干熄焦装置冷却段耐材研究应用新进展
干熄焦冷却段的作用
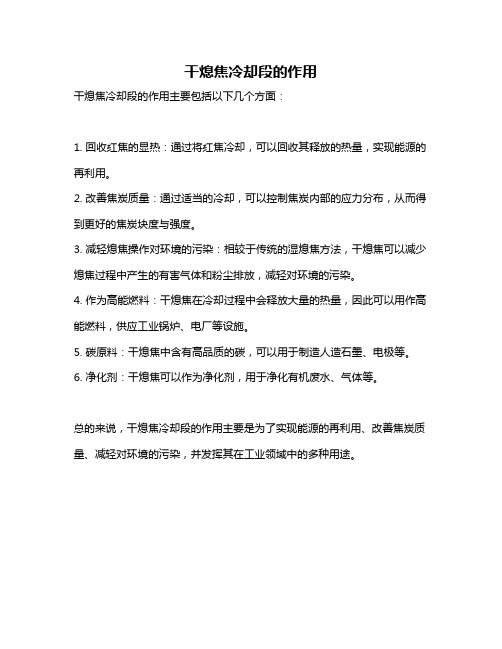
干熄焦冷却段的作用
干熄焦冷却段的作用主要包括以下几个方面:
1. 回收红焦的显热:通过将红焦冷却,可以回收其释放的热量,实现能源的再利用。
2. 改善焦炭质量:通过适当的冷却,可以控制焦炭内部的应力分布,从而得到更好的焦炭块度与强度。
3. 减轻熄焦操作对环境的污染:相较于传统的湿熄焦方法,干熄焦可以减少熄焦过程中产生的有害气体和粉尘排放,减轻对环境的污染。
4. 作为高能燃料:干熄焦在冷却过程中会释放大量的热量,因此可以用作高能燃料,供应工业锅炉、电厂等设施。
5. 碳原料:干熄焦中含有高品质的碳,可以用于制造人造石墨、电极等。
6. 净化剂:干熄焦可以作为净化剂,用于净化有机废水、气体等。
总的来说,干熄焦冷却段的作用主要是为了实现能源的再利用、改善焦炭质量、减轻对环境的污染,并发挥其在工业领域中的多种用途。
我国干法熄焦技术发展与应用
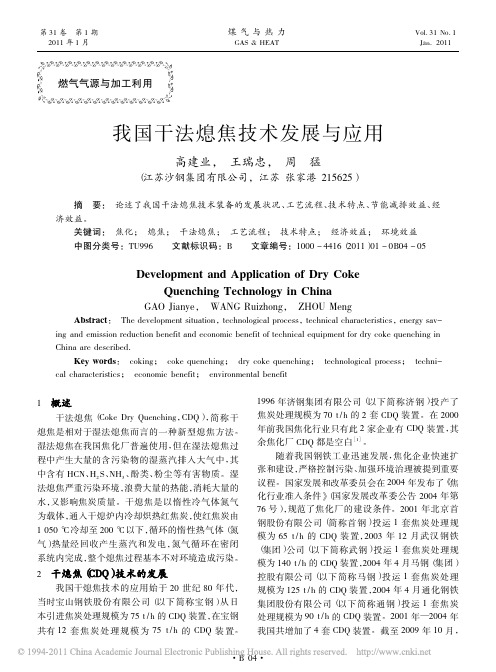
单套 CDQ 装置 企业 涟源钢铁集团有限公司 杭州钢铁集团公司 鄂城钢铁集团有限责任公司 通化钢铁集团股份有限公司 昆明钢铁集团有限责任公司 南京钢铁联合有限公司 广西柳州钢铁( 集团) 公司 宁波钢铁有限公司 太原钢铁( 集团) 有限公司 本溪钢铁( 集团) 公司 宝钢集团上海梅山有限公司 包头钢铁( 集团) 有限责任公司 的焦炭处理规
Development and Application of Dry Coke Quenching Technology in China
GAO Jianye, WANG Ruizhong, ZHOU Meng
Abstract: The development situation, technological process, technical characteristics, energy saving and emission reduction benefit and economic benefit of technical equipment for dry coke quenching in Key words: coking; coke quenching; dry coke quenching; cal characteristics; economic benefit; environmental benefit technological process; techni-
形烟道排出干熄炉。高温循环氮气经过一次除尘器 分离粗颗粒焦粉后进入70 ~ 190 ℃ 。 低温循环氮气从干熄焦余热锅炉出来, 经过二次除 尘器进一步分离细颗粒焦粉后, 由循环风机送入给 水预热器。给水预热器将循环氮气的温度从 160 ~ 180 ℃ 冷却至约 130 ℃ , 再进入干熄炉循环使用。
干熄焦系统干熄炉结构、冷却原理及控制措施

干熄焦系统干熄炉结构、冷却原理及控制措施1、干熄炉结构:⑴、圆型干熄炉由预存段、斜道区及冷却段组成。
⑵、干熄炉为圆形截面竖式槽体,外壳用钢板及型钢制作,内衬隔热耐磨材料,干熄炉顶设置环形水封槽。
⑶、干熄炉上部为预存段,中间是斜道区,下部为冷却段。
⑷、预存段的外围是汇集36个斜道气流的环形气道,它沿圆周方向分两半汇合通向一次除尘器。
⑸、预存段设有料位计、压力测量装置、测温装置及放散装置。
⑹、环形气道设有空气导入装置、循环气体旁通装置、气流调整装置。
⑺、冷却段设有温度测量孔、干燥时的排水汽孔、人孔及烘炉孔。
