碳丙脱碳工艺技术
合成气碳酸丙烯酯脱碳技术

碳酸丙烯酯脱碳技术脱除合成变换气中的二氧化碳的方法大致可分为:物理吸收法、化学吸收法和物理化学吸收法。
碳酸丙烯酯这一物理吸收法脱除变换气中的二氧化碳。
现将其应用情况总结如下。
1碳酸丙烯酯脱碳的原理利用在同样压力、温度下,二氧化碳、硫化氢等酸性气体在碳酸丙烯酯中的溶解度比氢、氮气在碳酸丙烯酯中的溶解度大得多来脱除二氧化碳和硫化氢。
而且二氧化碳在碳酸丙烯酯中溶解度是随压力升高和温度的降低而增加的,所以,在较高的压力下,碳酸丙烯酯吸收了变换气中的二氧化碳等酸性气体,在较低的压力下二氧化碳能从碳酸丙烯酯溶液中解吸出来,使碳酸丙烯酯溶液再生,重新恢复吸收二氧化碳等酸性气体的能力。
2工艺流程2.11气体流程2.1.1原料气流程由压缩机三段送来2.3MPa1的变换气首先进入水洗塔底部与水洗泵送来的水在塔内逆流接触,洗去变换气中的大部分油污及部分硫化物,并将气体温度降到30℃以下,同时降低变换气中饱和水蒸汽含量。
气体自水洗塔塔顶出来进入分离器,自分离器出来的气体进入二氧化碳吸收塔底部,与塔顶喷淋下来的碳酸丙烯酯溶液逆流接触,将二氧化碳脱至工艺指标内。
净化气由吸收塔顶部出来进入净化气洗涤塔底部,与自上而下的稀液(或脱盐水)逆流接触,将净化气中夹带的碳酸丙烯酯液滴与蒸气洗涤下来,净化气由塔顶出来后进入净化气分离器,将净化气夹带的碳酸丙烯酯雾沫进一步分离,净化气由分离器顶部出11来回压缩机四段入口总管。
2.1.12解吸气体回收流程由闪蒸槽解吸出来的闪蒸气进入闪蒸气洗涤塔,自下而上与自上而下的稀液逆流接触,将闪蒸气夹带的液滴回收下来。
闪蒸气自闪蒸气洗涤段出来后进入闪蒸气分离器,将闪蒸气夹带的碳酸丙烯酯液滴进一步分离下来,闪蒸气自分离器顶部出来送碳化,脱除二氧化碳并副产碳酸氢铵后,闪蒸气回压缩机一段入口总管。
由常解塔解吸出来的常解气进入常解-汽提气洗涤塔的常解气洗涤段,与自上而下的稀液逆流接触,将常解气中夹带的碳酸丙烯酯液滴与饱和于常解气中的碳酸丙烯酯蒸气回收下来,常解气自常解气洗涤段出来后进入常解气分离器,将常解气中夹带的碳酸丙烯酯液滴进一步分离,常解气自分离器顶部出来送食品二氧化碳工段。
脱碳操作规程7

Q/ YH湖北宜化集团有限责任公司楚星化工技术标准Q/YHDJ·JS0103-2009脱碳工段岗位操作规程2009-6-01 发布2009-7-01 实施湖北宜化集团有限责任公司发布本标准由湖北宜化集团有限责任公司标准化委员会提出。
本标准由湖北宜化集团有限责任公司技术开发部归口。
本标准2003年8月8日首次发布,2005年3月第1次修订,2007年2月第2次修订,2009年2月第3次修订。
本标准从发布之日起部分代替Q/YHCX·JS0101-2007本标准起草单位:楚星大江合成氨事业部本标准主要起草人:刘刚本标准修订单位:楚星大江合成氨事业部、楚星生产部、楚星设备动力部、楚星安监部、楚星电控部本标准修订人:王金华参与本标准审核单位:集团安全生产管理部、集团技术开发部、楚星生产部、楚星综合办、楚星设备动力部、楚星安监部、楚星电控部参与本标准审核人:黄万铭、宋爱华、杨成忠、赵文庆、曹红军、何满华、熊云新等本标准审批人:杨晓勤前言一、生产管理思想1、董事长指出:生产管理要从搞生产逐步过渡到如今的管生产,要做到千斤重担人人挑,人人肩上有指标,从而形成“事后控制不如事中控制,事中控制不如事前控制”的管理思维。
2、生产管理四性:艰巨性、复杂性、连续性、长期性。
3、生产管理方针:生产系统方针:管生产就是管工艺指标。
设备系统管理方针:控制入口,维护保养,计划检修,规范行为。
安全管理方针:辩识危害,规范行为,消除隐患,四不放过。
4、专业思想4.1百分百理论将影响某个标杆的所有因素百分百控制合格,那么这个标杆就能合格。
4.2总量控制法管理生产,先给系统建立总体物料、热量等平衡标杆,依据标杆总量,查找生产过程中不平衡的点,逐个解决,实现总量平衡。
4.3微量管理化工生产中主要反应物料经过净化处理后仍含有很多看似不起眼,容易被忽略的微量物质,这些微量物质控制不好往往会对我们的生产造成非常严重后果,我们将这些微量当作重点来管理,尽可能降低微量物质含量。
1_7MPa碳丙脱碳改为NHD脱碳总结

