全钢子午胎胎体变形(帘线弯曲)分析
全钢载重子午胎质量缺陷产生原因及解决措施

全钢载重子午胎质量缺陷产生原因及解决措施1胎里露线胎里露线是指轮胎里面钢丝骨架材料内表面覆胶不足,钢丝露出胎里表面。
胎里露线多在肩部或侧部出现。
经过里程实验,出现露线的外胎在耐久实验15小时左右即出现肩部鼓包或爆破,基本没有使用价值,由于影响因素较多,因此,胎里露线是废品率很高的一种缺陷,也是全钢胎制造过程中最容易出现、最难解决的问题。
1.1原因分析1.1.1胎里露线主要原因是机头平宽设计偏小或在成型过程中胎圈定位撑块出现漂移造成。
成型机头宽度窄,两胎圈之间的帘线长度短,当硫化给内压时,由于胎胚外直径小于设计尺寸,伸张变形大,这样帘线会抽出内衬层导致胎里露线。
1.1.2材料分布不足也会产生胎里露线,如果胎面或垫胶的厚度或长度不够标准,在成型时强行拉伸,导致局部材料缺失,肩部内轮廓帘线伸展过渡,易出现胎里露线现象。
1.1.3内衬层的厚度及各部位的尺寸低于设计尺寸,或成型时贴合偏移,造成局部材料分布不均,或密封层的塑性过大均会造成肩部漏钢丝的现象。
1.1.4硫化定型失控也是造成成品肩部漏钢丝的不可忽视的原因。
在硫化定型时,如果定型压力不能稳定在规定值,那么在合模过程中,胎胚外直径一直处于逐渐增大的状态,这样会有肩部部分胶料随着花纹块下移,造成上模花纹块处缺胶,成品胎里肩部露线。
1.1.5硫化机机械手定位高度过低,胎胚的中心线与胶囊中心线不吻合,定型时胎胚上部过度伸张,钢丝帘线析出内衬层表面,出现露线现象。
1.2 解决措施:1.2.1 结构设计是内在因素,工艺和操作是外部因素。
若存在着普遍的胎里露线现象,并且通过X光检测,发现胎体帘线成直线排列,则应重新考虑平宽的选取,一般增大2~4mm可解决。
严格控制挤出、压型半成品部件的的尺寸,不合格的半成品部件严禁使用。
1.2.2 严格控制成型操作,每班开产前必须对成型鼓的平宽、送料架的定位尺寸进行测量,不符合要求的应通知维修人员解决后方可生产。
同时要检查各种半成品部件是否符合施工条件,不合格的半成品严禁使用。
全钢载重胎体帘线缺陷原因分析及解决措施
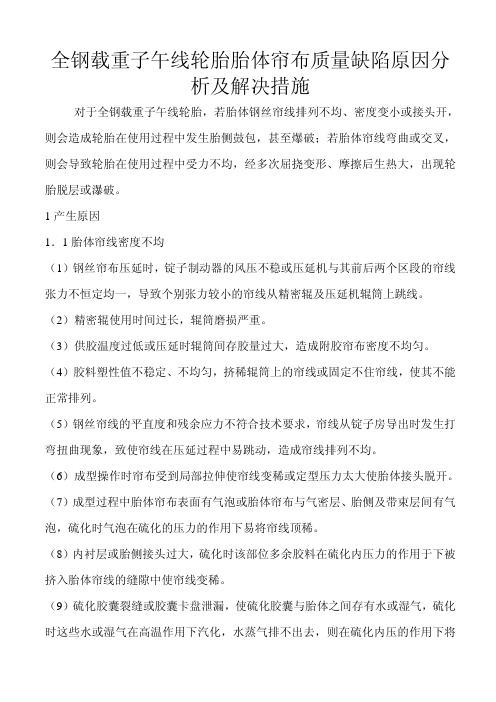
全钢载重子午线轮胎胎体帘布质量缺陷原因分析及解决措施对于全钢载重子午线轮胎,若胎体钢丝帘线排列不均、密度变小或接头开,则会造成轮胎在使用过程中发生胎侧鼓包,甚至爆破;若胎体帘线弯曲或交叉,则会导致轮胎在使用过程中受力不均,经多次屈挠变形、摩擦后生热大,出现轮胎脱层或瀑破。
1产生原因1.1胎体帘线密度不均(1)钢丝帘布压延时,锭子制动器的风压不稳或压延机与其前后两个区段的帘线张力不恒定均一,导致个别张力较小的帘线从精密辊及压延机辊筒上跳线。
(2)精密辊使用时间过长,辊筒磨损严重。
(3)供胶温度过低或压延时辊筒间存胶量过大,造成附胶帘布密度不均匀。
(4)胶料塑性值不稳定、不均匀,挤稀辊筒上的帘线或固定不住帘线,使其不能正常排列。
(5)钢丝帘线的平直度和残余应力不符合技术要求,帘线从锭子房导出时发生打弯扭曲现象,致使帘线在压延过程中易跳动,造成帘线排列不均。
(6)成型操作时帘布受到局部拉伸使帘线变稀或定型压力太大使胎体接头脱开。
(7)成型过程中胎体帘布表面有气泡或胎体帘布与气密层、胎侧及带束层间有气泡,硫化时气泡在硫化的压力的作用下易将帘线顶稀。
(8)内衬层或胎侧接头过大,硫化时该部位多余胶料在硫化内压力的作用于下被挤入胎体帘线的缝隙中使帘线变稀。
(9)硫化胶囊裂缝或胶囊卡盘泄漏,使硫化胶囊与胎体之间存有水或湿气,硫化时这些水或湿气在高温作用下汽化,水蒸气排不出去,则在硫化内压的作用下将胎体帘布顶稀。
1.2胎体帘线裂缝胎体帘线裂缝表现为胎体帘线在接头处(90°帘布裁断机接头处或成型接头处)裂开。
(1)90°帘布裁断机接头装置风压低或接头装置间隙过大。
从外观看,90°帘布裁断机接头后在接头处开缝或接头处胶料过多,帘线间距大于正常压延间距,甚至是正常帘线间距的几倍。
(2)附胶帘布停放时间过长、帘布粘性不好或帘布喷霜。
(3)成型或硫化时定型压力过大。
(4)成型过程中供料与导开速度不匹配,帘布受到拉伸。
全钢载重子午线轮胎胎里拱的原因分析及解决措施
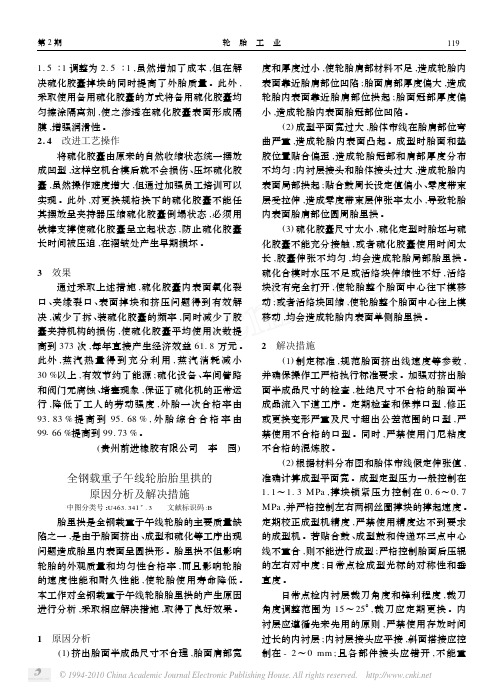
第2期1.5∶1调整为2.5∶1,虽然增加了成本,但在解决硫化胶囊掉块的同时提高了外胎质量。
此外,采取使用备用硫化胶囊的方式将备用硫化胶囊均匀擦涂隔离剂,使之渗透在硫化胶囊表面形成隔膜,增强润滑性。
2.4 改进工艺操作 将硫化胶囊由原来的自然收缩状态统一摆放成凹型,这样空机合模后就不会损伤、压坏硫化胶囊,虽然操作难度增大,但通过加强员工培训可以实现。
此外,对更换规格换下的硫化胶囊不能任其摆放呈夹持器压缩硫化胶囊倒塌状态,必须用铁棒支撑使硫化胶囊呈立起状态,防止硫化胶囊长时间被压迫,在褶皱处产生早期损坏。
