冷轧乳化液吹扫系统的改进
单机湿平整及吹扫系统改进
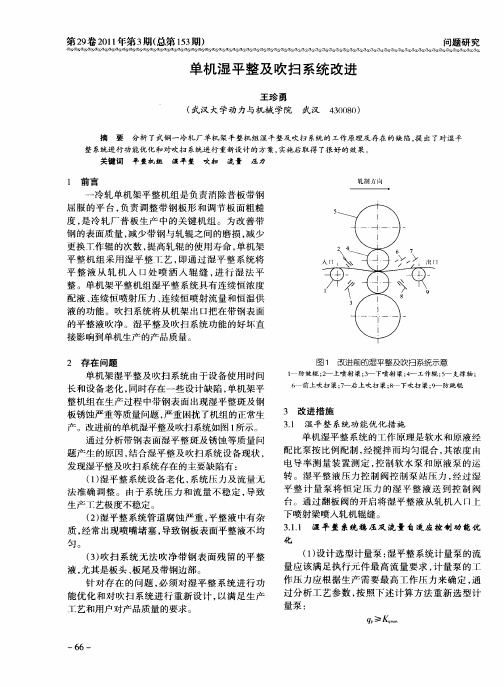
板锈 蚀严 重 等质量 问题 , 重 困扰 了机组 的正 常 生 严 产 。改 进前 的单 机湿平 整及 吹扫系统如 图 1 所示 。 通 过 分 析带 钢 表 面 湿平 整 斑 及锈 蚀 等 质 量 问 题 产 生 的原 因 , 合 湿平 整 及 吹扫 系统设 备 现 状 , 结 发 现湿 平整 及 吹扫 系统存 在 的 主要缺 陷 有 : ( ) 平 整 系统 设 备 老 化 , 统 压力 及 流 量 无 1湿 系 法 准 确 调 整 。 由 于 系统 压 力 和 流 量 不 稳 定 , 致 导
了孔径 03m . m的喷嘴 。安装使用后效果明显 , 5 平 整液能均匀的喷洒进辊缝 。为了安装新改型的喷 嘴 , 喷射梁结构进行改进 , 对 将原 1 个喷嘴改为 l 3 1 个, 喷射 梁 可 以根 据 生 产 实 际需 要 调 整 角 度 。改 进后平整液喷射均匀 , 完全满足生产工艺的要求。
下 喷射 梁 喷人 轧机辊 缝 。
311 湿 平 整 系 统 稳 压 及 流 量 自适 应 控 制 功 能 优 ..
化
针对存 在的问题 , 必须对湿平整 系统进 行功 能 优 化 和对 吹 扫 系统 进 行 重 新设 计 , 以满 足 生 产 工 艺 和用 户对产 品质量 的要 求 。
生 产T 艺极 度不 稳 定 。
3 改进 措 施
31 湿 平整 系统 功 能优 化 措施 .
单 机 湿 平 整 系统 的 工作 原 理是 软水 和 原 液经 配 比泵按 比例 配 制 , 经搅 拌 而 均匀 混 合 , 浓度 由 其 电导率测量装置测定 , 控制软水泵 和原液 泵的运
31 湿平 整 系统附件 改 进 .- 3
冷轧生产过程乳化液异味的改进研究
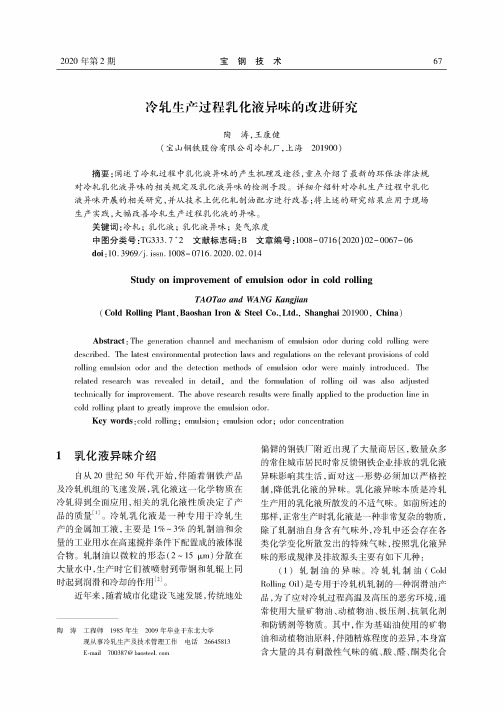
2020年第2期宝钢技术67冷轧生产过程乳化液异味的改进研究陶涛,王康健(宝山钢铁股份有限公司冷轧厂,上海201900)摘要:阐述了冷轧过程中乳化液异味的产生机理及途径,重点介绍了最新的环保法律法规对冷轧乳化液异味的相关规定及乳化液异味的检测手段&详细介绍针对冷轧生产过程中乳化液异味开展的相关研究,并从技术上优化轧制油配方进行改善;将上述的研究结果应用于现场生产实践,大幅改善冷轧生产过程乳化液的异味&关键词:冷轧;乳化液;乳化液异味;臭气浓度中图分类号:TG333.7(2文献标志码:B文章编号:1008-0716(2020)02-0067-06doi:10.3969/j.issn.1008-0716.2020.02.014Study on improvement of emulsion odor ic cold rollingTAOTao ang WANG Kangjian(C o US Rolling Plant,Baoshan Iron&Steel Co^Ltt.,Shanghai201900,China)Abstract:The generation channel and mechanism of emulsion odor during cold oiling wered esc eob ed.Th eeat est en eoeonm entaep eot ect oon eawsand eegueatoonson theeeeeeantpeoeosoonsotcoedoiling emulsion odor and the detection methods of emulsion odor were mainly introduced.The related research was revealed in detail,and the foanulation of oiling oil was also adjusted technically for impovement.The above research results were finty applied to the poduction line in cold oiling plant to greatly improve the emulsion odor.Key worls:cold rolling;emulsion;emulsion odor;odor concentration1乳化液异味介绍自从20世纪50年代开始,伴随着钢铁产品及冷轧机组的飞速发展,乳化液这一化学物质在冷轧得到全面应用,相关的乳化液性质决定了产品的质量[1]&冷轧乳化液是一种专用于冷轧生产的金属加工液,主要是1%-3%的轧制油和余量的工业用水在高速搅拌条件下配置成的液体混合物&轧制油以微粒的形态(2-15)m)分散在大量水中,生产时它们被喷射到带钢和轧辐上同时起到润滑和冷却的作用[2]&近年来,随着城市化建设飞速发展,传统地处陶涛工程师1985年生2009年毕业于东北大学现从事冷轧生产及技术管理工作电话26645813E-mail700387@ 偏僻的钢铁厂附近出现了大量商居区,数量众多的常住城市居民时常反馈钢铁企业排放的乳化液异味影响其生活,面对这一形势必须加以严格控制,降低乳化液的异味&乳化液异味本质是冷轧生产用的乳化液所散发的不适气味&如前所述的那样,正常生产时乳化液是一种非常复杂的物质,除了轧制油自身含有气味外,冷轧中还会存在各类化学变化所散发出的特殊气味,按照乳化液异味的形成规律及排放源头主要有如下几种:(1)轧制油的异味&冷轧轧制油(Cold Rolling Oil)是专用于冷轧机轧制的一种润滑油产品,为了应对冷轧过程高温及高压的恶劣环境,通常使用大量矿物油、动植物油、极压剂、抗氧化剂和防锈剂等物质&其中,作为基础油使用的矿物油和动植物油原料,伴随精炼程度的差异,本身富含大量的具有刺激性气味的硫、酸、醛、酮类化合68宝钢技术2020年第2期物[3];此外,极压剂、抗氧化剂和防锈剂等物质也富含各类刺激性味道,使用过程中这些物质就会散发气味,有很多刺激气味&(2)轧制油反应分解的异味&冷轧轧制油作为一种复杂的化学混合物,在钢铁金属元素的催化及辐缝内高温高压的条件下,产生了一系列的化学反应,主要是矿物油、动植物基础油及合成脂在高温含氧环境下发生热裂解及氧化反应,生成了有机酸化合物;此外,大量的添加剂,例如极压剂内富含的有机硫化合物在一定条件下反应产生含硫的恶臭物质⑷,这些物质所散发的气味通常会伴随着冷轧生产而持续产生并排放,成为又一个异味排放源。
