氧化铝基板加工图样
氧化铝生产流程图

一.工艺简介氧化铝的生产工艺,是用碱来处理铝矿石,使矿石中的氧化铝转变成铝酸钠溶液。
矿石中的铁、钛等杂质和绝大部分的硅则成为不溶解的化合物,将不溶解的残渣与溶液分离,经洗涤后弃去或综合利用,以回收其中的有用组分。
纯净的铝酸钠溶液分解析出氢氧化铝,经与母液分离、洗涤后进行焙烧,得到氧化铝产品。
分解母液可循环使用,处理另外一批矿石。
-整个生产工艺分为8个工段:原料磨、溶出、赤泥沉降、控制过滤、分解分级、蒸发、成品过滤、焙烧。
下面从这八个工段分别介绍。
-二.原料磨在原料磨工段,铝土矿、石灰及循环母液按比例加入棒磨和球磨机中磨制原矿浆,原矿浆由水力旋流器进行分级,分级机溢流为合格的原矿浆,送入原矿浆槽,再用矿浆泵送往溶出车间的常压脱硅工段。
--三.溶出从原料车间送来的原矿浆进入常压脱硅工段的加热槽中,采用蒸汽加热,将矿浆温度控制在100℃~110℃,然后送入脱硅槽中进行连续脱硅。
在脱硅槽的末槽用母液调整经脱硅后的原矿浆RP和温度。
合格原矿浆送至高压泵房的隔膜泵,脱硅机理底部设有返砂管、返砂泵,每班定期将粗砂返回原料磨工段。
-用隔膜泵将原矿浆送往溶出工段的套管预热器,由六级套管加热器将原矿浆温度预热至174~180℃,而后采用高压新蒸汽间接加热,原矿浆加热至260℃,保温停留60分钟。
溶出后料浆经十级闪蒸,温度从260℃降至125℃,然后送入稀释槽。
从赤泥洗涤送来的赤泥洗液同时加入稀释槽中,稀释料浆用泵送往溶出后槽,停留守4小时以上,以脱除溶液中的硅、铁、锌等杂质。
--四.赤泥沉降从溶出后槽送来的稀释料浆与从絮凝剂制备工段来的絮凝剂一同进入分离沉降槽中,分离沉降槽底流含固量约38%~42%,用泵送往洗涤沉降槽,采用四次反向洗涤,洗水从末槽加入,末次洗涤底流固体含量约46%~54%,拟用高压隔膜泵送往赤泥堆场堆存。
--五.控制过滤分离沉降槽溢流送控制过滤工段的粗液槽,控制过滤采用立式叶滤机,同时将少量石灰乳加进粗液槽中作为助滤剂,叶滤得到的精液送分解车间的精液板式热交换工段,叶滤渣进滤渣槽中,用泵送回一洗沉降槽。
氧化铝常见用途有哪些

氧化铝常见用途有哪些
氧化铝是一种白色晶体固体,具有高熔点、高硬度、高绝缘性、化学稳定性好等特点。
由于它的优异性能,氧化铝被广泛应用于各个领域。
以下是氧化铝常见的用途:
1.陶瓷工业
氧化铝具有良好的化学稳定性和高温性能,因此它是生产陶瓷的重要原料。
在生产陶瓷时,氧化铝能够增加瓷器的硬度和抗磨性,并能够提高釉料的透明度和亮度。
2.电子工业
由于氧化铝具有良好的绝缘性和导电性,因此它被广泛用于电子工业中。
用氧化铝作为基板可以制作高密度的电路板,也可以用来制作电子陶瓷。
3.建筑工业
氧化铝可以用来制作各种建筑材料,如人造石材、人造木材、防火板等。
氧化铝制成的人造材料具有良好的耐久性和耐磨性,可以替代天然木材和石材,降低资源消耗。
4.磨料工业
氧化铝颗粒是一种常见的磨料,因为它具有硬度高、刚性好、耐磨损等特点,可以用于金属加工、磨削、抛光等领域。
5.化工工业
氧化铝可以用来制造各种化工产品,如氧化铝胶体、氧化铝水凝胶等。
这些产品被广泛应用于催化剂、阻燃剂、吸附材料等领域。
6.医药工业
氧化铝可以用来制造医用陶瓷和人工关节等医疗器械,也可以用来制作药物控释剂。
由于氧化铝具有良好的生物相容性和化学稳定性,因此其在医药领域中有着广泛的应用前景。
总的来说,氧化铝是一种十分重要的工业原料,被广泛应用于各个领域。
随着科技的不断进步,氧化铝的应用前景将越来越广阔。
氧化铝ppt课件
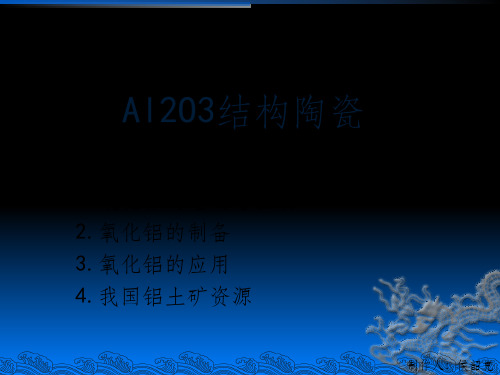
下仍能保持其性能不变;
水系流延成形 Al2O3陶瓷基片,利用非水系
(2 )高强度 ,在很大压力梯度操作 流延成形可以制备表面光滑 、平整、致密
下 , 不会被压缩或产生蠕变,机械性能好;度高的Al2O3陶瓷基片,但在制备工艺中,
(3 )化学稳定性好 ,能耐强酸强碱 基片的烧结温度高、耗能大。 因此可以在
氧化铝陶瓷基片
Al2O3陶瓷膜在净化工业用水加工、海
Al2O3陶瓷基片具有机械强度高、绝缘
水淡化、气体分离、催化反应等方面都具有 性好、避光性高等优良性能,广泛用于多层
大量的应用,陶瓷膜与有机高分子膜相比: 布线陶瓷基片、电子封装及高密度封装基片。
(1 )耐高温 、热稳定性好 ,在高温
目前 , 在工业应用中大部分都采用非
了氮化硅基陶瓷刀具材料及ZrO2相变增韧陶瓷刀具材料,80年代后期
到90年代,发展了晶须增韧陶瓷刀具材料。
增韧 Al2O3陶 瓷 刀 具 是 指 在 Al2O3基 体 中 添 加 增韧
或增强材料。 目前常用的增韧方法有:ZrO2相变增韧、晶须增韧、
第二相颗粒弥散增韧等。
.
3.氧化铝的应用
多通道管式陶瓷膜元件
CaO • Al2O3
-Al2O3
Al2O3有很多种晶型,目前发现的在十二种以上,其中 常见的有 、、、、、等。其中是高温稳定晶型, 其它均为不稳定的过渡晶型,在高温下可以转变为相。
.
