800KN M自由锻操作机技术研究
大型锻造操作机的进展
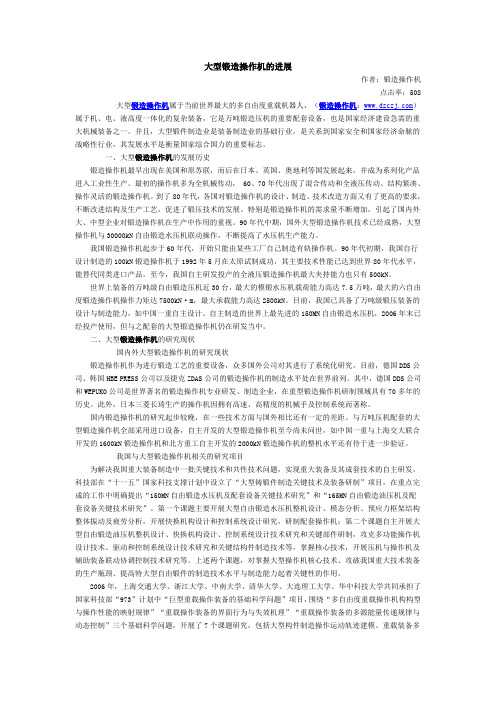
大型锻造操作机的进展作者:锻造操作机点击率:508 大型锻造操作机属于当前世界最大的多自由度重载机器人,(锻造操作机:)属于机、电、液高度一体化的复杂装备,它是万吨锻造压机的重要配套设备,也是国家经济建设急需的重大机械装备之一。
并且,大型锻件制造业是装备制造业的基础行业,是关系到国家安全和国家经济命脉的战略性行业,其发展水平是衡量国家综合国力的重要标志。
一、大型锻造操作机的发展历史锻造操作机最早出现在美国和原苏联,而后在日本、英国、奥地利等国发展起来,并成为系列化产品进入工业性生产。
最初的操作机多为全机械传动, 60、70年代出现了混合传动和全液压传动、结构紧凑、操作灵活的锻造操作机。
到了80年代,各国对锻造操作机的设计、制造、技术改造方面又有了更高的要求,不断改进结构及生产工艺,促进了锻压技术的发展。
特别是锻造操作机的需求量不断增加,引起了国内外大、中型企业对锻造操作机在生产中作用的重视。
90年代中期,国外大型锻造操作机技术已经成熟,大型操作机与30000kN自由锻造水压机联动操作,不断提高了水压机生产能力。
我国锻造操作机起步于60年代,开始只能由某些工厂自己制造有轨操作机。
90年代初期,我国自行设计制造的100kN锻造操作机于1992年5月在太原试制成功,其主要技术性能已达到世界80年代水平,能替代同类进口产品。
至今,我国自主研发投产的全液压锻造操作机最大夹持能力也只有500kN。
世界上装备的万吨级自由锻造压机近30台,最大的模锻水压机载荷能力高达7.5万吨,最大的六自由度锻造操作机操作力矩达7500kN·m,最大承载能力高达2500kN。
目前,我国已具备了万吨级锻压装备的设计与制造能力,如中国一重自主设计、自主制造的世界上最先进的150MN自由锻造水压机,2006年末已经投产使用,但与之配套的大型锻造操作机仍在研发当中。
二、大型锻造操作机的研究现状国内外大型锻造操作机的研究现状锻造操作机作为进行锻造工艺的重要设备,众多国外公司对其进行了系统化研究,目前,德国DDS公司、韩国HBE PRESS公司以及捷克ZDAS公司的锻造操作机的制造水平处在世界前列。
锻造操作机发展现状与研究方向

国 外 锻 造 操 作 机 的 制 造 商 主 要 有 德 国 的 DDS
公 司 、 MS MEE 公 司 、 L S — R G AMA 公 司 、 捷 克 Z DAS
公 司 、 E UKO公 司 、 国 HB RE S公 司 等 。 图 W P 韩 SP S
la 所 示 为 S — () MS MEE 为 俄 罗 斯 生 产 的 2 0 k R 5 0 N/ 6 0 k ・ 锻 造 操 作 机 , 是 目前 世 界 上 最 早 投 入 使 3 0N m
具 有 现 代 控 制 技 术 锻 造 操 作 机 的 发 展 起 到 了 至 关 重
要 的 推 动 作 用 , 目前 已 经 成 功 制 造 了 多 台 2 0 k 5 0 N/
60 k m锻造操 作 机 。 3 0机 械 结 构 形 式 以 及 未 来 研 究 方 向 ,为 我 国 大 型 锻 造
熟 , 与 锻 造 压 机 配 合 使 用 , 大 提 高 了锻 造 生 产 效 它 大 率 、 件 精度 和 质 量 , 时提 高 了材料 利 用 率 , 低 锻 同 降
了能耗 。
命 ; 高锻 件精 度 , 少 机加 工量 ; 高生 产效 率 , 提 减 提 增
加 经 济 效 益 ; 全 环 保 , 善 劳 动 环 境 已成 为 自 由 锻 安 改 件 生 产 行 业 的共 识 。 锻 造 操 作 机 是 锻 件 精 确 制 造 的 基 本 装 备 之 一 ,与 自 由锻 造 压 机 配 合 进 行 锻 造 作 业 能 极 大 提 高 锻 造 生 产 效 率 和 锻 件 制 造 质 量 , 降 低 制
基 金项 目: 国家科技重大专项项 目(0 0 X 4 1— 2 ) 2 1Z 0 0 3 0 1 收稿 日期 :01- 2 2 2 1 1— 0 作者简介 : 张营杰( 9 5 ) 男, 1 6 一 , 教授 级高工, 从事锻压装备 与工艺技
自由锻工艺过程

智能化发展趋势与挑战
1 2 3
数据驱动模型
基于大数据和机器学习技术,建立数据驱动模型, 实现自由锻工艺的智能化预测和优化。
智能传感器与控制系统
研发高精度、高稳定性的智能传感器和控制系统, 实时监测和调整自由锻工艺参数,提高产品质量 和生产效率。
多学科交叉融合
结合材料科学、力学、热力学等多学科知识,深 入研究自由锻工艺机理,为智能化发展提供理论 支撑。06自由锻数值模拟与 Nhomakorabea能 化发展
数值模拟技术应用现状
有限元法(FEM)应用
通过建立物理模型的数学方程,利用有限元法模拟自由锻过程中 的应力、应变和温度分布。
有限体积法(FVM)应用
有限体积法适用于处理复杂几何形状和边界条件,广泛应用于自由 锻工艺模拟。
粒子法(SPH)应用
光滑粒子流体动力学方法(SPH)适用于模拟大变形和自由表面流 动,为自由锻工艺提供了新的模拟手段。
辅助工序
为了保证锻件质量和提高生产效率,自由锻还包括一些辅助工序,如预锻、修整、校直等。预锻是为了减少终锻 时的变形量,提高锻件的精度和表面质量;修整是对锻件进行局部的加工和调整,以满足尺寸和形状要求;校直 是对弯曲的锻件进行矫正,以保证其直线度。
冷却与热处理
冷却
锻造完成后,需要对锻件进行冷却。冷却方式包括空冷、坑 冷、炉冷等。冷却速度对锻件的组织和性能有很大影响,因 此需要根据锻件材质和要求选择合适的冷却方式。
应变分析
应变是金属在自由锻过程中发生的形状和尺寸变化。通过应变分析,可以了解金属的变形程度和分布 情况,进而评估锻件的几何形状和尺寸精度。同时,应变分析还可以为后续的工艺优化提供重要依据 。
工艺参数优化方法
试验法
800 MN模锻压机用大拉杆热处理调质研究

