IATF16949潜在失效模式及后果分析程序(含配套表格)
潜在失效模式及后果分析程序(PFMEA).
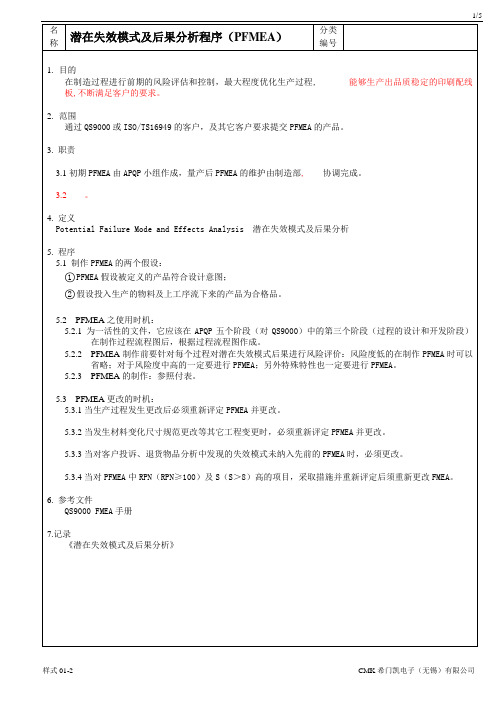
样式 01-2
CMK 希门凯电子(无锡)有限公司
将重要特性转化成潜在不良模式
失效模式是对该特定的过程/产品特性不合理由的详细 描述
识别其潜在的失效后果
是
失效后果以不符合产品功能或过程作业功能要求的方式 描述,如果该失效涉及不符合政府法规的潜在因素或对 产品相关操作人员安全的潜在影响则必须加以指出.
是否有其它的 潜在失效模式 检查是否有遗漏了其它的潜在失效模式.
否
判定严重度
按照严重度评分标准,评估严重度.
分级
按照严重度分级基准分类.
确认潜在不良原因
原因必须以某种可以改正或控制的方式加以描述, 避免模 棱两可的语句.
判定频度数
按照频度数评分标准,评估频度数.
A
样式 01-2
CMK 希门凯电子(无锡)有限公司
3/5
名 称
潜在失效模式及后果分析程序( 潜在失效模式及后果分析程序(PFMEA) )
高:现有控制在后道工序或中间检查中(在制造过程完成之前)几乎肯定能发现存在的缺陷。 3-4 现有控制在后道工序或中间检查中(在制造过程完成之前)几乎肯定能发现存在的缺陷。 - 非常高/早期:现有控制几乎是在制造过程中, 非常高 早期:现有控制几乎是在制造过程中,在产品移动到下一工序或别的部门前肯定能发 早期 1-2 - 现缺陷的存在。 现缺陷的存在。
追踪
样式 01-2
CMK 希门凯电子(无锡)有限公司
4/5
名 称
潜在失效模式及后果分析程序( 潜在失效模式及后果分析程序(PFMEA) )
分类 编号
付表-2
严重度、频度、探测度定级表
1、严重度定级标准 、 失效后果的严重度
定级
非常高:潜在的失效模式可能会导致生产现场失效( ) 或构成安全性危害, ,或构成安全性危害 非常高:潜在的失效模式可能会导致生产现场失效(9) 或构成安全性危害,或不符合某项 , 9-10 - 政府法规的要求 高:由于失效的性质导致顾客高度不满意。可能会导致后续产品加工过程的严重中断或导致 由于失效的性质导致顾客高度不满意。 产品不能满足其销售规范。会导致顾客投诉和产品退货。在顾客进行最终产品试验过程中, - 产品不能满足其销售规范。会导致顾客投诉和产品退货。在顾客进行最终产品试验过程中, 7-8 该种失效有可能被查出来。 该种失效有可能被查出来。 中等:失效会引起顾客有些不满意且可能导致顾客投诉。为适应该种材料, 中等:失效会引起顾客有些不满意且可能导致顾客投诉。为适应该种材料,顾客可能需要对 可能导致顾客投诉 5-6 - 他们的过程进行修改或调整。 他们的过程进行修改或调整。 低:失效只会引起外观的轻微不良或顾客轻微的恼怒。顾客将注意到产品或产品加工只有一 失效只会引起外观的轻微不良或顾客轻微的恼怒。 3-4 - 些轻微劣化或不便。 些轻微劣化或不便。 微弱:顾客合理地认为该失效的微弱性对产品或其加工不会引起任何实质性后果。 微弱:顾客合理地认为该失效的微弱性对产品或其加工不会引起任何实质性后果。顾客甚至 1-2 - 可能注意不到这种失效。 可能注意不到这种失效。 2、频度定级标准 、 失效的频度 非常高:失效几乎总是不可避免的。需要开发其他过程步骤以解决失效问题。 非常高:失效几乎总是不可避免的。需要开发其他过程步骤以解决失效问题。 高:类似的过程曾有过重复失效的发生。该过程不处于统计受控状态。 类似的过程曾有过重复失效的发生。该过程不处于统计受控状态。 中等:类似的过程曾经有过偶尔失效,但比例不大。过程是处于统计受控状态。 类似的过程曾经有过偶尔失效,但比例不大。过程是处于统计受控状态。 非常低:类似的过程只有个别或极个别的失效发生。 非常低:类似的过程只有个别或极个别的失效发生。 极低:不太可能有失效发生。几乎同样的过程从未发生有关的失效。 极低:不太可能有失效发生。几乎同样的过程从未发生有关的失效。过程处于统计受控状态 或已采取了防错措施。 或已采取了防错措施。 3、探测度定级标准 、 缺陷被发现的可能性及其在过程中的位置 绝对的不确定:现有控制不会或不能发现存在的缺陷。 绝对的不确定:现有控制不会或不能发现存在的缺陷。 定级 9-10 - 定级 9-10 - 7-8 - 5-6 - 3-4 - 1-2 -
CP12-IATF16949-2016潜在失效模式及后果分析管理程
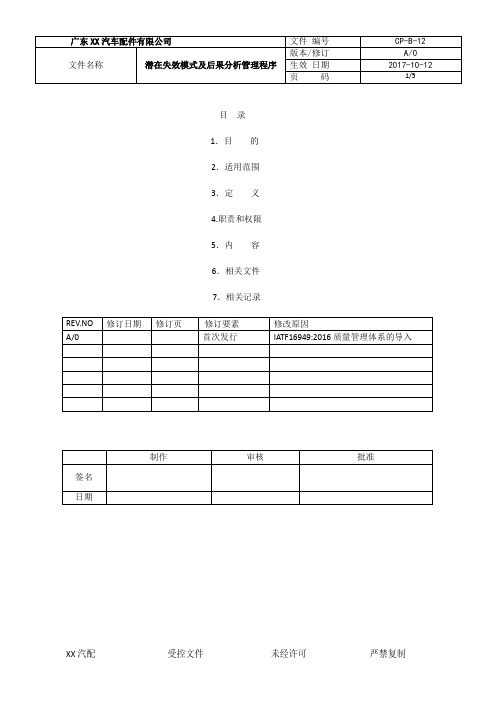
目录1.目的2.适用范围3.定义4.职责和权限5.内容6.相关文件7.相关记录1.目的本程序确定了与产品和过程相关的潜在的失效模式和潜在制造或装配过程失效的机理/起因,评价了潜在失效对顾客产生的后果和影响,阐明了如何采取控制来降低失效产生频度或失效条件探测度的过程变量和能够避免或减少这些潜在失效发生的措施。
2.适用范围本程序适用于公司所有新产品/过程或修改过的产品/过程及应用或环境发生变更的原有产品/过程的样品试制和批量生产。
3.定义3.1PFMEA—指Process Failure Mode and Effects Analysis(过程潜在失效模式及后果分析)的英文简称。
由负责制造/装配的工程师/小组主要采用的一种分析技术,用以最大限度地保证各种潜在的失效模式及其相关的起因/机理已得到充分的考虑和论述。
3.2严重度(S)—指一给定失效模式最严重的影响后果的级别,是单一的FMEA范围内的相对定级结果。
严重度数值的降低只有通过制作更改或重新制作才能够实现。
3.3频度(O)—指某一特定的起因/机理发生的可能发生,描述出现的可能性的级别数具有相对意义,但不是绝对的。
3.4不易探测度(D)—指在零部件离开制造工序或装配之前,利用第二种现行过程控制方法找出失效起因/机理过程缺陷或后序发生的失效模式的可能性的评价指标;或者用第三种过程控制方法找出后序发生的失效模式的可能性的评价指标。
3.5风险优先数(RPN)—指严重度数(S)和频度数(O)及不易探测度数(D)三项数字之乘积。
4.职责和权限APQP小组负责过程潜在失效模式及后果分析(PFMEA)的制定与管理。
5.内容5.1提出:5.1.1凡属需要高度保证、可靠度偏低、制造或装配作业较为复杂,且较难达成工程规范的制程,往往是产品问题的所在,由生产单位,QC部或技术部提出实施FMEA制度要求。
5.1.2当新产品制作展开,由品质规划小组进行。
5.2辨认每一作业的重要特性:5.2.1工程机能:了解检讨产品的需要理由、目的及其被要求的机能,具体的记录下来。
新版IATF16949风险和机遇应对措施管理程
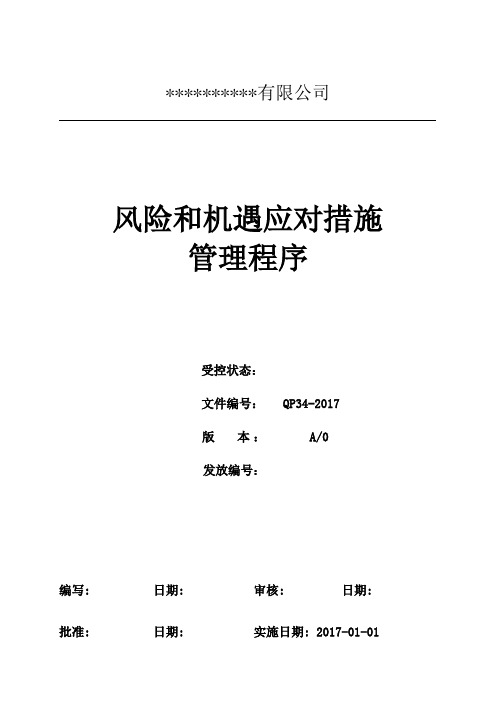
**********有限公司风险和机遇应对措施管理程序受控状态:文件编号: QP34-2017版本: A/0发放编号:编写: 日期: 审核: 日期: 批准: 日期: 实施日期: 2017-01-01*********有限公司修订履历表1 目的完善质量管理体系,建立风险管理体系,确保我司在生产经营时对各种风险进行有效识别和评估,以便根据评估结果制订应急预案及商业风险防范业务持续计划,达到规避风险和降低损失的目的。
2 范围适用于在公司质量管理体系活动中应对风险和机遇的措施的控制。
3 职责3.1总经理负责定期对战略决策中存在的风险进行识别和评估,并针对企业发展战略中的风险组织制定应急对策。
3.2 管理者代表负责按本文件所要求的周期组织实施风险和机遇的评审,落实跟进风险和机遇评估中所采取措施的完成情况及有效性。
3.3 各部门负责本部门的风险和机遇的识别与评估,并制定和实施相应的措施以控制风险。
4 定义风险:不确定性的影响。
5工作程序5.1 公司在建立质量管理体系时,应考虑内外部因素及相关方要求,确定所有管理体系过程中可能出现的风险和机遇,并采取应对的措施。
5.2风险管理原则:科学评估、预防为主、及时响应、动态调整。
5.3风险和机遇管理过程:5.4风险识别5.4.1风险识别范围1)针对影响公司目标和战略方向相关并影响其实现质量管理体系预期结果的各种内外部因素,展开分析;2)相关方的需求和期望相对应的风险和机遇;3)针对公司质量管理体系过程存在的风险和机遇;4)针对设计和开发中与产品和制造过程相对应的风险和机遇。
5)风险分析中至少包含从产品召回、产品审核、使用现场的退货和修理、投诉、报废及返工中吸取的经验教训。
5.4.2风险识别过程1)战略风险由总经理负责定期(至少每年一次)对战略决策中存在的风险进行识别和评估,各部门参与战略风险的评估,收集与本部门有关的内外部因素。
具体按《经营计划和目标管理程序》要求执行。
过程潜在失效模式及后果分析PFMEA制作流程图
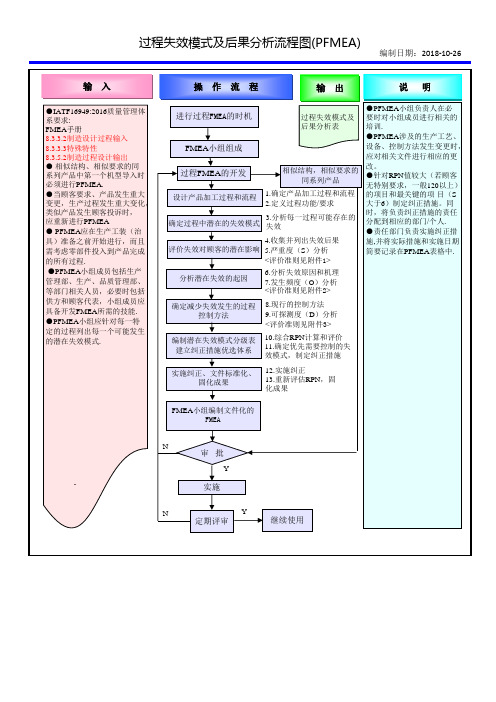
过程失效模式及后果分析流程图(PFMEA)输入操作流程输出说明●PFMEA 小组负责人在必要时对小组成员进行相关的培训.●PFMEA 涉及的生产工艺、设备、控制方法发生变更时,应对相关文件进行相应的更改。
●针对RPN 值较大(若顾客无特别要求,一般120以上)的项目和最关键的项目(S大于6)制定纠正措施。
同时,将负责纠正措施的责任分配到相应的部门/个人.●责任部门负责实施纠正措施,并将实际措施和实施日期简要记录在PFMEA 表格中.进行过程FMEA 的时机FMEA 小组组成●IATF16949:2016质量管理体系要求:FMEA 手册8.3.3.2制造设计过程输入8.3.3.3特殊特性8.3.5.2制造过程设计输出●相似结构、相似要求的同系列产品中第一个机型导入时必须进行PFMEA.●当顾客要求、产品发生重大变更,生产过程发生重大变化,类似产品发生顾客投诉时,应重新进行PFMEA●PFMEA 应在生产工装(治具)准备之前开始进行,而且需考虑零部件投入到产品完成的所有过程.●PFMEA 小组成员包括生产管理部、生产、品质管理部、等部门相关人员,必要时包括供方和顾客代表,小组成员应具备开发FMEA 所需的技能. ●PFMEA 小组应针对每一特定的过程列出每一个可能发生的潜在失效模式.过程失效模式及后果分析表N设计产品加工过程和流程评价失效对顾客的潜在影响分析潜在失效的起因编制潜在失效模式分级表建立纠正措施优选体系实施纠正、文件标准化、固化成果过程FMEA 的开发FMEA 小组编制文件化的FMEA审批Y实施相似结构,相似要求的1.确定产品加工过程和流程2.定义过程功能/要求3.分析每一过程可能存在的失效4.收集并列出失效后果5.严重度(S )分析<评价准则见附件1>6.分析失效原因和机理7.发生频度(O )分析<评价准则见附件2>8.现行的控制方法9.可探测度(D )分析<评价准则见附件3>10.综合RPN 计算和评价11.确定优先需要控制的失效模式,制定纠正措施12.实施纠正13.重新评估RPN ,固化成果确定过程中潜在的失效模式确定减少失效发生的过程控制方法继续使用YN编制日期:2018-10-26定期评审。
IATF16949全套文件和表格
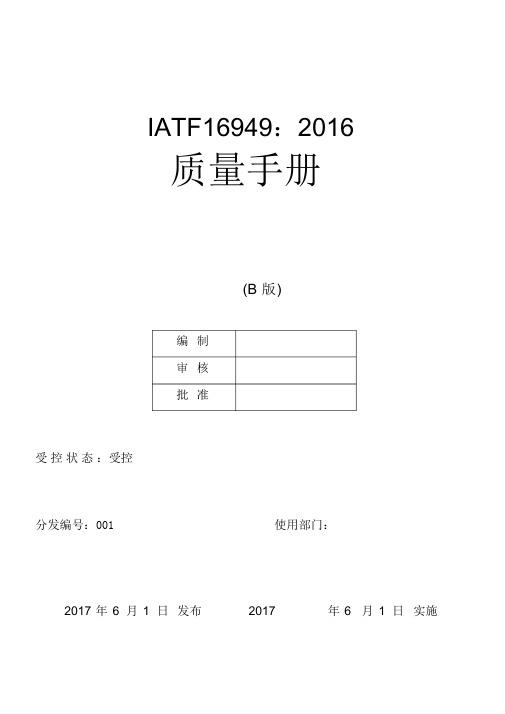
IATF16949:2016质量手册(B 版)编制审核批准受控状态:受控分发编号:001 使用部门:2017 年6 月1 日发布2017 年6 月1 日实施文件修订履历版本修订内容修订页次制/ 修日期TS16949-2009 A.0 版全面升级为IATF16949-2016B.0 B.0 版54 2017-6-1 制定审核批准4.组织环境4.1 了解组织及环境 4.2了解相关方的需求和期望目 录章 节标 题 识别的过程 页码封面 0 目录 1-7 前言 8 颁布令 9 质量方针 10 企业概况11 1. 管理原则 11 2. 范围与应用 12 3. 引用标准、术语和定义12-13 14 14 144.2.1了解相关方的需求和期望 - 补充144.3确定质量管理体系范围14 4.3.1确定质量管理体系范围 - 补充144.3.2顾客特殊要求 144.4质量管理体系及其过程14-16 4.4.1 组织应按标准建立、实施、保持和改进管理体系164.4.1.1产品和过程一致性174.4.1.1.1产品安全 174.4.1.2外包过程 174.4.2必要时 175.领导作用185.1领导作用和承诺M1 领导作用 18 5.1.1总则185.1.1.1 企业责任185.1.1.2 过程效率185.1.1.3 过程所有者185.1.2 以顾客为关注焦点185.2 方针185.2.1 质量方针的制定185.2.2 质量方针的沟通18M1领导作用5.3 组织的角色、职责、和权限185.3.1 组织的角色、职责和权限- 补充185.3.2 产品要求符合性和纠正措施186. 