黄铜焊接管焊裂原因的分析
焊黄铜的技巧

焊黄铜的技巧
焊黄铜的技巧有以下几点:
1. 清洁表面:在焊接之前,必须确保黄铜表面是干净的,没有任何污垢、油脂和氧化物。
可以使用刚性刷子、砂纸或溶剂清洁表面。
2. 预热:黄铜是一种导热性较好的金属,所以在焊接之前需要进行预热。
通常可以使用火焰喷灯或专用的预热设备将焊接区域加热到适当温度(一般在300C 至400C之间)。
3. 选择合适的焊条:黄铜焊接时一般使用黄铜焊条或银焊条。
不同的焊接任务可能需要不同种类的焊条,所以选择合适的焊条非常重要。
4. 使用适当的焊接技术:常用的黄铜焊接技术包括气焊、TIG焊、MIG焊和电阻焊等。
选择合适的焊接技术取决于焊接任务的要求和操作者的经验。
5. 控制焊接温度:黄铜的熔点较低,所以在焊接时要注意控制焊接温度,避免过热导致黄铜熔化或产生裂纹。
6. 使用适当的焊接电源:根据焊接任务的要求,选择合适的焊接电源,确保能提供足够的电流和电压。
7. 使用适当的焊接设备和工具:使用高质量的焊接设备和工具,确保焊接过程的稳定和安全。
8. 注意保护自己:焊接过程中会产生高温和火花,所以要注意佩戴适当的个人防护装备,如焊接手套、面罩和护目镜。
请注意,焊接是一项需要一定技术和经验的操作,如果没有足够的经验和知识,建议找专业人士进行焊接。
压力管道焊接接头裂纹原因分析

压力管道焊接接头裂纹原因分析摘要:在工业生产中,一些企业会用到锅炉压力容器设备,由于该设备运转环境较为特殊,所以易产生各类运行问题。
做好压力管道检验十分重要,在检验过程中,裂纹是一种常见问题,也是较为严重的问题[1]。
因此,在检验中如何快速地找出裂纹,采取措施解决管道裂纹问题非常有必要,这对于设备机组稳定运行至关重要。
关键词:压力管道;焊接;裂纹1 锅炉压力容器压力管道检验中裂纹的问题1.1 蠕变裂纹由于长期受到高温影响以及应力粘合作用,压力管道容易出现蠕变开裂现象,导致管道金属结构出现损坏,管道部分区域出现变形问题,降低了压力管道的安全性。
通常情况下,蠕变开裂多发生于集管热影响区、高温蒸汽管、加热膨胀管等区域[2]。
蠕变开裂特征十分明显,裂纹方向大多都是与最大拉应力垂直,裂纹的走势通常为曲折形式,出现裂纹的区域面积较大,而且各条裂纹大多以平行排列的方式排列,主裂纹位置大多在裂纹中部区域内。
蠕变问题还有一些细微的特征,例如蠕变孔,在裂纹区域会分布一些不规则的小孔,裂纹孔形状普遍为椭圆形。
此外,裂纹在焊缝受损区域排列较为特殊,大多与焊缝方向平行分布,裂纹会顺着焊缝表面延伸至焊缝内容,主裂纹两侧的平行微裂纹则会沿晶粒进行分布,向着主裂纹的边界进行扩展,形成裂纹区。
1.2 焊接裂缝现阶段我国使用的锅炉压力容器压力管道大多由金属板焊接而成,所以锅炉承压设备在受到压力作用后焊接裂缝容易出现裂纹现象,裂纹产生的影响因素多集中于高温环境下管道结构强度降低,受到压力后出现热裂纹现象[3]。
通常情况下,在制造锅炉后,需要将锅炉静置冷却,才可以投入使用,所以在制造锅炉时,也会带来冷裂纹问题,从而影响到锅炉运转的安全性。
由于焊接时氢元素会与金相组织接触,所以在焊接冷却时,奥氏体慢慢转变为铁元素,此时管道结构中的氢元素逐渐向着中部靠拢,在焊接冷却过程中形成氢裂纹。
1.3 应力腐蚀裂纹管道在受到应力作用下,或者接触到腐蚀质时,也会出现裂纹现象。
焊接裂纹的产生原因及防止措施
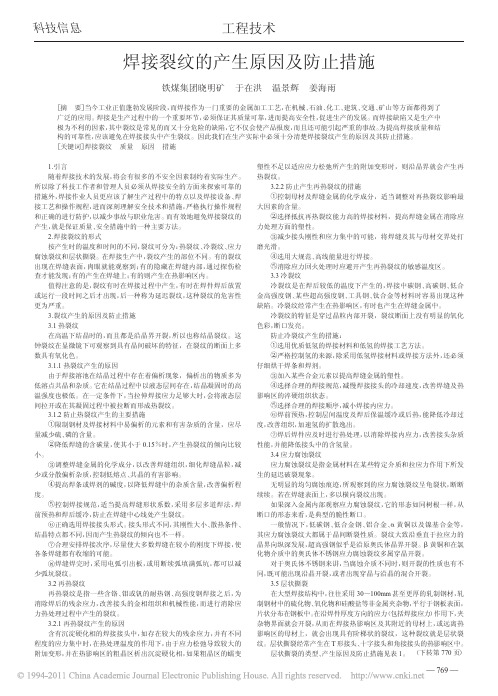
车载式颠簸累积仪等,各种测定平整度的方法均有不同的特点,并适用
于不同的场合。 1、影响农村公路路面平整度的主要因素 导致农村公路路面平整度差的原因是多方面的,主要由以下几个
原因造成。 1.1 基层顶面平整度较差 基层顶面平整度不好,将直接影响到沥青路面的平整度。由于沥青
(2)碾压方法 在碾压过程中可遵循以下规则:由低度向高处(横坡)碾压,先静止
后振动碾压;碾压时驱动轮在前,从动轮在后;后退时沿前进碾压的轮