C
Si
Mn
P
S
Co Ni Mo
0.30 0. 17 0.40 u
u 1.40 u 0. 15
〜0.38 〜0.37 -0.70 0.035 0.035 〜1.70 0.40 〜0.30
1.2力学性能要求
大拉杆力学性能要求为凡W690 MPa,乩l W 490 MPa,4W12 % ,ZW32 % ,KU2 W31 J,根据制造 技术规范JB/T 5000. 8—2007要求,大拉杆在工
2技术措施
项目组对大拉杆的调质热处理工艺进行大胆 技术创新,提出全新的淬火方式:将大拉杆进行短 暂的喷水冷,喷水冷的主要目的只是降低工件表 面温度,为后续的油冷作铺垫,防止油冷着火,但 又必须控制喷水冷的程度,将工件温度控制在组 织转变之上400 - 500W之间,防止组织转变导致 组织应力过大,从而降低大拉杆喷水淬裂的风险。 大拉杆调质热处理工艺见图2。
1大拉干调质前情况介绍
1.1化学成分要求 大拉杆材质为34CrNiMo,化学成分要求如表
1所示。
收稿日期:2019 -03 -22
50
大拉杆长度达到17.39 m,冶炼过程中主要 控制工件两端C偏析和合金聚集,同时将P、S含 量控制在U0.01%,提高钢水的纯净度,减少大拉 杆后续的淬裂风险。
表1 34CrNiMo钢化学成分要求 Table 1 Chemical composition requirementt of
Abstract: The quenching process for the large pull eod used in the 800 MN die forging press exceeds the quenching capacity oO the existing water tank and oil tank of the company. By changing the heat treatment quenching process, the limitation of quenching equipment hasbeen broken, and the risk of cracking of large rod has been avoided. Meanwhile, the mechanical properties have been qualified in one time.
大型自由锻压机组精度与可靠性提升研究

大型自由锻压机组精度与可靠性提升研究
陈欣;刘宏宇;邱腾飞
【期刊名称】《设备管理与维修》
【年(卷),期】2024()11
【摘要】研究大型自由锻压机组3150 t压机的疑难故障,提出创新改进措施,以满足高端制造业对精密压制工艺的严格要求。
对3150 t压机故障问题进行分析,找出故障的根本原因,并提出一系列创新改进措施,包括完善维护策略、改进控制方法和改造冷却回路等。
实验结果表明,上述方法能够有效提高压机的精度与可靠性。
【总页数】3页(P109-111)
【作者】陈欣;刘宏宇;邱腾飞
【作者单位】河南中原特钢装备制造有限公司锻压公司;河南中原特钢装备制造有限公司设备工程部
【正文语种】中文
【中图分类】TG315
【相关文献】
1.大型风力发电机组变桨距系统结构可靠性设计研究
2.基于马尔科夫过程的大型机组三状态可靠性研究
3.乙烯生产大型关键机组可靠性研究及维护对策
4.高功率激光系统中大型光机组件的装配精度研究
5.基于流固耦合的某大型柴油发电机组中冷管路可靠性研究
因版权原因,仅展示原文概要,查看原文内容请购买。
自由锻名词解释
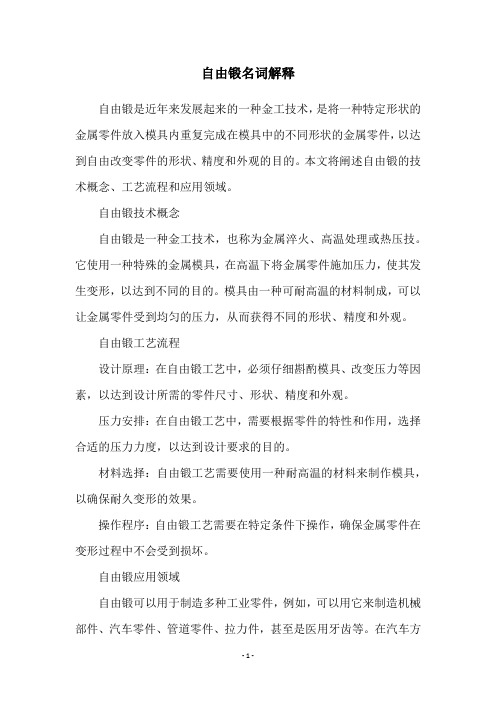
自由锻名词解释自由锻是近年来发展起来的一种金工技术,是将一种特定形状的金属零件放入模具内重复完成在模具中的不同形状的金属零件,以达到自由改变零件的形状、精度和外观的目的。
本文将阐述自由锻的技术概念、工艺流程和应用领域。
自由锻技术概念自由锻是一种金工技术,也称为金属淬火、高温处理或热压技。
它使用一种特殊的金属模具,在高温下将金属零件施加压力,使其发生变形,以达到不同的目的。
模具由一种可耐高温的材料制成,可以让金属零件受到均匀的压力,从而获得不同的形状、精度和外观。
自由锻工艺流程设计原理:在自由锻工艺中,必须仔细斟酌模具、改变压力等因素,以达到设计所需的零件尺寸、形状、精度和外观。
压力安排:在自由锻工艺中,需要根据零件的特性和作用,选择合适的压力力度,以达到设计要求的目的。
材料选择:自由锻工艺需要使用一种耐高温的材料来制作模具,以确保耐久变形的效果。
操作程序:自由锻工艺需要在特定条件下操作,确保金属零件在变形过程中不会受到损坏。
自由锻应用领域自由锻可以用于制造多种工业零件,例如,可以用它来制造机械部件、汽车零件、管道零件、拉力件,甚至是医用牙齿等。
在汽车方面,自由锻可以用来制造车身零件和车轮,以提高汽车的整体性能和安全性。
此外,自由锻还可以用于制造家具件、机器件和航空部件等,展示了它在工业领域的多样性。
结论从上述内容可以看出,自由锻是一种有用的金工技术,不仅可以用来制造多种工业零件,还可以用于为汽车等设备提供更高的安全性。
自由锻的技术概念、工艺流程及其应用领域都是非常重要的,为了保证质量、可靠性和可靠性,必须有一套严格的工艺和操作准则。
只有在正确的环境中,采用正确的工艺和操作准则,才能制造出精确的零件,并为其优质的工业应用带来更大的价值。
第4章自由锻主要工序分析.