3 效果 通过采取上述措施,硫化胶囊内表面氧化裂口、夹缘裂口、表面掉块和挤压问题得到有效解决,减少了拆、装硫化胶囊的频率,同时减少了胶囊夹持机构的损伤,使硫化胶囊平均使用次数提高到373次,每年直接产生经济效益61.8万元。
此外,蒸汽热量得到充分利用,蒸汽消耗减小30%以上,有效节约了能源;硫化设备、车间管路和阀门无腐蚀、堵塞现象,保证了硫化机的正常运行,降低了工人的劳动强度,外胎一次合格率由93.83%提高到95.68%,外胎综合合格率由99166%提高到99.73%。
(贵州前进橡胶有限公司 李 园)全钢载重子午线轮胎胎里拱的原因分析及解决措施中图分类号:U463.341+.3 文献标识码:B 胎里拱是全钢载重子午线轮胎的主要质量缺陷之一,是由于胎面挤出、成型和硫化等工序出现问题造成胎里内表面呈圆拱形。
胎里拱不但影响轮胎的外观质量和均匀性合格率,而且影响轮胎的速度性能和耐久性能,使轮胎使用寿命降低。
本工作对全钢载重子午线轮胎胎里拱的产生原因进行分析,采取相应解决措施,取得了良好效果。
1 原因分析 (1)挤出胎面半成品尺寸不合理,胎面肩部宽度和厚度过小,使轮胎肩部材料不足,造成轮胎内表面靠近胎肩部位凹陷;胎面肩部厚度偏大,造成轮胎内表面靠近胎肩部位拱起;胎面冠部厚度偏小,造成轮胎内表面胎冠部位凹陷。
全钢载重子午线轮胎肩部帘线弯曲问题分析

w—— 预硫 化后 胎圈 的宽 度 。 从 上式 可 以看 出 , 若 取 值 过小 , 计算 的成 型 平 宽偏 大 , 钢丝 帘线 过 长而伸 展不 充分 , 会导 致肩
钢 丝 圈平面 宽设 置 过 大 ( 如图 1所 示 ) 原应 ,
处于 B B 的钢 丝 圈位 于 A— , 丝 圈 A— — A处 钢 A 之
第 8期
许 庆江 . 钢 载 重 子 午 线 轮 胎 肩 部 帘 线 弯 曲 问题 分 析 全
57 0
( )成 型机 胎 定型 和超 定型 过程 中撑 块锁不 住 胎体帘 线 , 在
帘线 向 内抽 入 , 造成 帘线 发生 变化 。
中 图 分 类号 : 6 . 4 . / 6 U4 3 3 1 3 . 文献 标 识 码 : B 文 章 编 号 : 0 6 8 7 ( 0 7 0 — 5 60 1 0 — 1 1 2 0 ) 80 0 — 2
全 钢载 重子 午 线 轮 胎 生产 工 艺 复 杂 , 件 较 部 多 , 成 型 、 化 时受 力 变形 较 大 , 生产 过 程 中 且 硫 故
露 线缺 陷 。
1 4 钢 丝 圈 平 面 宽 .
成 型平 宽 ( 是 胎 体 鼓 上两 胎 圈 的 间距 , B) 通 常采 用下式 计算 :
一
2 L一 ( 一 2 ) B 一2 B。 W / W
式中 — —胎 体钢 丝 帘线 的假定 伸张 值 ; 2 —— 轮胎 钢丝 帘线 展开 长度 ; L
1 2 半成 品体 积 .
在 模具 已固定 的空 间 内 , 余 的钢 丝 在 胎 肩 处 聚 多
集而 产生 弯 曲 , 重 时胎 坯 经成 型机 定 型 后 在胎 严
肩发生 弯 曲 。
全钢载重子午线轮胎胎肩帘线弯曲原因分析及解决措施
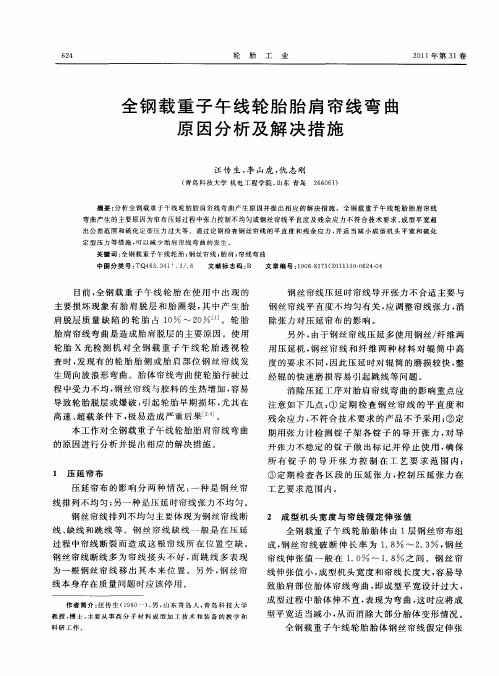
65 2
值 ( ) 成 型 鼓 宽 度计 算 中 的 一 个 重要 参 数 , 是 其 值 选 取 是 否 合 理 将 严 重 影 响 胎 肩 质 量 。 如 果
在锁块 锁 紧状 态下 排 气 阀有 风 , 明 主 轴锁 块 密 说
封 圈 密 封 不 严 , 能 满 足 压 力 要 求 , 种 情 况 也 会 不 这
所有锭子 的导开 张力控制在 工艺要求 范 围内;
③ 定 期 检 查 各 区 段 的 压 延 张 力 , 制 压 延 张 力 在 控
1 压 延 帘 布
压 延帘 布的影 响 分两 种 情 况 : 一种 是 钢 丝 帘
线 排列 不均匀 ; 另一种 是压延 时帘 线张力 不均匀 。 钢 丝帘线排 列不均 匀 主要 体现 为钢丝 帘线断
肩 脱 层 质 量 缺 陷 的 轮 胎 占 1 ~ 2 口 。 轮 胎 0 0 ]
钢 丝帘 线压延 时帘 线导开 张力 不合适 主要与
钢丝帘 线平 直度不 均匀 有关 , 调整 帘线 张力 , 应 消 除张力 对压延 帘布 的影 响 。
胎肩 帘线弯 曲是造 成胎肩 脱层 的主要原 因 。使 用 轮胎 X光检 测 机 对 全钢 载 重 向波浪形 弯 曲。胎体帘 线弯 曲使轮胎 行驶过
程 中受 力 不 均 , 丝 帘 线 与 胶 料 的 生 热 增 加 , 易 钢 容
消 除压延 工序对 胎肩 帘线弯 曲的影 响重点 应
注 意 如 下 几 点 : 定 期 检 查 钢 丝 帘 线 的 平 直 度 和 ①
导 致轮胎 脱层或 爆破 , 引起轮 胎早期 损坏 , 其在 尤 高 速 、 载条件下 , 超 极易 造成严 重后果 ] 。。
