铸造一体化桥壳的潮模砂工艺开发
潮模砂铸钢工艺流程
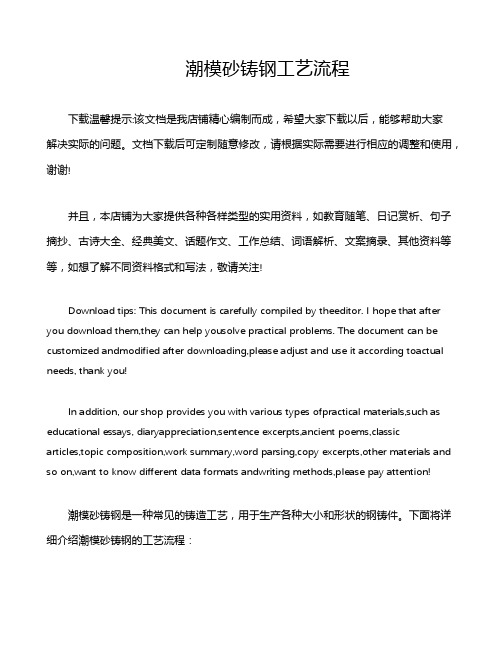
潮模砂铸钢工艺流程下载温馨提示:该文档是我店铺精心编制而成,希望大家下载以后,能够帮助大家解决实际的问题。
文档下载后可定制随意修改,请根据实际需要进行相应的调整和使用,谢谢!并且,本店铺为大家提供各种各样类型的实用资料,如教育随笔、日记赏析、句子摘抄、古诗大全、经典美文、话题作文、工作总结、词语解析、文案摘录、其他资料等等,如想了解不同资料格式和写法,敬请关注!Download tips: This document is carefully compiled by theeditor. I hope that after you download them,they can help yousolve practical problems. The document can be customized andmodified after downloading,please adjust and use it according toactual needs, thank you!In addition, our shop provides you with various types ofpractical materials,such as educational essays, diaryappreciation,sentence excerpts,ancient poems,classicarticles,topic composition,work summary,word parsing,copy excerpts,other materials and so on,want to know different data formats andwriting methods,please pay attention!潮模砂铸钢是一种常见的铸造工艺,用于生产各种大小和形状的钢铸件。
下面将详细介绍潮模砂铸钢的工艺流程:1. 设计模型:首先根据产品的设计要求,制作出相应的模型。
潮模砂铸造工艺介绍课件
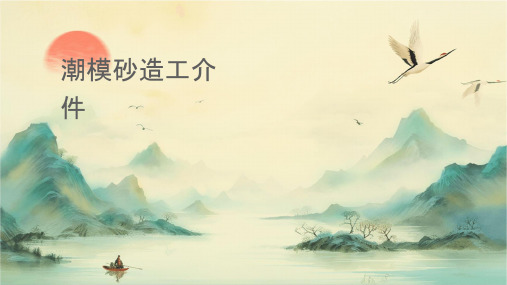
制定详细的检验规范,明确检验 项目、检验方法、判定依据等内 容,以确保铸件质量稳定可靠。
05
潮模砂造工案例析
案例一:某复杂铸件的生产过程
总结词
工艺流程复杂,需精确控制各个环节
详细描述
该复杂铸件的生产过程涉及多道工序,包括模具制作、砂型制作、浇注、冷却和清理等。 由于铸件结构复杂,对模具设计和制作要求极高,需确保模具精度和稳定性。同时,在 砂型制作过程中,需严格控制砂型强度和紧实度,以确保铸件尺寸精度和表面质量。浇 注和冷却过程需精确控制温度和时间,防止出现缩孔、气孔等缺陷。
浇口设计
根据铸造产品的特点和要求,设计合适的浇口形式和尺寸,以确保金属液能够顺利流入模具型腔。
溢流槽设计
在浇注系统中设置溢流槽,以收集多余的金属液,防止金属液溢出模具型腔。
熔炼与浇注参数控制
熔炼温度
控制金属液的熔炼温度,以保证金属液的纯净度和流动性。
浇注温度
控制金属液的浇注温度,以保证金属液在浇注过程中不出现凝固和夹渣等缺陷。
冷却速度与时间控制
冷却速度
通过调整冷却水的流量和温度,控制模 具的冷却速度,以获得符合要求的铸造 产品。
VS
冷却时间
根据铸造产品的特点和要求,合理设置冷 却时间,以保证铸造产品能够充分冷却并 获得良好的机械性能。
04
潮模砂造工
铸造缺陷及其预防措施
气孔
气孔是由于潮模砂铸造过程中气 体未完全排出而形成的缺陷。 预 防措施包括优化模具设计、控制
发展
近年来,随着环保要求的提高, 潮模砂铸造工艺在技术上不断改 进,提高了生产效率和环保性能。
应用领域
01
02
03
04
汽车工业
潮模砂砂处理工艺研究

