炼化企业吸收稳定系统中影响吸收的操作因素
d第二章 第三节 吸收稳定岗位操作法

第三节吸收稳定岗位操作法操作原则:在稳定四塔(T301、T302、T303、T304)压力情况下,要根据生产方案的要求,保证稳定汽油,液态烃、干气的质量和收率,操作不正常时要及时处理,严防事故扩大,引起超温超压,火灾等事故,发生事故时要沉着冷静,查明原因,正确果断处理。
在操作不平稳情况下,要保证瓦斯压力平衡,严禁瓦斯带油,要保证火炬线畅通。
一、正常操作法:1、干气中C3含量的控制。
干气中C3含量控制≯3%,C3含量高是由吸收塔(T301)吸收效果差而造成的。
影响因素:(1)吸收塔温度高。
(2)富气量过大E202及空冷冷却效果差,造成压缩富气进塔温度高。
(3)吸收剂量不足(即液气比小)或吸收剂温度高。
(4)吸收塔压力过低或波动过大。
(5)解吸塔(T302)温度高,将大量C3、C4组分脱出,增加吸收塔负荷。
(6)仪表失灵。
调节方法:(1)提高两中段回流量或降低中段冷后温度。
(2)提高冷E302冷却效果,降低压缩富气入塔温度,若富气量大,是由冷201冷却效果差造成的,应提高冷却器的冷却效果。
(3)增大补充吸收剂量,提高液气比,调节E301、E302、E202冷却效果,降低吸收剂温度。
(4)适当提高吸收塔压力,并保持平稳。
(5)降低E306出口温度。
(6)仪表改手动或付线控制及时联系仪表处理。
2、吸收塔塔顶压力控制。
提高T301压力有利于吸收,即可降低干气中C3含量,但T301压力受汽压机出口压力额定值限制,塔压超高,会使汽压机飞动,或使T301、T302安全阀跳开,严重时吹扫塔盘,压力太低造成吸收效果不好。
影响因素:(1)富气量大,压力上升,富气中C3以上组分增加,压力上升。
(2)E302冷却效果差,压缩富气温度升高,压力升高。
(3)中段回流量及冷后温度变化。
(4)解吸塔压力变化,解吸塔压力升高,吸收塔压力升高。
(5)瓦斯管网压力过高,干气排不出去,压力升高。
(6)再吸收塔压控失灵。
(7)气压机出口压力变化。
吸收稳定岗位操作法

第一节吸收稳定岗位一、操作要点1.影响吸收塔吸收效果的操作因素主要有操作温度、压力、液气比等。
降低温度对吸收有利,吸收塔的温度受富气进塔温度、吸收油和补充吸收油进塔温度以与各中段回流取热量大小等因素的影响。
提高操作压力有利于吸收过程的进行,但吸收塔的压力已由压缩机的出口压力和压缩富气进吸收塔前的压降所决定,所以一般很少调节,但操作时要注意维持塔压,不使之波动较大。
液气比指吸收剂量(包括粗汽油和补充吸收油)与进塔压缩富气量之比。
加大液气比可以提高吸收率,富气量一定时液气比的大小取决于吸收剂量的多少。
2.解吸塔的操作要点是控制脱乙烷汽油中的C2含量,它是关系到稳定塔顶回流罐排不排不凝气的关键因素之一。
高温低压对解吸有利,由于解吸气还要进入吸收塔,其压力必须比吸收塔压力高0.05MPa 左右。
所以解吸塔的主要操作要求是控制好解吸温度即塔底重沸器的油气出口温度。
3.由于柴油很容易溶解汽油,所以再吸收塔用焦化柴油作为再吸收油吸收贫气中夹带的汽油组分,正常情况下给定了再吸收油流量后不需要经常调节即可满足干气质量要求。
再吸收塔的主要操作要点是控制好塔底液位,防止因液位失控造成干气带油或瓦斯窜入分馏塔4.稳定塔的主要操作因素有[wiki]回流比[/wiki]、压力、塔底温度。
回流比是回流量与产品流量之比。
由于稳定塔顶组成变化很小,从温度上反映不很灵敏,因此不可能通过控制塔顶温度而调节回流量,而是按一定回流比来调节以保证精馏效果,一般回流比为1.7〜2.0。
塔顶压力是以控制液化气中C3、C4完全冷凝为准,也就是使操作压力大于液化气在冷后温度下的饱和蒸气压。
塔顶压力受解吸效果的影响较大,塔顶压力的调节主要取决于冷凝冷却器管束被浸没的面积•(液面上气相中的管束起冷凝冷却的作用,处于液相中的管束只起冷却作用)•而不是取决于通过热旁路的气体流量。
通过控制热旁路调节阀的开度来改变热旁路调节阀的压降,从而改变冷凝冷却崐器管束的浸没面积,从而调节冷凝冷却器的取热量,最终达到控制稳定塔顶压力不变。
吸收稳定操作原则

●吸收稳定操作原则吸收—稳定系统的任务是将来自分馏塔顶粗汽油和富气,通过吸收塔和解吸塔分离成干气和脱乙烷汽油,再通过稳定塔将脱乙烷汽油分离成液态烃和稳定汽油。
对于吸收操作,温度越低、压力越高、吸收剂量越大越有利于吸收;对于解吸操作,温度越高,压力越低越有利于解吸。
吸收和解吸操作又相互影响,要从吸收和解吸整体分离效果来考虑控制各自的操作条件。
吸收过度将增加解吸负荷,解吸过度又会增加吸收负荷,吸收或解吸过度后反而会造成分离效果恶化。
因此必须树立吸收—解吸系统整体操作的思想。
对于稳定塔操作,影响分离精度的主要因素是回流比,在塔底重沸器热源充足和塔顶冷凝品负荷允许的情况下,塔顶回流越大,分离效果越好。
但回流过大,将增加塔底重沸器加热负荷和塔盘的气液相负荷,一旦塔盘气、液相负荷超标后,将出现液泛或雾沫夹带,产品分割度变差。
所以稳定塔操作需要根据进料组成、流量的变化,及时调整塔顶回流量,塔顶温度作为液态烃C5含量控制的关键指标,塔底重沸器出口温度作为稳定汽油10%点控制的关键指标。
正常操作●产品质量控制⑴干气中>C3含量的控制①干气冷后温度高;②吸收剂量不足或吸收剂温度高,吸收效果差(干气中C3含量高);③吸收塔温度高或中段回流取热量少,吸收效果差;④稳定深度不够,补充吸收剂用量过大;⑤吸收塔压力过低或波动大;⑥解吸塔温度过高,大量C3、C4组分过度解吸,增加吸收塔的负荷;⑦不凝气排放。
⑵液态烃C2含量的控制a.影响因素①解吸塔底重沸器出口温度低,解吸效果差;②吸收过度导致解吸塔进料中会有大量C2。
