谈谈如何降低粗纱重量不匀提高半制品质量
粗纱重量不匀问题

谈谈粗纱重量不匀问题
浙江华一纺纱线有限责任公司周勇
粗纱作为前纺的最后一道工序,除了条干、波谱、毛羽等指标对细纱纱线影响大外,重不匀也是影响细纱纱线的一个重要因素。
粗纱重不匀包括单锭不匀、锭间不匀、以及更让值得注意的粗纱机里外排重量偏差等。
粗纱重量不匀率主要控制
1、由于筒管直径大小差异以及筒管孔径或底部磨灭、锭子凹槽与锭翼销子配合不良、压掌弧形或位置不当以及压掌圈数不一、锭子高低不一或因其他原因造成的锭子运转不平稳都会造成同一排粗纱伸长律的锭间差异,影响粗纱的条干。
通过波普图有时还会发现有卷绕波出现。
应加强机件和筒管日常性检修工作。
2、由于卷绕齿轮选择不当而造成的同一锭子大、中、小纱之间伸长的差异,应合理配置粗纱卷绕成形齿轮,保证一落纱大、中、小纱张力的基本一致。
此外粗纱的张力也随车间的温湿度变化而变化,这就要对张力齿轮的更换具有实时性。
3、假捻器的摩擦系数会影响成纱的毛羽量,要合理选择粗纱前后排假捻器,减少前后排粗纱张力差异,前排假捻数多于后排。
4、棉条筒的摆放。
棉条筒摆放要避免规律性发生。
比如供里排纱的棉条筒放在离机器近的位置,供外排纱的棉条筒放在离机器远的位置,这样就会导致供外排纱的棉条行程长,从而也会引起里外排纱重量不匀。
摆放的时候也得注意尽量使棉条垂直于导棉棍平面,避免倾斜。
5、导棉棍的旋转速度也要控制好。
减少棉条喂入时形成的意外牵伸。
6、梳棉并条设备的日常检查维护和试验室的质量把关。
偏差大也会导致细纱重不匀大,强力CV大等严重质量问题。
技术|如何减少纺纱过程中的纱疵

技术|如何减少纺纱过程中的纱疵随着客户对纱线质量要求的不断提高,纺纱企业必须把纱疵控制在正常的范围内,目前影响布面质量的有害疵点主要有粗节、细节、条干不匀、飞花、棉结和异常疵点等。
通过规范生产操作,注重设备维护保养、工艺调整和质量控制,可以将纱疵控制在正常范围内。
长期以来在成纱质量中,纱疵是纺纱过程中一个难以解决的重要问题,它严重影响了成纱的质量,也给后道针织和机织纱的用户造成了一定的损失。
一、纱疵分类根据纱疵出现的几率可分为常发性纱疵和偶发性纱疵。
常发性纱疵一般为棉结、短粗节和细节。
常发性纱疵短而小、小而多 ,一般对后工序的加工和织物影响不大 ,通常不易清除彻底 ,但对高档织物也必须控制常发性纱疵的数量。
偶发性纱疵通常是突然发生、覆盖面较广、危害较大,也叫突发性纱疵。
偶发性纱疵一般都表现为粗大、细长,该类纱疵大部分是由于生产管理不善、操作不良、设备完好及专件运转状态不良、工艺设计不合理所致。
该类纱疵大而少,但对后道工序和织物质量影响显著,所以必须清除。
纺纱企业常见的偶发性纱疵主要包括短粗节、棉结杂质、毛羽增加及条干类疵点。
在生产过程中,偶发性纱疵往往随某些影响因素的改变而突然出现,迅速波及生产线上的部分品种或区域,使某些质量指标出现较大幅度的波动。
偶发性纱疵的数量从总体上来说不是很多,但危害较大,往往会造成成纱、坯布质量降等,影响织机效率,因此是纺纱生产过程中质量控制的重要工作之一。
二、减少突发性纱疵的措施1、合理配置工艺参数改善半成品的内在质量减少纺部半成品纱疵可以有效地降低细纱千锭时断头率,从而提高产量,稳定成纱质量,降低吨纱成本,为提升企业产品竞争力创造有利条件。
梳棉工序:定期检查牵伸齿形带、圈条齿形带的张力状态和磨损情况,合理调整圈条张力,在减少圈条器拥堵的同时可以降低并条导条架断头的几率。
如气流纺车间前纺梳棉细支生产线改粗支生产线时,通过工艺优选,调整定量、速度与棉网张力的相互关系,减少了梳棉断头、接头的次数,提高了梳棉生产效率,既减轻了工人劳动强度,又改善了半成品条子质量。
纺纱过程中出现的问题及解决措施

纺纱过程中出现的问题及解决措施纺纱疵点及解决措施1. 纱线不匀原因:原料品质不佳、梳理不充分、牵伸不均匀、锭子质量差解决措施:采用优质原料、加强梳理、优化牵伸工艺、更换或维修锭子2. 毛羽原因:原料纤维过短、梳理不足、牵伸过度、加捻不当解决措施:选用较长纤维原料、加强梳理、调整牵伸工艺、优化加捻参数3. 太紧原因:牵伸过大、加捻过多、锭子调整不当解决措施:减少牵伸倍数、降低加捻强度、调整锭子4. 太松原因:牵伸不足、加捻过少、锭子调整不当解决措施:增加牵伸倍数、提高加捻强度、调整锭子5. 粗细不均原因:原料纤维粗细不均、牵伸不均匀、加捻不均匀解决措施:选用均匀原料、优化牵伸工艺、调整加捻参数6. 结头原因:原料中有杂质、梳理不充分、牵伸不均匀、加捻过大解决措施:去除原料中的杂质、加强梳理、优化牵伸工艺、降低加捻强度7. 条痕原因:原料染色不均匀、混纺原料不匹配、牵伸不均匀、加捻不均匀解决措施:均匀染色原料、选择匹配的混纺原料、优化牵伸工艺、调整加捻参数8. 花疵原因:原料中有杂色纤维、梳理不充分、牵伸不均匀、加捻不均匀解决措施:去除原料中的杂色纤维、加强梳理、优化牵伸工艺、调整加捻参数9. 脆硬原因:原料纤维成熟度差、梳理不足、加捻过度解决措施:选用成熟度高的原料纤维、加强梳理、降低加捻强度10. 棉结原因:原料中有棉结、梳理不充分、牵伸不均匀、加捻过大解决措施:去除原料中的棉结、加强梳理、优化牵伸工艺、降低加捻强度11. 裂口原因:原料纤维强度低、梳理过度、牵伸过大、加捻过大解决措施:选用强度高的原料纤维、加强梳理、优化牵伸工艺、降低加捻强度12. 僵硬原因:原料纤维弹性差、梳理不足、牵伸过大、加捻过度解决措施:选用弹性好的原料纤维、加强梳理、优化牵伸工艺、降低加捻强度13. 刺毛原因:原料纤维中含有短纤维、梳理不足、牵伸不均匀、加捻过度解决措施:去除原料中的短纤维、加强梳理、优化牵伸工艺、降低加捻强度14. 络筒时断头原因:原料强度低、梳理不足、牵伸不均匀、加捻不足、络筒张力过大解决措施:选用强度高的原料纤维、加强梳理、优化牵伸工艺、调整加捻参数、降低络筒张力。
技术三类粗纱常见纱疵的解决措施

