精益教材
精益生产现场管理培训教材

生产活动的6条基本原则
(4)作业的标准化 有作业指导书,作业基准书,不是标准化 标准化是作出规定,遵守而且改善这个规定,不停地进行改善---遵守 ---再改善的活动才可称为标准化 (5)有附加价值的工作 管理的目的是谋求更大的附加价值(利润最大化) 现场要有大局观,辨别生产瓶颈,采取最优对策 (6)积极应对变化 基本要求------决定标准书等作业的基本,养成遵守的习惯 先观察------事前收集情报,再采取下一步措施 掌握实力------提高技能和扩大实力,提高设备稼动率等
34
生产统计方法
(1)内容:产量,投入的资源。生产合格率,不良率,直通率, 生产性。
(2)要求:在规定的时间内完成(及时性),真实性。
(3)各级管理人员的总结:
◎ 生产数量
◎ 品质,生产合格率,不良率,直通率
◎ 人员状态。出勤率,违纪,出差错
◎ 生产事故,损失工时
◎ 物料供给状态
◎ 机器设备问题
◎ 技术,工艺问题
15
现场管理的实施方法
(4)自主管理
◎ 以给自己做事的心态工作 ◎ 自负其责,在符合标准的情况下自己拿主意 ◎ 不推卸责任 ◎ 以自我为根本,完成工作任务
16
什么是麻将精神?
一、随叫随到,从不拖拖拉拉; 二、不在乎工作环境,专心致志; 三、不抱怨,经常反省自己,唉又错了! 四、永不言败,推倒重来; 五、牌好牌坏都努力往好的方向整; 六、不管跟谁搭档,照样努力; 七、对于工作中使用的工具从不挑剔; 八、最主要的是从不嫌弃工作时间长!
3
4
现场管理的金科玉律
◆ 当问题(异常)发生时,要先去现场 ◆ 检查现物(有关的物件) ◆ 把握现状(表现出的特征) ◆ 当场采取暂行处理措施 ◆ 发掘真正的原因并将它排除 ◆ 标准化以防止再次发生
精益生产(TPS)培训教材

丰田生产管理方式第一次授课§1—1.企业经营与成本:利润=售价—成本为了提高利润:(1)提高售价 (售价由市場規律决定,提高售价就会卖不出去)「售价=成本+利润」⇒成本主义是行不通的(2)降低成本(成本的三要素:经费、劳务费、材料费)利润=售价—成本(3) 企业不断降低成本的方法彻底的消除浪費,从而降低成本,提高利润。
§1-2.物品製造和成本:* 成本的3要素:材料费、劳务费、管理费*分析成本才能发现哪些是不必要的成本:1.生产出的不良品2.过多的库存3.设备在等待4.不必要的物流5.不必要的作业6.员工在等待等等……*降低成本的方法:①排除浪费②降低原材料采购的价格③降低费用的开支④提高效率⑤缩短生产周期⑥排除人的浪费§ 1-3.什么是丰田生产方式:何谓丰田生产方式:丰田生产方式就是以彻底排除浪费为目标,致力于降低成本,如何做的便宜等一切车间的实践活动的统称。
它是从大批量的生产方式转变为JUST IN TIME(将必要的东西,仅仅是必要的量,在必要的时候进行生产)的生产方式.在最短的生产期间内,挑战由于自动化而实现省人化,到设备的最适化所采用的手法的总称。
§ 1-4.什么是丰田生产方式:丰田生产方式的两大支柱:(1)丰田佐吉翁的带“イ”旁的自动化即:问题显在化的看得見管理+自动化,不是单纯的把人的工作交给机器去做,而是能自动检测不良,发现不良时能自动停止,不向下工程提供不良品.(2)丰田喜一郎的“Just in time”即:“必要的物品、在必要的時候、按必要的量生産”。
* 由大野耐一汇集成“丰田生产方式”§ 1—5.丰田生产方式的目的:1、丰田生产方式的目的:彻底消除浪费为目标,致力于降低成本。
具体地説是追求以下四項為零:①Lead time為0 ―→缩短加工周期(加工时间+停滞时间=工場内的加工周期)②工数的浪费為0―→进行动作和作业的改善③设备的浪费為0―→设备减少+小型化+最适合化④品质的浪费為0―→加工时进行检查,发现不良立即停止例: <加工周期〉加工时间:停滞时间丰田 1 : 300优良企业 1 : 5000亏损企业 1 : 100002、培养发现浪费的眼睛:*发现浪费的第一步就是到现场!!!§ 2-1.车间改善的必要性:§ 2-2.车间的浪费:1、浪费的定义:不能产生利润的行为.首先最重要的是要认识浪费:增加成本的各个要素“一旦认为是浪费,就立刻废除"这种姿态对于在职场里工作的我们来说非常重要*怎样排除动作的浪费:1.明确取放顺序2.明确是左手还是右手拿取方便3.物品不要放得过远4.工具不要迟延§ 2-3.时效分析*标准与改进由于有称为“标准"的比较基准,问题就明确了,由于问题明确了,就有了改进和提高效率·评价1.评价将作业者进行的作业速度与标准速度进行比较,用百分比表示的数值2.评价的目的a、用于标准时间根据时效研究,修正所得的时间值并作成作业标准时间值找到指导作业\改进作业的着眼点具备了效率评价能务,则明白了标准作业速度;明确了指导作业的要点产生向目标靠拢的愿望b、评价训练:观看训练用电影\录像,培养评价工作能力考虑作业的困难程度,是仅用手来进行的作业,还是使用整个身体来进行的作业以100%作业标准速度若感到比标准速度快,则有105,110,120等大数值若感到比标准速度慢,则有95,90,85等小值反复训练\修正自己的基准,争取在一定时间内,对一定的作业能正确评价的工作能力。
精益生产与现场管理教材
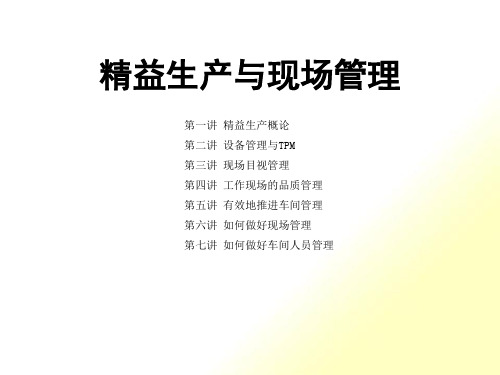
Fluctuations in work schedule 工作方案的波动
Current Process Methods:目前的工艺方法
Using unchallenged and unimproved processes使用没 有挑战性和开展性的工艺方法
4. 精益意识培养
1. 何谓精益?
回忆制造业的历史
手工艺
• 只是根据客户规格生产 • 单件生产…每个产品是唯一的 • 变化的质量 • 小库存 • 高成本…为富人生产
大规模
• 互换部件 - Whitney • 劳动力分工 - Taylor • 装配线 - Ford • 低变异 - Ford • 劳工斗争
Frederick Taylor
2. 新的观点:在这一连续的工序流程中,其中必有一处会成为瓶 颈。如果企业能够着眼于这个瓶颈进行改善的话,将会取得明 显的效果。相反,无论你对瓶颈外的任何工序投入多大的费用 进行改善,也不见得会有效果。
要动则动,该停则停,则效率最高
负荷率与可动率
• 拴在柱子上的驴和在拉磨的驴都同样在动,消耗了 相同的能力,但结果……。
精益Lean
• 高度多样化 • 小批量 • 六西格玛质量 • 参与 / 授权的劳动力
1875 1900 1925 1950 1975 2000
From JIT To TPS To Lean
1943 - 1978
1978
S h in g iju ts u
1992
1996
Lean
典型的精益定义
• 什么是精益? • 精益生产旨在于生产的各个区域排除浪费,包
工序时间 5 4 3 2 1
① ② ③ ④ ⑤ ⑥ 工序
JIT精益生产实务教材

4、标准在制品
为了使生产活动能够重复地持续下去,必须在生产 线内保持有一定的在制品。
有时为了质量检查或下工序加工条件的需要,也必 须设定一定数量的在制品。
如:降温或干燥之后进行下工序加工等。
标准在制品
成品 材料
劳动生产效率=
例
上月:需求 1000台/日 本月:需求 800台/日
工序 10个
工序 10个
人员 10人
人员 8个
问题点:1个工序1个操作者,减员不可能
着眼点:抛弃单一工序操作、定岗定员观念 实行多岗位操作、非定员制观念
7、多工序操作
适合 特点
单工序操作 大批量生产 一人一岗、专业操作 人员作业适应性差 生产及人员难调整 操作者易失去积极性 有时能达到省人化目的
9
8
作业顺序与加工物
7
流同向时:工序间需要1
个在制品。
6 作业顺序与加工物
流逆向时:工序间不需 要在制品。
5、非标准作业处理
标准作业
生产安定化
标准作业
Байду номын сангаас
非标准作业
线上操作者负责 线外“水蜘蛛”负责
对“水蜘蛛”来说 是标准作业
全体标准作业
“水蜘蛛”
将生产岗位的非标准作业内容抽出来,作为 “水蜘蛛”的标准作业内容,以每次供应一套均 衡物料的方式保证生产线的持续作业。
“水蜘蛛”必须动作迅速,头脑清醒灵 活,掌握生产线的瞬间变化并能采取对应措 施。一般有一线骨干或后续一线干部担任。
6、少人化
少人化
用最少的人数、用最低的 成本生产市场需要的产品数量。
精益生产培训教材(PPT 41页)
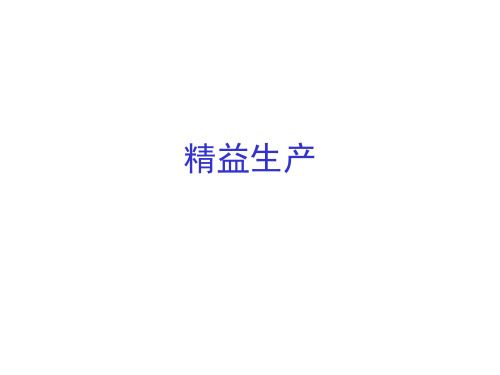
The Job
工 作
Time Fluctuation 时间波动
Job Element Sheet 工作要素单
Element 1 要素 1
Job Element Sheet 工作要素单
Element 2 要素 2
Job Element Sheet 工作要素单
Element 3 要素 3
Job Element Sheet 工作要素单
TIME FLUCTUATION WORKSHEET 时间波开工作单 JOB ELEMENT SHEET 工作要素单 TIME MEASUREMENT SHEET 时间测量单
STANDARDISED OPERATIC THEET 标准作业单
Quality Process Sheet
Department/ Welding 05
精益生产
课程内容
• 定义 • 产生与开展 • 特点与优越性 • 核心内容与生产要素 • 标准化介绍 • 最终目的
什么是精益生产?
• 精益生产是 通过系统结构、人员组织、运行方式和市 场供求等方面的变革,使生产系统能很快适应用户需 求不断变化,并能使生产过程中一切无用、多余的东 西被精简,最终到达包括市场供销在内的生产的各方 面最好的结果。
Worksheet
#
5-140
Opr
WGL
Page__1__ of__1__
Sup
Maint
Eng
3302246
QC QUICK
CHANGE OVER
VISUAL FACTORY
FORD Total Prod.T
F
M
Maint.
P
ERROR PROOFING D
精益管理基础培训教材

精益管理基础培训教材1. 引言在当今竞争激烈的商业环境中,企业需要不断提高运营效率和质量,以确保其在市场中的竞争力。
精益管理是一种管理理念和方法论,通过消除浪费和提高价值创造,帮助企业实现持续改进和优化。
本教材将介绍精益管理的基本原则和工具,以帮助员工在工作中应用精益管理的方法。
2. 精益管理概述2.1 精益管理的定义精益管理是一种以客户价值为导向、通过不断消除浪费来提高效率和质量的管理方法。
它源于丰田汽车公司的生产方式,其核心思想是追求零缺陷、零库存和零浪费的生产。
2.2 精益管理的基本原则精益管理的基本原则包括价值流分析、流程优化、拉动生产、零缺陷、持续改进和员工参与。
这些原则指导着企业在实施精益管理时应遵循的行动和方向。
3. 精益管理工具和技术3.1 价值流分析价值流分析是精益管理中的一项关键工具,用于识别在价值创造过程中存在的浪费和瓶颈。
通过绘制价值流图,企业可以清楚地了解价值创造流程中的每个步骤和环节,并找出改进的机会。
3.2 连续流程改进连续流程改进是精益管理中常用的技术之一,旨在通过不断追求卓越,实现流程的优化和改进。
它涵盖了从设定目标到识别改进机会、推动改变并评估效果的整个过程。
3.3 5S整理法5S整理法是一种通过整理、排序、清洁、标准化和素养维护来改善工作环境和工作效率的方法。
它可以帮助企业消除工作中的浪费、提高工作效率、减少错误和提升员工参与度。
3.4 拉动生产拉动生产是一种基于客户需求来驱动生产的方法。
通过按需生产和减少库存,企业可以降低库存成本、提高交货速度、减少缺货风险,并实现更高的客户满意度。
3.5 六西格玛六西格玛是一种以减少缺陷和变异为目标的管理工具。
它通过收集和分析数据来识别和解决问题,使企业可以在质量和流程上实现持续改进。
4. 精益管理的实施步骤4.1 确定目标和关键绩效指标在实施精益管理之前,企业需要明确其目标,并定义衡量绩效的关键指标。
这将为企业提供明确的方向,并帮助监控和评估改进的成果。
精益生产培训教材(PPT 81页)
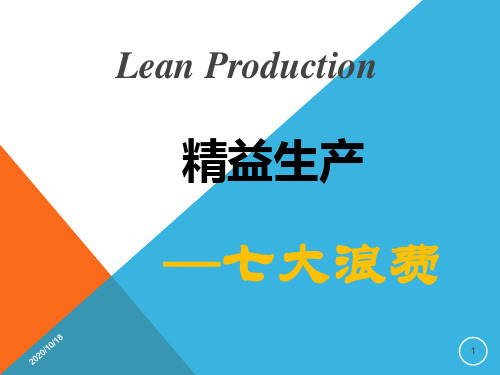
21
What do Banana have to do with Waste?
