第四章 烧结过程燃烧与传热
第四章 烧结过程燃烧与传热

(5)、实际燃烧产物量
4.1 烧结过程燃料燃烧基本原理
(一)气体燃料燃烧的热力学
(6)、燃烧温度 理论燃烧温度
t
i总 Cp
Q q 燃 q空 C p V
理论燃烧温度通常要比冶金炉内的实际温度高出10~25% 平衡燃烧温度
4.1 烧结过程燃料燃烧基本原理
(二)固体燃料燃烧的热力学
第四章 烧结过程燃烧与热量传输规律
4.1 烧结过程燃料燃烧基本原理 4.2 烧结料层中燃烧带的特性分析
4.3 固体燃料特性及用量对烧结过程的影响
4.4 烧结料层中的温度分布及蓄热
4.5 烧结过程传热规律及应用
4.6 烧结节能的主要途径及措施
4.1 烧结过程燃料燃烧基本原理
(一)气体燃料燃烧的热力学
4.5 烧结过程传热规律及应用
(3)传热规律在烧结中的应用 ②传热速度及燃烧速度对产量的影响
垂直烧结速度 台时产量
V
H t
mm/min
q 60 B L V
t/h
烧结料层中的温度最高点的移动速度,它实际上反映了 料层中碳燃烧带的移动速度和燃烧带下部热传递速度
试验表明,当炭用量一定时,垂直烧结速度主要由热传 递速度决定
4.4 烧结料层中的温度分布及蓄热
(3)烧结过程的“自动蓄热现象”
无固体燃料 烧结料层中热平衡图
有固体燃料
沿烧结料层高度蓄热的 变化图
4.4 烧结料层中的温度分布及蓄热
(4)烧结生产中对“自动蓄热现象”扬长避短的技术对策
• 扬长
厚料层烧结 料层高度为180~220mm时,自动蓄热率为 35~45%;料层高度为400mm时,自动蓄热 率为65%; 基于烧结自动蓄热原理的厚料层烧结技术 ,为降低固体燃料提供了可能,也为低温烧 结技术创造了有利条件。同时,对改善烧结 矿质量亦有好处。
烧结第四章2

耗较少的情况下获得必要的高温。
武汉工程大学本科生课程
润滑作用
水分子覆盖在矿粉颗粒表面,起类似润滑
剂的作用,降低表面粗糙度,减少气流阻力。
武汉工程大学本科生课程
助燃作用
固体燃料在完全干燥的混合料中燃烧缓慢
根据CO和C的链式燃烧机理,要求火焰中有一 定含量H+和OH-,混合料适当加湿是必要的。 (水煤气反应→C+H2O=H2+CO)
1 1 Pk lg ( ) r1 r2
武汉工程大学本科生课程
导热作用
水的导热系数为130-400kJ/m2·· h ℃,
矿石的导热系数为0. 60kJ/m 2· ℃ h·
水改善了烧结料的导热性,料层中的热交换
条件好,有利于使燃烧带限制在较窄的范围内,减
少了烧结过程中料层的阻力,同时保证了在燃料消
混合料的适宜水分是根据原料的性质和粒度组成来确定的。
物料粒度越细、比表面积越大,所需适宜水分越高。 原料类型:表面松散多孔的褐铁矿烧结时所需水量达20%, 而致密的磁铁矿烧结时适宜的水量为6%~9%。最适宜的水分
范围很小,超过±0.5时,对混合料的成球性产生显著影响。
当烧结过程开始后,在料层的不同高度和不同的烧结阶段
武汉工程大学本科生课程
(2) 水分在烧结过程中的作用
制粒作用、导热作用、润滑作用、助燃作用
武汉工程大学本科生课程
制粒作用
水在混合料粒子间产生毛细力,在混合料的滚
动过程中互相接触而靠紧,制成小球粒,以改善料
层的透气性;
武汉工程大学本科生课程
两个大小相同球形颗粒之间形成-个双凹透镜形的液体连 接桥。由于它的侧面是凹凸形的、所以具有两种曲率半径r1和 r2。根据拉普拉斯公式:
无机材料科学基础《烧结》知识点

(1)常压烧结:又称无压烧结。
属于在大气压条件下坯体自由烧结的过程。
在无外加动力下材料开始烧结,温度一般达到材料的熔点0.5-0.8即可。
在此温度下固相烧结能引起足够原子扩散,液相烧结可促使液相形成或由化学反应产生液相促进扩散和粘滞流动的发生。
常压烧结中准确制定烧成曲线至关重要。
合适的升温制度方能保证制品减少开裂与结构缺陷现象,提高成品率。
(2)热压烧结与热等静压烧结:热压烧结指在烧成过程中施加一定的压力(在10~40MPa),促使材料加速流动、重排与致密化。
采用热压烧结方法一般比常压烧结温度低100ºC左右,主要根据不同制品及有无液相生成而异。
热压烧结采用预成型或将粉料直接装在模内,工艺方法较简单。
该烧结法制品密度高,理论密度可达99%,制品性能优良。
