数控车床剃削螺纹头尾扣不完整部分的加工方法
压力容器大直径螺纹孔不完整螺纹的加工
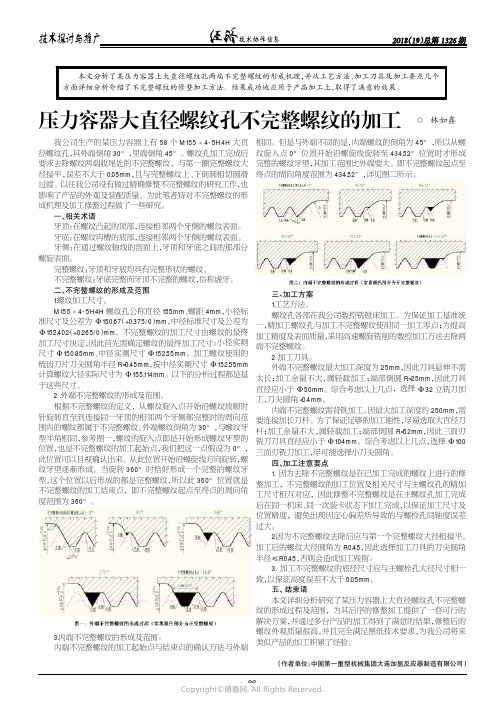
我公司生产的某压力容器上有58个M155×4-5H4H大直径螺纹孔,其外端倒角30°,里端倒角45°。
螺纹孔加工完成后要求去除螺纹两端收尾处的不完整螺纹,与第一圈完整螺纹大径接平,误差不大于0.05mm,且与完整螺纹上、下倒圆相切圆滑过渡。
以往我公司没有做过精确修整不完整螺纹的研究工作,也影响了产品的外观及装配质量。
为此笔者特对不完整螺纹的形成机理及加工修整过程做了一些研究。
一、相关术语牙顶:在螺纹凸起的顶部,连接相邻两个牙侧的螺纹表面。
牙底:在螺纹沟槽的底部,连接相邻两个牙侧的螺纹表面。
牙侧:在通过螺纹轴线的剖面上,牙顶和牙底之间的那部分螺旋表面。
完整螺纹:牙顶和牙底均具有完整形状的螺纹。
不完整螺纹:牙底完整而牙顶不完整的螺纹,俗称虚牙。
二、不完整螺纹的形成及范围1.螺纹加工尺寸。
M155×4-5H4H螺纹孔公称直径155mm、螺距4mm,小径标准尺寸及公差为Φ150.67(+0.375/0)mm,中径标准尺寸及公差为Φ152.402(+0.265/0)mm。
不完整螺纹的加工尺寸由螺纹的最终加工尺寸决定,因此首先需确定螺纹的最终加工尺寸:小径实测尺寸Φ150.85mm、中径实测尺寸Φ152.55mm。
加工螺纹使用的梳齿刀片刀尖圆角半径R=0.45mm,按中径实测尺寸Φ152.55mm 计算螺纹大径实际尺寸为Φ155.114mm。
以下的分析过程都是基于这些尺寸。
2.外端不完整螺纹的形成及范围。
根据不完整螺纹的定义,从螺纹旋入点开始沿螺纹线顺时针旋转直至到连接同一牙顶的相邻两个牙侧都完整时的周向范围内的螺纹都属于不完整螺纹。
外端螺纹倒角为30°,与螺纹牙型半角相同,参考图一,螺纹的旋入点即是开始形成螺纹牙型的位置,也是不完整螺纹的加工起始点,我们把这一点假设为0°,此位置可以目视确认出来。
从此位置开始沿螺旋线方向旋转,螺纹牙型逐渐形成。
当旋转360°时恰好形成一个完整的螺纹牙型,这个位置以后形成的都是完整螺纹,所以此360°位置就是不完整螺纹的加工结束点,即不完整螺纹起点至终点的周向角度范围为360°。
g92螺纹去半扣程序实例

g92螺纹去半扣程序实例一、什么是螺纹去半扣程序螺纹去半扣程序是一种用于加工螺纹的程序,通过指定不同的参数和算法,可以实现精确的螺纹加工。
螺纹去半扣程序是数控加工中的一项重要技术,它可以提高加工效率和加工质量,减少人为误差。
二、螺纹去半扣程序的原理螺纹去半扣程序的原理是根据螺纹的几何特征和加工要求,通过计算机控制工具路径的生成和移动,实现螺纹的加工。
它主要包括以下几个方面的内容:1. 螺纹参数的确定在编写螺纹去半扣程序之前,首先需要确定螺纹的参数,包括螺纹的直径、螺距、螺纹类型等。
这些参数将直接影响到螺纹加工的精度和质量。
2. 螺纹刀具的选择根据螺纹的参数和加工要求,选择适合的螺纹刀具。
螺纹刀具的选择将直接影响到螺纹加工的效率和质量。
3. 生成工具路径根据螺纹的参数和螺纹刀具的几何特征,通过计算机辅助设计软件生成工具路径。
工具路径是螺纹去半扣程序的核心内容,它决定了螺纹加工的轨迹和顺序。
4. 控制工具的移动通过数控系统控制工具的移动,实现螺纹加工。
数控系统根据工具路径和螺纹刀具的几何特征,控制工具的进给和转速,实现螺纹的加工。
三、螺纹去半扣程序的编写螺纹去半扣程序的编写需要遵循一定的规范和语法,下面是一个示例:N10 G90 G54 G92 S1000 M03 ; 程序开始,设置坐标系、初始速度和主轴转向N20 G00 X0 Z0 ; 快速移动到起始位置N30 G01 Z-10 F100 ; 沿Z轴线性插补下降到加工深度N40 G92 Z-10 ; 设置Z轴坐标为-10N50 G92.1 ; 取消坐标系设定N60 G00 X10 ; 快速移动到下一个位置N70 G01 Z-20 F100 ; 沿Z轴线性插补下降到加工深度N80 G92 Z-20 ; 设置Z轴坐标为-20N90 G92.1 ; 取消坐标系设定N100 M05 ; 关闭主轴N110 M30 ; 程序结束四、螺纹去半扣程序的应用螺纹去半扣程序广泛应用于各种机械零部件的加工中,特别是在汽车、航空航天、船舶等领域。
车床加工螺纹的方法

车床加工螺纹的方法嘿,咱聊聊车床加工螺纹的方法呗。
这车床加工螺纹啊,那可是个技术活呢。
首先呢,得准备好材料和工具。
材料就是要加工螺纹的那个零件啦,工具呢,有车床、刀具啥的。
车床可得选个好用的,别到时候老出毛病。
刀具也很重要哦,得选那种专门加工螺纹的刀具。
