1700轧机工艺规程
1700轧机轧制1556宽度高光亮铝箔生产工艺
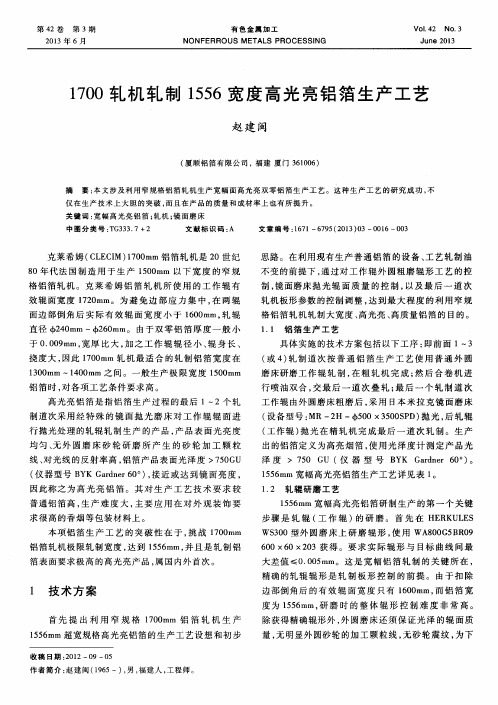
( 厦 顺 铝 箔 有 限公 司 ,福建 厦 门 3 6 1 0 0 6 )
摘
要: 本 文 涉 及 利 用 窄规 格 铝 箔 轧 机 生 产 宽 幅面 高 光 亮 双 零 铝 箔 生 产 工 艺 。 这 种 生 产 工 艺 的 研 究 成 功 , 不
仅 在 生 产 技 术 上 大 胆 的突 破 , 而 且 在 产 品 的质 量 和 成 材 率 上 也 有 所 提 升 。 关键词 : 宽 幅 高光 亮 铝 箔 ; 轧机 ; 镜 面 磨 床
箔 表 面要求 极高 的高 光亮 产 品 , 属 国 内外首 次 。
1 技 术 方 案
首先 提 出利 用 窄 规格 1 7 0 0 m m 铝 箔 轧 机 生 产 1 5 5 6 mm超 宽规格 高光 亮铝 箔 的生产 工 艺设 想 和初 步
收 稿 日期 : 2 0 1 2—0 9—0 5
铝 箔轧 机极 限轧 制宽 度 , 达到 1 5 5 6 m m, 并 且 是轧 制 铝
1 5 5 6 m m 宽 幅高光 亮铝箔 研制 生产 的第 一个 关 键 步骤 是 轧 辊 ( 工 作 辊 )的研 磨 。首 先 在 H E R K U L E S WS 3 0 0型外 圆磨 床 上 研 磨 辊 形 , 使 用 WA 8 0 0 G 5 B R 0 9 6 0 0× 6 0× 2 0 3获 得 。要 求 实 际 辊形 与 目标 曲线 间最 大差值 ≤0 . 0 0 5 mm。这 是 宽 幅铝 箔 轧 制 的关 键 所 在 , 精确 的轧 辊 辊 形 是 轧 制 板 形 控 制 的 前 提 。 由于 扣 除 边部 倒角 后 的 有效 辊 面宽 度 只有 1 6 0 0 m m, 而 铝 箔 宽
面边 部倒 角 后 实 际有 效 辊 面 宽 度 小 于 1 6 0 0 mm, 轧 辊 直径 6 2 4 0 m m ~d  ̄ 2 6 0 m m。 由于双 零 铝 箔 厚度 一 般 小
1700冷轧连退炉施工工艺
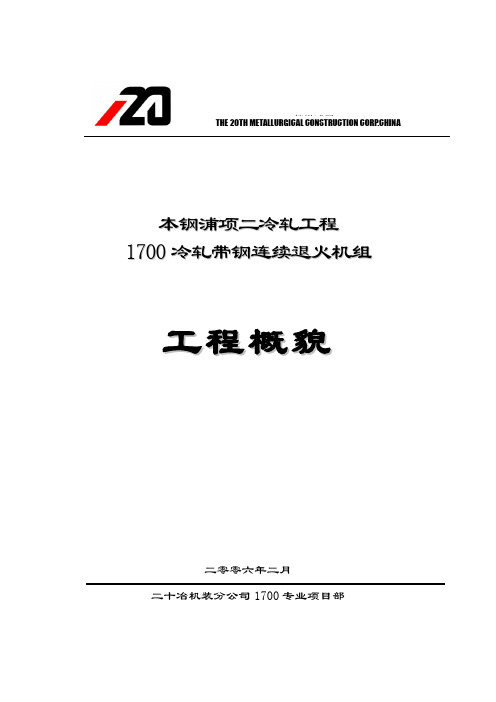
本钢浦项二冷轧工程1700冷轧带钢连续退火机组工程概貌二零零六年二月二十冶机装分公司1700专业项目部管道试压 THE 20TH METALLURGICAL CONSTRUCTION CORP .CHINA编制说明1、本作业设计的编制是依据连退机组的设计图纸和日方提供的安装指导书以及1700冷轧项目连退机组的合同(03BGJC—099)附件2机械设备部分,参照1700冷轧的组织设计而编制的。
2、连退机组的机械设备一部分为日方直接提供的重要和关键部件(附件2)如焊机。
其它为日方提供配套件的国内合作制造设备(附件14)和现场制作的非标件及结构件(附件3)3、设备安装精度要求是依据日方提供的指导书上的精度要求和冶金设备安装规范的标准以及本钢关于1700冷轧施工的有关规定而编制的。
4、施工方法的编制是依据日方提供的安装指导书和设计要求以及国内施工规范的要求,并结合自身的施工经验而编制的。
5、在编制过程中,由于图纸资料不全,和施工条件的限制,加之自身施工经验有限,因此编制时定有不足之处。
敬请审阅者提出宝贵意见,使作业设计真正起到指导施工作用,圆满地完成施工任务。
目录1、概述……………………………………………………………..2、施工前准备……………………………………………………..3、施工进度网络和设备安装进度………………………………..4、施工方法………………………………………………………..1)设备安装程序……………………………………………….2)设备安装…………………………………………………….3)结构安装…………………………………………………….4)管道安装…………………………………………………….5)液压润滑系统安装………………………………………….6)设备安装精度表…………………………………………….5、质量保证措施……………………………………………………6、机具计划…………………………………………………………7、人力安排…………………………………………………………8、安全措施…………………………………………………………一、工程概况1.1、业主名称:本钢浦项二冷轧工程1.2、工程名称:1700冷轧带钢连续退火机组1.3、设计单位:日本JFE ENGINEERING CORPORATION 中冶南方工程技术有限公司1.4、监理单位:本钢监理公司1.5、计划建设工期:2005年1月15日~2005年8月15日1.6、质量目标:工程产品:符合合同和设计要求;保证设计所具有的安全、经济运行和使用功能;符合政府法律、条例和规定,达到国家验收标准。
1700mm机组工艺流程简介--本钢集团有限公司PPT文件模板(2011版)-加单位名称
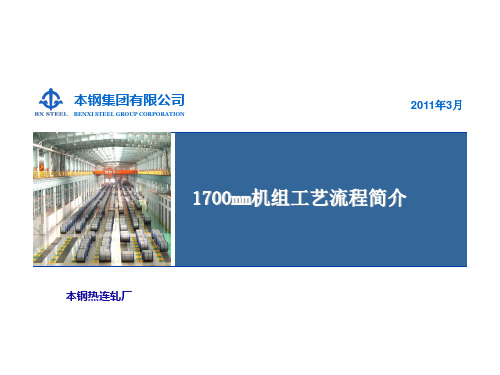
本钢热连轧厂
11
精轧机组
机架号 Stand number 型式 model 允许最大轧制力KN(机械) Max. rolling force 额定轧制力矩KN.M(总的) Rated rolling torque (total) 轧制速度(辊径最大)(m/s) Max. rolling speed 功率(KW) power 转速(rpm) speed 本钢热连轧厂 210/ 360 1715 1.53 ~ 2.62 1540 1.70 ~ 2.92 668 3.93 ~ 7.85 7000 210/ 420 100/ 200 100/ 250 190/ 380
单位 Unit
1#卷取机 1# down coiler 三助卷辊气动式 3 wrappers pneumatic
2#卷取机 2# down coiler 液压跳步式 Hydraulic jump 1.2~20× 750~1550 762
3#卷取机 3# down coiler 三助卷辊气动式 3 wrappers pneumatic 1.2~14× 750~1550 762
四辊不可逆 Four-high roughing mill 交流 AC 9000 500 3.8 25000
电源方式 Power 电机功率 kw Motor power 电机转数 rpm Motor speed 轧制速度 m/s Rolling speed 最大轧制力 KN Max. rolling force 本钢热连轧厂
18 95
本钢热连轧厂
剪切、平整分卷机组
本钢热连轧厂
19
剪切线概况
• 横切机组薄线: 93年6月投产,日本东研机械制 作所制造,钢带厚度 1.2-6.0 mm,钢带宽度 700-1560 mm,卷重max 24 t。 • 横切机组厚线: 92年7月投产,日本石川岛播磨 制造,钢带厚度 3.0-10.0 mm,钢带宽度 700- 1850 mm,卷重max 24 t。
1700mm5机架冷连轧机“甩机架”轧制策略及应用
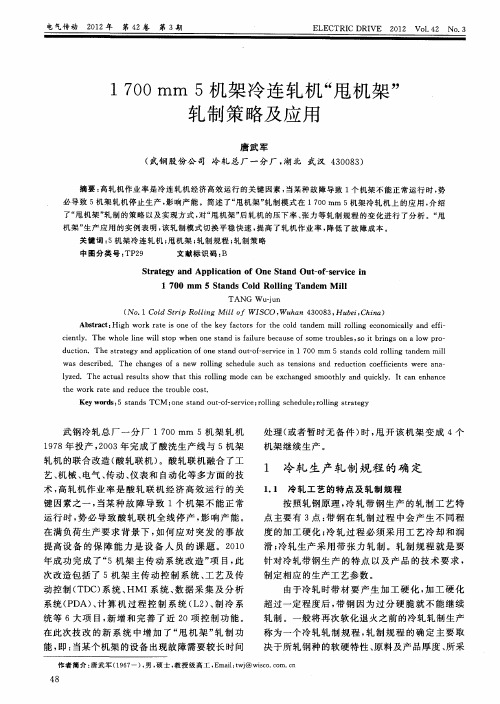
1 冷 轧 生 产 轧 制规 程 的确 定
1 1 冷 轧 工 艺 的 特 点 及 轧 制 规 程 .
键 因素之 一 , 当某种 故 障导 致 1个 机架 不 能 正 常 运行 时 , 必 导致 酸 轧 联机 全 线停 产 , 响 产 能 。 势 影 在满 负荷 生产 要求 背 景 下 , 何 应 对 突发 的事 故 如
电 气传 动 2 1 0 2年 第 4 2卷 第 3 期
E E TR C DR VE 2 1 Vo 42 L C I I 0 2 1
.
No .3
17 0mm 架 冷 连 轧 机 “ 机 架 ’ 0 5机 甩 ’ 轧 制 策 略及 应 用
唐 武军
( 钢股份 公 司 冷轧 总厂 一分 厂 , 武 湖北 武汉 4 0 8 ) 3 0 3
摘 要 : 轧 机 作 业 率 是 冷 连 轧 机 经 济 高 效 运 行 的关 键 因素 , 高 当某 种 故 障导 致 1 机 架 不 能 正 常 运 行 时 , 个 势
必 导 致 5机 架 轧 机 停 止 生 产 , 响 产 能 。简 述 了“ 机 架 ” 制模 式 在 1 0 影 甩 轧 0mm 7 5机架 冷 轧 机 上 的应 用 , 绍 介 了“ 机 架 ” 制 的 策 略 以 及 实 现方 式 , “ 机架 ” 轧 机 的 压 下 率 、 力 等 轧 制 规 程 的变 化 进 行 了分 析 。“ 甩 轧 对 甩 后 张 甩 机 架 ” 产 应 用 的实 例 表 明 , 轧 制模 式 切换 平稳 快速 , 高 了轧 机 作 业 率 , 低 了故 障成 本 。 生 该 提 降 关 键 词 : 架 冷 连 轧 机 ; 机 架 ; 制 规程 ; 制 策 略 5机 甩 轧 轧 中图 分 类 号 : 2 TP 9 文 献 标 识 码 : B
年产120万吨1700mm冷轧带钢压下规程课程设计
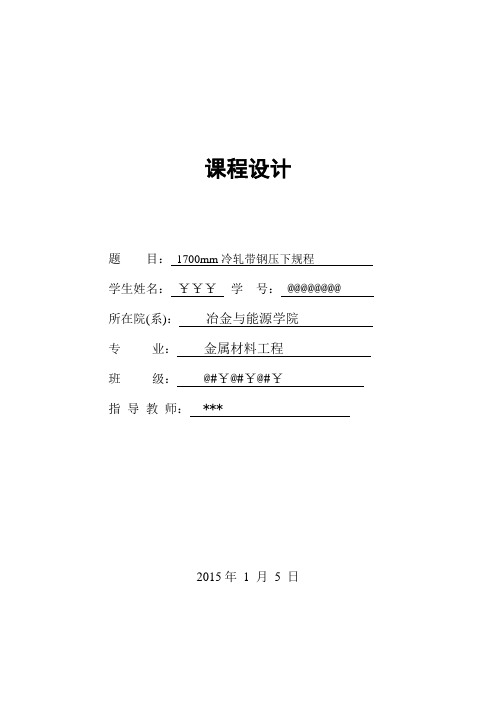
课程设计题目:1700mm冷轧带钢压下规程学生姓名:¥¥¥学号: @@@@@@@@ 所在院(系):冶金与能源学院专业:金属材料工程班级: @#¥@#¥@#¥指导教师: ***2015年1 月5 日摘要冷轧带钢具有表面质量高、性能好、品种多和用途广等特点。
特别是汽车工业和家电行业的迅速发展,人们对汽车及家电外壳的质量和性能要求也越来越高,因此发展冷轧板带钢十分必要。
本设计是参照唐钢五连轧厂而进行的冷轧带钢车间设计,设计年产量120吨。
本设计在参考唐钢五连轧设备条件下,参照了诸多文献及实际资料,以年产量为基础,结合各产品市场前景合理地分配了个产品产量,并制定了轧制制度,校核了部分只要设备车间年产量,综合了各项技术经济指标,此做了篇关于五连轧压下规程制度的设计。
关键词表面质量,轧制制度,校核,连轧目录1压下规程........................................................................................................... - 4 - 1.1 压下规程确定 ................................................................................................ - 4 - 1.1.1 原料尺寸.. (4)1.1.2 各轧机压下量分配 (4)1.1.3 连轧机组压下量分配及速度制度 (5)1.1.4 五机架连轧各架轧机的压下量分配 (5)1.2 确定轧机速度制度 ......................................................................................... - 6 - 1.2.1 轧制速度的确定.......................................................................................... - 6 - 1.2.2 轧辊转速的确定.. (6)1.2.3 加速度的选择 (7)2力能参数计算 ................................................................................................... - 8 - 2.1 轧制压力的计算............................................................................................. - 8 - 2.2 轧制力矩的计算.......................................................................................... - 11 - 2.2.1轧制力矩的确定 .. (11)2.2.2摩擦力矩的确定 (11)2.2.3轧机的空转力矩(M K) (13)2.2.4动力矩的计算 (14)2.3 电机能力验算 ............................................................................................. - 14 -3 轧辊强度校核 ................................................................................................ - 19 - 3.1 综述 ............................................................................................................ - 19 - 3.2 轧辊强度校核 ............................................................................................. - 19 - 3.2.1支撑辊强度校核........................................................................................ - 19 - 3.2.3工作辊强度校核 (21)3.2.3工作辊与支撑辊间的接触应力 (23)1压下规程1.1 压下规程确定压下规程是轧制制度(规程)最基本的核心内容,直接关系着轧机的产量和产品的质量。
