[现代电动,混合动力和燃料电池汽车基础,理论和设计].Modern.Electric,.Hybrid
混合动力汽车、纯电动汽车及燃料电池毕业设计翻译
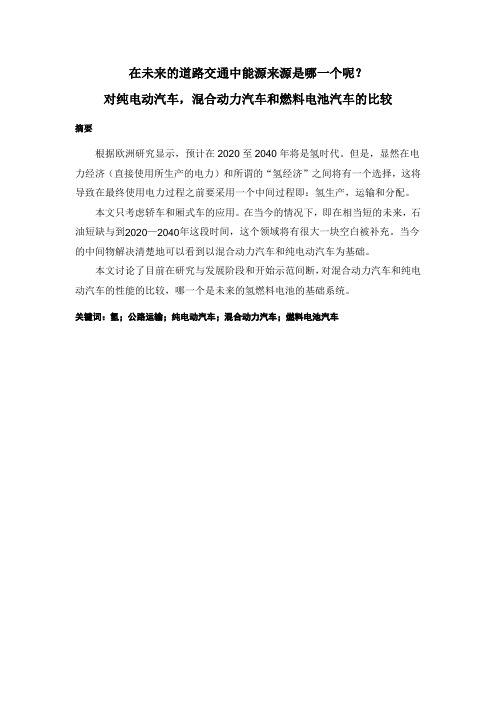
在未来的道路交通中能源来源是哪一个呢?对纯电动汽车,混合动力汽车和燃料电池汽车的比较摘要根据欧洲研究显示,预计在2020至2040年将是氢时代。
但是,显然在电力经济(直接使用所生产的电力)和所谓的“氢经济”之间将有一个选择,这将导致在最终使用电力过程之前要采用一个中间过程即:氢生产,运输和分配。
本文只考虑轿车和厢式车的应用。
在当今的情况下,即在相当短的未来,石油短缺与到2020—2040年这段时间,这个领域将有很大一块空白被补充。
当今的中间物解决清楚地可以看到以混合动力汽车和纯电动汽车为基础。
本文讨论了目前在研究与发展阶段和开始示范间断,对混合动力汽车和纯电动汽车的性能的比较,哪一个是未来的氢燃料电池的基础系统。
关键词:氢;公路运输;纯电动汽车;混合动力汽车;燃料电池汽车1.引言电动车是解决穿梭都市的一个最佳的方案,因为它不排放废气的。
特别是在城市和在恶劣气候条件,路上行驶的车辆产生的废气可以把空气质量降低到直接威胁人们的身体健康。
已经有几个城市多次申请严厉的交通限制。
电动车也非常适合在进入新的交通一体化管理概念,如自动出租的汽车系统和货物配送中心,或小型客车城市中心服务。
对于所有这些原因,越来越多的有关城市和环境的公司,在他们车队中引进电动汽车。
今天,显然有必要来推广支持欧洲准备组织下一步的氢燃料电动汽车。
在初始发展的步伐中,石油危机是显然,并将要采取令人吃惊的规模[1-3]要求引进急需的替代燃料为带有电的公路运输发挥了重要作用。
然而,电力存储仍然是一个关键点。
替代电池系统的发展与一个重要市场的发展一致显示了一个真正的技术决策和经济突破在性短期或中期的可能。
高温新电池的电池类型,如镍氢电池,锂基电池已经在市场或将在未来数年提供。
由于其高能量密度(镍氢为70Wh/kg和锂电池为125Wh/kg,相比40Wh/kg铅电池和60Wh/kg镍镉电池[4]),他们将提供前所未有的车速,高达250多公里,甚至通过更引进范围扩充使车速更高。
现代电动汽车技术复习资料知识分享

现代电动汽车技术复习资料知识分享现代电动汽车技术复习资料第⼀章绪论1.电动汽车的定义:电动汽车是指汽车⾏驶的动⼒全部或部分来⾃电机驱动系统的汽车,它主要以动⼒电池为车载能源,是涉及机械、电⼦、电⼒、微机控制等多学科集成的⾼科技产品。
2.电动汽车的优点:尾⽓排放少、能源⼴泛化、能量效率⾼、运⾏费⽤低、系统可控性好。
3.发展电动汽车⽬前存在的主要问题:初始成本⾼;续驶⾥程短,载质量⼩;基础设施投⼊⼤;蓄电池的⽐能量和能量密度⽐燃油低得多。
4.电动汽车分为纯电动汽车、混合动⼒电动切换、插电式混合动⼒汽车、燃料电池电动汽车。
5.⼀般发展电动汽车的技术路径是:近期—混合电动汽车;中期—纯电动汽车;远期—燃料电池电动汽车。
第⼆章纯电动汽车1.纯电动汽车的定义:是指利⽤动⼒电池作为储能动⼒源,通过电池向电机提供电能,驱动电机运转,从⽽推动汽车前进的⼀种新能源汽车。
2.纯电动汽车的优点:(1)零排放、零污染、噪声⼩;(2)结构简单、维修⽅便;(3)⾏驶平稳、乘坐舒适、安全性好及驾驶简单轻便;(4)可使⽤多种能源、机械结构多样化等。
3.纯电动汽车的缺点:(1)低的电池能量密度。
(2)过重的电池组。
