连铸
连铸生产工艺流程
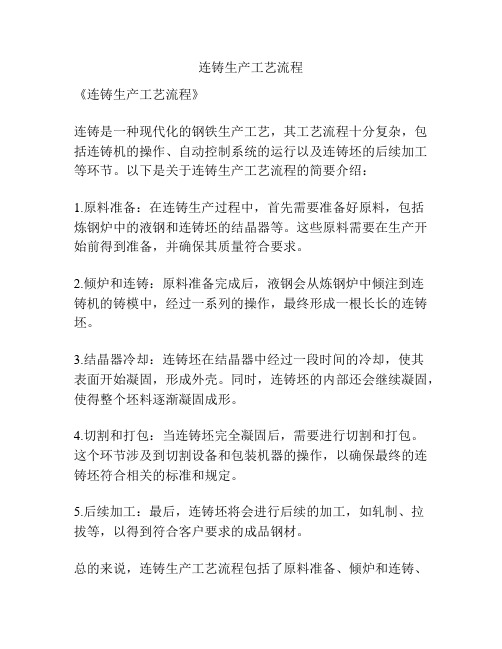
连铸生产工艺流程
《连铸生产工艺流程》
连铸是一种现代化的钢铁生产工艺,其工艺流程十分复杂,包括连铸机的操作、自动控制系统的运行以及连铸坯的后续加工等环节。
以下是关于连铸生产工艺流程的简要介绍:
1.原料准备:在连铸生产过程中,首先需要准备好原料,包括
炼钢炉中的液钢和连铸坯的结晶器等。
这些原料需要在生产开始前得到准备,并确保其质量符合要求。
2.倾炉和连铸:原料准备完成后,液钢会从炼钢炉中倾注到连
铸机的铸模中,经过一系列的操作,最终形成一根长长的连铸坯。
3.结晶器冷却:连铸坯在结晶器中经过一段时间的冷却,使其
表面开始凝固,形成外壳。
同时,连铸坯的内部还会继续凝固,使得整个坯料逐渐凝固成形。
4.切割和打包:当连铸坯完全凝固后,需要进行切割和打包。
这个环节涉及到切割设备和包装机器的操作,以确保最终的连铸坯符合相关的标准和规定。
5.后续加工:最后,连铸坯将会进行后续的加工,如轧制、拉
拔等,以得到符合客户要求的成品钢材。
总的来说,连铸生产工艺流程包括了原料准备、倾炉和连铸、
结晶器冷却、切割和打包以及后续加工等几个主要环节。
通过这些操作,连铸生产工艺可以实现高效、自动化的生产,为钢铁行业的发展做出了重要贡献。
连铸生产工艺流程

连铸生产工艺流程
连铸生产工艺流程是一种将熔化的金属直接铸造成连续条坯的工艺。
它能够实现高效、高质量的铸造,广泛应用于铝、铜等金属的生产中。
以下为连铸生产工艺流程的详细步骤:
首先,将金属料加热至熔点以上,通常会采用电阻加热炉或火焰加热炉进行预热。
接着,将熔化的金属转移到连铸机的浇铸池中。
浇铸池上方有一个配有多个喷嘴的结晶器,喷嘴射出的氮气形成液膜,使熔融金属形成一条连续的柱状流动。
然后,通过结晶器内部的冷却水进行快速冷却。
冷却过程中,金属变为固态,并开始在结晶器内形成一条连续的坯料。
接着,通过压辊系统进行压力控制,将结晶的金属坯料带出结晶器。
通过压辊的调节,可以控制坯料的粗细以及断面形状。
然后,需要对坯料进行进一步的冷却和拉伸。
在连铸机的下游,设有一系列的冷却设备和拉伸设备,用于进一步冷却坯料并控制其尺寸和形状。
最后,通过定尺切割设备,将连续的坯料切割成所需的长度。
切割完成后,坯料可以直接进入下一道工序进行加工。
总结来说,连铸生产工艺流程主要包括熔炼、浇铸、结晶、压
辊控制、冷却拉伸和定尺切割等环节。
这种工艺能够实现连续生产,提高生产效率,同时还能够保证铸造坯料的质量和形状。
连铸的原理

连铸的原理
连铸是一种先进的铸造工艺,它通过在同一设备上连续进行浇铸和凝固,实现了铸坯的一次成型,大大提高了生产效率和产品质量。
连铸的原理主要包括连续浇铸、连续凝固和连续切割三个方面。
首先,连续浇铸是指在连铸设备上通过连续浇注熔融金属,使金属液不间断地流入结晶器中。
这样可以避免浇注过程中的温度变化和氧化,保证了金属液的纯净度和温度稳定性。
同时,连续浇铸还可以减少浇注过程中的气体夹杂和金属液的氧化,提高了产品的内部质量。
其次,连续凝固是指在结晶器中,熔融金属通过连续往复的凝固过程,逐渐形成固态铸坯。
在这个过程中,结晶器内部的冷却系统不断地将热量带走,使金属液逐渐凝固成固态金属。
通过控制结晶器的温度和冷却速度,可以实现对铸坯组织和性能的精确控制,从而获得更高质量的产品。
最后,连续切割是指在连铸设备的出口处,通过连续的切割装置将凝固成型的铸坯切割成所需长度的产品。
这样可以避免传统浇铸中的冷却等待时间,提高了生产效率。
同时,连续切割还可以减少铸坯表面的氧化和变形,保证了产品的表面质量和尺寸精度。
总的来说,连铸的原理是通过连续浇铸、连续凝固和连续切割,实现了铸坯的一次成型,大大提高了生产效率和产品质量。
这种先进的铸造工艺在现代工业生产中得到了广泛应用,为各种金属制品的生产提供了可靠的技术保障。
连铸过程原理及数值模拟

连铸过程原理及数值模拟连铸是一种重要的金属成形工艺,广泛应用于钢铁、铝合金等金属材料的生产和加工中。
连铸过程原理及数值模拟是研究连铸工艺的关键内容,通过对连铸过程的原理分析和数值模拟,可以优化连铸工艺参数,提高产品质量和生产效率。
连铸过程是将熔融金属直接注入到连续运动的铸坯中,通过冷却和凝固过程,将熔融金属转化为固态铸坯。
连铸的基本原理是利用连续运动的铸坯带走热量,使熔融金属迅速凝固,形成连续的固态铸坯。
在连铸过程中,主要包括液相区、液固两相区和固相区三个区域。
在液相区,熔融金属通过连续浇注,填充到铸坯的空腔中。
