高速线材飞剪机控制优化
邯钢2250mm热轧线飞剪常见故障分析及控制优化
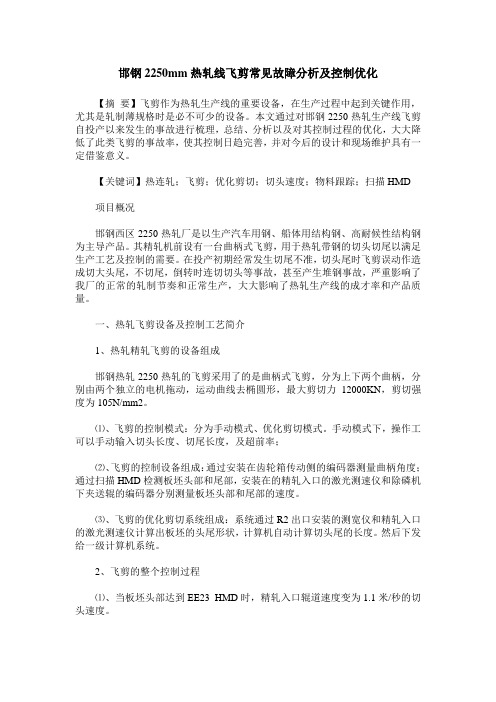
邯钢2250mm热轧线飞剪常见故障分析及控制优化【摘要】飞剪作为热轧生产线的重要设备,在生产过程中起到关键作用,尤其是轧制薄规格时是必不可少的设备。
本文通过对邯钢2250热轧生产线飞剪自投产以来发生的事故进行梳理,总结、分析以及对其控制过程的优化,大大降低了此类飞剪的事故率,使其控制日趋完善,并对今后的设计和现场维护具有一定借鉴意义。
【关键词】热连轧;飞剪;优化剪切;切头速度;物料跟踪;扫描HMD 项目概况邯钢西区2250热轧厂是以生产汽车用钢、船体用结构钢、高耐候性结构钢为主导产品。
其精轧机前设有一台曲柄式飞剪,用于热轧带钢的切头切尾以满足生产工艺及控制的需要。
在投产初期经常发生切尾不准,切头尾时飞剪误动作造成切大头尾,不切尾,倒转时连切切头等事故,甚至产生堆钢事故,严重影响了我厂的正常的轧制节奏和正常生产,大大影响了热轧生产线的成才率和产品质量。
一、热轧飞剪设备及控制工艺简介1、热轧精轧飞剪的设备组成邯钢热轧2250热轧的飞剪采用了的是曲柄式飞剪,分为上下两个曲柄,分别由两个独立的电机拖动,运动曲线去椭圆形,最大剪切力12000KN,剪切强度为105N/mm2。
⑴、飞剪的控制模式:分为手动模式、优化剪切模式。
手动模式下,操作工可以手动输入切头长度、切尾长度,及超前率;⑵、飞剪的控制设备组成:通过安装在齿轮箱传动侧的编码器测量曲柄角度;通过扫描HMD检测板坯头部和尾部,安装在的精轧入口的激光测速仪和除磷机下夹送辊的编码器分别测量板坯头部和尾部的速度。
⑶、飞剪的优化剪切系统组成:系统通过R2出口安装的测宽仪和精轧入口的激光测速仪计算出板坯的头尾形状,计算机自动计算切头尾的长度。
然后下发给一级计算机系统。
2、飞剪的整个控制过程⑴、当板坯头部达到EE23 HMD时,精轧入口辊道速度变为1.1米/秒的切头速度。
⑵、当板坯头部到达KZ21HMD时,飞剪曲柄动作到310度的等待剪切位。
⑶、当板坯头部到达MA01扫描HMD时,激光测速仪开始测量板坯通过HMD的距离。
广钢高线厂N1飞剪的电气与PLC控制系统分析

为保证剪切 质量 , 系统 控 制要 求快 速 、 确 , 该 精
一
方 面保 证 切 除 轧 件 头 尾 轧 损 的 部 分 , 一 方 面 又 另
尽 量 少 切 除 合 格 的 部 分 , 提 高 成 材 率 。 因此 , 系 以 该
式 及系 统设 计方 法 。
关键词
N ELECTRI & PLC C CO NTRO L SYS TEM FO R I N FLYI NG — H EAR F I H — PEED I E S o H G S W R FACTo RY N S I GI C
4 0 电 流 5 0 励 磁 电 压 2 0 电 流 2 A, 速 4 V, 4 A, 2 V, 6 转
6 27r m 。 p
飞 剪 是 在 轧 件 运 动 过 程 中 , 刃 产 生 相 对 运 动 剪
而将 轧 件 切 断 的 设 备 。 在 广 钢 高 线 厂 的 生 产 过 程
中, N1飞 剪 位 于 I 中轧 机 与 Ⅱ中 轧 机 之 间 , 来 对 用  ̄5 mm 轧 件 进 行 切 头 、 尾 和 事 故 碎 断 时 进 行 剪 2 切
a r cs l o e s r he s a i ua iy by m e nso nd p e ie y t n u e t he rng q lt a fPLC .The a tc e d pit he c t o ln r il e c st on r li g mod e a he s s e d sg t od o 1 fy n s e re e t i i e a nd t y t m e i n me h fN l i g— h a l c rc drv nd PLC u o tc c t o n t e p o— a t ma i on r li h r
高速线材主控台控制操作技术

第一章主控台操作分工与操作技术素质要求主控台是控制全轧线生产的中心操作室,是全厂的中央信息处理站,在高速线材轧机的连轧控制中,主控台对轧制的正常顺利进行起着关键作用。
一、主控台所管辖的区域设备主控台所管辖的区域设备有:(1)加热炉出口处夹送辊、粗轧机组、中轧机组、预精轧机组、精轧机组以及夹送辊、吐丝机。
(2)粗轧机组1#机架前卡断剪、粗轧机组8#机架后的曲柄剪、预精轧机组前的回转飞剪、事故卡断剪、精轧机组前的回转飞剪、事故碎断剪及事故卡断剪。
(3)轧线上所有活套控制器。
(4)出炉辊道、分钢辊道(5)预水冷段,水冷段二、主控台的职能与控制对象主控台的职能与控制对象有:(1)设定、调用、修改轧制程序。
(2)控制上述所有轧制区设备的动作及运行。
(3)监控轧制区的轧制过程,实现轧制工艺参数和程序控制最优化。
(4)控制轧机各机组的轧辊冷却水开与闭。
(5)组织、协调轧制生产工艺,保证生产的正常进行。
(6)担负轧制生产线的日常生产信息传递,进行轧制区物料跟踪方面的操作。
(7)有关生产数据报表的记录与汇总。
(8)监视全生产线的机械、电气、能源介质供应系统的设备运行状况与故障显示。
三、主控台与生产调度室及各操作台(点)的分工和关系1、主控台与生产调度室的关系主控台主要负责生产线上轧制生产的组织与协调,即偏重于轧钢生产人员本身的内部指挥;生产调度室主要负责轧制生产的总体指挥与协调,它的任务有:与水、电、风、气等外部能源介质供应单位的联系,对高速线材厂(车间)各专业(轧钢、电气、机修)的指挥与协调,即偏重于轧钢外部的联系。
2、主控台与各操作台(点)的关系根据高速线材生产工艺流程特点,轧制生产线上配置有6 个操作台:入炉加热出钢操作台(负责原料区原料的入炉与计量、加热炉加热工艺操作和出钢操作);主控台(负责轧制区的轧制生产工艺操作和轧钢生产协调);集卷操作台(负责散卷采集操作);打包操作台(负责将散卷打包操作);称重标牌操作台(负责成品盘卷的称量,标牌打印操作);卸卷操作台(负责卸卷操作)。
高速棒材倍尺飞剪工艺技术改进

山西冶金SHANXI METALLURGYTotal181No.5,2019 DOI:10.16525/14-1167/tf.2019.05.45总第181期2019年第5期高速棒材倍尺飞剪工艺技术改进李罗扣,刘强,李文平,丁建军(首钢长治钢铁公司轧钢厂,山西长治046031)摘要:简要介绍了长钢轧钢厂高速棒/线材复合生产线工艺布置,通过对高棒倍尺飞剪后摆杆系统改进、尾部倍尺进行优化,降低了故障率,提高了生产效率。
关键词:高速棒材倍尺飞剪改进中图分类号:TG334.9文献标识码:A文章编号:1672-1152(2019)05-0113-02收稿日期:2019-08-10第一作者简介:李罗扣(1973—),男,本科,毕业于内蒙古科技大学,工程师,现为首钢长治钢铁有限公司轧钢厂厂长。
121—前伺服电缸摆杆;2—倍尺飞剪;3—气缸式后摆杆分钢器图1飞剪结构示意图生产实践·应用技术首钢长治钢铁公司(全文简称长钢)轧钢厂高棒生产线是在原轧钢厂高线北线生产线中,从预精轧后通过分岔通道引出改造而成的复合型生产线。
该生产线新增4号剪前夹送辊1套,4号飞剪及碎断剪1套,侧活套1套,4架顶交45毅精轧机组1套,倍尺飞剪前夹送辊1套,高速倍尺圆盘飞剪(以下简称倍尺飞剪)1套,夹送制动辊2套,108m转毂式落料系统及冷床1套,以及后续棒材精整设备1套。
根据生产产品及规格要求可以在高线和高棒之间切换。
生产线于2018年8月1日一次性热负荷试车成功,并于次月达到设计目标。
1高速棒材倍尺飞剪系统组成倍尺飞剪系统由前伺服电缸控制摆杆系统、倍尺飞剪及后气缸控制摆杆分钢导槽组成。
其中伺服电缸摆杆位于高速飞剪前,可水平左右摆动,伺服电机驱动电缸带动摆杆做水平往复运动。
电缸摆杆工作时有两个工位,飞剪剪切后,摆杆摆动到另一个工位,此时飞剪再进行剪切,循环往复。
后气缸控制摆杆分钢导槽有左右两个通道,引导剪切后的轧件进入不同的通道。
热轧2032生产线飞剪剪切异常分析与优化方案
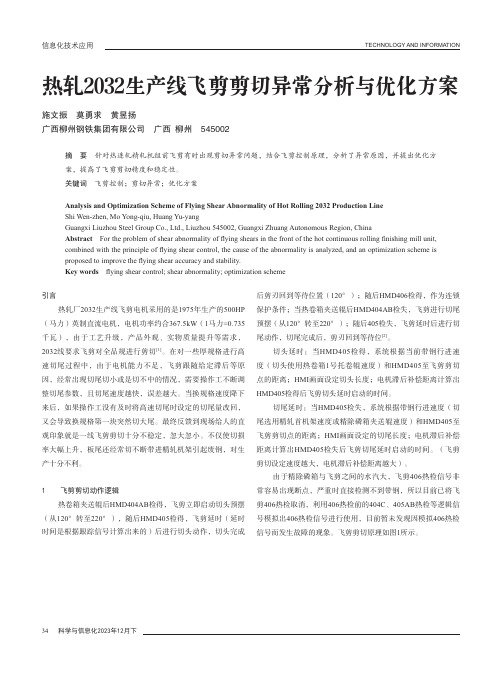
TECHNOLOGY AND INFORMATION34 科学与信息化2023年12月下热轧2032生产线飞剪剪切异常分析与优化方案施文振 莫勇求 黄昱扬 广西柳州钢铁集团有限公司 广西 柳州 545002摘 要 针对热连轧精轧机组前飞剪有时出现剪切异常问题,结合飞剪控制原理,分析了异常原因,并提出优化方案,提高了飞剪剪切精度和稳定性。
关键词 飞剪控制;剪切异常;优化方案Analysis and Optimization Scheme of Flying Shear Abnormality of Hot Rolling 2032 Production Line Shi Wen-zhen, Mo Yong-qiu, Huang Yu-yangGuangxi Liuzhou Steel Group Co., Ltd., Liuzhou 545002, Guangxi Zhuang Autonomous Region, ChinaAbstract For the problem of shear abnormality of flying shears in the front of the hot continuous rolling finishing mill unit, combined with the principle of flying shear control, the cause of the abnormality is analyzed, and an optimization scheme is proposed to improve the flying shear accuracy and stability.Key words flying shear control; shear abnormality; optimization scheme引言热轧厂2032生产线飞剪电机采用的是1975年生产的500HP (马力)英制直流电机,电机功率约合367.5kW (1马力=0.735千瓦),由于工艺升级,产品外观、实物质量提升等需求,2032线要求飞剪对全品规进行剪切[1]。
高速液压飞剪控制系统优化

L I U J i e ,XI N Ya n g g u i
( 1 . G u a n g z h o u A r t g e t T e c h n o l o g y C o . , L t d . , G u a n g z h o u G u a n g d o n g 5 1 0 6 6 3 ,C h i n a ;
系统是拉拔机生产线 的关键设备 ,其控 制性 能的好 坏 直接影 响产 品的成 材率 和生产效率 。 为 了提 高生产 效率和成材率 ,必须对液压飞剪控 制 系统进行 优化 。液压飞剪控制系统包括液压 和控制 系统 两部分 ,不仅需要 同时对液压 系统 和控制 系统两
ห้องสมุดไป่ตู้
器用于检测或反馈 电机 的运行速度 ,其采集的数据准 确与否直接影响 同步 的效果 ;直流 电机为棒线材 的输
送提供源动力 ;人机界面 实现参数 的设定 和对设备基 本状 况的实 时监控 等功能。
中图分类号 :T P 2 7 1+ . 3 1 文献标识码 :B 文章编号 :1 1 3 0 1 — 3 8 8 1( 2 0 1 3 )2 2— 0 8 3~ 2
Opt i mi z a t i o n o f Co n t r o l S y s t e m o f Hi g h- S p e e d Hy d r a ul i c Fl y i n g- S he a r
飞剪设备使用、维护说明书

目录一、技术参数 (1)1. 工艺描述 (1)2. 主要技术参数 (1)二、起吊、运输、安装 (2)三、工作环境 (3)四、润滑 (3)五、运行 (4)1. 运行前检查 (4)2. 启动 (4)3. 运行 (5)六、安全 (11)七、维护保养 (11)八、故障处理 (12)一、技术参数1. 工艺描述小棒飞剪:面对剪刃侧,走钢线为从左至右。
高线飞剪:面对剪刃侧,走钢线为从右至左。
功能:在正常工作时,飞剪用于对轧件进行切头,确保轧件无端部变形、黑头或开裂,有利于轧件进入下游轧机组;在发生事故时对轧件进行碎断以缩短事故处理时间。
形式:小棒粗轧飞剪启停式曲柄飞剪小棒一中轧飞剪启停式曲柄飞剪小棒二中轧飞剪启停式回转剪小棒精轧后飞剪启停式曲柄-回转组合剪小棒碎断剪连续式回转剪高线粗轧飞剪启停式曲柄飞剪高线中轧飞剪启停式回转剪2. 主要技术参数剪切断面(mm)剪切速度(m/s)电机功率(kW)电机转速(r/min)小棒粗轧Φ102~Φ1150.38~1.0425743小棒一中轧Φ53~Φ82 1.1~3.3600745小棒二中轧Φ30~Φ44 3.42~9.0425743小棒精轧后Φ19.6~Φ78 1.35~15.4600745小棒碎断剪Φ19.6~Φ41 5.3~15.4901450高线粗轧Φ72~Φ77.30.45~1.6425743高线中轧Φ32.5~Φ34.6 2.48~8.0425743二、起吊、运输、安装在起吊、运输、安装过程中应遵循如下注意事项:1) 起吊整个机列时,应使用底座上的吊耳。
注意: 钢丝绳钢链条与底座接触部分应垫橡胶皮等物加以保护。
2) 飞剪机列运输、存放时应放在木块上或平滑干燥的基础之上,请勿直接放在水泥地面上。
3) 请勿推、拉飞剪机列,以免损伤接触底面。
4) 飞剪机列到货后如半年之内不安装,要对外露的加工面重涂防锈油,谨防锈蚀。
5) 飞剪机列安放在安装基础上之后,需用水平仪找正,其水平度不得低于0.1/1000。
二高线1号飞剪剪切方式的改进

从而损坏减速箱的问题 ,也使飞剪运行周期 降
如 果 只 是 单 纯 提 高 飞 剪 的速 度 ,则 飞剪 的
2 0 7 。
b 改进后的飞剪剪切动作示意 图
切 尾 长 度 不 容 易 控 制 。 对 于提 高 成材 率 有 较 大 的影 响 ,而 且 会 造 成 钢 的 尾 部 往 上拱 起 ,容 易 损 坏 导卫 。如果 在 飞剪 升 速 的过程 中开 始剪 切 , 就 可 减 少 原 来 飞 剪 在 减 速 过 程 中 的剪 切 时 间 ,
Cu tn o e Re o m a i n f r No 1 Fl i g S e r o . ti g M d f r to o . y n h a fNo 2
H i h-s e i e R o ne g pe d W r d Li
ZHAO n — ng Do g— pi
作相 同。当 1 号飞剪前 的热检检测到无钢信号
时 ,飞剪 中的 T 0 经 过相 应 的延 迟 时 间 ,飞 4 0板
剪开 始 剪切 ,剪 切完 成后 ,等 待下 一动 作 。
2 存在 问题及其 改进
21 剪切 问题 .
