前支承壳体加工工艺案例研究
支承套零件的数控加工工艺
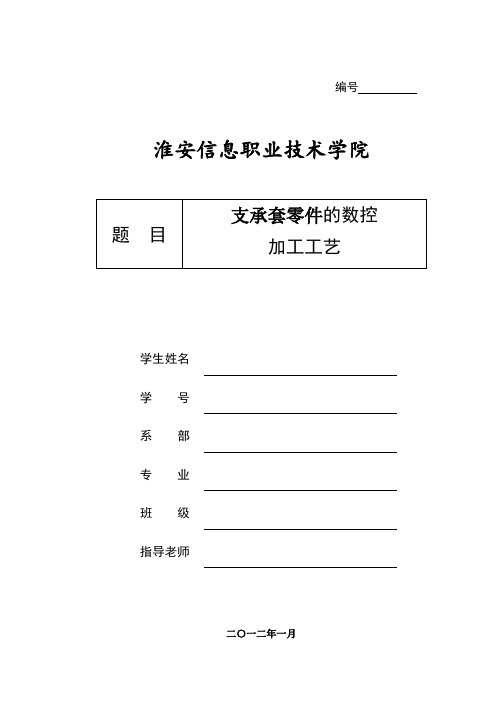
编号淮安信息职业技术学院题目支承套零件的数控加工工艺学生姓名学号系部专业班级指导老师二〇一二年一月支承套零件的数控加工工艺如图所示为升降台铣床的支承套,在两个互相垂直的方向上有多个孔要加工,在加工中心上加工,只需一次安装即可完成。
零件材料为45钢,中批量生产,分析其加工工艺。
零件图一、零件图工艺分析1)加工内容该零件主要由平面、圆弧外表面、多个简单孔和螺纹孔组成,几何元素之间关系描述清楚完整,尺寸标注完整。
毛坯为110mm×90mm棒料,加工内容主要包括上平面,左右两端面、圆弧外表面ø60×12孔,ø35H7孔,ø17×11孔,2×11孔,2×ø15H7孔以及2×M6-6H深25的螺纹孔和几处倒角。
2)加工要求①零件主要加工要求为ø35H7和2×ø15H7内孔的尺寸公差等级为7级,表面粗糙度要求较高,其值为Ra=1.6μm。
2×M6-6H 深25的螺纹孔尺寸公差等级为6级,尺寸公差等级要求较高。
零件的上平面、左右两端面和圆弧外表面以及ø60孔的右端面表面粗糙度值为1.6μm,表面粗糙度要求较高;ø35H7孔表面和ø17×11孔表面表面粗糙度值为12.5μm,粗糙度要求一般,其余表面粗糙度值要求为25μm。
②对ø60孔和ø35H7有同轴度要求,同轴度值为0.08,并以A面(零件圆弧外表面的左面)为基准;对ø60×12孔的端面和零件圆弧外表面有跳动率要求,跳动值小于0.025,并且ø60×12孔以B面(ø35H7孔表面)为基准,零件圆弧外表面的右面以A面为基准。
对2×ø15H7孔有平行度要求,其平行度不得大于0.05,以C面(零件圆弧外表面的右面)为平行基准。
壳体类零件数控加工工艺分析研究报告

壳体类零件数控加工工艺分析研究报告【摘要】壳体类零件在生产实际中有着极其广泛的应用,本文通过对壳体类零件种类结构特点的分析,研究了壳体类零件数控加工技术,并融入了虚拟仿真技术。
对进一步提高零件的加工效率和机床的利用率,提高产品质量,缩短生产周期等现代化生产的需要具有积极作用和指导意义。
1.项目技术背景壳体类零件在仪表、工程机械、航空航天、航海等领域都有着重要应用。
但由于壳体类零件特殊的结构和工艺特点,对制造与加工技术提出了新的挑战。
数控加工技术由于其在机械加工中的优越性正逐步取代普通机床,在生产加工领域内占有着举足轻重的地位,同时也是一个国家基础产业发达程度的象征。
2.研究意义了解机械加工技术的现状;了解机械加工的技术特点、发展情况;掌握壳体类零件的加工方法;对自己未来的专业学习和就业打下基础。
3.研究内容3.1五轴数控机床结构类型分析机加工工艺特点3.1.1五轴联动数控机床的结构分析五轴联动数控机床的整体结构由床身、十字滑头、滑枕、立柱、AC联动铣头、自动供油系统、冷却系统、数控系统、进给系统等组成。
安装在床身上面的十字滑头带动工作台沿X、Y轴两个方向运动,安装在立柱上的滑枕带动A、C轴联动铣头沿Z轴方向运动铣刀绕Z轴摆动和旋转,从而形成了三个直线轴和两个回转轴的五轴运动系统。
一、五轴联动加工中心五轴联动加工中心大多是3 + 2的结构,即X, Y, Z三个直线运动轴加上分别围绕X, Y, Z轴旋转的A, B, C三个旋转轴中的两个旋转轴组成。
三个直线轴的运动分别由三个伺服电机通过滚珠丝杠完成。
绕两个回转轴的运动分别有两个伺服电机通过可消隙的蜗轮蜗杆装置完成,Y 向导轨采用直线滚动导轨,刚性好、摩擦系数小、运动灵敏度高;Z向采用巨型贴塑导轨,承载能力强,精度高。
五轴联动加工中心有高效率、高精度的特点,工件一次装夹就可完成五面体的加工。
五轴联动数控机床一般分为立式和卧式两种类型,根据轴运动的形式,由二个旋转轴的组合形式来分,大体上有双转台式、转台加上摆头式和双摆头式三种形式。
浅谈壳体加工工艺技术研究与应用

浅谈壳体加工工艺技术研究与应用摘要:本文主要从壳体加工的工艺特点及难点,工艺设计及工艺技术的实践应用入手,对壳体加工的工艺技术进行了深度的分析及研究,进而能够充分利用壳体加工的工艺技术各项功能优势,提升壳体加工的质量及效率。
关键词:壳体;加工;工艺;技术;研究;应用;前言壳体件(Shell parts),为我国航空业发动机的燃油总控制系统当最为核心的零部件,为各种分布器、调节器、油泵等相关组件装配的母体。
在燃油的总控制系统当中,壳体所起到的功能作用为支撑所有高中低的压油路及控制元件之导引性作用。
