粮油厂自动供料系统设计
项目一、自动送料装车控制系统的设计、安装与调试

项目一、自动送料装车控制系统的设计、安装与调试一、系统示意图如下图:控制要求:如上图所示,初始状态时红灯L2灭,绿灯L1亮,表示允许汽车进来装料,此时料斗K2、电动机M1、M2、M3皆为OFF。
汽车到来时(用S2开关接能表示),L2亮、L1灭。
M3运行,M2在M3电动机通2S后运行,M1在M2通2S后运行。
再延时2S后,料斗K2打开出料。
当汽车装满后(用S2为“0”表示),料斗K2关闭,电动机M2延时2S后停止,M2在M1停2S后关,M3在M2停2S 后关。
此时,L1亮、L2灭,表示汽车可以开走。
S1是料斗中料位检测开关,其闭合“1”表示料满,K2可以打开;S1断开时表示无料,K1可以打开,K2不可以打开。
二、实训目的:1)熟练掌握控制要求的分析。
2)熟练掌握复杂程序的设计。
3)熟练掌握程序的调试。
三、实训器材:1)FX-20P简易编辑器一个。
2)三菱FX系列PLC一台。
3)RS-232数据通信线一条。
4)送料控制单元一块。
5)导线若干。
四、根据以上信息,列出I/O分配表:五、器件型号表:六、根据I/O分配表可画出电路图;123456A BC D 123456CDAB校 对审 核设 计日 期第 张共张图 号机电工程分院FU1FU2FU3FUKM1KM2KM3PLCFRFR FR XT 端子板自动送料装车系统-安装布置图线糟线糟线糟4409.12.16赵德总七、根据顺序功能图可画出梯形图:八、指令表及调试说明:调试说明:在我们的几番讨论下,在我们的多次试验调试下,这个程序终于被我们调试出来了,在这个过程中,我们遇到了问题,例如说,在按下S1时,K1打开,这时K2不能打开,当S2按下时,小车运行,电动机逐个运行,到达落料口进行落料。
在结束的时候,电动机逐个停止。
但是我们没有考虑到急停,就是说我们要小车停下的时候,整个系统都应该停下的,但是我们按下S2让它停的时候,只是不再继续,但有的电动机还是运行的。
自动配料模拟控制系统设计..

引言自动配料控制系统是采用PLC控制方式以及新颖的变频调速喂料机构,配合配料控制软件包,实现物料传送、配料控制、配方设计、生产数据管理等功能。
并可以通过网络实现多个配料系统的集合控制。
自动配料控制系统设计步骤:1.主电路设计,并画出接线示意图。
2. 分配I/O地址,列出分配表.3。
设计系统控制的程序框图。
4。
根据程序框图设计该系统的控制梯形图.5. 上机调试通过。
6。
利用PLC系统进行模拟运行1自动配料控制系统结构和工作原理1.1自动配料控制系统方案系统启动后,配料装置能自动识别货车到位情况及对货车进行自动配料,当车装满时,配料系统自动关闭.本设计的突出点是故障检测部分的设计,首先,当某一节传送带发生故障时,该节传送带和其前面的传送带会立即停止,该节之后的传送带会在一定的延时后停止。
其次,当某节传送带上的物体过重时,该节传送带和其前面的传送带会立即停止,并且数码显示电路会显示发生故障的电机的号码,该节之后的传送带会在一定的延时后停止。
1。
2 自动配料控制系统基本结构自动配料的模拟面板如图1.1所示,从图中可以看出四节传送带是本次设计的核心电路,PLC编程也是围绕此面板进行的图1。
1 自动配料系统图自动配料系统的功能是利用四节传送带为小车自动配料,重物通过传送带进行传输,发生故障时系统自动停机。
自动配料实验面板与PLC接线控制对应关系如表1。
1。
1所示。
表1。
1。
1 输入/输出接线列表面板SB1 SB2 S1 SQ1 SQ2 D1PLC I0.0 I0。
1 I0。
2 I0。
4 I0.5 Q0。
0面板D2 D3 D4 L1 L2 M1PLC Q0。
1 Q0。
2 Q0.3 Q0。
4 Q0.5 Q0.6面板M2 M3 M4 A B CPLC Q0。
7 Q1。
0 Q1。
1 I0.6 I0。
7 I1.0面板 D I1.2 I1。
3 I1。
4 I1.51. DOP数码显示电路DOP数码显示电路如图1。
2所示。
粮油输送自动化系统

油泵房项目自动化控制系统操作说明一.首先介绍一下各气动阀与泵的控制方式。
控制方式1:在MCC控制柜(控制各台泵)与PLC控制柜(控制各个气动阀)柜门上都装有手自动转换开关与启动、停止按钮,若转换开关打到手动挡,则操作人员可以在柜门上通过启动、停止按钮达到对现场的泵(或气动阀)的启停(或开关)效果。
备注:在此状态下在工控机监控画面上无法对现场设备进行控制,只能监视现场各设备的状态。
控制方式2:若手自动转换开关打到自动挡,则操作人员可以在监控主画面上通过手动点击所需控制的阀或泵,弹出相应的控制画面,通过点击相应控制画面上的启动、停止按钮,从而达到对现场的泵(或气动阀)的启停(或开关)效果。
备注:在此状态下无法通过柜门上的启停按钮实现对现场设备进行控制,除非将手自动转换开关打到手动状态。
控制方式3:若手自动转换开关打到自动挡,则操作人员可以在码头收/发油,汽车收/发油控制画面选择合适的线路,点击线路预览按钮,进入线路预览画面,在线路预览画面中点击此线路的启动、停止按钮,从而实现自动关闭相关阀,自动启动本条线路上所有阀与泵的效果。
备注:在此状态下无法通过柜门上的启停按钮实现对现场设备进行控制,除非将手自动转换开关打到手动状态。
二.自动化控制系统各控制画面的介绍。
1:启动组态软件WINCC之后,系统会自动激活项目并自动跳转到监控主画面,见图1:图1主画面主要功能是对整个控制系统进行监视和对各设备进行独立的启停,在监控主画面中有以下几个方面需要说明:1)阀体状态说明。
图2 图3 图4当气动阀处于开状态时,阀体显示为绿色,如图2所示;当气动阀处于关状态时,阀体显示为红色,如图3所示;当气动阀不处于开状态也不处于关状态,即处于故障状态时,阀体显示为黄色,此时需要专业维护人员检查阀体状态,如图4所示。
2)管道泵、加压泵与发油泵状态说明。
加压泵:当加压泵处于运行状态时,加压泵显示为绿色,如图5所示:图5当加压泵处于停止状态时,加压泵显示如图6所示:图6管道泵:当管道泵处于运行状态时,管道泵显示为绿色,如图7所示:图7当管道泵处于停止状态时,管道泵显示如图8所示:图8发油泵:当发油泵处于运行状态时,发油泵显示为绿色,如图9所示:图9当发油泵处于停止状态时,发油泵显示如图10所示:图103)点击监控主画面中的任意气动阀图标时会弹出相应的阀门控制画面,如图11所示,其中包含阀门的启动与停止按钮、手/自动状态(自动状态即为远程状态)、开关状态。
自动化配料系统策划书
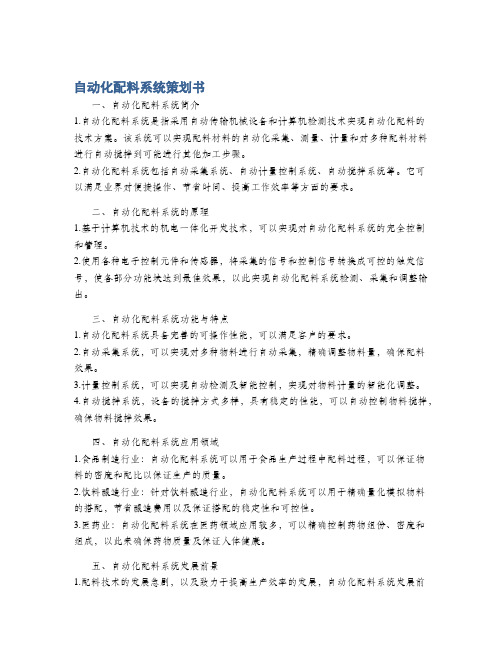
自动化配料系统策划书一、自动化配料系统简介1.自动化配料系统是指采用自动传输机械设备和计算机检测技术实现自动化配料的技术方案。
该系统可以实现配料材料的自动化采集、测量、计量和对多种配料材料进行自动搅拌到可能进行其他加工步骤。
2.自动化配料系统包括自动采集系统、自动计量控制系统、自动搅拌系统等。
它可以满足业界对便捷操作、节省时间、提高工作效率等方面的要求。
二、自动化配料系统的原理1.基于计算机技术的机电一体化开发技术,可以实现对自动化配料系统的完全控制和管理。
2.使用各种电子控制元件和传感器,将采集的信号和控制信号转换成可控的触发信号,使各部分功能块达到最佳效果,以此实现自动化配料系统检测、采集和调整输出。