制 柜通 过 pob s rf u 网传递 数 据 。6 A 0柜 内加 装 i R 7
处 于 第 六 架 初 轧 机 之 后 ,第 七 架 轧 机 之 前 ,主 要 功能是 切 头 、切 尾 和事故 碎 断等 。
1 飞 剪 的控 制 系 统 由 S — 0 号 7 4 0西 门子 P C L. 6 A 0控 制 柜 及 现 场 执 行 设 备 组 成 ,P C与 控 R 7 L
生 产 节 奏 不 快 ,飞 剪 运 行 较 正 常 ,随着 生 产 节 奏 加 快 ,飞 剪 剪 切 问题 逐 渐 暴 露 出来 :切 尾 时 速 度 过 快 会 造 成 钢 的尾 部 往 上 弯 ,极 易 损 伤 第
论述稳定飞剪头尾剪切长度的技术改造

论述稳定飞剪头尾剪切长度的技术改造在高速线材轧制厂中,飞剪起着至关重要的作用,是保证正常的连续轧制,满足最优的工艺要求及轧制事故的处理的关键设备。
1 飞剪的主要功能飞剪主要完成轧件的切头、切尾和事故剪切功能。
飞剪的头尾剪切功能在轧制工艺中非常重要,它能够切除轧件易出事故的头尾,是保证轧件高通过率的关键。
飞剪头尾剪切长度的稳定控制在飞剪的控制技术中极为重要,一方面必须保证切除干净轧制工艺所要求的长度,如果短于要求的长度会导致轧件易出事故的头尾部分残留造成堆钢,另一方面剪切长度不宜超出设定长度,否则会切掉完好的轧件,造成头尾剪切损耗过大,从而降低成材率。
我厂飞剪头尾剪切的长度一直不稳定,实际偏离设定长度较大,有时比设定长度长一些,有时又比设定短很多。
剪切长度的不稳定,容易造成堆钢事故,影响生产的顺利行进。
2 飞剪的头尾剪切控制的基本原理我厂飞剪的电控系统采用美国GE公司的GE90-30系列PLC与西门子6RA70系列直流传动装置。
其头尾长度的控制主要使用GE90-30系列PLC的高速计数器HSC,轧线上的两个热检信号和上机架的脉冲编码器信号送入高速计数器,当轧件通过第1个热检时高速计数器开始对脉冲编码器信号计数,当轧件通过第2个热检时将计数值保存到存储器中,计数器继续计数。
根据保存到存储器中的计数值计算轧件出口速度与脉冲当量,最终计算出切头启动的计数值,当高速计数器一直累加的计数值达到高速计数器启动计数值,则启动切头,切尾的原理与切头大致相同。
飞溅控制系统图如图1所示:图1 飞剪控制系统图3 稳定头尾剪切长度的技术改进措施3.1 增加热检来稳定1#热检预置信号,精确脉冲当量计算飞剪剪切长度变化时,经常是由于脉冲当量计算不准确导致。
脉冲当量的含义为单个脉冲对应轧件所走的距离,是头尾剪切计算的重要依据。
脉冲当量通过两个热检之间的实际距离除以轧件通过2#热检时保存的计数值得到。
两个热检之间的实际距离固定,但轧件通过2#热检时保存的计数值与两个热检的信号有关。
棒材倍尺飞剪的控制与优化
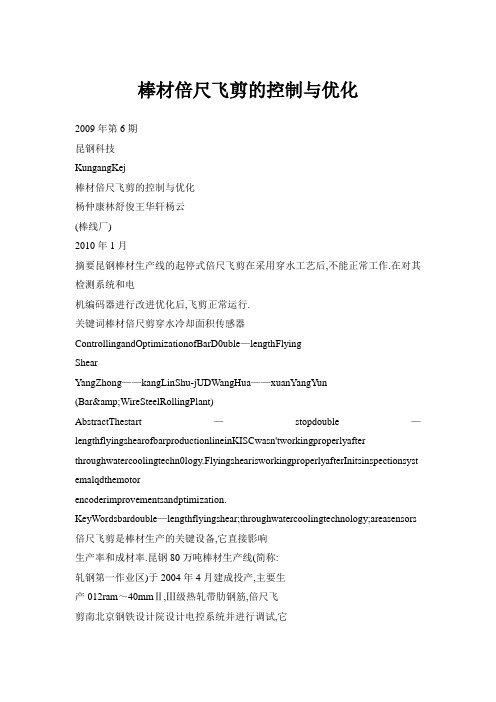
棒材倍尺飞剪的控制与优化2009年第6期昆钢科技KungangKej棒材倍尺飞剪的控制与优化杨仲康林舒俊王华轩杨云(棒线厂)2010年1月摘要昆钢棒材生产线的起停式倍尺飞剪在采用穿水工艺后,不能正常工作.在对其检测系统和电机编码器进行改进优化后,飞剪正常运行.关键词棒材倍尺剪穿水冷却面积传感器ControllingandOptimizationofBarD0uble—lengthFlyingShearYangZhong——kangLinShu-jUDWangHua——xuanYangYun(Bar&WireSteelRollingPlant)AbstractThestart—stopdouble—lengthflyingshearofbarproductionlineinKISCwasn'tworkingproperlyafter throughwatercoolingtechn0logy.FlyingshearisworkingproperlyafterInitsinspectionsyst emalqdthemotorencoderimprovementsandptimization. KeyWordsbardouble—lengthflyingshear;throughwatercoolingtechnology;areasensors 倍尺飞剪是棒材生产的关键设备,它直接影响生产率和成材率.昆钢80万吨棒材生产线(简称:轧钢第一作业区)于2004年4月建成投产,主要生产012ram~40mmⅡ,Ⅲ级热轧带肋钢筋,倍尺飞剪南北京钢铁设计院设计电控系统并进行调试,它操作简单,维护方便,工作稳定,剪切精度高,能够获得最大的产品收得率.该系统在生产线采用穿水冷却新技术后,出现了不剪切的问题,经过改进优化,倍尺飞剪动作的可靠性和倍尺精度得到保证.1设计原理起停式飞剪在不剪切时是静止的,此位置称之为原位,当控制系统发出剪切信号时,剪刀机从静止迅速加速到最高速度对轧件进行分断剪切,剪切完成后迅速停止于原位,其运转不大于一周.整个倍尺飞剪由机械部分和电气部分组成.剪机为组合式结构,分3种形式:回转式,曲柄式,曲柄+飞轮式;传动系统为美国GE公司全数字直流调速装置6KDV31350Q4F40D3型;电机采用上海南洋电机厂生产的ZTFS一315—42型280KW低惯量电机(满足起,停要求),额定电压440V,额定电流704A,基速650r/min,励磁电压220V,励磁电流24A.控制系统由CPU,高速计数器模块(HSC),轴定位模块(APM),数字输人输出模块(DI/D0)等组成.检测系统由HMD一0,HMD一1,HMD一2(热金属检测器),轧线出口脉冲编码器,电机轴脉冲编码器组成,见图1.昆钢科技2009年第6期(誓0谁牦I乏一一.0一:二j0二二圈lIs控利糸统Figure1ControlSystemofFlyingShear1.1轧件长度测量及剪切长度控制原理式中:LPP一一脉冲当量,mm;飞剪系统对轧件长度的测量及剪切长度控制原Dw——工作辊径,ram;理如式(1),轧件通过长度与单位脉冲对应,当PPR一一编码器每转脉冲数;成品轧机工作辊径不变时,LPP基本为常数,L与Ni一一轧机减速箱速比,倍. 成正比,长度测量变成脉冲计数.通过两个HMD测量脉冲当量的方法称为测量L:N×LPP(1)优先,即直接测量法,计算公式为式(3):式中:L一一轧件长度,mm;N——成品轧机编码器输出脉冲数,个;LPP一一脉冲当量,mm.式(1)可理解为:假设HMD一1,HMD一2之间的距离为10米,所需分段的倍尺长度为100米,轧件头部通过此l0米的时间为1秒,计数器所记录的出口机架脉冲数为10240个,那么在轧件速度稳定的情况下lO秒后计数器所记录的出口机架脉冲数为102400个,轧件通过长度为100米,此时达到设定长度,控制系统发出命令启动飞剪,从而得到一个倍尺品.1.2脉冲当量的计算脉冲当量的计算有两种方式:辊径优先和测量优先.从工作辊径计算脉冲当量的方法称为辊径优先(理论计算法),计算公式为式(2):LPP=竹Dw/(PPRxi1(2)LPP=L/N(3)式中:LPP一一脉冲当量,mm;L一一HMD一1~HMD一2之间的距离,mm;N一一轧件头部通过HMD一1~HMD一2时记录的脉冲数,个.两种计算方法各有优,缺点.对于辊径优先而言,其优点是:脉冲当量值稳定不变,即脉冲当量的稳定度非常好;缺点是:1)辊径估计不准.工艺上有两个辊径,即工作辊径和辊环直径.轧线上设置的出口线速度是按照工作辊径计算出来的,而轧件实际行走的线速度是比设置的出口线速度快的,轧件经过轧辊的挤压有一定的前滑量,前滑值一般在3%~5%之间,因此,在飞剪设置工作辊径时可以按工艺工作辊径×5%进行设置.辊环直径是所安装的轧辊的最大辊径,因此在辊径估计不准时,可以先按辊环直径进行设置.2)辊径变化2009年第6期杨仲康,林舒俊,王华轩等:棒材倍尺飞剪的控制与优化不能自适应.在轧钢的过程中,随着时间的推移,因为下列原因可导致工作辊径的变化:轧辊压下量调整,轧辊磨损,轧辊温度变化引起的轧辊变形等等.而辊径优先法永远按照设定辊径进行测长,测速,剪切,对辊径的变化不能自动改变.对于测量优先而言,其优点是:脉冲当量值准确度高,能自动适应辊径变化;缺点是:易产生随机误差.测量优先的脉冲当量值完全依赖于轧件头部瞬间经过HMD一1和HMD一2热金属检测器时,能否被检测到.对于辊径优先和测量优先的使用通常是根据两种测量方法的优势和缺陷,可以在轧钢的初期,即调试完成后第一次轧钢,或更换热检后或调整热检角度及灵敏度后或调整热检位置后的第一次轧钢,或增加水冷以后的第一次轧钢,操作人员对热检检测不信任时,先用辊径优先法,待在轧辊压下量调整完毕,轧件尺寸合格后,经过几根钢的轧制,十个脉冲当量的测量值偏差均在2‰以内,确认热检测量准确后,再使用测量优先.1.3应急剪切模式倍尺飞剪的应急剪切模式,是针对当来自出口机架脉冲信号有故障时或HMD一1或HMD一2有故障时,在轧线速度稳定时,也可获得较好的剪切精度.所选定的关键热金属检测器(通常为HMD一2)必须完好.进入应急剪切状态后,系统根据设定的轧件线速度及分段长度给出分段参考时间来对轧件进行分断剪切.但在实际生产过程中,轧线速度往往不稳定,从而倍尺得不到优化,有时成材率和定尺率不能满足要求.2倍尺飞剪系统的优化2.1倍尺飞剪存在的问题倍尺飞剪检测系统工作时,通过热金属检测器采集可见红外光源,经光电处理输出一个高电平信号,进入PLC系统.比如:轧件HMD一1到HMD一2之间的距离为A,HMD一2到倍尺剪之间的距离为B.各个品种的线速度不同,所以通过A所需的时间也不同,在PLC系统中,倍尺的长度是根据出口机架编码器的脉冲数量来计算的.假设轧件的头部在通过A这段距离时PLC系统共测得N个脉冲数量,倍尺长度为L,则:(L/A)×N就等于当前倍尺长度对应的脉冲数量,当PLC系统的高速记数模块计够当前倍尺长度对应的脉冲数量时,发出剪切信号使剪刀机动作,剪切出符合要求的倍尺产品.同时在剪刀机的剪刃闭合瞬问倍尺剪PLC系统发出一个剪刃闭合信号给冷床PLC系统,延时以后冷床裙板动作.当尾钢倍尺剪不进行剪切时,冷床裙板动作的HMD2信号消失,同时剪刀机的剪刃未闭合,倍尺剪PLC系统同样发出一个信号给冷床PLC系统, 延时以后冷床裙板动作.当应用穿水冷却工艺生产时,在精轧机出口,即穿水冷却系统的人口处,HMD1检测到轧件信号至轧件通过HMD2(穿水冷却系统出口处)的一段距离内,由HMD2发出两路高电平信号分别送到倍尺剪控制系统和高速计数模块,这时高速计数模块开始采集成品出口机架电机编码器的脉冲数量,并与倍尺剪控制系统所设定的倍尺长度对应的脉冲数量进行比较,在达到设定倍尺长度对应的脉冲数量时,控制系统发出剪切信号使倍尺剪动作,进行剪切.由此可以看出,决定倍尺剪能否正常剪切的关键是:HMD1,HMD2能否准确,稳定的检测到轧件通过信号,而通常所选用的低温型热金属检测器检测的被测物的表面辐射温度需~E300~C~1400~C 之间才能正常工作.在穿水轧制过程中,因为轧件的表面温度过低(300cC左右),导致了HMD2不能检测到轧件信号,破坏了剪刀机正常工作的条件,导致剪刀机不能剪切.为了解决这个问题,采用剪刀机"应急剪切"功能,只能选择HMD1为关键检测器.这样一来,第一段倍尺是HMD1检测到轧件信号才开始计时,所以倍尺长度比设定值短了25m(穿水管道的长度),而尾钢则长出25米,从而使得尾钢上不了冷床.因此,导致成品的倍尺长度不能调整,尾钢上不了冷床等一系列问题.此外,倍尺剪电机的编码器控制着倍尺剪的剪切和定位,若编码器出现故障则会出现堆钢事故,因编码器的电源出现问题而导致的跳轧事故是较为常见的原因.编码器的工作电源取自数字调速装昆钢科技2009年第6期置.通过对比发现:不同的数字调速装置所提供的编码器电源的电压并不相同,即使是同一台数字调速装置所提供的电源电压也不稳定,而编码器工作在一个电源不稳定的条件下,它的数据反馈也就变得不稳定甚至是错误的,最终出现速度反馈信号丢失而跳闸.2.2检测系统的优化由于倍尺剪的控制程序受设计单位的知识产权保护,不能通过修改或优化控制程序中的相关部分来解决和改善这一问题.第一作业区以简单可行,稳定运行,投入少,并能保证实现倍尺剪的全部功能为思路,设计了优化方案.1)保持原有的控制程序,仍然采用光电检测元件进行检测,重新改制一个检测元件替代原有的HMD2安装在穿水冷却系统出口处,以使轧件通过信号得到有效检测.2)保证在较宽视场范围内(垂直视场70ram)有效检测跳动较大的小物体,如:直径012mm的轧件,以避免因轧件跳动后脱离视场范围而产生信号误动作;检测距离在0.6~1.8m范围.3)保证改制的光电检测元件能同时输出两个常开性质的高电平接点信号给控制系统和高速计数模块,以满足控制条件.4)现场的安装条件不作任何变更.发射器接收器5)为编码器提供稳定的工作电源.2.3优化措施实施2.3.1检测系统通过对比测试多种光电检测元件,选择以面积传感器作为改进的基本检测元件.面积传感器是一种特殊的光电开关,可以在较宽的视场范围内检测很小的目标,它不受被测物温度高低的影响,只要有物体从面积传感器的发射器和接收器之间通过,传感器问的光束被挡住,就会输出检测信号.