技术三类粗纱常见纱疵的解决措施普梳纯棉纱纱疵多,既影响棉纱评等,又影响到布面外观、棉布内在质量和使用价值,这样不但给纱厂带来不利,也给织布生产经营带来不利,直接影响到厂家切身利益。
结合我公司普梳纯棉纱生产实践,现总结出普梳粗纱常见的3种纱疵原因及解决方法。
1 三种常见纱疵1.1粗细纬纱疵主要原因:1)并粗接头时,搭头过长、过短或包圈过紧、过松,形成粗细纬。
2)棉条、纱条所经部位(如集束器、喇叭口、锭翼通道等)不光滑,产生挂花带入纱条或条子运输过程中碰毛或棉条筒口破损形成不均匀粗细纬。
3)粗纱断头时,须条飘入相邻纱条、双纱喂入形成粗纬。
4)处理并粗绕胶辊、罗拉时,细条未拉净或断头自停装置失灵少条不停,形成细纬。
5)粗纱机后条子挂毛、掉批,值车工未及时发现,喂入粗纱,形成细纬。
6)粗纱机换牙时操作不当、卸加压时胶辊移动或开关车时的传动惯性等,形成细纬。
1.2竹节纱主要原因:1)不按操作法执行,使并、粗工序中的绒板花,喇叭口处的短绒及各种积花带入、飞花搬家等,形成绒板竹节纱。
2)并条压力棒位置不当,并粗传动齿轮啮合过松,键槽或轴孔磨灭松动产生间歇性棉网,形成竹节纱。
3)并粗胶辊表面毛糙,罗拉沟槽不光洁,有毛刺,各部分纱条通道不光洁,有粘缠、堵挂现象,形成竹节纱。
4)并粗清洁装置失灵,绒圈不转、吸风装置吸力过小、粗纱下绒板不接触罗拉或不清洁造成绒板花附入,形成竹节纱。
5)梳棉后车肚漏底未及时清扫,造成生条上车肚花进入,形成绒板纱。
6)平揩车过程中,工作不良或清洁工作不慎形成油花竹节纱。
1.3条干不匀纱疵条干不均匀纱疵分规律性条干不匀和非规律性条干不匀。
规律性条干不匀一般为突发性纱疵,主要是机械部位不良,工艺参数不当,原料波动,车间温湿度突变所致。
非规律性条干不匀主要是牵伸力大于控制力,主要原因有:1)并条集束器破损,开口过小,不光滑,导条架宽度太大,胶辊加压失效。
2)胶辊轴承缺油,并条吸风装置吸力过大。
纱线不匀解决方法

6、温湿度的影响
2021/4/8
3
解决方法
在纺纱过程中,使纤维混合均匀,严格控制牵伸工艺 完善牵伸件和传动件 避免偶然事件的的发生(比如飞花黏附、齿轮嵌花、操作不良、空调故障、棉糖黏辊 等)
2021/4/8
4
2021/4/8
5
感谢您的阅读收藏,谢谢!
2021/4/8
6
第三组
解决纱线不匀率的方法
2021/4/8
1
1、什么是纱线条干不匀率?
纱条的条干不匀常以纱条表观外径或粗细尺寸的均方差表示,或用纱条单位 长度的质量的均方差表示。其均方差系数可以比较不同线密度纱条条干不匀的程 度,称为条干不匀率。
2、检测沙线条干不匀率的方法
2.1、条干不匀的黑板检测 2.2、条干不匀的仪器检测
2.3 、偶发性条干不匀的仪器检测
2.4、2切021断/4/称8 重法
2
纱线条干不匀产生的原因
1、纱线的性质差异
2、纤维的随工艺不良 纤维混合不均匀,牵伸工艺不良等。
4、纺纱机械缺陷 由于牵伸件、传动件的缺损而产生的周期性不匀,称为机械波。
5、偶然事件引起的不匀
纺纱过程中出现的问题及解决措施

纺纱过程中出现的问题及解决措施纺纱是把纤维材料经过一系列的加工步骤之后,使其成为可以用来织造纺织品的线状材料的过程。
纺纱的过程可能会出现各种问题,这些问题会严重影响纺纱的质量和生产效率。
本文将介绍纺纱过程中常见的问题及其解决措施。
一、纤维质量不均匀纤维材料的质量不均匀会导致纺纱时出现断裂、断头、打摆等问题,影响纱线的均匀度和强度。
解决措施包括:1.对原料进行分类分级,在纺纱前先对原料进行分类分级,把质量相近的原料放在一起,以提高纤维的一致性。
2.优化纺纱工艺,在纺纱过程中采取适当的拉伸、捻合和梳理等措施,以平衡纤维的不均匀性。
3.使用预处理设备,在纺纱前使用预处理设备,比如预并条机、预并梳机等,对原料进行预处理,使得原料的质量更加均匀。
二、纱线强度不足纱线的强度不足会导致织造时易断裂,影响纺织品的质量。
解决措施包括:1.选用合适的纤维材料,增加纤维的长度和粗度,选择合适的纤维组合,以提高纱线的强度。
2.优化纺纱工艺,调整纺纱的各道工艺参数,比如拉伸倍率、捻度、卷绕张力等,以提高纱线的强度。
3.设备维护保养,定期对纺纱设备进行维护保养,保证设备处于最佳工作状态,以增加纱线的强度。
三、纺纱设备故障纺纱设备故障会导致工作中断,影响生产效率。
解决措施包括:1.设备定期保养,做好设备的定期检查和保养工作,确保设备处于良好的工作状态。
2.做好备件储备,及时更新设备备件,确保设备备件的充足,以应对突发设备故障。
3.培训员工,培训工人掌握基本的设备维修和故障排除能力,提高设备故障处理的能力。
四、能耗高纺纱过程中的能耗问题不仅增加了生产成本,同时也会对环境产生负面影响。
解决措施包括:1.更新能效设备,更新能效设备可以降低能耗,达到节能减排的目的。
2.优化工艺流程,优化纺纱工艺流程,减少能源消耗,提高能源利用率。
3.强化员工意识,加强员工节能意识教育培训,提高员工对于能源的节约利用意识。
五、产品质量不稳定产品质量不稳定会导致退货率增加,影响企业的声誉和市场竞争力。
降低粗纱重量不匀的技术措施

降低粗纱重量不匀的技术措施粗纱定量是的重要工艺参数,它的偏差大小直接影响成纱的质量。
因此只有将粗纱重量差异控制在一定范围内,才能降低粗纱及细纱的重量不匀率。
为了减少在粗纱工序引起的重量差异。
这里介绍粗纱工序的意外伸长对粗纱重量不匀的影响。
(1) 我厂粗纱机导条架基本都是高架形式,通过链条、链轮来传动,各导条辊、后罗拉之间配有很小的张力牵伸。
由于,熟条中的纤维伸直较好,纤维抱合力差,特别是精梳后的熟条,因此在粗纱机后导条过程中,因张力小不足以承受从条桶内引出时的自重张力及导条辊与导条辊之间的张力,致使棉条产生意外伸长。
将远离后罗拉的两排棉条桶称之为后排,离后罗拉近的两排棉条桶称之为前排,后排棉条的意外伸长大。
因此在日常工作中我们要加强导条架部分的维护,使导条辊运转灵活,减少后罗拉与导条辊之间的张力牵伸,降低导条过程中产生的意外牵伸,控制粗纱重量的差异。
(2) 粗纱机锭翼顶孔的边缘到前罗拉钳口的纱条部分为捻陷区,捻陷区捻度小,很容易引起纱条的意外伸长。
粗纱外排的捻陷区长,意外伸长也大。
使用假捻器增加捻陷区的捻度,增加纺纱强力,防止意外伸长,降低粗纱重量不匀。
经过以上分析,粗纱机前、机后都会产生意外伸长,我们可以通过合理搭配缩小粗纱之间的意外伸长。
搭配的方式:粗纱的后排的棉条对应里排的粗纱,前排的棉条对应外排的粗纱,以此减少粗纱之间的意外伸长。
我们在a454型粗纱机上对c/t53.2tex、c9.7tex等品种进行试验,采用两种方案进行试验,方案一:粗纱机后排并条对应纺里排粗纱、前排并条对应纺外排粗纱。
方案二:粗纱机前排并条对应纺里排粗纱、后排并条对应纺外排。
两种方案的重量差异见表1 表1两种方案的重量差异比较经过试验证实,合理搭配后方案一的粗纱重量偏差较小,控制在2%以内方案二的重量偏差超过2.5%,最大时达到5.99%。
方案一在并条重量偏差较大时,效果更是明显。
实际生产中在其他条件相同的情况下,经过合理搭配的机台的粗纱重量偏差小且稳定,对粗纱重量不匀率起到了良好的控制效果。
技术|粗细节、条干不匀等五大常见疵点的影响、成因及改善措施