然后呢,把零件固定在车床上。
这可不能随便固定,得固定得稳稳当当的,不然加工的时候零件乱动,那可就麻烦啦。
可以用夹具把零件夹住,拧紧螺丝,确保零件不会松动。
接着就是调整车床的参数啦。
要根据零件的大小和要加工的螺纹规格来调整。
比如说转速啊、进给量啊啥的。
这可得有点经验,要是调不好,螺纹可能会加工得不好看或者尺寸不对。
开始加工的时候,要小心操作。
先让刀具轻轻接触零件,然后慢慢进给。
看着刀具在零件上切削出螺纹的形状,那感觉还挺神奇的呢。
加工的时候要注意观察,要是有啥不对劲的地方,赶紧停下来检查。
加工完一面之后,还得把零件翻过来加工另一面。
这时候也要小心,确保两面的螺纹能对齐。
要是对不齐,那可就不好看啦。
我给你讲个我叔叔加工螺纹的事儿吧。
叔叔是个老车工了,有一回他要加工一个螺纹零件。
他先把零件固定好,然后仔细调整车床参数。
开始加工的时候,他全神贯注地看着刀具和零件,一点都不敢马虎。
加工完一面后,他又小心翼翼地把零件翻过来加工另一面。
最后,那个螺纹零件加工得可漂亮了,尺寸也非常准确。
叔叔可高兴了,说这是他的得意之作呢。
总之呢,车床加工螺纹要准备好材料和工具,固定好零件,调整好参数,小心操作。
这样才能加工出漂亮的螺纹零件来。
关于数控车床螺纹车削的加工工艺常见问题分析及解决办法探讨

关于数控车床螺纹车削的加工工艺常见问题分析及解决办法探讨数控车床螺纹车削是机械加工中常见的一种工艺,常常用于制造螺纹连接件、螺纹轴等零部件。
在实际的加工过程中,经常会遇到一些常见的问题,这些问题不仅影响了生产效率,还可能导致产品质量不达标。
探讨数控车床螺纹车削的加工工艺常见问题及解决办法对于提高加工质量和效率具有重要意义。
一、加工过程中的常见问题分析及解决办法1、螺纹质量不达标螺纹质量不达标是数控车床螺纹车削中常见的问题之一。
造成这一问题的原因是多方面的,比如刀具磨损严重、切削参数设置不当、机床振动过大等。
针对这些问题,可以采取以下一些解决办法。
(1)定期更换刀具,确保刀具的切削性能;(2)合理设置切削参数,包括进给速度、主轴转速等,保证切削质量;(3)对机床进行定期维护,减小机床振动,改善加工质量。
2、芯部和头部连接不紧密螺纹加工中,芯部和头部连接不紧密会导致产品的质量问题。
这一问题可能是由于机床的刚性不够、夹具安装不稳等原因导致的。
对于这一问题,可以采取以下措施加以解决。
(1)提高机床的刚性,加强机床的支撑和固定;(2)优化夹具的设计和安装方式,确保夹具的稳定性;(3)增加刚性支撑,减小加工振动,保证连接的紧密性。
3、螺纹表面粗糙二、如何提高数控车床螺纹车削的加工效率除了解决加工过程中的常见问题外,提高数控车床螺纹车削的加工效率也是非常重要的。
以下是一些提高加工效率的方法。
1、优化切削参数合理设置切削参数,比如切削速度、进给速度、切削深度等,是提高加工效率的关键。
通过优化切削参数,可以达到快速而稳定的加工效果。
2、提高刀具和设备的使用寿命通过定期更换刀具、科学维护设备等方法,可以保证刀具和设备的良好状态,提高使用寿命,减少因刀具和设备磨损导致的停机次数,从而提高加工效率。
3、精心设计夹具和工装合理设计夹具和工装,确保工件的固定和稳定,可以有效地提高加工效率。
夹具和工装的设计应该考虑到工件的特性和加工过程的需要,从而提高加工效率。
螺纹首部去半扣的几种方法

1.螺纹刀或外圆刀(宏程序)采用“赶刀法”,就是使刀的X向定位不变,通过改变Z向定位的方式慢慢车掉半个牙距,把它给赶出来。
用G92和G32都可以车,下面以M24*3的螺纹来编宏程序。
G99T0101 M03 S500G0 X30.0 Z10.0#1=3.0N1 #1=#1-0.2IF[#1LT1.5] THEN #1=1.5 G0 Z#1G92 X20.7 Z-1.5 F3 J0 K0 IF[#1GT1.5] GOTO1G0 Z150.0M30 G99T0101 M03 S500G0 X30.0 Z10.0#1=3.0N1 #1=#1-0.2IF[#1LT1.5] THEN #1=1.5 G0 Z#1X20.7G32 Z-1.5 F3G0 X30.0(无退尾不用G32)IF[#1GT1.5] GOTO1G0 Z150.0M30注:一般不使用G76赶刀,由于X和Z方向都在移动,刀路比较复杂。
2.切槽刀用切槽刀来车,使用G76较为简单,前提是槽刀宽度大于半个牙底宽度,从牙顶车到牙底;还可使用G92、G32,采用X向“赶刀法”,即和车螺纹的刀路一致车到牙底;或G92、G32加宏程序都可以实现。