潮模砂砂处理工艺研究摘要:用粘土作为粘结剂造型生产铸件,是历史悠久的工艺方法,也是应用范围最广的铸造工艺方法。
在各种化学粘结砂蓬勃发展的今天,粘土湿型砂的地位仍是其他造型材料无法比拟的。
近年来我国在砂处理设备在研制、开发及实际应用等方面有了长足的进步,特别是大量国外先进设备的引进,使砂处理工部产生了革命性的变化。
本文就在潍柴现有设备基础上通过工艺流程和质量控制两方面入手研究,探讨适合现阶段符合现代先进水平的潮膜砂砂处理工艺,为砂处理工作顺利的展开提供一定的借鉴。
潍柴是具有60年悠久历史的大型柴油机生产企业,各种先进设备的发展在潍柴得到了很好的见证,潍柴新建铸造工业园采用了世界较为先进设备,其中砂处理系统中引进了如高效双转子混砂机、机电一体化自动测温、比例增湿双盘冷却器等先进设备。
随着装备水平的不断提高,在改善了工作环境及工作效率的同时,也使粘土湿型砂面临许多新的问题,这也促使我们还需对粘土湿型砂的研究不断加强、认识不断深化.从这方面出发,基于先进砂处理系统,从生产实际出发在保证型砂性能的同时兼顾成本,通过试验新工艺及控制要点,降低铸件因型砂造成的废品率,提高铸件产品品质,响应企业号召树立良好的品牌形象。
借助先进砂处理设备的应用,通过实践研究新的砂处理工艺及控制要点,从原材料选择,工艺参数等方面入手,改善型砂性能,降低铸件因型砂问题造成的废品率。
一、砂处理工艺流程控制砂处理在我厂一直以来是制约造型线生产效率的主要原因,如何使用先进的设备混制出高性能的型砂是目前面对的主要问题,由于现代化高效率高可靠斗式提升机的系列定型、供货,使砂处理工部布局产生了革命性的变化-—塔式布置。
不仅省去了大量无效水平输送的皮带机,尤其工艺设备可以直接衔接,总体布局紧凑、工艺过程更合理.工艺流程图:1、旧砂工艺处理单元落砂滚筒或落砂机排出的湿热旧砂落在皮带上,由地坑爬出地面后进行悬挂磁选和皮带机磁选头轮二道磁选,随即由高效斗提机提升至第一塔;进入上部的大端进料精细破碎六角筛,筛孔5—6mm,筛出旧砂中直径≥3mm礓子砂豆,并保证旧砂回收率≥99%。
潮模砂铸造工艺介绍PPT课件

•Page 8
5.一次清理(去除浇冒口)
落砂后的铸件 转运至清理采 用锤击或液压 钳进行分离
落砂后的铸件需对浇注系统进行分离。 铸铁件采用锤击或浇冒口分离器进行分离。 铸钢件采用气割方式去除浇冒口。
•Page 9
6.抛丸精整
抛丸后的铸件进行表面打磨修整
根据铸件大小采用吊钩或履带式抛丸机对铸件进行抛丸清理。 粗抛后去除铸件表面的砂粒。 精整对铸件表面残留进行打磨和修整。
模具
型板或外模 芯盒
机械加工
入库
混砂
熔化
造型
合箱浇注
制芯
下芯
刷漆
检验
精整
落砂
去 除 浇 冒 口
抛丸清理
•Page 4
流程详介
1.工装模具准备
根据接收或PLM上的产品图工艺员绘制工艺,工艺审核批准后下发 至木模车间制作模具。(重点产品安装制作金属工装) 对制作的外模及芯盒进行尺寸划线检查。 根据需要工艺员安排以零活或上型板的方式进行工艺试制。 工艺验证合格后模具入库。
注控制系统
中频感应电炉熔化。配备热电偶测温及光谱分析仪,控制合格铁水
温度及化学成分。
浇注方式为手工浇注和浇注机浇注两种。
•Page 7
4.落砂
振动落砂床落砂
滚筒落砂
铸件的落砂在振动落砂床上进行落砂,新园区小件线则采用滚筒落 砂的方式进行。
落砂后的铸件采用叉车转用或通过鳞板输送机运输至清理车间进行 一次清理(去除浇冒口)。
潮模砂铸造工艺介绍
•Page 1
2012.06.15
提纲
☆铸造工艺流程 ☆铸造基本知识
•Page 2
一、铸造工艺流程
工装模具准备流程
一体化铸钢桥壳铸造及热处理工艺优化

一体化铸钢桥壳铸造及热处理工艺优化汽车的驱动桥壳是汽车上的关键部件,具有承载汽车自重与传递载荷的重要作用,桥壳质量的好坏直接影响汽车的安全性能与使用寿命。