迹行驶;压路机折返的平面位置不在同一断面上,而是呈阶梯形等。 (3)碾压控制压实度 沥青面层压实度越高,使用过程中平整度变化越小,因此切不可为
用制动而增加摊铺机的阻力。 (5)合理选择自动找平方式。一般底面层利用基准钢丝绳来确保高
程控制,中、上面层利用浮动基准梁(平衡梁)来达到较好的平整度。 2.5 碾压控制 (1)碾压温度 沥青混合料在限定的范围内温度越高,其可塑性越大,越容易在外
力作用下缩小其空隙率和增加其密实度,越容易获得平整效果。因此, 复压和终压温度必须严格地控制。
塑性不足以适应应力松弛所产生的附加变形时,则沿晶界就会产生再 热裂纹。
3.2.2 防止产生再热裂纹的措施 ①控制母材及焊缝金属的化学成分,适当调整对再热裂纹影响最 大因素的含量。 ②选择抵抗再热裂纹能力高的焊接材料,提高焊缝金属在消除应 力处理方面的塑性。 ③减少接头刚性和应力集中的可能,将焊缝及其与母材交界处打 磨光滑。 ④选用大规范、高线能量进行焊接。 ⑤消除应力回火处理时应避开产生再热裂纹的敏感温度区。 3.3 冷裂纹 冷裂纹是在焊后较低的温度下产生的,焊接中碳钢、高碳钢、低合 金高强度钢、某些超高强度钢、工具钢、钛合金等材料时容易出现这种 缺陷。冷裂纹经常产生在热影响区,有时也产生在焊缝金属中。 冷裂纹的特征是穿过晶粒内部开裂,裂纹断面上没有明显的氧化 色彩,断口发亮。 防止冷裂纹产生的措施: ①选用优质低氢的焊接材料和低氢的焊接工艺方法。 ②严格控制氢的来源,除采用低氢焊接材料或焊接方法外,还必须 仔细烘干焊条和焊剂。 ③加入某些合金元素以提高焊缝金属的塑性。 ④选择合理的焊接规范,减慢焊接接头的冷却速度,改善焊缝及热 影响区的淬硬组织状态。 ⑤选择合理的焊接顺序,减小焊接内应力。 ⑥焊前预热,控制层间温度及焊后保温缓冷或后热,能降低冷却过 度,改善组织,加速氢的扩散逸出。 ⑦焊后焊件应及时进行热处理,以消除焊接内应力,改善接头杂质 性能,并能降低接头中的含氢量。 3.4 应力腐蚀裂纹 应力腐蚀裂纹是指金属材料在某些特定介质和拉应力作用下所发 生的延迟破裂现象。 无明显的均匀腐蚀痕迹,所观察到的应力腐蚀裂纹呈龟裂状,断断 续续。若在焊缝表面上,多以横向裂纹出现。 如果深入金属内部观察应力腐蚀裂纹,它的形态如同树根一样,从 断口的形态来看,是典型的脆性断口。 一般情况下,低碳钢、低合金钢、铝合金、α 黄铜以及镍基合金等, 其应力腐蚀裂纹大都属于晶间断裂性质。裂纹大致沿垂直于拉应力的 晶界向纵深发展,超高强钢似乎是沿原奥氏体晶界开裂。β 黄铜和在氯 化物介质中的奥氏体不锈钢应力腐蚀裂纹多属穿晶开裂。 对于奥氏体不锈钢来讲,当腐蚀介质不同时,则开裂的性质也有不 同,既可能出现沿晶开裂,或者出现穿晶与沿晶的混合开裂。 3.5 层状撕裂 在大型焊接结构中,往往采用 30~100mm 甚至更厚的轧制钢材,轧 制钢材中的硫化物、氧化物和硅酸盐等非金属夹杂物,平行于钢板表面, 片状分布在钢板中。在沿焊件厚度方向的应力(包括焊接应力)作用下,夹 杂物界面就会开裂,从而在焊接热影响区及其附近的母材上,或远离热 影响区的母材上,就会出现具有阶梯状的裂纹,这种裂纹就是层状裂 纹。层状撕裂经常产生在 T 形接头、十字接头和角接接头的热影响区中。 层状撕裂的类型、产生原因及防止措施见表 1。 (下转第 770 页)
压力管道焊接接头裂纹原因分析

压力管道焊接接头裂纹原因分析摘要:近年来,随着我国工业的快速发展,压力管道的数量和种类快速增长,其潜在的安全隐患与日俱增。
如何对压力管道实行高效地检验,从而减少安全隐患,保障管道的安全运行显得格外重要。
裂纹是压力管道最容易产生同时也是最具危害性的缺陷,它的产生将显著减少承载面积,裂纹的端部形成尖锐的缺口,造成应力高度集中,裂纹扩展到一定程度可造成材料断裂,从而导致安全事故的发生。
基于此,对压力管道焊接接头裂纹原因进行研究,仅供参考。