不过此烧结法不易生产形状复杂制品,烧结生产规模较小,成本高。
作为陶瓷烧结手段,利用来自于表面能的表面应力而达到致密化的常压烧结法虽是一般常用的方法,但是,不依赖于表面应力,而在高温下借助于外压的方法,也是可以采用的。
这就是称为热压法的烧结方法。
广义来说,在加压下进行烧结的方法包括所有这类方法,超高压烧结和热等静压(HIP)烧结也属于这类方法。
不过,一般都作为在高温下施加单轴压力进行烧结的方法来理解。
其基本结构示于图1。
首先,制备粉体试料,置于模型中,在规定温度下加热、加压,获得烧结体。
由于下述原因而采用这种方法:(1)烧结温度降低;(2)烧结速度提高;(3)使难烧结物质达到致密化。
因为能够在颗粒成长或重新结晶不大可能进行的温度范围达到致密化,所以,可获得由微小晶粒构成的高强度、高密度烧结体。
图2所示,是热压对陶瓷致密化影响效果之一例。
将热压作为制造制品的手段而加以利用的实例有:氧化铝、铁氧体、碳化硼、氮化硼等工程陶瓷。
连续热压烧结生产效率高,但设备与模具费用较高,又不利于过高过厚制品的烧制。
热等静压烧结可克服上述弊缺,适合形状复杂制品生产。
烧结物理化学过程

烧结物理化学过程烧结过程是许多物理化学变化的综合过程。
这个过程不仅错综复杂,而且瞬息万变,在几分钟甚至几秒钟内,烧结料就因强烈的热交换而从70℃以下被加热到1200~1400℃,与此同时,它还要从固相中产生液相,然后液相又被迅速冷却而凝固。
这些物理化学变化包括:1>、燃料的燃烧和热交换;2>、水分的蒸发及冷凝;3>、碳酸盐的分解,燃料中挥发分的挥发;4>、铁矿物的氧化、还原与分解;5>、硫化物的氧化和去除;6>、固相间的反应与液相生成;7>、液相的冷却凝结和烧结矿的再氧化等。
第一节燃料的燃烧和热交换一、烧结矿生产使用的燃料烧结生产使用的燃料分为点火燃料和烧结燃料两种。
1、点火燃料现在烧结使用的点火燃料有气体燃料(高炉煤气、焦炉煤气、发生炉煤气和天然气等)和液体燃料(重油)两种,发生炉煤气在这里不再介绍,因固体燃料已经不再使用,在这里也不做介绍。
⑴、气体燃料:①、高炉煤气高炉煤气是高炉冶炼时的一种副产品。
高炉每炼一吨生铁可以获得3500~4000米3的高炉煤气。
其成分随冶炼时所采用的燃料种类及高炉操作条件而不同。
一般含有大量氮、二氧化碳等气体(约占63~70%)。
因此,它的发热量不高,约为850~1100千卡/标米3(其成分见表2-1),若不经过预热,高炉煤气燃烧温度达不到1250,高炉煤气中一般含尘量为50~80毫克/米3,所以必须除尘后才能应用。
做为烧结点火用的煤气含尘量不应大于30毫克/米3,经过除尘后高炉煤气含尘量可以降至5~20毫克/米3,煤气温度在40℃以下。
输送到烧结厂的煤气压力一般为300毫米水柱左右。
②、焦炉煤气焦炉煤气是炼焦过程产生的副产品。
平均每吨干煤炼焦时可产生320米3的焦炉煤气,约占全部产品的17.6%,经过洗涤后的煤气含焦油量为0.00~0.02克/标米3,用于烧结的焦炉煤气的发热量为4000千卡/标米3左右(其成分见表2-2)。
烧结过程的三个阶段
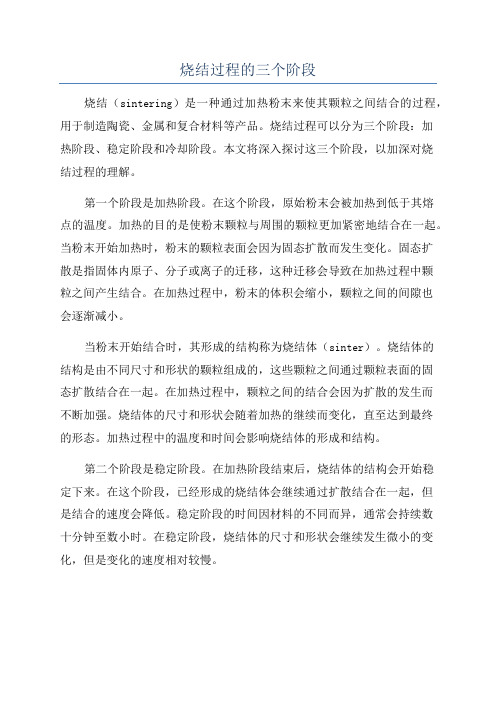
烧结过程的三个阶段烧结(sintering)是一种通过加热粉末来使其颗粒之间结合的过程,用于制造陶瓷、金属和复合材料等产品。
烧结过程可以分为三个阶段:加热阶段、稳定阶段和冷却阶段。
本文将深入探讨这三个阶段,以加深对烧结过程的理解。
第一个阶段是加热阶段。
在这个阶段,原始粉末会被加热到低于其熔点的温度。
加热的目的是使粉末颗粒与周围的颗粒更加紧密地结合在一起。
当粉末开始加热时,粉末的颗粒表面会因为固态扩散而发生变化。
固态扩散是指固体内原子、分子或离子的迁移,这种迁移会导致在加热过程中颗粒之间产生结合。
在加热过程中,粉末的体积会缩小,颗粒之间的间隙也会逐渐减小。
当粉末开始结合时,其形成的结构称为烧结体(sinter)。
烧结体的结构是由不同尺寸和形状的颗粒组成的,这些颗粒之间通过颗粒表面的固态扩散结合在一起。
在加热过程中,颗粒之间的结合会因为扩散的发生而不断加强。
烧结体的尺寸和形状会随着加热的继续而变化,直至达到最终的形态。
加热过程中的温度和时间会影响烧结体的形成和结构。
第二个阶段是稳定阶段。
在加热阶段结束后,烧结体的结构会开始稳定下来。
在这个阶段,已经形成的烧结体会继续通过扩散结合在一起,但是结合的速度会降低。
稳定阶段的时间因材料的不同而异,通常会持续数十分钟至数小时。
在稳定阶段,烧结体的尺寸和形状会继续发生微小的变化,但是变化的速度相对较慢。
稳定阶段的主要目的是确保烧结体的稳定性和一致性。
稳定阶段的结束标志是燃料在烧结体中完全燃尽。
当燃料燃尽时,烧结体的温度会开始降低,以进入第三个阶段。
第三个阶段是冷却阶段。
在冷却阶段,加热源会被移除,并且烧结体会开始冷却。
烧结体的冷却速度会影响其最终的性能和结构。
如果冷却速度过快,可能会导致烧结体的内部产生应力,从而引起开裂或变形。
因此,冷却过程需要在控制的条件下进行,以确保烧结体的质量。
综上所述,烧结过程的三个阶段是加热阶段、稳定阶段和冷却阶段。
加热阶段是使粉末颗粒结合的起始阶段,通过固态扩散来形成烧结体。
第四章 烧结理论-2

再结晶后晶粒尺寸d f d f = d / f 要发生晶粒长大: d f >d0
d/d0 =d/df =f =0.1 d、d0 —孔隙、原始晶粒(颗粒)尺寸
f—孔隙体积分数
f<0.1才发生晶粒长大
School of Materials Science and Engineering
School of Materials Science and Engineering
一、 烧结的基本过程(烧结阶段的划分) 1. 烧结过程的现象 (1)辅助添加剂的排除(蒸发与分解) →形成内压 →若内压超过颗粒间的结合强 度 →膨胀, 起泡或开裂等 →废品
School of Materials Science and Engineering
School of Materials Science and Engineering
一、无限互溶多元系固相烧结
无限互溶:两种或两种以上组元在固态和液态下都能以 任意成分互溶。
简单的二元互溶系:Fe-Ni、Cu-Ni、Cu-Ag、 Co-Ni、Cu-Au、W-Mo……
烧结的本质:合金化(扩散均匀化Homogenization) 遵从固相扩散的一般规律
r=3nm,接触压力为817MPa r=6nm,接触压力为408MPa r小于1.5nm,为排斥力
School of Materials Science and Engineering
(2)烧结颈形成与长大(neck growth)
前期的特征:形成连续的孔隙网络,孔隙表面光滑化; 后期的特征:孔隙进一步缩小,网络坍塌并且晶界发生
School of Materials Science and Engineering
烧结热力学
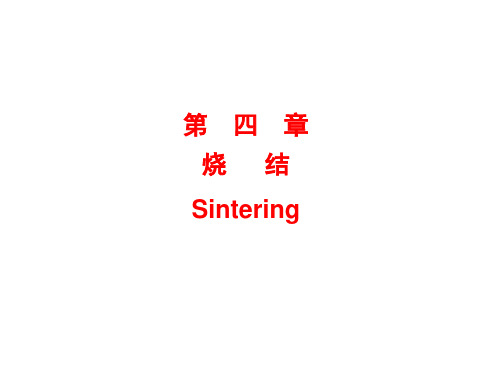
应发生的可能性,而不问其现实性,只指出反应的方向、变化前后的状
态,而不能得出变化的速率。 烧结热力学:用来判断金属粉末在烧结过程中能否粘结在一起的热力学。对于
某些微细金属粉末(羰基铁粉),只要没有氧化,在室温条件下保存也会有粘结
或结块的倾向。这是一种自发过程,说明粉末体稳定性差,并且是一种不可逆过 程,原因是粉末体比同一物质的块状材料具有多余的能量,这部分能量成为烧结 过程的原动力。
式中γ——表面张力; ρ——烧结颈的曲率半径; “-”表示作用于曲颈面上的应力是张力。
图4-3烧结的两球模型
从图可看出,由于张力方向朝外,使烧结颈扩大,随着烧结颈的扩 大,负曲率半径的绝对值也增大,说明烧结动力σ减小。
第四章烧结 b.烧结原动力公式:
Cv
Cv0
kT 2
M——由粉末颗粒大小决定的指数项。
上式在x/R小于0.3有效,其中,n、m、B值取决于物质的迁移机构,
第四章烧结 Ⅰ粘性流动机构 粘性流动是由于在接触颈部表面张力的作用产生的表面应力作用所引
结; 液相烧结:为了生产高密度制品,在粉末中加入易熔组元,以便其在烧
结时成为液相,因液相的存在可保证烧结制品孔隙很少,甚至
没有孔隙。
第四章烧结
1.烧结过程的热力学 (1)烧结热力学 热力学主要是从能量转化的观点来研究物质的热性质,它揭示了能量从 一种形式转换为另一种形式时遵从的宏观规律。 热力学主要研究某一变化在一定条件下能否发生,若能发生,其方向和 限度如何,而无法解释其发生的道理,也不可能预测实际产量,只预测反
总是向着熵增加的方向进行,当熵到达最大值时,系统到达平衡态。
熵的定义: ds
Q
T
第四章烧结 (2)烧结的基本过程 a.强度提高
烧结 原理

烧结原理
烧结是一种将金属或非金属粉末通过热处理使其结合变硬的工艺。
它广泛应用于制造陶瓷、金属件和复合材料等产品。
烧结的原理是将粉末在高温下加热,使其表面熔化并黏合在一起。
在烧结过程中,粉末颗粒之间发生热扩散,使得颗粒接触面积增大。
随着温度升高,金属或非金属颗粒之间的原子迁移速度增加,有利于形成更密实的结合。
同时,由于粉末之间存在表面张力,烧结过程中颗粒表面逐渐熔化并形成颗粒间的接触点。
烧结的过程分为初烧结和返炉烧结两个阶段。
初烧结阶段,通过升高温度使颗粒间的结合更紧密,但仍然存在空隙。
返炉烧结阶段是在初烧结的基础上继续加热并施加压力,以进一步减小颗粒间的空隙,达到更高的密度和硬度。
烧结工艺的优势包括高材料利用率、高生产效率和良好的产品均匀性。
同时,烧结还可以用于制造复杂形状的产品,如陶瓷模具和金属零件。
然而,烧结过程中也存在一些问题,例如颗粒间的烧结不均匀、气孔和缺陷的产生等,这些问题需要在工艺设计和优化中加以解决。
总之,烧结是一种通过高温加热将粉末熔结在一起的工艺。
通过烧结,可以制造出高密度、硬度和耐磨的材料,广泛应用于各个领域。
烧结过程的理论基础

烧结过程的理论基础烧结是一种通过高温和压力将细粉状材料压制成成型体的加工方法。
在烧结过程中,粉末颗粒之间发生了部分熔融、扩散、结合和收缩现象,最终形成了密实的、具有一定机械强度和结构稳定性的成型体。
烧结过程的理论基础主要涉及燃烧理论、传热理论、材料科学等方面的知识。
1.燃烧理论烧结过程中常用的燃烧方式包括气相燃烧、固相燃烧和液相燃烧。
在燃烧过程中,燃料与氧化剂反应产生高温高能的燃烧产物,为烧结提供了必要的热能。
燃烧产物的温度越高,烧结过程中的热传递效果越好,有利于颗粒间的结合和收缩。
2.传热理论热传递是烧结过程中的一个重要环节。
热传递可以通过传导、对流和辐射等方式进行。
传导是指热量通过颗粒之间或颗粒内部的分子振动和传递,对于高温下的烧结过程尤为重要。
对流是指在气体或液体中,通过流体的对流传导热量,对于烧结中的气体流动和温度分布具有重要影响。
辐射是指物体表面的热能以电磁波的形式辐射出去,对于高温烧结具有显著效果。
3.材料科学烧结过程中,粉末颗粒之间的结合主要是通过扩散和熔融发生的。
扩散是指原子或分子在固体中由高浓度区向低浓度区传递的过程,是粉末颗粒烧结过程中结合的主要方式。
熔融是指粉末颗粒在高温下部分熔化,形成液相,通过液相的黏结作用形成连续的成型体。
材料科学中的物理化学性质、晶体学、材料力学等知识对于理解和控制烧结过程中的结合机制和力学性能具有重要意义。
总之,烧结过程的理论基础涉及燃烧理论、传热理论和材料科学等多个方面的知识。
这些理论和原理的深入研究和应用,可以帮助理解烧结过程中颗粒的结合机制、热传递现象以及成型体的力学性能,为烧结工艺和材料应用提供理论指导。
烧结过程燃烧与传热

4.2 烧结料层中燃烧带的特性分析
(一)烧结过程燃烧带厚度的计算
I0 ut 0 6
nd ln(CO / CH ) 2(1 m) (1f 2f )(1 barctg
1
)
b
b m (1 V) T V
燃烧带的宽度是由燃料粒的直径d,空气流速ω,原始气体中的氧的浓 度CH,料层的透气性质m及n,以及系数b来决定。
(2)影响燃烧比的因素有: ①燃料粒度和用量; ②料层负压大小; ③空气过剩系数; ④料层高度和返矿量。
一般燃烧废气中平均含CO1~2%,热量损失占总热量的10~25%。
4.3 固体燃料特性对烧结过程的影响
(1)固体燃料的粒度
烧结粉矿(-8mm):1~2mm适宜 烧结精矿(-1mm):0.5~3mm适宜
4.1 烧结过程燃料燃烧基本原理
(一)气体燃料燃烧的热力学
(2)、主要煤气成分燃烧的热力学 主要成分:CO、H2、CH4
离解:
转化:
总反应:
4.1 烧结过程燃料燃烧基本原理
(一)气体燃料燃烧的热ቤተ መጻሕፍቲ ባይዱ学
(3)、气体燃烧发热量的计算