策划18-196.1 应对风险和机遇的措施18-196.1.1 确定需处理的风险和机会18-196.1.2 策划和处理方案18-196.1.2.1 风险分析18-196.1.2.2 应急计划18-19M2 策划6.2 质量目标及其实现的策划18-196.2.1 质量目标18-196.2.2 策划和实施18-196.2.2.1 质量目标及其实现的策划的- 补充18-196.3 变更的策划18-1919 7. 支持7.1 资源197.1.1 总则197.1.2 人员197.1.3 基础设施S1 基础设施管理19-207.1.3.1 工厂、设施和设备计划19-207.1.4 过程和运行的环境207.1.4.1 过程运行环境- 补充207.1.5 监视和测量资源20-227.1.5.1 总则20-22S2 监视和测量资源管7.1.5.1.1 测量系统分析20-22理7.1.5.2 测量溯源20-227.1.5.2.1 校准/ 验证记录20-2220-227.1.5.3 实验室要求S2 监视和测量资源管7.1.5.3.1 内部实验室20-22理7.1.5.3.2 外部实验室20-227.1.6 组织的知识20-22 7.2 能力22-2322-237.2.1 培训22-237.2.1.1 在职培训S3 人力资源管理7.3 意识22-237.3.1 意识- 补充22-237.3.2 员工激励授权22-23 7.4 沟通23 7.5 形成文件的信息237.5.1 总则237.5.1.1 质量管理体系文件237.5.1.2 质量手册S4 文件记录管理237.5.2 创建与更新24247.5.3 形成文件的信息控制7.5.3.2.1 记录的保存247.5.3.2.2 工程规范248. 运行258.1 运行策划和控制258.2 产品和服务的要求258.2.1 顾客沟通25C1 市场营销8.2.1.1 顾客沟通- 补充258.2.1.2 顾客沟通- 培训2525-268.2.2 产品和服务要求的确定C2 报价及项目确定8.2.2.1 产品和服务要求的确定- 补充25-2626-278.2.3 产品和服务要求的评审C3 订单管理8.2.4 产品和服务要求的更改26-278.3 产品和服务的设计和开发C4 过程设计和开发27-288.3.1 总则27-288.3.2 设计开发的策划27-288.3.2.1 多方论证方法27-288.3.2.2 设计开发策划- 培训27-288.3.2.3 产品设计技能27-288.3.3 设计开发的输入27-2827-288.3.3.2 制造过程设计输入C4 过程设计和开发8.3.3.3 特殊特性27-288.3.4 设计开发的控制27-288.3.4.1 监测27-288.3.4.2 设计开发确认27-288.3.4.3 样件计划27-288.3.4.4 产品批准过程27-288.3.5 设计和开发的输出27-288.5.1.3 作业准备验证 8.5.1.4 停机后验证8.5.1.5全面生产维护S6 设备管理8.3.5.2 制造过程的设计输出 27-28 8.3.6设计开发的更改27-28 8.4外部提供过程、产品和服务的控制28-29 8.4.1 总则 28-29 8.4.1.1总则 - 补充28-29 8.4.1.2 供应商选择过程 28-298.4.1.3 顾客提定的供货来源 28-29 8.4.2 控制类型和程序 28-29 8.4.2.1 控制类型和程序 - 补充S5 采购控制28-29 8.4.2.2 法律法规要求 28-29 8.4.2.3 供应商质量管理体系要求28-29 8.4.2.3.1 产品嵌入式软件 28-29 8.4.2.4 供应商监测 28-29 8.4.2.4.1 二方审核 28-29 8.2.4.5 供应商开发28-29 8.2.4.5.1 供应商质量管理体系开发28-29 8.4.2.5.2 供应商绩效开发 28-29 8.4.3 外部供方信息 S5 采购控制28-29 8.4.3.1外部供方信息 - 补充 28-29 8.5生产和服务的提供30-318.5.1生产和服务提供的控制30-318.5.1.1 控制计划30-31C5 产品制造8.5.1.2标准作业 - 操作作业指导书和可视化标准30-31 30-3130-31318.5.1.6 生产工装和生产、试验检验工装和设备的管理S7 工装管理31-328.5.1.7 生产计划328.5.2 标识和可追溯性C5 产品制造328.5.3 顾客或外部供方的财产328.5.4 防护S8 产品防护32-338.5.5 交付后活动33C6 产品交付8.5.5.1 服务信息反馈34-35C7 顾客反馈处理8.5.5.2 与顾客的服务协议34--358.5.6 更改控制358.5.6.1 更改控制- 补充358.5.6.1.1 应急过程控制35 8.6 产品和服务的放行35-368.6.1 产品和服务放行- 补充35-368.6.2 全尺寸和功能试验35-368.6.3 外观项目35-36S9 产品和服务的放行8.6.4外部提供产品和服务的符合性验证和接收35-368.6.5 法律法规的符合性35-368.6.6 接收准则35-36 8.7 不合格输出的控制36-378.7.1 总则36-378.7.1.1 顾客特许36-378.7.1.2 不合格控制- 顾客规定的过程S10 不合格品控制36-378.7.1.3 可疑产品的控制36-378.7.1.4 返工产品的控制36-378.7.1.5 顾客通知36-378.7.1.6 不合格品的处置36-378.7.2 组织应保留形成文件的信息36-379. 