技术|粗细节、条干不匀等五大常见疵点的影响、成因及改善措施对于纯棉精梳细号纱线,从危害程度和发生频次看影响布面质量的有害疵点主要是粗细节、条干不匀、飞花、棉结和异常疵点。
这些疵点对后工序有哪些影响?影响布面质量的有害疵点01粗细节粗节,布面表现为一个突出的粗节,影响织物外观,甚至造成布面降级。
布厂可以通过人工挑修改善外观,但是挑修操作困难、费时费工;细节,因为比正常纱细,就会形成纱线强力弱环,造成准备和织造过程的断头,影响准备和织造的效率,即使未发生断头在布面表现为细于正常纱的疵点,且无法修复,数量多时会造成布面降级。
02条干不匀影响织物外观,造成布面降级,特别严重时在织物布面表现为条影或木纹,较轻的情况下布面外观浑浊、不光洁似有云斑,条干不匀还会造成染色不匀。
03棉结布面表现为棉点或白星,星星点点分布在布面上,影响织物外观。
布厂可通过人工挑修来降低棉点,但数量过多时挑修不能达到良好的效果,而且费时费工。
此类疵点较多或较大时在准备、织造中纱线断头率会增加,影响准备织造效率,影响织物外观及平整,造成布面降级。
04飞花布面表现介于粗节和大棉结之间,比粗节短、纤维松散,影响布面光洁程度。
通过人工挑修可得到改善。
异常疵点多表现为长片段,发生频率低,如单纱中的双线纱,股线中的三股纱和四股纱等,以及长粗节、长细节。
此类疵点严重影响织物外观,造成布面降级,制衣厂一般都需要做避裁处理,会降低布的利用率。
更严重时甚至会延误订单的交期,赔偿客户的损失。
不同的布种对纱线的质量要求可以看出纱线疵点对后工序尤其是织物的布面效果有较大影响。
从布厂的产品种类看,不同的布种对纱线的质量要求也不同。
a)净色布种(经纬纱线同色或不同色的平纹织物):根据经纬颜色的反差大小,对纱线的棉结要求不同,经纬颜色反差越大,对棉结要求越高,尤其经特殊后整理的布种对粗节、棉结要求更高。
b)米通条布种(经向、纬向或经纬两方向相邻纱线颜色不同的织物):纱线颜色反差越大,对粗节、棉结和条干均匀度的要求越高。
操作管理是降低纱疵提高实物质量的关键
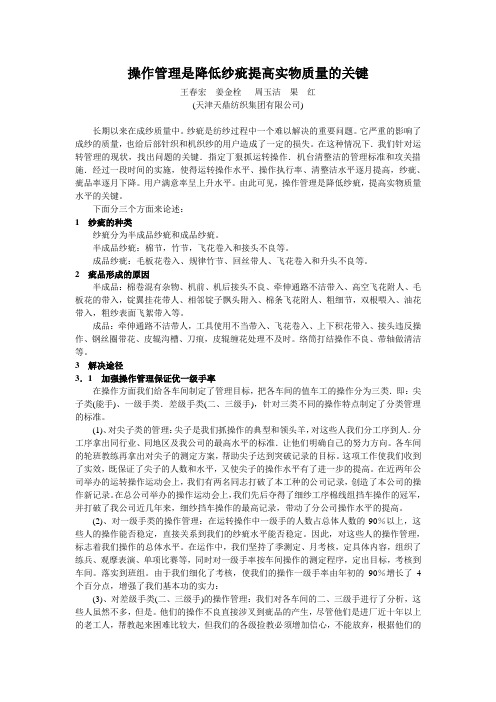
操作管理是降低纱疵提高实物质量的关键王春宏姜金栓周玉洁果红(天津天鼎纺织集团有限公司)长期以来在成纱质量中。
纱疵是纺纱过程中一个难以解决的重要问题。
它严重的影响了成纱的质量,也给后部针织和机织纱的用户造成了一定的损失。
在这种情况下.我们针对运转管理的现状,找出问题的关键.指定丁狠抓运转操作.机台清整洁的管理标准和攻关措施.经过一段时间的实施,使得运转操作水平、操作执行率、清整洁水平逐月提高,纱疵、疵品率逐月下降。
用户满意率呈上升水平。
由此可见,操作管理是降低纱疵,提高实物质量水平的关键。
下面分三个方面来论述:1 纱疵的种类纱疵分为半成品纱疵和成品纱疵。
半成品纱疵:棉节,竹节,飞花卷入和接头不良等。
成品纱疵:毛板花卷入、规律竹节、回丝带人、飞花卷入和升头不良等。
2 疵品形成的原因半成品:棉卷混有杂物、机前、机后接头不良、牵伸通路不洁带入、高空飞花附人、毛板花的带入,锭翼挂花带人、相邻锭子飘头附入、棉条飞花附人、粗细节,双根喂入、油花带入,粗纱表面飞絮带入等。
成品:牵伸通路不洁带人,工具使用不当带入、飞花卷入、上下积花带入、接头违反操作、钢丝圈带花、皮辊沟槽、刀痕,皮辊缠花处理不及时。
络筒打结操作不良、带轴做清洁等。
3 解决途径3.1 加强操作管理保证优一级手率在操作方面我们给各车间制定了管理目标,把各车间的值车工的操作分为三类.即:尖子类(能手)、一级手类.差级手类(二、三级手),针对三类不同的操作特点制定了分类管理的标准。
(1)、对尖子类的管理:尖子是我们抓操作的典型和领头羊,对这些人我们分工序到人.分工序拿出同行业、同地区及我公司的最高水平的标准.让他们明确自己的努力方向。
各车间的轮班教练再拿出对尖子的测定方案,帮助尖子达到突破记录的目标。
这项工作使我们收到了实效,既保证了尖子的人数和水平,又使尖子的操作水平有了进一步的提高。
在近两年公司举办的运转操作运动会上,我们有两名同志打破了本工种的公司记录,创造了本公司的操作新记录。
降低粗纱重量不匀率的实践

2 5 粗 纱 工 序 .
车 , 车第 一个棉 卷应 为退 卷 , 绝 由供棉不 良而 开 杜 产生 质量波 动 ; 确保 圆盘 内原料 横 向 、 向密度均 纵 匀一 致 , 以提高 下机正 卷率 。 ( ) 过试 验 , 长 率 控 制 在 1 5 以 内 时 , 5通 伸 .%
棉卷 重量不 匀率 较好 。 2 2 降低 生条 重量不 匀率 .
棉 卷 辊要按 时加 油 , 防止棉 卷辊处 于滞 后状 态 ; 其 次生 头时 , 值车 工可用 手转 动棉 卷辊 帮助加 速 , 使
之快 速达 到平衡 状态 ; 最后 , 值车 工在棉 卷 生头 时
要用 专用生 头板 生头 。 () 4 供棉 不足 或上包 时 ( 未装 多仓 ) 应立 即关
( ) 纱 工 序 。无 论是 前 后 排 , 是 台与 台 5粗 还
3 ; 0 g 三是值 车 工 自行 调整 质量 之 间 的差 异 ; 四是 每盘 花包 头与 包底 质 量 差 异 大 ; 五是 棉卷 伸 长 率
的差 异大 。
作 者 简介 : 贺梅 (9 5 ) 女 , 理 工 程 师 , 阳 , 100 17 一 , 助 咸 7 20 收稿 日期 :0 10 -3 2 1 -91
HeM e Zh n u s e g i a gJ nh n
( h a x B fn e teC . L d ) S an i a gT x l o , t . a i
Abs r t To rdu e r vn i h e e n sa d i t ac e c o ig weg tun v n es n mprveis p s a e,a t r fef ei g rvig weg ne e o t a s rt f co so fe tn o n ihtu v n— he s we e a ay e i cud n n v nn s flp, ad sie , o s r n lz d,n l i g u e e e s o a c r lv r c mbe lv r, a sie r vng tnso e e n s , ・ d sie drw lv r,o i e in un v n e s me
贯彻新国标降低涤棉纱重量不匀率和纱疵的初步经验