(4)、气体燃烧理论和实际空气需要量
过剩空气系数,人工操作时取1.15~1.20,自动操作取1.05~1.10
③一般,燃烧带温度,即分布曲线上 的最高点温度随着烧结过程的进行有 所上升,这主要由于料层的蓄热作用。
1-燃烧带,2-预热干燥带,3-水分冷凝带,4-铺底料,5-烧结矿带
t (℃) -Δp (mmH2O)
烧结负压及料层温度的变化情况
1800
1500
1200
900
600
300
z1
0
0
5
烧结过程概述
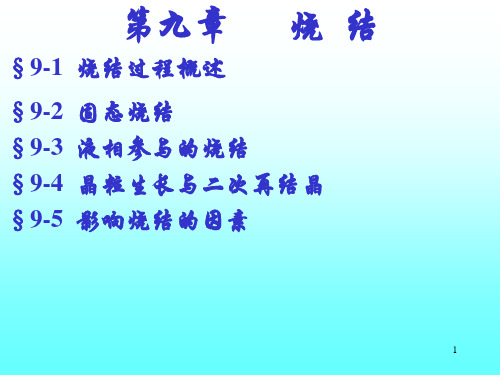
[Cn ] exp(
G f kT
)
) [C0 ] exp( ) kT
G f kT
[Ct ] exp(
G f kT
) [C0 ] exp( ) kT
15
若(ζΩ)/kT<<1,按级数展开: exp( ) 1 exp( ) 1 ; kT kT kT kT
[C0 ] exp(
——无应力区的空位浓度
D空
D* C0
19
dV D * 2C0 2D * ( 2 )A A 2 dt C0 kT kT
将ρ=x2/2r,A=πx3/r代入上式得: dV D * 8r dt kTx
x 4 V 2r
球形颗粒连接处曲率半径ρ和接触颈部半径x之间的开尔文公式:
P M 1 1 1 ln ( ) P0 dRT x
P1——曲率半径为ρ处的蒸气压; P0——球形颗粒表面的蒸气压; γ——表面张力;d——密度; M——分子量; x— —接触颈部半径; ρ ——颈部表面曲率半径
当压力差ΔP=P0-P1很小时,且x>>ρ,
主要传质方式有:蒸发-凝聚;扩散;塑性流变。
一.蒸发-凝聚传质(如图) 在球形颗粒表面有一正曲率半径,在 二个颗粒连接处有一小的负曲率半径 的颈部。
P 2M 根据开尔文公式: ln P0 dRTr
质点从凸表面蒸发向凹表面(颈部) 迁移、凝聚,使颈部逐渐被填充。
x
r
图9-4 蒸发-凝聚传质
10
x r
0
r 3 / 5 (m 3 / 5 )
0.10
0.20
图9-10 在1600℃烧结100h Al2O3的颗 粒尺寸对接触面积生长的影响
烧结过程及机理

(二)烧结过程的模型示意图
根据烧结性质随温度的变化,我们可以把烧结 过程用图6的模型来表示,以增强我们对烧结过 程的感性认识。
图6 粉状成型体的烧结过程示意图
a)烧结前
b)烧结后
图7 铁粉烧结的SEM照片
坯体中颗粒重排,接触处
烧结初期
产生键合,空隙变形、缩
烧
小(即大气孔消失),固-
结
气总表面积没有变化。
c'c0
c
3
exp
1
c0
c0
一般烧结温度下,
于是
c 3 1
c0 kT
c
3 k T
c0
从式可见,在一定温度下空位浓度差是与表面 张力成比例的,因此由扩散机理进行的烧结过 程,其推动力也是表面张力。
由于空位扩散既可以沿颗粒表面或界面进行, 也可能通过颗粒内部进行,并在颗粒表面或颗 粒间界上消失。为了区别,通常分别称为表面 扩散,界面扩散和体积扩散。有时在晶体内部 缺陷处也可能出现空位,这时则可以通过质点 向缺陷处扩散,而该空位迁移到界面上消失, 此称为从缺陷开始的扩散。
烧结是一个自发的不可逆过程,系统表面 能降低是推动烧结进行的基本动力。
表面张力能使凹、凸表面处的蒸气压P分别低于和高
于平面表面处的蒸气压Po,并可以用开尔文本公式
表达: 对于球形表面
ln P 2M (1)
P0 dRTr
对于非球形表面
ln P M ( 1 1 )(2)
P0 dRT r1 r2
表面凹凸不平的固体颗粒,其凸处呈正压,凹处呈负 压,故存在着使物质自凸处向凹处迁移。
过
程 的
烧结中期
传质开始,粒界增大,空 隙进一步变形、缩小,但
烧结过程物质流和能量流分析

烧结过程物质流和能量流分析
烧结过程物质流和能量流分析
烧结是一种常用于生产硬质合金和复合材料的工艺。
烧结可分为低温烧结和高温烧结。
烧结过程主要包括物质流和能量流的变化。
物质流的变化以原料的进入烧结室为起点,在烧结过程中,原料及其熔融质分别与已烧结的产品混合,使其具有良好的流动性,这就是原料的“物质进射”。
其次,热风或电弧高温作用,加热融化原料,“液态熔融物”及各种不同的混合物,经过物料流动,将混合物分散,填充在热受体体系中,然后析出各种固态晶粒,构成成品。