随着近年来我国汽车行业的迅猛发展,对高质量高可靠性驱动桥壳的需求量越来越大,现有桥壳的性能已经不能满足重型商用车的实际使用需求,因此亟需一款工艺简单、成本低廉的高强度桥壳来满足市场需求。
本文正是基于市场需求,旨在开发一种性能优良、成本低廉、专门用于生产整体铸造桥壳的高强度铸钢新材料,以及高质量低污染的桥壳绿色精铸成型技术和配套的热处理工艺。
本文通过查阅和研究不同合金元素对钢组织与性能的影响,设计出一款以碳、硅、锰、铬合金元素为主,同时添加RE、Ti、B等微量元素的低合金高强铸钢,其牌号为ZG27Mn2Si2Cr B。
本文通过计算机模拟仿真技术来设计与优化铸造工艺,在保证铸件成型质量的同时,缩短产品试制周期,从而降低生产成本。
我们模拟出桥壳铸型内金属液的流动状态和规律、铸造过程的热量传递和温度梯度变化、铸件与铸型间的界面换热状况及相互作用等,根据模拟结果可以直观、科学的分析铸造充型、凝固规律和铸造缺陷形成机理,从而确定与优化具体工艺参数,实现科学预测与优化生产,达到优质、高效、低耗、清洁的目标。
本文为了更加精准的制订热处理工艺,使用Gleeble3800热模拟试验机对试验钢的动态CCT曲线进行了绘制。
通过分析试验钢的动态CCT曲线我们可以发现,试验钢贝氏体转变平台较宽,且淬透性良好,可以在较低冷却速度下获得贝氏体和马氏体。
随后本文探讨了ZG27Mn2Si2Cr B的热处理工艺参数,首先确定以退火态为初始态进行热处理试验。
试验钢经退火预处理后,分别加热至815℃(亚温处理)和900℃(全奥氏体化处理)进行保温,随后以不同冷却速度冷却并在不同温度回火,结果发现试验钢经815℃两相区处理后性能较差,不能达到设计标准,这是因为试验钢铁素体的形貌与分布恶化了试验钢性能;经过900℃处理的试验钢性能更加优良。
壳型铸造工艺及装备研发生产方案(一)

壳型铸造工艺及装备研发生产方案一、实施背景随着制造业的不断发展,高效、环保、节能已成为铸造行业的重要发展方向。
壳型铸造工艺作为一种先进的铸造技术,具有较高的生产效率、较低的能耗和良好的产品质量,因此受到广泛关注。
然而,国内壳型铸造工艺及装备研发生产方面仍存在一定的问题,如技术水平不高、生产效率低下、产品质量不稳定等,难以满足市场需求。
因此,开展壳型铸造工艺及装备研发生产具有重要的现实意义和市场需求。
二、工作原理壳型铸造工艺是一种利用覆膜砂或其他类似材料制成的壳型进行浇铸的工艺方法。
其主要工作原理包括以下几个方面:1.覆膜砂制壳:利用覆膜砂材料,通过喷射、流化等手段制成具有一定厚度的壳型,其内部为空心结构。
2.熔融金属浇铸:将熔融的金属液体通过浇口注入到壳型中,待金属液体冷却凝固后形成铸件。
3.脱壳、清理:经过一定时间的冷却后,打开壳型,取出铸件,进行表面清理及处理。
三、实施计划步骤1.需求分析:对市场需求进行调研,明确产品类型、规格、质量要求等。
2.技术研究:开展覆膜砂材料、制壳技术、熔融金属浇铸技术等方面的技术研究。
3.装备设计:根据实际需要,设计相应的制壳设备、浇铸设备等。
4.生产调试:对所研发的设备进行调试,确保其正常运行并逐步优化生产工艺。
5.批量生产:在确保产品质量和稳定性的前提下,逐步扩大生产规模,实现批量生产。
四、适用范围壳型铸造工艺及装备适用于各种大中小型铸件的生产,尤其适用于复杂形状、高精度要求的铸件。
在汽车、航空航天、船舶、机械制造等领域得到广泛应用。
五、创新要点1.采用新型覆膜砂材料:通过选用高性能的覆膜砂材料,提高壳型强度和耐高温性能,从而提高产品质量和生产效率。
2.制壳工艺优化:改进制壳工艺流程,实现自动化、智能化制壳,降低劳动强度,提高生产效率。
3.熔融金属高效浇铸:研究高效浇铸技术,提高金属熔融温度和浇注速度,减少能源消耗和废品率。
4.集成化装备设计:将制壳、浇铸、脱壳等工艺流程集成在一台或多台设备上,实现流水线生产,提高生产效率。
离强度一体化铸造桥秦的霈发