三、自动化配料系统功能与特点1.自动化配料系统具备完善的可操作性能,可以满足客户的要求。
2.自动采集系统,可以实现对多种物料进行自动采集,精确调整物料量,确保配料效果。
3.计量控制系统,可以实现自动检测及智能控制,实现对物料计量的智能化调整。
4.自动搅拌系统,设备的搅拌方式多样,具有稳定的性能,可以自动控制物料搅拌,确保物料搅拌效果。
四、自动化配料系统应用领域1.食品制造行业:自动化配料系统可以用于食品生产过程中配料过程,可以保证物料的密度和配比以保证生产的质量。
2.饮料酿造行业:针对饮料酿造行业,自动化配料系统可以用于精确量化模拟物料的搭配,节省酿造费用以及保证搭配的稳定性和可控性。
3.医药业:自动化配料系统在医药领域应用较多,可以精确控制药物组份、密度和组成,以此来确保药物质量及保证人体健康。
五、自动化配料系统发展前景1.配料技术的发展急剧,以及致力于提高生产效率的发展,自动化配料系统发展前景广阔。
2.随着生产企业不断完善自动化配料系统,自动化配料系统未来将会得到更多应用,自动化配料系统将会把生产效率提高到前所未有的水平。
3.由于自动化配料系统可以降低人工开销,大大提高了运行效率,未来自动化配料系统将会是市场上重要的产品。
关于粮库自动化系统的设计与实现
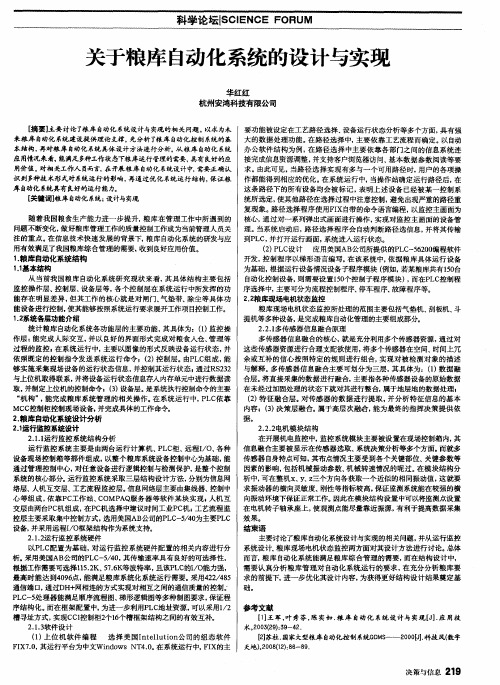
提 机等多种设备 , 是完成 粮库 自动化管理 的主要 组成部分。 2 . 2 . 1 多传感 器信息融 合原 理 多传感器 信息融合 的核 , 就是 充分利 用多个 传感器资源 , 通过 对 这 些传感 器资源进行 合理支 配欲使用, 将 多个传感器 在空 间、 时间上冗 余 或互补 的信心 按照 特定 的规则 进行 组合, 实 现对被 检 测对象 的描 述 与解释 。 多传感 器信 息融合主 要可划分 为三层 , 其 具体为 :( 1 ) 数据 融 合层 。 将直接 采集的数 据进行 融合, 主 要指各种传感 器设备 的原始数 据
科学论坛I S CI E N C E F O R U M
关于粮库 自动化系统的设计与实现
华红红
杭州安鸿科 技有 限公司
[ 摘 要】 主要 讨论了 粮库 自 动化系统设计与实现的相关问题 , 以求为未 来粮库 自 动化 系统建设提供理论支撑。 先 分析 了 粮库自 动化控 制系统 的基 本结构 , 再对粮库 自 动化 系统具体设计方法进行分析。 从 粮库 自 动化 系统 应甩I 睛 况来看, 能满足多种工作 状态下粮库运行管理的需要, 具有良好 的应 要 功能被设 定在工艺 路径选择 、 设备运 行状态分析 等多个方面 , 具有强 大 的数 据处理 功能 。 在 路径 选择 中, 主要 依靠 工艺流程 而确定 。 以自动 办 公软件 结 构为例 , 在 路径 选择 中主要 依靠 各部 门之间 的信息 系统 连 接 完成信息资源调整 , 并支持客户浏 览器访 问 基 本数 据参数 阅读等 要
1 . 2 系统各 层功 能介绍 统 计粮库 自动化 系统各功 能层 的主要功 能, 其 具体为 :( 1 ) 监控 操 作层 : 能 完成 人 际交 互, 并 以 良好 的界面 形式完 成对粮 食人仓、 管理 等 过 程的监 控 , 在系统 运 行 中, 主要 以图像 的形式反 映设备运 行状态 , 并 依 照既定 的控 制指令发送 系统 运行 命令 ,( 2 ) 控制层 。 由P L C 组成 , 能 够 实施采集 现场设备 的运行状 态信 鼠, 并控制其运 行状态 , 通 过R S 2 3 2 与上位机 取得联系 , 并将设备运行状 态信息存人 内存单元 中进行数据 读 取, 并制定上位 机的控制命令 ,( 3 ) 设备层 。 是系统 执行控制命令的主要 “ 机构” , 能完成 粮库 系统管理 的相 关操 作。 在 系统运 行 中, P L C 依 靠 MC C 控制柜控制 现场设备, 并完成具体 的工作命令。
基于PLC控制的自动供料及加工系统设计 毕业设计
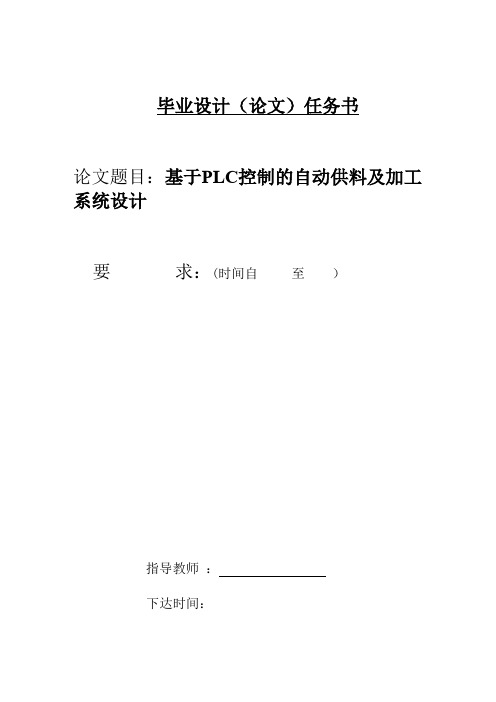
毕业设计(论文)任务书论文题目:基于PLC控制的自动供料及加工系统设计要求:(时间自至)指导教师:下达时间:设计说明(论文)摘要:一、设计题目基于PLC控制的自动供料及加工系统的设计(PLC在自动生产线中的应用)二、题目来源亚龙自动生产线AL335型号实验实训装置的使用三、设计的目的1)掌握自动供料及加工系统的工作原理、工作过程以及其控制操作方式。
2)掌握电气控制元件的选择与计算方法。
3)掌握电气控制系统的设计方法。
4)掌握用PLC改造电气设备的方法选择。
5)掌握PLC控制的设计方法以及编程方法。
6)掌握系统调试方法以及故障检测及排除方法。
四、设计要求结合所学内容根据要求选择合适型号的PLC,用于实施系统的PLC控制操作。
1)完成系统的电气控制线路的设计、调试任务,能够按照要求实施电气控制操作。
2)完成PLC对自动供料及加工系统实施控制操作的设计任务,并进行程序编写以及调试,按照要求完成各项控制操作。
注意:(1)机械手各项动作的先后顺序。
(2)各种动作间联锁关系。
(3)相关动作的工作状态指示。
3)能够进行现场组态监控操作。
五、完成的任务(1)完成电气元器件的选择,电气控制线路的设计,位置分布图及安装接线图的设计及绘制。
(电气绘图软件的使用,如PCschematic 7.0,或AOTCAD2008电气绘图软件)(2)选择PLC型号,分配I/O端口,设计I/O电路、选择元件,绘制梯形图、编织语句表。
(3)组态软件的选择、应用,系统设计、程序编写及通讯调试工作的完成。
目录第1章绪论................................. . (6)1.1 设计的目的和要求 (6)1.2 亚龙自动生产线概述 (6)第2章生产线简介 (9)2.1 生产线基本情况 (9)第3章电器元件、设备的选择 (11)3.1 PLC机型的选择 (11)3.2 传感器 (12)3.3 电磁阀 (14)第4章控制系统的软硬件设计 (15)4.1 控制系统的硬件设计 (15)4.2 控制系统的软件设计 (30)第5章设计小结 (38)参考文献 (40)毕业设计(论文)说明书专用纸第1章绪论1.1 设计目的及要求目前,PLC在国内外已广泛应用于钢铁、石油、化工、电力、建材、机械制造、汽车、轻纺、交通运输、环保及文化娱乐等各个行业,因此PLC在控制领域取得广泛应用。
自动供料系统的设计-毕业论文

自动供料系统的设计-毕业论文南京信息职业技术学院作者权亮亮学号 21014X25 系部机电学院专业机电一体化技术题目自动供料系统的设计指导教师王春峰评阅教师日完成时间: 2013年 4 月 22毕业设计(论文)中文摘要题目:提升机摘要:目前,现代工业控制设备(PLC、变频器、触摸屏、现场总线、上位机)在电子产品装配线的应用越来越普及,随着技术进步和设备更新,对现场技术人员和维护人员的要求也越来越高。
不能充分结合现场工艺发挥功能和效益,尤其在设备出现故障时,不能快速有效地判断和处理故障,影响了正常生产秩序。
采用变频控制的提升电机,其优越的制动可以使提升机获得平稳、安全、可靠的制动运行状态,避免严重的机械磨损,防止较大的机械冲击,减少机械部分维修的工作量,延长提升机的使用寿命。
变频调速控制可以实现提升机的恒加速和恒减速控制,能很好的防止提升机过卷和过放事故发生。