1.氧化铝的结构与性质
图:-Al2O3晶体结构
-Al2O3为刚玉结构,属于三方晶系。正负 离子配位数为6:4,在三次轴平面内O2-作近似六 方密排(A-B-A-B),而Al3+则位于氧的八面体 间隙(在两氧离子层之间),填充三分之二八面 体间隙。
氧化铝基产品,-概述说明以及解释

氧化铝基产品,-概述说明以及解释1.引言1.1 概述概述氧化铝是一种常见的化工原料,具有广泛的应用领域。
作为一种重要的陶瓷材料,氧化铝具有优异的物理和化学性质,被广泛应用于建筑材料、电子器件、汽车制造、医疗设备等领域。
随着科学技术的不断进步,氧化铝基产品已经成为了现代工业中不可或缺的一部分。
本文将对氧化铝基产品的基本性质、制备方法以及应用领域进行详细介绍。
首先,我们将介绍氧化铝的基本性质,包括其物理性质、化学性质、结构特点等,帮助读者更好地理解这一材料。
然后,我们将深入探讨氧化铝的制备方法,包括传统的氧气燃烧法、水热法以及气相沉积法等,以期为氧化铝生产过程提供参考和借鉴。
最后,我们将重点介绍氧化铝基产品在不同领域的应用,包括建筑材料中的外墙饰面、电子器件中的绝缘材料、汽车制造中的陶瓷刀具等,以展示氧化铝的多样化应用潜力。
通过深入了解氧化铝基产品的相关知识,我们可以更好地认识和利用这一材料,在推动相关产业发展和提高产品性能方面起到积极的作用。
本文的结论部分将对氧化铝基产品的重要性进行总结,并对未来的研究方向和发展趋势进行展望,以期为相关研究者提供参考和启发。
在本文的剩余部分中,我们将逐一介绍氧化铝的基本性质、制备方法和应用领域,希望读者能够通过详细了解这一材料的各个方面,对氧化铝的重要性和潜力有更加清晰的认识。
同时,我们也希望本文能够为相关研究者提供一些思路和启示,促进氧化铝基产品的进一步发展和应用。
1.2 文章结构文章结构部分的内容可以编写为:文章结构:本文将分为三个部分进行介绍和讨论。
首先,在引言部分将概述本文的主题和目的,为读者提供一个整体的认识。
其次,在正文部分将从三个方面对氧化铝基产品进行详细阐述。
分别是氧化铝的基本性质、氧化铝的制备方法以及氧化铝基产品的应用领域。
这三个方面将形成一个完整的氧化铝基产品的知识体系,帮助读者全面了解和掌握相关知识。
最后,在结论部分将对全文进行总结和展望。
总结氧化铝基产品的重要性,回顾本文所涉及的关键点,强调其在工业和科学研究领域的价值。
氧化铝工艺流程图及概述
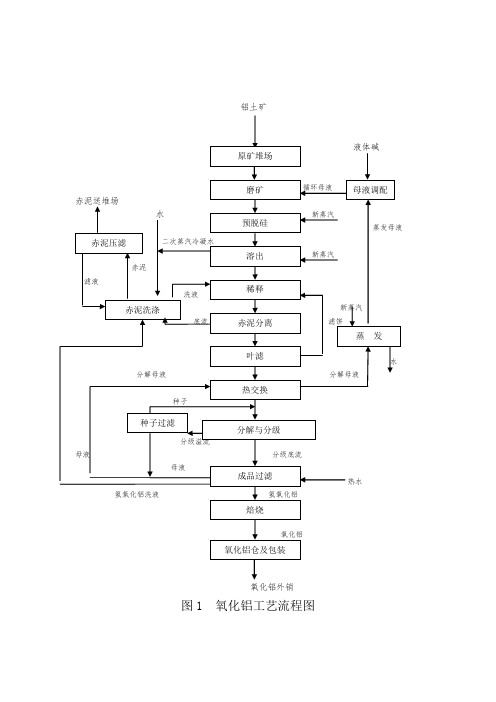
铝土矿液体碱循环母液 赤泥送堆场水新蒸汽 蒸发母液二次蒸汽冷凝水新蒸汽赤泥 滤液洗液新蒸汽 底流 滤饼水分解母液 分解母液种子分级溢流母液 分级底流母液热水氢氧化铝洗液 氢氧化铝氧化铝氧化铝外销图1 氧化铝工艺流程图原矿堆场 磨矿 预脱硅 溶出 稀释赤泥分离 叶滤 热交换 分解与分级成品过滤 焙烧氧化铝仓及包装母液调配 蒸 发赤泥洗涤 种子过滤 赤泥压滤氧化铝厂工艺流程概述我公司用拜尔法生产氧化铝。
海外来的铝土矿经汽车运至卸矿站卸入矿仓后,由板式给料机和胶带输送机送至铝矿均化堆场或磨头仓。
铝矿均化堆场的铝土矿用悬臂式堆取料机取料后经皮带运输机送至磨头仓。
由铝矿和蒸发来的循环母液按一定配比进球磨和水旋器组成的磨矿分级系统,分级溢流(原矿浆)进入原矿浆槽。
原矿浆经6~8h脱硅后的成品矿浆用隔膜泵送入溶出系统。
首先由3级套管进行逐级预热,再用约0.8Mpa新蒸汽间接加热第九级套管和压煮器内矿浆到规定溶出温度140℃~150℃,后进入保温溶出罐保温溶出30分钟左右,经四级自蒸发器闪蒸降温后,溶出矿浆用赤泥洗液稀释。
闪蒸产生的二次蒸汽用于3级套管预热,新蒸汽冷凝水经闪蒸成0.6Mpa蒸汽并入全厂低压蒸汽管网,新蒸汽不含碱冷凝水返回热电厂。
二次蒸汽冷凝水及新蒸汽含碱冷凝水送热水站。
稀释矿浆经过3~4h脱硅后,送入在Ф22×18m锥形沉降槽内进行液固分离,底流进入洗涤沉降槽进行四次赤泥反向洗涤,热水加入末次洗涤,末次洗涤底流送至赤泥堆场,经压滤机压滤后滤饼进行堆存,滤液返回赤泥洗涤。
分离沉降槽中添加由絮凝剂工序制备好的絮凝剂,洗涤槽视情况也可适量添加。
分离沉降槽溢流自压至粗液槽,再用泵送往综合过滤的立式叶滤机进行过滤,过滤时加入助滤剂(石灰乳)。
滤饼送至稀释槽,滤液(精液)送板式热交换器。
精液经板式热交换器与种分母液和冷却水进行热交换冷却到设定温度,再与种子过滤滤饼(晶种)混合后至分解槽,经过约50h的连续晶种分解后,用立式泵抽取分解浆液去进行旋流分级,分级前加入部分种分母液稀释,分级溢流进如下一个分解槽。
氧化铝基板制备方法(一)

氧化铝基板制备方法(一)氧化铝基板制备方法方法概述在电子元器件、光学器件、热导材料等领域中,氧化铝基板是一种常用的基础材料。
本文将介绍几种常见的氧化铝基板制备方法,以便读者了解和选择适合自己需求的方法。
1. 碳化铝法碳化铝法是一种常见的制备氧化铝基板的方法之一。
具体步骤如下:•准备碳化铝粉末和氧化铝粉末;•将碳化铝粉末和氧化铝粉末按一定比例混合均匀;•将混合粉末放入高温炉中,在氧气氛围中进行烧结;•在适当的温度下保温一段时间,使混合粉末烧结成为氧化铝基板;•冷却后取出氧化铝基板,进行后续处理。
碳化铝法制备的氧化铝基板具有高纯度、均匀性好的特点,适用于制备高质量氧化铝基板。
2. 溶胶-凝胶法溶胶-凝胶法是另一种常见的氧化铝基板制备方法。
以下是该方法的主要步骤:•制备溶胶:将适量的铝源与溶剂混合,在适当的温度下进行搅拌,形成均匀的溶胶;•凝胶处理:将溶胶静置,在常温下进行凝胶化处理;•干燥:将凝胶体进行干燥,使其转变成为固体凝胶;•烧结:将固体凝胶样品放入高温炉中,在氧气氛围中进行烧结处理;•冷却后取出氧化铝基板。
溶胶-凝胶法制备的氧化铝基板具有高纯度、均匀性好、成本较低等优点,在一些特定领域得到了广泛应用。
3. 等离子体增强化学气相沉积法(PECVD)等离子体增强化学气相沉积法是一种常用的氧化铝基板制备方法之一,其步骤如下:•准备合适的基板样品,确保其表面干净平整;•加入适量的氧化铝前体气体,如三乙醇氧铝(TEA),并进行残留空气排除;•施加高频电场或射频电场,产生等离子体;•等离子体激活前体气体,使其分解并生成氧化铝薄膜;•控制沉积时间和沉积条件,使薄膜达到所需厚度;•关闭等离子体,冷却后取出氧化铝基板。
PECVD法具有制备速度快、薄膜均匀性好、可以在较低温度下进行等优点,适用于大规模生产。
4. 氧化铝模板法氧化铝模板法是一种通过模板制作氧化铝基板的方法,具体步骤如下:•准备金属模板,如铝模板;•在模板表面形成氧化铝层,可以通过阳极氧化等方法实现;•在模板上涂覆适量的防粘剂,以便后续去除模板;•将模板放入溶剂中,使其与粘附的氧化铝分离;•对分离的氧化铝进行后续处理,如清洗、烧结等。
氮化铝陶瓷基板与氧化铝陶瓷基板三个方面的不同点
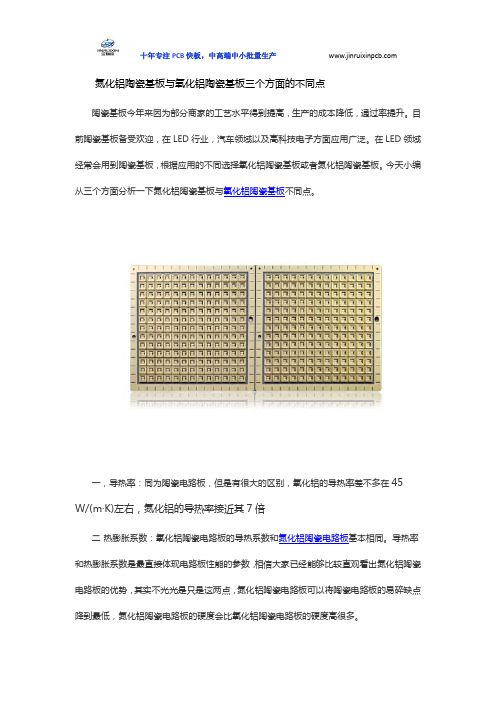
氮化铝陶瓷基板与氧化铝陶瓷基板三个方面的不同点
陶瓷基板今年来因为部分商家的工艺水平得到提高,生产的成本降低,通过率提升。
目前陶瓷基板备受欢迎,在LED行业,汽车领域以及高科技电子方面应用广泛。
在LED领域经常会用到陶瓷基板,根据应用的不同选择氧化铝陶瓷基板或者氮化铝陶瓷基板。
今天小编从三个方面分析一下氮化铝陶瓷基板与氧化铝陶瓷基板不同点。
一,导热率:同为陶瓷电路板,但是有很大的区别,氧化铝的导热率差不多在45
W/(m·K)左右,氮化铝的导热率接近其7倍
二热膨胀系数:氧化铝陶瓷电路板的导热系数和氮化铝陶瓷电路板基本相同。