作者简介: 王建东 (!4'46&4Y) , 吉林白城人, 毕业于吉林工学院铸 造工艺及设备专业, 高级工程师, 主要从事铸铁缸体、 缸盖、 桥壳、 曲轴等汽车铸件的工艺研究工作。
图 ! 驱动桥壳 O7B6! MP7W79B ?NSD
!"!" # $ 现代铸铁
林
!"#"$%&'"() %* +,-./0)1"(-). 2()"-13)"4 536) 78$" +%96,(;<=0 >7?9:@A9B, ;<=0 C+D9B:B?9B, 0<E 0F?9B:GFA, HIJ K?7:LD9B, ;<=0 MA9B:NF, .< H79 (O7P8Q <FQA-AR7SD OAF9@PT CA6UHQ@6, C+?9BV+F9 !%&&!!, C+79?) :;6)13<): /+D VS?887L7V?Q7A9 ?9@ 8QPFVQFPD AL 79QDBP?QD@ @P7WD ?NSD +AF879B XDPD 79QPA@FVD@6 K7B+YZDPLAP-?9VD 79QDBP?QD@ V?8Q ?NSD ZPA@FVQ7A9 ZPAVD88 X?8 @D8VP7RD@ ?8 LASSAX8: PD879 8?9@ -AS@79B, VAPD -?G79B ?9@ A9D QTZD X7Q+ QXA Z7DVD86 <VVAP@79B QA Q+D SAX ZPA@FVD@ P?QD @78?@W?9Q?BD8 AL AP7B79?S ZPAVD88, DNAQ+DP-7V P78DP X?8 F8D@, -A@DS79B @7LL7VFSQ7D8 X?8 PD@FVD@ ?9@ 87@D P78DP X?8 V?9VDSSD@6 /+D8D ?@5F8Q-D9Q8 -?GD Q+D ZPAVD88 T7DS@ 79VPD?8D@ LPA- '&(,'*( QA AWDP *&(6 /A PD@FVD V?8Q79B @DLAP-?Q7A9, ZAFP79B X?8 ZDPLAP-D@ % +AFP8 ?LQDP 8QP7ZZ79B ?9@ 8+?GD AFQ X?8 ZDPLAP-D@ , +AFP8 ?LQDP ZAFP79B6 /+D @DLAP-?Q7A9 PD@FVD@ QA SD88 Q+?9 ! -- RT Q+D8D -D?8FPD86 /A PD@FVD V?8Q79B VAPD 8+7LQ, AX9 @D87B9D@ ?9@ -?9FL?VQFPD@ %YS79GD@ .!$ V+?ZSDQ X?8 F8D@ 798QD?@ AL AP7B79?S ." ?9@ .!& V+?ZSDQ6 /+D VAPD 8+7LQ 78 SD88 Q+?9 ! -- RT Q+78 7-ZPAWD-D9Q6 ="> ?%146: @FVQ7SD 7PA9; 79QDBP?QD@ V?8Q ?NSD; DNAQ+DP-7V P78DP; @DLDVQ8
潮模砂流水线生产球墨铸铁桥壳铸造工艺开发

潮模砂流水线生产球墨铸铁桥壳铸造工艺开发宋波;曹月山;侯广怀;曹恒成【摘要】介绍了载货汽车AC16桥壳的结构特点,设计了合理的适合潮模砂流水线生产的浇注系统、补缩工艺及优化的砂芯结构,实现了质量稳定、一致性好、效率高及成本低的目标。
【期刊名称】《金属加工:热加工》【年(卷),期】2016(000)011【总页数】3页(P46-47,48)【关键词】铸造桥壳;潮模砂;铸造工艺【作者】宋波;曹月山;侯广怀;曹恒成【作者单位】中国重汽济南铸锻中心;中国重汽济南铸锻中心;中国重汽济南铸锻中心;中国重汽济南铸锻中心【正文语种】中文桥壳是车桥安装主减速器、差速器、半轴及轮的装配基体,是重型汽车的关键零部件之一。
我公司铸造桥壳原采用简易树脂砂线生产,存在着效率低、劳动强度大,毛坯表面质量差,以及尺寸一致性差等问题。