⑶液态烃C5含量的控制a.影响因素①稳定塔顶回汉量小或冷却器效果差,造成塔顶温度高;②稳定塔底重沸器出口温度控制过高;③稳定塔压力低或波动大;④进料位置不同,进料口以上的精馏段塔盘娄目不同,影响精馏效果。
⑤回炼轻汽油后塔盘上液相负荷降低,相当于降低了塔顶回流比;⑥粗汽油流量下降或稳定塔进料中液态烃组分含量上升,液态烃C5含量上升。
石油炼化关键装置的风险因素及合理应对
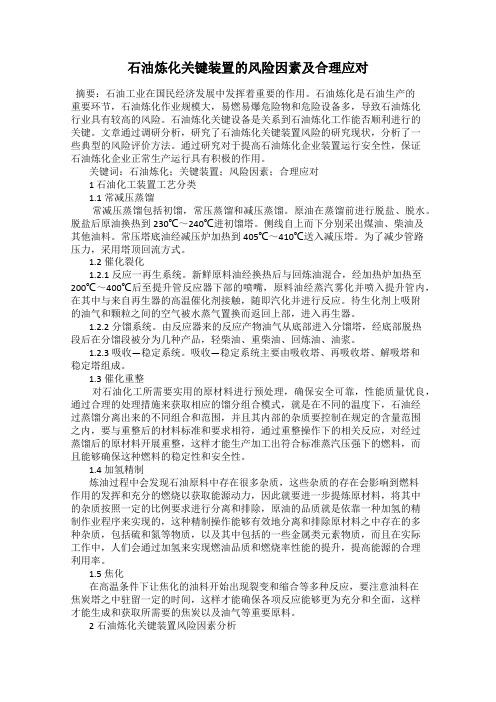
石油炼化关键装置的风险因素及合理应对摘要:石油工业在国民经济发展中发挥着重要的作用。
石油炼化是石油生产的重要环节,石油炼化作业规模大,易燃易爆危险物和危险设备多,导致石油炼化行业具有较高的风险。
石油炼化关键设备是关系到石油炼化工作能否顺利进行的关键。
文章通过调研分析,研究了石油炼化关键装置风险的研究现状,分析了一些典型的风险评价方法。
通过研究对于提高石油炼化企业装置运行安全性,保证石油炼化企业正常生产运行具有积极的作用。
关键词:石油炼化;关键装置;风险因素;合理应对1 石油化工装置工艺分类1.1常减压蒸馏常减压蒸馏包括初馏,常压蒸馏和减压蒸馏。
原油在蒸馏前进行脱盐、脱水。
脱盐后原油换热到230℃~240℃进初馏塔。
侧线自上而下分别采出煤油、柴油及其他油料。
常压塔底油经减压炉加热到405℃~410℃送入减压塔。
为了减少管路压力,采用塔顶回流方式。
1.2催化裂化1.2.1反应一再生系统。
新鲜原料油经换热后与回炼油混合,经加热炉加热至200℃~400℃后至提升管反应器下部的喷嘴,原料油经蒸汽雾化并喷入提升管内,在其中与来自再生器的高温催化剂接触,随即汽化并进行反应。
待生化剂上吸附的油气和颗粒之间的空气被水蒸气置换而返回上部,进入再生器。
1.2.2分馏系统。
由反应器来的反应产物油气从底部进入分馏塔,经底部脱热段后在分馏段被分为几种产品,轻柴油、重柴油、回炼油、油浆。
1.2.3吸收—稳定系统。
吸收—稳定系统主要由吸收塔、再吸收塔、解吸塔和稳定塔组成。
1.3催化重整对石油化工所需要实用的原材料进行预处理,确保安全可靠,性能质量优良,通过合理的处理措施来获取相应的馏分组合模式,就是在不同的温度下,石油经过蒸馏分离出来的不同组合和范围,并且其内部的杂质要控制在规定的含量范围之内,要与重整后的材料标准和要求相符,通过重整操作下的相关反应,对经过蒸馏后的原材料开展重整,这样才能生产加工出符合标准蒸汽压强下的燃料,而且能够确保这种燃料的稳定性和安全性。
浅析吸收稳定系统操作
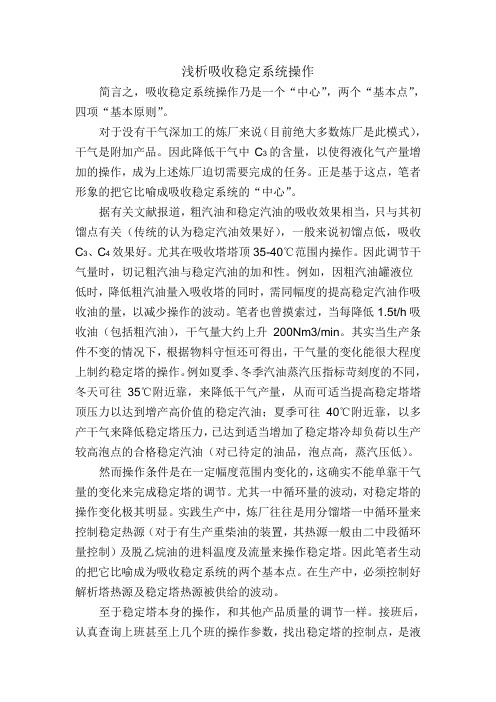
浅析吸收稳定系统操作简言之,吸收稳定系统操作乃是一个“中心”,两个“基本点”,四项“基本原则”。
对于没有干气深加工的炼厂来说(目前绝大多数炼厂是此模式),干气是附加产品。
因此降低干气中C3的含量,以使得液化气产量增加的操作,成为上述炼厂迫切需要完成的任务。
正是基于这点,笔者形象的把它比喻成吸收稳定系统的“中心”。
据有关文献报道,粗汽油和稳定汽油的吸收效果相当,只与其初馏点有关(传统的认为稳定汽油效果好),一般来说初馏点低,吸收C3、C4效果好。
尤其在吸收塔塔顶35-40℃范围内操作。
因此调节干气量时,切记粗汽油与稳定汽油的加和性。
例如,因粗汽油罐液位低时,降低粗汽油量入吸收塔的同时,需同幅度的提高稳定汽油作吸收油的量,以减少操作的波动。
笔者也曾摸索过,当每降低1.5t/h吸收油(包括粗汽油),干气量大约上升200Nm3/min。
其实当生产条件不变的情况下,根据物料守恒还可得出,干气量的变化能很大程度上制约稳定塔的操作。
例如夏季、冬季汽油蒸汽压指标苛刻度的不同,冬天可往35℃附近靠,来降低干气产量,从而可适当提高稳定塔塔顶压力以达到增产高价值的稳定汽油;夏季可往40℃附近靠,以多产干气来降低稳定塔压力,已达到适当增加了稳定塔冷却负荷以生产较高泡点的合格稳定汽油(对已待定的油品,泡点高,蒸汽压低)。
然而操作条件是在一定幅度范围内变化的,这确实不能单靠干气量的变化来完成稳定塔的调节。
尤其一中循环量的波动,对稳定塔的操作变化极其明显。
实践生产中,炼厂往往是用分馏塔一中循环量来控制稳定热源(对于有生产重柴油的装置,其热源一般由二中段循环量控制)及脱乙烷油的进料温度及流量来操作稳定塔。
因此笔者生动的把它比喻成为吸收稳定系统的两个基本点。
在生产中,必须控制好解析塔热源及稳定塔热源被供给的波动。
至于稳定塔本身的操作,和其他产品质量的调节一样。
接班后,认真查询上班甚至上几个班的操作参数,找出稳定塔的控制点,是液化气控制(主要是C5控制,C2一般用回流罐排放不凝气操作就能合格,阀位笔者摸索为0-25%较好),还是稳定汽油控制。
5.6吸收操作分析

影响吸收操作的因素
影响吸收操作的组要因素有气流速度、 喷淋密度、温度、压力、吸收剂的纯度,要 依据影响情况作出合理选择。
喷淋密度:单位时间内,单位塔截在常温常压下进行。 • ②吸收操作是变温过程,当溶解热较大时, 必须移走热量。 • ③黏度及扩散系数影响吸收效率。 • ④解析操作在高温低压下进行。 • ⑤闪蒸过程 闪蒸:就是高压的饱和液体进入比较低压的 容器中后,由于压力的突然降低,使这些饱 和液体变成一部分的容器压力下的饱和蒸汽 和饱和液。
5.7、其他吸收
一、化学吸收
特点:浓度梯度由扩散速率、化学反应速率以及反应物的扩散速率共 同影响。 推动力:反应消耗吸收质,有效溶解度显著增加,平衡分压降低,增
大了吸收过程的推动力。
阻力:部分溶质扩散途中因化学反应而消耗,使过程阻力减少,吸收 系数增大。