(3)有限的续驶⾥程与汽车动⼒性能。
(4)电池组昂贵的价格及有限的循环寿命。
(5)汽车附件的使⽤受到限制。
4. 从电⽓构成⾓度,纯电动汽车可分纯电动汽车系统可分为三个⼦系统:电动机驱动⼦系统、能源⼦系统和辅助⼦系统。
1)电动机驱动⼦系统包括:由车辆控制器、功率转换器(电⼒电⼦变换器)、电机、机械传动装置和驱动车轮组成。
2)能源⼦系统由能源、能量管理单元和能量的燃料供给单元构成。
3)辅助⼦系统由功率控制单元、车内⽓候控制单元和辅助电源组成。
5.整车控制器:整车控制器是整个纯电动汽车的核⼼控制部件,它采集加速踏板信号、制动踏板信号及其他部件信号,并做出相应判断后,控制下层的各部件控制器的动作,驱动汽车正常⾏驶。
作为汽车的指挥管理中⼼,动⼒总成控制器主要功能包括:驱动⼒矩控制、制动能量的优化控制、整车的能量管理、CAN⽹络的维护和管理、故障的诊断和处理、车辆状态监视等,它起着控制车辆运⾏的作⽤。
混合动力汽车
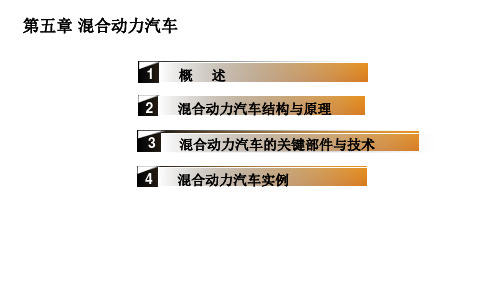
混合动力汽车的关键部件
• 机电耦合装置
•
4、辅助功能,机电耦合装置最好能充分发挥电机低
速大转矩的特点来实现整车起步,利用电机的反转来实现
倒车,从而取消倒档机构。
混合动力汽车的关键部件
• 机电耦合装置 • 单行星排耦合系统
混合动力汽车的关键部件 • 机电耦合装置
• 转速合成式并联混合动力汽车的发动机和 电动机通过离合器和一个“动力组合器” 来驱动汽车。可以利用普通内燃机汽车的 大部分传动系统的总成,电动机只需通过 “动力组合器”与传动系统连接,结构简 单,改制容易,维修方便。为获得最佳传 动效果,控制装备往往十分复杂
混联式驱动系统是串联式与并联式的综合,其结构示意图如图所示
荷非经济区域。发动机最大功率定为车辆以100Km/h速度在平路上行 驶时需求功率的10倍,或者是在6%坡度上以100Km/h速度行驶时需 求功率的3—4倍。
混合动力汽车的关键部件
• 混合动力汽车发动机特点
•
在混合动力汽车中,由于电机驱动系统的参与,发动
机的工作过程有了优化的基础。例如,可采用小径的曲轴
增程器(通常为小功率的发动机-发电机组或燃料电池发
电系统等),延长动力电池组一次充电续驶里程,满足日
常行驶的需要。相比纯电动汽车,增程式电动汽车可以采
用较小容量的动力电池组,有利于降低动力电池组的成本
。相比串联混合动力汽车,增程器功率偏小,动力电池组
容量配置偏高。
混合动力汽车的关键部件——发动机
• 在混合动力汽车上,发动机作为唯一的一个耗油部件,其 性能和控制特性的好坏直接决定了整车的燃油经济性。由 于混合动力汽车上还具备电机驱动系统以及动力电池组等 电能存储单元,发动机的工作过程和控制特性与常规汽车 发动机有了明显的区别,这也为混合动力汽车中发动机的 优化奠定了基础。
现代电动汽车发展及技术
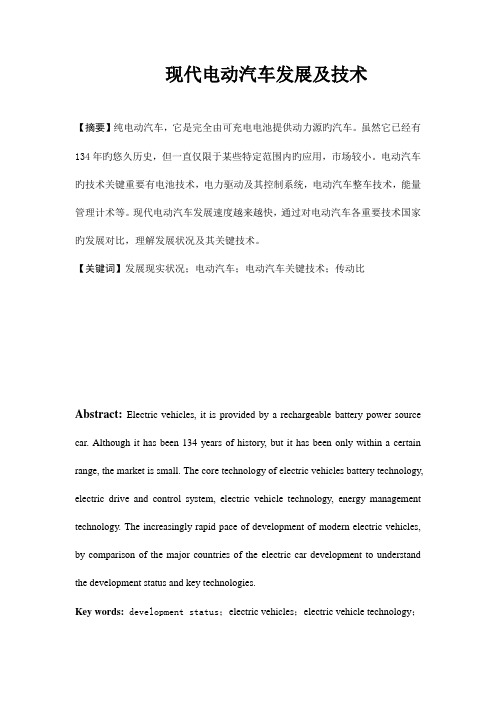
现代电动汽车发展及技术【摘要】纯电动汽车,它是完全由可充电电池提供动力源旳汽车。
虽然它已经有134年旳悠久历史,但一直仅限于某些特定范围内旳应用,市场较小。
电动汽车旳技术关键重要有电池技术,电力驱动及其控制系统,电动汽车整车技术,能量管理计术等。
现代电动汽车发展速度越来越快,通过对电动汽车各重要技术国家旳发展对比,理解发展状况及其关键技术。
