基于超声波压接技术在汽车线束生产工艺中的研究
生产工艺的超声技术研究与应用

生产工艺的超声技术研究与应用1、引言超声技术作为一种非常重要的生产工艺手段,在工业生产中发挥着越来越重要的作用。
它通过超声波的作用,能够实现材料的加工、清洗、焊接等多种功能,被广泛应用于汽车制造、电子设备、医疗器械等领域。
本文将重点探讨超声技术在生产工艺中的研究和应用,深入分析其原理、特点以及发展趋势。
2、超声技术的原理及特点超声波是指频率高于人类听觉范围的声波,通常在20kHz以上。
超声波在材料中传播时,能够产生声波的机械作用、热作用和化学作用,从而实现材料的加工和改性。
超声波在密实材料中传播时,会产生谐振现象,形成声波的驻波,从而实现对材料的精细处理。
超声技术具有高效、环保、无损、精密等特点。
其能量传递迅速,可在瞬间内完成材料的加工;同时不产生污染物,对材料本身几乎没有热影响,保持材料的原始性能;其无损作用使得材料的质量得到保证;精密的作用使得超声技术特别适用于微小零件的加工和装配。
3、超声技术在材料加工中的应用超声技术在材料加工中有着广泛的应用,主要包括超声切削、超声焊接、超声清洗等几个方面。
超声切削是指利用超声波的震荡作用,对材料进行微小切削。
与传统的切削方法相比,超声切削具有高效、精准的特点,特别适用于硬度较高的材料。
超声切削还可以减少刀具磨损,延长刀具使用寿命。
超声焊接是指利用超声波的机械振动,使两个工件在较高频率下产生相对运动,从而实现材料的焊接。
超声焊接具有焊接速度快、焊缝强度高、焊接质量好等优点,广泛应用于汽车制造、电子设备、医疗器械等领域。
超声清洗是指利用超声波在清洗液中的作用,对工件进行清洗。
超声波的振动作用可以将清洗液中的微小气泡破裂,产生冲击力,从而彻底清除污垢。
超声清洗具有高效、环保、不伤害工件表面等优点,被广泛应用于电子零件、光学元件、医疗器械等领域。
4、超声技术在汽车制造中的应用超声技术在汽车制造中有着重要的应用价值。
以超声焊接为例,在汽车制造中,超声焊接可以用于汽车车身的组装、塑料零部件的焊接等多个环节。
汽车线束制造工艺

汽车线束制造工艺汽车线束是连接汽车不同系统的重要部件,其制造工艺直接影响着汽车的性能和质量。
随着汽车产业的不断发展,也在不断创新,以适应新的需求和技术发展。
本文将深入研究汽车线束制造工艺的相关内容,分析其在汽车制造中的重要性和影响。
首先,汽车线束制造工艺涉及到多种材料的选择和使用。
在汽车线束制造过程中,需要考虑导电性能、耐热性、耐磨性等多种性能指标,并且不同部位的线束可能需要不同材料来满足其特定的要求。
因此,对材料的选择和使用至关重要,直接影响着线束的性能和寿命。
其次,汽车线束制造工艺还涉及到生产流程和工艺技术的优化。
在传统的汽车线束制造过程中,往往需要大量的人工操作和多道工序,效率低下且易出现质量问题。
因此,采用先进的自动化设备和智能化生产技术进行线束制造已经成为汽车制造企业的重要发展方向。
通过优化生产流程和工艺技术,可以提高生产效率、降低成本,并且提升产品质量。
此外,随着汽车电子技术的不断发展,汽车线束制造工艺也在不断演进。
现代汽车线束不仅仅是传统的导线束,还包括了各种传感器、通讯模块等电子元器件。
这些电子元器件的加入使得汽车线束制造工艺变得更加复杂,需要更高的技术水平和质量控制。
因此,汽车线束制造企业需要不断进行技术升级和人才培养,以适应新的市场需求。
此外,环保和可持续发展也成为当前汽车线束制造工艺发展的重要方向。
传统的线束制造工艺往往会产生大量的废弃物和排放物,对环境造成严重污染。
因此,汽车线束制造企业需要采取环保措施,减少废物排放,推广循环利用技术,实现生产过程的可持续发展。
只有在环保和可持续发展的基础上,汽车线束制造工艺才能真正实现长远发展和持久竞争力。
梳理一下本文的重点,我们可以发现,汽车线束制造工艺在汽车制造中起着至关重要的作用。
只有不断创新和完善线束制造工艺,才能为汽车行业的发展注入强劲动力,提升汽车产品的质量和性能。
相信随着技术的不断进步和产业的不断发展,汽车线束制造工艺会迎来更加灿烂的未来。
汽车线束之超声波焊接工艺

汽车线束之超声波焊接⼯艺线束⾏业中常⽤的焊接⼯艺有:扩散焊接(成本太⾼)、⾼频焊接(焊接温度⾼)、冷压焊接(需要压⼒⼤)和超声波焊接,但是由于前3中焊接⽅式有其⾃⾝的局限性,未能⼤规模的使⽤,只有超声波焊接以其特有的简单,经济成为线束⾏业中的主流焊接⽅式。
超声波焊接是利⽤⾼频振动波传递到两个需焊接的线束⼯件表⾯,在加压的情况下,使两个线束⼯件表⾯相互摩擦⽽形成分⼦层之间的熔合。
其优点在于快速、节能、熔合强度⾼、导电性好、⽆⽕花、接近冷态加⼯;缺点是所焊接⾦属件不能太厚(⼀般⼩于或等于5mm)、焊点位不能太⼤、需要加压。
如下是超声波焊接的两种形态,双边焊接和单边焊接。
双边焊接单边焊接超声波焊接在线束⾏业中根据超声波所在的位置,分为以下3种焊接⼯艺,预装焊接,线边焊接,在线焊接;接下来我们分别介绍这三种焊接⼯艺的优缺点:第⼀种,预装焊接,顾名思义,它是在预装区域焊接导线的⼀种⼯艺,它的特点是原线开线后直接送到预装区域超声波压接,优点是原线运输距离近,同时,由于处于预装区域,它对应总装区域的所有项⽬,因此可以实现集中式⽣产,⼤批量⽣产;在物料充⾜,库存允许的情况下,不间断⽣产可以⼤⼤提⾼了设备的利⽤率;但是也有很⼤的缺点,缺点是由于在预装区域,对于总装的需求信息严重滞后,导致必须要以计划主导的⽣产⽅式,这样就会存在⼤量的WIP物料放在物料暂存区,⼀旦出现订单的波动或者⼯艺参数错误,就会造成⼤量的压接看板报废。