⑻、冷却段下部壳体上有两个进气口,冷却段底部安装有供气装置。
⑼、预存段用于接受间歇装入的红焦,具有缓冲功能,可补偿生产的波动。
⑽、在冷却段,红焦与低温循环气体进行热交换,经降温冷却后排出。
⑾、斜道区位于预存段与冷却段之间,从干熄炉底部供气装置进入的低温循环气体吸收红焦的显热后经斜道及环形气道排出,并流经干熄焦锅炉进行热交换。
2、主要技术规格:⑴、预存室容积:320m3;⑵、允许上限中断供焦时间:1h;⑶、预存室直径:~8040mm;⑷、装料孔直径:~3100mm;⑸、冷却室总容积:580m3;⑹、冷却室容积:420m3;⑺、冷却室直径:~9000mm;⑻、干熄炉总高度(含供气装置):~25900mm;⑼、公称处理能力:130.35t/h;⑽、排焦上限处理能力:145t/h;⑾、入干熄炉冷循环气体量:~180000m3/h;⑿、入炉循环气体的吨焦气料比:~1250m3/tJ。
3、干熄焦焦炭冷却原理:⑴、在干熄炉冷却室,焦炭向下流动,循环气体向上流动,焦炭通过与循环气体进行热交换而冷却。
焦炭的冷却时间主要取决于气流与焦炭的对流传热和焦块内部的热传导,冷却速度则主要取决于循环气体的温度和流速,以及焦块的温度和外形表面积等。
⑵、进入干熄炉的循环气体的温度主要由干熄焦锅炉的省煤器决定。
省煤器入口的除盐、除氧水温度为104℃左右,出省煤器的循环气体温度可降为约160℃,由循环风机加压后再经过热管式换热器进一步降温至约130℃后进入干熄炉与焦炭逆流传热,干熄炉排出的焦炭可冷却至200℃以下。
干熄焦技术装备应用与发展
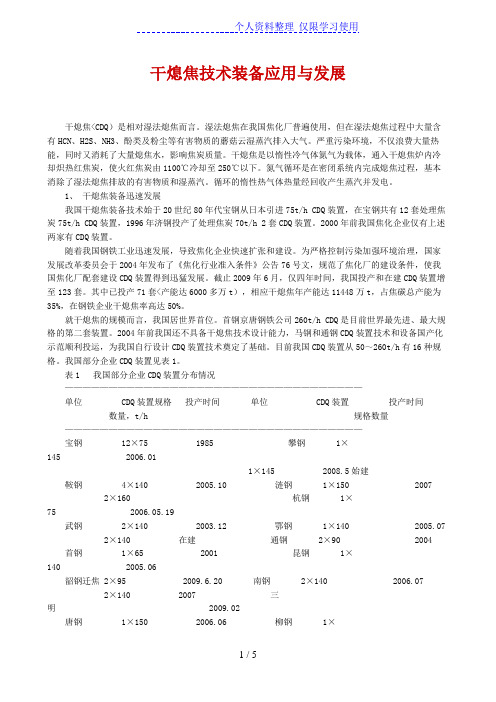
干熄焦技术装备应用与发展干熄焦<CDQ)是相对湿法熄焦而言。
湿法熄焦在我国焦化厂普遍使用,但在湿法熄焦过程中大量含有HCN、H2S、NH3、酚类及粉尘等有害物质的蘑菇云湿蒸汽排入大气。
严重污染环境,不仅浪费大量热能,同时又消耗了大量熄焦水,影响焦炭质量。
干熄焦是以惰性冷气体氮气为载体,通入干熄焦炉内冷却炽热红焦炭,使火红焦炭由1100℃冷却至250℃以下。
氮气循环是在密闭系统内完成熄焦过程,基本消除了湿法熄焦排放的有害物质和湿蒸汽。
循环的惰性热气体热量经回收产生蒸汽并发电。
1、干熄焦装备迅速发展我国干熄焦装备技术始于20世纪80年代宝钢从日本引进75t/h CDQ装置,在宝钢共有12套处理焦炭75t/h CDQ装置,1996年济钢投产了处理焦炭70t/h 2套CDQ装置。
2000年前我国焦化企业仅有上述两家有CDQ装置。
随着我国钢铁工业迅速发展,导致焦化企业快速扩张和建设。
为严格控制污染加强环境治理,国家发展改革委员会于2004年发布了《焦化行业准入条件》公告76号文,规范了焦化厂的建设条件,使我国焦化厂配套建设CDQ装置得到迅猛发展。
截止2009年6月,仅四年时间,我国投产和在建CDQ装置增至123套。
其中已投产71套<产能达6000多万t),相应干熄焦年产能达11448万t,占焦碳总产能为35%,在钢铁企业干熄焦率高达50%。
就干熄焦的规模而言,我国居世界首位。
首钢京唐钢铁公司260t/h CDQ是目前世界最先进、最大规格的第二套装置。
2004年前我国还不具备干熄焦技术设计能力,马钢和通钢CDQ装置技术和设备国产化示范顺利投运,为我国自行设计CDQ装置技术奠定了基础。
目前我国CDQ装置从50~260t/h有16种规格。
我国部分企业CDQ装置见表1。