关于冷轧卷板面残油问题的分析
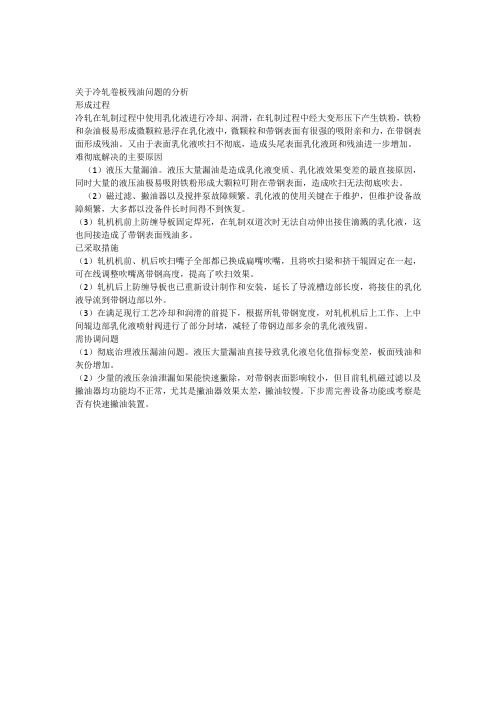
关于冷轧卷板残油问题的分析
形成过程
冷轧在轧制过程中使用乳化液进行冷却、润滑,在轧制过程中经大变形压下产生铁粉,铁粉和杂油极易形成微颗粒悬浮在乳化液中,微颗粒和带钢表面有很强的吸附亲和力,在带钢表面形成残油。
又由于表面乳化液吹扫不彻底,造成头尾表面乳化液斑和残油进一步增加。
难彻底解决的主要原因
(1)液压大量漏油。
液压大量漏油是造成乳化液变质、乳化液效果变差的最直接原因,同时大量的液压油极易吸附铁粉形成大颗粒叮附在带钢表面,造成吹扫无法彻底吹去。
(2)磁过滤、撇油器以及搅拌泵故障频繁。
乳化液的使用关键在于维护,但维护设备故障频繁,大多都以没备件长时间得不到恢复。
(3)轧机机前上防缠导板固定焊死,在轧制双道次时无法自动伸出接住滴溅的乳化液,这也间接造成了带钢表面残油多。
已采取措施
(1)轧机机前、机后吹扫嘴子全部都已换成扁嘴吹嘴,且将吹扫梁和挤干辊固定在一起,可在线调整吹嘴离带钢高度,提高了吹扫效果。
(2)轧机后上防缠导板也已重新设计制作和安装,延长了导流槽边部长度,将接住的乳化液导流到带钢边部以外。
(3)在满足现行工艺冷却和润滑的前提下,根据所轧带钢宽度,对轧机机后上工作、上中间辊边部乳化液喷射阀进行了部分封堵,减轻了带钢边部多余的乳化液残留。
需协调问题
(1)彻底治理液压漏油问题。
液压大量漏油直接导致乳化液皂化值指标变差,板面残油和灰份增加。
(2)少量的液压杂油泄漏如果能快速撇除,对带钢表面影响较小,但目前轧机磁过滤以及撇油器均功能均不正常,尤其是撇油器效果太差,撇油较慢。
下步需完善设备功能或考察是否有快速撇油装置。
关于冷轧中乳化液的技术指标
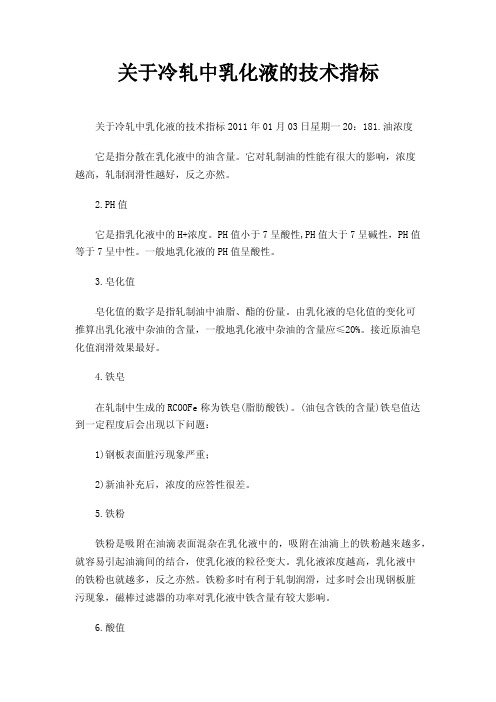
关于冷轧中乳化液的技术指标关于冷轧中乳化液的技术指标2011年01月03日星期一20:181.油浓度它是指分散在乳化液中的油含量。
它对轧制油的性能有很大的影响,浓度越高,轧制润滑性越好,反之亦然。
2.PH值它是指乳化液中的H+浓度。
PH值小于7呈酸性,PH值大于7呈碱性,PH值等于7呈中性。
一般地乳化液的PH值呈酸性。
3.皂化值皂化值的数字是指轧制油中油脂、酯的份量。
由乳化液的皂化值的变化可推算出乳化液中杂油的含量,一般地乳化液中杂油的含量应≤20%。
接近原油皂化值润滑效果最好。
4.铁皂在轧制中生成的RCOOFe称为铁皂(脂肪酸铁)。
(油包含铁的含量)铁皂值达到一定程度后会出现以下问题:1)钢板表面脏污现象严重;2)新油补充后,浓度的应答性很差。
5.铁粉铁粉是吸附在油滴表面混杂在乳化液中的,吸附在油滴上的铁粉越来越多,就容易引起油滴间的结合,使乳化液的粒径变大。
乳化液浓度越高,乳化液中的铁粉也就越多,反之亦然。
铁粉多时有利于轧制润滑,过多时会出现钢板脏污现象,磁棒过滤器的功率对乳化液中铁含量有较大影响。
6.酸值酸值的数值表示轧制油中脂肪酸的量。
1)脂肪酸的优点:酸基对钢板表面有较强的附着力,因此它对润滑性和防锈性都很好。
2)脂肪酸的缺点:脂肪酸过多,将会促进油箱以及管道的腐蚀,此外还将生成大量铁油泥,使钢板表面及轧机机组的脏污急剧增加。
7.电导率一般指乳化液的导电能力,是电阻的倒数。
(离子高则容易油水分离!)8.温度温度是个管理项目,它对性能有很大的影响。
1)温度较低时容易出现的问题:①润滑不良,轧制力升高,振动现象多发;②容易产生轧后钢板表面脏污现象;③钢板表面水分蒸发困难,钢板容易生锈。
2)温度较高时容易出现的问题:①乳化不安定,附着量增加,容易产生打滑现象;②蒸汽大量产生,污染工作环境。
乳化液在轧制过程中的润滑和冷却乳化液在冷轧中的主要作用是润滑和冷却。
在轧制过程中,轧制变形区产生的高温使乳化液产生油水分离,油吸附在轧辊与钢板表面形成油膜,起到润滑作用。
冷轧罩退产品缺陷分析及改进措施[论文]
![冷轧罩退产品缺陷分析及改进措施[论文]](https://img.taocdn.com/s3/m/370f72cd9ec3d5bbfd0a7413.png)
冷轧罩退产品缺陷分析及改进措施摘要:本文针对冷轧罩退产品产生的缺陷加以总结分析,从生产操作,设备控制等多角度找出其原因所在,结合作者的生产实践寻求其改善的措施和方法。
关键词:冷轧罩退平整缺陷分析1、前言:冷轧带钢以其良好的表面质量和冲压性能,在很多领域得到了广泛的应用。
在冷轧过程中产生的加工硬化使得带钢的强度和硬度提高,而塑性、冲压性能降低。
因此非常有必要加强对该缺陷的分析研究,查找问题的根源,制定相应的控制措施,提高冷轧钢带的表面质量。
2、罩退产品缺陷分析冷轧罩退产品主要的生产工艺流程如图1所示,热轧生产的产品供酸轧线生产冷硬卷,冷硬卷经罩式退火后,再经过平整生产出最终的罩退产品。
在实践中发现,整个工艺流程中所涉及到的每一道工序的工艺技术、设备状况、管理力度等因素,都对罩退产品的质量有很大的影响。
