转炉除尘灰的高附加值利用)
转炉除尘灰资源化利用研究

转炉除尘灰资源化利用研究作者:周鹤斌梁康姚雄健林振来源:《科学导报·学术》2020年第27期摘要:转炉除尘灰是在转炉吹炼过程中产生的,全铁含量较高,氧化钙、氧化钾、氧化钠等含量根据除尘灰的类别差别较大。
目前转炉除尘灰的利用方法较多,但主要是针对其中的铁资源进行回收利用,包括生产烧结矿、冷压球团、制备铁系颜料等。
由于球团炼钢法具备能耗低、降低生产成本、减少石灰用量等优势,且对转炉生产无影响,已逐渐成为转炉除尘灰未来的利用趋势。
关键词:转炉除尘灰;铁资源;回收利用;球团1 前言转炉除尘灰是在转炉吹炼过程中产生的。
在吹练过程中产生含铁粉尘,经烟道后进入除尘系统收集所得[1]。
因炼钢温度较高,因此含铁粉尘温度较高,可达1400℃,对除尘系统要求较高。
目前主流的除尘方法有两种,一种为湿法除尘,也就是OG法除尘;另一种为干法除尘,也就是LT法除尘[2]。
实际中还存在有以上两种除尘方法的基础上进行改进的方法,但总体可分为干法和湿法。
由于湿法存在能耗高,且除尘系统复杂,配套要求较高,目前该方法已逐步被淘汰。
而干法除尘无需废水处理设备,且能耗低,系统运行稳定,因而受到广大钢厂欢迎。
转炉除尘灰产量非常大,据相关资料统计,冶炼1吨钢所产生的除尘灰达15~20kg[3],2018年全国粗钢产量为8亿吨,按吨钢产生15kg除尘灰统计,产生的除尘灰达1200万吨。
随着钢铁产能的不断扩大,转炉除尘灰的产量将逐年上升。
转炉除尘灰铁和钙含量丰富,将其弃置,不仅造成土地污染,同时还会造成资源的浪费。
柳州钢铁集团目前钢产能达1300万吨,每年将有近20万吨的除尘灰产生。
随着环保的要求越来越严格,除尘灰的资源化利用势在必行。
2 转炉除尘灰利用状况2.1 转炉除尘灰成分以柳钢为例,柳钢转炉除尘灰的的主要成分及含量见表1、图1、图2、图3所示。
一次除尘细灰全铁含量高达55.56%,氧化钙含量较低,一次除尘粗灰全铁含量为39.57%,氧化钙含量较高,二次除尘灰中K2O、Na2O含量较高。
炼钢除尘泥(灰)资源化利用分析

炼钢除尘泥(灰)资源化利用分析吾塔;臧疆文;丁国东;王新成;宋维兆【摘要】低碳循环经济是当今国际社会推进的可持续发展的一种新型实践模式,它强调最有效利用资源和保护环境.钢铁企业炼钢过程产生大量除尘产物,这些除尘产物是很好的二次资源.仅2009年,八钢公司转炉炼钢过程产生除尘干污泥约5.8万t,平均含铁量在50%以上;电炉炼钢过程产生的除尘灰1.4万t以上,平均含铁量在42%以上,科学合理地利用这些资源,既可创造经济效益又能减轻环境负担.目前转炉除尘污泥的利用途径是加人烧结混合料,烧结后进入炼铁高炉进行循环.这种做法虽然解决了污泥给环境造成的污染,但极不科学.实践证明,各种含铁尘泥不经预处理,直接加入烧结混合料中进行烧结并非经济科学的利用途径,其主要危害是转炉尘泥中含有害杂质,如ZnO、PbO、Na2O、K2O等,随烧结矿加入高炉,将影响高炉顺行和寿命.其次化学成分、粒度、水分均存在较大差异,污泥的含铁量低(与精矿粉相比),配人烧结后降低了烧结矿的质量和品位,增加高炉能耗,使炼铁产率降低.经分析将这些转炉炼钢除尘污泥和电炉炼钢除尘灰加工成炼钢造渣剂,加入转炉循环使用,有利于降低炼钢成本和环境保护,是科学利用这些资源的最佳途径,将为企业带来巨大的经济效益和社会效益.【期刊名称】《新疆钢铁》【年(卷),期】2010(000)004【总页数】3页(P14-16)【关键词】转炉除尘泥;电炉除尘灰;科学利用【作者】吾塔;臧疆文;丁国东;王新成;宋维兆【作者单位】宝钢集团八钢公司制造管理部;宝钢集团八钢公司制造管理部;宝钢集团八钢公司制造管理部;宝钢集团八钢公司制造管理部;宝钢集团八钢公司制造管理部【正文语种】中文【中图分类】X756低碳循环经济是当今国际社会推进的可持续发展的一种新型实践模式,它强调最有效利用资源和保护环境,表现为“资源——产品——再生资源”的经济增长方式,做到生产和消费“污染排放最小化”,以最小成本获得最大的经济效益和环境效益。
转炉除尘灰的循环利用技术和应用

转炉除尘灰的循环利用技术和应用
张沅;徐铁;陈高亮
【期刊名称】《包钢科技》
【年(卷),期】2017(043)006
【摘要】转炉炼钢过程中会产生大量有害烟尘,经现代化的环保除尘设备处理回收后,可以得到粒度细小且含铁料高的除尘灰.通过采取一定的技术措施,成功开发出符合转炉使用的除尘灰压块.经炼钢转炉现场使用证明除尘灰压块具有良好的冷却和化渣效果,可以替代铁皮球、渣钢和铁矿石,实现了转炉除尘灰的"全闭路"综合利用.【总页数】3页(P17-19)
【作者】张沅;徐铁;陈高亮
【作者单位】内蒙古科技大学材料与冶金工程学院,内蒙古包头 014010;内蒙古包钢钢联股份有限公司稀土钢板材厂,内蒙古包头 014010;内蒙古包钢钢联股份有限公司稀土钢板材厂,内蒙古包头 014010;内蒙古包钢钢联股份有限公司稀土钢板材厂,内蒙古包头 014010
【正文语种】中文
【中图分类】TF805.3
【相关文献】
1.天津荣钢转炉干法除尘灰压球应用实践 [J], 利强;金鑫;房兴华
2.转炉喷溅渣循环利用技术的开发与应用 [J], 颜景春;邢东方;赵景泉;孙惠玲
3.太钢转炉除尘灰冷固球团技术及应用 [J], 王鹏
4.酒钢集团榆钢公司干法除尘灰冷压球转炉应用实践 [J], 亢神周;高勇
5.酒钢集团榆钢公司干法除尘灰冷压球转炉应用实践 [J], 亢神周;高勇
因版权原因,仅展示原文概要,查看原文内容请购买。
高炉除尘灰中锌的高附加值资源化利用研究

高炉除尘灰中锌的高附加值资源化利用研究高炉除尘灰中锌的高附加值资源化利用研究摘要:高炉除尘灰是高炉炼铁过程中产生的一种固体废弃物,其中含有大量的锌元素。
本文对高炉除尘灰中锌的高附加值资源化利用进行了研究。
通过实验室分析和试验,分析了高炉除尘灰中锌的性质和存在形式,并提出了利用高炉除尘灰中锌进行资源化利用的途径和方法。
研究表明,高炉除尘灰中锌可以作为重要的锌资源进行回收利用,通过合适的提取方法,可以得到高纯度的锌产品。
这对于节约锌资源、降低环境污染具有重要的意义。
1. 引言高炉除尘灰是高炉炼铁过程中产生的一种固体废弃物,其中含有大量的锌元素。
传统上,高炉除尘灰被视为废弃物,直接填埋或处理。
然而,高炉除尘灰中的锌元素是一种重要的有色金属资源,具有很高的经济价值。
因此,对高炉除尘灰中锌的高附加值资源化利用具有重要的意义。
2. 高炉除尘灰中锌的性质和存在形式高炉除尘灰中的锌主要以氧化锌的形式存在,同时还存在一定量的金属锌。
经过酸溶解或碱溶解后,锌元素可以溶解出来,并通过适当的分离和提取方法得到锌产品。
3. 高炉除尘灰中锌资源化利用的途径和方法高炉除尘灰中锌的资源化利用可以通过以下几种途径和方法实现:3.1. 酸溶解法采用浓硫酸或盐酸等酸性介质对除尘灰进行溶解,将锌溶解出来。
然后通过过滤、沉淀、干燥等工艺步骤得到高纯度的锌产品。
3.2. 碱溶解法采用氢氧化钠或碳酸钠等碱性介质对除尘灰进行溶解,将锌溶解出来。
然后通过离心、过滤、干燥等工艺步骤得到高纯度的锌产品。
3.3. 电解法通过电解的方式,将高炉除尘灰中的锌元素析出。
这种方法可以得到高纯度的锌产品,同时还可以回收电解液中的其他有用金属。
3.4. 浸出法采用氯化法、硫酸法等浸出方法,将锌从除尘灰中浸出。
然后通过沉淀、过滤等工艺步骤得到锌产品。
4. 结果和讨论通过实验室分析和试验,我们发现高炉除尘灰中锌可以作为重要的锌资源进行回收利用。
通过适当的提取方法,可以得到高纯度的锌产品。
除尘灰利用价值
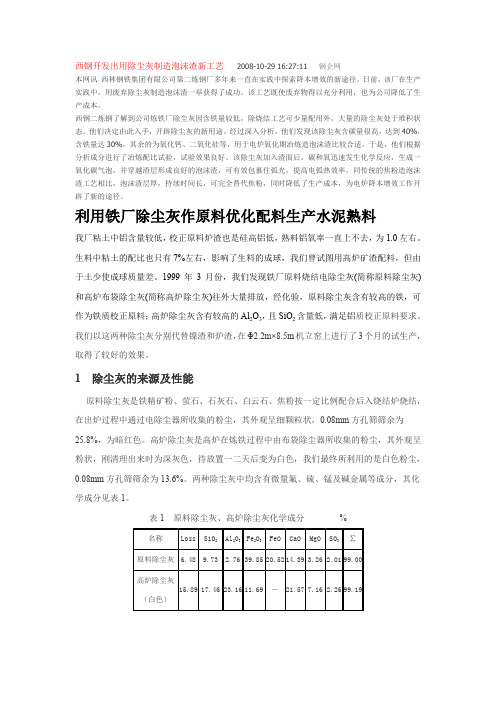
西钢开发出用除尘灰制造泡沫渣新工艺2008-10-29 16:27:11 钢企网本网讯西林钢铁集团有限公司第二炼钢厂多年来一直在实践中探索降本增效的新途径。
日前,该厂在生产实践中,用废弃除尘灰制造泡沫渣一举获得了成功。
该工艺既使废弃物得以充分利用,也为公司降低了生产成本。
西钢二炼钢了解到公司炼铁厂除尘灰因含铁量较低,除烧结工艺可少量配用外,大量的除尘灰处于堆积状态。
他们决定由此入手,开辟除尘灰的新用途。
经过深入分析,他们发现该除尘灰含碳量很高,达到40%,含铁量达30%,其余的为氧化钙、二氧化硅等,用于电炉氧化期冶炼造泡沫渣比较合适。
于是,他们根据分析成分进行了冶炼配比试验,试验效果良好。
该除尘灰加入渣面后,碳和氧迅速发生化学反应,生成一氧化碳气泡,并穿越渣层形成良好的泡沫渣,可有效包裹住弧光,提高电弧热效率,同传统的焦粉造泡沫渣工艺相比,泡沫渣层厚,持续时间长,可完全替代焦粉,同时降低了生产成本,为电炉降本增效工作开辟了新的途径。
利用铁厂除尘灰作原料优化配料生产水泥熟料我厂粘土中铝含量较低,校正原料炉渣也是硅高铝低,熟料铝氧率一直上不去,为1.0左右。
生料中粘土的配比也只有7%左右,影响了生料的成球,我们曾试图用高炉矿渣配料,但由于土少使成球质量差。
1999年3月份,我们发现铁厂原料烧结电除尘灰(简称原料除尘灰)和高炉布袋除尘灰(简称高炉除尘灰)往外大量排放,经化验,原料除尘灰含有较高的铁,可作为铁质校正原料;高炉除尘灰含有较高的Al2O3,且SiO2含量低,满足铝质校正原料要求。
我们以这两种除尘灰分别代替镍渣和炉渣,在Φ2.2m×8.5m机立窑上进行了3个月的试生产,取得了较好的效果。
1除尘灰的来源及性能原料除尘灰是铁精矿粉、萤石、石灰石、白云石、焦粉按一定比例配合后入烧结炉烧结,在出炉过程中通过电除尘器所收集的粉尘,其外观呈细颗粒状,0.08mm方孔筛筛余为25.8%,为暗红色。
炼钢除尘灰的资源化利用

1.文献综述1.1 除尘灰概况1.1.1 除尘灰来源在钢铁厂生产过程中,生产出来的副产品和粉尘主要是除尘灰,而这些除尘灰会在多个方面产生,比如电炉灰和高炉灰,不仅如此,在烧结冶炼过程中,也会产生大量的除尘灰,这些有害物对环境造成了严重的影响。
除尘灰的来源是多方面的,生活过程中会产生一部分的有害物,这些有害物中含有烟尘[1]等,除了生活中还有交通运输过程中,一些交通工具的尾气排放等产生的有害物也是除尘灰的来源,除尘灰的来源最多的是工艺生产中,这就是除尘灰的主要来源。
现在除尘灰每年排放130万吨,造成了严重的环境污染,而电炉炼钢是造成烟尘污染最主要的来源。
在进行的电炉炼钢阶段,通常经过几道工序来完成生产电炉灰,最终在袋式除尘器来捕集电炉烟尘,这样完成了对电炉灰的生产,占产出炉料装入量2%~3%。
电炉在冶炼过程中产生大量烟尘,每吨钢发生量大约为12~20 kg/t,烟尘中含FeO的在40 %以上。
在钢铁这一行业当中电炉能够生出许多的烟尘,平均一年就可以捕集10万多吨,如果加上重机、电力制造、造船等行业数百台电炉排出的烟尘,数量就更为可观,这么多的烟尘会造成十分恶劣的环境污染,对人的健康造成影响,所以我们要对其进行有效的治理,不仅如此还要加以利用,变废为宝不浪费宝贵的资源[2]。
在钢铁企业,近些年越来越多人开始注意怎样再次利用烟尘[3]。
对除尘灰的综合利用在国内研究课题中十分重要,目前对除尘灰的利用主要是两个方面,一个是球化后作为建材用料,另一个是作为原料进行回炉再利用,当作建材用料的时候,用作磁性材料的研究现在看来还是十分的少的。
除尘灰球化后在回炉中作为炼钢原料还可以作一些像氧化红铁等技术水平低的材料,当作为这些技术水平低的材料时,对于除尘灰的资源是非常大的浪费,所以这些还有待考虑。
国外和我国一样,对回收利用除尘灰这一项目也十分看重,他们回收其中的炭来作为墨水等等,或者作为活性炭这种吸附能力强的物质,对于水的合格和吸入的大气都起到了净化的作用[4]。
炼钢厂转炉灰的用途

炼钢厂转炉灰的用途
炼钢厂转炉灰是在钢铁冶炼过程中产生的一种废弃物料,通常指转炉炼钢后产生的废渣和灰渣。
这些废弃物料通常包含氧化铁、氧化钙、氧化硅等成分。
转炉灰虽然是废弃物,但可以通过合理的处理和利用,实现资源化和环保目的,具体用途如下:
1.道路基础材料:
转炉灰可以作为道路基础材料的一部分,尤其适用于建设土路或者辅助道路。
其颗粒特性和抗压强度使其成为一种较为理想的道路基础填料。
2.水泥生产:
转炉灰中含有氧化钙等成分,可以作为水泥生产的原料之一。
在水泥生产中,将转炉灰与其他适当的原材料混合,经过煅烧后可以得到矿渣水泥,用于建筑行业。
3.钢渣处理:
转炉灰中含有氧化铁等金属成分,可以通过相应的处理工艺,将其中的金属分离提取,实现废渣的资源化再利用。
4.土地改良:
由于转炉灰中富含氧化钙,可以用作土地改良剂,有助于提高土壤的肥力和改良土壤结构。
5.填埋场覆盖材料:
将转炉灰作为填埋场的覆盖材料,可以降低填埋场渗漏液的渗透速度,减缓填埋场的渗漏问题,有助于环保。
6.矿石冶炼:
转炉灰中的一些金属氧化物可以在冶炼过程中作为助熔剂,有
助于提高冶炼效率。
7.砖瓦生产:
转炉灰中的部分成分可以与其他原材料混合,用于砖瓦等建筑材料的生产。
需要注意的是,转炉灰的具体用途可能会因灰渣的成分差异、处理工艺和当地法规标准而有所不同,因此在利用转炉灰时需要进行科学的分析和处理,确保其合理而环保的利用。
钢铁企业除尘灰的综合利用

钢铁企业除尘灰的综合利用钢铁企业的除尘灰是指从烧结到轧钢的各个工序通过电除尘器、重力除尘器和布袋除尘器等除尘设备提供的灰尘。
据统计,钢铁企业除尘灰产生总量约为钢产量的10%。
所述除尘灰分为烧结机头灰、高炉布袋灰和转炉灰三种。
目录1.除尘灰的性质 (1)1.1.烧结机头除尘灰 (1)1.2.高炉布袋除尘灰 (1)1.3.转炉除尘灰 (2)1.4.电炉除尘灰 (2)2.资源化利用 (3)2.1.研究现状 (3)3.2.产业化现状 (3)3.结语 (4)1.除尘灰的性质1.1.烧结机头除尘灰烧结机头灰是指在烧结工序中,烧结烟气通过大烟道到电除尘器产生的灰尘。
其中所含有害元素主要为钾、钠和氯,局部钢厂的烧结机头灰里氧化钾含量高达30%。
烧结机头灰的粒度极细,呈灰白色,平均粒径在100 um左右,堆密度在0.5〜lg/cn? o烧结机头灰中的铁主要以氧化铁和磁铁矿的形式存在,钾和钠主要以氯化钾和氯化钠的形式存在,同时也存在氯化钙、氯化镁、氯化铅和氯化锌等氯化物。
烧结机头灰如果返回烧结使用,会造成碱金属富集,常见的影响是烧结“糊篦条,引起烧结矿产量、质量降低。
烧结机头灰因有价元素含量较低,利用价值不高。
1.2.高炉布袋除尘灰高炉布袋灰,也称为高炉瓦斯灰或高炉二次灰,是在高炉冶炼过程中从炉第1页共5页顶产生的烟气经重力除尘器、布袋除尘提供的灰尘。
高炉布袋灰中的有害元素主要是锌、钾、钠和氯,同时含有较多的铁和碳,其产生量为3〜6kg/t铁水。
高炉布袋灰的粒度较烧结机头灰粗,呈黑灰色,平均粒径在130u m左右,堆密度在0.7〜l.lg/cn?,外观类似于磁铁精粉。
高炉布袋灰中的铁主要以氧化铁和磁铁矿的形式存在,碳那么以单质碳的形式存在。
高炉布袋灰中的钾和钠同样主要以氯化钾和氯化钠的形式存在,锌那么以氧化锌、铁酸锌和氯化锌的形式存在。
高炉布袋灰中锌含量<1%时可以返回烧结配料使用。
但大局部钢厂高炉布袋灰含锌量在1%以上,如果返回烧结工序继续使用,会造成烧结矿中的锌富集,导致高炉锌负荷超标,易产生降低焦炭强度,侵蚀耐火砖,形成炉瘤,破坏风口等问题。
高炉含锌除尘灰的综合利用---杨春雷课案
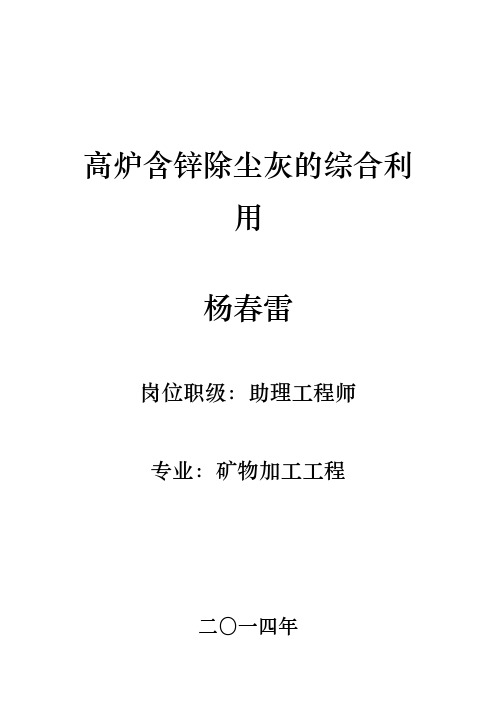