第⼆种、线边压接,意思是在总装线线边压接,他与预装压接的区别在于将压接设备从预装区域搬到总装区域,从预装到总装区域的移动,⽣产⽅式也随之转变,从计划⽣产⽅式(推动式)改为拉动式⽣产⽅式,⽣产⽅式的转变导致⼯位之间的WIP⼤量减少,但由于WIP看板减少,则必须在设计⽣产线时,给超声波⼯位预留⼀定的提前期⽤来备料,否则会存在物料供应不及时呆滞停线的风险。
⽣产流程:总装⽣产线上根据⽣产订单⽣产,在⽣产的过程中,流⽔线上产⽣压接看板需求,此时将拉动看板传递到sonic⽣产区域,⽣产⼈员根据拉动看板信息,给出导线拉动看版需求,从导线暂存区拿取单线看板,然后将单线看板送到总装超声波压接区域,单线通过超声波压接后变成压接看板,压接好的看板然后送⾄总装流⽔线上需求位置。
超声波焊接技术在汽车制造中的应用
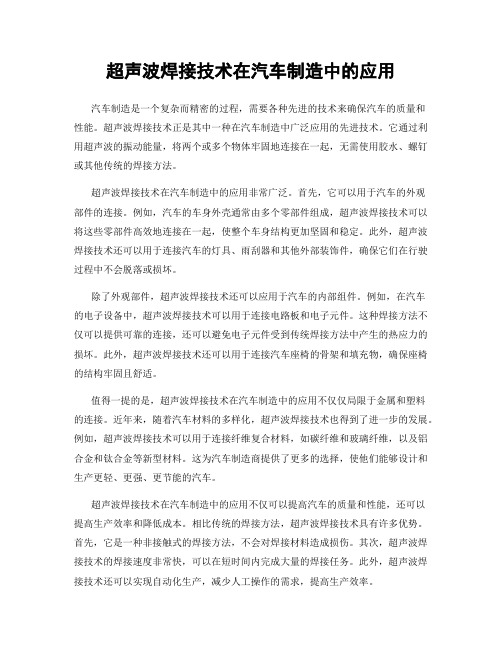
超声波焊接技术在汽车制造中的应用汽车制造是一个复杂而精密的过程,需要各种先进的技术来确保汽车的质量和性能。
超声波焊接技术正是其中一种在汽车制造中广泛应用的先进技术。
它通过利用超声波的振动能量,将两个或多个物体牢固地连接在一起,无需使用胶水、螺钉或其他传统的焊接方法。
超声波焊接技术在汽车制造中的应用非常广泛。
首先,它可以用于汽车的外观部件的连接。
例如,汽车的车身外壳通常由多个零部件组成,超声波焊接技术可以将这些零部件高效地连接在一起,使整个车身结构更加坚固和稳定。
此外,超声波焊接技术还可以用于连接汽车的灯具、雨刮器和其他外部装饰件,确保它们在行驶过程中不会脱落或损坏。
除了外观部件,超声波焊接技术还可以应用于汽车的内部组件。
例如,在汽车的电子设备中,超声波焊接技术可以用于连接电路板和电子元件。
这种焊接方法不仅可以提供可靠的连接,还可以避免电子元件受到传统焊接方法中产生的热应力的损坏。
此外,超声波焊接技术还可以用于连接汽车座椅的骨架和填充物,确保座椅的结构牢固且舒适。
值得一提的是,超声波焊接技术在汽车制造中的应用不仅仅局限于金属和塑料的连接。
近年来,随着汽车材料的多样化,超声波焊接技术也得到了进一步的发展。
例如,超声波焊接技术可以用于连接纤维复合材料,如碳纤维和玻璃纤维,以及铝合金和钛合金等新型材料。
这为汽车制造商提供了更多的选择,使他们能够设计和生产更轻、更强、更节能的汽车。
超声波焊接技术在汽车制造中的应用不仅可以提高汽车的质量和性能,还可以提高生产效率和降低成本。
相比传统的焊接方法,超声波焊接技术具有许多优势。
首先,它是一种非接触式的焊接方法,不会对焊接材料造成损伤。
其次,超声波焊接技术的焊接速度非常快,可以在短时间内完成大量的焊接任务。
此外,超声波焊接技术还可以实现自动化生产,减少人工操作的需求,提高生产效率。
总而言之,超声波焊接技术在汽车制造中的应用是一种高效、可靠且创新的方法。
它可以用于连接汽车的外观部件和内部组件,提高汽车的质量和性能。
超声波焊接在线束中应用(全)
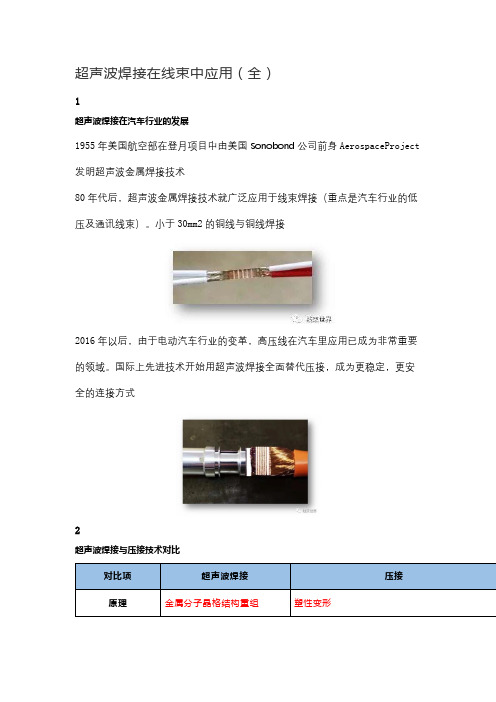
超声波焊接在线束中应用(全)1超声波焊接在汽车行业的发展1955年美国航空部在登月项目中由美国Sonobond公司前身AerospaceProject 发明超声波金属焊接技术80年代后,超声波金属焊接技术就广泛应用于线束焊接(重点是汽车行业的低压及通讯线束)。
小于30mm2的铜线与铜线焊接2016年以后,由于电动汽车行业的变革,高压线在汽车里应用已成为非常重要的领域。
国际上先进技术开始用超声波焊接全面替代压接,成为更稳定,更安全的连接方式2超声波焊接与压接技术对比3超声波焊接原理1, 超声波发生器(配件1)将电能通过内部整流、变压、专用功率管放大成20KHz的高压电源,再设计低阻值导线,输出给压电陶瓷式换能器(配件2). 2, 压电换能器中的压电陶瓷在高压电源的电极下,产生径面振动,振动通过上下金属盖板传导到换能器工作面,根据工作需要换能器盖板可做成放大形状,将陶瓷的振动振幅做初步放大。
(如有需要可再连接变幅杆做振幅二次放大)。
3, 换能器的振动传递到专用耦合器(配件3)上,拉动耦合器的运动杆(配件3)做横向振动。
4, 焊头安装在横向振动端,超声作用时,在振动杆的垂直方向,向下施加压力给耦合器、压力方向与超声振动方向相互垂直,达到摩擦焊接的作用。
来源杭州海颂4超声波检验标准拉力和撕拉力的首检、例检和末检首检:采用一根短样进行拉力或撕拉力首检。
若首检拉力或撕拉力值在表的绿色区域,开始生产;若首检拉力或撕拉力值在表的黄色区域,重新采用一根短样进行拉力或撕拉力测试,若重测短样数值落在绿色区域,可以开始生产;若重测短样数值落在黄色区域,调整参数之后重新首检;若重测短样数值落在红色区域,停产检查,之后重新首检。
欧洲项目撕拉力值必须在绿色区域才可以生产;若首检拉力或撕拉力值落在表的红色区域,停产检查,之后重新首检。
例检和末检拉力测试:如该批次生产数量≤200pcs,不做例检和末检;如200pcs﹤该批次生产数量≤400pcs,需做末检,不做例检;如该批次生产数量>400pcs,需做例检和末检,且例检频率为每400pcs检查一个短样;撕拉力测试:例检频率为每400pcs检查一个短样,如该批次≤400pcs,需做末检,不做例检;例检和末检时,拉力和撕拉力值要在黄色或绿色区域,若发现在红色区域,在此段时间内生产的产品以红牌控制,产品按评审意见处理;超声波焊接控制要求操作工完成首件后,若首件检验合格,则将首件做好标识,标识上应写明日期、时间、看板号、操作工工号、机器号,质量人员对无自检资格员工的首件进行确认。
汽车线束接点的设计与防护研究
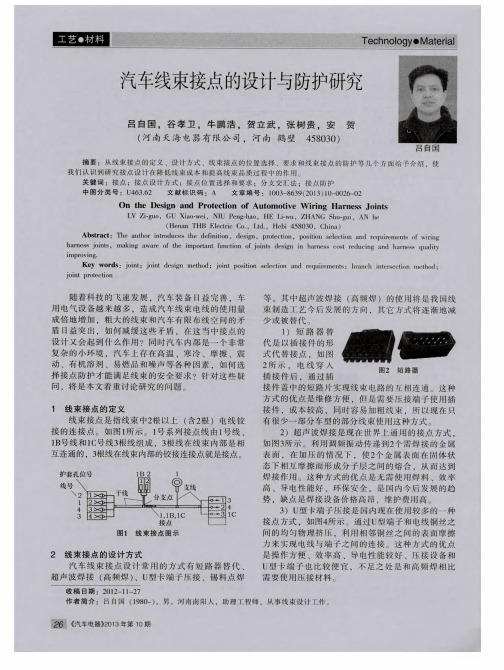
1
1 C
R O. 85
R 0. 85
交汇点 1
交 汇点2
图6 分 支 交 汇 法 二
1 R O. 85 接点1Leabharlann 接点2 1 B
R O. 85
1 C
l A
R O. 85
R 0. 85
图7 双 接 点 铰 接 方 式
般 情 况 下 ,不 建 议 多 点 铰 接 .因 为 接 点 越 多 ,电路 的安 全性 能 就相 对越 差 。 因此 当单 接 点线 径 较 大 或 能 节 省 较 多 电 线 时 .可 考 虑 采 用 双 点 铰 接 ,以避 免接 点过 大 和节 省 电线 。根 据 经验 ,一般 套 整 车线 束 接点 线组 数 在7 O 组左 右 ,若 能 正 确地 选 择 接 点 位 置 ,可 降 低 电 线 原 材 料 成 本 2 %左 右 。 可 以说 正 确地 选择 接 点位 置 .在减 缓 线柬 加 粗 、优 化装 配 、降低 成 本等 方面 具有很 大 的作用 。
3 线 束 接 点 位 置 的 选 择 和 要 求
数 多 于交 汇 点 2 处右 边 的分 支 数 .则接 点 应 选 在 交 汇点 1 右 边 附近 ,反 之应 选 在交 汇点 2 左 边 附近 。若 两交 汇 点处 两边 的 分支数 相 等 ,则 接 点应 选在 两 交 汇点 之 间 。若 两 个交 汇 点之 间 的距 离 比较 长 .可 考 虑 双 点 铰 接 , 即在 交 汇 点 1 处右边附近选择 1 个 接 点 ,在交 汇 点2 处 左 边 附近再 选 择第 2 个 接 点 .以尽 量 减 少 电 线 的长 度 。双 接 点 铰 接 方 式 如 图7 所示 。 l C线 号 为公 共 线 ,1 B 线号铰接在1 C 线 上 。此 种 设 计 与设 计 1 个接 点 相 比 ,可 以节 省 1 B 线 号接 点 1 和接 点2 之 间 的 电线 长 度 。但 设 计 双接 点 时 ,要 注 意公 共 负载 线 1 C 线 号 的电流 负载 能力 。
超声波焊接技术在汽车工业中的应用研究
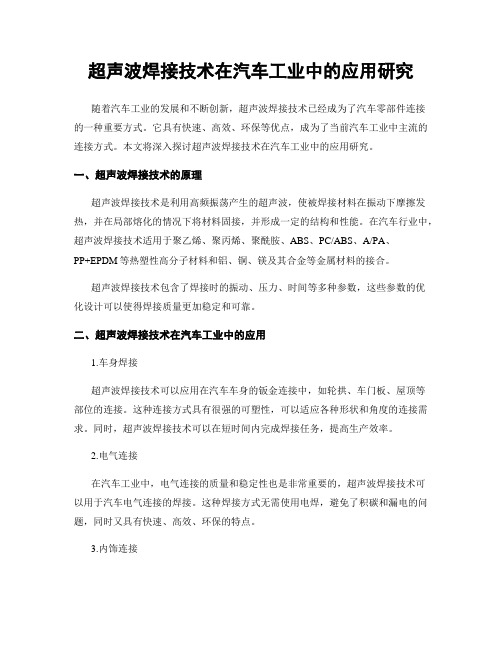
超声波焊接技术在汽车工业中的应用研究随着汽车工业的发展和不断创新,超声波焊接技术已经成为了汽车零部件连接的一种重要方式。
它具有快速、高效、环保等优点,成为了当前汽车工业中主流的连接方式。
本文将深入探讨超声波焊接技术在汽车工业中的应用研究。
一、超声波焊接技术的原理超声波焊接技术是利用高频振荡产生的超声波,使被焊接材料在振动下摩擦发热,并在局部熔化的情况下将材料固接,并形成一定的结构和性能。
在汽车行业中,超声波焊接技术适用于聚乙烯、聚丙烯、聚酰胺、ABS、PC/ABS、A/PA、PP+EPDM等热塑性高分子材料和铝、铜、镁及其合金等金属材料的接合。
超声波焊接技术包含了焊接时的振动、压力、时间等多种参数,这些参数的优化设计可以使得焊接质量更加稳定和可靠。
二、超声波焊接技术在汽车工业中的应用1.车身焊接超声波焊接技术可以应用在汽车车身的钣金连接中,如轮拱、车门板、屋顶等部位的连接。
这种连接方式具有很强的可塑性,可以适应各种形状和角度的连接需求。
同时,超声波焊接技术可以在短时间内完成焊接任务,提高生产效率。
2.电气连接在汽车工业中,电气连接的质量和稳定性也是非常重要的,超声波焊接技术可以用于汽车电气连接的焊接。
这种焊接方式无需使用电焊,避免了积碳和漏电的问题,同时又具有快速、高效、环保的特点。
3.内饰连接汽车内饰的连接方式大多采用注塑和接口技术,在某些特殊的情况下,这些连接方式可能会出现质量不稳定的情况,而超声波焊接技术可以用于汽车内饰各种零部件的连接。
这种技术可以同时完成多个焊点,大大提高了工作效率。
4.制动系统制动系统的连结对汽车的制动效果和安全性有着至关重要的作用,超声波焊接技术可以用于制动系统的某些零部件的连接。
这种技术可以将材料焊接在一起,无需使用铆钉,避免了由过度磨损而引起的接口松动问题。
三、超声波焊接技术在汽车工业中的未来随着汽车工业的发展和创新,超声波焊接技术在汽车工业中的应用将会越来越广泛。
汽车高压线束端子超声波焊接
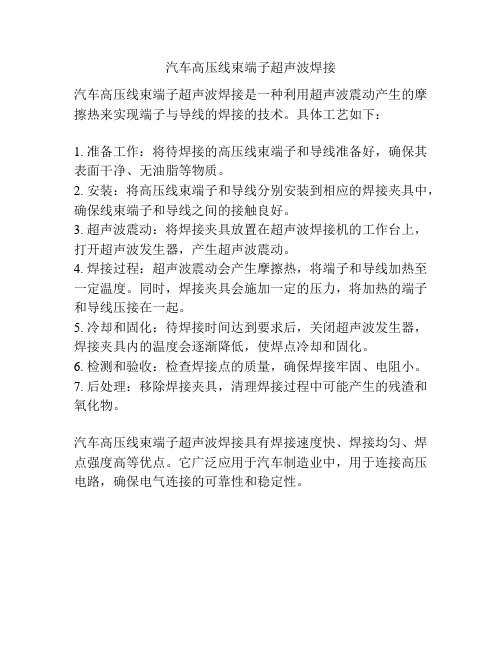
汽车高压线束端子超声波焊接
汽车高压线束端子超声波焊接是一种利用超声波震动产生的摩擦热来实现端子与导线的焊接的技术。
具体工艺如下:
1. 准备工作:将待焊接的高压线束端子和导线准备好,确保其表面干净、无油脂等物质。
2. 安装:将高压线束端子和导线分别安装到相应的焊接夹具中,确保线束端子和导线之间的接触良好。
3. 超声波震动:将焊接夹具放置在超声波焊接机的工作台上,打开超声波发生器,产生超声波震动。
4. 焊接过程:超声波震动会产生摩擦热,将端子和导线加热至一定温度。
同时,焊接夹具会施加一定的压力,将加热的端子和导线压接在一起。
5. 冷却和固化:待焊接时间达到要求后,关闭超声波发生器,焊接夹具内的温度会逐渐降低,使焊点冷却和固化。
6. 检测和验收:检查焊接点的质量,确保焊接牢固、电阻小。
7. 后处理:移除焊接夹具,清理焊接过程中可能产生的残渣和氧化物。
汽车高压线束端子超声波焊接具有焊接速度快、焊接均匀、焊点强度高等优点。
它广泛应用于汽车制造业中,用于连接高压电路,确保电气连接的可靠性和稳定性。
探析TRIZ理论在汽车线束制造工艺改进中的应用

10.16638/ki.1671-7988.2020.17.016探析TRIZ理论在汽车线束制造工艺改进中的应用强晓刚(陕西万方天运汽车电器有限公司,陕西西安710201)摘要:文章针对TRIZ基本理论体系进行简要介绍,并在该理论的指导下,对汽车线束制造工艺进行优化改进,包括问题描述、矛盾分析、资源分析与解决方案等内容。
立足根本,通过研究,使线束制造中存在的技术瓶颈得到有效突破,在提高制造效率的基础上,节约更多成本投入。
关键词:TRIZ理论;汽车线束制造;工艺优化中图分类号:U462.1 文献标识码:A 文章编号:1671-7988(2020)17-53-03Analysis on the Application of TRIZ Theory in the Improvement of AutomobileWire Harness Manufacturing ProcessQiang Xiaogang( Shaanxi Wanfang Tianyun Automobile Electrical Appliance Co., Ltd., Shaanxi Xi'an 710201 )Abstract:This paper briefly introduces the basic theoretical system of TRIZ, and under the guidance of this theory, optimizes and improves the manufacturing process of automotive wiring harness, including problem description, contradiction analysis, resource analysis and solutions. Based on0 the foundation and through the research in this paper, the technical bottleneck in harness manufacturing has been effectively broken through, and on the basis of improving manufacturing efficiency, more cost investment has been saved.Keywords: TRIZ theoryMade; Automobile wiring harness manufacturing; Process optimizationCLC NO.: U462.1 Document Code: A Article ID: 1671-7988(2020)17-53-03引言在汽车行业飞速发展之下,对其舒适性与智能性也提出了较高要求,车内的功能电器数量不断增加,使得各类电器线束导线回路量随之增多,线束制造工艺也越发复杂,传统的制造方式难以满足现实需求,急需在TRIZ理论的引导下,促进制造工艺的优化和改进,使技术问题得到有效解决。
基于超声波压接技术在汽车线束生产工艺中的探讨

0引言汽车线束在汽车电路中具有非常重要的作用,是汽车网络主体,相当于人体中的神经系统,如果汽车线路出现问题必然会导致汽车电路无法正常运行。
传统汽车线束工艺中主要应用的材料为钢材,通过冲制的方式形成接触端子,通过与电线电缆进行压接,为了保护线体,需要在外部塑压绝缘体或者加铸一层金属外壳,将线束通过捆扎的方式形成电路组件。
当前汽车工艺不断发展,各种通讯设备以及电子产品开始进入到汽车装配中,对汽车线束电信号的传输要求更高。
为了保证信号传输以及高精度电压传导要求,必须要在传统线束工艺基础上对材料进行优化,比如采用镀金端子、屏蔽线等。
但是这些材料的更新和优化对于一些电子设备的信号传输作用并不大。
比如安全气囊、CAN 控制器信号以及音频信号传输线路等。
虽然当前端子导线压接工艺中通过材料创新在功能方面已经改善,但是在信号传输过程中仍然容易出现失真或者衰减的情况。
因此超声波压接技术在汽车线束生产中的研究显得尤为必要。
1超声波压接技术超声波压接技术是一种内部连接方式,将裸片金属表面或者器件逻辑电路进行有效互联的一种方式,通过对这些裸片和器件的连接实现芯片信号的连接。
在线束以及芯片等方面的连接具有绝对优势,因此当前汽车线路连接中90%以上都会采用这种连接方式。
一套超声波焊接系统的组件包括很多构件,比如超声波发生器、焊头三联组、换能器变幅杆、机架和模具等,在压接过程中热能来源于一定的压力,通过一个工件在另一个工件表面的振幅或者位移等,在达到预期焊接程度后,会立即停止振动,但是这两个工件上仍然会存在一定的压力,导致刚焊接完成的两个部分冷却、固化,保证连接的紧密性。
轨道式振动摩擦焊接方式主要是通过热能实现焊接作用。
通过将上部构件利用固定速度在轨道上移动的方式沿着各个方向进行圆周运动。
通过运动的方式产生热能,进而使需要焊接的位置达到熔点。
工件熔化后,即可以停止运动,使两个工件焊接位置凝固、连接。
如果夹持力小的情况下会使工件发生轻微变形的情况,但是工件直径不大,在10英寸范围内,可以采用轨道振动摩擦的方式实现焊接。
论线束端口的压接工艺

一
道 非常 重要 的工 序 ,在保证 整个 汽车 线束 生产 中