(3)修整工序:指用来精整锻件尺寸和形 状使其完全达到锻件图要求的工序。 鼓形滚圆、端面平整、弯曲校正等。
第4章 自由锻主要工序分析
修整工序
鼓形滚圆
端面平整
弯曲校正
图4.3 自由锻修整工序
第4章 自由锻主要工序分析
4.2 镦粗工序 镦粗的定义:
使坯料高度减小而 横截面积增大的成形 工序。
eh 坯料高度方向的对数变形 εh 坯料高度方向的相对变形
H0 eh ln H H0 H h
H0
第4章 自由锻主要工序分析
3. 平砧镦粗变形分析
II
h
III III I I
图4.5 平砧镦粗变形分布与应力状态分析
r
II
第4章 自由锻主要工序分析
根据镦粗后网格的变形程度分为三个变形区:
第4章 自由锻主要工序分析
第四章 自由锻主要工序分析
第4章 自由锻主要工序分析
概 述
自由锻:利用冲击力或压力使加热好的金属 在上、下抵铁之间产生变形。 自由锻分类:手工锻造和机器锻造。 自由锻工艺研究的内容:锻件的成型规律和 提高锻件的质量两个方面。
第4章 自由锻主要工序分析
4.1 自由锻工艺过程特征和工序分类 4.1.1 自由锻工艺过程特征
4.2.3 局部镦粗 :
•作用:锻造凸肩直径和高度较大的饼块锻件, 或端部带有较大法兰的轴杆锻件。 •特点:与平砧镦粗相似,但受“刚端”的 影响。
第4章 自由锻主要工序分析
4.13
局部镦粗
第4章 自由锻主要工序分析
局部镦粗成型的坯料尺寸,应按杆部直 径选取。为了避免镦粗时产生纵向弯曲, 坯料变形部分高径比 H 头 /D0 应小于 2.5-3 , 而且要求端面平整。对于头部较大而杆部 较细的锻件,只能采用大于杆部直径的坯 料。锻造时先拔杆部,然后再镦粗头部; 或者先局部镦粗头部,然后再拔长杆部。
800KN全液压锻造操作机
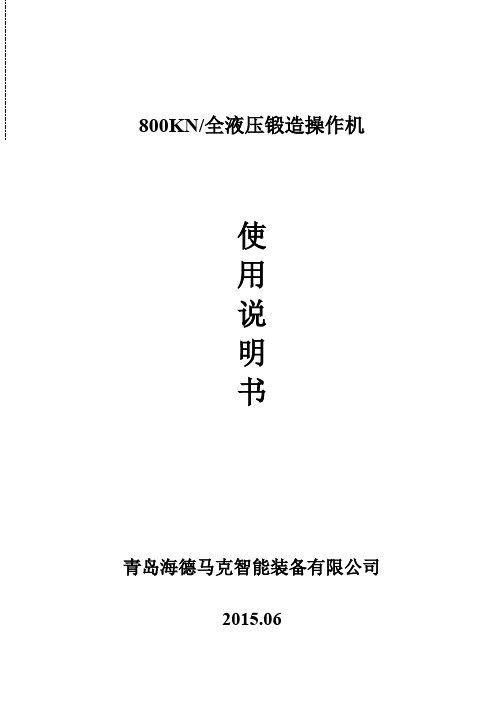
1. 前言
²锻造操作机主要用于夹持锻件配合主机完成锻造工艺,也可以用 于夹持模具、工具做一些辅助工作。
²本操作机在出厂之前经过仔细的检验和操作试验,确保为集高性 能、高质量、低操作费用和耐用于一体的产品。
²要使操作机能够发挥出最高的使用效率,很大程度上取决于操作 人员和维护保养人员。
²本说明提供给操作人员和维护保养人员阅读。
机构,使用维修方便。 ²平行升降油缸及前吊杆均通过球铰与销轴连接。 ²所有销轴均采用台阶轴形式,方便维修和更换。 ²采用电液换向阀控制,使起/停平稳无冲击。 2.2.4.2 钳杆仰俯机构 ²钳杆仰俯机构由仰俯油缸、平行升降机构构成 ²仰俯缸的伸缩可带动钳身后吊点上下升降,钳头随之仰俯。 ²仰俯缸通过球铰与销轴连接。 ²仰俯缸始终无杆腔承受高压,受力合理,密封容易。 ²采用电液换向阀控制,具有自动调平功能。 2.2.4.3 侧移机构 ²侧移机构由前后侧移缸、前后侧移横梁、侧移径向定位及缓冲装 置等构成。 ²侧移横梁与侧移缸为一体结构,通过横梁在前后摆臂中的移动带
第 12 页
表上实时显示油温值
4. 电气及控制系统 4.1 电气简介
直缓冲量时,外力迫使平行升降液压缸将多于液压油排入蓄能 器;当外力消失后,蓄能器将先前排入液压油重新排入平行升 降液压缸,钳身回复到原有高度,该过程是弹性缓冲。 ²当钳身需要的缓冲量大于弹性缓冲量时,液压缸内多余的液压 油通过安全阀直接排入油箱,该过程为非弹性缓冲。
第9页
2.2.5.2 水平缓冲装置 ²水平缓冲装置由钳身左右水平缓冲缸等构成。 ²水平缓冲装置通过铰链与车体连接,便于钳身水平摆动。 ²水平缓冲是双作用缓冲,即对钳身前、后均能缓冲。 ²水平缓冲缸两端通过关节轴承分别与摆臂和前联板连接。 ²水平缓冲装置具有锁定功能,用于辅助压机切断料头。
自由锻操作机技术研究

mm、宽为240 mm,接触面压为50 MPa,作为冲击载荷滑动
轴承,应力偏高,实际使用中每两个月更换一对轴承。改用复 合材料轴承后,寿命提高了两倍以上。 1.1.3吊挂装置及升降倾斜装置 吊挂装置由4个升降拐臂、上下两对水平悬挂轴、4根铅垂 悬吊杆、2个水平主轴、2个升降缸、2个倾斜缸、2个垂直缓冲 吊置、吊挂装置、钳杆旋转装置、后桥、大车驱动装置、液压控 制系统、电气控制系统、轨道驱动链、基础附件和升降倾斜装置 和水电引入拖链装置等部分组成。操作机的液压系统由油箱、 油泵电机组、控制阀组、蓄能器组、冷却过滤装置、管道系统等 组成。电气系统主要包括PLC装置、电机控制柜、操作台、钳杆 转角检测、大车行走位置检测、夹钳缸压力检测、倾斜缸压力检 测等。 1.1操作机本体 1.1.1夹钳、钳杆及旋转装置 夹钳采用销轴V型结构,V型块采用耐热钢制作。钳头固 定在空心钳杆上,锻件夹紧和松开是通过钳口、杠杆、拉杆、导 向套支撑、夹紧油缸来实现的。夹紧缸的密封起直线运动密封 和旋转密封作用。低速大转矩液压马达通过减速齿轮驱动空 心钳杆,实现钳头和钳杆的正反回转,采用光电编码器检测钳 杆的回转角度位置。钳杆前端和后端通过合金铜套安装在钳 杆架体中,钳杆架体通过两根抬杆及球面关节回转轴承与吊杆 相连接。钳杆架体可以在吊杆上前后倾及水平侧摆。该操作 机钳口夹紧缸采用了后置结构,芯杆长度6
头。
系统、自动化系统、分布式外设和智能现场装置之间交换,总线 的传输速率可达1.5 1.3.4自动化系统 操作机的自动控制系统以SIMATC S7—314系统为基础, 其具有模块化结构,极好的升级容量与坚固性。 I/O外设使用分布式ET200M连接,ET200M通过PROFI.
BUS Mbit/s。
机械设计
200
自由锻工艺