最终,在负荷作用下,在烧结过程中发生的密度、流变性能的变化,使烧结的物料形成“团状物”。
能量流的变化以热源的提供为起点,热源可以是外加的热量,也可以是介质本身带来的能量,如炉体热源。
其次是热传递,能量从热源传递到烧结室,从而推动物质和热力作用,使其彼此混合均匀、熔融,从而形成团状物。
烧结过程中,多余能量会通过热辐射、热对流而损失。
可以看到,烧结过程是一个物质与能量变化交互作用的过程,以上物质流和能量流的变化是烧结过程一个重要的特点。
它是烧结过程的关键过程,也是烧结工艺的依据。
只有通过系统掌握这些物质和能量流变化,才能更加有效地控制烧结工艺参数,才能得到优质的产品。
烧结第四章1解剖

Wuhan Institute of Technology
燃烧废气组成
Sintering and pelletizing
计算氧平衡时,考虑碳酸盐的分解、铁氧化物的氧化或还
原,废气中(CO2+1/2CO+O2)与空气和单一碳的燃烧反应的 平衡组成不同。
Wuhan Institute of Technology
Sintering and pelletizing
氧气浓度 气流速度 燃料粒度 燃烧温度
在“动力学燃烧区”与“扩散燃烧区”存在一个 过渡燃烧区。
不同反应由动力学区进入扩散区的温度不同: C和O2的反应于800℃左右开始转入; C和CO2的反应则在1200℃时才转入。
Wuhan Institute of Technology
Sintering and pelletizing
烧结过程影响燃烧速度的因素:
在点火后不到1min,料层温度升高到1200~1350℃, 烧结过程燃烧反应基本上是在扩散区内进行。
一切能够增加扩散速度的因素,都能提高燃烧反 应速度,强化烧结过程:
Wuhan Institute of Technology
气相组成
Sintering and pelletizing
0
2
4
6
8
10 12
图 在烧结试验过程测得废气成分的变化
Wuhan Institute of Technology
Sintering and pelletizing 燃烧比:[CO/(CO十CO2)] 衡量烧结过程中碳的化学能的利用程度。 a)燃烧比大则碳素
四、烧结.ppt
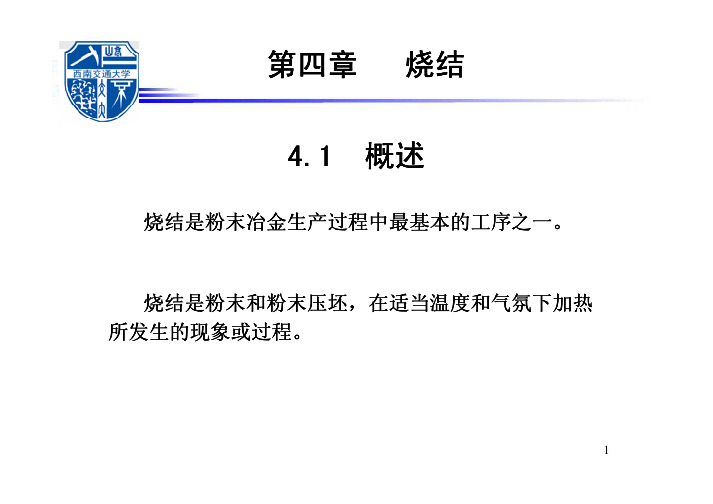
1第四章烧结4.1 4.1 概述概述烧结是粉末冶金生产过程中最基本的工序之一烧结是粉末冶金生产过程中最基本的工序之一。
烧结是粉末和粉末压坯烧结是粉末和粉末压坯,,在适当温度和气氛下加热所发生的现象或过程所发生的现象或过程。
2按烧结过程有无明显的液相出现和烧结系统的组成分为和烧结系统的组成分为::1)单元系烧结2)多元系固相烧结3) 3) 多元系液相烧结多元系液相烧结3粘结阶段颗粒的原始接触点或面转变成晶体结合颗粒的原始接触点或面转变成晶体结合,,即通过成核即通过成核、、结晶长大等原子过程形成烧结颈等原子过程形成烧结颈。
烧结体密度烧结体密度、、烧结体强度烧结体强度、、导电性等的变化烧结颈长大阶段原子向颗粒结合面迁移原子向颗粒结合面迁移,,烧结颈扩大烧结颈扩大,,颗粒间距缩小颗粒间距缩小,,晶粒长大,晶界越过孔隙移动晶界越过孔隙移动。
烧结体密度烧结体密度、、烧结体强度等的变化闭孔隙球化和缩小阶段烧结体致密度达到烧结体致密度达到90%90%90%以上以上以上,,孔隙闭合后孔隙闭合后,,孔隙形状趋于球形并缩小缩小。
4.2 4.2 烧结的基本过程烧结的基本过程41)烧结为什么会发生烧结为什么会发生??2)烧结是怎样进行的烧结是怎样进行的??4.34.3 烧结理论的两个最基本的问题51)烧结为什么会发生烧结为什么会发生??烧结是系统自由能减低的过程。
•由于颗粒结合面的增大和颗粒表面的平直化,粉末体的总表面积和总表面自由能减小•粉末体内孔隙的总体积和总表面积减小•粉末内晶格畸变的消除62)烧结是怎样进行的烧结是怎样进行的??烧结的机构和动力学问题,研究烧结过程中各种物质迁移方式以及速率。
7单元系烧结是指:纯金属或有固定成分的化合物的粉末在固态下的烧结,不会出现新组成物或者新相,也不会出现凝聚状态的改变。