目前冷轧罩退产品常见的主要缺陷有异物压入、翘皮、隆起、黑斑、粘结、边皱等,这些缺陷主要是受原料质量(包括热轧料和冷硬卷)、罩退及平整工艺的影响产生的,其中异物压入、翘皮、隆起主要是由热轧板卷生产过程中产生,在冷板后道工序生产中无法消除而造成的缺陷;黑斑、粘结、边皱主要是由酸轧、罩退及平整工艺过程产生的缺陷,对罩退产品表面质量影响也很大。
下面就对这几种缺陷进行分析,并对每种缺陷的特征、产生原因及解决方法进行简要的介绍。
2.1热轧工艺产生的缺陷(1)异物压入异物压入,又称“夹杂”,主要是在热轧生产中形成的板面缺陷,如图2所示。
在热轧生产过程中,由于设备、工艺等方面的原因,致使带钢除鳞不净,造成氧化铁皮等物质附着在带钢表面,再经轧制、挤压后形成点状、线状、块状等缺陷。
另外在炼钢、精炼、连铸过程中,保护渣、耐火材料、脱氧产物等物质卷入铸坯或铸坯表面有缺陷等都会造成罩退产品产生异物压入缺陷。
热轧料生产的主要工艺过程是:炼钢→精炼→连铸→热轧。
实践证明[1],控制好各工序中的钢水及铸坯的成分及工艺,提高热轧板的质量,可以有效减少后期罩退产品异物压入的缺陷量。
冷轧机的乳化液控制与回收系统
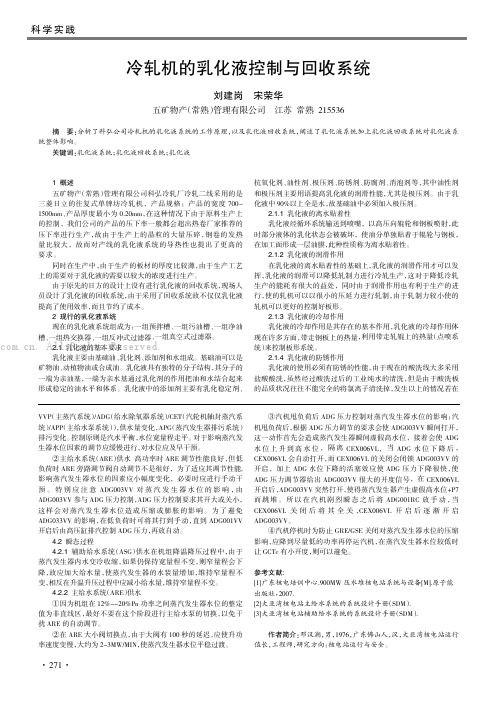
VVP(主蒸汽系统)/ADG(给水除氧器系统)/CET(汽轮机轴封蒸汽系统)/APP(主给水泵系统)),供水量变化,APG(蒸汽发生器排污系统)排污变化。
控制原则是汽水平衡,水位宽量程走平。
对于影响蒸汽发生器水位因素的调节应缓慢进行,对水位应及早干预。
②主给水系统(ARE)供水高功率时ARE调节性能良好,但低负荷时ARE旁路调节阀自动调节不是很好,为了适应其调节性能,影响蒸汽发生器水位的因素应小幅度变化,必要时应进行手动干预。
特别应注意ADG003VV对蒸汽发生器水位的影响,由ADG003VV参与ADG压力控制,ADG压力控制要求其开大或关小,这样会对蒸汽发生器水位造成压缩或膨胀的影响。
为了避免ADG033VV的影响,在低负荷时可将其打到手动,直到ADG001VV 开启后由高压缸排汽控制ADG压力,再放自动。
4.2瞬态过程4.2.1辅助给水系统(ASG)供水在机组降温降压过程中,由于蒸汽发生器内水变冷收缩,如果仍保持宽量程不变,则窄量程会下降,故应加大给水量,使蒸汽发生器的水装量增加,维持窄量程不变,相反在升温升压过程中应减小给水量,维持窄量程不变。
4.2.2主给水系统(ARE)供水①因为机组在12%--20%Pn功率之间蒸汽发生器水位的整定值为非直线区,最好不要在这个阶段进行主给水泵的切换,以免干扰ARE的自动调节。
②在ARE大小阀切换点,由于大阀有100秒的延迟,应使升功率速度变慢,大约为2-3MW/MIN,使蒸汽发生器水位平稳过渡。
③汽机甩负荷后ADG压力控制对蒸汽发生器水位的影响:汽机甩负荷后,根据ADG压力调节的要求会使ADG003VV瞬间打开,这一动作首先会造成蒸汽发生器瞬间虚假高水位,接着会使ADG 水位上升到高水位,隔离CEX006VL,当ADG水位下降后,CEX006VL会自动打开,而CEX006VL的关闭会闭锁ADG003VV的开启,加上ADG水位下降的活塞效应使ADG压力下降很快,使ADG压力调节器给出ADG003VV很大的开度信号,在CEX006VL 开启后,ADG003VV突然打开,使得蒸汽发生器产生虚假高水位+P7而跳堆。
冷轧板带缺陷及消除方法
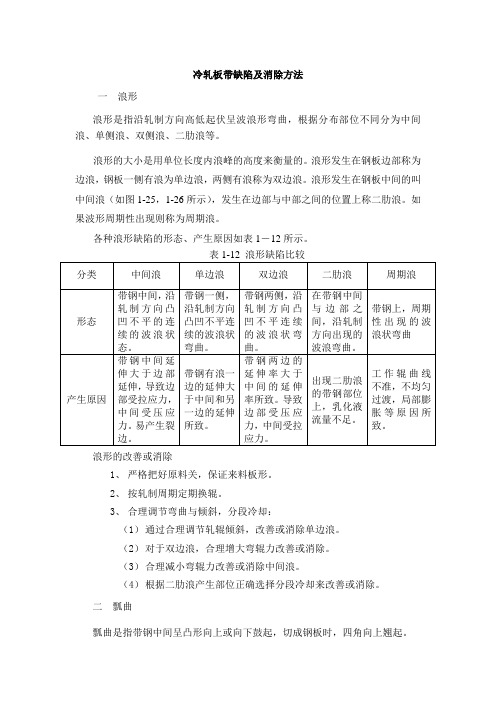
冷轧板带缺陷及消除方法一浪形浪形是指沿轧制方向高低起伏呈波浪形弯曲,根据分布部位不同分为中间浪、单侧浪、双侧浪、二肋浪等。
浪形的大小是用单位长度内浪峰的高度来衡量的。
浪形发生在钢板边部称为边浪,钢板一侧有浪为单边浪,两侧有浪称为双边浪。
浪形发生在钢板中间的叫中间浪(如图1-25,1-26所示),发生在边部与中部之间的位置上称二肋浪。
如果波形周期性出现则称为周期浪。
各种浪形缺陷的形态、产生原因如表1-12所示。
浪形的改善或消除1、严格把好原料关,保证来料板形。
2、按轧制周期定期换辊。
3、合理调节弯曲与倾斜,分段冷却:(1)通过合理调节轧辊倾斜,改善或消除单边浪。
(2)对于双边浪,合理增大弯辊力改善或消除。
(3)合理减小弯辊力改善或消除中间浪。
(4)根据二肋浪产生部位正确选择分段冷却来改善或消除。
二瓢曲瓢曲是指带钢中间呈凸形向上或向下鼓起,切成钢板时,四角向上翘起。
(一)产生原因:1、工作辊凸度太大,或在轧制时轧辊中间温度太高,使带钢中间延伸大于两边。
2、由于某种原因压下量变小,产生中心延伸大于两边。
3、原料瓢曲大,轧后不易消除。
4、板形调节不当。
(二)改善或消除措施:1、合理分配辊型,正确分配压下量。
2、精心操作,勤观察板形。
3、原料横向厚度公差应尽量小。
三辊印辊印是一种常见的缺陷,各工序都能产生。
一般由辊面凸凹缺陷引起,缺陷的部位确定并有周期性。
酸洗辊辊印主要是金属碎块粘在张力辊表面上,又压在带钢表面上产生,压印有规律性。
轧制辊印种类比较多,但其特点是周期出现,印坑形状大小相同。
周期长度L Y与工作辊径D有关,即:L Y = uπ D在成品道次时u=l,其它道次可根据延伸情况计算出来。
按缺陷特点辊印可分为4种形式:第一种是粘辊辊印。
它是由于轧辊表面粘有金属,从而在轧制时,在带钢表面形成压印。
其形状与粘有金属形式一致,多呈点状、条状或块状。
当原料有破边、折叠等缺陷进入轧机,或者穿带、甩尾时,辊缝不大,带钢与轧辊接触并相对滑动,造成金属粘于轧辊表面上,称做粘辊,如不磨除干净,就在轧制时造成辊印。
冷轧板带缺陷及消除方法