关键词:压力管道;焊接;接头;裂纹原因1压力管道焊接中的问题1.1焊接压力管道的打底层对打底层进行焊接,是焊接过程中最关键的一个环节,正常条件下,具体操作过程中经常使用氢弧焊来打底,一般试焊之后才能进行下一步,因为只有在氢气质量符合条件,且配备足够的情况下才能保证焊接的质量达标,另外在正常焊接期间还要留意周围的环境,以防对焊接造成损害,并且要随时查看焊接的效果,避免产生裂缝。
由于重力的作用,常常会使焊缝的下端发生顶板向里面凹陷的情况,为了防止这一情况的发生,最好能用角磨机把接头的地方磨一下。
还有在正常焊接期间,常常采用短弧焊轮流焊接,先于左边实施起弧操作,一旦坡口融合在一起,就可以进行灭弧,然后右边进行相同的操作,但左右的熔孔尺寸要接近2mm,不能有太大的区别,并且焊条的斜度要保证前后一致。
1.2分析管道材质,选择最合适的焊接工艺评定由于一种管道对应着一种焊接技术,并且还要采用配套的焊接材料,所以为了有效提高焊接的质量,挑选最佳的焊接技术,要提前对焊接工艺进行评价操作。
也就是焊接实验,这就要求要设置一个模拟的场所,并做好跟正式焊接相一致的准备工作,然后就可以按照约定好的焊接工序开展焊接操作了,当焊接结束后,要按照一定的流程,开展成果的查验工作,按照具体的操作标准给予合适的评价。
其实焊接工艺评定的作用,能够使焊接工艺更精准,减少正式焊接操作时出错的概率。
所以在没有开展实际焊接工作的时候,通过一定的实验验证焊接工艺的合理性是非常有必要的,这就要求工人首先要明确管道是什么材料,有什么功能,并按照他相应的特点,合理的选择与之相符合的焊接工艺评定,能促进焊接质量的有效提升。
焊接裂纹产生原因及防治

焊接裂纹产生原因及防治背景焊接裂纹就其本质来分,可分为热裂纹、再热裂纹、冷裂纹、层状撕裂等。
下面仅就各种裂纹的成因、特点和防治办法进行具体的阐述。
1.热裂纹在焊接时高温下产生的,故称热裂纹,它的特征是沿原奥氏体晶界开裂。
根据所焊金属的材料不同(低合金高强钢、不锈钢、铸铁、铝合金和某些特种金属等),产生热裂纹的形态、温度区间和主要原因也各不相同。
目前,把热裂纹分为结晶裂纹、液化裂纹和多边裂纹等三大类。
1)结晶裂纹主要产生在含杂质较多的碳钢、低合金钢焊缝中(含S,P,C,Si缝偏高)和单相奥氏体钢、镍基合金以及某些铝合金焊缝中。
这种裂纹是在焊缝结晶过程中,在固相线附近,由于凝固金属的收缩,残余液体金属不足,不能及时添充,在应力作用下发生沿晶开裂。
防治措施:在冶金因素方面,适当调整焊缝金属成分,缩短脆性温度区的范围控制焊缝中硫、磷、碳等有害杂质的含量;细化焊缝金属一次晶粒,即适当加入Mo、V、Ti、Nb等元素;在工艺方面,可以通过焊前预热、控制线能量、减小接头拘束度等方面来防治。
2)近缝区液化裂纹是一种沿奥氏体晶界开裂的微裂纹,它的尺寸很小,发生于HAZ近缝区或层间。
它的成因一般是由于焊接时近缝区金属或焊缝层间金属,在高温下使这些区域的奥氏体晶界上的低熔共晶组成物被重新熔化,在拉应力的作用下沿奥氏体晶间开裂而形成液化裂纹。
这一种裂纹的防治措施与结晶裂纹基本上是一致的。
特别是在冶金方面,尽可能降低硫、磷、硅、硼等低熔共晶组成元素的含量是十分有效的;在工艺方面,可以减小线能量,减小熔池熔合线的凹度。
3)多边化裂纹是在形成多边化的过程中,由于高温时的塑性很低造成的。
这种裂纹并不常见,其防治措施可以向焊缝中加入提高多边化激化能的元素如Mo、W、Ti等。
2、再热裂纹通常发生于某些含有沉淀强化元素的钢种和高温合金(包括低合金高强钢、珠光体耐热钢、沉淀强化高温合金,以及某些奥氏体不锈钢),他们焊后并未发现裂纹,而是在热处理过程中产生了裂纹。
焊接裂纹形成的原因及防止措施
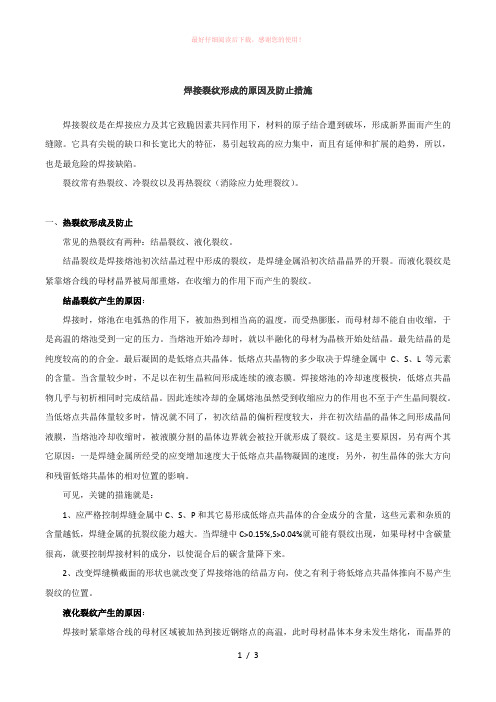
焊接裂纹形成的原因及防止措施焊接裂纹是在焊接应力及其它致脆因素共同作用下,材料的原子结合遭到破坏,形成新界面而产生的缝隙。
它具有尖锐的缺口和长宽比大的特征,易引起较高的应力集中,而且有延伸和扩展的趋势,所以,也是最危险的焊接缺陷。
裂纹常有热裂纹、冷裂纹以及再热裂纹(消除应力处理裂纹)。
一、热裂纹形成及防止常见的热裂纹有两种:结晶裂纹、液化裂纹。
