工厂合理化讲义布局Layout
layout基本知识培训 PPT

基本型式
原 材 料 1仓 U字型配置 库 轴 完成品 类
布置例
热
⑨
⑧处
理
⑦
⑥
总 装
置 场
⑤ 品
仓 库
成
齿
类
材料
铸 造
①
②
③
配
④
零件C
零件D
零件E 零件A 零件B 零件F
第三部分:Layout基本元素介绍
29
Johnson Controls PowerPoint Guidelines | February 8, 2008
□ 最大限度地减少建筑物结构上的障碍因素 - 应能灵活地改变生产线(设备)布置。 - 最大限度地减少建筑柱子、Utility设施等障碍因素 。
最佳布置
设定适当的工作空间和通道 - 确保人员、材料、通道布置的效率与安全性。 - 易于监督管理的布置。
第三节 成品资材仓库
3.资材成品仓库
3.1 资材成品仓库原则
19
三、LAYOUT基本形式
1)固定式布局方法(产品中心) 以产品为中心,人、机械、道具、移动。
主体
三、LAYOUT基本形式
1)固定式布局方法(产品中心)的特点 具备灵活性,容易适应变化。 把产品固定,作业人员移动。 对产品的质量意识提高了。 改进作业方法等的余地很大。
三、LAYOUT基本形式
2)按功能及加工方法布局(设备中心) 传统布局(乱流)
按功能区域防止的布局,精益生产称之为乱流布局
车床 A产品 钻床 铣床
B产品
C产品
三、LAYOUT基本形式
图表 1—2 A产品与B产品的工艺流程法
23
三、LAYOUT基本形式
layout(工厂布局)(课堂PPT)
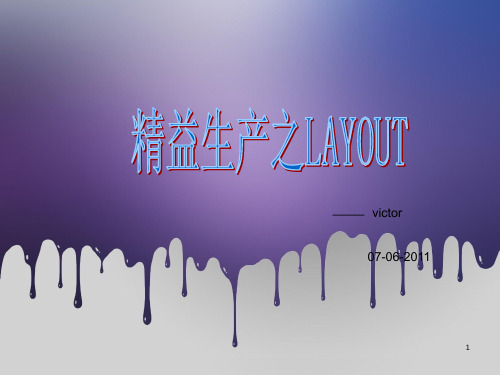
2020/4/7
4
种类
目的
特征程分析
的工艺流程
作业流程分 主要分析作业
析
者的作业流程
2020/4/7
多人通过多 台设备制造 同一产品
一人通过不 同设备或不 同工序,制造 多个产品的 过程
(1).改变包装作业流 程
打保证书
贴标签
品 质 部 出 库
2020/4/7
数外 搬
输
量观 运
入
检检 至
机
查查 电
身
脑
号
处
包
传
封
装
送
箱
加
工
改善后包装作业流程图
搬储 运存 至 成 品 仓
17
2.改变车间布局
品质部开关盒储存区
辅料存放区
包装车间开关盒 临时存放区
电脑输入出
保
证 书
包装LINE A
打
印
包装LINE B
(1).Leadtime
A.Leadtime的定义
从客户下订单到工厂交货,这个过程所花费的时间就是leadtime, 即完成某项目标所花费的流程时间
B科特尔法则
Leadtime=存货数量×生产节拍或存货数量×生产能力
C. 生产节拍
生产节拍是指每生产一个产品所需要的间隔时间
例如:一台设备的生产能力是每小时生产120个产
P4
P6
P9
P5
P7
P8
P10
工序8
产品分族矩阵
2020/4/7
33
生产线排单: Line A:生产P1产品 Line B生产P2产品 Line C生产P3产品 Line D生产P4 P6 P9产品 Line E生产P5 P7产品 Line F生产P8 P10产品
Layout规划经验谈
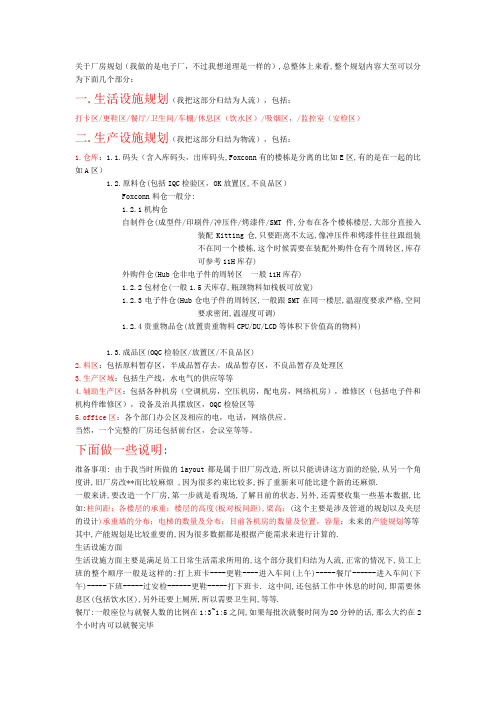