。
因此 我们 从 8 7 年开 始进 行 了全 面 试 8 年 元 月开
,
,
套 始
G
。
2 月 同年 1
13e t
x
通 过 了 省轻 工 业 厅
、
,
省标 准计 量 局 的 采 用 国 际标 准 的验 证确 认
,
,
涤棉 纱 用 G B 5 3 2 4 一 8 5 进行 定 等考 核
的 复 审稿
。
9 年元 月起 我 厂 生 产的所 有 精梳 涤棉纱 采 用 8
,
在提 高 涤棉纱 质 量 中我 们 着重 在降 低 重 蚤 现将 我们 的 初 步做 法介 绍如 下
不 匀率 和 减 少 十万 米纱 疵 中做 了 一 定 工 作取 得 了 一定 成 绩
~
食
.
严 格控 制
浙 江省 涤棉 8 9 标 准 试 套 统计 情 况
1一 9
,
,
降低 盆 , 不 匀 率
,
降 等 的 第一大 因 素
x
B 5 3 2 4 一8 9
进 行定 等
,
。
1一 9 月 份
13 t e
0 纱 的 优等 品 率 达 到 5 % 纱和 2
一 等 及以
,
上 品 率 达 到 9 9%
回 顾 半 年多 来 的 工作
我 们 深 深 体 会到
,
,
要执 行好 新标 准
、
,
促 进产 品 质 量的不 断提 高
、
在 思 想 上 要 牢 固树 立 质 量 第一 观 点 项 基 础管 理 工 作 作不放 松
,
、宁
正 常 的半 制 品 混入 下道 工序
如何控制棉纱锭差

如何控制棉纱锭差棉纱锭差是指在棉纱纺织过程中,由于原料质量、生产设备、工艺参数等因素引起的纱线质量不均匀现象,表现为棉纱锭的纱线粗细不一致。
要控制棉纱锭差,提高纺织品的质量和降低生产成本,需要从以下几个方面进行控制:1.原料选择与质量控制确保原料的质量稳定和纤维长度的一致性,采用统一的采购标准,严格把关原料的进货质量。
在起毛前对原料进行分类和分级,分选出纤维长度较短、杂质较多的纤维进行二次利用或混纺。
此外,可以采用化学处理方法,如苛洗、漂白等,来优化原料质量。
2.生产设备的维护与升级定期对纺纱设备进行维护,确保纺纱设备的稳定性和正常运转。
及时更换损坏的部件,对关键设备进行定期检修和保养,保证设备的工作质量和生产效率。
对老化、低效的设备及时进行淘汰和升级,引进先进的工艺和设备,提高纺纱效率和产品质量。
3.工艺参数的优化通过调整和优化纺纱过程中的关键工艺参数,如筛选机的排棉速度、蒸汽对纱的温度和湿度、牵伸力等,来改善棉纱锭差问题。
合理设置纺纱机的工作速度、张力、风压等参数,保证纱线质量的稳定性和一致性。
通过控制牵伸力、检控等手段,提高纱线的紧密度和一致度。
4.生产过程的监控与调控建立完善的生产过程监控系统,利用先进的仪器设备对生产过程进行实时监控和数据采集,及时发现异常情况,快速做出调整。
通过设置报警阈值、定期检测和分析纺纱质量数据,及时发现问题,并制定解决方案。
同时,制定适当的生产计划和排产安排,避免产能过剩和压力过大的情况,以保证生产的稳定性和高效性。
5.人员培训与管理加强对纺纱工人的技能培训,提高他们的操作技能和质量意识。
通过定期培训和考核,提高纺纱工人对纺纱质量控制的理解和应对能力。
加强对工人的管理,确保纺纱过程中的各项操作符合规范,并制定奖惩机制,激励工人积极参与质量控制工作。
综上所述,控制棉纱锭差需要从原料选择与质量控制、生产设备的维护与升级、工艺参数的优化、生产过程的监控与调控以及人员培训与管理等方面进行综合控制。
纱线主要疵点成因分析与改善措施

纱线主要疵点成因分析与改善措施对于纯棉精梳细号纱线,从危害程度和发生频次看影响布面的有害疵点主要是粗节、细节、条干不匀、飞花、棉结和异常疵点。
为切实满足客户的要求和控制质量成本,纺纱厂必须找到纺纱生产过程中形成这些疵点的原因,并采取有效的措施控制降低疵点,从而提高纱线的质量。
粗节、细节1成因常见的布面粗节长短不等:1 cm~2 cm居多,中间粗两头渐细,大多为细纱牵伸不良、牵伸区周围游离飞花附入、粗纱条干片断不匀、粗纱疵点附入、络筒清纱参数设置不当等原因造成;少部分为细纱接头不良或络筒机捻结不良造成。
细节主要是由细纱牵伸不良和络筒捻结不良造成。
2措施对于细纱牵伸不良引起的粗节、细节,可从以下四方面预防和解决:a)降低粗纱捻度,即在不增加断头的前提下尽量采用小的粗纱捻度;b)保证细纱和粗纱牵伸元件状态良好,保持适当的胶辊研磨周期、胶圈更换周期,并随时检查是否有起槽、划痕等问题,随时解决;c)保持恒定的温湿度,避免出现短时大幅度的波动;d)优化细纱工艺,主要是隔距、上销位置和摇架压力的一致性。
对于细纱纺纱过程中产生的粗节和细节,只能利用络筒清纱器切除,这样会引起清纱器切次的增加,需要特别关注捻接质量避免因捻接不良二次形成粗节和细节。
条干不匀1成因布面呈现有规律或无规律的条干阴影;主要因牵伸元件(胶辊、胶圈、罗拉)运转失常、表面毛糙凹凸、胶辊缠花纺纱及落后锭子等纺纱专件异常造成。
2措施牵伸区工艺优化、保持良好的胶辊胶圈状态;控制好单并与粗纱的号数偏差和条干均匀度,发现异常及时隔离;及时修理细纱的坏锭及异常锭,要求挡车工走巡回遇到胶辊、胶圈、罗拉等异常情况及时报告并通知相关人员处理。
在络筒机上对清纱器设置支数变异和珠链纱疵剪切和报警参数,可切除疵点并剔出有问题的管纱。
飞花1成因纺纱生产中因清洁不及时、集棉装置故障、断头急剧增加、空调温湿度异常或气流不畅等情况引起机台上、地面和空气中飞花增加并集聚,纺纱时附入到纱体中形成飞花疵点。
学习控制细纱质量、降低细纱不匀,看这一篇就够了!
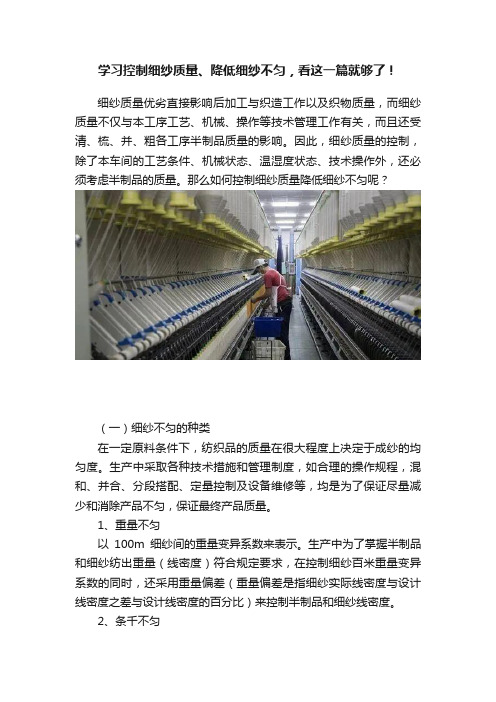
学习控制细纱质量、降低细纱不匀,看这一篇就够了!细纱质量优劣直接影响后加工与织造工作以及织物质量,而细纱质量不仅与本工序工艺、机械、操作等技术管理工作有关,而且还受清、梳、并、粗各工序半制品质量的影响。
因此,细纱质量的控制,除了本车间的工艺条件、机械状态、温湿度状态、技术操作外,还必须考虑半制品的质量。
那么如何控制细纱质量降低细纱不匀呢?(一)细纱不匀的种类在一定原料条件下,纺织品的质量在很大程度上决定于成纱的均匀度。
生产中采取各种技术措施和管理制度,如合理的操作规程,混和、并合、分段搭配、定量控制及设备维修等,均是为了保证尽量减少和消除产品不匀,保证最终产品质量。
1、重量不匀以100m细纱间的重量变异系数来表示。
生产中为了掌握半制品和细纱纺出重量(线密度)符合规定要求,在控制细纱百米重量变异系数的同时,还采用重量偏差(重量偏差是指细纱实际线密度与设计线密度之差与设计线密度的百分比)来控制半制品和细纱线密度。
2、条千不匀细纱的条干不匀代表细纱短片段粗细差异程度。
细纱按规定绕在黑板上与标准样照对比观测十块黑板所得的结果,即代表细纱短片段的条干质量;或用条干均匀度试验仪测出条干不匀率,简称条干CV值。
3、结构不匀细纱结构上的差异称为结构不匀。
如细纱横截面或纵向一定区域内纤维的混和不匀、批与批之间原纱色调不一以及由于条干不匀而引起的捻度不匀等,都属于细纱结构不匀。
细纱的重量不匀或条干不匀,当用仪器测试时,常表现一种波动形态,具有一定的波长和波幅。
当产品的不匀波形接近周期性波动时,通常称周期性不匀。
如由于罗拉或皮辊偏心、齿轮啮合不良所形成的不匀,其波形表现为周期性的波动,且具有相近的波长和波幅。
周期性的不匀在成纱制品中若波形较短,在数十毫米以内的不匀常影响产品的条干均匀度;若波形较长,如几十米或更长片段,这种不匀影响产品的重量不匀率。
由随机性或偶然性因素所形成的不匀波形,常没有明显规律,这种不匀称非周期性不匀。
深度分析如何控制细纱质量降低细纱不匀