结晶裂纹是焊接熔池初次结晶过程中形成的裂纹,是焊缝金属沿初次结晶晶界的开裂。
而液化裂纹是紧靠熔合线的母材晶界被局部重熔,在收缩力的作用下而产生的裂纹。
结晶裂纹产生的原因:焊接时,熔池在电弧热的作用下,被加热到相当高的温度,而受热膨胀,而母材却不能自由收缩,于是高温的熔池受到一定的压力。
当熔池开始冷却时,就以半融化的母材为晶核开始处结晶。
最先结晶的是纯度较高的的合金。
最后凝固的是低熔点共晶体。
低熔点共晶物的多少取决于焊缝金属中C、S、L等元素的含量。
当含量较少时,不足以在初生晶粒间形成连续的液态膜。
焊接熔池的冷却速度极快,低熔点共晶物几乎与初析相同时完成结晶。
因此连续冷却的金属熔池虽然受到收缩应力的作用也不至于产生晶间裂纹。
当低熔点共晶体量较多时,情况就不同了,初次结晶的偏析程度较大,并在初次结晶的晶体之间形成晶间液膜,当熔池冷却收缩时,被液膜分割的晶体边界就会被拉开就形成了裂纹。
这是主要原因,另有两个其它原因:一是焊缝金属所经受的应变增加速度大于低熔点共晶物凝固的速度;另外,初生晶体的张大方向和残留低熔共晶体的相对位置的影响。
可见,关键的措施就是:1、应严格控制焊缝金属中C、S、P和其它易形成低熔点共晶体的合金成分的含量,这些元素和杂质的含量越低,焊缝金属的抗裂纹能力越大。
当焊缝中C>0.15%,S>0.04%就可能有裂纹出现,如果母材中含碳量很高,就要控制焊接材料的成分,以使混合后的碳含量降下来。
2、改变焊缝横截面的形状也就改变了焊接熔池的结晶方向,使之有利于将低熔点共晶体推向不易产生裂纹的位置。
压力管道焊接接头裂纹原因分析

压力管道焊接接头裂纹原因分析摘要:压力管道的焊接质量直接关系到管线的安全运行。
裂纹是压力管道最容易产生同时也是最具危害性的缺陷,焊缝易产生延迟裂纹和再热裂纹,裂纹一般在靠近熔合线附近的焊缝中产生,裂纹的深度与接头成形状况直接相关,成形越差,裂纹深度越大,为穿晶断裂形式裂纹。
在返修补焊的焊接接头焊趾处过渡圆滑,未发现此处有裂纹产生。
因此在实际的设计与施工过程中要特别关注。
在具体项目的设计过程中,可以将一些重要的焊接工艺要求写入设计说明;在现场施工焊接时,应严格遵照设计说明、焊接工艺评定报告和焊接作业指导书进行,确保焊接质量,保证管道的安全稳定运行。
关键词:压力管道;焊接接头;裂纹原因引言压力管道的应用极为广泛,和我们的日常生活也日益息息相关。
采取有效的预防措施和检验手段来控制压力管道裂纹的发生,减少因为裂纹而产生的失效形式,确保压力管道安全的运行具有重要的意义。
1压力管道焊接接头裂纹原因分析压力管道焊接应根据焊接工艺评定报告和焊接工艺指导书进行。
施焊单位要对施工现场的焊接环境进行严格的管理,当环境温度过低、焊件表面潮湿,或者在下雨、下雪、刮风期间,如对焊件无适当保护措施时,不应进行焊接作业,以免影响焊接质量。
1.1应力腐蚀裂纹应力腐蚀裂纹主要是管道在应力与腐蚀环境共同作用下产生的裂纹。
常见的应力腐蚀裂纹有碳钢在碱液中发生开裂,奥氏体不锈钢在氯离子溶液中开裂以及金属在湿硫化氢溶液中腐蚀开裂。
应力的来源可以是外加应力,也可以是在经过焊接、冷加工后管道内部的残余应力。
残余应力可能由于内部结构改变引起体积改变造成的,也有可能是升温后降温不均匀造成的。
应力腐蚀破裂通常有一个孕育周期,有经过几天就开裂,也有可能数年后才开裂。
应力腐蚀裂纹通常发生在焊缝的焊波处、引弧坑、焊缝的咬边以及孔蚀的凹坑等应力集中处,因此,裂纹发生时通常不止有一条裂纹,而常常是多源的裂纹。
应力腐蚀裂纹的形态主要是不断扩展的裂纹,具有分叉、多源和宏观走向与主应力大致垂直等特征。
铜制结构焊接质量缺陷及处理方法

铜制结构焊接质量缺陷及处理方法1. 引言铜制结构焊接是一种常见的金属焊接方法,广泛应用于各个领域。
然而,焊接过程中可能会出现一些质量缺陷,这些缺陷可能会影响到焊接的强度和稳定性。
本文将介绍铜制结构焊接的常见质量缺陷以及相应的处理方法。