在原产品的基础上将普通光敏二极管更换为高灵敏度光敏管,数量由l0只增加到12只;检测视窗范围由55mm增加至70mm.为保证检测距离在0.6~1.8m范围,将光敏管工作电压提高了3V,仍然保持在额定范围内.经过72/bt~通电老化试验,元件温升保持在27~35℃正常范围内;至此,改制的传感器已具备装机条件.由于普通面积传感器输出接点均为一常开一常闭,而控制系统和高速计数模块进入控制状态需要的是两个常开性质的高电平接点,为此需将其进行输出改制,在传感器无空间容纳更多元件的情况下,新增输出接点采取了以面积传感器输出信号推动一个外接的带两常开,两常闭接点的中间继电器给出两个常开信号的方式,满足了控制要求.改进后的电气控制系统见图2.棕色701—24V棕色电源电源蓝色70一0V蓝色电源电源白色白色3S4—24V\70103(3S4.16)同步信号同步信号黑色黑色3S4—24V\701—03SH/HMD-2输出输出701—01(24V)厂—]701-0Vll…一电骡々1日怂器一…,,自弃图2改进后的飞剪控制系统Figure2ImprovedControlSystemofFlyingShear(下转44页)呲斛至至昆钢科技2009年第6期模拟量的遥测;支持2路4~20mA直流模拟量输出.⑤通讯接口:双以太网,双RS485,电力行业标准DL/T667—1999(IEC60870—5—103标准)的通讯规约.⑥对时功能:软件报文对时;硬件脉冲对时功能(支持IRIG—B码对时).⑦保护信息方面的主要功能:装置描述的远方查看;装置参数的远方查看;保护定值,区号的远方查看,修改功能;保护功能软压板状态的远方查看,投退;装置保护开入状态的远方查看;装置运行状态(包括保护动作元件的状态和装置的自检信息)的远方查看;远方对装置实现信号复归;故障录波(包括波形数据上送)功能.⑧具备冶金,钢铁行业系统的防爆认证.7结束语采用综合自动化控制方式和测控继电保护分层布置方案,并实施无人值班管理模式是变电站自动化技术的发展趋势,不仅技术上先进可行,功能完善,而且也极具经济性.鉴于变电站综合自动化系统当前缺乏统一的国家标准,因此,在草铺新区供配电网络的综合自动化系统的功能组合和设计优化过程中,应根据项目的具体情况,遵循科学,严谨的工作原则,集思广益,用发展的眼光来进行变电站综合自动化系统的建设,以保证电网安全,经济,可靠运行.参考文献:[1]丁书文,黄训诚,胡启迪,变电站综合自动化原理及应用[M].北京中国电力出版社,2002 (上接32页)因HMD2的安装位置与控制系统中的运算值是相对应的,因此在现场安装上,把改制的面积传感器安装于原HMD2的位置处.在使用中,又出现穿水管的水和蒸汽干扰了HMD2信号的问题,倍尺剪不能正常工作.为此提出了新的优化方案:将HMD2的安装位置由倍尺剪前移到倍尺剪后,并对PLC程序进行相应的修改,实现倍尺剪的稳定运行.2.3.2电机编码器编码器的工作电源直接由直流24V稳压电源提供,从根本上解决了电源的不稳定性.2.4优化效果2.4.1检测系统HMD2由热金属检测器换为面积传感器,并将其移到倍尺剪之后,保证了检测信号的可靠性又避免了外界对信号的干扰因素,确保了倍尺剪的稳定性和剪切精度.投入使用后,穿水轧制钢种的定尺率及成材率得到大幅提高,避免了"应急剪切"中出现的首段倍尺短,末段倍尺长且不能上冷床的情况.2.4.2电机编码器编码器采用工作电源单独供电后,没有出现过"速度反馈丢失"报警,从而保证了生产顺行.3结束语经过对倍尺剪的优化,达到了预期的目标;"轧机倍尺剪控制检测装置"成为公司实用新型技术专利;优化过程中积累的经验,为今后让设备发挥更好的性能提供了借鉴和参考.。
高速线材自动检测与控制安装调试工法

高速线材自动检测与控制安装调试工法中冶集团华冶资源公司天津工业设备安装分公司王文凯彭廷生杨千里薛玉龙刘艳丽1 前言近年来,随着科学技术的不断进步,国内各大钢铁公司加大对企业的技术改革,建成了一批当今世界上比较先进的新型轧机生产线,轧机采用全新的工艺布置,综合计算机管理及过程控制、网路通讯、交流变频调速等先进技术,进一步加强过程自动化控制,实现了以生产过程自动控制为主流的生产工艺。
本工法以天津钢铁有限公司全连续式140万吨/年高速线材工程自动检测与控制系统安装调试为例进行编制而成的。
2 工法特点2.1运用系统工程原理,将复杂的工程原理分解成各个层面、各个区段进行安装、调试。
将检测控制元件,进行分类、区域划分,便于设备安装和调试的实施。
2.2运用模拟手段进行系统回路的预调试,缩短了调试的绝对工期。
2.3充分利用先进的调试设备,保证了安装和调试精度。
充分利用设备和系统的自身性能,节约人力、物力。
2.4本工法适用性强,具有较强的操作性。
3 工法适用范围本工法适用于高速线材安装调试工程,同时也可以适用于轧钢棒材生产线安装调试工程。
4 工艺原理高速线材电气自动化系统配置5台SIEMENS公司的S7-400系列PLC,设有3个操作站,加热炉区、轧机区、风冷线各1个,另外还在主电室设有工程师站。
每个站均配有SIEMENS 公司的PIII工控机。
现场的润滑、液压系统以及轧线各区域配有35台ET200M,主传动采用SIEMENS公司的6RA70系列产品,交流辅传动采用SIEMENS公司的6SE70变频器,每套传动装置均配有一块CBP通信模板,用作6RA70和6SE70调速装置与PROFIBUS-DP相连的接口板。
操作站、工程师站、PLC之间的通信采用工业以太网,通信介质采用同轴电缆,PROFIBUS-DP主要完成PLC与6RA70、6SE70、WINCC以及远程ET200M之间的数据信息通信功能,PROFIBUS-DP的通信介质采用工业屏蔽双绞线。
高速棒材倍尺飞剪工艺技术改进

180管理及其他M anagement and other高速棒材倍尺飞剪工艺技术改进苏 鹏(河钢股份有限公司承德分公司、河北省钒钛工程技术研究中心,河北 承德 067000)摘 要:轧钢厂棒材产线主要由轧机、辊道、飞剪、倍尺飞剪、冷床、打包机等设备组成,棒材产线按照客户的定制需求进行轧制,在满足客户需求上倍尺飞剪起到了关键作用,是确保轧制精度的关键设备。
同时,随着客户需求的不断高端,需要对棒材倍尺剪进行持续优化,释放设备的技术效能。
基于此,本文对高速倍尺飞剪工艺技术改进进行分析,仅供参考。