深度分析如何控制细纱质量降低细纱不匀细纱是目前纺织品市场上一种非常重要的原材料,它不仅应用于纺织品、服装等领域,还用于医疗卫生、建筑、汽车等各个行业。
然而,由于细纱本身的特殊性质,其制作过程中很容易出现不匀的现象,这不仅影响到纱线的质量,更会对下游产品的品质产生很大影响。
因此,如何控制细纱质量并降低细纱不匀已成为纺纱生产中的一个重要课题。
一、分析细纱质量与不匀的原因在制作细纱时,出现不匀现象的原因主要有以下几个方面:1.纤维不均匀纤维是制作细纱的原材料,如果纤维本身就存在一定的不均匀性,那么在制作细纱的过程中就很难保证纱线的均匀度。
例如,在制作棉纱时,由于棉质纤维可以从不同的地区采集而来,其颜色、长度和粗细等方面的差异就很大,如果对这些纤维不进行组合,那么细纱的均匀度就会受到影响。
2.纺纱工艺的问题另外,细纱的不匀还与纺纱工艺的水平有很大关系。
纺纱工艺中使用的设备和机械很可能存在生产制造方面的差异,这些差异包括设备的型号、大小、质量、维护情况等等,这些都会对细纱的质量和均匀度产生影响。
3.质量控制的不严格还有一种可能是因为生产厂家对细纱的质量把控不够严格,或者是因为规定不严格、执行不力等原因导致细纱的不匀。
二、如何控制细纱质量降低不匀1.采用质量最优的原料为了避免纤维本身的不均匀性对细纱的影响,我们需要选择质量最优的纤维,这样能够增加细纱的均匀度。
同时,还需要注意不同纤维种类之间的组合,这样也能够降低纱线不匀的可能性。
2.加强纺纱工艺面对工艺的不同问题,我们可以尝试加强纺纱工艺的管理和规范,包括对设备的维护保养、质量的检测和控制等方面的严格管理。
这样可以通过调整喷气力、旋转速度等因素,使细纱质量得到有效的提升。
3.完善质量控制标准为了确保细纱能够达到质量要求,我们可以逐步完善质量控制标准,规范生产流程,做到质量口径统一,依据科学的质量管理理念进行精确的质量控制,从而达到降低细纱不匀的目的。
三、结语细纱是目前市面上非常重要的纺织品原材料,其制作过程中很容易出现不匀的现象。
降低成纱重量不匀率

降低成纱重量不匀率、减少成纱棉结、杂质成纱重量不匀率,也称为特数不匀率。
实际上都是表示成纱长片段之间的重量不匀。
重量不匀率的大小,不仅关系到成纱的强力不匀、品质指标,以及细纱车间的断头多少,而且与织物的质量、织造的工艺都有密切关系。
要降低成纱重量不匀率空白文化衫,除细纱工序外,更重要的是在前纺各工序中注意以下几方面。
(1)提高梳理前道半成品的均匀度。
’(2)降低生条重量不匀率。
(3)降低熟条重量不匀与重量偏差。
(4)控制粗纱重量不匀率。
(5)细纱工序应注意的问题。
细纱工序和粗纱工序一样,主要的问题是防止重量不匀的恶化。
为此应注意以下三个方面的工作。
(1)同一品种应使用同一机型,尽可能做到所有变换齿轮(包括轻重牙)的齿数统一。
(2)值车工加强巡回,将不合格的粗纱(过粗或过细、接头不良)及时摘去或换下,并正确使用粗纱机上的前后排粗纱。
(3)加强保全、保养及维修工作文化衫印刷,特别要加以注意的是胶辊、胶圈的回转灵活性,罗拉加压可靠性。
(1)合理配置原棉。
原棉的成熟度系数与成纱中的棉结数几乎成直线的负相关关系,因此配棉时合理控制原棉的成熟度系数是非常重要的,且其值一般控制在1.56~1.75为宜。
另外,原棉中僵棉、软籽表皮等疵点极易造成染色过程中的白星,所以亦应严格的控制。
短绒率的控制也是配棉中的重要问题,因为短绒不但影响条干、强力,而且也是形成棉结的主要因素。
(2)选择合理的清、梳工艺,减少棉网棉结、杂质。
棉网结杂粒数与成纱结杂粒数关系密切,因此如何减少棉网结杂数、提高梳棉机的分梳效果对控制成纱结杂是非常关键的。
然而,梳棉机分梳、除杂作用的好坏,除与梳棉机本身的机械状态有关外,很大程度上还依赖棉卷结构质.广告衫。
纺织工艺设计与质量控制-提高成纱粗细均匀度