2. 质量缺陷及处理方法2.1 未熔合缺陷- 描述:未熔合缺陷是指焊接接头中部分区域未达到完全熔化或未与基材充分融合的现象。
- 处理方法:对于未熔合缺陷,首先应检查焊接设备和焊接参数是否正确设置。
然后,可以采用适当的焊接技术,如增加电流或加热时间,来确保焊接接头完全熔化和与基材充分融合。
2.2 焊缝裂纹- 描述:焊缝裂纹是指焊接接头中出现的裂纹现象,可能会导致焊接接头强度下降。
- 处理方法:对于焊缝裂纹,可以采用预热和控制焊接残余应力的方法来减少裂纹的生成。
此外,选择合适的焊接材料和焊接方法也是防止焊缝裂纹的重要措施。
2.3 气孔缺陷- 描述:气孔缺陷是指焊接接头中出现的气孔或气泡现象,可能会影响焊接接头的密封性。
- 处理方法:对于气孔缺陷,可以采用适当的焊接工艺控制气体含量和排除气泡。
此外,焊接环境的清洁和焊接面的预处理也是减少气孔缺陷的重要因素。
2.4 金属夹渣- 描述:金属夹渣是指焊接接头中存在的金属夹杂物,可能会降低焊接接头的强度和表面质量。
- 处理方法:对于金属夹渣缺陷,应采取适当的焊接设备和焊接工艺,以减少夹渣的生成。
此外,焊接接头的清洁和表面处理也是防止金属夹渣的重要措施。
3. 结论铜制结构焊接质量缺陷的处理需要综合考虑焊接设备、焊接参数以及焊接工艺等因素。
通过合理的焊接技术和措施,可以有效修复焊接质量缺陷,提高铜制结构焊接接头的质量和可靠性。
压力管道焊接接头裂纹原因分析

压力管道焊接接头裂纹原因分析摘要:经济的发展,促进我国各类工程建设数量的增多。
把液体或气体从一个地方运到另一个地方一般采用压力管道,所以管道质量的好坏对是否能够有效运送起着关键的作用,不同材料的管道所能承受的压力是不一样的,一般都有好几个级别,但制作的工序一般相同,都是先进行下料,然后弯曲首尾相接,接着滚圆退火,最后是环缝焊接,经过有效的查看发现在焊接处经常有一定的裂缝存在,基于此,本文就压力管道焊接接头裂纹原因这探讨。
关键词:焊接接头;裂纹;失效分析引言压力管道属于危害较大的特种设备,具有应用领域广、跨度空间大、承载压力大、输送介质多等特点。
裂缝是压力管道最容易产生和危害最大的缺陷,裂缝延伸到一定程度会引起材料断裂,造成安全事故。
1压力管道概念简单来说,一些易燃易爆物以及一些有毒的物质经常使用压力管道进行长距离的输送,对于压力管道而言,要么是管外有压力,要么是管内存在压力,由于这种独特的情况,因此,在制造压力管道的时候,焊接工序是异常关键的,这就对焊接工人提出了更高的要求,只有精湛的焊接工艺才能制造出高质量的管道,另外,在管道安装的过程中,也不得不进行焊接,所以焊接技术的好坏对整个安装起着至关重要的作用,并且高效的焊接能有效提升工程的质量,并能促进系统后期的有效运行。
2管道焊接工艺裂纹分类裂纹出现的因素管线焊接施工过程中易受到外界环境因素的影响导致管道焊缝裂纹的存在,通常状况下,普通的裂纹可以分为冷裂纹、热裂纹以及再加热裂纹。
冷裂纹的出现主要是由于焊接施工焊口处出现了其他组织的影响,除此之外,焊接过程中产生的大量氢气也会导致冷裂纹的形成,而焊接过程中,管道材料会产生较大的焊缝拉伸力,这三种力量作用之间相互影响,都可能会导致管道焊接过程中冷裂纹的形成。
但这其中,焊接材料产生的大量氢气是对冷裂纹影响最为显著的因素。
热裂纹主要是指管道焊接过程中,在热量影响下产生的裂纹,也就是说,在焊接施工过程中,施工设备产生的高热量会导致管道表面形成热片息反应,而高热量条件下有可能会形成溶点较低的其它结晶体,这种结晶体在高温状态下处于液态状况,并且具有温度较低的特征,而这种结晶体随着时间的推移也会逐渐凝固,在这种情况下,如果焊接施工过程中出现了较大的拉伸应力,那么,液态状况下的其他结晶体或在转变为固态状况下的结晶体,就可能会在结构不稳定的状况下产生裂纹。
纯铜铆裂原因分析报告

纯铜铆裂原因分析报告摘要:纯铜铆连接是一种常见的连接方式,广泛应用于工程和制造领域。
然而,铆连接在一些情况下会出现裂纹问题,影响连接的强度和可靠性。
本报告通过实验和分析,探讨了纯铜铆裂的原因,并提出了相应的解决方案。