关于厂房规划(我做的是电子厂,不过我想道理是一样的),总整体上来看,整个规划内容大至可以分为下面几个部分:一.生活设施规划(我把这部分归结为人流),包括:打卡区/更鞋区/餐厅/卫生间/车棚/休息区(饮水区)/吸烟区,/监控室(安检区)二.生产设施规划(我把这部分归结为物流),包括:1.仓库:1.1.码头(含入库码头,出库码头,Foxconn有的楼栋是分离的比如E区,有的是在一起的比如A区)1.2.原料仓(包括IQC检验区,OK放置区,不良品区)Foxconn料仓一般分:1.2.1机构仓自制件仓(成型件/印刷件/冲压件/烤漆件/SMT件,分布在各个楼栋楼层,大部分直接入装配Kitting仓,只要距离不太远,像冲压件和烤漆件往往跟组装不在同一个楼栋,这个时候需要在装配外购件仓有个周转区,库存可参考11H库存)外购件仓(Hub仓非电子件的周转区一般11H库存)1.2.2包材仓(一般1.5天库存,瓶颈物料如栈板可放宽)1.2.3电子件仓(Hub仓电子件的周转区,一般跟SMT在同一楼层,温湿度要求严格,空间要求密闭,温湿度可调)1.2.4贵重物品仓(放置贵重物料CPU/DU/LCD等体积下价值高的物料)1.3.成品区(OQC检验区/放置区/不良品区)2.料区:包括原料暂存区,半成品暂存去,成品暂存区,不良品暂存及处理区3.生产区域:包括生产线,水电气的供应等等4.辅助生产区:包括各种机房(空调机房,空压机房,配电房,网络机房),维修区(包括电子件和机构件维修区),设备及治具摆放区,OQC检验区等5.office区:各个部门办公区及相应的电,电话,网络供应。
当然,一个完整的厂房还包括前台区,会议室等等。
下面做一些说明:准备事项: 由于我当时所做的layout都是属于旧厂房改造,所以只能讲讲这方面的经验,从另一个角度讲,旧厂房改**而比较麻烦 ,因为很多约束比较多,拆了重新来可能比建个新的还麻烦.一般来讲,要改造一个厂房,第一步就是看现场,了解目前的状态,另外,还需要收集一些基本数据,比如:柱间距;各楼层的承重;楼层的高度(板对板间距),梁高;(这个主要是涉及管道的规划以及夹层的设计)承重墙的分布;电梯的数量及分布;目前各机房的数量及位置,容量;未来的产能规划等等其中,产能规划是比较重要的,因为很多数据都是根据产能需求来进行计算的.生活设施方面生活设施方面主要是满足员工日常生活需求所用的,这个部分我们归结为人流,正常的情况下,员工上班的整个顺序一般是这样的:打上班卡----更鞋----进入车间(上午)-----餐厅------进入车间(下午)-----下班-----过安检------更鞋-----打下班卡. 这中间,还包括工作中休息的时间,即需要休息区(包括饮水区),另外还要上厕所,所以需要卫生间,等等.餐厅:一般座位与就餐人数的比例在1:3~1:5之间,如果每批次就餐时间为20分钟的话,那么大约在2个小时内可以就餐完毕卫生间:对于不同功能,其数量是不一样的,如果是集中用,比如生产线休息的时候,这时候上厕所的人就特别多,所以生产区域的数量就要多,我记得我看过一个法规建议值:15人/个(中小学生),对于office区域,由于都是不定时使用,所以比例可以高一些,我记的我们当时基准是40人/个车棚:这个需要实际统计,包括自行车,小轿车,电动车的数量各自为多少.休息区:这个要根据实际需要测算,一般根据每批次休息人数来规划安检区:安检门的数量根据高峰下班时段的人数来进行计算,这个部分如果从理论上讲,是排队论的一些运用,当然在实际中,不用考虑那么负责,我们当时设计的方案是估算高峰时段的人力Q,然后测量一下一个人过安检门需要多少时间T(s),在给一个目标时间,比如20分钟可以让所有人过完,这样,就可以根据公式(Q*T)/(20*60)来得到所需数量,此外还需要考虑回流的路线设计.打卡区:这个的规划和安检门的规划所用的原理差不多.生产设施方面: 一般来讲,一个电子厂的比较正常的流程是:供应商送货至码头-----仓管收货,盘点------到暂存区-----IQC检验------入库-----生产部门领料(or仓库发料)------暂存区(Kitting 仓)------发料至生产线-----成品暂存区-------成品仓在规划整体的布局的时候,基本上可以按照物流的流向来进行考虑.当然,这只是正常的顺序,实际上,还存在回流的情况,比如IQC验货NG的时候,需要退料,成品抽检NG,需要重工,等等.一些杂七杂八的点:1.仓库:一般来说,电子厂的料主要分为三大类:电子件,机构件(包括塑胶件和五金件),包材,这三类的存储要求还是有很多区别的,尤其是电子料,一般都有温湿度的管控要求,所以一般都是单独建仓库来放置,而机构件和包材对环境要求不大.还有一些比较贵重的料,可能会存在一些比较安全的区域,考虑另外码头的分布,对于整个物流路线的规划起着很重要的作用.2.对于物流,现在一般厂房都有好几层,所以都有电梯,个人觉得电梯的分布对整个物流的顺畅起着很重要的作用,所以对于电梯的分布一定需要注意从整体上去考虑,很多时候可以通过合理设置电梯的分布避免物流的交叉,另外,电梯的宽度大小及其高度及承重是按照其所运送货物的栈板的最大宽度和高度来确定的,当然,需要有15%左右的宽放.3夹层,建夹层是为了增加空间的利用率,但是这有个约束,就是楼层的高度,如果需要车间需要安装空调,风管等管道,从经验上讲,这些管道要占到80cm左右的高度,那么楼层的高度如果低于6m就很难建夹层.4.吊顶:一般来讲,吊顶的高度距离地面不要低于 2.8m,否则人就会感觉很压抑,这也是为什么如果板对板的间距低于6m,就很难建夹层.(如果梁高50cm,风管+桥架+灯具要占到80cm,这样就去掉1.3m,吊顶2.8m,那么夹层的高度最多只有2.7m了)5.各种通道的设计:通道的实际一般都是参考车间里所用的运输工具来设计的,比如,在车间内部一般都是用叉车拉栈板,所以通道的宽度至少要比最宽栈板的宽度大15%左右.物流通道:包括主物流通道油压车,双行 2.76 3m次物流通道油压车,单行 1.38 1.5m线体间通道平板车,双行 1.38 1.4m电动叉车通道叉车转弯半径/栈板大小 3.75 4m备注:栈板按1.2m*1.2mTV:这里讲的CCTV不是指中央电视台,而是监控系统.监控系统主要就是摄像头的分布,摄像头的分布一般参考所在区域是否有贵重物品,一般来说,库房里摄像头是比较多的,此外,各个门口基本上都要安装摄像头,还有就是重工区,料区,等等.7.各种机房:如上面所讲,工厂的机房一般都包括水塔(水),配电房(电),空压机房(气),空调机房(冰水主机室),网络机房等等,需要注意的是压降问题,对于一些比较精密的设备,可能对于电压要求比较高,所以如果配电房到设备所在地过远,可能会有压降导致设备不能正常运转,这个问题,可以请教专门电气施工人员,当然,网络也有这样的问题,从交换机出来的网线如果超过100m,信号就会发生衰减.8.线槽:这个设计到布线,工厂所用的线包括强电和弱电,大部分情况下强弱电是可以并在一起走的,但是有些情况下最好不要合并.这个可以请教专业人士.9.消防系统:消防系统要按照法规来进行,这个一般建厂的都比我们有经验,只是在设计layout的时候一定要把这个因素考虑进去,有时候规划可能很合理,但是却不符合消防法规,在消防规划中,包括逃生动线,各种********(包括烟感器,防烟垂壁,喷淋头,消火栓,灭火器)的摆放等等.10.施工:施工从一般性来讲分为土建和机电两个部分.从我的经验讲,了解一些施工的知识对于画layout是很有帮助的.在整个厂房的规划中,layout基本上随施工一直在调整,因为有时候你规划是这样,但是随着施工的进行,发觉有些规划并不是那么合理,所以需要进行调整.可以说,施工没有结束,layout就会一直调整.11.各楼层的电力负荷.。