表1 我国部分企业CDQ装置分布情况——————————————————————————————————单位 CDQ装置规格投产时间单位 CDQ装置投产时间数量,t/h 规格数量——————————————————————————————————宝钢 12×75 1985 攀钢 1×145 2006.011×145 2008.5始建鞍钢 4×140 2005.10 涟钢 1×150 2007 2×160 杭钢 1×75 2006.05.19武钢 2×140 2003.12 鄂钢 1×140 2005.07 2×140 在建通钢 2×90 2004 首钢 1×65 2001 昆钢 1×140 2005.06韶钢迁焦 2×95 2009.6.20 南钢 2×140 2006.07 2×140 2007 三明 2009.02唐钢 1×150 2006.06 柳钢 1×150 2007.11.281×160 2009-7-201×180 2008.7建宁波 1×140 在建济钢 2×70 1996 太钢 2×150 2008.05.282×150 2006 本钢 2×150沙钢 3×140 2005 梅钢 1×140 2008.06莱钢 2×140 2005.12.28 包钢 3×125 2006-2007 马钢 3×125 2004.04 新余 2×90 2008 2×130 2007.6 1×155首钢京 1×260 2009.5.19唐公司 1×260 在建开滦中润 1×140 2009.6.30 安阳钢厂 1×75 2009-7-28山东石 1×95 沙钢 2×140 2008建横特钢——————————————————————————————————2、干熄焦技术特点以某厂干熄焦装置处理能力140t/h为例。
(整理)国内外干熄焦技术状况及发展趋势
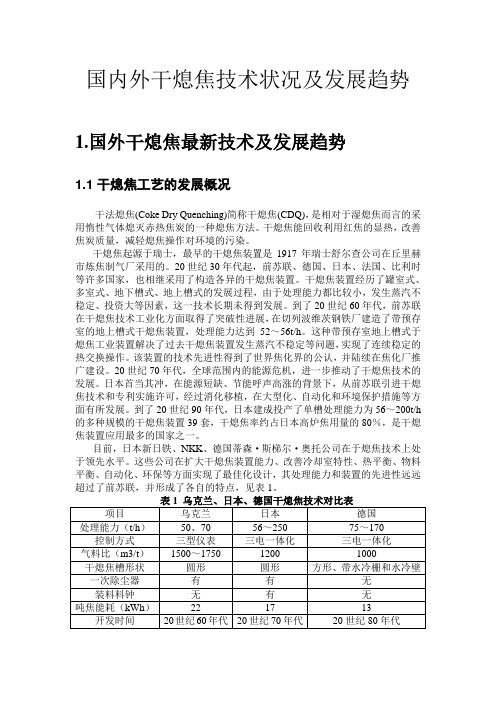
处理能力(t/h)
50、70
56~250
75~170
控制方式
三型仪表
三电一体化
三电一体化
气料比(m3/t)
1500~1750
1200
1000
干熄焦槽形状
圆形
圆形
方形、带水冷栅和水冷壁
一次除尘器
有
有
无
装料料钟
无
有
无
吨焦能耗(kWh)
22
17
13
开发时间
20世纪60年代
20世纪70年代
20世纪80年代
同时在保持原焦炭质量不变的条件下,采用干熄焦可扩大弱粘结性煤在炼焦用煤中的用量,降低炼焦成本。
两种熄焦方法焦炭质量指标对比见表2。
表2干熄焦工艺和湿熄焦工艺焦炭质量对比表
焦炭质量指标
湿熄焦
干熄焦
(干基)(%)
10.5
10.4
挥发分(%)
0.5
0.41
米库姆转M40(%)
2.
2.1
我国干熄焦技术的应用,始于上海宝钢建设。1985年,上海宝钢一期工程引进日本4×75t/h干熄焦装置正式投产运行,这是我国最早引进投产的干熄焦装置。同年,上海浦东煤气厂引进前苏联2×70t/h干熄焦装置,并于1994年投产。1991年和1997年宝钢二期、三期采用日本技术的两组4×75t/h干熄焦,1999年济钢采用乌克兰技术的2×70t/h干熄焦,2001年首钢采用日本技术的1×65t/h干熄焦装置相继建成投产,2003年马钢的干熄焦工程被列入“九五”国家重大引进技术消化吸收项目一干熄焦“一条龙”项目中的消化吸收创新工程,是国内第一条自行设计制造的,其国产化率达90%以上。此外,武钢、鞍钢、昆钢、通钢等许多国内钢铁企业也都在进行干熄焦工艺的建设。迄今为止,国内已有17套干熄焦装置投入运行。
干熄焦CDQ冷却室耐磨浇注料的研制和应用
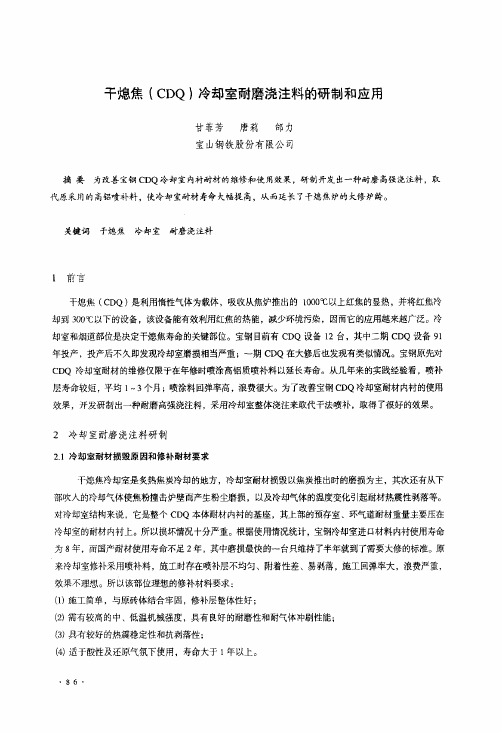
表2不同粒度组成设计
2.5纤维增强对热震的影响
图3粒度组成对材料强度的影响
在浇注料中加入1—5%的钢纤维,可以提高耐材强度,对材料增韧,使材料有良好的热震稳定性和抗剥落性。