G99T0101(螺纹刀)M03 S500G0 X30.0 Z3.0G76 P010060Q100R50G76 X20.7Z-30.0P1600Q500F3 G0 Z150.0T0202(4mm切槽刀)M03 S500G0 X30.0 Z1.5G76 P010000Q100R50G76 X20.7Z-1.5P1600Q500F3 G0 Z150.0M30 G99T0101(螺纹刀)M03 S500G0 X30.0 Z3.0G92 X23.0Z-30.0 F3 ......X20.7G0 Z150.0T0202(4mm切槽刀)M03 S500G0 X30.0 Z1.5G92 X22.5 Z-1.5 F3 J0 K0 ......X20.7G0 Z150.0M30注:G76进刀角度无所谓,最后一刀落刀点在工件上就行。
数控螺纹尾部去半扣编程方法

数控螺纹尾部去半扣编程方法数控螺纹加工是现代机械加工中广泛应用的一种工艺,其高效性和精度优势使得它成为许多行业不可或缺的一部分。
而数控螺纹尾部去半扣编程方法则是在螺纹加工中的一种重要技术,它能够有效地解决螺纹尾部半扣的问题,提高螺纹加工的质量和效率。
在传统的螺纹加工中,螺纹的尾部通常会出现半扣现象,即尾部部分螺纹无法加工完成,给后续工序的装配或使用带来麻烦。
因此,为了解决这个问题,数控螺纹尾部去半扣编程方法应运而生。
数控螺纹尾部去半扣编程方法的主要步骤如下:第一步,确定螺纹加工开始和结束的位置:根据实际零件的要求,确定加工的起始和结束位置。
通常情况下,螺纹加工是从零件的一侧开始,然后沿着轴向依次加工到另一侧。
确定好加工的起始和结束位置可以帮助编程人员更好地安排加工路径和刀具补偿。
第二步,计算螺纹加工的参数:在进行数控螺纹编程时,需要计算出与螺纹相关的几个重要参数,包括螺距、螺纹角、圆整直径等。
这些参数是编程的基础,通过它们可以确定加工路径和加工方式。
第三步,分析尾部半扣原因并确定修正措施:通过对半扣现象的分析,可以确定其根本原因。
常见的尾部半扣原因包括刀具切削离开时间过早、切深或切宽设置不正确、切入切出策略设置错误等。
根据具体情况,可以采取适当的修正措施,如调整刀具补偿、优化刀具路径、调整刀具轨迹等。
第四步,编写加工程序并进行仿真验证:根据前面的步骤和参数计算结果,编写数控螺纹尾部去半扣的加工程序。
编写程序时要注意合理安排切削路径、刀具切入切出方式和切削参数。
完成编程后,可以利用机床的仿真功能进行验证,确保编写的程序可以正确地实现螺纹尾部去半扣的目标。
通过以上方法,可以有效解决螺纹加工中尾部半扣问题,提高加工的质量和效率。
但需要注意的是,在实际应用中,由于零件形状和要求的不同,编程的方法也会有所差异,需要根据具体情况进行调整和改进。
总之,数控螺纹尾部去半扣编程方法是一种有效解决螺纹加工中尾部半扣问题的技术。
螺纹去尾半扣加工实例

螺纹去尾半扣加工实例
下面是螺纹去尾半扣加工实例的步骤:
1. 准备工作:选择合适的螺纹去尾半扣刀具,并安装好在车床主轴上。
2. 将待加工的螺纹材料固定在车床上,注意材料的位置要够稳固,以避免加工时出现材料晃动等情况。
3. 调整刀具高度:在车床的X、Z轴上调整刀具的高度,使其正好与待加工的材料表面相切。
4. 调整刀具的偏角:根据实际需要,对刀具进行微调,使其能够顺利地加工出螺纹去尾半扣的形状和尺寸。
5. 加工螺纹去尾半扣:开动车床,控制好加工的速度和深度,让刀具沿着材料的螺纹方向切削,并逐步地将螺纹去尾半扣的形状加工出来。
6. 关注加工表面质量:加工过程中,需要经常关注加工表面质量和尺寸精度,及时进行调整,以保证最终的加工效果符合要求。
7. 完成加工:等到螺纹去尾半扣加工完成后,停机将材料取下,检查加工质量,并及时清理车床上的切屑和油污。
以上就是螺纹去尾半扣加工实例的详细步骤,需要注意的是,在实际加工过程中,一定要严格遵守安全操作规程,避免发生安全意外。
数控车床去除螺纹不完整螺扣宏程序研究

数控车床去除螺纹不完整螺扣宏程序研究螺纹被广泛应用于航空航天领域,是最常见的机械结构之一。
由于螺纹螺旋线的特殊性质,使螺纹在加工后会在所在轴径的起始端、结束端形成尖锐的不完整螺扣,该不完整螺扣易产生弯曲变形使得装配难度加大,降低螺纹的使用寿命,同时不完整螺扣在工作过程中脱落后会污染油路系统,对机器运行产生很大影响。
目前采用人工手动打磨或使用专用设备用以去除该部分,效率低、质量差,同时受工件结构限制,工装工具往往无法到达指定位置。
文章介绍了依据数控车床螺纹成形原理编制宏程序,实现螺纹加工、去除不完整扣一道工序高质量、高效率加工。
