FMEA的国内外研究现状
fmea在国内的应用

FMEA在国内的应用现状学号:姓名:关键词:FMEA 故障分析国内应用现状摘要潜在失效模式与后果分析(Failure Mode and Effects Analysis,FMEA),是在产品/过程/服务等的策划设计阶段,对构成产品的各子系统、零部件,对构成过程,服务的各个程序逐一进行分析,找出潜在的失效模式,分析其可能的后果,评估其风险,从而预先采取措施,减少失效模式的严重程序,降低其可能发生的概率,以有效地提高质量与可靠性,确保顾客满意的系统化活动。
FMEA是一种防患于未然的可靠性管理技术,是生产过程中一项事前预防的分析手段。
从过去的相关文献,我们可以知道FMEA己经成功地应用在军用航空领域、一般工业的产品制造和生产过程设计等领域。
本文结合各种资料,简单谈一下FMEA的发展,着重讲述FMEA在中国国内的发展及应用。
FMEA应用发展简史50年代初,美国第一次将FMEA思想用于一种战斗机操作系统的设计分析;60年代中期,FMEA技术正式用于航天工业(Apollo计划);1976年,美国国防部颁布了FMEA的军用标准,但仅限于设计方面。
70年代末,FMEA技术开始进入汽车工业和医疗设备工业。
80年代初,进入微电子工业。
80年代中期,汽车工业开始应用过程FMEA确认其制造过程。
1988年,美国联邦航空局发布咨询通报要求所有航空系统的设计及分析都必须使用FMEA。
1991年,ISO-9000推荐使用FMEA提高产品和过程的设计。
1994年,FMEA又成为QS-9000的认证要求。
《潜在失效模式与后果分析:FMEA》第四版已由AIAG发布,并于2008年11月开始生效。
这是目前最新的FMEA版本。
FMEA的功用:现今的产品设计开发不仅要求品质功能要达到客户要求,也要求开发时程要缩短。
两者看似鱼与熊掌,其实若妥善使用潜在失效模式及后果分析FMEA方法,即可兼得。
FMEA 能能使多功能小组很快总结出所有有关品质、功能、成本的失效模式,并达成共识,从而为下一步改善提供指导。
失效模式和效果分析(FMEA)在制药行业的应用
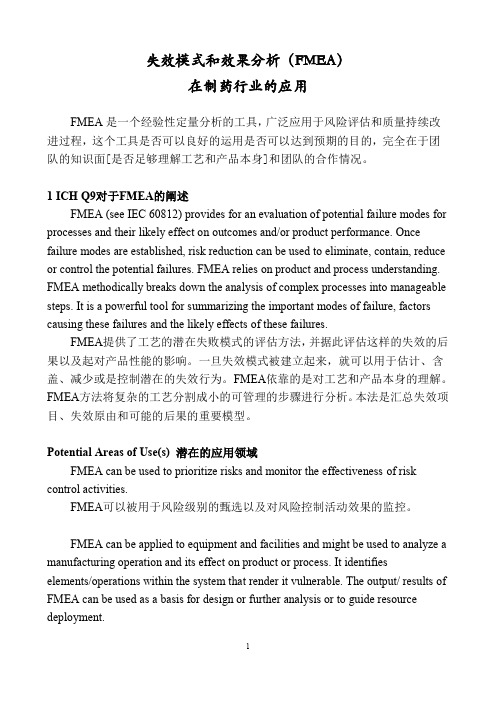
失效模式和效果分析(FMEA)在制药行业的应用FMEA是一个经验性定量分析的工具,广泛应用于风险评估和质量持续改进过程,这个工具是否可以良好的运用是否可以达到预期的目的,完全在于团队的知识面[是否足够理解工艺和产品本身]和团队的合作情况。
1 ICH Q9对于FMEA的阐述FMEA (see IEC 60812) provides for an evaluation of potential failure modes for processes and their likely effect on outcomes and/or product performance. Once failure modes are established, risk reduction can be used to eliminate, contain, reduce or control the potential failures. FMEA relies on product and process understanding. FMEA methodically breaks down the analysis of complex processes into manageable steps. It is a powerful tool for summarizing the important modes of failure, factors causing these failures and the likely effects of these failures.FMEA提供了工艺的潜在失败模式的评估方法,并据此评估这样的失效的后果以及起对产品性能的影响。