【关键词】发展现实状况;电动汽车;电动汽车关键技术;传动比Abstract: Electric vehicles, it is provided by a rechargeable battery power source car. Although it has been 134 years of history, but it has been only within a certain range, the market is small. The core technology of electric vehicles battery technology, electric drive and control system, electric vehicle technology, energy management technology. The increasingly rapid pace of development of modern electric vehicles, by comparison of the major countries of the electric car development to understand the development status and key technologies.Key words: development status;electric vehicles;electric vehicle technology;drive ratio1 背景及发展1.1 背景环境在全球能源和环境问题旳严峻形势下, 汽车工业正面临巨大挑战, 节能与减排旳技术变革迫在眉睫。
现代汽车技术第四讲燃料电池汽车能源动力系统PPT课件

Bipolar Plates 7%
2020/11/27
22
燃料电池技术的发展-成本
2020/11/27
燃料电池技术的发展-耐久性
2020/11/27
燃料电池技术的发展-冷启动性能
2020/11/27
燃料电池技术的发展-功率密度
2020/11/27
储氢技术
2020/11/27
储氢技术
• 燃料电池汽车的直接贮氢方式有如下三种:
动力控制
DCDC,DCAC,DCL
通讯网络
CAN总线通讯
仪表
数字化智能仪表
2020/11/27
1 燃料电池汽车动力系统结构型式
2020/11/27
1 燃料电池汽车动力系统结构型式
2020/11/27
1 燃料电池汽车动力系统结构型式
2020/11/27
1 燃料电池汽车动力系统结构型式
燃料电池车
• 目前,国际上从事质子交换膜燃料电池研究开发的大公司,包 括 加拿大Ballard Power Systems、美国的通用汽车公司等, 在燃料电池发动机研究开发上均高压力(相对压力≥2个大气 压)运行的技术路线,导致高压运行的燃料电池发动机中的 空压机功耗大,超过整个发动机输出功率的20%,且价格极高 (高压)。
2020/11/27
现代汽车技术 第四讲
燃料电池汽车
1、燃料电池汽车动力系统结构型式 2、燃料电池汽车能量管理与动力控制策略 3、燃料电池发动机及及其管理系统 4、其它
2020/11/27
燃料电池汽车结构
2020/11/27
燃料电池汽车结构
2020/11/27
1 燃料电池汽车动力系统结构型式
dSpace
新能源汽车概论 第2版 项目四 混合动力汽车的认知
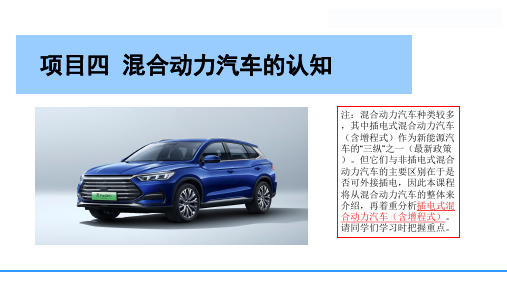
学习课题
一. 混合动力汽车的基础知识 二. 混合动力汽车的结构与原理 三. 混合动力汽车的实例
引导问题1: 什么是混合动力汽车?