冷轧板带缺陷及消除方法浪形浪形是指沿轧制方向高低起伏呈波浪形弯曲,根据分布部位不同分为中间浪、单侧浪、双侧浪、二肋浪等。
浪形的大小是用单位长度内浪峰的高度来衡量的。
浪形发生在钢板边部称为边浪,钢板一侧有浪为单边浪,两侧有浪称为双边浪。
浪形发生在钢板中间的叫中间浪(如图1-25,1-26所示),发生在边部与中部之间的位置上称二肋浪。
如果波形周期性出现则称为周期浪。
各种浪形缺陷的形态、产生原因如表1-12所示表1-12浪形缺陷比较1、严格把好原料关,保证来料板形。
2、按轧制周期定期换辊。
3、合理调节弯曲与倾斜,分段冷却:(1)通过合理调节轧辊倾斜,改善或消除单边浪。
(2)对于双边浪,合理增大弯辊力改善或消除。
(3)合理减小弯辊力改善或消除中间浪。
(4)根据二肋浪产生部位正确选择分段冷却来改善或消除瓢曲瓢曲是指带钢中间呈凸形向上或向下鼓起,切成钢板时,四角向上翘起。
(一)产生原因:1、工作辊凸度太大,或在轧制时轧辊中间温度太高,使带钢中间延伸大于两边。
2、由于某种原因压下量变小,产生中心延伸大于两边。
3、原料瓢曲大,轧后不易消除。
4、板形调节不当。
(二)改善或消除措施:1、合理分配辊型,正确分配压下量。
2、精心操作,勤观察板形。
3、原料横向厚度公差应尽量小。
三辊印辊印是一种常见的缺陷,各工序都能产生。
一般由辊面凸凹缺陷引起,缺陷的部位确定并有周期性。
酸洗辊辊印主要是金属碎块粘在张力辊表面上,又压在带钢表面上产生,压印有规律性。
轧制辊印种类比较多,但其特点是周期出现,印坑形状大小相同。
周期长度L Y 与工作辊径D 有关,即:L Y = u 冗D在成品道次时u= l,其它道次可根据延伸情况计算出来。
按缺陷特点辊印可分为4 种形式:第一种是粘辊辊印。
它是由于轧辊表面粘有金属,从而在轧制时,在带钢表面形成压印。
其形状与粘有金属形式一致,多呈点状、条状或块状。
当原料有破边、折叠等缺陷进入轧机,或者穿带、甩尾时,辊缝不大,带钢与轧辊接触并相对滑动,造成金属粘于轧辊表面上,称做粘辊,如不磨除干净,就在轧制时造成辊印。
1420mm冷轧机组吹扫器对钢带质量的影响

吹扫器 在安装 时 风刀 与板 面 成 3 。 5 角并 可 进 行 调 节 , 吹扫 器 的高 度 、 度都 可 进行 调 节 , 上 角 使
吹扫效 果 明显提 高 。 3 改造后效 果 吹扫器 改造 安 装完 成 后 , 钢 带 表 面质 量 进 对 行 了跟踪统 计 。2 0 0 5年 1 1月共 生产 钢卷 7 8 8 0 .7 t其 中 A 级 品 7 . 5 , 1 . % ; 级 品 , 8 65 t 占 1 7 B 2 1 4 5 t 占 3 . % ; 级 品 2 5 4 5 ,占 1 .4 , 15 C 7 . 9 t
面质量 。
关键词 : 冷轧机 ; 吹扫器 ; 结构 ; 钢带质量
中 图分 类 号 :G 3 . 2 T 337 文 献 标 识 码 : B
I a to r i g De i e o 2 mp c fPu g n v c f1 4 0 mm
C l ol gMiso eQ ai f te Sr odR ln l nt u lyo el tp i l h t S i
C N A Y E UP N HIA HE V Q IME T
积, 形成立体 的吹扫系统 , 保证钢带表 面的洁净度 。
高 了板 面 的清洁度 。 吹扫器改 进后结 构 见 图 2 。
2 2 吹扫器 结构形 式 . 风刀形 式对 压缩 空气 的气 阻及 流动 状态 有很
大 的影 响。 当风 刀采 用 线 形 的开 口形 式 布置 时 ,
况。
1 吹扫器 改进 前 结构及 钢 带表 面质量 情 况
原八 钢冷 轧机 组 吹扫器 设备 随 主体设 备从 日 本 引进 后 , 进行 了原 样恢 复 , 于 2 纪 8 代 属 0世 0年
密闭吹扫的问题以及优化对策
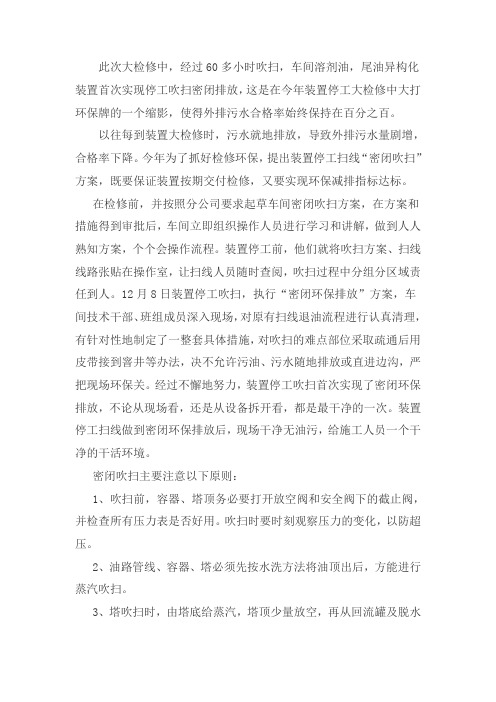
此次大检修中,经过60多小时吹扫,车间溶剂油,尾油异构化装置首次实现停工吹扫密闭排放,这是在今年装置停工大检修中大打环保牌的一个缩影,使得外排污水合格率始终保持在百分之百。
以往每到装置大检修时,污水就地排放,导致外排污水量剧增,合格率下降。
今年为了抓好检修环保,提出装置停工扫线“密闭吹扫”方案,既要保证装置按期交付检修,又要实现环保减排指标达标。
在检修前,并按照分公司要求起草车间密闭吹扫方案,在方案和措施得到审批后,车间立即组织操作人员进行学习和讲解,做到人人熟知方案,个个会操作流程。
装置停工前,他们就将吹扫方案、扫线线路张贴在操作室,让扫线人员随时查阅,吹扫过程中分组分区域责任到人。
12月8日装置停工吹扫,执行“密闭环保排放”方案,车间技术干部、班组成员深入现场,对原有扫线退油流程进行认真清理,有针对性地制定了一整套具体措施,对吹扫的难点部位采取疏通后用皮带接到窨井等办法,决不允许污油、污水随地排放或直进边沟,严把现场环保关。
经过不懈地努力,装置停工吹扫首次实现了密闭环保排放,不论从现场看,还是从设备拆开看,都是最干净的一次。
装置停工扫线做到密闭环保排放后,现场干净无油污,给施工人员一个干净的干活环境。
密闭吹扫主要注意以下原则:1、吹扫前,容器、塔顶务必要打开放空阀和安全阀下的截止阀,并检查所有压力表是否好用。
吹扫时要时刻观察压力的变化,以防超压。
2、油路管线、容器、塔必须先按水洗方法将油顶出后,方能进行蒸汽吹扫。
3、塔吹扫时,由塔底给蒸汽,塔顶少量放空,再从回流罐及脱水阀放空。
4、管线吹扫,原则上是从各泵入口扫线阀反向吹扫,在放空阀处放空或拆开法兰放空,不得长时间经过泵体。
5、塔和容器一定要保证吹扫时间,通常在48h以上,取样做爆炸分析合格。