一旦失效模式被建立起来,就可以用于估计、含盖、减少或是控制潜在的失效行为。
FMEA依靠的是对工艺和产品本身的理解。
FMEA方法将复杂的工艺分割成小的可管理的步骤进行分析。
医疗失效模式与效应分析在医院安全用药管理中的应用进展

医疗失效模式与效应分析在医院安全用药管理中的应用进展陈富超;方宝霞;李鹏;林洁;吴进;马光银【摘要】失效模式与效应分析(Failure mode and effect analysis,FMEA)在医院安全用药管理中应用广泛,本文查阅近期国内相关文献,对其应用现状进行分析总结,结果表明,FMEA能提升医院安全用药管理质量,提高患者用药的有效性和安全性.同时,药学部门应充分借鉴国内外学者应用FMEA的成功经验,开展安全用药管理研究,以保障患者的用药安全.【期刊名称】《实用药物与临床》【年(卷),期】2014(017)008【总页数】3页(P1073-1075)【关键词】医疗失效模式与效应分析;药品安全;管理【作者】陈富超;方宝霞;李鹏;林洁;吴进;马光银【作者单位】湖北医药学院附属东风医院药学部,湖北十堰 442008;湖北医药学院附属东风医院药学部,湖北十堰 442008;湖北医药学院附属东风医院药学部,湖北十堰 442008;湖北医药学院附属东风医院药学部,湖北十堰 442008;湖北医药学院附属东风医院药学部,湖北十堰 442008;湖北医药学院附属东风医院药学部,湖北十堰442008【正文语种】中文0 引言加强医院管理,保障医疗安全是医院管理工作的重中之重。
医院管理及发展与医院药品安全管理水平紧密联系,药品安全管理水平也是表现医院医疗水平的重要元素[1]。
医疗失效模式与效应分析(HFMEA)为前瞻性评估系统流程的方法,它作为一种质量管理模式,目前已广泛的应用于护理、临床输血、手术、检验、安全用药等风险管理中[2-5]。
本文主要就其在医院安全用药管理中的应用现状进行总结,分析其存在的问题,希望引起国内医药管理者对HFMEA的重视,并能够应用此方法进行用药安全管理,从而保障患者的用药安全。
1 FMEA简介FMEA起源于20 世纪60 年代中期美国的航天工业公司,是一种系统性、前瞻性的系统分析方法,旨在通过分析系统中有可能产生的故障模式,提出可以或可能采取的预防改进措施,以减少缺陷,提高质量的技术过程[2]。
FMEA

4.评分标准
表4 不易探测度评判标准 (D)
分值
等级
事件描述
10~9 8~7 6~5
非常可能 失败原因几乎无法发现
很可能
失败发生后,一段时间内(后出院)可以 发现
有可能 失败发生后,最终执行者检查时可以发现
4~2 1
不太可能 失败发生后,至下一工作者可发现 罕见 失败发生后,当事者可及时发现
4.评分标准
火灾
理火警与毒泄 住
4.评分标准
分值 1
2~4 5~6 7~8
9~10
表3 发生频率(O)评判标准
等级 罕见 偶尔 不常 经常
发生概率 1/10 000 1/5000
1/200 1/100
描述 6~30年内曾经发生过 3~5年内曾经发生过 1~2年内发生若干次
1年内发生若干次
很经常
1/20
1年内发生超过10次
4
污染或怀疑污染无菌端口采取补救措施 不及时
506.2
5
预防腹膜感染措施不当
各人员预防腹膜感染意识薄弱
493.26
6
未进行术前备皮或皮肤清洁不到位
护士责任心不强
436.06
7
未培训或培训不到位
医护人员培训不到位
433.24
8
未评估或评估不足
营养状况差
386.55
9
操作环境不合格 合计
术后未更换干净被褥 4913.35
员工影响
工作人员致死 或3人以上住 院
工作人员1~2 人住院或3人 以上暂无法工 作
