汽车车身材料技术发展动态
汽车车身材料技术的创新应用与发展趋势
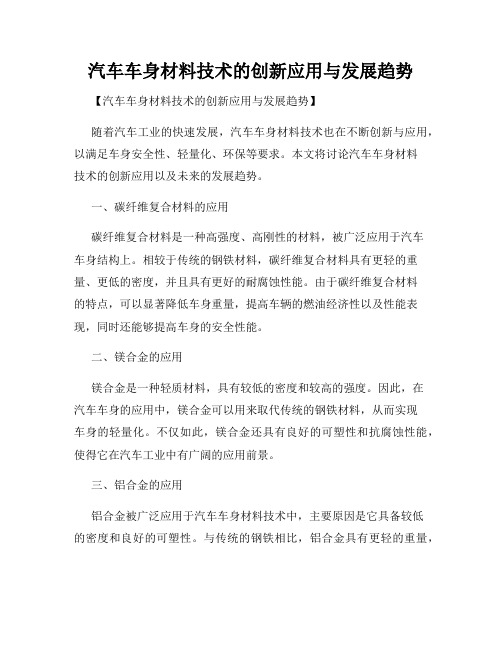
汽车车身材料技术的创新应用与发展趋势【汽车车身材料技术的创新应用与发展趋势】随着汽车工业的快速发展,汽车车身材料技术也在不断创新与应用,以满足车身安全性、轻量化、环保等要求。
本文将讨论汽车车身材料技术的创新应用以及未来的发展趋势。
一、碳纤维复合材料的应用碳纤维复合材料是一种高强度、高刚性的材料,被广泛应用于汽车车身结构上。
相较于传统的钢铁材料,碳纤维复合材料具有更轻的重量、更低的密度,并且具有更好的耐腐蚀性能。
由于碳纤维复合材料的特点,可以显著降低车身重量,提高车辆的燃油经济性以及性能表现,同时还能够提高车身的安全性能。
二、镁合金的应用镁合金是一种轻质材料,具有较低的密度和较高的强度。
因此,在汽车车身的应用中,镁合金可以用来取代传统的钢铁材料,从而实现车身的轻量化。
不仅如此,镁合金还具有良好的可塑性和抗腐蚀性能,使得它在汽车工业中有广阔的应用前景。
三、铝合金的应用铝合金被广泛应用于汽车车身材料技术中,主要原因是它具备较低的密度和良好的可塑性。
与传统的钢铁相比,铝合金具有更轻的重量,能够显著降低车辆的燃油消耗,并且大大提高汽车的操控性能。
此外,铝合金还具有良好的抗腐蚀性和可回收性,符合环保要求。
四、高强度钢的应用高强度钢是一种强度较高的钢材,可以在车身结构中替代常规钢材。
高强度钢的应用可以增加车辆的刚性,提高车身的安全性能,同时可以减轻车身重量,提高车辆整体性能。
高强度钢的不断创新和应用,为汽车车身材料技术带来了更加广阔的发展空间。
五、发展趋势未来,汽车车身材料技术的发展趋势将更加注重轻量化、高强度化、绿色环保化。
随着社会对环保和节能的要求越来越高,汽车工业将更加注重汽车车身材料的环保性能,例如使用可回收的材料和提高材料的可循环性。
此外,随着电动汽车的普及,汽车车身材料技术也将逐渐向电动汽车和新能源汽车的需求倾斜,以满足电动汽车的需求和要求。
总结起来,汽车车身材料技术的创新应用与发展趋势主要集中在碳纤维复合材料、镁合金、铝合金和高强度钢的应用上。
汽车车身材料的发展趋势

汽车车身材料的发展趋势随着科技的不断进步和人们的需求不断变化,汽车车身材料也在不断发展和改进。
从最早的钢铁车身到现在的复合材料,汽车车身材料在轻量化、安全性和环保性方面有了巨大的进步。
本文将从这几个方面探讨汽车车身材料的发展趋势。
一、轻量化是汽车车身材料的发展方向之一。
轻量化能够减少汽车的重量,降低能耗,提高燃油经济性。
传统的钢铁材料在车身上占据了很大的比例,但其密度较高,重量较大。
为了实现轻量化,汽车制造商开始探索使用新型材料,如高强度钢、铝合金和碳纤维等。
高强度钢具有优异的强度和韧性,可以减少车身重量并提高碰撞安全性。
铝合金具有较低的密度和良好的成形性能,能够有效减轻车身重量。
碳纤维是一种轻质高强度的材料,具有优异的抗拉强度和刚度,但成本较高,限制了其在大规模生产中的应用。
二、安全性是汽车车身材料发展的另一个重要方向。
汽车车身在碰撞事故中起到保护车内乘员的作用。
传统的钢铁材料在碰撞时具有较好的塑性变形能力,但也存在一定的局限性。
为了提高车身的安全性,汽车制造商开始研发新型材料和结构设计。
高强度钢具有更好的抗撞性能,能够吸收和分散碰撞能量,提高车身的刚度。
同时,汽车制造商还采用了复合材料和蜂窝结构等新技术,提高车身的强度和刚度,进一步提高了车身的安全性能。
三、环保性是汽车车身材料发展的另一个重要方向。
随着人们对环境保护意识的增强,汽车制造商开始关注汽车的环保性能。
传统的钢铁材料在生产和回收过程中会产生大量的二氧化碳和废弃物,对环境造成一定的影响。
为了减少环境污染,汽车制造商开始使用可回收和可循环利用的材料,如铝合金和碳纤维等。
铝合金具有良好的回收性能,可以减少能源和资源的消耗。
碳纤维具有较长的使用寿命和较低的环境影响,是一种环保的材料。
汽车车身材料的发展趋势主要包括轻量化、安全性和环保性。
轻量化能够减少汽车的重量,提高燃油经济性;安全性能能够保护车内乘员的安全;环保性能能够减少对环境的污染。
随着科技的不断进步和人们对汽车的需求不断变化,相信未来汽车车身材料会继续发展和改进,为人们带来更加安全、环保和高效的出行方式。
金属材料科技在汽车制造中的发展现状与未来趋势分析

金属材料科技在汽车制造中的发展现状与未来趋势分析随着汽车工业的快速发展,金属材料科技在汽车制造中扮演着至关重要的角色。
本文将探讨金属材料科技在汽车制造中的发展现状,并展望其未来的趋势。
1. 金属材料在汽车制造中的应用现状金属材料被广泛应用于汽车制造各个方面,如车身、引擎、悬挂系统和制动系统等。
目前,汽车用金属材料主要包括钢铁、铝合金和镁合金等。
钢铁作为传统汽车材料,具有良好的强度和刚性,但同时也存在重量过大的问题。
相比之下,铝合金具有较低的密度和良好的耐腐蚀性能,能够有效降低车身质量,提高燃油经济性。
镁合金则具有更低的密度和更高的强度,被认为是未来汽车材料的发展方向。
2. 金属材料科技在汽车工艺中的应用进展随着金属材料科技的发展,汽车制造工艺也在不断演进。
例如,冷成型技术的应用使得车身零部件的加工更加高效、精确。
而热成型技术则提供了更多设计自由度,使得车身结构更为复杂,从而提高了整体车身的刚性和安全性。
此外,新型的焊接技术如激光焊接和摩擦焊接等,有效地改善了焊接质量和效率。
3. 金属材料科技在汽车性能提升中的应用金属材料科技对汽车性能的提升起着至关重要的作用。
通过优化金属材料的组成和结构,可以提高车身的刚性和轻量化水平。
同时,金属材料的高温性能和耐磨性能也对汽车引擎性能的提升起着关键作用。
例如,采用镁锂合金替代传统材料制造车轮,可以降低车轮质量,提高汽车操控性和燃油经济性。