引导问题1: 什么是混合动力汽车?
➢ 混合动力汽车通常是指由不同动力源驱动的汽车,包括油电 混合动力汽车、气电混合动力汽车。目前天然气汽车通常也 是油气混合动力的一种。本文主要介绍油电混合动力汽车。
串联式的工作模式通常有三种:纯电动模式、纯发动机模式、 混合模式。 纯电动模式即发动机关闭,车辆行驶完全依靠电池组供电
驱动; 纯发动机模式则仅在发动机运行情况下驱动车辆,蓄电池
电力充足时作为储备,不足时,发动机同时为其充电; 混合模式,即整车动力是通过发动机与电池组共同提供。
引导问题1: 串联式混合动力汽车?
增程式电动汽车动力系统原理图
引导问题5:增程式汽车——典型工作模式
(1)纯电动模式 当动力电池电量充足时,电能从电池输出,通过电机控制器将电能 输送给电动机,电动机将电能转换为机械能通过动力传动装置将动力输 送给驱动轮,从而驱动汽车运行,能量传递路线如图所示。此时增程器 不工作,相当于纯电动汽车运行。
混联式混合动力电动汽车的功能结构图
引导问题3: 混联式混合动力汽车
混联式混合动力系统的特点在于内燃机系统和电机驱动系 统各有一套机械变速机构,两套机构或通过齿轮系,或采 用行星轮式的结构结合在一起,从而综合调节内燃机与电 动机之间的转速关系。
与并联式混合动力系统相比,混联式混合动力系统可以更 加灵活地根据工况来调节内燃机的功率输出和电机的运转。 唯一的缺点就是价格高,结构复杂。
式结构简单,成本低。本田的Accord和Civic采用的是并联式联结方式。
引导问题2: 并联式混合动力汽车
《新能源汽车技术》教学课件 第2章 电动汽车基础

J 电流密度,单位A/mm² I 电流强度,单位安培 A 导线横截面, 单位mm²
2.1 电工基础知识
导线最大允许通过的电流:
导线横截面积 0.75mm² 1.0 mm² 1.5 mm² 2.5 mm² 4 mm²
最大允许电流 13A 16A 20A 27A 36A
2.1 电工基础知识
2.1.4 线圈
新能源又称非常规能源
2.1 电工基础知识 2.2 电动机 2.3 蓄电池 2.4 逆变器与变频器 2.5 空调与转向系统
21世纪伊始,世界 汽车工业又站在了革命的 门槛上;电动车(包括纯 电动车,混合动力汽车, 燃料电池电动车)概念的 提出,将会是未来世界汽 车工业发展的新方向。
2.1 电工基础知识
新能源汽车
主讲人:XXX 教授
第二章
电动汽车基础
新能源又称非常规能源
蒸汽机启动了18世纪第一次产业革命以后,19世纪 末到20世纪电机又引起了第二次产业革命,使人类进入 了电气化时代。20世纪下半叶的信息技术引发了第三次 产业革命,是生产和消费从工业化向自动化,智能化时 代转变;推动了新一代高性能电机驱动系统与伺服系统 的研究与发展。
2.1 电工基础知识
使用电流夹钳测量: 另外一种测量电流的 方法是使用电流钳。 如果待测电流强度> 10 A,那么用电流夹 钳测量电流的优势非 常突出。另一个优点 是测量电流强度时无 需打开电路。
2.1 电工基础知识
2.1.3电流密度
电流密度表示一个导体内电子挤压在一起时的紧密程度。电子 越多且越紧密的聚集在一起,电子撞击原子的频率就越高、强度就越 大。相撞时释放出热能。导体的温度升高。该过程可能会持续进行, 直至导体赤热或燃烧。
2. 交流电压:数值大小和极性不断变化的电压和电流称为交流电压和 交流电流。 交流电压的典型代表是家庭常用的“来自插座的电流”
7第七章 现代汽车科技 5《汽车文化 》曲金玉、任国军主编
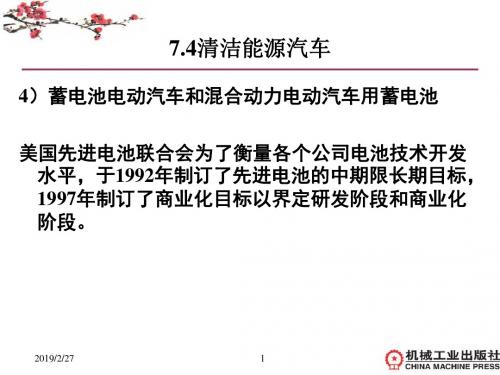
2019/2/27
10
7.4清洁能源汽车
2、电器系统 是太阳能汽车的核心,由电池和电子执行器件组 成,控制和管理整个系统所有的输入和输出。
2019/2/27
11
7.4清洁能源汽车
3、传动机构
