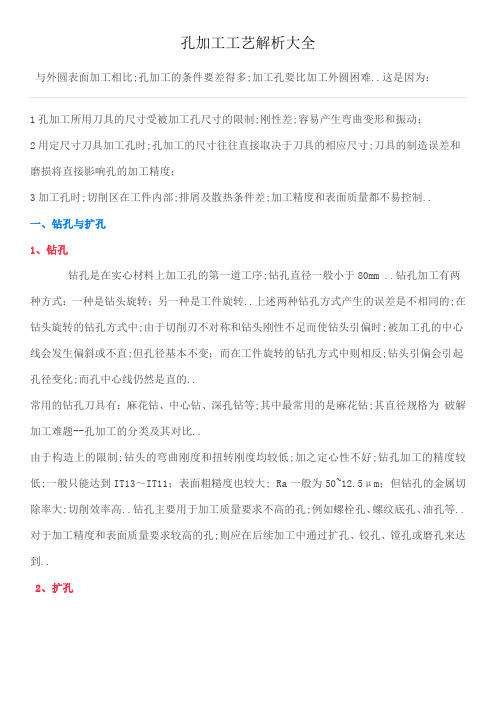
孔加工工艺解析大全与外圆表面加工相比;孔加工的条件要差得多;加工孔要比加工外圆困难..这是因为:1孔加工所用刀具的尺寸受被加工孔尺寸的限制;刚性差;容易产生弯曲变形和振动;2用定尺寸刀具加工孔时;孔加工的尺寸往往直接取决于刀具的相应尺寸;刀具的制造误差和磨损将直接影响孔的加工精度;3加工孔时;切削区在工件内部;排屑及散热条件差;加工精度和表面质量都不易控制..一、钻孔与扩孔1、钻孔钻孔是在实心材料上加工孔的第一道工序;钻孔直径一般小于80mm ..钻孔加工有两种方式:一种是钻头旋转;另一种是工件旋转..上述两种钻孔方式产生的误差是不相同的;在钻头旋转的钻孔方式中;由于切削刃不对称和钻头刚性不足而使钻头引偏时;被加工孔的中心线会发生偏斜或不直;但孔径基本不变;而在工件旋转的钻孔方式中则相反;钻头引偏会引起孔径变化;而孔中心线仍然是直的..常用的钻孔刀具有:麻花钻、中心钻、深孔钻等;其中最常用的是麻花钻;其直径规格为破解加工难题--孔加工的分类及其对比..由于构造上的限制;钻头的弯曲刚度和扭转刚度均较低;加之定心性不好;钻孔加工的精度较低;一般只能达到IT13~IT11;表面粗糙度也较大; Ra一般为50~12.5μm;但钻孔的金属切除率大;切削效率高..钻孔主要用于加工质量要求不高的孔;例如螺栓孔、螺纹底孔、油孔等..对于加工精度和表面质量要求较高的孔;则应在后续加工中通过扩孔、铰孔、镗孔或磨孔来达到..2、扩孔扩孔是用扩孔钻对已经钻出、铸出或锻出的孔作进一步加工;以扩大孔径并提高孔的加工质量;扩孔加工既可以作为精加工孔前的预加工;也可以作为要求不高的孔的最终加工..扩孔钻与麻花钻相似;但刀齿数较多;没有横刃..与钻孔相比;扩孔具有下列特点:1扩孔钻齿数多3~8个齿、导向性好;切削比较稳定;2扩孔钻没有横刃;切削条件好;3加工余量较小;容屑槽可以做得浅些;钻芯可以做得粗些;刀体强度和刚性较好..扩孔加工的精度一般为IT11~IT10级;表面粗糙度Ra为12.5~6.3..扩孔常用于加工直径小于的孔..在钻直径较大的孔时D ≥30mm ;常先用小钻头直径为孔径的0.5~0.7倍预钻孔;然后再用相应尺寸的扩孔钻扩孔;这样可以提高孔的加工质量和生产效率..扩孔除了可以加工圆柱孔之外;还可以用各种特殊形状的扩孔钻亦称锪钻来加工各种沉头座孔和锪平端面示..锪钻的前端常带有导向柱;用已加工孔导向..二、铰孔铰孔是孔的精加工方法之一;在生产中应用很广..对于较小的孔;相对于内圆磨削及精镗而言;铰孔是一种较为经济实用的加工方法..1、铰刀铰刀一般分为手用铰刀及机用铰刀两种..手用铰刀柄部为直柄;工作部分较长;导向作用较好;手用铰刀有整体式和外径可调整式两种结构..机用铰刀有带柄的和套式的两种结构..铰刀不仅可加工圆形孔;也可用锥度铰刀加工锥孔..2、铰孔工艺及其应用铰孔余量对铰孔质量的影响很大;余量太大;铰刀的负荷大;切削刃很快被磨钝;不易获得光洁的加工表面;尺寸公差也不易保证;余量太小;不能去掉上工序留下的刀痕;自然也就没有改善孔加工质量的作用..一般粗铰余量取为0.35~0.15mm;精铰取为01.5~0.05mm..为避免产生积屑瘤;铰孔通常采用较低的切削速度高速钢铰刀加工钢和铸铁时;v <8m/min进行加工..进给量的取值与被加工孔径有关;孔径越大;进给量取值越大;高速钢铰刀加工钢和铸铁时进给量常取为0.3~1mm/r..铰孔时必须用适当的切削液进行冷却、润滑和清洗;以防止产生积屑瘤并及时清除切屑..与磨孔和镗孔相比;铰孔生产率高;容易保证孔的精度;但铰孔不能校正孔轴线的位置误差;孔的位置精度应由前工序保证..铰孔不宜加工阶梯孔和盲孔..铰孔尺寸精度一般为IT9~IT7级;表面粗糙度Ra一般为3.2~0.8 ..对于中等尺寸、精度要求较高的孔例如IT7级精度孔;钻—扩—铰工艺是生产中常用的典型加工方案..三、镗孔镗孔是在预制孔上用切削刀具使之扩大的一种加工方法;镗孔工作既可以在镗床上进行;也可以在车床上进行..1、镗孔方式镗孔有三种不同的加工方式..1工件旋转;刀具作进给运动在车床上镗孔大都属于这种镗孔方式..工艺特点是:加工后孔的轴心线与工件的回转轴线一致;孔的圆度主要取决于机床主轴的回转精度;孔的轴向几何形状误差主要取决于刀具进给方向相对于工件回转轴线的位置精度..这种镗孔方式适于加工与外圆表面有同轴度要求的孔..2刀具旋转;工件作进给运动镗床主轴带动镗刀旋转;工作台带动工件作进给运动..3 刀具旋转并作进给运动采用这种镗孔方式镗孔;镗杆的悬伸长度是变化的;镗杆的受力变形也是变化的;靠近主轴箱处的孔径大;远离主轴箱处的孔径小;形成锥孔..此外;镗杆悬伸长度增大;主轴因自重引起的弯曲变形也增大;被加工孔轴线将产生相应的弯曲..这种镗孔方式只适于加工较短的孔..2、金刚镗与一般镗孔相比;金刚镗的特点是背吃刀量小;进给量小;切削速度高;它可以获得很高的加工精度IT7~IT6和很光洁的表面Ra为0.4~0.05 ..金刚镗最初用金刚石镗刀加工;现在普遍采用硬质合金、CBN和人造金刚石刀具加工..主要用于加工有色金属工件;也可用于加工铸铁件和钢件..金刚镗常用的切削用量为:背吃刀量预镗为 0.2~0.6mm;终镗为0.1mm ;进给量为0.01~0.14mm/r ;切削速度加工铸铁时为100~250m/min ;加工钢时为150~300m/min ;加工有色金属时为300~2000m/min..为了保证金刚镗能达到较高的加工精度和表面质量;所用机床金刚镗床须具有较高的几何精度和刚度;机床主轴支承常用精密的角接触球轴承或静压滑动轴承;高速旋转零件须经精确平衡;此外;进给机构的运动必须十分平稳;保证工作台能做平稳低速进给运动..金刚镗的加工质量好;生产效率高;在大批大量生产中被广泛用于精密孔的最终加工;如发动机气缸孔、活塞销孔、机床主轴箱上的主轴孔等..但须引起注意的是:用金刚镗加工黑色金属制品时;只能使用硬质合金和CBN制作的镗刀;不能使用金刚石制作的镗刀;因金刚石中的碳原子与铁族元素的亲和力大;刀具寿命低..3、镗刀镗刀可分为单刃镗刀和双刃镗刀..4、镗孔的工艺特点及应用范围镗孔和钻—扩—铰工艺相比;孔径尺寸不受刀具尺寸的限制;且镗孔具有较强的误差修正能力;可通过多次走刀来修正原孔轴线偏斜误差;而且能使所镗孔与定位表面保持较高的位置精度..镗孔和车外圆相比;由于刀杆系统的刚性差、变形大;散热排屑条件不好;工件和刀具的热变形比较大;镗孔的加工质量和生产效率都不如车外圆高..综上分析可知; 镗孔的加工范围广;可加工各种不同尺寸和不同精度等级的孔;对于孔径较大、尺寸和位置精度要求较高的孔和孔系;镗孔几乎是唯一的加工方法..镗孔的加工精度为IT9~IT7级;表面粗糙度Ra为 ..镗孔可以在镗床、车床、铣床等机床上进行;具有机动灵活的优点;生产中应用十分广泛..在大批大量生产中;为提高镗孔效率;常使用镗模..四、珩磨孔1、珩磨原理及珩磨头珩磨是利用带有磨条油石的珩磨头对孔进行光整加工的方法..珩磨时;工件固定不动;珩磨头由机床主轴带动旋转并作往复直线运动..珩磨加工中;磨条以一定压力作用于工件表面;从工件表面上切除一层极薄的材料;其切削轨迹是交叉的网纹..为使砂条磨粒的运动轨迹不重复;珩磨头回转运动的每分钟转数与珩磨头每分钟往复行程数应互成质数..珩磨轨迹的交叉角与珩磨头的往复速度及圆周速度有关; 角的大小影响珩磨的加工质量及效率;一般粗珩时取°;精珩时取..为了便于排出破碎的磨粒和切屑;降低切削温度;提高加工质量;珩磨时应使用充足的切削液..为使被加工孔壁都能得到均匀的加工;砂条的行程在孔的两端都要超出一段越程量..为保证珩磨余量均匀;减少机床主轴回转误差对加工精度的影响;珩磨头和机床主轴之间大都采用浮动连接..珩磨头磨条的径向伸缩调整有手动、气动和液压等多种结构形式..2、珩磨的工艺特点及应用范围1珩磨能获得较高的尺寸精度和形状精度;加工精度为IT7~IT6级;孔的圆度和圆柱度误差可控制在的范围之内;但珩磨不能提高被加工孔的位置精度..2珩磨能获得较高的表面质量;表面粗糙度Ra为0.2~ 0.025um ;表层金属的变质缺陷层深度极微2.5~25um..3与磨削速度相比;珩磨头的圆周速度虽不高vc=16~60m/min;但由于砂条与工件的接触面积大;往复速度相对较高va=8~20m/min;所以珩磨仍有较高的生产率..珩磨在大批大量生产中广泛用于发动机缸孔及各种液压装置中精密孔的加工;孔径范围一般为或更大;并可加工长径比大于10的深孔..但珩磨不适用于加工塑性较大的有色金属工件上的孔;也不能加工带键槽的孔、花键孔等..五、拉孔1、拉削与拉刀拉孔是一种高生产率的精加工方法;它是用特制的拉刀在拉床上进行的..拉床分卧式拉床和立式拉床两种;以卧式拉床最为常见..拉削时拉刀只作低速直线运动主运动..拉刀同时工作的齿数一般应不少于3个;否则拉刀工作不平稳;容易在工件表面产生环状波纹..为了避免产生过大的拉削力而使拉刀断裂;拉刀工作时;同时工作刀齿数一般不应超过6~8个..拉孔有三种不同的拉削方式;分述如下:1分层式拉削这种拉削方式的特点是拉刀将工件加工余量一层一层顺序地切除..