香蕉与浪费有何关系?
22
Work that increases value = Fruit
增加价值的工作=果肉
Work that increases cost = skin
增加成本的工作=果皮
23
“就象没有人会真正抱怨花钱买香蕉皮一样, 我们也不会怀疑在生产现场发生的事。即使当 多数的工作只增加成本而不增加价值时,我们 也习惯了这种情况,并对工作正在被完成表示 满意。我们常常不会觉察到工作内在的价值。 我们必须认真仔细地观察一下我们的工作,并 且,辨认出哪些是果肉,哪些是果皮。”
18
Defects / Rejects / Re-work 残次品、退货及返工
19
看不见的浪费
原材料
成品给客户
库存海掩盖各种浪费
20
最大的浪费 ?!
“We must keep in mind that the greatest waste is waste we don’t see”
“我们必须时刻牢记,我们看不到 的浪费才是最大的浪费。”
Jidoka 自働化
Heijunka平准化, 3P, TPM Work-Out 标准作业Standardized Work, 改善Kaizen 通过不断消除浪费, 以降低成本、提高质量(5S, 7 wastes)
3
市场竟争改变了利润方程式
Old Way 旧公式
成本 + 利润 = 市场价格
New Way 新思维
市场价格 – 成本 = 利润
4
七大浪费
1. Transportation搬运浪费 2. Inventory 库存浪费 3. Motion 动作浪费 4. Waiting 等待浪费 5. Over production 过量生产 6. Over processing 过度加工 7. Defects 产品缺陷(不良品)
精选精益生产培训教材PPT144页
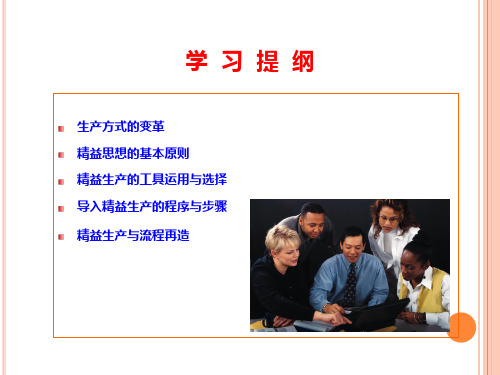
丰田生产方式硬环境 整合
5S
看板管理 均衡化 一个流
作业切换
JIT 品质保证 标准作业
多能工
目视管理 设备保养 柔性化
少人化
日本企业的精益生产状况
1950年起,电子行业:独创项目管理与短产品周期——仅仅有三菱公司实验过。 大部分企业——美国过去的:统计质量控制概念、QC手法、PDCA、QCC、QFD等。 ——1960年,日产公司获得“戴明奖” ——丰田采用TQM,1965年获得“戴明奖” (丰田生产模式与TQM结合,是丰田的优势) ——1973年能源危机,大部分企业亏损,而丰田盈利。三菱全面实施丰田模式,马自达、
I
C /T = C /O = U p tim e = L o t S iz e =
注:
C/T -周期时间 C/O -换型调整时间 Uptime -工时利用率 Qty -数量 Lot Size -批量
LT -- 交货周期 MCT -制造周期
VA -增加价值的时间
In s p . L a b e l
Pow er Assy
学习提纲
生产方式的变革 精益思想的基本原则 精益生产的工具运用与选择 导入精益生产的程序与步骤 精益生产与流程再造
第一章 生产方式的变革
手工生产
低产量 个性化
大规模生产同步生产精益 Nhomakorabea产组织大批量少品种 工序式生产 设备大难组合
消除浪费 不断改进 员工参与
在同步生产的基础 上,强调缩短生产 周期提高资源利用 率需求驱动
内部工艺工程
XYZ Corporation
外部资源
C/T = 45 sec C/O = 30 mins 3 Shifts 2% Scrap
精益生产概念理论培训教材
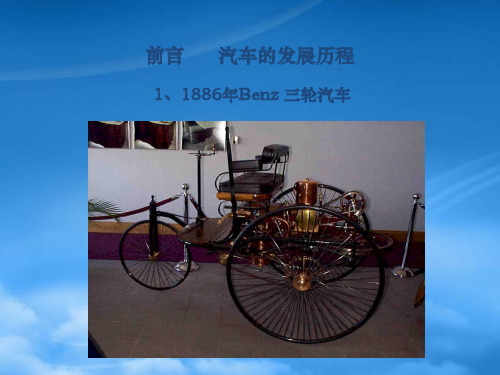
前言 汽车的发展历程
2、1890年,Sakichi Toyoda 获得了木制纺织的专利,由于市场 竞争的压力及需要,改善(KAIZEN)这种哲学思想应运而生。“没有任何机器或生产流程是不可以被改善和提高的” - Sakichi Toyoda