全钢 载重 子午线 轮胎胎 体 由 1层钢 丝帘布 组
子午线轮胎质量分析

论据分析
通过各部位材料能量耗散所占比例分配可以看出,轮胎材料滞后损失能量 (生热量)主要集中在胎面部位,其次是胎圈部位。就是说胎面胎圈部位 材料能量耗散分布所占的比例最大,产生的滞后损失就大,产生的热量相 应也大,同时对应部件越易出现问题。 1、轮胎在滚动时,胎肩部位所受到的交变应力(即,拉伸,压缩,剪切 各种应力同时存在的多项应力)最大也最复杂,产生滞后损失而生热量最 大,出现问题的几率就大。 2、带束层承受着胎体的60——75%的应力,所以带束层端点蠕动量最 大,生热量就大,端点包胶就容易脱离,从而造成肩部脱层/带束层端点 松散。 3、轮胎内磨擦产生的能量消耗占轮胎总能量消耗的80%以上。 4、胎圈部位出现问题多的原因也是如此。 5、子午线轮胎由于胎体帘线呈子午向(径向)排列,在负荷状态下胎侧 径向变形大,因侧向刚性低,胎侧胶承受的应力高。在此情况下,胎侧中 部橡胶经受双向伸张(这也是造成胎侧拉链爆的原因之一),而胎圈区 和胎面边端则为双向压缩,从而致使胎圈区产生屈挠裂口或导致带束层与 胎面边端脱层。
轮胎在使用过程中, 各部位材料能量耗散分布所占比例
胎面39%.带束层8%,胎体帘布6%,基部 胶5%。 胎冠及胎肩部位材料能量耗散合计为58%。 胎圈14%,三角胶13%,胎体帘布6%。 子口部位材料能量耗散合计为33%。 内衬层8%,胎侧胶7%,胎体帘布6%。 胎侧部位材料能量耗散合计21%。
客户服务培训
全钢载重子午线轮胎 质量鉴定知识
轮胎损坏的原因1
使用问题:超载、不标准气压、非标轮辋及轮辋变形或爆破、 车况不良、使用环境与轮胎性能不匹配、撞击、扎伤、急转弯/ 转弯半径过小、急刹车。 性能问题(能力问题):如超载性能、高速性能、散热性能。 性能问题实际与使用问题也有关系。也是受大环境的影响,人 为或少数人不能改变的问题。 制造问题:胶部件脱层(气泡、杂质、粘合不好)、部件之间 无差级或带束层上偏(一般发生在成型工序)、部件尺寸或性 能不合格或胎侧及内衬层接头过大、胎体帘布稀线(一般在压 延裁断帘布尾线部分时)、辟缝(成型定型压力过大或扯拉用 力过大时易造成辟缝)、帘线交叉。 人为制造:用人为制造假病象来掩盖轮胎出现的真实问题。
全钢载重子午线轮胎胎侧蛇形弯曲原因分析及解决措施
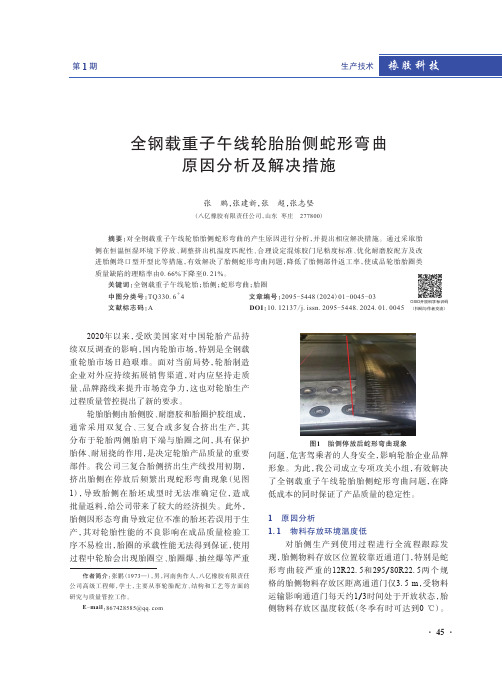
45全钢载重子午线轮胎胎侧蛇形弯曲原因分析及解决措施张 鹏,张建新,张 超,张志坚(八亿橡胶有限责任公司,山东 枣庄 277800)摘要:对全钢载重子午线轮胎胎侧蛇形弯曲的产生原因进行分析,并提出相应解决措施。
通过采取胎侧在恒温恒湿环境下停放、调整挤出机温度匹配性、合理设定混炼胶门尼粘度标准、优化耐磨胶配方及改进胎侧终口型开型比等措施,有效解决了胎侧蛇形弯曲问题,降低了胎侧部件返工率,使成品轮胎胎圈类质量缺陷的理赔率由0.66%下降至0.21%。
关键词:全钢载重子午线轮胎;胎侧;蛇形弯曲;胎圈中图分类号:TQ330.6+4 文章编号:2095-5448(2024)01-0045-03文献标志码:A DOI :10.12137/j.issn.2095-5448.2024.01.00452020年以来,受欧美国家对中国轮胎产品持续双反调查的影响,国内轮胎市场,特别是全钢载重轮胎市场日趋艰难。
面对当前局势,轮胎制造企业对外应持续拓展销售渠道,对内应坚持走质量、品牌路线来提升市场竞争力,这也对轮胎生产过程质量管控提出了新的要求。
轮胎胎侧由胎侧胶、耐磨胶和胎圈护胶组成,通常采用双复合、三复合或多复合挤出生产,其分布于轮胎两侧胎肩下端与胎圈之间,具有保护胎体、耐屈挠的作用,是决定轮胎产品质量的重要部件。
我公司三复合胎侧挤出生产线投用初期,挤出胎侧在停放后频繁出现蛇形弯曲现象(见图1),导致胎侧在胎坯成型时无法准确定位,造成批量返料,给公司带来了较大的经济损失。
此外,胎侧因形态弯曲导致定位不准的胎坯若误用于生产,其对轮胎性能的不良影响在成品质量检验工序不易检出,胎圈的承载性能无法得到保证,使用过程中轮胎会出现胎圈空、胎圈爆、抽丝爆等严重图1 胎侧停放后蛇形弯曲现象问题,危害驾乘者的人身安全,影响轮胎企业品牌形象。
为此,我公司成立专项攻关小组,有效解决了全钢载重子午线轮胎胎侧蛇形弯曲问题,在降低成本的同时保证了产品质量的稳定性。
全钢丝子午线轮胎成型及硫化过程胎坯变形与帘线伸张综述
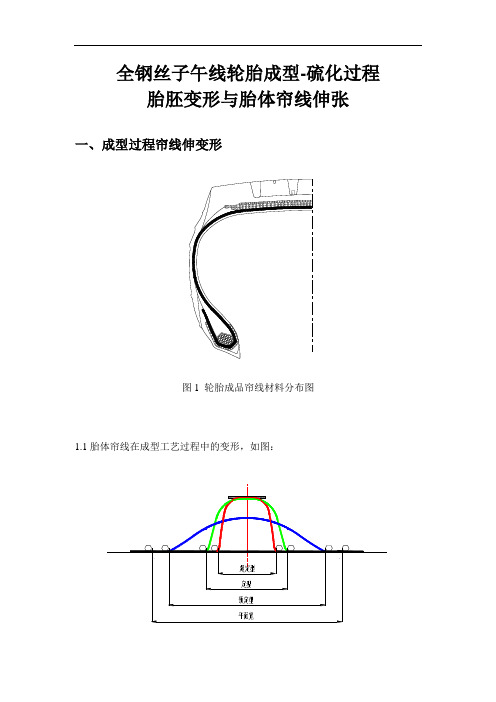