与传统汽车不同,由电机和能把电机的电能传送到 车轮而使汽车行驶的装置组成,由于产生的功率 不到5HP,常在汽车的一个后轮上装有电动机。
陶瓷轴承,发动机涡轮增压转子等零部件具有耐 高温,耐腐蚀,高速运转离心力小,运转温升 低等优良性能。
氧化硅发动机废气涡轮增压器 陶瓷涡轮转子
2019/2/27
23
7.5汽车新材料及应用
氧化硅球轴承
2005上海国际车展展出的奔驰 陶瓷材料制动盘
2019/2/27
24
7.5汽车新材料及应用
6、复合材料 是一种多相材料,是由有机高分子,无机非金属 和金属等材料复合而成; 按机体材料类型分:
质子交换膜燃料电池内部化学反应
2019/2/27
7
7.4清洁能源汽车
三、太阳能汽车 组成部分:
驾驶控制系统; 电器系统; 传动系统; 机械系统; 车身和底盘; 太阳能电池板。
2019/2/27 8
7.4清洁能源汽车
参加比赛的太阳能汽车
2019/2/27
9
7.4清洁能源汽车
1、驾驶控制系统 转向灯,制动灯,加速器踏板,后视镜,空气流 通装置和巡航控制系统。
7.4清洁能源汽车
4)蓄电池电动汽车和混合动力电动汽车用蓄电池 美国先进电池联合会为了衡量各个公司电池技术开发 水平,于1992年制订了先进电池的中期限长期目标, 1997年制订了商业化目标以界定研发阶段和商业化 阶段。
电动及混合动力系统简介
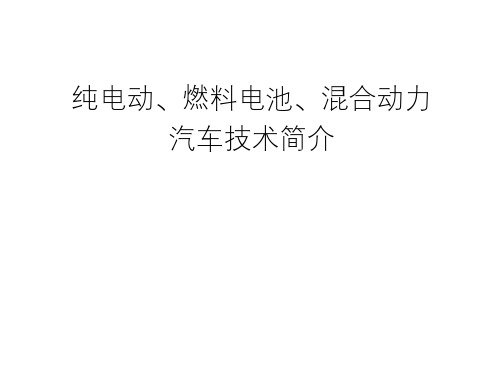
V or 36V
Starter Quick & Noiseless
ECU
Alternator Efficiency + 5-10%
丰田的 THS-M 皮带传动ISG系统
• • • 用于丰田的CROWN牌轿车 2001年8月开始在东京出租车 上试运行 引擎:
• 3升, 6缸, 24阀 • 147kW/5000rpm
ISG
Vehicle Control
Engine Control
Trans. Control
Motor Control
Battery Control
IPU
Battery
7-10kW
丰田THS混合动力系统
• 引擎:
• 1.5升, 4缸, 16阀 • 输出功率:53kW、 (4500rpm) • 最大力矩: 115Nm (4200 rpm)
NO NO
NO NO
3% 5 - 6% 8% - 12% 20%39% 35% 55% >50%
YES
(> 0.3 sec) YES
Minimal (< 3 kW) Modest (< 9 kW)
YES (-30% disp. AND Atkinson) YES
曲轴驱动ISG (42V)
(PbA/Adv. Battery)
Generator Range Extender Engine Control
Vehicle Control
Motor/Generator Control
Battery Control
Power Electronics Controller
Battery
Traction Motor
《现代电动汽车技术》课程教学大纲
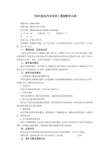
《现代电动汽车技术》课程教学大纲课程代码:0806615010课程名称:现代电动汽车技术英文名称:Modern Electric Vehicle Technology总学时:24 讲课学时:22 实验学时:2学分:1.5适用专业:车辆工程专业先修课程:机械设计基础、电工电子技术、单片机原理及应用、电力电子技术、汽车构造、汽车电子电气一、课程性质、目的和任务《现代电动汽车技术》课程是车辆工程专业(车辆电子电气方向)的专业限选课。
通过本课程教学,使学生对于现代电动汽车的基本结构及相关知识有系统的了解,为学生今后从事电动汽车设计、制造、运用及试验等打下必需的专业基础知识。
二、教学基本要求通过本课程的教学,旨在使学生了解现代电动汽车的定义及发展状况,掌握电动汽车及混合动力汽车的结构及工作原理、能量存储及再生制动的形式。