熔融金属的温度高于固相线,处于液态状态。
随着熔融金属的注入,液相区的长度逐渐增加。
在液固两相区,熔融金属和正在凝固的铸坯同时存在。
由于熔融金属的温度高于固相线,所以熔融金属仍然保持液态。
而铸坯由于受到液相的热量传递,开始逐渐凝固。
在这个区域中,液相区的长度逐渐减小,凝固铸坯的长度逐渐增加。
在固相区,整个铸坯都已经完全凝固。
熔融金属已经完全转化为固态,形成连续的固态铸坯。
在这个区域中,液相区的长度为零,凝固铸坯的长度为整个连铸过程的长度。
为了研究连铸过程的细节和优化连铸工艺参数,数值模拟成为一种重要的方法。
数值模拟是通过数学模型和计算机仿真技术,对连铸过程进行模拟和分析。
数值模拟可以准确地计算连铸过程中的温度场、流场和凝固结构等关键参数,为工艺优化提供科学依据。
在连铸过程的数值模拟中,需要考虑多个物理过程的相互作用。
首先是流体力学过程,包括熔融金属的流动和铸坯带走热量的过程。
其次是热传导过程,包括熔融金属的冷却和凝固过程。
最后是凝固结构演化过程,包括铸坯的晶粒生长和偏析等现象。
为了建立连铸过程的数值模型,需要考虑材料的物理性质、流体力学和热传导方程等方面的参数。
同时,还需要考虑边界条件和初始条件等参数。
通过数值模拟,可以预测连铸过程中的温度分布、流速分布和凝固结构等重要参数,为工艺优化提供指导。
连铸的名词解释
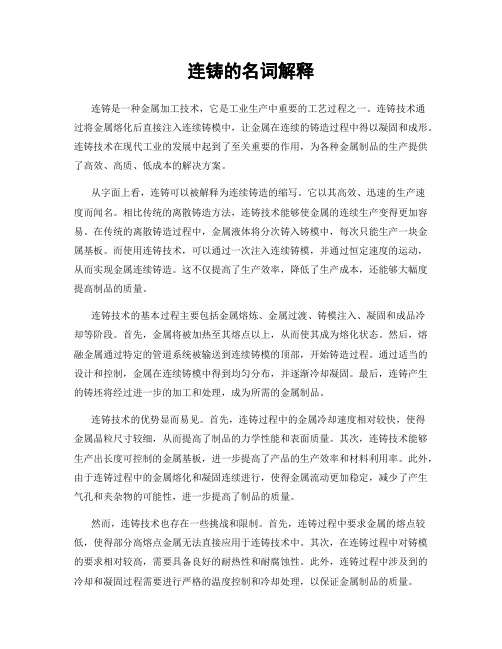
连铸的名词解释连铸是一种金属加工技术,它是工业生产中重要的工艺过程之一。
连铸技术通过将金属熔化后直接注入连续铸模中,让金属在连续的铸造过程中得以凝固和成形。
连铸技术在现代工业的发展中起到了至关重要的作用,为各种金属制品的生产提供了高效、高质、低成本的解决方案。
从字面上看,连铸可以被解释为连续铸造的缩写。
它以其高效、迅速的生产速度而闻名。
相比传统的离散铸造方法,连铸技术能够使金属的连续生产变得更加容易。
在传统的离散铸造过程中,金属液体将分次铸入铸模中,每次只能生产一块金属基板。
而使用连铸技术,可以通过一次注入连续铸模,并通过恒定速度的运动,从而实现金属连续铸造。
这不仅提高了生产效率,降低了生产成本,还能够大幅度提高制品的质量。
连铸技术的基本过程主要包括金属熔炼、金属过渡、铸模注入、凝固和成品冷却等阶段。
首先,金属将被加热至其熔点以上,从而使其成为熔化状态。
然后,熔融金属通过特定的管道系统被输送到连续铸模的顶部,开始铸造过程。
通过适当的设计和控制,金属在连续铸模中得到均匀分布,并逐渐冷却凝固。
最后,连铸产生的铸坯将经过进一步的加工和处理,成为所需的金属制品。
连铸技术的优势显而易见。
首先,连铸过程中的金属冷却速度相对较快,使得金属晶粒尺寸较细,从而提高了制品的力学性能和表面质量。
其次,连铸技术能够生产出长度可控制的金属基板,进一步提高了产品的生产效率和材料利用率。
此外,由于连铸过程中的金属熔化和凝固连续进行,使得金属流动更加稳定,减少了产生气孔和夹杂物的可能性,进一步提高了制品的质量。
然而,连铸技术也存在一些挑战和限制。
首先,连铸过程中要求金属的熔点较低,使得部分高熔点金属无法直接应用于连铸技术中。
其次,在连铸过程中对铸模的要求相对较高,需要具备良好的耐热性和耐腐蚀性。
此外,连铸过程中涉及到的冷却和凝固过程需要进行严格的温度控制和冷却处理,以保证金属制品的质量。
尽管如此,连铸技术在如今的工业生产中扮演了重要的角色。
连铸工艺流程

连铸工艺流程连铸是一种常用的铸造工艺,适用于生产长条状或板状金属材料。
它是通过将熔化的金属直接倒入连续流动的水冷铜板中,使其冷却并形成连续的长条状或板状产品。
连铸工艺具有高效率、低能耗、高品质等优点,广泛应用于钢铁、铝合金等行业。
连铸工艺流程主要包括准备工作、连续浇铸、冷却和切割四个阶段。
首先是准备工作。
这个阶段包括准备熔炉、铜板、铸模、流动水和其他所需设备和材料。
熔炉中加入合适的金属原料,加热使其熔化。
同时,准备好冷却水,并确保其具有足够的流动性和温度适宜。
铜板和铸模是制造连铸机的主要部件,需要进行充分的清洗和检查,以确保表面平整和无缺陷。
接下来是连续浇铸。
将熔化的金属倒入连铸机的铜板中,通过喷头将金属喷向铸模,并使其连续地流动。
连铸机的喷头是一个关键部件,可以调整金属流动的速度和方向,以保证产品的质量。
同时,需要控制好浇注速度和温度,以避免金属过热或过冷,影响产品的性能。
然后是冷却。
在连铸过程中,金属材料与铜板接触,通过快速传热,使金属迅速冷却并凝固。
冷却水通过铜板流过,吸收金属的热量,并保持适宜的温度。
