物料催料单
发料、领料、退料

三.退料缴库:
生产工厂为使制造现场生产活动顺利进行,必须妥善拟定发料与领料制度 。然而 使制造现场井然有序,实在有必要将存放在现场里久不用得物料退料缴库,退料缴库 是指由制造现场将多余的物料不良品退回物料仓库管理部门缴库。通常制造现场进行 物料退回缴库的对象包括下列数项:规格不符的物料、超发的物料、不良的物料、呆 料、废料。就一般工厂而言,由于生产计划稳定,物料控制适当且严格,故制造现场 呆料的情形很少发生,因此除超发物料外,其他退回缴库的物料均视为报废品,故处 理上容易很多。但为节约起见,退回缴库的物料不应轻易视为报废品,而必须经过品 管检验,将退回缴库的物料区分为良品、不良品与报废品。其中良品可再用,不良品 退库还厂商,而报废品以残值出售。
一.发料与领料
仓库中村村的物料必须通过发放和零用,制造部门才能进行产品的制造工作。 然而有物料发放和零用,必有物料的退库与缴库,因为物料的发放或领用于物料的 退库与缴库是一体两面。 1.含义与功能:发料是指物料管理部门或仓储单位根据生产计划,将仓库储存的物料直 1.含义与功能:发料是指物料管理部门或仓储单位根据生产计划,将仓库储存的物料直 接向制 造部门的生产现场发放的现象。领料是指制造部门的现场人员在某项产品 制造前,填写领料单向仓库单位领料的现象。就物料管理的有效性而言,发料远比 领料适当,因为发料有下列五项特点: 1)仓库部门能够积极、主动、直接掌握物料。仓库部门根据生管部门开出来的 制造通知单备料发料,只要生管部门生产计划稳定,则仓库发料自然能够顺利,于 是仓库部门对于发料也就能直接掌握。 2)仓库管理较为顺利:仓库部门根据生产计划或制造通知单备料并一次发料, 如此仓储人员工作较顺利,能腾出更多的时间去仓库整理,实施各种仓储管理的改 善措施。 3)促使制造部门加强对用料、损耗、不良的控制:由于仓库部门直接根据制造 通知单一次发料,促使制造部门不得不加强对用料、损耗、不良的控制。若制造现 场由于某项因素造成损耗、不良高于既定标准,那么制造部门势必要前往仓库补料, 否则生产目标无法达成,而由于损耗、不良的增加引起的补料往往需要上级的批准 或提供厂务会议检讨,因为制造部门不得不加强对用料、损耗、不良的控制。 4)有利于成本会计的记账 :既然物料的数据容易掌握,成本会计自然容易记账。 5)有利于生管部门制造日程的安排:既然无聊、用料、损耗、不良易于控制, 生管部门的制造日程安排当然也愈发顺利。
物料控制专员(MC)基础知识问答

物料控制专员(MC)基础知识问答,十六条工作基本常识一、物料控制的精髓是什么?物料控制的精髓是“三不〞,即:1. 不断料、待料:不会让生产线停工等待所必需的物料。
2. 不呆料、滞料:必需要使用、可以使用的物料购进来,不要让不必需要使用、不可以使用的物料进入货仓或呆在货仓不动。
3.不囤料、积料:物料购入要适时,贮存数量要适量,以减少资金的积压。
二、物料的区分方式有哪些?物料通常也称为材料,指用来维持产品制造所必需的原料、零配件等等,一般从以下方式来进行区分:1. 从功能上区分:1)主要材料:为构成制成品的主要部分,如原料、零件等。
2)辅助材料:配合主要材料的加工而附属于在制品上的材料,如包装箱、油漆等。
2. 从形态上区分:1)素材:仍须加工的材料,它又分为料材与粗型材。
2)成型材:已加工之材料,它又分为配件、零件、组合件。
3. 从成本控制上区分:1)直接材料:直接供产品制造的材料,其消耗与产品的产量成正比,一般会记录于材料清册上〔BOM〕。
2)间接材料:指间接帮助产品制造的材料,其消耗不一定与产品的产量成正比,上述辅助材料有时亦包括于间接材料,其他如消耗品、机器维护用的油类等。
4. 从调度方法上区分:1)外部调度的第一次材料:指公司采购的材料与外发加工的材料。