工作人员1或 2人需治疗
未影响工作 人员工作
设备设施 影响
损害超过25万 美元
损害超过10万 美元
化工工艺安全设计中的危险识别和控制研究

化工工艺安全设计中的危险识别和控制研究随着化工产业的不断发展,化工企业在生产过程中面临着各种安全隐患和风险,化工工艺安全设计成为保障化工生产安全的重要环节。
在化工工艺安全设计中,危险识别和控制是至关重要的环节,只有充分了解可能存在的危险因素,采取相应的措施加以控制,才能有效预防和减少事故的发生。
对化工工艺安全中的危险识别和控制进行深入研究,对提升化工生产安全水平具有重要意义。
一、危险识别危险识别是化工工艺安全设计的第一步,其目的是确定潜在的危险因素,为后续的危险控制提供依据。
在化工工艺中,可能存在的危险因素包括物理性的、化学性的、生物性的以及机械性的危险。
对于化工工艺中可能存在的危险因素,可以从以下几个方面进行识别:1. 工艺流程中的危险物质:化工生产中使用的化学品和原料可能具有毒性、腐蚀性、易燃易爆等特性,对其进行全面的分析和评估,确定其潜在危险性。
2. 高压设备和高温设备:化工生产中常常涉及到高压和高温的工艺装置和设备,对这些设备进行全面评估,确定其潜在的危险因素。
3. 工艺操作人员的安全:工艺操作人员在生产过程中可能受到化学品的直接接触、高温、高压等多种危险因素的影响,必须对其安全进行充分考虑。
4. 环境因素:化工生产过程中可能对环境造成污染,对环境风险进行全面评估。
在对这些潜在危险因素进行识别的过程中,可以采用HAZOP(危害与操作程序分析)、FMEA(故障模式与效应分析)等分析方法,进行全面细致的危险识别工作。
二、危险控制危险控制是在危险识别的基础上,采取相应的措施对危险因素进行控制,从而减少事故的发生概率和减轻事故的后果。
在化工工艺安全设计中,危险控制可以采取以下几种方式:1. 工艺改进:通过工艺改进,减少危险物质的使用量,降低生产过程中的危险因素。
2. 设备改进:对高压设备、高温设备进行改进,增加设备的安全性能,降低事故的发生概率。
3. 采用集中控制系统:通过采用自动化集中控制系统,降低人为操作的风险,提高生产过程的安全性。
FMEA和FTA分析
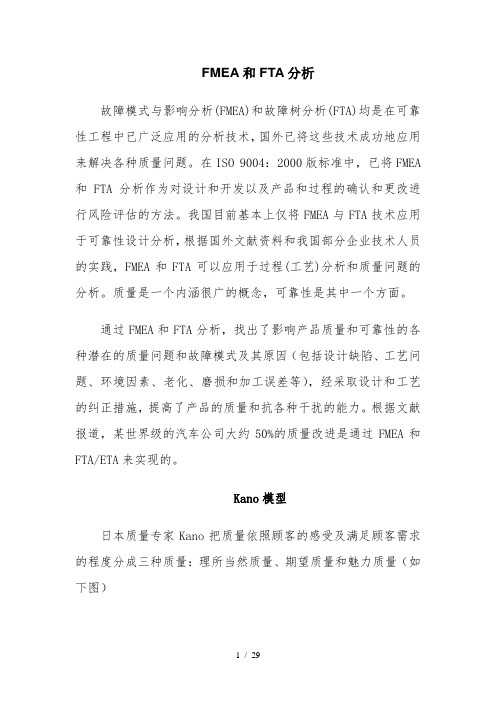
FMEA和FTA分析故障模式与影响分析(FMEA)和故障树分析(FTA)均是在可靠性工程中已广泛应用的分析技术,国外已将这些技术成功地应用来解决各种质量问题。
在ISO 9004:2000版标准中,已将FMEA 和FTA分析作为对设计和开发以及产品和过程的确认和更改进行风险评估的方法。
我国目前基本上仅将FMEA与FTA技术应用于可靠性设计分析,根据国外文献资料和我国部分企业技术人员的实践,FMEA和FTA可以应用于过程(工艺)分析和质量问题的分析。
质量是一个内涵很广的概念,可靠性是其中一个方面。
通过FMEA和FTA分析,找出了影响产品质量和可靠性的各种潜在的质量问题和故障模式及其原因(包括设计缺陷、工艺问题、环境因素、老化、磨损和加工误差等),经采取设计和工艺的纠正措施,提高了产品的质量和抗各种干扰的能力。
根据文献报道,某世界级的汽车公司大约50%的质量改进是通过FMEA和FTA/ETA来实现的。
Kano模型日本质量专家Kano把质量依照顾客的感受及满足顾客需求的程度分成三种质量:理所当然质量、期望质量和魅力质量(如下图)Kano模型A:理所当然质量。
当其特性不充足(不满足顾客需求)时,顾客很不满意;当其特性充足(满足顾客需求)时,无所谓满意不满意,顾客充其量是满意。
B:期望质量也有称为一元质量。
当其特性不充足时,顾客很不满意,充足时,顾客就满意。
越不充足越不满意,越充足越满意。
C:魅力质量。
当其特性不充足时,并且是无关紧要的特性,则顾客无所谓,当其特性充足时,顾客就十分满意。