冷却水的流量和温度需要根据不同金属材料进行调整,以确保产品的结晶组织和力学性能。
最后是切割。
冷却后的连铸坯可以根据需要进行切割成适当的长度,以便进一步加工。
切割可以通过割断或切削进行。
割断是指使用切割设备将连铸坯切成所需长度,并去除不良部分。
切削是指使用机械切割工具将连铸坯切割成规定的尺寸和形状。
总之,连铸工艺是一种高效、高品质的铸造工艺,适用于生产长条状或板状金属材料。
其主要流程包括准备工作、连续浇铸、冷却和切割。
通过合理调整浇注速度、温度和冷却设备,可以制造出具有良好结晶组织和优异性能的产品。
连铸工艺的应用范围广泛,为钢铁、铝合金等行业的发展提供了重要的支撑。
炼钢厂连铸工艺流程

炼钢厂连铸工艺流程1.钢水准备:从炼钢炉中输出得到熔化的钢水,然后通过脱氧、温度调节和脱气等工艺处理,得到适合连铸工艺的钢水。
2.连铸结晶器:将处理后的钢水通过倾转、倾倒和挤压等技术,直接浇注到连铸机结晶器中。
结晶器内部有一组多孔结晶器衬套,通过冷却水的循环,将钢水快速冷却并结晶。
3.凝固:钢水在结晶器中快速冷却,开始凝固成为连续铸坯。
凝固过程中,还会通过控制结晶器内的冷却水温度和流量,来调节钢坯的凝固速度和结晶器壁的温度。
4.伸展:连续铸坯凝固后,通过拉伸机构将钢坯从结晶器中拉出,使其变长,同时也能控制钢坯的截面形状。
这个过程中,还会进行坯底冷却,以控制坯底凝固的厚度。
5.切割:钢坯经过拉伸后,通过切割机构将其切断成合适的长度,以供后续工序使用。
6.冷却:切割成合适长度的连续铸坯通过冷却水箱,进行冷却。
冷却的目的是使钢坯的内部和外部温度均匀降低,以便后续的轧制工艺。
7.钢坯调整:冷却后的连续铸坯,根据需要可能需要进行尺寸调整。
这个过程中通常使用钢坯矫直机、切割坯边机等设备,对钢坯进行校直和修边,使其符合轧制工艺要求。
8.轧制:经过调整后的钢坯将被送入炼钢厂的轧机进行轧制。
根据需要,钢坯可能还会经过多道次的轧制和调整。
9.检测:轧制后的产品将进入质检环节,通过各种非破坏性和破坏性检测手段,对产品进行检测,以确保其质量符合要求。
10.成品:经过检测合格后,轧制后的产品成品将根据需求进行打包、标记和存储,以便销售和运输。
综上所述,炼钢厂连铸工艺流程是将熔化的钢水通过连续铸造技术直接浇注到连铸机结晶器中,经过凝固、伸展、切割、冷却、调整、轧制、检测等一系列工艺处理,最终得到质检合格的连续铸坯。
这种工艺流程具有工艺连续、设备高效、产品质量稳定等优点,已被广泛应用于炼钢厂的生产中。
连铸生产工艺

连铸生产工艺
连铸是指采用连续浇铸工艺将熔融金属连续浇铸成长条状的铸件,常用于生产铜、铝等金属材料。
连铸工艺相比传统离散铸造工艺具有高效、节能、高质量等优势,被广泛应用于现代金属材料的生产。
首先,连铸工艺的核心是焊接,由于金属的熔点通常很高,因此需要在高温环境下进行。
在连铸过程中,金属先经过一组预热炉,使其温度达到熔点以上,并保持恒定。
然后,熔融金属经过调漏口进入连铸机的浇注坑,通过直径大小不同的浇口,将金属流注到已经加热和涂有抗粘涂料的铸模中。
接下来,金属在连铸机中由于连铸速度以及冷却系统的作用,逐渐冷却凝固,在冷却过程中逐渐形成金属栅格状的微晶结构。
冷却速度的控制是连铸工艺中至关重要的一环,过快的冷却速度会导致过早的凝固,产生气孔和其他缺陷,而过慢的冷却速度则会影响生产效率。
因此,连铸工艺中通常通过调节冷却水的流量和温度以及调整浇注速度来控制冷却速度。
最后,凝固后的铸坯经过拉伸机进行拉拔,使其变为所需要的尺寸和形状。
拉拔是通过对铸坯施加轴向拉力来实现的,拉拔过程中金属的晶粒结构逐渐细化,从而提高了材料的强度和韧性。
拉拔机通常由一组连续的牵引辊和摩擦刹车组成,牵引辊以恒定的速度运转,将铸坯拉伸成所需尺寸。
在拉拔过程中,还可以通过在线热处理和表面处理,对材料进行进一步的改性和提高其耐腐蚀性。
总之,连铸生产工艺是一种高效、节能的金属材料生产工艺。
通过连续浇注和拉拔,可以大大提高生产效率,减少人工操作和能源消耗,同时还能提高材料质量和性能。
随着技术的不断进步,连铸工艺将继续发展,为金属材料的生产提供更好的解决方案。
连铸原理与工艺
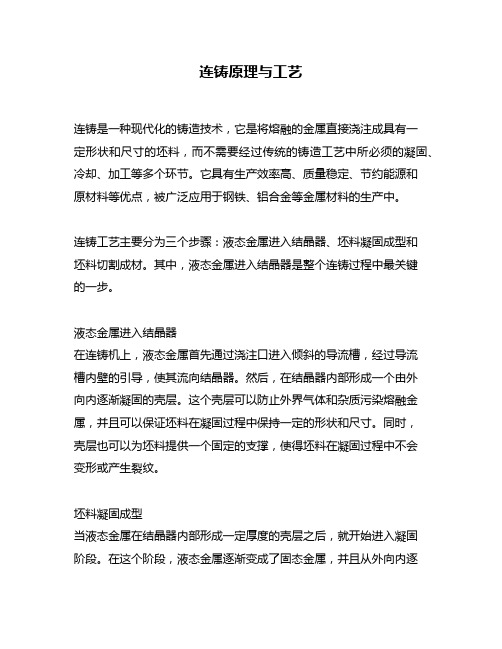
连铸原理与工艺连铸是一种现代化的铸造技术,它是将熔融的金属直接浇注成具有一定形状和尺寸的坯料,而不需要经过传统的铸造工艺中所必须的凝固、冷却、加工等多个环节。
它具有生产效率高、质量稳定、节约能源和原材料等优点,被广泛应用于钢铁、铝合金等金属材料的生产中。