二、高组成气体吸收
1、气液两相的摩尔流量沿塔高有较大的变化。 2、吸收过程有显著的热效应。 3、吸收系数不是常数。
吸收塔的操作和条件
1、吸收操作要点 ①减少起控制作用的阻力。 ②选择有较高吸收速率的塔设备。 ③注意流量的稳定。 ④掌握好气体的流速。 ⑤经常检查出口气体的雾沫夹带情况。 ⑥经常检查塔内的操作稳定 ⑦及时清洗填料
2、吸收塔的调节 调节手段只能是改变吸收剂的入口条件, 包括流量、温度、组成三大要素。 增大吸收剂用量,降低吸收剂温度,降 低吸收剂入口的溶质浓度都能增大全塔的平 均推动力,但将受到再生操作的制约,应同 时考虑再生设备的能力。
三、多组分吸收
-----两个以上的组份被吸收剂吸收。
特点:组份间相互影响,复杂;均符合亨利定律;稀溶液;关键组分
四、解吸
①目的:获得所需较纯的气体溶质;使溶剂 再生,循环利用 ②推动力:与吸收相反 ③工业上
吸收稳定操作原则

●吸收稳定操作原则吸收—稳定系统的任务是将来自分馏塔顶粗汽油和富气,通过吸收塔和解吸塔分离成干气和脱乙烷汽油,再通过稳定塔将脱乙烷汽油分离成液态烃和稳定汽油。
对于吸收操作,温度越低、压力越高、吸收剂量越大越有利于吸收;对于解吸操作,温度越高,压力越低越有利于解吸。
吸收和解吸操作又相互影响,要从吸收和解吸整体分离效果来考虑控制各自的操作条件。
吸收过度将增加解吸负荷,解吸过度又会增加吸收负荷,吸收或解吸过度后反而会造成分离效果恶化。
因此必须树立吸收—解吸系统整体操作的思想。
对于稳定塔操作,影响分离精度的主要因素是回流比,在塔底重沸器热源充足和塔顶冷凝品负荷允许的情况下,塔顶回流越大,分离效果越好。
但回流过大,将增加塔底重沸器加热负荷和塔盘的气液相负荷,一旦塔盘气、液相负荷超标后,将出现液泛或雾沫夹带,产品分割度变差。
所以稳定塔操作需要根据进料组成、流量的变化,及时调整塔顶回流量,塔顶温度作为液态烃C5含量控制的关键指标,塔底重沸器出口温度作为稳定汽油10%点控制的关键指标。
正常操作●产品质量控制⑴干气中>C3含量的控制①干气冷后温度高;②吸收剂量不足或吸收剂温度高,吸收效果差(干气中C3含量高);③吸收塔温度高或中段回流取热量少,吸收效果差;④稳定深度不够,补充吸收剂用量过大;⑤吸收塔压力过低或波动大;⑥解吸塔温度过高,大量C3、C4组分过度解吸,增加吸收塔的负荷;⑦不凝气排放。
⑵液态烃C2含量的控制a.影响因素①解吸塔底重沸器出口温度低,解吸效果差;②吸收过度导致解吸塔进料中会有大量C2。
⑶液态烃C5含量的控制a.影响因素①稳定塔顶回汉量小或冷却器效果差,造成塔顶温度高;②稳定塔底重沸器出口温度控制过高;③稳定塔压力低或波动大;④进料位置不同,进料口以上的精馏段塔盘娄目不同,影响精馏效果。
⑤回炼轻汽油后塔盘上液相负荷降低,相当于降低了塔顶回流比;⑥粗汽油流量下降或稳定塔进料中液态烃组分含量上升,液态烃C5含量上升。
吸收稳定系统优化操作总结
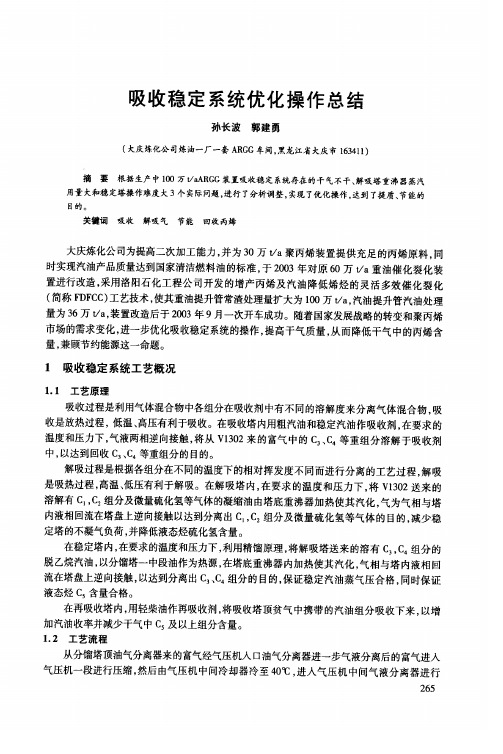
吸收稳定系统优化操作总结孙长波郭建勇(大庆炼化公司炼油一厂一套ARGG车间,黑龙江省大庆市163411)摘要根据生产中100万L/a A R G G装置吸收稳定系统存在的干气不干、解吸塔重沸器蒸汽用量大和稳定塔操作难度大3个实际问题,进行了分析调整,实现了优化操作,达到了提质、节能的目的。
关键词吸收解吸气节能回收丙烯大庆炼化公司为提高二次加工能力,并为30万∥a聚丙烯装置提供充足的丙烯原料,同时实现汽油产品质量达到国家清洁燃料油的标准,于2003年对原60万L/a重油催化裂化装置进行改造,采用洛阳石化工程公司开发的增产丙烯及汽油降低烯烃的灵活多效催化裂化 (简称FDFCC)工艺技术,使其重油提升管常渣处理量扩大为100万∥a,汽油提升管汽油处理量为36万L/a,装置改造后于2003年9月一次开车成功。
随着国家发展战略的转变和聚丙烯市场的需求变化,进一步优化吸收稳定系统的操作,提高干气质量,从而降低干气中的丙烯含量,兼顾节约能源这一命题。
1 吸收稳定系统工艺概况1.1工艺原理吸收过程是利用气体混合物中各组分在吸收剂中有不同的溶解度来分离气体混合物,吸收是放热过程,低温、高压有利于吸收。
在吸收塔内用粗汽油和稳定汽油作吸收剂,在要求的温度和压力下,气液两相逆向接触,将从V1302来的富气中的C,、C。
等重组分溶解于吸收剂中,以达到回收C,、C。
等重组分的目的。
解吸过程是根据各组分在不同的温度下的相对挥发度不同而进行分离的工艺过程,解吸是吸热过程,高温、低压有利于解吸。
在解吸塔内,在要求的温度和压力下,将V1302送来的溶解有C,,C:组分及微量硫化氢等气体的凝缩油由塔底重沸器加热使其汽化,气为气相与塔内液相回流在塔盘上逆向接触以达到分离出C。
,C:组分及微量硫化氢等气体的目的,减少稳定塔的不凝气负荷,并降低液态烃硫化氢含量。
在稳定塔内,在要求的温度和压力下,利用精馏原理,将解吸塔送来的溶有C,,C。
组分的脱乙烷汽油,以分馏塔一中段油作为热源,在塔底重沸器内加热使其汽化,气相与塔内液相回流在塔盘上逆向接触,以达到分离出C,、c。
2022国开化工单元操作形考任务一答案

2022国开化工单元操作形考任务一答案“操作形考”是2020年国开建设考试的一种特殊形式,主要考查知识和技能。
也就是你需要做的题。
“操作形考”在国开建设考试中出现的频率很高,也就是考一些基本知识,如操作流程图、阀门图等。
主要以计算题为主,很多小伙伴不知道如何进行解题。