高炉含锌除尘灰的综合利用杨春雷岗位职级:助理工程师专业:矿物加工工程二〇一四年摘要结合钢铁企业节能减排、建立循环经济的发展方向,针对除尘灰的循环利用导致高炉中锌的富集,高锌灰已经成为影响高炉冶炼的重要因素。
本文根据酒钢除尘灰的情况,介绍国内外多种高锌除尘灰处理工艺和基本原理,为高锌除尘灰处理提供思路和方式。
关键词:高锌除尘灰酒钢集团处理工艺节能减排一、除尘灰简介钢铁企业资源和能源密集、生产规模和物流量大、工序流程长,因而产生大量固体废弃物,成为公认的污染大户。
近20年来国外不少发达国家如德、日、英、美、俄等加大了对冶金工业固体废弃物研究开发力度,取得了很好的成绩。
例如在冶金废渣利用方面,美国的利用率已经达到80"--85%,日本为70"--80%,德国和西班牙接近100%。
,而在国内,随着近年来钢铁产量高速增长,环境问题更为突出。
日益增长的钢铁生产能力对周围环境的压力越来越大。
如何提高资源和能源的使用效率,减轻环境负荷,走循环经济的道路,实现可持续发展,已成为未来我国钢铁行业发展的必然方向。
目前我国的钢铁企业冶金流程主要集中于烧结一高炉一转炉一轧钢长流程生产,占钢铁总生产能力的70%以上。
在烧结、高炉炼铁、转炉及电炉炼钢等工序均可产生的大量粉尘及其副产品,统称为除尘灰。
若不加以有效处理,这些堆积和飞扬的除尘灰将对厂区及周围的环境造成严重污染,对农田的生态环境也有很大的危害。
如果能对各类除尘灰合理地开发和利用,不但可以防止产生二次污染,有效地改善周边环境,而且还能变废为宝,将除尘灰作为二次资源来利用。
近年来随着高炉大型化的发展,高炉粉尘发生量不断增多,高炉布袋除尘灰有以下特征:l、粒径小、比重轻。
一般200目过筛率在50"--65%,甚至更细,极易飘散在大气中,严重污染周围环境;2、易反应。
含有较多粒径小的低沸点金属,与空气接触时,易于空气中氧反应,产生自燃。
3、强烈的腐蚀性。
高炉含锌除尘灰的综合利用杨春雷
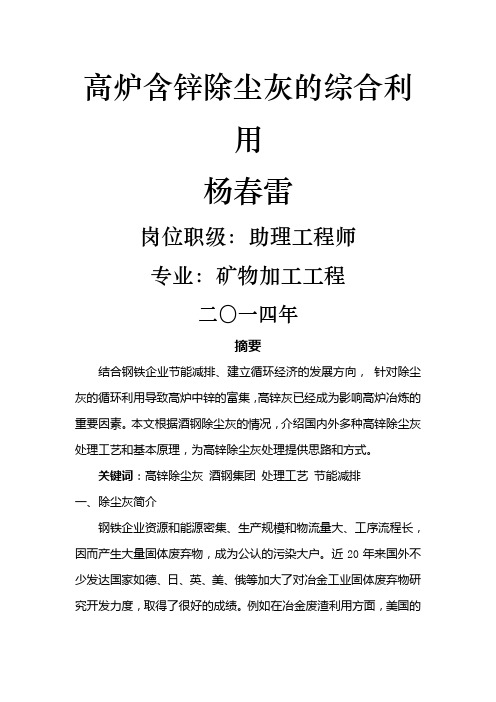
高炉含锌除尘灰的综合利用杨春雷岗位职级:助理工程师专业:矿物加工工程二〇一四年摘要结合钢铁企业节能减排、建立循环经济的发展方向,针对除尘灰的循环利用导致高炉中锌的富集,高锌灰已经成为影响高炉冶炼的重要因素。
本文根据酒钢除尘灰的情况,介绍国内外多种高锌除尘灰处理工艺和基本原理,为高锌除尘灰处理提供思路和方式。
关键词:高锌除尘灰酒钢集团处理工艺节能减排一、除尘灰简介钢铁企业资源和能源密集、生产规模和物流量大、工序流程长,因而产生大量固体废弃物,成为公认的污染大户。
近20年来国外不少发达国家如德、日、英、美、俄等加大了对冶金工业固体废弃物研究开发力度,取得了很好的成绩。
例如在冶金废渣利用方面,美国的利用率已经达到80"--85%,日本为70"--80%,德国和西班牙接近100%。
,而在国内,随着近年来钢铁产量高速增长,环境问题更为突出。
日益增长的钢铁生产能力对周围环境的压力越来越大。
如何提高资源和能源的使用效率,减轻环境负荷,走循环经济的道路,实现可持续发展,已成为未来我国钢铁行业发展的必然方向。
目前我国的钢铁企业冶金流程主要集中于烧结一高炉一转炉一轧钢长流程生产,占钢铁总生产能力的70%以上。
在烧结、高炉炼铁、转炉及电炉炼钢等工序均可产生的大量粉尘及其副产品,统称为除尘灰。
若不加以有效处理,这些堆积和飞扬的除尘灰将对厂区及周围的环境造成严重污染,对农田的生态环境也有很大的危害。
如果能对各类除尘灰合理地开发和利用,不但可以防止产生二次污染,有效地改善周边环境,而且还能变废为宝,将除尘灰作为二次资源来利用。
近年来随着高炉大型化的发展,高炉粉尘发生量不断增多,高炉布袋除尘灰有以下特征:l、粒径小、比重轻。
一般200目过筛率在50"--65%,甚至更细,极易飘散在大气中,严重污染周围环境;2、易反应。
含有较多粒径小的低沸点金属,与空气接触时,易于空气中氧反应,产生自燃。
3、强烈的腐蚀性。
转炉干法除尘灰的炉内循环利用实践

物通 过带 式输送 机进 入烘十 系统 ,筛下物返 回压球
机后继续参与压球 。烘干 系统主要采川 l l 0 ~ 1 5 0 低
除 尘获 冷 圈成球 工艺 除 灰冷 同成球 的T艺流程 图 1 所示 l 从罔
l 可 以肴 f J j ,除 尘 灰 冷 同 成 球 的 【 艺 主 要 包 括 原 料
河 钢集 庸 钢公 司长材部转 炉 采用先 进 的干法 利用价值 。
除 1 一 艺 ,除尘灰 的产生量 为2 0 k g / t 左 右 ,高效利月 j
炼钢 的经济效 益。
除尘灰 中的铁 元素 ,有利 于降低 钢铁 料消 耗和提 高 料会 造成烧 结料 透气性 差 .而影 响烧结 产 通过
Ca 0
7 . 2 7
P
考察 和调 研 国内除尘灰 球 的 回收 和使 刚情 况 ,将 除
作 行 位 :} , i l 钢策刚脚钢公 司长材部 .河北
翩l J 0 6 3 0 1 6
■ 4 2 2 o 1 7 年第4 期
囝 蛭
表1 除尘灰的主要成分( 质量分数)