连铸工艺主要分为三个步骤:液态金属进入结晶器、坯料凝固成型和坯料切割成材。
其中,液态金属进入结晶器是整个连铸过程中最关键的一步。
液态金属进入结晶器在连铸机上,液态金属首先通过浇注口进入倾斜的导流槽,经过导流槽内壁的引导,使其流向结晶器。
然后,在结晶器内部形成一个由外向内逐渐凝固的壳层。
这个壳层可以防止外界气体和杂质污染熔融金属,并且可以保证坯料在凝固过程中保持一定的形状和尺寸。
同时,壳层也可以为坯料提供一个固定的支撑,使得坯料在凝固过程中不会变形或产生裂纹。
坯料凝固成型当液态金属在结晶器内部形成一定厚度的壳层之后,就开始进入凝固阶段。
在这个阶段,液态金属逐渐变成了固态金属,并且从外向内逐渐缩小。
同时,由于液态金属的收缩率和晶粒长大率不同,所以在凝固过程中会形成一定数量的热裂纹和气孔。
为了解决这个问题,连铸工艺中采用了多种措施来控制坯料的凝固过程。
例如,在结晶器内部设置冷却水管道来降低壳层温度、使用高效保护气体来防止氧化等。
此外,在连铸工艺中还可以通过调整浇注速度、结晶器倾角、结晶器长度等参数来控制坯料的凝固速度和形状。
坯料切割成材当坯料完全凝固之后,它会被自动切割成一定长度的材料。
在连铸工艺中,切割方式主要分为两种:火焰切割和机械切割。
火焰切割是利用氧炔火焰将坯料加热到一定温度后进行切割,适用于较大尺寸的坯料。
机械切割则是使用钢丝、钢锯等工具将坯料进行切割,适用于较小尺寸的坯料。
总之,连铸工艺是一种高效、节能、环保的现代化铸造技术。
它通过控制液态金属的流动和凝固过程,使得金属材料可以以一种更加稳定和高效的方式生产出来。
同时,在连铸工艺中还可以通过调整参数、优化设备等手段来不断提高产品质量和生产效率,为现代制造业的发展做出了重要贡献。
连铸工艺与设备连铸的工艺流程与设备
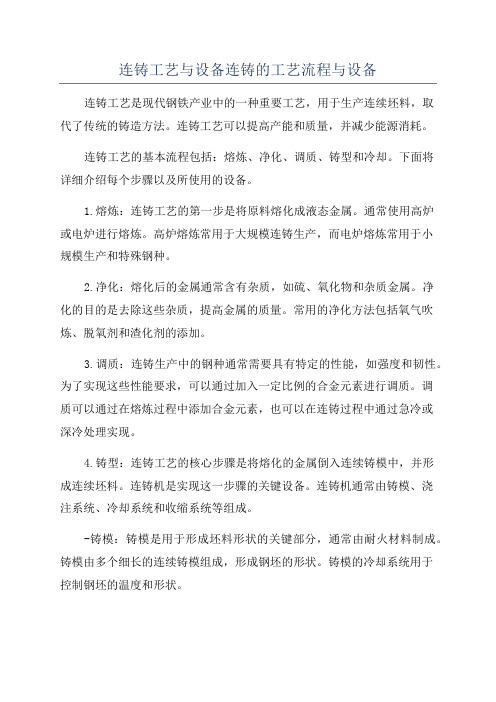
连铸工艺与设备连铸的工艺流程与设备连铸工艺是现代钢铁产业中的一种重要工艺,用于生产连续坯料,取代了传统的铸造方法。
连铸工艺可以提高产能和质量,并减少能源消耗。
连铸工艺的基本流程包括:熔炼、净化、调质、铸型和冷却。
下面将详细介绍每个步骤以及所使用的设备。
1.熔炼:连铸工艺的第一步是将原料熔化成液态金属。
通常使用高炉或电炉进行熔炼。
高炉熔炼常用于大规模连铸生产,而电炉熔炼常用于小规模生产和特殊钢种。
2.净化:熔化后的金属通常含有杂质,如硫、氧化物和杂质金属。
净化的目的是去除这些杂质,提高金属的质量。
常用的净化方法包括氧气吹炼、脱氧剂和渣化剂的添加。
3.调质:连铸生产中的钢种通常需要具有特定的性能,如强度和韧性。
为了实现这些性能要求,可以通过加入一定比例的合金元素进行调质。
调质可以通过在熔炼过程中添加合金元素,也可以在连铸过程中通过急冷或深冷处理实现。
4.铸型:连铸工艺的核心步骤是将熔化的金属倒入连续铸模中,并形成连续坯料。
连铸机是实现这一步骤的关键设备。
连铸机通常由铸模、浇注系统、冷却系统和收缩系统等组成。
-铸模:铸模是用于形成坯料形状的关键部分,通常由耐火材料制成。
铸模由多个细长的连续铸模组成,形成钢坯的形状。
铸模的冷却系统用于控制钢坯的温度和形状。
-浇注系统:浇注系统用于将熔化金属引入铸模,通常由浇注槽、分流器和导流板等组成。
浇注系统的设计和控制是影响连铸质量的重要因素。
-冷却系统:连铸过程中,冷却系统起到冷却钢坯并凝固的作用,以形成坯料。
连铸机的冷却系统通常由冷却水道和冷却喷嘴组成。
-收缩系统:收缩系统用于控制钢坯在冷却过程中的收缩,以避免出现内部缺陷。
收缩系统通常包括伸缩器、定位器和收缩量控制装置。
5.冷却:连铸过程中,钢坯会在铸模和冷却系统中逐渐凝固,并形成连续坯料。
冷却过程中,冷却水道和冷却喷嘴将水喷洒到钢坯上,以加快冷却速度和均匀性。
总结来说,连铸工艺是通过将熔融金属倒入连续铸模中,利用连铸机的浇注系统和冷却系统,控制金属的凝固和收缩过程,最终获得连续坯料。
连铸计算公式大全

连铸计算公式大全连铸(Continuous Casting)是一种金属加工工艺,用于生产连续长度的金属坯料。
在连铸过程中,液态金属被直接铸造成坯料,而不需要通过传统的浇铸过程。
连铸计算涉及到多个方面,包括熔炼过程、铸模设计、冷却和结晶过程等。