1 n
CB0 ( L)2
K 2 (E 1)2 E2 N
CB2(L) CB1(L)
对于纱条的牵伸与并合,纱条的并合作用在进行牵伸以后进 行比较合适,可以得到长片段较均匀的纱条。对于短片段不
匀率来说,采用先牵伸后并合的方式也是比较有利的。
4 纺纱机械中的机件缺陷对纱条条干的影响
4.1 罗拉钳口(握持点)移动
牵伸波是一个波长和波幅不断变化的准周期波。
(2)影响牵伸波的因素
喂入须条中捻回分布的变化;
在保证细纱后区正常牵伸的条件下,适当增加 粗纱捻系数。
喂入须条中纤维的状态(如缠结、弯曲和 排列形态等);
须条中纤维的伸直平行度差时,就可能形成牵 伸波
纱条中纤维长度分布差异; 纱条中结杂含量等。
阻力加大等。
又如胶辊压力不足、有飞花附入或缺油等 造成的胶辊回转阻力加大等。
第二节 提高纱条条干均匀度
1 合理选配纺纱原料
1.1 纺纱原料性能对成纱条干的影响
1.1.1 纤细度对成纱条干的影响
如取纱条截面中的纤维平均根数为n,则由于成纱各个截面内纤 维根数分布不匀造成的成纱截面不匀的变异系数为:
3.2.2 牵伸倍数、并合数与纱条长片段不匀的关系
牵伸机构对纱条产生的长片段不匀率附加值用下式
(5-8)表示:
CBD (L)
K (E 1) EN
(5-8)
式中:CBD(L)—牵伸机构对纱条片段长 度L所产生的纱条长片段不匀率附加值;
E—牵伸装置的牵伸倍数;
N—喂入牵伸装置的纱条公制支数;
K—经验常数(棉纺工程中K的取值范围: 并条机4.8,粗纱机10.5,细纱机42).
但当具有潜在不匀的纱条经过下道工序 的高倍牵伸后,如不考虑纤维浮游运动 的影响,则纤维头端排列的周期波长λ值 将以相同于牵伸倍数的比例增加,此时 由于L/ λ减小,会使R/r值增大。说明经 过牵伸后潜在不匀将愈来愈显著地反映 到纱条的实际不匀上来。
降低普梳纱质量不匀率的实践
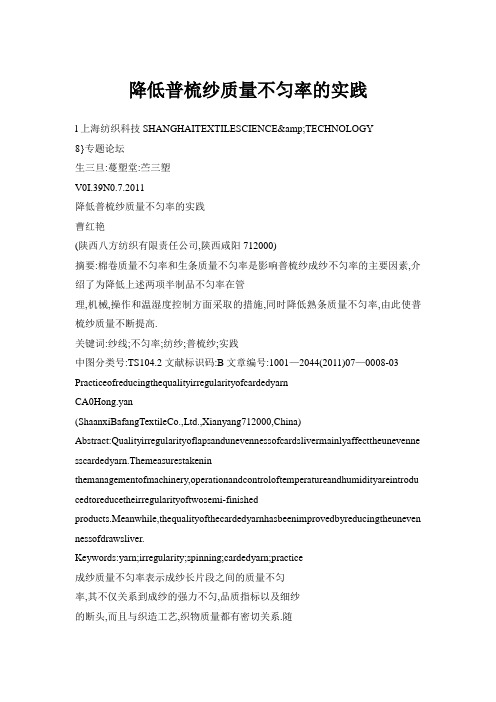
降低普梳纱质量不匀率的实践l上海纺织科技SHANGHAITEXTILESCIENCE&TECHNOLOGY8}专题论坛生三旦:蔓塑堂:苎三塑V0I.39N0.7.2011降低普梳纱质量不匀率的实践曹红艳(陕西八方纺织有限责任公司,陕西咸阳712000)摘要:棉卷质量不匀率和生条质量不匀率是影响普梳纱成纱不匀率的主要因素,介绍了为降低上述两项半制品不匀率在管理,机械,操作和温湿度控制方面采取的措施,同时降低熟条质量不匀率,由此使普梳纱质量不断提高.关键词:纱线;不匀率;纺纱;普梳纱;实践中图分类号:TS104.2文献标识码:B文章编号:1001—2044(2011)07—0008-03 PracticeofreducingthequalityirregularityofcardedyarnCA0Hong.yan(ShaanxiBafangTextileCo.,Ltd.,Xianyang712000,China)Abstract:Qualityirregularityoflapsandunevennessofcardslivermainlyaffecttheunevenne sscardedyarn.Themeasurestakeninthemanagementofmachinery,operationandcontroloftemperatureandhumidityareintrodu cedtoreducetheirregularityoftwosemi-finishedproducts.Meanwhile,thequalityofthecardedyarnhasbeenimprovedbyreducingtheuneven nessofdrawsliver.Keywords:yarn;irregularity;spinning;cardedyarn;practice成纱质量不匀率表示成纱长片段之间的质量不匀率,其不仅关系到成纱的强力不匀,品质指标以及细纱的断头,而且与织造工艺,织物质量都有密切关系.随着2007乌斯特公报的发布,对成纱各项质量指标的要求都大幅提高.特别是喷气织机的广泛运用和稀薄织物的开发,对成纱单强不匀率及质量不匀率提出了更高的要求.通过实践找出了影响成纱质量不匀率的主要因素,并落实了一系列措施,使各品种的成纱质量不匀率持续降低,从原来2007乌斯特公报的50%水平提升为5%水平.现以纯棉普梳纱为例介绍如下.1影响半制品质量不匀率的因素实践证明,要降低成纱质量不匀率,除调控好原料外,控制好半制品的质量不匀率尤为重要,前纺各工序特别要注意降低棉卷,生条,熟条和粗纱的质量不匀率及其质量偏差.因此,笔者通过实践,从工艺,操作,设备等方面对各工序的影响因素进行了分析.1.1棉卷质量不匀率的影响因素棉卷质量不匀率分为纵向不匀和横向不匀,在生产中以控制纵向不匀为主.生产实践证明,棉卷的正卷率,每米质量不匀率与成纱的质量不匀率关系密切.因此,要降低成纱质量不匀率,首先要从提高棉卷均匀度着手.影响棉卷正卷率和质量不匀率的因素:一是定量供应不足或混棉不匀造成棉卷内部每米间的质量收稿日期:2011-O1—24作者简介:曹红艳(1975~),女,陕西咸阳市人,主要从事纺织质量检测及控制研究.差异较大;二是棉卷逐个称量后值车工根据称取的棉卷质量差异情况,自行调整清棉自调匀整装置,调整范围的掌握不够准确,往往会使棉卷前后段之间,棉卷之间的质量产生较大的波动;三是棉卷生头不良,造成棉卷头1~2in棉层质量范围差异达1O一30g;四是上满包或圆盘清底时的棉卷质量差异较大,值车工把关不严,流入梳棉工序;五是温湿度影响,通常质量控制范围固定,不随温湿度的变化调节,因而,温湿度过小,棉卷回潮小,棉卷实际干质量偏大;反之棉卷实际干质量偏小.另外,温湿度的变化还影响棉层密度的变化,会给控制棉卷均匀度带来一定的困难.1.2生条质量不匀率的影响因素生条质量不匀率除受棉卷影响外,还受梳棉机各机台落棉的差异,机械状态不良及运转操作不当的影响.梳棉机机械状态不良或温湿度波动造成的棉网破洞,烂边,小漏底积花,刺辊返花等都会造成生条质量不匀.梳棉值车工操作不当也会影响生条质量,一是梳棉机开关车前后一段时间内的条子定量有波动,值车工未清除或清除不彻底,从而引起生条质量不匀率增大;二是值车工更换棉卷不及时或由于操作不当而造成接头不良,从而引起生条定量的变化.1.3并条机的作用并条工序质量波动的原因除生条影响外还有:一是个别试验工经验不足,调换并条机牙齿不到位,使并条质量不匀率增大;二是并条机机后断头自停失灵或吸风过量,将部分条子吸入风洞,造成条子过轻.粗纱机台与台之间质量差异大.兰!!主三旦:篁堂:蔓!塑V01.39NO.7.20112降低纯棉普梳纱成纱质量不匀率的措施2.1提高下机正卷率.