粗轧机区域1
热连轧-粗轧部分资料

五、E2R2改造的相关情况
3、目前E2R2轧机存在的主要问题 新E2R2投用后,E2R2速度匹配的问题一直没有得到很好的解决,尤其R2
工作辊新辊上机初期,轧制时其速度不匹配的问题反映得尤为突出,对中间 坯板形控制带来较大影响。
24
六、粗轧轧制时常见的异常情况
1、设备不定位或误动作 原因:
分别是3#液压站、AWC液压站、伺服液压站。 润滑系统:分干油和稀油两个系统。
各液压站的作用 3#液压站:为R1R2轧机接轴平衡、轧辊
平衡,立辊轧机平衡,R1R2轧机换辊系统等提供 动力。3#液压站有“平衡”和“换辊”两种工况, 除进行换辊作业时在“换辊”工况外,粗轧区域 的其他作业3#液压站均应在“平衡”状态。
HD2055
RT204
HD207A HD207B HD206
RT205
RT206
HD208 2085 HD209
HD210
WG201
WG202
除鳞箱
E1前工 作辊道
E1
R1后工 R1后延1段
2段
作辊道
R1
E2前工 作辊道 E2
R2后工作 R2后延1段2段 辊道 R2
4
一、粗轧主要设备及功能
粗轧区的液压、润滑系统 液压系统:粗轧区域共有三个液压系统,
轧
开速 停
度 度 始 制 始度 转
梯形速度制度图
第二道次
时间
16
三、粗轧机的速度制度
2、三角形速度制度
速
第一道次
度
待 轧
咬
咬 钢
减
抛减
钢 升速 钢 速
速
速
速 开
开
速停
度 度 始始 度 转
轧钢厂卷取部分相关设备介绍

第一部分:1、体积不变定律:金属在压力加工过程中,变形前后金属的体积不变。
2、最小阻力定律:物体在变形过程中,其质点有向各个方向移动的可能时,则各质点将沿阻力最小的方向移动。
3、塑性变形:物体受力作用发生变形,当引起物体变形的力不存在时,物体不回复原状,这种变形称之为塑性变形。
4、咬入条件:咬入角≤摩擦角,咬入角和摩擦系数是影响轧辊咬入轧件的两个因素。
当摩擦系数一定时,为了使轧件易于咬入,必须减少咬入角减少咬入角的方法有以下两种:1)当压下量一定时,增加轧辊直径;2)当轧辊直径一定时,减小压下量。
但是轧机确定后,轧辊直径一般改变不大,而减少压下量又对提高生产率不利,为了解决这一矛盾,常采用以下几种措施:a)降低咬入时的轧制速度,增加摩擦系数。
b)增加轧辊粗糙度,从而增加摩擦系数。
c)利用冲击力改善咬入条件。
5、凸度、楔形6、轧线生产工艺流程7、常见的晶格形式有三种:a、体心立方晶格;b、面心立方晶格; c、密排六方晶格。
8、强度:强度是指构件应有足够的抵抗破坏的能力。
刚度:刚度是指构件应有足够的抵抗变形的能力。
塑性:塑性是指材料受外力作用时发生永久变形而不破坏其完整性的能力。
塑性衡量的指标有两种:相对延伸率和断面收缩率。
9、当金属内部存在应力,其表面又有尖角、尖缺口、结疤、折叠、划伤、裂纹等缺陷存在时,应力将在这些缺陷处集中分布,使这些缺陷部位的实际应力比正常应力高数倍。
这种现象叫应力集中。
应力集中提高了金属的变形抗力,降低了金属的塑性,金属的破坏往往从应力集中的地方开始。
10、宽展:轧制时轧件的高度减小,被压下的金属在长度方向上延伸外,还有一部分金属沿横向流动,使轧件的宽度发生变化,这种横向变形叫宽展。
轧件在轧制前后的宽度差叫宽展量。
宽展的种类:自由宽展、限制宽展、强迫宽展,我厂轧制过程中的宽展都属于自由宽展。
影响宽展的因素:压下量的影响(压下量越大宽展量越大),轧辊直径的影响(在其他条件不变的情况下,随着轧辊直径的增加,宽展值相应增大),轧件宽展的影响(随着轧件宽度的增加,导致宽展量减小),轧辊表面对宽展的影响(轧辊表面越粗糙,摩擦系数越大,轧件的宽展量越大),轧制速度与温度对宽展的影响(轧制速度越高,摩擦系数越低;轧制温度越高,摩擦系数越低,从而轧件宽展量减小)。
高速线材粗中轧轧机调整

高速线材粗中轧轧机的调整【摘要】:本文详细叙述了高速线材粗中轧轧机的调整与操作以及在轧制过程中容易发生的一些轧制技术的分析与处理.通过本文的分析让读者对高速线材生产进一步了解。
在实践过程操作中对工艺流程所提出改进方法.【关键词】:调整轧辊导位操作方法企业的发展动力来源于员工的较高素质,轧钢工的专业知识与技能的熟练握是企业高效率生产及操作技能水平。
在生产中的炸鸡调整是操作的基础,也为将来的工作打下了坚实的基础。
无论是实际应用中。
还是在理论研究方面。
都尽量使它符合实际操作。
本文笔者比较侧重实际操作技能。
所以不断要求自己提高实际动手解决为体的能力。
使自己的工作水平更上个台阶以及对我国钢铁企业尽一份自己的微薄之力。
1、粗中轧区域的轧机1.1机架由两个两个框架状的轧机牌坊联结而成、轧机牌坊的敞开部分叫做“窗”,在这个“窗”中安装轧辊的轴承座。
通常高速线材粗轧机采用闭式机架,这是因为闭式轧机具有刚性大的优点。
二辊机架排放通常由铸钢铸造而成,也可用厚钢板焊接而成,后者的强度与刚性较好,并且具有体积小,重量轻的优点。
1.2轧辊基本结构分为三个部分:既辊身、辊颈、辊头,辊身是轧辊与轧件接触的工作部分,型钢轧机的轧辊辊身是圆柱体,上面车有孔槽.辊颈是轧辊的支撑部分,轧辊是依靠辊身两侧的辊颈而支撑在轴承上.辊身和辊颈交界处由于断面变化可能成为集中的地方,容易断裂.所以,为了提高轧辊强度,交界处应有适当的过渡圆角。
轧辊的辊头具有连接传动接轴.传递轧制力矩的作用。
轧辊直径:许轧机组轧辊辊身直径一般为轧件平均高度的4到5倍,这不仅是为了有足够的强度和刚度以及咬入能力,也是为了轧制时的变形渗透,以避免轧件端部出现由表面变形造成的双叉鱼尾状,而在继续轧制时发生顶撞入口导位的故障.1.3轧辊平衡装置:轧辊平衡装置起着平衡上辊及其轴承座重量的作用.b 轧辊水平调整装置:轧辊的水平调整包括轧机中心线的标高调整和上.下辊间距的调整.轧机中心线的标高通过改变下轧辊轴承座底部的垫块厚度来调整;上下辊的最大间距是由改变上辊平衡器的垫片厚度来设定.1.4 轧机的压下装置是实现上辊压下,调整辊缝的机构.压下装置的形式有电动压下、液压压下、气动压下和手动压下几种、在高速线材轧机上多采用电动压下或者气动压下形式,辅以手动压下.电动和气动压下装置的压下调整速度快、省事省力,用于辊缝的粗调;而手动压下是用于对辊缝进行微量的精确调整.不论采取何种方式,均要求调整后,轧辊两侧的辊缝相等、粗轧机轧辊径向调整量较大,一般为轧辊直径的15%左右。
粗轧考试4答案

粗轧区域考试题(4)答案一、填空(每题3分,共计30分)1、板坯宽度精度的控制主要在粗轧机,粗轧机常用的板坯宽度控制方式为宽度自动控制(AWC)。
2、R2四辊粗轧机液压压下和侧导板液压系统为四辊粗轧机液压压下和E1R1/E2R2侧导板液压缸提供动力源。
3、为了得到所要求的产品质量包括精确成形及改善组织和性能,在轧机机组上采用的一切生产工艺制度称为轧制工艺制度,其中包括轧制变形制度、轧制速度制度、轧制温度制度。
4、热轧过程中氧化铁皮压入带钢表面形成的一种表面缺陷称为压入氧化铁皮。
按其产生原因不同可分为炉生(一次)氧化铁皮、轧制过程中产生的(二次)氧化铁皮或轧辊氧化膜脱落压入带钢表面形成的(二次)氧化铁皮。
5、粗轧机根据所轧带坯的长短有梯形和三角形两种速度制度,如果所轧带坯的长度超过临界长度时为梯形速度制度,当所轧带坯长度小于临界长度时为三角形速度制度6、R1轧机的减速点压下开口度为 260 mm、换辊极限压下开口度为 280 mm、大极限压下开口度为 300 mm、超大极限压下开口度为 320 mm、小极限压下开口度为 15 mm。
7、阶梯垫下辊标高调整装置主要由液压缸、垫架、9级阶梯垫块、两挡固定垫块(在下支撑辊轴承座上)、防水罩等组成。
8、AWC宽度自动控制功能是用轧制力的变化来修正宽度差。
利用水平轧机AGC的原理,当轧制力变化时,立辊辊缝也会随之变化。
AWC即为抵消这一变化,以保证宽度波动在要求的范围内。
9、E1轧机道次最大侧压量可达 80 mm,主要用于变宽轧制时控制轧件宽度;E2轧机道次最大侧压量为80mm,主要用于消除轧件在水平轧制过程中产生的宽展。
10、在分配粗轧机压下量时,要充分考虑各种限制因素,其主要目的是要充分发挥设备的潜力,各道次负荷的平衡,同时也要照顾产品质量。
二、选择(每题3分,共计30分)1. 为了降低热轧时的轧制压力,应采用( A )的方法。
A.轧制时增大前、后张力 B.增大轧辊直径C.增大压下量 D.增大轧制速度2. 轧件被轧辊咬入的条件是( A )。
高速线材主控台控制操作技术