组成 T F e F e O C a O S i O2 AI 2 O3 Mg O Mn O
I! : 兰 二 = :l
广=■
r
料 碾 压 筛 烘
I竺: 皇 I
O O O
混匀
-
压
球
分
干
3
●
8
图I 除 尘 灰 冷 固 球 团 工 艺 流 程
表2 除尘灰球主要成分和性能
质垃分数/ %
项目
F e 2 03
F e o
温 热炯 气进行烘 叶 二 ,热源 为钢铁 厂其他丁 序产 生的 废 气等 。烘 _ f后的熟 球经过 筛分 后 ,成 品球 通过 汽 车运 出,筛下物返 同碾压 T序继续进行压球 除尘灰 球 的成分 与性 能
除尘灰综合利用简介
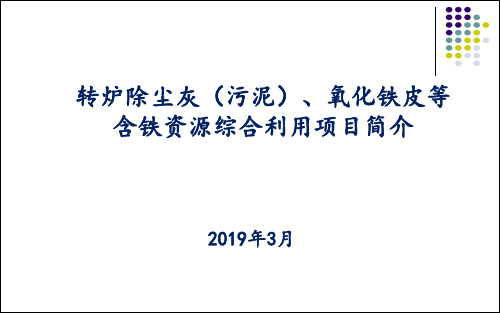
4、转炉干法除尘灰和湿法污泥的区别
干法除尘灰是通过静电除尘器收集的炼钢粉 尘,保持了粉尘中CaO的活性。湿法除尘产生的 污泥,由于经过了水的浸泡处理,污泥中的CaO 已经反应形成了Ca(OH)2,没有活性。
三、除尘灰(污泥)的利用方法
l 钢厂直接外卖处理(最简单处理方式) l 通过烧结配料回收利用(简称长流程法) l 直接返回转炉炼钢回收利用(简称短流程法)
六、经济效益分析(详情见分析报告)
1、不同处理方式经济效益对比分析
计算依据:
工序 除尘灰——冷固球
加工费 (元/吨)
200
回收率 100%
备注 1吨灰产1吨球
除尘灰——烧结矿
172
100%
1吨灰产1吨烧结矿
烧结矿——铁水
681
62.2%
1.6吨矿产1吨铁水
铁水——钢水
480
92.5%
铁水收得率
冷固球——钢水
[1] 毕秀荣,刘润藻,朱荣,等.转炉炼钢烟尘形成机理研究[J].工业加热,2010,39(6):13. [2] 王令福.炼钢粉尘处理工艺的最新发展[J].冶金能源,2006,25(4):46.
3、转炉除尘灰(污泥)的典型成分及特征
典型成分:
名称
TFe
转炉除尘灰(细灰) 61.30
转炉除尘灰(粗灰) 55.44
3、不同利用方式优缺点对比分析
使用方法
项目
利用周期
直接 外卖
简单直接
经济效益
廉价处理
造成钢厂含 铁资源的浪 费,效益最 低。
使用特点
长流程
短流程
长
短
处理成本高,有一定效益。 处理成本低,效益最大化。
烧结配料时不易润湿和混合,可代替铁矿石、烧结返矿作
转炉除尘灰的高附加值利用)

核心提示:摘要:随着转炉炼钢生产的发展,炼钢工艺的日趋完善,相应的除尘技术也在不断地发展完善。
炼钢烟气的净化回收方法主要有两种,一种是湿法(OG 法),一种是干法(LT 法)。
LT 法(干法)为德国Lurgi 公司与Thyssen 钢铁厂研制成功的一种转炉烟气净化及煤气回收干式系统,该除尘方式不用大量浊环水洗涤烟气,而是采用蒸发冷却器+静电除尘器+煤气冷却器系统。
它以净化效率高、能耗低、干粉尘可设置压块系统,粉尘经压块后直接供转炉利用等特点,得到广泛应用。
转炉除尘灰的高附加值利用卜二军耿丽君刘红艳随着转炉炼钢生产的发展,炼钢工艺的日趋完善,相应的除尘技术也在不断地发展完善。
炼钢烟气的净化回收方法主要有两种,一种是湿法(OG 法),一种是干法(LT 法)。
LT 法(干法)为德国Lurgi 公司与Thyssen 钢铁厂研制成功的一种转炉烟气净化及煤气回收干式系统,该除尘方式不用大量浊环水洗涤烟气,而是采用蒸发冷却器+静电除尘器+煤气冷却器系统。
它以净化效率高、能耗低、干粉尘可设置压块系统,粉尘经压块后直接供转炉利用等特点,得到广泛应用。
邯钢转炉烟气采用干法除尘技术,与湿法相比,分别节电、节水约1/3,减少建设用地1/2,烟尘含量由50mg/Nm3降到10mg/Nm3,同时烟尘可被全部回收再利用,实现节能4. 5kgce/t 钢。
现一炼钢厂的煤气回收量已稳定达到140Nm3/t 钢,回收煤气热值稳定在150 0kcal/Nm3以上。
这对我国转炉炼钢节能减排、实现负能炼钢起到了积极的推动作用。
但是转炉除尘灰具有温度高、金属化程度高、易自燃、粒度细、扬尘二次污染大等特性,造成其处理及综合利用难度大,亟待开发一种适合干法粉尘特性的新型处理工艺。
1国内转炉除尘灰的利用现状及合理性1.1 热压块热压块工艺是利用粉尘的自燃特性将粉尘加热,利用其在高温下的塑性,经高压压球机压制成块,然后在氮气密封状态下冷却后输送到转炉,代替废钢或矿石。
烧结厂关于除尘灰综合利用的报告

4、该工艺主要设备为:料仓、混料仓、搅拌机、压球机,以及铲
车、叉车、除尘灰运输车等车辆。
该工艺建成后,能够消化厂内产生的除尘灰,充分利用废渣资源,
变废为宝。
五、投资概算:
日产150吨除尘灰压球机报价单
序号 设备名称
型号
数量 (台)
价格(万 元)
1
料仓
10m³
4
12.8
2
皮带输送机 Байду номын сангаас00mm×8m
1
4# 5.04 8.61 4.74 1.99 43.63 4.06 0.106 0.55 1.13
预计 压球 后成 分
四、除尘灰利用初步设想: 为了有效利用烧结、高炉、转炉除尘灰及炼钢污泥,回收铁成份。
回收企业生产过程中的废弃物,降低生产成本。结合国内先进的处理技