标签:螺纹;不完整螺扣;宏程序Abstract:Thread is widely used in the field of aerospace and is one of the most common mechanical structures. Because of the special properties of the spiral thread,the thread will form sharp incomplete snails at the beginning and end of the shaft diameter after machining. The incomplete screw thread is prone to bend and deform,which makes the assembly more difficult and reduces the service life of the thread. At the same time,the incomplete snails will pollute the oil system after falling off during the working process,which has a great impact on the operation of the machine. At present,manual grinding or the use of special equipment to remove this part has low efficiency and poor quality;at the same time,due to the structure of the workpiece constraints,tooling devices often can not reach the designated position. In this paper,in accordance with the principle of CNC lathe thread forming,the macro program is compiled to realize thread processing and remove incomplete buckles in a process of high quality and high efficiency.Keywords:thread;incomplete screw;macro program螺紋常见的加工方法有:攻丝、套丝、数控车、数控铣、滚压螺纹、磨螺纹等,其中数控车螺纹因其生产效率高、质量稳定、通用性强而被广泛应用。
数控车床螺纹的加工方法

数控车床螺纹的加工方法摘要:螺纹加工是车床操作工必备技能。
在目前的数控车床中,螺纹切削一般有G32直进式切削方法、G76斜进式切削方法,结合我院实践教学融入质量控制技术,争取加工出高精度的零件及高的合格率。
关键词:数控加工螺纹切削加工方法一、数控加工中螺纹的主要加工方法在目前的数控加工中,螺纹切削一般有两种方法:G32直进式切削方法和G76斜进式切削方法,由于切削方法不同,编程的方法不同,加工误差也不同。
我们在操作使用中要仔细分析。
其中指令G32用于加工单行程螺纹,编程任务重,程序复杂;指令G76克服了指令G32的缺点,可以将工件从坯料到成品螺纹一次性加工完成,且程序简捷,可节省编程时间。
1.G32直进式切削方法,由于两侧刃同时工作,切削力较大,而且排削困难,因此在切削时,两切削刃容易磨损。
在切削螺距较大的螺纹时,由于切削深度较大,刀刃磨损较快,造成螺纹中径产生误差;但是其加工的牙形精度较高,因此一般多用于小螺距螺纹加工。
由于其刀具移动切削均靠编程来完成,因此加工程序较长;由于刀刃容易磨损,因此加工中要做到勤测量。
2.螺纹加工完成后可以通过观察螺纹牙型判断螺纹质量及时采取措施,当螺纹牙顶未尖时,增加刀的切入量会使螺纹大径增大,增大量视材料塑性而定;当牙顶已被削尖时,增加刀的切入量,则大径成比例减小。
要根据这一特点正确对待螺纹的切入量,防止报废。
二、车削螺纹应注意的问题1.确定车螺纹切削深度的起始位置,将中滑板刻度调到零位,开车,使刀尖轻微接触工件表面,然后迅速将中滑板刻度调至零位,以便于进刀记数。
2.试切第一条螺旋线并检查螺距。
将床鞍摇至离工件端面8―10牙处,横向进刀0.05左右。
开车,合上开合螺母,在工件表面车出一条螺旋线,至螺纹终止线处退出车刀,开反车把车刀退到工件右端;停车,用钢尺检查螺距是否正确。
3.用刻度盘调整背吃刀量,开车切削。
螺纹的总背吃刀量ap与螺距的关系按经验公式ap≈0.65P,每次的背吃刀量约0.1。
数控车床上加工螺纹的各种方法(附螺纹宏程序实例)