第一章主控台操作分工与操作技术素质要求主控台是控制全轧线生产的中心操作室,是全厂的中央信息处理站,在高速线材轧机的连轧控制中,主控台对轧制的正常顺利进行起着关键作用。
一、主控台所管辖的区域设备主控台所管辖的区域设备有:(1)加热炉出口处夹送辊、粗轧机组、中轧机组、预精轧机组、精轧机组以及夹送辊、吐丝机。
(2)粗轧机组1#机架前卡断剪、粗轧机组8#机架后的曲柄剪、预精轧机组前的回转飞剪、事故卡断剪、精轧机组前的回转飞剪、事故碎断剪及事故卡断剪。
(3)轧线上所有活套控制器。
(4)出炉辊道、分钢辊道(5)预水冷段,水冷段二、主控台的职能与控制对象主控台的职能与控制对象有:(1)设定、调用、修改轧制程序。
(2)控制上述所有轧制区设备的动作及运行。
(3)监控轧制区的轧制过程,实现轧制工艺参数和程序控制最优化。
(4)控制轧机各机组的轧辊冷却水开与闭。
(5)组织、协调轧制生产工艺,保证生产的正常进行。
(6)担负轧制生产线的日常生产信息传递,进行轧制区物料跟踪方面的操作。
(7)有关生产数据报表的记录与汇总。
(8)监视全生产线的机械、电气、能源介质供应系统的设备运行状况与故障显示。
三、主控台与生产调度室及各操作台(点)的分工和关系1、主控台与生产调度室的关系主控台主要负责生产线上轧制生产的组织与协调,即偏重于轧钢生产人员本身的内部指挥;生产调度室主要负责轧制生产的总体指挥与协调,它的任务有:与水、电、风、气等外部能源介质供应单位的联系,对高速线材厂(车间)各专业(轧钢、电气、机修)的指挥与协调,即偏重于轧钢外部的联系。
2、主控台与各操作台(点)的关系根据高速线材生产工艺流程特点,轧制生产线上配置有6 个操作台:入炉加热出钢操作台(负责原料区原料的入炉与计量、加热炉加热工艺操作和出钢操作);主控台(负责轧制区的轧制生产工艺操作和轧钢生产协调);集卷操作台(负责散卷采集操作);打包操作台(负责将散卷打包操作);称重标牌操作台(负责成品盘卷的称量,标牌打印操作);卸卷操作台(负责卸卷操作)。
粗轧机工作原理

粗轧机工作原理全文共四篇示例,供读者参考第一篇示例:粗轧机是钢铁生产中的一种重要设备,主要用于对原料进行初次轧制,使其在粗轧机上经过一系列轧压的作用后得到一定的形状和尺寸。
粗轧机的工作原理是通过辊子的旋转进行轧制,将原材料加工成所需的形状和尺寸。
粗轧机主要由上辊和下辊组成,通过辊子的旋转运动,使原料在辊子之间受到挤压和拉伸,从而得到所需的形状和尺寸。
在辊子旋转的过程中,原料会在辊子之间经历一系列的变化,包括压缩、拉伸和弯曲等过程。
通过这些过程,原料的结构和形状会逐渐发生变化,最终得到所需的产品。
粗轧机的工作原理可以简单描述为:先将原料放入粗轧机的进料口,经过辊子之间的挤压和拉伸,原料逐渐变形,最终在出料口处得到所需形状和尺寸的产品。
在整个工作过程中,辊子的旋转速度、辊子之间的距离和压力等参数都会对成品的质量产生影响,因此需要进行精确的调整和控制。
在粗轧机的工作过程中,需要不断监测和调整工艺参数,以确保产品的质量和成型效果。
还需要对设备进行定期的维护和保养,以确保设备的正常运行和长期稳定性。
粗轧机是钢铁生产中不可或缺的设备之一,通过辊子的旋转轧制原料,将其加工成所需的形状和尺寸。
粗轧机的工作原理是通过辊子之间的挤压和拉伸来实现原料的变形,从而得到所需的产品。
粗轧机在钢铁生产中扮演着重要的角色,不仅可以提高生产效率,还能提高产品质量,保证生产的顺利进行。
第二篇示例:粗轧机是钢铁生产中非常重要的一种设备,它主要用于将钢坯进行初次轧制,形成一定的形状和尺寸,为后续的中轧和精轧工序做好准备。
粗轧机工作原理简单清晰,但在实际操作中需要严格掌握一些技术要点,以确保生产安全和生产效率。
粗轧机的工作原理主要包括以下几个步骤:1. 钢坯进料:将待轧钢坯通过进料辊道输送到粗轧机的进料口,进入轧辊之间的轧制区域。
2. 轧制过程:待轧钢坯在进入轧辊之间受到挤压和拉伸的作用,逐渐变形成所需的形状和尺寸。
轧辊的旋转使钢坯在轧制区域内来回通过,不断受力,最终形成产品。
2032热轧线L1L2控制系统升级及精轧板形控制优化

2032热轧线L1/L2控制系统升级及精轧板形控制优化Upgrading of L1/L2 Control System for Hot Rolling 2032 Rolling Line and Optimization of Finishing Strip Shape Control供稿|申世武1,黄盛声2,廖峰峰1,黄小刚1 / SHEN Shi-wu1, HUANG Sheng-sheng2, LIAO Feng-feng1, HUANG Xiao-gang1DOI: 10.3969/j.issn.1000–6826.2019.01.018柳钢热轧厂2032热轧线L1/L2控制系统及精轧板形控制于2005年10月投产运行。
目前L1和L2控制系统均存在软硬件需要更新换代的问题,L1控制系统中精轧AGC使用专用控制器,控制功能和备品备件存在很大隐患,L2控制系统中服务器竟然还是Windows 2003系统,系统硬件和控制软件均存在升级困难,备件处于停产状态,给系统安全可靠的运行带来很大隐患。
对于钢铁企业来讲,软实力首先体现在低成本、低消耗、高质量上,为此,必须打通产品设计、业务管理和制造过程之间的数字化通道,改善对生产过程的管理与控制能力;必须改变制造过程中人工主导、效率低下的运作模式,充分发挥制造资源的效益和作用。
2032热轧板带生产线控制系统升级改造对柳钢实现业务策略、提高竞争力具有重要战略意义。
热轧2032轧线的主要机械设备采用步进式加热炉、液压AGC控制系统、粗精轧快速换辊、轧线全自动过程控制、西门子Simadyn-D传动系统、西门子TDC、S7-400基础自动化控制系统等技术。
作者单位:1. 广西华锐钢铁工程设计咨询有限责任公司,广西柳州 545002;2. 广西柳州钢铁集团有限公司热轧厂,广西柳州 545002成果展示Achievements Exhibition热轧控制为有效控制带钢热连轧生产线的整个生产过程,根据生产工艺的连贯性、分布位置及控制要求,对控制系统按统一、分区、分级的方式进行系统配置。
粗轧操作规程

(停机时已完成)
将主轴和立辊断开
“”
“”
使机侧盘在复位状态
大分类
粗轧
中分类
手顺操作
小分类
立辊手动更换
序号
工作程序
操作内容
确认
注意事项
STEP2
传动侧轴承座连接集管“拆开”
工作侧立辊定位在收回位置即最大开口度位置
传动侧定位在“换辊位置”即电动侧压伸出至极限位置-10mm
传动侧回拉缸停
传动侧上下液压缸前进40mm
为ON状态
大分类
粗轧
中分类
手顺操作
小分类
RM工作辊自动换辊
序号
工作程序
操作内容
确认
注意事项
4.6
4.7
换辊电源开
轧机模式切轧制状态
大分类
粗轧
中分类
手顺操作
小分类
RM工作辊手动换辊
序号
工作程序
操作内容
确认
注意事项
1
1.1
1.2
1.3
1.4
1.5
1.6
1.7
1.8
1.9
1.10
1.11
2
2.1
准备
台上
到换辊计划前10块钢之前通知磨辊间备辊,旧辊核对轧制吨位;新辊检查、辊号、辊径检查、检查新辊组装,辊面质量与涂油情况,扁头是否垂直
主轴定位
自动运转启动
模式选择:确定为工作辊换辊模式并指明为自动换辊
换辊步骤选择
STEP 0
自动主轴定位
主辅助盘的()在“”
()和()两机侧台面
按“”→按“”
(检查入口游横移小车对准机架牌坊窗口且新辊是否放置在横移小车出口侧)
粗轧、中精轧课件综述