4.4 4.4 单元系烧结单元系烧结8一、烧结温度和时间•单元系的烧结主要机构是扩散和流动构是扩散和流动。
烧结热力学
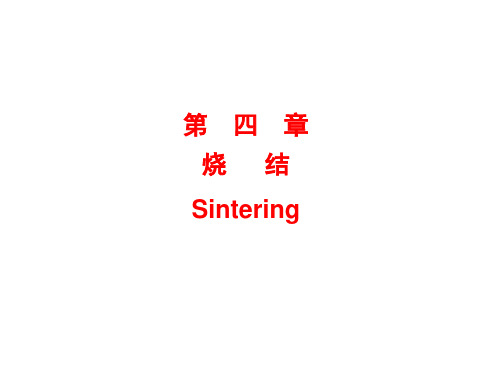
图4-7三种扩散机构
第四章烧结 从图可看出:空位与原子交换位置时,一个空位移动了5个原子间距, 而5个原子各移动了一个原子间距,说明空位扩散速度远大于原子扩散速
度,金属相互扩散形成孔隙就是因为空位和空位扩散机构。
烧结过程中,由于空位和扩散起重要作用,因此体积扩散机构中,以烧 结颈为扩散空位“源”。
第
烧
四
章
结
Sintering
第四章烧结 烧结定义:把坯块或松装粉末体加热到其基本组元熔点以下的温度,约 0.7~0.8T绝对熔点或2/3熔点,并在此温度下保温,从而使粉末颗粒相互结 合起来,改善其性能的一种热处理过程。 烧结过程坯块变化:用低于熔点的温度加热坯块时,坯块收缩而致密 化,结果强度增加,物理化学性能提高。烧结温度达到一定值时,水分或 有机物蒸发或挥发,吸附气体排出,应力消除,粉末颗粒表面氧化物还 原,接着是原子的相互扩散,粘性流动和塑性流动,颗粒间接触面增大,
Q——扩散激活能;R——气体常数;T——绝对温度。 从上式可看出,扩散系数随温度升高而增大。
正常烧结温度下,扩散系数很高,烧结体可以均匀化。如Fe-石墨结构
件,在1100℃下,C向奥氏体中扩散的扩散系数是7×10-9m2· sec-1。 Fe-Ni合金,在1100℃下,Fe往Ni中扩散的扩散系数是8 ×10-14m2· sec-1。
Ⅲ最终阶段——闭孔隙球化和缩小阶段 多数孔隙被分离使闭孔隙数量增加,并不断球化和缩小。这一阶段由于
小孔隙数量逐渐较少,烧结块缓慢收缩。
第四章烧结
图4-2烧结阶段示意图
第四章烧结 (3)烧结原动力 烧结过程中孔隙大小发生变化,粉末体总表面积减小,孔隙表面自由 能的降低即是烧结原动力。 a.烧结动力公式:
- 1、下载文档前请自行甄别文档内容的完整性,平台不提供额外的编辑、内容补充、找答案等附加服务。
- 2、"仅部分预览"的文档,不可在线预览部分如存在完整性等问题,可反馈申请退款(可完整预览的文档不适用该条件!)。
- 3、如文档侵犯您的权益,请联系客服反馈,我们会尽快为您处理(人工客服工作时间:9:00-18:30)。
VkCO2
1 1 1 k kD kR
4.1 烧结过程燃料燃烧基本原理
(三)固体燃料燃烧动力学分析
对于-3mm的碳粒,在Re为100的情况下: <700℃为动力学燃烧区 700~1250℃ 为中间速度区 >1250℃ 为扩散燃烧区
烧结过程在点火后不到一分钟,料层温度升高到1200~1350℃,一 般在1300~1500℃,故其燃烧反应基本上是在扩散区内进行,因 此,一切能够增加扩散速度的因素,如减小燃料粒度、增加气流 速度(改善料层透气性、增风机风量等)和气流中的氧含量等, 都能提高燃烧反应速度,强化烧结过程。
③一般,燃烧带温度,即分布曲线上 的最高点温度随着烧结过程的进行有 所上升,这主要由于料层的蓄热作用。
1-燃烧带,2-预热干燥带,3-水分冷凝带,4-铺底料,5-烧结矿带
t (℃) -Δ p (mmH2O)
烧结负压及料层温度的变化情况
1800
1500
1200
900
600
300
z1
0
0
5
1500
Δp
刚点火毕
点火终了后 1~2分钟
开始烧结后 8—10分钟 烧结终了前
(1)烧结料层中的温度分布特点
①由低温到高温,然后又从高温迅 速下降到低温。
②燃烧带下部的热交换是在一个很窄 的加热及干燥带完成的,它的高度一 般小于50mm,尽管距离很短,但气 体可以自1400~1500℃冷却到50~ 60℃。主要是气流速度大,温差大, 对流传热量大。另一方面由于料粒有 很大的比表面积,彼此紧密接触,传 导传热也在迅速进行。
(2)固体燃料的种类
焦粉优于无烟煤 不能用烟煤
(3)固体燃烧的用量
磁铁矿,一般为5%~6% 3~5% 赤铁矿,一般为7%~9% 5~7% 菱铁矿和褐铁矿,更高。铬铁矿烧结有时高达10%以上。
(4)固体燃料在料层中的赋存状态
燃烧的添加方式
(5)固体燃烧燃烧催化剂的影响
4.4 烧结料层中的温度分布及蓄热
(1) 气 体 燃 料 种 类
①、高炉煤气