自由锻工艺自由锻造是利用冲击力或压力使金属在上下砧面间各个方向自由变形,不受任何限制而获得所需形状及尺寸和一定机械性能的锻件的一种加工方法,简称自由锻。
自由锻的基本目的:经济地获得所需的形状、尺寸和内部质量的锻件。
锻件的类型有大型和中小型锻件。
小型锻件以成形为主,大型锻件(尤其是重要件)和特殊钢以改善内部质量为主。
钢锭经过锻造,粗晶被打碎,非金属夹杂物及异相质点被分散,内部缺陷被锻合,致密程度高,流线分布合理,综合力学性能大大提高。
钢锭中的常见缺陷有:偏析、夹杂、气泡、缩孔、缩松、裂纹等。
自由锻的特点优点:①设备的通用性好、工具简单、灵活性大;②可锻小到不足1公斤,大可到几百吨大型件,且大型锻件的组织致密、力学性能好;自由锻主要用于单件、小批量生产,且是生产大型和特大型锻件的唯一方法。
缺点:③锻件形状简单、加工余量大、精度低;④自由锻操作技术要求高、生产率低、劳动强度大。
自由锻工序自由锻工艺方法包括:基本工序、辅助工序和修整工序。
基本工序包括:镦粗、拔长、冲孔、扩孔、弯曲、扭转、错移、切割和锻焊等。
辅助工序是为了配合基本工序使坯料预先变形的工序,如钢锭倒棱、预压钳把、分段压痕。
修整工序安排在基本工序之后,用来修整锻件的尺寸和形状。
1、基本工序(1)镦粗镦粗:是使坯料高度减小、横截面积增大的工序。
在坯料局部进行的镦粗叫局部镦粗。
适于饼块、盘套类锻件的生产。
镦粗的方法一般分为三类:平砧镦粗、垫环镦粗和局部镦粗i.平砧镦粗坯料在上下两个平砧间或镦粗平板间进行的镦粗。
镦粗时的锻造比: 常用镦粗前后坯料的高度之比即镦粗比K H来表示镦粗的变形程度。
K H=H0/H镦粗时的高径比:镦粗时,坯料高度与直径之比称为高径比。
通常坯料高径比H0/D=0.8-2.0。
H0/D≈3时,镦粗后产生双鼓形。
H0/D>3时,镦粗时坯料易产生纵向弯曲,如不及时矫正易产生折叠。
凹形坯镦粗可以减小“鼓肚”的程度,从而避免侧表面出现裂纹。
80MN自由锻压机中的控制系统研究

现代制造技术与装备502017第4期 总第245期自由锻造油压机是冶金锻造行业的重要设备。
随着我国锻造工业的快速发展,人们对压机的锻造精度、锻造速度及自动化程度要求越来越高。
因此,电气控制系统的作用尤为重要。
本文重点介绍80MN自由锻压机电气控制系统的特点。
该款自由锻压机由锻造油压机、移动换砧台、移动工作台、旋转升降台、操作机械手等组成,采用计算机可编程控制,大大提高了自动化程度。
该机组逻辑控制采用PLC,系统设有内容丰富、界面汉化及操作简便的上位监控系统和图形实时监控系统,使操作者能在控制室内观察到机组的实时数据和设备的工作状态,并能够设置参数。
经过实践证明,该系统自动化程度高,性能稳定,锻造尺寸精度为±1mm,且油压机和操作机能够实现联动控制。
1 该控制系统的基本组成及作用该控制采用西门子工控机和PLC分布式I/O。
压机和操作机CPU均选用西门子416-2系列,其中压机架设6个ET200M分布站,操作机架设3个ET200M分布站。
整个电控系统更稳定,兼容性更好。
CPU和各分布站之间通过PROFIBUS通讯,对现场信号进行采集。
压机CPU和操作机CPU之间通过PROFIBUS通讯,从而实现压机与操作机的联动工作。
压机位置传感器的数据由西门子SM338模块来采集。
压机和操作机的油箱油温数据、液位数据及各油缸的压力数据,均由西门子模拟量输入模块6ES7331来采集。
编程软件采用西门子step7。
工控机上装有西门子Wincc组态软件。
通过MPI网络与PLC进行连接通讯采集信号,从而显示压机及操作机的重要数据和工作状态。
画面包括参数设定画面、主机电机启停监控画面、操作机电机启停监控画面、主机液压系统图、操作机液压系统图,操作机比例阀设定画面、压力温度显示画面及报警画面。
画面有利于工作状态的监视及故障排查,缩短维修时间。
控制系统组态,如图1、图2所示。
2 系统的控制原理80MN自由锻压机的控制组成,如图3所示。
第三节自由锻的工具设备与工艺过程

机械制造工艺基础
第三节 自由锻的工具设备与工艺过程
知 识 •掌握自由锻的工具设备与工艺过程等内容。 目 标
技
能
•学会自由锻的工艺过程。
目
标
Logo
机械制造工艺基础
一、概述
1、概念
只用简单的通用性工具,或在锻造设备的上、下砧间直接使坯 料变形而获得所需的几何形状及内部质量的锻件的锻造方法。
Logo
机械制造工艺基础
三、自由锻设备
1、空气锤
以压缩空气为工作介质,驱动锤头上、下运动打击锻件,使其 获得塑性变形的锻锤。
空气锤是由工作 缸、压缩缸、锤身 、操纵机构、传动 机构、落下部分等 组成。
适用于中小型锻 件的生产。
Logo
机械制造工艺基础
2、水压机
水压机是以水作为介质传 递能量的机器。工作时以静压 力作用在锻件上,使其发生变 形。
•镦粗 冲孔
芯轴扩孔
平整端面
Logo
机械制造工艺基础
•4、厚壁环形锻件:
•镦粗
滚圆
平整端面
冲孔
滚圆
修整孔壁
Logo
机械制造工艺基础
•知识小结:
一、自由锻工具
•二、自由锻设备 •1.空气锤 •2.水压机 •3.蒸汽——空气锤 •三、自由锻基本工序 •四、自由锻变形工艺过程
Logo
机械制造工艺基础
Logo
机械制造工艺基础
局部镦粗:把坯料上某一部分进行的镦粗称为局部镦粗。用来制 造带凸座的盘类锻件。
Logo
机械制造工艺基础
Logo
机械制造工艺基础
2、拔长
拔长:使毛坯横断面积变小、长度增加的锻造工序。 拔长的形式有在芯轴上拔长和在平面上拔长,主要用来锻制长度 较大的轴类锻件。
锻造操作机发展现状与研究方向