1.3 粗轧机前延伸辊道
数量:12 个 功能:布置在粗轧机前工作辊道的前面,承接高压水除鳞 后的钢坯,与轧机前工作辊道一同将轧件送入轧机轧制。 型 式: 单独传动、可逆式 辊子直径×辊身长度: φ 350×2500 mm 辊 距: 1200 mm 辊子数量: 12 根 辊面速度: 0~±3 m/s 辊面标高 +670 mm 电机: 12 台 额定功率: AC15 kW 额定转速: 1470 r/min 轴承处辊颈直径:φ 180 mm
Designed by ywq
1.9 粗轧机主传动
功能:轧机主传动系统安装于主电机到 轧机工作辊之间,用来传递轧制力矩。 技术参数: 主电机功率: AC4500 kW 主电机转速:0/50/100 r/min
Designed by ywq
1.10 粗轧机后推床
用途:布置在粗轧机后工作辊道上,推床推板夹持轧件沿 辊道表面横向移动,使其对准轧辊孔型。 技术参数: 型 式:电动齿轮齿条型式翻钢/推钢轧件长度范围4~30 m 推板长度: 约 12000 mm 推板工作行程: 操作侧: 2500 mm(轧制中心线两侧各 1250mm。 传动侧: 2500 mm(轧制中心线两侧各 1250mm) 推板高度: 不大于 550 mm 单侧推板检修行程距轧制中心线~2200 mm 推力: 300 kN 推板移动速度: max.700 mm/s(单侧) 推床定位精度 约±2 mm 推床传动电机: 2 台 额定功率: AC 160 kW 额定转速:1000 r/min 推床减速机传动比: 45 箱型梁冷却水量: 12 m3/h 工作压力: 0.4~0.6 MPa
Designed by ywq
TMEIC冲击速降补偿功能在热轧主传动系统中的应用

TMEIC冲击速降补偿功能在热轧主传动系统中的应用摘要:在热连轧机组轧制过程中,主轧机在咬钢时会有冲击速降,本文介绍了柳钢防城港基地1780mm热连轧,采用先进的TMEIC-70e2传动系统作为轧机主传动电机的驱动系统是如何对冲击速降进行预补偿的。
柳钢防城港基地1780mm 热连轧采用的TMEIC-70e2传动系统具有冲击补偿功能,通过在轧机咬钢之前对传动主电机速度进行预补偿,以减少冲击速降引起的扰动。
柳钢防城港基地1780mm热轧主传动采用此功能后,对于减少冲击速降引起的轧制扰动效果明显,保证了轧制的稳定性。
关键词:冲击速降;补偿;热轧;主传动1、热轧主传动系统柳钢防城港基地1780mm热连轧机2021年初投入生产,采用TMEIC先进的控制工艺、控制系统和控制设备。
轧线粗轧区域有R1和R2两架粗轧机,并且轧机前分别有E1和E2立辊。
精轧区域由F1-F7七架连轧机组成。
2、冲击速降的原理及控制系统的补偿方法2.1冲击速降在轧机的轧制过程中,当轧机由空载运行到负载时,负载转矩ML视为阶跃扰动,负载转矩等于MN,根据电机动力学方程可得:-MN=GD2/375×dn/dt(1)可以得到在此轧制扰动下的速降:-Δn=-375MN/GD2×TS(2)式中:TS为电机电磁转矩响应时间;GD2为转动惯量。
热连轧主传动机组在咬钢的瞬间都存在冲击速降,冲击速降的大小因传动系统的动态性能、机械传动特性而不同,一般说MN/GD2越大则冲击速降Δn越大,同时冲击速降恢复时间和系统响应时间有关。
2.2TMEIC传动控制系统的冲击速降补偿原理TMEIC-70e2传动系统采用预补偿技术,当轧机在咬钢之前,会有一个很小的速度补偿量发给传动装置,这个补偿量为轧机速度的5%~10%。
这个补偿速度与轧机正常轧制速度叠加形成传动装置最终的速度给定。
当轧机咬钢后,传动电磁转矩绝对值达到装置的带载设定值时,就会撤掉这个补偿量。
轧钢操作规程

总则1、适用范围:本规程适用于热轧圆钢和热轧带肋钢筋生产。
产品规格为φ14、φ16、φ18、φ20、φ22、φ25、φ28、φ32、φ36、φ40热轧圆钢和热轧带肋钢筋,热轧圆钢以符号φ表示,热轧带肋钢筋以符号表示。
2、生产工艺流程图:原料准备 - 加热 - 轧制 - 倍尺剪切 - 冷却 - 定尺剪切 - 检查 - 打包 - 过磅 - 入库3、生产工艺流程简述:本车间轧机采用6—6—6串列式全连续工艺布置,轧机机组为平立交替布置,全线实现无扭轧制。
生产工艺流程如下:原料150mm方连铸坯由15吨刚性耙式电磁吊成批地吊放在步进式台架下料端,由拨钢机单根顺序地拨到原料输送辊道上,经人工检查挑出短尺和废料,合格钢坯经过输送辊道送入加热炉内进行加热到1100℃~1250℃。
接到要钢信号时,启动摩擦式出钢机将其推出一段,然后由拉钢机将其全部拉出至机前辊道送入粗轧机组进行轧制,在粗轧机组进行6道轧制后,轧件经过1#飞剪切头后进入中轧机组,经过6道次轧制,经2#飞剪切头,通过水平侧活套形成器进入精轧机组,粗、中轧实现微张力轧制,中轧机组和精轧机组之间实现无张力轧制。
轧件在精轧机组进行轧制后,经过意大利倍尺飞剪剪切成倍尺后,由冷床前输送辊道送入步进式冷床冷却,然后由500吨冷剪剪切成定尺,经过人工检查后,由打包机打包、称重、人工挂牌后入库堆放。
4、棒材孔型系统:棒材粗轧机组采用扁箱—立箱—变态椭圆—圆—椭圆—圆孔型系统,中轧、精轧机组采用椭圆—圆孔型系统,热轧带肋钢筋成品孔及成品前孔采用平椭圆—螺纹孔型系统。
5、有关生产的台帐、卡片、检验报告等质量记录均由有关岗位操作人员、检查人员按格式逐项认真填写并签名。
所有记录、台帐、卡片、检验报告均应妥善保管。
6、各生产岗位操作人员、管理人员严格执行本岗位规程。
1.轧机区主要设备技术性能1.2中轧机技术性能:1.3精轧机技术参数2、轧钢工技术操作规程2.1轧钢生产前准备2.1.1与上班各岗位工对口接班,询问轧制情况、红坯尺寸与成品质量。
铝板带“1+4”热连轧设备特点探析

工程 技术
铝 板 带 “ 1 + 4 ’ ’热 连 轧 设 备 特 点 探 析
崔 建 华 ,刘金 朋 ,马金 伟
( 河南 中孚 实业股份有 限公 司,河南 巩 义 4 5 1 2 6 1 )
摘 要 :文章 论 述 了铝 热连 轧 生产 线设备 配 置的特 点 ,分析 了 目前主 要设 备 的结构特 点 连 轧机 设备
结构 的配置和选择 对 于一 条铝轧制 生产线 的成功建设 非常 重要 。
关 键 词 :连 轧 机 ;立 辊 轧 机 ;机 架辊 道
中 图分类 号 :T G3 3 5
文献 标识 码 :A
文 章编 号 :2 0 9 5 — 0 7 4 8 ( 2 0 1 5 ) 0 7 — 0 0 3 4 — 0 2
产 线及 目前 魏 桥 正在 安 装 的热 连 轧 生 产线 都采 用 了 此种 配 置方式 。
产 效 率高 、产 品质 量 好 、能 源消 耗 低 、 自动 化 程 度
高 的特 点 。
河南 中孚实业股 份有限公 司正在 建设的 “ 1 + 4 ”热
连 轧生产 线 , 目前 从德 国西马 克公司 引进 相关 设备和
2 “ 1 + 4 "铝 热 连 轧 机 机 械 设 备 的 组 成
热 连 轧 机 组 主体 机 械 设 备 主 要 包 含 以 下组 成 部 设 计 ,通过 结 合 分析 外 方 设 计 的设 备结 构和 设 计特 分 :1 . 粗 轧 机 入 口辊 道 ;2 . 立 辊 轧 机 ;3 . 对 中导 点 ,探究 国外先进 理念 ,对于 国际主流轧 机 的设 备结 尺 ;4 . 可 逆式粗 轧 机 ;5 . 轻 、重型 剪 刀 ;6 . L 架连 构的研 究以及 设备维护具有 十分重要 的意义。 轧机 ;7 . 张 力辊 ;8 . 多通道 凸度 仪 ;9 . 园盘 剪 及碎
轧钢厂精轧区域安全风险公告栏