术,将除尘灰配加氧化铁皮、生石灰、煤粉等压实成球,作为转炉冶炼
0.9
3
双轴搅拌机 1m×4m
1
12
4
皮带输送机 800×12m
1
1.44
5
除尘灰压球 机
750型
1
16
电器综合配
6
1
电柜 合计
44.14
炼铁事业部烧结厂做出以下考虑搅拌一压球一干燥一炼钢将各种除尘灰铁泥煤粉等原料进行混合加入粘结剂进行搅拌再用压球机成球最后通过光照和风等自然干燥过程形成干燥主料
烧结厂关于除尘灰综合利用的报告
一、编制原因 随着高炉项目顺利投产,烧结高炉除尘灰在原料场进一步聚集,机
械化料场不具备使用除尘灰的条件。目前,原料场储存烧结、高炉、转 炉除尘灰进2000吨。由于除尘灰粒度较细、密度较轻,在存放过程中遇 风造成二次扬尘,造成环境污染;另一方面,高炉干法除尘及烧结机机 头电除尘碱性金属ZnO、K2O、Na2O等含量较高,不利于烧结生产配加。 二、除尘灰烧结配加对高炉生产的负面影响
转炉干法除尘灰循环利用合理性探讨及试验研究
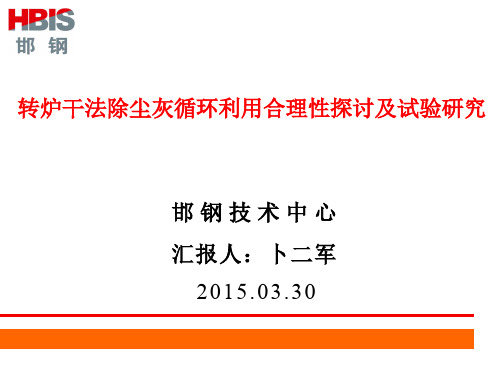
西区炼钢厂
一炼钢厂
174433
1974526
27.00
27.70
表2 2014年12月转炉干法除尘灰产量及回收量ቤተ መጻሕፍቲ ባይዱ
工序产量(t) 单位 指标 品种 当月 22 kg/t 22 kg/t 炼钢粗灰 炼钢细灰 炼钢粗灰 炼钢细灰 461188 累计 5152091 本月(t) 2766 7910 1568 4063 累计(t) 30685 89398 17992 43309 当月(kg/t) 23.15 累计(kg/t) 23.31 回收量
图8 链篦机-回转窑生产线
图7 加料系统
20
四、实验研究
4.2 利用转炉除尘细灰制备永磁铁氧体粉料
图9 铁氧体预烧料
烧结温度 1195 1200 1220 1230 1235 Br (mT) 408.7 403.0 407.5 410.1 414.0 Hcb (kA/m) 249.0 267.7 246.1 241.6
12
三、邯钢转炉除尘灰基本情况
3.4 邯钢转炉除尘分析检测
Element O Si Ca Fe Wt% 30.83 0.64 1.32 64.79 At% 60.06 0.71 1.03 36.17
图4 转炉干法除尘细灰的表面形貌及能谱分析结果
转炉除尘灰杂质含量比较多,其中包括CaO、SiO2,能谱打点位置上除去 杂质中氧含量为: At%( O )= 57.61%。从能谱分析结果经计算可以看出, 转炉除尘灰中氧化铁的含量比较高,含有少量Fe3O4,是制备铁系颜料的理 想原料。
15
四、实验研究
4.1 利用转炉除尘细灰制备氧化铁红
1000 800
炉内温度(℃)
600
除尘灰综合利用简介
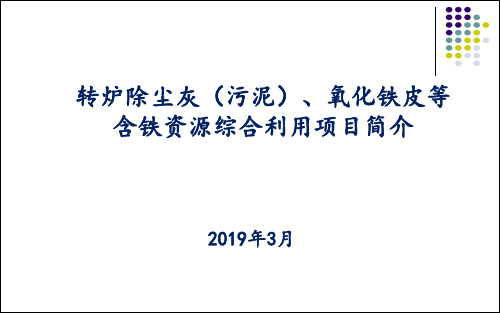
3、转炉除尘灰(污泥)的典型成分及特征
典型成分:
名称
TFe
转炉除尘灰(细灰) 61.30
转炉除尘灰(粗灰) 55.44
4、转炉干法除尘灰和湿法污泥的区别
干法除尘灰是通过静电除尘器收集的炼钢粉 尘,保持了粉尘中CaO的活性。湿法除尘产生的 污泥,由于经过了水的浸泡处理,污泥中的CaO 已经反应形成了Ca(OH)2,没有活性。
三、除尘灰(污泥)的利用方法
l 钢厂直接外卖处理(最简单处理方式) l 通过烧结配料回收利用(简称长流程法) l 直接返回转炉炼钢回收利用(简称短流程法)
五、除尘灰冷固球的使用方法
1、使用目的
用除尘灰冷固球(部分或全部)代替转炉冶炼过程使用的铁 矿石、烧结返矿等,促进冶炼前期化渣,提供氧化剂,调节炉内 温度,提高脱磷效率,降低钢铁料消耗。
2、加入方式及时机
通过高位料仓加入,在转炉吹炼前期随石灰等辅料分批加入。 为保证除尘灰中的金属收得率,加入时间需保证在返干前加完。 如果作为后期调温剂,也须在提枪前2分钟加完。
2、直接返回转炉炼钢回收利用(简称短流程方法)
1)短流程法回收利用的工艺流程 除尘灰——冷固球——转炉炼钢
2)短流程法回收利用的原理及目的 通过特殊加工处理工艺,生产高强度冷固球,保留除尘灰中CaO活性, 通过转炉高位料仓分批加入,回收Fe、 CaO等有益成分。
3)短流程法回收利用的价值 直接加入炼钢转炉,前期起到助熔化渣、强化脱磷的作用,同时回收 Fe、 CaO等有益成分。
- 1、下载文档前请自行甄别文档内容的完整性,平台不提供额外的编辑、内容补充、找答案等附加服务。
- 2、"仅部分预览"的文档,不可在线预览部分如存在完整性等问题,可反馈申请退款(可完整预览的文档不适用该条件!)。
- 3、如文档侵犯您的权益,请联系客服反馈,我们会尽快为您处理(人工客服工作时间:9:00-18:30)。
核心提示:摘要:随着转炉炼钢生产的发展,炼钢工艺的日趋完善,相应的除尘技术也在不断地发展完善。
炼钢烟气的净化回收方法主要有两种,一种是湿法(OG 法),一种是干法(LT 法)。
LT 法(干法)为德国Lurgi 公司与Thyssen 钢铁厂研制成功的一种转炉烟气净化及煤气回收干式系统,该除尘方式不用大量浊环水洗涤烟气,而是采用蒸发冷却器+静电除尘器+煤气冷却器系统。