数控车床上加工螺纹的各种方法(附螺纹宏程序实例)数车螺纹加工常用的三种进刀方式:直向进给侧向进给交替进给不同的进给加工方式,对刀具磨损和螺纹质量具有不同的影响。
一、直向进给这种切削方法,需要刀具牙型和螺纹牙型完全一样。
螺纹刀切入零件后,整个切削刃都受力。
随着车刀切的越深,刀具切削刃切削的长度越长。
当切削刃切削的长度越长,刀具和零件承受的切削力越大。
好,理解这种走刀方式的特点之后,解决办法:1,这种走刀方式,小螺距螺纹优先选用。
2,编程时候切深随着切深越深,刀具切削刃切削的长度越长,切削力会越来越大,所以切深最好逐渐减少。
下面举个例子,比如加工M20x2的外螺纹(底径17.825)二、侧向进给这种切削方式是,主要靠刀具一侧的切削刃来切削。
刀牙型可以小于或等于螺纹牙型,若选择的刀具等于螺纹牙型,也就是所谓的成形刀,随着切削越深,刀具整个切削刃也都受力。
所以建议选择刀具比螺纹牙角度略小一些,这样加工大螺距螺纹可以减少切削过程中的震动。
好,下面我用一个宏程序举个例子,比如牙型比较大的圆弧螺纹,来完成侧向车削。
通过圆的参数方程式很快就完成程序编写,程序比较简单不再赘述。
三、交替进给刀具以左右交替进给的方式切入工件,把螺纹牙槽逐渐扩展到规定的尺寸。
这种切削适用于极大螺距的螺纹,可以显著减少切削过程中的震动。
需要注意:刀具牙型尺寸要小于螺纹牙型尺寸,这样才能完成交替借刀。
好,下面我用一个宏程序举个例子,比如牙型比较大的圆弧螺纹并,来完成交替车削,直接采用变量,代替零件的具体尺寸,简图如下:好了,更多思路上的分析就不详细讲了。
用心看一下上面程序用心看上面变量之间逻辑推理关系,因为太多人泛泛一看觉得知道了,甚是令人担忧。
大家切记,知道不等于会,只有认真思考,勤于实践,方能学到真本事!好东西,你要学!。
快速定位螺纹起点去除不完全螺纹的方法研究及实施

2018年第8期时代农机TIMES AGRICULTURAL MACHINERY第45卷第8期Vol.45No.82018年8月Aug.2018快速定位螺纹起点去除不完全螺纹的方法研究及实施周晓星(中国航发南方通发公司,湖南株洲412002)摘要:螺纹的起端和终端都有不完全的螺纹,这部分螺纹就称作不完全螺纹。
螺纹不完全齿齿形逐渐形成锋利的飞边,在入口处齿形薄如刃口,在加工过程中由于切削力的因素或热处理因素极易变形,在装配时会产生无法拧入或咬死的现象。
对于传动螺纹的不完全齿的去除则更显重要。
关键词:不完全螺纹;螺纹起点定位;零件加工作者简介:周晓星(1987-),男,河南郑州人,大学本科,助理工程师,主要研究方向:机械加工。
不完全螺纹的去除方法有车工去除、钳工去除、数铣去除。
对于较小的螺纹,钳工去除的效率高且成本低;一般的螺纹均可使用车工去除,但大的传动螺纹如ACME 螺纹等则使用数铣方式要快,且数控机床加工的质量稳定。
本方案采用卧式加工中心去除不完全螺纹的首扣。
1存在的主要问题经常不能完全去除不完全螺纹,不合格率达95%,需要经常返修;加工中靠操作者目视确定螺纹起点作为编程的零点,但螺纹起点不易确定,对操作者的要求较高,需要调整8-10次才能完成加工,在调整过程中,还容易对完整的螺纹造成过切,存在较大的质量风险。
2原因分析造成返修和加工中多次调整的主要原因在于:不完全螺纹的起点不易确定,仅靠操作者目视不能准确定位螺纹起点,这样,零件的零点就与数控程序中编程零点不重合,导致需要多次调整零件位置,确定螺纹起点也即零件零点与程序零点重合进行加工,在调整过程中,还要对程序中的深度进行调整,这样还导致刀具对完整螺纹造成过切,具有极大的质量风险。
虽说这是个小问题,但是该零件加工费$4031.6,材料费$1309.5,总费用达到$5,341.21,且该去除不完全螺纹工序已经到最后工序,如果不能保证不完全螺纹完美的去除,损失也是很大的。
常用螺纹切削加工方法,车螺纹避免出现乱扣、扎刀,该怎么操作

常用螺纹切削加工方法,车螺纹避免出现乱扣、扎刀,该怎么操作常用螺纹切削加工方法
工艺流程
车端面一车螺纹大径(d<公称直径)一车退刀槽(<螺纹小径)→倒角→车螺纹(多刀车削)
安装技巧
•安装工件
选择合适的夹紧位置。
有足够的夹紧力。
•安装刀具
安装要点:刀尖分角线垂直于工件轴线。
•机床调整
针对螺纹车削
调整主轴转速
调整螺距
螺纹车削操作方法与步骤
•正反车车削法
•抬闸法
利用开合螺母的压下和抬起来车削螺纹。
注意事项
1、避免“乱扣”
【如果后一刀未能准确的落在前一刀已车出的反车的方法螺纹槽中,造成工件报废。
】
•若丝杠螺距不是工件螺距的整数位,须用正反车的方法采取倒顺车进行车削.