2)内部调度的第二次材料:指规模较大的公司内部部门颇多,由一个部门的材料调度至另一个部门使用。
5. 从准备方法上区分:1)常备材料:依据存量控制原理,定期采购一定数量的材料作为贮备,以供生产必需要。
2)非常备材料:特别材料、不常常使用或使用量少等材料,依据生产计划的必需要来决定是否采购的材料。
三、物控员的工作使命有哪些?物料控制员〔MC〕的工作使命主要有:1. 物料的分析与计算。
2. 物料的请购。
3. 物料进度的跟催。
4. 存量控制。
5. 有关部门之间事务的沟通协调。
四、什么是BOM?BOM〔Bill of Material〕叫做物料清单〔也叫零件结构表、物料表等〕,将产品的原材料、零配件、组合件予以拆解,并将各单项材料依材料编号、名称、规格、基本单位、供应厂商、单机用量、产品损耗率等依制造流程的顺序记录下来,排列为一个清单,这就是物料清单,也就是BOM。
物料管理MRP概念

性
各類依其特性分別決
大 Leverage
strategic 定下列模式: 1.採購模式。
2.物料控管模式。
3.倉庫發料方式。
小 Routine Bottleneck 4.物料扣帳方式。
輕
重
物料重要性
物料屬性及其管理方式
供應商訪談紀錄表
MRP參數的訂定的重要性
MRP參數設定 = 物料管理方式
依據: -物料持有成本v.s.採購成本之平衡 -決定物料的屬性, 設定其管理方式
山米与白鹤
贝特西.贝尔斯
物料管理MRP概念
大綱
物料管理概論 物料管理體系之功能分析 物料管理的實務作業要點 倉儲管理的實務運作要點 物料請採購的方式 MRP概論 新產品開發資材應注意事項 物料的持有成本 v.s. 採購成本 物料屬性及其管理方式 MRP參數的訂定及其重要性
物料 管理
物料管理概論
材料
料是到齊,讓生產線可以順利生產非只關心由資材備料的部份.
6.所有銘牌條碼申請是否ok? 7.ICT測試治具是否ok?未 ok前應如何處理?
新產品開發資材應注意事項
三.MPS/生產排程 1.請業務提供預估,並依據開發進度擺放 MPS,並隨時依據開發進度做修正.
2.由於開發當中會有陸續試作的狀況,會需要由資材備料,所以需與 R&D,業務 協調在量產前備多少量,給試作用. 3.生產需提供新產品的產能資料,以便安排量產時用. 4.IP(R3) 階段產品可以預排在排程中,但未通過 IP(R3)不可正式生產. 5.CA(R4) 階段產品可以上線生產,但要出貨時需經QA認可方可出貨.
96.8.23 說明 負責下採購單的人員編號 暫不用 暫不用 自動 PR 轉 PO 設定催交函的時間 暫不用 暫不用 採購若對同一材料要對兩家供應商同時採購可以建立配額 PO下單的供應商需在 source list 中 暫不用 暫不用 暫不用 0% 0%
单据操作管理规范

1 .目的为规范公司ERP 物料管理类单据的操作,提升公司物料管理能力,特制定本规范。
2 .合用范围本规范合用于公司物料管理类单据的填制、审核、传递等管理。
3.术语与定义无4 .涉及部门及其权责4.1 各物料需求部门:负责领料单据的填制、递交签核和传递。
4.2 各物料入库部门:负责入库单据的填制、递交签核和传递。
4.3 PMC 部:4.3.1 PMC 仓库负责各类物料出入库单据的复核、监督以及借出物品的跟催还回。
4.3.2 PMC 计划负责厂内制令和委外制令的下达、跟进、结案,并不定期进行异常制令的清理工作。
4.4 总经办:负责单据格式的修改、操作权限的设置及监督本规范的执行。
4.5 财务部:负责本规范的监督执行。
5 .单据种类及用途5.1 入库及退货类单据:5.1.1 《进货凭单》:用于外购物料经检验合格后办理入库。
5.1.2 《进货退出单》:用于外购物料入库后因材料质量等问题办理退货。
5.1.3 《厂内入库单》:用于厂内制令完工产品经检验合格后办理入库。
5.1.4 《委外入库单》:用于委外制令完工产品经检验合格办理入库。
5.1.5 《委外退库单》:用于委外制令产品入库后,因质量等问题办理退货。
5.2 领用及退库类单据:5.2.1 《厂内领料单》:用于厂内制令单领取原材料、半成品、客退品等。
5.2.2 《厂内合并领料单》:用于多个厂内制令单合并领取原材料、半成品、客退品等。
5.2.3 《厂内退料单》:用于厂内制令单领取的原材料、半成品、客退品等办理退库。
5.2.4 《厂内超领单》:用于厂内制令单办理原材料、半成品等超额领用。
5.2.5 《料件请领凭单》:用于非生产制令物料领用。
5.2.6 《委外送料单》:用于委外加工制令BOM 用料的发出。
5.2.7 《委外合并领料单》:用于多个委外加工制令BOM 用料的合并发出。
5.2.8 《委外退料单》:用于委外加工制令发料后,经品质确认为我司材料问题,赋予外协厂办理退料。
物料需求

例: X对A的需求
周
1 2 3 45
毛需求 10 量
20 15
Y对A的需求
6 71 2 3 4
25
30 40
独立A需求
5612 20 10 15 15
30 40
10
20 15
25
15
20 10
2020/8/11
2. 物料统管: 库存控制、物料搬运、厂内外运输、外协外包
、利废利材、采购供应、厂内仓库等由一个物料经理统一领 导。
3. 物料编码:唯一性:同一零件不同加工阶段、不同颜色就
是不同零件。编码最大可达15位。6位编码可编号为: 000,000——999,999 , 100万种。
4. 项目主文件: 2020/8/11
1U的数目=1 200 +2V的数目=2 300
=800
2U的数目=2 200=400
2V的数目=2 300=600
一个简单的MRP例子
现在考虑获得上述物料项的时间
假设:T需要1周;U需要2周;V需要2周;W需要3周; X需要1周;Y需要1周。
所有物料何时订货?何时到货?才能满足生 产产品T的需要。
1 主生产计划(MPS):
各种型号产品时段计划 展开的零件时段计划
主生产计划
2. 物料清单(BOM): 根据产品结构而定
BOM
物物料料需需求求计计划划
库存信息
的零件 3。库存信息
结果如何?
N CP
看能力平衡(CP)
Y
2020/8/11
生产计划
采购计划
§10-2 MRP的运算依据(续)
MRP运行所需的信息
2020/8/11
一个简单的MRP例子
采购交期管理规定

采购交期管理制度1.总则1.1制定目的为了确保购用物为之交货期限,使交期管理更为顺畅,特制定本规章.1.2适用范围本公司采购之物料的交期管理,除另有规定外,悉依本规章执行. 1.3权责单位(1)采购部负责本规章制定、修改、废止之起草工作.(2)总经理负责本规章制定、修改、废止之核准.2.交期管理规定3.1确保交期的重要性交期管理是采购的重点之一,确保交期的目的,是必要的时间,提供生产所必需的物料,以保障生产并达成合理生产成本之目标.2.1.1交期延迟的影响交期延迟造成的不良影响有以下方面:(1)导致制造部门断料,从而影响效率.(2)由于物料交期延迟,间接导致成品交期延迟.(3)由于效率受影响,需要增加工作时间,导致制造费用的增加. (4)由于物料交期延误,采取替代品导致成本增加或品质降低. (5)交期延误,导致客户减少或取消订单,从而导致采购物料之囤积和其他损失.(6)交期延误,导致采购、运输、检验之成本增加.(7)断料频繁,易导致互相配合的各部门人员士气受挫.2.1.2交期提前太多的影响交期提前太多也有不良之影响,主要有:(1)导致库存成本之增加.(2)导致流动资金周转率下降.(3)允许交期提前,导致供应商优先生产高单价物料而忽略低单价物料.