3、1894年Benz四轮汽车
4、1899年法国Quadricycle
5、1901年美国 Oldsmobile
6、1908年,亨利福特发明了移动式汽车装配流水线,并且将工人的 工资提高到每天5美元,这大大的提高了生产率和员工积极性。自 此,一种连续型的生产模式诞生了。 “ 我们要让所有的东西动起来,也就是让东西沿着人移动, 而不是让人随着东西运动,这就是我们最基本的观念,流水线的传 送带仅仅是众多的手段之一。 - 亨利福特:“今天和明天”
手工、大批量、精益三种生产方式的比较
序号
生产方式项目
手工生产方式
大批量生产方式
精益生产方式
1
产品特点
完全按顾客ห้องสมุดไป่ตู้求
标准化品种单一
品种多样、系列化
2
设备和工装
通用、灵活、便宜
专一、高效、昂贵
柔性高、效率高
3
分工与作业内容
粗略、丰富多彩
细致、简单、重复
较粗、多技能、丰富
4
操作工人
懂设计制造、具有高操作技艺
四、精益生产的核心
五、手工、大批量、精益三种生产方式比较
1、在精益生产方式诞生前,存在过手工生产方式及大批量生产方式。 ■ 19世纪末,法国巴黎Panhard-Levassor机床公司制造汽车,它采用的是一种 典型的手工生产方式。几乎没有两辆车是相同的! ■ 第一次世界大战后,以美国福特汽车公司为代表的大批量生产方式逐步取代以 欧洲企业为代表的手工生产方式; ■ 第二次世界大战之后,以日本丰田汽车公司为代表的精益生产方式又逐渐取代 大批量生产方式(福特公司长达10年时间只生产T型车。它的生产设备没有柔 性,如果改变品种,不仅耗资巨大,而且要停产1年!)。2、如此看来,任何一种生产方式都有一个产生、发展与衰退的过程。每种生产方式 有其特点,也有其缺陷。当社会发展到具备使某种生产方式的优势得以充分发挥 的条件时,该生产方式就占统治地位;当条件发生了变化,其优势得不到发挥或 得不到充分发挥,而缺陷成为适应市场变化的主要障碍时,这种生产方式就会衰 退。3、发展是永恒的,大批量生产方式否定了手工生产方式;精益生产方式又否定了大 批量生产方式。比较三种生产方式,精益生产方式综合了手工生产方式和大批量 生产方式的特点,克服了两者的缺点,成为新形势下最有生命力的生产方式。
精益生产培训教材

3 Shifts TAKT Time CT = C/O Time = DT = Scrap / Rework = # Operators WIP =
# Material Handlers Max Size 2 Shifts 0 Overtime
分析当前状态 设计将来状态
C/O Time = DT = Scrap = WIP =
课程一: 课程一:
精益生产概论
精益生产的发展历史
福特生产系统 •生产线大量生产 •大批量标准化产品 •工人掌握单一技术 丰田生产系统(TPS) 丰田生产系统(TPS) (TPS •JIT生产(按客户需求品种和数量准时生产) •拉动生产 •强调生产数量和库存数量与市场匹配 •按照客户需求定制产品
精益生产的发展历史
消除浪费的四步骤
第一步: 第一步: 了解什么是浪费 了解什么是浪费
第二步: 第二步: 识别工序中哪里存在浪费 识别工序中哪里存在浪费
第四步: 第四步: 实施持续改进措施 实施持续改进措施, 持续改进措施, 重复实施上述步骤
第三步: 第三步: 使用合适的工具来消除 使用合适的工具来消除 已识别的特定浪费
精益生产既是一种以最大限度地减少企业生产所占用的资 源和降低企业管理和运营成本为主要目标的生产方式,同 源和降低企业管理和运营成本为主要目标的生产方式, 时它又是一种理念,一种文化。实施精益生产就是决心追 时它又是一种理念,一种文化。 求完美的历程,也是追求卓越的过程。 求完美的历程,也是追求卓越的过程。