三、教学内容及要求1. 环境影响与现代交通运输的历史应对环境和石油能源问题关于交通运输工具发展策略的重要性,电动车及混合动力汽车发展的历史,燃料电池车的历史。
2. 电动汽车电动汽车的结构和性能,正常行驶下的牵引力。
3. 电驱动系统直流电动机驱动,感应电动机驱动,永磁无刷直流电动机驱动。
4. 混合动力驱动系结构和设计混合动力电驱动系统的概念和构造,串联式混合动力驱动系统、并联式混合动力驱动系统和混联式混合动力驱动系统。
5. 能量存储电化学蓄电池组的基本概念,蓄电池技术(铅酸蓄电池、镍基电池及锂电池),超级电容,超高速飞轮。
6. 再生制动的基本原理制动中的能量损耗,前后轮上的制动功率和能量,电动汽车和混合动力电动汽车的制动系统,串联制动-最佳感觉、串联制动-最佳的能量回收和并联制动。
四、实践环节现代电动汽车技术系统实验安排在现代电动汽车技术课程内,开设1个实验:课程实验:现代油电混合动力汽车结构与工况实验2学时五、课外习题及课程讨论为达到本课程的教学基本要求,课外习题(包括自测题)不应少于15题。
第7章现代汽车与未来汽车―林振琨版《汽车文化》概要
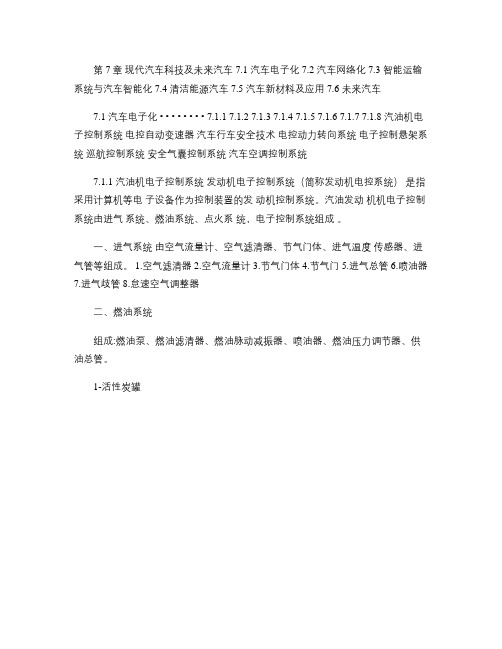
第7章现代汽车科技及未来汽车 7.1 汽车电子化 7.2 汽车网络化 7.3 智能运输系统与汽车智能化 7.4 清洁能源汽车 7.5 汽车新材料及应用 7.6 未来汽车7.1 汽车电子化• • • • • • • • 7.1.1 7.1.2 7.1.3 7.1.4 7.1.5 7.1.6 7.1.7 7.1.8 汽油机电子控制系统电控自动变速器汽车行车安全技术电控动力转向系统电子控制悬架系统巡航控制系统安全气囊控制系统汽车空调控制系统7.1.1 汽油机电子控制系统发动机电子控制系统(简称发动机电控系统)是指采用计算机等电子设备作为控制装置的发动机控制系统。
汽油发动机机电子控制系统由进气系统、燃油系统、点火系统,电子控制系统组成。
一、进气系统由空气流量计、空气滤清器、节气门体、进气温度传感器、进气管等组成。
1.空气滤清器 2.空气流量计 3.节气门体 4.节气门 5.进气总管 6.喷油器7.进气歧管 8.怠速空气调整器二、燃油系统组成:燃油泵、燃油滤清器、燃油脉动减振器、喷油器、燃油压力调节器、供油总管。
1-活性炭罐2-炭罐电磁阀3-燃油压力调节器4-燃油分配管5-喷油器6-燃油滤清器7-燃油箱8-电动汽油泵9-燃油添加口10-回油管11-供油管12-油气排放管三、点火系统组成:点火电子组件、点火线圈、火花塞、高压导线。
四、电子控制系统根据进气量和发动机转速计算出喷油器基本喷油持续时间。
然后对数据进行修正,确定喷油持续时间,控制喷油器喷油。
7.1.2 电控自动变速器一、电控液力自动变速器(EAT组成:液力变矩器行星齿轮机构液压操纵系统电子控制系统二、电控无级自动变速器1.组成:液力变矩器无级变速机构液压系统控制系统2.工作原理7.1.3 汽车行车安全技术一、电控防抱死制动系统(ABS1971年德国博世公司首次推出ABS,并从集成电路控制发展为电子控制。
ABS系统组成:1、ABS制动系统的功用1减小制动距离。
混合动力电动汽车技术概况概要
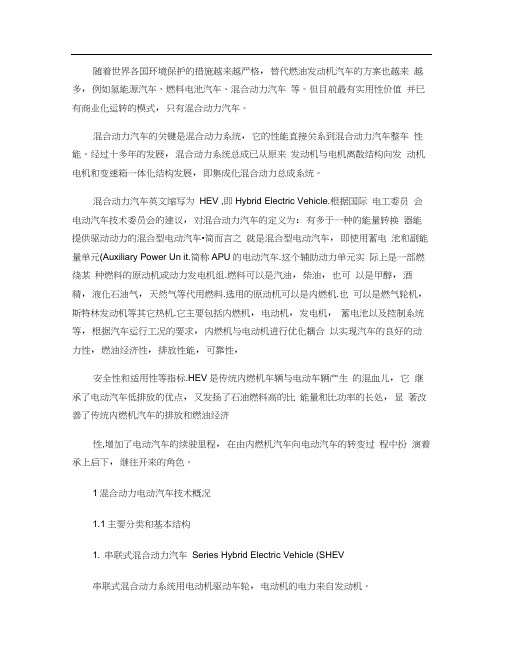
随着世界各国环境保护的措施越来越严格,替代燃油发动机汽车的方案也越来越多,例如氢能源汽车、燃料电池汽车、混合动力汽车等。
但目前最有实用性价值并巳有商业化运转的模式,只有混合动力汽车。
混合动力汽车的关键是混合动力系统,它的性能直接关系到混合动力汽车整车性能。
经过十多年的发展,混合动力系统总成已从原来发动机与电机离散结构向发动机电机和变速箱一体化结构发展,即集成化混合动力总成系统。