锻造操作机发展现状与研究方向张营杰;卫凌云;牛勇;韩炳涛【摘要】锻造操作机是自动化锻造作业中不可缺少的重要装备之一,在提高生产效率,保证加工质量等方面发挥着重要作用.本文综述了锻造操作机的发展历史、研究现状、机械结构形式,提出了今后的研究方向,为我国大型锻造操作机的研究发展提供参考.%The developing history, research status, and the mechanical structure of the forging manipulator have been overviewed in the text. The researching trend has been put forward, which provides reference for the development of domestic heavy-duty forging manipulator.【期刊名称】《锻压装备与制造技术》【年(卷),期】2012(000)002【总页数】4页(P11-14)【关键词】机械制造;锻造操作机;发展现状;研究方向【作者】张营杰;卫凌云;牛勇;韩炳涛【作者单位】中国重型机械研究院有限公司金属挤压与锻造装备技术国家重点实验室,陕西西安710032;中国重型机械研究院有限公司金属挤压与锻造装备技术国家重点实验室,陕西西安710032;中国重型机械研究院有限公司金属挤压与锻造装备技术国家重点实验室,陕西西安710032;中国重型机械研究院有限公司金属挤压与锻造装备技术国家重点实验室,陕西西安710032【正文语种】中文【中图分类】TG315国民经济的高速发展,极大地促进了我国航空航天、国防、交通运输、船舶动力、电力电器和机械制造等行业的发展。
对大型自由锻件的需求,无论在规格、数量和质量上都提出了新的要求。
提高产品开发速度,加速锻造现代化;提高锻件质量,延长使用寿命;提高锻件精度,减少机加工量;提高生产效率,增加经济效益;安全环保,改善劳动环境已成为自由锻件生产行业的共识。
自由锻造液压机的技术现状及设计分析
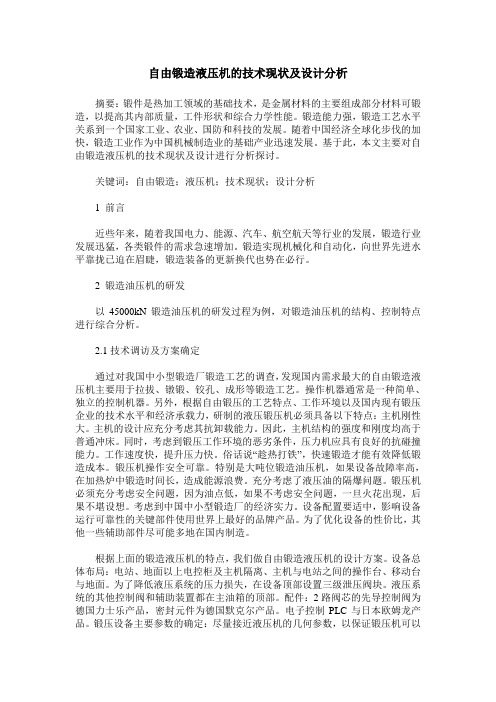
自由锻造液压机的技术现状及设计分析摘要:锻件是热加工领域的基础技术,是金属材料的主要组成部分材料可锻造,以提高其内部质量,工件形状和综合力学性能。
锻造能力强,锻造工艺水平关系到一个国家工业、农业、国防和科技的发展。
随着中国经济全球化步伐的加快,锻造工业作为中国机械制造业的基础产业迅速发展。
基于此,本文主要对自由锻造液压机的技术现状及设计进行分析探讨。
关键词:自由锻造;液压机;技术现状;设计分析1 前言近些年来,随着我国电力、能源、汽车、航空航天等行业的发展,锻造行业发展迅猛,各类锻件的需求急速增加。
锻造实现机械化和自动化,向世界先进水平靠拢已迫在眉睫,锻造装备的更新换代也势在必行。
2 锻造油压机的研发以45000kN锻造油压机的研发过程为例,对锻造油压机的结构、控制特点进行综合分析。
2.1技术调访及方案确定通过对我国中小型锻造厂锻造工艺的调查,发现国内需求最大的自由锻造液压机主要用于拉拔、镦锻、铰孔、成形等锻造工艺。
操作机器通常是一种简单、独立的控制机器。
另外,根据自由锻压的工艺特点、工作环境以及国内现有锻压企业的技术水平和经济承载力,研制的液压锻压机必须具备以下特点:主机刚性大。
主机的设计应充分考虑其抗卸载能力。
因此,主机结构的强度和刚度均高于普通冲床。
同时,考虑到锻压工作环境的恶劣条件,压力机应具有良好的抗碰撞能力。
工作速度快,提升压力快。
俗话说“趁热打铁”,快速锻造才能有效降低锻造成本。
锻压机操作安全可靠。
特别是大吨位锻造油压机,如果设备故障率高,在加热炉中锻造时间长,造成能源浪费。
充分考虑了液压油的隔爆问题。
锻压机必须充分考虑安全问题,因为油点低,如果不考虑安全问题,一旦火花出现,后果不堪设想。
考虑到中国中小型锻造厂的经济实力。
设备配置要适中,影响设备运行可靠性的关键部件使用世界上最好的品牌产品。
为了优化设备的性价比,其他一些辅助部件尽可能多地在国内制造。
根据上面的锻造液压机的特点,我们做自由锻造液压机的设计方案。
800 MN模锻液压机主缸缸底锻件关键成形技术的研究

800 MN模锻液压机主缸缸底锻件关键成形技术的研究张清华;刘鑫刚;祁荣胜;金淼;郭宝峰【摘要】利用数值模拟的技术,研究了采用平面、球面、锥形砧型时,800 MN模锻液压机主缸缸底锻件镦粗过程中锻件内部的应变、静水应力以及心部孔洞尺寸的变化情况.通过对不同砧型时锻件内部等效应变、静水应力、孔洞闭合程度以及镦粗工艺力的考察,得到了球面砧优于另外两种砧型的结论.【期刊名称】《大型铸锻件》【年(卷),期】2010(000)006【总页数】5页(P1-5)【关键词】缸底锻件;镦粗;砧型;孔洞【作者】张清华;刘鑫刚;祁荣胜;金淼;郭宝峰【作者单位】中国第二重型机械集团公司,四川,618013;燕山大学机械工程学院,河北,066004;燕山大学机械工程学院,河北,066004;燕山大学机械工程学院,河北,066004;燕山大学机械工程学院,河北,066004【正文语种】中文【中图分类】O242800 MN模锻液压机主要用于生产大型铝合金、镁合金、钛合金等模锻件,是发展我国大飞机项目必备的关键设备。
该设备的建设对于改变我国大型模锻件长期依赖进口的局面有重大战略意义。
800 MN模锻液压机主缸采用锻焊结构,其缸底部分的锻件直径为3 100 mm、高度1 700 mm,属于大型饼形锻件。
该锻件锻造成形的技术难度较大,主要表现为两个方面:一是钢锭中的孔洞在成形过程中消除困难,探伤检测不易通过;二是锻件几何尺寸较大,已经涉及到二重现有锻造能力的极限。
因此,需要对缸底的锻造过程进行分析和研究,为制定成形工艺提供技术支持。
关于孔洞闭合的理论问题,国内已有大量的研究成果[1~5]。
早期,清华大学的王祖唐教授采用刚-粘塑性有限元法模拟了大型钢锭的拔长过程,研究了孔洞锻合过程的主要影响因素[1]。
近几年,上海交通大学的崔振山教授基于MARC软件研究了圆柱体内部孔洞热锻闭合过程,提出了高温变形是改善含有孔洞材料性能的必要条件[2];北京科技大学的韩静涛教授研究开发了耦合热及细观损伤分析的刚粘塑性有限元分析软件RVTDA,并将其用于饼类锻件镦粗过程中应力、应变、温度等的分析[3]。
800MN大型模锻液压机极限设计制造技术创新