成分
范围 %
CO2
9.0~15. 5
CO 25~31
②、焦炉煤气
CH4
H2
0.3~0.5 2.0~3.0
N2 55~58
发热量/千卡/米3 850~1100
成分
H2
CO
CH4
CO2
N2
范围 % 54~59 5.5~7.0 23~28 1.5~2.5 3~5
O2 0.3~1.7
4.2 烧结料层中燃烧带的特性分析
(一)烧结过程燃烧带厚度的计算
I0u0t62(1m )(n 1d fln C 2(fO )/1 (C H)barc1tg )
b b m (1V)
T V
燃烧带的宽度是由燃料粒的直径d,空气流速ω,原始气体中的氧的浓 度CH,料层的透气性质m及n,以及系数b来决定。
(一)气体燃料燃烧的热力学
(2)、主要煤气成分燃烧的热力学 主要成分:CO、H2、CH4
离解:
转化:
总反应:
4.1 烧结过程燃料燃烧基本原理
(一)气体燃料燃烧的热力学
(3)、气体燃烧发热量的计算
(4)、气体燃烧理论和实际空气需要量
过剩空气系数,人工操作时取1.15~1.20,自动操作取1.05~1.10
从燃烧带出来的氧浓度CO取决于燃料在烧结料中的比例及吸入空气中氧 的浓度,因此,在焦粉配比一定时,它是不变的。
系数b取决于燃料比表面积αT和其他混合料比表面积αm,以及混合料中 燃料的体积V
4.2 烧结料层中燃烧带的特性分析
(二)燃烧带特性与燃烧废气组成
(1)烧结料层的燃烧特点: ①烧结料层中碳含量少、粒度细而且分散; ②烧结料层的热交换十分有利,固体碳颗粒燃烧迅速, 二次燃烧反应不明显; ③烧结料层中一般空气过剩系数较高(常为1.4~1.5)。
1200
900
600
z3
z2
300
0 10 15 20 25 30
τ (min)
第四章 烧结过程燃烧与热量传输规律
4.1 烧结过程燃料燃烧基本原理 4.2 烧结料层中燃烧带的特性分析 4.3 固体燃料特性及用量对烧结过程的影响 4.4 烧结料层中的温度分布及蓄热 4.5 烧结过程传热规律及应用 4.6 烧结节能的主要途径及措施
4.1 烧结过程燃料燃烧基本原理
(一)气体燃料燃烧的热力学
4.1 烧结过程燃料燃烧基本原理
(一)气体燃料燃烧的热力学
(5)、实际燃烧产物量
4.1 烧结过程燃料燃烧基本原理
(一)气体燃料燃烧的热力学
(6)、燃烧温度
理论燃烧温度
t i总 Qq燃q空
Cp
CpV
理论燃烧温度通常要比冶金炉内的实际温度高出10~25%
平衡燃烧温度
4.1 烧结过程燃料燃烧基本原理
(2)影响燃烧比的因素有: ①燃料粒度和用量; ②料层负压大小; ③空气过剩系数; ④料层高度和返矿量。
一般燃烧废气中平均含CO1~2%,热量损失占总热量的10~25%。
4.3 固体燃料特性对烧结过程的影响
(1)固体燃料的粒度
烧结粉矿(-8mm):1~2mm适宜 烧结精矿(-1mm):0.5~3mm适宜
发热量/千卡/米3 3160~4580
③、天然气
成分
H2
CO
范围% 0.4~0.8 0.1~0.3
CH4 85~95
H2S
N2
O2
发热量/千卡/米3
0.9 1.5~5.0 0.2~0.3 8000~9000
④、液体燃料
重油:发热值高(大于9000千卡/公斤)、粘性大
4.1 烧结过程燃料燃烧基本原理
C O2
①氧气向固体碳表面扩散迁移的速率为:
VDkD(CO2 CS O2)
C
S O
2
②相界面上的化学反应速率为:
V RkR(C S O 2)nkR C S O 2
(1)氧由气流本体通过界面层扩散到固体碳的表面; (2)氧在碳粒表面上吸附; (3)吸附的氧与碳发生化学反应; (4)反应产物的解吸; (5)反应பைடு நூலகம்物由碳粒表面通过界面层向所相扩散。
(二)固体燃料燃烧的热力学
(1)、热力学分析 C氧化 初级
气相氧化 次级
4.1 烧结过程燃料燃烧基本原理
(二)固体燃料燃烧的热力学
(2)、固体燃料燃烧计算 发热量
理论空气需要量
固体燃料燃烧温度
4.1 烧结过程燃料燃烧基本原理
(三)固体燃料燃烧动力学分析
固体燃料的燃烧属多相扩散燃 烧:首先要使氧气到达固体表 面,在相界面上发生多相化学 反应;其后,化学反应所需的 物质则靠自然扩散或强制扩散 形成的物质转移来提供。