发 挥着 不可 替代 的作用 。压 接需要 连接 导体 ,因而
需要 采 用安全 可靠 的压 接方式 。线束端 口一 般 由端 子 、导 线和 密封 圈构成 ,将 这些 原材料 加 工成线 束 部 件需要 进行 压接 工作 ,而 压接质 量 的好坏 直接 影 响着 导线连 接的 电气 性能和机械 性能 。
压 接 其 实 就 是 通 过 外 力 将 电线 和 端 子 强 制 结 合 。在 进行 具体工 作 的时候 ,模 具 的上下 刀片依 靠
压 接机 的力 量来 完成整 个压 接工 作 ,其实质 就是 将 端子 从 自由弯 曲向校 正弯 曲完成转变 。
2 电线的顶端剥 皮工作和剥 皮长度 1 关于电 线柬压接
1 . 2 压 接的工作原理
运 行 。线束 是构 成 电路 网络 的主体 ,汽 车 电路依 赖 于 线束 的存 在而 存在 。现 代汽 车无 论是 高档还 是 中 低 档 ,采用 的都 是 同样 的编程 形式 ,所 用到 的基 本 元 件都 是 电线 、接插 件和 传感 器等 。和 其它 的线 束 相 比 ,汽车 线束 所在 的环 境更 加恶 劣 ,因而 安全 可 靠 性也就 成 为 了汽车 线束 在设 计和 生产 环节 首先要 考 虑的 问题 。
1 . 1 压 接 的 概 念 和 作 用
压接 前 ,要 提前 将 电线剥 皮 ,且 在剥 皮 时要 满 足 以下要 求 :首先 ,剥 皮 的长度 不宜太 长或 太短 ;
其 次 ,为了保 证 良好 的导 电性 能 ,绝对 不 允许有 铜 丝 断裂 的情况 ;剥皮 的时候要 注 意 ,绝 对不 允许 有
线束 一 向被 称 为 “ 汽车 的 神经 ” ,汽 车各 种 电 器 功能 的实 现都 是通 过它 来完 成 的 。如 果说 线束 是 汽车 的 “ 神 经 ” ,那 么端 子 则 是 神经 网络 的连 接 点 。 只有熟 练掌 握端 子 的特性 与使 用方 法 ,才 能 更
超声波在汽车制造中的应用有哪些
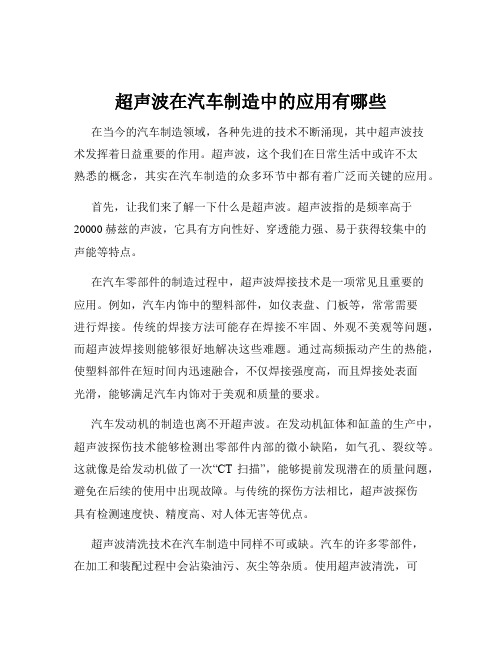
超声波在汽车制造中的应用有哪些在当今的汽车制造领域,各种先进的技术不断涌现,其中超声波技术发挥着日益重要的作用。
超声波,这个我们在日常生活中或许不太熟悉的概念,其实在汽车制造的众多环节中都有着广泛而关键的应用。
首先,让我们来了解一下什么是超声波。
超声波指的是频率高于20000 赫兹的声波,它具有方向性好、穿透能力强、易于获得较集中的声能等特点。
在汽车零部件的制造过程中,超声波焊接技术是一项常见且重要的应用。
例如,汽车内饰中的塑料部件,如仪表盘、门板等,常常需要进行焊接。
传统的焊接方法可能存在焊接不牢固、外观不美观等问题,而超声波焊接则能够很好地解决这些难题。
通过高频振动产生的热能,使塑料部件在短时间内迅速融合,不仅焊接强度高,而且焊接处表面光滑,能够满足汽车内饰对于美观和质量的要求。
汽车发动机的制造也离不开超声波。
在发动机缸体和缸盖的生产中,超声波探伤技术能够检测出零部件内部的微小缺陷,如气孔、裂纹等。
这就像是给发动机做了一次“CT 扫描”,能够提前发现潜在的质量问题,避免在后续的使用中出现故障。
与传统的探伤方法相比,超声波探伤具有检测速度快、精度高、对人体无害等优点。
超声波清洗技术在汽车制造中同样不可或缺。
汽车的许多零部件,在加工和装配过程中会沾染油污、灰尘等杂质。
使用超声波清洗,可以将这些杂质迅速清除,而且能够到达零部件的细微缝隙和复杂形状部位,清洗效果远远优于传统的清洗方法。
不仅如此,超声波清洗还具有高效、节能、环保等优点,能够提高汽车制造的生产效率和质量。
在汽车涂装环节,超声波可以用于测量涂层的厚度。
准确的涂层厚度对于汽车的防腐、美观等方面都至关重要。
传统的测量方法可能会对涂层造成损伤,而超声波测量则是非接触式的,不会对涂层产生任何破坏,同时还能够提供高精度的测量结果。
此外,超声波还在汽车零部件的质量检测中发挥着作用。
比如汽车的传动轴、齿轮等零部件,通过超声波检测可以判断其材质是否均匀、内部是否存在疏松等问题,从而确保零部件的质量符合汽车制造的严格标准。
超声焊接技术在汽车制造中的应用

超声焊接技术在汽车制造中的应用随着汽车制造业的发展及技术的进步,越来越多的新材料、新工艺、新技术被广泛应用。
而焊接技术是汽车制造过程中不可或缺的一环,其质量和效率直接影响着汽车的性能和工艺。
近年来,随着超声焊接技术的不断普及和发展,越来越多的汽车生产厂商把这项技术应用到汽车焊接中,提高汽车制造的质量和效率。
超声焊接技术是一种利用超声波产生的能量,将工件的接合面振动产生焊接效果的高科技焊接方法。
相比传统的电弧焊、气体焊等,超声焊接技术具有很多优点。
首先,其焊接速度快,一个焊点只需0.1~0.5秒即可完成,大幅缩短了汽车制造的生产周期。
其次,焊接过程中不需要使用电弧,不会产生电磁干扰和有害气体,环保安全。
再者,超声焊接可以焊接高强度钢和铝合金等新材料,而传统的焊接方法很难处理这些新材料,因此其应用于汽车制造中广泛受到欢迎。
在汽车制造中,超声焊接技术被广泛应用于车身、底盘等大型部件的焊接。
如车门、发动机盖、车门等部位,这些部位通常需要焊接大量细小的联接件,传统的焊接方式往往难以满足要求。
而超声焊接技术由于其高速、高效的特点,可以在很短的时间内完成大量的焊接任务,提高生产效率。
同时,其焊接质量高,接合强度好,不会形成焊渣、气孔等缺陷,确保车身结构的牢固性和密封性。
除了在车身重要零部件的焊接中应用,超声焊接技术在汽车生产中还有很多其他方面的应用。
