零件的分析
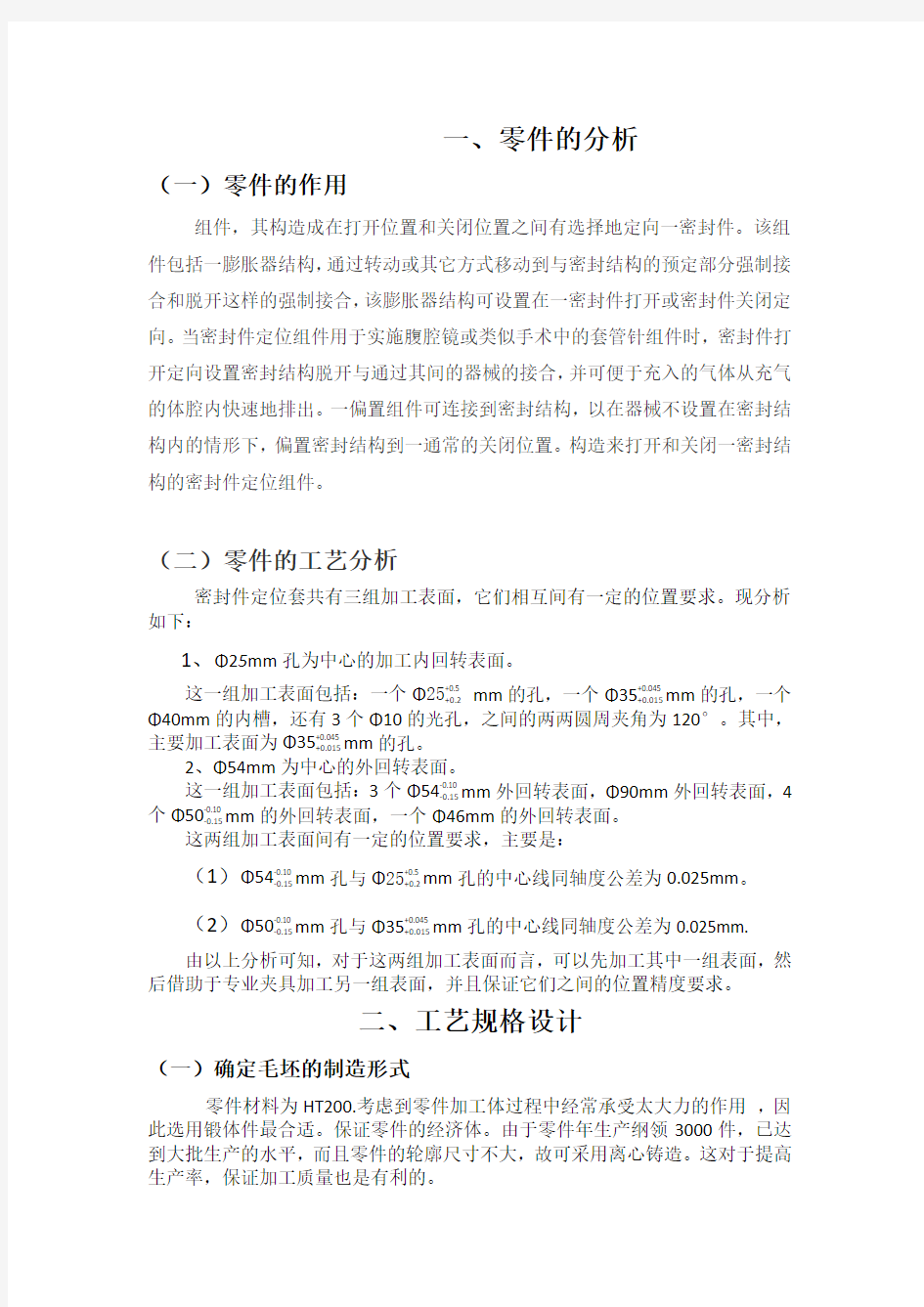
- 1、下载文档前请自行甄别文档内容的完整性,平台不提供额外的编辑、内容补充、找答案等附加服务。
- 2、"仅部分预览"的文档,不可在线预览部分如存在完整性等问题,可反馈申请退款(可完整预览的文档不适用该条件!)。
- 3、如文档侵犯您的权益,请联系客服反馈,我们会尽快为您处理(人工客服工作时间:9:00-18:30)。
一、零件的分析
(一)零件的作用
组件,其构造成在打开位置和关闭位置之间有选择地定向一密封件。该组件包括一膨胀器结构,通过转动或其它方式移动到与密封结构的预定部分强制接合和脱开这样的强制接合,该膨胀器结构可设置在一密封件打开或密封件关闭定向。当密封件定位组件用于实施腹腔镜或类似手术中的套管针组件时,密封件打开定向设置密封结构脱开与通过其间的器械的接合,并可便于充入的气体从充气的体腔内快速地排出。一偏置组件可连接到密封结构,以在器械不设置在密封结构内的情形下,偏置密封结构到一通常的关闭位置。构造来打开和关闭一密封结构的密封件定位组件。
(二)零件的工艺分析
密封件定位套共有三组加工表面,它们相互间有一定的位置要求。现分析如下:
1、 Φ25mm 孔为中心的加工内回转表面。
这一组加工表面包括:一个Φ25+0.5 +0.2 mm 的孔,一个Φ35+0.045 +0.015mm 的孔,一个Φ40mm 的内槽,还有3个Φ10的光孔,之间的两两圆周夹角为120°。其中,主要加工表面为Φ35+0.045 +0.015mm 的孔。
2、Φ54mm 为中心的外回转表面。 这一组加工表面包括:3个Φ54-0.10 -0.15mm 外回转表面,Φ90mm 外回转表面,4个Φ50-0.10 -0.15mm 的外回转表面,一个Φ46mm 的外回转表面。
这两组加工表面间有一定的位置要求,主要是:
(1) Φ54-0.10 -0.15mm 孔与Φ25+0.5
+0.2mm 孔的中心线同轴度公差为0.025mm 。
(2) Φ50-0.10 -0.15mm 孔与Φ35+0.045 +0.015mm 孔的中心线同轴度公差为0.025mm.