降低棉卷质量不匀率要保证成纱质量不匀率稳定降低,清花工序棉卷质量不匀率应控制在1.0%以内,下机正卷率达到99%以上.(1)充分发挥清棉机控制机构的均匀作用.在做好配棉,原料接批和加强开清棉机械开松混合的基础上,调节好各储棉箱的储棉量.A092A型双棉箱给棉机中储棉箱摇板的开关角度和摆动决定棉箱存棉密度的松紧和棉箱内棉量的差异限度,要保证其角度准确; 各光电控制装置也要灵敏和准确;保证均棉罗拉与角钉帘隔距及角钉帘速度的合理配置,充分发挥匀棉机构的作用,保证各储棉箱储棉均匀.通过调节尘笼和综合打手转速以及尘笼两侧吸风口的位置和风量,控制好尘笼凝棉.在A076C型单打手成卷机上,充分发挥天平调节装置的作用,对给棉箱给棉棉层厚度的变化及棉层密度的变化有预见性地进行调节,把好棉卷均匀度的最后一道关.(2)做好定量供应,提高单机运转率.要保证棉卷均匀,必须解决好原料输入,机内定量和筵棉输出的关系.均匀的原棉供应量取决于各个机台运转率的正确配合,靠一系列控制原棉容量的机构及单独控制的喂给机构来保证.在单位时间内,整套开清棉联合机所有各机台的出棉量必须与制成棉卷的定量保持一定的关系,要使喂人量略大于输出量.除应考虑后面机台的落棉量外,再加上5%~10%的安全系数,尽可能提高棉箱机械的运转率.在开清棉联合机组中主要要控制好以下机台的运转率,即抓棉机85%,混棉机90%,豪猪开棉机95%.运转率高,可减少因给棉机械停动而引起的出棉量波动,从而获得较均匀的棉卷. 在原棉密度,产量以及工艺参数调整后,要及时测定机台运转率,若不合要求,需及时调节有关参数,如速度, 隔距,棉箱的厚度等,以保证供给机台之间的产量平衡.为更好做到定量供给,还必须保证开清棉联合机的联动装置反应灵敏,在棉箱内棉量充满或不足时,立即通知后方机台停止给棉或及时给棉.(3)操作注意事项:一是抓棉值车工做到排包均匀,高度一致,定量混用,这是保证棉卷均匀的前提;二是成卷值车工合理掌握棉卷定量,熟练调节天平调节装置,特别是加强圆盘清底或上满包时的调试工作,并保证疵卷不流人梳棉工序;三是成卷值车工要定时加SHANGHAITEXTILESCIENCE&TECHNOLOGY上海纺织科技l 专题论坛l9油,保证棉卷轴卷取及生头正常,保证棉卷生头质量;四是加强对新进人员的操作培训.(4)控制好车间温湿度,使棉卷回潮率趋于稳定,一般温度控制在23%一29%,相对湿度控制在60%一67%.温湿度的控制还必须结合室外环境气候.2.2降低生条质量不匀率实践表明,生条质量不匀率对成纱质量不匀率的影响占纺纱工艺全部过程影响的一半以上.生条的质量不匀率一般应控制在3.5%以下.(1)定期平揩车,整顿梳棉机机械状态,统一梳棉机工艺参数,保证工艺上车.在平车和重点检修时还应注意以下问题:一是刺辊齿条的锋利度,新换的刺辊因齿条锋利,握持作用强,落棉率低,应相应调整工艺,保证落棉率;二是小漏底入口隔距,除尘刀的高低位置和安装角度,前上罩板上口与锡林针面的隔距要准确;三是保证除尘装置吸风状况良好.吸落棉风力不足时单机台的质量差异会增大.(2)指定专人定期逐台试验落棉率,及时调整,减小落棉差异.将落棉合格率作为车间的一项大指标,提高对其的重视度.(3)严格操作规程,特别是加强新进人员的操作培训,防止在换卷和生条接头时造成接头不良.(4)控制好温湿度,防止黏卷,棉网破洞,烂边.2.3降低熟条质量不匀率与质量偏差棉条的定量控制和调整范围有两种,一是单机台各眼棉条的控制,另一种是同一品种全部机台棉条定量的控制.全机台的定量控制是为了控制细纱的质量偏差,使细纱在少调或不调牵伸齿轮的情况下,所纺纱的特数符合国家规定的标准.单机台的定量控制能及时消除并条机各机台间纺出定量的差异,既有利于降低棉条和细纱的质量不匀率,又有利于降低细纱的质量偏差.生产实践证明,严格控制单机台棉条的质量差异,对于减少全机台棉条的质量偏差,降低棉条质量不匀率效果明显.生产实验证明,若单机台棉条定量差异控制在±1%以内,则该品种所有机台棉条定量差异一般可在±0.5%,此时细纱的质量不匀率就能稳定在1.5%以下.要做好定量控制工作,除周期试验,严格操作规程外,关键是要做好牵伸变换齿轮的调节工作.调换牙齿应注意以下问题:一是单机台调牙时,应控制末并同一品种各机台间牵伸变换齿轮的差异不能多于冠牙3I上海纺织科技SHANGHAITEXTILESCIENCE&TECHNOLOGY 10l专题论坛个齿,尽量控制在2齿以内;二是遇"野格林"或温湿度波动,应注意追踪,具体情况具体对待,若温湿度波动,应在其正常后进行复试,视具体情况决定调牙与否;三是并条调牙要掌握好调换幅度,以免引起细纱质量不匀的变化;四是由于操作或机台运转不正常,造成同一台并条机单眼棉条过轻或过重,可将两眼机后条进行调换再复试,依复试结果查原因或调换牙齿;五是目前采用的这种测试调整方法,由于不是积极主动的调节方法,而是事后的补救措施,不但存在调整滞后现象,而且会因特殊情况的分析不准确而造成调整错误. 因此,在生产稳定的情况下,以少调变换齿轮为宜. 2.4控制好粗纱质量不匀率除改变品种外,粗纱的牵伸变换齿轮一般是不调整的.因此,粗纱对于由并条带来的质量偏差和质量不匀率是不易改变的.在粗纱工序要力求熟条的指标不恶化或少恶化.这主要是靠合理调节粗纱张力,严格控制粗纱伸长差异来实现:一是按一定周期对粗纱伸长率进行测试与调整,粗纱不允许有负伸长,最大伸长率不应超过3%,同一品种的平均粗纱伸长机台间差异不应超过1%;二是减少大,小纱之间的伸长差异,同一台车大,小纱伸长差异不应超出1%;三是减小前后排粗纱伸长差异,粗纱机机后后排熟条供后排粗纱,前排熟条供前排粗纱;四是加强经常性的维修工作,实行锭子与锭翼对号制度,不合规格的筒管应及时修理或报废,减少各种原因引起的锭子运转不平稳现象,从而减少锭间粗纱伸长差异.圭三旦:苎塑堂:蔓三塑V01.39N0.7.20112.5细纱工序应注意的问题细纱工序主要是防止质量不匀的恶化.一是同一品种应采用同一机型,同一品种轻重牙不能超过两种牙齿;二是值车工加强巡回,将不合格的粗纱及时换下;三是加强保全,保养及维修工作,特别是胶辊,胶圈的回转灵活性,罗拉加压的可靠性,这些都会因"野格林"的产生导致质量不匀,必须重视.3成纱质量不匀率改善情况C19.5W成纱质量不匀率2007年全年平均值为1.3%,比2006年下降了0.2个百分点.质量不匀率从2007乌斯特公报的50%水平上升到25%水平.2009年全年平均值为1.1%,又比2007年下降了0.2个百分点,质量不匀率从2007乌斯特公报的25%水平上升到5%水平,且一直较稳定.4结语(1)在选用,调控好原料的基础上,优选工艺参数,保证清花单机运转率,发挥好均匀机构的作用,控制好梳棉的落棉率.