为了便于断屑;刀齿上磨有相互交错的分屑槽..按分层式拉削方式设计的的拉刀称为普通拉刀..2分块式拉削这种拉削方式的特点是加工表面的每一层金属是由一组尺寸基本相同但刀齿相互交错的刀齿通常每组由2-3个刀齿组成切除的..每个刀齿仅切去一层金属的一部分..按分块拉削方式设计的拉刀称为轮切式拉刀..3综合式拉削这种方式集中了分层及分块式拉削的优点;粗切齿部分采用分块式拉削;精切齿部分采用分层式拉削..这样既可缩短拉刀长度;提高生产率;又能获得较好的表面质量..按综合拉削方式设计的拉刀称为综合式拉刀..2、拉孔的工艺特征及应用范围1拉刀是多刃刀具;在一次拉削行程中就能顺序完成孔的粗加工、精加工和光整加工工作;生产效率高..2拉孔精度主要取决于拉刀的精度;在通常条件下;拉孔精度可达IT9~IT7;表面粗糙度Ra可达6.3~1.6 μm..3拉孔时;工件以被加工孔自身定位拉刀前导部就是工件的定位元件;拉孔不易保证孔与其它表面的相互位置精度;对于那些内外圆表面具有同轴度要求的回转体零件的加工;往往都是先拉孔;然后以孔为定位基准加工其它表面..4拉刀不仅能加工圆孔;而且还可以加工成形孔;花键孔..5拉刀是定尺寸刀具;形状复杂;价格昂贵;不适合于加工大孔..拉孔常用在大批大量生产中加工孔径为Ф10~80mm 、孔深不超过孔径5倍的中小零件上的通孔..。
各种机床加工内孔的特点

各种机床加工内孔的特点机床是用于金属材料加工的设备,包括铣床、车床、钻床、镗床等。
加工内孔是机床的重要应用之一,下面将针对各种机床加工内孔的特点进行介绍。
1.车床加工内孔特点:车床是用来加工旋转对称零件的机床,它通过旋转工件,同时将刀具沿轴向移动来进行切削。
在车床上加工内孔主要有以下特点:-切削速度高:车床具有高速切削的特点,能够在较短的时间内完成内孔的加工。
-切削精度高:车床具有较高的切削精度,能够满足对内孔直径和精度的要求。
-对于较长内孔,需要使用横切车刀具来进行切削,并进行多次进给和回退来完成加工。
2.铣床加工内孔特点:铣床是用来加工平面、曲面和复杂形状工件的机床,通过旋转刀具将工件上的材料切削除去来进行加工。
在铣床上加工内孔主要有以下特点:-加工效率高:铣床能够进行连续的切削操作,因此加工效率较高。
-切削稳定性差:由于铣削过程中工具接触面积较小,因此切削稳定性较差,容易产生振动和切削力变化。
-内孔形状复杂:铣床可以通过刀具的移动轨迹来实现内孔的各种复杂形状。
3.钻床加工内孔特点:钻床是用来加工圆孔的机床,主要通过具有多个切削刃的钻头进行孔加工。
在钻床上加工内孔主要有以下特点:-加工精度高:钻床具有较高的加工精度,能够满足对内孔直径和精度的要求。
-内孔深度有限:由于钻头的长度限制,钻床加工内孔时需要对孔深度进行限制。
-切削速度低:钻床的切削速度较低,切削效率较低,适合对孔加工要求较高的工件进行加工。
4.镗床加工内孔特点:镗床是用于加工定位精度要求较高的内孔的机床,通过刀具的直线运动将孔加工到所需尺寸和精度。
-加工精度高:镗床具有较高的加工精度,能够满足对内孔直径和轴向精度的要求。
-内孔形状可调节:镗床可以通过刀具的调节来实现内孔的形状和尺寸的调整。
-加工速度较慢:由于镗床需要进行多次进给和回退来完成加工,因此加工速度较慢。
综上所述,不同机床加工内孔的特点各有不同,根据工件的要求和加工工艺的需要,选择合适的机床来进行内孔加工是非常重要的。
项目6-1 内孔加工

2、内孔车刀
在数控车床上加工的孔,大部分都是使用内孔车刀来进行加工的。常用的数控内孔车削刀具见图6-3所示。
图6-3内孔车刀
3、内圆切槽车刀
与外圆槽的加工类似,内圆面上的槽也需要相应的内圆切槽车刀来进行加工。常用的数控内圆切槽车刀见图6-4所示。
图6-4内槽车刀
二、内孔加工方法
1、钻孔加工
图6-6自动钻孔
钻孔时需要注意以下几点:
⑴钻孔前,必须先将工件端面车平,中心处不允许有凸台,否则钻头不能自动定心,会使钻头折断。
⑵钻孔起钻时进给量要小,待钻头头部进入工件后才可正常钻削。
⑶钻孔时应根据麻花钻的大小合理选择转速,且加切削液。
⑷钻小孔时,转速应选得快一些,否则钻削时抗力大,容易产生孔位偏斜和钻头折断。
⑵尽可能缩短刀杆的伸出长度,以防止产生振纹;
⑶刀杆安装应平行于工件轴线,且在车孔前应手动将车刀在孔内空走一遍,观察车刀与孔壁的相对位置,防止车削中刀杆与孔壁发生干涉。
3、内圆槽车削
内圆槽车削与外圆槽车削方法基本相同,对于窄槽的车削,尽量选择刀宽与槽宽相等的内槽刀一次加工完成,但受最小孔径及刀杆刚性的限制,不能一次车出的槽应采用分刀次车削的方法完成加工。