例如,座椅框架的焊接、燃油箱的焊接、制动器和悬挂系统的焊接等。
这些部件的焊接可以通过超声焊接工艺实现高效自动化,大幅提高了生产效率和焊接质量。
而且,超声焊接技术还可以被应用于汽车的维修和保养领域,通过其高精度、高效的焊接方式,可以为汽车修补提供更多的选择,节省了时间和成本。
除了应用于汽车制造中的大部件焊接,超声焊接技术在汽车制造的各个环节中都有应用,其应用的领域还在不断扩大和深入。
当然,这项先进的技术在应用过程中也有其局限性和不足之处。
例如,焊接厚度过大的部位和不同材料之间的焊接等,都需要考虑到其范围和限制。
超声波线束焊接工艺的优势探讨

超声波线束焊接工艺的优势探讨摘要:伴随我国交通物流系统的不断完善,对工业搬运车辆设计与应用提出更高的要求。
以叉车为例,作为物流系统中主要搬运设备,在许多如仓库、工厂、港口、机场以及车站中均有所体现,这在一定程度上要求叉车整体设计质量不断提高。
本次研究将对超声波线束焊接工艺做简单介绍,分析超声波线束焊接工艺在叉车线束工艺中的应用表现,在此基础上提出超声波线束焊接工艺应用的具体优势与前景。
关键词:叉车线束;超声波线束焊接工艺;优势前言:作为当前汽车制造领域中常见的电连接工艺,超声波线束焊接属于摩擦焊、冷压焊两种工艺间的一种技术,通过其高密度能量完成焊接过程。
值得注意的是,尽管近年来汽车制造领域中,如叉车线束方面逐渐引入超声波线束焊接工艺,但对其技术应用原理以及技术优势了解较少,可能导致工艺技术应用优势被限制。
因此,本文对超声波线束焊接工艺的研究,具有十分重要的意义。
1超声波线束焊接工艺基本概述关于超声波线束焊接工艺,其中的超声波属于一种高频率震动下产生的高于人类听力声波,通过该能量可满足非铁金属焊接要求。
而线束工艺,可将线束理解为一种载体,主要用于负载源提供信号与电力,负责信号控制以及能量传输,在许多行业领域中均有所涉及,如家用电器、航空航天设备、轮船、农用设备、工程机械设备以及汽车等。
结合近年来大多研究,可发现线束中应用较为广泛的是铜质材料,在几公里长度范围内,铜质线束均可到达,这在帮助控制信号传播以及能量传递等有积极作用,若能将其引入到压接、焊接中,更有助于组织的可靠连接。
目前,线束连接方式中选择超声波线束焊接,在汽车制造领域如叉车线束工艺组中优势极为突出,这也是行业发展的重要趋势[1]。
2超声波线束焊接工艺在叉车线束工艺中的应用表现2.1超声波线束焊接工艺基本原理叉车线束工艺中,将超声波线束焊接工艺引入,其实现的原理首先表现在两块工件夹持状态下,在焊接端头、硬砧中有静压力产生,工件顶部位置将接收超声波能量,该能量可保持短暂时间,使表面沾污物质、氧化膜摩擦破碎清除,此时有清洁的新生金属暴露,相互结合两个表面达到焊接目的。
浅谈超声波焊接与u型端子压接

电线束是电气原理图的产品反映,是电气系统电源信号或数据信号进行传递或交换,实现电器部件功能,满足车辆行驶安全、可靠、娱乐实时控制的载体。
而导线在汽车线束和整车电气系统中占有极其重要的地位。
理想状态下,导线、端子、用电器之间的连接应该是零电位、零阻抗的载体。
由于连接端的物理特性、环境特性和材料的特性,汽车电气系统中总是存在一定的电压降。
一般来说,线路的电压降应当不超过电路电压的3%。
例如在12V 电路中,最大电压降不能超过0.36V ,剩余的97%电压(11.64V )应该有效用于电器负载。
由于汽车线束所用的导线直接存在多根导线合线连接的必然性,借助不同的工装设备、工艺方法,最大限度地降低因导线因素而引起的电压降,通常情况下,小于3mV 均为合格电压降。
在汽车线束的生产制造过程中,对于需要合线连接的导线一般采用U 型端子打卡连接、超声波焊接机对合线接点进行焊接,以及端子双线、多线共压连接等工艺方法。
本文对U 型端子打卡连接和超声波焊接的接点电压降做出分析与比较。
1导线集中连接时通常采用的两种方式目前导线集中连接时通常采用两种方式,一种是采用U 型连接端子冷冲压接,另一种是采用超声波焊接。
关于采用这两种方法的简要介绍和电压降对比,本文作了简要叙述,浅见与大家共同探讨。
1.1U 型连接端子冷冲压接U 型连接端子冷冲压接简称U 型压接,是传统的导线连接压接方式。
U 型压接是根据接点线径总和选择U 型端子(图1)和压接机,并为每个型号的U 型端子制定专用的压接模具和钳口,然后将两根或两根以上的导线借助U 型端子压接设备冷冲压在一起的过程。
U 型压接示意图如图2所示。
U 型端子和压接机的选择对照见表1,接点压接标准样表见表2。
压接机配备有压力监控装置,如图3所示。
当出现异常情况(浅打、深打、漏线、铜丝打断、芯线翘出等)时,自动报警并锁定压接设备,必须手动解除锁定。
压接参数和检测依据应符合QC /T29106的要求。
汽车线束生产的防错工艺大全

汽车线束生产的防错工艺大全通常情况下,汽车线束的制造分为切线压接、合线压接(焊接)、预装配、总装配、检验、包装工序组成。
前工程的切线压接和合线压接(焊接)工序的自动化程度相对较高,后工程的预装配、总装配、检验、包装工序的自动化程度较低,基本上依靠人工集中组装完成,是典型的离散式制造,同时又是劳动密集型制造类型。
因此,其生产线的防错尤为重要。
我们一起来看看线束生产线到底有哪些防错。
切线压接工序(MES系统防错)切线压接工序是汽车线束制造中自动化程度最高的工序。
因此切线压接工序是制造错误出现几率较低的一个工序,通常出现的制造错误是导线、端子、防水栓物料使用错误,导线长度错误,以及压接模具用错导致压接标准不正确,导致半成品返修或报废。