•工件与主轴之间的相对位置不能变动。
•如果换刀或磨刀,则应重新对刀。
2、防止“扎刀”
【加工余量分配不合理,或一次车削的余合理分多,而使螺纹两侧面粗糙严重甚至崩刃。
】
•工件、刀具装夹
•合理分配余量,选择合适的进刀方法
•及时退刀。
大螺距螺纹端部及牙顶修整方法

大螺距螺纹端部及牙顶修整方法大螺距螺纹端部及牙顶修整方法■ 山西平阳重工机械有限责任公司(侯马 043003)孟雅琴陶祥玉韩伟摘要:随着公司对数控车床的普及应用,对于大螺距螺纹加工,在车削螺纹端头以及尾部时,因不足以形成一个完整的牙型而形成的飞边毛刺较大的问题,探索出了一种在数控车床上螺纹车削完毕后,直接去除螺纹扣头扣尾的方法。
公司近年来研制的液压支架、立柱的导向套与缸筒普遍采用了螺纹式联接。
螺纹由以前的普通三角螺纹逐步改进为大螺纹(一般为10mm、8mm)的梯形螺纹和矩形螺纹。
1. 大螺距螺纹传统加工方法的弊端此类大螺距螺纹由于一般切得较深且螺距较大,在车削螺纹端头以及尾部时,因不足以形成一个完整的牙型而导致飞边毛刺较大,直接影响装配,致使在装配过程中给螺纹的导入带来极大的不便,经常划伤零件配合表面,造成螺纹研伤甚至零件报废;另外矩形螺纹牙顶毛刺,也会给螺纹导入及装配带来极大的不便。
传统规避毛刺的两种方法:①完全由手工操作,用挫刀或者风动砂轮来打磨修整,这样的方法需要具有一定技能的工人来实施,加工质量不稳定;打磨时砂轮粒容易飞出而造成安全隐患。
②用铣工铣削来修整牙型,可有效避免人工操作的弊端,但容易夹伤零件表面,且准备工作繁琐,清理一次也要花费一些时间,不仅制约生产进度,还会导致工艺执行不到位,形成质量安全隐患。
2. 螺纹扣头扣尾去除方法随着公司对数控车床的普及应用,我们探索出了一种在数控车床上车削完螺纹后,直接去除螺纹扣头扣尾的方法。
原理是充分利用数控车床的特性,即在车削螺纹时的快速收尾(退刀)功能,同时Z向每次都能停在一个固定点上,分多次退刀,反复车削,使其形成一个固定曲线,从而达到去除扣头扣尾的目的。
用此方法去除扣头扣尾需注意以下几个问题:①去扣头刀具宽度必须大于螺纹牙根宽度,以便一次去除成功。
②去扣头刀具与车削螺纹刀具的入扣问题,通过改变螺纹起始点,使两把刀具在同一点入扣。
③去除扣头刀具与车削螺纹刀具方向一致,去除刀具则相反。
如何在数控车床上修复螺纹
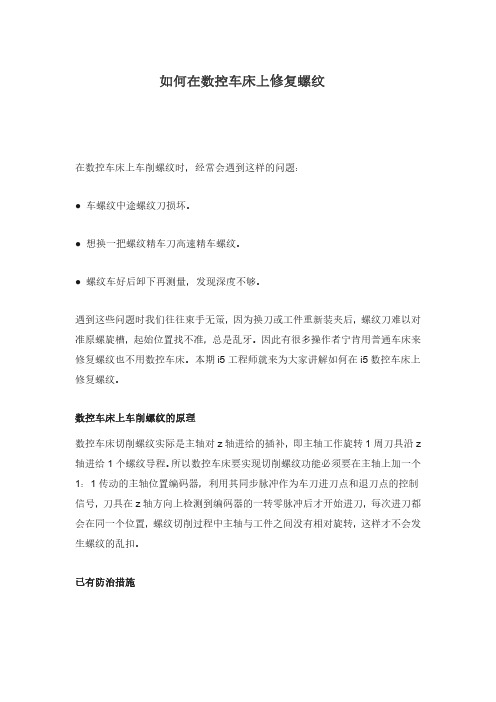
如何在数控车床上修复螺纹在数控车床上车削螺纹时,经常会遇到这样的问题:● 车螺纹中途螺纹刀损坏。
● 想换一把螺纹精车刀高速精车螺纹。
● 螺纹车好后卸下再测量,发现深度不够。
遇到这些问题时我们往往束手无策,因为换刀或工件重新装夹后,螺纹刀难以对准原螺旋槽,起始位置找不准,总是乱牙。
因此有很多操作者宁肯用普通车床来修复螺纹也不用数控车床。
本期i5工程师就来为大家讲解如何在i5数控车床上修复螺纹。
数控车床上车削螺纹的原理数控车床切削螺纹实际是主轴对z轴进给的插补,即主轴工作旋转1周刀具沿z 轴进给1个螺纹导程。
所以数控车床要实现切削螺纹功能必须要在主轴上加一个1:1传动的主轴位置编码器,利用其同步脉冲作为车刀进刀点和退刀点的控制信号,刀具在z轴方向上检测到编码器的一转零脉冲后才开始进刀,每次进刀都会在同一个位置,螺纹切削过程中主轴与工件之间没有相对旋转,这样才不会发生螺纹的乱扣。
已有防治措施目前,在企业中使用数控车床车削螺纹时,多数采用一把机夹刀车削。
粗、精都采用—把刀,同一个转速。
如中途刀坏了,则不卸刀杆,直接换刀片来防止乱牙。
但如果粗车.精车两把刀分开进行车削或零件重新装夹,则就带来了乱牙的问题。
解决方法目前数控机床上常用修复螺纹的方法有螺纹入刀位置动态修正法和零位信号线标记法。
螺纹人刀位置动态修正法(图一):是先大概确定螺纹的人刀位置,慢速空车螺纹,观察螺纹的轨迹是否和原螺纹的螺旋槽重合,再动态地修正螺纹的入刀位置,直到螺纹的轨迹和原螺纹重合。
这种方法修复螺纹费时、麻烦且很难找准螺纹的人刀位置和原来位置重合,易乱扣,修复成功率低。
△图一零位信号线标记法(如图二):在卡盘圆周表面相应位置刻零位信号标记,以确定螺纹车削起点,使零位信号标记刻线和工件螺纹的起始位置在同一轴向剖面内。
