DFMEA功能框架图
DFMEA工具培训学习课件
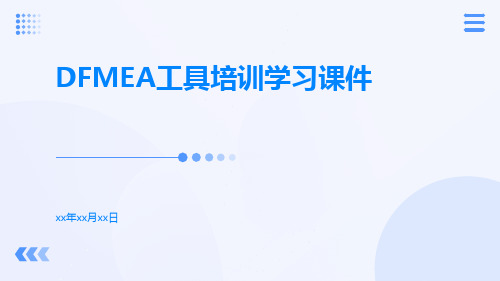
人工智能技术
人工智能技术的不断发展,为DFMEA工具带来更多创新可能 ,如机器学习和深度学习等技术将被广泛应用于缺陷分析、 风险评估等领域。
大数据技术
大数据技术的不断发展,为DFMEA工具带来更高效的数据处 理和分析能力,有助于更准确地进行缺陷预测和风险评估。
DFMEA工具的应用前景
汽车行业
DFMEA工具将继续在汽车行业中得到广泛应用,进一步降低汽车产品的缺陷 率和提高产品质量。
其他行业
除了汽车行业,DFMEA工具也将不断拓展到其他行业中,如电子产品、机械 设备等领域,为更多行业提供质量保障支持。
06
总结与回顾
本次培训的主要内容回顾
DFMEA工具的概念 和原理
DFMEA是一种以故障模式与影 响分析(FMEA)为基础的质量 工具,用于在产品设计过程中识 别和解决潜在的设计问题。
电子行业DFMEA应用 案例
某电子制造企业在生产过程中遇到了 一个严重的质量问题,导致产品批量 报废。通过应用DFMEA工具,企业 发现故障原因为原材料质量不过关, 及时更换供应商并采取其他质量控制 措施,避免了类似事件的再次发生。
04
DFMEA工具的进阶技巧
如何提高DFMEA工具的效率
01
熟练掌握快捷键
03
DFMEA工具的应用案例
DFMEA工具在汽车行业的应用
汽车行业应用背景
随着汽车行业的不断发展,产品复杂度不断提高,市场竞争日益激烈。应用DFMEA工具 可以帮助汽车制造企业更好地分析产品设计、生产和制造过程中潜在的风险,提高产品质 量和安全性。
DFMEA在汽车行业的应用流程
DFMEA工具在汽车行业的应用主要包括以下步骤:制定项目计划、收集相关数据和信息 、进行故障模式分析、建立故障影响矩阵、制定改进措施、跟踪和监督实施情况等。
DFMEA介绍(共53张)

测试和型号资料
其他
第20页,共53页。
DFMEA表格
(biǎogé)
第21页,共53页。
DFMEA实例(shílì)说 明
第22页,共53页。
第23页,共53页。
1) FMEA编号(biān hào)
• 填入FMEA文件编号, 以便查询。
第24页,共53页。
2) 系统、子系统或零部件的名称(míngchēng) 及编号
第2页,共53页。
FMEA 的起源(qǐyuán)
FMECA(Failure Mode Effects and Criticality Analysis)
•1950’s 起源于宇航和美国军方,美国Grumman公司第一次把
FMEA思想用于一种战斗机的操纵系统的设计分析,取得较好效
果,以后逐渐推广.
装配、制造、材料、 质量、服务和供方,以及负责下一总成的设计部门。
❖ FMEA可成为促进有关部门间充分交换意见的催化剂,从而提高整个集
体的工作水平。 ❖ 此外,任何(内部或外部的)供方设计元素应向有关负责设计的工程师
进行咨询。 ❖ 设计FMEA是一份动态文件,应在一个设计概念最终形成之时或之前
开始,而且,在产品开发各阶段中,当设计有变化或得到其它信息时, 应及时,不断地修改,并最终在产品加工图样完成之前全部结束。
,在产品图样、规范发放前结束。 • 改进设计、或对设计重新评估。 • D-FMEA要及时反映最新的产品更改级别,和最新的相关实施措施.
在D-FMEA中,不应把克服潜在设计缺陷的方法,寄托于 过程控制。相反地,应当充分考虑制造过程本身的限制因素,
考虑可制造性和装配性。
第17页,共53页。
DFMEA完整教程幻灯片

5) 年型/車型
? 填入将使用和/或正被分析的设计所影响 的预期的年型及车型(如果已知的话)。
31
6) 关键日期
? 填入FMEA初次预定完成的日期,该日 期不应超过计划的生产设计发布的日期。
32
7) FMEA日期
? 填入编制 FMEA原始稿的日期及最新修 订的日期。
33
设计FMEA表
系统 子系统 零组件: 型号/年份: 核心小组:
? FMEA能夠減少或消除因修改而帶來更大損失的 機會。
? 適當的應用FMEA是一個相互作用的過程,永無
止境。(隨著新的失效模式的出現 , FMEA文件是
一個動態文件 )
7
失效的定義
? 失效 :
–在規定條件下 (環境、操作、時間 )不能完成 既定功能。
–在規定條件下 , 產品參數值不能維持在規定的 上下限之間。
? 填入FMEA文件編號, 以便查询。
27
2) 系统、子系统或零部件的名称及编号
? 注明适当的分析级别并填入所分析系統、 子系統或零件的名稱、編號
28
3) 設計責任
? 填入整车厂(OEM)部門和小組, 如果 知道,还应包括供方的名稱。
29
4)编制者
? 填入负责FMEA准备工作的工程师的姓 名、电话和所在公司的名称。
? FMEA可成為促進有關部門間充分交換意見的 催化劑,從而提高整個集體的工作水平。
? 此外,任何(內部或外部的)供方設計項目應向 有關負責设计的工程師進行諮詢。
17
集體的努力
? 設計 FMEA 是一份動態文件,應在一個設計概 念最終形成之時或之前開始,而且,在產品開 發各階段中,當設計有變化或得到其它信息時, 應及時,不斷地修改,並最終在產品加工圖樣 完成之前全部結束。
DFMEA培训

DFMEAReport Time:Reporter:C ONTENTS Part 1Part 2Part 3Part 4Part 52of 75FMEA简介PART 13of 754of 75一、FMEA简介FMEA 历史AIAG&VDA5of 75一、FMEA简介FMEA 版本变更AIAGAutomotive Industry Action Group汽车工业行动小组(美国)VDAVerband der Automobilindustrie汽车工业协会(德国)目前公司使用版本6of 75一、FMEA简介2019年7月份正式实施结合AIAG范围分析结合AIAG评估结合AIAG管理结合VDA五步法框架FMEA 新版后续讲解中要采用新版的工具和部分内容FMEA定义•FMEA:是一个以小组为导向,系统的,定性分析方法工具。
•FMEA:被视为一个单点故障分析方法。
•对于定量和多点故障分析,可以采用FTA(故障树分析)等工具,这些工具能够计算和分析相关指标,达到量化的分析结构。
7of 758of 75FMEA目的FMEA分类9of 75DFMEA准备PART 210of 75二、DFMEA准备1.DFMEA小组成员确立:设计、工艺、质量、试验、专家、供应商、协调员等2.DFMEA成员职责定义:以设计为主导,设置协调员3.DFEMA项目计划:根据产品开发节点需求开展4.DFEMA输入资料准备:过往失效信息、设计变更、结构BOM、原理图、相关法规标准、DVP、质量特性等11of 7512of 75二、DFMEA准备FMEA是一个事发前行为,而不是先期产品质量策划(APQP阶段)FMEA时间安排13of 75成熟度保证(MLA)阶段FMEA时间安排14of 7515of 75二、DFMEA准备4、DFEMA输入资料准备:过往失效信息、设计变更、结构BOM、原理图、相关法规标准、DVP、质量特性等过往失效信息:设计变更:哪些是设计变更?设计变更要分析产品中哪些部件进行了设计变更,以及变更程度有多大;设计变更可能带来新的可靠性风险(潜在失效);一个好的设计,源于对产品设计更改的正确认识,所以DFMEA要对功能、参数、材料、结构等发生变更的要素进行潜在失效分析。
DFMEA标准教材PPT课件

9
DFMEA实施
团队方法:DFMEA是由一个多方论证(跨职能)的小组来开 发和维护的。小组通常由负责设计的工程师领导。
设计及制造等相关工作人员
ห้องสมุดไป่ตู้
团队要求
- 经验/过去问题处理积累的知识,转变为公司的无形资产;
- 有效的团队管理;
- 对所有活动的结果文件化;
多方参与应用DFMEA,有助于理清产品和过程分析、评审的 思路
2020年3月29日
1
课程目的
掌握DFMEA的概念 和运用时机
发现、评价产品设计中 潜在的失效及其后果
找到能够避免或减少这 些潜在失效发生的措施
2020年3月29日
将上述过程总结形成文 件
2
DFMEA
Design Potential Failure Model And Effect Analysis
DFMEA应用的主要行业 -- 航空业 ——复杂的体系,产品和过程, 小批量生产 -- 汽车业——复杂的体系,产品和过程, 大批量生产 -- 其它行业
2020年3月29日
3
DFMEA发展简史
• 正式使用DFMEA技术是美国六十年代的 阿波罗登月计划。
能否预测人类第一次登月会出现 的后果以及提前采取对策。
有效运用 DFMEA 可减少事后追悔
2020年3月29日
7
DFMEA介绍
• 及时性是成功实施DFMEA的最重要因素之一。 • 它是“事前的预防”而不是“事后的追悔”。 • 事先花时间进行DFMEA分析,能够容易且低成本地对产
品设计或制程进行修改,从而减轻事后修改的危机。 • DFMEA能够减少或消除因修改而带来更大损失的机会,
30
常用的一种DFMEA结构
DFMEA——设计失效模式和后果分析(一)
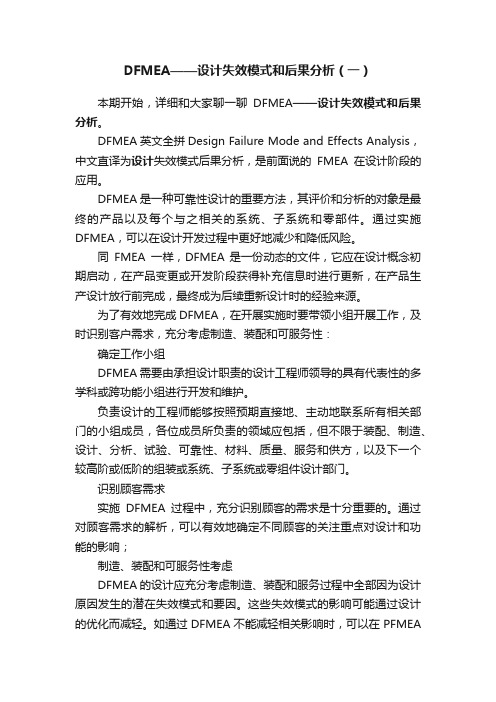
DFMEA——设计失效模式和后果分析(一)本期开始,详细和大家聊一聊DFMEA——设计失效模式和后果分析。
DFMEA英文全拼Design Failure Mode and Effects Analysis,中文直译为设计失效模式后果分析,是前面说的FMEA在设计阶段的应用。
DFMEA是一种可靠性设计的重要方法,其评价和分析的对象是最终的产品以及每个与之相关的系统、子系统和零部件。
通过实施DFMEA,可以在设计开发过程中更好地减少和降低风险。
同FMEA一样,DFMEA 是一份动态的文件,它应在设计概念初期启动,在产品变更或开发阶段获得补充信息时进行更新,在产品生产设计放行前完成,最终成为后续重新设计时的经验来源。
为了有效地完成DFMEA,在开展实施时要带领小组开展工作,及时识别客户需求,充分考虑制造、装配和可服务性:确定工作小组DFMEA需要由承担设计职责的设计工程师领导的具有代表性的多学科或跨功能小组进行开发和维护。
负责设计的工程师能够按照预期直接地、主动地联系所有相关部门的小组成员,各位成员所负责的领域应包括,但不限于装配、制造、设计、分析、试验、可靠性、材料、质量、服务和供方,以及下一个较高阶或低阶的组装或系统、子系统或零组件设计部门。
识别顾客需求实施DFMEA过程中,充分识别顾客的需求是十分重要的。
通过对顾客需求的解析,可以有效地确定不同顾客的关注重点对设计和功能的影响;制造、装配和可服务性考虑DFMEA的设计应充分考虑制造、装配和服务过程中全部因为设计原因发生的潜在失效模式和要因。
这些失效模式的影响可能通过设计的优化而减轻。
如通过DFMEA不能减轻相关影响时,可以在PFMEA或后续的风险分析中进行控制。
DFMEA实施的主旨不应仅仅依靠过程控制去克服潜在设计弱点,但它可以充分考虑在制造和装配过程中增加技术和物理限制,更好的识别和控制风险。
DFMEA 的开展应聚焦于交付于最终顾客产品、过程或服务的设计。
DFMEA文件ppt

制定DFMEA文件的维护计划,包括维护内 容、时间间隔、责任人等方面的规定。
数据统计
持续改进
对DFMEA文件的更新和维护数据进行统计 和分析,以便了解DFMEA文件的整体情况 和改进方向。
通过对DFMEA文件的持续改进,提高 DFMEA分析的准确性和效率,为产品或系 统的可靠性提供有力支持。
THANKS
FMEA文件的审查要点
1 2
完整性检查
检查FMEA表格中是否涵盖了所有可能的故障 模式。
准确性检查
检查故障模式的识别是否准确,措施和建议是 否有效。
3
充分性检查
检查FMEA文件中是否充分考虑了所有相关方 的需求和要求。
FMEA文件的改进方向
针对FMEA文件中存在的不足之处,应提出改进措施和建议。 在设计和制造过程中,应不断更新FMEA文件,以便及时反映新的故障模式和措施。 在产品开发周期中,应定期审查FMEA文件,以便评估其有效性和适用性。
05
DFMEA文件的编制和管理
DFMEA文件的编制流程
确定DFMEA范围
明确DFMEA分析的产品或系统范围,并根据范围确定 所需的分析内容。
搜集信息
收集与产品或系统相关的技术信息、故障数据、用户需 求等,以备后续分析使用。
功能划分
将产品或系统划分为若干功能或子系统,并对每个功能 或子系统进行编号和描述。
化工行业是基础原材料工业的重要领 域,涉及石油化工、有机化工、无机 化工、橡胶制品等多个领域。
02
DFMEA在化工生产 中的应用
化工生产过程中,DFMEA可以应用于 生产工艺控制、设备维护、安全管理 等多个环节,提高生产效率和产品质 量。
03
案例分析
以某大型化工企业为例,通过运用 DFMEA工具,发现并解决了一个潜在 的生产安全隐患,避免了可能出现的 生产事故和人员伤亡。
全面质量管理-DFMEA介绍PPT课件

三、FMEA方法--探测度D
探测时机
标准制程控制中侦测问题的可能
测检
肯定不可能探测
当前过程无法控制,不能侦测或不能够分析
几乎不可能
任何工序不能探测
失效模式或发生的原因不易被侦测出来(如:巡检)
可能性极小
后制程可探测 材料的探测 后制程可探测 材料的探测 后制程可探测 材料的探测 失效探测/问题预防 不需要探测
FMEA是对确定设计或过程必须做哪些事情才能使顾客 满意这一过程的补充。
益
授课:XXX
-
7
二、FMEA的益处:
√ 改进产品的质量、可靠性与安全 √ 提升企业的形象和竞争力 √ 降低成本 √ 减少浪费 √ 降低保证成本 √ 书面规定并跟踪减少风险所需的措施
主要作用——预防!