关键词:轧钢厂;棒材;倍尺飞剪工艺中图分类号:TG333.21 文献标识码:A 文章编号:11-5004(2020)10-0180-2收稿日期:2020-05作者简介:苏鹏,男,生于1985年,汉族,河北承德人,本科,工程师,研究方向:电气工程及其自动化。
轧钢厂棒材生产线对倍尺飞剪后摆杆和尾钢操控系统实施改良后,使成材率提升了百分之三十。
这也要求电气技术人员要持续对倍尺飞剪工艺进行改进,不断引进新的技术,确保倍尺飞剪充分发挥作用,满足高端客户对棒材精度的严苛要求。
1 概述飞剪的传动程序重点包括电机、齿轮减速箱、剪机和碎料搜集设备等。
其中每个电机都属于交流电机,而传动程序均是应用的西门子的SinamicsS120系列的产品。
西门子企业创建的SinamicsS120属于是新型的将矢量控制、V/F 和伺服控制集于一身的驱动控制程序,其不但可以对一般的三相异步电动机进行操控,还可以对同步电机、扭矩电机和直线电机进行操控。
它拥有非常强大的定位性能,可以做到轴的绝对和相对定位。
其内部构成的DCC 性能,采用PLC 的CFC 编程语言来完成逻辑、计算和不复杂的技术等性能。
SinamicsS120产品重点包含:用在共直流母线的逆变器DC/AC 与用在单轴的变频器AC/AC。
共直流母线的逆变器DC/AC 还可以称作是SinamicsS120多轴驱动器,其主要的构成模式是电机模块与电源模块隔开,三相交流电被一个电源模块整流成为540V 或者是600V 的直流电,把单个或者所有电机模块均链接到这一直流母线上,非常适宜用在多轴操控上,特别是包装、印刷、纺织以及钢铁等领域中。
高速线材轧机主控台操作技术
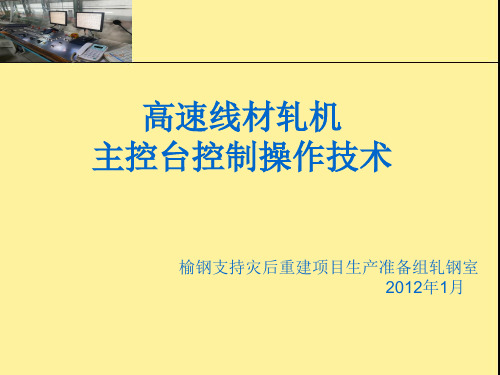
(3)动态速降小与恢复时间短。 轧机主传动电机在受到突加负载(咬钢)时,会产生转速 的降低,由于速度调节系统的作用使电机在转速恢复过程 中,转速的变化呈阻尼衰减的波动形状。其中开始转速下 降至最大值称为动态速降值,转速恢复到静态速降的时间 称为恢复时间。 动态转速降和恢复时间越小,表明系统抗扰性能越好。 (4)调速快。 有上升时间、峰值或最大值时间、调节时间、最大超调量 四个指标。 调节时间越小表明系统跟随性越快。最大超调量越小表明 跟随性和稳定性越好。 在榆钢高线采用了SIEMENS原装全数字交流调速装置主 使轧线电机的静态速度误差不超过±0.1%。
高速线材轧机 主控台控制操作技术
榆钢支持灾后重建项目生产准备组轧钢室 2012年1月
培 训 提 纲
一、高速线材主控台的职能和对操作人员素质 要求 二、高速线材轧机对电气传动和自动化控制系 统的要求 三、榆钢高线工艺布置简介 四、榆钢高线主控台主要设备功能介绍 五、榆钢高线人机界面(HMI)功能及基本操作介 绍 六、高速线材轧机工艺参数调整与操作 七、主制台安全操作要点与常见故障分析处理
剪切长度的调整通常靠改变时间延时来实现,在主控 台上可通过改变剪切长度设定值来修改剪切长度。
⑵、卡断剪及其控制
卡断剪安装在预精轧机组和精轧机组的入口 处,其剪刃靠气缸压力卡住运动中的轧件, 使轧件在轧辊的拖拽力作用下被切断,卡 断剪一般用于轧件取样和故障时卡断运行 中的轧件,或作为预精轧、精轧机组停轧 调整时的安全保护装置。 卡断剪接受由程序控制发出的动作指令,也 可由人工手动干涉控制。
3.3 剪机控制
用于高速线材轧机的剪机一般有两种类型: 一种是借助于电动机运转的回转剪,如回 转式飞剪和碎断剪; 一种是靠气缸压力运动闭合的卡断剪,如 预精轧及精轧机组前的卡断剪。
飞剪调试注意事项
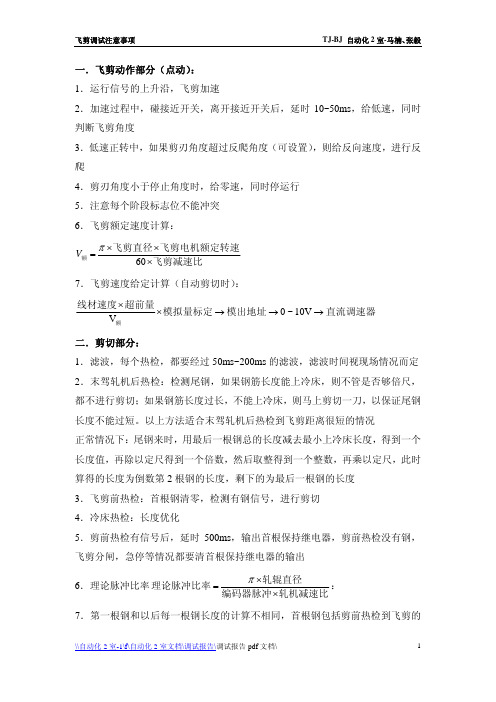
一.飞剪动作部分(点动):1.运行信号的上升沿,飞剪加速2.加速过程中,碰接近开关,离开接近开关后,延时10~50ms ,给低速,同时判断飞剪角度3.低速正转中,如果剪刃角度超过反爬角度(可设置),则给反向速度,进行反爬4.剪刃角度小于停止角度时,给零速,同时停运行5.注意每个阶段标志位不能冲突6.飞剪额定速度计算:60V π××=×额飞剪直径飞剪电机额定转速飞剪减速比7.飞剪速度给定计算(自动剪切时):0~10V V ××→→→额线材速度超前量模拟量标定模出地址直流调速器 二.剪切部分:1.滤波,每个热检,都要经过50ms~200ms 的滤波,滤波时间视现场情况而定2.末驾轧机后热检:检测尾钢,如果钢筋长度能上冷床,则不管是否够倍尺,都不进行剪切;如果钢筋长度过长,不能上冷床,则马上剪切一刀,以保证尾钢长度不能过短。
以上方法适合末驾轧机后热检到飞剪距离很短的情况正常情况下:尾钢来时,用最后一根钢总的长度减去最小上冷床长度,得到一个长度值,再除以定尺得到一个倍数,然后取整得到一个整数,再乘以定尺,此时算得的长度为倒数第2根钢的长度,剩下的为最后一根钢的长度3.飞剪前热检:首根钢清零,检测有钢信号,进行剪切4.冷床热检:长度优化5.剪前热检有信号后,延时500ms ,输出首根保持继电器,剪前热检没有钢,飞剪分闸,急停等情况都要清首根保持继电器的输出6.理论脉冲比率π×=×轧辊直径理论脉冲比率编码器脉冲轧机减速比:7.第一根钢和以后每一根钢长度的计算不相同,首根钢包括剪前热检到飞剪的距离8.首根钢是剪前热检的上升沿给高速计数器清零信号,其他是飞剪接近开关给高速计数器清零信号9.第一根钢长度对应的脉冲数=(剪前热检到飞剪的距离+倍尺长度)/ 实际(理论)比率10.非首根钢长度对应的脉冲数=倍尺长度/ 实际(理论)比率11.计算实际比率:首根钢时,因为是剪前热检给高速计数器清零,所以应用钱前热检到冷床热检的距离除以钢头到达冷床热检时的脉冲数,非首根钢则用剪切位置到冷床热检的距离除以钢头到达冷床热检的脉冲数,此时得到的比率为实际比率。
C965-C 优化剪切系统

可选用 21 英寸彩色 CRT 监视器。
用户图形接口 电子单元和操作控制盘组成一个图形用户接口。可以访问:
− 带钢参数,如额定宽度和温度校正曲线号(可选) − 带钢状况,例如当前宽度,平均宽度,最小宽度和最大宽度 − 上一个带钢数据(可选) − 仪器状况,包括所有的警告和报警信息 − 模拟输出配置 − 硬件测试 用户图形接口在实时 QNX 视窗环境下运行。
±10VDC,400kΩ 输入阻抗 或 0~20mA,500Ω 输入阻抗 轧制速度 带钢温度
模拟量输出(七通道,成组隔离):
量程:
可以定义为 0~10V 或±10VDC
输出可驱动 1000Ω 负载
典型模拟量输出参数:
- 绝对宽度
- 宽度偏差
- 带钢中心偏移
数ቤተ መጻሕፍቲ ባይዱ量输入: 类型: 典型数字量输入参数:
闭合触点或电压输入。 测量允许方式:这个输入用于可逆式轧机。 在逆向轧制时,测量禁止。
1个
标定装置用灯
1个
·轮子 安装在扫描器和充气箱的支架下,以便将测头推到离线位置,进行
标定和检修
·用户提出的输入输出功能
·操作控制盘
·“屏幕转储”功能
·“屏幕转储”打印机
·远端彩色图象监视器,用于显示宽度或宽度偏差,安装于轧机工作室
·带钢轨迹跟踪系统,安装在辊道的上方或下方
第8页
·并行轧机计算机接口 ·Fieldbus 接口(有多种协议) ·宽度或宽度偏差图表记录 ·大型操作控制盘监视器 ·客户定制与主机通讯协议 如有特殊要求,联系 KELK。
高速线材轧机自动控制系统控制要点分析

高速线材轧机控制系统控制要点分析何小书(北京二十一世纪科技发展有限公司100096)高速线材轧机控制系统控制要点分析何小书(北京二十一世纪科技发展有限公司100096)[摘要]本文探讨了高速线材轧机自动控制系统的组成架构和控制要点,通过实际项目应用分析和工艺数据统计获得的数据印证了理论分析的正确性。
[关键词]:金属秒流量控制、动态速降和负载分配控制、旋转飞剪控制、十二脉冲串联调速系统、工业现场总线应用、物料跟踪和数据监控引言:2006年11月,我公司与伊朗纳坦兹钢铁公司签订了该厂RM3高速线材热轧机组自动控制系统项目改造合同。
我公司为其提供全线电气控制系统全部控制柜、操作台、PLC系统和上位监控系统。
该项目从设计制造到调试验收历时四年,通过项目工作积累了大量宝贵经验和详尽数据。
在此,我将对项目中的控制要点逐一分析,并提出相关的控制观念。
高速线材轧机机组的组成架构和控制流程如下:1、冷态钢坯推入步进式加热炉,在炉内充分加热,温度升至摄氏900~1050度并推入粗轧机入口辊道;2、钢坯由导卫装置导入粗轧机,经8机架粗轧机轧制后切头尾进入中轧机;3、钢坯经中轧机8架轧制后由导卫装置导入1#或2#线中精轧机,期间为消除机组间张力推出1号活套;4、钢坯经中精轧机轧制后经2#活套进入终轧机;5、终轧机轧制完成后经水冷却线进入吐丝机,吐出成品盘条,经风冷辊道进入成品储运系统;6、盘条经成品储运系统进入打包机,经打包和成品标识形成最终成品并进入成品库。
高速线材轧机电气控制系统根据功能划分包括以下几部分:直流调速电机控制系统、交流调速电机控制系统、辅助电机控制系统、PLC 控制系统、人机操作界面、上位监控系统、远程维护系统。
根据区域划分可分为粗中轧段、精轧吐丝段、成品储运和打包段、液压/润滑/水处理辅助段。
总控制柜多达80余面,操作台箱30余台,全部设计图纸超过3000张。
为保证控制实时性和规模可控性,将全线设备按区域划分三组,即粗中轧段、精轧吐丝段、成品储运和打包段,将液压/润滑/水处理部分根据区域划入上述三段。
如何提高飞剪的剪切精度

如何提高飞剪的剪切精度飞剪的主要作用是对粗轧后带坯不规则的头部和尾部进行剪切。
剪切的精度对带坯的成功卷取至关重要,直接影响到产品的合格率。
但飞剪的控制受外界条件影响较大,有时会发生切不到头或切大头的现象,直接造成废钢。
针对此种情况我们对飞剪的设备及程序进行了一系列的研究分析,采取有效措施提高飞剪的剪切精度。
1.控制对象及控制任务1.1. 飞剪的本体设备飞剪的主体设备包括:飞剪电机及转鼓。
飞剪机械结构属于转鼓式飞剪,由安装在同一个转鼓座里的两个转鼓组成。
在转鼓上安装有两对剪刃,两队剪刃差90°,前剪刃为切尾剪刃,后剪刃为切头剪刃。
两台直流电机串联后通过减速箱驱动上、下两个转鼓,一台编码器用于飞剪电机测速,一台编码器用于剪刃位置检测,一个接近开关用于停车位置检测,一个抱闸用于停车位置控制。
1.2. 飞剪的辅助设备飞剪的辅助设备包括:溜槽门的打开和关闭,飞剪剪刃调整液压马达等。
1.3. 飞剪的控制任务飞剪的控制任务主要包括飞剪本体的控制,飞剪辅助设备的逻辑控制,剪前侧导板的位置控制,飞剪前辊道控制及高压水的除鳞控制。
2.控制系统的硬件构成2.1. 硬件构成飞剪控制系统有L301 柜1 台,操作台CTC11 1 台,操作箱CXC11 1台。
L301采用S7-400 PLC,包括以下模板:PS407电源模板,CPU模板,CP443工业以太网通讯模板,PROFIBUS-DP网通讯模板,2块FM450高速计数器模板,8路模拟量输入模板,32点数字量输入模板,32点数字量输出模板。
远程站操作台ET200M包括模板如下:PS307电源模板,IM153接口模板,SM338位置输入模板,3块16点数字量输入模板,2块16点数字量输出模板。
2.2. 通讯网络主柜L301与远程站操作台CTC11通过PROFIBUS-DP 电缆进行连接,飞剪机旁操作箱通过硬线同CTC11 直接相连。
PLC 间通过以太网进行通讯。
高速线材飞剪剪臂及进出口导钢装置的改进

(3) 发 生事 故 后 ,存 在 转 辙 器 不 能 正 确 地 把 轧 件拨 人碎 断导槽 ,导 致碎 断剪 不能 进行 碎 断。
2.3 原 因分 析
经 仔细 观察发 现 ,导钢装 置 内壁未 能 实 现平 滑 过 渡 ,轧件 头部撞 击导 钢装 置后产 生 弯头 ,使 得 轧 件头部 运行 轨迹偏 离轧 制 中心线较 大 ,产 生堆 钢 事 故 。
1 前 言 邯郸 钢铁公 司 线 材 厂 高 线 车 间 2#飞 剪 由切 头
剪 、碎 断剪 组成 ,分别 进行 切 头和事 故碎 断 ,此设 备 由意大利 西马 克公 司购人 。经 过一 段 时间 的使 用 之后 ,飞 剪剪臂 及 前 后 导 钢 装 置 发 生 事 故 比较 频 繁 ,造 成 堆钢 、顶钢 ,影 响 了作 业 率 、成 材 率指标 的提高 。2#飞剪 是高 速线 材生 产线 上 的关 键 辅助 设 备 ,轧件 头部剪 切质 量 的好坏 对精 轧机 的顺 利 咬人 有着 重要影 响 ,同时 碎断 功能 的稳定 运行 对 减少 事 故 时间起 到 了明显作 用 。根据 实际 情况 对其 合理 改 进 ,大大 降低 了轧线设 备 事故 率 ,提高 轧机 作业 率 和成 材率 。 2 生产 中存在 的 问题及 原 因分析