4. 金属材料科技在新能源汽车中的应用前景随着全球环保意识的日益增强,新能源汽车的发展趋势成为了行业的焦点。
金属材料科技在新能源汽车中有着广阔的应用前景。
例如,铝合金的引入可以提高电池耐腐蚀性能,降低电池重量,从而提高电动汽车的续航里程。
此外,金属材料科技还能够解决电动汽车在电池冷却和散热方面的技术难题,提高电池的寿命和安全性。
5. 未来金属材料科技的发展趋势未来,金属材料科技将继续以轻量化、高强度和高温耐久性为目标发展。
首先,新型合金的研发将使得汽车部件更加轻薄坚固。
汽车涂装的最新工艺技术及发展趋势
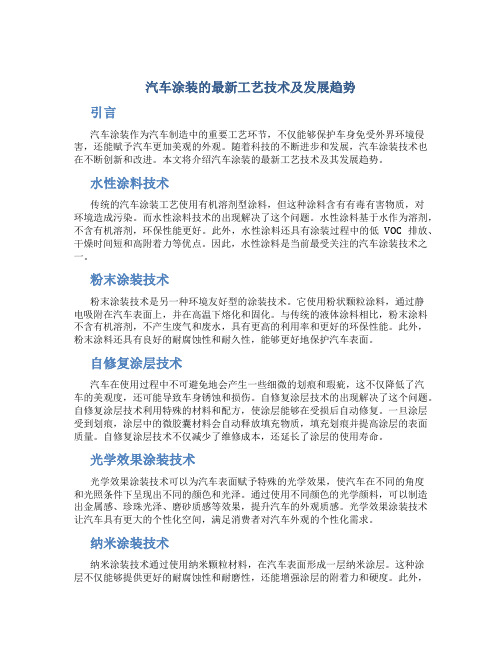
汽车涂装的最新工艺技术及发展趋势引言汽车涂装作为汽车制造中的重要工艺环节,不仅能够保护车身免受外界环境侵害,还能赋予汽车更加美观的外观。
随着科技的不断进步和发展,汽车涂装技术也在不断创新和改进。
本文将介绍汽车涂装的最新工艺技术及其发展趋势。
水性涂料技术传统的汽车涂装工艺使用有机溶剂型涂料,但这种涂料含有有毒有害物质,对环境造成污染。
而水性涂料技术的出现解决了这个问题。
水性涂料基于水作为溶剂,不含有机溶剂,环保性能更好。
此外,水性涂料还具有涂装过程中的低VOC排放、干燥时间短和高附着力等优点。
因此,水性涂料是当前最受关注的汽车涂装技术之一。
粉末涂装技术粉末涂装技术是另一种环境友好型的涂装技术。
它使用粉状颗粒涂料,通过静电吸附在汽车表面上,并在高温下熔化和固化。
与传统的液体涂料相比,粉末涂料不含有机溶剂,不产生废气和废水,具有更高的利用率和更好的环保性能。
此外,粉末涂料还具有良好的耐腐蚀性和耐久性,能够更好地保护汽车表面。
自修复涂层技术汽车在使用过程中不可避免地会产生一些细微的划痕和瑕疵,这不仅降低了汽车的美观度,还可能导致车身锈蚀和损伤。
自修复涂层技术的出现解决了这个问题。
自修复涂层技术利用特殊的材料和配方,使涂层能够在受损后自动修复。
一旦涂层受到划痕,涂层中的微胶囊材料会自动释放填充物质,填充划痕并提高涂层的表面质量。
自修复涂层技术不仅减少了维修成本,还延长了涂层的使用寿命。
光学效果涂装技术光学效果涂装技术可以为汽车表面赋予特殊的光学效果,使汽车在不同的角度和光照条件下呈现出不同的颜色和光泽。
通过使用不同颜色的光学颜料,可以制造出金属感、珍珠光泽、磨砂质感等效果,提升汽车的外观质感。
光学效果涂装技术让汽车具有更大的个性化空间,满足消费者对汽车外观的个性化需求。
纳米涂装技术纳米涂装技术通过使用纳米颗粒材料,在汽车表面形成一层纳米涂层。
这种涂层不仅能够提供更好的耐腐蚀性和耐磨性,还能增强涂层的附着力和硬度。
汽车车身制造技术发展现状及趋势分析
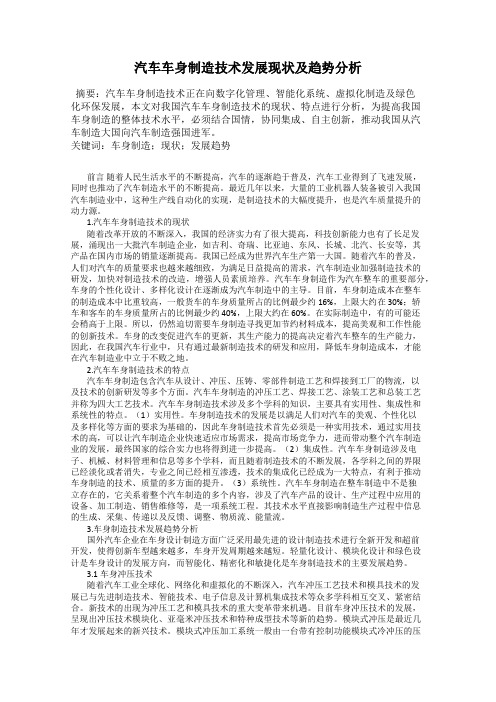
汽车车身制造技术发展现状及趋势分析摘要:汽车车身制造技术正在向数字化管理、智能化系统、虚拟化制造及绿色化环保发展,本文对我国汽车车身制造技术的现状、特点进行分析,为提高我国车身制造的整体技术水平,必须结合国情,协同集成、自主创新,推动我国从汽车制造大国向汽车制造强国进军。
关键词:车身制造;现状;发展趋势前言随着人民生活水平的不断提高,汽车的逐渐趋于普及,汽车工业得到了飞速发展,同时也推动了汽车制造水平的不断提高。
最近几年以来,大量的工业机器人装备被引入我国汽车制造业中,这种生产线自动化的实现,是制造技术的大幅度提升,也是汽车质量提升的动力源。
1.汽车车身制造技术的现状随着改革开放的不断深入,我国的经济实力有了很大提高,科技创新能力也有了长足发展,涌现出一大批汽车制造企业,如吉利、奇瑞、比亚迪、东风、长城、北汽、长安等,其产品在国内市场的销量逐渐提高。
我国已经成为世界汽车生产第一大国。
随着汽车的普及,人们对汽车的质量要求也越来越细致,为满足日益提高的需求,汽车制造业加强制造技术的研发,加快对制造技术的改造,增强人员素质培养。
汽车车身制造作为汽车整车的重要部分,车身的个性化设计、多样化设计在逐渐成为汽车制造中的主导。
目前,车身制造成本在整车的制造成本中比重较高,一般货车的车身质量所占的比例最少约16%,上限大约在 30%;轿车和客车的车身质量所占的比例最少约 40%,上限大约在 60%。
在实际制造中,有的可能还会稍高于上限。
所以,仍然迫切需要车身制造寻找更加节约材料成本,提高美观和工作性能的创新技术。
车身的改变促进汽车的更新,其生产能力的提高决定着汽车整车的生产能力,因此,在我国汽车行业中,只有通过最新制造技术的研发和应用,降低车身制造成本,才能在汽车制造业中立于不败之地。
2.汽车车身制造技术的特点汽车车身制造包含汽车从设计、冲压、压铸、零部件制造工艺和焊接到工厂的物流,以及技术的创新研发等多个方面。
2024年汽车喷漆市场发展现状

2024年汽车喷漆市场发展现状简介汽车喷漆是指在汽车制造、维修和个性化改装过程中对车身进行喷涂的工艺。
随着汽车消费需求的不断增长,汽车喷漆市场也在持续发展壮大。
本文将对当前汽车喷漆市场的发展现状进行探讨和分析。
市场规模汽车喷漆市场是汽车售后服务领域的重要组成部分,市场规模庞大。
随着全球汽车保有量的增加以及人们对汽车外观的要求提高,汽车喷漆市场呈现出稳步增长的态势。
根据市场研究机构的数据,全球汽车喷漆市场预计将以每年X%的复合增长率增长,到2025年市场规模有望达到X亿美元。
市场驱动因素1.全球汽车保有量增加:随着全球人口的增加和经济的发展,汽车保有量不断增加,带动了汽车喷漆市场的需求增长。
2.个性化改装需求增强:现代消费者对于汽车外观的个性化要求越来越高,喷漆可以为车身提供各种颜色和效果,满足消费者个性化改装需求。
3.事故修复市场需求增长:随着汽车保有量的增加,事故概率也相应增加,导致汽车喷漆市场的事故修复需求不断增长。
4.技术进步促进市场创新:随着喷漆技术的不断改进和创新,新型喷漆技术的应用为汽车喷漆市场带来了更多的机会和发展空间。
市场分析1.汽车喷漆市场主要分为原厂喷漆和非原厂喷漆两个市场。
原厂喷漆市场由汽车制造商和品牌认证修理厂主导,非原厂喷漆市场则由维修厂、个体工匠和专业喷漆店等组成。
2.高端汽车喷漆市场表现出强劲增长势头,豪华汽车品牌在车身外观设计和个性化服务方面的投入越来越大,推动了高端市场的发展。
3.环保和节能意识的提高对汽车喷漆市场带来了新的挑战。
消费者对于环保喷漆材料和工艺的需求越来越高,推动了市场向环保型喷漆材料转型发展。
4.互联网技术的发展为汽车喷漆市场带来了新的商机。
线上汽车喷漆平台的兴起为消费者提供了更多选择,也促使传统喷漆店加快数字化转型。
市场竞争格局1.全球汽车喷漆市场竞争激烈,市场份额集中在少数大型汽车制造商和喷漆品牌之间。
2.喷漆技术和材料的突破是企业保持竞争优势的重要因素,各大企业加大研发投入,不断提升技术水平和产品质量。
我国汽车材料的应用及未来发展趋势

我国汽车材料的应用及未来发展趋势随着我国经济不断发展,汽车产业也稳步增长,成为国民经济中一个重要的支柱产业。
而作为汽车制造的重要组成部分,汽车材料的应用和发展趋势备受关注。
本文将从我国汽车材料的现状及应用、未来发展趋势等方面展开阐述。
一、我国汽车材料的现状及应用1. 金属材料金属材料一直是汽车制造的主要原材料之一,包括钢铁、铝合金、镁合金等,广泛应用于汽车车身、发动机、底盘及其他部件的制造中。
高强度钢材是近年来的研究热点,具有重量轻、强度高的特点,能够满足汽车节能、环保的需求。
2. 塑料材料随着汽车轻量化的趋势,塑料材料在汽车制造中的应用也逐渐增多。
如聚丙烯、聚氨酯等塑料材料在汽车内饰、外饰、发动机罩等部件中得到广泛应用,具有重量轻、耐腐蚀、成型性好等优点。
3. 复合材料复合材料由不同性质的材料组成,具有高强度、轻质、耐磨损等特点,广泛应用于汽车的车身结构、车轮、燃油箱等部件中。
我国复合材料行业发展迅速,为汽车制造提供了更多选择。
4. 其他材料除了上述材料外,玻璃、橡胶、陶瓷等材料也在汽车制造中得到广泛应用。
汽车玻璃在安全、节能方面发挥了重要作用,橡胶密封件在汽车减震、密封等方面发挥了重要作用。
二、未来发展趋势1. 轻量化材料的应用将继续增加随着汽车节能、环保的要求日益提高,轻量化材料在汽车制造中的应用将继续增加。
在金属材料方面,高强度钢材、铝合金、镁合金等将得到更广泛的应用;在非金属材料方面,各类复合材料、塑料材料的应用也会得到进一步推广。
2. 材料多样化发展未来,汽车材料的发展趋势将是多样化的。
传统材料的改进和新材料的开发将是今后的发展方向。
具有自愈合功能的新型涂料、具有自我修复能力的新型材料等将逐渐应用于汽车制造中。
3. 绿色环保材料将受到更多关注随着绿色环保理念的日益普及,绿色环保材料将受到更多关注。
在汽车制造中,可降解材料、再生材料等将成为未来的发展趋势,符合节能减排、循环利用的要求。
汽车车身材料的现状及其发展趋势

汽车车身材料的现状及其发展趋势下载提示:该文档是本店铺精心编制而成的,希望大家下载后,能够帮助大家解决实际问题。
文档下载后可定制修改,请根据实际需要进行调整和使用,谢谢!本店铺为大家提供各种类型的实用资料,如教育随笔、日记赏析、句子摘抄、古诗大全、经典美文、话题作文、工作总结、词语解析、文案摘录、其他资料等等,想了解不同资料格式和写法,敬请关注!Download tips: This document is carefully compiled by this editor. I hope that after you download it, it can help you solve practical problems. The document can be customized and modified after downloading, please adjust and use it according to actual needs, thank you! In addition, this shop provides you with various types of practical materials, such as educational essays, diary appreciation, sentence excerpts, ancient poems, classic articles, topic composition, work summary, word parsing, copy excerpts, other materials and so on, want to know different data formats and writing methods, please pay attention!汽车车身材料的现状及其发展趋势随着汽车工业的发展,车身材料的选择对汽车性能、安全性和环境影响起着至关重要的作用。
汽车车身材料应用现状与发展趋势

汽车车身材料应用现状与发展趋势汽车车身材料是指汽车的整个车身结构所使用的材料,包括钢铁、铝合金、碳纤维等材料。
随着科技的不断发展和环保意识的加强,汽车车身材料也在不断地更新换代。
目前,在汽车车身材料的应用中,钢材占据了主要的市场份额。
对于低端车型来说,普通的碳钢材质仍然是首选的材料。
但是,对于高端车型来说,高强度钢、先进高强度钢和再结晶钢等新型材料的应用越来越广泛。
这些材料具有重量轻、刚性好、防腐耐用、热稳定性和能耗节约等优秀特性,能够有效地提升汽车的安全性能和燃油效率。
除了钢材,铝合金在汽车车身材料中也有着广泛的应用。