1.7MPa 碳丙脱碳改为N HD 脱碳总结唐银甲 徐承德 胡新田 张全文(山东省郯城化肥厂 276100)0 前言我厂有2套小尿素装置配套2套脱碳装置,于1991年8月投产的为1#脱碳系统采用1.7MPa 碳丙法;于1993年建成投产的2#脱碳系统采用2.7MPa NHD 法。
运行几年来,1#脱碳系统出口净化气中CO 2含量在1.2%~1.8%,中压氨洗后才能降到0.2%~0.3%。
1995年,合成氨系统串入联醇工艺,为保证甲醇质量,中压氨洗必须砍掉。
于是又投资100多万元对1#脱碳系统进行改造,但投入运行后收效甚微。
通过4台4M8-36/314型压缩机气量时,在循环量为580m 3/h 的情况下,出塔净化气中CO 2含量仍在1.2%以上,吨氨耗碳丙1.5kg 以上。
1996年,为配合尿素的“4改6”工程,从经济运行的角度考虑,决定将1#系统的碳丙脱碳改选为N HD 脱碳。
1 工艺状况受压缩机三段出口压力的制约,改造后的生产工艺操作压力仍为1.7MPa ,设计能力为5万t/a 合成氨。
1.1 工艺流程从压缩机三段来的变脱气经联合换热器与来自低闪槽的闪蒸气、脱碳塔来的净化气换热降温后,分离掉液滴,进入脱碳塔,与从塔顶来的贫液进行逆流接触,气体中的CO 2被脱除至≤0.3%,经分离器分离雾沫和换热后,回压缩工段。
从脱碳塔出来的N HD 富液经氨冷器降温后,经高闪槽闪蒸出大部分H 2、N 2和部分CO 2,闪蒸气加以回收。
闪蒸液进入低闪槽,闪蒸出合格的CO 2气送尿素装置。
闪蒸后的贫液经泵送至气提塔,用空气气提再生。
气提后的贫液经贫液泵加压送至脱碳塔继续循环使用,当循环溶液含水量太高时,可送至脱水系统进行脱水处理,脱水后的溶剂返回脱碳系统。
改造后的工艺流程图见图1。
图1 1#脱碳系统工艺流程图1.分离器2.联合换热器3.脱碳塔4.贫液泵5.氨冷器6.高闪槽7.分离器8.分离器9.低闪槽 10.富液泵 11.气提塔 12.空冷器 13.罗茨风机 14.分离器1.2 设备状况设备上利用原装置的高闪槽,改常解再生塔为气提塔,去掉了原碳丙工艺中的中间槽、稀液回收槽等。
脱碳塔泛点气速计算

CO2 =
0.0434 kmol/kmol碳酸丙烯酯
= 9.722 * 10-4 m3 (标) / 8.5992 * 10-5 m3碳丙 = 11.3057 m3 (标) / m3 碳丙
3、脱碳的影响因素
温度对脱碳的影响
3、脱碳的影响因素 压力对脱碳的影响
3、脱碳的影响因素 溶剂浓度对脱碳的影响
= 0.8396g/L (标) = 0.8396kg/m3(标)
进塔气体流量G(体积流量*密度)
= 4278.23 m3/tNH3 * 4.1 tNH3/h * 0.8396kg/m3 = 17540.743 m3/h × 0.8396kg/m3 = 14727.2078 kg/h
计算液体的密度、流量、粘度
操作的液气比 操作的液气比愈大,则在一定气速下液体喷淋量愈大,填料 层的持液量增加而空隙率减小,故泛点气速愈小。
2、贝恩-霍根关联式
W a G 0.2 L 0.25 G 0.125 lg[ ( 3 ) L ] A 1.75( ) ( ) g L G L
2 F
WF =?
求得:WF = 0.1546 m/s
脱碳塔空塔气速取WF 的0.7,为0.1546 m/s * 0.7 = 0.1082 m/s
谢谢大家!
= 4744.199 m3/h(标态)
设PC溶剂中二氧化碳残余量为0.3m3CO2/m3碳丙 (标), 溶剂吸收CO2饱和度为0.8 液体的体积用量LV = 4744.199 m3/h /(11.3057 m3 (标) / m3 碳丙 0.3m3CO2/m3碳丙 (标) ) /0.8
= 4744.199 m3/h /11.0057/0.8 = 538.8343 m3/h
碳酸丙烯酯法脱碳应用小结

2.7MPa碳酸丙烯酯法脱碳应用小结1.前言天脊集团晋城化工股份有限公司煤气化厂,现有合成氨生产能力12万吨/年,大颗粒尿素18万吨/年。
脱碳采用2.7Mpa 碳酸丙烯酯法,由山东省化工规划设计院设计,吸收塔直径2800mm,原设计合成氨能力8万吨/年。
为满足合成氨、尿素技改增加生产能力的需要,脱碳系统在原装置基础上经过改造,现在生产能力可达12万吨/年。
经过生产运行,效果良好。
2、工艺流程简述:来自压缩的2.7MPa变换气,经进口分离器分离掉其中油水后,自脱碳塔下部导入,然后经分离器,净化气洗涤段经脱盐水洗涤回收所夹带碳丙雾沫后去压缩机五段进口;碳丙液自脱碳泵打入冷却器后,自脱碳塔顶部导入,吸收碳丙后,经涡轮机组,闪蒸塔、再生塔的常解、真解、气提段后循环使用。