6、临氢系统停工后用N2吹扫置换,并分析氢气+烃<1%(v)为合格。
7、换热器吹扫时须打开冷源侧阀门,以防蹩压。
固定管板换热器严禁使用蒸汽吹扫。
8、冷却器吹扫前关上下水阀放尽存水,敞开放空阀。
浅析冷轧带钢表面缺陷成因及控制措施

-70- 浅析冷轧带钢表面缺陷成因及控制措施 □新余钢铁股份有限公司 廖海秋 刘胜赫 / 文冷轧产品表面的质量对提高整个产品质量有重要作用,也使对其市场的前景有决定作用的关键因素,本文主要对冷轧带钢表面的缺陷进行分析,然后提出一些控制的措施,进而促进行业发展。
冷轧带钢 表面缺陷 成因 控制措施自2011年新钢冷轧厂投产以来,通过不断摸索和改进,取得骄人的成绩,被广泛用于汽车、家电、建筑、食品等行业。
社会在不断发展,人们对冷轧带钢的表面要求也不断提高,对表面的缺陷进行控制受到更多的关注,控制的水平高低已经成为向高端客户供货的重要因素。
表面缺陷种类与形成的原因比较复杂,炼钢和热轧以及冷轧甚至用户的使用,各个环节都可能使表面出现缺陷,成因会涉及组织生产、技术和设备,以及管理操作和工艺等,通过在处理质量异议中,收集并分析部分表面质量缺陷。
冷轧带钢表面出现的缺陷的及成因(A)孔洞翘皮(B)夹杂(1)炼钢来料方面的缺陷,比如孔洞、夹杂、翘皮等这一缺陷在炼钢和热轧时就已经出现,在进行冷轧是不能消除并暴露。
孔洞在规格比较薄的冷轧带钢内,是一种比较常见的缺陷,一般在铸坯内表面的裂纹、卷渣和夹杂等在轧制时形成,孔洞可以使用肉眼进行识别,对于高速运行的带钢而言,可以使用一些仪器设备进行检测。
夹杂则是因为在板坯内残留的颗粒状夹杂物质,经过冷轧之后,沿着轧制的方向,颜色为灰白、灰黑或者黑色的长条状的缺陷,没有规律的在带钢的表面分布,一些夹杂在经过热轧是就会在表面暴露,但是一些夹杂只有经过冷轧后在可以在表面暴露。
出现夹杂的原因主要是:钢液在凝固时,夹杂物逐渐向内弧侧不断上浮,然后集聚形成;或者因为结晶器钢水出口角度出现了偏差,造成保护渣被卷进铸坯的表层然后形成;热轧加热炉内耐火的材料落入带钢的表面形成。
(2)热轧来料方面缺陷氧化铁皮压入。
直接在厚度为12毫米的胚料表面,黏上热轧氧化铁皮,热轧到1毫米,然后冷轧到0.4毫米。
双机架可逆式轧机带钢吹扫系统优化改造

双 机 架 可 逆 式 轧 机 带钢 吹 扫 系统 优 化 改造
刘法奎
摘要
关键 词
公茂 海
介 绍双机架轧机 的乳化液喷射 系统 、 吹扫 系统 , 对带钢表面残 留乳化液的原 因进行分析 , 出相应 的改进措施 , 提 并取得 了
乳化液 吹扫 残留 改 造
结束后 , 割枪会 自动驶向最后选定的流待机 位。c . 在切割结束后
的 3 钟 内 ,选 定 下 次 想 切 的 流 待 机 位按 钮 ,s 割 枪 自动 驶 向 s 3后
最后所选定 的流待机位 , 否则 , 割枪会 自动返 回当前所切的流待
机位 。
关, 对好 切缝 , 对钢坯边缘进行 预热 , 操作工掌握预热时间。 然后
此 时 可 根 据 经 验 进 行 割 枪 调 速 , 切 割速 度 调至 最 佳 。 切 割 氧 将 在 打 开 后 的割 枪 行 进 过 程 中 , 序 自动进 行 , 程 由安 装 在 电 机 侧 的 割
热/ 切割停按钮 , 关闭火焰 , 割枪停止 。 由操作工将 割枪开 至下 再
一
切 割 位 或 开 回南北 极 限 位 。
③ 自动操作 。 将选择开关选择至“ 自动”按下 待切 流对应按 。 钮, 操作 台上对应流待机位灯闪烁 , 切割小车快速驶往选定 的待 机 位 , 位 后 , 应 流 灯 常 亮 , 割 小 车 自动 停 止 。待 钢 坯 到 位 到 对 切 后, 人为按下找边 缘按钮 , 操作 台上 找边缘灯亮 , 割枪 小车 自动 驶 向钢坯边 缘 , 待割枪边缘碰锤 与钢坯接 触时 , 割枪小车 自动停 止( 如果此 时边缘 碰锤与钢坯不 能接触 , 以按下 预热按钮 , 可 预 热火焰打开, 并且割枪停 止 , 再人为调整预热边缘 )预热火焰打 。 开( 如果火焰没预 热到钢坯边缘 , 可操 作南北 向开关 , 整预热 调 边缘 )操作 台上预热灯亮 。 , 此时可操作东 西向开关 , 进行对割缝
冷轧硬卷板面质量的改进
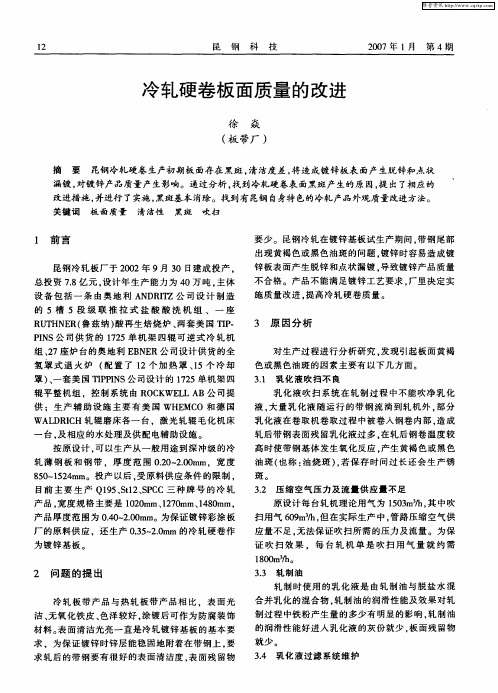
求 ,为保 证镀 锌 时锌 层能 稳 固地 附着在 带 钢上 , 要 求 轧 后 的带 钢要 有很 好 的表 面清 洁度 , 面 残 留物 表
维普资讯
2 0 年 1月 第 4期 o7
昆
钢
科
技
l 3
施质 量改进 。 高 冷轧硬 卷 质量 。 提
R T E 鲁兹纳) U HN R( 酸再 生 焙烧 炉 、 套 美 国 1 P 两 r. I
PN I S公 司 供 货 的 1 2 7 5单 机 架 四辊 可 逆 式 冷 轧 机 组 、 7座炉 台的奥地 利 E N R公 司设 计 供货 的全 2 B E
不均 匀 出现 的漏 吹 。
常泄 漏 . 化液 中杂 油含 量 过 高 , 成 乳 化液 润 滑 乳 造 性能下降 , 使轧 后 板 面残 油 过 多 , 成 镀 锌前 脱 脂 造
材 料 。 面清 洁光 亮 一直 是冷 轧镀 锌基 板 的基 本要 表
33 轧制 油 -
轧 制 时 使 用 的乳 化 液 是 由轧 制 油 与脱 盐 水 混 合并 乳 化 的混合 物 , 制 油 的润滑 性能及 效 果对 轧 轧 制 过程 中铁 粉产 生量 的 多少 有 明显的 影响 , 轧制 油 的润滑 性能 好进入 乳 化液 的 灰份 就少 , 面残 留物 板
3 原 因分 析
对生 产过 程进 行分 析研 究 . 发现 引起 板面 黄褐 色或 黑色 油斑 的 因素 主要有 以下几方 面 。
31 乳化液 吹扫 不 良 .