益
授课:XXX
-
8
二、FMEA的分类 ★系统FMEA—早期构思设计阶段
授课:XXX
11
三、DFMEA 人员构成:
DFMEA人员构成:
在筹备样件期间开始 ➢ 设计工程师-通常的小组领导 ➢ 检验工程师 ➢ 可靠性工程师 ➢ 制造工程师 ➢ 最终服务工程师 ➢ 项目经理 ➢ 质量工程师 ➢ 顾客联系人 ➢ 其他:销售、开发、过程、
QA/QC等。
PFMEA人员构成:
在新品试产期间开始
后制程作业员通过目视/感觉/听觉来检测出问题
本制程作业员通过目视/感觉/听觉来检测出问题点或后制程人 员通过使用检测工具侦测(如:go/no go,治具,手动扭 力记等)
后制程人员通过使用检测工具或者本工站操作员通过使用检测 工具侦测(如:go/no go,治具,手动扭力记等)
本制程作业员通过检测工具或自动测试控制装置能够识别出部 分问题来提醒操作者(如:灯光、喇叭等)检测的手段可以 设定在首件确认侦测
DFMEA的制作和应用.ppt
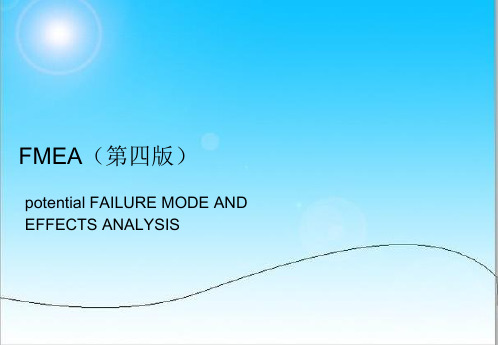
➢ DFMEA 应该包含任何由设计导致的在制造或装配过程中发生的潜在失效模式和要因。 ➢ 那些失效模式可能被设计更改减轻。(如预防零件装配在错误的位置上的设计特性,也即是:防错)。 ➢ 当在DFMEA 分析中不能减轻时(对于这样情况应该记录在措施计划),他们的验证、后果,和控制应该传递到PFMEA 中,PFMEA 应覆盖这些内容。
三、DFMEA
DFMEA的简介
设计失效模式后果分析,也称DFMEA。DFMEA 通过以下几方面降低风险支持设计过程:
➢ 有助于对设计包括功能要求和设计方案在内的设计进行客观评价; ➢ 对制造、装配、服务和回收要求的最初设计进行评价; ➢ 提高在设计/开发过程中,考虑潜在失效模式极其对系统和车辆运行影响的可能性; ➢ 为全面、有效的的设计、开发和项目确认的策划提供更多的信息; ➢ 根据潜在失效模式对“顾客”的影响,对其进行分级列表,进而建立一套设计改进、开发和验证试验/分析的优先系统; ➢ 为建议和跟踪降低风险的措施,提供一个公开的讨论形式; ➢ 为将来阐述售后市场关切情况、评价设计更改及开发先进的设计提供参考(如:学到的经验)。
DFMEA准备
• 建立DFMEA工作小组; • 收集必要的资料
➢ 设计意图 ➢ 车辆要求 ➢ 质量功能展开图 ➢ 已知的产品要求、制造要求、装配要求 ➢ 类似的DFMEA资料
• 准备DFMEA表格
DFMEA的开发
前提条件:
➢ 框(边界)图—(图1) ➢ 参数(P)图— (图2) ➢ 功能要求:一般考虑产品的目的和产品的整体设计意图;安全性;政府法规;可靠性(功能寿命);装载和工作循环:顾客产品使用表;安静操作:噪
DFMEA 不依靠过程控制去克服潜在设计弱点,但它可以考虑对制造和装配采取技术和物理限制,例如:
DFMEA工具培训学习课件

DFMEA与其他可靠性分析工具的比较
其他可靠性分析工具包括故障树分析(FTA)、故障物理(Failure Physics)、环境应力 筛选(ESS)、可靠性增长试验等。
这些工具各有特点和应用范围,例如故障树分析主要用于识别导致系统故障的原因,故障 物理则研究故障的物理机制,环境应力筛选用于筛选出产品中潜在的故障部位,可靠性增 长试验则通过试验数据来评估产品的可靠性水平。
详细描述
在进行可维护性分析时,需要考虑以下几点
• 维护过程分析
分析维护过程中可能出现的故障模式及其影响,从而优化 维护过程。
• 可维护性需求
明确产品或过程的维护需求,包括预防性维护、预测性维 护和修复性维护等。
• 可维护性与可靠性的权衡
在满足可维护性的同时,也要考虑对产品可靠性可能带来 的影响,以取得最佳的平衡。
根据故障模式对产品设计 或制造过程的影响程度, 评估其影响范围和严重性 。
分析故障模式能否被现有 检测方法发现,从而评估 其潜在风险的大小。
常见问题三:如何进行可维护性分析?