导热率和热膨胀系数是最直接体现电路板性能的参数,相信大家已经能够比较直观看出氮化铝陶瓷电路板的优势,其实不光光是只是这两点,氮化铝陶瓷电路板可以将陶瓷电路板的易碎缺点降到最低,氮化铝陶瓷电路板的硬度会比氧化铝陶瓷电路板的硬度高很多。
三,应用市场的不同
氮化铝陶瓷基板多用于大功率散热比如LED大功率照明,或者需要绝缘性非常好的通讯产品领域;氧化铝陶瓷基板,一般多用于中小功率方面,也包括LED灯珠照明,以及传感器等产品上。
国内目前能专业做好陶瓷线路板厂家不多,金瑞欣特种电路是专业的陶瓷基板生产厂家,主营陶瓷pcb打样和中小批量生产,可以加工精密线路,实铜填孔,3D工艺和围坝工艺等,更多详情可以咨询金瑞欣特种电路官网。
氮化铝和氧化铝陶瓷基板

氮化铝和氧化铝陶瓷基板1. 简介氮化铝(AlN)和氧化铝(Al2O3)是两种常见的陶瓷材料,它们具有优异的热导率、电绝缘性能和机械强度,因此被广泛应用于电子、光电子和高功率器件等领域。
本文将详细介绍氮化铝和氧化铝陶瓷基板的特性、制备方法以及应用领域。
2. 氮化铝陶瓷基板2.1 特性氮化铝陶瓷基板是一种具有高导热性和优异机械强度的材料。
其具体特性如下:•高导热性:氮化铝具有较高的热导率(约170-230 W/m·K),能够有效地散发器件产生的热量,提高器件的散热效果。
•低CTE:氮化铝的线膨胀系数(CTE)较低,与硅片等材料匹配良好,减少因温度变化引起的应力。
•优异机械强度:由于其晶体结构的特殊性,氮化铝具有较高的抗弯强度和抗压强度,能够在高温和高压环境下保持稳定性。
•优良的电绝缘性:氮化铝是一种优良的电绝缘材料,能够有效地隔离器件之间的电流。
2.2 制备方法氮化铝陶瓷基板的制备方法主要包括热压烧结法和化学气相沉积法。
•热压烧结法:将预制的氮化铝粉末在高温高压条件下进行烧结,使其形成致密的陶瓷基板。
这种方法制备出来的基板具有较高的密度和机械强度。
•化学气相沉积法:通过将金属有机化合物蒸发在基板表面,并与氨反应生成氮化物,从而在基板上沉积出薄膜。
这种方法可以制备出较薄且表面光滑的氮化铝陶瓷基板。
2.3 应用领域由于其优异的导热性、电绝缘性和机械强度,氮化铝陶瓷基板被广泛应用于以下领域:•电子器件:氮化铝陶瓷基板可以作为高功率电子器件的散热基板,提高器件的散热性能,延长器件的使用寿命。
•光电子器件:氮化铝陶瓷基板具有优异的光学性能,可以用于制备光电子器件中的光学窗口、反射镜等组件。
•半导体封装:氮化铝陶瓷基板可作为半导体封装材料,用于制备高功率封装模块和LED封装等产品。
•太阳能电池:氮化铝陶瓷基板具有较好的耐高温性能和机械强度,可以作为太阳能电池的基底材料。
3. 氧化铝陶瓷基板3.1 特性氧化铝陶瓷基板是一种常见的绝缘材料,具有以下特性:•优良的绝缘性:氧化铝具有较高的介电常数和体积电阻率,可以有效地隔离器件之间的电流。
什么是氧化铝陶瓷基板 氧化铝陶瓷基板都有哪一些种类

什么是氧化铝陶瓷基板氧化铝陶瓷基板都有哪一些种类氧化铝陶瓷基板在很多行业发挥重要的作用,近几年的增长非常快,无论是高校、研发机构、还是产品终端企业都开启了陶瓷基板pcb的研发和生产。
氧化铝陶瓷基板是陶瓷基板的一种,导热性好、绝缘性、耐压性都很不错,因为受欢迎。
今天小编来分享一下:什么是氧化铝陶瓷基板以及氧化铝陶瓷基板都有哪些种类。
一,什么是氧化铝陶瓷基板氧化铝陶瓷基板核心成分是三氧化二铝陶瓷为主体的陶瓷材料,氧化铝陶瓷有较好的传导性、机械强度和耐高温性。
需要注意的是需用超声波进行洗涤。
氧化铝陶瓷基板是一种用途广泛的陶瓷基板,因为其优越的性能,在现代社会的应用已经越来越广泛,满足于日用和特殊性能行业领域的需要。
氧化铝陶瓷分为普通型、纯高型两种:普通型氧化铝陶瓷基板系按Al2O3含量不同分为99瓷、95瓷、90瓷、85瓷等品种,有时Al2O3含量在80%或75%者也划为普通氧化铝陶瓷系列。
其中99氧化铝瓷材料用于制作高温坩埚、耐火炉管及特殊耐磨材料,如陶瓷轴承、陶瓷密封件及水阀片等;95氧化铝瓷主要用作耐腐蚀、耐磨部件;85瓷中由于常掺入部分滑石,提高了电性能与机械强度,可与钼、铌、钽等金属封接,有的用作电真空装置器件高纯型氧化铝陶瓷基板系Al2O3含量在99.9%以上的陶瓷材料,由于其烧结温度高达1650—1990℃,透射波长为1~6μm,一般制成熔融玻璃以取代铂坩埚;利用其透光性及可耐碱金属腐蚀性用作钠灯管;在电子工业中可用作集成电路基板与高频绝缘材料。
氧化铝陶瓷基板导热率氧化铝陶瓷基板的导热率很高,一般在30W~50W 不等,板材厚度越薄,导热更好,板厚越厚则导热相对稍低。
但是整理的导热效果是普通PCB板的100倍甚至更多。
氧化铝陶瓷基板膨胀系数氧化铝陶瓷基板因为是陶瓷基材质,所属无机材料,硬度较大。
耐压,膨胀系数低,一般不易变形。
更多氧化铝陶瓷基板优势咨询金瑞欣特种电路。
二,氧化铝陶瓷基板的种类主要分为以下几类:1,薄膜氧化铝陶瓷基板一般采用是DPC薄膜工艺制作的三氧化二铝陶瓷基板,主要精密度较高,可以加工精密线路。
氧化铝陶瓷基板加工制作工艺流程和成型办法

氧化铝陶瓷基板是这样制成的!你知道多少?氧化铝陶瓷基板加工制作工艺流程和成型办法氧化铝陶瓷基板加工制作工艺流程和方法与普通的电路板是否一样?氧化铝陶瓷基板是这样制成的!你知道多少?相信关注氧化铝陶瓷基板的企业或者技术采购人员也是比较关注的。
今天小编全面分享一下这其中的“故事”。
一,氧化铝陶瓷基板加工工艺目前市面上采用的氧化铝陶瓷基板大多采用薄膜工艺、厚膜工艺,DBC工艺、HTCC 工艺和LTCC工艺。
氧化铝陶瓷基板薄膜工艺薄膜法是微电子制造中进行金属膜沉积的主要方法,其中直接镀铜(Direct plating copper)是最具代表性的。
直接镀铜(DPC),主要用蒸发、磁控溅射等面沉积工艺进行基板表面金属化,先是在真空条件下溅射钛,铬然后再是铜颗粒,最后电镀增厚,接着以普通pcb工艺完成线路制作,最后再以电镀/化学镀沉积方式增加线路的厚度。
DPC工艺适用于大部分陶瓷基板,金属的结晶性能好,平整度好,线路不易脱落,且线路位置更准确,线距更小,可靠性稳定等优点。
氧化铝陶瓷DBC工艺陶瓷覆铜板英文简称DBC,是由陶瓷基材、键合粘接层及导电层而构成,它是指铜箔在高温下直接键合到氧化铝或氮化铝陶瓷基片表面上的特殊工艺方法,其具有高导热特性,高的附着强度,优异的软钎焊性和优良电绝缘性能,但是无法过孔,精度差,表面粗糙,由于线宽,只能适用于间距大的地方,不能做精密的地方,并且只能成批生产无法实现小规模生产。
HTCC工艺就是采用的高温共烧工艺,HTCC陶瓷发热片就是高温共烧陶瓷发热片,是一以采用将其材料为钨、钼、钼\锰等高熔点金属发热电阻浆料按照发热电路设计的要求印刷于92~96%的氧化铝流延陶瓷生坯上,4~8%的烧结助剂然后多层叠合,在1500~1600℃下高温下共烧成一体,从而具有耐腐蚀、耐高温、寿命长、高效节能、温度均匀、导热性能良好、热补偿速度快等优点,而且不含铅、镉、汞、六价铬、多溴联苯、多溴二苯醚等有害物质,符合欧盟RoHS等环保要求。
氧化铝生产工艺流程课件-PPT

铝酸钠溶液诱导期
铝酸钠溶液的诱导期即过饱和铝酸钠溶液自发 分解析出氢氧化铝的时间长短。诱导期即是 在开头一段时间内溶液不发生明显的分解, 在此期间溶液主要是发生内部变化—离子聚 合或晶核开始形成。
诱导期的长短取决于溶液的组成(浓度、αK杂 质和温度)等因素。αK和浓度高以及有机物 等存在时,诱导期长。添加晶种时也有诱导 期,但诱导期的延续时间比不添加种子时工业上几乎全部采用碱法生产氧化铝。
酸法生产氧化铝
酸法生产氧化铝就是用硫酸、盐酸、硝酸等无机酸处 理铝矿石,得到含铝盐溶液,然后用碱中和这些盐溶 液,使铝成氢氧化铝析出,焙烧氢氧化铝或各种铝盐 的水合物晶体,便得到氧化铝。