砸伤
D
25
粗轧轧制作业
更换粗轧立辊区域狭小机 架下深空隙大
摔伤
D
26
粗轧轧制作业
换粗轧工辊轴承座孔与定 位销位置不正
挤伤
D
27
粗轧轧制作业
处理中间辊道中间坯温度 过高,防护不当
烫伤
D
28
粗轧轧制作业
选用吊具不当,站位不 当,众人指挥天车
碰伤
D
29 粗轧轧制作业 切割中间坯不戴防护镜
烫伤
D
30
粗轧轧制作业
其他伤害
1、施工方必须制定专项施工安全方案;2、施工方必须
B
组织作业人员对施工安全方案进行传达学习;3、现场设 轧钢厂
专人监管,督促落实。
8
各作业区
动火、有限空间、高处、 动土、临时用电、吊装等
高危作业未办理作业证
火灾、中毒和 窒息、高处坠 落、触电、物
体打击
B
1、高危作业必须办理作业票,无作业票严禁进行高危作 业;2、作业票证填写应规范并严格履行逐级审批程序。
绞伤
C
15 粗轧轧制作业 跨越辊道,不走安全过桥
挤伤
C
做好安全确认,开车前及时沟通 操作前,确认好安全销 劳保穿戴齐全 按规定走安全过桥 测量过程中联系要及时 按规定走安全过桥
生产作业区 生产作业区 生产作业区 生产作业区 生产作业区 生产作业区
16 精轧轧制作业 劳保用品穿戴不齐
烫伤
C
17
精轧轧制作业
挤伤
D
劳保穿戴齐全 开车前必须鸣警报 检查前先做好安全确认 操作前,确认好后在操作 按规定调整轧制线标高
保持安全距离 推床前做好安全确认
生产作业区 生产作业区 生产作业区 生产作业区 轧线班组 轧线班组 轧线班组
梅钢热轧1422过程控制系统改造实践

梅钢热轧1422过程控制系统改造实践摘要:梅钢热轧1422产线自动化控制系统从TMEIC公司引进,运行已二十多年。
控制设备老化,备件难以采购,给日常维护、系统功能完善和新功能的开发带来了很大难度。
梅钢从2022年12月开始对热轧1422产线进行粗轧R1机械设备、L1、L2自动化系统进行升级改造。
L2系统完成了过程控制服务器硬件、系统、数据库和平台的升级,模型程序升级为64位,并结合智慧制造、新R1轧机等进行适应性同步改造。
此次改造在实际生产中取得了满意的效果。
关键词:热轧、过程控制、影子系统、离线测试、在线测试1、引言随着梅钢热轧1422产线产能的不断提升,原有轧机设备和工艺已不能适应生产需求,自动化系统硬件面临设备老化、备件订购困难的问题,给日常维护、系统功能完善和新功能的开发带来了很大难度。
2022年12月年修期间,热轧1422产线进行了粗轧R1机械设备、L1、L2自动化系统升级改造。
此次L1、L2自动化系统改造TMEIC公司将 L1基础自动化系统由原GE公司的 Innovation 系列更新为 TMEIC公司的NV系列,并同步对现场控制电缆进行更换;L2过程控制系统升级操作系统、数据库和平台,模型及应用程序从原有的32位系统升级为64位,并结合智慧制造、新R1轧机等进行适应性同步改造。
本文重点介绍L2过程控制系统的改造实现。
2、L2过程控制系统概况L2过程控制系统是实现对板坯从加热炉抽出开始,经除鳞箱、粗轧、中间辊道、热卷箱、精轧、卷取机、称重、喷印到快速运输链为止的相关设备的过程控制。
梅山钢铁热轧1422产线采用的TMEIC公司的过程控制系统,完成过程控制系统的通信、数据采集、物料跟踪、进程管理、报警及日志等所有功能开发。
2.1 L2过程控制系统L2过程控制系统主要由过程控制服务器SMGL2PRI、数据库服务器SMGDB、画面服务器HMISVR和通讯网关服务器GATEWAY等组成。
过程控制服务器SMGL2PRI是整个系统的核心,使用Pasolution组态软件,完成通讯数据管理、跟踪、计算、报警、数据采集等功能;另外,模型计算程序的运行也在SMGL2PRI上;数据库服务器SMGDB使用SQL SERVER2019数据库实现对PDI、历史、模型、、轧辊、报警等数据的存放和读取;画面服务器HMISVR配置CIMPLICITY11.5人机接口软件,负责轧线L2画面的画面工程的管理,画面工程包含现场操作600多幅画面的配置与编译,近4万多个EGD通讯信号的定义及管理;根据现场操作画面需求划分操作权限。
轧机简图
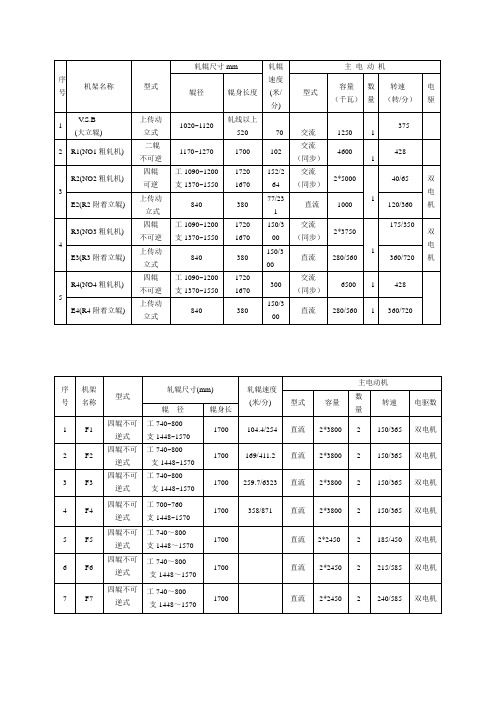
支1448~1570
1700
直流
2*2450
2
185/450
双电机
6
F6
四辊不可逆式
工740~800
支1448~1570
1700
直流
2*2450
2
215/585
双电机
7
F7
四辊不可逆式
工740~800
支1448~1570
1700
直流
2*2450
2
240/585
双电机
四辊
可逆
工1090~1200
支1370~1550
1720
1670
152/264
交流
(同步)
2*5000
1
40/65
双
电
机
E2(R2附着立辊)
上传动
立式
840
380
77/231
直流
1000
120/360
4
R3(NO3粗轧机)
四辊
不可逆
工1090~1200
支1370~1550
1720
1670
150/300
直流
280/560
1
360/720
序号
机架
名称
型式
轧辊尺寸(mm)
轧辊速度
(米/分)
主电动机
型式
容量
数量
转速
电驱数
辊径
辊身长
1
F1
四辊不可逆式
工740~800
支1448~1570
1700
104.4/254
直流
2*3800
2
150/365
双电机
轧钢二级专业英语对照表