它以净化效率高、能耗低、干粉尘可设置压块系统,粉尘经压块后直接供转炉利用等特点,得到广泛应用。
转炉除尘灰的高附加值利用卜二军耿丽君刘红艳随着转炉炼钢生产的发展,炼钢工艺的日趋完善,相应的除尘技术也在不断地发展完善。
炼钢烟气的净化回收方法主要有两种,一种是湿法(OG 法),一种是干法(LT 法)。
LT 法(干法)为德国Lurgi 公司与Thyssen 钢铁厂研制成功的一种转炉烟气净化及煤气回收干式系统,该除尘方式不用大量浊环水洗涤烟气,而是采用蒸发冷却器+静电除尘器+煤气冷却器系统。
它以净化效率高、能耗低、干粉尘可设置压块系统,粉尘经压块后直接供转炉利用等特点,得到广泛应用。
邯钢转炉烟气采用干法除尘技术,与湿法相比,分别节电、节水约1/3,减少建设用地1/2,烟尘含量由50mg/Nm3降到10mg/Nm3,同时烟尘可被全部回收再利用,实现节能4.5kgce/t 钢。
现一炼钢厂的煤气回收量已稳定达到140Nm3/t 钢,回收煤气热值稳定在1500kcal/Nm3以上。
这对我国转炉炼钢节能减排、实现负能炼钢起到了积极的推动作用。
但是转炉除尘灰具有温度高、金属化程度高、易自燃、粒度细、扬尘二次污染大等特性,造成其处理及综合利用难度大,亟待开发一种适合干法粉尘特性的新型处理工艺。
1 国内转炉除尘灰的利用现状及合理性1.1 热压块热压块工艺是利用粉尘的自燃特性将粉尘加热,利用其在高温下的塑性,经高压压球机压制成块,然后在氮气密封状态下冷却后输送到转炉,代替废钢或矿石。
该方法不需要另外添加黏结剂,粉尘团块的强度也很高,可直接用于转炉作冷却材料使用,是现在LT 粉尘处理应用最多的一种方法。
但是,热压块生产需在高温和隔绝空气的条件下进行,对设备和工艺控制要求很高,一次性投资大、工艺条件苛刻、设备故障率很高,难以长期顺利生产。
1.2 冷压块有企业在除尘灰及污泥中加入部分添加剂,通过冷固工艺制成转炉造渣剂压块,用于转炉造渣,强化了造渣,改善了脱磷效果,脱磷率提高;化渣效果好,能够起到防喷溅的作用。
1.3 返回烧结邯钢西区转炉除尘灰的利用途径是加入烧结混合料中,经烧结后进入炼铁高炉进行循环。
虽然该方法不需要增加设备,但粒度过细且能够自燃的干法除尘灰不利于烧结矿质量的控制和热量的平衡。
除尘灰含有有害杂质,而烧结难以有效地去除这些杂质,使得烧结配加和稳定操作困难,入高炉后将影响高炉正常操作和炉衬寿命;其化学成分、粒度、水分均存在较大差异,不利于烧结矿生产和质量的提高;该方法仅能回收部分含铁粉尘,从某利意义上讲,对这些宝贵的二次资源没有起到真正意义上的回收。
因此,在烧结配料中加入除尘灰进行循环利用极不科学。
1.4 竖炉球团配加有企业在竖炉中配加炼钢除尘细灰,经过近20 个月的摸索和改进,实现了生产稳定顺行,并保证了质量稳定。
转炉干法除尘灰用于竖炉球团配加生产是可行的,配加量在5%以内,可减少对竖炉生产的影响。
但是还存在炼钢除尘灰质量不稳定、成分波动大、倒运过程中二次扬尘太大等问题。
2 邯钢转炉除尘灰基本情况2.1 转炉除尘灰产量及回收量邯钢以转炉LT 除尘灰为研究对象,探索转炉除尘灰的高附加值利用途径。
转炉除尘灰分为粗灰、细灰两种。
粗灰来自蒸发冷却器底部,细灰是炼钢过程中产生的烟尘经干法除尘、沉降得到的。
2014 年12 月邯钢炼钢除尘灰当月产量、累计量及回收量,如表1 所示。
2.2 转炉除尘灰的化学成分转炉除尘灰的化学成分,见表2。
转炉除尘粗灰为灰黑色,为细颗粒。
转炉除尘细灰为红-褐色,颜色与氧化铁红相近,粒度较细,100 目的占70%以上。
转炉除尘细灰中氧化铁的含量比较高,含有少量Fe3O4,是制备铁系颜料的理想原料。
3 创新研究邯钢以转炉除尘细灰为原料,以制备出高附加值产品为目标,提出氧化焙烧制备成高纯氧化铁红的方案。
氧化铁红制备试验采用高温氧化培烧法。
3.1 制备氧化铁红的研究1)烘干除水工艺对转炉除尘灰进行现场取样,在烘箱中烘干2h 以上,温度控制在100℃左右。
2)混匀物料工艺转炉除尘灰质量不稳定,TFe 和CaO 含量波动较大。
-应采取质量控制措施,即将其进行初步混匀处理,以降低成分波动。
3)磨样制备工艺转炉除尘灰为粒度较细的粉尘,为了达到粒度均匀、氧化效果好的目的,采用制样机对转炉除尘灰进行一次粗破,其出料粒度200 目达到92%以上。
4)焙烧氧化工艺本研究是在碳管炉内进行静态焙烧氧化制备氧化铁红,氧化过程中所需氧气来自空气,工艺温度控制在850-900℃,恒温时间为30mmin。
其炉内反应为:碳管炉升温速率的控制如图1 所示。
焙烧所得物料产生结块,经简单磨细至-200 目占90%以上,可获得纯度较高的氧化铁红产品。
氧化铁红的化学成分,如表3 所示。
氧化铁红质量与标准对比,如表4 所示。
该产品不存在有机着色物,不仅可用作涂料或建材的着色剂或添加剂,更适宜做磁性材料的原料,可直接生产铁氧体预烧料。
3.2 制备磁性材料的研究以氧化铁红为原料生产高品质铁氧体预烧料,进而生产铁氧体材料已被磁性材料厂广泛采用。