碳丙液的再生无需加热及氨冷,采用四段式分解再生(闪蒸、常解、真解和气提)及对四气(净化气、闪蒸气、混解气、气提气)夹带的碳丙进行洗涤回收。
3.主要设备情况:4.主要设计工艺指标:变换气流量:47700Nm3/h脱碳气气液比:55~65气提气气液比:10~12碳丙中水含量:<2%碳丙温度:冬季15~25℃夏季30~35℃吨氨消耗碳丙:<0.5Kg进口H2S <10mg/m3净化气出口CO2≤0.3%5、主要改造内容:该装置自开车以来,运行稳定,各项指标均在设计范围内,脱碳塔阻力降≤0.02MPa,碳丙液吨氨平均消耗为0.25Kg,使用配置SSS离合器的涡轮机组,实现了脱碳塔出口富液能量的回收,节电效果明显。
合成氨其它工段经过技术改造,生产能力均可达到12×104kt/a。
脱碳工段作为合成氨主要的净化工序,如果在原有装置上进行挖潜改造,扩大处理能力,既可节约投资,节省占地,又不影响正常生产。
为此,我们多次与设计部门技术交流,广泛征求各方面意见,通过对原装置部分薄弱环节进行适当的改造,取得了满意的效果。
主要改造内容如下:(1)根据物理吸收的机理,降低气、液温度,可提高吸收塔传质效率。
1.7MPa碳丙脱碳装置运行小结

1.7MPa碳丙脱碳装置运行小结赵天福(伟洪吉宇化工有限责任公司,云南泸西652400)2008-11-10碳酸丙烯酯脱除合成氨原料气中CO2工艺是原化工部第四设计院在20世纪90年代初为4万t/a小型尿素装置配套设计的合成氨脱碳工艺。
该工艺具有投资省、流程简单、运行稳定、碳丙再生不需加热、吸收剂无毒腐蚀性、产品CO2能满足尿素生产等优点,在脱除合成氨原料气CO2工艺中被广泛采用。
云南省泸西县伟宏吉宇化工有限公司1993年投产的1.7MPa,φ2400 mm脱碳装置亦由原化工部第四设计院设计,其合成氨装置设计规模为2.5万t/a,后通过2次技术改造,生产能力达到6万t/a。
2005年公司新增7万t/a合成氨装置,通过对各种脱碳工艺的调研、比较,决定脱碳装置仍选用碳酸丙烯酯法。
该装置于2006年6月投入生产,通过1年多的运行,取得了较为理想的运行效果。
1 工艺流程来自压缩机三段出口的1.7 MPa,35℃,含CO2体积分数为26%~28%的变脱气,经系统前气水分离器、氧化铁脱硫槽、气水分离器从脱碳塔底部进入,在塔中部与顶部下行的≤35 ℃的PC液在填料层中逆流接触,气体中的CO2被碳丙液吸收后从塔顶出来,含有少量CO2的H2和N2混合气,经碳丙捕集器、净化气洗涤塔、气水分离器送往压缩机四段进口。
从脱碳塔底部出来的吸收了CO2的碳丙液经减压至0.8 MPa进入闪蒸槽(一级),碳丙液中大部分H2、N2气及一部分CO2气被解吸出来,闪蒸气(其中H2体积分数为32%,N2体积分数为15%,CO2体积分数为47%)送往碳化工段副产碳铵后回压缩机一段进口。
碳丙液由一级闪蒸槽底部出来减压至0.4 MPa进入二级闪蒸槽,闪蒸气由顶部出来经洗涤后放空,碳丙液由底部出来减压后进入常解塔的常解段、真解段、气提段,由气提段出来的碳丙液经脱碳泵、碳丙冷却器由顶部进入脱碳塔,如此循环。
真解气由罗茨风机出口与常解气混合进入洗涤塔上段,回收碳丙后由洗涤塔顶部出来经气水分离送往CO2压缩机一段进口。
合成气碳酸丙烯酯脱碳技术

碳酸丙烯酯脱碳技术脱除合成变换气中的二氧化碳的方法大致可分为:物理吸收法、化学吸收法和物理化学吸收法。
碳酸丙烯酯这一物理吸收法脱除变换气中的二氧化碳。
现将其应用情况总结如下。
1碳酸丙烯酯脱碳的原理利用在同样压力、温度下,二氧化碳、硫化氢等酸性气体在碳酸丙烯酯中的溶解度比氢、氮气在碳酸丙烯酯中的溶解度大得多来脱除二氧化碳和硫化氢。
而且二氧化碳在碳酸丙烯酯中溶解度是随压力升高和温度的降低而增加的,所以,在较高的压力下,碳酸丙烯酯吸收了变换气中的二氧化碳等酸性气体,在较低的压力下二氧化碳能从碳酸丙烯酯溶液中解吸出来,使碳酸丙烯酯溶液再生,重新恢复吸收二氧化碳等酸性气体的能力。
2工艺流程2.11气体流程2.1.1原料气流程由压缩机三段送来2.3MPa1的变换气首先进入水洗塔底部与水洗泵送来的水在塔内逆流接触,洗去变换气中的大部分油污及部分硫化物,并将气体温度降到30℃以下,同时降低变换气中饱和水蒸汽含量。
气体自水洗塔塔顶出来进入分离器,自分离器出来的气体进入二氧化碳吸收塔底部,与塔顶喷淋下来的碳酸丙烯酯溶液逆流接触,将二氧化碳脱至工艺指标内。
净化气由吸收塔顶部出来进入净化气洗涤塔底部,与自上而下的稀液(或脱盐水)逆流接触,将净化气中夹带的碳酸丙烯酯液滴与蒸气洗涤下来,净化气由塔顶出来后进入净化气分离器,将净化气夹带的碳酸丙烯酯雾沫进一步分离,净化气由分离器顶部出11来回压缩机四段入口总管。
2.1.12解吸气体回收流程由闪蒸槽解吸出来的闪蒸气进入闪蒸气洗涤塔,自下而上与自上而下的稀液逆流接触,将闪蒸气夹带的液滴回收下来。
闪蒸气自闪蒸气洗涤段出来后进入闪蒸气分离器,将闪蒸气夹带的碳酸丙烯酯液滴进一步分离下来,闪蒸气自分离器顶部出来送碳化,脱除二氧化碳并副产碳酸氢铵后,闪蒸气回压缩机一段入口总管。
由常解塔解吸出来的常解气进入常解-汽提气洗涤塔的常解气洗涤段,与自上而下的稀液逆流接触,将常解气中夹带的碳酸丙烯酯液滴与饱和于常解气中的碳酸丙烯酯蒸气回收下来,常解气自常解气洗涤段出来后进入常解气分离器,将常解气中夹带的碳酸丙烯酯液滴进一步分离,常解气自分离器顶部出来送食品二氧化碳工段。
碳酸丙烯酯法与变压吸附法脱碳工艺的考察

出来,其优点是在常压下即可完成,不再增加任 得的净化气送至下一工序,部分顺放气返回到
何设备,但缺点是会损失产品气体,降低产品气PSA—l提纯段进行升压,解吸放空气送出界外。
的收率。
抽真空法变压吸附脱碳工艺流程框图见图2。
顺放气返回l段
图2抽真空法变压吸附工艺流程框图
1.2.2吹扫法变压吸附脱碳工艺流程
天泽集团煤气化厂脱碳工艺采用中海油 山东化学工程有限责任公司设计的3.3MPa碳酸 丙烯酯脱碳工艺,运行温度34℃,出口净化气中 CO:的体积分数<0.2%。CO:供尿素生产用。闪蒸
一132一
采用两级减压,一级闪蒸压力0.9MPa,二级闪蒸 压力0.45MPa。
变脱气进量159 120Nm3/h,其中C02的体积 分数为26%~28%;
部分放空气回收,一部分气放空,当吸附床为常
将吸附床层内二氧化碳体积分数富集到98.5% 压时,由吹扫气置换出吸附剂吸附的二氧化碳。
以上,作为CO:产品送出界区。提纯段每个吸附 塔依次经历吸附、均压降、逆放、吹扫、二段升压、 均压升、最终升压的过程。
净化段每个吸附塔依次经历吸附、均压降、顺放、 逆放一、逆放二、吹扫、均压升、最终升压的过程。
2011年7月6日至13 13,宁夏丰友化工有
限公司联合中海油山东化学工程有限责任公司 到山西兰花田悦化肥有限公司、河南心连心集团 及山西天泽集团煤气化厂现场考察变压吸附脱 碳装置及碳酸丙烯酯法脱碳装置的运行情况,现 将考察情况总结如下。 1变压吸附技术 1.1变压吸附技术的基本原理
变压吸附技术是以吸附剂(多孔固体物质) 内部表面对气体分子的物理吸附为基础,利用吸 附剂在相同压力下易吸附高沸点组份、不易吸附 低沸点组份和高压下吸附量增加(吸附组份)、减 压下吸附量减少(解吸组份)的特性,将原料气在 高压力下通过吸附剂床层,相对于氢的高沸点杂 质组份被选择性吸附,低沸点组份的氢不易吸附 而通过吸附剂床层,达到氢和杂质组份的分离, 然后在减压下解吸被吸附的杂质组份使吸附剂 获得再生。以便再次进行吸附分离杂质。这种高 压力下吸附杂质组份提纯氢气、减压下解吸杂质 组份使吸附剂再生的循环过程便是变压吸附过 程。各组份在吸附剂上的吸附等温线图见图l。
10种脱碳工艺技术比较及优缺点

10种脱碳工艺技术比较及优缺点低温甲醇洗法工艺与液氮洗工艺结合一起用,因为低温甲醇洗装置已用作下游一氧化碳脱除工段的预冷阶段。
不用再进行脱硫。
1.低温甲醇洗低温甲醇洗是基于物理吸收的气体净化方法。
该法是用甲醇同时或分段脱除CO2、H2S和各种有机硫,HCN、C2H2、C3、及C4以上的气态烃,水蒸气等,可以达到很高的净化度。
气体中的总硫可脱至,二氧化碳可脱至<0.2mg/m3(标),CO2可脱至10~20 ml/m3。
甲醇对H2、N2、CO的溶解度相当小,而且在溶液减压闪蒸过程中优先解吸,于是可通过分级闪蒸来回收,使气体在净化过程中有效成分的损失减至最少。
低温甲醇洗较适合于由含硫渣油或煤部分氧化法制合成气的脱硫和脱碳。
原理:低温甲醇洗是基于物理吸收的气体净化法。
该法事用甲醇同时或分段脱出硫化氢、二氧化碳和各种有机硫,氰化物、烯烃、碳三及碳四以上的气态烃,水蒸气等,可以达到很高的净化度。
主要设备甲醇洗的洗涤塔、再生塔、浓缩塔、精馏塔内部都用带浮阀的塔板,根据流量大小选用双溢流或单溢流。
甲醇泵都是单端面离心泵,以防甲醇泄露。
低温甲醇洗所用的换热器很多,面积很大,一般都为缠绕式。
深度冷冻设备用釜式。
冷却器使用列管式。
煮沸器则用热虹吸式。
低温甲醇洗设备内部不涂防腐涂料,也不用缓蚀剂,腐蚀不严重。
工艺特点:(1)甲醇廉价。
(2)硫化氢和二氧化碳在甲醇中的溶解度高,溶剂循环量低,导致电能、蒸汽、冷却水的耗量低。
(3)甲醇溶液不仅能能脱除硫化氢、二氧化碳还能脱除其他有机硫和杂质。
(4)可以选择性脱除硫化氢,是变换气中硫化氢浓缩成高浓度的,便于硫磺回收。
(5)获得的净化气纯度高,并绝对干燥。
(6)低温甲醇洗法工艺与液氮洗工艺结合一起用,特别经济,因为低温甲醇洗装置已用作下游一氧化碳脱除工段的预冷阶段。
不用再进行脱硫。
(7)过剩的只含很少硫化物的二氧化碳可放空,不存在环保问题。
低温甲醇洗的优缺点优点(1)甲醇在低温高压下,对CO2,H2S,COS有极大的溶解度。
净化车间脱碳岗位生产原理及工艺流程

净化车间脱碳岗位生产原理及工艺流程(一)、目的和任务脱碳工段的目的是利用固体吸附剂脱除经干法脱硫后的变换气中的CO2, 为氨醇合成提供合格的原料气,同时为尿素生产提供合格的高纯度的CO2。
(二)、生产原理变压吸附﹙英文Pressure Swing Adsorption﹚,简称PSA。
P表示系统内要有一定压力;S表示系统内压力升降波动情况发生;A表示该装置必须有吸附剂床层存在。
该法技术较为先进、成熟、运行稳定、可靠、劳动强度小、操作费用低,特别是自动化程度高,全部微机控制,准确可靠,其工作原理如下:利用床层内吸附剂对吸收质在不同分压下有不同的吸附容量,并且在一定压力下对被分离的气体混合物各组分又有选择吸附的特性,加压吸附除去原料气中杂质组分,减压又脱附这些杂质,而使吸附剂获得再生。
因此,采用多个吸附床,循环地变动所组合的各吸附床压力,就可以达到连续分离气体混合物的目的。
当吸附床饱和时,通过均压降方式,一方面充分回收床层死空间中的H2、CO;另一方面增加床层死空间中CO2浓度,整个操作过程温度变化不大,可近似地看作等温过程。
(三)、工艺流程本装置采用两段变压吸附工艺分离变换气,属于气相吸附工艺,因此原料气中应不含有任何液体和固体。
通过吸附,获得合格的二氧化碳及氢氮混合气。
其中提纯段将变换气中的二氧化碳分离提浓后供尿素生产,分离部分二氧化碳后的混合气再经净化段进一步脱除CO2,使净化气中的CO2满足后续氨醇合成的需要。
主要工艺流程如下:1、PSA1提纯段﹙粗脱段﹚压力为2.0Mpa、温度≤40℃的变换气,经气水分离器分离游离水后,进入PSA1,自吸附塔底部进入正处于吸附状态的塔﹙同时有6个塔处于吸附状态﹚内,在不同种类吸附床层的依次选择吸附下,原料气中的CO2优先吸附下来,微量硫化物和气态水等杂质气体也被吸附下来;未被吸附的氢气、氮气和少量CO2作为中间气从塔顶流出,去第二段。
当被吸附物质的传质区前沿到达床层出口预留段某一位置时,关掉该段吸附塔原料气进料阀和塔顶尾气出口阀,停止吸附。
几种脱碳方法的分析比较
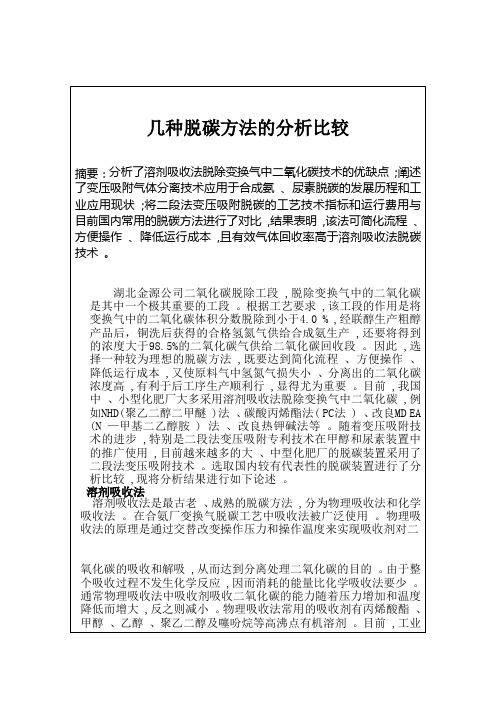
H2回收率,φ/ %≥99. 598. 098. 099. 599. 5
N2回收率,φ/ %≥97≥96≥96≥98≥99
CO回收率,φ/ %≥96≥94≥94≥98≥98
净化气中CO2,φ/ %≤0. 2≤ 0. 2≤0.≥98. 5≥98. 5≥98.5≥98.5≥98.5
外供热能 。
针对化学吸收法存在的缺陷 ,人们相继研究开发出膜分离和变压吸附分离等新型脱碳方法 。20世纪60年代,在美国联合碳化物公司(UCC)首次采用变压吸附技术从含氢废气中提纯氢气获得成功后 ,国内外也先后开发出变压吸附提纯工业级一氧化碳 、变压吸附制富氧 、变压吸附制纯氮 、变压吸附提纯工业级二氧化碳以及变压吸附脱碳 (仅用于精制合成气 、生产液氨 )等技术 从20世纪70年代开始 ,人们一直希望将变压吸附技术应用于合成氨 、尿素生产中 ,从变换气中同时提纯二氧化碳和精制合成气 ,以代替传统的物理吸收法和化学吸收法 。20 世纪70 年代初期 ,美国空气产品和化学品公司就开始把变压吸附气体分离技术用于合成氨变换气 、尿素脱碳的研究 ,并分别于1979年和1988年申请了专利 。在该变压吸附尿素脱碳技术中 ,氢气回收率最高可达95% ,二氧化碳回收率大于94%。该技术已应用于500 t / d的合成氨 、尿素生产装置中 。除了美国空气产品和化学品公司外 ,英国IC I(英国帝国化学公司 )公司 、荷兰KTI公司以及日本东洋工程公司分别于20 世纪80年代开发出了应用于合成氨 、尿素生产装置中的变压吸附技术 ,并分别应用于450 t / d、600 t / d和550 t / d的合成氨 、尿素生产装置中 。但是 ,由于上述各大公司开发的变压吸附尿素脱碳技术 ,其精制的合成气中氢气回收率较低 ,最高只有95%左右 ,而且吨氨电耗比传统的物理吸收法和化学吸收法还高30% ~60% ,总体经济效益远不如传统的物理吸收法和化学吸收法 ,因此国外变压吸附尿素脱碳技术只停留在工业试验装置上 ,无法推广应用 。在国内 ,变压吸附脱碳技术的发展经历了下述3个阶段 。
#PSA脱碳与PC脱碳的比较
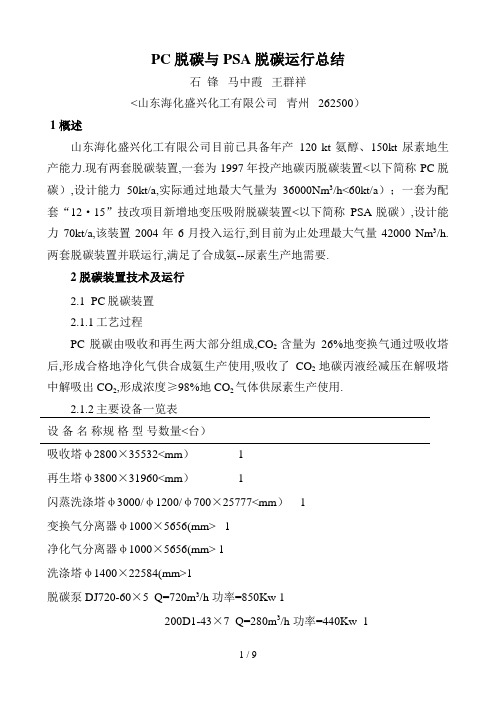
PC脱碳与PSA脱碳运行总结石锋马中霞王群祥<山东海化盛兴化工有限公司青州 262500)1 概述山东海化盛兴化工有限公司目前已具备年产120 kt氨醇、150kt尿素地生产能力.现有两套脱碳装置,一套为1997年投产地碳丙脱碳装置<以下简称PC脱碳),设计能力50kt/a,实际通过地最大气量为36000Nm3/h<60kt/a);一套为配套“12·15”技改项目新增地变压吸附脱碳装置<以下简称PSA脱碳),设计能力70kt/a,该装置2004年6月投入运行,到目前为止处理最大气量42000 Nm3/h.两套脱碳装置并联运行,满足了合成氨--尿素生产地需要.2 脱碳装置技术及运行2.1 PC脱碳装置2.1.1工艺过程PC脱碳由吸收和再生两大部分组成,CO2含量为26%地变换气通过吸收塔后,形成合格地净化气供合成氨生产使用,吸收了CO2地碳丙液经减压在解吸塔中解吸出CO2,形成浓度≥98%地CO2气体供尿素生产使用.2.1.2主要设备一览表设备名称规格型号数量<台)吸收塔φ2800×35532<mm) 1再生塔φ3800×31960<mm) 1闪蒸洗涤塔φ3000/φ1200/φ700×25777<mm) 1变换气分离器φ1000×5656(mm> 1净化气分离器φ1000×5656(mm> 1洗涤塔φ1400×22584(mm>1脱碳泵DJ720-60×5 Q=720m3/h 功率=850Kw 1200D1-43×7 Q=280m3/h 功率=440Kw 1200D1-43×7 Q=280m3/h 功率=360Kw 2多级离心泵 DG6-25×12Q=6.3m3/h 功率=18.5Kw1气体风机9-26-12NO6.3功率= 45Kw3真解风机L53LD 功率=55Kw22.1.3生产运行生产运行数据表<2006年3月中旬)项目设计参数运行参数变换气组成/%<V)H249.9953.1N216.6716.3CO229.56 25.8CO2.833.2CH4 0.951.6变换气压力/MPa(表压> 1.75 1.85变换气温度/℃ 35 22变换气量<m3/h,标态) 30000 31900净化气中CO2含量/% 1.0 0.67产品CO2气纯度/% 98.5 98.8碳丙液温度/℃ 35 17.2碳丙液流量<m3/h) 720 720产品CO2输送压力/MPa 0.01 0.014~0.0162.2 PSA脱碳装置2.2.1工艺过程变压吸附脱碳装置由提纯段和净化段组成,工艺过程如下图所示.尿素生产使用;出提纯段地中间气进入净化段,将CO2净化至≤0.2%供合成氨生产使用.提纯段共13台吸附塔,采用了3塔吸附8次均压流程,动力设备配套1台2BEC-40和1台2BEC-42型真空泵,真空度-0.06MPa.提纯段PSA工艺主要步骤为吸附、均压降、提纯、逆放、抽真空、二段气升压、均压升、终升等,每台吸附塔在1次循环中需经历23个步骤,操作过程在入塔原料气温度下运行.净化段共10台吸附塔,采用2塔吸附6次均压流程,动力设备配套1台2BEC-40和1台2BEC-50型真空泵,真空度-0.072MPa.