2006自由曲面刀具路径生成及误差分析
自由曲面铁削加工的刀位轨迹生成方法
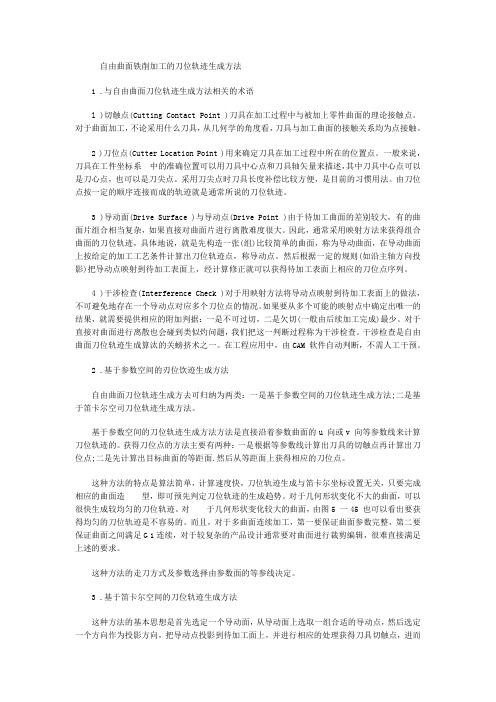
自由曲面铁削加工的刀位轨迹生成方法1 .与自由曲面刀位轨迹生成方法相关的术语l )切触点(Cutting Contact Point )刀具在加工过程中与被加上零件曲面的理论接触点。
对于曲面加工,不论采用什么刀具,从几何学的角度看,刀具与加工曲面的接触关系均为点接触。
2 )刀位点(Cutter Location Point )用来确定刀具在加工过程中所在的位置点。
一般来说,刀具在工件坐标系中的准确位置可以用刀具中心点和刀具轴矢量来描述,其中刀具中心点可以是刀心点,也可以是刀尖点。
采用刀尖点时刀具长度补偿比较方便,是目前的习惯用法。
由刀位点按一定的顺序连接而成的轨迹就是通常所说的刀位轨迹。
3 )导动面(Drive Surface )与导动点(Drive Point )由于待加工曲面的差别较大,有的曲面片组合相当复杂,如果直接对曲面片进行离散难度很大。
因此,通常采用映射方法来获得组合曲面的刀位轨迹,具体地说,就是先构造一张(组)比较简单的曲面,称为导动曲面,在导动曲面上按给定的加工工艺条件计算出刀位轨迹点,称导动点。
然后根据一定的规则(如沿主轴方向投影)把导动点映射到待加工表面上,经计算修正就可以获得待加工表面上相应的刀位点序列。
4 )干涉检查(Interference Check )对于用映射方法将导动点映射到待加工表面上的做法,不可避免地存在一个导动点对应多个刀位点的情况。
如果要从多个可能的映射点中确定出唯一的结果,就需要提供相应的附加判据:一是不可过切,二是欠切(一般由后续加工完成)最少。
对于直接对曲面进行离散也会碰到类似灼问题,我们把这一判断过程称为干涉检查。
干涉检查是自由曲面刀位轨迹生成算汰的关螃挤术之一。
在工程应用中,由CAM 软件自动判断,不需人工干预。
2 .基于参数空间的刃位饮迹生成方法自由曲面刀位轨迹生成方去可归纳为两类:一是基于参数空间的刀位轨迹生成方法;二是基于笛卡尔空司刀位轨迹生成方法。
自由曲面的刀具路径生成与公差分析翻译
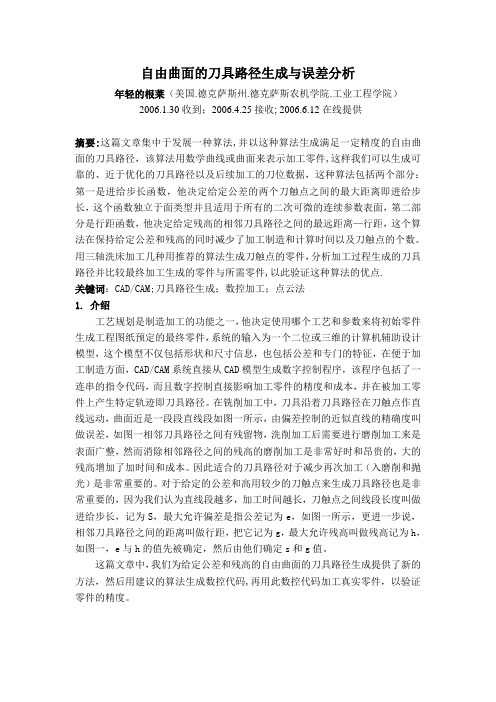
自由曲面的刀具路径生成与误差分析年轻的根莱(美国.德克萨斯州.德克萨斯农机学院.工业工程学院)2006.1.30收到;2006.4.25接收; 2006.6.12在线提供摘要:这篇文章集中于发展一种算法,并以这种算法生成满足一定精度的自由曲面的刀具路径,该算法用数学曲线或曲面来表示加工零件,这样我们可以生成可靠的、近于优化的刀具路径以及后续加工的刀位数据,这种算法包括两个部分:第一是进给步长函数,他决定给定公差的两个刀触点之间的最大距离即进给步长,这个函数独立于面类型并且适用于所有的二次可微的连续参数表面,第二部分是行距函数,他决定给定残高的相邻刀具路径之间的最远距离—行距,这个算法在保持给定公差和残高的同时减少了加工制造和计算时间以及刀触点的个数。
用三轴洗床加工几种用推荐的算法生成刀触点的零件,分析加工过程生成的刀具路径并比较最终加工生成的零件与所需零件,以此验证这种算法的优点.关键词:CAD/CAM;刀具路径生成;数控加工;点云法1.介绍工艺规划是制造加工的功能之一,他决定使用哪个工艺和参数来将初始零件生成工程图纸预定的最终零件,系统的输入为一个二位或三维的计算机辅助设计模型,这个模型不仅包括形状和尺寸信息,也包括公差和专门的特征,在便于加工制造方面,CAD/CAM系统直接从CAD模型生成数字控制程序,该程序包括了一连串的指令代码,而且数字控制直接影响加工零件的精度和成本,并在被加工零件上产生特定轨迹即刀具路径。
