SMT焊点可靠性
smt焊接工艺技术指标
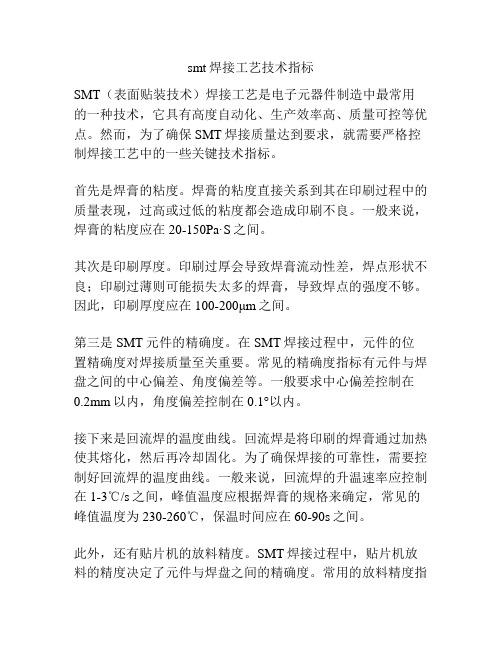
smt焊接工艺技术指标SMT(表面贴装技术)焊接工艺是电子元器件制造中最常用的一种技术,它具有高度自动化、生产效率高、质量可控等优点。
然而,为了确保SMT焊接质量达到要求,就需要严格控制焊接工艺中的一些关键技术指标。
首先是焊膏的粘度。
焊膏的粘度直接关系到其在印刷过程中的质量表现,过高或过低的粘度都会造成印刷不良。
一般来说,焊膏的粘度应在20-150Pa·S之间。
其次是印刷厚度。
印刷过厚会导致焊膏流动性差,焊点形状不良;印刷过薄则可能损失太多的焊膏,导致焊点的强度不够。
因此,印刷厚度应在100-200μm之间。
第三是SMT元件的精确度。
在SMT焊接过程中,元件的位置精确度对焊接质量至关重要。
常见的精确度指标有元件与焊盘之间的中心偏差、角度偏差等。
一般要求中心偏差控制在0.2mm以内,角度偏差控制在0.1°以内。
接下来是回流焊的温度曲线。
回流焊是将印刷的焊膏通过加热使其熔化,然后再冷却固化。
为了确保焊接的可靠性,需要控制好回流焊的温度曲线。
一般来说,回流焊的升温速率应控制在1-3℃/s之间,峰值温度应根据焊膏的规格来确定,常见的峰值温度为230-260℃,保温时间应在60-90s之间。
此外,还有贴片机的放料精度。
SMT焊接过程中,贴片机放料的精度决定了元件与焊盘之间的精确度。
常用的放料精度指标有X轴、Y轴方向的偏差。
一般要求X轴、Y轴方向的偏差控制在±0.05mm以内。
最后是可靠性测试。
在SMT焊接工艺中,可靠性测试是评估焊接质量是否达到要求的重要指标之一。
常见的可靠性测试有剪切力测试、耐热性测试、振动测试、冷热冲击测试等。
通过可靠性测试,可以评估焊接过程中是否存在缺陷或潜在问题。
综上所述,SMT焊接工艺技术指标是确保SMT焊接质量达到要求的重要因素。
在实际生产中,需要控制好焊膏的粘度、印刷厚度、元件的精确度、回流焊的温度曲线、贴片机的放料精度等。
通过严格控制这些指标,可以保证焊接质量的可靠性和稳定性。
表面组装技术SMT基本常识简介

基础知识SMT基础知识SMT(Surface Mounted Technology)是目前电子组装行业最流行的技术和工艺。
SMT有什么特点:电子产品组装密度高,体积小,重量轻。
贴片元器件的体积和重量只有传统插件的1/10左右。
一般采用SMT 后,电子产品体积会缩小40%~60%,重量会减轻60%~80%。
可靠性高,抗振能力强。
焊点不良率低。
良好的高频特性。
减少了电磁和射频干扰。
易于实现自动化,提高生产效率。
成本降低30%-50%。
节省材料、能源、设备、人力、时间等。
为什么要用SMT:电子产品追求小型化。
过去用的打孔插件,并不能减少电子产品的功能,让电子产品更齐全。
所用的集成电路(IC)没有冲压元件,特别是大规模、高集成度的IC,不得不采用表面贴装元件,进行批量生产和自动化。
制造商应以低成本和高产量生产高质量的产品,以满足客户需求,并加强开发具有市场竞争力的电子元件。
随着集成电路(IC)的发展和半导体材料的多种应用,电子技术革命势在必行,追逐SMT工艺流程的国际潮流——双面组装工艺A:来料检验、PCB的A面丝印焊膏(点胶)、烘干(固化)、A面回流焊、清洗、翻板、PCB的B面丝印焊膏(点胶)、烘干和回流焊(B:来料检验、PCB的A面丝印焊膏(点胶)、烘烤(固化适用于PCB板A面回流焊和B面波峰焊。
在组装在PCB B侧的SMD 中,当只有SOT或SOIC(28)引脚在下方时,应采用这种工艺。
助焊剂产品的基本知识。
表面贴装用助焊剂的要求:残留在基板上的助焊剂残渣具有一定的化学活性,热稳定性好,润湿性好,能促进焊料的膨胀,对基板无腐蚀性,可清洗性好的氯含量在0.2%(W/W)以下。
二。
通量的作用。
焊接过程:预热/开始熔化焊料/形成焊料合金/形成焊点/固化焊料。
作用:辅助传热/去除氧化物/减少表面力/防止再氧化。
描述:溶剂蒸发/被加热,助焊剂覆盖基板和焊料。
表面,使传热均匀/释放活化剂与基板表面的离子氧化物反应,去除氧化膜/使熔融焊料的表面力变小,润湿良好/覆盖高温焊料表面,控制氧化提高焊点质量。
SMT焊点的可靠性研究
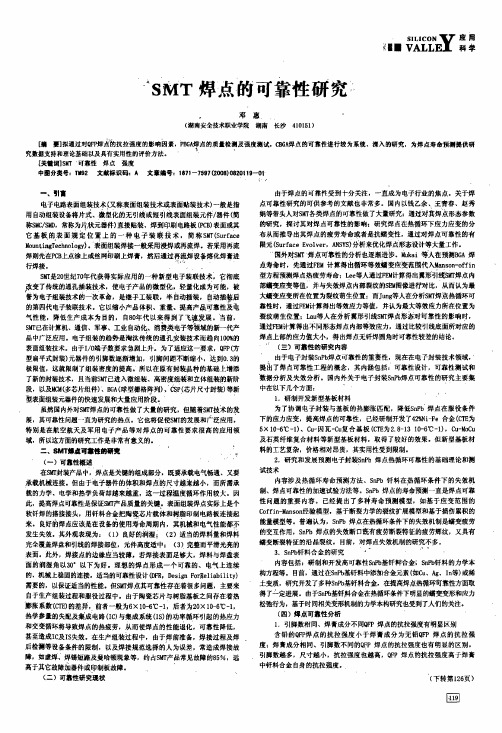
由于焊点的可靠性受到十分关注,一直成为电子行业的焦点。关于焊
点可靠性研究的可供参考的文献也非常多。国内以钱乙余,王青春、赵秀
娟 等带 头人 对 s 耵 各类 焊点 的 可靠 性 做了 大量 研 究: 通过 对 真焊 点 形态 参数
的研究,探讨其对焊点可靠性的影响;研究焊点在热循环下应力应变的分
布从而推导出其焊点的疲劳寿命或者是抗蠕变性,通过对焊点可靠性的有
行焊 接。
。…,
S耵是20世纪70 年代获得实际应用的一种新型电子装联技术。它彻底
改变了传统的通孔插装技术。使电子产品的微型化,轻量化成为可能,被
誉为电子组装技术的一次革命,是继手工装联,半自动插装,自动插装后
的第四代电子装联技术。它以缩小产品体积、重量、提高产晶可靠性及电
气性能,降低生产成本为目的,自8 0年代以来得到了飞速发展。当前, sMT已在计算机、通信、军事、工业自动化,消费类电子等领域的新~代产
通过F酬计算得出不同形态焊点内部等效应力,通过比较引线底面所对应的
焊点 上部 的应 力值 大小 ,得 出焊 点无钎 焊圆 角时 可靠 性较 差的 结论 。
’
究数据支持和 理论基础以及具有实用性的 评价方法。
[ 关麓词】s盯7可靠性焊点强度
中图分类号 :T_92 文献标识 码:^ 文章编号 :187卜一75 97( 2咖) ∞趵11 9一01_
i .t