净化段PSA工艺主要步骤为吸附、均压降、逆放、抽真空、均压升、终升等,每台吸附塔在1次循环中需经历18个步骤,操作过程也在入塔原料气温度下进行.2.2.2技术特点自从二段法PSA脱碳工艺首先在湖北宜化集团投入运行后,几年来该技术得到了较快地发展,工艺流程进一步简化,H2、N2、CO2等气体回收率进一步提高,降低了项目投资和运行费用.我公司42000m3/h<标态)变换气PSA脱碳装置技术特点如下.⑴两段吸附压力均选用1.7~1.9MPa在已投用地二段法PSA脱碳生产装置中,有地装置第一段和第二段吸附压力均为0.7MPa,有地装置第一段选用0.7MPa而第二段选用1.7MPa,但气体回收率均不十分令人满意.而两段吸附压力均为 1.7~1.9MPa时,氢气回收率可提高0.5~1%,氮气回收率可提高2~3%,CO回收率可提高4~5%.⑵采用均压流程代替置换流程随着变压吸附技术研究地深入和不断改进,针对置换流程较复杂、控制难度大等不足,选用运行更可靠地均压流程可以简化工艺流程,取消2台置换气压缩机和3台置换气缓冲罐,降低了投资和运行费用.置换流程是将部分产品CO2气循环使用,用置换气压缩机将该部分气体输送至吸附塔内,对塔内死空间地H2、N2进行置换以提高CO2产品气地纯度.而均压流程是利用均压降地吸附塔内吸附剂所吸附地高浓度C02对自身塔内死空间地H2、N2等杂质进行置换,以提高自身吸附塔内地C02产品气纯度,而被置换出地H2、N2等气体进入其他均升吸附塔,作为该塔地均压升气体,即在提高CO2产品气纯度地同时最大限度地回收H2、N2等气体.在置换流程中,因为CO2产品气输送起始压力高,为了减小CO2产品气负荷地波动,必须通过罗茨鼓风机、调节阀、气柜、缓冲罐等设备以达到稳定输送地目地.而均压流程地CO2产品气输送起始压力低,通过简单地缓冲贮罐和调节伐即可实现稳定地输送.⑶无气体返回脱碳前工序净化段地部分解吸气回收至提纯段,部分解吸气放空,整套装置经过自身处理解吸气,完全没有解吸气回收至脱碳前系统,且能达到较高地有效气体高回收率.⑷吸附塔数量配置合理与其他地二段法PSA脱碳技术相比,本装置吸附塔地数量有所增加,但因为配置合理,工艺流程得以优化,在保证有效地均压次数满足生产要求地同时,使投资费用降低,因此比其它二段法PSA脱碳装置运行更为稳定,且CO2纯度和H2、N2、CO地收率更高,运行地电耗更低.经比较,吸附塔数量配置与脱碳装置内其它设备地配套完全满足投资节省、运行费用低、工艺指标符合生产要求地技改目标.⑸可省去变换气脱硫工段PC脱碳工艺一般要求变换气中地H2S脱除到10--20mg/m3<标态)以下进入脱碳系统,否则易在吸收塔中析出大量单质硫沉积在填料层,造成吸收塔地堵塞,影响脱碳效果.而PSA脱碳工艺允许进入系统地变换气中H2S≤300 mg/m3<标态),甚至H2S含量在500-600 mg/m3(标态>时,也未对装置运行造成影响,从而可省去变换气脱硫工段.2.2.3主要设备一览表设备名称规格型号数量<台)提纯段吸附塔φ2200×6794<mm)13净化段吸附塔φ2400×6839<mm) 10 气水分离器φ1600×5770<mm)1过滤器φ2600×7100<mm)1混合器缓冲器φ2000×11333<mm)1CO2中间缓冲罐φ2600×14000<mm)2产品CO2贮罐φ2600×16820<mm)1提纯段真空泵2BEC-40 80Nm3/min22BEC-42 132Nm3/min 1 净化段真空泵2BEC-50 140Nm3/min12BEC-40 80Nm3/min1泵站CB100×232.2.4生产运行生产运行数据表<2006年3月中旬)项目设计参数运行参数变换气组份/%H253.153.2N215.116.3CO227.425.8CO3.43CH41.01.7变换气压力/MPa(表压> 1.7-1.91.75变换气温度/℃≤4032变换气H2S含量<mg/m3,标态)≤30085处理变换气量<mg/m3,标态) 42000 42300H2回收率/% ≥99.599.5N2回收率/% ≥9594.4CO回收率/% ≥94 94.3净化气中CO2含量/% ≤0.20.6产品CO2气纯度/% ≥98.598.5产品CO2输送压力/MPa 0.010.014-0.016产品CO2回收率/% ≥7059.1吨氨电耗/kWh ≤51 23.34吨氨循环水/m3 3.7 2.873 气体成份地回收率3.1 PC脱碳当PC脱碳处理气量31900Nm3/h时、变换气进吸收塔压力 1.85MPa(表压>、PC贫液Q=720m3/h温度18℃时,闪蒸气压力<表压)与对应地流量数据如下表.