全钢丝子午线轮胎成型-硫化过程胎胚变形与胎体帘线伸张一、成型过程帘线伸变形图1 轮胎成品帘线材料分布图1.1胎体帘线在成型工艺过程中的变形,如图:图2 成型过程中帘线变化1.2 几种典型规格的平面宽度(成型钢圈内外宽度)(单位mm)规格平面宽度预定型度定型宽度超定型宽度8.25R20 536 460 360 3209.00R20 636 500 360 32010.00R20 674 520 360 35011.00R20 728 535 370 35512.00R20 779 560 390 36011R22.5 650 510 400 35012R22.5 702 545 420 36013R22.5 724 555 460 365275/80R22.5 656 560 440 370295/80R22.5 694 580 480 400315/80R22.5 718 600 470 410315/70R22.5 680 570 460 380315/75R22.5 684 580 480 380385/65R22.5 780 630 460 400425/65R22.5 870 670 580 4901.4 成型工艺胎体帘线由贴合平铺到定型胎体变形的重要性成型工艺过程,胎体帘布从平铺形状逐渐变形到胎胚,接近成品的形状。
这个过程中,两个胎圈中间的距离逐渐减小,胎胚内的空气逐渐增加,胎胚中心逐渐隆起,直到两胎圈之间距离接近成品相应宽度,冠部与带束层接触。
予定型是定型的准备阶段。
定型是比较主要和基本的阶段。
超定型是为了钢圈进一步靠近,胎胚胎肩部位和带束层更紧密结触,不留空隙,不产生气泡。
●这个过程的充气压力要求逐渐增加,如0.3-0.5-0.8 Kg/cm^2,不可过快过高,避免胎体帘线的密度改变,最终充气压力1Kg/cm^2左右●胎圈收缩要对称收缩,做到胎体中心线两侧宽度均等,帘线匀称。
●胎体变形要均匀,不可塌陷扭曲而导致异常变形,造成稀密不均。
全钢载重子午线轮胎质量缺陷问题分析

全钢载重子午线轮胎质量缺陷问题分析子午线轮胎制造工艺复杂,要求精度高。
根据全钢载重子午线轮胎常见质量缺陷,进行了原因分析,并提出了相应的解决措施。
1、胎里露钢丝与肩部帘线弯曲胎里露线是指轮胎里面钢丝骨架材料内表面覆胶不足,钢丝露出胎里表面。
胎里露线多在肩部或侧部出现帘线露出或“露肋骨”现象。
在使用中胎里露出的钢丝容易损坏内胎,使轮胎胎体鼓包甚至爆破。
肩部帘线弯曲是指轮胎肩部胎体帘线出现周向弯曲。
帘线弯曲在轮胎行驶当中受力不均,使钢丝与胶的生热增加,导致轮胎脱层或爆破,引起轮胎的早期损坏。
全钢丝载重子午线轮胎胎里露线和肩部帘线弯曲是生产和使用中困扰轮胎技术人员的一大难题。
由于胎里露线和肩部帘线弯曲是相辅相成的,是一对矛盾的统一体,所以将两个问题一起讨论。
1.1 原因分析(1)胎里露钢丝与肩部帘线弯曲主要原因是机头宽度与帘线假定伸张值选取不合理。
胎体由一层钢丝帘布组成,帘线断裂伸张率为1.8~2.3之间,胎体的钢丝帘线伸张值一般在 1.0%~1.8%之间。
帘线伸张值大,成型机头宽度窄,帘线长度短。
当伸张值达到极限值;帘线会抽出内衬层导致胎里露线。
帘线伸张值小,成型机头宽度宽,帘线长度长,容易导致肩部胎体帘线弯曲。
半成品的尺寸和重量是根据材料分布图计算出来的,当半成品尺寸和质量过大,会导致胎体帘线的材料过剩从而使胎体帘线弯曲。
材料分布不足就会产生胎里露线,胎面或垫胶的厚度或长度超公差,使得肩部材料过剩,厚度增加,内轮廓帘线舒展不开,导致肩部帘线弯曲。
反之,内轮廓帘线伸展过渡,易出现胎里露线现象。
(2)胎坯外周长的大小也是影响胎里露线和肩部帘线弯曲的一个因素。
胎坯外周长达不到标准,则轮胎在硫化过程中伸张变形大,出现胎里露线;反之,胎坯外周长大,轮胎在硫化过程中伸张变形小,将易出现帘线肩部弯曲。
(3)一次法成型机传递环故障或鼓的撑块出现故障,成型过程中胎圈定位、撑块定位发生漂移或者平宽设定有误,造成内轮廓帘线较标准帘线长度增大,胎体帘线伸张不足,硫化后产生肩部帘线弯曲。
全钢载重子午线轮胎胎圈质量缺陷的原因分析及解决措施

胶囊进 出管路 的气 动 阀门 是 否泄 漏 或 堵 塞 , 必要
时 更 换 密 封 件 和 阀 门 。多 台 硫 化 机 抽 真 空 不 彻 底
时 , 检查 控制 抽真 空 的电磁 阀是否 复位 , 应 防止其 它介 质进 入真空 泵 。 ( ) 具使 用一定 次数 后应 喷涂 脱模剂 , 3模 并保
( 岛黄 海 橡 胶 集 团 有 限 责 任公 司 , 青 山东 青 岛 2 6 4 ) 6 0 1
摘 要 : 析 全 钢 载 重 子 午 线轮 胎 胎 圈 部 位 裂 口 、 线 、 胶 、 形 、 泡 、 边 、 丝 圈 上 抽 和 胎 趾 圆 角 等 质 量 缺 陷 分 露 缺 变 气 胶 钢 的产 生 原 因 , 提 出 相 应解 决措 施 。通 过 采 取 合 理 设 计 半 成 品 尺 寸 、 期 检 查 并 定 调
1 胎 圈裂 口
2 胎 圈 露 线
胎 圈露线 是指 在胎 圈附 近露 出胎 圈包 布或胎
体 帘布 , 为胎 圈底 部 露线 、 圈 外侧 露 线 ( 集 分 胎 多
中于无 内胎 轮胎 ) 和胎 圈 内侧 露线 。
2 1 原 因 分 析 .