氢罩式退 火炉 ( 置 了 1 配 2个 加 热 罩 、5个 冷 却 1
罩 ) 一套 美 国 T P I S公 司设 计 的 1 2 、 IPN 7 5单 机架 四 辊平 整 机组 。控 制 系统 由 R C WE LAB公 司 提 O K L 供 :生 产 辅 助 设 施 主 要 有 美 国 WHE O 和德 国 MC WA DR C L I H轧 辊磨 床各 一 台 ,激光 轧 辊 毛化 机 床
自主管理JK课题(降低轧机出口飞剪故障率)
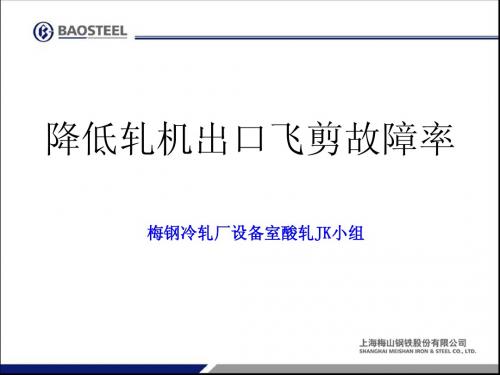
板形质量改善
七、对策实施
改进效果
时间 优化前 目标 优化后
出口断带次数(次/年)
55
40
35
剪切时出口 断带次数(次/年) 剪切时断带 所占比率
32
8
6
58.2%
20.0%
17.1%
飞剪故障次数的箱线图
60
飞剪剪切异常次数(次数/年)
55
50
40
40 35 32
30
20
10
8
6
改进后
0 改进前 目标
故障率24.9%
故障率13.6%
√
选择《降低轧机出口飞剪故障率》为JK课题
二、现状调查
飞剪剪切发生故障时,引起剪切异常,5#机架出口 容易失张断带, 轧机停机。同时,轧机重新开机时, 要进行强制剪切分小卷。
1.设备故障时间(每次故障处理需30min-45min);
2.5#机架出口失张断带,分小卷,降低了成材率
1
下夹送辊接近开关位置不合理
2
3
5#机架工作辊弯辊剪切补偿不合理
出口下夹送辊压力设置不合适
4
5
出口磁力皮带速度不同步
飞剪剪切原始位接近开关挡块
六、制定对策
序 主要原因 号 出口下夹 送辊接近 开关位置 不合理 5#工作辊 弯辊剪切 补偿不合 理 出口下夹 送辊上升 压力设置 不合理 对策 目标 措施 地点 轧机 出口 下夹 送辊 负责人 完成日期
二、现状调查
2012年1月-2013年6月飞剪故障时间统计
时间 飞剪故障时间 时间 飞剪故障时间 时间 飞剪故障时间 (2012年) (分钟) (2012年) (分钟) (2013年) (分钟) 1月 2月 0 35 7月 8月 29 15 1月 2月 0 13
冷轧带钢常见缺陷
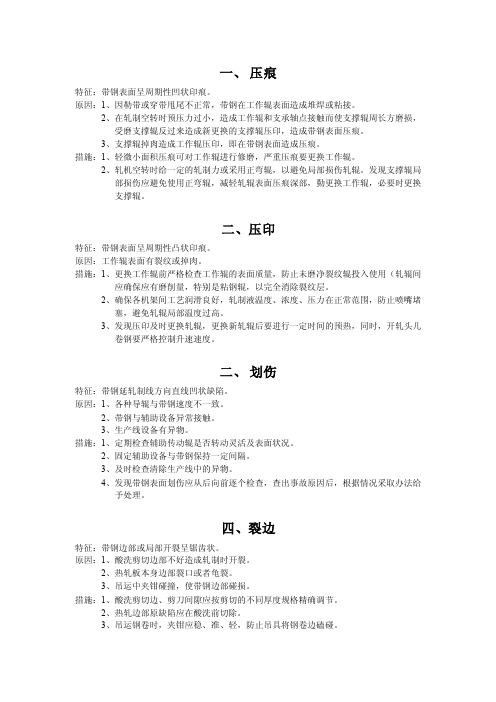
一、压痕特征:带钢表面呈周期性凹状印痕。
原因:1、因勒带或穿带甩尾不正常,带钢在工作辊表面造成堆焊或粘接。
2、在轧制空转时预压力过小,造成工作辊和支承轴点接触而使支撑辊周长方磨损,受磨支撑辊反过来造成新更换的支撑辊压印,造成带钢表面压痕。
3、支撑辊掉肉造成工作辊压印,即在带钢表面造成压痕。
措施:1、轻微小面积压痕可对工作辊进行修磨,严重压痕要更换工作辊。
2、轧机空转时给一定的轧制力或采用正弯辊,以避免局部损伤轧辊。
发现支撑辊局部损伤应避免使用正弯辊,减轻轧辊表面压痕深部,勤更换工作辊,必要时更换支撑辊。
二、压印特征:带钢表面呈周期性凸状印痕。
原因:工作辊表面有裂纹或掉肉。
措施:1、更换工作辊前严格检查工作辊的表面质量,防止未磨净裂纹辊投入使用(轧辊间应确保应有磨削量,特别是粘钢辊,以完全消除裂纹层。
2、确保各机架间工艺润滑良好,轧制液温度、浓度、压力在正常范围,防止喷嘴堵塞,避免轧辊局部温度过高。
3、发现压印及时更换轧辊,更换新轧辊后要进行一定时间的预热,同时,开轧头几卷钢要严格控制升速速度。
二、划伤特征:带钢延轧制线方向直线凹状缺陷。
原因:1、各种导辊与带钢速度不一致。
2、带钢与辅助设备异常接触。
3、生产线设备有异物。
措施:1、定期检查辅助传动辊是否转动灵活及表面状况。
2、固定辅助设备与带钢保持一定间隔。
3、及时检查清除生产线中的异物。
4、发现带钢表面划伤应从后向前逐个检查,查出事故原因后,根据情况采取办法给予处理。
四、裂边特征:带钢边部或局部开裂呈锯齿状。
原因:1、酸洗剪切边部不好造成轧制时开裂。
2、热轧板本身边部裂口或者龟裂。
3、吊运中夹钳碰撞,使带钢边部碰损。
措施:1、酸洗剪切边、剪刀间隙应按剪切的不同厚度规格精确调节。
2、热轧边部原缺陷应在酸洗前切除。
3、吊运钢卷时,夹钳应稳、准、轻,防止吊具将钢卷边磕碰。
五、热划伤特征:带钢沿轧制线方向无规律的条状凹痕。
原因:1、轧辊和热带温度过高。
平整机吹扫工艺优化

第30卷 第4期2008年8月四川冶金Sichuan M eta llurgy Vol .30 No .4Aug .,2008作者简介王金华,济钢技术中心副主任,高级工程师。
李平(),男,工程师,双学士学位,主要从事冷轧产品开发和冷轧工艺研究。
电子信箱3@平整机吹扫工艺优化王金华 李 平(济钢股份有限公司技术中心,济南 250101)【摘 要】 主要分析了由于平整机吹扫效果不佳造成带钢表面乳化液残留多的原因,系统研究了単机架平整机吹扫系统结构,并通过改造上防缠导板气缝、下防缠导板边部吹扫,调整平整液的喷射角度,优化吹扫系统的开启关闭程序,实现了吹扫系统稳定高效运行,使冷轧带钢表面质量得到大幅度的提高。
此类问题的解决,为国内同行带钢表面粘性流体吹扫系统的技术改造及维护运行有较好的借鉴价值。
【关键词】 平整机 乳化液斑 吹扫系统 平整液系统RESEARC H AN D O PT I M IZING O F TE M PER A IRB LOW CRAFTW ang J inhua L i Ping(Technology Cen t of J i Nan Steel Co .,Ltd,J i nan 250101)[Abstra ct] I n this pa per,the eff ects of te mper a ir bl ow on stri p surface emulsi on residual a r e ana 2lyzed,the structure of blow syste m on single shelf temper is studied .B y means of upper gobble guard sl ot reconstructi on,lower gobble guard edge airbl ow,oil spray dir ecti on adjust m ent,and op ti m izing of openand close p r ocedure in airbl ow syste m ,the stable and efficient operati on of air blow system can be a 2chieved,and the cold 2r olled strip sur face qua lity be significantly i mpr oved .The s oluti on of such pr oble m s has made references f or Chinese steel m ills upon rec onstruction and m aintenance of stri p sur face air blow syste m.