绩效评价379.1 监视、测量分析和评价379.1.1 总则379.1.1.1 制造过程的监视和测量379.1.1.2 统计工具的识别379.1.1.3 基础统计概念知识379.1.2 顾客满意37-38S11 顾客满意度测量9.1.2.1 顾客满意- 补充37-389.1.3 分析和评价38-39M3 分析和评价9.1.3.1 优先级38-399.2 内部审核399.2.2.1 内部审核方案399.2.2.2 质量管理体系审核39M4 内部审核9.2.2.3 制造过程审核399.2.2.4 产品审核399.2.2.5 内部审核员资格399.3 管理评审409.3.1 总则409.3.1.1 质量管理体系绩效40M5 管理评审9.3.2 评审的输入409.3.2.1 管理评审输入- 补充409.3.3 评审的输出409.3.3.1 评审输出- 补充M5 管理评审4010 改进41M6改进10.1 总则4110.2 不合格和纠正措施4110.2.1 处理4110.2.2 证据信息4110.2.3 问题的解决4110.2.4 防错4110.2.5 保修管理4110.2.5.1 顾客投诉及现场失效测试分析4110.2.6 预防措施41 10.3 持续改进4110.3.1 组织的持续改进4111.0 附件11.1 顾客特殊要求4211.2 组织架构图4311.3 质量负责人任命书4411.4 职能分配表4511.5标准条款及相关联的47程序文件11.6 过程绩效表48 11.7 过程关系图49 11.8 质量体系保证图50前言本质量手册依据IATF16949:2016 编制,本手册发布日期即为生效日期,按生效日期开始执行。
过程失效模式及后果分析控制程序IATF16949

过程失效模式及后果分析控制程序IATF169491.目的确定与产品和过程相关的潜在的失效模式和潜在制造或装配过程失效的机理/起因,评价潜在失效对顾客产生的后果和影响,采取控制来降低失效产生频度或失效条件探测度的过程变量和能够避免或减少这些潜在失效发生的措施。
2.范围适用于公司用于汽车零组件的所有新产品/过程或修改过的产品/过程及应用或环境发生变更的原有产品/过程的样品试制和批量生产。
3.定义3.1失效:在规定条件下(环境、操作、时间),不能完成既定功能或产品参数值和不能维持在规定的上下限之间,以及在工作范围内导致零组件的破裂卡死等损坏现象。
3.2严重度(S):指一给定失效模式最严重的影响后果的级别,是单一的FMEA范围内的相对定级结果。
严重度数值的降低只有通过设计更改或重新设计才能够实现。
3.3频度(O):指某一特定的起因/机理发生的可能发生,描述出现的可能性的级别数具有相对意义,但不是绝对的。
3.4探测度(D):指在零部件离开制造工序或装配之前,利用第二种现行过程控制方法找出失效起因/机理过程缺陷或后序发生的失效模式的可能性的评价指标;或者用第三种过程控制方法找出后序发生的失效模式的可能性的评价指标。
3.5风险优先数(RPN):指严重度数(S)和频度数(O)及不易探测度数(D)三项数字之乘积。
3.6 CFT:多功能小组4.职责CFT:负责过程失效模式及后果分析(PFMEA)的制定与管理。
5.工作流程5.1 FMEA策划5.1.1新产品进入试生产之前,要使用PFMEA分析;5.1.2现有的产品出现质量故障时,要使用PFMEA去分析;5.2 组建CFT,根据需要,小组成员可包括制造、采购、质量、工程、和顾客方面的代表;5.3收集FMEA所需的信息5.3.1零部件生产过程流程图;5.3.2过程有关的产品质量特性;5.3.3制造和装配的要求;5.3.4与成熟产品相近的产品过程质量情况等信息。
5.4失效模式确认5.4.1 FMEA小组分析产品的功能失效模式;5.4.2可以使用鱼骨图,从人、机、料、法、环五方面分析失效模式的每一个起因或机理;5.4.3确定潜在的失效模式;5.5 严重度评价5.5.1分析潜在失效的后果,根据严重度评价准则进行严重度评定;5.6频度评价5.6.1对失效模式的起因或机理,根据频度评价准则进行频度评价;5.7探测度评价5.7.1选择现行的控制方法,根据探测度评价准则进行探测度评价;5.8确定风险顺序数5.8.1根据严重度、频度、探测度的评定,计算出风险顺序数(RPN);5.9制定改正措施5.9.1CFT列出RPN值先后次序表,首先对级数高、严重度高或最关键的项目要制定改正。
失效模式及后果分析控制程序(含表格)

失效模式及后果分析控制程序(IATF16949-2016/ISO9001-2015)1.0目的:本规则介绍了本公司的制品在工程FMEA的实施阶段的运用程序及有关规定,其主要目的是:1)确定与产品相关的过程潜在的实效模式;2)评价失效时对顾客的潜在影响;3)确定潜在制造或装配过程失效的起因,确定减少失效发生或找出失效条件的过程控制变量;4)编制潜在失效模式等级表,然后建立考虑纠正措施的顺序。
2.0范围:2.1生产部在新产品投入时,依据关联规程《产品质量先期策划控制程序》,在生产可行性评价阶段或之前,进行潜在的失效模式及后果分析(PFMEA);2.2 PFMEA是一种动态文件,在新产品的制造策划阶段、对新过程或修改的过程进行早期评价和分析能够促进预测、解决或监控潜在过程问题。
应包括工场内所有可能影响到制造和装配操作的过程,它应始终反映过程设计的最新状态,以及最新的相关措施。
3.0定义:3.1FMEA:潜在的失效模式及后果分析(Potential Failure Mode and Effects Analysis简称FMEA)。
是在制品/工程等的策划设计阶段,对构成制品的各种部品,对构成工程的各个程序逐一进行分析,找出潜在的失效模式,分析其可能的后果,苹果其风险,从而预先采取措施,减少失效模式的严重程度,降低其可能发生的概率,以有效地提高质量与可靠性,确保顾客满意的一系列活动。
3.2 DFMEA和PFMEA:设计FMEA和工程FMEA(Design FMEA和Process FMEA)。
3.3FMEA的顾客:不仅是指最终顾客、也可以是下一道工序或组立工程及服务等。
3.4其它(如:严重度、频度等)的定义在后述5项中说明。
4.0职责:4.1PFMEA应由CFT(Cross-Functional Team部门横向协调小组)小组来开发和维护。
4.2CFT小组的成员应包括:技术、生产、生产管理、品质管理;必要时包括采购、品证、供应商、后续装配领域等人员。
IATF16949失效模式分析程序(FMEA)
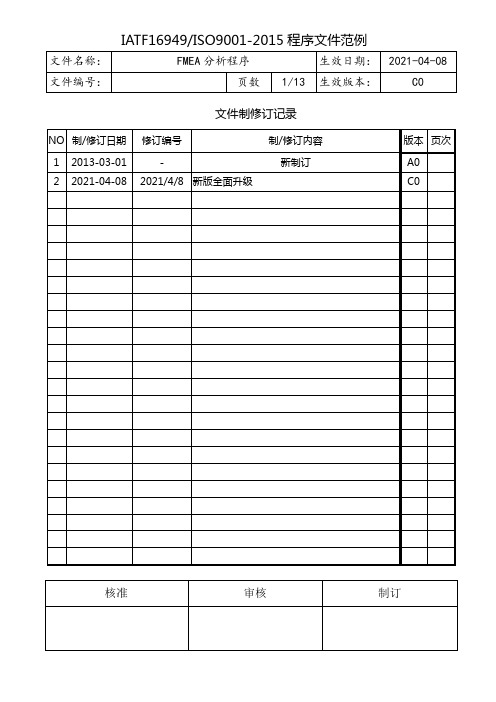
文件制修订记录1.0目的为确保量产的质量性能稳定,事前进行分析,以预防不良发生而制定控制体系。
2.0范围凡是执行IATF16949:2016质量系统的制程。
3.0权责3.1 CFT小组成员:负责产品DFMEA的制定, 工程部产品项目工程师及工模部设计人员主要负责DFMEA分析与制定,其它部门的CTF成员参与各方案的议定。