用酸法处理铝矿石时,存在于矿石中的铁、钛、钒、 铬等杂质与酸作用进入溶液中,这不但引起酸的消耗, 而且它们与铝盐分离比较困难。氧化硅绝大部分成为 不溶物进入残渣与铝盐分离,但有少量成为硅胶进入 溶液,所以铝盐溶液还需要脱硅,而且需要昂贵的耐 酸设备。
铝土矿中的硅是碱法处理铝土矿制取氧化 在于溶液中。
精制粗液的设备目前在工业生产上大都采用叶滤机。 如果转速太慢,将降低窑的产能。
铝过程中最有害的杂质,铝土矿的铝硅 (1) 铝同氧的反应,生成Al2O3即:
拜耳法生产氧化铝的基本原理
比是衡量铝土矿质量的主要指标之一。 阴极碳块中的温度在很大程度上受阴极钢棒传热的影响,它是槽底部的一个重要散热通道,欲减少其散热量,应该加强所在部位的保
温能力。 目前,氧化铝厂熟料湿磨溶出使用的球磨机得比较多的有格子球磨机、溢流型球磨机、圆锥球磨机。
铝硅比是指铝土矿中的氧化铝和二氧化硅 (3)因不易产生过磨现象,溶出后赤泥为黑绿色,细度均匀适中,改善了赤泥沉降性能,提高了沉降槽的产能,同时可降低溶出过程
氧化铝基板制备方法(二)

氧化铝基板制备方法(二)
氧化铝基板制备方法
概述
氧化铝基板是一种常用的电子材料,具有优异的绝缘性能和热传导性能。
本文将介绍几种常见的氧化铝基板制备方法。
方法一:磨削法
1.将氧化铝材料切割成合适大小的块状;
2.使用研磨机械设备对氧化铝块进行磨削,使其表面光滑平整;
3.使用喷砂等方法去除氧化铝表面的杂质;
4.检查氧化铝基板的表面质量,确保其符合要求。
方法二:化学沉积法
1.准备铝源溶液和氧化铝基片;
2.将氧化铝基片放置在铝源溶液中,控制反应条件;
3.进行化学反应,使铝源溶液中的铝离子沉积在氧化铝基片表面;
4.洗涤和干燥氧化铝基片,以获得制备好的氧化铝基板。
方法三:热氧化法
1.准备氧化铝材料和高温炉设备;
2.将氧化铝材料放置在高温炉中,控制温度和气氛条件;
3.对氧化铝材料进行热氧化处理,使其表面形成致密的氧化铝层;
4.冷却、清洁和检查氧化铝基板的质量。
方法四:溶胶凝胶法
1.准备氧化铝溶胶和基片;
2.将氧化铝溶胶涂覆在基片表面;
3.进行凝胶化反应,使氧化铝溶胶形成均匀的凝胶层;
4.将凝胶层进行热处理,使其转变为致密的氧化铝基板。
方法五:电化学沉积法
1.准备电化学电解槽和氧化铝基片;
2.将氧化铝基片置于电解槽中,控制电解液和电流条件;
3.进行电解沉积反应,使氧化铝基片上的金属离子还原沉积成氧化
铝层;
4.清洗、干燥和检查氧化铝基板的质量。
以上是几种常见的氧化铝基板制备方法,每种方法都有其适用的场景和优缺点。
根据实际需求选择合适的制备方法,可以得到具备高质量和稳定性的氧化铝基板。
细晶氧化铝陶瓷基板的流延成型和显微结构控制研究

第42卷第9期2023年9月硅㊀酸㊀盐㊀通㊀报BULLETIN OF THE CHINESE CERAMIC SOCIETY Vol.42㊀No.9September,2023细晶氧化铝陶瓷基板的流延成型和显微结构控制研究邓佳威1,熊新锐1,徐协文1,刘㊀鹏1,杨现锋1,谢志鹏2(1.长沙理工大学材料科学与工程学院,长沙㊀410004;2.清华大学材料学院新型陶瓷与精细工艺国家重点实验室,北京㊀100083)摘要:采用砂磨工艺获得了亚微米氧化铝复合粉体,用于制备微晶氧化铝陶瓷基板,研究了浆料组成对浆料流变学性质㊁生坯密度㊁生坯应力-应变行为的影响,以及烧结制度对平均晶粒尺寸和基板抗弯强度的影响㊂结果表明,固相含量㊁R 值(增塑剂和黏结剂的质量比)和分散剂用量等关键因素决定了流延浆料的流变学性质㊂R 值增大导致生坯强度和密度降低,提高固相含量有利于增加最大可流延厚度,优化工艺条件下可制备0.16~1.20mm 的坯片㊂当烧结温度为1550ħ㊁升温速率为2.5ħ/min㊁保温时间为60min 时,制备的陶瓷基板平均晶粒尺寸为1.1μm 左右,晶粒尺寸分布均匀,抗弯强度达到(440ʃ25)MPa㊂关键词:氧化铝;陶瓷基板;流延成型;晶粒尺寸;烧结制度中图分类号:TQ174㊀㊀文献标志码:A ㊀㊀文章编号:1001-1625(2023)09-3306-09Tape Casting and Microstructure Controlling of Fine Grained Al 2O 3Ceramic SubstrateDENG Jiawei 1,XIONG Xinrui 1,XU Xiewen 1,LIU Peng 1,YANG Xianfeng 1,XIE Zhipeng 2(1.School of Materials Science and Engineering,Changsha University of Science &Technology,Changsha 410004,China;2.State Key Laboratory of New Ceramic and Fine Processing,School of Materials Science and Engineering,Tsinghua University,Beijing 100083,China)Abstract :The submicron Al 2O 3composite powder was obtained by sand milling process,which was used to prepare fine grained Al 2O 3ceramic substrates.The effect of slurry composition on rheological properties of slurry,bulk density and stress-strain behavior of green tape was investigated,and the influence of sintering schedule on average grain size and flexural strength of ceramic substrate was also studied.The results show that key factors such as solid content,R value (mass ratio of plasticizer to binder)and dispersant dosage determine the rheological properties of slurry.The increase of R value leads to the reduction of tensile strength and density of green tape,and the increase of solid content is beneficial to increase the possible maximum casting thickness.Under the optimized process conditions,0.16~1.20mm green sheets can be prepared.At a sintering temperature of 1550ħ,a heating rate of 2.5ħ/min and a holding time of 60min,the average grain size of the prepared ceramic substrate is about 1.1μm,the grain size distribution is uniform,and the flexural strengthreaches (440ʃ25)MPa.Key words :Al 2O 3;ceramic substrate;tape casting;grain size;sintering schedule 收稿日期:2023-05-11;修订日期:2023-05-29基金项目:国家自然科学基金(52172063);江西省重点研发计划(20232BBE50029)作者简介:邓佳威(1994 ),男,硕士研究生㊂主要从事工程陶瓷材料方面的研究㊂E-mail:180****6393@通信作者:杨现锋,博士,教授㊂E-mail:yangxfcsut@0㊀引㊀言氧化铝陶瓷具有原料来源丰富㊁价格低廉㊁绝缘性高㊁耐热冲击㊁抗化学腐蚀及机械强度高等优点,是一种综合性能优异的陶瓷基片材料,占陶瓷基片材料总量的80%以上㊂国内电子封装领域的氧化铝基板年需求量超过100万平方米㊂在功率器件㊁5G 通信㊁压力传感器等领域,高性能96(Al 2O 3质量分数约为96%)和第9期邓佳威等:细晶氧化铝陶瓷基板的流延成型和显微结构控制研究3307㊀99(Al 2O 3质量分数达到99%)氧化铝陶瓷基板得到了广泛应用㊂为适应器件高功率㊁高密度封装和长寿命的要求,氧化铝基板需要具备更高的热导率㊁抗弯强度㊁介电常数㊁可靠性以及更低的介质损耗[1-2]㊂陶瓷基板的流延成型主要采用有机流延浆料或水系流延浆料体系㊂有机流延浆料采用二元或三元共沸溶剂体系,具有挥发速度快㊁浆料稳定㊁坯体缺陷尺寸小以及与其他有机添加剂相容性好等优点,在氧化铝基板的工业化生产中得到广泛应用㊂但有机流延体系所用的有机溶剂对人体和环境有害,对尾气处理要求高,限制了其进一步应用㊂水系流延体系使用水代替有机溶剂,虽然克服了有机流延体系的环境危害问题,但是存在水与有机添加剂相容性较差的问题,流延浆料极易发生沉降,并且由于水中羟基含量较高,粉体团聚现象明显㊂此外,由于水的挥发速度较慢,干燥过程中容易发生干裂和翘曲现象[3-4]㊂细晶化是提高氧化铝基板性能的主要途径,细晶氧化铝陶瓷的显微结构更均匀,机械性能和可靠性显著提升[5-6]㊂氧化铝粉体的颗粒大小和粒度分布是影响氧化铝陶瓷显微结构的首要因素,粒度分布窄的亚微米氧化铝粉体有利于制备细晶氧化铝陶瓷[7-8]㊂此外,采用纳米级的烧结助剂或者采用新型的烧结助剂也是降低烧结温度和控制氧化铝晶粒尺寸的主要途径[9-10]㊂影响氧化铝陶瓷晶粒大小的另外一个决定性因素是烧结制度,研究者一般采用低温烧结或者二步烧结㊁放电等离子体烧结㊁震荡压力烧结等特种烧结技术来抑制氧化铝晶粒长大,从而获得细晶结构[11-15]㊂然而,这些研究主要关注单一影响因素对氧化铝陶瓷显微结构的影响,而高性能细晶氧化铝陶瓷基板的制备需要建立粉体特征㊁浆料流变学性质㊁烧结制度和力学性能之间的关联㊂本文采用砂磨+喷雾干燥工艺,获得粒度分布集中的亚微米氧化铝粉体并使助烧剂均匀分散,然后研究了有机溶剂组成对浆料流变学性质和成型性能的影响;重点通过优化烧结制度获得微晶化显微结构并分析了烧结制度对基片抗弯强度的影响,采用透射电子显微镜分析了烧结助剂的分布与存在形式,旨在为高性能氧化铝陶瓷基板的材料设计和工艺优化提供参考㊂1㊀实㊀验1.1㊀原㊀料采用Alteo 公司的氧化铝粉体(P662LSB),D 50为3.4μm㊂流延成型采用有机溶剂体系,包括无水乙醇(国药集团药业股份有限公司)㊁乙酸乙酯(国药集团药业股份有限公司)和乙酸丁酯(国药集团药业股份有限公司)㊂有机黏结剂采用聚乙烯醇缩丁醛(PVB,国药集团药业股份有限公司)㊂增塑剂采用邻苯二甲酸二丁酯(DBP,国药集团药业股份有限公司)㊂烧结助剂为CaCO 3(上海亮江钛白化工制品有限公司,D 50为300nm)㊁纳米SiO 2(江苏天行新材料有限公司,D 50为60nm)㊁纳米MgO(宣城晶瑞新材料有限公司,D 50为100nm)㊂分散剂为蓖麻油(CHO)和三油酸甘油酯(GTO)㊂按照Al 2O 396%+CaO 1%+MgO 1%+SiO 22%的质量比在砂磨机(长沙西丽纳米研磨科技有限公司,XL-1L,0.8mm 锆球,转速1200r /min)中研磨40min,得到的浆料通过喷雾干燥制得原料粉体㊂氧化铝粉体和砂磨后粉体的粒度分布㊁颗粒形貌分别如图1㊁2所示㊂砂磨后,原料粉体的D 50为0.8μm㊂图1㊀砂磨处理前后粉体的粒度分布曲线Fig.1㊀Particle size distribution of powder before and after sand milling3308㊀陶㊀瓷硅酸盐通报㊀㊀㊀㊀㊀㊀第42卷图2㊀砂磨处理前后粉体的SEM照片Fig.2㊀SEM images of powder before and after sand milling1.2㊀试验过程将原料粉体和溶剂在行星球磨机中混合120min,转速为600r/min,然后加入黏结剂和增塑剂继续混合120min,转速为600r/min,最后将转速降至300r/min混合30min得到流延成型用的浆料㊂得到的浆料在真空除泡机(TPJ,北京东方泰阳科技有限公司)上除泡,除泡后在流延成型机(LYJ-253-3,北京东方泰阳科技有限公司)上流延得到生坯片㊂将生坯片裁剪后放入排胶炉中排胶,然后在马弗炉中进行常压烧结㊂排胶制度为:在0~200ħ以0.5ħ/min的速率升温,在200~600ħ以1ħ/min的速率升温,达到600ħ后保温120min㊂1.3㊀测试与表征采用排水法测试材料的体积密度㊂采用电脑式伺服拉压力试验机(PT-1176,东莞市宝大仪器有限公司)测试流延生坯片(13mmˑ1.4mmˑ2.0mm)的拉伸强度和应力-应变曲线㊂切割烧结后的基片,得到13mmˑ1.0mmˑ2.0mm的样品,测试基片材料的三点抗弯强度㊂采用旋转流变仪(DHR-2,TA,美国)测试浆料的流变学性质㊂对陶瓷基本表面进行抛光研磨后,在马弗炉中进行热腐蚀处理(1200ħˑ0.5h),然后使用场发射扫描电子显微镜(Hitachi,S4800,日本)观察晶粒形貌并采用ImageproPlus软件统计测量晶粒平均尺寸㊂采用透射电子显微镜(Tecnai,F30,日本)分析表征晶界结构和助烧剂元素的分布状况㊂2㊀结果与讨论2.1㊀浆料组成对浆料流变学性质的影响浆料黏度是陶瓷粉体-液相分散体系内部复杂相互作用的综合反映,是影响流延坯片质量的重要参数㊂本文研究了固相含量㊁R值和分散剂含量对浆料黏度的影响,剪切黏度随剪切速率的变化曲线如图3所示㊂流延成型过程中,剪切速率可以通过膜带速率和刀口高度之比进行估算㊂对于本研究制备的浆料,当剪切速率在1~3s-1时,表观黏度-剪切速率曲线陡峭,剪切速率轻微变化就会导致黏度剧烈变化,对流延过程产生不利影响㊂固相含量是影响流延浆料黏度的首要因素㊂由图3(a)可知,当固相含量由26%(体积分数)增大到28%时,浆料黏度显著增大㊂图3(b)为不同R值时剪切黏度随剪切速率的变化㊂由图可知,随着R值增大,浆料黏度显著降低㊂这是因为增塑剂小分子插入黏结剂聚乙烯醇缩丁醛(PVB)高分子链之间,增加了长链的距离,起到了润滑作用从而降低了黏度㊂图3(c)分别采用了蓖麻油(CHO)㊁三油酸甘油酯(GTO)和CHO与GTO的混合分散剂(质量比1ʒ1),考察了不同分散剂对浆料流变学性质的影响,可以发现GTO的引入可以显著降低浆料的黏度㊂但当单独采用GTO时,由于GTO的引入量较高,GTO在润湿粉体表面的同时,显著减弱了粉体颗粒之间的粘合力,导致生坯容易出现开裂缺陷㊂因此本研究采用GTO和CHO复合分散剂[16]㊂2.2㊀坯片流延成型本研究接着探讨了R值对流延生坯拉伸强度㊁体积密度和应力-应变行为的影响,结果如图4所示㊂由图4(a)可知,随着R值增大,生坯片的拉伸强度呈下降趋势,这是由于在黏结剂和增塑剂总量不变的情况第9期邓佳威等:细晶氧化铝陶瓷基板的流延成型和显微结构控制研究3309㊀下,R 