2010年投资建设桥壳潮模砂生产线,该生产线采用HWS静压线;配有型砂质量在线检测系统的爱立许强力混砂机;DISA精抛机和悬链式水帘喷漆、烤漆线;配备两台C1210机械手用于去除浇冒口,两台160L冷芯机、砂芯存储立体库,带电磁桥式起重机与电磁配秤自动称量加料车的15t/h中频感应电炉、浇注机,以及自动取芯、下芯机。
该线生产HC和AC系列载货汽车铸造桥壳,本文重点介绍AC桥铸造桥壳潮模砂铸造工艺开发的特点及经验,与大家分享。
国内现有很多种球墨铸铁桥壳潮模砂铸造工艺,有采用暗冒口无冷铁工艺、暗冒口加冷铁工艺,也有采用保温冒口或保温冒口加冷铁工艺等。
AC16桥壳产品结构如图1所示,重约190kg,轮廓尺寸为1558mm×419mm×276mm,材质为ZQQT-1,要求本体性能强度和伸长率高。
该桥壳轴头为一段式结构,装配简单、牢固。
为减轻桥壳重量,板簧座两侧设计了减重空腔。
这种桥壳结构的特殊性为铸件工艺设计带来很大难度,板簧座截面清晰地显示(见图2),掏空结构将板簧座的热节分散在不集中的位置,且掏空位置需要设置砂芯,这决定了冒口无法设置在最佳补缩位置。
- 1、下载文档前请自行甄别文档内容的完整性,平台不提供额外的编辑、内容补充、找答案等附加服务。
- 2、"仅部分预览"的文档,不可在线预览部分如存在完整性等问题,可反馈申请退款(可完整预览的文档不适用该条件!)。
- 3、如文档侵犯您的权益,请联系客服反馈,我们会尽快为您处理(人工客服工作时间:9:00-18:30)。
20510.16638/ki.1671-7988.2018.15.076铸造一体化桥壳的潮模砂工艺开发白利权(陕西金鼎铸造有限公司,陕西 宝鸡 722408)摘 要:轴头和桥壳一体化的零件结构以及高性能QT600-7的材质要求,熔炼采用冲入法进行球化、孕育处理,造型采用潮模砂工艺在1950*1200*400/350砂箱中对角布置进行开发,并将开发过程中遇到的各种问题逐一采取措施进行攻关改进,得到了稳定生产。
关键词:铸造一体化桥壳;QT600-7;保温冒口;型砂;砂芯中图分类号:TG24 文献标识码:A 文章编号:1671-7988(2018)15-205-04Development of an integrated axle housing with QT600-7 material by meansof plunge method and tidal sand processBai Liquan( Shananxi jinding casting limited company, Shaanxi Baoji 722408 )Abstract: The structure of the axle head and axle housing is integrated and the material requirements of high performance QT600-7, The smelting process is spheroidization and inoculation. The model is used to develop the diagonal layout of the 1950*1200*400/350 sand box, and the problems encountered in the development process are taken one by one to carry out the improvement and get the stable production.Keywords: Casting integrated axle housing; QT600-7; insulating riser; molding sand and core CLC NO.: TG24 Document Code: A Article ID: 1671-7988(2018)15-205-041 开发的背景随着国家环保政策的实施以及运输道路政策及油价上涨等因素的影响,作为货物主要运输工具之一,同等使用条件下重卡的轻量化已成为用户追求利润最大化的基本要求之一。