3.2工艺工程师:负责PFMEA的制定, 其它部门的 CTF成员参与各方案的议定。
4.0定义4.1 DFMEA:设计失效模式及后果分析,正确评估及预测产品设计过程中的某些设计目标出现潜在失效,如: 对产品外观﹑结构﹑功能﹑法律法规﹑环境要求及性能稳定性﹑可靠性之影响和效应等, 并针对各种问题进行分析评估后,在产品结构设计中所采取的预防和改善措施。
4.2 PFMEA:过程失效模式及后果分析,正确评估及预测产品制造/装配过程中某些制程异常现象一旦失效所带来的对产品质量各种问题影响和效应, 并针对之进行分析评估后所采取的改善和预防措施。
4.3 CFT: Cross Function Team跨功能小组。
5.0流程图:无。
6.0程序内容6.1 新产品的合同评审合格后,公司各相关部门经理确定本部门的CFT小组成员, 针对在产品的设计与制作过程中的不同阶段之潜在的可更改和不可更改的不良设计时,对产品带来的质量因素形成DFMEA及PFMEA数据,以确保产品质量得到保障。
6.2 FMEA文件编号的编制方法: D-FMEA-XXXX或P-FMEA-XXXX ; 其中第一位”D”表示DFMEA;”P”表示PFMEA; 后面四位”X XXX”表示4位流水号,交文控发行至相关部门。
6.3 DFMEA 编制方法:6.3.1 CFT小组成员中负责DFMEA编制的成员应召开产品设计讨论会议,主要分析新产品的设计﹑制造﹑装配﹑各试验分析﹑可靠性﹑材料﹑质量及法律法规等要求,用附件表1框图的方式阐述各组件﹑部件之间的装配关系,并加以记录形成DFMEA文件。
IATF16949-风险分析及失效模式控制程序
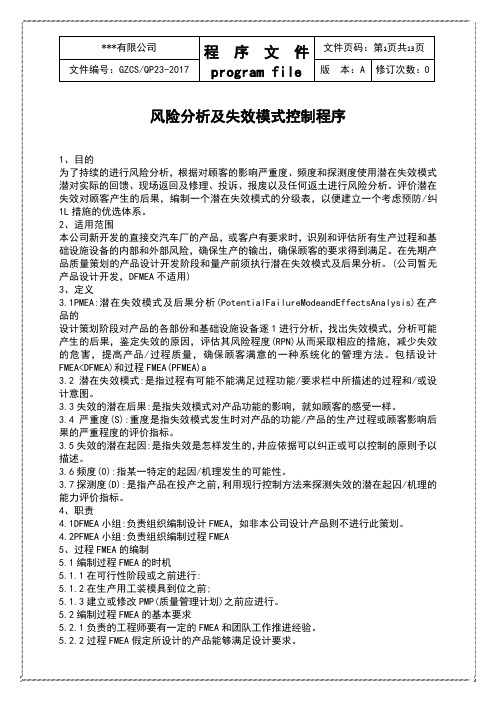
风险分析及失效模式控制程序1、目的为了持续的进行风险分析,根据对顾客的影响严重度、频度和探测度使用潜在失效模式潜对实际的回馈、现场返回及修理、投诉、报废以及任何返土进行风险分析。
评价潜在失效对顾客产生的后果,编制一个潜在失效模式的分级表,以便建立一个考虑预防/纠1L措施的优选体系。
2、适用范围本公司新开发的直接交汽车厂的产品,或客户有要求时,识别和评估所有生产过程和基础设施设备的内部和外部风险,确保生产的输出,确保顾客的要求得到满足。
在先期产品质量策划的产品设计开发阶段和量产前须执行潜在失效模式及后果分析。
(公司暂无产品设计开发,DFMEA不适用)3、定义3.1PMEA:潜在失效模式及后果分析(PotentialFailureModeandEffectsAnalysis)在产品的设计策划阶段对产品的各部份和基础设施设备逐1进行分析,找出失效模式,分析可能产生的后果,鉴定失效的原因,评估其风险程度(RPN)从而采取相应的措施,减少失效的危害,提高产品/过程质量,确保顾客满意的一种系统化的管理方法。
包括设计FMEA<DFMEA)和过程FMEA(PFMEA)a3.2潜在失效模式:是指过程有可能不能满足过程功能/要求栏中所描述的过程和/或设计意图。
3.3失效的潜在后果:是指失效模式对产品功能的影响,就如顾客的感受一样。
3.4严重度(S):重度是指失效模式发生时对产品的功能/产品的生产过程或顾客影响后果的严重程度的评价指标。
3.5失效的潜在起因:是指失效是怎样发生的,井应依据可以纠正或可以控制的原则予以描述。
3.6频度(0):指某一特定的起因/机理发生的可能性。
3.7探测度(D):是指产品在投产之前,利用现行控制方法来探测失效的潜在起囚/机理的能力评价指标。
4、职责4.1DFMEA小组:负责组织编制设计FMEA,如非本公司设计产品则不进行此策划。
4.2PFMEA小组:负责组织编制过程FMEA5、过程FMEA的编制5.1编制过程FMEA的时机5.1.1在可行性阶段或之前进行:5.1.2在生产用工装模具到位之前;5.1.3建立或修改PMP(质量管理计划)之前应进行。
失效模式及后果分析控制程序(IATF16949)
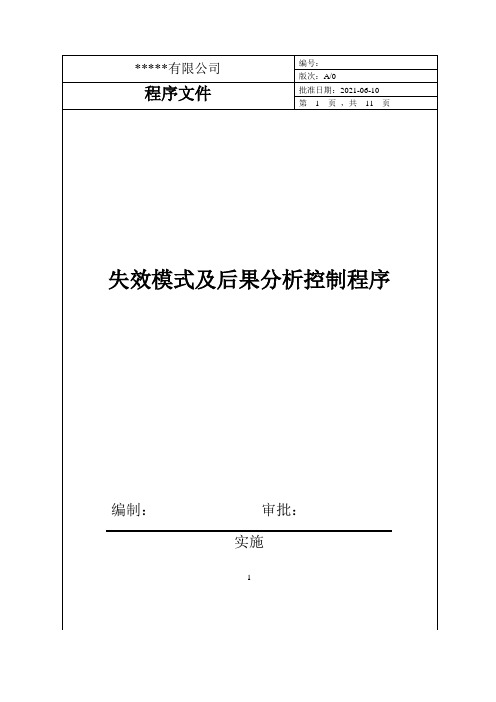
修改记录1.目的规范FMEA活动,评价和发现产品在设计中和工艺过程开发中存在的潜在失效及其后果, 并将能够避免减少这些潜在失效产生的措施正式书面文件化,对产品质量前期进行缺陷预防,以确保产品质量。
2.范围适用于本公司所有的新产品的开发与工艺过程开发,以及量产后提出改进措施。
3.术语和定义:DFMEA: 设计失效模式分析,应采用多方论证方法,在新产品开发立项前启动,最终配方和产品规范定稿时结束。
PFMEA:过程失效模式分析,应采用多方论证方法,在新产品过程开发、工装开发前启动,最终设备和工装完工前结束。
失效:在规定条件下(环境、操作、时间),不能完成既定功能或产品参数值和不能维持在规定的上下限之间,以及在工作范围内导致零组件的破裂卡死等损坏现象。
4.职责:APQP小组负责失效模式及后果分析(FMEA)的制定与管理。
5 流程图无6 内容6.1 FMEA的三情形:情形1—新设计、新技术或新过程。
FMEA的范围是全部设计、技术或过程。
情形2—对现有设计或过程的修改(假设已有FMEA)。
FMEA的范围应集中于对设计或过程的修改、由于修改可能产生的相互影响。
情形3—将现有的设计或过程用于新的环境、场所或应用(假设已有FMEA)。
FMEA的范围是新环境或场所对现有设计或过程的影响。
6.2 DFMEA由负责产品设计的工程师制定和实施,技术部接到销售部转来的顾客产品资料,经过评审后应开始启动DFMEA,在产品开发的各个阶段,发生更改或获得更多的信息时,持续予以更新,在产品加工配方完工之前全部完成。
6.3 DFMEA的评审应包括制造、设计、品质及销售人员,必要时可包括顾客代表,小组成员应由经验丰富的工程师参加。
对该产品设计过程中存在的潜在失效模式及后果进行综合分析评估预测,以减小或消除产品设计不合格或导致产品设计报废的机会。
6.4 对DFMEA开发的失效模式、后果和原因及机理进行严重度(S)、频度(O)及探测度(D),6.5 对于DFMEA的中RPN排序,分数高的项目及严重度(S)特别高和项目,如大于8以上时,应优先考虑提出措施,以降低其RPN和S值。
IATF16949-潜在失效模式与效应分析管理规定FMEA