这种方法找正的时间长,加工效率低。
△图二下面介绍i5数控车床主轴自动定位修复螺纹的方法。
螺纹的修复要进行二次装夹,很难保证螺纹工件的入刀位置与主轴位置编码器的一转零脉冲信号位置重合,会形成一定的角度,并且对刀的难度也很大,所以螺纹的修复加工比较困难,操作不好,很容易破坏原来的螺纹形状。
7数控车床螺纹切削方法分析与应用

数控车床螺纹切削方法分析与应用在目前的数控车床中,螺纹切削一般有两种加工方法:G32 直进式切削方法和G76 斜进式切削方法,由于切削方法的不同,编程方法不同,造成加工误差也不同。
我们在操作使用上要仔细分析,争取加工出精度高的零件。
1.两种加工方法的编程指令G32 X〔U〕_Z〔W〕_F_;说明:X、Z 用于绝对编程;U、W 用于相对编程;F 为螺距;G32 编程切削深度分配方式一般为常量值,双刃切削,其每次切削深度一般由编程人员编程给出。
G76P〔m〕〔r〕〔a〕Q(△dmin〕R〔d〕;G76X 〔U〕Z〔w〕R〔i〕P〔k〕Q〔△d〕F〔l〕;说明:o m:精加工重复次数;o r:倒角宽度;o a:刀尖角度;o △dmin:最小切削深度,当每次切削深度〔△d·n?-△d·(n-1)?〕小于△dmin 时,切削深度限制在这个值上;o d:精加工留量;o i:螺纹局部的半径差,假设i=0,为直螺纹切削方式;o k:螺纹牙高;o△d:第一次切削的切削深度;o l:螺距。
G76 编程切削深度分配方式一般为递减式,其切削为单刃切削,其切削深度由控制系统来计算给出。
2.加工误差分析及使用G32 直进式切削方法,由于两侧刃同时工作,切削力较大,而且排削困难,因此在切削时,两切削刃容易磨损。
在切削螺距较大的螺纹时,由于切削深度较大,刀刃磨损较快,从而造成螺纹中径产生误差;但是其加工的牙形精度较高,因此一般多用于小螺距螺纹加工。
由于其刀具移动切削均靠编程来完成,所以加工程序较长;由于刀刃容易磨损,因此加工中要做到勤测量。
G76 斜进式切削方法,由于为单侧刃加工,加工刀刃容易损伤和磨损,使加工的螺纹面不直,刀尖角发生变化,而造成牙形精度较差。
但由于其为单侧刃工作,刀具负载较小,排屑容易,并且切削深度为递减式。
因此,此加工方法一般适用于大螺距螺纹加工。
由于此加工方法排屑容易,刀刃加工工况较好,在螺纹精度要求不高的情况下,此加工方法更为方便。
- 1、下载文档前请自行甄别文档内容的完整性,平台不提供额外的编辑、内容补充、找答案等附加服务。
- 2、"仅部分预览"的文档,不可在线预览部分如存在完整性等问题,可反馈申请退款(可完整预览的文档不适用该条件!)。
- 3、如文档侵犯您的权益,请联系客服反馈,我们会尽快为您处理(人工客服工作时间:9:00-18:30)。
0 引言
螺纹加工时在头 、尾 部分 因不足 以形成 完整 牙形 ,于是会 产生不完整的尖 锐部分 ,由于受切削力及残余 应力影 响其会发 生弯曲变形 ,这是螺纹加工 中无法避免的现象。
用 常规 的数控JJHT-方法加工螺纹 时 ,对于螺 纹头尾 扣的不 完整部分 ,通常采用人 工打磨 或其他 设备来 去 除 ,去 除过程 完 全是 由人工操作 ,加工质量不稳定 ,还极易损伤到相邻 的牙 形。
2011—03—01 8.55 147.87 l_7 0 0 0 0 156.42
2011 03—02 7.27 134.21 1.9 0 0 0 0 141.48
201l—O3—03 8.08 144.07 l_4 0 0 0 0 152.15
2011-03—04 0 0 0 0 0 0 0
现 以 SIEMENS 802D操 作系 统为例 ,编 制一个 剃 削 Tr80 × 12螺纹 头尾 扣 不 完 整 部 分 的车 削 程 序 (图 1)。
迹 和每 一 条 这 种 斜 直 线 运 动 的起 始 点 和 终 止 点 。 每 一 条 曲线 就是一条端面锥度螺纹曲线 ,其锥 角的大小决定 了渐 升面 的陡 峭程度 ,渐升面越 陡峭,被修整掉的尖锐部分 就越少 ;渐升面越 平缓 ,被修 整掉 的尖锐部分就越多 。