(4)由于交期经常提前,导致库存囤积、空间不足.(5)交期提前频繁,使供应商对交期的管理松懈,导致下次的延误. 2.2交期延迟的原因2.2.1供应商责任因供应商责任导致交期延误的状况:(1)接单量超过供应商的产能.(2)供应商技术、工艺能力不足.(3)供应商对时间估计错误.(4)供应商生产管理不当.(5)供应商之生产材料出现货源危机.(6)供应商品质管理不当.(7)供应商经营者的顾客服务理念不佳.(8)供应商欠缺交期管理能力.(9)不可抗力原因.10其他因供应商责任所致之情形.2.2.2采购部责任因采购部责任导致交期延误的状况:(1)供应商选定错误.(2)业务手续不完整或耽误.(3)价格决定不合理或勉强.(4)进度掌握与督促不力.(5)经验不足.(6)下单量超过供应商之产能.(7)更换供应商所致.(8)付款条件过于严苛或未能及时付款.(9)缺乏交期管理意识.10其他因采购原因所致的情形.2.2.3其他部门责任因采购以外部门导致交期延误的状况:(1)请购前置时间不足.(2)技术资料不齐备.(3)紧急订货.(4)生产计划变更.(5)设计变更或标准调整.(6)订货数量太少.(7)供应商品质辅导不足.(8)点收、检验等工作延误.(9)请购错误.10其他因本公司人员原因所致的情形.2.2.4沟通不良所致之原因因本公司与供应商双方沟通不良导致交期延误的状况:(1)未能掌握一方或双方的产能变化.(2)指示、联络不确实.(3)技术资料交接不充分.(4)品质标准沟通不一致.(5)单方面确定交期,缺少沟通.(6)首次合作出现偏差.(7)缺乏合理的沟通窗口.(8)未达成交期、单价、付款等问题的共识.(9)交期理解偏差.10其他因双方沟通不良所致的情形.2.3确保交期要点2.3.1事前规划(1)制订合理的购运时间采购部将请购、采购、供应商生产、运输及进料验收等作业所需的时间予以事先规划确定,作为各部门的参照依据.(2)确定交货日期及数量预先明确交期及数量,大订单可采用分批交货方式进行.(3)了解供应商生产设备利用率可以合理分配订单,保证数量、交期、品质的一致性.(4)请供应商提供生产进度计划及交货计划尽早了解供应商之瓶颈与供应能力,便于采取对策.(5)准备替代来源采购人员应尽量多联系其他物料提供来源,以确保应急.2.3.2事中执行(1)提供必要的材料、模具、技术支援给供应商适时了解供应商之瓶颈,协助处理.(2)了解供应商生产效率及进度状况必要时,向供应商施加压力,以获取更多之关照,适时考虑向替代供应商下单之必要性.(3)交期及数量变更的及时联络与通知以确保维护供应商的利益,配合本公司之需求.(4)尽量避免规格变更如果出现技术变更,应立即联系供应商停止原规格生产,并妥善处理遗留问题.(5)加强交货前的稽催工作提醒供应商及时交货.(6)必要的厂商辅导及时安排技术、品管人员对供应商进行指导,必要时可以考虑到供应商处进行验货,以降低因进料检验不合格导致断料发生之情形. 2.3.3事后考核(1)对供应商进行考核评鉴依供应商评鉴办法进行考核,将交期的考核列为重要项目之一,以督促供应商提高交期达成率.(2)对交期延迟的原因进行分析并研拟对策确保重复问题不再发生.(3)检讨是否更换供应商依供应商考核结果与配合度,考虑更换、淘汰交期不佳之供应商,或减少其订单.(4)执行供应商的奖惩办法必要时加重违约的惩罚力度,并对优良厂商予以适当之回馈.4.附件附件GB06-1物料订购跟催表附件GB06-2催料表附件GB06-1物料订购跟催表催料表。
物料管控管理办法
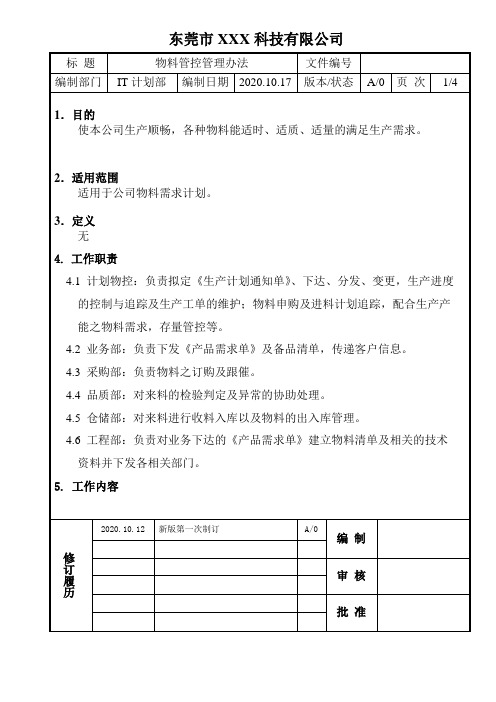
5.5良品入库
5.5.1收物料经IQC检验合格后,由采购账务员进行入账,仓库把物料从
待检转移至良品库进行管理存放。对于进料未及时检验未及时入库的,物、控进行追踪,监督执行。