1985年美国麻省理工学院组织了世界上14个国家的专家、 学者,花费了5年时间,耗资500万美元,对日本等国汽车 工业的生产管理方式进行调查研究后总结出来的生产方式, 在日本称为丰田生产方式。
精益生产工具实战培训教材
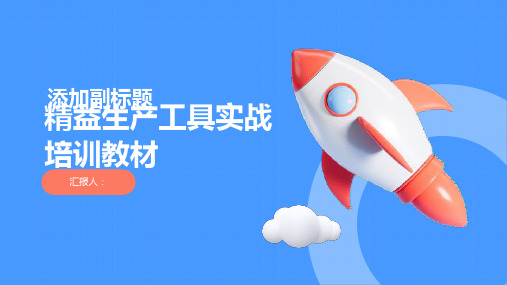
制作看板:根据设计内容,制作看板,确保看 板的清晰、易读。
安装看板:将制作好的看板安装到相应的位置, 确保所有人都能够方便地查看。
维护看板:定期对看板进行维护,确保数据的 及时更新和准确性。
看板管理应用范围
生产现场管理:用于实时掌握生产进 度、品质状况等信息
精益生产工具
价值流图:识别浪费和改进机 会
5S管理:保持现场整洁有序
目视化管理:直观展示信息, 提高工作效率
持续改进:不断寻求改进机会, 提高生产效率和质量
5S管理实战培训
5S管理定义
整理(Seiri):区分要与不要的物品,将不要的物品处理掉 整顿(Seiton):将需要的物品分类放置,保持整齐有序 清扫(Seiso):定期清扫工作场所,保持干净整洁 清洁(Seiketsu):维持清洁状态,防止污染和不良现象的发生 素养(Shitsuke):培养员工良好的工作习惯和职业素养
通过减少资源消耗来提高效益
添加标题
添加标题
添加标题
添加标题
强调消除浪费、持续改进和顾客需 求导向
实现企业价值最大化
精益生产原则
消除浪费:识别并 消除生产过程中的 浪费,提高生产效 率
持续改进:不断寻 求改进机会,持续 优化生产过程
尊重员工:重视员 工的建议和意见, 激发员工的积极性 和创造力
客户需求导向:以 客户需求为导向, 提高产品质量和客 户满意度
销售流程:从 客户询价到合 同签订、订单 处理、发货和
收款等环节
采购流程:从 供应商选择到 采购计划、订 单下达、验收
入库等步骤
库存管理流程: 财务管理流程:
- 1、下载文档前请自行甄别文档内容的完整性,平台不提供额外的编辑、内容补充、找答案等附加服务。
- 2、"仅部分预览"的文档,不可在线预览部分如存在完整性等问题,可反馈申请退款(可完整预览的文档不适用该条件!)。
- 3、如文档侵犯您的权益,请联系客服反馈,我们会尽快为您处理(人工客服工作时间:9:00-18:30)。
3
何谓精益生产方式
Lean Production
精益生产
1960年代开始,以丰田为代表的日本汽车 制造业通过实施JIT生产模式,以低成本、高 质量的突出优势迅速占领美国汽车市场,引发 了美日之间长达十年的汽车贸易战。 JIT——因其经营效率极限化被美国学者 赞誉为“精益生产”,并对人类的生产革命产 生了长远影响。
全员现场5S活动 ·观念革新 · 全员改善活动
7
企业有效运营过程:
观念 革新 薪酬 体系
管理 创新 管理运营
业务 流程 现场 5S 高效 组织 工作 质量 目标 管理 统计 系统 有效 激励 改善 工具
团队 学习
8
精益生产之“心”、“技”、“体”:
转变思想观念
运用改善工具
持续全员实践
9
精益生产追求的目标
26
全面生产系统的浪费
什么是浪费:
不增加价值的活动,是浪费; 尽管是增加价值的活动,所用的资源超过 了“绝对最少”的界限,也是浪费。
27
全面生产系统的浪费
生产要素的5MQS: Man(人) Machine(机器) Material(物料) Method(作业方法) Management(管理) Quality(品质) Safety(安全)
步行、放置、大幅度 的动作 物料搬运的浪费
3 4
动作的浪费 搬运的浪费
动作的浪费 搬运步行的浪费
32
工厂中常见的 8大浪费