800M N大型模锻液压机极限设计制造技术创新曾祥东,杨固川,张华,于江,胡孟君,陈文( 中国第二重型机械集团公司重型机械设计研究院,四川成都610052)摘要: 简述800 M N大型模锻液压机上巨大尺寸、重要零件的极限设计制造,特别是机架C形板、主工作缸、活动横梁中梁等的极限设计技术以及在铸造、锻造、焊接方面的极限制造技术。
设计过程中对C形板进行优化设计,使过渡圆角处的最大应力由原来的456M Pa降为237.1M Pa; 对主工作缸的局部进行设计优化,使进液孔内壁的最大主应力和等效应力分别降低到192和217M Pa,应力值降低幅度超过40%。
经过国家科技重大专项课题组联合技术攻关,成功解决了大尺寸重要零件极限设计制造关键技术的难题。
关键词: 模锻液压机; 极限设计; 极限制造D O I: 10.13330/j.iss n.1000-3940.2014.02.019中图分类号: TH163文献标识码: A文章编号: 1000-3940( 2014) 02-0096-06C r e a t io n of li m i t d esig n and manu f a c t u r i n g t ec hn i qu e fo rclose-d ie fo r gi n g h y d r au lic p r ess of 800 M NZ en g Xian g d o n g,Yan g Guchuan,Z han g Hua,Yu Jian g,Hu M en g jun,C hen Wen ( T he Hea vy M achiner y Desi g n andResearch Institute,China Nati o nal Er z h o n g Gr o up C o〃,Chen g du610052,China )A b s t r a c t: T he limit desi g n and manu f acturin g technique of imp o rtant parts w ith lar g e si z es in the800 M N cl o se-die fo r g in g h y draulic press w as described brie f l y,especiall y the limit desi g n techn o l ogy of the“C”shaped plate in f rame,the main c y linder and the c o unter beam of m ov in g cr o sshead,and the limit manu f acture of castin g,fo r g in g and w eldin g〃 T he ma x imum stress at the f illet radius of“C”shaped plate w as reduced f r o m456t o 237.1 M Pa thr o u g h the o ptimi z ati o n desi g n〃 T he ma x imum principal stress and the equi v alent stress of liquid in- let h o le in the main wo rkin g c y linder w ere reduced t o 192and217M Pa respecti v el y b y a l o cal o ptimi z ati o n desi g n,and the stresses w ere decreased b y m o re than40%〃 T hr o u g h j o int technical research of the nati o nal science and techn o l ogy maj o r special pr o ject g r o up,the ke y technical pr o blems of limit desi g n and manu f acture ab o ut imp o rtant parts w ith lar g e si z es w ere success f ull y res o l v ed〃K ey wo r d s: cl o se-die fo r g in g press; limit desi g n; limit manu f acture我国自主设计制造的、世界最大的800 M N ( 8 万吨) 大型模锻油压机,是国家科技重大专项课题,压机于2013年4月在中国二重投产。
自由锻造安全技术

自由锻造安全技术自由锻造是指利用自由变形的原理,以机械或液压力为动力,在活塞、上模、下模和工件之间形成自由空间,将金属料锻造成所需形状的加工方法。
在制造业中,锻造加工被广泛应用于汽车、机械、航空、航天等领域,拥有着非常重要的地位。
但是,锻造加工过程中存在着很多安全隐患,特别是在自由锻造加工中,因为工艺特点和生产条件等因素,使得安全风险更加突出,必须进行细致而全面的安全措施。
锻造加工中的常见安全隐患在锻造加工过程中,由于工艺流程、机器设备和人员操作等方面的影响,常常发生安全事故,经常会有以下问题:1. 锤头脱落锻造机锤头是锻造加工过程中重要的设备,当其脱落时,很容易导致人员伤亡事故的发生。
2. 锻造机冲击在锻造加工过程中,机器设备可能出现冲击的情况,特别是在高速冲击的过程中,更加容易引发人员伤亡事故。
3. 工件移动由于锻造加工过程中金属材料经过高温和高力的作用,考虑到金属材料和设备之间的磨损问题,工件在锻造过程中很容易移动并造成危险。
4. 温度过高在锻造加工过程中,温度会非常高,容易影响人员的健康,特别是暑热天气会更为明显。
综上所述,锻造加工过程中常规的锻造机器设备、人员等方面普遍存在着安全隐患,需要采取相应的措施进行保障。
自由锻造安全措施为了保证锻造加工过程的安全性,自由锻造必须采取相应的安全措施,以减少事故的发生和最大限度地确保生产活动、工作人员以及现场的安全。
常用的安全措施包括以下方面:1. 监控氧气浓度在锻造过程中,会发生一定量的火产生,使其室内空气中的氧气浓度降低。
如果氧气浓度过低,容易引发爆炸和燃烧等危险,因此应当安装氧气侦测器进行预警和报警。
2. 安装防护装置在锻造过程中,可能会发生各种意外,如工件坠落、锤头脱落等,造成严重的人员伤害,因此应安装相应的防护装置和安全网。
3. 掌握操作技巧操作人员应该经过专业培训,掌握锻造加工中的相关技巧和安全知识,提高操作水平,从而减少事故发生的可能性。
800MN多向模锻液压机本体结构设计及分析

beam up—beam,lower
and horizontal beam by the丘nitc element soRware
ANSYS.It analysed their rationality.
By the contact method,the dissertation analysed the prestressed unitized
1.2多向模锻工艺简述
模锻生产在提高锻件的精度,节约金属材料,减少机械加工等方面具 有重要的作用,随着我国工业飞跃的前进,模锻已在工业生产中得到广泛 的应用。模锻的成形实质是将金属毛坯加热到锻造温度使其具有良好的塑 性,然后置于锻模的模腔内,在模锻设备的压力作用下,使其产生不可逆 的塑性变形而充满模腔,于是获得所需形状锻件的一种压力加工方法。
With this understanding,the dissertation designed the unitized construction of up—beam,lower beam and horizontal beam.
The dissertation analysed the key part three-dimensioned mode of unitary
论文基于液压机设计理论,参考已有大型模锻液压机结构和设计经验, 通过可行性分析,确定了800MN多向模锻液压机的结构与技术参数,给出 了压机的本体结构设计方案,在此基础上,论文分别给出了压机关键部件 包括上、下横梁及水平梁的分块组合结构设计。
论文以大型有限元软件ANSYS作为分析工具,对800 MN多向模锻液 压机的关键部件包括上、下横粱及水平梁的整体结构进行了三维计算,对 其结构设计的合理性进行了分析。
大型模锻液压机主要用于生产大型铝、镁合金以及钛和钛合金的模锻 件。过去,飞机的大梁是用铆接方式组合,大梁的重量重,铆钉孔容易产 生应力集中。采用大型压机整体模锻大粱,可以减轻重量,减少了接头, 消除应力集中。另外,采用自由锻件和轧材为毛坯进行机械加工时,由于 金属纤维被切断,机械强度被严重削弱,而模锻件的纤维方向与零件的轮 廓形状相符合,因此零件的强度高,使用寿命长。同时,还可以节约贵重 的高强度合金,减少零件机械加工与装配的工作量,用自由锻件或轧材制 造零件时金属利用率非常低,而用模锻件时金属利用率最高可达90%。
自由锻造安全技术