资料并下发各相关部门。
5. 工作内容
修订履历
2020.10.12
新版第一次制订
A/0
编制
审 核
批 准
东莞市XXX科技有限公司
标题
物料管控管理办法
文件编号
编制部门
IT计划部
编制日期
2020.10.17
版本/状态
页次
2/4
5.1物控需求维护作业
5.1.1物控依据业务下达的《产品需求单》以及备品清单结合工程提供的物料
6.2《IT制造中心生产管理规范》……………IT-PD-C008
7.0 相关记录
7.1《产品需求单》……………………………IT-SD-F001
东莞市XXX科技Βιβλιοθήκη 限公司标题物料管控管理办法
文件编号
编制部门
IT计划部
编制日期
2020.10.17
版本/状态
页次
4/4
7.2《IQC进料检验报告》……………………IT-IQC-F017
关部门。
5.7制程不良
5.7.1订单生产中会出现很多物料制程不良,物控需要及时掌握在线物料的品
质状况,当物料不良率超过一定比率,必须及时通知品质部门以及采购,
做好补料准备。
5.7.2订单生产清尾中,需要制造部在结合仓库库存、客户备品的同时提供准
物料清单BOM
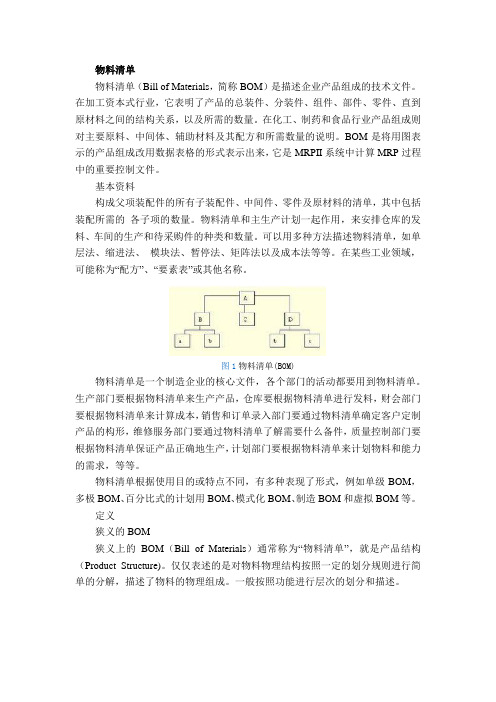
物料清单物料清单(Bill of Materials,简称BOM)是描述企业产品组成的技术文件。
在加工资本式行业,它表明了产品的总装件、分装件、组件、部件、零件、直到原材料之间的结构关系,以及所需的数量。
在化工、制药和食品行业产品组成则对主要原料、中间体、辅助材料及其配方和所需数量的说明。
BOM是将用图表示的产品组成改用数据表格的形式表示出来,它是MRPII系统中计算MRP过程中的重要控制文件。
基本资料构成父项装配件的所有子装配件、中间件、零件及原材料的清单,其中包括装配所需的各子项的数量。
物料清单和主生产计划一起作用,来安排仓库的发料、车间的生产和待采购件的种类和数量。
可以用多种方法描述物料清单,如单层法、缩进法、模块法、暂停法、矩阵法以及成本法等等。
在某些工业领域,可能称为“配方”、“要素表”或其他名称。
图1物料清单(BOM)物料清单是一个制造企业的核心文件,各个部门的活动都要用到物料清单。
生产部门要根据物料清单来生产产品,仓库要根据物料清单进行发料,财会部门要根据物料清单来计算成本,销售和订单录入部门要通过物料清单确定客户定制产品的构形,维修服务部门要通过物料清单了解需要什么备件,质量控制部门要根据物料清单保证产品正确地生产,计划部门要根据物料清单来计划物料和能力的需求,等等。
物料清单根据使用目的或特点不同,有多种表现了形式,例如单级BOM,多极BOM、百分比式的计划用BOM、模式化BOM、制造BOM和虚拟BOM等。
定义狭义的BOM狭义上的BOM(Bill of Materials)通常称为“物料清单”,就是产品结构(Product Structure)。
仅仅表述的是对物料物理结构按照一定的划分规则进行简单的分解,描述了物料的物理组成。
一般按照功能进行层次的划分和描述。
图2时间坐标上的物料清单广义上的BOM是产品结构和工艺流程的结合体,二者不可分割。
离开工艺流程谈产品结构,没有现实意义。
要客观科学的通过BOM来描述某一制造业产品,必须从制造工艺入手,才能准确描述和体现产品的结构。
PMC流程

采购
采购依据物料请购单向供应商下达采购订单
排程工作 责任人 作业流程 查订单库存
生产排程工作流程图
操作叙述 PMC生管接到商务销售订单后安排查看库存是否 足够 库存足通知商务出货,不足则进行生产计划和物 料需求计划 PMC物控跟据订单数量及库存数量计算出满足订 物料需求计算表 单出货的需求数量 相关表单
仓库 1.PMC物控要及时掌握物料流动状况,发 现缺料时,要及时通知采购进行催料; 生产车间