理所当然的质量是基线质量,是最基本的需求满足。
期望质量是质量的常见形式。
魅力质量是质量的竞争性元素。
通常有以下特点:具有全新的功能,以前从未出现过;性能极大提高;引进一种以前没有见过甚至没考虑过的新机制,顾客忠诚度得到了极大的提高;一种非常新颖的风格。
Kano模型三种质量的划分,为6Sigma改进提高了方向。
如果是理所当然质量,就要保证基本质量特性符合规格(标准),实现满足顾客的基本要求,项目团队应集中在怎样降低故障出现率上;如果是期望质量,项目团队关心的就不是符合不符合规格(标准)问题,而是怎样提高规格(标准)本身。
FMEA的应用及分析
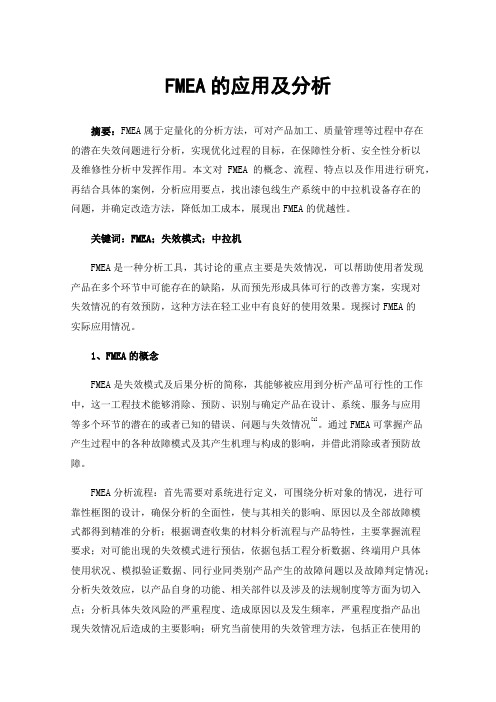
FMEA的应用及分析摘要:FMEA属于定量化的分析方法,可对产品加工、质量管理等过程中存在的潜在失效问题进行分析,实现优化过程的目标,在保障性分析、安全性分析以及维修性分析中发挥作用。
本文对FMEA的概念、流程、特点以及作用进行研究,再结合具体的案例,分析应用要点,找出漆包线生产系统中的中拉机设备存在的问题,并确定改造方法,降低加工成本,展现出FMEA的优越性。
关键词:FMEA;失效模式;中拉机FMEA是一种分析工具,其讨论的重点主要是失效情况,可以帮助使用者发现产品在多个环节中可能存在的缺陷,从而预先形成具体可行的改善方案,实现对失效情况的有效预防,这种方法在轻工业中有良好的使用效果。
现探讨FMEA的实际应用情况。
1、FMEA的概念FMEA是失效模式及后果分析的简称,其能够被应用到分析产品可行性的工作中,这一工程技术能够消除、预防、识别与确定产品在设计、系统、服务与应用等多个环节的潜在的或者已知的错误、问题与失效情况[1]。
通过FMEA可掌握产品产生过程中的各种故障模式及其产生机理与构成的影响,并借此消除或者预防故障。
FMEA分析流程:首先需要对系统进行定义,可围绕分析对象的情况,进行可靠性框图的设计,确保分析的全面性,使与其相关的影响、原因以及全部故障模式都得到精准的分析;根据调查收集的材料分析流程与产品特性,主要掌握流程要求;对可能出现的失效模式进行预估,依据包括工程分析数据、终端用户具体使用状况、模拟验证数据、同行业同类别产品产生的故障问题以及故障判定情况;分析失效效应,以产品自身的功能、相关部件以及涉及的法规制度等方面为切入点;分析具体失效风险的严重程度、造成原因以及发生频率,严重程度指产品出现失效情况后造成的主要影响;研究当前使用的失效管理方法,包括正在使用的可行性评审、安全与失效设计与设计评审等方法,展开难检度分析与关键性分析;确定改进措施,确保检测度、发生度与严重度都得到控制;最后对失效模式的严重度、难检度、发生率与改善情况等数据进行汇总。
丘陵山地薯类收获机设计毕业论文

营销渠道优化
选择有效的销售渠道,包括直 销、经销商合作等,以扩大产 品影响力,增加销售收入。
环境影响分析
环境友好的生产
丘陵山地薯类收获机的设计应该充分考虑 对当地环境的影响,采用低碳、可持续的生 产方式,减少对植被和土壤的破坏,维护生态 平衡。
可持续发展
该收获机应能与当地社区的可持续发展相 协调,为乡村振兴贡献力量,改善农民生活,促 进社会和经济的协调进步。
分析测试
对试验过程进行仔细观察和数据采集,运用专业分析手段对试验结果进行深入分析。确定优化方向,为下一步改进提供依据。
试验结果分析
85%
平均收获效率
92%
土豆完整性
15min
5%
平均收获时间
残留率
在实验田地中对研制的原型机进行了全面的性能测试。结果显示,该丘陵山地薯 类收获机的平均收获效率达到85%,土豆完整性高达92%,平均收获时间不到15分 钟,残留率仅5%。这表明设计方案实现了良好的收获效果,为后续进一步优化和 产业化奠定了基础。