卡车铸件已逐渐由原来的粗、笨、重向轻、便、巧转变,零部件的一体化设计成为重卡行业研究发展的对象,一体化桥壳的开发,就体现了这一点,同时相比冲焊桥壳,一体化桥壳成本降低了约300元/根。
2 铸件基本描述铸件材质QT600-7,尺寸为*×*×*,最小壁厚为7(+2.5,-0.5)mm (桥包处),主壁厚为10.5(0,+3),铸件重量*Kg ,产品结构如下图:图1 产品结构图3 铸态QT600-7材质的开发材质的选型:相比国标QT600-3,采用铸态更高强韧性的QT600-7,保证桥壳具有良好的疲劳强度、可靠性,同时作者简介:白利权(1975-),男,助理工程师,在职 MBA ,从事铸造行业铸造技术及管理工作。
汽车实用技术206 工艺要简单、生产过程要稳定,成本可控,对铸态600-7的批量稳定生产提出了更高要求。
为此,应研究保证石墨球化良好、细小,球化不超过3级,球化率80%以上、石墨大小6级以上、共晶团即石墨数量多;基体为一定比例铁素体+珠光体混合组织,消除碳化物等不利影响,同时不得产生影响桥壳性能的铸造缺陷。
在以下方面做了重点思考:3.1 原材料(面包铁、锰铁、废钢)质量控制、配比设计,低硫、低锰、低杂质采用建邦生铁、纯洁干净一致的冷轧板下脚料,使用少量废钢加增碳剂的熔炼方式,调整炉内铁水,保证低杂质元素含量的原铁水成分。
3.2 化学成分选择控制低S 含量,保证球化良好,控制P 、Mn ,避免因共晶团晶界上的偏析带来的不利影响,合理选择C 、Si 、碳当量,添加铜等合金元素保证得到一定比例的铁素体+珠光体混合组织,克服碳化物、石墨异常等组织缺陷,满足力学性能要求;3.2.1 碳和硅碳和硅是促进石墨化元素,调高碳当量,析出的石墨球数多,石墨球小,可调高石墨圆整度。
随着硅含量的增加,同时高硅会显著降低材料的低温冲击性能,硅脆性体现明显。
在不漂浮的条件下,提高碳当量,同时保证孕育的条件下,尽量降低硅含量。
将C3.6—3.75%,Si2.4—2.6%控制。
3.2.2 锰是促进珠光体的元素但锰的存在容易造成偏析,易造成碳化物,同时过高的锰可满足材质的强度,但会影响材质的韧性。
因此为保证高韧性,将Mn 控制在0.2以内[1];3.2.3 磷、硫在球墨铸铁中是有害元素P 含量高易造成缩孔和磷共晶,影响材质的韧性、塑性,因此必须严格控制P 含量。
S 为反球化元素,降低其含量是为确保球化效果的前提。
为保证高品质的铸件材质可按P <0.04%,S <0.02%控制[1]。
3.3 球化、孕育工艺的考虑原铁液出炉温度、成分,选择铸态专用稀土镁球化剂,确定加入工艺(粒度、加入方式),保证吸收率稳定、高效;考虑到产品的单重、结构、出铁量及生产条件,选用粒度为5-25mm 、含Sb 的珠光态球化剂,充分利用球化剂中的微量的Sb 细化石墨的特性,使用三明治法保证球化爆发稳定。
选择高效复合孕育剂和珠光体专用随流孕育剂,采用多次、瞬时孕育,强化孕育效果;考虑到石墨形态及数量对组织及性能的影响,我们充分利用预处理提高球墨铸铁冶金质量的特性(细化石墨、增加石墨球数、提高球化率、改善铁水流动性、降低缩孔、缩松倾向),多步骤有效的孕育,强化孕育效果,提升组织,改善性能。
复合珠光体形成元素,避免因金属单独添加导致的熔化不均、成分波动较大等不利影响;采用预处理工艺,强化孕育效果,提高共晶团数,细化石墨,改善圆整度。
从以上方面进行考虑后,熔化工艺最终选择为: (1)炉料配比:表1(2)成分控制: (3)过程控制: 1)包内加料顺序及用量:1.5% 球化剂 +*预处理剂 +*铜(堤坝另一侧) 2)孕育处理:*孕育剂(全倒包)+*随流孕育 3)温度控制:出炉温度:1510-1530℃ 浇注温度:1390-1350℃(单包浇注3箱)4 造型工艺设计[3](1)铸造缩尺的制定:根据球铁件金属工装缩尺选择原则,缩尺选择0.9%,同时借鉴以前类似桥壳的经验,在局部难于收缩的位置给于局部补正处理;(2)加工余量的设计:根据产品图纸要求,在装配要求面上给于4-6毫米的加工余量;(3)砂芯芯盒的设计:根据产品结构,冷芯1颗,芯重110.5kg ,尺寸为*mm ×*mm , 芯盒选择150升,具体芯子结构如下图。