其原理及化学方程式如下:碳酸盐分解反应:(300-0-800℃)中间反应:(600-800℃)通过以上流程制得的铁氧体性能优良,与利用铁鳞作原料制备的铁氧体预烧料性能相当或优于铁鳞。
邯钢于2012 年分别建成铁鳞、氧化铁红生产永磁铁氧体预烧料生产线,采用链篦机-回转窑的方法,每年可生产出2 万多吨永磁铁氧体预烧料,现已稳定生产运行两年多。
氧化铁红和铁鳞的利用提高了邯钢产品的综合利用程度及科技含量,填补了邯钢磁性材料的空白,发展壮大了其非钢产业。
如果通过转炉除尘灰批量生产氧化铁红,进而再生产铁氧体材料,附加值水平将得到更大提升。
针对这种情况,邯钢进行了利用转炉干法除尘细灰制备铁氧体预烧料的试验研究,材料磁性能检测结果如表5 所示。
3.3 经济性能评价炼钢除尘灰的价格约100-200 元/t,氧化铁红的价格为1400 元/t,铁氧体预烧料的价格则超过3000 元/t,采用炼钢除尘灰生产氧化铁红,进而再生产高性能永磁铁氧体,昔日炼钢除尘灰作为固体废弃物易污染、难治理的现状将得到根本性的改善,其高附加值、高效的利用得以实现。
4 结语邯钢西区转炉除尘细灰的处理方式为返回烧结配料,利用档次低,经济效益不明显。
除尘细灰返回烧结配加困难,经常造成烧结故障。
本工艺可将转炉除尘细灰全部回收利用生产出氧化铁红,不仅有效回收利用了二次资源、减少环境污染,而且提高了除尘细灰的利用水平,对企业的可持续发展有重要意义,以利用促治理,可达到经济效益、环境效益和社会效益协调发展的目的。
1)通过开展转炉除尘灰的二次回收利用试验研究,拓展了思路,验证了可行性,为进一步工业化生产铺平了道路。
2)转炉除尘灰作为氧化铁红生产的原料,资源丰富,可利废为宝,生产中不使用酸、碱及其他化学原料进行处理、无废物排放,可防止环境污染、方法简单快捷、能耗小、生产成本低,成品中氧化铁红含量高达95%以上,具有竞争力。
3)利用制备出来的氧化铁红制备铁氧体预烧料,将会创造更多利润。
焦粉分布对准颗粒燃烧速度的影响1 研究背景由于原料价格大幅度上涨、环保政策更加严格及原料质量变差,导致铁矿烧结生产形势愈发严峻,因此必须改进烧结生产工艺。
在烧结过程中,焦粉燃烧速度是影响烧结矿质量和烧结机利用系数最重要的因素之一。
为了提高焦粉燃烧效率,开发出新的喷涂制粒方法,如图1所示。
在该方法中,将焦粉和石灰石喷涂于准颗粒的表面。
采用喷涂制粒法能够改善焦粉的燃烧性,提高烧结机利用系数,生产出优质烧结矿。
日本九州大学研究了焦粉在准颗粒中的分布对焦粉燃烧速度的影响。
2 讨论2.1 试验试样和步骤使用氧化铝粉末和焦粉制备模拟准颗粒的试验试样。
为了简化试验条件,制备氧化铝粉末以替代铁矿。
在试验过程中,忽略液相生成、铁矿还原和二次氧化对焦粉燃烧的影响。
选取焦粉的粒度小于125μm,氧化铝粉末的粒度小于250μm,按照表1示出的质量比进行混合。
制备四种具有不同焦粉分布的试样。
全部原料和试样示意图如图2所示。
该试样分为内核和涂层。
把氧化铝与焦粉进行混合后,用不锈钢冲模将混合料压成直径10mm的圆片,将该圆片作为内核,圆片厚度为10mm,孔隙比为35%。
然后对内核进行喷涂,并压成直径15mm的圆片,该圆片厚度为15mm,孔隙比为35%。
涂层中焦粉配比的变化范围为33vol%~55vol%。
在本次研究中用热天平测量试样在焦粉燃烧期间的重量损失如图3所示。
将该试样放入铂制篮子内。
使用立式电阻炉营造等温加热条件,等温区的温度达到1073K、1223K、1373K和1523K。
在燃烧试验前,在N2气氛下按照给出的各个温度进行热处理,以便从试样中脱除水分和挥发分。
然后,把反应管的里面换成空气,空气流量为4NL/min。
当试样的重量损失为零时,表明试验已经结束。
2.2 试验结果在本次研究中将反应率定义为试样中固定碳的去除率。
如果产生的CO气体可以忽略不计,那么碳燃烧反应的化学方程式如(1)式:C(s)O2(g)=CO2(g)(1)在燃烧试验中,把试样的重量损失作为固定碳的降低量。
从而得出反应率的计算公式,如(2)式:Δω1F= ———(2)W观察在1073K和1523K温度下分级反应曲线可知,当加入的焦粉在试样表面产生偏析时,焦粉的燃烧速度较快。
在高温下进行试验,燃烧速度加快。
3 动力学分析燃烧反应分为五个步骤:第一步O2通过气膜由气相传输至颗粒表面;第二步在焦粉燃烧后,O2通过氧化铝粉末层由颗粒表面传输至反应界面;第三步在反应界面发生燃烧反应;第四步在焦粉燃烧后CO2通过氧化铝粉末层由反应界面传输至颗粒表面;第五步CO2通过气膜由颗粒表面传输至气相。
根据动力学分析结果,发现准颗粒的焦粉分布不但对界面反应速度产生影响,而且对氧气扩散也具有影响。
换句话说,当加入的焦粉在准颗粒表面产生偏析时,准颗粒中氧气的扩散速度较快,这是采用新的制粒方法制备的准颗粒中焦粉燃烧速度加快的主要原因之一。
4 烧结模拟4.1 模拟方法采用本次研究结果对喷涂方法进行模拟。
对于常规方法与喷涂方法来说,焦粉在准颗粒中的分布各不相同。
用S′、C和P代表采用常规方法制备的准颗粒,用C′和P′代表采用喷涂方法制备的新型准颗粒。
4.2 计算条件实际烧结生产的常规计算条件见表2,准颗粒中的焦粉见表3。