第二架1700冷轧机设计
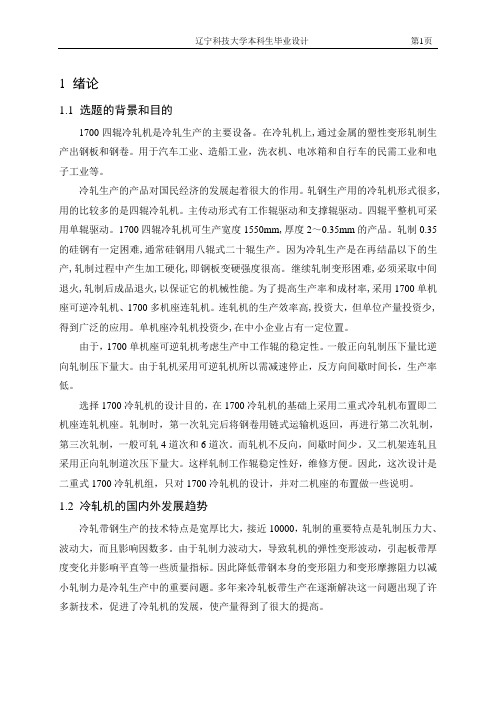
1绪论1.1 选题的背景和目的1700四辊冷轧机是冷轧生产的主要设备。
在冷轧机上,通过金属的塑性变形轧制生产出钢板和钢卷。
用于汽车工业、造船工业,洗衣机、电冰箱和自行车的民需工业和电子工业等。
冷轧生产的产品对国民经济的发展起着很大的作用。
轧钢生产用的冷轧机形式很多,用的比较多的是四辊冷轧机。
主传动形式有工作辊驱动和支撑辊驱动。
四辊平整机可采用单辊驱动。
1700四辊冷轧机可生产宽度1550mm,厚度2~0.35mm的产品。
轧制0.35的硅钢有一定困难,通常硅钢用八辊式二十辊生产。
因为冷轧生产是在再结晶以下的生产,轧制过程中产生加工硬化,即钢板变硬强度很高。
继续轧制变形困难,必须采取中间退火,轧制后成品退火,以保证它的机械性能。
为了提高生产率和成材率,采用1700单机座可逆冷轧机、1700多机座连轧机。
连轧机的生产效率高,投资大,但单位产量投资少,得到广泛的应用。
单机座冷轧机投资少,在中小企业占有一定位置。
由于,1700单机座可逆轧机考虑生产中工作辊的稳定性。
一般正向轧制压下量比逆向轧制压下量大。
由于轧机采用可逆轧机所以需减速停止,反方向间歇时间长,生产率低。
选择1700冷轧机的设计目的,在1700冷轧机的基础上采用二重式冷轧机布置即二机座连轧机座。
轧制时,第一次轧完后将钢卷用链式运输机返回,再进行第二次轧制,第三次轧制,一般可轧4道次和6道次。
而轧机不反向,间歇时间少。
又二机架连轧且采用正向轧制道次压下量大。
这样轧制工作辊稳定性好,维修方便。
因此,这次设计是二重式1700冷轧机组,只对1700冷轧机的设计,并对二机座的布置做一些说明。
1.2 冷轧机的国内外发展趋势冷轧带钢生产的技术特点是宽厚比大,接近10000,轧制的重要特点是轧制压力大、波动大,而且影响因数多。
由于轧制力波动大,导致轧机的弹性变形波动,引起板带厚度变化并影响平直等一些质量指标。
因此降低带钢本身的变形阻力和变形摩擦阻力以减小轧制力是冷轧生产中的重要问题。
1700铸轧机技术规格书
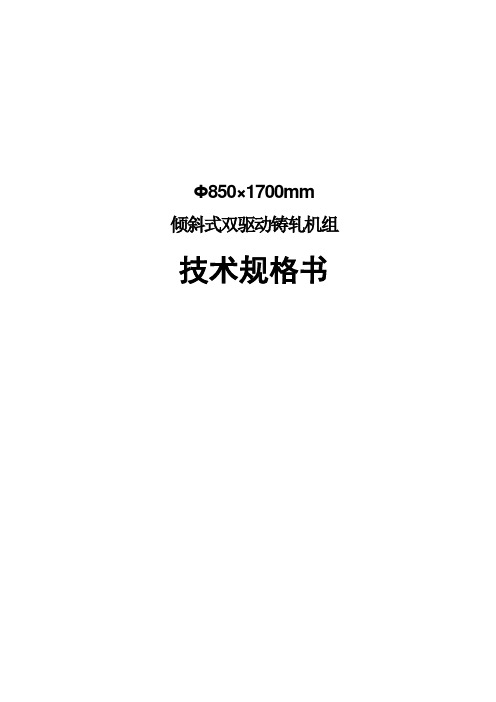
Φ850×1700mm 倾斜式双驱动铸轧机组技术规格书目录附件一、工艺描述及装机水平附件二、主要技术参数附件三、设备交货范围附件四、设备组成及详细说明附件五、设备质量标准及要求附件六、买方供货范围附件七、买卖双方设计责任附件八、设计联络及资料交付附件九、培训、监制及售后服务附件十、设备交货及预验收附件十一、包装及运输附件十二、设备的安装及验收附件十三、设备的调试及验收测试附件十四、项目进度附件十五、机组供电、供水、供风的要求附件一、设备工艺描述及装机水平生产工艺描述铸轧机是把在经过静置炉精炼后的铝液,经静置炉口⇒液面自动控制装置⇒除气箱内进一步精炼⇒过滤⇒前箱嘴子⇒相向转动且内部通有循环冷却水的铸轧辊,使铝液结晶并产生一定的变形率,从而实现铝及铝合金由熔融的液态金属铸轧成6~10 mm铸轧板材,在经过切头⇒卷取后,形成铸卷带材的工艺过程。
本铸轧机架的轴线与地面垂直线成15°倾斜配置(垂直中心线与轧机中心线间),使得在轧制过程中对克服金属偏析和减少金属氧化膜处的表面张力方面具有独到之处。
熔炉和铸轧机之间稳定的液面对轧制的顺利运行至关重要。
液面由一流口流量控制装置,通过调节出口流量来保持恒定。
铸轧的铝合金熔体必须连续供给,并必须清洁,且具有一致的化学成份,经除气装置进一步精炼,接着流入过滤装置,经过过滤后的铝液流入铸轧机前箱。
在熔炉和铸轧机之间,由钛丝送给器把最多两根铝钛硼丝按预先设定的恒定速度送入流槽系统,从而达到细化晶粒的目的。
该铸轧机特有的15︒倾角和前箱内精确的液位控制装置结合,保证前箱能在极其精确的压力下为铸嘴供给铝液。
通过铸嘴的注口,将铝液注入经冷却水冷却的轧辊上,铝液沿轧辊表面宽向分布。
这时,金属处于稍前于轧辊中心线的辊缝处,使液态金属在很短的时间内冷却、凝固,完成整个铸造结晶过程,接着受热轧制成形,形成铸轧板带。
在该过程中熔溶状态铝液的大量热能被轧辊迅速带走。
由于热量是通过铸轧辊传递的,这就要求辊套导热性能必须好。
1700冷轧连退炉施工工艺
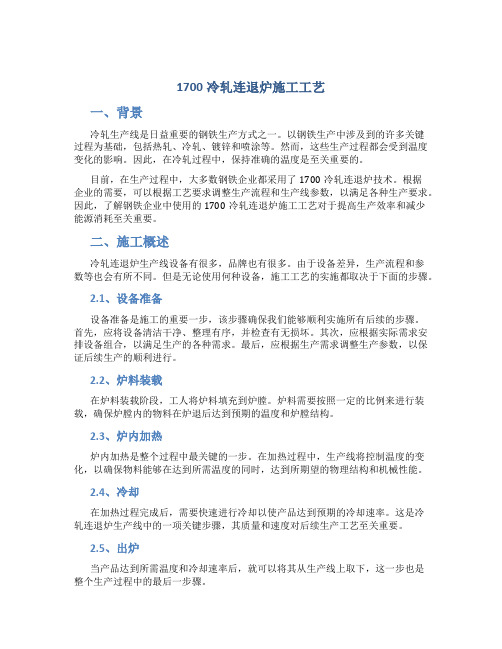
1700冷轧连退炉施工工艺一、背景冷轧生产线是日益重要的钢铁生产方式之一。
以钢铁生产中涉及到的许多关键过程为基础,包括热轧、冷轧、镀锌和喷涂等。
然而,这些生产过程都会受到温度变化的影响。
因此,在冷轧过程中,保持准确的温度是至关重要的。
目前,在生产过程中,大多数钢铁企业都采用了1700冷轧连退炉技术。
根据企业的需要,可以根据工艺要求调整生产流程和生产线参数,以满足各种生产要求。
因此,了解钢铁企业中使用的1700冷轧连退炉施工工艺对于提高生产效率和减少能源消耗至关重要。
二、施工概述冷轧连退炉生产线设备有很多,品牌也有很多。
由于设备差异,生产流程和参数等也会有所不同。
但是无论使用何种设备,施工工艺的实施都取决于下面的步骤。
2.1、设备准备设备准备是施工的重要一步,该步骤确保我们能够顺利实施所有后续的步骤。
首先,应将设备清洁干净、整理有序,并检查有无损坏。
其次,应根据实际需求安排设备组合,以满足生产的各种需求。
最后,应根据生产需求调整生产参数,以保证后续生产的顺利进行。
2.2、炉料装载在炉料装载阶段,工人将炉料填充到炉膛。
炉料需要按照一定的比例来进行装载,确保炉膛内的物料在炉退后达到预期的温度和炉膛结构。
2.3、炉内加热炉内加热是整个过程中最关键的一步。
在加热过程中,生产线将控制温度的变化,以确保物料能够在达到所需温度的同时,达到所期望的物理结构和机械性能。
2.4、冷却在加热过程完成后,需要快速进行冷却以使产品达到预期的冷却速率。
这是冷轧连退炉生产线中的一项关键步骤,其质量和速度对后续生产工艺至关重要。
2.5、出炉当产品达到所需温度和冷却速率后,就可以将其从生产线上取下,这一步也是整个生产过程中的最后一步骤。
三、在上述工艺中,冷却过程是最关键的环节之一。
对于某些型材,需要进行快速而准确的冷却,而对于其他型材,需要缓慢而稳定地冷却。
因此,冷轧连退炉施工工艺的速度和温度变化是至关重要的,可以根据不同的生产需求进行调整。
轧机工艺流程
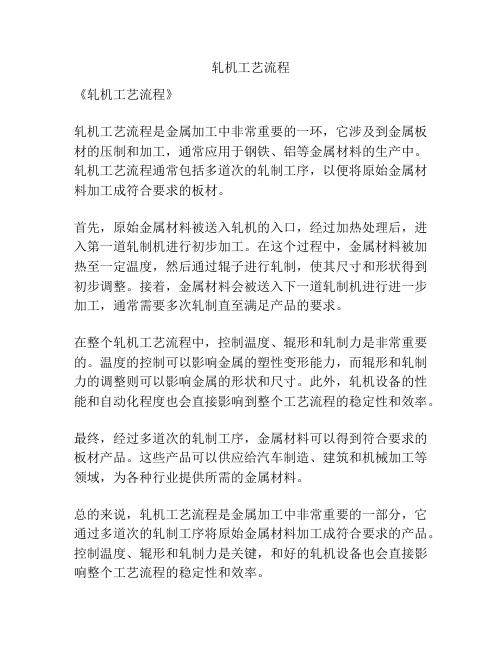
轧机工艺流程
《轧机工艺流程》
轧机工艺流程是金属加工中非常重要的一环,它涉及到金属板材的压制和加工,通常应用于钢铁、铝等金属材料的生产中。
轧机工艺流程通常包括多道次的轧制工序,以便将原始金属材料加工成符合要求的板材。
首先,原始金属材料被送入轧机的入口,经过加热处理后,进入第一道轧制机进行初步加工。
在这个过程中,金属材料被加热至一定温度,然后通过辊子进行轧制,使其尺寸和形状得到初步调整。
接着,金属材料会被送入下一道轧制机进行进一步加工,通常需要多次轧制直至满足产品的要求。
在整个轧机工艺流程中,控制温度、辊形和轧制力是非常重要的。
温度的控制可以影响金属的塑性变形能力,而辊形和轧制力的调整则可以影响金属的形状和尺寸。
此外,轧机设备的性能和自动化程度也会直接影响到整个工艺流程的稳定性和效率。
最终,经过多道次的轧制工序,金属材料可以得到符合要求的板材产品。
这些产品可以供应给汽车制造、建筑和机械加工等领域,为各种行业提供所需的金属材料。
总的来说,轧机工艺流程是金属加工中非常重要的一部分,它通过多道次的轧制工序将原始金属材料加工成符合要求的产品。
控制温度、辊形和轧制力是关键,和好的轧机设备也会直接影响整个工艺流程的稳定性和效率。
年产100万吨1700冷轧车间工艺设计
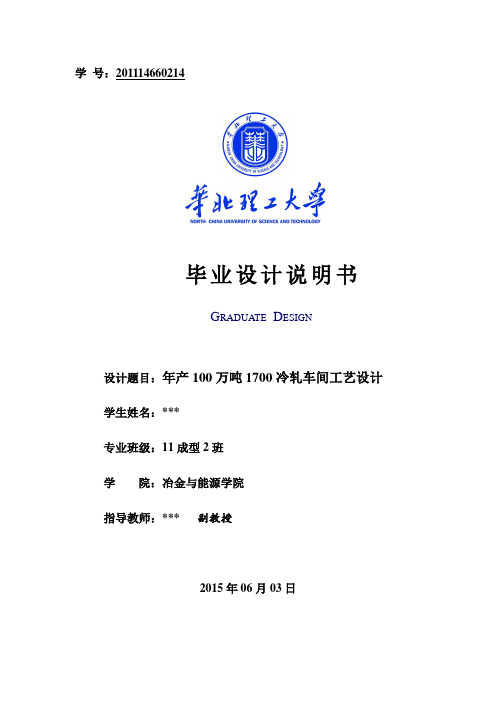
钢的冷轧于19世纪中叶始于德国,最初只能生产宽20-25mm的冷轧带钢[1]。美国与1859年制造建成了25mm冷轧机,1887年生产出宽150mm的低碳钢,宽的冷轧薄板是在热轧成卷带钢的基础上发展起来的[2]。美国早在1920年第一次成功的轧制出宽带钢,并很快由单机不可逆轧制跨入单机可逆式轧制。1926年阿姆柯公司巴特勒工厂建成四机架冷连轧机。日本1938年在东洋钢板松下工厂安装了第一台可逆式冷轧机。1940年在新日铁建立了第一套四机架1420冷连轧机。1951年苏联建设了一套2030全连续五机架冷连轧机,年产250万吨[3]。
3)冷轧薄板可以通过调节轧制和退火工艺,获得具有更多样的力学性能。即可生产高强度冷轧板,也可生产软、冲压性能很高的汽车面板,其具有性能好、品种多、用途广诸多优点,可以在比较广的范围内满足用户的要求。
1.3 国内外冷轧薄板的发展现状
武钢—武钢股份投资83.7亿元建的2130mm冷轧机组,年产量215万吨,产品厚度0.2-0.5mm,最大宽度2080mm,最大强度800MPa,其产品用于以轿车板和家电板为代表的覆盖面极广的高档冷轧产品。
冷轧薄板发展如此迅速的的主要原因是:
1)钢材热轧过程中的温降和温度分布不均匀给生产带来了难题。
特别是在轧制厚度小而长度大的薄板带产品时,冷却上的差异引起的轧件首尾温差往往带使产品尺寸超出公差范围,性能出现显著差异。当厚度小到一定时,轧件在轧制过程中温降剧烈,以致根本不可能在轧制周期之内保持热轧所需的温度。
关键词1700冷轧薄板;酸轧联合机组;冷轧工艺与设备;压下规程
Abstract
As cold rolling sheet has high dimensional accuracy, surface quality and excellent overall performance,so it has been more widely used in all areas of production and constrcution,especially in the household appliances and motor vehicle plates.This article combines with the information of Wusteel Cold Mill Plant.At the same time ,it refer to other modern cold mill plant.So I design an 1700 Cold Rolling Mill Plant with an annual output of1.0million tons.The component of design includes the choice of rolling mill forms,the arrangement of mills,according to the typical varieties(thickness of 2mm)to design the reduction of order and calculation(the parameters of force and energy,the strength of roll and the capacity of electrical motor),the choice of auxiliary equipment(including galvanized line,color coating line).The main equipment uses the continuous picking line coupled to tandom mill.The annealing furnace chooses bell-type annealing furnace.The mills choose CVC rolls to control the shape of sheet.
1700热轧生产线的设计
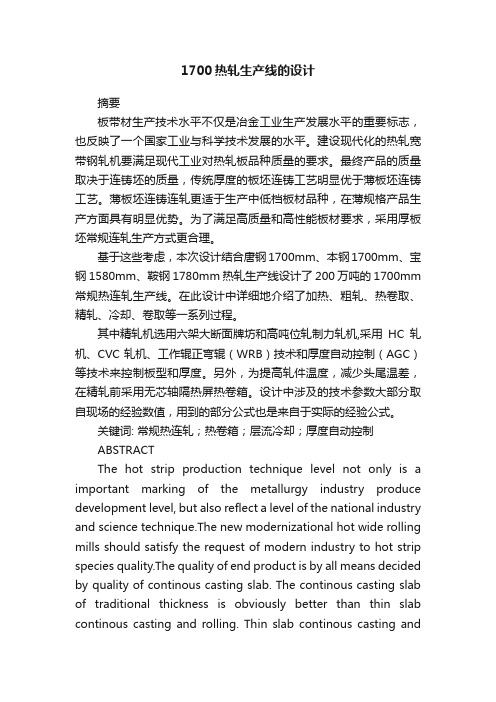
1700热轧生产线的设计摘要板带材生产技术水平不仅是冶金工业生产发展水平的重要标志,也反映了一个国家工业与科学技术发展的水平。
建设现代化的热轧宽带钢轧机要满足现代工业对热轧板品种质量的要求。
最终产品的质量取决于连铸坯的质量,传统厚度的板坯连铸工艺明显优于薄板坯连铸工艺。
薄板坯连铸连轧更适于生产中低档板材品种,在薄规格产品生产方面具有明显优势。
为了满足高质量和高性能板材要求,采用厚板坯常规连轧生产方式更合理。
基于这些考虑,本次设计结合唐钢1700mm、本钢1700mm、宝钢1580mm、鞍钢1780mm热轧生产线设计了200万吨的1700mm 常规热连轧生产线。
在此设计中详细地介绍了加热、粗轧、热卷取、精轧、冷却、卷取等一系列过程。
其中精轧机选用六架大断面牌坊和高吨位轧制力轧机,采用HC轧机、CVC轧机、工作辊正弯辊(WRB)技术和厚度自动控制(AGC)等技术来控制板型和厚度。
另外,为提高轧件温度,减少头尾温差,在精轧前采用无芯轴隔热屏热卷箱。
设计中涉及的技术参数大部分取自现场的经验数值,用到的部分公式也是来自于实际的经验公式。
关键词: 常规热连轧;热卷箱;层流冷却;厚度自动控制ABSTRACTThe hot strip production technique level not only is a important marking of the metallurgy industry produce development level, but also reflect a level of the national industry and science technique.The new modernizational hot wide rolling mills should satisfy the request of modern industry to hot strip species quality.The quality of end product is by all means decided by quality of continous casting slab. The continous casting slab of traditional thickness is obviously better than thin slab continous casting and rolling. Thin slab continous casting androlling is suitable to produce medium low file time plank material species and have obvious advantage at the thin specification product.For satisfying the request of obtaining the high quality and high performance strip, thick slab continous casting produce method is considered more reasonable.Based on the above premise, this design combine Tang steel 1700 ,Ben steel 1700, Bao steel 1580 and An steel 1780 hot rolling production line to design 2.0 million ton traditional hot continuous rolling workshop. In this paper it is detailly introduced the heat furnace, the rough rolling, the hot curl, the finish rolling, the laminar cooling, the curl and so on.Among them, The finishing mill still selected the big cross section memorial arch and the high tonnage rolling stand, and choosed HC mill,CVCmill,work roll bend technique and automatic gauge control to control strip shape and thickness. Moreover, in order to raise the temperature of rolling metal and reduce the difference temperature between tail and head of rolling metal,I establish a hot curl box between the rough rolling and the finishing rolling. The coefficient in this design and parts of formulas come from actual experience.Key words: convensional continuous rolling , the laminar cooling, automatic gauge control引言板带产品的技术要求具体体现为产品的标准,包括四个方面:(1)尺寸精度高。
1700冷轧带钢
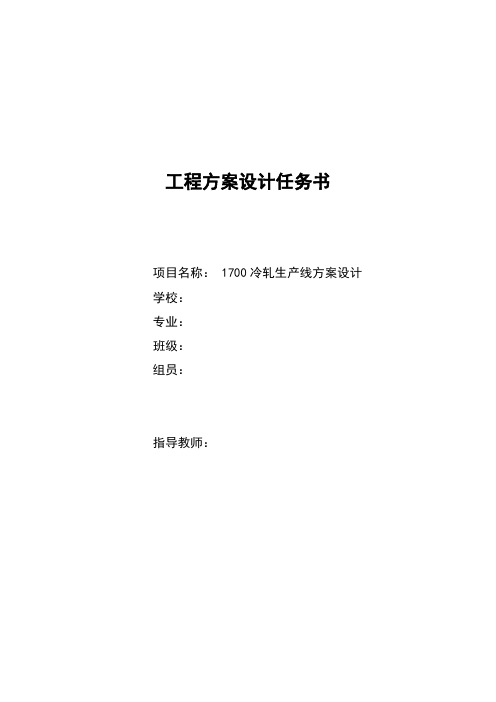
工程方案设计任务书项目名称: 1700冷轧生产线方案设计学校:专业:班级:组员:指导教师:工程方案设计任务书目录1.综述 (1)1.1冷轧概况 (1)1.2国外冷轧发展史 (1)1.3我国冷轧发展状况 (1)2.产品方案 (3)2.1产品大纲 (3)2.1.1产品大纲及钢种 (3)2.1.3产品详细分类 (4)2.2金属平衡计算 (4)2.2.1计算成品(材)率(金属消耗系数) (4)2.2.2影响成品率的主要因素 (4)2.2.3编制金属平衡表 (5)2.3产品与技术要求 (5)3.生产工艺流程及概述 (6)3.1工艺流程 (6)3.2工艺流程简图 (6)3.3主要设备 (7)3.3.1开卷机 (7)3.3.2酸洗机 (7)3.3.3轧机 (7)3.3.4退火炉 (7)3.3.5平整机 (8)3.3.6飞剪机 (8)3.3.7剪切机 (9)3.3.8圆盘剪 (9)3.3.9矫直机 (9)3.3.10运输机 (10)4.主要设备及参数选择 (11)4.1开卷机 (11)4.2酸洗机组 (11)4.3轧机(五架连轧机组) (12)4.4平整机 (13)4.5飞剪 (13)4.6矫直机 (14)4.7卷取机 (14)5.力能参数计算 (15)5.1轧制力计算 (15)5.2对工作辊受力分析 (17)5.3电机功率选择 (18)5.4电机选择 (18)6.车间年产量计算 (20)6.1轧机工作图表 (20)6.2轧机轧制节奏的确定 (20)6.3轧机小时产量计算 (20)6.4轧机的平均产量计算 (21)6.5影响轧机小时产量的因素 (22)6.6车间年产量计算 (22)7.生产线布局图 (24)8.车间技术经济指标 (25)8.1 概述 (25)8.2 车间各项技术经济指标分析及指定 (25)9.投标文件 (28)9.1投标函 (28)9.2投标目录 (29)参考文献 (30)1.综述1.1冷轧概况1553年法国人布律列尔(Brulier)制成一台轧机,轧制造币用的金板和银板。
1700轧机工艺规程.docx
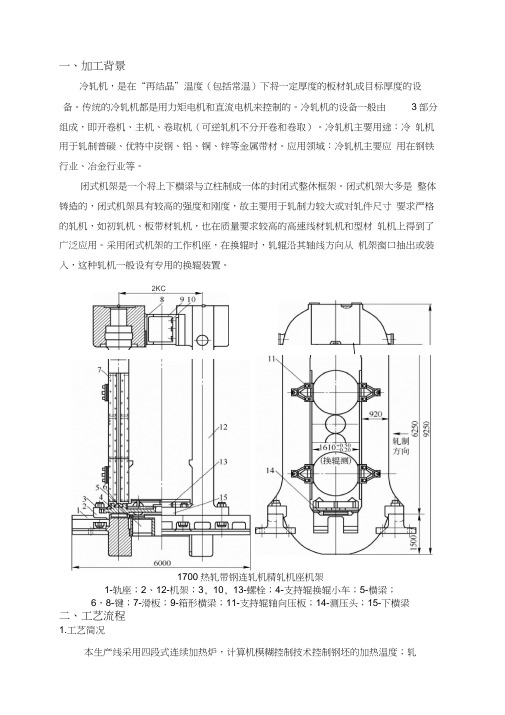
一、加工背景冷轧机,是在“再结晶”温度(包括常温)下将一定厚度的板材轧成目标厚度的设备。
传统的冷轧机都是用力矩电机和直流电机来控制的。
冷轧机的设备一般由3部分组成,即开卷机、主机、卷取机(可逆轧机不分开卷和卷取)。
冷轧机主要用途:冷轧机用于轧制普碳、优特中炭钢、铝、铜、锌等金属带材。
应用领域:冷轧机主要应用在钢铁行业、冶金行业等。
闭式机架是一个将上下横梁与立柱制成一体的封闭式整休框架。
闭式机架大多是整体铸造的,闭式机架具有较高的强度和刚度,故主要用于轧制力较大或对轧件尺寸要求严格的轧机,如初轧机、板带材轧机,也在质量要求较高的高速线材轧机和型材轧机上得到了广泛应用。
采用闭式机架的工作机座,在换辊时,轧辊沿其轴线方向从机架窗口抽出或装入,这种轧机一般设有专用的换辊装置。
2KCK)\1700热轧带钢连轧机精轧机座机架1-轨座;2、12-机架;3, 10, 13-螺栓;4-支持辊换辊小车;5-横梁;6,8-键;7-滑板;9-箱形横梁;11-支持辊轴向压板;14-测压头;15-下横梁二、工艺流程1.工艺简况本生产线采用四段式连续加热炉,计算机模糊控制技术控制钢坯的加热温度;轧机布置形式为往复跟踪式布置,二辊式轧机;第一、二机架为直流、可逆式,第3〜6机架为交流电动机传动、不可逆;成品轧件经热锯后冷却、离线矫直、检验入库。
本轧机以生产型钢为主,年设计能力方坯一火成材。
30万吨;使用的主要燃料为焦炉煤气,连铸扁坯和2.产品大纲槽钢12#~16#轮辋钢7.00T、7.50V工字钢14#~16# 角钢8#~12.5# 球扁钢14#~20#3.生产工艺制度矿用槽帮钢和刮板钢圆钢①50~0 66、①75薄板坯9.5~15.3 3 240(1)轧制道次5-3-1-1-1-13-3-1-1-1-1(2)开、终轧温度开轧温度:1050 C ~1180C终轧温度:800~950C左右轧制周期控制在5分钟以内三、加热工艺技术操作规程3.1技术条件(包括技术参数、设备参数等)3.1.1 加热炉技术参数:a)尺寸:有效尺寸32016*4524b)形式:四段连续式侧出料推钢加热炉c)进料排数:1排d)使用燃料:焦炉煤气(热值:15910KJ/Nm)e)加热钢料材质:普碳钢、低合金钢f)炉底强度:508Kg/h2吊g) 额定生产能力:坯65t/hh) 燃料最大消耗量:7000 m3/hi) 空气最大消耗量:32200 m3/hj) 单位热耗:1800KJ/Kg3.1.2液压推钢机(一台)技术参数:a) 推力:P=120tb) 推速:前进v=0.1m/s ;返回v=0.15 m/sc) 行程:工作行程1600mm;最大行程2500mm3.1.3可横移摩擦式出钢机a)最大推力:2.2tb)推钢速度: 1.25m/sc)返回速度: 2.45m/sd)工作行程: 5.6me)最大行程:6m3.1.4 空气预热器(WJZ-3-3)(加热炉尾右侧烟道)技术参数:a) 形式:斜管插入件式2b) 换热面积:680 mc) 空气进口温度:常温20Cd) 空气出口温度:150~350Ce) 烟气进口温度:"705 Cf) 烟气出口温度:w 345Eg) 空气预热量:32600 m3/hh) 入预热器的烟气量:37500 m3/hi) 空气阻力:1900Paj) 烟气阻力:90Pa3.1.5装料辊道(加热炉尾部):辊子直径(mrj) 3辊身长度(mm 3辊距(mm 3辊数(mma) I 组:3003 12003 9003 9——8100b) U组:3003 12003 ( 10003 3+9003 6) ——8400c) 辊道速度:1 —2m/s3.1.6离心式通风机(2台,加热炉右风机房):辊道长度(mma)型号:9—19—NO16左旋135°b)风量:44842 m3/hc)风压:14900Pad)配电机型号:Y355M—4 电压:380V 功率:315KW 3.1.7汽化冷却系统:a)汽包(加热炉左侧):© 12283 143 8000内径:1200mm公称长度:7000mm容积:9.59 m3设计压力:1.4Mpa工作压力:0.2 —1.3 Mpa安全阀开启压力:1.05 Mpab)蒸汽产量:0—12.5t/h (平均:5t/h )c)给水压力:0—1.5 Mpad)给水(软水)量:0—25t/he)纵横水管、上升和下降管材质:20#f)下降管集:1根© 3253 8g)上升管:11根© 1333 4h)横水管:13 根© 1593 303 6064;3 根矩形管200 3 1603 253 6064i)纵水管:3根© 1143 16j)炉筋间距:1400mmk)汽化冷却管道色环标志:a型号:QB- 9汽缸工作压力:0.88 — 1.37Mpa水缸工作压力:0.73Mpa活塞往返频率:26—45次/分供水量:22.5 —44mVhb)离心式清水泵(电动泵)两台:型号:2GC-53 6流量:10mVh (2.8L/s )扬程:192m转速:2950r/min允许吸上真空高度:5.5m叶轮直径:168mm配电机:型号:y160L—2;转速:2930r/min ;功率:18.5kw标准编号:JB3074— 82软水池:1个;容积=30 m33.10加热常见缺陷及其处理方法:加热常见缺陷及其处理方法:3.10.1施严禁出钢,避免粘钢后发生抵死端墙事故。
1700mm热连轧机组的生产设备与生产技术分析
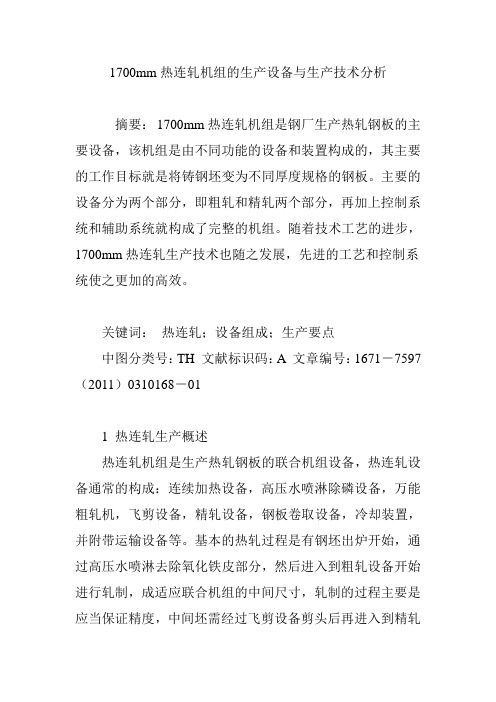
1700mm热连轧机组的生产设备与生产技术分析摘要:1700mm热连轧机组是钢厂生产热轧钢板的主要设备,该机组是由不同功能的设备和装置构成的,其主要的工作目标就是将铸钢坯变为不同厚度规格的钢板。
主要的设备分为两个部分,即粗轧和精轧两个部分,再加上控制系统和辅助系统就构成了完整的机组。
随着技术工艺的进步,1700mm热连轧生产技术也随之发展,先进的工艺和控制系统使之更加的高效。
关键词:热连轧;设备组成;生产要点中图分类号:TH 文献标识码:A 文章编号:1671-7597(2011)0310168-011 热连轧生产概述热连轧机组是生产热轧钢板的联合机组设备,热连轧设备通常的构成:连续加热设备,高压水喷淋除磷设备,万能粗轧机,飞剪设备,精轧设备,钢板卷取设备,冷却装置,并附带运输设备等。