为此,给大家整理了2022年国开化工单元操作形考一选题参考答案详解,希望对各位小伙伴有所帮助!2020年7月14日:化工装置中的蒸汽管道中如果压力大于1.6 MPa时,首先应将它加热至100℃后再减压;如果低压阀门打开时压力小于1.5 MPa则可能导致局部蒸汽泄漏,因此应立即关闭进风阀门或排出炉内的空气;蒸汽管压力大于1.5 MPa时如果不采取减压措施可能会造成局部蒸汽泄漏并引起局部高温和局部腐蚀;当介质粘度较大时如果不采取减压或在容器内加入一定量的粘稠剂(如乳化剂)可以降低介质粘度以避免局部压力过大进而引发局部燃烧。
根据上述说法,本题所涉及的危险源是()。
1.根据《石油化工装置安全规程》(GB/T14554-2001)的规定,在热、冷设备系统中没有危险气体的介质通常有()。
A.化学物品或热物质;B.可燃气体;C.易燃液体及气体混合液;D.其他可燃或有毒物质;E.高温物质。
B.化学试剂蒸汽; E.高温或过热的蒸汽;F.高压、超高压或温度较高的蒸汽或气体等都属于危险源。
故本题答案为 ABCD。
《石油化工装置安全规程》(GB/T14554-2001)中规定,对于热、冷设备系统中没有危险气体的介质通常有无特殊要求,不应以化学物品、蒸汽或气体为主作为危险源点。
A.气体常压容器 B.真空容器 C.高温管道 D。
解析:上述规定适用于具有危险特性的机械设备及管道等。
2.根据《电气工程施工及验收规范》(GB50181-2008),在电气、仪表、照明装置安装时,应检查灯具位置是否与电源开关、熔断器等相位一致,电缆桥架的水平和垂直距离不应小于1.5 m,电缆必须铺设完毕并且有明显的标记和标识线。
吸收稳定泄压的原因、方式、注意事项

吸收稳定泄压的原因、方式、注意事项吸收稳定泄压相关主题的文章内容没有提示,可能需要对相关知识进行阐述;也可以将其与现实生活中的情境相结合,以便更好地理解这一主题。
不过我会就这个话题提供一些一般性的信息。
一、吸收稳定泄压的原因稳定泄压是指通过某些方式,对于压力较高的系统或设备进行减压的过程。
其原因主要包括以下几点:1. 减少系统内部压力:当系统内部压力超过了其承受范围时,需要通过泄压措施进行稳定,以避免系统破裂或爆炸。
2. 保护设备和人员安全:稳定泄压可以避免由于高压引起的设备损坏或人员伤害,保障生产安全。
3. 控制系统运行:在一些工艺系统中,通过稳定泄压可以控制系统压力,确保系统正常运行。
二、吸收稳定泄压的方式吸收稳定泄压的方式通常包括以下几种:1. 安全阀:安全阀是一种根据压力设定值进行自动启闭的装置,通常会装置在系统的高压侧,当系统压力超过设定值时,安全阀会打开并进行泄压。
2. 压力释放装置:这种装置通常是一种手动操作的泄压系统,当系统压力超过限制时,工作人员可以通过操作该装置进行泄压。
3. 泄压阀:泄压阀是根据系统压力变化自动调节泄压的装置,可以在系统压力过高时自动启动,进行泄压操作。
三、吸收稳定泄压的注意事项在进行吸收稳定泄压时,需要注意以下几点:1. 定期检查和维护泄压设备:安全阀、泄压阀等泄压设备需要定期检查和维护,确保其正常运行。
2. 确保泄压过程的安全性:在进行泄压操作时,需要确保周围人员和设备的安全,避免意外发生。
3. 合理选择泄压装置:根据具体系统的特点,选择合适的泄压装置进行安装和使用,确保其稳定可靠。
总结:吸收稳定泄压是保障系统运行安全的重要措施,通过正确的选择和使用泄压装置,可以有效地减少系统压力过高带来的风险,确保设备和人员的安全。
影响球化剂吸收率和球化稳定性的主要因素

影响球化剂吸收率和球化稳定性的主要因素冲入法处理球铁操作简便,安全可靠,处理铁水量灵活,而且冲入法无须特殊的工艺装备,容易上马,因而被越来越多地用于代替压力加镁法,成为目前应用最广泛的球化处理方法。
冲入法处理流程为:把球化剂(如块度15〜20毫米的稀土镁硅铁)堆放在铁水包一侧,稍加紧实,并根据铁水出炉温度不同加不同的覆盖剂(如硅铁粉、铁屑、铁板等),铁水包装载后预热至暗红色,将铁水包的另一侧对向出铁槽,球化示意图见图1。
球化处理时先出所需铁水总量的60%^75%待铁水与球化剂反应的翻腾基本结束后,再出余量铁水,同时冲入孕育剂,作孕育处理,然后搅拌、扒渣、浇注。
图1冲入法球化示意图1.铁水包2.球化剂3.覆盖剂对于处理少量铁水,可一次出完并作孕育处理,效果更好,温度损失也少。
冲入法球化工艺要保证铁水中残留适当含量的镁和稀土,并使二者有合适的比例,这是保证球化的必要条件。
铁水中残留镁量与稀土量的比例主要依靠球化剂中镁和稀土的比例来保证。
球化元素残留量的绝对值则取决于球化剂的加入量和吸收率。
在冲入法球化处理时,球化元素的主要损耗是氧化烧损和脱硫损耗。
影响球化剂吸收率和球化稳定性的主要因素如下:一、原铁水含硫量的影响原铁水含硫量越高,消耗在脱硫上的球化剂越多。
因此球化剂加入量必须随铁水含硫量增高而加大。
对于含Mg 8%〜10% Si 35%-40%勺稀土镁硅铁,在1380c〜1450c处理,对壁厚100毫米以下铸件,球化剂加入量与含硫量关系见表1。
表1 稀土镁硅铁加入量与原铁水含硫量的关系原铁水含硫量(衿<0.03 0.03〜0.05 0.05〜0.07 0.07〜0.10球化剂加入量(衿0.6〜0.8 0.8〜1.1 1.1〜1.3 1.3〜1.6二、处理温度的影响铁水温度是影响稀土镁硅铁冲入法处理球墨铸铁质量的一个重要因素。
由于球化剂、覆盖剂以及孕育剂的熔化需要耗费大量热量,使整个冲入法处理过程中铁水温度下降较大,1吨〜2吨包降低50c〜100C,大型浇包降温较少。
煤气净化回收工题库带答案

煤气净化回收工题库带答案一、单选题1.下列选项中,(B)会造成换热器出口超温。
A.冷剂量增大B.冷剂量减小C.进口冷剂温度下降D.被冷物料进口温度下降2.润滑油温度对油膜的影响是(B)。
A.温度高油膜层厚B.温度低油膜层厚C.温度对油膜层无影响D.温度高形成油膜的时间多3.下列不能提高对流传热膜系数的是( B)。
A.利用多管程结构B.增大管径C.在壳程内装折流挡板D.冷凝时在管壁上开一些纵槽4.蒸汽中硅含量长时间高,会使透平(C)。
A.转速高B.排汽温度高C.效率下降D.功率下降5.投用蒸汽时,一定要做好充分的疏水与暖管,开阀的速度不能过快,防止(D)。
A.压力过高而损坏设备B.温度过高而损害设备C.流量过大而损害设备D.产生水击而损害设备6.进入甲醇洗工段的变换气中水含量随变换气温度的升高而(C)。
A.减少B.不变C.增大D.大幅度减少7.下面关于气体溶解度的说话不正确的是(D)。
A.气体在水里的溶解度,与气体的性质有关B.气体在水里的溶解度,与气体的压强有关C.温度对气体的溶解度有很大影响D.气体在水里的溶解度,与气体的压强无关8.低温甲醇洗系统的腐蚀主要在(D)。
A.变换气到原料气冷却器进口管线B.再生塔C.水分离塔D.以上三项9.下列不属于压力容器的安全附件的是(C)。
A.温度计B.压力表C.截止阀D.液位计10.吸收操作应选用(C)的溶剂。
A.挥发性大B.粘度高C.腐蚀性小D.比热容小11.关于流动阻力描述,下列说法正确的是(B)。
A.流动阻力的大小与管的形状无关B.流动阻力分为直管阻力与局部阻力C.管路的变径对流动阻力没有影响D.管路中弯头越多,流动阻力越小12.对于离心压缩机的喘振,下列处理方法正确的是(C)。
A.关小出口阀门B.减小流量C.降低出口压力D.立即停机13.甲醇洗气提塔加入气提气是降低( C)的分压。
A.甲醇蒸汽B.氢气C.二氧化碳D.一氧化碳14.甲醇洗原始开车建立液位后将各塔压力按正常生产压力进行充氮气的目的是(A)。
吸收稳定操作法
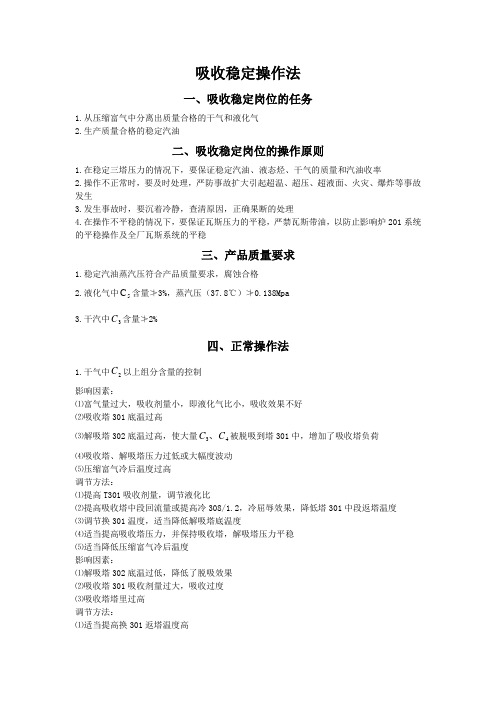
吸收稳定操作法一、吸收稳定岗位的任务1.从压缩富气中分离出质量合格的干气和液化气2.生产质量合格的稳定汽油二、吸收稳定岗位的操作原则1.在稳定三塔压力的情况下,要保证稳定汽油、液态烃、干气的质量和汽油收率2.操作不正常时,要及时处理,严防事故扩大引起超温、超压、超液面、火灾、爆炸等事故发生3.发生事故时,要沉着冷静,查清原因,正确果断的处理4.在操作不平稳的情况下,要保证瓦斯压力的平稳,严禁瓦斯带油,以防止影响炉201系统的平稳操作及全厂瓦斯系统的平稳三、产品质量要求1.稳定汽油蒸汽压符合产品质量要求,腐蚀合格2.液化气中5C 含量≯3%,蒸汽压(37.8℃)≯0.138Mpa3.干汽中3C 含量≯2%四、正常操作法1.干气中2C 以上组分含量的控制影响因素:⑴富气量过大,吸收剂量小,即液化气比小,吸收效果不好⑵吸收塔301底温过高⑶解吸塔302底温过高,使大量43C C 、被脱吸到塔301中,增加了吸收塔负荷 ⑷吸收塔、解吸塔压力过低或大幅度波动⑸压缩富气冷后温度过高调节方法:⑴提高T301吸收剂量,调节液化比⑵提高吸收塔中段回流量或提高冷308/1.2,冷屈辱效果,降低塔301中段返塔温度 ⑶调节换301温度,适当降低解吸塔底温度⑷适当提高吸收塔压力,并保持吸收塔,解吸塔压力平稳⑸适当降低压缩富气冷后温度影响因素:⑴解吸塔302底温过低,降低了脱吸效果⑵吸收塔301吸收剂量过大,吸收过度⑶吸收塔塔里过高调节方法:⑴适当提高换301返塔温度高⑵适当降低塔301吸收剂量,调节液汽化⑶根据情况适当降低吸收塔压力C含量的控制:3.液化气中5影响因素:⑴稳定塔303塔顶温度高⑵稳定塔303压力低⑶稳定塔底重沸器303返塔温度高⑷汽提热旁路调节幅度过大⑸稳定塔进料温度高,进料位置不合适调节方法:⑴适当增加塔顶回流量,降低塔顶温度,一般回流比保持在1.5~2.0⑵适当提高塔303压力,并保持平稳⑶降低稳定塔底重沸器温度⑷不要大幅度调节气体热旁路阀⑸降低进料温度,改变进料口位置4.吸收塔、解吸塔压力控制:影响因素:⑴反应深度变化,富气量变化⑵解吸塔302底温变化,造成压力波动⑶塔301吸收剂量,塔302进料量变化⑷塔301底U型管液封被破坏调节方法:⑴联系反应调整操作,稳定塔301压力⑵调节塔302底重沸器换301返塔温度并保持平稳⑶控制稳吸收剂量及温度,控制稳进料量⑷重新建立U型液封,保持U型管两端压力平衡5.再吸收塔压力控制:影响因素:⑴富气量变化(装置处理量、反应深度、反飞动量变化)⑵气压机出口变化⑶吸收塔301顶温度⑷再吸收塔304液面过高⑸干气出装置压控仪表失灵⑹吸收效果变差调节方法:⑴正常错左时,压力由再吸收塔干气出装置调节阀来控制T304压力⑵联系气压机岗位进行处理,本岗位要及时调节⑶适当降低塔302底温⑷维持塔304正常液面⑸仪表失灵,立即改善吸收塔的吸收效果⑹调节液汽比,改善吸收塔的吸收效果6.稳定塔压力控制:影响因素:⑴稳定塔底温变化⑵稳定塔进料量,进料组成变化⑶稳定塔顶回流量变化过大⑷稳定塔进料和顶回流带水⑸液态烃空冷器负荷过大或冷却效果不好C组分带到稳定塔,使塔303压力上升⑹解吸塔操作不稳,大量2⑺V302液面过高⑻不凝气出装置控制阀失灵,分程控制系统失灵⑼仪表失灵调节方法:⑴调节T303底温并保持平稳⑵控制好T302底液面和温度,防止稳定塔进料量,组成变化⑶适当调节T303顶回流量并保持平稳⑷加强V301、V302脱水⑸查找原因,相应处理,提高冷却效果C组分⑹T301、T302操作平稳,使脱乙烷汽油尽量少带2⑺控制V302液面平稳⑻正常操作时通过分程控制热旁路调节阀和不凝气调节T303压力。
液化气腐蚀问题的原因分析及解决措施
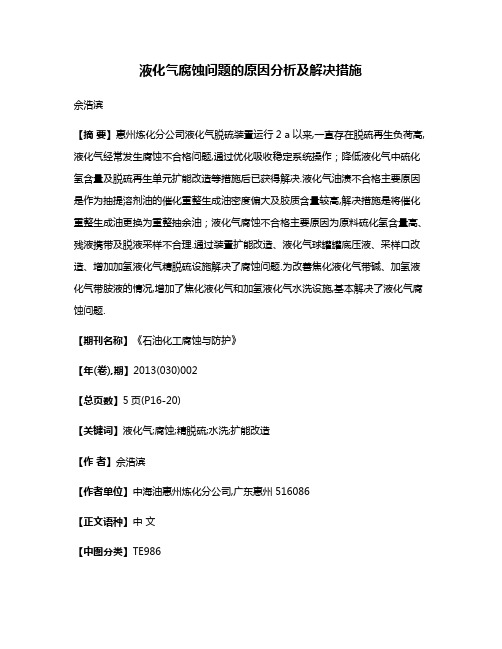