关键词:可靠性;变频控制;控制系统;PLC;自动控制;提升机;机电一体化毕业设计(论文)外文摘要Title : elevating conveyorAbstract: Currently, modern industrial control equipment (PLC, inverter,touch screen, field bus, the host computer) in the application of electronic product assembly lines is becoming increasingly popular. Withthe development of technology and equipment innovation, on-sidetechnicalpersonnel and maintenance personnel are increasingly high requirements. Notfully integrated on-site process function and efficiency, especially in the event of equipment failure, you can not judge and deal withfaults quickly and effectively, affecting the normal production order. The lifting motor adopts frequency control, its superior braking canhoist to obtain stable, safe, reliable braking operation state, to avoid serious mechanical wear, prevent the large mechanical impact, reduce the workload of the mechanical parts, extend the service life of the machine. Frequency control can beachieved hoist constant acceleration and constant deceleration control, and can be very good to prevent hoist volumes and over-discharge accident.keywords: Reliability; frequency control; control system; PLC; automation; elevating conveyor; mechanical-electrical integration 目录1 引言 (1)2 整体设计方案 ......................................................... 1 2.1 控制部分方案的确定 ................................................. 4 2.2动力部分方案的确定 (9)2.2.2 直流电机 ....................................................... 10 2.2.3 变频电机 ....................................................... 10 2.3 传动部分方案的确定 ............................................... 13 2.3.1 齿轮传动 . (13)2.3.2 链传动 .........................................................13 3 提升机的机械结构的设计 .............................................143.1 提升机的主要组成部分 ............................................. 14 3.2 电动机功率计算 .................................................... 18 3.3 链的计算 .......................................................... 19 3.4 轴的设计 ......................................................... 21 4 提升机的电器控制 (24)4.1 变频器的选择 .....................................................244.2 外部电路介绍 ..................................................... 26 4.3 软件流程图 ........................................................ 28 结论 (36)致谢 .................................................................. 36 参考文献 (37)1 引言提升机作为一种垂直运输工具,在各种社会生产中占有极其重要的地位。
自动供料控制系统的设计

襄樊职业技术学院(毕业)论文自动供料控制系统的设计专业班级:机电一体化1002班学生:陈祥学号: ********* 指导教师:***教学单位:电子信息工程学院毕业届: 2013届毕业设计(论文)课题任务书电子信息工程学院系(院)机电一体化专业1002班学生陈祥毕业设计(论文)课题自动供料控制系统的设计二、毕业设计(论文)工作自2012年10 月01 日起至2012年10月30日止三、毕业设计(论文)进行地点襄樊职业技术学院学院四、毕业设计(论文)的内容要求:新颖性、真实性五、主要参考文献[1] 汤晓华可编程控制器应用技术. 湖北:湖北科技出版社2008[2] 杜玉红生产线组装单元气动搬运机械手的设计. 液压与气动2006 (5)[3] 于洋等基于PLC的小型模拟自动生产线. 机械设计与研究2007 (3)[4] 王寿斌基于PLC回转自动化控制生产线仿真示教设备的设计与实现. 现代制造技术与设备 2007(5)[5] 高然生进口生产线的安装与调试. 设备管理与维修 2008 (8)指导教师雷红华学生___ 陈祥 __目录目录: (2)摘要: (3)关键词: (3)前言: (3)第一章自动供料机构概述 (3)1.1供料机构控制要求 (3)1.2工料机构主要组成与功能 (4)第二章动力硬件的选择 (5)2.1电机的选择 (5)2.2驱动控制系统的组成 (5)2.3PLC与驱动系统的接线 (6)2.4步进电机与驱动器的接线 (6)2.5电磁阀的选择 (7)2.6空气泵的型号和技术参数 (7)第三章PLC的选型 (8)3.1PLC的应用特点 (8)3.2PLC模块 (8)3.3端子接线 (9)3.4西门子PLC控制原理图 (10)第四章工料系统的程序设计 (11)4.1程序的要求和工作流程 (11)结束语 (15)参考文献 (15)我院计算机专业机房维护方案设计与实现学生:陈祥指导教师:雷红华摘要伴随时代发展,进入21世纪崭新工业控制领域,PLC仍然能够引导自动化行业的发展,主要是由于在最初其采用计算机的设计思想和适应各种现场应用,随着电子事业的飞速发展,PLC已经可以在各个领域去适应不同的客户要求。