基本的热轧过程是有钢坯出炉开始,通过高压水喷淋去除氧化铁皮部分,然后进入到粗轧设备开始进行轧制,成适应联合机组的中间尺寸,轧制的过程主要是应当保证精度,中间坯需经过飞剪设备剪头后再进入到精轧设备中,一次轧制成需要的规格然后再进行卷取,且中间都需要进行二次除鳞。
热轧机目前已经进入了全线自动化的阶段,并且采用厚度自动控制、弯辊系统等新兴技术。
九十年代末期,连轧设备广泛的应用在薄钢板的轧制加工中,从炼钢到轧制钢板形成了一个连贯的自动化生产流程,形成了短流程、低能耗、高效率的生产线。
目前正向着热轧复合板技术发展,并成功的轧制了不锈钢复合卷板。
2 1700mm热连轧机组的设备组成下面就某钢厂的1700mm热连轧机组为例具体说明热连轧机组的设备构成。
1)基本组成。
某钢厂的1700mm热连轧机组主要构成有:四台步进梁式加热炉,粗轧机三台,立辊轧机三台,高速飞剪一台,七机架精轧机组,配套冷却设备,卷取机三台,钢卷检查装置一套,自动打捆机和喷号系统及步进梁运卷系统。
这些设备构成了一条完整的热连轧机组,从加热到轧制到成品运输构成了一个完整的成产线。
1700冷轧说明书

燕山大学轧机设计课程设计说明书1700冷轧压下规程设计、机架校核及有限元分析学院(系):机械工程学院班级:10轧钢3班组员:王风强黄伟彬李飞(前)李志远郑雷琨张坤指导教师:李学通刘丰孙静娜日期:2013年12月25日燕山大学轧机设计课程设计说明书1 燕山大学课程设计(论文)任务书院(系): 机械工程学院 基层教学单位:冶金机械系 小组成员 李志远 黄伟彬 王风强 李飞(前) 张坤 郑雷琨设计题目1700冷轧压下规程设计、机架校核及有限元分析 设计技术参数原料厚度:1-8mm ;产品:0.2-2.0mm ; 材质: Q235 08F 不锈钢 45#设计要求1、制定轧制规程:确定道次压下量、速度,计算轧制力和轧制力矩;2、设计机架尺寸并进行三维设计和工程图;3、有限元分析一个道次的轧制过程和机架强度校核; 工作量 1、完成工程图至少1张; 2、完成设计计算说明书1份,其中包含有限元分析报告; 3、查阅文献5篇以上。
工 作 计 划1、2013.12.2 准备参考资料;2、2013.12.2~12.12 计算;画草图;3、2013.12.12 中期检查;4、2013.12.13~2013.12.25 工程图,分析,写说明书;5、2013.12.26~2013.12.27 考核答辩;参考资料 1、徐乐江编著 《板带冷轧机板形控制与机型选择》冶金工业出版社 20102、王海文主编 《轧钢机械设计》 机械工业出版社 1986.63、曹鸿德主编《塑性变形力学基础与轧制原理》 机械工业出版社4、周纪华 管克智 著《金属塑性变形阻力》 机械工业出版社指导教师 李学通 刘丰 孙静娜 基层教学单位主任(签字)1700冷轧压下规程设计、机架校核及机架分析目录前言 (3)第1章HC轧机工作原理 (4)第2章冷轧薄板生产工艺流程及轧机特性 (5)2.1工艺流程图 (5)2.2坯料的选择 (5)2.3轧机的主要特性 (5)第3章轧制规程及相关参数确定 (6)3.1轧辊主要参数的确定 (6)3.2轧制规程的制定 (6)3.3确定各道次变形抗力 (7)3.4计算各道次带钢张力 (8)3.5各道次轧制力计算 (8)3.6计算轧制力矩 (12)第4章有限元分析某道次轧制过程 (13)4.1模拟几何建模 (13)4.2施加载荷及求解过程 (13)4.3读取结果 (14)第5章机架的设计及校核 (16)5.1机架主要结构参数的确定 (16)5.2机架强度校核 (17)5.3刚度校核 (20)第6章机架的有限元分析 (21)6.1建模过程 (21)6.2施加载荷和求解 (21)6.3读取结果 (21)6.4结论 (24)设计心得体会 (25)参考文献 (26)附表2燕山大学轧机设计课程设计说明书前言HC轧机全名为HITACHI HIGH CROWNCONT ROLMILL,即日立中心高性能轧辊凸度控制轧机。
- 1、下载文档前请自行甄别文档内容的完整性,平台不提供额外的编辑、内容补充、找答案等附加服务。
- 2、"仅部分预览"的文档,不可在线预览部分如存在完整性等问题,可反馈申请退款(可完整预览的文档不适用该条件!)。
- 3、如文档侵犯您的权益,请联系客服反馈,我们会尽快为您处理(人工客服工作时间:9:00-18:30)。
冷轧机,是在“再结晶”温度(包括常温)下将一定厚度的板材轧成目标厚度的设备。
传统的冷轧机都是用力矩电机和直流电机来控制的。
冷轧机的设备一般由3部分组成,即开卷机、主机、卷取机(可逆轧机不分开卷和卷取)。
冷轧机主要用途:冷轧机用于轧制普碳、优特中炭钢、铝、铜、锌等金属带材。
应用领域:冷轧机主要应用在钢铁行业、冶金行业等。
闭式机架是一个将上下横梁与立柱制成一体的封闭式整休框架。
闭式机架大多是整体铸造的,闭式机架具有较高的强度和刚度,故主要用于轧制力较大或对轧件尺寸要求严格的轧机,如初轧机、板带材轧机,也在质量要求较高的高速线材轧机和型材轧机上得到了广泛应用。
采用闭式机架的工作机座,在换辊时,轧辊沿其轴线方向从机架窗口抽出或装入,这种轧机一般设有专用的换辊装置。
1700热轧带钢连轧机精轧机座机架1-轨座;2、12-机架;3,10,13-螺栓;4-支持辊换辊小车;5-横梁;6,8-键;7-滑板;9-箱形横梁;11-支持辊轴向压板;14-测压头;15-下横梁1.工艺简况本生产线采用四段式连续加热炉,计算机模糊控制技术控制钢坯的加热温度;轧机布置形式为往复跟踪式布置,二辊式轧机;第一、二机架为直流、可逆式,第3~6机架为交流电动机传动、不可逆;成品轧件经热锯后冷却、离线矫直、检验入库。
本轧机以生产型钢为主,年设计能力30万吨;使用的主要燃料为焦炉煤气,连铸扁坯和方坯一火成材。
2.产品大纲槽钢12#~16#工字钢14#~16#角钢8#~12.5#球扁钢14#~20#轮辋钢7.00T、7.50V 矿用槽帮钢和刮板钢圆钢Φ50~Φ66、Φ75 薄板坯9.5~15.3³2403.生产工艺制度(1)轧制道次5-3-1-1-1-13-3-1-1-1-1(2)开、终轧温度开轧温度:1050℃~1180℃终轧温度:800~950℃左右轧制周期控制在5分钟以内三、加热工艺技术操作规程3.1 技术条件(包括技术参数、设备参数等)3.1.1 加热炉技术参数:a) 尺寸:有效尺寸32016*4524b)形式:四段连续式侧出料推钢加热炉c)进料排数: 1排d)使用燃料:焦炉煤气(热值:15910KJ/Nm3)e)加热钢料材质:普碳钢、低合金钢f)炉底强度:508Kg/h²m2g)额定生产能力:坯65t/hh)燃料最大消耗量:7000 m3/hi)空气最大消耗量:32200 m3/hj)单位热耗:1800KJ/Kg3.1.2 液压推钢机(一台)技术参数:a) 推力:P=120tb)推速:前进 v=0.1m/s;返回 v=0.15 m/sc)行程:工作行程 1600mm;最大行程 2500mm3.1.3 可横移摩擦式出钢机a) 最大推力:2.2tb)推钢速度:1.25m/sc)返回速度:2.45m/sd)工作行程:5.6me)最大行程:6m3.1.4 空气预热器(WJZ-3-3)(加热炉尾右侧烟道)技术参数:a) 形式:斜管插入件式b)换热面积:680 