( ) 化 定型过 程 中胎坯 严重 装偏 , 1硫 不能 正确 装 入模 具 , 成 胎 圈部 位 胶料 流 失 , 部 出胶 边 , 造 局 导 致胎 圈底部 胶 料 严 重不 足 , 出胎 圈 包 布或 者 露 胎 体钢 丝 。 () 2 半成 品 尺 寸不 符 合 工 艺要 求 , 胶料 不 足 , 造 成胎 圈底 部露钢 丝 。 () 3 胎侧 耐磨胶 粘度 低 , 硫化 时胎 圈部位 胶料 流 动过度 , 圈外侧 胶料 不足 , 出胎 圈包 布 。 胎 露 ( ) 型机平 宽不符 合工 艺要 求 , 成胎 坯轮 4成 造 廓 过 小 , 化 时 胎 圈 区域 膨 胀 过 度 , 使 胶 料 不 硫 致 足, 造成 露线 。 ( ) 内胎 轮胎 胎 圈倾 斜 角 度 比有 内 胎轮 胎 5无 大, 若胎 圈部 位胶料 不 足 , 导致硫 化 时胎踵 到装 则 配线 间的胶料 不足 。 () 6 硫化 操作 时硫 化胶囊 抽 真空不 充分 , 上环 下 降到 定型 高度 时 , 化 胶 囊在 胎 圈处 打 褶将 胶 硫 料 挤走 , 造成 胎 圈内侧 露线 。
子午线轮胎常见外观缺陷原因分析及应对措施
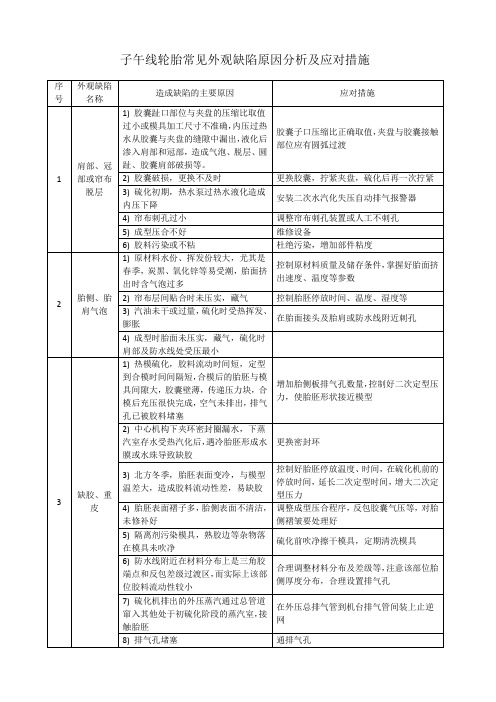
14
胎面花纹圆角
1)胎面胶料不足
控制胎面的尺寸、重量
2)花纹排气性不好
花纹设计排气顺畅
3)模具孔堵塞
通排气孔
15
胎圈发软
1)硫化不熟
护胶未加硫磺或促进剂
下钢棱漏水
16
胎里裂口(内衬裂口)
2)机头宽度过大
调整机头宽度(减窄)
3)内衬层接头搭接不当
正确搭接内衬层接头
3)钢丝帘布胶门尼粘度偏低
控制胶料的门尼粘度
4)硫化定型压力过大
调整硫化工艺
5)胎面过厚
保证胎面的尺寸、重量
6)成型机卡盘活块松脱,钢丝上抽
维修设备
7)装错胎胚
为规范胎胚收发
13
内衬层泡
1)内衬层复合后存气
控制胶料门尼粘度均匀性
2)内衬层胶小料分散不均
保证内衬层胶料小料分散良好
3)硫化过程冷凝水没有排泄干净
2)胎圈部位材料不足,硫化时钢丝圈易移位
合理选钢丝圈,肩部和侧面的压缩率取值,钢丝圈直径
3)帘线收缩率过大
原材料检验严格把关,设计时考虑工艺波动的影响
4)成型扣圈偏歪
检查扣圈盘对中、同心度、钢丝圈直径
5)胎面偏歪影响内轮廓及胎体伸张
检查传递环对中度,压辊对称性
6)定型不当,定型高度、装胎高度不合适,胶囊膨胀不均
胶囊老化应及时更换,控制好定型压力
4)胶囊欠硫,弹性小
严格控制硫化条件及胶囊质量
5)一、二次定型进气太慢,气压不够,胶囊伸展不开
查动力供给及测漏点
6)隔离剂浓度过低或质量差,失效
合理配用隔离剂
7)胶囊过大
更换合适的胶囊
5
钢丝圈上抽,胎圈过窄,胎圈露线、胎趾局部大边
全钢载重汽车子午线轮胎胎体帘线常见质量问题及解决措施
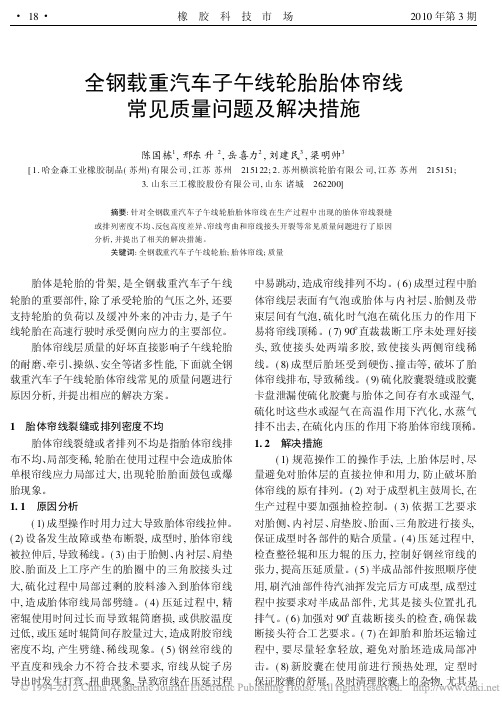
全钢载重汽车子午线轮胎胎体帘线常见质量问题及解决措施陈国栋1,邢东升2,岳喜力2,刘建民3,梁明帅3[1.哈金森工业橡胶制品(苏州)有限公司,江苏苏州215122;2.苏州横滨轮胎有限公司,江苏苏州215151;3.山东三工橡胶股份有限公司,山东诸城262200]摘要:针对全钢载重汽车子午线轮胎胎体帘线在生产过程中出现的胎体帘线裂缝或排列密度不均、反包高度差异、帘线弯曲和帘线接头开裂等常见质量问题进行了原因分析,并提出了相关的解决措施。
关键词:全钢载重汽车子午线轮胎;胎体帘线;质量胎体是轮胎的骨架,是全钢载重汽车子午线轮胎的重要部件,除了承受轮胎的气压之外,还要支持轮胎的负荷以及缓冲外来的冲击力,是子午线轮胎在高速行驶时承受侧向应力的主要部位。
胎体帘线层质量的好坏直接影响子午线轮胎的耐磨、牵引、操纵、安全等诸多性能,下面就全钢载重汽车子午线轮胎体帘线常见的质量问题进行原因分析,并提出相应的解决方案。
1胎体帘线裂缝或排列密度不均胎体帘线裂缝或者排列不均是指胎体帘线排布不均、局部变稀,轮胎在使用过程中会造成胎体单根帘线应力局部过大,出现轮胎胎面鼓包或爆胎现象。
1.1原因分析(1)成型操作时用力过大导致胎体帘线拉伸。
(2)设备发生故障或垫布断裂,成型时,胎体帘线被拉伸后,导致稀线。
(3)由于胎侧、内衬层、肩垫胶、胎面及上工序产生的胎圈中的三角胶接头过大,硫化过程中局部过剩的胶料渗入到胎体帘线中,造成胎体帘线局部劈缝。
(4)压延过程中,精密辊使用时间过长而导致辊筒磨损,或供胶温度过低,或压延时辊筒间存胶量过大,造成附胶帘线密度不均,产生劈缝、稀线现象。
(5)钢丝帘线的平直度和残余力不符合技术要求,帘线从锭子房导出时发生打弯、扭曲现象,导致帘线在压延过程中易跳动,造成帘线排列不均。
(6)成型过程中胎体帘线层表面有气泡或胎体与内衬层、胎侧及带束层间有气泡,硫化时气泡在硫化压力的作用下易将帘线顶稀。
(7)90b直裁裁断工序未处理好接头,致使接头处两端多胶,致使接头两侧帘线稀线。
全钢载重子午线轮胎胎体质量缺陷原因分析及解决措施

关键 词 : 钢 载 重 子 午 线 轮胎 ; 体 ; 丝 帘 线 全 胎 钢
中 图分 类 号 : 6 . 4 +. / 6 U4 3 3 1 3 . 文 献 标 志 码 : B 文 章 编 号 : 0 68 7 ( 0 2 0 — 2 8 0 1 0 — 1 1 2 1 ) 50 9 — 4
波动 , 过 从 原 材 料 控 制 、 工设 计 和 工 艺 控 制 等 方 面 采 取 相 应 解决 措 施 , 有 效 提 高 胎 体 质 量 , 胎体 质 量 缺 陷 率 降 通 施 可 使 低 5个 百 分 点 以 上 , 胎 x 光 检 测 合 格 率 达 到 9. 以上 。 轮 99
31 0
1 2 5 成 型 定 型 压 力 ..