缺料状况表
物料需求 采购催货/下单
PMC物控 采购部 2.了解各车间的用料情况,对其中的不合 理用料采取合理措施,以前少物料的浪费. 仓库
PMC物控了解到缺料信息,计算缺料具体数量,通 知采购对已下未交的订单催,对还没有下单的物 料需求下达采购订单. 采购到货,物料满足需求,物控通知产线领料上 线生产. 生产线领料上线生产,并注意物料使用状况,随 时反映给PMC物控. PMC物控定期对生产线物料消耗状况统计,调整 物料使用标准,规范用料,避免物料浪费. 根据统计情况,调整物料需求计划. 产品BOM表 联络单
生产订单
2.生产车间出现生产材料不足时,应及 时通知PMC物控催料,如客供料未到,就 要通知PMC物控,让PMC物控跟商务沟通, 催客户将材料送来;如是已经下单采购的 物料,则要PMC物控通知采购向供应商催 料.
PMC生管
生产日排表
生产车间
PMC生管要及时向了解各生产部门生产状况,如 发现生产线生产异常,要及时通知上级,作出解 决方案,并通知各部门.
销售订单
1.PMC物控接到生产订单,对产品订单进 行确认;
PMC生管
库存足否 不足 生产计划
PMC生管接到订单后转仓库查库存是否满足出 货,如满足则通知商务出货,如不够则进行生产 计划.
物料管理B纵表格格式

物料管理B纵表格格式 Document number:PBGCG-0857-BTDO-0089-PTT1998五B02 订购单 No.五B07 合同评审表 No.日期:五B08 买卖合同当事人:甲方:乙方:兹为甲方向乙方购下列货品,双方议定各项条件如下:甲 方: 乙 方:负责人: 负责人: 地 址: 地 址:年 月 日 年 月 日五B09 供应商调查表 No.日期:五B10 供应商评估表No.日期:五B11 供应商等级评核表日期:年月日经理:品管主管:制表:说明:1.评比=100-50[(不合格批数/全部检验批数)+(全部不良品样品数/全部样品数)]。
2.不合格批数包括特认批数。
3.评分E:60分以下;D : - 70;C: - 80;B: - 90;A: - 100。
等级E:不合格;D:不甚好;C:平;B:好;A:优良。
4.交货等级A:交货准时;B:交货延迟二天之内;C:交货延迟三至四天;D:交货延迟五至六天;E:交货延迟七天以上。
五B13 采购比较表月份:日期:核准:复核:制表:五B14 采购控制表(A)主管:制表:五B15 单价变动月报表 No.日期:总经理:主管:制表:五B16 特别采用申请书No.申请日期:年月日五B17 物料订购跟催表分类:跟催员:五B18 材料检验报告五B19 损失索赔通知书No.五B20 试制样品试用检验 No. □新开发零件零件名称□设计更改零件编号□新开发厂商厂商名称试用检验意见试用结果:□可用□尚需改进生产单位主管检验结果:□可用□有待改善品管单位主管技术单位主管。
物料管理表格

物料管理表格Document number:PBGCG-0857-BTDO-0089-PTT1998五A10 请购单(A) No.日期:批准人/日期:审核人/日期:请购人/日期:五A10 请购单(B) No.部门:日期:批准/日期;审核/日期:请购:五A12 委外加工申请单 No.日期:批准/日期:审核/日期:制表:五A13 原料耗用分析表 No. 月份: 分析日期:厂长:主管:分析员:说明:1.领料单用量+特别领料单用量=实际用量;2.用来计算直接材料成本。
五A14 物料供应计划(存量订货型用)No.批准/日期:核对:填写:五A01 物料订单订购流程图五A02 物料存货订购示意图存量订购点安全存量时间变动AB CD注: 安全存量=平均一日用量×紧急订购时间五A03 订单订购流程五A04 物料分析表分析日期:分析员:说明:1.依据订单及BOM表分析用料;2.备用率=(进料不良率+工程不良率)×。