图2 芯子结构图(4)浇注系统的设计:根据桥壳的结构以及尺寸预采用均衡凝固大孔出流理论[2]设计加长桥壳浇注系统各参数,具体核算各单元浇注系统尺寸确定如下:白利权:铸造一体化桥壳的潮模砂工艺开发207式中 A 内:内浇道截面积,cm 2μ3:内浇道流量系数 hp: 内浇道平均压头,cm G :金属液重量230 kg t=G 1/2+G 1/3:浇注时间为21s式中的h p 是内浇道平均压头,不单考虑了压头H p 而且考虑了各组元的截面比。
·铸造桥壳浇注重量220 kg ,一型1件,采用中注浇注系统,直浇道Hp=40cm ,铸件高度25cm (内浇道以上铸件高度H C =7.8cm)。
·计算h P·采用中注式,hp=K 22/(1+K 21+ K 22)×H P ·H P =H 0-H C /8=35-7.8/8=34·k 1=(u 1A 1)/ (u 2A 2) =(0.6×1)/(0.6×2) =0.5 ·k 2=(u 1A 1)/ (u 3A 3) =(0.6×1)/(0.55×1.5) =0.73 ·μ1=0.6, μ2=0.6, μ3=0.55·A 直:A 横:A 内=A 1:A 2:A 3=1:2:1.5 ·按公式计算·hp=K 22/(1+K 21+ K 22)×H P =0.732/(1+0.52+0.732)×34=10.16·μ3取0.55,计算得到A 内=20.2cm 2,A 直=13.5 cm 2,A 横=27 cm 2·计算得到:直浇道直径为Φ42mm ,单侧横浇道为30×45(高) (如下图所示,采用T 型浇道,面积应取0.5 A 横),内浇道共6道进水(单侧各3道),面积为20.2/6=3.4,取宽度68,厚度为5。
初定浇注系统(T 型)图3为更好的杜绝铸件内部夹渣等缺陷,横浇道处单侧各增加面积为100*100的过滤块。
5)型板布置图4图5利用原有1950*1200*400/350的静压造型桥壳线,根据现有资源只能进行对角布局。
5 生产过程出现的问题按照上述工艺组织实施后,铸件出现了如下问题,并采取了相应措施:(1)桥壳上局部独立热节处缩孔,分析后采取保温冒口以及冷铁激冷的办法解决。
(2)桥壳上表面呛火,根据呛火的位置分析为型腔憋气所致,采用最高处扎出气针解决此问题。
通过以上措施实施后:最终造型工艺为:1颗冷芯,5道68*5和2道34*5的进水,7个出气针,对8处孤立热节采用保温冒口予以实施,顶部的排气采用出气针对型腔进行排气解决。
实施后废品率控制在6%以内,生产过程顺畅。
表1图66 检测结果(1)尺寸稳定,能够达到图纸要求范围,并控制在国标CT8范围;(2)成分性能检测结果; (3)台架试验能够达到的数据。
表2汽车实用技术208加长桥壳选用材质为QT600-7,既满足使用性能,又得到了过程稳定的生产。
7 结论(1)加长桥壳用潮模砂生产,紧实度能够满足要求,轮廓、尺寸能够予以保证。
(2)QT600-7用冲入法合金控制在一定范围内,多次孕育,能够达到性能要求,并能稳定生产。
(3)用均衡凝固理论设计的桥壳浇注系统充型过程稳定,局部孤立热节采用保温冒口和冷铁予以局部补偿能够保证产品的质量要求,并能稳定生产。
参考文献[1] 陆文华.铸铁及其熔炼[M].西安交通大学.机械工业出版社.[2] 魏兵,袁森,张卫华.铸件均衡凝固技术及其应用[M].北京:机械工业出版社,1988.[3] 王文清,李魁盛,铸造工艺学[M].北京:机械工业出版社,2009.(上接第198页)3.3 预埋件的处理方法仪表台发泡件上一般不能像金属件那样直接使用螺栓、自攻进行装配。