通用部分(计算机)Transmission Control Protocol/Internet Protocol (TCP/IP) 传输控制/网际协议Socket 套接字Domain Name 域名User Accounts 用户帐号Mask 掩码Database administrator ( DB)数据库管理员Redundant Server 冗余服务器Disk Imaging 磁盘镜像Emergency repair disk 紧急修复磁盘Simulation Test 仿真测试Cold Run Test 冷运行测试Interface 接口Roll Shop Computer轧辐间计算机Sensor 传感器Heartbeat健康信号(表示两个系统之间能够保持正常连接)PDI request PDI 请求Rolling schedule request 轧制计划请求Coil Yard 卷取区/钢卷库Protocol 协议GSM(global shape management) 板形全局控制,平直度控制Feedback 反馈EGD (ethernet global data) 以太网全局数据Bridge 网桥Steel grade family (SGF)钢种分类Steel grade code (SGC) 钢种代码Material code 原料代码PDI (Primary Data Input) 初始化数据输入data gathering 数据采集Slab ID 板坯号Coil ID 钢卷号Parameter 参数Post-coiler tracking 加速卷曲机跟踪Tracking Data 跟踪数据Supervisory L2 and Process Models Server (SCC) 2 级监控系统和工艺模型服务器Data Base Server (DBS) 数据库服务器Development Server (DEV) 开发服务器mirrored disk 镜像盘Fiber based Ethernet switch 光纤以太网交换机Hard disk drive 硬盘驱动器Human Machine Interface (HMI) 人机接口HMI terminal HMI 终端network printer 网络打印机Database 数据库OS 操作系统Symmetrical Multi-Processing对称多线处理Data Server 数据服务器Redundant Array of Independent Disks (RAID) 冗余独立磁盘阵列piece-oriented data handling 物料定向数据处理logical tracking 逻辑跟踪specialized interface 专用接口Setup Model Feedback 启动模型反馈panels with hinged door front and back 前后开门盘柜1-way Double Module Redundancy 单向双模冗余Redundant power supply 备用电源redundant memory 备用内存Front Side Bus 前向总线PCI expansion slot PCI 扩展插槽Ethernet port 以太网端口mirrored disk drive 镜像盘驱动器Video Card 显卡Video Adapter 显示适配器External tape drive外部磁带驱动器电缆USB键盘串行鼠标串行端口USB 端口串行调制解调器144 MB Diskette Drive144 MB软盘驱动器DVD RW DVD 可读写光驱Drive 驱动器Input Voltag e 输入电源Cache 缓存Monitor 监视器Workstation 工作站master time 系统时钟Ethernet LAN 太局域网programmable switcher可编程交换器Router 路由器Media Convertor 媒体转换器AC input voltage 交流输入电源Number of phase 相数Internet Diagnostic Support因特网诊断支持Mill Pacing 轧制调步Macro and Micro Tracking宏观与微观跟踪Data Collection 数据收集Mill Delay 轧机延时CableUSB keyboardSerial MouseSerial PortUSB PortASNSystem Testing 系统测试Internet Service Provider (ISP)因特网服务提供商通用部分(模型)Finishing stands FM (精轧机组)Laminar cooling 层冷High speed shear(HSS)高速飞剪Downcoilers DC 卷取机Boundary 边界Equation 方程式Extract 抽取,出钢Duration持续时间Conveyor 运输链Emissivity发射率;辐射系数Tabulate表格化Coefficient 系数Derive 获得起源Ambient 周围环境Ferrite 铁素体Austenite奥氏体Compensation 补偿Practice 实例Resistance 阻力、抗力Expansion 膨胀Property 性能Accuracy 精确Radiation 辐射Convection 对流Conductivity 传导Calibration 标定(calibrate 校准)Boundary 边界Equation 方程式Volume体积Transformation 转变Velocity 速率Initial初始的Residual残余的Division 分配Acquisition 采集Iterative 迭代Vernier补偿微调Slope斜坡Accumulate 累计Concatenate 连结的;连锁Temporary 临时的Identification IDUnique独一无二的dead band 死区隧道炉连铸区域(控制)TSC (thin slab caster)薄板坯铸机Descaler 除磷Pendulum shear(PS)摆剪Tunnel furnace(TF)隧道炉Torch cutter (TCI)火切1Shuttle横移段Torch cutter (TC2)火切2Edger立辊HR (High reduction stand)大压下机组Crop shear (CS)飞剪Induction heater (IH) 感应加热Intensive cooling (IC)强冷Heat ID 炉次Sequence 浇次Strand铸流Cast浇铸TSC Turret大包回转台MDB 冶金数据库Mold (塑造模具)结晶器Tundish 中包Ladel大包Ladel gate大包滑盖Tundish weight 中包重量Ladle weight大包重量Cast speed 拉速Dummy bar 引锭杆(dummy-空过) Oscillation stroke结晶器震动振幅negative strip 负活脱Primary circuit water flow 结晶器主循环水流动Extraction rolls force 夹持辐拉坯力laboratory analysis实验室成分分析Mixed Steel calculatio 混钢模型计算Ladel thermal model大包温度模型Tundish thermal model 中包温度模型Quality Control calculation 质量控制计算Cut optimization calculation 剪切优化计算Steel spec.grav. cool 钢铁冷态属性 (密度) Steel spec.grav. liquidus 钢铁液态属性(密度)Steel spec.grav. hot 钢铁热态属性 (密度) PDB 产品数据库RTDB 实时数据库TSC CASTING PROFILE 连铸曲线QCS质量分类系统PWS 工程师站OWS 操作工界面Prime slabs 质量正常板坯Scrap slabs碎断板坯Head crops头部切除Tail crops尾部切除Ladle skull大包铸余tundish skull中包铸余Pulpit 操作台metallurgist,s offH艺工程师室Permanent database 永久数据库Real-time database 实时数据库“Area Supervisor” (SPV)区域过程监控Model processes (MOD)模型进程Driver processes (DRV)驱动进程Auxiliary processes (AUX)辅助进程TCP SOCKET TCP套接字报文PLC Driver PCL 驱动Metallurgical 工艺的Supervisors,监控Communications Drivers 通讯驱动production route ID 产品序列ID OWS PCSI 操作工操作画面retrieving data 检索数据terminal 终端Data storage数据存储Data process数据进程TWS隧道炉技术工作站Stock虚拟或者是真是存在的板坯Soaking均热段Shuttle横移车轧机区域(控制) Constant Force Regulation (CFR) 恒张力调节Coiling Temperature Control (CTC) 卷曲温度控制COOLING PATTERN 冷却模式Combustion ratio 空燃比Thermocouple 热电偶Zone 区Subzone 子区The acceleration point 力口速点MPC (model predictive control)模型预设定Furnace adaptation力口热炉自学习Offset补偿值Steel group 钢种族Stock class板坯类型Density 密度Conductivity 导热性Convection 热交换Specific heat 比热Emissivity辐射系数Heat diffusion 热扩散率PWS隧道炉过程工作站Data flow数据流Material flow 材料流Set-point 设定值COILING TEMPERATURE SET U P (CTSU) 层冷设定Short Stroke Control(SSC)短行程控制Rolling sequence 轧制序歹列Mill line tracking 轧线跟踪Transport Director 运输导向Roughing Mill Tracking 粗轧跟踪Finishing Mill Tracking 精轧跟踪Post-Coiler Tracking 加速卷曲跟踪looper control 活套控制RM descale spray code粗轧除鳞喷淋代码Target finishing thickness目标成品厚度Target finishing width 目标成品宽度Target finishing temperature目标成品温度Target coiling temperature目标钢卷温度Target crown 目标凸度Target wedge 目标楔度Target flatness 目标平直度Finishing thickness tolerance成品厚度公差Finishing width tolerance成品宽度公差Finishing temperature tolerance成品温度公差Coiling temperature tolerance钢卷温度公差Crown tolerance 凸度公差Wedge tolerance 楔度公差Flatness tolerance 平直度公差Run-out table spray code输出辊道喷淋代码Strapping code 打捆代码Roughing Mill Setup (RSU)粗轧启动Holding Table Transfer (HTT)辊道保持传输Finishing Mill Setup (FSU) 精轧启动DeliveryTemperature Control (FDTC) 成品传输温度控制Tracking Director(TD)跟踪系统导向RollThermal and Wear(RTW)轧辊温度和磨损值Operation and Material Flow (OMF) 操作和物流Mill Event Diagram (MED)轧机事件图Roughing stand 粗轧机架Automatic Gauge Control(AGC) 自动厚度控制Back Up Roll(BUR) 支撑辐Cold Metal Detector(CMD)冷金属检测Crop Shear(CS) 切头剪Coiler SetUp(CSU) 卷曲机设定Coiling Temperature FeedBackControl(CTFB)卷曲温度反馈设定CTC Management and Interface Control(CTMI)Coiling Temperature Learning Calculation (CTLC)卷曲温度学习计算Coiling Temperature SetUp calculation (CTSU)卷曲温度设定计算FM Delivery Temperature Control (FDTC)精轧出口温度控制Width gage at FM Delivery(FDW)精轧出口宽度仪表Pyrometer at FM Entry(FET)精轧入口高温计Finisher Model Learning Calculation (FMLC)精轧计算模型Finisher Scale Breaker(FSB)精轧除鳞Finisher SetUp(FSU)精轧设定Finisher SetUp Calculation(FSUC)Blow off 吹扫Trimming cooling 修正冷去却Edge masking 边部遮挡Roll force distribution mode轧制力分配模Roll force ratio 轧制力比Hot Metal Detector(HMD)热金属检测器Hydraulic Position Control (HPC)液压位移控制Hydraulic Scale Breaker(HSB)除鳞Heat Transfer Table(HTT)热传输辊道Inter-Stand Cooling spray(ISC)机架间冷却Multi Function Gage(MFG)多功能仪表Roll Gap Lubrication(RGL)辊缝润滑Roll Gap Spray(RGS)辐缝喷嘴Run Out Table(ROT)输出辐道Rougher SetUp(RSU)粗轧设定Rougher SetUp Calculation(RSUC)WR cooling Spray(WCS)工作辐冷AGC 自动辐缝控制BUR 支撑辐CMD 冷金属检测仪CS, C/S 飞剪卷曲温度控制管理和接口控制精轧设定计算CSU 卷取设定CT 卷取入口高温计CTC 卷取温度控制CTFB 卷取温度反馈控制CTLC 卷取温度自学习计算CTSU 卷取温度设定计算DC, D/C 地下卷取机Ei Ei 立辑(i=1,2)F1E 精轧前立辊Fi Fi精轧机架(i:机架号)FDH精轧出口测厚仪FDF精轧出口平直度仪FDP精轧出口凸度仪FDT精轧出口高温计FDTC 终轧温度控制FDW精轧出口宽度仪FET 精轧入口高温计FM 精轧FMLC 精轧模型自学习计算FSB 精除鳞FSS抑尘水FSU 精轧设定FSUC 精轧设定计算HMD 热金属检测仪HPC 液压位置控制HSB高压除鳞装置HTT中间辊道ISC机架间冷却水ISD机架间除鳞ISF感应加热炉MFG多功能仪表MT 层冷辊道中间温度计MTFB 中间温度反馈控制MTFF 中间温度前馈控制PDI 原始数据输入PET 侧压机入口高温计PEW 侧压机入口测宽仪Ri Ri粗轧机(i=1,2)RiDT Ri出口高温计RiDW Ri出口宽度仪RF 加热炉RGL 辐缝润滑RGS 辐缝水RMLC 粗轧模型自学习计算ROT层冷(输出)辐道RSU 粗轧设定RSUC 粗轧设定计算SSP 侧压机SSUC 板形设定计算TVD 时间速度距离曲线WR 工作辐WCS 工作辐冷却FMET精轧入口温度FDT (轧机出口温度)MT (层冷中间温度)CT (卷曲温度)实际值Top sprays 上喷淋bottom sprays 下喷淋cross sprays 吹扫喷淋invoked 被调用dry head干头(不浇水)hot head热头(少浇水)hot tail 热尾Ghost rolling模拟轧制SCC (Supervisory Computer Control)GFC功能文档ROT Run Out Table 输出辐道Mandrel 芯轴Side guide 侧导板(SG)Pinch roll夹送辐Default默认(拖欠,违约)Target profile 目标凸度Coil Dia 钢卷卷径(Outer Diameter)Auto Step Control自动踏步控制Treading Device 穿带设备Wrapper Roll 助卷辐constant table 常量表Coil to Coil slab 单卷板坯semi-endless slab 半无头板坯C/E/SE单卷/无头/半无头Full Expand Wrap芯轴膨胀圈数Wrapper Roll Open Wrap助卷辐压靠圈数coil to coil单卷模式RTC roll thermal crown 轧辐凸度控制edge contour边部形状strip shape control 板形控制CVC 为Continuously Variable CrownSSUC板形设定计算SSU板形设定SMLC板形自学习设定FGC flying gauge control 动态厚度控制FPC flying gauge point control厚度快速变化点控制Bar中间坯MLC Model self-learning calculation 模型自学习计算ISC (机架间冷却水)ISD机架间除鳞批次间(LTL-lot to lot)GCI二级钢种代码索引表grade code index FDW final data width 精轧测宽仪CEW测宽仪Closed loop control 闭环控制Spare field备用字段Flow chart scheme流程图方案Pick up得到信号Torque model转矩模型Thermal conductivity 导热系数Emissivity辐射系数Specific heat 比热容Thermal diffusivity 扩散系数Thermal effusivity 蓄热系数Elasticity弹性系数Transfer bar 中间坯Width draft 减宽量Proportional valves 比例阀Coil marking 喷号机FDM finite difference method 有限差分法specific heat 比热coolant冷却液fraction 分数latent heat 潜热threading speed 穿带速度preset预设load cell 压头pressure transducer 压力传感器SIS surface inspection system 表检系统HSM hot strip millMMMS Muti-Mode Mill Set-upAWC automatic width control 自动宽度控制Thermal diffusivity 热扩散系数Thermal effusivity 蓄热系数Multiplier 乘数Enthalpy热函,焓,热含量SEM spray efficiency modifierIHSU induction heater setup calculationIHDC induction heater dynamic controlIHFFIHFBIHLC induction heater model learning calculationICSU intensive cooling set up calculationICDC intensive cooling dynamic controlICFF intensive cooling feed forward controlMMLC Mill model learning calculationStd.i Mill stand numberBunit Unit widthCp Specific heatCs Cooling rateLunit Unit lengthQtransfer Latent heat released by phase transformation Qspy Heat transfer of laminar and bottom sprays Camber镰刀弯Levitation 翘头Commissioning 试车Roll shop轧辐间CTDC CT Dynamic Control Mandrel speed芯轴速度。
粗轧机功能描述-rev01