总结词
可维护性分析是DFMEA工具中评估产品设计或制造过程 可维护性的关键步骤。
• 可维护性设计
评估产品设计是否便于进行维护,如维修窗口、易于更换 的组件等。
案例三
某医疗诊断设备的DFMEA分析
DFMEA工具在航空航天行业的实战应用案例
01
02
03
案例一
某航空发动机的DFMEA 分析
案例二
某航天飞行器的DFMEA 分析
案例三
某导弹制导系统的 DFMEA分析
THANKS
感谢观看
DFMEA分析的步骤
定义范围和目的
如何做DFMEA(PPT53页)

12
DFMEA
设计FMEA表头
设计职责(C):输入负责设计的OEM、组织、部门或小组;适 用时,输入供应商组织名称。
车型年/项目(D):输入将使用或者受分析的设计影响的预期车型 年和项目(如果知道)。
关键日期(E):输入FMEA最初的预定完成日期,它不能超过 计划的生产设计发布日期。
13
DFMEA
项目、功能和失效模式
系统
发动机 设计目标: 1.功率XXkw; 2.最大输出扭矩; 3.最高转速; …… 功能:
提供充足的动力 潜在失效模式:
动力不足; ……
传动系统
行驶系统
制动系统
转向系统
车身
电器
附件
子系统
点火系 功能:
按照发动机工作循环,在规 定的时刻给火花塞提供足够高 的电压,使火花塞产生火花点燃 混合气,便发动机做功. 潜在失效模式:
26
DFMEA
27
DFMEA
严重度评价理解
➢FMEA小组应对评价准则和分级规则达成一致意见。 ➢组织可对准则进行修改,不推荐修改9和10的准则。 ➢严重度的定级可以通过修改设计、使之补偿来减轻失效
的后果来降低。如:“瘪胎”可以减轻突然爆胎的严重 度,“安全带”可以减轻车辆碰撞的严重程度。
➢“车辆/项目”在用于其他产品时,可理解为“最终产 品/生产产品”。如电视机/显示器、电脑/接线端子等 。
FMEA编号: A 设计职责: C 关键日期: E
页 码: 第1 页 共 1 页 编制人:H FMEA日期(编制):F(修订)
11
DFMEA
设计FMEA表头
表头应清楚的说明FMEA的关注点,以及文件开发和过程控制中的相关 信息。
DFMEA制作方法培训讲解ppt课件

Confidential Information
潜在的失效起因/机理(Potential Cause/Mechansim of Failure)
●典型的失效起因有: 材料选择不当,设计寿命评估不当,应力(强 度)过大,润滑不足,维修保养说明不当,环境 保护不够,计算错误等。
●典型的失效机理有:屈服,疲劳,材料不稳定, 磨损,腐蚀等。
介绍(Recommend)
Confidential Information
● 什么是FMEA?