头 质量 ; 控制 胎体 钢 丝 帘 布 的悬 垂 长 度 和存 放 时
间, 防止 大 , 成 胎体 钢 丝帘 线 内抽 。 造 ( ) 际压力 与设 定压 力不 一致 , 型机 扇形 2实 成 块、 中鼓 密 封 差 , 定 型 过程 中 , 形 块 往 中鼓 串 在 扇 风 , 易造 成 定 型 压力 过 高 , 扇 形 块 风压 降 低 , 容 而 发生 胎体 内抽 现 象 , 化 时 胎 体 钢 丝 帘线 伸 张 不 硫 足 , 生 弯 曲现象 。 产
() 1 大卷 钢丝 帘 布 存 放 超期 或 胶 料 粘 合性 能
差 , 丝帘布 接头 开裂 。 钢
() 2 大卷 钢丝 帘布 导开 , 自动 或手 动修边 后余
胶 量 过 多 或 过 少 。 胶 量 过 多 , 丝 帘 布 接 头 处 余 钢
第 5期
黄奉 康 等 . 钢 载 重 子午 线 轮 胎 胎 体 质 量 缺 陷 原 因分 析 及 解 决 措 施 全
全钢子午胎胎体变形(帘线弯曲)分析
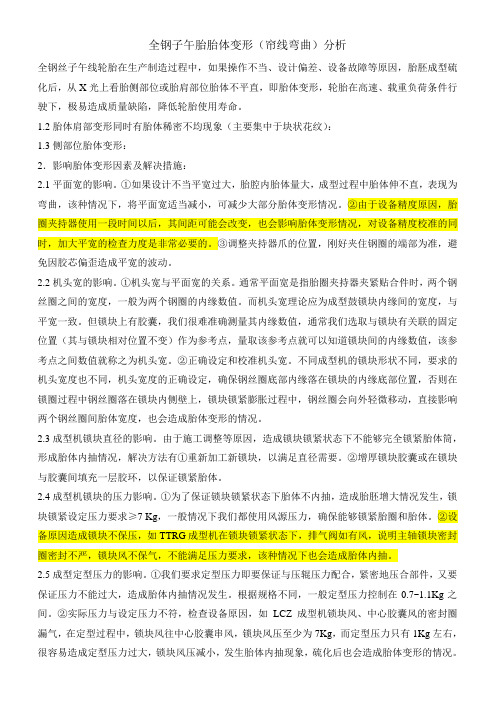
全钢子午胎胎体变形(帘线弯曲)分析全钢丝子午线轮胎在生产制造过程中,如果操作不当、设计偏差、设备故障等原因,胎胚成型硫化后,从X光上看胎侧部位或胎肩部位胎体不平直,即胎体变形,轮胎在高速、载重负荷条件行驶下,极易造成质量缺陷,降低轮胎使用寿命。
1.2胎体肩部变形同时有胎体稀密不均现象(主要集中于块状花纹):1.3侧部位胎体变形:2.影响胎体变形因素及解决措施:2.1平面宽的影响。
①如果设计不当平宽过大,胎腔内胎体量大,成型过程中胎体伸不直,表现为弯曲,该种情况下,将平面宽适当减小,可减少大部分胎体变形情况。
②由于设备精度原因,胎圈夹持器使用一段时间以后,其间距可能会改变,也会影响胎体变形情况,对设备精度校准的同时,加大平宽的检查力度是非常必要的。
③调整夹持器爪的位置,刚好夹住钢圈的端部为准,避免因胶芯偏歪造成平宽的波动。
2.2机头宽的影响。
①机头宽与平面宽的关系。
通常平面宽是指胎圈夹持器夹紧贴合件时,两个钢丝圈之间的宽度,一般为两个钢圈的内缘数值。
而机头宽理论应为成型鼓锁块内缘间的宽度,与平宽一致。
但锁块上有胶囊,我们很难准确测量其内缘数值,通常我们选取与锁块有关联的固定位置(其与锁块相对位置不变)作为参考点,量取该参考点就可以知道锁块间的内缘数值,该参考点之间数值就称之为机头宽。
②正确设定和校准机头宽。
不同成型机的锁块形状不同,要求的机头宽度也不同,机头宽度的正确设定,确保钢丝圈底部内缘落在锁块的内缘底部位置,否则在锁圈过程中钢丝圈落在锁块内侧壁上,锁块锁紧膨胀过程中,钢丝圈会向外轻微移动,直接影响两个钢丝圈间胎体宽度,也会造成胎体变形的情况。
2.3成型机锁块直径的影响。
由于施工调整等原因,造成锁块锁紧状态下不能够完全锁紧胎体筒,形成胎体内抽情况,解决方法有①重新加工新锁块,以满足直径需要。
②增厚锁块胶囊或在锁块与胶囊间填充一层胶环,以保证锁紧胎体。
2.4成型机锁块的压力影响。
①为了保证锁块锁紧状态下胎体不内抽,造成胎胚增大情况发生,锁块锁紧设定压力要求≥7 Kg,一般情况下我们都使用风源压力,确保能够锁紧胎圈和胎体。
全钢载重子午线轮胎胎里拱的原因分析及解决措施

全钢载重子午线轮胎胎里拱的原因分析及解决措施全钢载重子午线轮胎是一种广泛应用于商用车辆的轮胎,其优点包括较高的载重能力、稳定性和耐磨性。
然而,有时候在使用过程中,全钢载重子午线轮胎的胎里会出现拱起的现象,这会影响轮胎的使用寿命和安全性。
下面将对全钢载重子午线轮胎胎里拱的原因进行分析,并提供解决措施。
造成全钢载重子午线轮胎胎里拱的原因可以是多方面的,主要包括以下几点:1.过载:当车辆超载行驶时,轮胎承受的载荷超过其设计承载能力,从而导致胎里拱起。
超载会使胎面产生过大的弯曲变形,从而导致轮胎胎里产生拱起。
解决措施:严格遵守车辆的载重限制,合理分配载荷,避免超载行驶。
2.胎压不准确:过低或过高的胎压都会导致轮胎胎里拱起。
胎压过低会使轮胎承受过大的弯曲变形,导致胎里拱起;而胎压过高会使轮胎胎面的中央部分凸起,同样导致胎里拱起。
解决措施:定期检查和调整轮胎的胎压,确保胎压符合轮胎制造商的建议。
3.不平衡负载:如果车辆的重心不平衡,或者装载物体的重量分布不均匀,会使轮胎承受的载荷不均匀,从而导致胎面出现凹凸不平,甚至出现胎里拱起的情况。
解决措施:合理分配载荷,确保车辆的重心平衡,避免不平衡负载对轮胎造成影响。
4.轮胎过度磨损:当轮胎磨损过度时,胎面的花纹深度减小,轮胎的硬度增加,从而导致轮胎变得僵硬,并容易出现胎里拱起。
解决措施:定期检查轮胎的磨损情况,并及时更换磨损严重的轮胎。
5.使用不当:不正确的驾驶技巧,如急刹车、急转弯或快速加速等,会增加轮胎胎里拱起的风险。
解决措施:掌握正确的驾驶技巧,并遵守交通规则,避免过度对轮胎施加压力。
综上所述,全钢载重子午线轮胎胎里拱起的原因主要包括过载、胎压不准确、不平衡负载、轮胎过度磨损和使用不当等。
为了解决这些问题,我们应该遵守车辆的载重限制,定期检查和调整胎压,合理分配载荷,定期检查轮胎磨损情况,并使用正确的驾驶技巧。