混合动力汽车英文缩写为HEV ,即Hybrid Electric Vehicle.根据国际电工委员会电动汽车技术委员会的建议,对混合动力汽车的定义为:有多于一种的能量转换器能提供驱动动力的混合型电动汽车•简而言之就是混合型电动汽车,即使用蓄电池和副能量单元(Auxiliary Power Un it.简称APU的电动汽车.这个辅助动力单元实际上是一部燃烧某种燃料的原动机或动力发电机组.燃料可以是汽油,柴油,也可以是甲醇,酒精,液化石油气,天然气等代用燃料.选用的原动机可以是内燃机.也可以是燃气轮机,斯特林发动机等其它热机.它主要包括内燃机,电动机,发电机,蓄电池以及控制系统等,根据汽车运行工况的要求,内燃机与电动机进行优化耦合以实现汽车的良好的动力性,燃油经济性,排放性能,可靠性,安全性和适用性等指标.HEV是传统内燃机车辆与电动车辆产生的混血儿,它继承了电动汽车低排放的优点,又发扬了石油燃料高的比能量和比功率的长处,显著改善了传统内燃机汽车的排放和燃油经济性,增加了电动汽车的续驶里程,在由内燃机汽车向电动汽车的转变过程中扮演着承上启下,继往开来的角色。
1混合动力电动汽车技术概况1.1主要分类和基本结构1. 串联式混合动力汽车Series Hybrid Electric Vehicle (SHEV串联式混合动力系统用电动机驱动车轮,电动机的电力来自发动机。
串联式混合动力系统利用发动机动力发电,从而带动电动机驱动车轮其基本结构是由电动机、发动机、发电机、HV蓄电池、变压器组成。
- 1、下载文档前请自行甄别文档内容的完整性,平台不提供额外的编辑、内容补充、找答案等附加服务。
- 2、"仅部分预览"的文档,不可在线预览部分如存在完整性等问题,可反馈申请退款(可完整预览的文档不适用该条件!)。
- 3、如文档侵犯您的权益,请联系客服反馈,我们会尽快为您处理(人工客服工作时间:9:00-18:30)。
• High efficiency: BLDC motors are the most efficient of all electric motors. This is due to the use of PMs for the excitation, which consume no power. The absence of mechanical commutator and brushes means low mechanical friction losses and therefore higher efficiency.
high operation efficiency. These prominent advantages are quite attractive for
their application in EVs and HEVs. Of the family of PM motors, the BLDC motor drive is the most promising candidate for EV and HEV applications.4
Electric Propulsion Systems
201
a
b
c Va Vb
Vc ia, i*a
ib, i*b
ic, ic*
0
1/2p
p
3/2p
2p
FIGURE 6.41 Current-controlled voltage source inverter (5% tolerance bandwidth).
• Low maintenance, great longevity, and reliability: The absence of brushes and mechanical commutators suppresses the need for associated regular maintenance and suppresses the risk of failure associated with these elements. The longevity is therefore only a function of the winding insulation, bearings, and magnet life-length.