液化气腐蚀问题的原因分析及解决措施佘浩滨【摘要】惠州炼化分公司液化气脱硫装置运行2 a以来,一直存在脱硫再生负荷高,液化气经常发生腐蚀不合格问题,通过优化吸收稳定系统操作;降低液化气中硫化氢含量及脱硫再生单元扩能改造等措施后已获得解决.液化气油渍不合格主要原因是作为抽提溶剂油的催化重整生成油密度偏大及胶质含量较高,解决措施是将催化重整生成油更换为重整抽余油;液化气腐蚀不合格主要原因为原料硫化氢含量高、残液携带及脱液采样不合理.通过装置扩能改造、液化气球罐罐底压液、采样口改造、增加加氢液化气精脱硫设施解决了腐蚀问题.为改善焦化液化气带碱、加氢液化气带胺液的情况,增加了焦化液化气和加氢液化气水洗设施,基本解决了液化气腐蚀问题.【期刊名称】《石油化工腐蚀与防护》【年(卷),期】2013(030)002【总页数】5页(P16-20)【关键词】液化气;腐蚀;精脱硫;水洗;扩能改造【作者】佘浩滨【作者单位】中海油惠州炼化分公司,广东惠州516086【正文语种】中文【中图分类】TE986中海油惠州炼化分公司(惠州炼化分公司)液化气脱硫装置根据全厂总工艺流程的安排,采用集中脱硫、集中再生方式进行处理;主要处理加氢裂化、催化裂化、延迟焦化液化气。
液化气脱硫采用传统MDEA脱硫工艺,液化气脱硫醇采用美国Merichem公司的纤维膜脱硫醇工艺,胺液再生为传统的汽提再生工艺;脱硫脱硫醇后的催化液化气去气分装置,脱硫后的加氢液化气部分去烷基化装置,其余与焦化装置液化气一同作为产品进行销售。
惠州炼化分公司气体脱硫装置于2009年4月随加氢、焦化、催化装置一同开车后运行正常,产品质量能够满足设计要求。
但是随着全厂加工负荷逐渐提高,特别是含硫含酸原油比例增加后,脱硫装置脱硫能力不够,经常出现液化气铜片腐蚀、油渍试验不合格等问题。
1 液化气质量不合格原因分析1.1 硫化氢腐蚀不合格由于原料硫含量高、加工负荷高,液化气硫含量高于设计值,原设计液化气脱硫、胺液再生负荷不够,导致液化气硫化氢超标不合格。
焦化吸收稳定操作优化及其效果分析

≥C3组 含 份 量
3.4 3.5 3.6 3.7 3.8 3.9
36 37
4
38
39
40
41
42
43
44 45 46 47 48 VARY 1 E711 PA RAM TEMP C
49
50
51
52
53
54
55
56
6、效果分析
压力
6.5
6、效果分析
通过对焦化富气、贫气、脱吸气、干气、液态烃的组 成进行详细分析,找出吸收稳定系统存在的主要瓶颈有: 稳定塔顶冷凝器E706冷却负荷偏小,液化气回流温度 高,部分液化气不能冷凝,导致液化气罐和稳定塔顶压力 较高,影响吸收效果。 分馏塔顶后冷温度高,尤其在夏天最高达到50℃左右, 对气压机运行不利,增加了气压机后冷负荷。粗汽油温度 高,影响吸收效果。 补充吸收剂温度较高,需进一步降低吸收剂温度以改 善吸收效果。 焦碳塔每天轮流切换对吸收稳定操作影响较大。
Sensitivity S-1 Results Summary
5.5
6
≥C3组 含 份 量
3
0.8 0.825
3.5
4
4.5
5
0.85
0.875
0.9
0.925
0.95 0.975 1 1.025 1.05 1.075 VARY 1 T702 1 P-SPEC PRES MPAG
1.1
1.125
1.15
4、吸收稳定流程
5、操作优化
影响吸收的操作因素很多,主要有:油 气比、操作温度、操作压力、吸收塔结构、 吸收剂和被吸收气体的性质、塔内气液流 动状态、塔盘数以及塔盘结构等。对具体 装置来讲,吸收塔的结构、吸收剂和气体 性质等因素都已确定,吸收效果主要靠适 宜的操作条件来保证。
炼化工艺流程

预处理原因:原油中的盐和水的存在,给炼油装置的稳定操作、设备防腐带来了危害,因此在原油蒸馏前必须进行脱水脱盐。
因此原油进入炼油厂后,必须先进行脱盐脱水,使含水量达到0.1%~0.2%。
含盐量<5mg/l,对于有渣油加氢或重油催化裂化过程的炼油厂,要求原油含盐量<3mg/l。
电脱盐原理:原油中的盐大部分溶于水中,脱水的同时,盐也被脱除。
常用的脱盐脱水过程是向原油中注入部分含氯低的新鲜水,以溶解原油中的结晶盐类,并稀释原有盐水,形成新的乳状液,然后在一定温度、压力和破乳剂及高压电场作用下,使微小的水滴,聚集成较大水滴,因密度差别,借助重力水滴从油中沉降、分离,达到脱盐脱水的目的。
2常减压装置蒸馏装置是炼油厂重要的加工装置之一,几乎所有的炼油厂的原油都要通过常减压蒸馏装置进行一次加工,常减压蒸馏装置主要通过蒸馏过程加工原油,加热后的原油在蒸馏塔内实现各组分的分离。
分离出来的产品即为一次加工产品,主要有气体、石脑油、柴油、蜡油及渣油等,有的炼油厂根据加工方案的不同,可能还会有煤油、溶剂油等产品;燃料—润滑油型的炼油厂,在减压塔部分生产一部分润滑油原料。
初馏经过了第一步的脱盐脱水操作之后,原油要经过换热器提高温度,当温度达到200℃~250℃时,才可以进入初馏塔装置。
在这里,将原油里剩余的水分、腐蚀性气体和轻汽油排出,这样就减少了塔的负担,保证了塔的稳定状态,起到了提高产品质量和尽可能多的回收原油的效果。
常压蒸馏从上一步骤出来的油叫拔顶油。
经过输送泵进入常压炉后加热,加热要求是360℃左右,然后进入常压塔。
从塔顶分离出来的油和气,经过冷凝和换热后,一些就成为汽油,一些就成为了煤油和柴油。
减压蒸馏减压蒸馏的主要工艺装置是减压塔,减压塔是将从常压塔里出来的重油,通过减压的方式进行深加工。
常减压蒸馏装置开工时的主要危险及预防措施3催化裂化装置催化裂化装置是炼油厂重要的二次加工装置之一,以常减压蒸馏装置的一次加工重油产品或某些二次加工装置的重组分产品为原料,通过在高温下与催化剂的接触作用,裂化为轻质油品组分。
影响吸收塔吸收效果的原因及处置措施

影响吸收塔吸收效果的原因及处置措施摘要:硫磺回收装置吸收塔运行状况会直接影响到硫磺回收装置加氢还原尾气的吸收效果,进而影响硫磺收率,硫含量转化率降低一方面会导致产品收率降低,另外还会导致尾气中硫化物超标。
含硫气体不仅污染环境,并且会直接导致国控源波动,甚至超标,而且腐蚀设备,使正常生产无法进行,缩短设备的正常寿命,造成经济损失。
吸收塔的吸收效果对硫磺回收装置硫收率及国控源稳定有着至关重要的作用,如何保证吸收塔的吸收效果,是我们探讨的方向。
因此,提高硫磺回收装置吸收塔的吸收效果,不仅可以提高硫磺装置产品的收率,而且可以防止设备腐蚀,保障国控源不超标,对硫磺回收装置具有十分重要的意义。
关键词:胺液;尾气回收系统;吸收塔;环境一、工艺介绍天津石化炼油部1#硫磺回收装置由中国石化北京石化工程公司做基础设计,中国石化南京设计院做施工图设计,处理量为6万吨/年,装置年开工时数按8400小时计算,连续生产。
原料酸性气是由脱硫酸性气、污水汽提酸性气组成。
采用改良克劳斯燃烧反应,尾气处理采用加氢还原法,Claus尾气经过加氢还原后产生的气体经过急冷塔后,采用高效脱硫剂吸收H2S达到提高硫收率,净化尾气,确保排放达标。
尾气回收系统是在吸收塔中用脱硫再生系统送来的胺液吸收其中的H2S,从吸收塔中出来的净化尾气进入尾气焚烧炉在燃料气和过量空气存在的条件下,经高温充分燃烧后,排入大气。
二、影响吸收塔吸收效果的因素及对策1、选择高效脱硫剂作为吸收塔的吸收剂目前市场上可选的胺液吸收剂种类很多,天津石化炼油部联合四车间选用的是N-甲基二乙醇胺CH3N(C2H4OH)2 脱硫剂,其反应机理如下:H2S+R3N→R3NH++HS- (瞬间反应)(1)CO2+H2O+ R3N→R3NH++HCO3(缓慢反应)(2)N-甲基二乙醇胺的特点:①N-甲基二乙醇胺对硫化氢的吸收率比较高,而对二氧化碳吸收较少,从而使溶液再生后产生的酸性气中硫化氢浓度提高,对后续的克劳斯硫磺回收装置是有利的。
催化稳定岗位试题A卷

稳定岗位试题A卷一、填空题(每空1分,共20分)1、稳定塔的任务是将脱乙烷汽油进一步分离为(液化气)(稳汽)等合格产品。
2、富气量过大,吸收剂量小,故(液气)比小,吸收效果(不好)。
3、稳定用(蒸汽)作热源,稳定压力来自于(富气压缩机)。
4、稳定岗位采(干气)样和(液化气)样时需防冻伤。
5、构成石油液化气的主要组分是(碳3)和(碳4)。
6、蒸汽压表示液体的(蒸发和汽化)能力,蒸汽压越高液体(越易汽化)。
7、解析塔底的热源是(蒸汽)。
8、吸收塔的作用(吸收富气中的C3、C4 )。
9、影响稳定汽油蒸汽压的关键组分是( C4)。
10、液化气中C5含量指标为(≯3%)。
11、液化气中C5含量高,稳定塔底温度应(降低)。
12、停工开人孔时应遵照 (先上后下 )的原则,打开通风一段时间,并做 (含氧分析 ),合格后方可进人。
13、吸收塔所用的吸收剂是(粗汽油、稳定汽油)。
二.选择题:(每题2分,共20分)1、干气的主要组分范围是(A)。
A、C1、C2B、C3、C4C、C5、C62、油品的饱和蒸汽压越高(B)。
A、油品越易液化B、油品越易汽化C、油品既不汽化,也不易液化3、吸收塔的作用( B ).A.是压缩富气和解析塔之间的缓冲塔B.吸收富气中的液化气和汽油C.调节汽油的蒸汽压4、T302冲塔的因素有(A )A、T302温度高,压力低B、进料组成变化,塔内气相负荷大C、冷、热路分配比例不当5、为了提高吸收效果,吸收塔的操作原则是( A )A低温高压 B.高温低压 C.高温高压6、液化气中C2含量高,解析塔温度应( A ).A.提高B.不变C.降低7、稳定塔底温度低,则稳汽蒸汽压( A )A.高B.不变C.低8、解析塔底温度一般要求在( A )度左右A.120B.130C.1009、V302液面调节是( B )A.就地调节B.室内仪表调节C.人工调节10、稳定塔顶重关键组分为(A)(A) C4 (B) C5三、判断题(每题2分,共20分)1、压缩富气短时间中断时,关压缩富气去稳定手阀,关干气压控阀,平稳稳定操作.(√)2、稳定塔压力的变化对汽油蒸汽压没有影响.( × )3、吸收温度高对吸收不利.( √ )4、T303不能压空.( √ )5、稳定塔冷回流越大越好.( × )6、整个稳定塔由精馏段,进料段,提馏段三部分组成。
- 1、下载文档前请自行甄别文档内容的完整性,平台不提供额外的编辑、内容补充、找答案等附加服务。
- 2、"仅部分预览"的文档,不可在线预览部分如存在完整性等问题,可反馈申请退款(可完整预览的文档不适用该条件!)。
- 3、如文档侵犯您的权益,请联系客服反馈,我们会尽快为您处理(人工客服工作时间:9:00-18:30)。
炼化企业吸收稳定系统中影响吸收的操作因素浅析摘要:吸收稳定系统的任务是将富气和粗汽油分离成干气
(c1、c2)、液化气(c3、c4)及稳定汽油,并保证产品质量。
但干气“不干”即干气中携带的c3 及以上组分含量的现象有时存在;而后续液化气、稳定汽油或c2组分超标影响质量或产品收率大幅度降低。
这都是吸收稳定系统第一步的吸收操作不当引起的。
本文结合催化装置的生产实际,找出最优的操作参数解决这一问题。
关键词:吸收解吸温度压力干气
一、前言
吸收稳定系统是催化裂化装置的后部处理过程,主要由吸收塔、解析塔、稳定塔、再吸收塔及相应的辅助设备构成。
作用是利用吸收和精馏方法将富气和粗汽油分离成干气(c1、c2)、液化气(c3、c4)及稳定汽油。
二、催化装置吸收与解吸的基本原理