以下是一些可能涉及的连铸计算公式的示例:1. 铸坯截面积计算公式:A = L ×W其中:A -铸坯截面积L -铸坯长度W -铸坯宽度2. 铸坯体积计算公式:V = A ×H其中:V -铸坯体积A -铸坯截面积H -铸坯高度3. 结晶器截面积计算公式:A_mold = π×(D/2)²其中:A_mold -结晶器截面积D -结晶器直径4. 结晶器长度计算公式:L_mold = (8 ×V_mold) / (π×D_mold)其中:L_mold -结晶器长度V_mold -结晶器内腔体积D_mold -结晶器内腔直径5. 冷却水流量计算公式:Q = C ×A ×ΔT/Δt其中:Q -冷却水流量C -冷却水比热容A -冷却面积ΔT -冷却前后温度差Δt -时间间隔这些公式只是连铸计算中的一部分,实际生产中还需要考虑其他因素,如钢种、浇铸温度、浇铸速度等。
在实际应用中,需要根据具体生产情况选择合适的计算公式并进行相应参数的调整。
这只是连铸计算中的一小部分公式示例,实际的计算可能涉及到更多的参数和方程,具体取决于金属类型、连铸机型号、操作条件等因素。
在实际应用中,专业的冶金工程师通常会根据具体情况进行计算和优化。
连铸机工作原理
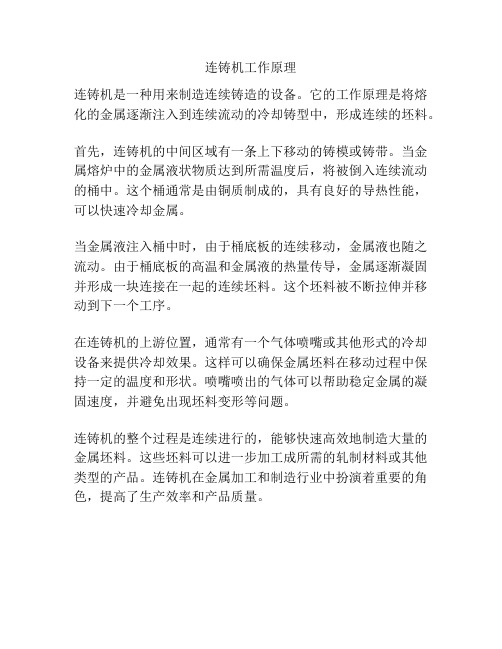
连铸机工作原理
连铸机是一种用来制造连续铸造的设备。
它的工作原理是将熔化的金属逐渐注入到连续流动的冷却铸型中,形成连续的坯料。
首先,连铸机的中间区域有一条上下移动的铸模或铸带。
当金属熔炉中的金属液状物质达到所需温度后,将被倒入连续流动的桶中。
这个桶通常是由铜质制成的,具有良好的导热性能,可以快速冷却金属。
当金属液注入桶中时,由于桶底板的连续移动,金属液也随之流动。
由于桶底板的高温和金属液的热量传导,金属逐渐凝固并形成一块连接在一起的连续坯料。
这个坯料被不断拉伸并移动到下一个工序。
在连铸机的上游位置,通常有一个气体喷嘴或其他形式的冷却设备来提供冷却效果。
这样可以确保金属坯料在移动过程中保持一定的温度和形状。
喷嘴喷出的气体可以帮助稳定金属的凝固速度,并避免出现坯料变形等问题。
连铸机的整个过程是连续进行的,能够快速高效地制造大量的金属坯料。
这些坯料可以进一步加工成所需的轧制材料或其他类型的产品。
连铸机在金属加工和制造行业中扮演着重要的角色,提高了生产效率和产品质量。
连铸工艺要点

连铸工艺要点连铸工艺是指连续铸造技术,是铁合金、钢铁等冶金行业中的一种主要生产工艺。
其工艺特点是连续铸造、高效能、高品质、节能环保等。
下面我们来了解一下连铸工艺的要点。
1. 连铸设备连铸设备是连铸工艺的核心,由铸机、结晶器、引伸器、切割机、输送机等组成。
铸机是整个设备的主体,结晶器是铸机的核心部分,引伸器是为了延长铸坯结晶器内的结晶长度,切割机是将连续铸坯切割成长度符合要求的坯料,输送机将坯料送到后续加工工序。
2. 连铸模具连铸模具是决定铸坯质量和工艺效果的重要因素,也是连铸设备的重要组成部分。
模具材料要求高强度、高温耐用、不易变形。
常用的模具材料有高硅铸铁、高铬铸铁、尿素醛树脂等。
模具结构形式有直立式、倾斜式、水平式等,不同结构形式适用于不同铸造条件。
3. 冷却水系统连铸过程中,冷却水系统起着非常重要的作用。
冷却水系统包括结晶器水口、结晶器壁面、引伸器、切割机等部位的冷却系统。
冷却水系统的稳定性和冷却效果直接影响铸坯的质量。
冷却水的温度、流量、压力等参数的调节需要精细控制。
4. 铸造工艺参数连铸工艺参数的优化对铸坯质量和生产效率有重要影响。
铸造参数包括结晶器冷却、引伸器速度、拉拔速度、切割位置等。
优化铸造参数可以控制铸坯中的缺陷、提高铸坯表面质量、降低成本并提高生产效率。
5. 质量控制质量控制是连铸工艺中的重要环节。
铸坯质量的稳定性和可控性直接影响产品的质量和生产效率。
质量控制包括铸坯表面质量检测、铸坯内部缺陷检测、坯料长度检测等。
不同的质量控制手段需要不同的检测设备和技术支持。
连铸工艺的要点包括连铸设备、连铸模具、冷却水系统、铸造工艺参数和质量控制。
在实际生产中,要根据不同的生产条件和产品要求,综合考虑这些要点,优化工艺流程,提高生产效率和产品质量。
连铸工艺流程

连铸工艺流程
《连铸工艺流程》
连铸工艺是一种现代金属材料生产工艺,它利用连续铸造设备,将熔化的金属直接连续铸造成坯料或板材,省去了传统铸造工艺中的铸型、浇注、凝固和脱模等环节,大大提高了生产效率和质量。
具体来说,连铸工艺流程包括以下几个关键步骤:
1. 熔炼:将原料金属经过熔炼炉的高温熔化,形成熔融金属。
2. 连铸机:熔融金属通过连铸机器,经过喷水冷却,以得到坯料或板材。
连铸机在正常情况下可连续工作数周甚至数月。
3. 切割:将冷却后的坯料或板材进行切割成所需长度。
4. 表面处理:对坯料或板材进行表面处理,以去除氧化层、锈蚀和杂质,得到光洁的表面。
5. 加工:对坯料或板材进行进一步的热处理、冷加工等工艺,以获得所需的最终产品。
连铸工艺流程的优点在于,它能够大幅提高金属材料的生产效率,减少人工干预,降低能源消耗,减少生产废料,提高产品质量和一致性。
因此,在诸如钢铁、铝合金等金属材料的生产中,连铸工艺已成为重要的生产方式。
总的来说,《连铸工艺流程》的不断改进和创新,将为金属材料生产带来更高效、更绿色、更经济的生产方式,对于促进工业制造业的可持续发展具有重要的意义。
连续铸造原理和连铸设备简介
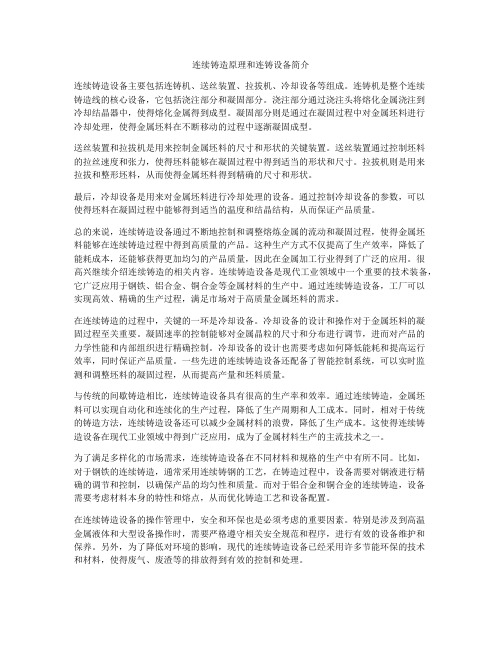
连续铸造原理和连铸设备简介连续铸造设备主要包括连铸机、送丝装置、拉拔机、冷却设备等组成。
连铸机是整个连续铸造线的核心设备,它包括浇注部分和凝固部分。
浇注部分通过浇注头将熔化金属浇注到冷却结晶器中,使得熔化金属得到成型。
凝固部分则是通过在凝固过程中对金属坯料进行冷却处理,使得金属坯料在不断移动的过程中逐渐凝固成型。
送丝装置和拉拔机是用来控制金属坯料的尺寸和形状的关键装置。
送丝装置通过控制坯料的拉丝速度和张力,使得坯料能够在凝固过程中得到适当的形状和尺寸。
拉拔机则是用来拉拔和整形坯料,从而使得金属坯料得到精确的尺寸和形状。
最后,冷却设备是用来对金属坯料进行冷却处理的设备。
通过控制冷却设备的参数,可以使得坯料在凝固过程中能够得到适当的温度和结晶结构,从而保证产品质量。
总的来说,连续铸造设备通过不断地控制和调整熔炼金属的流动和凝固过程,使得金属坯料能够在连续铸造过程中得到高质量的产品。
这种生产方式不仅提高了生产效率,降低了能耗成本,还能够获得更加均匀的产品质量,因此在金属加工行业得到了广泛的应用。
很高兴继续介绍连续铸造的相关内容。
连续铸造设备是现代工业领域中一个重要的技术装备,它广泛应用于钢铁、铝合金、铜合金等金属材料的生产中。
通过连续铸造设备,工厂可以实现高效、精确的生产过程,满足市场对于高质量金属坯料的需求。
在连续铸造的过程中,关键的一环是冷却设备。
冷却设备的设计和操作对于金属坯料的凝固过程至关重要。
凝固速率的控制能够对金属晶粒的尺寸和分布进行调节,进而对产品的力学性能和内部组织进行精确控制。
冷却设备的设计也需要考虑如何降低能耗和提高运行效率,同时保证产品质量。
一些先进的连续铸造设备还配备了智能控制系统,可以实时监测和调整坯料的凝固过程,从而提高产量和坯料质量。
与传统的间歇铸造相比,连续铸造设备具有很高的生产率和效率。
通过连续铸造,金属坯料可以实现自动化和连续化的生产过程,降低了生产周期和人工成本。
连铸连轧知识点

连铸连轧知识点连铸和连轧是金属工业中常见的两个工艺过程。
连铸是指将液态金属连续铸造成坯料的过程,而连轧是指将坯料经过一系列压制和变形操作,连续地轧制成所需尺寸的金属板、带材或线材的过程。
本文将介绍连铸和连轧的基本概念、工艺流程和主要应用。
一、连铸连铸是一种高效的金属铸造技术,具有生产速度快、坯料质量好等优点。
连铸主要应用于钢铁、铜、铝等金属的生产中。
1. 连铸的基本原理连铸的基本原理是将熔融的金属通过连续浇注的方式,直接铸造成连续的坯料。
具体原理如下:首先,将金属熔融至液态,并通过加热设备保持在一定温度范围内;然后,通过连续浇注系统,将熔融金属均匀地注入到连铸结晶器中;在连铸结晶器中,通过冷却剂的作用,使金属迅速凝固,并形成坯料;最后,通过一系列传动装置,将连续产生的坯料送往下游的轧制设备或其他后续处理过程中。
2. 连铸的工艺流程连铸的工艺流程一般包括以下几个关键步骤:(1)冶炼:将矿石等原料经过熔炼处理,得到液态的金属合金;(2)调温:通过加热设备将金属保持在一定的液态温度;(3)连续浇注:通过连续浇注系统,将熔融金属注入到连铸结晶器中;(4)结晶与凝固:在连铸结晶器中,通过冷却剂的作用,使金属迅速凝固,并形成坯料;(5)切割和输送:将连续产生的坯料切割成合适的长度,并送往下游的加工设备。
3. 连铸的应用连铸广泛应用于钢铁、铜、铝等金属的生产中。
在钢铁工业中,连铸可以直接将炼钢铁水铸造成连续坯料,用于后续轧制成钢板和钢材。
在有色金属工业中,连铸可以将液态金属铸造成连续的板材、带材和线材,用于制造电线电缆、汽车零部件等产品。
二、连轧连轧是一种将金属坯料经过多道次的压制和变形操作,连续地轧制成所需尺寸的金属板、带材或线材的工艺过程。
连轧具有高效快速、坯料成形完整等特点,广泛应用于钢铁、有色金属等工业领域。
1. 连轧的基本原理连轧的基本原理是通过一系列的压制和变形操作,使金属坯料逐渐减小厚度、增大长度,并达到所需的尺寸要求。