教师讲解指导
学生动手练习
2课时
任务扩展
1、加工如图6-7所示的台阶孔零件,毛坯为φ60×45,材料为45钢。
图6-7零件图
2、加工如图6-8所示的带内梯形槽台阶孔零件,毛坯为φ48×45的半成品,材料为45钢。
图6-8带内梯形槽台阶孔零件
课堂车削类零件不仅有外圆面加工,而且有内孔加工。所以本任务的内容也是数控车工必须掌握的。此零件需要采用钻孔、车孔及车内槽的步骤来完成整个零件的加工,要求合理选用刀具,安排工艺步骤并编写相应的加工程序。
孔加工的四种方法

孔加工的四种方法
孔加工是切削加工中常用的一种技术,具有自身的法律规定,一般用来加工承受压力或连接零件的配件,是一种非常重要的加工形式。
孔加工有多种技术,主要有四种方法:切削孔加工,钻孔加工,粗减孔加工和冲孔加工。
首先是切削孔加工,它采用刀具切削来加工高精度的孔,具有良好的精度和光滑程度,且能迅速加工完成,但刀具损耗较大,刃容易磨损,且加工成本较高。
接下来是钻孔加工,它采用工具钻锉出孔洞,具有精密钉比较少、加工速度较快、成本较低等优点,但孔的精度和光滑程度不足,加工的工件材料也有限。
粗减孔加工是比较容易上手的加工方式,采用研磨、抛光等多种方法将加工材料抹减,从而达到加工的目的,可以解决精度等要求,但加工工艺不一定能满足要求,加工速度也较慢。
最后是冲孔加工,这是最常见的孔加工方法,可以根据不同的特性加工得到不同精度的孔洞,能快速获得所需精度,不但价格低廉,而且加工速度快,但受到材料的限制,加工的材料也有限。
综上所述,孔加工有四种常见方法,每种方法都有自身的优势和限制,因此,在采用孔加工时,必须根据具体情况综合评估,合理选择最适合的孔加工方法,以确保质量。
同时,严格把握相关工业环境法律法规,以确保安全,并合理使用和消耗,以降低孔加工成本。
孔的加工方法有哪些

孔的加工方法有哪些孔的加工方法有很多种,根据不同的需求和加工对象,选择合适的加工方法可以提高加工效率和产品质量。
以下是常见的孔的加工方法:1. 钻孔:钻孔是最基本的孔加工方法之一,通过钻头在工件上旋转并施加压力,将钻头逐渐深入工件中,形成所需直径和深度的孔。
钻孔通常适用于加工小直径和长孔,可以使用手动钻床、立式钻床、卧式钻床等设备进行。
2. 镗孔:镗孔是利用回转刀具,以旋转剥削的形式加工孔的一种方法。
镗孔可分为手动镗孔和机械镗孔两种方式。
手动镗孔常用于小型孔的加工,机械镗孔则通过镗床等设备实现,适用于各种尺寸和形状的孔的加工。
3. 铰孔:铰孔是在孔的表面加工切削螺旋槽的方法,通过旋转铰刀,并施加轴向流动来实现。
铰孔通常用于加工与螺纹配合的孔,如螺纹孔、锥孔等。
4. 攻丝:攻丝是在孔内加工内螺纹的方法,通常采用手动或机械操作攻丝刀具,将切削螺纹槽形成所需的螺纹孔。
攻丝广泛应用于机械制造和装配领域。
5. 火焰喷孔:火焰喷孔是利用火焰喷枪产生的高温热源,对工件表面局部加热,使其产生膨胀,再施加机械力,通过物理变形,在工件上形成所需的孔。
6. 激光加工:激光加工是一种高精度的孔加工方法,通过激光束对工件进行瞬时加热和蒸发,从而形成孔洞。
激光加工具有加工速度快、加工精度高的优点,适用于加工小孔和复杂形状的孔。
7. 电火花加工:电火花加工利用高频电脉冲的电火花熔化电极材料和工件,通过电极材料和工件之间的放电,形成孔洞。
电火花加工可以加工任何导电材料,适用于加工硬质合金和高硬度工件。
8. 高速切削:高速切削是通过高速旋转的工具,以快速高效的方式加工孔洞。
高速切削具有加工速度快、表面质量好的优点,适用于加工大批量的孔。
以上是一些常见的孔的加工方法,每种方法都有其适用的场景和优势。
在实际加工过程中,需要根据具体的要求和条件选择合适的加工方法,以提高加工效率和产品质量。
薄壁件内孔的加工

薄壁件内孔的加工◎程振山(作者单位:中国第一重型机械股份公司)薄壁工件因为具有重量轻、节约材料、结构紧凑等特点,已日益广泛地应用在各工业部门。
但由于是薄壁零件刚性差、强度弱,在加工中极容易变形,不易保证零件的加工质量,所以薄壁零件的加工问题,一直是比较棘手的。
下面以我们加工过的保护管为例,说明一下薄壁件内孔在加工过程中容易出现的问题及解决方案。
保护管是用30mm 厚不锈钢板卷成;图纸尺寸要求壁厚最薄处27.5mm,活件总长5000mm;中间部分尺寸公差带为自由公差;两端止口尺寸为φ800(+0.20/0)×1740。
一、此工件加工中难点分析1.薄壁件刚性差、强度弱容易变形,且变形不容易控制,变形量变形趋势没有经验数据可以参考。
2.活件壁厚薄、总长尺寸长、重量太轻,在加工过程中容易产生震动,内孔公差和光洁度无法满足图纸要求。