Job 0053 ContractualitemZY-2004-66-NE-4-1ERZHONG item(04)325301TitleRoughing Mill Functional DescriptionApprovalsRemarks02 05-01-0501 04-12-8 ERZHONG ISSUE OF DETAIL DESIGNPHASEHu YiGe XianyuLu Qingchun Qi Xiaohu00 04-07-22 ERZHONG ISSUE OF DESIGN PHASE Hu YiGe XianyuLu Qingchun Qi XiaohuRev. File Date Revisions description Drawn Checked Approved1设备总体概况3 2设备分项说明32.132M2005-2021粗轧机本体(13253.204) (3)2.1.132M2005: R1 - MILL SPINDLE HEAD HOLDER (13253.204.11) (3)2.1.1.1设备概况 (3)2.1.1.2设备结构及传动示意图 (3)2.1.1.3技术参数 (3)2.1.1.4控制要求 (3)2.1.1.5电机和电器工艺检测仪表 (3)2.1.1.6液压控制系统电磁阀动作表及相关信息 (3)2.1.234M2006: Electromechanical Screwdown(13253.204.03) (3)2.1.2.1设备概况 (3)2.1.2.2设备结构及传动示意图 (3)2.1.2.3技术参数 (3)2.1.2.4控制要求 (3)2.1.2.5电机和电器工艺检测仪表 (3)2.1.332M2007: R1 - CLAMPING MECHANISM (13253.204.01) (3)2.1.3.1设备概况 (3)2.1.3.2设备结构及传动示意图 (3)2.1.3.3技术参数 (3)2.1.3.4控制要求 (3)2.1.3.5电机和电器工艺检测仪表 (3)2.1.3.6液压控制系统电磁阀动作表及相关信息 (3)2.1.432M2008: R1 W.R. RAILS LIFTING(13253.204.06) (3)2.1.4.1设备概况 (3)2.1.4.2设备结构及传动示意图 (3)2.1.4.3技术参数 (3)2.1.4.4控制要求 (3)2.1.4.5电机和电器工艺检测仪表 (3)2.1.4.6液压控制系统电磁阀动作表及相关信息 (3)2.1.532M2009: R1 W.R. BALANCE(13253.204.01) (3)2.1.5.1设备概况 (3)2.1.5.2设备结构及传动示意图 (3)2.1.5.3技术参数 (3)2.1.5.4控制要求 (3)2.1.5.5液压控制系统电磁阀动作表及相关信息 (3)2.1.632M2010: R1 BUR. BALANCE(13253.204.04) (3)2.1.6.1设备概况 (3)2.1.6.2设备结构及传动示意图 (3)2.1.6.3技术参数 (3)2.1.6.4控制要求 (3)2.1.6.5电机和电器工艺检测仪表 (3)2.1.6.6液压控制系统电磁阀动作表及相关信息 (3)2.1.732M2011: R1 HAGC (13253.204.12) (3)2.1.832M2002: R1 AC MAIN DRIVE(13253.205) (3)2.1.8.1设备概况 (3)2.1.8.2设备结构及传动示意图 (3)2.1.8.3技术参数 (3)2.1.8.4控制要求 (3)2.1.8.5电机和电器工艺检测仪表 (3)2.1.8.6液压控制系统电磁阀动作表及相关信息 (3)2.1.932M2013: R1 阶梯垫调整及支承辊换辊滑台 (13253.204.07) (3)2.1.9.1设备概况 (3)2.1.9.2设备结构及传动示意图 (3)2.1.9.3技术参数 (3)2.1.9.4控制要求 (3)2.1.9.5电机和电器工艺检测仪表 (3)2.1.9.6液压控制系统电磁阀动作表及相关信息 (3)2.1.1032M2015: R1 ENTRY /EXIT STRIPPERS AND GUIDES (13253.204.05) (3)2.1.10.1设备概况 (3)2.1.10.2设备结构及传动示意图 (3)2.1.10.3技术参数 (3)2.1.10.4控制要求 (3)2.1.10.5电机和电器工艺检测仪表 (3)2.1.10.6液压控制系统电磁阀动作表及相关信息 (3)2.1.1132M2016: R1 – ENTRY/EXIT FEED ROLLERS (13253.204.08) (3)2.1.11.1设备概况 (3)2.1.11.2设备结构及传动示意图 (3)2.1.11.3技术参数 (3)2.1.11.4控制要求 (3)2.1.11.5电机和电器工艺检测仪表 (3)2.1.1232M2013:油膜轴承润滑监测系统 (3)2.1.12.1控制要求 (3)2.1.12.2电机和电器工艺检测仪表 (3)2.1.1332M2021:工作辊冷却装置 (3)2.1.13.1设备概况 (3)2.1.13.2设备结构及传动示意图 (3)2.1.13.3技术参数 (3)2.1.13.4控制要求 (3)2.1.13.5电机和电器工艺检测仪表 (3)5) 32.1.1432M2021:支承辊冷却装置 (3)2.1.14.1设备概况 (3)2.1.14.2设备结构及传动示意图 (3)2.1.14.3技术参数 (3)2.1.14.4控制要求 (3)2.1.14.5电机和电器工艺检测仪表 (3)2.232M2101: R1-W.R.CHANGING SYSTEM (13253.206) (3)2.2.132M2101: R1-W.R.CHANGING SYSTEM (3)2.2.1.1设备概况 (3)2.2.1.2设备结构及传动示意图 (3)2.2.1.3技术参数 (3)2.2.1.4换工作辊步序 (3)2.2.232M2101:工作辊液压缸推拉装置 (3)2.2.2.1设备概况 (3)2.2.2.2设备结构及传动示意图 (3)2.2.2.3技术参数 (3)2.2.2.4控制要求 (3)2.2.2.5电机和电器工艺检测仪表 (3)2.2.2.6液压控制系统电磁阀动作表及相关信息 (3)2.2.332M2101:工作辊横移装置 (3)2.2.3.1设备概况 (3)2.2.3.2设备结构及传动示意图 (3)2.2.3.3技术参数 (3)2.2.3.4控制要求 (3)2.2.3.5电机和电器工艺检测仪表 (3)2.2.3.6液压控制系统电磁阀动作表及相关信息 (3)2.2.432M2101工作辊推拉缸翻转装置 (3)2.2.4.1设备概况 (3)2.2.4.2设备结构及传动示意图 (3)2.2.4.3技术参数 (3)2.2.4.4控制要求 (3)2.2.4.5电机和电器工艺检测仪表 (3)2.2.4.6液压控制系统电磁阀动作表及相关信息 (3)2.2.532M2101:工作辊轨道摆动装置 (3)2.2.5.1设备概况 (3)2.2.5.2设备结构及传动示意图 (3)2.2.5.3技术参数 (3)2.2.5.4控制要求 (3)2.2.5.5电机和电器工艺检测仪表 (3)2.2.5.6液压控制系统电磁阀动作表及相关信息 (3)2.332M2102: R1支承辊换辊系统(13253.206) (3)2.3.1.1设备概况 (3)2.3.1.2设备结构及传动示意图 (3)2.3.1.3技术参数 (3)2.3.1.4控制要求 (3)2.3.1.5电机和电器工艺检测仪表 (3)2.3.1.6液压控制系统电磁阀动作表及相关信息 (3)1 设备总体概况R1四辊可逆粗轧机是设置在热连轧带钢生产线粗轧区的关键设备,R1四辊可逆粗轧机位于E1立辊轧机之后、粗轧机输出辊道之前,与E1立辊轧机、粗轧机前后工作辊道、侧导板配合完成从连铸坯料轧制到中间坯的轧制过程。
热轧工艺设备简介