在铣削加工中,刀具沿着刀具路径在刀触点作直线远动,曲面近是一段段直线段如图一所示,由偏差控制的近似直线的精确度叫做误差,如图一相邻刀具路径之间有残留物,洗削加工后需要进行磨削加工来是表面广整,然而消除相邻路径之间的残高的磨削加工是非常好时和昂贵的,大的残高增加了加时间和成本。
因此适合的刀具路径对于减少再次加工(入磨削和抛光)是非常重要的。
对于给定的公差和高用较少的刀触点来生成刀具路径也是非常重要的,因为我们认为直线段越多,加工时间越长,刀触点之间线段长度叫做进给步长,记为S,最大允许偏差是指公差记为e,如图一所示,更进一步说,相邻刀具路径之间的距离叫做行距,把它记为g,最大允许残高叫做残高记为h,如图一,e与h的值先被确定,然后由他们确定s和g值。
自由曲面加工理论与应用(第04讲多轴加工刀具路径生成算法

SCHOOL OF MECHANICAL SCIENCE & ENGINEERING
自由曲面加工理论与应用
第04讲--刀具路径生成算法
11 June 2012
1
粗加工刀具路径生成算法 精加工刀具路径生成算法 补加工刀具路径生成算法 五轴加工刀具路径生成算法 基于点云数据的刀具路径生成算法 刀具轨迹后置处理技术 自由曲面加工刀具轨迹生成实例
一化就是所球包围盒的方向向量。 OBB的中心和半边长计算方法:将凸包上的点投影到方向向量上
向上的投影;
β1:过刀尖的水平线与下锥面母线的夹
角, ;
β2:刀轴与上锥面母线的夹角, ; h:刀具切削刃长度。
精加工刀具路径生成算法_多面体法
被加工曲面的多面体模型
10
11
0110 0111 00
0100
Root
00 01 10 11
0100 0101 0110 0111 0110 0110 0110 0110
切削区域边界
用等高面Zc与G-buffer求交
Zij < Zc,记录该网格点P(i, j) Zij > Zc,不记录该网格点P(i, j) 这些被记录的网格点集合{Pij}构成
切削区域无干涉边界点
切削区域边界追踪
利用图像处理中轮廓算法,顺序连 接位于切削区域边界上的网格点
切削区域
边界点筛选
粗加工刀具路径生成算法_Z-map方法
切削区域边界追踪 参照G-buffer方法
切削区域判定 边界描述树,参照G-buffer方法
自由曲面数控加工刀具轨迹映射算法
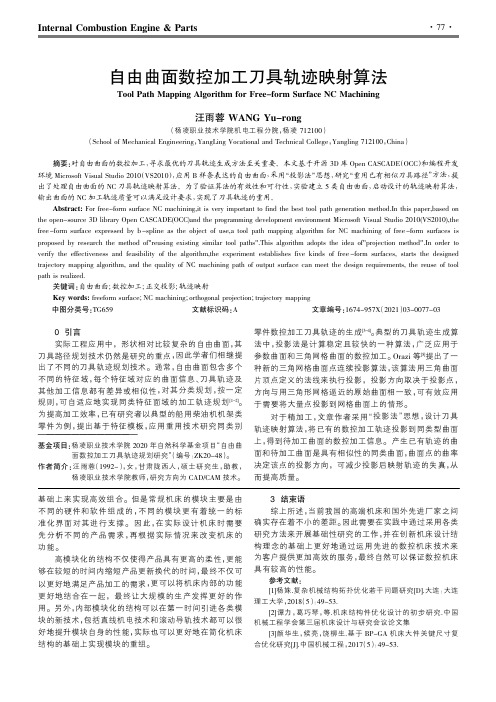
Internal Combustion Engine&Parts0引言实际工程应用中,形状相对比较复杂的自由曲面,其刀具路径规划技术仍然是研究的重点,因此学者们相继提出了不同的刀具轨迹规划技术。
通常,自由曲面包含多个不同的特征域,每个特征域对应的曲面信息、刀具轨迹及其他加工信息都有差异或相似性,对其分类规划,按一定规则,可自适应地实现同类特征面域的加工轨迹规划[1-2]。
为提高加工效率,已有研究者以典型的船用柴油机机架类零件为例,提出基于特征模板,应用重用技术研究同类别零件数控加工刀具轨迹的生成[3-4]。
典型的刀具轨迹生成算法中,投影法是计算稳定且较快的一种算法,广泛应用于参数曲面和三角网格曲面的数控加工。
Orazi等[5]提出了一种新的三角网格曲面点连续投影算法,该算法用三角曲面片顶点定义的法线来执行投影,投影方向取决于投影点,方向与用三角形网格逼近的原始曲面相一致,可有效应用于需要将大量点投影到网格曲面上的情形。
对于精加工,文章作者采用“投影法”思想,设计刀具轨迹映射算法,将已有的数控加工轨迹投影到同类型曲面上,得到待加工曲面的数控加工信息。
产生已有轨迹的曲面和待加工曲面是具有相似性的同类曲面,曲面点的曲率决定该点的投影方向,可减少投影后映射轨迹的失真,从而提高质量。
自由曲面数控加工刀具轨迹映射算法Tool Path Mapping Algorithm for Free-form Surface NC Machining汪雨蓉WANG Yu-rong(杨凌职业技术学院机电工程分院,杨凌712100)(School of Mechanical Engineering,YangLing Vocational and Technical College,Yangling712100,China)摘要:对自由曲面的数控加工,寻求最优的刀具轨迹生成方法至关重要。