壳体的结构相对较为复杂,对各项加工制造工艺及相关技术的要求相对较高。
1、工艺特点及难点分析1.1基本特点为了能够切实地保证壳体的加工工艺及相关技术应用效果,就需先从其实际的壳体结构及加工工艺特点上入手,做到从根本上了解与掌握壳体及其加工的相关要点。
那么,从壳体结构上分析,它主要的特点在于因其实际的安装空间相对较为有限,壳体的结构通常是较为复杂性的形状、紧凑性较为明显,位置的精度相对较高。
壳体内部的油路孔交错纵横,多数是大长径的深孔;而从壳体的加工工艺入手分析,为了将壳体整体结构的重量减轻,多数应用刚度性及强度性相对较高的一些有色的金属合金,如高强度性铝合金及高强度性的镁合金等材料。
那么,针对于这种材料工艺的设备选型、各项参数设计、加工来说,难度性相对较大。
壳体内部的深沟槽中孔系与其相贯的油路孔系加工与毛刺的去除,都有着较大的难度性。
燃油的控制系统中壳体上通常会进行活门的衬套安装,必须是热压性装配的衬套。
在一定程度上,这种壳体需进行研磨的配套,保证其活门与衬套间配合的间隙。
1.2主要难点如图1所示,以某壳体为例,它的结构极具紧凑性及复杂性,工作期间壳体承受着10MPa油压。
壳体最大的外形尺寸270mm*254mm*248mm,复杂的孔系共有12处,油路的孔多达130余条,多数是孔径、深孔、过桥孔尺寸均相对较小,有10余条Φ3.7mm、Φ3.2mm等较小直径的油路孔,孔深度为135mm-189mm。
某支承座机械加工工艺规程及夹具设计
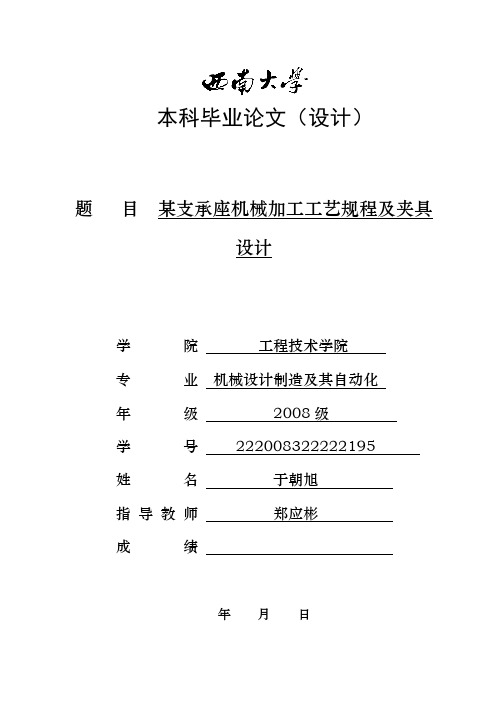
本科毕业论文(设计)题目某支承座机械加工工艺规程及夹具设计学院工程技术学院专业机械设计制造及其自动化年级2008级学号222008322222195姓名于朝旭指导教师郑应彬成绩年月日目录摘要 (1)Abstract (2)0 文献综述 (3)0.1 机械制造工艺的现状及发展趋势 (3)0.1.1 机械制造工艺发展现状 (3)0.1.2 机械制造工艺发展趋势 (4)0.2 机床夹具的现状及发展趋势 (4)0.2.1 机床夹具的发展现状 (4)0.2.2 机床夹具的发展趋势 (5)0.3 本课题研究的主要内容 (5)0.3.1 支承座机械加工工艺规程设计 (5)0.3.2 支承座专用夹具设计 (5)1 引言 (6)2 零件分析 (6)3 毛坯的选择 (7)4 零件机械加工工艺路线的制定 (7)4.1 定位基准的选择 (7)4.1.1 粗基准的选择 (8)4.1.2 精基准的选择 (8)4.2 拟定工艺路线 (8)4.2.1加工方法的选择和加工阶段的划分 (8)4.2.2 工艺路线的拟定 (9)4.3 加工余量和工序尺寸的拟定 (11)4.4 切削用量的确定 (14)5 量检具的选择 (20)6 钻夹具设计 (21)6.1 确定设计方案 (21)6.2 确定定位方式与定位元件 (21)6.3 确定导向装置 (21)6.4 确定夹紧机构 (22)6.4.1 工件的夹紧 (22)6.4.2 分度装置的夹紧 (22)6.5 定位误差分析 (23)6.6 基于Pro/E的夹具三维建模 (23)6.7 夹具操作说明 (25)7 总结 (25)参考文献 (25)致谢 (26)某支承座机械加工工艺规程及夹具设计于朝旭西南大学工程技术学院,重庆 400715摘要:支承座的各项技术要求要靠合理的加工工艺和工装设备来保证。
支承座零件的工艺性好不好,其毛坯如何选择,机械加工过程中选择哪些要素作为定位基准,机加工路线如何拟定,每道工序或者工步的切削用量怎么确定,用什么量检具来检验加工完成的支承座零件,这些都是本文支承座机械加工工艺规程所要解决的问题。
某壳体加工工艺研究

某壳体加工工艺研究摘要:某壳体以其结构复杂、尺寸精度高、技术条件要求严等特点,代表着发动机的设计与工艺加工技术水平。
对于我们来说极具挑战性,其研制的成功与否直接决定着壳体专业的发展,也可以说直接决定存亡的问题。
在机加方面某壳体的加工具有代表性,在装配与调试方面节流活门的试验与调整具有代表性,因此本文重点论述的是某壳体的加工工艺研究、节流活门的调试方法,及其在生产过程中出现问题及解决措施。
关键词:发动机壳体加工1. 引言某机发动机中壳体组件承担着核心作用,因此某壳体组件的结构复杂、内部组成零件多且尺寸及技术条件精度要求高,主要包括壳体、柱塞、主副喷口、旋流芯等。
无论是从机械加工、焊接专业、装配调试等专业要求的各项指标性能对加工和装配试验技术提出非常高的要求。
2.壳体组件的加工壳体的加工过程分为钎焊前的壳体加工及钎焊后的壳体加工。