自由锻造安全技术根据力的性质,自由锻造设备可分为锻锤和压机。
锻锤产生冲击力使金属变形,而压力机产生静压力使金属变形。
锻锤能力的大小,是用落下部分的重量来表示。
锻锤分为空气锤和蒸汽锤。
液压机用于锻造大型锻件,所锻钢锭的重量为1-300吨。
其动力来源于高压水。
1. 自由锻造的职业危害(1)挫伤、烫伤自由锻操作过程中,最可能的危险是工件在锤击过程中被吹走,或高温氧化铁屑飞溅,挫伤并烫伤操作者。
(2)振动引起的疾病自由锻操作过程中,掌钳的工人承受着由钳子传到手臂的局部振动,以及由于锻锤打下使地基振动而引起的全身振动。
其他参加自由锻造的工人也遭受了不同程度的全身振动。
振动(特别是局部振动)对人体的危害有以下几个方面:a.振动导致末梢神经、末梢循环、末梢运动机能障碍;b.导致中枢神经系统机能障碍;c.振动导致骨骼、关节和肌肉系统疾病;d.导致心血管系统症状。
振动除了对人体有直接危害外,对厂房也有危害。
当厂房因振动发生损坏时,对人体会造成间接危害。
(3)高温中暑由于锻造车间温度较高,自由锻劳动强度也较大,工人有时因高温而中暑。
(4)热辐射眼病自由锻常将加热到1000℃左右的钢料进行锻打使其成形。
工人在操作过程中,始终要注视灼热的工件,高温工件会发出大量辐射能量,伤害人的眼睛。
(5)有害气体一些锻造车间使用的加热设备是燃料炉,因燃煤或燃油而产生的CO、SO2等有害气体使车间空气受到污染,对长期在车间工作的工人,也有一定的危害作用。
(6)噪音危害适用于各锻造车间员工,噪声是普遍性的职业性危害。
2. 自由锻造的安全技术与安全管理(1) 安全技术a.操作安全镦粗时,坯料最长以不超过锻锤行程的75%为适合,坯料过长不易把住,也易打出砧外。
粗锻要求将坯料加热至正确的初始锻造温度,使整个坯料温度均匀,以确保在镦粗时塑性好,变形均匀,不产生偏斜。
当产生偏斜后,校正时必须在终锻温度以上进行,以免在校正、打棱角时,因料硬而打飞。
- 1、下载文档前请自行甄别文档内容的完整性,平台不提供额外的编辑、内容补充、找答案等附加服务。
- 2、"仅部分预览"的文档,不可在线预览部分如存在完整性等问题,可反馈申请退款(可完整预览的文档不适用该条件!)。
- 3、如文档侵犯您的权益,请联系客服反馈,我们会尽快为您处理(人工客服工作时间:9:00-18:30)。
摘要: 通过对引进的80 " 0 K m 自由锻造操作机常见故障进行分析, N 提出了改进方案。改进后 , 锻件夹紧和松开是 通过柑口、 杠杆、 拉杆、 导向套支 夹紧油缸来实现的, 撑、 进免了夹紧 扛密封的泄漏。 控制系 统改用软件逻挥系 消除了 统, 硬件逻辉系统引起的故障隐患。 关健词: 操作机; 柑杆; 变1泵; 清动轴承
上。
4 个升降拐臂联接上部水平悬挂轴, 根铅垂悬吊杆悬吊 4 下部水平悬挂轴, 水平悬挂轴支撑钳杆架体, 各臂、 轴之间 杆、 均用球面关节轴承联接, 以满足平摆动及复位的要求。 升降缸和倾斜缸等面积串联, 可实现平行提升; 升降缸固 定, 倾斜缸动作可实现钳杆的上、 下倾动作。平行下降、 下倾主 要靠 自 重实现。 垂直缓冲采用了四 组碟簧, 用于承受锻造过程中的冲击和 补偿锻件变形后钳杆中心的下降。 由于操作机对中主要靠自 因此锻件对中迟缓。 重, 11 轨道、 . . 4 驱动拖链及水电引人装置 行走轨道采用起重机钢轨, 操作机轨道与链条固定在整体 焊接架体上, 架体预埋在基础内, 链条采用双排标准滚子链。 水电引人拖链通过操作机侧面进人地下拖链小车, 再与固 定水管和电缆联接。 采用进口 拉绳式位移传感器, 检测大车行
上。
电源, 其中包括 30 8 V动力电源, 0 2 V控制电源, V控制电 2 2 4 源等。工厂供电电缆从缆沟接入本电源控制系统。 () 2 工程师系统。工程师系统将提供操作机的操作、 状态 监视、 报表输出等画面, 对设备的调试与维修提供支持。提高 设备使用率, 缩短停机时间。该系统硬件选用国际名牌计算 机; 配置为: C U Ie etm G Pnu 24 内存:1 M ; P : n l i . ; t 52 硬盘: G ; 6 B软驱: 0 14 M ; . B 显示器: 英寸( 4 1 7 分辨率 12 x ) 04 6 。 78 133 总线系统 ..
中圈分类号: 1 T35 G
文献标识码; A
文章编号; 0 - 4 0) 04 - 1 1 5( 6Z - 7 0 2 2 3 0 l 1 0 3
用上下双板联接主墙板。前后吊挂轴还承担了两个主墙板的 上部联接, 主墙板的后部设置了两个操作机液压系统油箱, 两 个主墙板还对钳杆架体的左右摆动起限位作用。 操作机架体通过轴承座、 6 轴、 个车轮支撑在行走轨道上, 操作机最前端设置两对( 个) 4 车轮, 主要承担锻件质量和操作 机自 前部车轮带有双侧边, 重, 用于平衡锻件侧翻时传递到操 作机上的倾翻力。 后部的两个车轮带有单侧边, 使操作机沿行 走轨道直线前进。 后部车轮旁设置低速大转矩液压马达驱动 的 链轮, 链轮与行走轨道旁的地面链条啮合。左右两套大车驱 动装置通过螺栓和键与主墙板联接。地面链条的两端通过张 紧螺栓与基础预埋架体联接, 将大车行走驱动力传递到基础
上。
进口8 k m操作机基本满足了6 M 0 N・ 0 N水压机的使用, 通过锻造操作机与水压机的配合, 可以完成开坯、 延伸( 拔长) 、 嫩粗、 精整等多种锻造工艺。对使用中发现的一些问题做了一 些改进, 对于新设计的操作机提出了建议。操作机额定载重量 3t 5 , 最大夹持力矩80 m 夹持圆钢直径60 1 m , 0K N・ , 2 一 30 0 m 钳杆回转直径2 m 钳杆回转速度 6 i, 30 0 m, r n行走速度 0- / m
该控制系统具有大、 快的特殊要求, 精、 在保证系统冲击小 的情况下, 阀门要有高速度的启闭特性。控制阀阀门的动作相 应时间短, 重复性好, 保证操作机的控制要求。系统的设计满 足锻造压机的低压快速锻造要求。 液压系统集成化程度高, 系统全部由插装阀组成, 所有阀 组分别装在集成块上, 块体中加工各种( 抛光) 孔道, 盖板上又 插装了所有的功能元件, 这样缩短了连接通道管路, 布置紧凑 合理, 减少泄漏和损失, 也减轻了液压系统的冲击。阀块和油 缸的管道接口 全部采用法兰联接, 避免使用 J 96 B 螺纹管接 6
2 0 年增 刊 06
机 械 设 计