精益生产之LAYOUT--ppt课件
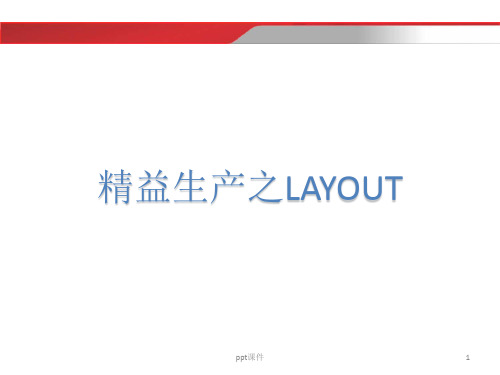
A.Leadtime的定义 从客户下订单到工厂交货,这个过程所花费的时间就是 leadtime,即完成某项目标所花费的流程时间
B.科特尔法则 Leadtime=存货数量X生产节拍或存货数量X生产能力
C.生产节拍 生产节拍是指每生产一个产品所需的间隔时间
例如:一台设备的生产能力是每小时生产120个产品,也就是说这台设
多人分割式U型生产线
ppt课件
25
c.诼兔式
诼兔式式U型生产线
ppt课件
26
B.I字型布局
ppt课件
27
B.Y字型布局
ppt课件
28
3.Cell布局五步法
1).通过产品分类确定生产类型
在进行产品分类时,可以通过P-Q分析法, P-Q分析法是指对企业目前的所有产品按 按加工工艺分类,同时对各类产品的生 产量进行统计分析的一种方法
流程分析的定义
掌握全部生产过程包括工艺加工过程、检查过程、 搬运过程、停滞等的实际状态,发现并消除其过程 中的浪费与不合理
ppt课件
3
1.准确把握工艺流程的整体状态
明确工艺流程的先后顺序 明确工艺工序的整体关系 确定各工序之间的作业时间 发现工艺流程中不合理,不平衡的状态
2.寻找发现工序的问题点
1.检查方法 2.不良率
等待原因
等待地点
等待时间
ppt课件
9
1.流程分析的图示符号
A.产品工艺流程分析符号
工序种类 符号
说明
加工 搬运 检查 停止储存
材料,零部件或新产品在加工过程中发生了外形规格性质 等的变化或为下一工序进行准备的状态
材料,零部件或产品在一定状态下不变,同时转移位置状 态
Layout系统性的厂房布局方案ppt课件
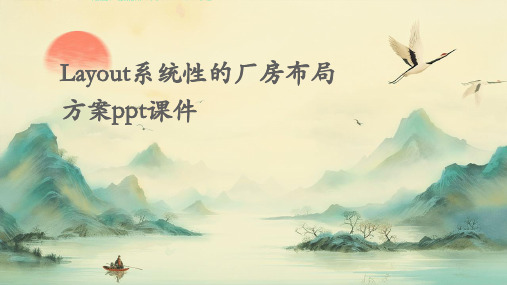
合理配置搬运设备数量和位置,确保物料搬运的及 时性和准确性。
03
考虑设备维护和保养需求,确保设备长期稳定运行。
搬运过程中安全防护措施
01
制定严格的安全操作规程,确保搬运过程中人员和设备的安全。
02
设置必要的安全防护设施,如防护栏、安全标识等。
定期对搬运设备进行安全检查和维护,及时发现并消除安全隐
03
厂房内部区域划分与功能定位
生产区域划分及依据
按工艺流程划分
根据产品生产工艺流程,将厂房划分为不同的生产区域,确保生产 流程的顺畅。
按设备类型划分
根据生产设备类型和功能,将相同或相似的设备集中放置在同一区 域,便于设备管理和维护。
按生产环境要求划分
根据生产环境要求,如温度、湿度、洁净度等,将厂房划分为不同的 生产区域,以满足产品生产的环境需求。
03
SLP法优势
逻辑性强、条理清晰、能够综合考虑多种因素、适用于不同规模和复杂
度的布局设计。
摆样法原理与实践
1 2
摆样法概述 摆样法是一种通过实际摆放物品来确定最佳布局 的方法,具有直观、易操作的特点。
摆样法实践步骤 明确摆放目标、准备物品和场地、进行实际摆放、 调整和优化布局、确定最终方案。
3
摆样法注意事项 确保物品与实际生产物品相符、考虑物品之间的 关联性和操作顺序、充分利用场地空间。
数学模型法优化布局
数学模型法概述
数学模型法是一种运用数学方法和计算机手段来求解最优布局的 方法,具有精确、高效的特点。