2.1 零件难点分析3.1.1基准的确定与加工:本着工艺基准与设计基准重合的原则,由于所有加工尺寸的起点源于安装面与中心线的交点,同时安装孔具有角向和定位作用,为此确定安装座为加工基准,由于零件的特殊形状导致安装面的加工困难,即定位及夹紧零件困难,同时安装面位置精度要求非常高。
2.1.2深孔加工:两2深孔的长径比大约在28以上,属深孔加工;两深孔相对2的位置精度保证与否,直接决定两油路的“连通”和密封性能的保证与否,同时也会影响最小壁厚的保证;由于两深孔内需要焊接隔热管,钎焊质量的保证主要取决于深孔与隔热管的间隙,还需控制孔径公差,以保证衬套钎焊焊接质量。
2.1.3壳体头部:型腔比较复杂,由于深孔加工在前内部存在断屑切削,内锥密封面表面粗糙度为Ra0.8,内螺纹及内锥面同轴度要求在φ0.05范围内,螺纹对基准的位置度为φ0.05,去掉夹具的制造误差、机床的误差及找正夹具的误差等,位置度φ0.05不易保证。
这样无论是加工内螺纹还是加工内锥面都是比较困难的。
2.1.4安装孔:孔的直径比较大且比较深,孔的公差为0.033,除了要保证孔的公差外,对孔的圆柱度也要适当控制,此项要求虽然设计未作规定,但从其工作状态来看,孔内与壳体外圆相配合,如果圆柱度不好最终直接影响性能。
支承套(薄壁筒)加工工艺设计及分析
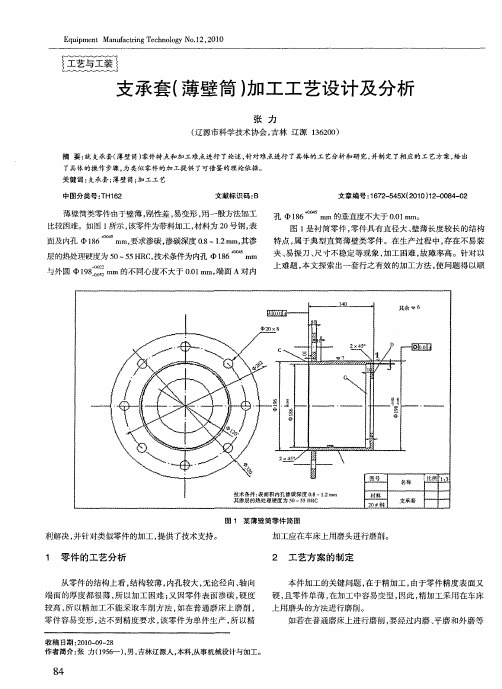
零 件 a2 m孔 中装人压 紧元件 夹紧 ,然后磨 削 中18。2 l 0m P 9 .. -2 0 . 0
:
mm外 圆及 端面 D。达到精度 、 粗糙度要求交检 。
3 结束语
经过实 践验证 , 上述工艺方法 和加工手段 , 按 对该零件加 工后 进行 了认真 的检 测 ,结果 印证 了该 方法保证 了产 品的各
较 高 , 以精 加工不 能采 取车 削方法 , 所 如在 普通磨 床上磨 削 ,
2 工艺 方案 的 制定
本 件加工 的关键 问题 , 于精 加工 , 在 由于零件精度表 面又
硬, 且零件 单薄 , 在加 工中容易变 型 , 因此 , 精加工采 用在车床
上用磨头 的方法进行磨 削。 如若在普 通磨床上进行磨 削 , 要经过 内磨 、 磨和外 磨等 平
上难题 , 本文探 索出一套行之有效 的加工方法 , 问题得 以顺 使
图 1 某薄壁简零件简 图
利解决 , 并针对类似零 件的加工 , 了技术支持 。 提供
加 工应 在车床上用磨头进行磨削 。
1 零件 的 工艺分 析
从零件 的结构上看 , 结构较 薄 , 内孔较 大 , 无论径 向、 向 轴 端面 的厚 度都很薄 , 以加工 困难 ; 因零 件表 面渗碳 , 所 又 硬度
关键词 : 支承套 ; 薄壁筒 ; 加工工 艺
中图分类号 : H1 2 T 6 文献标识码: B 文章编号 : 7 — 4 X( 0 0)2 0 8 - 2 1 2 5 5 2 1 1 —0 4 0 6
薄壁筒类零件由于壁薄 , 刚性差 , 易变形 , 用一般方法加 工 比较困难 。如图 1 所示 , 该零件为带料加工 , 材料为 2 号钢 , 0 表
壳体类零件数控高效加工工艺技术研究

壳体类零件数控高效加工工艺技术研究壳体类零件在各种机械设备中广泛应用,例如汽车引擎、机床、航空器等。
这些零件通常需要高精度、高质量和高效率的加工,以满足不同行业对产品的需求。
传统的加工方法已经不能完全满足生产需求,需要更加高效的数控加工技术来提高生产率和减少成本。
因此,本文将研究壳体类零件数控高效加工工艺技术。
一、壳体类零件加工技术需求分析壳体类零件通常由铝合金、钢或钛合金等材料制成,加工难度较大。
为了保证加工质量和生产效率,需要采用新的加工技术。
具体分析如下:1. 高精度加工壳体类零件是机械设备中精度要求较高的部件之一。
如何保证加工精度,直接关系到产品的质量和性能。
传统的加工方法受到机械装备制造水平的限制,很难达到高精度需求。
而数控加工一般具有高加工精度,能够满足壳体类零件的加工要求。
随着市场需求的增加和竞争的加剧,生产企业需要尽可能提高生产效率,以降低制造成本,以满足客户的要求。
传统的加工方式需要大量的人工操作,并且制造周期长,加工效率低下。
而数控加工则可以实现自动化加工,提高加工效率和产品制造周期。
3. 提高制造柔性现代生产的市场环境日益变化,市场对产品的要求也在不断变化。
企业需要根据市场需求进行生产调整,而传统的加工方式不利于生产灵活性。
相比之下,数控加工技术具有灵活性,在不同产品生产周期时容易进行生产调整,提高制造柔性。