本文基于开源3D库Open CASCADE(OCC)和编程开发环境Microsoft Visual Studio2010(VS2010),应用B样条表达的自由曲面,采用“投影法”思想,研究“重用已有相似刀具路径”方法,提出了处理自由曲面的NC刀具轨迹映射算法。
自由曲面加工刀具路径轨迹规划算法研究

自由曲面加工刀具路径轨迹规划算法研究一、本文概述随着现代制造业的快速发展,复杂曲面零件的加工需求日益增加,而自由曲面加工刀具路径轨迹规划作为决定加工质量和效率的关键因素,已成为研究的热点。
本文旨在探讨自由曲面加工刀具路径轨迹规划的相关算法,以期为提高加工精度和效率提供理论支持和实践指导。
本文将首先综述自由曲面加工刀具路径轨迹规划的研究背景和意义,分析当前国内外在该领域的研究现状和发展趋势。
在此基础上,深入探讨自由曲面加工的特点和难点,以及刀具路径轨迹规划的基本原则和要求。
随后,本文将重点研究自由曲面加工刀具路径轨迹规划的关键算法,包括曲面造型算法、刀具轨迹生成算法、轨迹优化算法等,并对这些算法进行详细的理论分析和实验验证。
通过本文的研究,旨在提出一种高效、稳定的自由曲面加工刀具路径轨迹规划算法,为复杂曲面零件的加工提供一种新的解决方案。
本文的研究成果也将为相关领域的研究人员提供有益的参考和借鉴,推动自由曲面加工技术的进一步发展。
二、自由曲面加工理论基础自由曲面加工,作为一种高度灵活的加工方式,在现代制造业中占据了重要的地位。
自由曲面,区别于传统的规则几何面,具有非常复杂和不规则的几何形状。
这类曲面的加工需要依赖先进的数控加工技术和精确的刀具路径轨迹规划算法。
自由曲面加工的理论基础主要包括数学几何理论、数控加工技术、刀具运动学以及切削力学等。
数学几何理论为自由曲面的描述和建模提供了基础,如参数化曲面、NURBS曲面等数学模型,能够精确地描述自由曲面的形状。
数控加工技术则负责将数学模型转化为具体的加工指令,通过数控系统控制机床的运动,实现曲面的加工。
在刀具路径轨迹规划方面,关键在于根据曲面的几何特征,选择适当的加工策略,生成无碰撞、平滑且高效的刀具路径。
这涉及到刀具运动学的知识,如刀具的姿态调整、切削速度的设定、刀具与工件的相对运动等。
切削力学则关注在加工过程中,刀具与工件之间的切削力、切削热等物理量的变化,以及这些物理量对加工质量的影响。
自由曲面高性能数控加工刀具路径技术研究

自由曲面高性能数控加工刀具路径技术研究一、本文概述随着现代制造业的快速发展,自由曲面零件在众多领域中得到了广泛应用,如航空航天、汽车制造、模具制造等。
自由曲面零件的加工精度和表面质量直接影响着产品的性能和使用寿命。
研究自由曲面高性能数控加工刀具路径技术,对于提高加工效率、保证加工质量和降低加工成本具有重要意义。
本文旨在探讨自由曲面高性能数控加工刀具路径技术的相关理论和方法,分析刀具路径生成过程中的关键因素,研究优化刀具路径的策略,并通过实验验证所提方法的有效性和可行性。
本文将对自由曲面数控加工刀具路径技术的研究现状进行综述,分析现有技术的优点和不足。
研究自由曲面数控加工中的刀具路径规划方法,包括刀具选择、路径生成和优化等方面。
接着,探讨基于不同优化算法的刀具路径优化技术,以提高加工效率和质量。
通过实验验证所提方法的有效性,并对实验结果进行分析和讨论。
本文的研究不仅有助于推动自由曲面数控加工技术的发展,还可为相关领域提供有益的参考和借鉴。
本文的研究成果对于提高我国制造业的整体水平和竞争力也具有一定的促进作用。
二、自由曲面数控加工技术概述自由曲面,作为一种复杂且不规则的几何形状,在航空、汽车、模具等制造领域具有广泛的应用。