只有采取有效的解决措施,才能保证全钢载重子午线轮胎胎里的正常运行,提高轮胎的使用寿命和安全性。
全钢子午线轮胎肩部帘线弯曲原因分析与改善措施
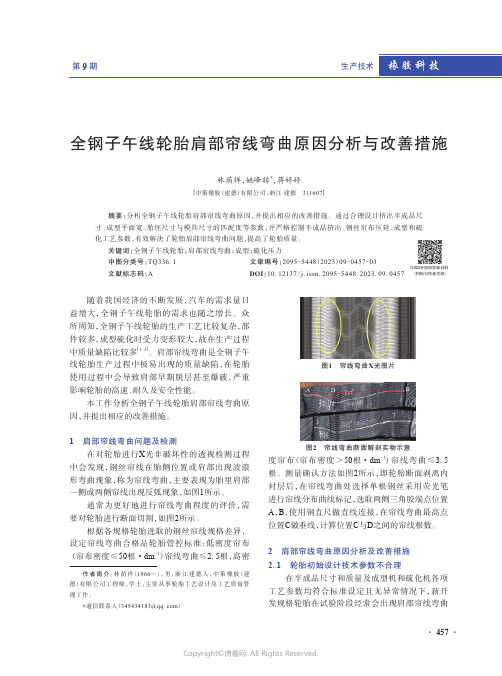
· 457 ·全钢子午线轮胎肩部帘线弯曲原因分析与改善措施林荫祥,姚峰转*,蒋婷婷[中策橡胶(建德)有限公司,浙江 建德 311607]摘要:分析全钢子午线轮胎肩部帘线弯曲原因,并提出相应的改善措施。
通过合理设计挤出半成品尺寸、成型平面宽、胎坯尺寸与模具尺寸的匹配度等参数,并严格控制半成品挤出、钢丝帘布压延、成型和硫化工艺参数,有效解决了轮胎肩部帘线弯曲问题,提高了轮胎质量。
关键词:全钢子午线轮胎;肩部帘线弯曲;成型;硫化压力中图分类号:TQ336.1 文章编号:2095-5448(2023)09-0457-03文献标志码:A DOI :10.12137/j.issn.2095-5448.2023.09.0457随着我国经济的不断发展,汽车的需求量日益增大,全钢子午线轮胎的需求也随之增长。
众所周知,全钢子午线轮胎的生产工艺比较复杂,部件较多,成型硫化时受力变形较大,故在生产过程中质量缺陷比较多[1-3]。
肩部帘线弯曲是全钢子午线轮胎生产过程中极易出现的质量缺陷,在轮胎使用过程中会导致肩部早期脱层甚至爆破,严重影响轮胎的高速、耐久及安全性能。
本工作分析全钢子午线轮胎肩部帘线弯曲原因,并提出相应的改善措施。
1 肩部帘线弯曲问题及检测在对轮胎进行X 光非破坏性的透视检测过程中会发现,钢丝帘线在胎侧位置或肩部出现波浪形弯曲现象,称为帘线弯曲,主要表现为胎里肩部一侧或两侧帘线出现反弧现象,如图1所示。
通常为更好地进行帘线弯曲程度的评价,需要对轮胎进行断面切割,如图2所示。
根据各规格轮胎选取的钢丝帘线规格差异,设定帘线弯曲合格品轮胎管控标准:低密度帘布(帘布密度≤50根·dm -1)帘线弯曲≤2.5根,高密图1 帘线弯曲X 光图片ACD 图2 帘线弯曲断面解剖实物示意度帘布(帘布密度>50根·dm -1)帘线弯曲≤3.5根。
测量确认方法如图2所示,即轮胎断面剥离内衬层后,在帘线弯曲处选择单根钢丝采用荧光笔进行帘线分布曲线标记,选取两侧三角胶端点位置A ,B ,使用钢直尺做直线连接,在帘线弯曲最高点位置C 做垂线,计算位置C 与D 之间的帘线根数。
全钢子午线轮胎中心色线偏歪原因分析及解决措施

Copyright©博看网. All Rights Reserved.57应用技术APPLIED TECHNOLOGY 图1 中心线偏歪图2 定型传递环偏歪二、中心线偏歪原因分析与解决措施半成品胎胚在硫化过程中,由于胎胚本身成型原因或硫化过程原因造成成品胎胎面中心标识偏离轮胎冠部中心线,见图1。
1.传递环精度成型过程传递环精度超出标准,定型后胎冠中心线与成型鼓中心灯标不重合,见图2。
解决措施成型过程中,传递环精度要符合要求。
辅鼓与传递环的径向跳动,手动模式下将传递环移动靠近辅鼓表座固定于轴上,百分表测量杆设置于传递环支撑环内圈上,辅鼓低速旋转一周以上,取此过程中百分表的最大跳动量不超出精度要求。
主鼓与传递环的径向跳动,手动模式下将传递环移至主鼓工作位,表座固定于主鼓上,百分表测量杆设置于传递环瓦块中心,低速旋转主轴一周以上,每片瓦块只检测中心处读书,取此过程中百分表的最大跳动量不超出精度要求。
传递环与定型鼓中心灯标对中度,定型后手动模式下将定型鼓低速旋转一周以上,胎面中心与定型鼓中心灯标对中度符合 要求。
图3 平面宽不对称2.平面宽对称性定型过程中鼓间收缩,中心充气使胎体与辅鼓组合件着合,如果平面宽不对称,会导致胎体中心线与辅鼓组合件不对中,如图3所示。
在成型过程中,虽然看似胎冠中心线与定型鼓中心灯标重合,但是因为平面宽不对称,导致钢圈内间距不对称(a ≠b )胎里中心线与胎面组合件中心线不重合,最终硫化过程中胎面中心线偏歪。
解决措施开班前检查平面宽对称性,超出标准不允许生产,要求设备精度进行校正,合格后,正常生产。
成型过程中还有一些因素可以间接造成平面宽不对称,比如成型过程中,中心充气,同时鼓间收缩,胎体受力会向胎圈内抽入,此时如果两侧钢圈锁紧力不一致,抽入量会不一致,也会造成两侧实际平面宽不对称,虽然在成型检点时,设备的平面宽是对称的,但是实际轮胎生产时,平面宽不对称,最终轮胎中心线偏歪。
全钢载重子午线轮胎肩部帘线弯曲原因分析及解决措施

全钢载重子午线轮胎肩部帘线弯曲原因分析及解决措施
周天明
【期刊名称】《轮胎工业》
【年(卷),期】2004(024)004
【摘要】分析全钢载重子午线轮胎肩部帘线弯曲质量缺陷的产生原因,并提出相应的解决措施.成型参数、挤出半成品尺寸、胎坯外周长和定型压力不当以及生产过程中的压延、挤出、成型、硫化工序出现偏差均会造成肩部帘线弯曲质量缺陷.控制钢丝帘线假定伸张值为1.2%~1.8%,准确制定半成品尺寸和胎坯外周长,一次定型压力设置为0.02~0.04 MPa,严格控制压延张力、成型及硫化工艺等措施均可有效避免肩部帘线弯曲缺陷的产生.