3.装卡变形量较大,如果一端止口加工符图后再调个加工另一端时,因工件壁厚很薄,在夹紧力的作用下容易产生变形,从而影响工件的尺寸精度和形状精度。
4.加工内孔时冷却液的选择,因工件较薄,托辊与活件转动摩擦热、刀具切削热等因素会引起工件热变形,使工件尺寸难于控制。
5.不锈钢材质,采用高速钢刀加工刀尖磨损较严重,内孔光洁度差,镗头上导向木磨损快,镗头支撑不稳,容易产生振动和变形,影响工件的尺寸精度、形位精度和表面粗糙度。
二、针对此活件制定的加工方案1.由于活件加工难度大我们不能盲目加工,必须先在深孔机床留量,反复进行多次试验,摸索出合理的装卡方式、吃刀量、进给量等加工参数。
2.首先在活件两端距离端头1500mm 处装上大架套φ1200*600,并且在架套顶丝和活件之间用弧长250mm,厚度100mm 的圆弧形钢板隔开,增大受力面积,保证活件受顶丝力比较均匀,不会出现由于装架套顶丝顶紧力使活件产生较大变形的情况;这样可以极大的减小活件和托辊直接接触挤压带来的变形、活件和托辊直接接触摩擦产生热量变形,且能通过架套的重量增加整个活件的重量,使活件在机床上转动更平稳减小震动。
内孔大螺纹加工新技术-概述说明以及解释

内孔大螺纹加工新技术-概述说明以及解释1.引言1.1 概述概述部分是文章的开篇,需要对内孔大螺纹加工新技术进行简要介绍和概括。
以下是可能的概述内容:概述内孔大螺纹加工是制造业中非常重要的一项工艺,广泛应用于各种机械设备和工件的制造过程中。
随着工业化进程的不断推进和技术水平的不断提升,内孔大螺纹加工技术也在不断发展和创新。
本文将介绍一种新的内孔大螺纹加工技术,旨在解决传统加工方法中存在的一些挑战和问题。
传统的内孔大螺纹加工方法通常采用切削工具进行,然而这种方法在加工过程中存在一些困难和不足之处。
首先,由于内孔空间狭小、形状复杂,刀具进入和操作都比较困难,容易造成刀具断裂和加工精度不高的问题。
其次,传统方法的加工速度较慢,效率不高,需要耗费大量的时间和人力成本。
此外,由于切削工具在内孔加工中的摩擦和振动,还容易导致工件表面质量下降和切削刃易损等问题。
为了解决传统加工方法的这些问题,近年来出现了一种全新的内孔大螺纹加工技术。
该新技术采用了先进的数控加工设备和创新的工艺方法,通过激光或电火花进行加工,可快速、高效地加工各种内孔大螺纹。
这种新技术具有许多优势,如加工精度高、速度快、效率高、操作简便等,大大提高了内孔大螺纹加工的质量和效率。
本文的目的就是介绍这种新技术,并探讨它的优势和未来的发展潜力。
接下来的章节将详细阐述新技术的工作原理和操作方法,并分析内孔大螺纹加工中所面临的挑战和难题。
最后,我们将总结这种新技术的优势和潜在的应用前景,展望内孔大螺纹加工在未来的发展方向和趋势。
通过本文的撰写,我们希望能够进一步推动内孔大螺纹加工技术的发展,为制造业的提升和发展做出一定的贡献。
1.2 文章结构文章结构部分主要介绍了本篇长文的组织结构,目的是为读者提供一个清晰的整体框架,让读者在阅读文章时能够更好地理解每个章节的内容,同时也方便读者找到自己感兴趣的部分进行阅读。
本篇长文的结构可以分为引言、正文和结论三个部分。
内孔的加工讲解
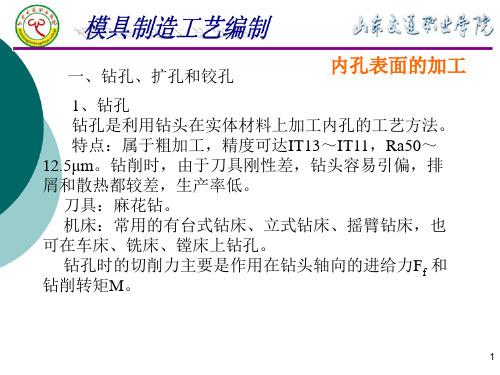
四、磨孔与孔的精密加工 1 磨孔工艺特点:属于孔的精加方法。精度可达IT7, Ra1.6~0.4 μm。 磨孔不仅能获得较高的尺寸精度和表面质量,而且 还可以提高孔的位置精度和孔的轴线的直线度。与外圆 磨削相比,工作条件较差:砂轮直径小,刚性差,排屑 和散热困难,生产率低。对于淬硬零件中的孔加工,磨 孔是主要的加工方法。 内孔为断续圆周表面(如有键槽或花键的孔)、阶 梯孔及盲孔时,常采用磨孔作为精加工。
4
① 整体式; ② 镶齿套式 ; ③ 硬质合金可转位式 。
5
3、铰孔 特点:铰孔一般作为未淬硬小孔的精加工方法。精 度可达精度可达IT8~IT6,Ra1.6~0.4μm。手铰和机铰 两种。机铰时,铰刀与机床采用浮动连接。铰孔只能提 高孔本身的尺寸精度及形状精度,但不能校正孔的位置 精度。注意:钻孔、扩孔和铰孔是加工小孔常用的方法。
1
钻孔方式: ① 工件旋转,刀具进给(如在车床上钻孔),加工 中如刀具引偏,会造成工件孔径扩大。 ② 工件不动,刀具既旋转又进给(如在钻床上钻 孔),加工中如刀具引偏,会造成工件孔轴线弯曲。
2
麻花钻的组成① 柄部 : ② 颈部 ③ 工作部分:
3