但耐热钢纤维的熔融温度和临界氧化温度较低,不宜在高温下使用,在于熄焦炉内小于1000,1200。
C下使用则没有问题。
研制的浇注料进行加与不加钢纤维的热震稳定性试验对比。
制成230x114×65ram试样三块,经养护并110't2×24h干燥。
试验条件为1200℃+—+水冷,观察其试样状况。
表3列出了试验结果。
可见,浇注料中加入钢纤维对材料的抗热震性是有利的。
表3
热震结果描述。
干熄焦的发展进展、原理及应用

干熄焦的发展进展、原理及应用1、国内干熄焦使用概况干法熄焦简称干熄焦(CDQ),是相对于湿熄焦而言的采用惰性气体熄灭赤热焦炭的一种熄焦方法。
干熄焦能回收利用红焦的显热,改善焦炭质量,减轻熄焦操作对环境的污染。
(1)干熄焦的发展过程干熄焦起源于瑞士,20世纪40年代许多发达国家开始研究开发干熄焦技术,采取的方式各异,而且一般规模较小,生产不稳定。
进入60年代,前苏联在干熄焦技术方面取得了突破性进展,实现了连续稳定生产,获得专利发明权,并陆续在国内多数大型焦化厂建成干熄焦装置。
到目前为止,前苏联有40%的焦化厂采用了干熄焦技术,单套处理量在50-70t/h。
但前苏联干熄焦装置在自动控制和环境措施方面起点并不高。
20世纪70年代的全球能源危机促使干熄焦技术得到了长足发展,资源相对贫乏的日本,率先从苏联引进了干熄焦技术,并在装置的大型化、自动控制和环境保护方面进行了有效地改进。
到90年代中期,日本已建成干熄焦装置31套,其中单套处理能力100t/h以上的装置有17套,日本新日铁和NKK 等公司建成的干熄焦单套处理量可达到200t/h以上;装置方式采用了料钟布料,排焦采用了旋转密封阀连续排焦,接焦采用了旋转焦罐接焦等技术,使气料比大大降低极大地降低了干熄焦装置的建成投资和装置的运行费用;在控制方面实现了计算机控制,做到了全自动无人操作;在除尘方面,采用了除尘地面站方式,避免了干熄焦装置可能带来的二次污染。
日本的干熄焦技术不仅在其国内被普遍采用,同时它将干熄焦技术输出到德国、中国、韩国等国家,其干熄焦技术已达到国际领先。
20世纪80年代,德国又发明了水冷壁式干熄焦装置,使气体循环系统更加优化,并降低了运行成本。
德国帝森尔奥托(TSOA)公司成功地将水冷栅和水冷壁置入干熄炉,并将干熄炉断面由圆形改成方形,同时在排焦和干熄炉供气方式上进行了较大改进,干熄炉内焦炭下降及气流上升,实现了均匀分布,大大提高了换热效率,使气料比降到1000m3/t焦下,进一步降低了干熄焦装置的运行费用。
干法熄焦技术进展及应用前景

干法熄焦技术进展及应用前景关键词:能源;高质量;干熄焦技术;发展;前言干法熄焦(CDQ),简称干熄焦是相对于湿法熄焦而言的一种新型熄焦方法。
湿法熄焦在我国焦化厂普遍使用,但在湿法熄焦过程中产生大量的含污染物的湿蒸汽排人大气中,其中含有HCN、H2S、NH,、酚类、粉尘等有害物质。
湿法熄焦严重污染环境,浪费大量的热能,消耗大量的水,又影响焦炭质量。
干熄焦是以惰性冷气体氮气为载体,通入干熄炉内冷却炽热红焦炭,使红焦炭由1050℃冷却至200oc以下,循环的惰性热气体(氮气)热量经回收产生蒸汽和发电,氮气循环在密闭系统内完成,整个熄焦过程基本不对环境造成污染。
一、干法熄焦技术(1)流程推焦机将红焦从炭化室推出后,红焦由拦焦机导入圆形旋转焦罐或方形焦罐,焦罐台车由电机车牵引至干熄焦提升井架底部,由提升机将焦罐提升至提升井架顶部;提升机挂着焦罐向干熄炉中心平移的过程中,与装入装置连为一体的炉盖由电动缸自动打开,装焦漏斗自动放到干熄炉上部;提升机放下的焦罐由装入装置的焦罐台接受,在提升机下降的过程中,焦罐底闸门自动打开,开始装入红焦;红焦装完后,提升机自动提起,将焦罐送往提升井架底部的空焦罐台车上,在此期间装入装置自动运行将炉盖关闭。