项目一任务8-自动供料系统控制工艺流程设计(精)
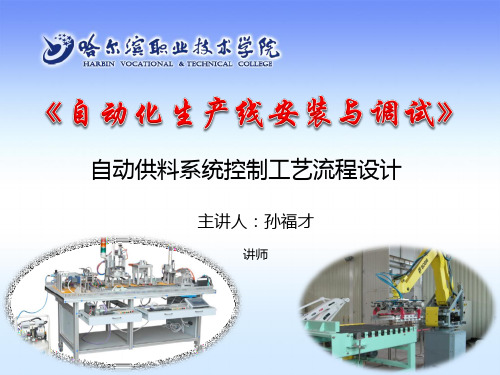
电传感器,工作定位装置等构成。供料单元的基本功 能是按照需要将放置在料仓中待加工的工件自动送出
到物料台上,以便输送单元的抓取机械手装置将工件
抓取送往其他工作单元。
项目构思
二、自动供料单元的动作过程
工件垂直叠放在料仓中,推料缸处于料仓的底层并且其活塞杆可从
料仓的底部通过。当活塞杆在退回位置时,它与最下层工件处于同一水 平位置,而夹紧气缸则与次下层工件处于同一水平位置。在需要将工件
自动供料系统控制工艺流程设计
主讲人:孙福才
讲师
项目构思
一、自动供料系统的认知
供料单元是自动生产线中的起始单元,向系统中 的其他单元提供原料,相当于实际生产线中的自动上 料系统。 之前,我们了解下自动供料系统基本结构和主要 功能:供料单元主要由工件库,工件锁紧装置,工件
推出装置。主要配置有:井式工件库,直线气缸,光
1)设备上电和气源接通后,若工作站的两个气缸均处于缩回位置,且料仓 内有足够的待加工工件,则“正常工作”指示灯HL1 常亮,表示设备准备好。 否则,该指示灯以1Hz 频率闪烁。若设备准备好,按下启动按钮,工作站启动 ,“设备运行”指示灯HL2 常亮。启动后,若出料台上没有工件,则应把工件 推到出料台上。出料台上的工件被人工取出后,若没有停止信号,则进行下一 次推出工件操作。 2)若在运行中按下停止按钮,则在完成本工作周期任务后,各工作站停止 工作,HL2 指示灯熄灭。 3)若在运行中料仓内工件不足,则工作站继续工作,但“正常工作”指示
灯L1以1Hz 的频率闪烁,“设备运行”指示灯HL2 保持常亮。若料仓内没有工
件,则HL1 指示灯和HL2 指示灯均以2Hz 频率闪烁。工作站在完成本周期任务 后停止。除非向料仓补充足够的工件,工作站不能再启动。
自动送料装车控制系统设计

自动送料装车控制系统设计1.设计任务(1)硬件设计自动送料装车系统控制电路设计煤矿或沙场自动送料装车系统。
完成工作流程图;主电路图;控制器接线图;元件选型;电机选择,有必要的设计计算。
(给简易控制系统示意图。
)(2)软件设计自动送料装车系统控制程序控制要求:能够控制启动/停止;装车完毕闪烁提示,汽车开走,进行下一轮的装载工作等。
(3)机械设计自动送料输送带机械结构。
2.要求(1)绘制硬件接线框图;控制流程框图及其它原理图。
(2)撰写设计说明书,并附程序清单及其功能注释。
(3)调试控制程序。
二、进度安排及完成时间1.设计时间三周(从2012年12月3日至2012年12月21 日)2.进度安排第1周:布置设计任务;补充相关知识;查阅资料;撰写绪论,确定系统组成方案。
第2周:输送带传动装置结构设计;绘制装配图、零件图。
控制系统硬件设计,选择电气元件,设计系统框图、外部电路接线图。
第3周:编写主程序、功能子程序并调试。
并记录存在的问题和解决问题的方法;整理设计资料;按格式模版撰写设计说明书;上交设计作业(打印稿及电子文档);并参加答辩。
注:程序设计2人;硬件电路设计2人;机械结构设计2~3人。
目录第1章绪论 (1)1.1自动送料装车控制的发展 (1)1.2自动送料装车控制系统设计的目的和意义 (1)第2章确定课题设计方案 (3)2.1 初定动力部分 (3)2.2 初定传动部分 (3)2.3 初定执行机构 (3)2.4 控制器选型 (4)2.5 系统总体工作流程 (5)第3章机械结构设计 (6)3.1系统设计的原始参数 (6)3.2初选输送带 (6)3.2带速和滚筒转速计算 (7)3.3牵引力和电动机功率计算 (7)3.4电机的选型和传动比的确定 (7)3.4.1电机的选型 (7)3.4.2传动比的确定 (7)3.5传动装置的布置方式 (8)3.6 传动滚筒的作用及类型 (8)第4章硬件部分设计 (10)4.1 主电路的设计 (10)4.2 PLC机型的选择 (11)4.4开关的选择 (11)4.5熔断器的选择 (11)4.6 接触器的选择(KM) (12)4.7 传感器的选择 (12)4.7.1称重传感器的选择 (12)4.7.2霍尔传感器的选择 (12)4.8 继电器的选择 (13)4.9 行程开关的选择 (13)4.10物位传感器的选择 (14)4.10.1电容式物位传感器 (14)4.10.2阻力式料位传感器 (15)4.11 I/O地址表 (16)第5章软件控制 (18)5.1 PLC程序流程图设计 (18)5.2 PLC程序框图 (19)5.3 PLC程序 (21)结论 (23)参考文献 (24)第1章绪论1.1自动送料装车控制的发展送料装车设备广泛地应用于建材、冶金、煤炭、电力、化工、轻工等工业生产部门。
粮油厂自动供料系统设计

粮油厂自动供料系统设计摘要:本文主要介绍通过对粮油厂自动送料系统的改造,将原来的传统继电器控制系统改造成PLC+触摸屏控制系统。
改造后的设备具有运行监控、出料控制、故障报警和电机控制等功能。
取代传统的手动供料,为了降低成本,消除累计误差,提高生产效率,该系统将采用比例阀与供料机构为配合的主要装置。
设计出能够代替人在饲料厂供料的自动供料机。
关键词:PLC;程序设计;供料;PLC控制;触摸屏1 引言目前,PLC的控制技术已步入成熟阶段,国内外应用的领域非常广泛,PLC的应用不但大大地提高了电气控制系统的可靠性和抗干扰能力,而且大大地简化和减少了维修维护的工作量。
PLC以其可靠性高、抗干扰能力强、编程简单、使用方便、控制程序可变、体积小、质量轻、功能强和价格低廉等特点。
广泛应用于钢铁、石油、化工、电力、建材、机械制造、汽车、轻纺、交通运输、环保及文化娱乐等各个方面,其应用的数量已占据各类工业自动化控制设备的首位。
本文的自动送料系统就是采用了PLC控制。
该系统是使用在饲料厂用于传送指定的饲料,实现自动供料。
传统的手动供料,不但效率低,工作环境差,同时有浪费劳动力。
为了降低成本,消除累计误差,提高生产效率,该系统将采用伺服电机与供料机构为配合的主要装置。
设计出能够代替人在饲料厂供料的自动供料机。
2 系统组成和控制要求2.1 系统组成图一如图所示,系统以8台伺服电机运行,以继电器、触摸屏、可编程序控制器PLC作为系统控制的核心部件。
系统主要是用于控制送料卷轮的自动供料,它既能减轻人的工作强度,又能自动准确的到达人所不能到达或很难到达的预定位置。
系统中有两个饲料仓,可以存储两种不同的饲料,可以根据不同的需要,分别传送饲料到两个仓。
两个仓的饲料可以根据需求,进行出料混合,混合的比例可以根据实际情况,在触摸屏设定出料阀数值,从而控制出料阀的打开以及打开大小。
通过触摸屏,可以对自动供料系统进行运行监控、出料阀控制、故障报警、电机控制等操作。
自动上料配料系统方案

照时数达1803 小时。
物料输送自动上料及配料系统方案一、工程概述锂电池负极材料生产线的前端DCS 自动上料及配料系统。