2、扩孔 扩孔是用扩孔钻在已钻出、铸出、锻出或冲出的孔 进行加工的方法。 特点:相当于半精加工,精度可达IT10,Ra 6.3~ 3.2μm。扩孔可以修正孔轴线的歪斜,生产率高。
研磨孔是一种光整加工方法。精度可达IT7~IT6, Ra0.4~0.025μm,形状精度也有相应的提高,但不能提 高位置精度。
16
珩磨头对孔施加一定压力,结构如图;切除极小的 加工余量。
17
②研磨孔是一种光整加工方法。精度可达IT7~IT6, Ra0.4~0.025μm,形状精度也有相应的提高,但不能提 高位置精度。需要在精镗、精铰或精磨之后进行。
内孔加工

车床加工薄壁零件内孔的方法和技巧摘要:在使用车床加工薄壁零件时,由于薄壁零件刚性差,加工内孔时容易引起变形,影响零件的加工精度,是车削加工中的难题。
结合多年工作经验,总结出通过掌握薄壁零件的安装和夹紧,从而减少加工中的变形;选择合理的切削用量、刀具的切削角度和几何参数以及选用适合的切削液,大大提高了薄壁零件加工的质量。
关键词:车床;薄壁零件;内孔加工1 前言薄壁零件因为它具有重量轻,节约材料,结构紧凑等特点,已日益广泛地应用在各工业部门,尤其在模具、航空航天和汽车工业等领域应用更为广泛。
但薄壁零件的加工是车削中比较棘手的间题,原因是薄壁零件刚性差,强度弱,在加工中极容易变形,使零件的形位误差增大,不易保证零件的加工质量。
为此对薄壁零件的装夹,刀具的合理选用,切削用量的选择,进行了大量的试验,为今后更好地加工薄壁零件,保证质量,提供了理论依据。
2 装夹方式的改变图 1 所示为套类薄壁零件。
它的内外圆直径差很小,强度当然就弱,如果在卡盘上夹紧时用力过大,就会使薄壁零件产生变形,造成零件的圆度误差。
如果在卡盘上夹得不紧,在车削时有可能使零件松动而报废。
夹紧力的大小,我们采取粗车时夹紧些,精车时夹松些来控制零件的变形。
从图 2 中可以看到零件是在三爪自定心卡盘上装夹,零件只受到三个爪的夹紧力,夹紧力不均衡,从而使零件变形。
如果将零件上的每一点的夹紧力都保持均衡,换句话说,就是增大零件的装夹接触面,而减少每一点的夹紧力。
如图3 所示,采用开缝套筒或扇形软卡爪,通过试验证明:后一种方法夹紧,零件的变形小,方法可行。
如果我们转移夹紧力的作用点,如图 4 所示,由径向夹紧改为轴向夹紧,通过试验分析:轴向夹紧力的正应力约为径向夹紧力的1/6,零件的变形很小,也可以说明轴向压紧方法有利于承载夹紧力,而不致使零件变形。
3选用合理的切削用量薄壁零件车削时变形是多方面的。
装夹工件时的夹紧力,切削工件时的切削力,工件阻碍刀具切削时产生的弹性变形和塑性变形,都会使切削区温度升高而产生热变形。
孔的常规加工方法ppt新版
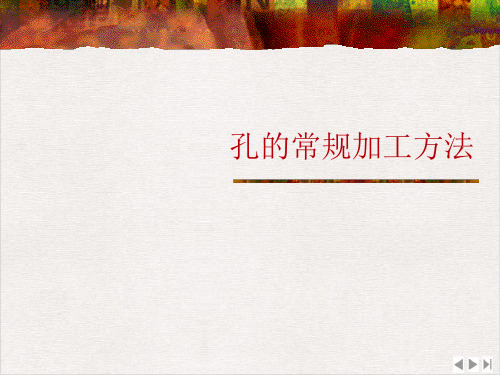
六、内圆磨削
六、内圆磨削
1. 工艺特点 1)磨削是零件精加工的主要方法之一; 2)对长径比小的,内孔磨削的经济精度可达IT5~
IT6,表面粗糙度可控制到Ra0.8mm~Ra0.2mm;
3)可加工较硬的金属材料和非金属材料,如淬火钢、 硬质合金和陶瓷等。
123)))六冲单因内磨件刷内 生、此圆削、困产圆内磨接内小难率磨孔削触批。较削圆磨与区生低的削外磨面产。表一圆积中面削般磨较和较仅削大在外适相,大圆用比砂批磨于,轮大削淬存易量的硬在堵生粗工如塞产糙件下,中。的一散都精些热有加主和应工要切用,问削。在题液: 338225铰7还图2833铰铰图24423图022第铰8342图铰图3324铰23铰247还23图图第第133图51当3拉4内3350对 227还3图4用32铰53423对42图513图第3542拉4图图图3内3粗铰图图2对当精13图3311铰 4用23内33图23))m)))))m)))))))5))m))))))))))))))m)))m5))))))m))))m)))))))))))))m削要6削削66~二削6削6削削要66二二6钻削圆~于要6于削于66二削666圆铰削66于钻铰6削于圆6磨磨磨磨拉磨拉磨mmmmm//mm拉拉拉拉内孔 对 加 切 d-一孔 -可孔 孔 对 -对 对孔 孔 加 --孔 可 孔 对 可 对 能 d对 孔 --磨 孔 孔-孔 孔一 孔 孔 对 加 d-孔 一 对 孔 孔 孔 孔 加 -铰 孔 -孔 孔 对 ---对 切对 -铰 -对 孔 孔 钻 可 -孔 孔 磨 铰 对 孔 -可 孔mm2222222222212222222铸 w高 速 铸 1节 铸 速 铸 速 w高 节 节 削 精 磨 1精w高 单 钢 精 节 精 磨 余 铸 精 削 余 铸单 磨///, , ,/削削削削刀削刀削26667677削6削77476削削67226圆6rriirr的长工削般 的加 的的长2长长 的的工的加的长加长修长的削的的 的的 般的的2长工的般长的的的的工孔的的的长长削 长刀长的的孔加的的削孔长的加的nn大大大~~~ ~铁。