连铸工艺流程
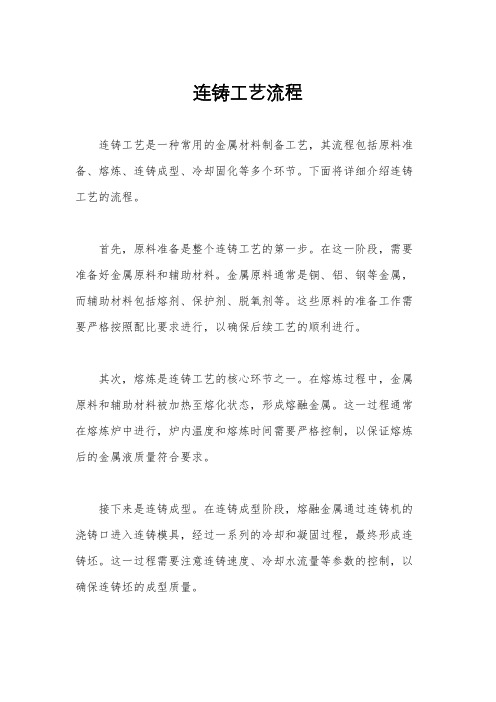
连铸工艺流程
连铸工艺是一种常用的金属材料制备工艺,其流程包括原料准备、熔炼、连铸成型、冷却固化等多个环节。
下面将详细介绍连铸工艺的流程。
首先,原料准备是整个连铸工艺的第一步。
在这一阶段,需要准备好金属原料和辅助材料。
金属原料通常是铜、铝、钢等金属,而辅助材料包括熔剂、保护剂、脱氧剂等。
这些原料的准备工作需要严格按照配比要求进行,以确保后续工艺的顺利进行。
其次,熔炼是连铸工艺的核心环节之一。
在熔炼过程中,金属原料和辅助材料被加热至熔化状态,形成熔融金属。
这一过程通常在熔炼炉中进行,炉内温度和熔炼时间需要严格控制,以保证熔炼后的金属液质量符合要求。
接下来是连铸成型。
在连铸成型阶段,熔融金属通过连铸机的浇铸口进入连铸模具,经过一系列的冷却和凝固过程,最终形成连铸坯。
这一过程需要注意连铸速度、冷却水流量等参数的控制,以确保连铸坯的成型质量。
最后是冷却固化。
连铸坯在成型后需要经过一定时间的冷却固
化过程,使其内部结构逐渐凝固成型。
这一过程需要注意控制冷却
速度和固化时间,以确保连铸坯的内部组织和性能达到要求。
总的来说,连铸工艺流程包括原料准备、熔炼、连铸成型和冷
却固化等多个环节,每个环节都需要严格控制各项参数,以确保最
终产品的质量。
希望本文能够对连铸工艺流程有所了解,谢谢阅读。
连铸工艺流程

连铸工艺流程连铸工艺流程是指将熔化状态的钢水通过连铸机连续铸造成连续铸坯的工艺流程。
该工艺流程主要包括加热与保温、定量浇注、连续铸造、凝固与定形、剪断与冷却等几个过程。
首先,加热与保温是连铸工艺的第一步。
钢水从炉中出来后,需要进行加热,使其达到适宜的铸造温度,一般为1500-1600℃。
然后,需要将加热后的钢水保温一段时间,以保持其熔化状态,一般保温时间为30-60分钟。
接下来是定量浇注过程。
在钢水进行保温的同时,需要将一定的钢水通过浇口定量地注入连铸机的浇注口。
这一过程需要控制好浇注速度和浇注时间,以确保钢水均匀地注入连铸机,避免铸坯出现缺陷。
随后是连续铸造过程。
连铸机将钢水从浇注口引入连铸机的结晶器中,结晶器内壁上涂有一层绝缘材料,以减小结晶器和铸坯之间的传热和冷却速度,使钢水逐渐凝固。
在结晶器中,钢水经过冷却后,开始凝固。
结晶器内还设有冷却水管,以维持适宜的结晶器温度,提高凝固质量。
凝固与定形是连铸工艺的关键过程。
当钢水进入结晶器后,在冷却的作用下,钢水开始凝固形成铸坯。
这一过程需要控制好结晶器的冷却温度和冷却速度,以确保钢水凝固成坯的过程中,铸坯的组织结构和尺寸能达到设计要求。
最后是剪断与冷却过程。
在连铸机的结晶器中,通过剪切装置将凝固成型的连续铸坯切断为定长的铸坯,同时进行冷却,使铸坯温度降低到适宜的水平。
然后,铸坯通过输送设备运输到下一道工序,如轧机进行轧制或其他后续加工工序。
总之,连铸工艺流程是一套将熔化状态的钢水连续铸造成连续铸坯的工艺流程。
该工艺流程主要包括加热与保温、定量浇注、连续铸造、凝固与定形、剪断与冷却等几个过程。
在每个步骤中,需要严格控制各个参数,以确保连铸坯的质量和成型效果。
同时,连铸工艺也具有高效、节能等优点,被广泛应用于钢铁工业。
连续铸造原理和连铸设备简介
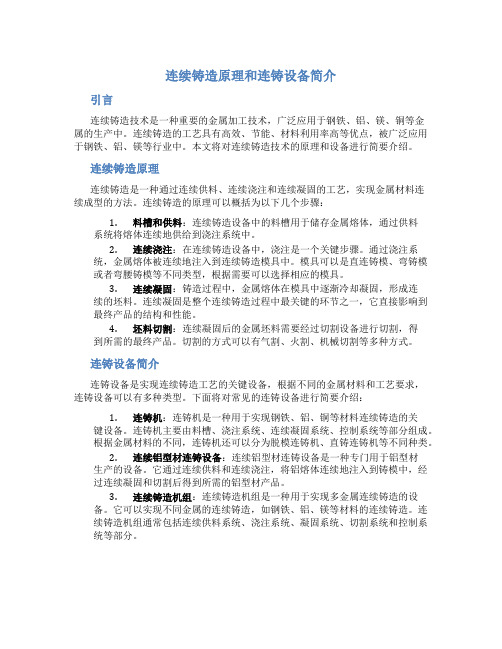
连续铸造原理和连铸设备简介引言连续铸造技术是一种重要的金属加工技术,广泛应用于钢铁、铝、镁、铜等金属的生产中。
连续铸造的工艺具有高效、节能、材料利用率高等优点,被广泛应用于钢铁、铝、镁等行业中。
本文将对连续铸造技术的原理和设备进行简要介绍。
连续铸造原理连续铸造是一种通过连续供料、连续浇注和连续凝固的工艺,实现金属材料连续成型的方法。
连续铸造的原理可以概括为以下几个步骤:1.料槽和供料:连续铸造设备中的料槽用于储存金属熔体,通过供料系统将熔体连续地供给到浇注系统中。
2.连续浇注:在连续铸造设备中,浇注是一个关键步骤。
通过浇注系统,金属熔体被连续地注入到连续铸造模具中。
模具可以是直连铸模、弯铸模或者弯腰铸模等不同类型,根据需要可以选择相应的模具。
3.连续凝固:铸造过程中,金属熔体在模具中逐渐冷却凝固,形成连续的坯料。
连续凝固是整个连续铸造过程中最关键的环节之一,它直接影响到最终产品的结构和性能。
4.坯料切割:连续凝固后的金属坯料需要经过切割设备进行切割,得到所需的最终产品。
切割的方式可以有气割、火割、机械切割等多种方式。