装入干熄炉的红焦,在预存段预存一段时间后,随着排焦的进行逐渐下降到冷却段,在冷却段通过与循环气体进行热交换而冷却,再经振动给料器、旋转密封阀、双岔溜槽排出,然后由专用带式运输机运出。
冷却焦炭的循环气体,在干熄炉冷却段与红焦进行热交换后温度升高,并经环形烟道排出干熄炉;高温循环气体经过一次除尘器分离粗颗粒焦粉后进入干熄焦锅炉进行热交换,锅炉产生蒸汽,温度降至约160℃的低温循环气体由锅炉出来,经过二次除尘器进一步分离细颗粒焦粉后,由循环风机送入给水预热器冷却至约130℃,再进入干熄炉循环使用。
(2)工艺路线焦粉工艺路线∶一次除尘器及二次除尘器从循环氮气中分离出来的焦粉,收集在粉焦储槽内,经处理后由汽车运走。
干熄焦技术的新特点和工程实践
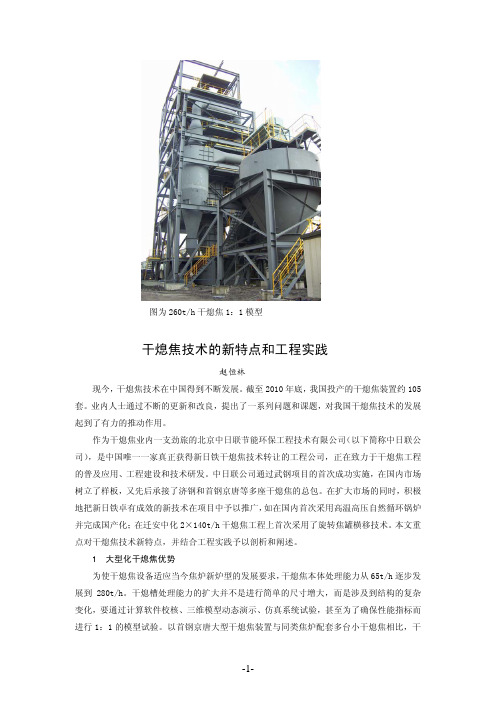
图为260t/h干熄焦1:1模型干熄焦技术的新特点和工程实践赵恒林现今,干熄焦技术在中国得到不断发展。
截至2010年底,我国投产的干熄焦装置约105套。
业内人士通过不断的更新和改良,提出了一系列问题和课题,对我国干熄焦技术的发展起到了有力的推动作用。
作为干熄焦业内一支劲旅的北京中日联节能环保工程技术有限公司(以下简称中日联公司),是中国唯一一家真正获得新日铁干熄焦技术转让的工程公司,正在致力于干熄焦工程的普及应用、工程建设和技术研发。
中日联公司通过武钢项目的首次成功实施,在国内市场树立了样板,又先后承接了济钢和首钢京唐等多座干熄焦的总包。
在扩大市场的同时,积极地把新日铁卓有成效的新技术在项目中予以推广,如在国内首次采用高温高压自然循环锅炉并完成国产化;在迁安中化2×140t/h干熄焦工程上首次采用了旋转焦罐横移技术。
本文重点对干熄焦技术新特点,并结合工程实践予以剖析和阐述。
1 大型化干熄焦优势为使干熄焦设备适应当今焦炉新炉型的发展要求,干熄焦本体处理能力从65t/h逐步发展到280t/h。
干熄槽处理能力的扩大并不是进行简单的尺寸增大,而是涉及到结构的复杂变化,要通过计算软件校核、三维模型动态演示、仿真系统试验,甚至为了确保性能指标而进行1:1的模型试验。
以首钢京唐大型干熄焦装置与同类焦炉配套多台小干熄焦相比,干熄焦规模处理能力的扩大带来的经济效益:一是节省占地面积;二是减少设备的数量;三是降低运行成本;四是增加投资回报。
其具体比较系数见下表:1)2套小干熄焦装置比1套大干熄焦占地增加了23%。
2)干熄焦本体的设备台套数及装机容量比较电机台套数比为1:1.57,装机容量比为1:1.14。
3)干熄焦本体的动力介质用量比较4)干熄焦本体的投资比较由此可见,建设大型化干熄焦不仅能够满足生产的需求,而且主要经济指标均优于目前国内大型化焦炉配套建设2套干熄焦的方案,经济效益非常明显。
2 设计方案多样化目前,北京中日联公司承建的干熄焦处理能力范围从65t/h~至280t/h,由于采用开拓性的进行多样化、合理化的总图布置,归纳和总结了几种类型的布置方案,可供企业参考和应用。
浅谈干熄焦技术的发展及应用
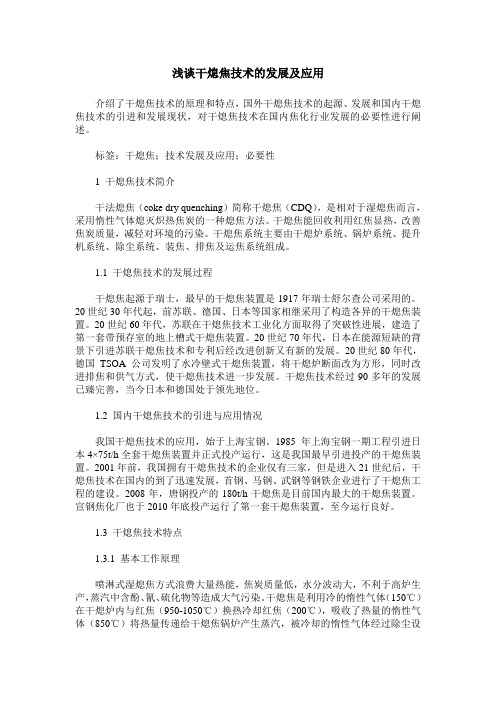
浅谈干熄焦技术的发展及应用介绍了干熄焦技术的原理和特点,国外干熄焦技术的起源、发展和国内干熄焦技术的引进和发展现状,对干熄焦技术在国内焦化行业发展的必要性进行阐述。
标签:干熄焦;技术发展及应用;必要性1 干熄焦技术简介干法熄焦(coke dry quenching)简称干熄焦(CDQ),是相对于湿熄焦而言,采用惰性气体熄灭炽热焦炭的一种熄焦方法。