3.1记录管制程序
3.2 Potential Failure Mode and Effects Analysis reference manual.
4、名词定义
4.1 FMEA:Potential Failure Mode and Effects Analysis的简称,潜在失效模式与效应分析。可分为设计FMEA(DFMEA)和制程FMEA(PFMEA)。
d.潜在失效模式:是以零件、子系统、系统之潜在失效,可能导致无法符合设计意图的方式来定义。潜在失效模式也可以是更高级别的子系统或系统的潜在失效模式的原因,或者是更低级别的零件的效应。列出特定项目及其功能的每一项潜在失效模式。并假设失效可能发生,但也可以不需要发生。在此建议一个起始点,那就是审查过去的错误事项,所关心事项的报告,以及团队的“脑力激荡”。潜在失效模式可能仅在某些操作条件下(例如:热、冷、干燥、生锈等)才可能发生,这些应列入考虑。
d.牵涉到产品安全性问题的特性,必须执行DFMEA。
6.1.3可接受的风险程度
a.RPN<100代表风险是可以被接受的,可继续下一步骤。并于需要时,再对该项目进行改善,以促成持续改善的活动。
b.RPN>100代表风险是不可接受的,须对该项目提出改善对策,以便将RPN降到100以下。不论RPN为多少,当严重度(Severity:S)高的时候(S>8),应该予以特别注意。
□副董事长
□财务部
□品质保证课
□第一生产部
□总经理
□总务部
□品质保证课
□第二生产部
□管理者代表
□生产管理部
□生产技术部
□第三生产部
1.目的
1.1执行设计或制造的失效模式与效应分析,以分析产品及制程的潜在失效模式及效应,并了解其相关的原因/机理,进而依据所推算出来的风险优先指数的优先级,对高风险的项目提出必要的改善,以降低其风险。
潜在失效模式及后果分析程序(含表格)
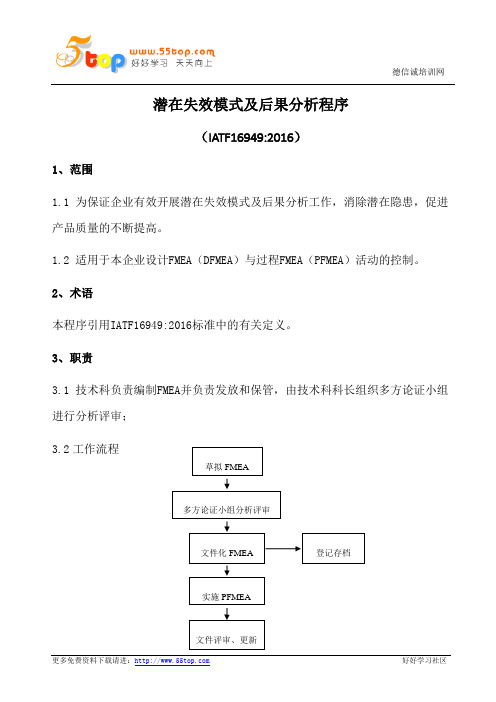
潜在失效模式及后果分析程序(IATF16949:2016)1、范围1.1 为保证企业有效开展潜在失效模式及后果分析工作,消除潜在隐患,促进产品质量的不断提高。
1.2 适用于本企业设计FMEA(DFMEA)与过程FMEA(PFMEA)活动的控制。
2、术语本程序引用IATF16949:2016标准中的有关定义。
3、职责3.1 技术科负责编制FMEA并负责发放和保管,由技术科科长组织多方论证小组进行分析评审;3.2工作流程草拟FMEA多方论证小组分析评审文件化FMEA 登记存档实施PFMEA文件评审、更新4、程序内容4.1组织准备4.1.1 技术人员在产品设计和开发过程中草拟FMEA,提请科长组织评定。
4.1.2由技术科长组织成立多方论证小组,并负责FMEA活动的组织与开发。
4.1.3其它各相关部门指定人员参加,必要时由生产科邀请顾客代表,生产科邀请供方代表参与。
4.2 DFMEA的开发与实施4.2.1在下列情况下DFMEA小组应针对整个产品的设计开展特殊特性失效模式及影响后果分析活动。
A)新产品设计与开发;B)定型产品有重大设计更改。
4.3 DFMEA的制定4.3.1 DFMEA必须的输入A) 经质量功能展开(QFD)而得到的设计要求;B)产品可靠性和质量目标;C)产品的使用环境;D)以往类似产品的失效分析(FMA)资料;E)初始工程标准;F)初始特殊特性明细表。
4.3.2 DFMEA必须的输出按FMEA手册第三版要求用“设计潜在失效模式及后果分析”表格和规定要求制定。
4.4 PFMEA的开发与实施4.4.1在下列情况下PFMEA小组应针对整个产品及制造工序开展特殊特性失效模式及影响后果分析活动。
A)开发新产品/产品更改;B)生产过程更改;C)生产环境/加工条件发生变化;D)材料或零部件变化;4.5 PFMEA的制定4.5.1技术科工艺人员制定过程流程图。
4.5.2多方论证小组根据过程流程图对工序进行风险评价,风险评价程度分高、中、低三级。
IATF16949失效模式和效果分析FMEA控制程序

文件制修订记录1.0目的利用失效模式与效应分析让FMEA小组在初期分析每一个相关系统、组装和零件及确认潜在失效模式和相关原因以降低设计过程失效风险。
2.0 适用范围本公司所有汽车件五金系列新产品及新工艺均适用。
注:非汽车件产品不强制要求执行该程序。
3.0 权责FMEA小组负责FMEA运作.4.0定义4.1 FMEA:利用工程去分析产品零、组件可能失效的模式及原因,研究失效的模式对系统可能产生的影响及严重程度;4.2失效4.2.1在规定条件下(环境、操作、时间等)不能完成既定功能;4.2.2在规定条件下,产品参数值不能维持在规定的上下限之间。
4.2.3产品在工作范围内,导致零组件如性能失效、重金属超标等正常规范以外之异常现象均属之。
4.3系统:此处专指FMEA之对象物,或为零件之某部位、或为零件、或为组合、或为总成、或为机构…。
4.3.1子系统:系统之构成件,如零件之对组合,组合之对总成等,为上游工程(前制程)状态。
5.0作业内容5.1失效模式与效应分析不是依靠制程管制来克服,是用现有技术或考虑制造及组装过程的限制来减少设计上潜在的问题,如:5.1.1需要的工艺流程图;5.1.2组装的空间或要求的工具;5.1.3产品材料的限制;5.1.4制程能力或效能。
5.2FMEA 编号:5.2.1填入FMEA文件编号以便可以追踪使用;5.2.2 FMEA表编号,依产品编订。
5.3型别:填入要分析设计产品型别。
5.4FMEA日期:填入最初FMEA被完成日期,和最新被修订日期。
5.5关键日期:填入FMEA计划完成的日期。
该日期不能超过开始计划生产日期。
5.6项目NO:以流水号1~99方式编入。
同一项目再细分时允许以“-”(允号)方式编号,例4-1,4-2,4-3。
5.7部位(构成部品)名称:填入被分析之构成部品或工程名称,使用之名词应和预定发行之工程规格上所显示的相符。
5.8机能:尽可能简洁地依设计意图填入被分析部位的机能。
IAFT16949 潜在失效模式及后果分析控制程序

FMEA 的开 发以小组 FMEA 的开 发以小组
12
采取的措施
13 纠正后的 RPN
1. FMEA 的开发以小组负责评估采用 纠正措施后 RPN 的值;
FMEA 的开 发以小组
14 其它说明 15 落实、完善 16 流程结束
1. FMEA 的开发以小组负责描述其它 说明; 1. FMEA 的开发以小组负责落实、完 善;
文件编号 发行日期 版次 求或设计意图的形式列出。
FE-QP-10 2016-12-08