一、 j I ■
电子电路表面组装技术( 又称表面组装技术或表面贴装技术) 一般是指
用自动组装设备将片式、微型化的无引线或短引线表面组装元件/器件( 简
部 蠕变 应变 等 值, 并 与失 效焊 点 内部 裂纹 的 s 雠 图像 进行 对 比, 从 而认 为最
李宁成博士“SMT如何选择无铅焊接材料达到焊点高可靠性”
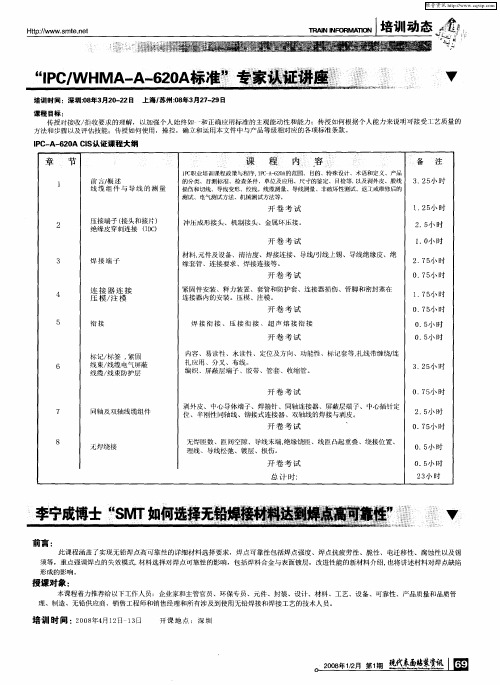
毋
培训 时 问 :深圳 :8 3 2 — 2日 上 海 , 州 :8 月2 — 9日 0年 月 02 苏 0 年3 7 2 课 程 目标 : 传授对接收/ 收要求的理解,以加强个人始终 如一和正确应用标准的主观 能动性和能力;传授如何根据 个人能力来说明可接受工 艺质量的 拒 方法和步骤 以及评估技能;传授如何使用,操控,确立和运用本文件中与产品等级相对应的各项标准条款。
冲压成形接 头、机制接头、金属环压接。
5 时 小
开 卷 考 试
焊 接 端 予 材 料 件 及 设备 、清 洁度 、 焊 接连 接 、 导线 / 元 引线 上 锡 、 导线 绝缘 皮 、 绝 缘 套 管 连接要求、焊接连接等 。
、
1 0 时 .小
2 7 小 时 .5
开 卷 考 试
1 .焊点 的腐 蚀性 1 锡 须 5 6 1 材料 对焊 点缺 陷 形成 的影 响。 7
讲师 简介一 宁成 博士 李
李宁成博士 1 6 至今,任职于美国铟科技公 司,现任该公司副总裁。在此之 前,任职 于W ih Ptesn 9年 8 rg t a tr 空军基地材料 实验室 ( 91 o 18—
的分类、 目测标准、检查条件,单位及应用、尺寸的鉴定、目检等. 以及剥外皮、股线 3 2 小 时 .5 损伤和切线、导线变形、绞线。线缆测量、导线测量、非破坏性测试、返工或维修后的
测试、电气测试方法、机械测试方法等。
0
压接端子 ( 头和接片) 接 绝缘皮穿刺连接 (D ) IC
形 成的 影 响 。
授课对象 :
本课程着力推荐给以下工作人 员:企业家和主管官员、环保专员 、元件、封装、设计 、材料 、工艺、设备、可靠性、产品质量和品质管
SMT的特点
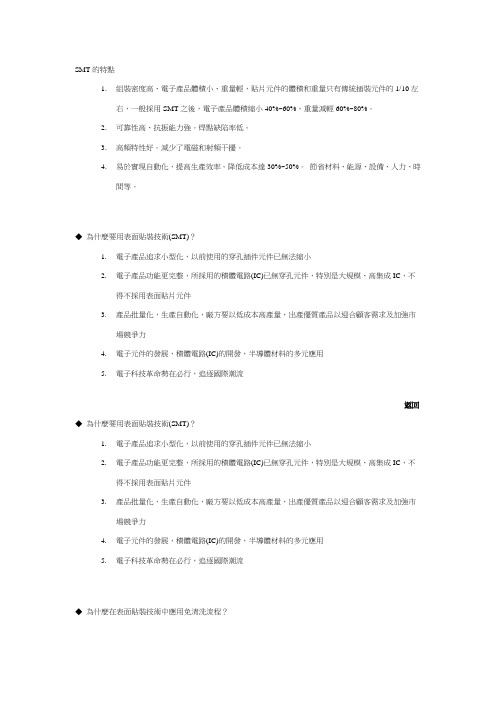
SMT的特點1.組裝密度高、電子產品體積小、重量輕,貼片元件的體積和重量只有傳統插裝元件的1/10左右,一般採用SMT之後,電子產品體積縮小40%~60%,重量減輕60%~80%。
2.可靠性高、抗振能力強。
焊點缺陷率低。
3.高頻特性好。
減少了電磁和射頻干擾。
4.易於實現自動化,提高生產效率。
降低成本達30%~50%。
節省材料、能源、設備、人力、時間等。
◆為什麼要用表面貼裝技術(SMT)?1.電子產品追求小型化,以前使用的穿孔插件元件已無法縮小2.電子產品功能更完整,所採用的積體電路(IC)已無穿孔元件,特別是大規模、高集成IC,不得不採用表面貼片元件3.產品批量化,生產自動化,廠方要以低成本高產量,出產優質產品以迎合顧客需求及加強市場競爭力4.電子元件的發展,積體電路(IC)的開發,半導體材料的多元應用5.電子科技革命勢在必行,追逐國際潮流返回◆為什麼要用表面貼裝技術(SMT)?1.電子產品追求小型化,以前使用的穿孔插件元件已無法縮小2.電子產品功能更完整,所採用的積體電路(IC)已無穿孔元件,特別是大規模、高集成IC,不得不採用表面貼片元件3.產品批量化,生產自動化,廠方要以低成本高產量,出產優質產品以迎合顧客需求及加強市場競爭力4.電子元件的發展,積體電路(IC)的開發,半導體材料的多元應用5.電子科技革命勢在必行,追逐國際潮流◆為什麼在表面貼裝技術中應用免清洗流程?1.生產過程中產品清洗後排出的廢水,帶來水質、大地以至動植物的污染。
2.除了水清洗外,應用含有氯氟氫的有機溶劑(CFC&HCFC)作清洗,亦對空氣、大氣層進行污染、破壞。
3.清洗劑殘留在機板上帶來腐蝕現象,嚴重影響產品質素。
4.減低清洗工序操作及機器保養成本。
5.免清洗可減少組板(PCBA)在移動與清洗過程中造成的傷害。
仍有部分元件不堪清洗。
6.助焊劑殘留量已受控制,能配合產品外觀要求使用,避免目視檢查清潔狀態的問題。
7.殘留的助焊劑已不斷改良其電氣性能,以避免成品產生漏電,導致任何傷害。
表面贴装焊点剪切力无合格判定标准的解析

表面贴装焊点剪切力无合格判定标准的解析发布时间:2022-08-29T01:30:36.513Z 来源:《科技新时代》2022年2期1月作者:杨绪瑶[导读] 在电子产品竞争日趋激烈的今天杨绪瑶连云港杰瑞电子有限公司江苏连云港222006摘要:在电子产品竞争日趋激烈的今天,产品质量水平不仅是企业技术和管理水平的标准,更与企业的生存和发展息息相关。
而随着元器件和PCB板的发展,SMT已成为电子组装的主流,提高产品质量已成为SMT生产中的最关键因素之一。
如何判断SMT器件焊点的可靠性,SMT工厂常常想用剪切力大小来评估。
但在整个电子制造行业中,包括国际电子工业联合会(IPC)在内的各个标准制定组织,并没有制定SMT焊接后器件的行业剪切力合格判断标准。
本文将从几个方面分析为什么行业中没有统一的器件剪切力合格判定标准,以及如何来判断SMT焊点质量是否合格。
关键词:表面贴装工艺、焊点、可靠性、标准、剪切力、合金层1、引言表面贴装工艺,又称表面贴装技术(SMT,Surface Mounted Technology的缩写),是一种无需在印制板上钻插装孔,而直接将表面组装元器件贴焊到印制线路板或其他基板表面的规定位置,用焊料使元器件与印制线路板之间构成机械和电气连接的电子组装技术。
表面贴装的最终目标是获得完美的焊点,即实现元器件与电路板之间机械和电气的完美连接。
焊点的可靠性就成为焦点关注的问题。
如何来判断焊点的可靠性是每位SMT从业人员所必须掌握的技能。
判断焊点的可靠性就需要参考相应的标准。
行业内通常想通过测试器件焊接后的剪切力值来判断焊点的可靠行。
然而,在整个电子组装行业中,有关于剪切力测试方法的标准,却没有判断剪切力值是否合格的标准。
国际电子工业联合会(IPC)作为著名的全球电子行业协会,其制定了涉及电子行业的涉及、制造和测试各个领域的标准,但依然没有焊点剪切力测试是否合格的标准。
本文就从几个专业技术角度来分析为什么整个电子组装行业没有统一的判断焊点剪切力是否合格的标准。
焊点可靠性之焊点寿命预测

— 1 —焊点可靠性之焊点寿命预测在产品设计阶段对SMT 焊点的可能服役期限进行预测,是各大电子产品公司为保证电子整机的可靠性所必须进行的工作,为此提出了多种焊点寿命预测模型。
(1) 基于Manson-Coffin 方程的寿命预测模型M-C 方程是用于预测金属材料低周疲劳失效寿命的经典经验方程[9]。
其基本形式如下:C N p f =ε∆β(1-1)式中 N f — 失效循环数;∆εp — 循环塑性应变范围;β, C — 经验常数。
IBM 的Norris 和Landzberg 最早提出了用于软钎焊焊点热疲劳寿命预测的M-C 方程修正形式[2]:)/exp()(max /1kT Q Cf N n p m f -ε∆= (1-2)式中 C, m, n — 材料常数;Q — 激活能;f — 循环频率;k — Boltzmann 常数;T max — 温度循环的最高温度。
Bell 实验室的Engelmaier 针对LCCC 封装SMT 焊点的热疲劳寿命预测对M-C 方程进行了修正[10]:c f f N /1'221⎪⎪⎭⎫ ⎝⎛εγ∆= (1-3))1ln(1074.1106442.024f T c s +⨯+⨯--=-- (1-4)式中 ∆γ — 循环剪切应变范围;f 'ε— 疲劳韧性系数,2f 'ε=0.65;c — 疲劳韧性指数;T s — 温度循环的平均温度。
采用M-C 型疲劳寿命预测方程,关键在于循环塑性应变范围的确定。
主要有两种方法:一种是解析法[10,11],通过对焊点结构的力学解析分析计算出焊点在热循环过程中承受的循环应变范围,如Engelmaier 给出[10]:— — 2 40010)]()([2-⨯-α--α=γ∆T T T T h Ls s c c (1-5)式中 L — LCCC 器件边长;h — 焊点高度;αc , αs — 分别为陶瓷芯片载体和树脂基板的热膨胀系数;T c , T s — 分别为陶瓷芯片载体和树脂基板的温度;T 0 — power-off 时的稳态温度。
回流时间对焊点质量的影响

回流时间对焊点质量的影响回流时间是指在表面贴装(SMT)中焊接过程中组件和电路板在回流炉中待留的时间。
回流时间对焊点质量有着重要的影响,以下将从不同方面进行探讨。
首先,回流时间对焊点的可靠性有直接影响。
过长的回流时间可能导致焊点过度加热,造成焊点熔化或虚焊的现象。
过短的回流时间则可能导致焊点无法完全熔化,形成不良的焊点。
因此,恰当的回流时间是确保焊点质量的关键因素之一其次,回流时间对焊点表面的润湿效果也有重要影响。
焊接时,焊料需要在焊点表面形成均匀的覆盖层,以实现焊接的连接功能。
过长或过短的回流时间都会影响焊料的润湿效果,从而影响焊点表面的质量。
适当的回流时间可以确保焊料充分润湿焊点表面,形成良好的焊点形态。
此外,回流时间还对焊点的冷却过程产生影响。
在焊接过程中,焊点瞬间受热到高温,需要通过回流时间的控制来实现冷却过程。
如果回流时间过短,焊点可能没有足够的时间进行冷却,导致焊点在受力或外界温度变化时易于出现裂纹或变形。
而过长的回流时间则可能导致焊点冷却不均匀,同样也会对焊点质量产生不良影响。
此外,回流时间还与焊接质量的一致性密切相关。
在大规模生产中,需要保证不同批次或不同型号的电路板焊接质量的一致性。
合理控制回流时间可以实现焊点质量的一致性,确保在不同批次或型号的焊接中焊点具有相似的质量水平。
最后,回流时间对于特殊组件的焊接也有重要影响。
例如,对于灵敏的电子元器件,如BGA芯片或QFN封装,焊接过程需要更加严格的控制。
过长的回流时间可能破坏组件的内部结构,导致焊接不良。
因此,对于特殊组件的焊接过程,需要根据其特性和要求,精确控制回流时间。
综上所述,回流时间对焊点质量有着重要影响。
与焊点可靠性、润湿效果、冷却过程、一致性和特殊组件的焊接等方面密切相关。
因此,在实际生产中,需要根据不同的焊接要求和组件特性,合理控制回流时间,以确保焊点质量的稳定性和可靠性。
SMT贴片机的性能考核指标

SMT贴片机的性能考核指标SMT贴片机(Surface Mount Technology Placement Machine),是一种用于电子元器件贴装的自动化设备。
其性能考核指标主要包括速度、精度、可靠性、柔性等。
以下将逐一分析这些指标。
速度是衡量SMT贴片机性能的一个重要指标。
它通常指的是SMT贴片机每小时能够完成元器件的贴装数量。
速度的高低与设备的生产效率直接相关。
靠前的SMT贴片机速度通常能达到10万个焊点/小时以上。
高速的设备能够提高生产效率和产能,降低生产成本,适应高强度的生产要求。
精度是衡量SMT贴片机性能的另一个关键指标。
它是指贴装元器件的精确定位能力。
具体来说,精度可分为以下几个方面的考量,包括:坐标定位精度、贴装偏移精度、贴装角度精度和复杂元器件贴装精度。
高精度的设备能够确保元器件的准确位置,保证电路的正常工作。
目前,SMT贴片机的精度一般在几十微米到几百微米之间。
可靠性是指SMT贴片机长时间稳定运行的能力,包括抗干扰能力、抗震动能力、抗磨损能力等。
这些性能指标保证设备在恶劣的环境条件下仍然可以正常运行,减少设备故障对生产的影响,提高设备的稳定性。
柔性是指SMT贴片机适应不同尺寸和类型的元器件的能力。
随着电子产品的不断发展,元器件的类型和尺寸呈多样化趋势。
因此,SMT贴片机需要具备良好的柔性,能够灵活调整和适应不同尺寸、形状和材料的元器件贴装工艺。
除了以上指标,还有一些辅助指标也需要考虑。
例如,设备的故障率是指设备在一定时间内发生故障的概率,高可靠性的设备具有低故障率;设备的易用性包括操作界面友好性、编程简单性等等。
另外,还有一些可选的指标可根据企业的具体需求进行考虑,如软件系统的稳定性、后期维护等。
总而言之,SMT贴片机的性能考核指标主要包括速度、精度、可靠性和柔性等。
正确评估和选择合适的机器是企业提高生产效率、降低成本、提升竞争力的重要一环。
SMT工艺材料介绍

SMT工艺材料介绍SMT工艺材料表面组装材料则是指SMT装联中所用的化工材料,即SMT工艺材料.它主要包括以下几方面内容:锡膏.焊剂和贴片胶等.一.锡膏锡膏是由合金焊料粉和糊状助焊剂均匀搅拌而成的膏状体.它是SMT工艺中不可缺少的焊接材料,广泛用于回流焊中.锡膏在常温下具有一定的粘性,可将电子元件初粘在既定的位置,在焊接温度下,随着溶剂和部分添加剂挥发,将被焊元件与PCB互联在一起形成永久连接.目前涂布锡膏多数采用丝钢网漏印法,其优点是操作简便.快速印刷后即刻可用.但其缺陷是:1.难保证焊点的可靠性,易造成虚焊.2.浪费锡膏,成本较高.现在有用计算机控制的自动锡膏点涂机可以克服上述缺陷.1.锡膏的化学组成锡膏主要由合金焊料粉末和助焊剂组成.其中合金焊料粉末占总重量的85%---9 0%,助焊剂占10%---15%.1)合金焊料粉末是锡膏的主要成分.常用的合金粉末如下:Sn63%---Pb37% 熔解温度为:183Sn62%---Pb36%---Ag2% 熔解温度为:179Sn43%---Pb43%---Bi14% 熔解温度为:114-163合金焊料粉末的形状.粒度和表面氧化程度对焊膏性能的影响很大.锡粉形状分成无定形和球形两种,球形合金粉末的表面积小,氧化程度低,制成的锡膏具有良好的印刷性能.锡粉的粒度一般在200—400目.粒度愈小,粘度愈大;粒度过大,会使锡膏粘接性能变差;粒度太细,表面积增大,会使其表面含氧量增高.,也不宜采用.下表是SMT引脚间距与锡粉颗粒的关系引脚间距/mm 0.8以上 0.65 0.5 0.4颗粒直径/um 75以下 60以下 50以下 40以下2).助焊剂助焊剂是锡粉的载体,其组成与通用助焊剂基本相同.为了改善印刷效果有时还需加入适量的溶剂.通过助焊剂中活性剂的作用,能清除被焊材料表面以及锡粉本身的氧化物,使焊料迅速扩散并附着在被焊金属表面.助焊剂的组成对锡膏的扩展性.润湿性.塌陷.粘度变化.清洗性.和储存寿命起决定性作用.2.锡膏的分类1).按锡粉合金熔点分普通锡膏(熔点178—183度)高温锡膏(熔点250度以上)低温锡膏(熔点150度以下)下表是不同熔点锡膏的再流焊温度合金类型熔化温度 /度再流焊温度/度Sn63/Pb37 183 208-223Sn60/Pb40 183-190 210-220Sn50/Pb50 183-216 236-246Sn45/Pb55 183-227 247-257Sn40/Pb60 183-238 258-268Sn30/Pb70 183-255 275-285Sn25/Pb75 183-266 286-296Sn15/Pb85 227-288 308-318Sn10/Pb90 268-302 322-332Sn5/Pb95 305-312 332-342Sn3/Pb97 312-318 338-348Sn62/Pb36/Ag2 179 204-219Sn96.5/Pb3.5 221 241-251Sn95/Ag5 221-245 265-275Sn1/Pb97.5/Ag1.5 309 329-339Sn100 232 252-262Sn95/Pb5 232-240 260-270Sn42/Bi58 139 164-179Sn43/Pb43/Bi14 114-163 188-203Au80/Sn20 280 300-310In60/Pb40 174-185 205-215In50/Pb50 180-209 229-239In19/Pb81 270-280 300-310Sn37.5/Pb37.5/In25 138 163-178Sn5/Pb92.5/Ag2.5 300 320-3302).按助焊剂的活性分无活性( R ) 中等活性(RMA) 活性(RA)3).按清洗方式分有机溶剂清洗型水清洗型免清洗型3.使用注意事项1).储存温度: 建议在冰箱内储存温度为5℃-10℃,请勿低于0℃。
SMT 产品可靠性检验流程
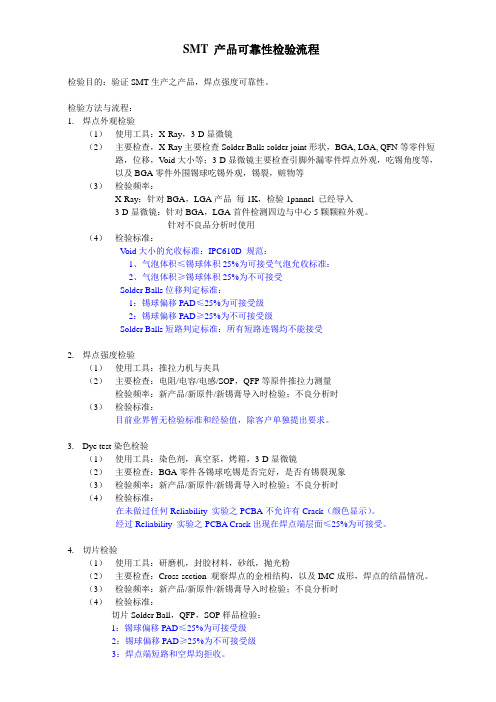
SMT 产品可靠性检验流程检验目的:验证SMT生产之产品,焊点强度可靠性。
检验方法与流程:1.焊点外观检验(1)使用工具:X-Ray,3-D显微镜(2)主要检查,X-Ray主要检查Solder Balls solder joint形状,BGA, LGA, QFN等零件短路,位移,V oid大小等;3-D显微镜主要检查引脚外漏零件焊点外观,吃锡角度等,以及BGA零件外围锡球吃锡外观,锡裂,赃物等(3)检验频率:X-Ray:针对BGA,LGA产品每1K,检验1pannel 已经导入3-D显微镜:针对BGA,LGA首件检测四边与中心5颗颗粒外观。
针对不良品分析时使用(4)检验标准:Void大小的允收标准:IPC610D 规范:1、气泡体积≤锡球体积25%为可接受气泡允收标准:2、气泡体积≥锡球体积25%为不可接受Solder Balls位移判定标准:1:锡球偏移PAD≤25%为可接受级2:锡球偏移PAD≥25%为不可接受级Solder Balls短路判定标准:所有短路连锡均不能接受2.焊点强度检验(1)使用工具:推拉力机与夹具(2)主要检查:电阻/电容/电感/SOP,QFP等原件推拉力测量检验频率:新产品/新原件/新锡膏导入时检验;不良分析时(3)检验标准:目前业界暂无检验标准和经验值,除客户单独提出要求。
3.Dye test染色检验(1)使用工具:染色剂,真空泵,烤箱,3-D显微镜(2)主要检查:BGA零件各锡球吃锡是否完好,是否有锡裂现象(3)检验频率:新产品/新原件/新锡膏导入时检验;不良分析时(4)检验标准:在未做过任何Reliability 实验之PCBA不允许有Crack(颜色显示)。
经过Reliability 实验之PCBA Crack出现在焊点端层面≤25%为可接受。
4.切片检验(1)使用工具:研磨机,封胶材料,砂纸,抛光粉(2)主要检查:Cross-section 观察焊点的金相结构,以及IMC成形,焊点的结晶情况。
跌落碰撞下SMT焊点可靠性研究进展
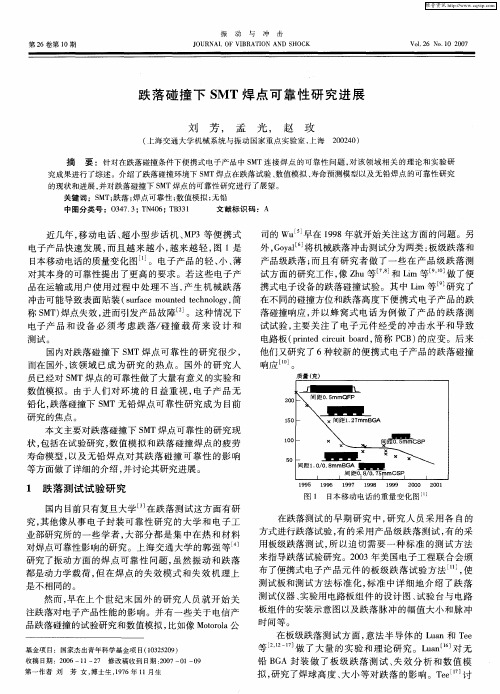
司 的 wu 早 在 19 9 8年 就开 始关 注 这方 面的 问题 。另
外 ,oa 6 G yl _将机械跌落 冲击测试分为两类 : 板级跌落和 产品级跌落 ; 而且有研究者做 了一些在产品级跌落测 试方面的研究工作 , Z u等 和 L 等 m 做了便 像 h i a r ’ 携式电子设备的跌落碰撞试验 。其 中 L i m等 研究 了 在不 同 的碰撞 方位 和跌 落 高度 下 便 携 式 电子 产 品 的跌 落碰撞 响应 , 以 蜂 窝 式 电话 为 例 做 了产 品 的跌 落 测 并 试试验, 主要关注了 电子元 件经受 的冲击水平和导致 电路板 (r t i ut or, 称 P B) 应 变 。后 来 pie cr ibad 简 nd c C 的 他 们又 研究 了 6种较 新 的便 携 式 电 子产 品 的跌 落 碰 撞
摘 要 :针对在跌落碰撞条件下便携式电子产品中 S T连接焊点的可靠性问题, M 对该领域相关的理论和实验研
究成果进行 了综述 。介绍 了跌落碰撞环境下 S MT焊点在跌落试验 、 数值模拟 、 寿命预测模型 以及无 铅焊点 的可靠性研究 的现状和进展 , 并对跌 落碰撞 下 S MT焊点 的可靠性 研究 进行 了展望 。
铅 B A封装 做 了板 级跌落测试 、 效分析 和数值模 G 失 拟, 研究了焊球 高度 、 大小等对跌落 的影 响。T e 讨 el 1
铅化, 跌落碰撞下 S T无铅焊点可靠性研究成为 目前 M 研 究 的焦 点 。 本文 主要对 跌 落碰撞 下 S MT焊点 可靠性 的研究 现
状, 包括在 试 验研究 , 值模 拟 和 跌 落碰 撞 焊 点 的疲 劳 数 寿命模 型 , 以及 无 铅 焊 点 对 其跌 落碰 撞 可 靠 性 的影 响
SMT工艺知识

SMT工艺知识什么是SMT工艺SMT(表面贴装技术)是一种电子元件组装技术,它通过将电子元件直接贴装在PCB(Printed Circuit Board)上,而不是通过穿孔插装的传统方法。
SMT工艺具有高效、灵活、高质量的特点,被广泛应用于电子产品的制造中。
SMT工艺的优势SMT工艺相比传统的插装工艺具有以下优势:1. 尺寸小:由于电子元件直接贴装在PCB上,可以减小电路板的尺寸,使产品更小巧轻便。
2. 重量轻:SMT工艺不需要通过插装来连接电子元件,因此可以减少用于插装的金属材料,从而减轻产品的重量。
3. 可靠性高:SMT工艺采用焊接技术,焊点可靠性高,能够在振动和温度变化等环境条件下保持稳定连接。
4. 生产效率高:SMT工艺能够实现自动化生产,提高了生产效率,降低了生产成本。
5. 电气性能稳定:SMT工艺使得电子元件与PCB之间的电气连接更加稳定,减少了传输信号的干扰,提高了产品的电气性能。
SMT工艺的步骤SMT工艺一般包括以下步骤:1. PCB制板:根据产品设计要求,制作PCB板。
2. 贴片:将电子元件粘贴在PCB板上,粘贴方式可以采用手工或机器贴片。
3. 焊接:通过回流焊接或波峰焊接等方式进行焊接,将电子元件与PCB板连接在一起。
4. 检测:对焊接后的电子元件进行检测,包括外观检查、功能测试等。
5. 焊盘处理:对焊接后的PCB板进行清洗和喷涂等处理,以提高焊接质量和外观。
6. 完成产品:经过上述步骤,最终完成SMT工艺的产品。
SMT工艺的应用SMT工艺广泛应用于电子产品的制造中,包括但不限于以下领域:1. 手机和平板电脑制造2. 汽车电子设备制造3. 智能家居设备制造4. 工业控制设备制造5. 医疗器械制造SMT工艺的应用范围正在不断扩大,随着技术的发展,我们可以期待更多领域将采用SMT工艺来提高产品的质量和性能。
总结SMT工艺是一种高效、灵活、高质量的电子元件组装技术。
它具有尺寸小、重量轻、可靠性高、生产效率高和电气性能稳定等优势。
smt心得体会

smt心得体会SMT(Surface Mount Technology)是一种现代的电子制造技术,它在电子产品的制造中起着至关重要的作用。
通过SMT,电子元件可以直接焊接到电路板的表面,而不需要传统的插针插座连接。
我在学习和实践SMT技术的过程中,深刻体会到了其重要性和优势。
首先,SMT技术具有高效性。
与传统的插针连接相比,SMT可以实现自动化的生产过程,大大提高了生产效率。
在SMT生产线上,通过使用具备高速度和高精度的设备,电子元件可以自动精确地放置在电路板上,从而减少了人工操作的过程。
这不仅使电子产品的制造更快速,还减少了制造过程中的人为错误。
通过SMT技术,公司可以更加高效地生产和交付电子产品,满足市场需求。
其次,SMT技术具有良好的可靠性。
由于电子元件直接焊接在电路板上,SMT可以有效地减少连接中的电阻、电感和串扰。
这意味着电路的稳定性得到了显著提高,减少了不稳定的因素对电子产品性能的影响。
此外,由于焊接面积更大,连接更坚固,SMT也能够在抗振动和抗冲击方面表现出更好的性能。
在工业和军事应用中,这是至关重要的优势。
此外,SMT技术还具有节省空间和成本的能力。
由于电子元件可以直接粘贴在电路板上,不需要额外的插针和插座,因此可以大大减少产品的体积。
这对于移动设备和微型电子产品尤其重要。
SMT还能够减少材料和能源的浪费,因为它使用更少的材料和更少的焊接步骤。
此外,SMT还使生产过程更加环保,因为它减少了有毒金属的使用和释放。
在学习和实践SMT技术的过程中,我也遇到了一些挑战。
首先是学习曲线的陡峭。
SMT技术是一门复杂的技术,涉及到电子元件的精确放置、焊接、设备操作等多个方面。
刚开始学习的时候,我感觉有点困惑和无从下手。
然而,通过不断的学习和实践,我逐渐掌握了各种技术和操作技巧。
其次是设备和材料的投入成本。
SMT技术所需要的设备和材料相对较贵,这对于一些小型企业来说可能具有一定的压力。
然而,随着市场需求的增长和技术的成熟,SMT设备的成本逐渐下降,使更多的企业和个人能够使用和受益于SMT技术。
Smt面试常用知识
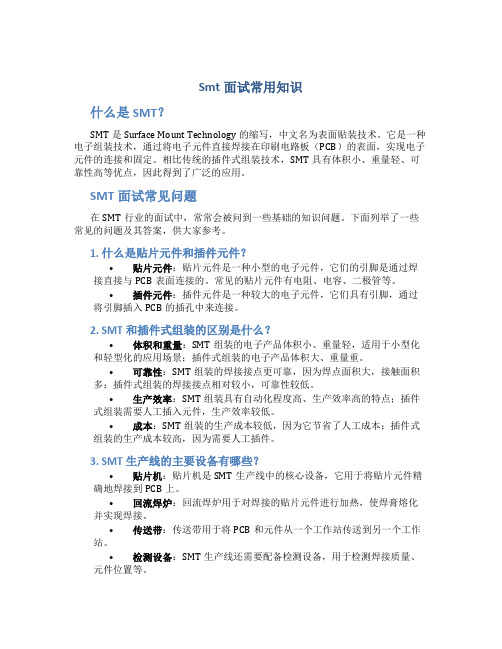
Smt面试常用知识什么是SMT?SMT是Surface Mount Technology的缩写,中文名为表面贴装技术。
它是一种电子组装技术,通过将电子元件直接焊接在印刷电路板(PCB)的表面,实现电子元件的连接和固定。
相比传统的插件式组装技术,SMT具有体积小、重量轻、可靠性高等优点,因此得到了广泛的应用。
SMT面试常见问题在SMT行业的面试中,常常会被问到一些基础的知识问题。
下面列举了一些常见的问题及其答案,供大家参考。
1. 什么是贴片元件和插件元件?•贴片元件:贴片元件是一种小型的电子元件,它们的引脚是通过焊接直接与PCB表面连接的。
常见的贴片元件有电阻、电容、二极管等。
•插件元件:插件元件是一种较大的电子元件,它们具有引脚,通过将引脚插入PCB的插孔中来连接。
2. SMT和插件式组装的区别是什么?•体积和重量:SMT组装的电子产品体积小、重量轻,适用于小型化和轻型化的应用场景;插件式组装的电子产品体积大、重量重。
•可靠性:SMT组装的焊接接点更可靠,因为焊点面积大,接触面积多;插件式组装的焊接接点相对较小,可靠性较低。
•生产效率:SMT组装具有自动化程度高、生产效率高的特点;插件式组装需要人工插入元件,生产效率较低。
•成本:SMT组装的生产成本较低,因为它节省了人工成本;插件式组装的生产成本较高,因为需要人工插件。
3. SMT生产线的主要设备有哪些?•贴片机:贴片机是SMT生产线中的核心设备,它用于将贴片元件精确地焊接到PCB上。
•回流焊炉:回流焊炉用于对焊接的贴片元件进行加热,使焊膏熔化并实现焊接。
•传送带:传送带用于将PCB和元件从一个工作站传送到另一个工作站。
•检测设备:SMT生产线还需要配备检测设备,用于检测焊接质量、元件位置等。
4. SMT生产线的工艺流程是什么?SMT生产线的工艺流程通常包括以下几个步骤:1.钢网制作:通过光刻和蚀刻工艺制作钢网,用于印刷焊膏。
2.印刷焊膏:将焊膏印刷到PCB上,为后续的元件焊接提供接触点。
几种SMT焊接缺陷及其解决措施

几种SMT焊接缺陷及其解决措施SMT焊接是一种常见的电子元器件连接方式,其缺陷会直接影响产品的质量和可靠性。
下面将介绍几种常见的SMT焊接缺陷及其解决措施。
1.冷焊:冷焊是指焊料没有完全熔化并附着在焊盘或引脚上的现象。
冷焊会导致焊点间接触不良,从而影响电气连接和传导。
解决冷焊的措施包括:-提高焊接温度和时间,确保焊料完全熔化。
-检查焊料的品质,确保焊料能够适应焊接过程要求。
-使用合适的焊接参数,如合适的预热时间、焊锡温度等。
2.焊接积焦:焊接积焦是指焊料在焊接过程中产生的氧化物、残留的颗粒等积累在焊接区域的现象。
焊接积焦会导致焊点质量降低,从而影响电气性能和可靠性。
解决焊接积焦的措施包括:-控制焊接温度和焊接时间,避免焊接区域过热。
-清洁焊接区域,保持焊接表面的清洁。
-使用高品质的焊料,避免余烟和氧化物的产生。
3.引脚未焊稳:引脚未焊稳是指焊料没有完全附着在引脚和焊盘上的现象。
引脚未焊稳会导致焊点松动,从而影响电气连接和机械可靠性。
解决引脚未焊稳的措施包括:-使用合适的焊锡形状和焊锡通孔尺寸,确保焊料能够充分填充焊盘和引脚之间的空隙。
-提高焊接温度和焊接时间,确保焊料完全熔化并形成可靠的焊接连接。
-检查焊接设备和工艺参数,保证焊接过程的稳定性和一致性。
4.锡球:锡球是指焊盘上未熔化的焊料形成的球状物。
锡球会导致焊接点短路和漏电等问题。
解决锡球问题的措施包括:-控制焊接温度和时间,避免焊料过热和氧化。
-使用合适的焊锡形状和焊锡通孔尺寸,确保焊料能够充分填充焊盘。
-使用合适的焊锡通孔形状,确保焊料能够完全熔化并形成可靠的焊接连接。
在实际生产中,为了避免SMT焊接缺陷,可以采取以下综合措施:-严格控制焊接设备和工艺参数,确保焊接过程的稳定性和一致性。
-优化焊接工艺,如预热、焊接时间和温度等参数的选择。
-选择合适的焊接材料,如焊料、焊锡通孔形状等。
-加强焊接操作人员培训,提高其技能和专业素质。
-密切关注焊接过程中的质量控制,及时发现和解决问题。
SMT

基本知识
什么是SMT?