【总页数】4页(P232-235)
【作者】周天明
【作者单位】银川佳通轮胎有限公司,宁夏,银川,750011
【正文语种】中文
【中图分类】TQ330.38+9;U463.341+.6
【相关文献】
1.全钢载重子午线轮胎胎体帘线变形原因分析及解决措施 [J], 岳耀平
2.全钢载重子午线轮胎胎体钢丝帘线锈蚀原因分析及解决措施 [J], 柴德龙;毛建清;张维雁
3.全钢载重子午线轮胎胎肩帘线弯曲原因分析及解决措施 [J], 汪传生;李山虎;仇志刚
4.全钢载重子午线轮胎胎体钢丝帘线间距不均匀的原因分析及解决措施 [J], 张庆辉
5.全钢载重子午线轮胎胎体帘线弯曲原因分析及解决措施 [J], 杨齐;张勋民;曾清因版权原因,仅展示原文概要,查看原文内容请购买。
- 1、下载文档前请自行甄别文档内容的完整性,平台不提供额外的编辑、内容补充、找答案等附加服务。
- 2、"仅部分预览"的文档,不可在线预览部分如存在完整性等问题,可反馈申请退款(可完整预览的文档不适用该条件!)。
- 3、如文档侵犯您的权益,请联系客服反馈,我们会尽快为您处理(人工客服工作时间:9:00-18:30)。
全钢子午胎胎体变形(帘线弯曲)分析
全钢丝子午线轮胎在生产制造过程中,如果操作不当、设计偏差、设备故障等原因,胎胚成型硫化后,从X光上看胎侧部位或胎肩部位胎体不平直,即胎体变形,轮胎在高速、载重负荷条件行驶下,极易造成质量缺陷,降低轮胎使用寿命。
1.2胎体肩部变形同时有胎体稀密不均现象(主要集中于块状花纹):
1.3侧部位胎体变形:
2.影响胎体变形因素及解决措施:
2.1平面宽的影响。
①如果设计不当平宽过大,胎腔内胎体量大,成型过程中胎体伸不直,表现为弯曲,该种情况下,将平面宽适当减小,可减少大部分胎体变形情况。
②由于设备精度原因,胎圈夹持器使用一段时间以后,其间距可能会改变,也会影响胎体变形情况,对设备精度校准的同时,加大平宽的检查力度是非常必要的。
③调整夹持器爪的位置,刚好夹住钢圈的端部为准,避免因胶芯偏歪造成平宽的波动。
2.2机头宽的影响。
①机头宽与平面宽的关系。
通常平面宽是指胎圈夹持器夹紧贴合件时,两个钢丝圈之间的宽度,一般为两个钢圈的内缘数值。
而机头宽理论应为成型鼓锁块内缘间的宽度,与平宽一致。
但锁块上有胶囊,我们很难准确测量其内缘数值,通常我们选取与锁块有关联的固定位置(其与锁块相对位置不变)作为参考点,量取该参考点就可以知道锁块间的内缘数值,该参考点之间数值就称之为机头宽。
②正确设定和校准机头宽。
不同成型机的锁块形状不同,要求的机头宽度也不同,机头宽度的正确设定,确保钢丝圈底部内缘落在锁块的内缘底部位置,否则在锁圈过程中钢丝圈落在锁块内侧壁上,锁块锁紧膨胀过程中,钢丝圈会向外轻微移动,直接影响两个钢丝圈间胎体宽度,也会造成胎体变形的情况。
2.3成型机锁块直径的影响。
由于施工调整等原因,造成锁块锁紧状态下不能够完全锁紧胎体筒,形成胎体内抽情况,解决方法有①重新加工新锁块,以满足直径需要。
②增厚锁块胶囊或在锁块与胶囊间填充一层胶环,以保证锁紧胎体。
2.4成型机锁块的压力影响。
①为了保证锁块锁紧状态下胎体不内抽,造成胎胚增大情况发生,锁块锁紧设定压力要求≥7 Kg,一般情况下我们都使用风源压力,确保能够锁紧胎圈和胎体。
②设备原因造成锁块不保压,如TTRG成型机在锁块锁紧状态下,排气阀如有风,说明主轴锁块密封圈密封不严,锁块风不保气,不能满足压力要求,该种情况下也会造成胎体内抽。
2.5成型定型压力的影响。
①我们要求定型压力即要保证与压辊压力配合,紧密地压合部件,又要保证压力不能过大,造成胎体内抽情况发生。
根据规格不同,一般定型压力控制在0.7~1.1Kg之间。
②实际压力与设定压力不符,检查设备原因,如LCZ成型机锁块风、中心胶囊风的密封圈漏气,在定型过程中,锁块风往中心胶囊串风,锁块风压至少为7Kg,而定型压力只有1Kg左右,很容易造成定型压力过大,锁块风压减小,发生胎体内抽现象,硫化后也会造成胎体变形的情况。
2.6硫化一次定型压力的影响。
硫化机合模前,要在胎胚内充入一定的高压蒸汽对胎胚进行一次定型,如果压力不足则会造成胶囊与胎胚内留有空气,硫化后外胎胎里不平,出现窝气现象。
但压力过大,生胎在短时间内就会在高压蒸汽的作用下,胎胚形状增大,合模后也会造成胎体变形情况。
一般情况下,可控制一次定型压力在0.8~1.2Kg之间较为合适,尤其是一次定型压力是由操作工手动进行调节,一定要加强其培训,必须要保证压力在工艺要求范围内。
2.7胶部件尺寸的影响。
如胎面肩厚、肩下厚度不足,成型过程胎肩部位缺少材料,硫化后从X 光上看表现为胎体变形,同时伴随有花纹块间稀线情况,该种情况下,适当调整胎面施工(主要为胎面肩下厚度)尺寸,即可解决胎体变形情况。
2.8胎侧反包不到位,胎肩部位缺少材料的影响。
尤其对边部横向块状花纹来说,更易因肩部缺少材料而导致变形和胎体间断稀密现象发生,所以适当控制肩部材料也可减少胎体变形情况出现。
①如是胶囊反包,在不调整胎侧子口宽度的情况下,可改用小反包胶囊进行反包。
如是机械鼓反包则增加束紧胶带数量,或减小支撑伞反包压力等措施,有效地拉伸胎侧,确保反包到位。
②适当调整胎侧子口宽度,确保反包到位。
③反包胶囊或反包伞漏风,也可造成局部胎侧反包不到位情况,及时修补胶囊或更换主轴密封圈。
④机械鼓反包时,鼓间宽度调整太大,也会造成反包不到位情况,在不影响其它质量情况下此时可调小数值,也将有利于胎侧反包到位.
2.9定型宽度太大的影响。
①空车进行测量,将机头缩至定型宽度,此时其值如超出工艺要求值,按要求重新调整到位即可。
②空车测量值(机头宽、预定型、定型)是对的,但负荷(成型轮胎)以后其值可能会增大,即鼓收缩不到位。
检查方法是压合完胎侧后手动进行卸胎,此时鼓间宽度即为定型宽,测量其值与标准值相比,如大了说明主轴有机械故障,打开主轴机箱,查看紧固螺丝是否松动、编码器、离合器是否正常等。
2.10压合的影响。
就目前而言,笔者只发现在625所研制开发的LCZ一3型全钢丝载重子午胎一次法成型机机型上发现有胎侧部位胎体变形情况,从X光图像上可以清楚地看到,变形多为三角胶芯边部胎体钢丝打弯现象,分析主要与反包形式有关,LCZ属反包臂(辊直径较小,只反包不压合)反包,为了确保胎侧反包顺畅、到位,主轴转数相当高,离心力很大,加之反包臂高压压合三角胶芯,过程中产生的侧向力较大,对胎体的冲击也相对较大,而其它机型压合胎侧和三角胶芯时多为圆盘辊,直径较大,对胎体冲击也较小,这也是其它机型胎侧部位胎体变形较少的原因。
解决的方法是可适当降低主轴转数、反包臂压力或减小胶芯径向压合距离等。