6.3 Permanent Magnetic BLDC Motor Drives
By using high-energy PMs as the field excitation mechanism, a PM motor drive can be potentially designed with high power density, high speed, and
• Ease of control: The BLDC motor can be controlled as easily as a DC motor because the control variables are easily accessible and constant throughout the operation of the motor.
• Ease of cooling: There is no current circulation in the rotor. Therefore, the rotor of a BLDC motor does not heat up. The only heat production is on the stator, which is easier to cool than the rotor because it is static and on the periphery of the motor.
200
Modern Electric, Hybrid Electric, and Fuel Cell Vehicles
a 1–
0
Dia
–h/2
h/2
FIGURE 6.39 Input–output characteristics of a hysteresis current controller.
• Compactness: The recent introduction of high-energy density magnets (rare-earth magnets) has allowed achieving very high flux densities in the BLDC motor. This allows achieving accordingly high torques, which in turns allows making the motor small and light.
a
b
c Va
Vb
Vc ia, i*a
ib, i*b
ic, i*c
0
1/2p
p
3/2p
2p
FIGURE 6.40 Current-controlled voltage source inverter (10% tolerance bandwidth).
6.40 and 6.41, in which the switching variables, line-to-neutral voltages, and currents for an inverter supplying a resistive-plus-inductive load are at values of h = 10 and 5% of the amplitude of the reference current, respectively. In practice, the tolerance bandwidth should be set to a value that represents an optimal trade-off between the quality of the currents and the efficiency of the inverter.