数学模型法应用步骤
建立数学模型、确定约束条件和目标函数、选择求解算法、进行 计算机求解、分析结果并优化布局。
数学模型法常用算法
线性规划、整数规划、动态规划、遗传算法等。这些算法可以根 据具体问题和约束条件进行选择和应用。
工厂布局设计方案课件PPT专业课件

工厂布局设计方案课件PPT专业课件标题:工厂布局设计方案课件PPT
介绍:
本课件将为大家详细介绍工厂布局设计方案的相关内容,包括布局设计原则、布局类型、布局过程以及布局实施等方面的内容。
通过本课件的学习,大家将了解到如何科学合理地设计工厂布局,提高工厂的生产效率和运作效益。
1.工厂布局设计的原则
1.1空间合理利用原则
1.2流程优化原则
1.3安全生产原则
1.4灵活可变原则
1.5环境友好原则
2.工厂布局的类型
2.1均衡类型:产品流程均衡、设备利用均衡、资源利用均衡
2.2分散类型:产品流程分散、设备利用分散、资源利用分散
2.3集中类型:产品流程集中、设备利用集中、资源利用集中
3.工厂布局的过程
3.1数据收集与分析:生产需求分析、设备数据收集、产品需求分析
3.2布局规划:流程分析、设备布局、功能划分
3.3布局优化:空间利用率优化、运输路径优化、设备关联度优化
3.4布局评估:生产效率评估、物流效率评估、安全评估
4.工厂布局的实施
4.1布局实施计划制定:布局工期计划、资金计划、资源计划
4.2设备搬迁与安装
4.3功能划分与标识
4.4生产过程优化调整
4.5布局效果评估与改进
总结:
通过对工厂布局设计方案的学习,我们了解了工厂布局设计的原则、类型、过程和实施等方面的内容。
工厂布局设计是一个复杂而综合性的过程,需要考虑多个因素并进行综合权衡,以达到最佳的布局效果。
合理的工厂布局设计能够提高工厂的生产效率和运作效益,并为企业的可持续发展奠定基础。
我们应该在实际操作中灵活运用这些知识,为企业创造更大的价值和竞争优势。
精益工厂布局精益知识普及版分钟快速讲解

23
Lean Layout
丰田生产模式TPS学习
精益布局的五种模式:
串联式布局 并联式布局 U型布局 单元化布局(/细胞布局,Cell Line) V型/L型布局
24
Lean Layout
丰田生产模式TPS学习
精益布局的五种模式:
1、串联式布局:
优点:
物流线路清晰
产量增加时只需增加列数即可
称,混乱式布局。
17
Lean Layout
丰田生产模式TPS学习
传统布局的缺陷和不足:
1、大批量生产; 2、过多的在制品; 3、不必要的搬运; 4、生产不均衡; 5、生产计划排程难; 6、生产缺乏柔性; 7、埋没了员工的智慧和创造力,无法获得满足感; 7、不便于发现生产流程中的问题和浪费; 8、……
丰田生产模式TPS学习
9
Lean Layout
布局的目的: 利用率: 提高人和设备的利用率; 提高空间利用率;
丰田生产模式TPS学习
10
Lean Layout
丰田生产模式TPS学习
传统布局模式
11
Lean Layout
传统布局的基本形式:
1、固定式布局(以产品为中心) 2、功能式布局(以设备为中心) 3、流程式布局(以流程为中心) 4、混合式布局(结合前三种布局)
精益布局的原则:6、灵活机动原则
内容: 适应变化,随机应变,采取灵活措施。
理由: 面对各工序的变化、增减等变化,尽可能随机应变、见
机行事。
50
Lean Layout
丰田生产模式TPS学习
实现精益布局的步骤
51
Lean Layout
实现精益布局的步骤:
丰田生产模式TPS学习
layout基本知识培训(PPT 85页)