一、引言纯铜铆连接的优点在于具有良好的导电性和导热性,广泛应用于电子设备和工业生产中。
然而,纯铜铆连接在使用过程中可能会面临一些问题,其中最常见的是裂纹的产生。
这些裂纹可能会导致连接件的松动、断裂和使用寿命的缩短,因此对于铆连接的裂纹问题进行深入的原因分析至关重要。
二、实验步骤1. 实验样品的制备:选择纯度99.99%的铜材料,并按照标准工艺制备相应的铆接样品。
2. 铆接实验:使用常见的铆接工具进行铆接实验,并保持相同的铆接参数。
3. 裂纹分析:对裂纹样品进行显微镜观察,并测量裂纹的长度和宽度。
4. 原因分析:根据裂纹的形状、位置和实验结果,进行深入的裂纹分析。
三、裂纹原因分析根据实验观察和分析,我们得出了以下导致纯铜铆裂的几个主要原因:1. 铆接参数不当:铆接参数对于铆连接的质量至关重要。
过高或过低的铆接压力都会导致裂纹的产生。
热处理过程中温度的变化也可能引起铆裂。
2. 材料硬度差异:如果铆接材料的硬度差异较大,铆接时容易产生应力集中,导致铆裂的发生。
3. 铆接位置不合理:铆接位置对于连接件的强度也有很大的影响。
如果铆接位置选择不合理,可能会导致局部应力集中,产生裂纹。
4. 加工表面不良:加工表面的粗糙度和平整度也是影响铆连接的重要因素。
如果表面不良,会增加裂纹产生的可能性。
四、解决方案针对以上裂纹原因,我们提出了以下解决方案:1. 合理选择铆接参数:根据不同的实际应用,合理选择铆接参数,确保在一定的范围内进行铆接,避免过高或过低的铆接压力。
2. 控制材料硬度差异:在选择铆接材料时,尽量控制材料硬度的差异,避免太大的硬度悬殊。
3. 合理选择铆接位置:通过合理的设计和选择铆接位置,避免局部应力集中,减少裂纹的发生。
焊接工艺中的焊接接头失效与破坏机理

焊接工艺中的焊接接头失效与破坏机理在焊接工艺中,焊接接头的失效与破坏是一个重要的问题。
了解焊接接头失效的机理对于提高焊接质量和安全性至关重要。
本文将探讨焊接接头失效与破坏的几种常见机理。
1. 焊缝开裂焊缝开裂是焊接接头失效的主要形式之一。
焊缝开裂可以分为冷裂纹和热裂纹两种类型。
冷裂纹是由于焊缝在凝固过程中产生的应力引起的。
在焊接过程中,焊缝材料会经历收缩和形变,这会产生应力。
如果焊缝的冷却速度过快或焊接不当,应力可能导致冷裂纹的形成。
热裂纹则是由于焊接过程中的高温引起的。
当焊接接头在高温下受热时,焊接金属中的某些元素可能发生相变,形成脆性相。
当焊接接头冷却时,这些脆性相可能导致热裂纹的形成。
2. 焊接接头腐蚀焊接接头腐蚀是另一种常见的问题。
焊接接头处于恶劣的工作环境中,易受到气体、液体或化学物质的侵蚀。
焊接接头的腐蚀可能导致金属的蚀损或结构的削弱,从而引起焊接接头的失效。
焊接接头腐蚀的主要原因包括缺乏保护措施、焊接材料本身的不耐腐蚀性以及工作环境中的腐蚀介质。
为了防止焊接接头腐蚀,可以采取合适的防护措施,如涂层、防腐蚀剂或选择耐腐蚀的焊接材料。
3. 焊接接头疲劳破坏焊接接头的疲劳破坏是由于反复加载引起的。
在实际使用中,焊接接头可能会受到循环载荷的作用,例如机械震动、脉动流体或周期性的负载。
这些循环载荷会导致焊接接头中的应力集中,从而引发疲劳破坏。
要预防焊接接头的疲劳破坏,可以采取以下措施:合理设计焊接结构,增加焊接接头的强度和硬度,使用高强度焊材,提高焊接接头的表面光洁度等。
4. 焊接接头变形焊接接头的变形是在焊接过程中常见的问题。
焊接接头加热和冷却会引起材料的热膨胀和收缩,从而导致接头产生变形。
焊接接头的变形可能会导致其几何形状不符合设计要求,从而降低焊接接头的强度和稳定性。
为了减少焊接接头的变形,可以采取一些措施,如使用适当的预热和焊接顺序、加强焊接接头的支撑和固定等。
总结起来,焊接接头失效与破坏的机理主要包括焊缝开裂、焊接接头腐蚀、焊接接头疲劳破坏和焊接接头变形。
黄铜制品开裂原因分析

参考文献:
[ 1 ] 钢铁热处理编写组. 钢铁热处理[M ]. 上海: 上海科学技术出版社, 1979. 227.