值增大意味着黏结剂PVB 降低,而黏结剂PVB 是生坯强度的主要决定因素㊂此外,R 值增大,生坯片的密度也明显下降,这是因为增塑剂DBP 的密度低于黏结剂PVB,添加总质量不变的情况下,R 值增大,增塑剂和黏结剂的体积增加,生坯片的密度下降㊂图4(b)为各R 值下坯片的应力-应变曲线㊂结果表明R 值为60时,生坯片可以承受更大的应变而不断裂,展现了更好的柔韧性㊂图3㊀浆料组成对流变学行为的影响Fig.3㊀Influence of suspension composition on rheologybehavior 图4㊀R 值对生坯性能的影响Fig.4㊀Influence of R value on properties of greentape 图5㊀不同固相含量浆料的最大流延厚度及干燥收缩Fig.5㊀Maximum tape thickness and drying shrinkage of suspension with different solid content 在基片的流延成型中,一般通过调节浆料的黏度来满足不同厚度基片的制备㊂本文对比研究了不同固相含量能够流延成型的最大基片厚度及其对应的干燥收缩,结果如图5所示㊂随着固相含量的增加,浆料黏度增加,可以成型的基片最大厚度变大㊂当固相含量为22%时,最大厚度约为0.6mm,对应收缩率接近75%;固相含量为28%时,可以制备得到完好的基片生坯,其厚度约为1.4mm,对应收缩率约为55%㊂以流延刀口高度2.5mm 为例,不同固相含量流片坯片外观如图6所示㊂当固相含量较低(22%和24%)时,由于浆料黏度较低,无法保持较厚液膜的稳定摊平,液膜厚度不一致㊂另外溶剂含量高,干燥收缩大,会导致干燥后的坯片出现开裂㊂当固相含量为30%时,浆料黏度过高,无法完成流延㊂对于固相含量3310㊀陶㊀瓷硅酸盐通报㊀㊀㊀㊀㊀㊀第42卷26%和28%的浆料,黏度适中,可以得到外观质量好㊁无明显缺陷的坯片㊂但是,高黏度浆料中容易裹挟气泡,干燥过程中可能导致坯片表面出现针孔,需要通过添加消泡剂或者改善球磨和除泡工艺以消除此类缺陷㊂图7所示为优化工艺条件下得到的0.16~1.20mm 生坯片㊂图6㊀不同固相含量浆料的坯片照片(刀口厚度2.5mm)Fig.6㊀Green blank made from suspension with different solid content (blade height:2.5mm)图7㊀不同厚度的生坯片Fig.7㊀Green blank with different thickness 2.3㊀烧结制度对基板显微结构和抗弯强度的影响氧化铝陶瓷基板的致密度㊁晶粒尺寸及均匀性直接影响基板的强度㊁韧性和可靠性㊂烧结过程中氧化铝晶粒的生长对温度非常敏感,易快速生长或各向异性生长㊂本文研究了烧结温度㊁保温时间和升温速率三个关键因素对氧化铝陶瓷基板显微结构的影响㊂图8为不同烧结温度下的基板的断片显微结构及晶粒尺寸分布统计㊂当烧结温度为1530和1550ħ㊁保温时间为60min㊁升温速率为2ħ/min 时,平均晶粒尺寸约1.1μm,晶粒尺寸分布均匀㊂当烧结温度为1570ħ时,出现了明显的异常长大,平均晶粒尺寸超过3.4μm㊂烧结基板的体积密度测试结果表明,当烧结温度为1530ħ时,基片的密度为95%,烧结温度为1550ħ时,相对密度达到98%㊂因此,选择烧结温度为1550ħ,分别研究保温时间和升温速率对基片显微结构的影响㊂图9为不同保温时间和升温速率下的断面SEM 照片及晶粒尺寸分布㊂由图9(a)㊁(b)可知,延长保温时间会明显导致晶粒长大和晶粒尺寸分布不均匀㊂当保温时间为120min 时,平均晶粒尺寸超过3μm㊂由图9(c)可知,当升温速率降低至1ħ/min 时,平均晶粒尺寸增大到3.39μm㊂因此,降低升温速率也不利于抑制氧化铝晶粒的长大㊂助烧剂在氧化铝陶瓷的烧结过程中扮演着重要角色,本文采用透射电子显微镜表征了晶界结构和助烧剂元素的分布状态,如图10所示㊂由图10(a)可知,两个氧化铝晶粒之间的相邻晶界和三角晶界处存在非结晶的玻璃相区域㊂图10(b)所示区域的元素分布如图10(c)~(f)所示㊂对比发现,Ca 和Mg 元素主要富集在三角晶界处形成玻璃相㊂Mg 元素均匀分布在样品中,没有参与玻璃相的形成㊂图10(f)中显示的ZrO 2颗粒由砂磨介质磨损引入,ZrO 2颗粒的引入能够起到应力诱导相变增韧的效果㊂图11所示为烧结制度对基板抗弯强度的影响㊂对比分析可知,抗弯强度的变化与晶粒平均尺寸的变化规律呈明显的相关性,平均晶粒细小的基板对应较高的抗弯强度㊂在烧结温度为1550ħ㊁升温速率为第9期邓佳威等:细晶氧化铝陶瓷基板的流延成型和显微结构控制研究3311㊀2ħ/min㊁保温时间为60min 时,抗弯强度达到(440ʃ25)MPa,达到同类产品的先进水平㊂图12为该条件下制备的80mm ˑ80mm ˑ1.0mm 陶瓷基板,外观平整,无明显翘曲和变形㊂图8㊀不同温度下烧结基板的断面SEM 照片和晶粒尺寸分布Fig.8㊀SEM images and grain size distribution of fracture surface of substrate sintered at differenttemperatures3312㊀陶㊀瓷硅酸盐通报㊀㊀㊀㊀㊀㊀第42卷图9㊀不同保温时间和升温速率下烧结基板的断面SEM 照片和晶粒尺寸分布Fig.9㊀SEM images and grain size distribution of fracture surface of substrate sintered at different holding time and heatingrate 图10㊀氧化铝基板晶界区域结构的TEM 照片和断面元素分布Fig.10㊀TEM images and element distribution of grain boundary structure in Al 2O 3substrate第9期邓佳威等:细晶氧化铝陶瓷基板的流延成型和显微结构控制研究3313㊀图11㊀烧结温度㊁保温时间和升温速率对陶瓷基板抗弯强度的影响Fig.11㊀Influences of sintering temperature,holding time and heating rate on flexural strength of ceramicsubstrate 图12㊀氧化铝陶瓷基板照片(80mm ˑ80mm ˑ1.0mm)Fig.12㊀Image of Al 2O 3ceramic substrate (80mm ˑ80mm ˑ1.0mm)3㊀结㊀论1)采用砂磨方法制备得到的亚微米复合粉体D 50为0.8μm,采用PVB 作为黏结剂,DBP 作为增塑剂,GTO 和CHO 作为复合分散剂,制备了最高固相体积分数为28%的适合流延成型的浆料,通过优化工艺制备了0.16~1.20mm 的坯片㊂R 值增大导致生坯强度和密度降低,合适的R 值为60㊂2)烧结基板的平均晶粒尺寸与烧结温度㊁保温时间和升温速率等参数紧密相关㊂在烧结温度为1550ħ㊁升温速率为2ħ/min㊁保温时间为60min 时,制备的陶瓷基板平均晶粒尺寸在1.1μm 左右,晶粒尺寸分布均匀,抗弯强度达到(440ʃ25)MPa㊂参考文献[1]㊀MA M,WANG Y,NAVARRO-CÍA M,et al.The dielectric properties of some ceramic substrate materials at terahertz frequencies[J].Journalof the European Ceramic Society,2019,39(14):4424-4428.