薯类收获机的工作原理
1
挖掘
薯类收获机使用专门设计的挖掘爪抱、翻转和分离土壤,将土送带或滚筒被传送到收集箱或运输车上。
3
清洁
收获机的振动筛网可以去除泥土和杂草,保持土豆的清洁。
关键部件设计
减速机
减速机在薯类收获机中起到减速并增加扭矩的作用,保证了机器的工作效率和抓取力度。
可靠性分析
故障模式分析
采用FMEA方法识别薯类收获机 各关键部件的潜在故障模式,评估 风险程度。制定相应的预防和控 制措施。
加速寿命试验
对收获机的关键零部件进行加速 寿命试验,在短时间内获得长期使 用下的可靠性数据。
可维修性分析
质量绩效评价模型与方法研究

质量绩效评价模型与方法研究一、本文概述随着全球市场竞争的日益激烈,质量已成为企业生存和发展的关键因素。
为了有效地评价和管理质量绩效,企业需要建立一套科学、合理、实用的质量绩效评价模型和方法。
本文旨在深入研究质量绩效评价模型与方法,为企业提供一种全面、客观、可操作的质量绩效评价工具,以帮助企业提高产品质量、增强市场竞争力。
本文将首先回顾质量绩效评价的发展历程和现状,分析现有评价模型和方法的优缺点。
在此基础上,本文将结合国内外先进的理论和实践,探讨适合中国企业特点的质量绩效评价模型和方法。
具体而言,本文将重点研究以下几个方面:质量绩效评价的概念和内涵:明确质量绩效评价的定义、目的和意义,阐述质量绩效评价与质量管理、绩效管理之间的关系。
质量绩效评价的指标体系:根据企业的实际情况和需求,构建全面、科学、实用的质量绩效评价指标体系,包括产品质量指标、过程质量指标、顾客满意度指标等。
质量绩效评价的方法和技术:研究适合中国企业特点的质量绩效评价方法和技术,如模糊综合评价、数据包络分析、平衡计分卡等,为企业选择合适的评价工具提供指导。
质量绩效评价的实施与改进:探讨质量绩效评价的实施步骤、方法和注意事项,分析评价结果的应用和改进方向,为企业提供持续改进的建议和措施。
通过本文的研究,期望能够为企业建立一套科学、合理、实用的质量绩效评价模型和方法,提高企业的质量管理水平和市场竞争力,实现企业的可持续发展。
同时,本文的研究也有助于丰富和完善质量绩效评价的理论体系和实践经验,为相关领域的研究和实践提供有益的参考和借鉴。
二、质量绩效评价理论基础质量绩效评价是组织对其内部过程和产品质量的全面评估,目的在于识别存在的问题,推动改进,并最终实现卓越绩效。
这一过程的理论基础主要来源于质量管理和绩效评价两大领域。
在质量管理领域,最为人所熟知的理论是戴明的PDCA循环和朱兰的质量三部曲。
PDCA循环,即计划(Plan)、执行(Do)、检查(Check)、处理(Act)的循环过程,强调了持续改进和不断学习的重要性。
FMEA在质量管理中的应用

FMEA 在质量管理中的应用摘要:在过去的一个世纪里,大规模的产业生产从繁荣过渡到衰退。
前者的生产管理模式不再有利。
如果产业企业想在产业上维持他们的主要地位,他们就必须革新。
为什么这么说呢,因为如果企业一直在做平时做的事情,那就只能得到通常能得到的东西。
激烈的竞争和危机感强的企业总是改变他们的面貌,促进变化的不确定性和风险。
风险管理分析的概念是针对经营风险尽可能地将风险控制在最小限度或最小化。
关键词:质量;预防措施;产品;方法;现状分析AbstractQuality scientists and reliability engineers have been through the operation of the enterprise system to find a comprehensive risk, in order to eliminate the risk, and finally found that the focus of risk control should be put on the prevention of all risks and defects.一、引言随着质量管理科学的逐步改进,质量管理的重点从后疗法到前预防逐渐变化。
预防可以事先带来各种优点:降低生产成本,降低产品的报废率,减少产品风险等。
但是,如何在每一个回合中分析失败模式和原因,以达到有效的预防效果?作为预防程序,PFMEA会给我们解决这个问题。
PFMEA(过程故障模式和影响分析)是1960年代NASA在开发航天飞机的过程中发明的预防程序。
为确保航天飞机的可靠性发挥了重要作用。
此后,pfmea广泛用于非军事领域,并通过持续改进成为有效的质量管理方法。
1.FMEA产生的背景2.1、FMEA的发展历史FMEA技术的应用非常快。
1950年代初期,美国首先将FMEA应用于战斗机操作系统的设计和分析。
1960年代中期,fmea技术在美国航空航天产业中被正式使用。
FMEA常见问题及改进措施

FMEA常见问题及改进措施摘要:本文主要阐述了故障模式及影响分析(FMEA)工作在产品研发过程中开展的意义,列举了FMEA工作开展过程中存在的一些问题,并针对这些问题提出了改进建议,使FMEA工作在提高产品可靠性方面发挥更大的效能。
关键词:故障模式,故障影响,预防纠正措施,使用补偿措施引言故障模式及影响分析(Failure Mode and Effect Analysis,FMEA)是指分析产品所有可能的故障模式及其可能产生的影响,并按每个故障模式产生影响的严重程度予以分类的一种归纳分析方法。
其目的是通过系统地分析,找出潜在的薄弱环节,并提出有针对性的改进措施,以提高产品的可靠性。
它是一种自下而上的(由元器件到产品)的故障因果关系的单因素的、定性的分析方法,该方法为人们提供了一种规范化、标准化、系统化的有效分析工具。
目前,大多数型号研制工作都要求开展FMEA工作,FMEA方法的技术核心其实并不复杂,但在实际开展过程中仍然存在种种问题。
下面分别从管理和技术两方面进行分析。
1FMEA工作存在的问题1.1FMEA工作中存在的管理问题1)FMEA工作缺乏系统性“关键项目”的确定、“约定层次”的划分、严酷度等级的定义、下级产品对上级产品层次的故障影响等工作,需经过设计师系统之间详细沟通和系统策划,而现状是单机、分系统和总体设计之间往往各自为战【1】。
另外,FMEA工作目前通常只在某一研制阶段开展,FMEA作为一个反复迭代的过程,放弃“FMEA与设计同步开展”的原则,在某种意义上讲,就是放弃了在设计阶段及时、全面发现设计薄弱环节并改进设计的机会。
2)FMEA工作没有闭环FMEA工作的目的是找出分析对象的薄弱环节,如“严酷度等级为Ⅰ、Ⅱ类的故障”、“关键项目/关重件”、“单点故障”、“不可检测故障”等,并针对薄弱环节提出设计改进措施、使用补偿措施。
目前FMEA工作大多被简化成了FMEA填表工作,只完成了FMEA报告,没有FMEA分析结果或有结果而未反馈到产品设计中,对促进产品改进设计的作用有限。
FMEA分析与应用研究
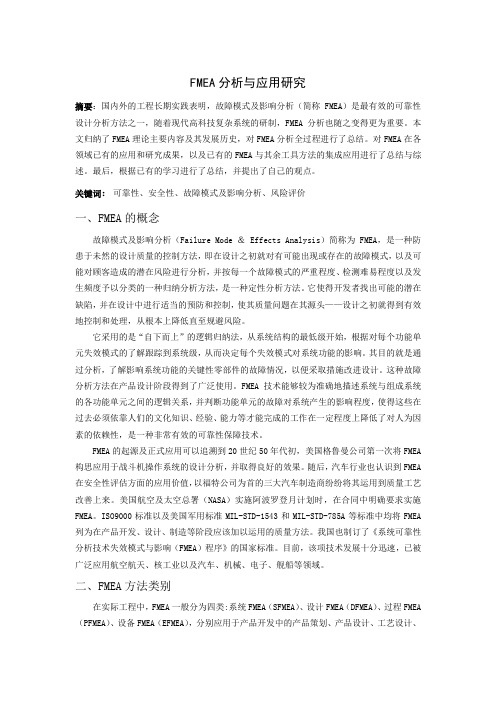
FMEA分析与应用研究摘要:国内外的工程长期实践表明,故障模式及影响分析(简称FMEA)是最有效的可靠性设计分析方法之一,随着现代高科技复杂系统的研制,FMEA分析也随之变得更为重要。
本文归纳了FMEA理论主要内容及其发展历史,对FMEA分析全过程进行了总结。
对FMEA在各领域已有的应用和研究成果,以及已有的FMEA与其余工具方法的集成应用进行了总结与综述。
最后,根据已有的学习进行了总结,并提出了自己的观点。