运用线束MES系统的工厂通常采用在切换不同看板时进行物料、模具条码扫码确认进行防错,扫码错误出现声音、图像报警,能有效的防治物料的错误使用。
半自动机压接工序(CFM压力监测系统防错)对有些极端的线束,太短或合压、合铆、带防水塞于无法上自动机的压接的,只能靠半自动机人工压接。
该工序自动化水平较低,因为其以人工作业为主导,包括手工穿栓、热缩管、闭口PVC管、绑线、单线手工压接端子、合线压接节点、超声波焊接节点等作业,同时也是出现制造错误较多的一个工序。
对于压接质量,端子机可以配置压力监测系统CFM和端子切面分析系统,对压接不合格的及时处理。
首件检验对端子做剖面分析及拉力测试、电压降测试也是确保压接质量,有效预防批量压接不良的重要途径。
对颜色、大小、形状相似或接近的防水栓,通过工艺编排在不同的工位进行手工作业,或者采用机器穿防水栓操作。
每种防水栓存储容器上带有物料号、描述、图片等醒目标识能有效识别。
每捆半成品导线标签的看板信息、导线信息、产品项目信息完整、清晰也能有效的防止看板导线的使用错误。
相同看板的半成品导线集中存放在缓存架、周转车、周转箱中且标识完整易于识别,也能有效的防止看板导线的错误拿取使用。
超声波线束焊接工艺优势
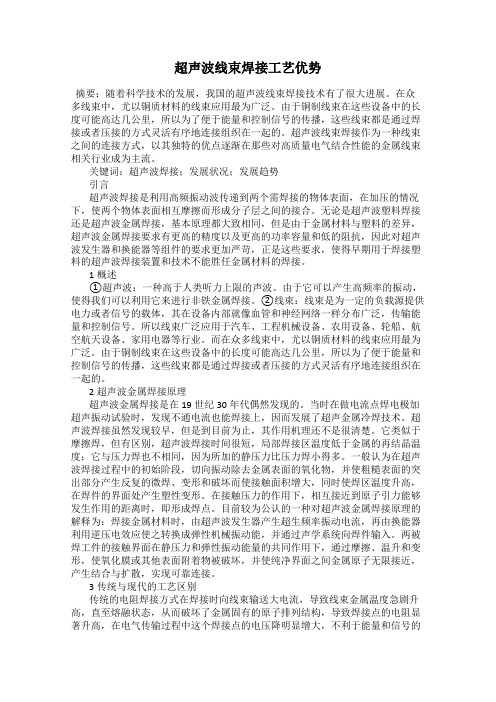
超声波线束焊接工艺优势摘要:随着科学技术的发展,我国的超声波线束焊接技术有了很大进展。
在众多线束中,尤以铜质材料的线束应用最为广泛。
由于铜制线束在这些设备中的长度可能高达几公里,所以为了便于能量和控制信号的传播,这些线束都是通过焊接或者压接的方式灵活有序地连接组织在一起的。
超声波线束焊接作为一种线束之间的连接方式,以其独特的优点逐渐在那些对高质量电气结合性能的金属线束相关行业成为主流。
关键词:超声波焊接;发展状况;发展趋势引言超声波焊接是利用高频振动波传递到两个需焊接的物体表面,在加压的情况下,使两个物体表面相互摩擦而形成分子层之间的接合。
无论是超声波塑料焊接还是超声波金属焊接,基本原理都大致相同,但是由于金属材料与塑料的差异,超声波金属焊接要求有更高的精度以及更高的功率容量和低的阻抗,因此对超声波发生器和换能器等组件的要求更加严苛,正是这些要求,使得早期用于焊接塑料的超声波焊接装置和技术不能胜任金属材料的焊接。
1概述①超声波:一种高于人类听力上限的声波。
由于它可以产生高频率的振动,使得我们可以利用它来进行非铁金属焊接。
②线束:线束是为一定的负载源提供电力或者信号的载体,其在设备内部就像血管和神经网络一样分布广泛,传输能量和控制信号。
所以线束广泛应用于汽车、工程机械设备、农用设备、轮船、航空航天设备、家用电器等行业。
而在众多线束中,尤以铜质材料的线束应用最为广泛。
由于铜制线束在这些设备中的长度可能高达几公里,所以为了便于能量和控制信号的传播,这些线束都是通过焊接或者压接的方式灵活有序地连接组织在一起的。
2超声波金属焊接原理超声波金属焊接是在19世纪30年代偶然发现的。
当时在做电流点焊电极加超声振动试验时,发现不通电流也能焊接上,因而发展了超声金属冷焊技术。
超声波焊接虽然发现较早,但是到目前为止,其作用机理还不是很清楚。
它类似于摩擦焊,但有区别,超声波焊接时间很短,局部焊接区温度低于金属的再结晶温度;它与压力焊也不相同,因为所加的静压力比压力焊小得多。
浅谈汽车线束中的搭铁线设计7-10
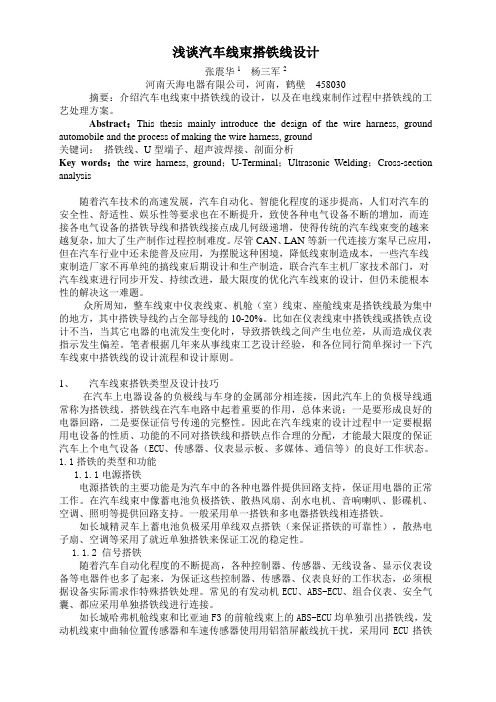
浅谈汽车线束搭铁线设计张震华1杨三军2河南天海电器有限公司,河南,鹤壁458030摘要:介绍汽车电线束中搭铁线的设计,以及在电线束制作过程中搭铁线的工艺处理方案。
Abstract:This thesis mainly introduce the design of the wire harness, ground automobile and the process of making the wire harness, ground关键词:搭铁线、U型端子、超声波焊接、剖面分析Key words:the wire harness, ground;U-Terminal;Ultrasonic Welding;Cross-section analysis随着汽车技术的高速发展,汽车自动化、智能化程度的逐步提高,人们对汽车的安全性、舒适性、娱乐性等要求也在不断提升,致使各种电气设备不断的增加,而连接各电气设备的搭铁导线和搭铁线接点成几何级递增,使得传统的汽车线束变的越来越复杂,加大了生产制作过程控制难度。
尽管CAN、LAN等新一代连接方案早已应用,但在汽车行业中还未能普及应用,为摆脱这种困境,降低线束制造成本,一些汽车线束制造厂家不再单纯的搞线束后期设计和生产制造,联合汽车主机厂家技术部门,对汽车线束进行同步开发、持续改进,最大限度的优化汽车线束的设计,但仍未能根本性的解决这一难题。
众所周知,整车线束中仪表线束、机舱(室)线束、座舱线束是搭铁线最为集中的地方,其中搭铁导线约占全部导线的10-20%。
比如在仪表线束中搭铁线或搭铁点设计不当,当其它电器的电流发生变化时,导致搭铁线之间产生电位差,从而造成仪表指示发生偏差。
笔者根据几年来从事线束工艺设计经验,和各位同行简单探讨一下汽车线束中搭铁线的设计流程和设计原则。
1、汽车线束搭铁类型及设计技巧在汽车上电器设备的负极线与车身的金属部分相连接,因此汽车上的负极导线通常称为搭铁线。