由于其形状复杂,传统的加工方法往往难以满足其精度和效率的要求,自由曲面数控加工技术应运而生。
数控加工技术通过计算机控制机床,实现对工件的精确加工,尤其适用于复杂曲面的加工。
自由曲面数控加工技术主要包括刀具路径规划、数控编程和机床控制三个核心环节。
刀具路径规划是数控加工的关键技术之一,它决定了加工过程中刀具的运动轨迹,直接影响着加工质量和效率。
刀具路径规划需要考虑的因素包括曲面形状、材料特性、加工精度、切削力、切削热等。
在刀具路径规划过程中,常用的算法有等参数线法等残留高度法、基于几何特征的刀具路径规划等。
等参数线法是根据曲面的参数方程,沿着参数线进行刀具路径规划,适用于参数化的自由曲面。
浅析自由曲面数控加工中刀具路径规划

由于通过直线插补大量刀位点来进行数控加工,存在很
多缺陷,利用NURBS刀具路径进行数控加工,已受到更加广 泛的重视。为了将有序刀位点表示的刀具路径,转化为 NURBS形式表示的刀具路径,必须对刀位点数据进行NURBS 曲线的拟合处理。由于刀位点数据特殊性的存在,特别是刀位 点数据量大的特点,使前面介绍的数据拟合方法在应用于刀 位点的NURBS曲线拟合时,往往出现较大的误差,无法得到 理想的曲线,不能满足NURBS刀具路径生成的需求。 2.4优化算法 设有m+1个有序刀位点只(_『=0,l,…,而,对这些刀位点
自由曲面数控加工中,刀具路径的规划问题较为复杂。近
所得到的点位信息较多;优点是计算比较简单。 (2)参数筛选法。首先按预设的等参数步长离散u或a参 数线,计算出零件表面对应的点列和每一点处的法矢,然后按 曲面的曲率和加工精度,从点列中筛选出点位信息。这种方法 中运用了过滤算法和细化算法,过滤算法用于依据曲率变化 合并一些间隔,以减少数据量;细化算法则依加工误差的要
2.3
NURBS刀具路径 为了克服线性插补刀具路径本身固有的缺陷,许多新型
数控系统己经配备了先进的NURBS曲线插补功能模块。由 NURBS曲线的性质可知,当曲线的阶次确定以后,NURBS曲
NURBS曲线拟合及刀具路径生成
线便可以由控制顶点、权重因子矢量和节点矢量三组参数所
唯一确定。通过NURBS插补,CNC系统可以控制机床精确实 现NURBS曲线刀具轨迹的运动,从而克服由线性插补来近似 曲线加工所带来的加工缺陷。这样,利用NURBS刀具路径进 行加工,就可以实现更加光滑连续的刀具轨迹,得到高精度的 光顺被加工表面质量。对相同的刀具路线,若以直线段插补的 刀具路径表示,当编程精度为0.05 lllm时,此路径曲线需要离 散成24段短小的直线段组成的刀具路径;当编程精度为0.02 Inn,!时,则需要39段直线段;对于更高的加工精度要求,则组 成刀具路径的直线段数量会更多,且该数量还会随着曲线形 状复杂程度的增加而增加。 在使用NURBS刀具路径进行数控加工时的NC程序指
自由曲面数控加工刀具轨迹的规划与计算

图7 短程线曲率半径的计算 根据短程线的几何性质可知,曲面上在给 定点处的短程线的主法矢方向是沿着曲面在该 点处的法矢方向,于是可以根据曲面的第一和 第二基本公式计算出短程线曲率半径
图 5 CL路径截面法生成刀具轨迹 对于复杂曲面的加工,截面法加工效果明 显,容易实现曲面间的光滑走刀。其不足之处在 于计算比较复杂,如果曲面求交算法的可靠性 不高或精度低,那么可能会导致计算结果错误 或者轨迹不满足精度要求。 采用截面法加工曲面时,如果曲面各处都 比较平坦,则可以生成分布比较均匀的刀具轨 迹,加工后可使零件表面上的残留高度比较均 匀。但是截面法加工的截面间距不易控制,难以 与曲面实际形状相吻合,导致在曲面的平坦处 轨迹较为密集,而在陡处轨迹比较稀疏,加工后 表面的残留高度不均匀,表面质量不一致,加工 效率也不高。下图为截面法加工马曲面的刀具 轨迹:
-122-
工 程 论 坛