[ 2 ] 金属机械性能编写组. 金属机械性能[M ]. 北京: 机械工业出版社, 1982. 70.
图 2 直接淬火 (a)、直接淬火+ 600℃回火 (b) 的渗层组织 3% 硝酸酒精溶液腐蚀 200×
参考文献:
[ 1 ] 苏联专刊№404, 905
(上接第 51 页)
图 7 静断区断口形貌
黄铜的晶粒度对其开裂也有一定的影响, 晶粒越 大, 开裂倾向越大。 由黄铜的金相组织分析知: 外表层 晶粒比内部明显粗大, 外表层又直接与介质接触, 所 以, 腐蚀开裂由圆筒外端部起源, 外表层组织已出现脱 锌腐蚀, 与纯铜组织相似。至于内外晶粒大小存在差别 的原因, 可以认为: 其一与黄铜冷变形不均匀有关; 其 二黄铜中铁含量偏析对此也有不利影响。 5. 2 从残余应力方面分析
Β相敏感性更大。所选材料含锌量偏高, 为 38%~ 39%
之间, 这对提高强度有利, 却易产生应力腐蚀, 增大开
裂倾向。
(下转第 56 页)
《热加工工艺》2000 年第 1 期
— 51 —
加入稀土以后, 降低了硼化物层硼的浓度梯度, 提高了 其扩散速度, 使 Fe2B 增多; 还可清洁工件表面, 提高硼 原子在钢铁表面吸附量, Fe2B 形核率增加, 渗层得到 改善。 因此, 我们选用 2 号渗剂用于生产。
某厂圆筒状黄铜制品存放期间出现开裂现象, 委 托我们进行失效分析。为此, 我们对黄铜开裂件进行了 宏观分析、金相组织分析; 并用电子探针测定了化学成 分; 观察了裂纹走向及裂纹尖端形貌; 分析了不同断裂 区的断裂特点。根据实验结果与分析讨论, 确定了黄铜 制品开裂的原因。
铜管钎焊热裂纹形成的原因与分析_田泽生

铜管钎焊热裂纹形成的原因与分析田泽生(北京万众空调制冷设备公司)摘 要 本文阐述了铜管钎焊裂纹形成的常见原因及其金相组织状态。
关键词 铜管 钎焊 热裂纹THE CAUSE &ANALYSIS AB OUT THE C OPPERTUBE CRAZE DURING WELDINGTIAN Ze Sheng(Beijing M TD Conditioning &Refrigeration Equipment Co rp .)ABSTRACT This article elaborates the reason about copper tube craze during w elding and the state of metallic crystalKEY W ORDS Copper -tube Welding Craze 空调制冷业中大量铜质管材用于制造换热器和输液管路。
铜管之间的连接以及铜管与其它器件的连接,普遍采用火焰硬钎焊工艺。
钎焊后有时会产生裂纹,造成在密封试验时泄漏。
分析裂纹形成的原因主要有以下两个方面。
1 操作不当造成钎焊温度过高钎焊是利用火焰加热母材和钎料使之达到钎料的熔化温度,熔化的钎料润湿在母材的表面并填充在结合间隙中。
常用的钎料如黄铜、磷铜、银铜焊丝等其熔点均在700℃以上。
钎焊时对母材加热应根据其形状、大小、异质材料的导热、散热性能照片1 80×以及选用的钎料种类等因素来掌握加热时间。
如果加热温度过高,一种情况是使材料内部组织晶粒过分长大,此时由于晶界在高温下强度降低甚至发生流变,导致晶间裂纹形成(照片1)。
另一种可能是高温使母材局部熔化并重新结晶,此时会在熔化区产生气孔(照片2),也使钎焊密封不良。
照片2 100×2 铜管存在自身缺陷有两种情况值得特别重视,一是铜管在生产加工过程中造成损伤,个别部位存在微小裂纹或深入管壁内部的缺陷(照片3、4)。
热锻黄铜阀门开裂原因及热脆机理分析

热锻黄铜阀门开裂原因及热脆机理分析
摘要:黄铜阀门在热锻后出现了开裂现象,通过化学成分分析、金相检验、扫描电镜和能谱分析等方法对阀门开裂原因进行了分析。结果表明:热脆现象是导致阀门沿晶开裂的主要原因。热锻过程中,铅元素在晶界处发生偏聚,形成富铅的低熔点共晶相,使晶界弱化;在拉应力作用下,裂纹从阀体表面起源,沿轴向扩展,最终导致脆性开裂。最后针对阀门开裂原因提出了预防措施。
1.4扫描电镜及能谱分析
进一步放大观察,可见一些沿晶界分布的物质,它们沿裂纹扩展方向将裂纹打开,采用扫描电镜(sem)观察断口微观形貌。断口较为平整,无塑性变形;断口表面呈块状或冰糖状,存在一定量的二次裂纹,未见韧窝等塑性断裂形貌。说明该黄铜阀门的失效形式为典型的沿晶脆性开裂。为查明裂纹沿晶开裂的原因,将断口表面形貌在sem背散射模式下呈白亮色,如图3c)所示。对白亮色物质进行能谱(EDS)分析,可见其化学成分主要为铅元素,说明在晶界上发生了铅偏聚现象。使用扫描电镜观察金相试样,如图4所示,清晰可见在晶界处存在大量亮白色物质,对其进行EDS分析,结果表明在主裂纹区和二次裂纹区的晶界处均发生了铅的偏聚,这与断口分析结果相一致。