干熄焦能回收利用红焦显热,改善焦炭质量,减轻对环境的污染。
干熄焦系统主要由干熄炉系统、锅炉系统、提升机系统、除尘系统、装焦、排焦及运焦系统组成。
1.1 干熄焦技术的发展过程干熄焦起源于瑞士,最早的干熄焦装置是1917年瑞士舒尔查公司采用的。
20世纪30年代起,前苏联、德国、日本等国家相继采用了构造各异的干熄焦装置。
20世纪60年代,苏联在干熄焦技术工业化方面取得了突破性进展,建造了第一套带预存室的地上槽式干熄焦装置。
20世纪70年代,日本在能源短缺的背景下引进苏联干熄焦技术和专利后经改进创新又有新的发展。
20世纪80年代,德国TSOA公司发明了水冷壁式干熄焦装置,将干熄炉断面改为方形,同时改进排焦和供气方式,使干熄焦技术进一步发展。
干熄焦技术经过90多年的发展已臻完善,当今日本和德国处于领先地位。
1.2 国内干熄焦技术的引进与应用情况我国干熄焦技术的应用,始于上海宝钢。
1985年上海宝钢一期工程引进日本4×75t/h全套干熄焦装置并正式投产运行,这是我国最早引进投产的干熄焦装置。
2001年前,我国拥有干熄焦技术的企业仅有三家,但是进入21世纪后,干熄焦技术在国内的到了迅速发展,首钢、马钢、武钢等钢铁企业进行了干熄焦工程的建设。
2008年,唐钢投产的180t/h干熄焦是目前国内最大的干熄焦装置。
宣钢焦化厂也于2010年底投产运行了第一套干熄焦装置,至今运行良好。
1.3 干熄焦技术特点1.3.1 基本工作原理喷淋式湿熄焦方式浪费大量热能,焦炭质量低,水分波动大,不利于高炉生产,蒸汽中含酚、氰、硫化物等造成大气污染。
大型干熄焦炉冷却段用耐磨耐火材料的研制与应用
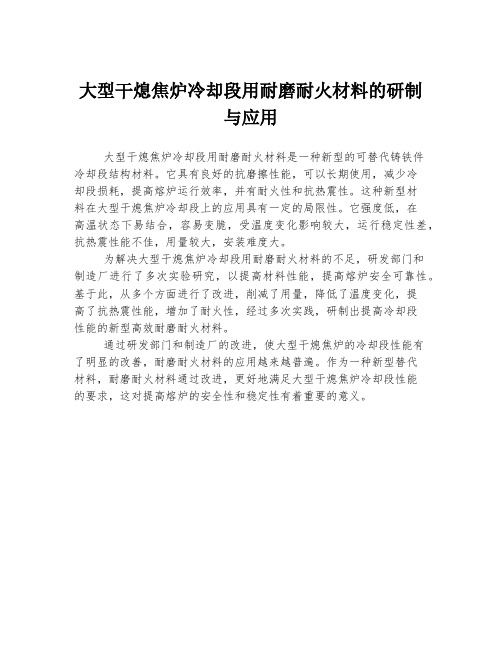
大型干熄焦炉冷却段用耐磨耐火材料的研制
与应用
大型干熄焦炉冷却段用耐磨耐火材料是一种新型的可替代铸铁件
冷却段结构材料。
它具有良好的抗磨擦性能,可以长期使用,减少冷
却段损耗,提高熔炉运行效率,并有耐火性和抗热震性。
这种新型材
料在大型干熄焦炉冷却段上的应用具有一定的局限性。
它强度低,在
高温状态下易结合,容易变脆,受温度变化影响较大,运行稳定性差,抗热震性能不佳,用量较大,安装难度大。
为解决大型干熄焦炉冷却段用耐磨耐火材料的不足,研发部门和
制造厂进行了多次实验研究,以提高材料性能,提高熔炉安全可靠性。
基于此,从多个方面进行了改进,削减了用量,降低了温度变化,提
高了抗热震性能,增加了耐火性,经过多次实践,研制出提高冷却段
性能的新型高效耐磨耐火材料。
通过研发部门和制造厂的改进,使大型干熄焦炉的冷却段性能有
了明显的改善,耐磨耐火材料的应用越来越普遍。
作为一种新型替代
材料,耐磨耐火材料通过改进,更好地满足大型干熄焦炉冷却段性能
的要求,这对提高熔炉的安全性和稳定性有着重要的意义。
大型干熄焦炉冷却段用耐磨耐火材料的研制与应用
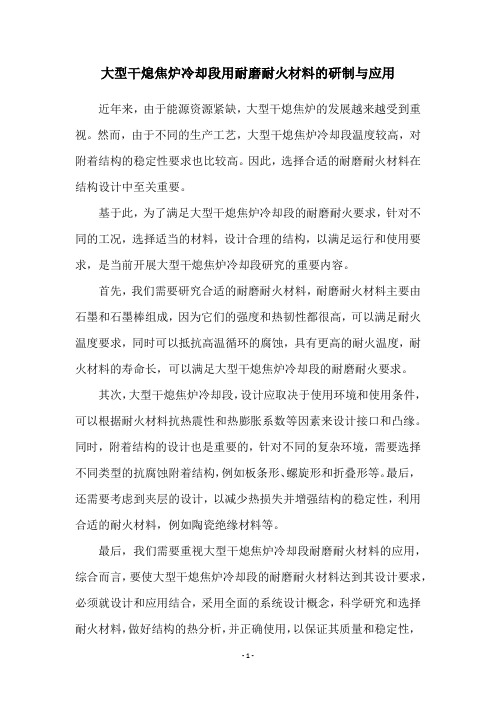
大型干熄焦炉冷却段用耐磨耐火材料的研制与应用近年来,由于能源资源紧缺,大型干熄焦炉的发展越来越受到重视。
然而,由于不同的生产工艺,大型干熄焦炉冷却段温度较高,对附着结构的稳定性要求也比较高。
因此,选择合适的耐磨耐火材料在结构设计中至关重要。
基于此,为了满足大型干熄焦炉冷却段的耐磨耐火要求,针对不同的工况,选择适当的材料,设计合理的结构,以满足运行和使用要求,是当前开展大型干熄焦炉冷却段研究的重要内容。
首先,我们需要研究合适的耐磨耐火材料,耐磨耐火材料主要由石墨和石墨棒组成,因为它们的强度和热韧性都很高,可以满足耐火温度要求,同时可以抵抗高温循环的腐蚀,具有更高的耐火温度,耐火材料的寿命长,可以满足大型干熄焦炉冷却段的耐磨耐火要求。
其次,大型干熄焦炉冷却段,设计应取决于使用环境和使用条件,可以根据耐火材料抗热震性和热膨胀系数等因素来设计接口和凸缘。
同时,附着结构的设计也是重要的,针对不同的复杂环境,需要选择不同类型的抗腐蚀附着结构,例如板条形、螺旋形和折叠形等。
最后,还需要考虑到夹层的设计,以减少热损失并增强结构的稳定性,利用合适的耐火材料,例如陶瓷绝缘材料等。
最后,我们需要重视大型干熄焦炉冷却段耐磨耐火材料的应用,综合而言,要使大型干熄焦炉冷却段的耐磨耐火材料达到其设计要求,必须就设计和应用结合,采用全面的系统设计概念,科学研究和选择耐火材料,做好结构的热分析,并正确使用,以保证其质量和稳定性,使大型干熄焦炉冷却段耐磨耐火材料可靠安全地运行。
综上所述,大型干熄焦炉冷却段中耐磨耐火材料的研制与应用,不仅是研究大型干熄焦炉冷却段结构设计的关键,而且是保证大型干熄焦炉冷却段安全可靠运行的关键。
因此,未来将继续深入研究大型干熄焦炉冷却段耐磨耐火材料的研制与应用,以更好地满足不断发展的实际需求。
延长干熄焦装置检修周期的应用与探索

延长干熄焦装置检修周期的应用与探索随着钢铁行业的发展和进步,生产设备越来越复杂化,同时生产周期也越来越紧张,设备的检修和维护变得尤为重要。
检修周期的延长不仅可以提高设备的可靠性和安全性,还可以降低生产成本和人力资源的投入。
本文将探讨如何延长干熄焦装置的检修周期,以提高生产效率和降低生产成本。
一、干熄焦装置概述干熄焦装置是钢铁生产中的一个关键装置,其主要作用是将生产出的焦末进行焦化和还原,产生高质量的焦炭。
传统的干熄焦系统通常由干熄焦塔、热风炉等组成,其工作原理是利用热风对焦末进行干燥和熄焦,同时将干燥后的焦末送入炼钢炉中进行还原反应。
干熄焦装置的检修周期通常是按照生产量和生产时间来进行计算的。
检修周期的长短直接影响到生产效率和生产成本。
短的检修周期可以确保设备的可靠性和安全性,但会大大降低生产效率,增加生产成本。
长的检修周期可以提高生产效率和降低生产成本,但会增加设备故障和安全事故的可能性。
1. 设计合理的干熄焦装置设计合理的干熄焦装置是延长检修周期的一项重要措施。
合理的设计可以降低设备的故障率和维修成本,从而延长检修周期。
具体措施包括考虑设备的强度和稳定性、设备的维护保养难度、设备的材料选择等。
2. 技术优化和改进技术优化和改进可以有效地延长干熄焦装置的检修周期。
技术优化包括改善设备的使用环境、提高设备的运行效率、优化设备的维护保养程序等。
技术改进包括采用新的材料和技术,改善设备的制造工艺和生产流程等。
3. 实施预防维护实施预防维护是延长检修周期的有效手段。
预防维护包括对设备进行定期检查、清洗、润滑和调整等,以保证设备的正常运行和长期可靠性。
通过实施预防维护,可以及时发现和排除设备故障,避免设备损坏和大修,从而延长检修周期。
4. 加强维修和保养管理加强维修和保养管理是延长检修周期的关键。
科学合理的维修和保养管理可以最大限度地提高设备的可靠性和安全性,降低设备的故障率和维修成本。
具体措施包括制定科学合理的维修和保养计划、对维修人员进行专业培训和技术培训、加强维修记录管理和设备监控等。
抗剥落耐磨砖在干熄焦炉冷却室的应用和改进
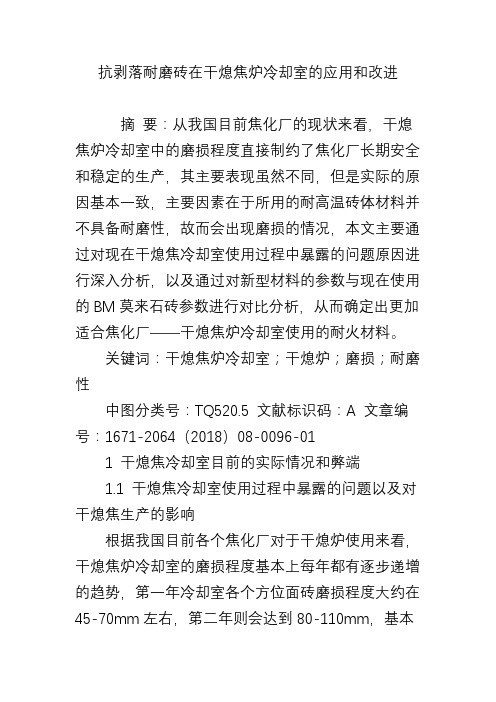
抗剥落耐磨砖在干熄焦炉冷却室的应用和改进摘要:从我国目前焦化厂的现状来看,干熄焦炉冷却室中的磨损程度直接制约了焦化厂长期安全和稳定的生产,其主要表现虽然不同,但是实际的原因基本一致,主要因素在于所用的耐高温砖体材料并不具备耐磨性,故而会出现磨损的情况,本文主要通过对现在干熄焦冷却室使用过程中暴露的问题原因进行深入分析,以及通过对新型材料的参数与现在使用的BM莫来石砖参数进行对比分析,从而确定出更加适合焦化厂――干熄焦炉冷却室使用的耐火材料。
关键词:干熄焦炉冷却室;干熄炉;磨损;耐磨性中图分类号:TQ520.5 文献标识码:A 文章编号:1671-2064(2018)08-0096-011 干熄焦冷却室目前的实际情况和弊端1.1 干熄焦冷却室使用过程中暴露的问题以及对干熄焦生产的影响根据我国目前各个焦化厂对于干熄炉使用来看,干熄焦炉冷却室的磨损程度基本上每年都有逐步递增的趋势,第一年冷却室各个方位面砖磨损程度大约在45-70mm左右,第二年则会达到80-110mm,基本已经将所有的工作面砖全部磨损了。
而由于冷却室这种每年逐步递增磨损,给干熄焦的生产带来十分严重的影响,例如:墙体不同程度损坏,会导致热量使用率的降低的问题,若是磨损严重的话还会带来不可预估的安全隐患。
1.2 此现状的目前的解决方法和各个方法的缺点(1)大、中、小型焦化厂通过不同方式在操作中减少磨损量,但实际的收效并不显著。
(2)大部分焦化厂会在在检修中也会通过浇注耐磨材料的方式进行维护,以求达到减少磨损的效果,但是这种方式会使得冷却效果直线下降。
既降低了热能的有效利用率同时也增加了排焦系统的运行风险。
2 冷却室中耐火材料的磨损机理针对干熄炉冷却室耐材磨损的问题,在多次的实验、分析、比对和试用中,发现目前使用的BM莫来石砖其耐磨指标相对来说比较低,就会造成冷却室大面积磨损损坏;结合用户使用要求使用复合相抗剥落耐磨砖,经在干熄炉冷却室试用,指标基本符合要求。
国内外干熄焦技术状况及发展趋势

国内外干熄焦技术状况及发展趋势1.国外干熄焦最新技术及发展趋势1.1干熄焦工艺的发展概况干法熄焦(Coke Dry Quenching)简称干熄焦(CDQ),是相对于湿熄焦而言的采用惰性气体熄灭赤热焦炭的一种熄焦方法。
干熄焦能回收利用红焦的显热,改善焦炭质量,减轻熄焦操作对环境的污染。
干熄焦起源于瑞士,最早的干熄焦装置是1917年瑞士舒尔查公司在丘里赫市炼焦制气厂采用的。
20世纪30年代起,前苏联、德国、日本、法国、比利时等许多国家,也相继采用了构造各异的干熄焦装置。
干熄焦装置经历了罐室式、多室式、地下槽式、地上槽式的发展过程,由于处理能力都比较小,发生蒸汽不稳定、投资大等因素,这一技术长期未得到发展。
到了20世纪60年代,前苏联在干熄焦技术工业化方面取得了突破性进展,在切列波维茨钢铁厂建造了带预存室的地上槽式干熄焦装置,处理能力达到52~56t/h。
这种带预存室地上槽式于熄焦工业装置解决了过去干熄焦装置发生蒸汽不稳定等问题,实现了连续稳定的热交换操作。
该装置的技术先进性得到了世界焦化界的公认,并陆续在焦化厂推广建设。
20世纪70年代,全球范围内的能源危机,进一步推动了干熄焦技术的发展。
日本首当其冲,在能源短缺、节能呼声高涨的背景下,从前苏联引进干熄焦技术和专利实施许可,经过消化移植,在大型化、自动化和环境保护措施等方面有所发展。
到了20世纪90年代,日本建成投产了单槽处理能力为56~200t/h 的多种规模的干熄焦装置39套,干熄焦率约占日本高炉焦用量的80%,是干熄焦装置应用最多的国家之一。
目前,日本新日铁、NKK、德国蒂森·斯梯尔·奥托公司在于熄焦技术上处于领先水平。
这些公司在扩大干熄焦装置能力、改善冷却室特性、热平衡、物料平衡、自动化、环保等方面实现了最佳化设计,其处理能力和装置的先进性远远超过了前苏联,并形成了各自的特点,见表1。
除前苏联、日本、德国拥有干熄焦装置外,印度、韩国、波兰、罗马尼亚、巴西、土耳其、尼日利亚和我国都相继建成了干熄焦装置。