中国科技信息 2005 年第 13 期 CHINA SCIENCE AND TECHNOLOGY INFORMATION Jul.2005
(a) 参数空间 (b) cartesian空间 图4 曲面离散过程
1)将曲面在参数空间沿 u 向和 v 向进行四叉 树划分,然后把四边形分解为两个三角形(如图 a 所示);
2 )曲面模型——刀触点轨迹——无干涉 刀位轨迹。其基本思路是首先生成不考虑干涉 问题的刀触点轨迹,然后通过干涉检查与处 理,生成无干涉刀位轨迹。这种策略非常适用 于四、五轴数控加工,因为在四五轴数控加工 中,由于刀轴控制的灵活性,很难由刀位点确 定刀触点和刀轴的最佳偏转角度,所以四五轴 数控加工尤其是非球头刀加工进刀具轨迹的生 成算法基本采用该策略。
自由曲面光学的超精密加工技术分析

自由曲面光学的超精密加工技术分析发布时间:2022-10-25T02:30:12.072Z 来源:《科技新时代》2022年10期作者:夏正华[导读] 通过对相关工艺技术进行系统研究,能够为相关零件加工提供有效参考信息。
富泰华工业(深圳)有限公司 518109摘要:现代化背景下进一步打破传统光学成像系统设计方法,在光学成像系统中引入自由曲面,能够有效提升系统能量传输效率和成像质量。
文章先分析了自由曲面光学的超精密加工技术,包括技术特征和技术框架,随后介绍了自由曲面光学的超精密加工技术方案,包括光学自由曲面超精密设计、刀具轨迹生成、加工仿真优化、自由曲面超精密测量,希望能给相关人士提供有效参考。
关键词:自由曲面光学;超精密加工;技术方案引言:在信息时代下,随着超精密加工技术创新发展,能够对非球面光学透镜进行直接加工,并为光电信息产业提供各种高质量光学组件。
合理应用自由曲面能够优化系统设计自由度,改善成像质量,降低系统重量,通过对相关工艺技术进行系统研究,能够为相关零件加工提供有效参考信息。
一、自由曲面光学的超精密加工技术(一)技术特征自由曲面光学元件相关设计、加工技术完全不同于传统元件。
自由曲面光学的超精密加工技术能够针对非对称轴相关光学自由曲面进行加工制作,无需抛光等后续处理便能够使元件加工精度达到纳米级粗糙度和亚微米级形状精度。
自由曲面光学元件是新型技术元件,广泛应用于各种光电装置当中。
自由曲面和非球面镜、传统求面镜比起来拥有突出优势,自由曲面从光学面形相关理论层面分析可以通过不规则以及非对称任意曲面组成,并为设计者提供多样设计自由度。
自由曲面因为整体结构形状较为独特,能够促进光学系统结构实现轻量化,改善产品性能结构。
合理应用自由曲面能够基于有限空间内支持高质量成像、清晰视场,提升能量传输效率,优化光学均匀性。
在自由曲面光学持续应用发展背景下,提升自由曲面光学的超精密加工技术以及检测技术水平成为我国工业领域发展基础要求。
自由曲面加工理论与应用(第02讲--自由曲面加工基础)

一、自由曲面加工概述
一、自由曲面加工概述
SSM系统组成
对应加工阶段,SSM系统包括以下模块:
• Roughing • Finishing • Clean-up
一、自由曲面加工概述
SSM-software的功能要求
两种功能要求:
• 生产率要求(productivity requirements) • 兼容性要求(compatibility requirements)
一、自由曲面加工概述
数控技术 数控编程:APT 数控系统 – 德国SIEMENS公司的840D – 日本Fanuc公司的16i/18i/21i/30i系列 – 美国DELTA TAU公司的PMAC – 德国Heidenhain公司的iTNC 530 – 法国NUM公司的1050 – 西班牙FAGOR 公司的CNC 8070 – 日本三菱公司的EZMotion-NC E60等
一、自由曲面加工概述
技术信息处理 (technological information processing)