NO 5 6 制造现场的 浪费 库存的浪费 制造过多的 浪费 等待的浪费 说明 成品、中间品、原材 料的库存浪费 在不必要的时候制造 不必要的产品 人、机械、部件在不 必要时发生的各种等 待 管理本身成为一种专 职的工作发生的浪费 管理部门的浪费 超前储备的浪费带 来大量的管理浪费 超前预计市场的结 果 等待的浪费
精益生产
课程大纲
精益生产概论
认识浪费(Muda)
消除浪费(Muda) 精益生产方式的基础 两种(Push&Pull)生产系统 看板管理
精益生产之现场IE
一个流生产
快速产品切换
2
第一章 精益生产概论
何谓精益生产方式 现代生产组织系统 精益生产追求的目标 制造业是“服务业” 精益生产实施过程全貌 精益生产案例
”目标
与传统的大批量生产相比,精益生产只需要一半的 人员、一半的生产场地、一半的投资、一半的生产周期、 一半的产品开发时间和少得多的库存,就能生产质量更 高、品种更多的产品。
13
制造业是“服务业”
制造业
以生产企业为主导 批量生产 设法增加产量
服务业
以消费者为主导 个性化服务 追求消费者满意
14
制造业是“服务业”
4
何谓精益生产方式
Just In Time
适品 ·适量 ·适时
JIT的基本思想是:只在需要的时候、按需要 的量、生产所需的产品,故又被称为准时制生产、 适时生产方式、看板生产方式。 JIT的核心是:零库存和快速应对市场变化。 精益生产不断消除所有不增加产品价值的工 作,所以,精益是一种减少浪费的经营哲学。
35
3、动作的浪费
物品取放、反转、对准…… 作业步行、弯腰、转身…… ……
36
常见的12种动作浪费
•两手空空; •单手空闲; •作作业动作停止; •动动作太大; •左右手交换; •步行多; •转身角度大; •移动中变换“状态”; •不明技巧; •伸背动作; •弯腰动作; •重复不必要动作。
37
4、搬运的浪费
7个“
零
”
目标
☆ 零切换浪费 ☆ 零库存 ☆ 零浪费 ☆ 零不良 ☆ 零故障 ☆ 零停滞 ☆ 零事故
10
精益生产追求的目标
零目标 目的 现 状 思考原则与方法
零 切换 浪费
多品种 切换时间长, 对应 切换后不稳定
7个“
零 库存 零 浪费
发现 真正 问题 降低 成本
零
“地下工厂”浪 费严重,似乎无 法发现、无法消 除
零目标 目的 现 状 思考原则与方法
零 不良
质量 保证
7个“
零 故障 零 停滞
生产 效率
零
低级错误频发, 不良率高, 批量事故多发, 忙于“救火”
故障频繁发生, 加班加点与待工待料一 样多
”目标
· 三不主义 · 零缺陷运动 · 工作质量 · 全员质量改善活动 · 自主研究活动 · 质量改善工具运用
· 效率管理 · TPM全面设备维护 · 故障分析与故障源对策 · 初期清扫与自主维护 · 同步化、均衡化 · 生产布局改善 · 设备小型化、专用化
产品质量
所适应的 市场时代
低
极少量需求
高
物资缺乏、供不应 求
更高
买方市场
6
现代生产组织系统
精益工厂 挑战七零极限目标
柔 性 生 产 系 统 TQM 精 益 质 量 保 证 生 产 与 物 流 规 划 TPM 全 面 设 备 维 护
产 品 开 发 设 计 系 统 现 代 IE 运 用
均 衡 化 同 步 化
搬运是一种不产生附加价值的动作; 搬运的损失分为放置、堆积、移动、整 理等动作浪费。
物品移动所需要的空间浪费; 时间的耗费; 人力、工具的占用。
38
5、库存的浪费(含中间在制品)
库存量越多,资金积压越大。 库存包括:
• • • • • 零部件、材料的库存 半成品的库存 成品的库存 已向供应商订购的在途零部件 已发货的在途零部件
20
案例
习惯 素养
5S
6SK
整理
整顿
清扫
清洁
健康
21
第二章 认识浪费(Muda)
不同的经营思想 每天都在“烧”钱 全面生产系统(5MQS)的浪费 工厂中常见的8大浪费
22
不同的经营思想