五A05 物料表(BOM)No.说明:1.产品开发完成后,即建立BOM表;2.设计(材料)变更时,BOM表须随之变更。
五A06 年度材料耗用预算表年度:说明:1.依据年度销售计划(产品别)预算;2.预算贵重材料耗用便于资金预算。
五A07 呆废料处理申请单No. 申请部门:日期:批准:主管:申请:说明:1.定期就部门内的呆料、废料提出处理;2.原则上每月一次。
五A08 呆废料处理报告No.日期:批准:审核:报告:五A09 ABC 分析法100908070605040302010100908070605040302010%%9%18%53%20%4%11%25%60%项目数% 成本区分 年用金额%项目金额(A)(B)(C)说明:1.使用于物料之重点管理法;2.A料控制资金,C料控制不断料。
五A11 外包申请单 No.日期:五B01 采购程序及准购权限表核准:制表:五B03 材料采购计划 No.日期:批准/日期:审核/日期:编制:五B04 用料订购计划表 No.批示:审核:主管:制表:五B05 采购询价单(A) No.日期:总经理:财会:主管:填单:五B06 询价单(B)台鉴: No. 请将下列各料给予报价,并于年月日前传真或寄交本公司采购部为荷。
物料员工作职责内容

物料员工作职责内容物料员工作职责内容篇11、备料:根据生产计划及生产通知单的货期提前三天开备料单。
2、催欠料:催踪所欠物料并填写《车间欠料报表》。
3、领料:要求每天领回来的物料,根据比例进行抽点,确保数据的准确性。
4、发料:根据车间开出的班组通知单进行发料并记录,保证数据准确。
5、质量:了解物料质量状况信息并及时向主任及MC反馈。
6、易耗品:负责车间易耗品领发工作。
7、报废:每周对报废物料进行监控和处理,汇报当天报废情况。
8、5S:做好物料室5S,物料分类、标示、防护要明确、清晰、到位。
既然是流水线上的物料员,当然是负责线上的所有物料了。
(1)负责生产线的领料,退料,补料及物料的发放工作。
(2)物料的.定期与不定期盘点工作。
(3)各项物料报表的填写与核对。
(4)巡线,当所有的物料及其他相关工作处理完以后,及时回线协助生产或巡线。
(5)做好生产现场的5S工作。
当然,也可根据贵公司的实际情况与安排视物料员的工作而定。
主要有以下几点职责:(1)定期清点车间物料存量。
(2)编制物料申请计划。
(3)按要求、按时间、按数量领取物料进入车间。
(4)对领取得物料进行初步验收。
(5)物料的保管保养。
(6)与物料供应部门交涉生产过程中物料存在的问题。
(7)物料成本核算等。
物料员工作职责内容篇2岗位职责:服从领导安排,遵守公司和仓库各项规章制度。
2、负责仓库日常收、发、存管理工作,努力达成帐、卡、单、物一致,使在库原材料和成品处于良好的品质状态。
3、对照生产领料出库单,按照先进先出原则发料。
4、按照采购入库通知单的数量进行收料5、物料进入仓库管理,库位的筹划与正确合理的摆放。
6、仓库的安全工作和原材料及成品保管工作。
7、每日原材料明细账目的登记和对车间入库成品进行点数。
8、负责盘点库存原材料和成品有较强的吃苦耐劳精神会基本的电脑操作有经验者优先。
物料员工作职责内容篇3职务宗旨:负责产线的物料领退、物料损耗核算及物料管理工作。
物料控制专员(MC)基础知识问答

物料控制专员(MC)基础知识问答,十六条工作基本常识一、物料控制的精髓是什么?物料控制的精髓是“三不”,即:1. 不断料、待料:不会让生产线停工等待所需的物料。
2. 不呆料、滞料:需要使用、可以使用的物料购进来,不要让不需要使用、不可以使用的物料进入货仓或呆在货仓不动。
3.不囤料、积料:物料购入要适时,贮存数量要适量,以减少资金的积压。