JU N O R AL F C I E E I N O MA H N D SG
20 06年 8 月
80 - 0 k m自由锻操作机技术研究’ N
崔怀旭‘密 2 2 , 建军 , 梁冰
(. 1天津市康库得机电技术有限公司, 天津 301; 鞍钢重型机械有限责任公司 锻造厂, 001 2 . 辽宁 鞍山 144 102
头。
主要阀站设有检测口, 检测各阀工作情况, 便于合理的调
试整个系统, 亦可使用仪器方便地检查系统的调试状况。
操作机的自动化控制系统以 S A I N T系列的总线 I T E M C P OIU D 连接, R F S B P 不需要复杂的安装就可以使数据在工程师 系统、 动化系统、 自 分布式外设和智能现场装置之间交换, 总线 的传输速率可达 1 M is . b/o 5 t 134 自 .. 动化系统 操作机的自 动控制系统以 S A C - I T S 34系统为基础, M 7 1 其具有模块化结构, 极好的升级容量与坚固性。 1 / 0外设使用分布式 E 20 T0M连接,T0M通过 P O I E 20 RF - B S 连接至中央部件C U 1 ID T P P , / 0外设使用S - 0 系列的信 7 30 号模块和功能模块组成提供高速、 可靠的控制操作。 自 动化系统属本电控系统中的关键系统, 完成机组联动机 设备协调运动控制, 它不但接收压机行程、 操作机大车行走、 钳 口 旋转等检测信号, 输出开关量对压机、 辅机、 操作机实施顺序 控制, 输出模拟量对操作机辅机的比例泵、 比例阀实施比例控 制。 同时它还对压机主缸、 回程缸和操作机液压系统的压力及 油温实时检测, 通过工程师系统实时显示或报警。
பைடு நூலகம்
13 电气控制系统 . 电气控制系统以西门子S 一 1 7 34为主控制器, 主操器、 按 钮和指示灯配置进口 施耐德手操器, 电气控制系统设有与主机 联动接口。 通过位移和压力检测信号, 程序上保护操作机不过 载, 不超出操作范围。
1 . 电控系统的特点 .8 3
() 1硬件设计考究, 关键元件选用进口件, 其中工程师系统 计算机和PC L 系统采用整机进口, 操作按钮及主操作手柄选用 施耐德等原装进口产品。 () 2 软件设计先进, 界面友好方便。在开发精度控制软件 时, 应用了实时性好、 算法准确的智能控制算法。开发的界面 软件, w dw 风格, 具有 i os n 使用方便而且完全汉化。 () 动化程度高。S 各系统各 自发挥固有的特长。它 3自 7 们相互协调工作, 实现了手动、 动、 动、 半自 自 联动操作方式, 达 到了较高的自动化水平。 () 4 可靠性高。系统中主要的易损件和关键元件都选用了 高质量的进口件, 还有全系统采用了软件逻辑, 消灭了过去硬 件逻辑而引起的故障隐患, 大大提高了系统的可靠性。机组中
4 0 / o 0 m s m
1 操作机整体结构及控制系统
操作机本体主要由夹钳装置、 钳杆装置、 水平侧移装置、 车 架装置、 吊挂装置、 钳杆旋转装置、 后桥、 大车驱动装置、 液压控 制系统、 电气控制系统、 轨道驱动链、 基础附件和升降倾斜装置 和水电引入拖链装置等部分组成。操作机的液压系统由油箱、 油泵电机组、 控制阀组、 蓄能器组、 冷却过滤装置、 管道系统等 组成。电气系统主要包括 PC L 装置、 电机控制柜、 操作台、 钳杆 转角检测、 大车行走位置检测、 夹钳缸压力检测、 倾斜缸压力检 测等。 11 操作机本体 . 111 夹钳、 . . 钳杆及旋转装置 夹钳采用销轴 V型结构, V型块采用耐热钢制作。钳头固 定在空心钳杆上, 锻件夹紧和松开是通过钳口、 杠杆、 拉杆、 导 向套支撑、 夹紧油缸来实现的。夹紧缸的密封起直线运动密封 和旋转密封作用。 低速大转矩液压马达通过减速齿轮驱动空 心钳杆, 实现钳头和钳杆的正反回转, 采用光电编码器检测钳 杆的回转角度位置。钳杆前端和后端通过合金铜套安装在钳 杆架体中, 钳杆架体通过两根抬杆及球面关节回转轴承与吊 杆 相连接。钳杆架体可以在吊杆上前后倾及水平侧摆。该操作 机钳口 夹紧缸采用了后置结构, 芯杆长度 6 m , 90 前端在钳 5 m 身滑套中 导向, 后中部与活塞头配合连接, 尾部与进出油路的 回转接头连接, 多级同心增加了机械卡紧和摩擦, 偏心磨损造 成密封的泄漏, 密封的频繁更换造成配合面的擦伤, 故夹紧缸 密封的泄漏是操作机主要故障之一。 11 车架装置及大车驱动 .. 2 车架体采用优质钢板整体焊接, 主墙板为箱形结构, 车架 体的前底部采用三根23 7 钢管联接主墙板, 车架体的后底部采
1 . 操作机电机控制系统 .5 3
操作机电机控制柜采用标准组合柜, 电机采用直接启动方
式。
1 . 操作机状态检测系统 .6 3 状态检测系统对操作机各个设备及装置的位置、 状态等非
电量参数进行检测, 并以电的形式反馈给控制系统。
1 夹钳装置; 钳杆装置; 水平侧移装r; 2 3 L 4车架装置; r挂装W; 5 } 6钳杆旋转装置;后桥;大车驱动装置;液压控制系统; 7 8 9 1 0电气控制 系统; 1 1 轨道、 驱动链、 基础附件;2升降倾斜装置; 1 1 3水电引人拖链 装置 圈1 0 " 锻造操作机原理圈 8 K m自由 0 N
137 电控系统的应用软件 ..
具有先进的设备组成, 配置优秀的应用软件, 才构成较完 美的电控系统。本电控系统采用 S M N PS 过程控制系 I E S 7 E C 统, 其中工程师系统计算机配置 S A I SE 7和 S A TC I TC P M T I AI M Wn , i c软件运行平台为 Wnos 0操作系统使工业应用更 c i w 20 , d 0 加安全, 功能更强大, 硬件实用性更好, 图形界面和用户沟通更 直接、 更方便、 更友好。
收稿日期: 6 0 - 8 20 - 6 2 0
前单车轮承担冲击载荷约60 , 0 k 车轮滑动轴承套内径为 N 1 m、 6 m 宽为20 , 0 4 m 接触面压为5 M a作为冲击载荷滑动 m 0 , P 轴承, 应力偏高, 实际使用中每两个月更换一对轴承。改用复 合材料轴承后, 寿命提高了两倍以上。 11 吊挂装置及升降倾斜装置 .. 3 吊挂装置由4 个升降拐臂、 上下两对水平悬挂轴、根铅垂 4 悬吊杆、 个水平主轴、 个升降缸, 个倾斜缸, 个垂直缓冲 2 2 2 2 吊杆组成。 个水平主轴、 个升降缸固定安装在左右主墙板 2 2