由以上分析可知,对于这两组加工表面而言,可以先加工其中一组表面,然后借助于专业夹具加工另一组表面,并且保证它们之间的位置精度要求。
二、工艺规格设计
(一)确定毛坯的制造形式
零件材料为HT200.考虑到零件加工体过程中经常承受太大力的作用 ,因
此选用锻体件最合适。保证零件的经济体。由于零件年生产纲领3000件,已达到大批生产的水平,而且零件的轮廓尺寸不大,故可采用离心铸造。这对于提高生产率,保证加工质量也是有利的。
(二)基面的选择
基面的选择是工艺规程设计中的重要工作之一。基面选择的正确、合理,可以保证加工质量,提高生产效率。否则,就会使加工工艺过程问题百出,严重的还会造成零件大批报废,是生产无法进行。
1.粗基准的选择
对于一般的套类零件而言,以端面体为粗基准是完全合理的,但对零件体而言,则不合理如果以Φ90mm的端面为基准,无法加工它为精基准做准备。故
选用Φ90mm的外圆作为基准,利用三爪定心卡盘,用以消除→
u、
→
z两个自由
度,又因三抓自定心卡盘上有很多类似的V型块,故可以消除→
y、
→
u、
→
z、
→
x,达到完全定位。
错误!未指定书签。错误!未指定书签。错误!未指定书签。错误!未指定书签。
2.精基准的选择
精基准的选择主要应该考虑基准重合的问题。当设计基准与工序基准不重合时,应该进行尺寸换算。
(三)工艺路线制定
制定工艺路线的出发点,应当是使零件的几何形状、尺寸精度以及位置精度等技术要求能得到合理的保证。在生产纲领已经确定为大批量生产的条件下,可以采用万能机床配以专用工。夹具,并尽量使工序集中来提高生产率。除此以外,还应考虑经济效果,以便降低生产成本。
1.工艺路线方案一
工序1:粗车两端面
工序2:半精车Φ90mm的端面及倒角。
工序3:粗车外圆Φ54mm,Φ90mm
工序4:半精车Φ54mm的外圆
工序5:粗车Φ35mm Φ25mm的两个内孔
工序6:镗40mm的内槽
工序7:精镗Φ35mm Φ25mm的两内孔
工序8:割四个槽
工序9:磨削Φ54mm的外圆
工序10:钻3xΦ10的孔
工序11:终检
2.工艺路线方案二:
工序1:粗车外圆
工序2:Φ90mm、54mm
工序3:精车外圆Φ54mm
工序4:车两端面
工序5:粗车Φ35mm Φ25mm的两个内孔
工序6:镗40mm的内槽
工序7:精镗Φ35mm Φ25mm的两内孔
工序8:割4个宽3mm深3mm的槽
工序9:钻孔
工序10:磨削Φ50的外圆表面
工序11:钻3xΦ10的孔
工序12:终检
3.工艺方案的比较与分析
上述两个工艺方案的特点在于:方案一与方案二均采用一面二孔为精基面加工Φ10mm的孔和外圆,而方案一是直接从铸件外圆粗车一刀,然后在作为基准,加工孔和外圆。显然方案二的粗基准的选择比方案一要好,但方案一的工时稍短些,更为经济,总结两种方案的优缺利弊,集两方案之所长,而重新编排,确定具体工序如下所示:
工序1:粗车一端面和一头外圆。
工序2:粗车另一端面和另一外圆。以粗车后的端为粗精准。
工序3 : 半精车法兰盘端面。
工序4:粗镗Φ25mm和Φ35mm的孔。
工序5:半精镗Φ25mm和Φ35mm的两孔。
工序6:精镗Φ25mm和Φ35mm的两孔。
工序7:粗车Φ54mm的外圆,以工序3、4、5、6为基准。
工序8:精车Φ54mm的外圆
工序9:割Φ50和Φ46的槽
工序10:钳工划线,划3xΦ10孔的中心位置
工序11:钻3x12mm的孔
工序12:磨削加工和的外圆表面
工序13:检验
工序14:入库
以上加工方案大致看来还是合理的的。但通过仔细考虑零件的技术要求以及可能采用的加工手段之后,知上述工艺路线中,是这样拟定的。采用基准重合,即保证设计基准与工艺基准相重合。若违反了基准重合原则,则产生基准不重合误差,甚至会因超差而报废的后果。为了解决这些问题,原有的加工路线仍可大致保持不变,采用合理的装夹,最后的加工路线确定如下: