熔模铸钢件气孔的产生与防止
铸件气孔产生原因及防治方案

气体在金属中的溶解和析出是一个可逆过程,随着温度的升高气体的溶解度增大,温度下降,其溶解度减小,气体析出增加。
气体的外界环境分压力降低时,气体在金属中的溶解度降低,气体也将析出。
气体的析出有三种形式。
第一种气体原子从金属内部扩散到金属表面,脱离吸附状态。
这种形式由于金属液的冷却速度快,粘度大,很难进行。
第二种气体原子与金属内部某元素形成化合物,以非金属夹杂物的形式析出。
第三种气体原子在金属内部形成气体分子,以气泡的形式析出。
如果气泡不能逸出金属液的表面,则将在金属内部形成气孔。
铸件中的气泡就是这样形成的。
在铸造过程中,气孔是由于型壳的透气性不良(没有烧透,材料选择错误,透气性差等),浇注时产生的大量气体不能及时排出,留在铸件内形成孔洞。
气孔不仅减少铸件的有效截面积,且使局部造成应力集中,成为裂纹源,尤其是成串存在的小气泡群,不仅增加缺口的敏感性,使金属强度下降,而且降低零件的疲劳强度。
气孔通常分为析出性气孔、反应性气孔和侵入性气孔。
1、析出性气孔。
金属液在冷却和凝固的过程中,因气体溶解度下降,析出的气体来不及排除,铸件由此而产生的气孔,称为析出性气孔。
这类气孔的特征是:在大型铸件截面上呈大面积分布,而靠近冒口、热节等温度较高区域则分布较密集。
通常金属含气量较多时,气孔形状呈裂纹状;含气量较多时,气孔较大,圆球状。
常发生在同一炉或同一浇包浇注的一批铸件中。
产生析出性气孔的气体,主要是氢气,其次是氮气。
影响析出性气孔形成的因素有:1)、金属液原始含气量。
金属液原始含气量越高,气孔越易形成,静置时间过短,金属溶液内的气体来不及排到熔液表面。
2)、冷却速度。
铸件冷却速度越快,气孔越不易形成。
3)、合金成分。
合金液态收缩大、结晶温度范围大的合金,则容易产生气孔或气缩孔。
4)、气体种类。
气体的扩散速度越快,气孔越不易形成。
2、反应性气孔。
金属液与铸型之间或在金属液内部发生化学反应产生的气体来不及排出,所产生的气孔,称为反应性气孔。
铸造气孔解决方法

铸造气孔解决方法一、背景介绍铸造是一种常见的制造工艺,但在铸造过程中,气孔是一个常见的缺陷。
气孔会降低铸件的强度和密封性,影响其使用寿命和品质。
因此,解决气孔问题对于提高铸件质量至关重要。
二、气孔的成因1.金属液中溶解氧过多2.熔融金属流动速度过快3.模具表面粗糙或有杂质4.金属液中含有挥发性物质三、预防措施1.减少金属液中溶解氧含量:可通过加入还原剂、增加保温时间等方法来实现。
2.控制熔融金属流动速度:可通过调整浇注系统设计、增加浇注口数量等方法来实现。
3.改善模具表面状态:可通过精密加工模具表面、清洁模具表面等方法来实现。
4.减少挥发性物质:可通过改变熔融金属组成、使用合适的保护剂等方法来实现。
四、处理方法1.机械处理法:包括打磨和修补。
打磨可通过砂轮、砂带等工具进行,修补则可采用填充剂填充气孔。
2.热处理法:包括退火和时效。
退火可使气孔内部的氧分子扩散到金属液中,使气孔逐渐消失;时效则是利用金属在高温下的再结晶过程来消除气孔。
3.化学处理法:包括浸泡、电解和喷涂等方法。
浸泡可将含有铝的溶液浸泡在铸件表面,形成一层保护膜以防止氧化;电解则是利用阳极溶解作用来填补气孔;喷涂则是将特定材料喷涂在铸件表面,形成一层密封膜。
五、常见问题及解决方法1. 气孔数量较多:应从预防措施入手,加强金属液净化、控制熔融金属流动速度等。
2. 气孔回火后仍存在:应采取机械处理法或化学处理法进行修复。
3. 铸件表面存在小气孔:可采用电解或喷涂等化学处理法进行修复。
六、结论气孔是铸造过程中常见的缺陷,但通过预防措施和处理方法,可以有效地减少或消除气孔问题。
在实际生产中,应根据具体情况采取不同的解决方法,以提高铸件质量和使用寿命。
铸钢件气孔缺陷的分析及预防

铸钢件气孔缺陷的分析及预防铸钢件是一种广泛应用于制造工业的产品,在各行各业都有着广泛的应用。
然而,在铸钢件的生产过程中,常常会出现气孔缺陷。
在本文中,将对铸钢件气孔缺陷的分析及预防进行详细的介绍。
气孔缺陷是铸钢件生产过程中经常出现的一种缺陷,其原因主要是由于铸造过程中,铸钢件内的气体无法顺利释放,而形成的空气泡所致。
具体分析如下:1.铸造温度过高或过低铸造温度过高或过低会导致铸造过程中熔化金属与气体相互作用不充分,或者是在凝固时,金属凝固异常迅速,导致铸造件内部气体排放不及时,进而形成气孔缺陷。
2.金属液中气体含量过高铸钢件气孔缺陷的一个重要原因是金属液中气体含量过高。
这主要是由于铸造过程中,将熔化的金属液错流于模具中时,金属液中气体无法快速排出,而形成的气泡后来就会形成气孔缺陷。
3.模具设计不合理模具是制造铸造件的核心部分之一。
如果模具设计不合理,例如模具壁厚不符合要求、孔隙率过高等造成模具过于松散、不好密封,使熔融金属鼓荡时容易进入焦模震荡区域,从而使气体被气团包裹形成气泡,而成为铸钢件气孔缺陷.了解了铸钢件气孔缺陷发生的原因,我们可以采取一些技术性措施来预防气孔缺陷的出现。
1.合适的铸造温度我们可以在铸造前对熔融金属的净化处理,或者使用真空、熔覆反应等特殊工艺。
这些技术手段可以有效地去除金属液中的气体,减少气孔的发生。
合理的模具设计可以有效地避免铸造中应力集聚,提供良好的流动通道和顺畅的气流通道,避免产生气泡,降低气孔发生的概率。
对于大型铸钢件,可以采用完整的、结构合理的模具,避免模具的壁厚不符合要求等情况。
4.严格的生产工艺控制在生产过程中,我们还需要严格执行质量控制方案,不断优化铸造工艺,并加强现场监督管理。
避免铸造过程中出现偏差,加强对炉温、铸型、冷却等关键环节的控制,并在浇注后及时进行冷却处理,以提高铸钢件的质量。
总结:铸钢件气孔缺陷的原因主要是铸造温度过高或过低导致气体无法充分释放,金属液中气体含量过高,模具设计不合理等情况所致。
铸件气孔的产生

型芯怎么防止铸件气孔的产生用什么办法才能防止型芯的干燥..树脂砂芯因浇注时会产生气体从而导致铸件产生气孔最终导致铸件打废品..1、防止侵入气孔的措施(1)提高砂型和砂芯的透气性,控制砂型的紧实度砂型和砂芯的透气性越差,紧实度越高,侵入气孔产生的倾向性越大。
应严格控制砂型的紧实度和透气性。
在保证砂型强度的条件下,尽量降低砂型的紧实度。
采用面砂加粗背砂的方法是提高砂型透气性的有效措施。
(2)控制气体产生的速度严格控制型砂和芯砂中发气物质的加入量,控制湿型的分。
干型应保证烘干质量,并及时浇注,停放时间不要过长。
冷铁或芯铁应保证表面清洁、干燥。
浇口圈和冒口圈应烘干后使用。
(3)提高砂型和砂芯的排气能力铸型上扎排气孔帮助排气,保持砂芯排气孔的畅通,铸件顶部设置出气冒口。
采用合理的浇注系统。
(4)适当地提高浇注温度提高浇注温度可使侵入气体有充足的时间排出。
浇注时应控制浇注高度和浇注速度,保证金属液平稳地流动和充型。
(5)提高金属液的熔炼质量尽量降低铁水中的含硫量,保证铁水的流动性。
防止金属液过分氧化,减小气体排出的阻力。
2、防止卷入气孔的措施尽量降低浇包与浇口的距离,控制浇注液流的大小,使金属液平稳流动和充型。
正确设计浇口杯的形状和尺寸,用扁圆形浇口杯替代圆锥形浇口杯,避免金属液直接进入直浇道。
横浇道可设计挡渣挡气装置,可采用开放式浇注系统。
对小型铸件或薄壁铸件不应浇注太快。
同时,提高金属液的熔炼质量对防止卷入气孔的产生具有很重要的作用。
3、防止析出气孔的措施炉料进炉前,对炉料应进行清理,保证炉料的清洁,可采用烘干和喷丸处理,去除炉料表面的氧化皮、油污和水分。
合理地选择熔炼设备和熔炼工艺,对要求比较高的铸件,可采用真空熔炼工艺。
严格控制炉料的配比,尽量降低废钢的用量。
采用各种脱气方法(如浮游气泡脱气、冷凝脱气)对金属液进行精炼,如铝合金熔炼应在铝液上面加覆盖剂并进行精炼;阻止气体析出,如铝合金铸件采用冷铁加速铸件的冷却。
如何避免铸钢件不会出现析出气孔?

如何避免铸钢件不会出现析出气孔?
——长城铸钢析出气孔主要是以原子溶解于金属液体中的氢、氮等气体元素,当液体凝固时,它们就会以分子的形态析出,从而形成气泡让铸钢件产生气孔,也就是常说的析出气孔。
于屋内形成气泡的气体是来自金属的,所以它也是一种内生气孔。
铸钢厂家为了能够让产品避免析出气孔的产生,就会进行脱气处理,这是指金属液态在熔炉坩埚中或者出炉在浇包中,而对金属液体进行脱气处理,在浇注前来降低液体中的含气量,还会去除金属液体中的杂物,脱气处理其实就是对金属液体的一种精炼。
1、采用浮游气泡进行脱气,让金属液体不与其产生反应,之后成为金属液中的浮游气泡。
气泡对于溶解气体来说,也是一种真空的空间,所以溶解气体会扩散其中,之后随同气泡上浮。
浮游气泡出现金属液面,气泡中气体进入大气,也就达成了脱气目的。
2、冷凝脱气让有色合金铸件先使金属液缓冷到冷凝温度,让溶解气体因为降温溶解度也会随之减少而析出脱气。
再迅速的加热到浇注温度,来进行浇注。
含气量过高,夹杂物多的低质量钢垫能够多次的进行重炼来改善质量。
3、氮稳定剂脱氮,能够与氮生成稳定化合物的元素,都被称为氮稳定剂。
如果液体中溶解氮浓度高,加入氮稳定剂生产较为稳定的氮化物,来降低溶解氮
浓度,也就减少含氮量,起到了脱氮的作用。
铸钢件气孔缺陷的分析及预防
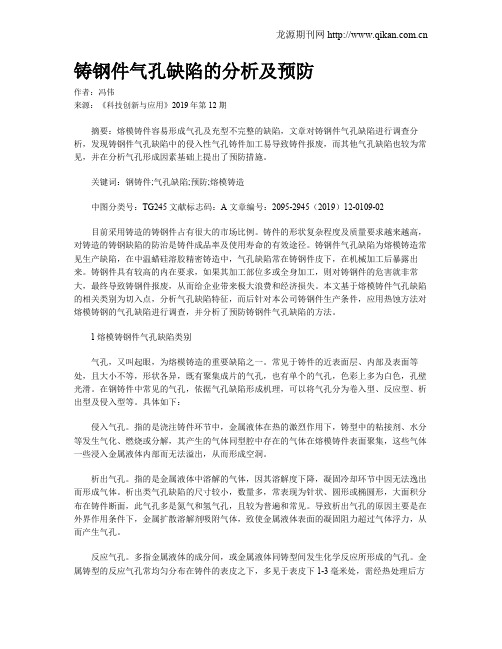
铸钢件气孔缺陷的分析及预防作者:冯伟来源:《科技创新与应用》2019年第12期摘要:熔模铸件容易形成气孔及充型不完整的缺陷,文章对铸钢件气孔缺陷进行调查分析,发现铸钢件气孔缺陷中的侵入性气孔铸件加工易导致铸件报废,而其他气孔缺陷也较为常见,并在分析气孔形成因素基础上提出了预防措施。
关键词:钢铸件;气孔缺陷;预防;熔模铸造中图分类号:TG245 文献标志码:A 文章编号:2095-2945(2019)12-0109-02目前采用铸造的铸钢件占有很大的市场比例。
铸件的形状复杂程度及质量要求越来越高,对铸造的铸钢缺陷的防治是铸件成品率及使用寿命的有效途径。
铸钢件气孔缺陷为熔模铸造常见生产缺陷,在中温蜡硅溶胶精密铸造中,气孔缺陷常在铸钢件皮下,在机械加工后暴露出来。
铸钢件具有较高的内在要求,如果其加工部位多或全身加工,则对铸钢件的危害就非常大,最终导致铸钢件报废,从而给企业带来极大浪费和经济损失。
本文基于熔模铸件气孔缺陷的相关类别为切入点,分析气孔缺陷特征,而后针对本公司铸钢件生产条件,应用热蚀方法对熔模铸钢的气孔缺陷进行调查,并分析了预防铸钢件气孔缺陷的方法。
1熔模铸钢件气孔缺陷类别气孔,又叫起眼,为熔模铸造的重要缺陷之一。
常见于铸件的近表面层、内部及表面等处,且大小不等,形状各异,既有聚集成片的气孔,也有单个的气孔,色彩上多为白色,孔壁光滑。
在钢铸件中常见的气孔,依据气孔缺陷形成机理,可以将气孔分为卷入型、反应型、析出型及侵入型等。
具体如下:侵入气孔。
指的是浇注铸件环节中,金属液体在热的激烈作用下,铸型中的粘接剂、水分等发生气化、燃烧或分解,其产生的气体同型腔中存在的气体在熔模铸件表面聚集,这些气体一些浸入金属液体内部而无法溢出,从而形成空洞。
析出气孔。
指的是金属液体中溶解的气体,因其溶解度下降,凝固冷却环节中因无法逸出而形成气体。
析出类气孔缺陷的尺寸较小,数量多,常表现为针状、圆形或椭圆形,大面积分布在铸件断面,此气孔多是氮气和氢气孔,且较为普遍和常见。
气孔类缺陷牲与防治方法
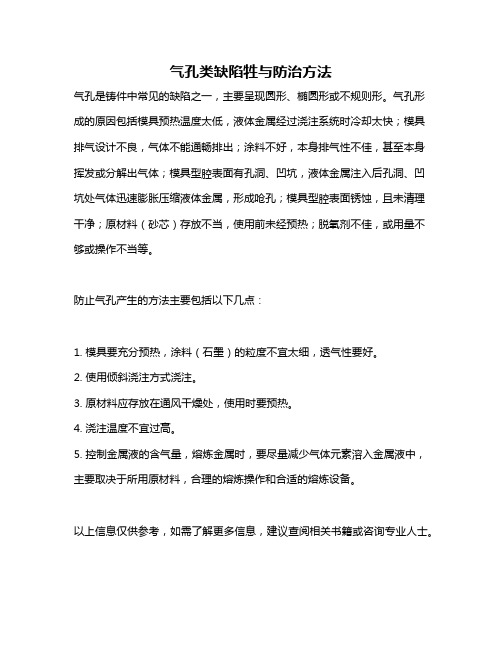
气孔类缺陷牲与防治方法
气孔是铸件中常见的缺陷之一,主要呈现圆形、椭圆形或不规则形。
气孔形成的原因包括模具预热温度太低,液体金属经过浇注系统时冷却太快;模具排气设计不良,气体不能通畅排出;涂料不好,本身排气性不佳,甚至本身挥发或分解出气体;模具型腔表面有孔洞、凹坑,液体金属注入后孔洞、凹坑处气体迅速膨胀压缩液体金属,形成呛孔;模具型腔表面锈蚀,且未清理干净;原材料(砂芯)存放不当,使用前未经预热;脱氧剂不佳,或用量不够或操作不当等。
防止气孔产生的方法主要包括以下几点:
1. 模具要充分预热,涂料(石墨)的粒度不宜太细,透气性要好。
2. 使用倾斜浇注方式浇注。
3. 原材料应存放在通风干燥处,使用时要预热。
4. 浇注温度不宜过高。
5. 控制金属液的含气量,熔炼金属时,要尽量减少气体元素溶入金属液中,主要取决于所用原材料,合理的熔炼操作和合适的熔炼设备。
以上信息仅供参考,如需了解更多信息,建议查阅相关书籍或咨询专业人士。
铸钢件气孔缺陷的分析及预防

铸钢件气孔缺陷的分析及预防铸钢件在工业生产中起着至关重要的作用,然而在铸钢件的制造过程中,气孔缺陷是一种常见的质量问题。
气孔缺陷会降低铸钢件的强度和硬度,影响其使用性能,严重时甚至会导致零部件的失效。
对铸钢件气孔缺陷进行分析并采取有效的预防措施,对于提高铸钢件的质量、延长零部件的使用寿命具有重要意义。
一、铸钢件气孔缺陷的成因分析1. 原料质量不良:铸造过程中使用的铸造原料如熔剂、砂型、砂芯等质量不良或含有杂质,会促使气体聚集并形成气孔。
2. 浇注过程不当:浇注过程中铸钢件内部的气体未能得到有效的排除,导致气孔的产生。
这与铸钢件的设计、浇注方式、浇注温度、浇注速度等因素密切相关。
3. 砂型和砂芯的设计不合理:砂型和砂芯的设计不合理、结构松散、容易剥落等都会导致气孔的产生。
4. 浇注温度过高:浇注温度过高会导致铸造原料的气体释放不完全,造成气孔缺陷。
5. 铸造工艺控制不当:在铸造工艺中,未能有效控制气体的排除和熔化金属的充填速度,是导致气孔缺陷产生的重要原因之一。
6. 熔化金属中含气过多:熔化金属中含气过多,未能得到有效的排除,会在铸钢件中形成气孔。
1. 优化原料选择:选择质量良好的铸造原料,尽可能减少熔剂、砂型、砂芯中的杂质含量。
2. 浇注过程的优化:合理设计浇注系统,采用适当的浇注方式和浇注温度,加强浇注过程中的气体排除。
3. 砂型和砂芯的优化:优化砂型和砂芯的设计,保证其结构紧密,避免砂型和砂芯剥落。
4. 控制熔化金属中的气体含量:采用适当的炉料和合理的炉前处理工艺,减少熔化金属中的气体含量。
5. 增强铸造工艺控制:加强铸造工艺中气体排除和熔化金属的充填控制,确保铸造工艺的稳定性和可靠性。
6. 合理设计铸造结构:在铸钢件的设计中,合理设计零部件的结构和形状,避免零部件内部的气体积聚,减少气孔的产生。
7. 强化检验和管控:强化对原料、砂型、砂芯、熔化金属和铸造工艺的检验和管控,确保所有加工环节都符合要求。
熔模铸钢件气孔的产生与防止
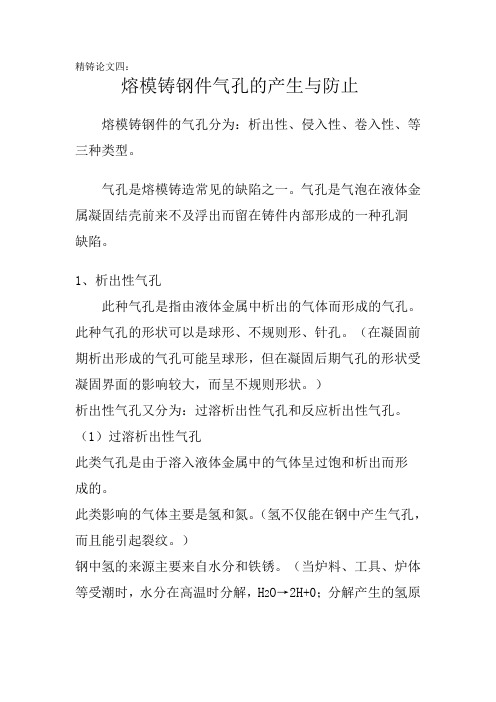
精铸论文四:熔模铸钢件气孔的产生与防止熔模铸钢件的气孔分为:析出性、侵入性、卷入性、等三种类型。
气孔是熔模铸造常见的缺陷之一。
气孔是气泡在液体金属凝固结壳前来不及浮出而留在铸件内部形成的一种孔洞缺陷。
1、析出性气孔此种气孔是指由液体金属中析出的气体而形成的气孔。
此种气孔的形状可以是球形、不规则形、针孔。
(在凝固前期析出形成的气孔可能呈球形,但在凝固后期气孔的形状受凝固界面的影响较大,而呈不规则形状。
)析出性气孔又分为:过溶析出性气孔和反应析出性气孔。
(1)过溶析出性气孔此类气孔是由于溶入液体金属中的气体呈过饱和析出而形成的。
此类影响的气体主要是氢和氮。
(氢不仅能在钢中产生气孔,而且能引起裂纹。
)钢中氢的来源主要来自水分和铁锈。
(当炉料、工具、炉体等受潮时,水分在高温时分解,H2O→2H+0;分解产生的氢原子极易被钢液吸收。
因此防止此类缺陷的主要措施是清洁炉料和保待炉体、浇包、炉料、铁合金、造渣剂、工具等干燥。
)一般说氮对钢中气孔的影响很小。
(2)反应析出性气孔此类气孔是由于液体金属中发生化学反应产生的气体析出而形成。
影响最大的是氧。
此类气孔可能呈现三种形态:①、当钢液严重氧化时,FeO高;②、当钢液脱氧不完善时,FeO高;③、当钢液脱氧后残铝量不够,浇注后产生二次氧化,形成FeO高。
预防措施:1、清洁炉料,特别是铁锈严重的炉料应经除锈处理。
(铁锈不仅带入FeO而且带入了H2O,H2O分解引起钢液吸氢。
)②、快速熔炼。
(缩短高温冶炼时间。
)③、充分脱氧。
(用AL量一般为0.04%-0.06%,不超过0.15%)2、侵入性气孔气体将侵入液体金属而形成气孔。
一般指水玻璃制壳,气体来源主要是NaCl。
避免措施:①、受潮型壳不得浇注,应力求热壳浇注;②、制壳时避免涂料堆积,硬化不充分;③、焙烧应充分。
3、卷入性气孔卷入性气孔的气体来自型腔,其中主要是大气。
(与型壳透气性有关。
)防止措施:①、铸造方案设计时应方便排气,尽量使液体金属能平稳的有序的充型。
铸钢件气孔缺陷的分析及预防
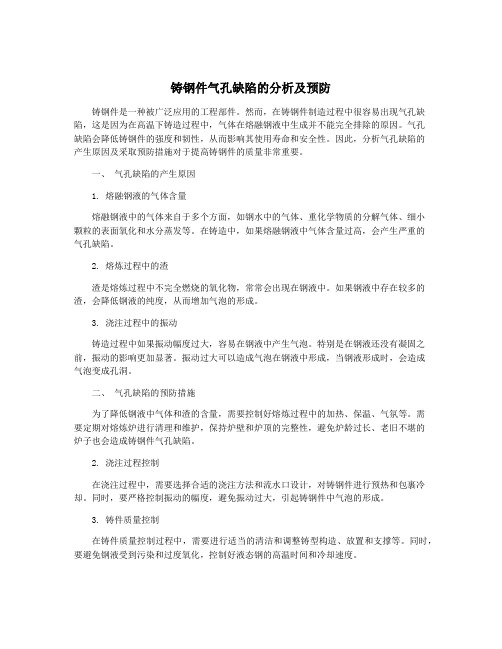
铸钢件气孔缺陷的分析及预防铸钢件是一种被广泛应用的工程部件。
然而,在铸钢件制造过程中很容易出现气孔缺陷,这是因为在高温下铸造过程中,气体在熔融钢液中生成并不能完全排除的原因。
气孔缺陷会降低铸钢件的强度和韧性,从而影响其使用寿命和安全性。
因此,分析气孔缺陷的产生原因及采取预防措施对于提高铸钢件的质量非常重要。
一、气孔缺陷的产生原因1. 熔融钢液的气体含量熔融钢液中的气体来自于多个方面,如钢水中的气体、重化学物质的分解气体、细小颗粒的表面氧化和水分蒸发等。
在铸造中,如果熔融钢液中气体含量过高,会产生严重的气孔缺陷。
2. 熔炼过程中的渣渣是熔炼过程中不完全燃烧的氧化物,常常会出现在钢液中。
如果钢液中存在较多的渣,会降低钢液的纯度,从而增加气泡的形成。
3. 浇注过程中的振动铸造过程中如果振动幅度过大,容易在钢液中产生气泡。
特别是在钢液还没有凝固之前,振动的影响更加显著。
振动过大可以造成气泡在钢液中形成,当钢液形成时,会造成气泡变成孔洞。
二、气孔缺陷的预防措施为了降低钢液中气体和渣的含量,需要控制好熔炼过程中的加热、保温、气氛等。
需要定期对熔炼炉进行清理和维护,保持炉壁和炉顶的完整性,避免炉龄过长、老旧不堪的炉子也会造成铸钢件气孔缺陷。
2. 浇注过程控制在浇注过程中,需要选择合适的浇注方法和流水口设计,对铸钢件进行预热和包裹冷却。
同时,要严格控制振动的幅度,避免振动过大,引起铸钢件中气泡的形成。
3. 铸件质量控制在铸件质量控制过程中,需要进行适当的清洁和调整铸型构造、放置和支撑等。
同时,要避免钢液受到污染和过度氧化,控制好液态钢的高温时间和冷却速度。
综上所述,铸钢件气孔缺陷是由于多种因素所引起的。
防止气孔缺陷的产生需要通过控制钢液中气体和渣的含量、严格控制振动幅度以及在铸件质量控制过程中进行适当的准备来实施。
只有采取有效的预防措施,才能提高铸钢件的质量和使用寿命。
铸钢件气孔缺陷的分析及预防

铸钢件气孔缺陷的分析及预防铸钢件气孔缺陷是一种常见的铸造缺陷,其主要原因是在熔融金属凝固过程中,金属中的气体不完全排出,形成气孔。
气孔缺陷不仅会降低铸钢件的强度和韧性,还会对其密封性和机械性能产生不利影响。
对于气孔缺陷的分析和预防具有重要意义。
气孔缺陷的形成与以下几个方面密切相关:1. 熔融金属中的气体含量较高:熔融金属中的气体主要来自于金属中的气体溶解度和金属液的气泡,而气泡往往是由于金属液中的杂质和气体不能及时排出而形成的。
要减少熔融金属中的气体含量,首先要提高金属液的纯净度和气体排出能力。
2. 浇注过程中的气体吸附:在金属液注入模具的过程中,气体往往会与铸钢件接触的模具表面接触,然后被吸附到铸钢件表面形成气孔。
为了减少这种情况的发生,可以在模具表面涂覆一层特殊的涂层或使用具有吸附气体能力的材料来减少气体的吸附。
3. 硅、锰等元素含量较高:铸钢件中的硅、锰等元素对气孔的形成有一定的影响,其中硅元素会使金属液变稠,增加气泡的数量,锰元素则会提高金属液的表面张力,使气泡难以排出。
在调整合金配方时要注意控制硅、锰等元素的含量。
4. 浇注温度过高或过低:浇注温度过高会导致金属液中的气体溶解度降低,造成气泡形成;而浇注温度过低则会使得金属凝固过程过长,气体排出不畅,同样会形成气孔。
要选择适宜的浇注温度,避免温度过高或过低。
为了预防铸钢件中气孔缺陷的发生,可以采取以下措施:1. 提高熔化金属的质量:要选择优质的原料,并进行严格的质量控制,确保金属液的纯净度和气体排出能力。
2. 优化模具设计:合理设计铸造系统,使得金属液能够顺畅地流动,减少气体的吸附和困留;采用有利于气体排出的模具结构,如设置适当的浇口和排气道。
3. 控制浇注工艺参数:包括浇注温度、浇注速度、浇注压力等。
要根据具体情况,选择合适的参数,以确保金属液能够充分流动,气体能够及时排出。
4. 加强铸造工艺监控:通过对浇注过程的实时监测,及时发现异常情况并采取相应的措施,避免气孔缺陷的发生。
铸钢件气孔缺陷的分析及预防

铸钢件气孔缺陷的分析及预防铸钢件作为工业制造中常见的零部件,其质量的好坏直接影响着整个产品的性能和安全性。
铸钢件在生产过程中常常会出现气孔缺陷,这种缺陷会严重影响铸钢件的质量和使用寿命。
对于铸钢件气孔缺陷的分析和预防具有非常重要的意义。
一、气孔缺陷的产生原因1.1 原料质量问题铸钢件的气孔缺陷的产生原因之一可能是原料的质量问题。
原料中含有过多的杂质或含氧量过高,会导致铸钢件的气孔缺陷。
1.2 浇注过程中的问题在铸造过程中,如果浇注温度控制不当或者浇注速度过快,都有可能造成气孔缺陷。
1.3 模具设计问题模具设计不合理或者模具使用过程中磨损严重,也会导致铸钢件的气孔缺陷。
1.4 涂料和砂芯问题在铸造过程中使用的涂料和砂芯,如果质量不过关,也会导致铸钢件的气孔缺陷。
二、气孔缺陷的危害气孔缺陷对铸钢件的性能和安全性都会造成严重影响。
气孔缺陷会降低铸钢件的力学性能,使得其承载能力大大降低。
气孔缺陷还会对铸钢件表面造成影响,使得表面粗糙度增加,从而影响其准确度。
最重要的是,气孔缺陷会严重影响铸钢件的耐久性和使用寿命,一旦出现气孔缺陷,铸钢件就容易出现断裂或者损坏,给使用带来了极大的安全隐患。
3.1 外观检查法通过外观检查法可以初步判断铸钢件是否存在气孔缺陷,一般来说,气孔缺陷的铸钢件表面会出现突起或凹槽。
3.3 X射线检测法X射线检测法是一种非破坏性检测方法,通过对铸钢件进行X射线检测可以清晰地观察到其中的气孔缺陷情况。
四、气孔缺陷的预防措施4.1 优化原料首先要做好原料的筛选工作,保证原料的质量符合要求,避免其中含有过多的杂质或氧化物。
4.3 设计优化模具对于模具的设计和使用,要进行优化和维护,确保模具的质量符合要求,避免因此造成气孔缺陷。
4.5 定期检测定期对铸钢件进行外观检查和X射线检测,发现问题及时进行处理,避免气孔缺陷的出现。
铸钢气孔缺陷产生原因是什么?怎样预防?
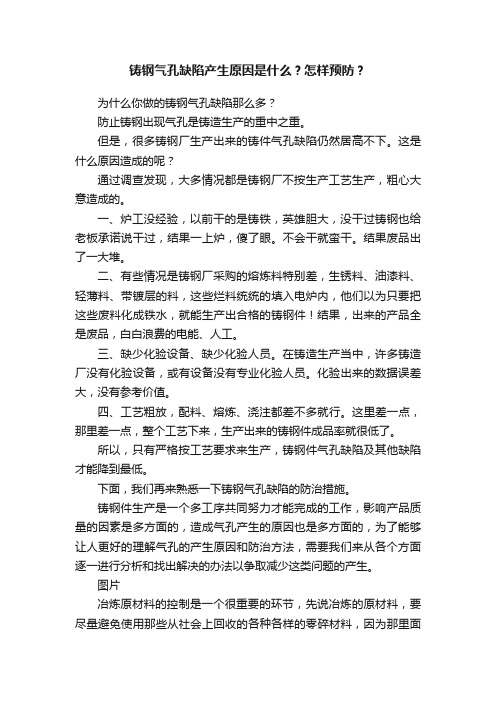
铸钢气孔缺陷产生原因是什么?怎样预防?为什么你做的铸钢气孔缺陷那么多?防止铸钢出现气孔是铸造生产的重中之重。
但是,很多铸钢厂生产出来的铸件气孔缺陷仍然居高不下。
这是什么原因造成的呢?通过调查发现,大多情况都是铸钢厂不按生产工艺生产,粗心大意造成的。
一、炉工没经验,以前干的是铸铁,英雄胆大,没干过铸钢也给老板承诺说干过,结果一上炉,傻了眼。
不会干就蛮干。
结果废品出了一大堆。
二、有些情况是铸钢厂采购的熔炼料特别差,生锈料、油漆料、轻薄料、带镀层的料,这些烂料统统的填入电炉内,他们以为只要把这些废料化成铁水,就能生产出合格的铸钢件!结果,出来的产品全是废品,白白浪费的电能、人工。
三、缺少化验设备、缺少化验人员。
在铸造生产当中,许多铸造厂没有化验设备,或有设备没有专业化验人员。
化验出来的数据误差大,没有参考价值。
四、工艺粗放,配料、熔炼、浇注都差不多就行。
这里差一点,那里差一点,整个工艺下来,生产出来的铸钢件成品率就很低了。
所以,只有严格按工艺要求来生产,铸钢件气孔缺陷及其他缺陷才能降到最低。
下面,我们再来熟悉一下铸钢气孔缺陷的防治措施。
铸钢件生产是一个多工序共同努力才能完成的工作,影响产品质量的因素是多方面的,造成气孔产生的原因也是多方面的,为了能够让人更好的理解气孔的产生原因和防治方法,需要我们来从各个方面逐一进行分析和找出解决的办法以争取减少这类问题的产生。
图片冶炼原材料的控制是一个很重要的环节,先说冶炼的原材料,要尽量避免使用那些从社会上回收的各种各样的零碎材料,因为那里面的杂质过于的复杂,容易给冶炼过程造成不必要的麻烦,延长冶炼时间,而冶炼过程又不是煮稀饭时间越长越好,随着时间的延长钢水中的各种成分含量在时刻发生着变化,像去年天津发生爆炸以后有许多小汽车报费了,说是送到炼钢厂去炼钢了,搞过冶炼的人一定知道这样的所为废钢是多么差的了,估计拿到这批废钢的单位干活的师傅们要难过了,要把这样的东西炼成好钢难度一定不小。
铸件气孔缺陷的成因及防止措施
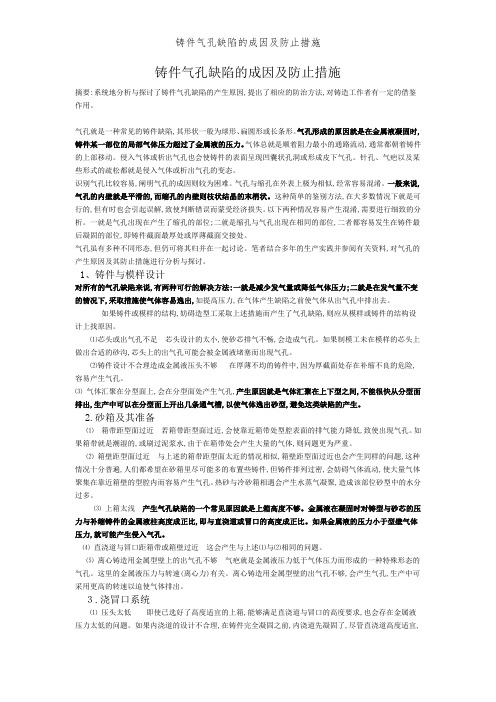
铸件气孔缺陷的成因及防止措施摘要:系统地分析与探讨了铸件气孔缺陷的产生原因,提出了相应的防治方法,对铸造工作者有一定的借鉴作用。
气孔就是一种常见的铸件缺陷,其形状一般为球形、扁圆形或长条形。
气孔形成的原因就是在金属液凝固时,铸件某一部位的局部气体压力超过了金属液的压力。
气体总就是顺着阻力最小的通路流动,通常都朝着铸件的上部移动。
侵入气体或析出气孔也会使铸件的表面呈现凹囊状孔洞或形成皮下气孔。
针孔、气疤以及某些形式的疏松都就是侵入气体或析出气孔的变态。
识别气孔比较容易,阐明气孔的成因则较为困难。
气孔与缩孔在外表上极为相似,经常容易混淆。
一般来说,气孔的内壁就是平滑的,而缩孔的内壁则枝状结晶的末梢状。
这种简单的鉴别方法,在大多数情况下就是可行的,但有时也会引起误解,致使判断错误而蒙受经济损失。
以下两种情况容易产生混淆,需要进行细致的分析。
一就是气孔出现在产生了缩孔的部位;二就是缩孔与气孔出现在相同的部位,二者都容易发生在铸件最后凝固的部位,即铸件截面最厚处或厚薄截面交接处。
气孔虽有多种不同形态,但仍可将其归并在一起讨论。
笔者结合多年的生产实践并参阅有关资料,对气孔的产生原因及其防止措施进行分析与探讨。
1、铸件与模样设计对所有的气孔缺陷来说,有两种可行的解决方法:一就是减少发气量或降低气体压力;二就是在发气量不变的情况下,采取措施使气体容易逸出,如提高压力,在气体产生缺陷之前使气体从出气孔中排出去。
如果铸件或模样的结构,妨碍造型工采取上述措施而产生了气孔缺陷,则应从模样或铸件的结构设计上找原因。
⑴芯头或出气孔不足芯头设计的太小,使砂芯排气不畅,会造成气孔。
如果制模工未在模样的芯头上做出合适的砂沟,芯头上的出气孔可能会被金属液堵塞而出现气孔。
⑵铸件设计不合理造成金属液压头不够在厚薄不均的铸件中,因为厚截面处存在补缩不良的危险,容易产生气孔。
⑶气体汇聚在分型面上,会在分型面处产生气孔,产生原因就是气体汇聚在上下型之间,不能很快从分型面排出,生产中可以在分型面上开出几条通气槽,以使气体逸出砂型,避免这类缺陷的产生。
铸钢件气孔缺陷的分析及预防

铸钢件气孔缺陷的分析及预防
铸钢件是一种重要的金属零件,广泛应用于各种机械设备和工程结构中。
然而,由于制造和铸造过程中可能发生气孔缺陷,影响其性能和寿命。
因此,对铸钢件气孔缺陷的分析和预防是非常重要的。
首先,分析铸钢件气孔缺陷的原因。
气孔缺陷是在铸造过程中由于气体存在所产生的孔洞。
常见的原因有以下几点:
1.铸造工艺不合理。
例如,铸造温度过低或过高,浇注速度过快或过慢,模具设计不合理等,都会导致气孔的产生。
2.原料质量问题。
铸造原料杂质含量高或含水量过多也会导致气孔的产生。
3.浇注系统不完善。
例如,浇口设计不合理、浇注系统中存在堵塞或过多的曲折通道等都会导致气孔的产生。
其次,预防铸钢件气孔缺陷可以从以下几个方面入手。
2.选择优质的原材料。
减少杂质含量、控制含水量等,有助于减少气孔的产生。
3.完善浇注系统。
设计合理的浇口和通道,以及设置无死角的通道,可以避免气孔的产生。
最后,对于已经产生的铸钢件气孔缺陷,可以采用以下方法处理。
1.打孔。
对于小型的气孔,可以通过钻孔或冲孔等方式将气孔的部分打通,减少对零件性能的影响。
2.热处理。
通过热处理的方式,可以将气孔的位置和体积减小,并达到改善铸钢件性能的目的。
综上所述,铸钢件气孔缺陷的分析和预防是非常重要的。
在铸造工艺、原材料选择和浇注系统设计等方面采取合理的措施,可以有效地降低气孔的产生,从而提高铸钢件的性能和寿命。
同时,对于已经产生的气孔缺陷,也可以通过打孔和热处理等方式来得到有效地处理。
铸件气孔缺陷的成因及防止措施

铸件气孔缺陷的成因及防止措施摘要:系统地分析和探讨了铸件气孔缺陷的产生原因,提出了相应的防治方法,对铸造工作者有一定的借鉴作用。
气孔是一种常见的铸件缺陷,其形状一般为球形、扁圆形或长条形。
气孔形成的原因是在金属液凝固时,铸件某一部位的局部气体压力超过了金属液的压力。
气体总是顺着阻力最小的通路流动,通常都朝着铸件的上部移动。
侵入气体或析出气孔也会使铸件的表面呈现凹囊状孔洞或形成皮下气孔。
针孔、气疤以及某些形式的疏松都是侵入气体或析出气孔的变态。
识别气孔比较容易,阐明气孔的成因则较为困难。
气孔和缩孔在外表上极为相似,经常容易混淆。
一般来说,气孔的内壁是平滑的,而缩孔的内壁则枝状结晶的末梢状。
这种简单的鉴别方法,在大多数情况下是可行的,但有时也会引起误解,致使判断错误而蒙受经济损失。
以下两种情况容易产生混淆,需要进行细致的分析。
一是气孔出现在产生了缩孔的部位;二是缩孔和气孔出现在相同的部位,二者都容易发生在铸件最后凝固的部位,即铸件截面最厚处或厚薄截面交接处。
气孔虽有多种不同形态,但仍可将其归并在一起讨论。
笔者结合多年的生产实践并参阅有关资料,对气孔的产生原因及其防止措施进行分析和探讨。
1.铸件和模样设计对所有的气孔缺陷来说,有两种可行的解决方法:一是减少发气量或降低气体压力;二是在发气量不变的情况下,采取措施使气体容易逸出,如提高压力,在气体产生缺陷之前使气体从出气孔中排出去。
如果铸件或模样的结构,妨碍造型工采取上述措施而产生了气孔缺陷,则应从模样或铸件的结构设计上找原因。
⑴芯头或出气孔不足芯头设计的太小,使砂芯排气不畅,会造成气孔。
如果制模工未在模样的芯头上做出合适的砂沟,芯头上的出气孔可能会被金属液堵塞而出现气孔。
⑵铸件设计不合理造成金属液压头不够在厚薄不均的铸件中,因为厚截面处存在补缩不良的危险,容易产生气孔。
⑶气体汇聚在分型面上,会在分型面处产生气孔,产生原因是气体汇聚在上下型之间,不能很快从分型面排出,生产中可以在分型面上开出几条通气槽,以使气体逸出砂型,避免这类缺陷的产生。
浅谈铸件气孔的产生及其防止措施

浅谈铸件气孔的产生及其防止措施气孔是铸造生产中常见的铸件缺陷之一。
在铸件的废品中,据统计,由于气孔导致的铸件废品占废品总数的三分之一左右。
气孔是气体聚集在铸件表面、皮下和内部而形成的空洞。
气孔的孔壁光滑,无一定的形状、尺寸和位置。
气孔有各种类型,其产生的原因各不相同,按气体来源,一般将气孔分为三类:侵入性气孔、析出性气孔和反应性气孔。
一、侵入性气孔由于浇注过程中液态金属对铸型激烈的热作用,使型砂和芯砂中的发气物(水分、粘接剂等)气化、分解和燃烧,生成大量气体,加上型腔中原有的气体,这些气体部分侵入液态金属内部而不能逸出所产生的孔洞,称为侵入性气孔。
1.侵入性气孔的形成条件由于浇注时铸型在液态金属的高温作用下产生大量气体,从而使液态金属和铸型界面上的气体压力骤然增加,气体可能侵入液态金属,也有可能从型砂或冒口、出气孔中排出型外,只有在满足下列条件的情况下型(芯)砂中的气体才会侵入液态金属即P气>p液+p阻+p腔式中p气:液态金属和砂型界面的气体压力;P液:液态金属的静压力(p液=ρgh)P阻:气体侵入液态金属时,由于液态金属表面张力而引起的阻力P腔:型腔中液态金属液面上的气体压力2.防止侵入性气孔的主要方法和工艺措施(1)降低砂型(芯)界面的气体压力是最有效的手段。
如选用透气性好,发气量低的造型材料;控制型砂的水分及其它发气附加物;应用发气量低、发气速度慢、发气温度高的粘结剂;砂型(芯)排气要畅通,增加出气孔,提高铸型的排气能力;浇注后及时引火。
引火后可听到气体的爆燃声和砂箱周围燃烧的火焰,砂箱移开后,可看到下部潮湿的痕迹。
说明有大量的气体产生如H2、O2、CO、H2S等气体。
(2)适当提高浇注温度,延迟凝固时间,使侵入的气体有充分的时间从液态金属中上浮和逸出。
(3)加快浇注速度,增加上砂型高度,使有效压力头增加,提高液态金属的静压力。
(4)浇注系统在设置时,应注意液态金属流的平稳,浇注千万不能中断,防止气体卷入金属液中。
铸件气孔形成的原因及解决的措施

铸件气孔形成的原因及解决的措施在工厂的生产实践中,人们对气孔的叫法不一样。
有的叫气眼、气泡、气窝,丛生气孔,划为一体统称为“气孔”。
气孔是铸件最常见的缺陷之一。
在铸件废品中,气孔缺陷占很大比例,特别是在湿模砂铸造生产中,此类缺陷更为常见,有时会引起成批报废。
球墨铸铁更为严重。
气孔是在铸件成型过程中形成的,形成的原因比较复杂,有物理作用,也有化学作用,有时还是两者综合作用的产物。
有些气孔的形成机理尚无统一认识,因为其形成的原因可能是多方面的。
各类合金铸件,产生气孔缺陷有其共性,但又都是在特定条件下生成的,因此又都具有特殊性。
所以要从共性中分析产生气孔的一般规律,也要研究特性中的特有规律,以便采取有效的针对性措施,防止气孔缺陷的产生。
一、气孔的特征气孔大部分产生在铸件的内表面或内部、砂芯面以及靠近芯撑的地方。
形状有圆形的、长方形的以及不规则形状,直径有大的、小的也有似针状丛生孔形。
气孔通常具有干净而光滑的内孔面,有时被一层氧化皮所覆盖。
光滑的孔内颜色一般是白色,或带有一层暗蓝色,有的气孔内壁还有一个或几个小铁豆豆,常把这种气孔称作“铁豆气孔”。
距铸件表面很近的气孔,又叫“皮下气孔”,往往通过热处理、清滚或者机械加工后才被发现。
还有一种常见的气孔,叫做“气缩孔”,是气体和铸件凝固时的收缩而共同促使其产生的,形状又有其特殊性。
铸钢和高牌号铸铁都常出这种名称的缺陷,但形成的机理有所差异。
气孔和缩孔是可以区别开的,一般说来气孔是圆形或梨形的孔洞,内壁光滑。
而不像缩孔那样内表面比较粗糙。
二、气体的来源各类铸造合金在熔炼及成型过程中,总要和气体相接触的,气体就会进入并以各种形式存在于合金中,气体来源是多方面的,归纳起来,主要来自以下几个方面:1、原材料带进的。
各种铁类、铁合金、燃料、熔剂等,自身就含有气体,有的带有雨雪潮湿,有的锈蚀,有的带有浊污,在熔炼过程中都有可能产生气体,其中一部分就会滞留在合金液中。
有人提出:炉料上带的雨水、雪湿、浊污随炉料进入炉内,在炉料还是固态仅发红时,它们就已蒸发或烧掉,怎么会留存在铁水里呢?在资料里,用语言详细解释的不多,但在实践中,只要炉料(生铁、废钢、回炉料)受雨雪淋湿,湿着入炉,铁水一定会氧化,这确是事实。
- 1、下载文档前请自行甄别文档内容的完整性,平台不提供额外的编辑、内容补充、找答案等附加服务。
- 2、"仅部分预览"的文档,不可在线预览部分如存在完整性等问题,可反馈申请退款(可完整预览的文档不适用该条件!)。
- 3、如文档侵犯您的权益,请联系客服反馈,我们会尽快为您处理(人工客服工作时间:9:00-18:30)。
精铸论文四:
熔模铸钢件气孔的产生与防止
熔模铸钢件的气孔分为:析出性、侵入性、卷入性、等三种类型。
气孔是熔模铸造常见的缺陷之一。
气孔是气泡在液体金属凝固结壳前来不及浮出而留在铸件内部形成的一种孔洞
缺陷。
1、析出性气孔
此种气孔是指由液体金属中析出的气体而形成的气孔。
此种气孔的形状可以是球形、不规则形、针孔。
(在凝固前期析出形成的气孔可能呈球形,但在凝固后期气孔的形状受凝固界面的影响较大,而呈不规则形状。
)
析出性气孔又分为:过溶析出性气孔和反应析出性气孔。
(1)过溶析出性气孔
此类气孔是由于溶入液体金属中的气体呈过饱和析出而形
成的。
此类影响的气体主要是氢和氮。
(氢不仅能在钢中产生气孔,而且能引起裂纹。
)
钢中氢的来源主要来自水分和铁锈。
(当炉料、工具、炉体等受潮时,水分在高温时分解,H2O→2H+0;分解产生的氢原
子极易被钢液吸收。
因此防止此类缺陷的主要措施是清洁炉料和保待炉体、浇包、炉料、铁合金、造渣剂、工具等干燥。
)一般说氮对钢中气孔的影响很小。
(2)反应析出性气孔
此类气孔是由于液体金属中发生化学反应产生的气体析出
而形成。
影响最大的是氧。
此类气孔可能呈现三种形态:
①、当钢液严重氧化时,FeO高;
②、当钢液脱氧不完善时,FeO高;
③、当钢液脱氧后残铝量不够,浇注后产生二次氧化,形成FeO高。
预防措施:
1、清洁炉料,特别是铁锈严重的炉料应经除锈处理。
(铁锈不仅带入FeO而且带入了H2O,H2O分解引起钢液吸氢。
)
②、快速熔炼。
(缩短高温冶炼时间。
)
③、充分脱氧。
(用AL量一般为0.04%-0.06%,不超过0.15%)
2、侵入性气孔
气体将侵入液体金属而形成气孔。
一般指水玻璃制壳,气体来源主要是NaCl。
避免措施:
①、受潮型壳不得浇注,应力求热壳浇注;
②、制壳时避免涂料堆积,硬化不充分;
③、焙烧应充分。
3、卷入性气孔
卷入性气孔的气体来自型腔,其中主要是大气。
(与型壳透气性有关。
)
防止措施:
①、铸造方案设计时应方便排气,尽量使液体金属能平稳的
有序的充型。
②、薄壁铸件充型末端建议设置集气包、溢气槽、排气边、出气口。
吴光来
二〇〇四年六月二十日。