四、热轧厂主要厂房、设备的分布
33000
外来坯 外供坯
33000 堆垛号 55~84
一、板坯库
33000
1-K
堆垛号 63~78
45000 21000
48000
PHS 堆垛号 71~78 PHS
PHS
014
PHS
012
011
PHS
PHS 堆垛号 55~62 PHS
PHS
010
009
008
007
• 精轧机组的穿带速度、加速度、最大轧制速度、各机架压 下量、PC轧机的交叉角、机架弯辊力等均由计算机控制系 统按轧制带钢的品种和规格进行计算和设定,并可动态调 整,实现板形的闭环控制。为了有效的控制带钢质量,在 F7精轧机出口处设有凸度、平直度以及厚度、宽度、温度 等轧线检测仪表。 由精轧机轧出的带钢经输出辊道上的层流冷却装置冷却, 将带钢冷却到规定的卷取温度。为提高冷却精度,该层流 冷却装置分为精调段和微调段,高位水箱布置在输出辊道 旁侧。计算机过程控制系统将根据钢种、规格、轧制速度、 终轧温度、卷取温度的不同要求,对层流冷却方式、冷却 速度和水量进行设定,以保证产品的机械性能。带钢经冷 却后,由三助卷辊式全液压卷取机卷取成钢卷。卷取后的 钢卷,由卸卷小车从卷取机卸出运送到打捆站,在打捆站 经打捆后,出口钢卷小车将钢卷送到快速运输链上。
连接辊道有10个辊子组成,位于2#加热炉装炉辊道 (A8)端头,是用于连接称量辊道(A6)和装炉辊道,将 板坯从板坯库运输到加热炉侧的装置。中间辊道(A9)有8 个辊子组成,位于1#、2#加热炉侧的两组装炉辊道(A8、 A10)之间,是用于连接装炉辊道和运送板坯的装置。
1、板坯称重辊道
位于板坯运输辊道端部,是用于联接板坯库运输辊道 与加热炉上料辊道线上的连接辊道(A7)的板坯运送装置, 板坯在该辊道上进行称量。 设备结构 辊子装配:辊子由安装在轴承座内的调心滚子轴承支撑, 轴承座固定在辊道架上。辊子为实心锻钢件,轴承座为铸 钢件。 传动机构:辊子为单独传动辊,每个辊子均采用带减速 电动机,通过齿形联轴器与辊子连接驱动,均可正、反转, 变频调速。 侧导板和导向板:侧导板和导向板为焊接件。辊道两侧 均安装有侧导板,以引导板坯正确运行。辊子间设置有导 向板,侧导板采用插入式与辊道架固定。 润滑:辊子轴承采用集中干油润滑,齿轮减速箱采用油 浴润滑。齿形联轴器采用干油枪 手工润滑加油 。 冷却:辊子的辊颈采用喷水冷却。
项目六 高速线材粗中轧操作教案