[Key words] Tempe r,Em ulsi on spot,Sur ge system ,R ust P r eventi on oil system1 前言济钢冷轧单机架平整机设备及控制系统都是由西马克公司引进,2006年9月投产后,产品出现的主要质量缺陷有平整液斑、平整纹、横向波浪、横折印、擦划伤、边皱等质量缺陷,经后序攻关,大部分缺陷都已杜绝或大量减少,唯有平整液斑缺陷一直无法去除,成为制约冷轧产品质量难题。
某钢厂HC冷轧机乳化液过滤系统研究与改进
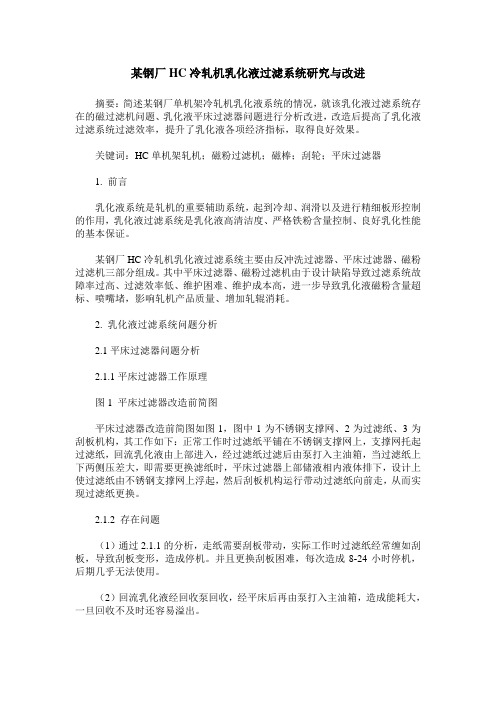
某钢厂HC冷轧机乳化液过滤系统研究与改进摘要:简述某钢厂单机架冷轧机乳化液系统的情况,就该乳化液过滤系统存在的磁过滤机问题、乳化液平床过滤器问题进行分析改进,改造后提高了乳化液过滤系统过滤效率,提升了乳化液各项经济指标,取得良好效果。
关键词:HC单机架轧机;磁粉过滤机;磁棒;刮轮;平床过滤器1. 前言乳化液系统是轧机的重要辅助系统,起到冷却、润滑以及进行精细板形控制的作用,乳化液过滤系统是乳化液高清洁度、严格铁粉含量控制、良好乳化性能的基本保证。
某钢厂HC冷轧机乳化液过滤系统主要由反冲洗过滤器、平床过滤器、磁粉过滤机三部分组成。
其中平床过滤器、磁粉过滤机由于设计缺陷导致过滤系统故障率过高、过滤效率低、维护困难、维护成本高,进一步导致乳化液磁粉含量超标、喷嘴堵,影响轧机产品质量、增加轧辊消耗。
2. 乳化液过滤系统问题分析2.1平床过滤器问题分析2.1.1平床过滤器工作原理图1 平床过滤器改造前简图平床过滤器改造前简图如图1,图中1为不锈钢支撑网、2为过滤纸、3为刮板机构,其工作如下:正常工作时过滤纸平铺在不锈钢支撑网上,支撑网托起过滤纸,回流乳化液由上部进入,经过滤纸过滤后由泵打入主油箱,当过滤纸上下两侧压差大,即需要更换滤纸时,平床过滤器上部储液相内液体排下,设计上使过滤纸由不锈钢支撑网上浮起,然后刮板机构运行带动过滤纸向前走,从而实现过滤纸更换。
2.1.2 存在问题(1)通过2.1.1的分析,走纸需要刮板带动,实际工作时过滤纸经常缠如刮板,导致刮板变形,造成停机。
并且更换刮板困难,每次造成8-24小时停机,后期几乎无法使用。
(2)回流乳化液经回收泵回收,经平床后再由泵打入主油箱,造成能耗大,一旦回收不及时还容易溢出。
2.2磁粉过滤机问题分析图2磁粉过滤机结构简图2.2.1过滤机结构原理磁粉过滤机工作原理简图见图2,过滤机传动机构通过链条带动刮磁机构前后运转,到达后限位后通过撞块与后限位的撞击使悬臂落下,刮板与磁棒接触,刮磁机构向前运行带动刮板将磁棒磁粉刮下;刮磁机构到达前限位后通过撞块与前限位的撞击使悬臂抬起,磁粉刮板与磁棒脱离,刮磁机构转向后运行,这样往复来回,达到过滤磁粉的目的。
乳化液斑迹的形成机理及对策
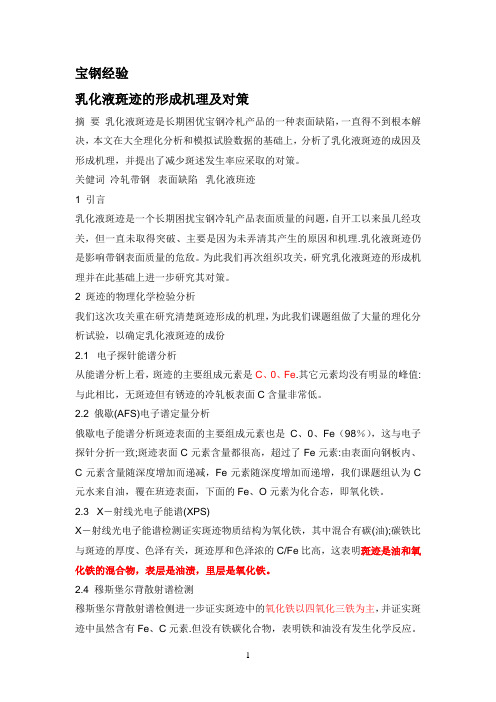
宝钢经验乳化液斑迹的形成机理及对策摘要乳化液斑迹是长期困优宝钢冷札产品的一种表面缺陷,一直得不到根本解决,本文在大全理化分析和模拟试脸数据的基础上,分析了乳化液斑迹的成因及形成机理,并提出了减少斑述发生率应采取的对策。
关健词冷轧带钢表面缺陷乳化液班迹1 引言乳化液斑迹是一个长期困扰宝钢冷轧产品表面质量的问题,自开工以来虽几经攻关,但一直未取得突破、主要是因为未弄清其产生的原因和机理.乳化液斑迹仍是影响带钢表面质量的危敌。
为此我们再次组织攻关,研究乳化液斑迹的形成机理并在此基础上进一步研究其对策。
2 斑迹的物理化学检验分析我们这次攻关重在研究清楚斑迹形成的机理,为此我们课题组做了大量的理化分析试验,以确定乳化液斑迹的成份2.1 电子探针能谱分析从能谱分析上看,斑迹的主要组成元素是C、0、Fe.其它元素均没有明显的峰值:与此相比,无斑迹但有锈迹的冷轧板表面C含量非常低。
2.2 俄歇(AFS)电子谱定量分析俄歇电子能谱分析斑迹表面的主要组成元素也是C、0、Fe(98%),这与电子探针分折一致;斑迹表面C元素含量都很高,超过了Fe元素:由表面向钢板内、C元素含量随深度增加而递减,Fe元素随深度增加而递增,我们课题组认为C 元水来自油,覆在班迹表面,下面的Fe、O元素为化合态,即氧化铁。
2.3 X-射线光电子能谱(XPS)X-射线光电子能谱检测证实斑迹物质结构为氧化铁,其中混合有碳(油);碳铁比与斑迹的厚度、色泽有关,斑迹厚和色泽浓的C/Fe比高,这表明斑迹是油和氧化铁的混合物,表层是油渍,里层是氧化铁。
2.4 穆斯堡尔背散射谱检测穆斯堡尔背散射谱检侧进一步证实斑迹中的氧化铁以四氧化三铁为主,并证实斑迹中虽然含有Fe、C元素.但没有铁碳化合物,表明铁和油没有发生化学反应。
2.5 表面碳分析表面碳分析显示:有斑迹试样表面与班迹带钢相比,表面有机碳的量和峰值要高出几倍至几十倍,即斑迹表面的含油量比无斑迹的高出几倍至几十倍;有斑迹试样表面的有机碳挥发较慢,峰值向右移,表明该有机碳代表的油挥发较慢;有斑迹试样表面有机碳的挥发曲线右侧出现拐点.说明斑迹中存在两种以上的油:该分折还说明油并未与铁发生化学反应而生成某种铁碳化合物,而是独立存在的.被加热时油仍能自由挥发出来2.6 热重分析(TGA)经分析发现轧机所使用的其它油种,蒸发开始温度均高于N428轧制油.蒸发率除液压油DTE-26以外均低于N128轧制油,即这些油的挥发性能低于N428轧制油,另外发现各种油在315°C时均有较大的挥发速率。
1420酸轧机组乳化液吹扫装置的分析及改进

喷 嘴吹 出 的压缩 空气 在 防缠板 前端 与表 面 的 乳 化 将
离开本 来 的流 动方 向并 随着 凸 出的物 体表 面流 动
・
3 6・
梅 山科 技
21 0 0年第 6期 压缩 空气 从 进 口输 入 , 入 环形 腔 , 由环 进 并
乳 化液 。
置 ,交 替 布 置 ,保 证 在 任 意 带 宽 都 能 抽 吸 到 乳
化液。
1 2 应 用 原 理 .