吸收是分离气体混合物的过程.利用混合气体中各组分在溶剂中溶解度的不同达到分离的目的。
反之则是解析过程。
在吸收塔内,吸收剂自塔顶入塔下行,与由塔底上升的烃类混合气体在塔板上进行多次气、液逆流接触,使得有效成分(关键组分c3及c3以上)在随气体上升的过程逐渐被吸收油溶解而由气相转入液相之中。
由于相平衡的关系,吸收剂在富含c3及c3以上组分同时,也不可避免地吸收了相当数量的c2组分,这就需要解析塔进一步脱除其中的
c2组分。
吸收塔底的富吸收油用泵送至解吸塔。
液流自解吸塔顶下行,与解吸塔底重沸器加热后逆流而上温度较高的气相在塔板上相互接触.使溶解在富吸收油中的c2组分被脱吸出来,进入气相中,再经过冷却返回吸收塔底部。
解吸塔底来的脱乙烷汽油进入稳定塔脱除c3、c4,塔顶得到液化气,塔底得到稳定汽油。
此系统即催化裂化装置的吸收稳定系统。
三、影响吸收的操作因素
影响吸收的操作因素很多,主要有:油气比、操作温度、操作压力、吸收塔结构、吸收剂和溶质气体性质等。
对具体装置来讲,如何利用优良的操作参数(温度、压力、油气比等)达到最优的吸收解析效果,从而提高目标产品的优效性成为关键性因素。
1.油气比
油气比是指吸收油用量(粗气油与稳定汽油)与进塔的压缩富气量之比。
当催化裂化装置的处理量与操作条件一定时,吸收塔的进气量也基本保持不变,油气比大小取决于吸收剂用量的多少。
增加吸收油用量,可以增加吸收推动力,从而提高吸收速率,即加大油气比,利于吸收完全。
从下图可以更形象的说明油气比与吸收的关系:
备注:(1)直线ab是操作线,其斜率l/g就是油气比;
(2)直线cd是平衡线,其斜率k是平衡常数,在温度压力恒定情况下,k值是不变的;
(3)操作线上任一点m与平衡线间的垂直距离即为吸收推动力;
从图可以看出来,当油气比增大,既l/g增大,操作线就会向上移动,与平衡线之间的距离就会加大,从而就加大了吸收的推动力。
实际操作中,油气比过大,会使过多的c2组分也被吸收,加大解析塔的负荷,同时影响后续产品的质量;再者,吸收油用量越大,吸收塔顶贫气(c1、c2组分)带出的油量也越多,而加大了再吸收塔与分馏塔的负荷,从而导致操作费用增加。
另一方面,油气比也不可过少,它受到最小油气比限制。
当油气比减少时,吸收油用量减少,吸收推动力下降,富吸收油浓度增加。
当吸收油用量减少到使富吸收油操作浓度等于平衡浓度时,吸收推动力为零,是吸收油用量的极限状况,称为最小吸收油用量,其对应的油气比即为最小油气比。
实际操作中采用的油气比应为最小油气比的1.1——2.0倍,一般吸收油与压缩富气的质量比大约为2.
2.操作温度
在吸收压力不变的情况下,吸收温度是影响吸收效果的重要因素。
吸收温度低,气体溶质溶解度大,吸收速度快,有利于提高吸收率。
吸收操作需达到的指标:干气尽可能干,c3 含量不大于3%(体积分数),实际操作中c3及以上组分含量当然是越低越好。
下面是一组有关于干气c3及c3以上组分的分析数据,从中可以了解到温度对吸收的影响
备注:(1)数据来源于某催化装置>
(2)此数据分析是在吸收压力恒定的情况下进行的
从上述列表可以看出,温度越高,干气中c3及c3以上组分就越多,从而会引起“干气不干”的问题,同时会影响后路液化气的产量,所以要想使干气达到相应的指标,就应相应地降低吸收温度。
由于吸收油吸收富气的过程有放热效应,吸收油自塔顶流到塔底,温度有所升高。
因此,在塔的中部设有两个中段冷却回流,经冷却器用冷却水将其热量取走,以降低吸收油温度。
降低吸收油温度,对吸收操作是有利的。
然而吸收油温度的降低,要靠降低入塔富气、粗气油、稳定汽油的冷却温度和增加塔的中段冷却取出量,这要过多地消耗冷剂用量,使操作费用增大。
吸收塔温度太低,使再吸收塔的温度降低而使轻柴油粘度增大,反而降低再吸收塔的吸收效果。
同时也使解析塔的温度降低而增大解析塔的能耗。
一般以控制约为40℃左右较为合适。
3.操作压力
在一定温度下,分压是直接决定溶解度(气液两相处于平衡状态时,溶质在液相中的含量称为溶解度)的参数。
总压不同意味着溶质的分压不同。
只要气相中组分的分压大于其溶液的平衡分压,吸收过程便会进行下去。
下有一组数据,可以说明压力与吸收的关系:
由图可以看出来,在温度一定时压力越高,干气中c3以上组分
含量就越少,所以提高压力有利于吸收。
提高吸收塔操作压力,有利于吸收过程的进行。
但加压吸收需要使用用大型压缩机,使塔壁增厚,费用增大。
同时, 随着吸收压力的提高, 相应地解吸塔压力也随之升高, 将被迫提高解吸塔塔底温度,进一步增加能耗。
实际操作中,吸收塔压力由压缩机的能力及吸收塔前各个设备的压降所决定,多数情况下,塔的压力很少是可调的。
四、结论
吸收塔操作的好坏直接影响着各个产品的质量,增大油气比,低温高压都有利于吸收,但是吸收稳定系统各个塔之间的操作并不是孤立的体系,各塔操作相互联系、相互影响,同时整个系统又与分馏系统、气压机系统密切联系的,优化操作应综合考虑还要考虑能耗、生产成本等经济因素。
根据上面分析以及对目前炼油催化装置的考察得出吸收系统操作参数如下所示:
针对各个催化装置处理量,原料油性质,催化剂选用等相关因素不同吸收塔相关操作参数给出一个相关范围,用来根据实际情况参考。
参考文献
[1]梁凤印等,流化催化裂化北京:中国石化出版社,2008年1月.
[2] 林世雄,石油炼制工程北京:石油工业出版社,1988.
[2] 程丽华,石油炼制工艺学北京:中国石化出版社,2007年9月.
[4]马伯文,催化裂化装置技术问答(第二版)北京:中国石化出版社,2005年1月.
[5]陈敏恒,丛德滋等,化工原理(下册)北京:化学工业出版社,2000年2月.。