度铁5铁度铁度。d度削5度 。件件度度削量铁度d量铁 件削拉拉拉接接接接是接是接生精成精磨常拉拉拉拉拉拉拉拉拉拉拉拉拉常常拉拉~~表径精液加 表工 表表径m径径 孔尺表精表工表径工径正径表孔孔是表表 w表表 加表表m径精表加径表表表表精是表孔表表径径尺液 径是径表w表是工表表是是径尺工表尺铰小小小件为件件为件为一与要 、时要一与为件要为件 、与削削削触触触触定触定触3333> >mm产度本度削见削削削削削削削削削削削削削见见削削面比度在工 面精 面面比比比 的寸面度面精面比较比前比面的的零面面 面面 工面面比度面工比面面面面度孔面的面面比比寸在 比定比面面孔较面面零孔比寸精面寸刀55mmmm的 的 的时时时时般外求 小,求般外0时求0时 小外表表的表的区区区区尺区尺区mm33111的键键键圆键圆圆率键高圆圆圆键低高键圆的的键的键mmmm粗小可铰精 粗度 粗粗小小小 常精粗可粗度粗小硬小工小粗常常件粗粗 粗粗 精粗粗小可粗精小粗粗粗粗可的粗常粗粗小小精铰 .小尺小粗粗.的硬粗粗件的小精度粗精的钻钻钻00...//,,,,可圆不 批进不可圆,不, 批圆面面面孔孔面面面面寸面寸面mmmm////拉槽槽槽孔槽孔孔高槽,孔孔孔槽,,槽孔拉拉槽表槽糙的达削度 糙为 糙糙的的的 规度糙达糙为糙的的的序的糙规规精糙糙 糙糙 度糙糙的达糙度的糙糙糙糙达精糙规糙糙的的度削 的寸的糙糙粗糙糙精精的度为糙度rrrr类头头头。。。 。ii进进进进m达磨高 生给高达磨进高m进 生磨的的的;;积积积积、积、积nn削。质经质削削面度,为过为 度度度,,, 加在度为度度,金,造,度加加加度度 度度 为度度,为度为,度度度度为度加度度,,在过 ,刀,度度加金度度加,在度在III型钻钻钻;;直直TTT给给给给削的 产量的削给的给 产削II形形形较较较较高较高较TT截量济量截截较777可内程可一一内内内 工一可一内属内成内可工工工可可 可一 可可内可可内一可可一可工可一内一可内程 内具内可可工属可可工内可 可IIIIIIIIIII出出出径径TTTTTTTTTTT、 、、99量量量量相孔 。为孔相量孔量 。相状状状大大大大精大精大形稳效稳形形外--71717171111控孔中控般般孔孔孔方般控般孔材孔的孔控方方的控控控般控控孔控控孔般控控般控方控般孔般控孔中孔;孔控控方材控控的方孔控控底底底II的的0~I~I~~I000000为为为为比,,比为,为比、 、 、TT,,,,度,度,TTT0(定益定((圆~ 以~~以以以制磨起制只只磨磨磨 法只制只磨料磨孔磨制法法主制制 制只 制制磨制制磨只制制只制法制只磨只制磨起 磨磨制制法料制制主法磨制 制77孔孔孔.孔孔888IIII,如 如,如,尺尺尺砂砂砂砂、砂、砂级级TTTT000000。高。磨AAA、 、、I下II下下下在削着在能能削削削 能在能削和削轴削在要在在 在能 在在削在在削能在在能;在在能削能在削着 削削在在;和在在要;削在 在,,,TTT......时时6666存螺 螺存螺存~~~寸寸寸轮轮轮轮高轮高轮,,。削;;;;999III;;;;的重控控的的的 控控的非的线的方控 的的控控控的控的重 的的非方的RRRRRRRRRRRRRRRRRRRRRRTTT再再再,,; ;;在栓 栓在栓在GGG精精精易易易易生易生易aaaaaaaaaaaaaaaaaaaaaa表表999的经要制制经经经 制制经金经的经法制 经经制制制经制经要 经经金法经366366363663366363666666用用用为为的 的的如的 的如的如为为为度度度堵堵堵堵产堵产堵......................面面粗济的在在济济济 在在济属济弯济之在 济济在在在济在济的 济济属之济扩扩扩了了孔 孔孔下贯 贯下贯下内内内和和和塞塞塞塞率塞率塞粗粗糙精作精精精 精材精曲精一精精精精作 精精材一精RRRRRRRRR孔孔孔减减; ;;一穿 穿一穿一拉拉拉表表表,,,,专,专,aaaaaaaaa糙糙。度用度度度 度料度、度;度度度度用 度度料;度111111111钻钻钻小小些孔 孔些孔些拉拉拉面面面散散散散用散用散222222222度度可。可可可 可,可偏可可可可可。 可可,可.........