铝合金是一种轻质、高强度的材料,具有良好的成形性和抗腐蚀性能。
因此,在高端车型中代码降低车身重量和提升燃油经济性方面,铝合金已成为首选的材料。
但是,铝合金的复合加工难度较高,成本也相对较高,这限制了它在低端车型中的应用。
随着全球经济的快速发展,碳纤维等新材料也开始应用于汽车车身中。
碳纤维具有较高的强度和刚度,同时也非常轻盈,同等强度下,其重量只有钢的1/5。
这些优越的性能使碳纤维在汽车车身中有着广泛的应用前景。
但是,碳纤维在加工和制造方面存在着一定的难度和成本问题,因此在当前阶段的应用仍然有一定的限制。
未来,随着环保和燃油经济性要求的不断提高,汽车车身材料将会更加趋向于轻量化和复合化。
使用新型材料,同时也需要满足强度和安全性的要求,以及生产成本的限制。
综合考虑各方面因素,汽车车身材料的未来发展主要有以下几个方向:一是材料轻量化。
随着汽车制造业环保和燃油经济性的要求日益提高,汽车车身材料的轻量化成为趋势。
轻量化是提升汽车能源利用效率和行驶性能的重要途径。
二是复合材料化。
汽车车身复合材料的应用是汽车轻量化与高于要求的强度、韧性等多种性能要求之间的一个完美协调的产物。
复合材料的高强度和轻量化是实现轻量化的重要途径。
复合材料的成本虽然比普通材料高,但随着其生产规模的不断扩大,成本也将逐渐降低。
我国汽车材料的应用及未来发展趋势
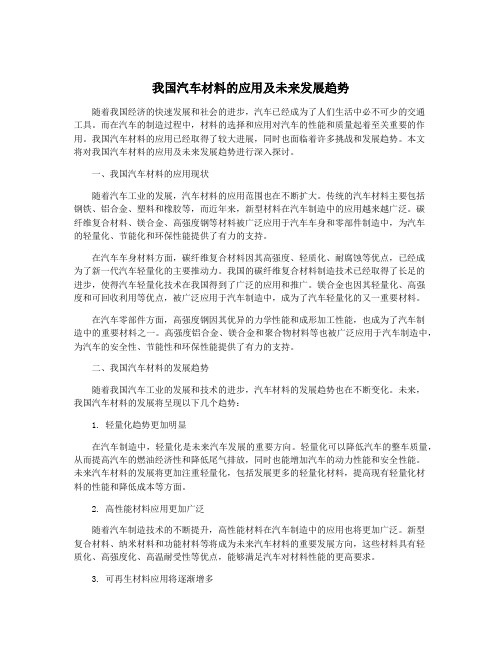
我国汽车材料的应用及未来发展趋势随着我国经济的快速发展和社会的进步,汽车已经成为了人们生活中必不可少的交通工具。
而在汽车的制造过程中,材料的选择和应用对汽车的性能和质量起着至关重要的作用。
我国汽车材料的应用已经取得了较大进展,同时也面临着许多挑战和发展趋势。
本文将对我国汽车材料的应用及未来发展趋势进行深入探讨。
一、我国汽车材料的应用现状随着汽车工业的发展,汽车材料的应用范围也在不断扩大。
传统的汽车材料主要包括钢铁、铝合金、塑料和橡胶等,而近年来,新型材料在汽车制造中的应用越来越广泛。
碳纤维复合材料、镁合金、高强度钢等材料被广泛应用于汽车车身和零部件制造中,为汽车的轻量化、节能化和环保性能提供了有力的支持。
在汽车车身材料方面,碳纤维复合材料因其高强度、轻质化、耐腐蚀等优点,已经成为了新一代汽车轻量化的主要推动力。
我国的碳纤维复合材料制造技术已经取得了长足的进步,使得汽车轻量化技术在我国得到了广泛的应用和推广。
镁合金也因其轻量化、高强度和可回收利用等优点,被广泛应用于汽车制造中,成为了汽车轻量化的又一重要材料。
在汽车零部件方面,高强度钢因其优异的力学性能和成形加工性能,也成为了汽车制造中的重要材料之一。
高强度铝合金、镁合金和聚合物材料等也被广泛应用于汽车制造中,为汽车的安全性、节能性和环保性能提供了有力的支持。
二、我国汽车材料的发展趋势随着我国汽车工业的发展和技术的进步,汽车材料的发展趋势也在不断变化。
未来,我国汽车材料的发展将呈现以下几个趋势:1. 轻量化趋势更加明显在汽车制造中,轻量化是未来汽车发展的重要方向。
轻量化可以降低汽车的整车质量,从而提高汽车的燃油经济性和降低尾气排放,同时也能增加汽车的动力性能和安全性能。
未来汽车材料的发展将更加注重轻量化,包括发展更多的轻量化材料,提高现有轻量化材料的性能和降低成本等方面。
2. 高性能材料应用更加广泛随着汽车制造技术的不断提升,高性能材料在汽车制造中的应用也将更加广泛。
我国汽车材料的应用及未来发展趋势

我国汽车材料的应用及未来发展趋势【摘要】我国汽车材料在汽车制造中扮演着至关重要的角色,不断推动着汽车产业的发展。
本文首先介绍了汽车材料的种类与应用,包括金属材料、塑料材料和复合材料等。
随后分析了我国汽车材料的发展现状,指出我国在汽车材料领域取得了不俗的成绩。
接着对未来发展趋势进行了分析,预测了新材料和环保材料在汽车制造中的应用将会更加广泛。
最后总结指出,我国汽车材料将迎来更加广阔的发展空间,未来汽车将会更加轻量化、智能化、环保。
这些趋势将助力我国汽车产业迈向更加繁荣和创新的未来。
【关键词】关键词: 汽车材料、应用、发展现状、未来趋势、新材料、环保、发展空间、轻量化、智能化。
1. 引言1.1 我国汽车材料的应用及未来发展趋势随着我国汽车产业的快速发展,汽车材料作为汽车的基础,起着至关重要的作用。
汽车材料不仅影响着汽车的品质和性能,也直接关系到汽车的安全性和环保性。
对我国汽车材料的应用及未来发展趋势进行深入分析和探讨,对汽车产业的发展具有重要意义。
在我国,汽车材料的种类与应用非常丰富。
传统的汽车材料包括钢铁、铝合金、塑料等,它们在汽车制造中发挥着各自的优势。
随着科技的进步,新材料的应用也逐渐增多,比如碳纤维、复合材料等,这些新材料具有更轻、更坚固、更耐高温等特点,被广泛运用于汽车制造中。
目前,我国汽车材料的发展现状呈现出多样化的趋势。
传统材料仍然是主流,但新材料的应用逐渐增多,市场需求也在不断扩大。
未来,我国汽车材料将迎来更加广阔的发展空间。
新材料在汽车制造中的应用将会更加深入,环保材料在汽车制造中的应用也将更加普及。
未来汽车将会更加轻量化、智能化、环保。
随着技术的不断发展和创新,我国汽车材料的应用和未来发展趋势将会更加多元化和前景广阔。
我们有理由相信,我国汽车材料行业将迎来更加美好的明天。
2. 正文2.1 汽车材料的种类与应用汽车在制造过程中需要用到各种不同种类的材料,这些材料的选择直接影响着汽车的性能、安全性和舒适性。
我国汽车材料的应用及未来发展趋势

我国汽车材料的应用及未来发展趋势
随着中国汽车市场的不断发展壮大,汽车材料的应用也日益广泛。
车身材料的选择直
接关系到汽车的性能和安全,而新材料的出现和应用更是推动着整个汽车工业不断进步。
目前我国广泛应用的汽车材料可以分为金属材料和非金属材料两大类。
金属材料方面,传统车身材料主要以钢材为主,分为普通冷轧钢、高强度钢、超高强
度钢、热轧钢等。
而近年来,汽车用铝合金也逐渐应用于汽车轻量化领域,尤其是在电动
汽车上应用更加广泛。
未来,随着智能化、环保化要求的提高,汽车材料的前景将更加广阔。
在金属材料领域,高强度钢的应用将会更加深入,新一代高强度铝合金的应用也将逐渐普及。
而在非金
属材料领域,由于碳纤维复合材料的不断发展,未来这种材料将在车身结构中得到广泛应用,能够有效实现车辆轻量化,同时也具备更好的安全性能。
综上所述,汽车材料在我国汽车工业中的应用越来越广泛,未来发展趋势也非常明朗。
汽车制造企业应该紧紧跟随国际技术发展潮流,持续升级和完善汽车材料的应用,推动整
个汽车工业的发展和进步。
汽车新材料发展现状及未来趋势分析

汽车新材料发展现状及未来趋势分析近年来,汽车工业一直在追求创新和发展。
为了满足消费者对更高质量、更环保和更经济的汽车需求,汽车制造商不断寻求新材料技术的突破。
本文将就汽车新材料的发展现状及未来趋势进行分析。
首先,我们来看一下汽车新材料的发展现状。
随着科技的不断进步,汽车新材料已经取得了相当大的突破。
其中最为突出的是轻量化材料的应用。
轻量化材料被广泛应用于汽车制造中,可以显著降低汽车重量,提高汽车燃油效率,并减少对环境的影响。
铝合金、复合材料和碳纤维等材料的使用,使得汽车的整体重量得到了减轻,从而提高了汽车的加速性能和操控性能。
除了轻量化材料,高强度材料也在汽车制造中得到了广泛应用。
高强度钢材具有优异的强度和韧性,可以提高汽车的安全性能。
另外,铝合金和碳纤维材料也具备较高的强度,可以用于汽车车身和底盘结构的制造。
这些材料的应用,不仅提高了汽车的整体刚性和抗冲击性能,还能减少碰撞时对驾乘人员的伤害。
与此同时,新能源汽车的发展也对新材料提出了更高的要求。
电动汽车需要更轻、更高效的电池,以提供可靠的能源供应。
因此,高性能电池材料的研发和应用成为了关键。
在最新的动力电池技术中,磷酸铁锂、氧化锰和钴酸锂等材料被广泛应用。
这些材料具有较高的储能密度和较低的自放电率,可以提供更长的续航里程和更快的充电速度。
除了轻量化、高强度和高能量密度材料,新材料在汽车制造中还有其他应用。
例如,自修复性材料可以通过智能化技术修复车身划痕和损伤,提高汽车的美观度和耐久性。
此外,透明陶瓷材料的应用,可以用于汽车玻璃和车灯等部位,提供更好的透视和耐磨性能。
这些新材料的应用,将进一步提高汽车的质量和性能。
接下来,让我们对汽车新材料的未来趋势进行分析。
随着科技和创新的不断推动,新材料在汽车工业中的应用前景非常广阔。
首先,材料轻量化仍是未来的主流趋势。
为了进一步提高汽车的燃油效率和减少对环境的影响,车身、底盘和发动机等部件将采用更轻、更强的新材料。
汽车车身新材料的应用及发展趋势

汽车车身新材料的应用及发展趋势现代汽车车身除满足强度和使用寿命的要求外,还应满足性能、外观、安全、价格、环保、节能等方面的需要。
在上世纪八十年代,轿车的整车质量中,钢铁占80%,铝占3%,树脂为4%。
自1978年世界爆发石油危机以来,作为轻量化材料的高强度钢板、表面处理钢板逐年上升,有色金属材料总体有所增加,其中,铝的增加明显;非金属材料也逐步增长,近年来开发的高性能工程塑料,不仅替代了普通塑料,而且品种繁多,在汽车上的应用范围广泛。
本文着重介绍国内外在新型材料应用方面的情况及发展趋势。
高强度钢板从前的高强度钢板,拉延强度虽高于低碳钢板,但延伸率只有后者的50%,故只适用于形状简单、延伸深度不大的零件。
现在的高强度钢板是在低碳钢内加入适当的微量元素,经各种处理轧制而成,其抗拉强度高达420N/mm2,是普通低碳钢板的2~3倍,深拉延性能极好,可轧制成很薄的钢板,是车身轻量化的重要材料。
到2000年,其用量已上升到50%左右。
中国奇瑞汽车公司与宝钢合作,2001年在试制样车上使用的高强度钢用量为262kg,占车身钢板用量的46%,对减重和改进车身性能起到了良好的作用。
低合金高强度钢板的品种主要有含磷冷轧钢板、烘烤硬化冷轧钢板、冷轧双相钢板和高强度1F冷轧钢板等,车身设计师可根据板制零件受力情况和形状复杂程度来选择钢板品种。
含磷高强度冷轧钢板:含磷高强度冷轧钢板主要用于轿车外板、车门、顶盖和行李箱盖升板,也可用于载货汽车驾驶室的冲压件。
主要特点为:具有较高强度,比普通冷轧钢板高15%~25%;良好的强度和塑性平衡,即随着强度的增加,伸长率和应变硬化指数下降甚微;具有良好的耐腐蚀性,比普通冷轧钢板提高20%;具有良好的点焊性能;烘烤硬化冷轧钢板:经过冲压、拉延变形及烤漆高温时效处理,屈服强度得以提高。
这种简称为BH钢板的烘烤硬化钢板既薄又有足够的强度,是车身外板轻量化设计首选材料之一;冷轧双向钢板:具有连续屈服、屈强比低和加工硬化高、兼备高强度及高塑性的特点,如经烤漆后其强度可进一步提高。
我国汽车材料的应用及未来发展趋势

我国汽车材料的应用及未来发展趋势【摘要】我国汽车材料在汽车制造中发挥着重要作用,本文主要讨论其应用及未来发展趋势。
目前,我国汽车材料主要应用于车身、发动机、底盘等方面,以提高车辆性能和安全性。
未来,新材料技术将成为发展趋势,如先进复合材料和智能材料的应用将带来更高效、轻量化的汽车制造。
推广环保材料将成为未来的趋势,以减少对环境的影响。
智能材料的发展也将改变汽车的功能和性能。
我国汽车材料产业前景广阔,技术创新对产业发展至关重要。
展望未来,我国汽车材料产业将迎来更多机遇和挑战,应用前景广阔,势必推动汽车产业迈向更高水平发展。
【关键词】关键词:汽车材料、应用、未来发展、新材料、环保、智能、产业前景、技术创新。
1. 引言1.1 我国汽车材料的重要性我国汽车材料在汽车制造过程中扮演着至关重要的角色。
汽车材料直接影响着汽车的性能、安全性和环保性,对汽车整体品质起着决定性作用。
随着汽车行业的不断发展壮大,对汽车材料的需求也愈发增长。
我国作为世界上最大的汽车市场之一,对于汽车材料的需求更是巨大。
汽车材料的选择直接影响着汽车的轻量化、节能化和智能化发展。
随着汽车工业向着智能化和环保化方向发展,对汽车材料提出了更高的要求。
传统的钢铁、铝合金等材料已经不能满足未来汽车发展的需要,因此新型材料的研发和应用显得尤为重要。
在建设资源节约型和环境友好型社会的大背景下,我国汽车材料的选择不仅要考虑其性能和成本,更要考虑其环保性和可持续性。
发展绿色环保材料,如碳纤维复合材料、生物基材料等,已经成为汽车制造业的发展趋势。
我国汽车材料的研究和应用具有重要的意义,不仅关乎汽车制造业的发展水平,更关乎整个国家汽车产业的竞争力和可持续发展能力。
只有不断推动汽车材料技术的创新和应用,我国汽车产业才能立于世界之林,赢得更大的市场份额和声誉。
1.2 本文内容概述本文将围绕我国汽车材料的应用及未来发展趋势展开深入探讨。
我们将介绍汽车材料在当前的应用现状,包括传统材料如钢铁、铝合金以及高强度材料等在汽车制造中的广泛应用情况。
汽车机械制造中的车身设计与制造技术进展

汽车机械制造中的车身设计与制造技术进展随着汽车行业的快速发展,车身设计与制造技术也迎来了巨大的进步。
在汽车制造的各个环节中,车身的设计和制造是至关重要的一环,它直接决定了汽车的外观、安全性以及乘坐舒适度。
本文将介绍汽车机械制造中的车身设计与制造技术的最新进展。
一、车身设计技术进展1. 材料选择的创新传统汽车车身的主要材料是钢铁,但是随着轻量化的需求日益增加,新型材料的应用成为设计的重点。
目前,铝合金、碳纤维及复合材料等轻量化材料被广泛应用于车身设计中,以降低车身重量,提升燃油效率和安全性能。
2. 结构设计的优化为了提高车身的刚度和强度,减少车辆在碰撞时的变形和损坏,结构设计的优化变得尤为重要。
使用先进的模拟分析软件,工程师可以模拟车身在不同条件下的应力和变形情况,以便进行设计调整和优化。
3. 流线型设计的应用流线型设计可以降低汽车的阻力,提高燃油效率,并增加行驶的稳定性。
随着气动学的发展,越来越多的汽车采用了流线型外观设计,使得车辆在高速行驶时减少了空气阻力,提高了整车的性能和操控稳定性。
二、车身制造技术进展1. 激光焊接技术相较于传统的点焊和穿孔焊接技术,激光焊接技术具有更高的焊接质量和效率。
激光焊接可以实现对车身零部件的精密焊接,减少焊接变形,提高焊缝的强度和密封性。
2. 3D打印技术3D打印技术在汽车车身制造领域的应用日益广泛。
利用3D打印技术可以快速制造出复杂形状的车身零部件,减少制造过程中的浪费和成本,并且提供更加灵活的设计和制造选择。
3. 自动化生产线随着机器人技术和自动化控制技术的发展,汽车车身制造过程中的各个环节都趋向于全自动化。
自动化生产线可以实现对车身零部件的高精度加工和组装,提高生产效率和质量稳定性。
三、未来展望随着科技的不断进步,汽车机械制造中的车身设计与制造技术将迎来更加广阔的发展前景。
未来,随着电动汽车、智能汽车等新型汽车的快速普及,对车身设计和制造技术的要求也将进一步提升。
汽车车身焊接的新技术和发展趋势

汽车车身焊接的新技术和发展趋势1.激光焊接技术激光焊接技术是一种高能量密度焊接工艺,通过激光束瞬间加热焊缝,实现焊接。
相比传统焊接技术,激光焊接具有焊缝小、热影响区小、变形小、焊缝牢固等优点。
而且,激光焊接还可以实现复杂形状焊接、异种材料焊接等特殊需求。
因此,激光焊接技术在汽车车身焊接中得到了广泛应用。
2.点焊技术点焊是汽车车身焊接的主要方式之一,它通过在焊缝两侧的金属片上加热电流,使其升温,然后施加一定压力,使金属片瞬间熔化并形成焊点。
传统的点焊技术存在焊接质量不稳定、焊点强度不高等问题。
为了解决这些问题,近年来研发出了先进的点焊技术,如双电源点焊、脉冲点焊、调节点焊等。
这些新技术通过优化电流和时间参数,提高了焊接质量和焊点强度,进一步提高了汽车车身的结构强度。
3.气囊焊接技术气囊焊接技术是一种新兴的焊接技术,它利用高压气体来产生冲击波,使焊接接头在瞬间产生高温和高压,从而实现焊接。
相比传统焊接技术,气囊焊接具有焊接速度快、焊接质量高、变形小等优点。
而且,气囊焊接技术可以用于焊接复杂形状的汽车车身零部件,提高了焊接效率和质量。
4.自动化和智能化随着工业4.0的发展和智能制造的兴起,汽车制造业也在向自动化和智能化方向发展。
在汽车车身焊接中,自动化和智能化技术可以大大提高生产效率和产品质量。
例如,焊接机器人可以代替人工完成复杂的焊接操作,提高焊接效率和一致性。
而且,通过集成传感器和智能控制系统,可以实现焊接参数的实时监测和调整,提高焊接质量和稳定性。
综上所述,激光焊接、点焊技术、气囊焊接技术以及自动化和智能化技术是汽车车身焊接的新技术和发展趋势。
随着科技的不断进步,这些新技术将进一步改善汽车车身焊接质量和效率,推动汽车工业的发展。
汽车车身轻量化技术发展趋势