该系统用于以石油炼解后的附产品石焦油为主要原料,通过物理及化学反响生产人工石墨生产线的自动上料、输送,自动配料,自动投放的系统把握,实现系统在线实时监测,信息、故障提示、生成生产记录、统计报表等。
为业主供给准确牢靠的数据报表、产出量报表等。
历史气候状况:该地区属于中亚温湿气候,年平均气温为17.3℃。
其中,一月份最冷,平均气温4.7℃,历史上极端最低气温为零下15.1℃,七月份最热,平均气温29℃,极端最高温曾在8 月初消灭达40.4℃。
全年平均降雨量为1612 毫米,最多年份达2264 毫米,最少年份只有1237 毫米,降雨量集中在4—6 月份,占全年的54%,7—9 月雨量石焦油参数:颗粒度〔D50〕8~10um,常规散装积存密度为:0.3~0.45,最低为:0.22,挤压后最大密度为:1.1 含水率:小于0.2%,物料安眠角:,硬度:1-2.工艺流程要求连贯、牢靠、严禁消灭跑漏冒等恶性事故的发生,确保系统全年正常生产。
生产线按年度需定期检查,提起排解故障隐患。
1、用户需求分析(1)、产品规模生产要求系统具有更大的产能、更高的稳定性;(2)、降低人工上料劳动强度、改善员工工作环境、提高计量精度;(3)、粉体及液体物料均应自动上料、自动计量;(4)、每次生产的不同配方〔原料配比〕均可在电脑上进展操作;(5)、生产过程实现自动化把握及远程监控,同时可依据操作级别设置就地操作和急停。
(6)、对储料罐设置上限和下限报警,超限停机。
2、工程设计、制造、安装、检验标准DCS 自动上料及配料系统在设计、制造和验收过程中应符合国家相关技术标准和标准,并以最版为准。
包括但不限于以下标准:削减,不到全年的28%。
年相对湿度平均为79%,无霜期年平均为260天左右,年日GB/T9969—2022 工业产品使用说明书总则GB/T14436—1993 工业产品保证文件GB/T6587 —1986 电子测量仪器GB/T7724—2022 称重显示把握器技术条件JJG555—1996 非自动秤通用检定规程QB 1563—2022 衡器产品型号编制方法GB/T7551—2022 称重传感器GB/T14249.1—93 JJG649-90GB/T14249.2-93 GB/T5185-1985GB1184GB1901GB/T1804GB1764JB/TQ4000.3 IEC/GBGB324-88GB8923GB9286JB8JB/ZQ4000.3B/ZQ4286-86GB4208TJ231(四)GBJ17-88GB191-2022GB3797-89GB4064-83GB14285-93电子衡器安全要求数字称重显示器电子衡器通用技术要求气焊、手工电弧焊及气体保护焊,焊缝坡口的根本形式与尺寸外形和位置公差、未注公差的规定公差与协作尺寸至500mm 孔、轴工差带与协作一般公差线性尺寸的未注公差漆膜厚度测定法焊接通用技术条件电动机技术标准钢焊缝符号表示法涂装钢材外表锈蚀等级和除锈等级色漆和清漆漆膜的划格试验产品标牌焊接通用技术要求包装通用技术条件外壳防护等级分类机械设备安装工程施工及验收标准钢构造设计标准包装储运图示标志电控设备其次局部装有电子器件的电控设备电气设备安全设计导则继电保护和安全自动装置技术规程GB/T1459898-91 电气装置安装工程电气设备交接试验标准GB1497-85 低压电器根本标准二、本方案自动上料及配料系统组成生产线配料主要完从与混料机下部料仓星型给料机下部开头:通过1 号物料输送机→2 号物料输送机→1~12 号下料器→1~12 计量仓→1~12 号仓下料排料阀→1~12 号水平输送机→1~12 号釜口气动球阀止。
自动供料系统的设计-毕业论文

自动供料系统的设计-毕业论文南京信息职业技术学院作者权亮亮学号 21014X25 系部机电学院专业机电一体化技术题目自动供料系统的设计指导教师王春峰评阅教师日完成时间: 2013年 4 月 22毕业设计(论文)中文摘要题目:提升机摘要:目前,现代工业控制设备(PLC、变频器、触摸屏、现场总线、上位机)在电子产品装配线的应用越来越普及,随着技术进步和设备更新,对现场技术人员和维护人员的要求也越来越高。
不能充分结合现场工艺发挥功能和效益,尤其在设备出现故障时,不能快速有效地判断和处理故障,影响了正常生产秩序。
采用变频控制的提升电机,其优越的制动可以使提升机获得平稳、安全、可靠的制动运行状态,避免严重的机械磨损,防止较大的机械冲击,减少机械部分维修的工作量,延长提升机的使用寿命。
变频调速控制可以实现提升机的恒加速和恒减速控制,能很好的防止提升机过卷和过放事故发生。
关键词:可靠性;变频控制;控制系统;PLC;自动控制;提升机;机电一体化毕业设计(论文)外文摘要Title : elevating conveyorAbstract: Currently, modern industrial control equipment (PLC, inverter,touch screen, field bus, the host computer) in the application of electronic product assembly lines is becoming increasingly popular. Withthe development of technology and equipment innovation, on-sidetechnicalpersonnel and maintenance personnel are increasingly high requirements. Notfully integrated on-site process function and efficiency, especially in the event of equipment failure, you can not judge and deal withfaults quickly and effectively, affecting the normal production order. The lifting motor adopts frequency control, its superior braking canhoist to obtain stable, safe, reliable braking operation state, to avoid serious mechanical wear, prevent the large mechanical impact, reduce the workload of the mechanical parts, extend the service life of the machine. Frequency control can beachieved hoist constant acceleration and constant deceleration control, and can be very good to prevent hoist volumes and over-discharge accident.keywords: Reliability; frequency control; control system; PLC; automation; elevating conveyor; mechanical-electrical integration 目录1 引言 (1)2 整体设计方案 ......................................................... 