3结论及建议
该黄铜阀门失效模式为热脆现象导致的沿晶开裂失效。热锻过程中,不合理的热锻工艺导致铅元素向晶界处聚集,形成富铅的低熔点共晶相,在拉应力作用下,形成沿晶微裂纹。裂纹从阀体表面应力集中处起源,沿轴向扩展,最终导致断裂失效。为预防热锻黄铜的热脆现象,应注意严格控制原材料的杂质元素含量以减轻元素偏析;制定合理的热锻工艺,防止材料在300~400℃脆性温度区间长时间停留;降低挤压速度和冷却速度,以免产生较高的内应力。
黄铜三通接头裂纹原因分析

黄铜三通接头裂纹原因分析尚尔峰;王志明;王亚勤【摘要】某黄铜三通接头在打压试验进行20天后产生裂纹.经过宏观及微观检验,结果表明,三通接头化学成分、显微组织及低倍组织均符合相关标准规定.由于接头内螺纹表面附着含S元素介质,断口显示沿晶断裂特征,本文从黄铜双空位机制脱锌腐蚀角度探讨了导致三通接头产生应力腐蚀开裂的原因.【期刊名称】《热处理技术与装备》【年(卷),期】2016(037)001【总页数】5页(P51-55)【关键词】黄铜;沿晶断裂;双空位;脱锌腐蚀;应力腐蚀开裂【作者】尚尔峰;王志明;王亚勤【作者单位】沈阳铸造研究所,辽宁沈阳110022;沈阳铸造研究所,辽宁沈阳110022;沈阳铸造研究所,辽宁沈阳110022【正文语种】中文【中图分类】TG146.1+1;TG113.23+1某企业安装的压力泄放装置在打压试验中保压20天后,三通接头产生裂纹。
试验温度为室温,介质为压缩空气,试验压力20 MPa。
接头为锌黄铜锻件,牌号H62。
锻造工艺为810℃(保温1 h)自由锻造,锻后无热处理。
三通接头宏观形貌如图1所示。
图2箭头指示为接头内表面的裂纹形貌。
裂纹起始于内螺纹下端第1~2螺距处,向管壁扩展。
裂纹长约12 mm,呈直线状。
靠近裂纹起始端约20 mm×10 mm区域内的内螺纹表面颜色呈褐色。
2.1 断口宏观分析采用万能试验机将裂纹扩大,并人为将断口完全分离。
断面颜色陈旧,表面有覆盖物,断裂源区呈黑、褐色;远离断裂源区颜色逐渐变浅,呈锈黄、灰等颜色。
断口平齐,无剪切唇,边缘无宏观塑性变形,显示脆性开裂特征(图3)。
断裂源产生于内螺纹下端第1~2螺距之间,沿横向开裂。
下部边缘区域新鲜断口是人为致裂断口。
2.2 断口微观分析用扫描电镜观察断口断裂源区(图4(a))、断裂源附近黑色区、浅色区以及人为破坏断口区域。
断口呈现沿晶断裂形貌(图4(b)),断面残留腐蚀产物(图4(c)),显示应力腐蚀开裂特征。
H68黄铜弹壳开裂原因分析

H68黄铜弹壳开裂原因分析崔刚【摘要】通过化学成分分析、裂纹宏观和微观检验、显微硬度测试与微区成分能谱分析等方法,分析了H68黄铜弹壳开裂失效的原因.结果表明:材料本身存在冶金缺陷β相偏析与零件收口处退火不良是造成弹壳开裂失效的原因.%The cracking reason of H68 brass shell was analyzed by means of chemical composition analysis, macroscopic and microscopic examination of crack, microhardness testing, energy spectrum analysis of micro area composition and so on. The results showed that the metallurgy defects of β phase segregation existed in materials and the undesirable annealing of part convergent resulted in cracking on the shell.【期刊名称】《理化检验-物理分册》【年(卷),期】2013(049)003【总页数】4页(P185-188)【关键词】H68黄铜;弹壳;开裂;偏析;滑移【作者】崔刚【作者单位】航宇救生装备有限公司理化中心,襄樊441003【正文语种】中文【中图分类】TJ411H68黄铜强度较高,适于冷冲压或深冲拉伸制造各种形状复杂的零件。
大量用于制造枪弹壳和炮弹壳,故有弹壳黄铜之称[1]。
某型功能弹的弹壳由Y态H68棒料制造。
经过车制加工,装入弹药后封口,按工艺要求封口处距弹壳端口5mm范围内经退火处理,以降低或消除应力。
在装机1a(年)后发现一枚弹壳在封口部位沿纵表面出现了穿透性裂纹,开裂弹壳的宏观形貌见图1。