-车身结构培训模块五❝1、为什么要轻量化❝2、世界各大研究机构的轻量化项目❝3、轻量化技术方案❝4、轻量化三步走❝1、为什么要轻量化❝2、世界各大研究机构的轻量化项目❝3、轻量化技术方案❝4、轻量化三步走☐欧洲居于全球油耗目标之首,且2025年2.9L 的目标必须大量采用新能源汽车才能实现☐四阶段中国油耗法规相较上一阶段下降30%,而2025年目标进一步收紧20%,直指 4.0L/100km 4.1 2.9 5.0 5.62 4.50 2.03.04.05.06.07.020152016201720182019202020212022202320242025EU China US L /100k m (N o r m a l i z e d t o N E D C T e s t C y c l e ) 4.0全球油耗法规日益严苛汽车对能耗和排放还有潜力吗Hybird和EV是趋势整车轻量化趋势白车身大约占到整车重量的20%~25%而各大主机厂都已经充分做好轻量化的技术储备,蓄势待发 未来的5~15年的技术更新速度将大大加快❝1、为什么要轻量化❝2、世界各大研究机构的轻量化项目❝3、轻量化技术方案❝4、轻量化三步走❝1、为什么要轻量化❝2、世界各大研究机构的轻量化项目❝3、轻量化技术方案❝4、轻量化三步走虚拟CAE仿真优化通过拓扑等手段发现高效传力路经,减轻重量研究断面特性,位置等对结构性能的影响,优化料厚,实现轻量化 优化计算方法,缩短计算时间,提高精度车身用材料展望新一代超高强度钢板的使用 第三代超高强钢的推进使用抗拉强度1500Mpa, 1700Mpa 的马氏体钢薄板冲压的逐步使用液压成型技术的应用无焊点的整体连接结构形式,大大提高零件的整体刚度以及碰撞吸能效果 变截面,可弯曲的液压成型技术可满足结构设计的多种用途激光拼焊管技术的使用焊缝整体连接结构形式,大大提高零件的整体刚度以及碰撞吸能效果 领先的成型技术代替拉延可以提高碰撞区零件的材料等级铝合金的机械特性密度仅为钢的1/3,但是弹性模量也只有钢的1/3,可通过其特有的成型方式来用几何弥补其刚度方面的先天不足未来的铝板强度会不段提高,6XXX系列的屈服已接近CR340的水平,而7XXX已经可以通过T7的热处理达到DP钢的强度水平铝板冲压工艺的应用技术相对成熟,主要用于门盖,翼子板等大型覆盖件未来的铝板强度会不段提高,供应商需要应对其低延展率以及高回弹的特点,向深拉伸零件挑战铝挤出工艺的应用截面形式相对冲压来说十分多变在实现轻量化的同时有效的提高车身的的刚度,或者碰撞吸能效果真空高压铸造工艺的应用 能实现高刚度可变厚度的零件设计要求零件集成度提高,大大减少零件的数量工艺复杂,并且产品的质量控制难度较高碳纤维技术的应用 碳纤维具有低密度,高弹性模量,高强度的特点大规模使用受限于目前行业制造能力以及其成本激光焊接技术的应用 具有单面可达的特点,充分拓宽了工程应用的范围缩短焊接边长度,实现减重的同时可达到更好的顾客感知效果铝-铝焊接技术的应用AL-AL点焊技术AL-AL点焊技术可以应用到冲压件,挤出件和铸造件的相互连接中当铝板和铸件焊接的时候,需要铝板为6000系列铝材铝件电阻点焊技术大大降低铝制车身的制造成本AL-AL弧焊技术制造成本取决于焊接长度,可以作为高强度要求的单面可达区域使用 可以作为超厚板连接的工艺手段SPR铆接技术的应用SPR可以满足于铝-铝,铝-钢,钢-钢, 塑料-金属等两层和三层板连接需求目前技术能达到的最高强度板连接是DP800→DP600,由于混合式材料车身将在未来的一段时间内长期存在,所以超高强钢,甚至是PHS的SPR连接技术是目前需要攻克的难题FDS紧固技术的应用FDS仅需要单面可达,并且相对于电弧焊来说没有热变形的影响,因此可以很好的解决封闭截面结构(如Extrusion RKR, Hydro-form Rail)的连接需求其连接方式类似于螺栓连接,因此可以广泛应用于铝-钢,铝-铝,钢-钢的连接应用中Cycle Time的长短取决于连接板材的强度以及厚度,一般在3~7s之间,因此其制造成本较高❝1、为什么要轻量化❝2、世界各大研究机构的轻量化项目❝3、轻量化技术方案❝4、轻量化三步走充分挖掘钢制车身的剩余价值 设计高效的白车身结构,提高Load Path上的结构效率大比例提高高强钢,超高强钢,热成型零件的使用比例结合新型钢材的特性改良,充分利用其机械性能上的潜力克服超薄板的成型焊接等问题,扩大其使用范围TWB,TRB技术的进一步开拓,合理分配质量配合结构胶,烧焊,激光焊接等技术的大规模使用,提高连接效率 适当考虑液压成型等技术的使用推进轻质在结构件上的使用 拓展5XXX, 6XXX系列的铝板在覆盖件以及深拉伸件上的范围真空高压铸造零件技术在车身结构设计上的技术储备标准化AL-AL焊接方面的技术规范SPR,FDS等新型连接技术的经验积累玻纤增强材料在非碰撞吸能区域的大量推进碳纤维材料在结构件设计上的技术储备混合式材料车身将是未来方向Thanks。
- 1、下载文档前请自行甄别文档内容的完整性,平台不提供额外的编辑、内容补充、找答案等附加服务。
- 2、"仅部分预览"的文档,不可在线预览部分如存在完整性等问题,可反馈申请退款(可完整预览的文档不适用该条件!)。
- 3、如文档侵犯您的权益,请联系客服反馈,我们会尽快为您处理(人工客服工作时间:9:00-18:30)。
32
铝合金板材在汽车车身上的应用
汽车车身约占汽车总重的30%,而在汽车内外板上用铝合金 来代替传统钢板就可使白车身减重约40%-50%,进而使整 车减重10%左右
(ULSA) 世界各大铝业公司结成了汽车铝材联盟 (Auto Aluminum Alliance)
中国汽车轻量化产业技术联盟
工作任务
典型车型轻量化技术
轻量化材料的共性技术研究
汽车轻量化材料的开发和研究
轻量化联盟的主要成员单位
中国汽车工程学会、一汽、东风、吉利、奇瑞、长安、
重庆汽车研究院、吉林大学、哈工大、宝钢、西南铝业、
Bent rollformed profiles
Thick material
钢板连续柔性轧制技术(Flexible Rolling) TRB(Tailor Rolled Blanks) 慕贝儿 (全球唯一) 7万吨/年 2001年投产TRB 2003年TRP
在车身、底盘中的应用实例
(5). 成本是新材料推广应用的重要因素
8 7
7 6 5
150 120 90 60
1995 2000 2005
140 120
6 5 4 4 3 3
Euro 3
0.50
0.25
D G
Euro 4
Euro 5
2010
YEAR 1995 2000
?