1 2.1 控制部分方案的确定 ................................................. 4 2.2动力部分方案的确定 (9)2.2.2 直流电机 ....................................................... 10 2.2.3 变频电机 ....................................................... 10 2.3 传动部分方案的确定 ............................................... 13 2.3.1 齿轮传动 . (13)2.3.2 链传动 .........................................................13 3 提升机的机械结构的设计 .............................................143.1 提升机的主要组成部分 ............................................. 14 3.2 电动机功率计算 .................................................... 18 3.3 链的计算 .......................................................... 19 3.4 轴的设计 ......................................................... 21 4 提升机的电器控制 (24)4.1 变频器的选择 .....................................................244.2 外部电路介绍 ..................................................... 26 4.3 软件流程图 ........................................................ 28 结论 (36)致谢 .................................................................. 36 参考文献 (37)1 引言提升机作为一种垂直运输工具,在各种社会生产中占有极其重要的地位。
饲料配料自动化生产线的设计与实现
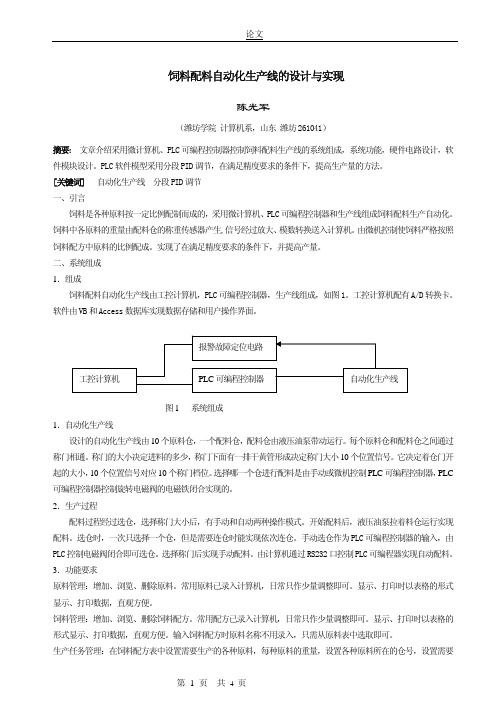
饲料配料自动化生产线的设计与实现陈光军(潍坊学院 计算机系,山东 潍坊261041)摘要: 文章介绍采用微计算机、PLC可编程控制器控制饲料配料生产线的系统组成,系统功能,硬件电路设计,软件模块设计。
PLC软件模型采用分段PID调节,在满足精度要求的条件下,提高生产量的方法。
[关键词] 自动化生产线 分段PID调节一、引言饲料是各种原料按一定比例配制而成的,采用微计算机、PLC可编程控制器和生产线组成饲料配料生产自动化。
饲料中各原料的重量由配料仓的称重传感器产生,信号经过放大、模数转换送入计算机。
由微机控制使饲料严格按照饲料配方中原料的比例配成。
实现了在满足精度要求的条件下,并提高产量。
二、系统组成1.组成饲料配料自动化生产线由工控计算机,PLC可编程控制器,生产线组成,如图1。
工控计算机配有A/D转换卡。
软件由VB和Access数据库实现数据存储和用户操作界面。
图1 系统组成1.自动化生产线设计的自动化生产线由10个原料仓,一个配料仓,配料仓由液压油泵带动运行。
每个原料仓和配料仓之间通过称门相通。
称门的大小决定进料的多少,称门下面有一排干黄管形成决定称门大小10个位置信号。
它决定着仓门开起的大小,10个位置信号对应10个称门档位。
选择哪一个仓进行配料是由手动或微机控制PLC可编程控制器,PLC 可编程控制器控制旋转电磁阀的电磁铁闭合实现的。
2.生产过程配料过程经过选仓,选择称门大小后,有手动和自动两种操作模式。
开始配料后,液压油泵拉着料仓运行实现配料。
选仓时,一次只选择一个仓,但是需要连仓时能实现依次连仓。
手动选仓作为PLC可编程控制器的输入,由PLC控制电磁阀闭合即可选仓。
选择称门后实现手动配料。
由计算机通过RS232口控制PLC可编程器实现自动配料。
3.功能要求原料管理:增加、浏览、删除原料。
常用原料已录入计算机,日常只作少量调整即可。
显示、打印时以表格的形式显示、打印数据,直观方便。
饲料管理:增加、浏览、删除饲料配方。
PLC自动配料系统设计-自动配料的控制系统设计plc程序

PLC自动配料系统设计-自动配料的控制系统设计plc程序基于PLC自动配料系统设计摘要PLC的定义有许多种。
国际电工委员会(IEC)对PLC的定义是:可编程控制器是一种数字运算操作的电子系统,专为在工业环境下应用而设计。
它采用可编程序的存贮器,用来在其内部存贮执行逻辑运算、顺序控制、定时、计数和算术运算等操作的指令,并通过数字式、模拟式的输入和输出,控制各种类型的机械或生产过程。
可编程序控制器及其有关设备,都应按易于与工业控制系统形成一个整体,易于扩充其功能的原则设计。
PLC具有通信联网的功能,它使PLC与PLC 之间、PLC与上位计算机以及其他智能设备之间能够交换信息,形成一个统一的整体,实现分散集中控制。
多数PLC具有RS-232接口,还有一些内置有支持各自通信协议的接口。
配料工人收到每天的生产作业表后, 将依次对每种原料进行称重?根据配料的多少, 先计算每种成分的重量,然后在各种成分的料桶中取料,传送到电子称上进行称重,最后进行包装。
目录1绪论 (5)1.1课题来源及现实意义 (5)1.1.1课题来源 (5)1.1.2 现实意义 (5)1.2设计任务与总体方案的确定 (5)1.2.1设计要求 (5)1.2.2控制要求 (5)2 PLC与自动化软件 (5)2.1 PLC的发展历史 (6)2.2 PLC的硬件和软件 (7)2.2.1 PLC的硬件构成 (7)2.2.2 PLC的软件构成 (8)2.3 PLC系统的辅助设备 (8)2.4 PLC的通讯联网 (9)2.5 PLC的注意事由 (9)2.6自动化软件发展历史及定义 (10) 2.7发展趋势 (10)3自动配料系统设计 (12)3.1自动配料系统简介 (12)3.1.1自动配料系统的特点 (12) 3.1.2自动配料系统组成 (12)3.2自动配料系统设计 (13)3.2.1配料系统的设计 (13)1称重方式选择 (13)2给料方式选择 (14)3生产线结构 (15)3.2.2配料系统的组成 (15)3.2.3输送装置的设计 (15)3.2.4计量系统的设计 (16)1 称重元件设计 (16)2 测速元件的设计 (17)4控制系统设计 (20)4.1 控制系统硬件设计 (20)4.1.1 PLC的选配 (20)4.1.2 称重仪表的选配 (23)4.1.3 操作站的选配 (23)4.2 控制系统软件设计 (23)4.2.1称量仪表参数设定 (23)4.2.2 PLC程序编制 (24)全文结论致谢参考文献1 绪论1.1课题的来源及现实意义1.1.1 课题的来源自动配料系统是一个针对各种不同类型的物料(固体或液体)进行输送、配比、加热、混合以及成品包装等全生产过程的自动化生产线。