模具置场 维护
标准的生产流程
进料零件 检查 保管
原 材检 料查 进
素材 库 素材加 库 成型 存 工工程 存 工程
表面 库 处理 存 工程
料
冲压、塑胶成
形,压铸成形
机械加工,
等
二次组装等
电镀、涂装、 热处理等
完
完成品 加工工
程
成交 库品 货 存出
货
机械加工,
二次组装
等
36
yout区块化布局思路
16
二、LAYOUT改善的基本原则
原则四:尽可能利用立体空间(面积最小原则) 减少地面放置立体空间摆放
里面有效利 用两层
网架式 立体存储
由小型升降机提供组装零件 利用空间时,要特别注意安全 货物必须易拿易放
17
二、LAYOUT改善的基本原则
原则五:在作业的角度注意:安全及便于操作
18
二、LAYOUT改善的基本原则
41
2.生产线设计
① 传动带 : 考虑工作者身体条件设计传送带。 ② 生产设备
- 按设备特点决定所需面积和设备数量。 - 按设备或者流程布置并设计流程方法。 ③ 通道 - 通道宽度设计 (考虑人和搬运工具) ④ 工作区域 - 设计间隔(人、设备、构筑物等)、工作高度及物料摆放等。
42
设备所需面积决定因素: 1设备的运行行程 2设备维修间距 3设备间最短距离 4设备配套区域面积
□详细LAYOUT设计
- 生产线: 通道宽度、线(line)布置和间隔、工作地区、线(line)长度、适当的 工作台等
- 仓库: 适当的库存、堆放方法、布置、通道设计等 - 配套设施: 设定办公室、休息室、洗手间的人均单位面积 - Dock场 : 设计Dock数量、布置间隔、进路、Leveler等 - 公司内道路和出入门 : 道路宽度、道路数量、与公司外道路连接等
工厂layout布局分析与设计
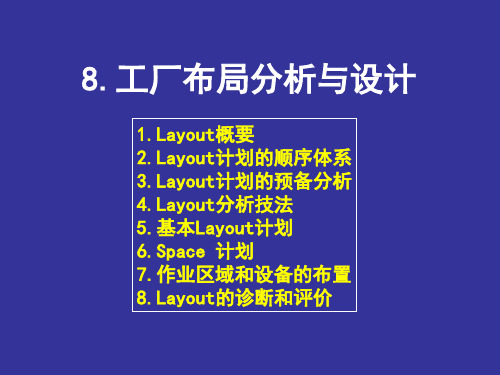
运行level
限制条件
yout计划预备分析
1)改善Layout的预备分析内容
Layout 变更可以 改善的问题领域
问题实际现象
-生产日程延迟 -过多的在制品 -高价设备运转率低 -用于搬运的工时 -人的移动距离 -空间的浪费 -活动之间的妨碍/干涉 -危险或不安全作业环境
ห้องสมุดไป่ตู้
原因/活动 效果分析
-所有A关系排列在模板的4边 -E关系至少排列在模板的四角 -X关系绝对隔离 -A关系连4角都没排到,X关系排到4边时 -A关系排到角落,X关系排到4角或E关系 边角都没排上
与基准模板有I,O,U,X 关系的模板,以相同的方法排列后 在 check mark 数评价layout
yout分析及方法
生产系统的构思
-制造工程/装配顺序 -设备所需台数及规格 -人力资源所需计划 -作业方式的构思 -现场及部门的区分 -管理及服务的要求功能 -搬运及库存系统运营 方式的构思
基本计划
-决定阶层构成要素 -物流及工程流程分析 -决定工厂生产率 -space 计划 -各要素间的搬运强度 /接近性评价 -各构成要素的规划分配 -评审物流设备
8.工厂布局分析与设计
yout概要 yout计划的顺序体系 yout计划的预备分析 yout分析技法 5.基本Layout计划 6.Space 计划 7.作业区域和设备的布置 yout的诊断和评价
yout概要
1)Layout 概要
Plant Layout 是指为增加设备,设施,资材,人力资源和能源使用的效率,对公司或工 厂内所有设施重新布置的一系列系统的活动 为使生产容易安全方便的进行,把4M画在图纸上
时间(T) 路径(R)
工厂Layout分析和设计