2005 2010 2015
Year
车重减少100Kg,每升油多行驶1km
40
10/15 Mode Fuel Efficiency (km/l)
北美轿车高强度钢应用的增长趋势
商用车驾驶室与车箱(厢)轻量化技术动向
发展方向
高强度钢 塑料
高强度钢 塑料
自卸车、厢式车、 挂车车箱,高档客 车车身,罐装车油 罐、气罐等
全铝结构
轻合金
23
(8) . 行业、企业、高校、院所联盟是推动 汽车材料技术进步的有效组织形式
美国的新一代汽车合作项目(PNGV)
用于座椅骨架可以显著减重,降幅可达50%成本可降低10— 20%
Nissan Murano PP-GM40+GMTexTM :10.5 kg
Audi PP-GM40:3.8 kg (2/3), 2.8 kg (1/3)
长玻璃纤维增强聚丙烯(LGF-PP) STAMAX公司最近开发了一种高弹性模量复合材料LGFPP,玻璃纤维的长度为12-25毫米 LGF-PP可取代现有的材料,用于仪表板托架、保险杠梁、 防溅板、车门等零件 图为用LGF-PP制造的福特Fiesta后车门,同钢车门相比, 其重量减少了50%
亨利· 福特Model T 型汽车 福特Prodigy、Jaguar new XJ 法拉利360等赛车 DaimlerChrysler Prowler 大众 3L Lupo、奥迪A2、A8 本田混合动力轿车 Insight、
NSX
均采用铝制车身
铝合金车顶盖和发动机罩盖
汽车后门盖内板
莲花汽车公司建立了名为“通用汽车构造”的铝平 台 用于其中小批量(5万台左右)的SUV、MPV和运 动车的开发 底盘由压铸铝合金铸件、铝冲压件和型材构成, 车身板也是铝件 铝零件之间采用了自铆和先进的粘结工艺进行连接 莲花汽车公司的铝合金底盘
汽车车身材料技术发展动态
东风汽车公司
敖炳秋 2009.10
一. 汽车车身材料技术发展动态 与趋势 二. 轻量化车身材料技术的应用
(1). 节能、环保、安全是促进 车身材料 技术进步 的主动力
CAFE standards in terms CO2 emissions (ACEA)
CO2 ( g/km )
成本与重量的关系
(6). 轻量化材料技术的内涵不断深化
高强度钢 铝合金
轻量化新材料开发 汽 车 轻 量 化 新 材 料 开 发 与 应 用
镁合金 塑料 复合材料 材料评价方法
新材料应用支撑技术
性能数据库 零件设计指南
成形技术
零件制造技术
连接技术
表面处理技术
-----
回收再生技术
(7). 钢板仍将保持相对稳定的主导地位 高强度钢用量将有较大的增长
东风驾驶室钢板材料技术应用
驾驶室共有冲压件 539种 约有160余件采用 高强度钢 冷轧板﹥340MPa 热轧板﹥510MPa 用量约86㎏
?
Magnesium Alloy:
AM30、AZ31、AM50
Aluminium Alloy: 5754、6063
High strength Steel:
HSLA350、DP600
Significant Vehicle Mass Saving
(2). 轻量化是车身材料技术的发展方向
高强度钢 铝合金 镁合金 工程塑料 非金属基 复合材料
典型轿车的重量构成
若车1质量比车2质量分别小10%、20% 车1死亡人数将分别高于车2 的45.8%和122% 轻量化会使车辆的安全性能大大下降
Energy Absorption Anti-Intrusion
镁质车体前端结构研究与开发进展 加拿大-中国-美国合作项目
研究进展(防撞性)
Safety
减重幅度通常可达50~65%
欧盟最近采用树脂传递模塑成型(RTM)工艺成功地试制出某轿车碳纤维底板 零件的数量由28个减少到8个,重量较钢约减轻50%,而白车身的性能达到 了原钢车身水平材料 美国除低成本碳纤维制备技术开发外,还在进行碳纤维增强树脂的开发,探 索碳纤维增强塑料零部件的大规模制造工艺
LGF-PP制造的 福特Fiesta后车门
长玻纤材料用于高度集成的前端系统 福特 Fusion 车型-集成了超过10个传统金属部 于一个塑料部件
把多个金属零部件的功能集成 在同一塑料零件上,如前端模块 支架 减轻重量40% 降低制造成本
欧洲和美国 SMC 汽车部件用量最多 应用领域包括悬架零件、车身及车身部件、发动 机盖下部件、车内装饰部件等 尤以保险杠、车顶、发动机罩、发动机隔音板、 前后翼子板等部件用量最大
奔驰驾驶室
MAN驾驶室
结构泡沫实际上是一种泡沫材料 聚氨酯、环氧树脂和尼龙/玻璃纤维复合材料 作为加强内衬用于轿车前端、摆梁(Rocker)、后侧骨架 和保险杠,A型柱-铰链柱结合部、车顶纵梁-B型柱结合 部等关键部位 结构泡沫能吸收更多的冲击能量
碳纤维增强聚合物基复合材料。适于制造车身和底盘零部件
(3). 多材料轻量化结构设计 的选材理念将得到进一步发展
多材料组合的轻量化结构(Lightweight construction by multi –material ) 合适的材料用于合适的部位(The right material in the right place ) 寻求轻量化效果、工艺性、性能、安全性、成本的总体上 最优化 多材料的理念能较好地兼顾各方面的要求,因而受到了广 泛的关注 欧洲正在应用于超轻混合汽车(Hybrid vehicle concepts)和多材料的最优化车辆(Multi-attribute vehicle optimisation)
一汽热冲压成型轻量化制造技术研究
高强度钢板防撞梁等零件成形工艺研究 与大连理工大学合作在长春建生产线 现为一汽大众试制部件,逐渐为一汽集团配套生产
一汽 滚压成型技术应用研究
车门窗框、前后保险杠骨架采用了滚压成型技术; 高强度钢板纵梁的成形试验研究; 北方工业大学试制一种柔性滚压设备,生产变截面零 件;正协商一种零件的柔性滚压技术,已发去数模。
高强度钢应用研究:
双相钢980Y原从日本进口,现与宝钢合作试制;将在一车型中研究 成形性及回弹补偿工艺
完成TRIP钢与HSLA钢点焊工艺研究
进行门防撞梁(强度1200MPa)冷成形工艺研究
一汽卡车大量采用抗拉强度340MPa级烘烤硬化
钢板、含磷钢板代替普通强度钢板生产CA1092
车身及驾驶室零件,使零件厚度减薄
210 180
ACEA AVERAGE
NOX, HC, CO & PM emissions
1.00
Liters / 100 km
GASOLINE DIESEL
9
ACEA – UE COMMITTEE AGREEMENT
8
NOx & PMx10 (g/Km)
Euro 2
0.75
Emission Standards
白车身高强度钢应用示意图
采用激光拼焊新工艺: 减重1.66 Kg;设计已完成,正在进行模具开发
左/右中柱加强板
厚度1.8mm 厚度1.2mm
左/右门槛加强板
厚度1.6mm 厚度1.2mm
此部位减薄0.6 重量减少1.04Kg
此部位减薄0.4 重量减少0.62Kg
NL-1前横梁总成采用GMT减重2.86kg
车身结构材料的发展趋势
全钢、全铝、全镁及多种材料的车身骨架技术
现已发展到能够进行工业化批量生产的程度
12
(4).与轻量化材料技术相关的新制造技术不断涌现
hot forming process Hydro formed profiles
Tailored Blank
Thin material
Thin material
欧盟超轻车身联合研发项目(ER Collaborative R&D Project SuperLIGHT-CAR) 美国汽车材料合作项目U.S. Automotive Materials Partnership (USAMP) 新型钢车身项目New Steel Body(NBS)