• 什么是SMT: SMT就是表面组装技术 (Surface Mounted Technology的缩写),是 目前电子组装行业里最流行的一种技术和工艺。 • SMT有何特点: 1、组装密度高、电子产品体积小、重量轻, 贴片元件的体积和重量只有传统插装元件的 1/10左右,一般采用SMT之后,电子产品体积 缩小40%~60%,重量减轻60%~80%。 2、可靠性高、抗振能力强。焊点缺陷率低。 3、高频特性好。减少了电磁和射频干扰。 4、易于实现自动化,提高生产效率。降低 成本达30%~50%。 节省材料、能源、设备、 人力、时间等。
G
Golden boy(金样):一个元件或电路装配,已经测试并知道功能达到技术规格,用来通 过比较测试其它单元。 H Halides(卤化物):含有氟、氯、溴、碘或砹的化合物。是助焊剂中催化剂部分,由于 其腐蚀性,必须清除。 Hard water(硬水):水中含有碳酸钙和其它离子,可能聚集在干净设备的内表面并引起 阻塞。 Hardener(硬化剂):加入树脂中的化学品,使得提前固化,即固化剂。 I
1、电子产品追求小型化,以前使用的穿孔插 件元件已无法缩小 2、电子产品功能更完整,所采用的集成电 路(IC)已无穿孔元件,特别是大规模、高集成 IC,不得不采用表面贴片元件 3、产品批量化,生产自动化,厂方要以低 成本高产量,出产优质产品以迎合顾客需求及 加强市场竞争力 4、电子元件的发展,集成电路(IC)的开发, 半导体材料的多元应用 5、电子科技革命势在必行,追逐国际潮流
SMT特点
• 1、组装密度高、电子产品体积小、重量轻, 贴片元件的体积和重量只有传统插装元件的 1/10左右,一般采用SMT之后,电子产品体积 缩小40%~60%,重量减轻60%~80%。 • 2、可靠性高、抗振能力强。焊点缺陷率低。 • 3、高频特性好。减少了电磁和射频干扰。 • 4、易于实现自动化,提高生产效率。降低成 本达30%~50%。 节省材料、能源、设备、人 力、时间等。
smt焊接检验标准
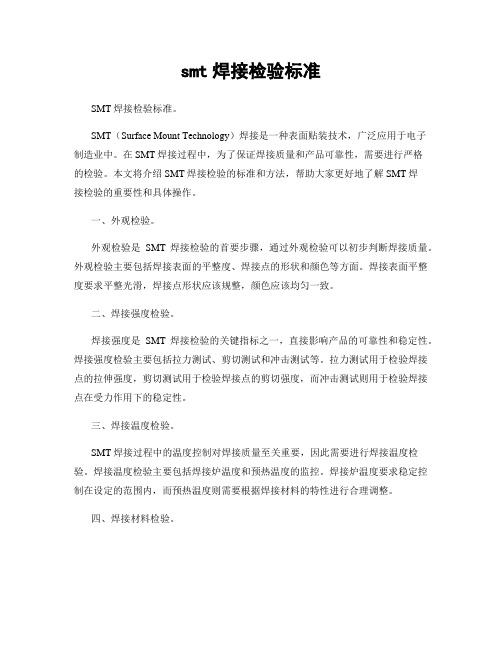
smt焊接检验标准SMT焊接检验标准。
SMT(Surface Mount Technology)焊接是一种表面贴装技术,广泛应用于电子制造业中。
在SMT焊接过程中,为了保证焊接质量和产品可靠性,需要进行严格的检验。
本文将介绍SMT焊接检验的标准和方法,帮助大家更好地了解SMT焊接检验的重要性和具体操作。
一、外观检验。
外观检验是SMT焊接检验的首要步骤,通过外观检验可以初步判断焊接质量。
外观检验主要包括焊接表面的平整度、焊接点的形状和颜色等方面。
焊接表面平整度要求平整光滑,焊接点形状应该规整,颜色应该均匀一致。
二、焊接强度检验。
焊接强度是SMT焊接检验的关键指标之一,直接影响产品的可靠性和稳定性。
焊接强度检验主要包括拉力测试、剪切测试和冲击测试等。
拉力测试用于检验焊接点的拉伸强度,剪切测试用于检验焊接点的剪切强度,而冲击测试则用于检验焊接点在受力作用下的稳定性。
三、焊接温度检验。
SMT焊接过程中的温度控制对焊接质量至关重要,因此需要进行焊接温度检验。
焊接温度检验主要包括焊接炉温度和预热温度的监控。
焊接炉温度要求稳定控制在设定的范围内,而预热温度则需要根据焊接材料的特性进行合理调整。
四、焊接材料检验。
焊接材料的质量直接影响焊接质量,因此需要进行焊接材料的检验。
焊接材料检验主要包括焊锡丝的成分分析、焊膏的粘度测试和焊盘的表面处理等。
通过对焊接材料的检验,可以确保焊接材料的质量符合要求,从而保证焊接质量。
五、焊接环境检验。
焊接环境对焊接质量也有重要影响,因此需要进行焊接环境的检验。
焊接环境检验主要包括温湿度监控、静电防护和通风排烟等。
良好的焊接环境可以有效减少焊接缺陷的发生,提高焊接质量。
六、焊接设备检验。
焊接设备的性能直接关系到焊接质量,因此需要进行焊接设备的检验。
焊接设备检验主要包括焊接机的稳定性测试、焊接头的清洁度检验和焊接机的维护保养等。
通过对焊接设备的检验,可以确保焊接设备的性能稳定,从而保证焊接质量。
焊点可靠性分析
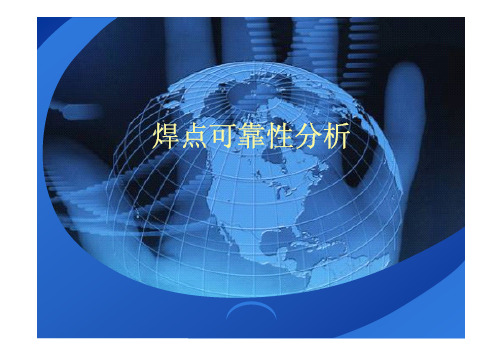
焊点可靠性分析目录焊点的基础知识1焊点的工艺流程2焊点的工艺评价3焊点的可靠性评价41.焊点的基础知识1.1焊点:无铅/锡铅焊料被加热到熔点以上,焊接金属表面在助焊剂的活化作焊点图片用下,对金属表面的氧化层和污染物起到清洗作用,同时使金属表面获得足够的激活能。
熔融的焊料在经过助焊剂净化的金属表面上进行浸润、发生扩散、冶金结合,在焊料和被焊接金属表面之间生成金属间结合层,冷却后使得焊料凝固,形成焊点。
在焊接界面形成良好滋润形成良好焊点的关键形成合适的金属化间化合物1.2形成良好焊点的关键1.3焊点的基本结构和基本作用�焊点的基本构成:器件引脚、焊料、PCB焊盘、界面的金属化层�焊点的基本作用:电气连接、机械连接2.焊点的工艺流程冷却后形成焊点表面清洗焊件加热焊料润湿扩散结合层焊接工艺表面清洁焊件加热焊料润湿扩散结合层冷却后形成焊点焊接过程分解助焊剂残留的影响高温和温度差异的影响焊点微观结构的差异2.1主要的焊接工艺软钎焊接:手工焊接软钎焊接:手工焊接 波峰焊接波峰焊接波峰焊接 SMT SMT SMT再流焊再流焊接其他焊接:激光焊接其他焊接:激光焊接 氩弧焊接氩弧焊接氩弧焊接 压焊等压焊等——主要针对钎焊接2.1.1手工焊接手工焊接工艺手工焊接工艺缺陷:焊料对引脚润湿不良;焊料对孔壁润湿、填充不足。
2.1.2波峰焊波峰焊:波峰焊是让插件板的焊接面直接与高温液态锡接触达到焊接目的,其高温液态锡保持一个斜面,并由特殊装置使液态锡形成一道道类似波浪的现象,所以叫"波峰焊"波峰焊曲线图2.1.3回流焊�回流焊:回流焊技术在电子制造领域并不陌生,我们电脑内使用的各回流焊接工艺种板卡上的元件都是通过这种工艺焊接到线路板上的,这种设备的内部有一个加热电路,将空气或氮气加热到足够高的温度后吹向已经贴好元件的线路板,让元件两侧的焊料融化后与主板粘结回流焊曲线图焊接缺陷案例2.2工艺不当主要失效模式工艺不当焊点冷焊静电损伤焊点偏位异常陶瓷电容破裂潮湿敏感损伤焊点过度焊接工艺缺陷原因汇总分析1包括元器件、助焊剂等材料控制不合理3后期检测的手段缺乏,不能及时发现问题2焊接工艺参数缺乏必要的控制和优化补充:技术人员对工艺控制的要求掌握不够3.焊点的工艺评价9.热分析技术(TGA/DSC/TMA)10.染色与渗透技术11.其他分析测试技术9.热分析技术(TGA/DSC/TMA)10.染色与渗透技术11.其他分析测试技术5.金相切片分析6.扫描电镜分析SEM 7.能谱分析EDAX 8.光电子能谱XPS 5.金相切片分析6.扫描电镜分析SEM 7.能谱分析EDAX 8.光电子能谱XPS 1.红外检查2.X 射线透视检查X-RAY 3.扫描超声显微镜检查 C-SAM 4.红外显微镜分析FT-IR 1.红外检查 2.X 射线透视检查X-RAY 3.扫描超声显微镜检查C-SAM 4.红外显微镜分析FT-IR3.1外观检查 Visual Inspection4.焊点可靠性分析焊点的主要可靠性问题�焊点缺陷(空洞、虚焊、冷焊等)�焊点疲劳失效(和长时间工作相关)�焊点开裂失效(通常和受热或机械应力相关焊点疲劳可靠性评价标准IPC-SM-785表面组装焊点可靠性加速试验实验指南IPC-9701 表面组装焊点性能测试方法和鉴定要求(给出了详细要求)JESD22-104-B 温度循环试验4.1温度循环/温度冲击�温度:0℃—100℃、-25℃—100℃、-40℃—125℃、-55℃—125℃、-55℃--100℃�高低温停留时间:有铅:10min\无铅:10min~30min 常用:15min�温度变化速率:<20℃/min 推荐10℃/min~15℃/min�循环数:200cyle\500cyle\1000cyle\1500cyle\2000cyle\�1%失效率计算�5年*365天=1825天*24=43800h*1%=438h*2=876cyle----1000cyle� 3年*365天=1095天*24=26280h*1%=262h*2=524cyle �温冲:500h 2pcs4.2高温高湿试验�85℃± 2℃,85± 2%RH,1000h(其他非标准时间:500H,168H客户指定时采用)\ JESD22A101�IPC-TM-650 2.6.14.1电迁移�40℃ ± 2℃, 93% ± 2% RH;�65℃ ± 2℃,88.5% ±3.5% RH; 85°C ± 2°C, 88.5% ± 3.5% RH�偏压:10VDC;时间:596H�85°C ± 2°C, 85% ±5% RH,1000-24/+168 小时JESD-22-A1014.3锡须观察�Min Temperature -55 to -40 (+0/-10) °C;Max Temperature +85 (+10/-0) °C,air to air; 5 to10 minute soak;3 cycles/hour 1000 cycles。
- 1、下载文档前请自行甄别文档内容的完整性,平台不提供额外的编辑、内容补充、找答案等附加服务。
- 2、"仅部分预览"的文档,不可在线预览部分如存在完整性等问题,可反馈申请退款(可完整预览的文档不适用该条件!)。
- 3、如文档侵犯您的权益,请联系客服反馈,我们会尽快为您处理(人工客服工作时间:9:00-18:30)。
对 于 一个 孤 立 的焊 点 ,没有 可 靠
通 ,用 手压住Q P F 本体 ,卡片工 作正 线 达 到 整 体 布 局 的 安 排 。 通 过 增 加 常 ,将此 不 良样板 QP 下 ,此位 置 QN F取 F 的接地散 热焊盘 面积并加 装散热
的焊盘 上加锡 ,再进 行焊接 ,测试结 器 ,使 用2 未出现焊 点开 裂现象 , 年
殊 的可 靠性 问题 。
电子产品的失效产生于不 良的设 计 、元件 问题及生产过程 中,电子产 品在 组装 中主要 以通孔 插 装 卜 ) r 和 r
ST焊 点可靠性的重要因素。 M 焊点的热疲劳失效与多种 因素有
11焊 点 失 效 .