现在 ,假设修整后螺纹尖锐部分 的最小 宽度为 2 mm,被修 整 的螺 纹 为 1/4扣 ,那 么 ,剃 扣 (最 后 一 刀 )的起 始 点 与 螺 纹 切 削 的起 始 点 Z 向距 离 应 该 是 螺 距 的 整 数 倍 加 上 一 个 螺 纹 牙 底 的 宽 度 。
切削方法就是将 螺纹 的起刀点 渐次后移 (或前移 ),先 走轴
机 电信 息 2015年第 12期 总第 438期 77
G。ngY vu snu:三至主茎 l
现 ,载 气 已无 压 力 ,需 更 换 载 气 。 表 5 恰甫其海水 电站 1#主 变 色谱 在 线 监 测 数 据 单 位 :t ̄L/L
时间
H CO CH C2H H Hz总 烃 总 可 燃 气 油 温 状 态
向螺 纹 ,走 到削一 平 点一后 ,转 为 走 端 面 锥 度 螺 纹 。 螺 头 剃 扣 的 走
刀 形 式 如 图 3所 示 。
盟
1兰
图 3 螺 头剃 扣 的 刀具 运 行 轨 迹
现在 ,假设彻时头螺 螺纹。切 削盘噜嘲时,ll y的/起一 一刀十一 点 z值 为 2O,剃扣 的轴 向进
N50 G33 Z=R4 K12(轴 向直 螺 纹 段 走 刀 ) N60 Z—R4— 3 X—R1+ 13 126(端 面锥 螺 纹 段 走 刀 ) N70 GO Z— R2(Z向 退 刀 ) N80 R2一 R2一R3 R4一 R4一 R3(给 起 刀 点 和 转 折 点 赋 增 量 ) N90 IF R4> 一一2 GOTOB TIKOU( ̄O断是否切 削完成 , 如果 尚未完成 ,转到循环起始点) N100 Z100 M5 M9(停主轴 ,关冷却液 ) N110 M17(子程序结束 ,返回主程序) (下转第 79页)
量 ,R4一 转 折 点 Z值 )
N40 TIKOU:X=R1 Z— R2(循 环 起 点 标 志 ,刀 具 到 走 刀 预 备 点 )
图 2 螺 纹 头 扣 尖锐 部 分 剃 削 前 后 对 比
现在就来 看看这个 渐升 面是如 何产生 的。我 们设 想有 这 样的两条平行曲线段 :它的一端 和螺 纹 的牙 底 (圆柱 面)相 切 , 另一端与螺纹的牙顶相交 ,它有着 和螺 纹相 同的升角 。我们将 这两条曲线的对应 点相 连 ,这些连线所构成 的 曲面就 是我们想 要 的 渐升 面 。 于是 ,要 去 除 螺 纹 尖 锐 部 分 ,就 是 要 构 建 一 簇 这 样 的曲线 。这个 曲线是 由刀具 的斜直线 运动加 上产 品 的旋转 运动 复合 出来 ,我们要做的事情就是确定刀具 斜直线 的运动轨
刀 量 为 0.1,则 剃 扣 第 一 刀 起 始 点 的 Z值 为 :2O+ 4.4+ 2—
一 26.4,转折点 的 Z值 为 0;第二 刀起刀点 的 z值为 26.3,转折点
为 一0.1;依 次 类 推 ,最 后 一 刀 起 刀 点 的 Z值 为 24.4,转 折 点 为
一 2。
塑 一 程序如下 :
G。ngYi vu—jsnu!三至主茎 l
数 控 车 床剃 削 螺 纹 头 尾 扣不 完整 部 分 的 加工 方 法
官 旭 苟永 明 王 向旗 (中石化 石油 工程 机械有 限公司 第 四机械 厂 ,湖 北 荆州 434024)
摘 要 :利 用数 控 车后 ,螺 纹头 尾会 出现 不完 整部 分 ,通 常需 采用 人工 打磨 或其 他 设 备来 去 除 ,这 不仅延 长 了产 品加工 周期 ,增加 了物 流成 本 ,还 占用 了其 他 资源 ,没有 充分 发挥数 控 车床 的优势 。现 经 过反 复试 验 摸索 ,编 制 了一 个加 工螺 纹头 尾扣 不完 整部 分 的宏 程 序 ,实 现 了在螺纹 加 工完 成后 同时 ̄t j ̄l j头 尾扣 的不 完整 部分 。
最一
般一
N10 T1 D1 G54 GO X82(调 取 刀 位 、刀补 值 和 零 偏 值 )
N20 Z100 M4 M8¥300(右 旋螺 纹 ,所 以机床 反 转 ,转 速
300 r/r ain,开 冷 却 液 )
N30 R1—68.4 R2—26.4 R3— 0.1 R4— 0(参 数 赋 初 值 , R1一 牙 底 直 径 ,R2一 起 刀 点 Z 值 ,R3一 每 次 切 削 的 轴 向 进 刀