- 1、下载文档前请自行甄别文档内容的完整性,平台不提供额外的编辑、内容补充、找答案等附加服务。
- 2、"仅部分预览"的文档,不可在线预览部分如存在完整性等问题,可反馈申请退款(可完整预览的文档不适用该条件!)。
- 3、如文档侵犯您的权益,请联系客服反馈,我们会尽快为您处理(人工客服工作时间:9:00-18:30)。
基于超声波压接技术在汽车线束生产工艺中的研究
作者:曹志良
来源:《科技资讯》2016年第18期
摘要:汽车线束是汽车电气系统的神经中枢,其设计制造工艺的优劣直接影响到整个汽车电器系统的正常工作。
电子和信息技术的发展,对汽车线束设计制造工艺提出了越来越苛刻的要求,尤其是对汽车线束传输信号的质量。
因而,仅仅通过在汽车线束生产中采用诸如屏蔽线、双绞线、镀金端子等远远满足不了这些要求。
事实上,超声波压接工艺也是提高汽车线束传输信号和输送电流质量的一大措施。
关键词:超声波压接汽车线束生产工艺
中图分类号:TP39 文献标识码:A 文章编号:1672-3791(2016)06(c)-0054-02
汽车线束是汽车电路的网络主体,汽车正常工作的神经元。
没有线束也就不存在汽车电路。
传统的汽车线束是指由铜材冲制而成的接触件端子(连接器)与电线电缆压接后,外面再塑压绝缘体或外加金属壳体等,以线束捆扎形成连接电路的组件。
随着汽车电子产品和各种通讯设备进入汽车,对汽车线束传输的电信号的要求也日益苛刻。
为应对这些高精度电压和信号传输的要求,传统的线束制造工艺上采用了一些特殊材料,比如双绞线、屏蔽线、镀金端子等。
然而,在多数的电子控制设备和一些特殊信号上仍然显得无济于事,例如CAN控制器信号传输线路、安全气囊信号传输线路以及一些音频信号传输线路。
现有的端子导线对压接工艺尽管采用了以上特殊材料,但在上述信号传输线路中,信号偶尔还是出现失真或较大衰减。
1 端子压接工艺的研究
采用传统压接工艺压接的汽车线缆,经解剖放大发现在铜丝与铜丝之间、铜丝与端子壁之间形成空洞[1]。
传统汽车线束生产工艺采用铜材冲制而成的接触件端子(连接器)与导线压接,仅对电线铜丝进行简单挤压,使铜丝产生物理变形,这样就有可能出现铜丝变形不足,在端子与导线进行压接后,必然形成上述空洞,这些空洞的存在,是不可避免的。
而这些空洞的存在,必然导致压接部位电阻系数增加,导电性下降,从而影响电流和信号的传输质量,进而影响其他电器及电子设备的正常工作。
同时,线束制作过程中因压接引起的质量缺陷[2],必将导致使用耐久性降低,并且易发热产生高温,形成线束烧损质量隐患点。
2 超声波压接和端子压接工艺对比分析
超声波压接是通过电晶体功能设备将工频50/60 Hz的电频转变成20 kHz或40 kHz的高频电能,供应给转换器,转换器将电能转换成高频机械振动能,调压装置将高频机械能传至超声波焊接机的焊头。
振动通过焊头传递到需要焊接的两个金属表面,两个金属表面相互摩擦形成热能使金属熔化,在短暂的压力下可以使熔化物在粘合面固化时产生强分子键,最终形成金属分子层之间的熔合,整个周期通常是不到一秒种便完成,但是其焊接强度却接近于一块连着的材料。
而传统的端子压接是通过金属端子的U型部位对电线铜丝进行简单物理挤压,利用相邻铜丝之间的表面摩擦力来保证电线与端子之间的连接。
事实上,无论是经超声波压接的导线还是端子和导线,在压接处呈矩形状,无松散的芯线和断头或裂开的芯线;而且,导线没有弯曲,而是在自熔合处呈直线引出。
超声波焊接是通过相邻金属表面熔化,形成金属分子层之间的熔合,相当于将相邻金属熔为一个整体,相比端子压接后相邻铜丝仍为独立金属个体而言,焊接部位的密实度更好,不会出现空洞。
导电性好,电阻系数极低或近乎于零,有效提高了使用耐久性,不易发热,无质量隐患。
如图1所示,为超声波压接截面[1]。
3 超声波压接和端子压接的试验数据分析
在进行压接处外观对比和截面分析基础上,笔者对两种压接工艺的导线进行了拉脱力和导电性能测试。
测试分别选取了0.75mm2、4.0 mm2、16.0 mm2导线进行试验。
试验方法和标准依据《QC/T29106-2004汽车用低压电线束技术条件》的要求进行,试验结果见表1[2]和表
2[2]。
从表1可以看出,超声波压接和端子压接在拉脱力性能上,均可以满足使用要求,但由于压接工艺本身差异,端子压接截面往往出现空洞,芯线外漏、绝缘层破损等质量缺陷。
从表2可以看出,超声波压接比端子压接的电压降在同样条件下要低得多,因而对导电性能和信号传输性能比端子压接要优越得多。
至少可以有以下3个方面的优点。
第一,解决端子压接形成的空洞,提高导电性能和整个电气系统的稳定性能[3]。
第二,减低因接触电阻引起的热量堆积[4],防止了线束局部温度升高和线束烧毁的质量隐患。
第三,防止了线束中导线受外界水分、灰尘、油气等不良因素影响而造成铜丝锈蚀、氧化,从而引起导电性能下降和信号传输失真。
基于上述研究,笔者认为对信号要求很高或电流较大的线路,在其端子与导线、导线与导线间的压接,采用超声波压接,对提高信号传输质量或电流输送能力是非常有效的,而且也可以提高汽车电气系统的稳定性。
参考文献
[1] 重庆长华汽车线束有限公司.超声波压接与端子压接对比分析报告[R].2010.
[2] QC/T29106-2004汽车用低压电线束技术条件[Z].2004.
[3] 秦明华.汽车电器与电子技术[J].北京理工大学出版社,2001.
[4] 德国BOSGH公司.译.汽车电气与电子[M].魏春源,等,译.北京理工大学出版社,2004.。