二、数控加工和机加工的比较2.1 数控加工的优势数控加工是一种利用计算机程序控制工具运动完成零件加工的方法,它具有以下优势:数控加工技术具有高精度的加工能力,能够控制工具的移动精度和加工深度,从而保证加工零件的高精度和表面质量。
2. 生产效率高数控加工可实现全自动化加工,无人值守操作,大大提高了生产效率。
此外,少量的零件加工也可以减少机床设备闲置时间,提高生产效率和生产工艺的柔性。
3. 生产周期短数控加工可以利用计算机程序编程,预先设置好工艺参数,可以减少零件加工的设计审核和制造过程,缩短制造周期。
箱体类机匣加工工艺研究——以某机前支承壳体加工为例
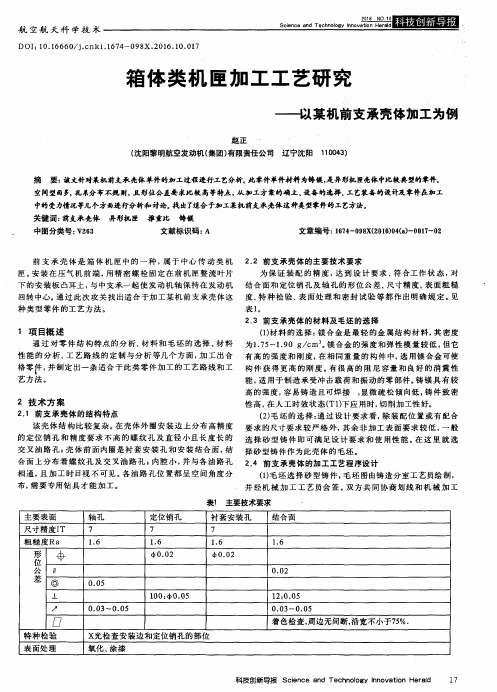
(2)毛 坯 的选 择 :通 过 设 计要 求 看 ,除 装 配 位 置或 有 配合
该 壳 体 结 构 比 较 复 杂 。在 壳 体外 圈安 装 边 上 分布 高 精 度 要 求 的尺寸要 求 较 严 格 外 ,其 余非 加 工表 面 要 求 较 低 ,一 般
的定 位 销 孔 和 精 度 要 求 不 高 的 螺 纹 孔 及 直 径 小 且长 度 长 的 选 择 砂 型 铸 件 即 可 满 足 设 计 要 求 和 使 用 性 能 。在 这 里 就 选
入信号要通过飞机数据网络即ima平台的一部分功能传递至综合监视计算机单元而基于ima架构的综合监视功能省去了信号的二次传输直接提高了数据的传输速度以及相关的可靠性和完整性指标
航 空 航 天 科 学 技 术
D OI:10.16660/j.CDki.16'74-098X .2016.10.017
! Q:!
性 能 的 分 析 、工 艺 路 线 的定 制 与 分 析 等几 个 方 面 ,加 工 出 合 有 高 的 强度 和 刚 度 ,在 相 同重 量 的 构 件 中,选 用 镁 合 金 可使
格零 ,并 制 定 出 一条 适 合 于 此 类零 件 加 工 的工 艺 路 线 和 工 构 件 获 得 更 高 的 刚 度 。有 很 高 的 阻 尼 容 量 和 良好 的 消 震 性
为 保 证 装 配 的 精 度 ,达 到 设 计 要 求 、符 合工 作 状 态 ,对
下 的 安 装板 凸耳上 ,与中 支 承一 起 使 发动 机 轴保 持 在 发 动 机 结合 面 和 定 位销 孔 及轴 孔 的形 位 公 差 、尺寸 精 度、表 面 粗 糙
回转 中心 。通过 此 次攻 关 找 出适 合 于加 工某 机 前 支 承壳 体 这 度、特 种 检 验 、表 面处 理和 密 封 试 验 等 都 作 出明确 规 定 。见
壳体零件的加工工艺及夹具设计本科论文

2.2.2确定毛坯的制造形式
毛坯的铸造方法:由上文可知,该壳体属于小批量生产,对于毛坯制造宜采用金属模机器造型、模锻、压力铸造等。本次采用金属模机器造型,这种铸造方法的特点是铸件内部组织致密,机械性能较高,单位面积的产量高,适用于泵体、泵盖、壳体、减速箱体、汽缸头等中、小型铸件。毛坯的材料是HT200。
零件的实际形状如上图所示,从零件图上看,该零件结构比较复
2.2.2
壳体零件共有两组加工表面,它们相互间有一定的加工要求。现分述如下:
(1)以φ20mm孔中心轴线为中心的加工表面。这一组加工表面包括:两个直径φ50mm的外圆端面,两个直径为φ90mm的外圆端面及倒角,还有8个φ15mm的通孔,其中,主要加工表面为8个φ15mm的通孔。
1.3
零件的生产纲领:根据机械设计制作工艺与机床夹具公式:
N = QN(1+a)(1+B)
说明:式中N:零件生产纲领。
Q:产品的生产纲领
n :每一产品包含该零件的数量
a : 零件的备用率一般情况下a = 4%。
B : 零件的平均废品率:取B=1%。 所以,4000 = Q×1(1+4%)(1+1%) Q=3808件
In addition,we also designed aset of speciallathefixture and specialfixture for drilling machine.First,determine the appropriatelocation,designspecific folders,and then select thepositioning element,clamping elementetc..Thencalculate the positioning error,the clamping forceand cutting force,rationality analysis offixture.