(2)增强新进人员的操作培训及质量把关意识.(3)加强设备状态的维修管理.(4)根据温湿度的变化加强棉条定量的调控.参考文献:[1]李先登.纱线重量不匀率降等的控制和实践[J].上海纺织科技,1996,24(4):18—19.[2]王俊英,王树英.控制生条质量不匀率新方法的实践[J].上海纺织科技,2007.35(4):39—40."正家"牛奶蛋白纤维上海正家牛奶丝科技有限公司的专家们付出多年心力,科技攻关,致力于改良纤维并已为国际纺织行业中树立了一个新的里程碑——"正家牌"牛奶蛋白纤维.牛奶蛋白纤维是纺织原料中的高科技新型纤维,本公司在国内为首创.牛奶蛋白纤维的出现改变了动物蛋白纤维的传统定义,它是天然与科技的完美组合,更符合了现代生活的高品质需要."正家牌"牛奶蛋白纤维经国家毛纺织产品质量检验测试中心(上海)测试鉴定,pH值为6.80,呈微酸性,与皮肤保持一致,也不含致癌偶氮染料,完全符合欧共体提出的纺织品生化标准ECO一100规定的"出口纺织品呈中性或微酸性"及"禁用致癌偶氮染料"规定."正家"牛奶纤维产品在我国为首创,并获国家专利,被列入上海市高新技术A级转化项目.正家牛奶纤维面料为国际流行面料.公司名称:上海正家牛奶丝科技有限公司公司地址:延安西路2299号上海世贸商城71306室E—mail:zhengyu@milkfashion.conl。
- 1、下载文档前请自行甄别文档内容的完整性,平台不提供额外的编辑、内容补充、找答案等附加服务。
- 2、"仅部分预览"的文档,不可在线预览部分如存在完整性等问题,可反馈申请退款(可完整预览的文档不适用该条件!)。
- 3、如文档侵犯您的权益,请联系客服反馈,我们会尽快为您处理(人工客服工作时间:9:00-18:30)。
谈谈如何降低粗纱
重量不匀提高半制品质量
浙江华一纺纺纱线有限公司前纺车间周勇
关键词:棉条;假捻器;张力;温湿度;筒管
粗纱定量是粗纱工序的重要工艺参数,它的偏差大小直接影响成纱的质量。
因此只有将粗纱重量差异控制在一定范围内,才能降低粗纱及细纱的重量不匀,提高成纱质量。
控制粗纱喂入棉条重量的差异。
我厂的A456C、FA421粗纱机采用高架喂入的导条架形式,通过链条、链轮来传动。
各导条辊、后罗拉之间配有很小的张力牵伸。
由于现在我们生产的色纺纱熟条很烂,纤维抱合力较差,尤其是采用条混多道并合后的熟条。
因此,在粗纱机后的导条喂入过程中,因条子烂,不足以承受从条桶内引出时的自重伸长与导条辊之间的张力,致使棉条产生意外伸长。
(远离后罗拉的两排棉条桶称之为后排,离后罗拉近的两排棉条桶称之为前排,后排棉条的意外牵伸比前排大)因此在日常工作中我们要加强导条架部分的维护,使导条辊运转灵活,减少后罗拉与导条辊之间的张力牵伸,降低棉条喂入过程中产生的意外牵伸。
粗纱机锭翼顶孔的边缘到前罗拉钳口的纱条部份为纺纱段,前罗拉钳口的捻陷区捻度小,极易引起纱条的意外伸长。
粗纱前排的纺纱段长,捻陷区也长,粗纱丝强力相比内排要差,意外伸长也大。
而A456C粗纱机内外排假捻时的导纱角存在较大差异,使得A456C粗纱机的锭差变得更为突出。
我们采用了按高低分内外排安装的新型高效假捻器来减少导纱角的差异,增加纺纱段的捻度,由于新型高效假捻器的应用,捻陷区长度明显缩短。
采用缩短捻陷区长度来增加纺纱纺纱段强力,减少意外伸长,降低粗纱重量不匀。
粗纱机的机前机后都会产生意外伸长,我们可以通过合理搭配来缩小粗纱之间的意外伸长。
搭配的方式:粗纱后排的棉条对应内排的粗纱锭子,前排的棉条对应外排的粗纱锭子,以此来调节前后排条桶和内外排锭子在纺纱过程中的张力差异,减少意外伸长,降低粗纱机锭与锭之间的重量差异。
粗纱机大、中、小纱张力的差异。
自前罗拉输出的须条经过加捻到筒管的行程中,必须克服锭翼顶端空心臂和压掌对粗纱的摩擦力。
为了正常卷绕,筒管的卷绕长度应比前罗拉输出长度稍大为宜,使粗纱在卷绕过程中始终保持一定的紧张程度,这种紧张程度称为粗纱张力。
它也是工艺上所必须要的。
粗纱张力对生产的影响很大,粗纱张力不适当时,一落纱的各段粗纱伸长率就不一样,卷绕时就会出现过松或紧,影响卷绕长度,破坏正常条干均匀度,同时还会增加粗纱断头和疵点,严重影响到产品质量及产量。
并且还在细纱退绕过程中也会增加粗纱断头及其它疵点,严重时会使成纱重不匀、条干CV%值、捻不匀、张力等多种试验项目数据恶化,超过国家及企业内部的质量标准。
因此,应加以重视设计与调整粗纱张力,从而为产品的质量、产量垫实重要的基
础。
粗纱张力的设计与调整是根据粗纱的原料、号数、捻度、卷绕条件、回潮率、温湿度等的影响而定。
在粗纱机一落纱过程中,前罗拉输出速度恒定不变,但卷绕在筒管上的粗纱直径在不断变大,由粗纱直径增大带来的卷绕线速度变大影响到粗纱张力的变化,因此,粗纱每增加一层卷绕,锥轮皮带就移动一个单位移动量,以此来调节粗纱的卷绕线速度,使卷绕线速度一直保持和前罗拉输出速度一致。
严格控制车间温湿度,当车间温度偏高、湿度偏大时,粗纱纱条与机件的摩擦阻力增加,则卷绕张力增加,卷绕直径的增量减小,同时由于纤维的回潮增加,纤维间抱合力增加,承受一定外力而产生的相对滑移必然减少,反映在纺纱段则为纱条松弛。
此时,张力增加,伸长率倒也未必增加,生产出来的粗纱松烂,毛羽会明显增加。
现在我们生产线上有大量的筒管内孔经改制扩大,上机回转时晃动;筒管外径有差异;有弯曲变形,导致卷绕线速度的不同引起粗纱伸长,这些因素都能增大粗纱机锭与锭之间的伸长率差异。
为了减小这种差异,应加强粗纱筒管的检修工作,并使外径一致,如筒管有明显晃动,应当及时报废。
档车工值车操作时一定要按操作规程以及工艺要求来做。
即在粗纱锭翼上端的导纱孔必须按工艺要求分为1/4或者3/4进行穿孔,穿孔过后的粗纱经过锭翼通道至压掌时,还要按要求分为单绕或双绕。
这两点必须按工艺要求操作,这完全是为了使同台同品种的粗纱在锭翼上的摩擦力相同,使张力、伸长率达到相关标准。
要做到设备没有任何缺陷是不可能的,所以工艺必须配合设备合理制定,不当的工艺同样会产生问题。
单纯地从设备方面着手并不能消除粗纱的重量不匀。
齐抓共管,防微杜渐。
在企业减少用工,增加挡车工看台数的情况下必然给生产管理增加难度。
一方面设备维护人员要加强之上的巡回检查力度,同时空调工要勤跑巡回,对于纺纱困难的区域要及时调节好温湿度;更重要的是运转班的挡车工、落纱工、机修工在跑巡回时注意留心,发现问题及时处理。
综上所述,企业要建立完善的质量检测反馈体系,发现有质量问题应立即反馈,及时查找原因采取措施。
平时各部门要注意控制好原料、质量、回潮率,保持车间内温湿度相对稳定,优化工艺参数,在满足纺纱工艺条件下减少意外牵伸,控制各道工序的半制品质量,确保生产合格的粗纱来供应后续工序加工生产。