智慧料场系统设计方案

智慧料场系统设计方案智慧料场系统是一种基于物联网和数据分析技术的智能化仓储管理系统,可以实时监测和管理仓库内的物资信息。
以下是一个智慧料场系统的设计方案。
一、系统架构智慧料场系统的架构包括前端设备、传感器网络、数据传输网络、云平台和应用程序。
前端设备包括智能终端设备,比如智能手持终端、智能标签和RFID设备等,用于采集和展示物资信息。
传感器网络包括各种传感器,如温湿度传感器、重量传感器、光照传感器等,用于监测仓库内的环境和物资状态。
数据传输网络采用互联网或物联网技术,将前端设备和传感器网络采集的数据传输到云平台。
云平台是一个数据存储和处理的中心,用于存储、分析和处理数据,并提供接口供应用程序调用。
应用程序是用户通过智能终端设备访问的界面,用于展示物资信息、查询库存和下单等操作。
二、系统功能智慧料场系统具有以下功能:1. 实时监测:通过传感器网络实时监测仓库内的温湿度、光照等环境信息,以及物资的重量、数量等状态信息。
2. 库存管理:通过RFID技术和智能标签,实现对物资的自动识别和管理,包括入库、出库、盘点等操作。
3. 物资追踪:通过RFID或其他定位技术,实现对物资的实时追踪和定位,提高物资的可见性和安全性。
4. 数据分析:通过云平台对采集到的数据进行分析和预测,提供物资需求预测、库存优化等决策支持。
5. 通知报警:根据设定的规则和条件,系统可以自动触发通知和报警,提醒用户进行相应的操作。
6. 移动办公:用户可以通过智能终端设备远程访问系统,实现移动办公和实时操作,方便管理和调度。
三、系统优势智慧料场系统相对传统的仓储管理方式具有以下优势:1. 实时性:系统可以实时监测物资的状态和环境信息,提供及时的数据支持和决策参考。
2. 准确性:采用自动识别技术,避免了传统人工盘点的误差,提高了数据的准确性和可靠性。
3. 效率性:系统可以自动化物资管理过程,减少人力成本和操作时间,提高仓库管理效率。
4. 精细化:系统可以对物资进行细化管理和追踪,提高库存管理的精细程度和灵活性。
自动配料系统设计毕业论文

自动配料系统设计毕业论文目录第一章引言 (1)第二章自动配料系统设计总框图 (2)第三章自动配料系统硬件的设计 (4)3.1 配料系统的设计 (4)3.2 计量系统的设计 (6)3.3 变频器的选择 (6)3.4 电机的选择 (6)3.5 传感器的选择 (6)第四章控制系统硬件设计 (16)4.1 PLC的选型 (16)4.2 称重仪表的选配 (19)4.3 操作站的选配 (20)第五章控制系统的软件设计 (21)5.1 称量仪表参数设定 (21)5.2 PLC程序编制 (22)5.3操作站WINCC组态系统 (27)第六章结束语 (33)参考文献 (34)毕业设计总结 (35)毕业设计致谢 (36)Computer Aided Design (1)附件(图纸) (45)英文翻译 (46)第一章引言自动配料系统是一个针对各种不同类型的物料(固体或液体)进行输送、配比、加热、混合以及成品包装等全生产过程的自动化生产线。
可以广泛应用于化工、塑料、冶金、建材、食品、饲料等行业。
自动配料系统的恒流量控制采用PID调节,流量计量控制是计量偏差与变频调速的结合。
依据系统工艺流程介绍了配料系统的流量控制方式和系统控制过程,详细讲述了PLC的选型及PLC配料系统变频控制中的硬件设置、参数设定和软件设计过程。
自动配料系统是精细化工厂生产工艺过程中一道非常重要的工序,配料工序质量对整个产品的质量举足轻重。
自动配料控制过程是一个多输入、多输出系统,各条配料输送生产线严格地协调控制,对料位、流量及时准确地进行监测和调节。
系统由可编程控制器与电子皮带秤组成一个两级计算机控制网络,通过现场总线连接现场仪器仪表、控制计算机、PLC、变频器等智能程度较高、处理速度快的设备。
在自动配料生产工艺过程中,将主料与辅料按一定比例配合,由电子皮带秤完成对皮带输送机输送的物料进行计量。
PLC主要承担对输送设备、秤量过程进行实时控制,并完成对系统故障检测、显示及报警,同时向变频器输出信号调节皮带机转速的作用。
- 1、下载文档前请自行甄别文档内容的完整性,平台不提供额外的编辑、内容补充、找答案等附加服务。
- 2、"仅部分预览"的文档,不可在线预览部分如存在完整性等问题,可反馈申请退款(可完整预览的文档不适用该条件!)。
- 3、如文档侵犯您的权益,请联系客服反馈,我们会尽快为您处理(人工客服工作时间:9:00-18:30)。
粮油厂自动供料系统设计发表时间:2019-01-03T16:17:28.867Z 来源:《基层建设》2018年第32期作者:林世平[导读] 摘要:本文主要介绍通过对粮油厂自动送料系统的改造,将原来的传统继电器控制系统改造成PLC+触摸屏控制系统。
湛江机电学校广东湛江 524000摘要:本文主要介绍通过对粮油厂自动送料系统的改造,将原来的传统继电器控制系统改造成PLC+触摸屏控制系统。
改造后的设备具有运行监控、出料控制、故障报警和电机控制等功能。
取代传统的手动供料,为了降低成本,消除累计误差,提高生产效率,该系统将采用比例阀与供料机构为配合的主要装置。
设计出能够代替人在饲料厂供料的自动供料机。
关键词:PLC;程序设计;供料;PLC控制;触摸屏 1 引言目前,PLC的控制技术已步入成熟阶段,国内外应用的领域非常广泛,PLC的应用不但大大地提高了电气控制系统的可靠性和抗干扰能力,而且大大地简化和减少了维修维护的工作量。
PLC以其可靠性高、抗干扰能力强、编程简单、使用方便、控制程序可变、体积小、质量轻、功能强和价格低廉等特点。
广泛应用于钢铁、石油、化工、电力、建材、机械制造、汽车、轻纺、交通运输、环保及文化娱乐等各个方面,其应用的数量已占据各类工业自动化控制设备的首位。
本文的自动送料系统就是采用了PLC控制。
该系统是使用在饲料厂用于传送指定的饲料,实现自动供料。
传统的手动供料,不但效率低,工作环境差,同时有浪费劳动力。
为了降低成本,消除累计误差,提高生产效率,该系统将采用伺服电机与供料机构为配合的主要装置。
设计出能够代替人在饲料厂供料的自动供料机。
2 系统组成和控制要求 2.1 系统组成图一如图所示,系统以8台伺服电机运行,以继电器、触摸屏、可编程序控制器PLC作为系统控制的核心部件。
系统主要是用于控制送料卷轮的自动供料,它既能减轻人的工作强度,又能自动准确的到达人所不能到达或很难到达的预定位置。
系统中有两个饲料仓,可以存储两种不同的饲料,可以根据不同的需要,分别传送饲料到两个仓。
两个仓的饲料可以根据需求,进行出料混合,混合的比例可以根据实际情况,在触摸屏设定出料阀数值,从而控制出料阀的打开以及打开大小。
通过触摸屏,可以对自动供料系统进行运行监控、出料阀控制、故障报警、电机控制等操作。
2.2 系统控制要求自动送料系统基本要求是:(1)两个饲料仓,可以存储两种不同的饲料,可以根据不同的需要,分别传送饲料到两个仓;(2)每个仓分别有5个出料阀,其中三个出料阀固定出料的多少,另外两个需要利用触摸屏设定;(3)两个仓的饲料根据需求,进行出料混合,在触摸屏控制出料阀打开或关闭;(4)通过触摸屏监控系统运行状态;(5)触摸屏可以控制与监控进仓、出仓的工作状态;(6)要有完善的报警功能,包括尾轮报警、电机报警等。