二、物料的区分方式有哪些?物料通常也称为材料,指用来维持产品制造所需的原料、零配件等等,一般从以下方式来进行区分:1. 从功能上区分:1)主要材料:为构成制成品的主要部分,如原料、零件等。
2)辅助材料:配合主要材料的加工而附属于在制品上的材料,如包装箱、油漆等。
2. 从形态上区分:1)素材:仍须加工的材料,它又分为料材与粗型材。
2)成型材:已加工之材料,它又分为配件、零件、组合件。
3. 从成本控制上区分:1)直接材料:直接供产品制造的材料,其消耗与产品的产量成正比,一般会记录于材料清册上(BOM)。
2)间接材料:指间接帮助产品制造的材料,其消耗不一定与产品的产量成正比,上述辅助材料有时亦包括于间接材料,其他如消耗品、机器维护用的油类等。
4. 从调度方法上区分:1)外部调度的第一次材料:指公司采购的材料与外发加工的材料。
2)内部调度的第二次材料:指规模较大的公司内部部门颇多,由一个部门的材料调度至另一个部门使用。
5. 从准备方法上区分:1)常备材料:根据存量控制原理,定期采购一定数量的材料作为贮备,以供生产需要。
2)非常备材料:特殊材料、不经常使用或使用量少等材料,根据生产计划的需要来决定是否采购的材料。
三、物控员的工作职责有哪些?物料控制员(MC)的工作职责主要有:1. 物料的分析与计算。
2. 物料的请购。
3. 物料进度的跟催。
4. 存量控制。
5. 有关部门之间事务的沟通协调。
四、什么是BOM?BOM(Bill of Material)叫做物料清单(也叫零件结构表、物料表等),将产品的原材料、零配件、组合件予以拆解,并将各单项材料依材料编号、名称、规格、基本单位、供应厂商、单机用量、产品损耗率等依制造流程的顺序记录下来,排列为一个清单,这就是物料清单,也就是BOM。
生产计划和物料控制程序

生产计划和物料控制程序1.目的:为达成公司目标,满足客户订单交期之需求,合理有效的安排生产,并有效的对物料进行管控,特制定本程序。
2.适用范围适用于本公司所有订单的生产计划和物料控制。
3.权责3.1.市场部:负责订单评审、接单及销售计划的制定。
3.2.PMC:负责制定物料计划,跟催物料按期入库;编排生产计戈U,跟进产成品按期入库。
3.2.1.PC(计划员):负责生产计划的拟定及进度控制。
3.2.2.MC(物控员):负责制定物料需求计划和跟进物料到位的进度。
3.3.生产部:负责生产计划的执行及生产作业的控制。
3.4.采购部:负责物料的采购、跟催。
3.5.工程部:负责产品标准、作业规范等工程资料作业。
4.6.仓库:负责物料的收料、备料、发料等作业。
5.7.品质部:进料、制程、出货的检验及品质异常的判定。
6.定义:无7.内容8.1.订单接收和评审5.1.1.业务部依《订单评审控制程序》,将已核准的客户订单或销售计划单分发至PMC o5.1.2.PMC订单审核和评估:5.1.2.1.PMC对业务每天下达的《进货核对单》的正确性进行审核,MC确认物料要求,PC确认生产要求,如单据不正确或不合理则与业务协商进行修改。
5.1.2.2.物料期确认:确认物料在数量和交期方面是否能满足,如不能满足则组织采购确认最快交期。
出货期确认:PMC人员依据业务订单出货日期、物料交期及工程部制定的产品标准工时,评估产能负荷,确认成品交期等是否能满足。
如不能满足则需组织产能评估!5.1.3. 产能评估:以业务的预测或实际接收的未完成订单为生产目标,由PMC主导,组织采购、生产、工程、业务等各相关部门对产能负荷进行评估,以决定是否进行外发或长期计划即增加人力和设备。
5.1.3.1.产能负荷评估结果为本公司生产能力或机器设备不能满足客户要求时,PMC应下外发加工申请单,审批后由采购部联系外发加工单位进行外发加工,具体操作依《外发加工控制程序》进行。