壳体类零件数控高效加工工艺技术研究

壳体类零件数控高效加工工艺技术研究随着制造业的快速发展,工件加工质量和效率要求也越来越高。
作为数控加工的一个重要领域,壳体类零件的加工工艺技术一直备受关注。
壳体类零件是指外形封闭的零件,通常用于机械设备的外壳、外壳、外盖等。
壳体类零件的加工要求高精度、高效率、高稳定性,对加工工艺技术的要求也相对较高。
本文旨在探讨壳体类零件的数控高效加工工艺技术,为提高壳体类零件加工的质量和效率提供技术支持。
一、壳体类零件加工特点壳体类零件通常具有以下几个特点:1. 复杂的外形结构:壳体类零件外形通常为曲面或复杂结构,要求加工精度高、表面光洁度好。
2. 加工难度大:由于壳体类零件的复杂外形结构和精度要求高,加工难度较大,加工工艺技术要求高。
3. 加工效率要求高:随着制造业的快速发展,壳体类零件加工的效率也要求有所提高,需要采用高效加工工艺技术来满足生产需求。
二、数控高效加工工艺技术为了满足壳体类零件加工的要求,提高加工质量和效率,需要采用一系列数控高效加工工艺技术,包括以下几个方面:1. 数控加工中心:数控加工中心是目前壳体类零件加工的主要设备之一,它可以进行多轴联动加工,提高加工效率的同时保证加工精度。
数控加工中心配备高速主轴和自动换刀装置,可实现快速刀具变换,满足不同工序的加工需求。
2. CAD/CAM技术:CAD/CAM技术是数控高效加工的重要支撑,它可以实现壳体类零件的数字化设计和加工,通过CAD软件设计零件的三维模型,然后通过CAM软件生成加工程序,最后加载到数控加工中心进行加工。
CAD/CAM技术可以大大提高设计和加工效率,减少人为误差。
3. 高速切削技术:壳体类零件加工通常需要进行高速切削,采用高速刀具和高速进给,以提高加工效率和表面质量。
高速切削技术需要配合高速数控加工中心和高速进给伺服系统,通过提高切削速度和进给速度,减少加工时间,降低加工成本。
4. 先进的表面处理技术:壳体类零件的表面质量对其外观和性能有很大影响,因此需要采用先进的表面处理技术来提高表面光洁度和硬度。
壳体的工艺与工装的设计讲解

扬州职业大学毕业设计论文设计(论文)题目:壳体的工艺与工装的设计系别:机械工程系专业:机电一体化技术班级03机电(3)班姓名:刘雷雷学号:0301020322指导老师:吴红完成时间:06 年5月目录(一)产品介绍-------------------------------------------------------------------1 (二)计算生产纲领-------------------------------------------------------------2 1,计算生产纲领决定生产类型2,生产纲领(三)零件的分析----------------------------------------------------------------31.零件的结构的分析2,零件的技术分析(四)确定毛坯--------------------------------------------------------------------4 1,毛坯的铸造方式2,铸件的尺寸3,铸件的加工余量4,零件—毛坯综合图的绘制(五)工艺规程设计--------------------------------------------------------------5a)定位基准的选择Ⅰ粗基准的选择Ⅱ精基准的选择b)制定工艺路线c)拟订定位方案和选择定位元件Ⅰ定位方案Ⅱ选择定位元件d)初步拟定加工工艺路线e)修改后的工艺路线6,选择加工设备7,填写机械加工工艺过程卡和机械加工工序卡(六)机床夹具设计----------------------------------------------------------------6 1,加工中心用的夹具Ⅰ零件体工序的加工要求分析Ⅱ确定夹具的类型2,工作台面与夹具体的设计Ⅰ定位装方案Ⅱ加紧机构设计Ⅲ夹具精度分析与计算Ⅳ绘制夹具总图Ⅴ总图的绘制(七)设计所参考书籍-----------------------------------------------------------------7第一章产品介绍世界上包括我国的中重型卡车用动力几乎百分之百采用柴油机。
典型零件加工工艺分析例.

一、支承套的加工工艺如图所示为升降台铣床的支承套,在两个互相垂直的方向上有多个孔要加工,若在普通机床上加工,则需多次安装才能完成,且效率低,在加工中心上加工,只需一次安装即可完成,现将其工艺介绍如下:支承套简图1.分析图样并选择加工内容支承套的材料为45钢,毛坯选棒料。
支承套φ35 H7孔对φ100f9外圆、φ60mm 孔底平面对φ35H7孔、2×φ15H7孔对端面C及端面C对内φ100f9外圆均有位置精+0.5mm尺寸两端面、度要求。
为便于在加工中心上定位和夹紧,将φ100f9外圆、800780其余加工表面(2×φ15H7-0.5mm尺寸上平面均安排在前面工序中由普通机床完成。
孔、φ35H7孔、φ60mm孔、2×φ11mm孔、2×φ17mm孔、2×M8-6H螺孔)确定在加工中心上一次安装完成。
2.选择加工中心因加工表面位于支承套互相垂直的两个表面(左侧面及上平面)上,需要两工位加工才能完成,故选择卧式加工中心。
加工工步有钻孔、扩孔、镗孔、锪孔、铰孔及攻螺纹等,所需刀具不超过20把。
国产XH754型卧式加工中心可满足上述要求。
该机床工作台尺寸为400mm×400mm,x轴行程为500 mm,z轴行程为400 mm,y轴行程为400mm,主轴中心线至工作台距离为100~500 mm,主轴端面至工作台中心线距离为150~550 mm,主轴锥孔为ISO40,定位精度和重复定位精度分别为0.02mm和0.01mm,工作台分度精度和重复分度精度分别为7″和4″。
3.工艺设计1)选择加工方法所有孔都是在实体上加工,为防钻编,均先用中心钻钻引正孔,然法再钻孔。
为保证φ35H7及2×φ15H7孔的精度,根据其尺寸,选择铰削作其最终加工方法。
对φ60 mm的孔,根据孔径精度,孔深尺寸和孔底平面要求,用铣削方法同时完成孔壁和孔底平面的加工。
各加工表面选择的加工方案如下:φ35H7孔:钻中心孔→ 钻孔→ 粗镗→ 半精镗→ 铰孔;φ15H7孔:钻中心孔→ 钻孔→ 扩孔→ 铰孔;φ60mm孔:粗铣→ 精铣;φ11mm孔:钻中心孔→ 钻孔;φ17mm孔:锪孔(在φ11mm底孔上);M6-6H螺孔:钻中心孔→ 钻底孔→ 孔端倒角→ 攻螺纹。
支承套零件加工工艺

数控加工工艺编制设计说明书项目: 支承套零件数控加工工艺规程编制指导:郑红老师班级:姓名:学号:组别:温州职业技术学院机械系二零零五年五月目录一、机械加工工艺规程的制定 (4)1.1分析被加工零件 (4)1.2选择毛坯 (4)1.3设计工艺过程 (4)1.4工序设计 (4)1.5编制工艺文件 (5)二、支承套零件机械加工工艺规程的制订 (6)2.1分析研究图1所示的支承套零件 (6)2.2选择设备 (7)2.3确定零件的定位基准和装夹方式 (7)2.4确定加工顺序及进给路线 (8)2.5刀具选择 (8)三、机械加工工艺规程的制订 (9)3.1机械加工工艺规程的作用 (9)3.2机械加工工艺规程的制定程序 (9)3.3毛坯的选择 (10)3.4定位基准的选择 (11)3.5零件表面加工方法的选择 (11)3.6加工顺序的安排 (12)四、零件工艺流程方案设计 (113)4.1零件加工工艺分析 (113)4.2毛坯的选择 (113)4.3数控加工工艺分析及工序设计 (113)4.4确定机械加工余量 (15)五、切削用量的确定 (16)1.主轴转速的确定 (16)2.进给速度的确定 (17)3.背吃刀量确定 (17)总结 (18)参考文献 (19)摘要数控加工工艺是采用数控机床加工零件时所运用各种方法和技术手段的总和,应用于整个数控加工工艺过程。
数控加工工艺是伴随着数控机床的产生、发展而逐步完善起来的一种应用技术,它是人们大量数控加工实践的经验总结。
数控加工工艺过程是利用切削刀具在数控机床上直接改变加工对象的形状、尺寸、表面位置、表面状态等,使其成为成品或半成品的过程。
数控加工工艺是采用数控机床加工零件时所运用各种方法和技术手段的总和,它包含了确定数控加工内容;进行工艺分析和零件图形的数学处理;制定工艺方案;选择数控机床的类型;确定工步和进给路线;选择或设计刀具、夹具和量具;确定切削参数;编写、校验和修改加工程序;编写加工工艺技术文件等方面内容。
支承套的工艺设计及其工装工艺设计【两套夹具】全套图纸
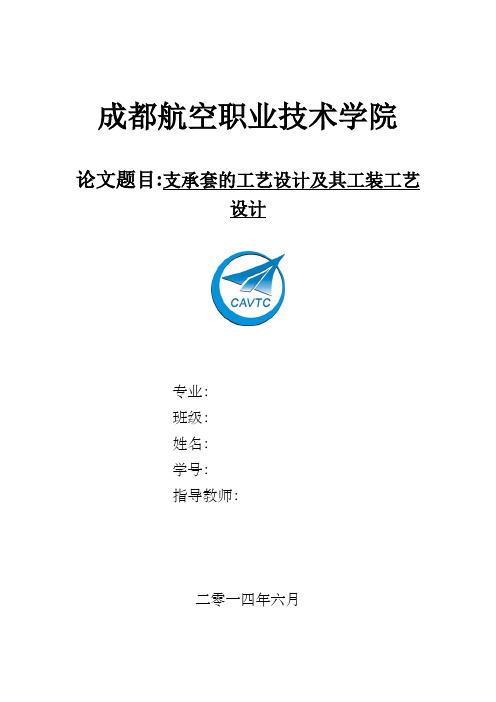
成都航空职业技术学院论文题目:支承套的工艺设计及其工装工艺设计专业:班级:姓名:学号:指导教师:二零一四年六月摘要本次毕业设计为某指定承套零件制造工艺整体方案设计。
其内容包括了支承套零件的二维平面图绘制、三维造型、零件的工艺性分析、工艺线路的制定、各工序安装方案的确信、专用夹具的设计及其工艺规程等内容。
本文对零件的二维、三维图绘制,零件的加工工艺进程,在加工进程工艺装备的选用和设计均做了详细的说明。
其中零件的造型说明论述了零件的特点结构分析、绘制进程简述及画图软件的选用;零件的工艺进程说明了包括零件材料,组成表面,技术条件,特点分析,粗、精基准的确立,工序尺寸的确信,设备及工艺装备的选用,切削用量的确信等;工艺装备的选用说明中,论述了各工序所利用到的夹具,其中包括零件的定位、夹紧方案及夹具各零件的工艺性分析等。
关键词:支承套工艺规程安装方案机构设计AbstractThe graduation project for a specified set of parts Order of the overall manufacturing process design, tooling process includes a two-dimensional plan drawing, 3D modeling, process analysis part of the development process route supporting sets of parts, design and technical rules to determine, for each step of installing a dedicated fixture this paper, the part of the two-dimensional, three-dimensional drawing, parts machining process, in the process of selection and design of process equipment have made a detailed description parts of the descriptiondescribes the characteristics of the shape analysis of structural parts, rendering the process outlined and mapping software selection,Explains part of the process, including parts and materials, the composition of the surface, technical conditions, characteristics analysis, rough, selection, cutting the amount of the fine benchmarks established process to determine the size, equipment and process equipment to selection process equipment description, describes the various processes used to fixture, including the process of analyzing the positioning of parts, clamping solutions and fixtures of each part.Keyword:Support sleeve,Process planning,Installation program,Mechanism Design目录摘要-------------------------------------------------------------------------------------------------------------- 2 Abstract -------------------------------------------------------------------------------------------------------------- 2一引言 ------------------------------------------------------------------------------------------------------------ 6二某支承套零件制造工艺整体方案设计 ---------------------------------------------------------------- 8(一)零件图的绘制和模型创建----------------------------------------------------------------------- 81.零件图的绘制 --------------------------------------------------------------------------------------- 82.三维模型的创建 ----------------------------------------------------------------------------------- 10图草图图旋转 --------------------------------------------------- 12②耳板的创建----------------------------------------------------------------------------------------------- 12图草图图拉深图镜像------------------------------------- 12③耳板孔 ----------------------------------------------------------------------------------------------------- 12图草图图凹槽----------------------------------------------------- 13④旋转槽 ----------------------------------------------------------------------------------------------------- 13图草图图旋转 --------------------------------------------------------------- 13⑤凸台 -------------------------------------------------------------------------------------------------------- 13图草图图拉深 ----------------------------------------------------------------- 14⑥凹槽 -------------------------------------------------------------------------------------------------------- 14图草图图凹槽 ----------------------------------------------------------------- 14⑦孔 ----------------------------------------------------------------------------------------------------------- 14图草图图凹槽-------------------------------------------------------------- 14⑧键槽 -------------------------------------------------------------------------------------------------------- 14图草图图凹槽 --------------------------------------------------- 15⑨凸台 -------------------------------------------------------------------------------------------------------- 15图草图图拉深图阵列------------------------------------- 15⑩零件成形-------------------------------------------------------------------------------------------------- 15图图-------------------------------------------------------------- 16(二)零件大体熟悉与分析------------------------------------------------------------------------- 161.零件概述-------------------------------------------------------------------------------------------- 162.零件的组成与构形 ------------------------------------------------------------------------------- 16图 -------------------------------------------------------------------------------------------------------------- 173.零件工艺性 ---------------------------------------------------------------------------------------- 17图 -------------------------------------------------------------------------------------------------------------- 18图 -------------------------------------------------------------------------------------------------------------- 18(三)零件加工工艺线路及工序内容设计 ------------------------------------------------------ 181.毛坯选择-------------------------------------------------------------------------------------------- 182.加工方式的选择 ---------------------------------------------------------------------------------- 193.工艺进程拟定 ------------------------------------------------------------------------------------- 194.基准选择-------------------------------------------------------------------------------------------- 205.加工余量的确信 ---------------------------------------------------------------------------------- 206.工序尺寸的确信 ---------------------------------------------------------------------------------- 217.切削用量的选择 ---------------------------------------------------------------------------------- 22(四)零件制造工艺装备选择------------------------------------------------------------------------- 231.设备选用-------------------------------------------------------------------------------------------- 232.刀具选用-------------------------------------------------------------------------------------------- 243.夹具选用-------------------------------------------------------------------------------------------- 254.量具选用说明 ------------------------------------------------------------------------------------- 26(五)夹具设计与制造(单件)---------------------------------------------------------------------- 261.专用夹具设计 ------------------------------------------------------------------------------------- 26图 -------------------------------------------------------------------------------------------------------------- 26图 -------------------------------------------------------------------------------------------------------------- 27图 -------------------------------------------------------------------------------------------------------------- 28图 -------------------------------------------------------------------------------------------------------- 302.机构装配-------------------------------------------------------------------------------------------- 303. 工程图的导出------------------------------------------------------------------------------------ 32结论 ----------------------------------------------------------------------------------------------------------------- 34致谢 ----------------------------------------------------------------------------------------------------------------- 35参考文献 ----------------------------------------------------------------------------------------------------------- 36一引言我所在专业是飞机制造技术,学习的课程要紧包括飞机结构、航空发动机等有关航空的知识和机械制造的相关知识,其支撑内容为机械制造。
基于支承轴探究其加工工艺及工装改装 颜凤玲

基于支承轴探究其加工工艺及工装改装颜凤玲摘要:随着市场经济的快速发展,我国现代机械零件加工生产企业也得到了广阔的发展空间,作为机械零件生产中不可缺少的重要组成部分,支承轴加工改装质量的好坏非常重要,不仅影响着机械零件加工生产效益的提升,同时还决定着加工精确度及加工效率的稳定性。
本文主要针对支承轴传统加工工艺及改进后的工艺修整与优化进行了分析,希望能够为支承轴加工工艺的工装改进提供相应的参考借鉴。
关键词:机械加工;支承轴;工装;改进0 引言最近几年我国机械加工制造领域有了非常明显的进步和发展,为了进一步的提升机械设备零件生产的质量,需要全面落实标准化要求,以此还能促进机械设备生产效益的提升。
本文所提到的支承轴机械加工工艺的改进对于优化机械意义重大,因此便需在实际的加工生产过程中进一步提高改进工艺运行优势,通过对多项机械加工作业项目的优化来提高支承轴机械加工实际效果,继而为支承轴机械加工生产提供有利的技术支持。
1 传统机械加工工艺的问题1.1 积累误差的形成机械生产中的零件加工过程难免会遇到这样那样的突发问题,如果处理不当就会引发各种误差问题存在,特别是对于加工工艺复杂的零件而言,其误差发生的几率就会更高一些,对此需要对零件的技术作业加工要求作出全面的优化和调整,以便于符合零件加工基本要求,以此避免零件加工误差的产生。