掌握导卫安装与调整方法。
能分析典型生产事故并提出解决措施。
重点
难点
粗中轧区域操作和各项参数
教学环节时间分配
3课时
教学手段、教学方法和实施步骤
多媒体
授课内容:
任务一:粗、中轧区的设备布置与参数
一、粗中轧轧制工艺与机组布置
1.粗、中轧的主要功能
粗轧是使坯料得到初步压缩和延伸,得到温度合适、断面形状正确、尺寸合格、表面良好、端头规矩、长度适合工艺要求的轧件。中轧的作用是继续缩减粗轧机组轧出的轧件断面。
(2)参照原孔型高度设定新孔型的辊缝值。
(3)调整冷却水管的位置,使冷却水能准确地浇在新轧槽上。
(4)横移轧机使新的在用轧槽处在轧制线位置上
三、粗、中轧机组轧制过程中的轧机调整操作
1.导卫操作
(1)辊式导卫的辊间距调整
原则:辊间距的设定是通过标准试棒进行的,以试棒在两导辊间能推拉带动两辊同时转动为合适。
(4)轧辊对装入机架辊头调整后,轧辊对即可被装入机架,涂抹润滑油。
(5)轧辊轴向定位、紧固与辊缝初步设定经常对轧机牌坊内侧的衬板,以及基准轧辊的垫板进行检查,更换必要的磨损件。在安装轧辊时,要用水平尺对基准辊进行水平度的测量。
2.导卫安装与调整
(1)导板梁标高的找正关系到轧制能否稳定进行
(2)导卫横梁移动通过横移导卫横梁来实现
5.粗轧后切头、尾
轧件头尾两端的散热条件不同于中间部位,轧件头尾两端温度较低,塑性较差;同时轧件端部在轧制变形时由于温度较低,宽展较大,同时变形不均造成轧件头部形状不规则,这些在继续轧制时都会导致堵塞入口导卫或不能咬入。为此在经过道次粗轧后必须将端部切去。通常切头切尾长度为70~200mm。
- 1、下载文档前请自行甄别文档内容的完整性,平台不提供额外的编辑、内容补充、找答案等附加服务。
- 2、"仅部分预览"的文档,不可在线预览部分如存在完整性等问题,可反馈申请退款(可完整预览的文档不适用该条件!)。
- 3、如文档侵犯您的权益,请联系客服反馈,我们会尽快为您处理(人工客服工作时间:9:00-18:30)。
粗轧机(工)换辊程序
选择粗轧机换辊模式。 接轴定位并关闭轧辊冷却水。 打开上下工作辊清辊器(WIPER),下工作辊平衡卸荷。 压下螺丝抬升至上限(上辊系和接轴平衡同时抬升),支撑辊安全锁栓 锁紧。 上接轴抬升到位并锁定。 工作辊换辊轨道抬升(下接轴平衡同时抬升)。 下接轴夹紧缸夹紧,下接轴平衡缸卸荷。 工作辊推拉缸推至轧机后挂钩并将下工作辊轴端挡板打开。
电动小车
移动行程:
约20m 移动速度: 17.8m /s 传动功率: 15kW@580rpm 速比: 47.4:1 工作辊直接由电动小车送入轧辊间
支撑辊换辊系统
推拉缸行程:
系统压力:
换辊速度:
约6500mm 160bar 最小35 mm /s 最大70 mm /s
系统压力: 160bar 操作速度: 25mm/s l 轨道的提升和下降由液压缸完成 l 轨道上装有耐磨衬板
工作辊,工作辊轴承座及轴承
辊子直径:
l l l l l
最大1200mm 最小1080mm 辊身长度: 1750 mm 辊子材质: 无限冷硬球磨铸铁 辊子硬度: 60-65肖氏硬度 轴承座材质: 铸钢 轴承类型: 4列圆锥滚子轴承 工作辊材质为无限冷硬复合球墨铸铁 工作辊轴承座由铸钢制成,装有可更换耐磨衬板 工作辊轴承采用四列圆锥滚子轴承 非传动侧的工作辊下轴承座上,装有与换辊油缸连接的卡座 轴承的润滑为手动干油润滑
支撑辊,支撑辊轴承座及轴承
l 支撑辊材质为锻钢
l 支撑辊轴承座为铸钢件
l 支撑辊轴承为摩根轴承 l 轴承座表面润滑由集中干油润滑系统提供 l 油膜轴承通过快速接头与稀油润滑系统连接 粗轧机和精轧机的支撑辊和油膜轴承完全相同,可以互换
支撑辊平衡系统
系统压力: 160bar 操作速度: 30mm/s 支撑辊平衡采用液压平衡
工作辊支撑辊的冷却系统
运行压力:
10bar 集管数量: 4 工作辊设有冷却集管,安装在牌坊之间的进口和出口导卫上 运行压力: 10bar 集管数量: 2 支撑辊用水冷却,冷却集管位于进口及出口导卫上
入口及出口除鳞系统
系统压力:
200bar 出口压力: 180bar 集管数量: 2×2 水流量: 180m3/hr×2 除鳞集管分上、下两部分,轧机的进口出口均装有除鳞集 管
粗轧机出口侧导板
推床开口度: 最小 750mm 最大1750mm 辊道速度: 0—100mm/s(每边) 最大夹紧力: 50t 总长: 约9850 mm · 侧导板由平行推头组成,安装在粗轧机出口侧辊道上 · 液压驱动,液压缸带位置传感器 · 推头带有可更换耐磨衬板 轴承的润滑由集中干油润滑系统提供
粗轧机(支)换辊程序
导杆、入口和出口侧导轨
导杆为铸钢件,分别装在轧机轧制线上下 入口和出口导轨安装在轴承座和轧辊托架上
粗轧机
类型:
四辊可逆式轧机 辊长度: 1750mm 最大轧制力: 40000kN 最大轧制速度: 5.5m/s(每边) 主传电机功率: 2×5000kW 立辊轧机位于粗轧机入口处。 l 型式:四辊可逆式 l 电动压下,预留HAGC液压缸位置 l 设有工作辊快速换辊系统 l 机架入/出口侧导卫上装有除鳞装置
l
Hale Waihona Puke 支撑辊由液压缸从轧机中拉出,用天车将更换的支撑辊吊走
支撑辊换辊时,由天车将盖板及横移小车吊走
粗轧机输出辊道
辊道长度:
辊距:
辊子数量:
约14800mm(在两个端辊中心线之间) 800和1000mm 19 Φ 400mm×1750mm
辊子尺寸:
辊道速度: 0-5.5m/s 驱动功率: 31.0kW · 输出辊道安装在粗轧机的出口侧 · 辊子为实心锻钢 · 辊身全长水冷 · 轴承与集中干油润滑系统连接 辊子通过齿式联轴器由电机直接单独传动
入口推床
推头
箱体
立辊轧机
类型:
全液压驱动型 辊缝开口度: 最小 700mm 最大1750mm 速度: 0-5.5m/s(每边) 最大减宽量: 90 mm(45 mm每边)对220厚的板坯 驱动功率: 2×900kW 转速: 0-180/480rpm 速比: 4.8:1 l 立辊通过齿轮箱和重型万向传动轴由立式马达(每辊配一个电机)传动 l 主传动马达电气同步 l 齿轮润滑采用稀油循环润滑
工作辊平衡系统
系统压力: 平衡液压缸:
160bar 上平衡缸4 下平衡缸4
支撑辊,支撑辊轴承座及轴承
辊子直径:
最大1450mm 最小1300mm 辊身长度: 1750 mm 辊子材质: 合金锻钢 辊子硬度: 55—60肖氏硬度 轴承座材质: 铸钢 轴承类型: 油膜轴承54”-75KLS 止推轴承: 锥形滚子轴承(非传动侧) 工作辊的平衡由设在平衡块上的液压缸平衡
工作辊推拉缸将下辊拉出220mm。
上工作辊平衡卸荷(下接轴同时下落),上接轴夹紧缸夹紧。 上接轴平衡泄荷,上工作辊轴端挡板打开。
粗轧机(工)换辊程序
工作辊推拉缸将辊拉出至横移位置并向前推25mm自动脱钩,退回初始位
置(油缸完全缩回)。 横移小车横移。 工作辊推拉缸将新辊推入轧机,调整入出口导卫板(STRIPPER)的正确 位置。 上接轴平衡ON,上接轴夹紧缸打开,上工作辊轴端挡板闭合,上工作辊 平衡ON。 上接轴平衡解锁。 工作辊推拉缸将下辊推到位并闭合下工作辊轴端挡板。 工作辊推拉缸退至中间位置。 下接轴平衡ON,下接轴夹紧缸打开。 工作辊轨道抬升缸下落,下工作辊平衡ON。 上下清辊器闭合,支撑辊安全锁栓解锁。 开启轧辊冷却水,启动主传爬行。 数据设定(调零),轧机设定(下一块板坯)。
机架辊
机架辊 机架辊 传动轴 轧机牌坊 机架辊 离合 机架辊 电机
工作辊更换系统
推拉缸行程:
约7800 mm 侧移缸行程: 约1650mm 系统压力: 160bar 换辊速度: 最小50 mm /s 最大200 mm /s 侧移速度: 100 mm /s 翻转速度: 70 mm /s l 工作辊换辊系统位于轧机非传动侧 l 工作辊换辊系统主要由拉出液压缸,横移小车等组成 工作辊推入、拉出及横移小车横移均为液压传动
入口和出口侧机架辊
辊子数量:
2(每边1根) 辊子尺寸: Φ450mm×1660mm 辊道速度: 0—5.5m/s 驱动功率: 60.0kW l 入口和出口侧机架辊位于下工作辊两边 l 机架辊为实心锻钢 l 机架辊单独传动、带冷却集管 l 轴承箱采用防水密封结构 机架辊的润滑由集中干油润滑系统供给
入口主辊道
滑架
辊子
联轴器
电机
长轴
粗轧机入口推床
推床开口度:
l
最小 750mm(在两个端辊中心线之间) 最大1750mm 速度: 0-100mm/s(每边) 总长: 约13700 mm 喇叭口长度: 约4800 mm 平行断长度: 约8900 mm l 侧导板由平行梁部分及拖梁组成,安装在粗轧机入口辊道上 l 侧导板为液压驱动,液压缸带位置传感器 l 侧导板平行梁部分及拖梁可快速拆卸,以便辊道检修及维护 轴承润滑由集中干油润滑系统提供
立辊轧机牌坊
l l
牌坊:铸钢结构 牌坊上装有可更换的耐磨衬板 滑动面的润滑由集中干油润滑系统提供
液压AWC(宽度自动控制)系统
宽度控制
液压缸驱动(每边2个) 系统压力: 290bar 工作压力: 250bar 液压缸行程: 575 mm 速度: 短行程(25m) 125mm/s 长行程40mm/s 平衡 液压推拉缸(每边1个) a) 立辊轧机装有用于轧辊辊缝设置、AWC调整、SSC功能的液压 缸, 液压缸带位置传感器。 b) 液压缸为电气同步。 c) 立辊的轧制力由AWC压力传感器测量
立辊轧机轧辊、轴承、轴承座和轧辊托架
辊子直径:
l l l l
l
最小1300/1000mm 最大1300/1100mm 辊身长度: 630 mm 辊子材质: 合金锻钢 辊子硬度: 45-50肖氏硬度 立辊轧机轧辊为锻钢件,采用抗磨圆锥滚子轴承 轧辊和轴承座可快速更换 轧辊采用水冷却 轧辊更换时,接轴由液压缸提升 轧辊平衡为液压方式
压下螺丝、螺母
压下螺丝
压下螺母
球面垫
轧机传动轴及电机中间轴
数量: 2 类型:十字轴式万向接轴 两接点之间距离:约11000mm 最大额定扭距: 2150kNm 最大设计扭距: 4000kNm 轧机传动轴为十字轴式万向接轴 工作辊通过万向接轴由电机单独传动 上、下万向接轴为液压平衡,并在维修时有液压传动 的锁紧装置 万向接轴两端的润滑均为手动干油润滑 电机中间轴
粗轧机
粗轧机机架、耐磨衬板及机架底板
牌坊立柱横切面面积: 约7000cm2
轧机刚度:
6MN/ mm 窗口尺寸: 7365 mm×1930 mm 机架高度: 约10500 mm 机架宽度: 约4500 mm l 轧机机架由两片铸钢牌坊及上下横梁组成,牌坊为闭式结构 l 在牌坊窗口内装有可更换的耐磨衬板。 l 机架底板用于牌坊固定 l 底板设有调节阶梯垫 测压头装在牌坊的下方
立辊轧机
立辊减速机 立辊提升装置
立辊牌坊
立辊万向轴
立辊扁头套 立辊轴承座
立辊