W ang Zhenm in,Zhang Pengfei,Feng Y anxiang (W ire Plant,Handan Iron and Steel Company,Handan,Hebei,056015) Abstract:Im provem ent has done against the problem s in upper—· and lower—-arm and fore —- and post—- guide of No.2 flying shears of W ire Plant of Han Steel, steel accum ulation breakdown got few er,operation ratio raised and products m ore qualified. Key W ords:flying shears; shears arm ; fore and post guide; im provem ent
- 1、下载文档前请自行甄别文档内容的完整性,平台不提供额外的编辑、内容补充、找答案等附加服务。
- 2、"仅部分预览"的文档,不可在线预览部分如存在完整性等问题,可反馈申请退款(可完整预览的文档不适用该条件!)。
- 3、如文档侵犯您的权益,请联系客服反馈,我们会尽快为您处理(人工客服工作时间:9:00-18:30)。
飞 剪机 剪切 速度 给 定值 : Q=1 3 4 _n() 6 8 n/ 5
2 剪切执行 过程
式 中F 为 飞 剪 机 电机 额 定转 速 。 i e
钢料位移 实际变化量为 : L AK× △ = (,L一 (5。 L+ L) ) 1
剪通道进行碎 断。
置 参 数P 4 中读 取 50
离 复 位 区 越 来越 近 时 , 定值 迅 速 减 小 , 给 既
加 速到 剪切速 度时 间为 : = n/ ) 保 证 剪 刃 快 速 返 回 , 有 利 于 剪 刃 的 准 确 t t × .n( 自动跟 随速 度计算 1 3 1 1 料 线 速 度 的 获 取 与 计 算 .. 钢
采 用 硬 线 直连 方式 。 体 设 置 方法 如 下 , 具 上
工 业 技 术
高速 线 材 飞剪机 控 制优 化
杨 建 满 ( 北钢铁集 团唐 山钢 铁股份有 限公 司 河 河北 唐山
030 ) 6 0 0
摘 要: 飞剪机是 高速 线材 生产 线上 的重 要设备 , 其控制精度 直接 影响 着产品成 材率 。 只有采 用响应速度 快 , 能稳定 的控 制 摹统 才能 性
计 算 钢料 位 移 的 变化 率 为 : K=T X △
装 置 、 流 电动 机 、 置码 盘 、 金 属 探 测 折 算 为 电 机转 速 : . _ r () 中i L / (4 L 为剪 前轧 机轴 心线 与 金属 探 直 位 热 n=V ×i D; 式 ; /丁 4 。 V —l 1 ) 。
当下 游 轧 机 无 负 荷 时 , 辙 器 处 于 切 3 2计 算飞 剪机 启动 延时 ,, 转 . L 为金 属探 测器 头 位 , 金 属 探 测 器 将 有 钢 信 号 时 输 入 到 剪 刃对 齐位 置距 离 , , 设定 切头 长 度 热 L 为 P C, L 根 据上 游 轧 机 系 统 的 电机 转 速 , L P C 剪 切 位 置 的 时 间 差 和 与 钢 料 速 度 相 匹 配 计 算 得 到 钢 料 到 达 剪 切 位 置 与 剪 刃 到 达 置 所 需 时 间 剪 刃 咬 入 点 到 剪 刃对 齐 位 置 的 距 离 :
靠 托 钢 器 托 动 由转 辙 器 进 入 下 游 轧 机 。 当
钢 料 从 金 属 探测 器到 被 剪 切 位 置所 需
零 。 置 按 照参 数 P 0 设 定 的斜 率 进 行 制 装 34
动停 车 。
位 置 码 盘 计 数 进 人 停 车 区 时 , 定 值 送 时 间为 : ( L 一 V l7式 中L 为金 3 4剪刃返 回 给 T = L + L ) g( ) / . 零 , 统 进 入 制 动 状 态 , 到 零 速 时 系 统 属 探测 器 到 剪 刃对齐 位 置距 离 , , 设定 切 系 达 L为
计 算 飞 剪机 启动 延 迟 时 间 时 , △ L 将 作
为修 正 值 与切 头 长 度 设 定 值 L 相 加 后 参 与 , 3 3 飞剪机 的制 动 . 飞 剪 剪 刃切 断 钢 料 进 入 停 止 区 后 ,
3 2 1钢料 从金 属 探 测 器到 被 剪切 位 计算 。 ..
Tz。
1 飞剪机系统构成
量, 则飞 剪 线 速度 : = 3式 中 K 为超 V;K V ()
飞 剪 机 系 统 主 要 由 上 位 机 、 L 驱 动 前 系 数 , 据 生产 实 际 一般 取 10 ~1 1 。 P C、 根 .5 .5 器 、 近开 关 、 辙 器及 机 械 部 分 组 成 。 接 转
由于 惯 性 较 大 , 刃 通 常 会 冲 过 复 位 剪
区范 围 , 需 要 在 停 止 后快 速 返 回复 位 区 , 故 的计 数 值 M与 复 位 区 差 值 绝 对 值 的平 方 根
3 2 2飞 剪 机 从 启 动 到 剪 刃接 触 钢 料 为 下 一 次 剪 切 做 好 准 备 。 序 中 采 用 码 盘 .. 程
满足 生 产需要 , 另外采 用更合 理的控 制算 法也是 十分 必要 的。 关键词 : 传动蓑置 P C 线速度 ・ 切延 时 L 剪
中 图分 类 号 : G3 T 3
文 献标 识 码 : A
文 章 编号 :6 2 3 9 ( 0 O0 () 0 9 — 1 1 7 - 7 12 1) 5a一 0 8 0
根据 位 置 环 的 反馈 执 行 复 位 动 作 , 回 复 头 长 度 。 返 位 区 停 止 , 成 一 次 切 头 过 程 。 时 在 下 完 同 游 轧 机 有 负 荷 后 转 辙 器 转 至 切 废 位 。 切 的 时 间 t 当 由加 速 时 间t 匀速 时 间t两 部 分 和 ,
的速 度给定值 , 制 飞剪 机快速 启动 , 控 将 L 7D × D 3 0 6式 中 D为咬 入 角 与钢 PLC向 装 置 发 出 停 车 命 令 , 定 值 变 为 r . / 6 () 给
钢 料 头 部 切 入 转 辙 器 下 层 进 入 料 坑 , 料 料 直 径 有 关 , 般 取 1 。 钢 一 0。
废 信 号 输 入 时 , 统 快 速 启 动 , 运 行 中 组 成 。 统 进 行 转 动 惯 量 优 化 后 得 到 飞 剪 乘 以 系数 K计 算返 回速 度给 定 值 , 样 剪 刃 系 将 系 这 的钢 料 切 断 , 余 钢 料 由 托 钢 器 托 入 碎 断 机加 速 到 额 定 转 速的 上 升 时 间t, 剩 该值 在 装 偏 离 复位 区 较 远 时 给 定 值 不 会 太 小 , 刃 剪