连铸设备简介连铸设备是实现连续铸造工艺的关键设备,根据不同的金属材料和工艺要求,连铸设备可以有多种类型。
下面将对常见的连铸设备进行简要介绍:1.连铸机:连铸机是一种用于实现钢铁、铝、铜等材料连续铸造的关键设备。
连铸机主要由料槽、浇注系统、连续凝固系统、控制系统等部分组成。
根据金属材料的不同,连铸机还可以分为脱模连铸机、直铸连铸机等不同种类。
2.连续铝型材连铸设备:连续铝型材连铸设备是一种专门用于铝型材生产的设备。
它通过连续供料和连续浇注,将铝熔体连续地注入到铸模中,经过连续凝固和切割后得到所需的铝型材产品。
3.连续铸造机组:连续铸造机组是一种用于实现多金属连续铸造的设备。
它可以实现不同金属的连续铸造,如钢铁、铝、镁等材料的连续铸造。
连续铸造机组通常包括连续供料系统、浇注系统、凝固系统、切割系统和控制系统等部分。
连铸工艺流程
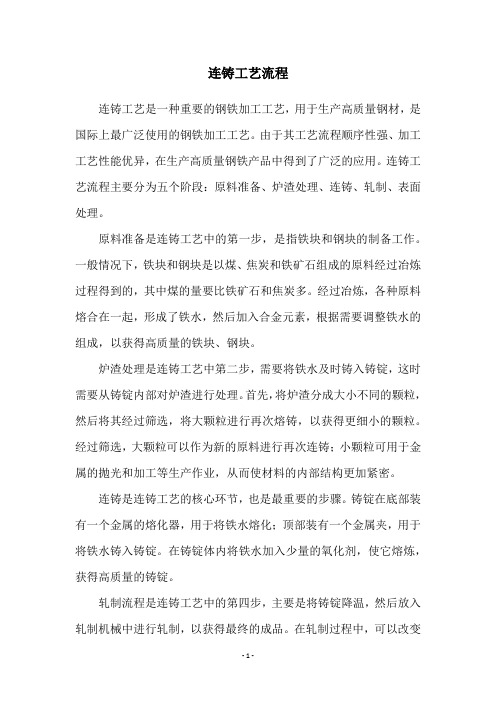
连铸工艺流程连铸工艺是一种重要的钢铁加工工艺,用于生产高质量钢材,是国际上最广泛使用的钢铁加工工艺。
由于其工艺流程顺序性强、加工工艺性能优异,在生产高质量钢铁产品中得到了广泛的应用。
连铸工艺流程主要分为五个阶段:原料准备、炉渣处理、连铸、轧制、表面处理。
原料准备是连铸工艺中的第一步,是指铁块和钢块的制备工作。
一般情况下,铁块和钢块是以煤、焦炭和铁矿石组成的原料经过冶炼过程得到的,其中煤的量要比铁矿石和焦炭多。
经过冶炼,各种原料熔合在一起,形成了铁水,然后加入合金元素,根据需要调整铁水的组成,以获得高质量的铁块、钢块。
炉渣处理是连铸工艺中第二步,需要将铁水及时铸入铸锭,这时需要从铸锭内部对炉渣进行处理。
首先,将炉渣分成大小不同的颗粒,然后将其经过筛选,将大颗粒进行再次熔铸,以获得更细小的颗粒。
经过筛选,大颗粒可以作为新的原料进行再次连铸;小颗粒可用于金属的抛光和加工等生产作业,从而使材料的内部结构更加紧密。
连铸是连铸工艺的核心环节,也是最重要的步骤。
铸锭在底部装有一个金属的熔化器,用于将铁水熔化;顶部装有一个金属夹,用于将铁水铸入铸锭。
在铸锭体内将铁水加入少量的氧化剂,使它熔炼,获得高质量的铸锭。
轧制流程是连铸工艺中的第四步,主要是将铸锭降温,然后放入轧制机械中进行轧制,以获得最终的成品。
在轧制过程中,可以改变板材的厚度和宽度来符合用户的要求,从而获得较高的价值。
表面处理流程是连铸工艺中的最后一步,主要是为了将板材表面处理成最终想要的光洁度,以达到良好的外观效果。
一般表面处理包括抛光、清洗、热处理等操作,通过这些处理,提高板材表面的质量,增强板材的耐腐蚀性,获得更优质的成品。
总之,连铸工艺是一种非常重要的钢铁加工工艺,工艺流程分为原料准备、炉渣处理、连铸、轧制、表面处理五个阶段。
其中原料准备是对煤、焦炭和铁矿石组成的原料经过冶炼过程得到的铁水,炉渣处理是将铁水熔合,连铸则是将上述原料熔合后的铁水铸入铸锭中,轧制是将铸锭降温,表面处理是将板材表面处理成最终想要的光洁度,以达到良好的外观效果。
- 1、下载文档前请自行甄别文档内容的完整性,平台不提供额外的编辑、内容补充、找答案等附加服务。
- 2、"仅部分预览"的文档,不可在线预览部分如存在完整性等问题,可反馈申请退款(可完整预览的文档不适用该条件!)。
- 3、如文档侵犯您的权益,请联系客服反馈,我们会尽快为您处理(人工客服工作时间:9:00-18:30)。
矿产资源开发利用方案编写内容要求及审查大纲
矿产资源开发利用方案编写内容要求及《矿产资源开发利用方案》审查大纲一、概述
㈠矿区位置、隶属关系和企业性质。
如为改扩建矿山, 应说明矿山现状、
特点及存在的主要问题。
㈡编制依据
(1简述项目前期工作进展情况及与有关方面对项目的意向性协议情况。
(2 列出开发利用方案编制所依据的主要基础性资料的名称。
如经储量管理部门认定的矿区地质勘探报告、选矿试验报告、加工利用试验报告、工程地质初评资料、矿区水文资料和供水资料等。
对改、扩建矿山应有生产实际资料, 如矿山总平面现状图、矿床开拓系统图、采场现状图和主要采选设备清单等。
二、矿产品需求现状和预测
㈠该矿产在国内需求情况和市场供应情况
1、矿产品现状及加工利用趋向。
2、国内近、远期的需求量及主要销向预测。
㈡产品价格分析
1、国内矿产品价格现状。
2、矿产品价格稳定性及变化趋势。
三、矿产资源概况
㈠矿区总体概况
1、矿区总体规划情况。
2、矿区矿产资源概况。
3、该设计与矿区总体开发的关系。
㈡该设计项目的资源概况
1、矿床地质及构造特征。
2、矿床开采技术条件及水文地质条件。