[2]㊀VALDEZ-NAVA Z,KENFAUI D,LOCATELLI M L,et al.Ceramic substrates for high voltage power electronics:past,present and future[C]//2019IEEE International Workshop on Integrated Power Packaging (IWIPP),Toulouse,France,2019.[3]㊀KRISHNAN P P R,VIJAYAN S,WILSON P,et al.Aqueous tape casting of alumina using natural rubber latex binder [J ].CeramicsInternational,2019,45(15):18543-18550.[4]㊀吕子彬,海㊀韵,吕金玉,等.陶瓷基片流延成型用浆料研究进展[J].武汉理工大学学报,2021,43(6):7-14.LYU Z B,HAI Y,LYU J Y,et al.Research of slurry in ceramic substrate casting[J].Journal of Wuhan University of Technology,2021,43(6):7-14(in Chinese).[5]㊀KAMBALE K R,MAHAJAN A,BUTEE S P.Effect of grain size on the properties of ceramics[J].Metal Powder Report,2019,73(3):130-136.[6]㊀TENG X,LIU H,HUANG C.Effect of Al 2O 3particle size on the mechanical properties of alumina-based ceramics[J].Materials Science &3314㊀陶㊀瓷硅酸盐通报㊀㊀㊀㊀㊀㊀第42卷Engineering A,2007,452(5):545-551.[7]㊀LEE H M,HUANG C Y,WANG C J.Forming and sintering behaviors of commercialα-Al2O3powders with different particle size distribution andagglomeration[J].Journal of Materials Processing Tech,2009,209(2):714-722.[8]㊀李建忠,张㊀勇,徐大余.氧化铝粉体性能对流延法生产陶瓷基板的影响[J].硅酸盐通报,2011,30(2):345-347+366.LI J Z,ZHANG Y,XU D Y.Influence of alumina raw materials on ceramic slices fabricated by tape casting[J].Bulletin of the Chinese Ceramic Society,2011,30(2):345-347+366(in Chinese).[9]㊀KZAB C,RHA B,GDAB C,et al.Effects of fine grains and sintering additives on stereolithography additive manufactured Al2O3ceramic[J].Ceramics International,2020,47(2):2303-2310.[10]㊀YANG Y,MA M,ZHANG F,et al.Low-temperature sintering of Al2O3ceramics doped with4CuO-TiO2-2Nb2O5composite oxide sintering aid[J].Journal of the European Ceramic Society,2020,40(15):5504-5510.[11]㊀KATARÍNA B A,B D G,PETER V B,et al.Grain growth suppression in alumina via doping and two-step sintering[J].CeramicsInternational,2015,41(9):11975-11983.[12]㊀GAO L,HONG J S,MIYAMOTO H,et al.Bending strength and microstructure of Al2O3ceramics densified by spark plasma sintering[J].Journal of the European Ceramic Society,2000,20(12):2149-2152.[13]㊀HAN Y,LI S,ZHU T,et al.Enhanced properties of pure alumina ceramics by oscillatory pressure sintering[J].Ceramics International,2017,44(5):5238-5241.[14]㊀LI J,YE Y,LI J,et al.Densification and grain growth of Al2O3nanoceramics during pressure less sintering[J].Journal of the AmericanCeramic Society,2010,89(1):139-143.[15]㊀侯清健,游㊀韬,王子鸣,等.烧结升温速率对低温共烧陶瓷基板性能的影响[J].硅酸盐通报,2022,41(3):1039-1043.HOU Q J,YOU T,WANG Z M,et al.Effect of sintering heating rate on properties of low temperature co-fired ceramic substrate[J].Bulletin of the Chinese Ceramic Society,2022,41(3):1039-1043(in Chinese).[16]㊀吕子彬,郭恩霞,海㊀韵,等.分散剂对低温共烧陶瓷流延浆料流变性能的影响[J].硅酸盐通报,2022,41(11):3979-3989.LYU Z B,GUO E X,HAI Y,et al.Effects of dispersants on rheological properties of LTCC casting slurry[J].Bulletin of the Chinese Ceramic Society,2022,41(11):3979-3989(in Chinese).。
氧化铝加工方法

氧化铝加工方法
氧化铝可是个厉害的东西呢!它在我们生活中的很多领域都有着重要的作用。
那氧化铝是怎么加工的呢?首先要进行原料的准备呀,选择高质量的铝矿石。
然后就是一系列的加工步骤啦!比如破碎、研磨,把铝矿石弄成细小的颗粒,就像把一个大西瓜切成好多小块一样。
接着进行高温煅烧,这可不能马虎,温度和时间都要控制好,不然可就达不到理想的效果啦!在这个过程中要特别注意安全,不能让温度过高导致危险呀,就像开车不能超速一样。
同时,设备的维护也很重要,要保证一切都正常运转,不然出了问题可就麻烦啦!