1.潜在的失效后果是指失效模式对内部或最终顾客可能发生何种状况影响的预估,包括 下一工序、直接顾客或最终顾客。如:降低使用寿命、制动力不足、不报警、噪音等。 3 潜在失效的后果 对工序的失效后果应用工艺性能来描述;对顾客影响的失效后果,一律用产品和系统的 性能来描述。如:产生裂纹、强度下降、危害操作、无法加工等。 1.通过严重度(S)评价潜在失效模式对顾客的影响后果的严重程度,且通过“严重度 评分标准表”将失效的后果分为“1-10”级进行评估。严重度数值的下降只有通过设计 4 严重度数评价 更改才能实现。 2.本公司的严重度分级按照附录一《严重度评分标准表》评估。 1.对需要附加的设计//过程控制的零件/系统的特殊性进行分级。如:关键 、主要、重 5 级别 要工序质量控制点等。并应通知相关设计工程师,确定相关控制标识工程文件 1.针对每一失效模式,分析其失效原因(即失效是怎么发生的) ,依据可以纠正或控制 潜在失效的起因 6 /机理 制方法。 1.通过频度(O)描述具体的失效起因/机理发生的可能性。频度的大小可以分“1-10” 7 频度 级,用以估计发生频度的相对级别。频度分级规则,参照附录二《频度分级评价表》 。 为尽可能防止失效模式的发生和探测失效模式及其起因必须进行现行过程控制,包括验 现行设计控制 8 (预防措施) 防和探测。 探测度(D)是指零部件离开制造工序或装配工位之前,评估过程缺陷或失效的被发现 的可能性的评价指标。对按现行设计//过程控制方法,在实施运行之前,探测出发生的 9 探测度 失效模式的能力定级评估,评价指标用“1”至“10”级评价探测的相对级别,参照附 录三《探测度分级评价表》 。 1.其值为严重度数、频度数、和探测度数的乘积。通过上述活动的展开,在特定的 FMEA 10 风险顺序数 范围内,对失效模式出现的风险进行排序,确定风险顺序数 RPN=(S)×(O)×(D) 。 [此值应在 1~1000], 11 建议措施 1. 对失效模式按 RPN 值排出先后次序后,应挑选 RPN 值较高者采取纠正/预防措施,重 证/确认、预防措施、防错,统计过程控制,过程后评价等。通常考虑的过程控制为预 的原则来描述(应具体清晰,不可含糊不清) ,并针对相关因素采取纠正措施,制定控
ISOIATF16949潜在失效模式与效应分析管理程序
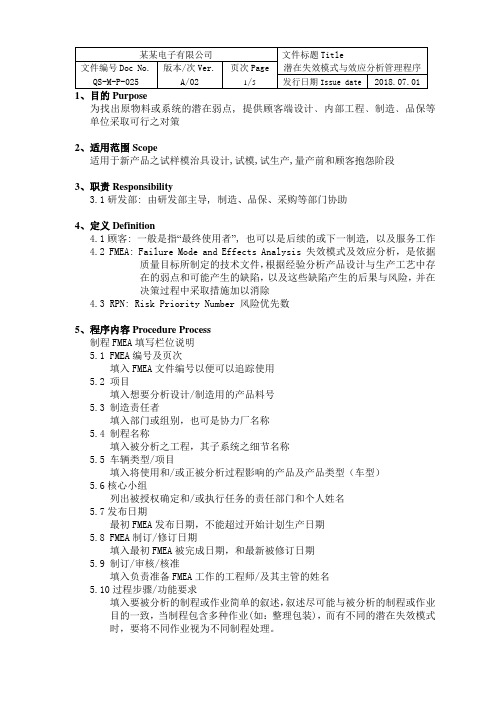
1、目的Purpose为找出原物料或系统的潜在弱点, 提供顾客端设计﹑内部工程﹑制造﹑品保等单位采取可行之对策2、适用范围Scope适用于新产品之试样模治具设计,试模,试生产,量产前和顾客抱怨阶段3、职责Responsibility3.1研发部: 由研发部主导, 制造、品保、采购等部门协助4、定义Definition4.1顾客: 一般是指“最终使用者”, 也可以是后续的或下一制造, 以及服务工作4.2 FMEA: Failure Mode and Effects Analysis 失效模式及效应分析,是依据质量目标所制定的技术文件,根据经验分析产品设计与生产工艺中存在的弱点和可能产生的缺陷,以及这些缺陷产生的后果与风险,并在决策过程中采取措施加以消除4.3 RPN: Risk Priority Number 风险优先数5、程序内容Procedure Process制程FMEA填写栏位说明5.1 FMEA编号及页次填入FMEA文件编号以便可以追踪使用5.2 项目填入想要分析设计/制造用的产品料号5.3 制造责任者填入部门或组别,也可是协力厂名称5.4 制程名称填入被分析之工程,其子系统之细节名称5.5 车辆类型/项目填入将使用和/或正被分析过程影响的产品及产品类型(车型)5.6核心小组列出被授权确定和/或执行任务的责任部门和个人姓名5.7发布日期最初FMEA发布日期,不能超过开始计划生产日期5.8 FMEA制订/修订日期填入最初FMEA被完成日期,和最新被修订日期5.9 制订/审核/核准填入负责准备FMEA工作的工程师/及其主管的姓名5.10过程步骤/功能要求填入要被分析的制程或作业简单的叙述,叙述尽可能与被分析的制程或作业目的一致,当制程包含多种作业(如:整理包装),而有不同的潜在失效模式时,要将不同作业视为不同制程处理。
5.11潜在的失效模式当制程可能不符合制程要求或设计意图,叙述规定作业的不合格事项。
- 1、下载文档前请自行甄别文档内容的完整性,平台不提供额外的编辑、内容补充、找答案等附加服务。
- 2、"仅部分预览"的文档,不可在线预览部分如存在完整性等问题,可反馈申请退款(可完整预览的文档不适用该条件!)。
- 3、如文档侵犯您的权益,请联系客服反馈,我们会尽快为您处理(人工客服工作时间:9:00-18:30)。
潜在失效模式及后果分析流程图1. 目的认可并评价在设计和制造过程中潜在的失效模式,分析其后果,评估其风险,从而预先采取措施,消除或减少失效发生的机会,有效地提高产品质量和可靠性,达到顾客满意。
2. 适用范围适用于新的或更改后的产品/过程的策划设计阶段,对构成产品的各子系统、零部件,对构成过程和服务的各个过程的潜在失效模式及后果进行分析的活动。
3. 术语和定义3.1 DFMEA:设计潜在失效模式和后果分析,是指产品设计人员采用的一门分析技术,在最大范围内保证充分地考虑失效模式及其相关的后果起因/机理,DFMEA以最严密的形式总结了工程技术人员进行产品设计时的指导思想。
3.2 PFMEA:过程潜在失效模式和后果分析,主要是由负责制造的工程师/多方论证小组采用的一种分析技术,用来保证在可能的范围内已充分地考虑到并指明潜在失效模式及其相关的起因或机理。
4. 职责4.1技术部职责4.1.1 组织由负责过程设计、制造、装配、售后服务、质量及可靠性等方面的专家成立多方论证小组。
4.1.2负责计算风险顺序数RPN,并编制《风险顺序数序列表》。
4.1.3负责对FMEA的输出整理归档。
4.2 多方论证小组职责4.2.1负责收集与PFMEA相关数据资料。
4.2.2负责进行PFMEA分析、评审、效果跟踪和确认。
5. 工作程序5.1 DFMEA5.1.1 由技术部组织设计人员、工艺人员、市场部、质量部、采购部相关人员成立多方论证小组,报管理者代表批准。
5.1.2多方论证小组根据设计任务书的设计要求和预期的工艺流程,对设计方案进行分析评审,分析产品在设计结构中的每一个关键部位、结构的风险,并确定需执行DFMEA的高风险的零部件/子系统/系统。
5.1.3 多方论证小组对确定为高风险的部位、结构进行DFMEA,并记录于表格《潜在的失效模式及后果分析(DFMEA)》,当顾客或总经办要求对中等风险的部位、结构进行DFMEA时,按确定的步骤实施。
5.2 按下列要求填写DFMEA表格:5.2.1 FMEA 编号:按过程号编号。
5.2.2项目名称:填入所分析项目的名称。
如零件/部件/子系统/系统;5.2.3设计责任部门:填入产品设计部门和/或小组名称5.2.4 编制者:填入负责编制的人员姓名、电话及所在部门名称。
5.2.5车型年:填入设计将要应用或影响的车辆年/项目(如已知)。
5.2.6关键日期:填入初次FMEA预定完成的日期,该日期不应超过产品加工图完成的日期。