工厂Layout分析和设计工厂的Layout分析和设计一、引言工厂的布局是指在有限的土地空间内,合理部署各个生产设备和工作区域,以实现生产过程的流畅运行和最大效益。
一个良好的工厂布局能够提高生产效率,降低成本,提高产品质量,改善员工工作环境。
本文将对工厂的布局进行深入分析和设计,以期实现工厂的高效运作。
二、工厂Layout分析1. 生产流程分析首先,需要对工厂的生产流程进行分析。
生产流程包括原材料的进货、存储和加工,产品的制造和包装,以及最终产品的出货。
通过对生产流程的分析,可以找出各个工序之间的依赖关系,确定哪些工序需要紧密配合,哪些工序可以分离等。
2. 设备和材料分析接下来,需要对工厂现有的设备和材料进行详细分析。
通过了解设备性能参数和材料的特性,可以确定各个设备的工作效率和容量,以及材料的存储和运输需求。
3. 人员和物料流动分析人员和物料的流动是工厂布局设计的重要考虑因素。
通过对工人和物料的流动路径进行分析,可以确定工作区域的位置和尺寸,提高生产效率和工作环境。
4. 安全和环境要求分析最后,需要对工厂的安全和环境要求进行分析。
这包括工人的安全和舒适度要求,以及环境污染和噪音控制要求等。
根据这些要求,可以设计出合适的工作区域和设备布局,以保证员工的安全和健康。
三、工厂Layout设计根据以上分析结果,可以进行工厂Layout的设计。
以下是一些常用的工厂布局设计原则。
1. 直线流动原则直线流动原则是指物料和工人在生产过程中的流动尽量保持直线方式。
这样可以减少运输距离和时间,提高生产效率。
在设计工厂布局时,需将生产设备和工作区域按照生产流程的顺序排列,同时确保物料和人员的有效流动。
2. 同类设备集中原则相似的设备尽量集中使用,以便共享配套设施和维护资源。
这样可以节约成本,提高设备利用率。
在工厂布局设计中,应将相似的设备放置在相邻的区域,便于管理和维护。
3. 空间优化原则根据生产设备的工作面积和物料的存储需求,合理利用空间资源。
Layout系统性的厂房布局方案

ABC16
ABC16
-18-
产品及物流量从至表
至 从
原料
锯床
车床
钻床
铣床
检验
包装
成品
合计
原料
AC104
C108
212
锯床
C60
A288
343
车床
C80 AB264
344
钻床
B48
C40 A144
232
铣床
A64
ABC416
480
检验
A80
ABC192
272
包装
ABC128 128
成品
0
合计 0 104 188 252 592 560 192 128 2016
系统化厂房布置
-7-
四、物料分类及产品—产量分析
• 现象:物料种类繁多,可运性不相同。 • 问题:如何统计量一物流系统中性质、特征各不相同的物料数量?
如何区分各物料的重要等级程度? 如何确定设施布置的型式?
1、物流量的计算 (1)定义: 在一定时间内(一年或一个月)通过两设施间的物料数量。可以 用重量、体积、托盘或货箱来表示。 (2)计算方法: 方法一:当量物流量——用物料的某一特征(重量、几何形状、 装载和包装形式等)来估算物流量。 可用下式表示:
2、Q数量或产量(Quantity) 指所生产、供应或使用的材料或产品的数量或服务的工作 量。这一要素影响着设施规模、设备数量、运输量、建筑 物面积等。
系统化厂房布置
-5-
3、R生产路线或工艺过程(Route)
指根据所生产的产品品种、数量等设计出的工艺流程、物 流路线、工序顺序等,可以用设备表、工艺路线卡、工艺 过程图等表示。它影响着各作业单位之间的关系、物料搬 运路线、仓库及堆放地的位置等。