在氧化铝加工过程中,安全性和稳定性那是至关重要的呀!稍有不慎可能就会引发大问题呢。
所以各种安全措施一定要做到位,工作人员也要时刻保持警惕。
就好像走钢丝一样,必须小心翼翼,才能确保万无一失。
而稳定性就像是建房子的根基,只有根基牢固了,房子才能稳稳当当的呀。
氧化铝的应用场景那可多了去啦!在陶瓷、电子、化工等好多行业都能看到它的身影呢。
它的优势也很明显呀,比如硬度高、耐高温、耐腐蚀。
这不就像一个全能战士吗?哪里需要就去哪里,而且还能出色地完成任务。
就拿陶瓷行业来说吧,加入氧化铝后的陶瓷制品那质量可真是杠杠的!更加坚固耐用,美观度也提高了不少呢。
这就好比给陶瓷穿上了一件坚固的铠甲,变得更厉害了呀!
氧化铝加工真的是一项非常重要的工艺呀!它为我们的生活带来了这么多的好处和便利,我们可一定要好好珍惜和利用呢!让我们一起为氧化铝加工点赞吧!。
氧化铝基板烧结工艺

氧化铝基板烧结工艺氧化铝基板烧结工艺是一种常用的制备氧化铝陶瓷材料的方法。
氧化铝陶瓷具有优良的绝缘性能、高熔点和耐高温性能,因此在电子、机械、航空航天等领域有着广泛的应用。
本文将介绍氧化铝基板烧结工艺的基本原理、工艺流程和影响烧结效果的因素。
1. 基本原理氧化铝基板烧结工艺是通过将氧化铝粉末经过一系列的处理和烧结过程,使其形成致密的结构。
烧结过程中,氧化铝粉末颗粒之间发生相互结合,形成颗粒间的颈部,最终形成致密的结构。
这种致密的结构使得氧化铝陶瓷具有优良的物理性能。
2. 工艺流程氧化铝基板烧结工艺一般包括以下步骤:(1)原料准备:选择高纯度的氧化铝粉末作为原料,并根据需求进行筛分和研磨处理,以获得均匀的颗粒粒径分布。
(2)浆料制备:将经过处理的氧化铝粉末与有机添加剂和溶剂混合,形成均匀的浆料。
添加剂的选择和控制可以影响烧结过程中的颗粒结合和致密度形成。
(3)浇注成型:将浆料倒入模具中,通过振动和压实等方式排除气泡,形成所需形状的绿胚。
(4)干燥:将绿胚进行适当的干燥处理,以去除浆料中的溶剂。
(5)烧结:将干燥后的绿胚置于高温炉中进行烧结。
烧结温度一般在1600~1800摄氏度之间,时间根据烧结效果的要求确定。
(6)表面处理:经过烧结后的氧化铝基板可以进行表面处理,如抛光、切割等操作。
3. 影响烧结效果的因素氧化铝基板烧结工艺的效果受多种因素的影响,主要包括原料性质、添加剂、烧结温度和时间等。
(1)原料性质:原料的纯度、颗粒大小和形状会影响烧结过程中的颗粒结合情况和致密度形成。
高纯度的氧化铝粉末可以提高烧结体的致密性和机械性能。
(2)添加剂:添加剂的选择和控制可以影响烧结过程中的颗粒结合和致密度形成。
常用的添加剂包括结合剂、增稠剂和抗烧结助剂等。
(3)烧结温度和时间:烧结温度和时间是决定烧结效果的重要参数。
过低的温度和时间会导致烧结不完全,致使陶瓷材料的致密性和力学性能不佳;过高的温度和时间则容易引起颗粒过度生长和晶粒长大,影响材料的细晶化效果。
陶瓷基板dbc工艺

陶瓷基板dbc工艺陶瓷基板DBC工艺随着电子技术的不断发展,陶瓷基板DBC工艺在高功率电子器件中的应用越来越广泛。
DBC工艺是一种将散热基板与电路层无缝结合的技术,它具有良好的导热性能和电气性能,因此被广泛应用于功率电子器件的制造中。
DBC是Direct Bonded Copper的缩写,即直接键合铜。
它通过高温和高压的工艺将导电层(一般是铜)与陶瓷基底(一般是氧化铝陶瓷)直接结合在一起。
这种直接结合的方式使得导热性能更好,电流传导能力更强,而且还能提高器件的可靠性。
DBC工艺的制备过程主要包括以下几个步骤:1.基板准备:选择合适的陶瓷材料作为基底,常用的有氧化铝陶瓷。
然后对基底进行加工,如切割、打磨等,以得到所需的形状和尺寸。
2.导电层制备:选择合适的金属材料作为导电层,常用的有铜。
将导电层加工成所需的形状和尺寸,然后进行表面清洁处理,以提高与陶瓷基底的结合强度。
3.直接键合:将陶瓷基底和导电层分别放置在热压机的加热板上,经过一定的温度和压力条件下进行加热和压制,使其直接结合在一起。
在这个过程中,金属层的表面氧化层与陶瓷基底的氧化层发生反应,形成化学键合,从而实现了金属层与陶瓷基底的无缝结合。
4.加工和测试:经过直接键合后的基板需要进行精密加工,如切割、钻孔等,以便制成所需的形状和尺寸。
然后对制成品进行电气测试和可靠性测试,以保证其质量和性能符合要求。
DBC工艺具有以下几个优点:1.导热性能好:直接键合的导电层与陶瓷基底之间没有界面接触电阻,导热性能更好,能够有效地散热,提高器件的功率密度。
2.电气性能优越:直接键合的金属层与陶瓷基底之间的结合强度高,电流传导能力强,能够承受高电流和高电压的工作环境。
3.尺寸稳定性好:直接键合的金属层与陶瓷基底之间的热膨胀系数相似,能够有效地抑制因温度变化引起的热应力,保持器件的尺寸稳定性。
4.可靠性高:直接键合的金属层与陶瓷基底之间形成了化学键合,结合强度高,能够承受高温和高湿等恶劣工作环境,提高器件的可靠性。