潜在的失效模式及后果分析(Potential Failure Mode and Effects Analysis,简称FMEA), 是在产品/过程 /服务等的策划设计阶段,对构成产品的子系统、零部件 、对构成过程、服务的各个阶段逐一进行分析,找出潜在 的失效模式,分析其可能的后果,评估其风险。从而预先 采取措施,减少失效模式的严重程度,降低其可能发生的 概率,以有效的提高质量与可靠性,确保顾客满意的系统 化工具。
Confidential Information
3
Future with ZATC
Laboratory affiliated with Shaanxi Zhongke New Energy Co.,Ltd. Zhongke Advanced Technology Center (ZATC)
编写FMEA的目的(purpose)
Confidential Information
●有助于对设计中问题的早期发现,从而避免和 减少后期修改带来的损失,使开发的成本下降。
●有助于在早期考虑可制造性和装配性,利于研发生产协调。 ●有助于设计更有利的控制方法,为制定设计计划,质量控
制计划提供正确的、恰当的根据。 ●通过IATF16949认证必须要有FMEA质量工具。
DFMEA的开发机理
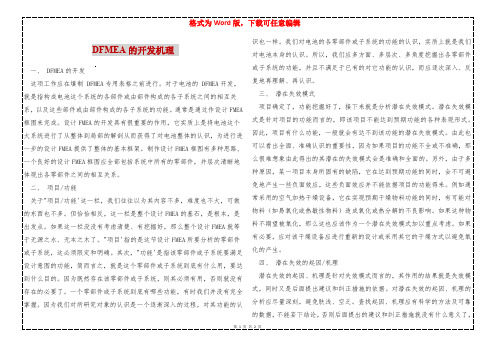
更不要谈有什么改善的效果了。
五、建议措施
当失效模式按RPN值排出次序后,应首先对RPN值最高的和最关键的项目采取纠正措施。
任何建议措施的目的都是为了减少频度、严重度及探测度三者中的任何一个或所有的值。
严重度一般不会发生变化,因为严重度是潜在失效模式发生时对下一个零部件或子系统或顾客影响后果的评价指标,它从侧面反映出被研究的项目在整个系统中的地位及重要程度。
因此,如果要使严重度级别降低,只能通过修改设计来实现。
增加设计确认、验证工作只能减少探测度,不能改变严重度和频度。
要减低频度只能通过修改设计来消除或控制一个或多个失效模式的起因、机理来实现。
因此,一个良好的建议和纠正措施是依据实效起因、机理提出的,旨在克服失效的起因、机理,以避免失效模式的发生,进而更好地实现项目的功能。
同时,一个良好的建议措施,还应综合考虑现有技术水平、成本等因素。
总之,设计FMEA的各部分内容之间紧密联系,有着良好的逻辑关系,必须将这些相互关系理解透,才能做好设计FMEA。
DFMEA-简体版

电动窗不作用、煞车不灵、跳动、乱档、冷却不 够、车辆性能退化, 产生臭气, 外观不良等 。
12) 严重度(S)
严重度是潜在失效模式发生时对下序零件、 子系统、系统或顾客影响后果的严重程度 (列于前一栏中)的评价指标。
严重度仅适用于后果
要减少失效的严重度级别数值,光能通过修 改设计来实现,严重度的评估分为1到10级。
FMEA 的顺序
系统 子系统 零组件: 型号/年份: 核心小组:
设计责任: 生效日期:
FMEA日期(制订)
FMEA 编号:
页次:
OF
准备者:
(修订)
项目
功能
功能 特性 要求
潜在失 潜在失 效模式 效效应
后果是 什么?
严等 重 度级
有多严 重?
会有什么 问题? 。无功能 。部分丧
失功能
。功能 间歇
。非预期 功能
设计或制造过程中应用了FMEA这一分 析方法。但首次正式应用FMEA技术则 是在六十年代中期航天工业的一项革 新。
FMEA的实施
❖由于不断追求产品质量是一个企业不可
推卸的责任,所以应用FMEA技术来识别 并消除潜在隐患有着举足轻重的作用。
❖对车辆回收的研究结果表明,全面实施
FMEA能够避免许多事件的发生 。
部件、子系统或系统时,一个工程师和设 计组的设计思想(其中包括,根据以往的经 验和教训对一些环节的分析) 。
❖这种系统化的方法体现了一个工程师在任
何设计过程中正常经历的思维过程,并使 之规范化、文件化 。
简介
❖ 在设计阶段使用FMEA时,能够用以下方法
降低产品的失效风险
有助于对设计要求的评估及对设计方案的相互 权衡 。