关键词:可靠性、安全性、故障模式及影响分析、风险评价一、FMEA的概念故障模式及影响分析(Failure Mode & Effects Analysis)简称为FMEA,是一种防患于未然的设计质量的控制方法,即在设计之初就对有可能出现或存在的故障模式,以及可能对顾客造成的潜在风险进行分析,并按每一个故障模式的严重程度、检测难易程度以及发生频度予以分类的一种归纳分析方法,是一种定性分析方法。
它使得开发者找出可能的潜在缺陷,并在设计中进行适当的预防和控制,使其质量问题在其源头——设计之初就得到有效地控制和处理,从根本上降低直至规避风险。
它采用的是“自下而上”的逻辑归纳法,从系统结构的最低级开始,根据对每个功能单元失效模式的了解跟踪到系统级,从而决定每个失效模式对系统功能的影响。
其目的就是通过分析,了解影响系统功能的关键性零部件的故障情况,以便采取措施改进设计。
这种故障分析方法在产品设计阶段得到了广泛使用。
FMEA技术能够较为准确地描述系统与组成系统的各功能单元之间的逻辑关系,并判断功能单元的故障对系统产生的影响程度,使得这些在过去必须依靠人们的文化知识、经验、能力等才能完成的工作在一定程度上降低了对人为因素的依赖性,是一种非常有效的可靠性保障技术。
FMEA的起源及正式应用可以追溯到20世纪50年代初,美国格鲁曼公司第一次将FMEA 构思应用于战斗机操作系统的设计分析,并取得良好的效果。
随后,汽车行业也认识到FMEA 在安全性评估方面的应用价值,以福特公司为首的三大汽车制造商纷纷将其运用到质量工艺改善上来。
数控机床可靠性技术的分析与研究

数控机床可靠性技术的分析与研究一、概述随着制造业的快速发展,数控机床作为现代制造技术的核心设备,其可靠性对于保证生产过程的稳定性和产品质量具有至关重要的作用。
数控机床可靠性技术是指研究数控机床在规定的条件下和规定的时间内,完成规定功能的能力。
这一技术的提升不仅关乎到企业的生产效率,更是决定产品竞争力的关键因素。
近年来,随着新材料、新工艺和新技术的不断涌现,数控机床的复杂性和精度要求越来越高,其可靠性问题也日益凸显。
对数控机床可靠性技术的研究和分析变得尤为重要。
通过对数控机床可靠性技术的研究,可以深入了解机床的失效模式和机理,为机床的设计、制造、使用和维护提供科学依据,进而提升机床的可靠性水平,确保生产过程的顺利进行。
同时,数控机床可靠性技术的研究也是制造业持续创新和发展的必然要求。
在全球经济一体化和市场竞争日益激烈的背景下,提高数控机床的可靠性水平,不仅可以提升企业的核心竞争力,还可以推动整个制造业的转型升级,实现可持续发展。
数控机床可靠性技术的研究与分析具有重要的理论意义和实践价值。
本文将从数控机床的可靠性定义出发,探讨其可靠性分析的方法和技术,分析影响可靠性的主要因素,并提出提高数控机床可靠性的措施和建议,以期为我国制造业的发展提供有益的参考。
1. 数控机床在现代制造业中的重要性在现代制造业中,数控机床的重要性不言而喻。
作为制造业的核心设备之一,数控机床的精度、效率、稳定性以及可靠性等性能直接影响到产品的质量和生产效率。
随着全球制造业的快速发展,特别是在中国这样的制造业大国,数控机床的需求量与日俱增。
对于数控机床可靠性技术的深入分析和研究,不仅有助于提升我国制造业的整体竞争力,更对保障国家经济安全具有重要意义。
数控机床的高精度和高效率是现代制造业追求的核心目标。
在许多高精度、高复杂度的零部件制造过程中,如航空航天、汽车制造、模具制造等领域,数控机床的作用无可替代。
其高精度加工能力能够确保零部件的尺寸精度和表面质量,满足产品性能和使用寿命的要求。
烟草内在质量评价体系的系统研究

烟草内在质量评价体系的系统研究烟草行业是全球范围内的重要产业之一,对于国家和地区的经济发展具有重要意义。
然而,随着消费者对于烟草产品的质量和使用风险越来越,烟草企业也面临着越来越大的挑战。
因此,建立一套科学、有效的烟草内在质量评价体系,对于提高产品质量、增强市场竞争力、保障公众健康具有重要意义。