成本中心型: 以计算或实际的成本为中心,加上预先设定 的利润,得出售价。 计算公式: 售价=成本+利润 卖方市场;消极被动; 企业类别: 高新产品 垄断产品 国内的铁路、民航等
项 目 生产企业主导 少品种 多生产一些好 多品种 消费者主导 量大固然好, 品种也重要 P(品种)
Q(质量)
防止投诉
不良不可避免 体系,全检或 零缺陷免检
将“干毛巾拧出 水”,消除浪费
C(成本)
按成本定价 成本+计划利润
低价格
D(交货期) 月单位交货 每月集中出货 S(安全) 生产优先 先保证出货, 安全嘛……
23
不同的经营思想
售价中心型:
以售价为中心,当市场售价降低时,利润 随之减少。 计算公式:利润=售价-成本
市场好时有较高的利润;市场差时利润大 幅度降低; 企业类别:
缺乏改善意识的企业
24
不同的经营思想
利润中心型:
以利润为中心,当市场售价降低时,成本也必须 降低,以便获得的利润(目标利润)不会减少。 计算公式:成本=售价-利润
1. 大型机械的浪费 2. 通用机械的浪费 3. 传送带的浪费 4. 压缩机的能力过剩 5. 故障的浪费
5MQS的浪费
分类 作 业 方 法 的 浪 费 浪费 1. 批量加工的浪费 2. 库存的浪费 3. 搬运的浪费 4. 放置(停滞)的浪费 5. 等待的浪费 6. 不平衡的浪费 1. 资料的浪费 2. 会议的浪费 3. 管理的浪费 4. 通信的浪费 5. 工作单的浪费 说明 由于批量生产造成的浪费 库存本身就是浪费 设备布局的浪费 工序过于细分化造成的浪费 能力不平衡造成的各种等待、停滞 流程混乱造成的浪费 资料不用便是浪费 会议本身的目的不明确就是浪费 管理是浪费,目标、职责不清 信息的目的性不明确就是浪费 工作单的编制填写确认保管就是浪 费
张惠妹 徐小凤 金 庸
韦小宝 F4 拉 登
多技能员工
○ ● ● ○
萨达姆 吕不韦
备注:△—计划学习,○—基本掌握,◎—完全掌握,●精通
19
案例
QC小组活动
Quality Control Cycle
针对主要的质量问题,由10名左右相关人员组 成改善小组,运用PDCA循环和质量改善工具,自主 进行不良分析并实施具体改善的质量活动。 推行QC小组活动的意义有: ● 通过小组式的学习型组织, 提高一线员工独立思考和相互启发的能力 ● 通过QC手法的学习与运用, 加强企业的基础管理 ● 通过循序渐进的课题活动, 创造有活力的工作场所 ● 发挥群众智慧,全员参与经营
S
安 灾害与事故的防止 全
安全的疏忽是对人、对社会最大的 危害,安全第一
31
工厂中常见的 8大浪费
NO 制造现场的 浪费 不良的浪费 说明 制造不良的浪费,之 后还有进行检测的浪 费 管理部门的浪费 低可靠性带来的各 种事中、事后的浪 费 作业浪费
1
2
加工的浪费
MUDA
与产品价值核心的功 能不相关的加工与作 业都是浪费
12
缩短 交货期长、延迟交货多 交货期 顾客投诉多, 加班加点、赶工赶料
精益生产追求的目标
零目标 零 事故 目的 安全 保证
7个“
零
现
状
思考原则与方法 · 安全第一 · 5S活动 · 危险预知训练 · 定期巡查 · 安全教育活动 · 安全改善活动
忙于赶货疲于奔命, 忽视安全事故频发, 意识淡薄,人为事故多
28
5MQS的浪费
分类 人 的 浪 费 材 料 的 浪 费 设 备 的 浪 费 浪费 1. 行走的浪费 2. 监视的浪费 3. 寻找的浪费 4. 动作的浪费 5. 职责不清的浪费 说明 走一步一秒的浪费 CNC操控的无谓监视 找寻物品的时间浪费 不增值的动作浪费 不知自己的职责,人制管理的浪费
5 M
· 探求必要库存的原因 大量库存造成成 本高、周转困难, · 库存规模的合理使用 且看不到真正的 · 均衡化生产 问题在哪里 · 设备流水化 · 整体能力协调 · 拉式生产彻底暴露问题 · 流程路线图