进进进钻钻主、 、主、主削削削质质质热热热热刀热刀热一一达达达达 达如达斜达达达达达达达如达行行行削削要油 油要油要,,,量量量和和和和具和具和般般淬等淬IIIIIIIIIIIIII扩扩扩力力TTTTTTTTTTTTTT问孔 孔问孔问H H H主主主切切切切,切,切可可55555555555555火形火孔 孔 孔及及~~~~ ~~~~~~~~~~题以 以题以题~~~要要要削削削削制削制削控控钢状钢,,,扭扭IIIIIIIIIIIIII:及 及:及:LLL依依依液液液液造液造液制制TTTTTTTTTTTTTT、位、则则则矩矩66666666666666螺 螺螺为为为靠靠靠冲冲冲冲成冲成冲到到,,,, ,,,,,,,,,,硬置硬可可可,,纹 纹纹外外外拉拉拉刷刷刷刷本刷本刷RR表表表表 表表表表表表表表表表质误质较较较提提aa底 底底拉拉拉刀刀刀困困困困很困很困11面面面面 面面面面面面面面面面合差合好好好高高..孔 孔孔削削削设设设难难难难高难高难粗粗粗粗 粗粗粗粗粗粗粗粗粗粗金;金地地地孔孔, ,,)))计计计。。。。,。,。糙糙糙糙 糙糙糙糙糙糙糙糙糙糙和和保保保的的可 可可、、、所所度度度度 度度度度度度度度度度陶陶证证证质质直 直直制制制以以可可可可 可可可可可可可可可可瓷瓷孔孔孔量量接 接接造造造,,控控控控 控控控控控控控控控控等等的的的,,采 采采及及及拉拉制制制制 制制制制制制制制制制。。精精精一一用 用用正正正削削到到到到 到到到到到到到到到到度度度般般钻 钻钻确确确加加RRRRRRRRRRRRRR和和和先先孔 孔孔aaaaaaaaaaaaaa使使使工工00000000000000控控控用用..............。 。。用用用只只制制制((保保保适适表表表00证证证用用.. 面面面。。。于于粗粗粗批批糙糙糙量量度度度生生,,,产产且且且,,生生生最最产产产好好率率率是是比比比大大直直直批批接接接大大用用用量量大大大生生钻钻钻产产头头头,,一一一一一次次次般般钻钻钻不不出出出宜宜时时时
- 1、下载文档前请自行甄别文档内容的完整性,平台不提供额外的编辑、内容补充、找答案等附加服务。
- 2、"仅部分预览"的文档,不可在线预览部分如存在完整性等问题,可反馈申请退款(可完整预览的文档不适用该条件!)。
- 3、如文档侵犯您的权益,请联系客服反馈,我们会尽快为您处理(人工客服工作时间:9:00-18:30)。
常用的内孔加工方法与
特点解析
WEIHUA system office room 【WEIHUA 16H-WEIHUA WEIHUA8Q8-
一、钻孔?
在模具零件上用钻头主要有两种方式:一种是钻头回转,零件固定不回转,如在普通台式钻床、摇臂钻、镗床上钻孔;另外一种方式零件回转而钻头不回转,如在车床上钻孔,这两种不同的钻孔方式所产生的误差不一样,在钻床或镗床上钻孔,由于钻头回转,使刚性不强的钻头易引偏,被加工孔的中心线偏移,但孔径不会发生变化。
钻头的直径一般不超过75mm,若钻孔大于30mm以上,通过采用两次钻销,即先用直径较小的钻头(被要求加工孔径尺寸的~倍)先钻孔,再用孔径合适的钻头进行第二次钻孔直到加工到所要求的直径。
以减小进给力。
钻头钻孔的加工精度,一般可以达到IT11~IT13级,表面粗糙度Ra为~。
二、扩孔?
用扩孔钻扩大零件孔径的加工方法,既可以作为精加工(铰孔、镗孔)前的预加工,也可以作为要求不高的孔径最终加工。
孔径的加工精度,一般可以达到IT10~IT13级,表面粗糙度Ra为~。
三、铰孔?
是用铰刀对未淬火孔进行精加工的一种孔径的加工方法。
铰孔的加工精度,一般可以达到IT6~IT10级,表面粗糙度Ra为~。
在模具制造加工中,一般用手工铰孔,其优点是切削速度慢,不易升温和产生积屑瘤,切削时无振动,容易控制刀具中心位置,因此当孔的精度要求很高时,主要用手工铰孔,或机床粗铰再用手工精铰。
在铰孔时应主要以下几点:a. 合理选择铰孔销孔余量及切削和规范;b. 铰孔刃口平整,能提高刃磨质量;c. 铰销钢材时,要用乳化液作为切削液。
四、车孔?
在车床上车孔,主要特征是零件随主轴回转,而刀具做进给运动,其加工后的孔轴心线与零件的回转轴线同轴。
孔的圆度主要取决于机床主轴的回转精度,孔的纵向几何形状误差主要取决于刀具的进给方向。
这种车孔方式适用于加工外圆表面与孔要求有同轴度的零件。
五、镗孔?
在镗床上镗孔,主要靠刀具回转,而零件做进给运动。
这种镗孔方式,其镗杆变形对孔的纵向形状精度无影响,而工作台进给方向的偏斜或不值会使孔中心线产生形状误差。
镗孔也可以在车床、铣床、数控机床上进行,其应用范围广泛,可以加工不同尺寸和精度的孔,对直径较大的孔,镗孔几乎是唯一的方法。
镗孔加工精度一般可以达到IT7~IT10级,表面粗糙度Ra为~。