本研究旨在系统地研究烟草内在质量评价体系,以期为烟草企业的质量管理和控制提供理论支持和实践指导。
近年来,国内外学者对于烟草内在质量评价体系进行了大量研究。
这些研究主要集中在化学成分、感官评价和风险评估等方面。
化学成分是烟草内在质量的重要指标之一,包括烟碱、总糖、还原糖、总氮、氯和钾等成分。
通过对烟草化学成分的分析和控制,可以有效提高烟草产品的质量和稳定性。
感官评价是评价烟草产品质量的重要手段之一,主要通过评吸的方式对烟草的香气、口感、刺激性等方面进行评价。
风险评估主要是对烟草产品中的有害成分进行检测和评价,以保障消费者的健康。
然而,现有的研究存在一定的不足和局限性。
化学成分方面的研究主要集中在单个成分的分析上,缺乏对于不同成分之间的相互作用和对于烟草产品质量的影响机制的研究。
感官评价方面,由于评吸的主观性和不确定性,容易导致评价结果的差异和不准确。
风险评估方面,对于有害成分的检测和评价尚未形成完整的体系,容易导致风险控制的疏漏。
本研究采用系统研究的方法,将从化学成分、感官评价和风险评估三个方面对烟草内在质量评价体系进行全面研究。
在化学成分方面,将对烟草中的主要成分进行分析,并研究不同成分之间的相互作用及其对烟草产品质量的影响机制。
在感官评价方面,将采用盲品测试和因子分析等方法,建立一套科学、有效的评价模型,以降低评吸的主观性和不确定性。
在风险评估方面,将对烟草产品中的有害成分进行检测和评价,并建立一套完整的评估体系,以全面了解有害成分的存在和风险水平。
通过以上研究方法,本研究将建立一套科学、有效的烟草内在质量评价体系,为烟草企业的质量管理和控制提供理论支持和实践指导。
FMEA潜在缺陷模式和影响分析报告
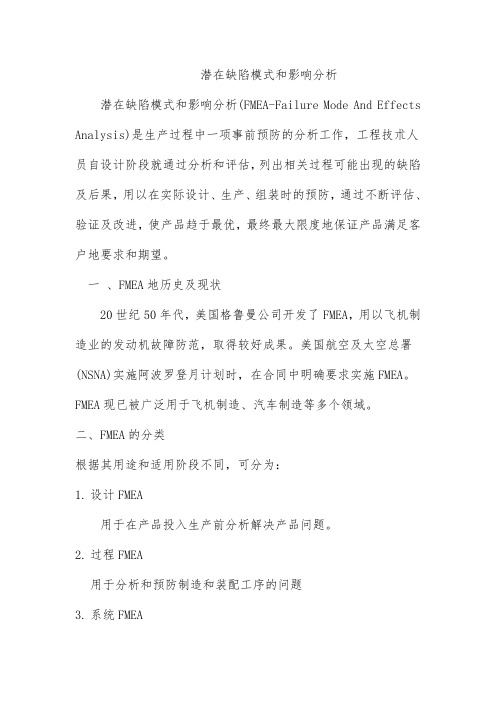
潜在缺陷模式和影响分析潜在缺陷模式和影响分析(FMEA-Failure Mode And Effects Analysis)是生产过程中一项事前预防的分析工作,工程技朮人员自设计阶段就通过分析和评估,列出相关过程可能出现的缺陷及后果,用以在实际设计、生产、组装时的预防,通过不断评估、验证及改进,使产品趋于最优,最终最大限度地保证产品满足客户地要求和期望。
一、FMEA地历史及现状20世纪50年代,美国格鲁曼公司开发了FMEA,用以飞机制造业的发动机故障防范,取得较好成果。
美国航空及太空总署(NSNA)实施阿波罗登月计划时,在合同中明确要求实施FMEA。
FMEA现已被广泛用于飞机制造、汽车制造等多个领域。
二、FMEA的分类根据其用途和适用阶段不同,可分为:1.设计FMEA用于在产品投入生产前分析解决产品问题。
2.过程FMEA用于分析和预防制造和装配工序的问题3.系统FMEA用于在概念阶段和设计阶段分析、预防系统和子系统存在的问题三、FMEA实施步骤-过程FMEA1.确认加工工序的流程及判定标准2.决定各过程的机能分析水准,依据对象过程的不同,分析水准亦不同3.明确加工过程,包括要求的质量、公差等4.作成加工过程的方块图5.针对每一加工工序,列出发生的不良模式6.整理造成不良品的原因之不良模式,选定作为检讨对象的不良模式7.列举不良发生的推定原因8.将不良模式及原因记入过程FMEA用表9.从影响程度、发生频度、可侦测性、对设备的熟悉程度为评判根据,对缺陷模式进行等级评价,分Ⅰ.Ⅱ.Ⅲ.Ⅳ等10.整理工序FMEA,确定何时、何人、对何工序实施FMEA11.实施四、FMEA的实施时机1.当新的系统、产品或工序在设计时2.现存的设计或工序发生变化时3.当现在的设计、工序用于新的环境或场合时4.完成一次纠正行动后5.对系统FMEA,在系统功能被确定,但特定的设备选择前6.对设计FMEA,产品功能已确定,但投入生产前7.对工序FMEA,当初步产品的图纸及作业指导作成时。