• 技术信息处理与切削条件、刀具选择和加工选项有关, 一旦在几何信息处理阶段确定了刀具路径走刀模式,那 么加工效率就只受主轴转速和进给速度的影响。这些飞 机和因素包括: – 加工误差 – 加工曲面质量,如粗糙度等 – 工件的材料特性,如硬度、强度、韧性等 – 刀具的材料、种类、形状等 – 机床特性 – 铣 削 方 式 的 选 择 : down-milling/up-milling 、 reversecuttin/plunge-cutting等 需解决的问题:影响因素多而复杂,如何建立实用的工艺数据库
一、自由曲面加工概述
自由曲面造型技术
包括: • 1)曲线、曲面和实体的数学描述 • 2)曲面建模方法 • 3)曲面逆向工程
光学自由曲面多轴精密加工机床几何误差测量及补偿方法

光学自由曲面多轴精密加工机床几何误差测量及补偿方法光学自由曲面在聚焦、成像和组成光学系统方面具有一定的优势,在众多领域得到广泛应用。
由于光学模具表面的曲面复杂性以及高精度特性,通常需要多轴联动精密机床加工获得。
机床的运动精度是影响光学模具加工精度的关键因素,其中几何误差是机床误差的主要来源,因此对数控机床几何误差进行精确地测量及补偿,可有效地提高机床的加工精度。
然而,在精密机床几何误差辨识时,由于传统辨识方法对仪器测量误差和仪器摆放误差敏感,致使在测量过程中引入的测量误差,将掩盖或显著影响精密机床自身的辨识误差。
为此,本文针对光学自由曲面多轴精密加工机床,开展了直线轴和旋转轴的几何误差测量和辨识理论与方法、整机的几何误差补偿策略、以及透镜阵列加工与补偿实验研究。
主要研究内容及成果如下:(1)以RTTTR型五轴精密加工机床为例,在分析了机床各轴拓扑结构的基础上,通过多体系统理论,依次沿刀具链和工件链,建立了机床的几何误差模型,并对其主要几何误差分布特点进行分析,明确辨识的几何误差对象,为后续的几何误差辨识与精密机床误差补偿提供基础。
(2)分析了仪器测量和仪器摆放误差对直线轴几何误差辨识结果的影响,提出一种基于多体系统理论的直线轴几何误差测量及辨识方法。
该方法通过引入空间冗余测量,实现直线轴几何误差的鲁棒性辨识。
在此基础上,分析了位置误差对辨识结果的影响,采用辨识矩阵范数评价方法,获得最优的测量位置,有效地降低了位置误差对辨识结果的影响。
仿真结果表明,该方法相比传统的三点法对测量仪器的测量误差,具有更好的鲁棒性。
测量实验结果显示,计算得到机床单轴的定位误差与实际测量值的最大偏差不大于0.18μm,从而证实该方法的有效性。
(3)针对转动轴几何误差数目多且受测量误差影响显著的特点,提出了一种基于球杆仪的转动轴几何误差辨识方法。
该方法基于运动学理论,推导了球杆仪测量的运动学方程,揭示球杆仪摆放位置和测量方向与辨识误差的敏感关系,从而实现转动轴角度误差和位移误差的解耦辨识,有效降低了辨识矩阵的条件数,提高辨识精度。
自由曲面加工刀具路径生成高精度变步长算法研究

自由曲面加工刀具路径生成高精度变步长算法研究
本文探讨了一种高精度的自由曲面加工刀具路径生成算法,该算法采用了变步长技术来提高加工精度。
首先通过对曲面进行数据采集和处理,得到曲面的离散点集,并根据点集数据建立曲面模型。
然后,根据曲面模型生成初步的加工路径,并通过逐步细化和优化路径来达到高精度的加工要求。
为了提高路径细化的精度,该算法采用了变步长的策略,即根据加工精度要求和曲面局部几何特征自适应地调整路径步长。
最后,通过实验验证了该算法的有效性和高精度性能。
- 1 -。
减小精确加工自由曲面刀具轮廓误差的方法

discrete motions to approximate complex paths incurs voluminous part programs and limits the “smoothness” with which the tool paths are executed.
2.
2.1
Relevant Work
Tool-Path Generation Background
In CNC machining, a tool-path generation algorithm is required for the realisation of a sculptured surface design. The surface generated as a result of this algorithm should follow the contour of the desired surface as closely as possible. In addition, the surface should fall within an acceptable tolerance. The following literature review gives an overview of the work that has been done on tool-path generation for CNC machines. In the past two decades, a number of effective CNC toolpath generation methods have been proposed for the CNC machining of various surface shapes [1–12]. These approaches were able to predict the step ahead positions of the cutter based on calculations using equation which are obtained from the mathematical integration of the velocity/acceleration components of the cutter. For linear path generation, the methods have been proved to be very good. However, when dealing with curved tool-path generation, they demonstrate certain limitations when producing smooth curvature gradients. Much work has been conducted in the past decades [13–21] on eliminating or reducing the drawbacks of curved toolpath generation. Yeung and Walton [13] have introduced a method of generating an NC tool path with an arc spline and with fewer data than a linear interpolation. The main advantage of this method is the data reduction. A biarc tool path proposed by them uses continuous circular arc segments to approximate the smooth curve. For a given tolerance, it can remove excess data points and simultaneously reduce the size of the cutter location file. Qiu et al. [14] have proposed a new algorithm for circular arc interpolation of planar curves. They have addressed the problems of how to determine the parameters of the circular arcs and how to minimise the number of arcs according to the desired interpolation accuracy. The Newton–Raphson method is employed for resolving the nonlinear equation and high computational efficiency is obtained. Experimental trials show the algorithm to be simple enough and it can be applied to NC contour manufacturing. Lo and Hsiao [15] have developed a CNC machine tool interpolator with path compensation for repeated contour machining. They propose a contour-error calculation, data extraction and contour-error interpolation algorithm. Lo [16] has developed a new type of CNC machine tool interpolator that can generate the cutter path for the ball-end milling of a freeform surface. This surface interpolator consists of on-line algorithms for cutter contact (CC) path scheduling, CC path interpolation, and tool offsetting. Yeh and Hsu [17] have reported a speed-controlled interpolator for machining parametric curves. The proposed algorithm has significantly improved the accuracy of the speed. It results in constant speed and also satisfies specified acceleration and deceleration requirements to meet the feedrate commands.
自由曲面加工全局干涉检验与刀位修正

自由曲面加工全局干涉检验与刀位修正丁爽;黄筱调;于春建;吴彬彬;李庆楠【摘要】针对自由曲面加工过程中的全局干涉问题,提出了一种基于自适应模拟退火遗传算法(SAGA)的快速全局干涉检验方法,将全局干涉检验转化为自由曲面上点到刀具轴线段的最短距离的寻优问题,获得了曲面上点到刀轴最短距离的直接求解方法,并基于矢量方法对干涉刀位进行了修正.设计了一种新的非线性自适应度函数,避免算法过早收敛于局部最优值.算法融合了自适应的交叉、变异算子以及模拟退火思想,经Schaffer函数测试其收敛概率约为99%.应用算例分析表明:自适应SAGA在全局干涉检验时计算量约为离散法的1/4,且避免了极值方法求解不收敛的问题,能直接计算出干涉点位置及干涉量,为全局干涉检验和刀位修正提供了科学依据.【期刊名称】《南京工业大学学报(自然科学版)》【年(卷),期】2015(037)002【总页数】6页(P59-64)【关键词】自由曲面;遗传算法;全局干涉检验;刀位修正【作者】丁爽;黄筱调;于春建;吴彬彬;李庆楠【作者单位】南京工业大学机械与动力工程学院,江苏南京211800;南京工业大学机械与动力工程学院,江苏南京211800;南京工大数控科技有限公司,江苏南京211899;南京工业大学机械与动力工程学院,江苏南京211800;南京工业大学机械与动力工程学院,江苏南京211800【正文语种】中文【中图分类】TP391;TG659在高新技术发展和新产品要求不断提高的情况下,自由曲面被广泛应用于航空航天、汽车、船舶等行业的复杂零件产品中,以满足不同的使用性能[1]。
在加工自由曲面时,由于曲面的不规律性且刀具处于多自由度状态,在曲率变化较大的场合,若刀轴控制不当,在加工过程中极易产生全局碰撞干涉,轻则影响加工表面的质量,损坏工件,重则损坏机床设备,造成安全隐患[2],因此全局干涉检验及刀具姿态修正对于加工自由曲面尤为重要。
Lee等[3]将曲面用控制多边形表示,检查刀具与控制多边形是否有交点来进行全局干涉检验,但此方法只能判断刀轴与曲面是否有交点,而不能直接计算出干涉量,同时求交算法计算量比较大,将曲面用控制多边形近似表示不够精确。
自由曲面铣削误差预测

自由曲面铣削误差预测林立【摘要】在航空航天工业等行业中,对于复杂薄壁曲面零件,极易产生由工件变形引起的加工误差,这直接影响了零件的加工精度及表面质量.本文研究了薄壁叶片型面精加工切削过程中工件变形对加工精度的影响:首先利用正交试验求出球头铣刀的铣削力公式,进而结合有限元方法,编写柔性切削变形迭代算法,计算出薄壁叶片的最终变形量,并分析了叶片的变形规律,这对提高叶片加工精度具有重要的实际应用价值.【期刊名称】《现代机械》【年(卷),期】2013(000)001【总页数】4页(P7-10)【关键词】B曲面;铣削力;叶片变形;迭代算法;误差预测【作者】林立【作者单位】陕西法士特齿轮有限责任公司,陕西西安 710119【正文语种】中文【中图分类】TG659叶轮是航空发动机、汽轮机、燃气轮机、压气机、水轮机、船舶推进装置的重要零件,被广泛应用于航天、航空及其他工业领域[1]。
本文主要考虑复杂薄壁叶片加工过程中的工件变形导致的加工误差。
国内外许多学者对薄壁工件的加工误差方面做了大量研究。
郑力等学者建立了一个基于刀具、工件和机床三者一体的受力状态模型[2]。
Philippe 等建立了端铣刀的铣削力模型,预测了刀具变形引起的铣削表面误差,并对误差进行了补偿,提高了加工质量[3-4]。
1 叶片CAD 造型及CAM 轨迹规划1.1 叶片曲面造型本文的叶片数据以空间点阵方式给出,属于自由曲面范畴,由于空间点阵比较稀疏,造型前首先需要利用B 曲面反算出曲面的控制点,然后正算加密曲面点,得到叶片网格曲面(图1(a)),同理,仿照叶盆曲面的算法可以计算出叶背曲面数据,如图1(b)所示。