而现代化零件加工对于加工精确度要求的逐步提升,使传统零件误差处理方法有效性难以保障。
尤其对于细小误差的处理方面,如误差处理效果不佳,则易产生误差累计的情况,继而便易使误差超出规定值。
积累误差的形成对于加工流程相对简单的零件而言,其控制难度较低。
而对于圆形零件的打磨处理则难以有效控制误差的产生,一旦在打磨过程中产生左右两侧弧度不对称情况,则易对零件加工效率及实际效益产生影响,因此在零件加工过程中,误差的产生影响巨大同时无可避免,但对于误差的有效控制却能够进一步降低误差对于零件应用及加工所产生的影响。
支承轴套零件的加工工艺分析

数控加工工艺大作业题目:分析与制定升降台铣床的支承套零件数控加工工艺专业:数控指导老师:刘永利班级:231010姓名:韩悦学号:23101007一、零件图的工艺分析如图所示为升降台铣床的支承套,在两个互相垂直的方向上有多个孔要加工,在加工中心上加工,只需一次安装即可完成。
图为支承套零件图支承轴套的材料为45钢,毛坯选择棒料。
支承套Ø35H7孔对Ø100f9外圆、Ø60mm孔底平面对Ø35H7孔对端面C及端面C对内Ø100f9外圆均有位置精度要求。
为便于在加工中心上定位和夹紧,将Ø100f9外圆、805.0mm尺寸两端面、78mm尺寸上平面均安排在前面工序中由普通机床完成。
其余加工表面(2ר15H7孔、Ø35H7孔、Ø60mm孔、2ר11mm孔、2ר17mm孔、2×M6—6H螺孔)确定在加工中心上一次安装完成。
二、选择加工设备由于全部加工表面都集中在一个面上,只需单工位加工即可完成,故选择立式加工中心,工件一次装夹后可自动完成铣、钻及攻螺纹等工步的加工。
三、拟定加工工艺1)选择加工方法由于毛坯为棒料,因此所有孔都是在实体上加工,为防止钻偏,需先用中心孔钻钻孔正孔,然后再钻孔。
孔Ø35H7及2ר15H7选择铰削作其最终加工方法。
对Ø60的孔,根据孔径精度,孔深尺寸和孔底平面要求,用铣削方法同时完成孔壁和孔底平面的加工。
各加工表面选择的加工方案如下:2ר15H7孔钻中心孔—钻孔—扩孔—铰孔Ø35H7孔钻中心孔—钻孔—粗镗—半精镗—铰孔Ø60孔粗铣—精铣2ר11孔钻中心孔—钻孔2ר17孔锪孔(在Ø11底孔上)2×M6—6H螺孔钻中心孔—钻底孔—孔端倒角—攻螺纹2)确定加工顺序为减少变换工位的辅助时间和工作台分度误差的影响,各个工位上的加工表面在工作台一次分度下按先粗后精的原则加工完毕。
- 1、下载文档前请自行甄别文档内容的完整性,平台不提供额外的编辑、内容补充、找答案等附加服务。
- 2、"仅部分预览"的文档,不可在线预览部分如存在完整性等问题,可反馈申请退款(可完整预览的文档不适用该条件!)。
- 3、如文档侵犯您的权益,请联系客服反馈,我们会尽快为您处理(人工客服工作时间:9:00-18:30)。
通过 以上分 析 , 确 定前 支 承壳 体 的 工 铸 件一 标 批次 号 一划 线 一 粗 本壳 体 结构 比较 复 杂 。 在壳 体 外圈 安 艺 路 线如 下 : 装 边 上 分 布 高 精 度 的定 位 销 孔 和精 度 要 车 第 一 面 一 粗 车 第 二 面一 去 毛 刺 一 清 求不高的螺纹孑 L 及 直径 小且 长度 长 的 交 洗 一 氧 化 一 内腔 气 密 试 验 一 清 洗 一 钻 L 一钻油路孑 L 一 钻油路孑 L 一 叉油 路 孔 ; 壳 体前 面 内 圈是 衬 套安 装 孔 和 孔 一 钻 油 路 孑
安装 结 合 面 , 结合 面 上分 布 着 螺纹 孔 及 交 钻 油 路 孔 一 钻 油 路 孑 L 一 钻 孔 一 钻 油 路 差 。同时 , 在 这 三个 步 骤 之 间按 照一 定 的 技术 文件 要 求 穿 插 氧 化 、 钻 油 叉 油路 孔 ; 内腔小 , 并 与各 油 路 孔 相通 , 且 孔 一 钻 孔 一 钻 孔 一 精 车 第 二 面一 精 车 第 工 艺 原 则 、 加工 时 目视 不可 见 。 各 油路 孑 L 位 置都 呈 空 面 一 车 端 面 一 铣 孔 口一 铣 槽 一 铣 端 间角 度分 布 , 需要 专 用钻 具才 能加 工 ( 有 五 面一 铣 端 面 一 铣 端 面 一 钻 孔 一 铣 安 装 坐标 数控 加 工设 备 的可不 用 ) 。 边一钻铰孑 L 一 镗 孔一 铣 锥 面一 铣槽 一倒 角、 去 毛 刺一 攻 螺 纹 一清 洗 一x光 检 查一 3 . 1 . 2前支承壳体的主要技术要求 :
1引 言
保 持 在发 动机 回转 中心 。 通 过 此工 艺研 究 4 ) 确 定 角 向基 准 ; 5 ) 油路孔的加工 ; 6 ) 精 保 证 零 件 的形 位公 差 。 同时 , 在 这 三个 步 然 骤 之 间按 照 一定 的工 艺原 则 、 技 术 文 件要 找 出适 合 于 加 工 某 机 前 支 承 壳体 这 种 类 车工 序 。首 先用 夹 具定 位 零 件第 一 面 , 型零 件 的 工艺 方法 。 也 可 为其 它相 似件 的 后 精 车第 二 面 , 采用 一 次 装卡 将 这 一端 加 求 穿 插 氧 化 、 钻 油路孔 、 密封 试验 、 铣 加 工尺 寸一 次加 工 出来 。 这 样形 位公 差就 可 工 、 倒 角、 去毛刺 、 攻 螺纹 、 x光 检 查 、 最 终 加 工提 供 宝贵 的经验 。 以依靠 机 床 的精度 来保 证 。 接 下来 反 向装 检 验 、 涂 漆等 对 零件 形 位公 差 没 有 影 响 的 2 项 目概述 精车 第 一 面 , 采 用 了涨 紧夹 具 , 排 工 序 , 保证 零件 符合 设计 图要 求 。 通 过 对零 件 结构 特 点 的分 析 、 材 料 性 卡零 件 , 除 了夹具 与 零件 之 间 的定 位 间 隙 , 使 定 位 通过 现 场对 本 工 艺方 案 的实 施, 确 保 能 的分 析 、 工 艺路 线 的定 制 与 分析 等 几 个 方面 , 加工 出合 格 零 件 , 并 制 定 出 一 条 适 误 差 趋 向 于 … 0 ’ ; 7 ) 孔 系的加工 ; 8 ) 倒角 、 了零 件 的尺 寸精 度 和位 置 精 度 , 工 艺路 线 攻 螺纹 等 工 序 ; 9 ) X光 检 查工 序 ; 安 排 合理 , 在加 工 中进 行 顺 利 。证 明 了本 合 于 此 类 零 件 加 工 的 工 艺 路 线 和 工 艺 方 去毛 刺 、 法, 并应 用 于实 践 。
摘 要 :本 文针 对 某机 前 支承 壳体 单件 的加 工过 程进 行 工 艺分析 . 从 加 工 方案 的确 立 、 设备 的 选择 、 工 艺装 备 的设 计 及 零件 在加 工 中的 受力 情 况等 几个 方面进 行 分析 和讨 论 。找 出了适合 于k _ r - 某机前 支承 壳体这 种类 型零件 的工 艺方 法。 关键 词 : 前 支承 壳体 ; 异形机 匣 ; 推重比; Z M一 2 中图 分类 号 : V 2 3 文 献标 识 码 : A 分散 , 合 理 安排 辅 助 加 工 工 序 , 最 后 拟 定 4工 作 总结 出最 优 的加 工路 线 。 通 过上 述 分析 , 整 个 前 支承 壳 体 的加 前支 承壳 体 是箱 体 机 匣 中 的一 种 , 属 于 中心传 动类 机 匣 。安 装 在压 气 机 前端 , 工艺 程序分 析 : 1 ) 毛坯 选择砂 型铸 件 ; 工过 程 实 际就 是一 个 基 准加 工 、 修 正 或转 用 精 密 螺 栓 固定 在 前 机 匣 整 流 叶 片 下 的 2 ) 安 排 划线 工序 , 分 析 毛 坯余 量 分 布 的正 换 的一个 过程 。 只要 针对 上述 三 个步 骤进 具 体 安 排 工 艺过 程 , 就完全可 以 安 装板 凸耳 上 , 与 中支 承一 起 使 发 动机 轴 确性 , 减 少废 品 的发 生 ; 3 ) 车 加工 精 就是 将复 杂 的过程 进行 简化 。 整
个 前 支 承 壳 体 的 加 工 过 程 实 际 就 是 一 个 基 准 加工 、 修 正 或转 换 的 一个 过 程 。 只要 针 对 上述 三个 步 骤 进行 控 制 , 具 体 安排 工 艺 过 程 ,就 完 全 可 以 保 证 零 件 的 形 位 公
3 . 1 总体 技术 方 案及 实施 过程 与效 果 3 : 1 . 1前 支承 壳 体的 结构 特点
1 O )检 验 工 序 ,确保 零 件 符合 设 计要 求 ; 工 艺方 案 的正 确性 和科 学性 。 1 1 ) 氧化 处 理工 序 。 5经 验 、 问题 与建议 5 . 1经 验 :此零 件工 艺 路线 和 方 案 的 3 . 1 . 5 工艺 路线 的制 定
2 Q 1
Q : Q ( 王)
工 业 技 术
Ch i na Ne w T e c h n o l o g i e s a n d P r o d u c t s
前支承壳体 加工工艺 案例研 究
赵宏亮 杨艳梅
( 沈阳黎 明航 空发动机 ( 集 团) 有 限责任公 司, 辽宁 沈 阳 1 1 0 0 4 3 )