m2c)空气进口温度:常温20℃d)空气出口温度:150~350℃e)烟气进口温度:≈705℃f)烟气出口温度:≤345℃g)空气预热量:32600 m3/hh)入预热器的烟气量:37500 m3/hi)空气阻力:1900Paj)烟气阻力:90Pa3.1.5 装料辊道(加热炉尾部):辊子直径(mm)³辊身长度(mm)³辊距(mm)³辊数(mm)——辊道长度(mm)a) Ⅰ组:300³1200³900³9——8100b) Ⅱ组:300³1200³(1000³3+900³6)——8400c) 辊道速度:1—2m/s3.1.6 离心式通风机(2台,加热炉右风机房): a) 型号:9—19—NO16左旋135° b) 风量:44842 m 3/h c) 风压:14900Pad) 配电机型号:Y355M —4 电压:380V 功率:315KW 3.1.7 汽化冷却系统:a) 汽包(加热炉左侧):φ1228³14³8000内径:1200mm 公称长度:7000mm 容积:9.59 m 3 设计压力:1.4Mpa 工作压力:0.2—1.3 Mpa 安全阀开启压力:1.05 Mpab) 蒸汽产量:0—12.5t/h (平均:5t/h ) c) 给水压力:0—1.5 Mpa d) 给水(软水)量:0—25t/h e) 纵横水管、上升和下降管材质:20# f) 下降管集:1根 φ325³8 g) 上升管:11根 φ133³4h) 横水管:13根 φ159³30³6064;3根矩形管 200³160³25³6064 i) 纵水管:3根 φ114³16 j) 炉筋间距:1400mm k) 汽化冷却管道色环标志:序号 名称 颜色 说明1 汽包 红色 色环的宽度为100mm 左右,环间间距为可观察到。
对一些部位,色环有脱落,可顺管道检查其它色环标志。
2 蒸汽管道 红色3 上升管道 红色加蓝环 4下降管道红色加绿环5 放汽管道红色加白环6 疏水管道红色加黑环7 排污管道红色加黑环8 给水管道深绿色3.1.8 汽化冷却操作站:a) 双缸往复式蒸汽泵2台(加热炉控制室楼下):型号:QB—9汽缸工作压力:0.88—1.37Mpa水缸工作压力:0.73Mpa活塞往返频率:26—45次/分供水量:22.5—44m3/hb)离心式清水泵(电动泵)两台:型号:2GC—5³6流量:10m3/h(2.8L/s)扬程:192m转速:2950r/min允许吸上真空高度:5.5m叶轮直径:168mm配电机:型号:y160L—2;转速:2930r/min ;功率:18.5kw标准编号:JB3074—82软水池:1个;容积=30 m33.10 加热常见缺陷及其处理方法:3.10.1加热常见缺陷及其处理方法:缺陷名称造成原因处理方法钢温低加热时间不足,轧制速度快提高炉温,延长加热时间钢上、下表面温差大下加热温度低,加热时间短,均热段停留时间不够提高下加温度,均热段保温趋于均匀后出钢粘钢加热温度高,炉内停留时间长,氧化性气氛严重,出料口温度低快速出钢,控制燃烧气氛,适当降低加热段炉温均热段严禁押火过度氧化空气过剩系数大,加热温度高,加热时间长减少风量,控制为弱氧化性气氛,缩短加热时间,降低加热温度过烧炉温控制高,局部烧嘴调整不当,炉内出现强氧化性气氛减少空、燃气用量,保持炉压,调整烧嘴温度一致,待轧时要控制炉温过热在高温下停留时间长,炉温高了解轧制速度,相应控制各段温度,降低炉温3.10.2 当粘钢后要加强出钢监视,出钢工应及时向调整工汇报,未经同意和采取措施严禁出钢,避免粘钢后发生抵死端墙事故。
3.14 出钢操作规程:(原规程25-26页)3.14.1 出钢节奏应是轧机均衡轧制。
3.14.2 掌握好钢坯出炉温度,不符合规定温度的钢坯不得出炉。
3.14.3 出钢应随时注意炉号标记,更换炉号时应同质检人员核实,并通知下工序(轧机);为避免混炉,必须待上一炉号的最后一条钢在第二架轧完后,方允许下一炉号的钢出炉轧制。
3.14.4 出钢时,应对每炉钢进行认真记数,每炉的出炉数量,必须与进炉数量相符,若发现差错,必须立即报告班长并停止出钢,待差错处理完毕后再出钢轧制。
3.14.5 出钢时不能只在出钢槽一个地方出钢,应保持出钢槽横向的均匀磨损。
3.16 工业水系统使用规程:3.16.1 加热炉工业水供水分两条道路,以保证在其中一条发生故障时有应急水源。
3.16.1 工业水使用压力应在0.196Mpa以上。
3.16.2 应根据各冷却部件部位调节水温和流量,出水温度应控制在40—50℃。
3.16.3 工业水在停炉24小时后可停止向冷却部件供水。
3.16.4 在加热炉点火前后应对各部件逐件检查是否通水。
3.17高温烟囱使用规程:3.17.1 高温烟囱是加热炉的重要组成部分。
必须和炉子的其它部分等同对待,不可偏废,各有关使用单位应设置专人负责高温烟囱的使用、维修和热工管理。
3.17.2 要严格掌握和控制钢结构、砖结构和钢筋混凝土结构的高温烟囱的烟气温度,不允许超过设计温度和排烟量,并实行监测制度。
3.17.3 对现有高温烟囱必须采取降温除尘措施。
凡是烟气温度和排烟量超过设计规定的,烟囱实行限制使用,尽快上降温除尘措施。
3.17.4 余热锅炉和预热器是保护烟囱的重要设备。
因此凡是有余热锅炉的烟囱必须加强管理,建立使用维修制度,不允许根据季节任意停开余热锅炉,更不允许把废气往烟囱排放。
余热锅炉检修应与设备检修密切配合。
原则上规定,余热锅炉停开,设备应停开。
3.17.5 凡牵涉增加烟囱负荷的挖、革、改项目,设计部门必须统一考虑,并对烟囱采取响应技术措施,切不可忽视和偏废。
不得“超负荷(热负荷)”使用烟囱。
3.17.6 要加强高温烟囱的技术状况管理,建立技术档案,作好温度、倾斜等技术测试记录。
要建立高温烟囱的检查和观测制度,定期配合炉子的大中修检查烟囱的筒壁和内衬状况,每一至二年对烟囱的基部进行一次槽探检查,每一至二年组织一次烟囱倾斜测量。
对严重倾斜的烟囱每年要组织两次或多次测量。
作好检查和观测记录,整理好有关技术资料定期上报主管单位。
3.17.7 在生产过程中应密切关注高温烟囱的烟气温度,同时应防止烟道入口处及烟道内积水。
烟气中如有残余煤气时,在生产操作上应采取措施(尽量保证完全燃烧),防止在烟囱筒内爆炸而损坏烟囱内衬或筒壁。
内衬应定期检查和检修,以保证其不产生裂缝和局部脱落。
烟囱底部的凹槽内沉落的积灰应定期清扫。
筒身上的金属爬梯、走台围盘和避雷针系统应保持完整,防止腐蚀。
3.17.8 砖烟囱或钢筋混凝土烟囱加固的钢箍,若有严重腐蚀时,应重涂防腐层,并检查螺栓是否松动,松动的应拧紧。
对高温烟囱加固的拖拉绳要定期检查和维护。
3.17.9 在高温烟囱的筒身上不允许任意打洞和栓拖拉绳。
在其四周应做好排水,在其周围周围的土壤中避免雨水、水管或水沟渗水,以防在地面以下钢筋混凝土筒壁遭受高温高湿而腐蚀损坏。
在烟囱基础部位的地面上,不准修各种建筑物,以防止造成基础不均匀降沉使烟囱倾斜。
3.17.10对“三类”高温烟囱的筒壁和内衬开裂、筒身倾斜等严重缺陷隐患,应组织专人定期检查和观测,特别是在遭遇暴雨、强风和地震时更要注意认真检查和观测,并把检查和观测记录情况及时上报主管单位。
“三类”高温烟囱在没进行大修前,要严加监护,如发现筒身有较大环型裂缝,内衬大面积脱落,烟囱倾斜有大的发展,应立即以重大事故上报,并停炉检修。