1.2 叶片数控加工轨迹规划将MATLAB 计算出的曲面密化后的数据点导入UG 中,生成整体叶轮造型完成如图2(a)所示。
本文加工刀具为6 mm 球头铣刀。
精加工切削余量为0. 5 mm。
本文中设置残余高度为0.01 mm,刀具接触点为单行151 个,弦高误差为0.005 mm。
- 1、下载文档前请自行甄别文档内容的完整性,平台不提供额外的编辑、内容补充、找答案等附加服务。
- 2、"仅部分预览"的文档,不可在线预览部分如存在完整性等问题,可反馈申请退款(可完整预览的文档不适用该条件!)。
- 3、如文档侵犯您的权益,请联系客服反馈,我们会尽快为您处理(人工客服工作时间:9:00-18:30)。
1. Introduction
Process planning is one of the functions for the manufacturing that determines which processes and parameters are to be used to product a part from its initial form to a final form predetermined in an engineering drawing. The input to the system will be a two- or three-dimensional computer-aided design (CAD) model. The model contains not only the shape and dimensioning information, but also the tolerance and special features [1]. A CAD/CAM system within a manufacturing facility generates a NC program containing a series of coded instruction directly from the CAD model. Also, the NC program directly affects the accuracy and cost of the part and makes specific trajectories on the part being processed called tool path. In milling operation, a tool moves along the tool path at cutter contact point (CC) linearly, that is a curved surface is approximated by a series of straight line segments as shown in Fig. 1. The accuracy of this linear approximation
Young-Keun ChoiÃ, A. Banerjee
Department of Industrial Engineering, Texas A&M University, College Station, TX, 77843-3131, USA
Received 30 January 2006; pted 25 April 2006 Available online 12 June 2006
controlled by deviation is called tolerance. There is also scallop or cusp between adjacent tool paths (Fig. 1). After the machining, a grinding operation is needed to smooths the machined surface. However, the grinding operation to remove the scallop between adjacent tool paths is very expensive and time consuming. The large scallops increase amount of machining time and cost to smoothen the machined surface. Therefore, appropriate tool path is very important to reduce the amount of secondary processes such as grinding and/or polishing. It is also important to generate tool path with less cutter contact point with given tolerance and scallop height because we assume that the more line segments, the more is the machining time. The length of each line segment between CC points is called a forward step denoted as s and the maximum allowable deviation is referred to as the tolerance denoted as e in Fig. 1. Further, the distance between two adjacent tool paths called the side step is denoted as g and the maximum allowable height of scallop is called the scallop height denoted as h in Fig. 1. The value of e and h are determined in advance and then s and g are determined from the value of e and h, respectively [2].
ÃCorresponding author. Tel.: +82 10 7731 7478; fax: +82 33 644 4004. E-mail address: youngkeun05@ (Y.-K. Choi).
0890-6955/$ - see front matter r 2006 Elsevier Ltd. All rights reserved. doi:10.1016/j.ijmachtools.2006.04.014
Abstract
This paper focuses on developing algorithms that generate tool paths for free-form surfaces based on the accuracy of a desired manufactured part. A manufacturing part is represented by mathematical curves and surfaces. Using the mathematical representation of the manufacturing part, we generate reliable and near-optimal tool paths as well as cutter location data file for post-processing. This algorithm includes two components. First is the forward-step function that determines the maximum distance, called forward step, between two cutter contact (CC) points with a given tolerance. This function is independent of the surface type and is applicable to all continuous parametric surfaces that are twice differentiable. The second component is the side step function which determines the maximum distance, called side step, between two adjacent tool paths with a given scallop height. This algorithm reduces manufacturing and computing time as well as the CC points while keeping the given tolerance and scallop height in the tool paths. Several parts, for which the CC points are generated using the proposed algorithm, are machined using a three-axes milling machine. As part of the validation process, the tool paths generated during machining are analyzed to compare the machined part and the desired part. r 2006 Elsevier Ltd. All rights reserved.
2. Overall conceptual approach
Fig. 1. Forward and side step.
In this paper, we propose a new methodology that generates tool path for free-form surfaces from the given tolerance and scallop height. Then, a real part is machined by NC codes generated by the proposed algorithm to verify the accuracy of the part.