3 设备选型主要硬件配置表:3.1 PLC选型可编程控制器选用三菱FX2N系列继电器输出型PLC,FX系列PLC的工作电源可以用交流220V电源,也可用直流24V电源,它具有抗干扰能力强,可靠性高等特点,可长期在恶劣的工业环境下工作。
而PLC主要分为三种形式,一为继电器型,这种形式的输出口是继电器驱动,能进行交直流控制,但反应速度慢,不能处理高速数据;二为晶体管型,这种形式的输出口是晶体管驱动,只能进行直流控制,反应速度是三种方式中最快,能处理高速数据;三为晶闸管型,输出口是晶闸管驱动,只能进行交流控制,反应速度中等,能处理一些高速数据;综合系统要求,选用继电器型PLC,型号规格为FX2N-48MR,已可以满足系统的需求。
3.2 触摸屏选型触摸屏选用步科的MT4300C。
MT4300系列人机界面产品采用32位RISC CPU和精简的LINUX内核,能显示各种真彩图形格式,其出众的处理速度和丰富的软件功能可以满足大多数用户的需要。
支持与绝大多数的PLC直接通信,能够轻松实现与其所连设备之间的数据交换。
MT4300C系列拥有直接在线模拟、间接在线模拟、大容量用户组态程序存储空间、与标准C语言兼容的宏指令等贴合客户需求的功能,能迅速有效地完成现场数据采集、运算、控制等功能。
产品特点:1、65536色TFT真彩显示,支持BMP、JPG、GIF等格式的图片导入;2、高性能32位400MHz RISC CPU,快速处理能力保障更高的工作效率;3、4.3〞至12.1〞多种显示尺寸;4、MT4000E系列配置10M/100M自适应以太网接口;5、集成1USB Slave及1个DB15/DB25打印机接口;6、强大的EV5000组态软件功能,支持C语言宏脚本;3.3其他模块3.3.1扩展模块选用PLC扩展模块选用FX2N-16EX。
三菱FX2N-16EX是三菱电机公司推出的一款FX2n系列PLC数字量输入模块,通过扩展电缆与PLC主机相连。
它拥有高速、高级的功能、逻辑选件以及定位控制等特点,FX2N-16EX是从16到256路输入/输出的多种应用的选择方案,最大范围的包容了标准特点、程式执行更快、全面补充了通信功能、适合世界各国不同的电源以及满足单个需要的大量特殊功能模块,可以为工厂自动化应用提供最大的灵活性和控制能力。
由于系统需要,为了满足控制系统的I/O端口数量要求,我们需要通过扩展模块来实现端口数量的扩充。
3.3.2特殊功能模块选用特殊功能模块选用FX2N-4DA。
三菱FX2N-4DA是一款模拟量模块。
首先给大家介绍一下模拟量模块的工作原理。
模拟量模块是将压力、液位、温度等信号转化为 1-5V,4-20mA(也有别的信号的,如0-10V,0-5V等)然后交给PLC进行处理的。
PLC是不知道具体电压或者电流信号的大小的。
所以,我们要用一个数字来表示它的大小,然后告诉PLC,PLC才能知道输入的电压、电流信号具体有多大。
数字量输入输出信号就是开关量信号,1或者0。
模拟量信号有2种,电压或者电流信号,一般是变送器传过来的信号,比如用压力变送器检测水管压力,它会输出一个模拟信号4--20ma或者0-10V的信号给PLC,PLC来进行数据处理。
三菱FX2N-4DA有4个输出通道。
提供了12位高精度分辨率的数字输入。
转换速度为2.1ms/4通道,使用的通道数变化不会改变转换速度。
输出的形式可为电压,也可为电流。
其选择取决于接线不同。
电压输出时,两个模拟输出通道输出信号为0~10V DC,0~5V DC;电流输出时为4~20mA DC。
分辨率为2.5mV(0~10V DC)和4uA(4~20mA)。
数字到模拟的转换特性可进行调整。
本模块需占用8个I/O 点。
根据系统要求,每个仓分别有两个出料阀需要通过模拟量来进行输出,所以我们需要4个输出通道,因此选用三菱FX2N-4DA。
3.3.3功能扩展模块选用功能扩展块选用FX2N-485-BD。
FX2N-485-BD功能概述:FX2N功能扩展板FX2N-485-BD,RS485串行通信扩展板,1通道。
在FX系列中,使用功能扩展板可以轻松地追加各种通信功能。
通过追加功能扩展板,便于实现数据链接以及与外部串行接口设备的通信。
4 控制设计4.1 根据控制控制要求,做出 PLC输入、输出点分配,具体如下表1 表1 输入点和输出点分配表4.4 系统控制原理系统由8台电机组成,自动运行工作模式下,由G095(黑色字体)先开机送料,当G095尾轮检测到有物料到达后,G096启动送料,当G096尾轮检测到有物料到达后,G097进行提升,当G097尾轮检测到有物料到达后。
根据1#和2#仓的选择情况,如果是选择1号,则电机G098、G099均不动作,1#仓门打开,如果选择的是2号,则电机G098先动作,G098尾轮检测到有物料到达后,G099打开,同时2#仓门打开。
出料时,1仓门和2仓门分别有5个出料口,其中每5个出料口分别有2个模拟量及3个开关量。
模拟量可控制出口的大小从面控制出料量。
开关直接控制出料口的关闭。
当时选择出料后,出料口相应的电机输送(1#是G100,2#是G101),尾轮检测到物料后,打开下一台电机,最终由G102出料.安全保护:1、任一台电机启动后一定时间,尾轮检测不到物料,均进行报警,直接在触摸屏上显示。
2、联锁模式下,所有电机按照先后顺序(G095-G096-G097-G098-G099)(G100-G101-G012)的顺序启停。
解锁模式下,所有电机均可自由启停。
4.5 系统PLC梯形图程序(附图)5 调试设计完成后,经过调试,程序运行中出现了触摸屏出错、电机运行故障报警等问题,经过请教同行及相关的专家,已解决问题,程序可以良好的运行工作。
6 结束语在设计过程中,遇到很多问题,经过各方面的修改和调试,该系统现已可使用。
该系统可运用于饲料厂的自动供料,使用方便,工作可靠,具有较好的控制效果。
系统采用触摸屏控制,可以对自动供料系统进行运行监控、出料阀控制、故障报警、电机控制等操作。
根据不同要求自动调节出料阀,调节混料比例,控制精度高,能保证供料混合稳定。
综上所述,采用PLC和触摸屏为核心部件构成的自动供料系统,具有很强的实用性,整个系统自动化程度高,不需人员职守,故障时可以自动保护并发出报警信号。
为供料领域的技术革新,开辟了切实有效的途径。
系统采用PLC控制,容易随时修改程序,以改变工作状况,满足不同控制要求,有较大的灵活性和通用性,有一定的推广应用价值。
参考文献:[1]廖常初编著.可编程序控制器应用技术(第三版).重庆:重庆大学出版社,2000[2]廖常初.PLC基础及应用.北京:机械工业出版社,2003:57~64[3]梁耀光、余文烋主编《电工新技术教程》北京:中国劳动社会保障出版社,2007[4]吴明亮. 《可编程序控制器实训教程》化学工业出版社. 2005[5]王永华等编.现代电气控制及PLC应用技术.北京:北京航空航天大学出版社,2003.9[6]MITSUISHI 人机界面图像数据显示操作终端 GOT. DU系列产品样本作者简介:本人林世平,中共党员,本科学历,1997年11月被评为电气讲师,2010年1月获得维修电工高级技师资格,1983年7月参加工作,从事电工与仪表自动化工作,1992年1月至2009年1月在技工学校任教,2009年1月至今在湛江机电学校任教,在学校中一直从事电工与电子课程教学任务。