2 缝式 喷嘴 )
位 于上 防缠 板 的前 端 , 缝 式 从
气幕 的产 生 主要 是 依 靠 压 缩 空 气 , 用 的是 应 柯 恩 达空 气放 大效 应 , 流体 ( 流或 气 流 ) 有 即 水 具
1 直 吹喷 嘴 ) 上 防 缠 板 上 方 安 装 有 2个 喷
将 4根钢 管 固定 在 支 架 上 , 管 头部 环 形 喷 嘴 对 钢
正 轧辊 辊缝 。通 过 压缩 空气 吹扫 , 带 钢 上 表 面 将
残 留的少 量乳 化 液 吹 向 带 钢两 侧 , 乳 化 液 从 带 使
钢 的两侧 流下 , 由下 一 步 的抽 吸 式喷 嘴吸 走 。 4 抽 吸式 喷 嘴 安 装 在 下 防 缠 板 上 ,将 带 )
钢 边缘 和下 表 面上残 留的乳化 液 吸净 ,直 接排放 到 乳化 液收 集槽 中。抽 吸 的范 围覆 盖 了带材 宽度
变化 的范 围 ,沿 带材 方 向设 置 了前 后两 排抽 吸装
嘴, 固定在 牌坊 窗 口的横 梁 上 , 喷嘴 正对 着上 工作
辊 与上 中间辊 之 问 的辊 缝 , 于 吹 扫辊 缝 之 间 的 用
的倾 向。当流体 与其流 过 的物 体表 面之 间存 在表
- 1、下载文档前请自行甄别文档内容的完整性,平台不提供额外的编辑、内容补充、找答案等附加服务。
- 2、"仅部分预览"的文档,不可在线预览部分如存在完整性等问题,可反馈申请退款(可完整预览的文档不适用该条件!)。
- 3、如文档侵犯您的权益,请联系客服反馈,我们会尽快为您处理(人工客服工作时间:9:00-18:30)。
行改进 。 并运 用分段控制 的方 法消除 了乳化液残 留问题 。 关键词
1 引言
当今 的冷板 市场 对冷 轧 板 带 的质 量 提 出 了更
高的要求 , 冷轧板带表面质量越来越受到人们的 关注, 尤其是家 电和汽车等行业 。冷轧板带表面 质量的好坏直接影响这些行业产品质量 。马钢第 四钢 轧 总厂 23 酸洗 冷 连轧 生产 线 主要 为下 道 工 10 序 提供 汽 车面 板 、 汽车结 构板 以及 高档家 电板 等 。生产线投产后 , 经常出现板带表面残 留乳化 液现象 , 在后续工序无法处理 , 从而造成了板带严 重 的质 量 问题 。
带表 面 残 留的 乳化 液 ( 图 l 示 ) 会造 成 冷 硬 如 所 也 卷在存放 过程 中发生锈蚀 , 对后续工序及外卖造 成 严重 影 响 。
2 乳化液的作用及其残留的影响 轧 制 乳 化 液 是 由 9%~ 9 7 9 %的水 和 l 3 %~ %的 轧制油经强烈搅拌 而形成的乳化 液( 主要成分 其 为水 、 矿物油及 油性剂 、 表面活性剂 、 极压剂 、 防腐 剂、 抗氧化剂等添加剂 ) 。轧制油乳化液在轧制过 图 1 钢板上残 留的乳化液 程中起润滑和冷却 双重作用 , 直接影 响到冷轧机 组 的产量和质 量。众所周知 , 乳化液 的使用性能 与轧后带钢表面清洁度有 密切 的关 系 , 直接影响 3 改进前 乳化 液 吹扫 系统状 况 马钢 2 3 酸连 轧 线 乳化 液 吹 扫 系统 位 于 5 10 号 着 冷 轧产 品 的表面 质量 。 共有 4 组喷嘴 , 分布在 5 防缠导板 、 号 乳 化液 残 留物 对下 道工序 连退生 产线 的影 轧机 出口侧 , 防溅导板等处 , 具体位置如 图2 所示 , 分别 响 : 退 火 的钢 板 表 面会 呈 现 象 岛 屿 形 状 的 黑 色 坝辊前 、 经 板带上表 面 、 板带下 表 或褐色不规则图形 , 常出现在带钢的头尾部 , 有时 用来 吹扫工作 辊 出 口侧 、 面、 板带边部上下表面 , 工作介质为压缩空气 , 系 出现在带钢边部 , 有时带钢通长都有 。产生的原 .~06 P 。 因是 在退 火 过 程 中 , 化 液残 留物燃 烧 形 成残 渣 , 乳 统 压力 05 .M a 由于 轧机 出 口乳 化 液吹 扫点 造 且退火时的热辐射使残留物 中的油脂产生分解反 多及喷嘴分布不合理等原 因, 成吹扫空气流量 压力过低 , 使板带表面的乳化液吹扫不干净 , 造成 应 , 出碳附着于钢板表面 , 析 铁粉在反应中起媒介 作用 , 加之 自身的污染使板面洁净度 降低 , 随含铁 后续工序 的一系列问题 。 量 的上 升板 面残 渣 量也 上升 , 而影 响表 面质 进 量。当铁颗粒较大时在轧制变形 区内又会硌伤辊 4 吹扫 系统 的 改进 残 留乳化液主要出现在靠 中心线 50 m处 , 0r a 面或带钢表面 , 从而造成划伤 、 辊痕等缺 陷。当乳 化液残 留在某些 部位时 , 由于钢带表 面颜色 的差 传 动侧较严重 。针对现场的实际状况再结合图纸 主要原因是 由于吹扫的喷嘴布局不合理。5 别会造成反射率的差异 , 在退火过程 中钢带颜色 分析 , 号轧机 出口的乳化液吹扫喷嘴其边部吹扫在防溅 深的局部温度偏高 , 钢带颜色低的局部温度偏低 , 是根据带钢 的宽度来调整。在防缠板后 温差极易造成钢带瓢 曲、 跑偏甚至断带。另外 , 板 导板上 ,
一
3 7—
第 2 卷 2 1年第 4 ( 9 0 1 期 总第 14 5 期)
面 的坝辊 上 的 吹扫 喷嘴 只有 3 , 个 主要 分 布在 轧 制 线 中 心部 分 , 由于 受 到 吹扫 压 缩 空气 气 压 及 流 量
技术改造与改进
侧( 侧) 右 的截 止 阀 打开 , 样 所 有 的 喷 嘴都 处 于 这 工 作状 态 , 将宽 带钢 上乳 化液 吹 扫干净 。 可
的限制 , 无法覆盖整个板带 , 所以防缠板 的喷嘴可 把边部吹扫干净 , 后面坝辊的 3 个喷嘴只能把板带 中 间的乳 化 液 吹到距 中心 50 m处 。根据 以上 分 0r a 析, 决定将边部吹扫的宽度加大 , 再将坝辊 的吹扫 管 道 重新 布 置 , 增 阀 台 , 总管 道 引入 气 源 以保 新 从 证 吹扫压力及流量 , 另外将喷射集管 的喷嘴重新 布置 , 并增加喷嘴数量。
/ . 、
{
. 一
辊
图 3 窄板出现 乳化液残 留 嘴 o: 钢带 冷却 喷嘴 ・: 气吹扫 喷 嘴 空
/ ‘
图 2 末架轧机冷却吹扫喷嘴位置
图4 轧机出口坝辊前空气吹扫集管改进示意
试用后 , 宽板吹扫效果 比较理想 , 但窄板会在 边 部 出现 两 条 乳 化 液 斑 迹 , 过 统 计 后 发 现 只 有 经 在生产 1 m以下 的板带时 , . 5 带钢边部才会 出现乳 化液斑迹 。原 因是部分喷嘴下 面没有钢带 ( 图 见 3, )直接吹扫在轧机牌坊和导板上 , 使此处汇集 的 乳化液飞溅 , 最终溅落在钢带的上表面 , 形成乳化 液 斑 迹 。研 究 后 决 定 将 喷 射 集 管 进 行 分 割 , 作 工 侧 和传动侧 两边 的喷嘴通 过 中间的细管道 连接 ( 图4, 见 ) 在生 产 窄 带 钢 时 , 作 侧 ( 侧 ) 工 右 的截 止 阀关闭 , 只有 中间部分 的喷嘴工作 , 这样就避免 了 边部喷嘴吹扫溅起乳化 液 ; 当生产宽带钢时 , 工作
技术改造与改进
第 2 卷 2 1 年第 4 ( 9 0 1 期 总第 14 5 期)
冷轧乳化液吹扫 系统 的改进
陈荣 华 ( 马鞍 山钢 铁股份 有 限公 司第四钢 轧 总厂 马鞍 山 230 ) 400
摘 要 针 对板带冷轧 时存在 的乳化液 残留 问题进行 了研 究, 在原有 设备的基础上 , 对乳化液吹扫 系统进