基板与表 贴元器件之间焊点的失
关, 已有研究结果表 明焊接工 艺、材
免的冲击 、振动等造成 的焊点机械损 伤;再有就是元件服役过程 中通断 电 或环 境温 度 变化 时 ,焊 点形 成热 循 环 , 元 件 与 基 板 材 料 的C E 配 失 T匹
效 ,引起裂纹 、扩展直至最终断裂造
成焊点失效 。
Байду номын сангаас
钜 凯 系 列 产 品
各种规格和温度系列的无铅锡膏 无卤助焊剂 水基清洗剂 环保型清洗剂
( T 焊 点比较特殊 ,ST S ) M M 焊点不仅提 供 电气互连 ,而且也是 电子元器件与 印制 电路板 (C ) P B 的机械 连接 ,电子
理想的焊点要求在 电气和机械上 形成可靠连接 ,要达到这个 目的 ,必 须要保证在设计过程中进行 连可靠 性设计,焊点可靠性依赖 于包括 焊点
电路中 电气信号畅通 、机械连接 的保
障 ,它的可靠性直接关 系到整个 电子 产品的可靠 性,焊 点失效 可能导致整 个 电子产品失效。 焊点失效一方面产生于生产焊接 过程中的焊接 故障,如焊料不足 、空 洞、针孔 、冷焊 、助焊剂残 留等 ;另
一
方面为在 使用过程 中,由于不可避
裂导致 不 良,在验证过程 中发现卡片 偶显示温度达到9 ℃,焊点在此温度 4 在放入 治具后取 出,第二 次将卡片再 下晶粒组织 长大 、IC M 增厚 ;运行时 放置治具后测试 ,测试结 果卡片连线 的温度变化会使焊 点发生循环疲劳 , 失 败 ,取 第 2 样 品先 通 电拼 包 正 最终 此Q N R F 焊点开裂 失效 。经过大量 常、网页正常 ,放入测试 治具测试 , 的分析 ,确认为设计人 员在设计时将
电子 胶 水 网 :h p/ w rec  ̄ : w. . / w 4 n
■ 作 者: 张绍波 深圳 同维 电子有限公司
S T 点 可靠 性 焊 M
【 要】 摘
本文针对典型ST M焊点在无铅条件下焊点的可靠性 问题 ,焊点的可靠性 问题主要是焊点在热循环过程 中由于 芯
片载体 与基板材料之 间的热膨胀 失配 (E) CT 而导致焊点的疲劳失效 。
e 7
8
表面 贴装 ( T 的混 合为 主要装 联 形 S ) M
式 ,在组装件的三 要素 中,元件 、电 路板 ( B 、互连焊 点 的可靠性 关联 P ) C 着 电子产品的使用 寿命 ,焊 点是 电子
- ~一一 Ⅵ sC d 薹 r n ~
在对经 历严酷机械振动或冲击载荷 的 产 品进行失效定义 时,可 能需要考虑
12失效 与疲劳机理 _
电子组件的可靠性取决于组件 的
各 组成 部 分 的可 靠性 、组 件 上 个体 之 间 的机 械 、热 、电 气 的结 合 部 位 的可
测试 通 过 ,取 卡 后 再放 入卡 片 测 试 不 中间散热焊盘缩 小,节约空间用于布
靠性,表贴焊料连接尤为重要,它不
仅提供 电气连接 ,也是 电子元器件与 印制电路板唯一的机械连接,同时还 承担关键的散热功能。
【 关键词 】无 可靠 铅; 性;焊 点;失 效
~~一~一 砌
器件外型尺寸在 不断缩小 ,导致
焊 点设计 不仅仅 着眼 于PB C 与器件之
热 和 电气 界 面 的 可 靠 性 ,表 面 贴 装
电 菱 篝 曩 试 验 莞
1 、焊点 的 可靠 性 设计 和 寿 命 扩展的力学因素 。
间的连 接 ,更扩 展 到 了器件 内部 ,
IC 9 0 是关于表贴焊点连接 的测试 P一71 方法 和认证 要求 ,给 出了5 种测试条
/ L
~ ~ ~~ ℃℃ . 暑 一
1 —1 —1
元器件在工作过程中产生的热量也是
件 ,从 比较 温和 的T 1 C 条件 的O 10 - 0 ∞ ∞ 外观几何形态在 内的诸 多因素 ,如焊 通 过 焊点 传递 到 印 制 电路 板进 行 散 度测 试到 最严酷 的T4 C ,各测 试条件 点的 内部质量、材料 的匹配性 、焊接 热 ,所 以ST 点 还 起 到 传 热 的 作 M焊 的停 留时 问 (w l ie 为 1分钟 , D e l Tm ) 0 材料的力学性能、焊点的热机 械加载 用 ,因此表面贴装的焊 点需要考虑 特 见 下 表 1 : 条件等,其中焊 点的几 何形态 是影 响
201 佣 0./ 1 2  ̄ B第
I E
S T M 贴片胶 邦定胶 底部填充胶 抗氧化还原粉等电子化工产品。
Htp:www . e.et t / / smt n
电子胶 水 网 :h p/ w rec t :w w. . t/ 4 n
累计疲 劳损伤作用下焊 点的机械弱化
效应 。
料 和焊点几何形态均影 响焊 点寿命 , 其 本质上焊 点的失效都表现为裂纹 的 萌生、扩展 直至最终 断裂 ,而焊 点内 的应 力应变是诱发焊点 内裂纹萌生与
效定义为:器件焊 点中的第 一个焊 点
存在 完全断裂;表 贴焊 点的疲劳特性 在大量的研 究中都有实验性地探讨 ,
聊~ 一一 一