5.2.7 FMEA日期:填入编制FMEA初稿的日期及最新修订的日期。
5.2.8主要参加人:填写执行此项工作的各责任部门和负责人(或参与人)。
5.2.9设计功能要求:简单描述被分析的产品或零件的功能和使用特性,若设计中包括许多具有不同失效模式的特性,应把这些行性作为独立的一项列出处理。
5.2.10潜在失效模式:是指零部件/子系统/系统可能发生的不符合设计功能的失效形式,是对具体特性不符合要求的描述,它可能是引发上一级子系统/系统失效的起因,也可能是下一级零部件失效的后果。
在FMEA准备中,应假定提供的零件/材料是合的。
5.2.11潜在失效后果:是指失效模式对顾客感受到的功能的影响。
在这里,顾客可以是下一道工序、后续工序或工位、代理商、最终用户。
当评价潜在失效后果时,应依据顾客可能注意到的或经历的情况来描述失效的后果。
对最终用户来说失效的后果应一律用产品或系统的性能来描述(如噪音、工作不正常、发热、外观不良、不起作用、间歇性工作等);若顾客是下一道工序、后续工序或工位,失效的后果应用过程/工序性能来描述(如无法紧固、不匹配、无法安装、加工余量过大或过小、危害操作者、损坏设备等)。
5.2.12严重度(S):是指潜在的失效模式对顾客的影响后果的严重程度的评价指标,严重度仅适用于失效的后果。
评价指标分为“1”到“10”级,按严重程度依次递增。
评价准则见表1。
5.2.13级别:对零部件、半成品或成品的一些特殊的设计特性进行分级(如关键、重要)。
如在DFMEA中确定了某一级别,质量部根据需要制定相应的控制计划。
5.2.14 潜在失效起因/机理:是指失效是怎么发生的,并依据易于纠正或控制的方式来描述。
针对每一个潜在失效模式,尽可能在广、深的范围内列出所有能想象到的失效原因,以便采取针对性的纠正措施。
5.2.15 频度(O):是指具体的失效起因/机理发生的频率。
频度的分级重在其含义而不是具体的数值。
评价指标分为“1”到“10”级,按严重程度依次递增。
评价准则见表2。
5.2.16现行设计控制:列出预防措施、设计确认/验证或其他活动,这些活动的完成或承诺将确保该设计对于所考虑的失效模式和/或机理来说是充分的。
现行的控制方法(如减压阀的失效/安全设计、道路试验、设计评审、可行性评审、数学研究、台架实验、样件试制、使用试验等)是指已经用于或正用于相同或相似设计中的方法。
应尽可能的把重点放在设计控制的改进上,如在实验室进行新系统试验、或创建新的系统模型化运算法等。
有两种类型的设计控制特性可以考虑:a、预防:预防起因/机理或失效模式的发生,或减少它们的频度;b、探测:在该项目投产前,以任何解析的或物理的方式,查出失效或失效模式的或起因/机理。
如有可能,优先选用第一种的预防控制方法,让预防控制方法作为设计意图的一部分,因为其将影响到最初的频度;最初的探测度将基于失效起因/机理探测或对失效模式探测的设计控制。
5.2.17探测度(D):是指零部件、半成品、成品、在安装使用前,利用现行设计的控制方法找出失效起因/机理过程缺陷的可能性的评价指标;或利用控制方法找出后续发生的实效模式的可能性的评价指标。
评价等级分为“1”到“10”级,按严重程度递增。
评价准则见表“3”。
表3:设计分析用探测度(D)评价准则5.2.18风险顺序数(RPN):风险顺序数是严重度(S)、频度(O)和探测度(D)的乘积。
即:RPN=S×O×D。
RPN取值在“1”到“1000”之间。
对设计中所有担心的事项可以用RPN值来排序。
设计工程师负责计算风险顺序数RPN,输出《产品设计/过程设计风险评估表》。
①当RPN>120(或依顾客要求)时,应采取改进措施。
②不管风险顺序数是多少,当S≥9时,都要采取改进措施。
③当RPN≤120,S<9时,对RPN从大到小排列,针对前四位采取后续改进措施。
5.2.19建议的措施当失效模式按RPN值排出先后次序后,应首先对排在最前面的问题和最关键的项目采取纠正措施。
任何建议措施的目的都是为了减少严重度、频度和探测度的数值。
如果对某一特定原因无建议措施,那么就在该栏中填写“无”,予以明确。
应考虑以下措施。
①为了减小失效发生的可能性,需要修改设计。
②只有修改设计,才能减小严重度数。
③为了增加探测的可能性,需要修改设计。
④积极的纠正措施是制订永久性的改进措施,以及采用统计过程控制(SPC)方法制订预防缺陷发生的措施。
5.2.20 责任及目标完成日期:填入建议措施的部门和个人,已及预定完成的日期。
5.2.21采取的措施:当实施一项措施后,简要记录具体的措施和生效日期。
5.2.22措施结果:当明确了纠正措施后,估算并记录措施后的严重度、频度和探测度,计算并记录纠正后的RPN值。
如未采取什么纠正措施,将措施后的RPN栏和对应的取值栏目空白即可。
所有纠正后的RPN值都应评审,而且如果有必要考虑进一步的措施,还应重复5.2.19到5.2.21的步骤。
5.2.23 跟踪5.2.23.1技术部应负责保证所有的建议措施已被实施或已妥善地落实。
5.2.23.2 FMEA是一个动态文件,它不仅应体现最新的设计水平,还应体现最新的有关纠正措施,包括产品正式投产后发生的设计更改和措施。
5.2.24 DFMEA的管理完成的DFMEA有技术部负责归档保管,如须分发、更改和回收按《文件管理程序》规定执行。
5.3 PFMEA5.3.1关键日期:指初次完成FMEA的日期,该日期的期限在正式生产之前。
5.3.2过程的功能与要求:指该过程或工序的目的是什么。
5.3.3潜在失效模式:指不能达到过程功能要求或过程设计意图的问题的表现形式。
5.3.4潜在失效后果:指该失效模式可能带来的对顾客的影响。
5.3.5严重度(S):指失效后果的严重程度。
评价准则见表“4”。
5.3.6失效原因/机理:指使失效模式发生的原因,这些原因的消除,可以使失效模式得到纠正或控制。
5.3.7频度:指具体的失效起因/机理使失效模式发生的可能性大小的评估。
评价准则见表“5”。
表5:过程分析用频度评价准则5.5.8现行的过程控制:现行过程控制是对尽可能阻止失效模式或失效原因/机理的发生,或者探测将发生的失效模式或失效原因/机理的控制的描述。
这些控制可以是防错、统计过程控制(SPC)或加工后评价的过程控制。
该控制可在某目标作业进行,也可在后续作业进行有两种类型的过程控制特性可以考虑:a、预防:预防失效起因/机理或失效模式的发生,或减少它们的频度;b、探测:探测失效或失效的起因/机理,并引导至纠正措施。
防止不合格品产生或流入下游工序。
如有可能,优先选用第一种的预防控制方法,让预防控制方法作为过程意图的一部分,因为其将影响到最初的频度;最初的探测度将基于失效起因/机理探测或对失效模式探测的设计控制。
5.3.9探测度(D):指零件在离开该制造工序或装配工序之前,找出失效模式和其发生的原因/机理的可能性的大小。
评价准则见表“6”。
表6:过程分析用探测度(D)评价准则。