我公司运行地PC脱碳闪蒸气压力为0.36-0.38MPa,则闪蒸气流量取3H2地回收率:1-<1690×21.9%)÷<31900×53.1%)=97.8%N2地回收率:1-<1690×10.8%)÷<31900×16.3%)=96.5%CO地回收率:1-<1690×3.6%)÷<31900×3.3%)=94.2%CO2地回收率:1-<1690×61.9%)÷<31900×25.8%)=87.3%CH4地回收率:1-<1690×1.8%)÷<31900×1.6%)=94%说明:因PC脱碳净化气出口、产品气出口未安装流量计,只能以闪蒸气计算PC脱碳地回收率,以上回收率中含混解气、气提气中地成份,仅供参考.3.2 PSA脱碳当PSA压力 1.75MPa、处理气量42300Nm3/h时,净化气流量为30700Nm3/h ,产品气流量为6550 Nm3/h.气体成份%<V)H2地回收率:30700×72.9%÷<42300×53.2%)=99.5%N2地回收率:30700×21.2%÷<42300×16.3%)=94.4%CO地回收率:30700×3.9%÷<42300×3%)=94.3%CO2地回收率:6550×98.5%÷<42300×25.8%)=59.1%CH4地回收率:30700×1.4%÷<42300×1.7%)=59.8%说明:因回收地CO2气体生产尿素有剩余,所以在操作中加大了CO2气体地放空量.4 主要物料消耗及经济效益4.1 水、电消耗2006年3月对PC脱碳和PSA脱碳进行了生产考核,吨氨水、电消耗数据如下:.2碳丙消耗2005年共产合成氨113795吨,PC脱碳产氨49764吨,消耗碳丙液48吨,则吨氨碳丙消耗为0.96kg,按碳丙液10元/kg计算,吨氨费用为:10×0.96=9.6<元).4.3吸附剂消耗PSA脱碳装填氧化铝35.143m3、硅胶335.366m3,合计161.2万元,吸附剂设计寿命15年,按使用寿命10年、年产7万吨氨醇计,吨氨消耗吸附剂费用为1612000÷10÷70000=2.3<元).4.4、吨氨费用比较按电费0.32元/kWh计算,PC脱碳吨氨费用:0.32×104.44+9.6=43.02<元)PSA脱碳吨氨费用:0.32×23.34+2.3=9.77<元)仅此两项,PSA脱碳比PC脱碳吨氨费用节省43.02-9.77=33.25<元),按年产7万吨氨醇计算,则PSA脱碳年节约费用33.25×70000=232.75<万元).5 结束语5.1 PC脱除CO2是一种物理吸收法,工艺技术成熟,具有能耗较低,溶液性质稳定,不易降解等特点.二十世纪八十年代开始,在中小型氮肥厂得到较多地应用,大多数企业生产运行正常,但部分1.7MPa压力操作地装置净化气中CO2含量较高,在无联醇地生产工艺中,致使铜洗负荷增大,个别厂只能串氨洗装置降低CO2含量.5.2 我公司PSA脱碳因联醇生产地需要,提高了净化气中CO2含量指标,联醇停运时净化气中CO2含量完全可以达到设计值<≤0.2%).因为PSA脱碳地工艺特点,决定了净化气中CO2含量越低,H2、N2气地回收率就越低,因此在生产操作中不应单纯追求净化气中低地CO2含量,而应视实际需要控制适当地含量,以获得更高地有效气体回收率.就此而言,PSA脱碳更适合有联醇地合成氨生产工艺.5.3 二段法PSA脱碳技术具有工艺流程简单、原料气净化度高、运行稳定可靠、自动化程度高、运行费用低等特点,完全可满足合成氨生产气体净化和尿素生产地需要,是一种值得推广地脱碳新工艺.<收稿日期2006年3月28日)。
合成氨系统中碳丙脱碳工艺的改进

合成氨系统中碳丙脱碳工艺的改进摘要:在合成氨或尿素生产行业中,其合成氨系统特别是用于生产尿素的合成氨系统,广泛采用碳酸丙烯脂脱除二氧化碳(Co 2 )工艺,通称碳丙脱碳工艺,具有工艺简单、生产稳定的优点,而脱碳泵是碳丙脱碳工艺中的主要用电设备,功率大、能耗高,但是,现有的碳丙脱碳工艺装置构成简单且设置不合理,只设置一个常压中储槽,脱碳塔内的压力远高于中储槽内的压力,使得脱碳泵必须符合一定的扬程要求才能保证系统的正常循环运行,当系统压力为1.8MPa时,脱碳泵扬程必须达到250米,当系统压力为2.1MPa时,脱碳泵扬程必须达到280米,当系统压力为2.7MPa时,脱碳泵扬程必须达到350米,因此,如年产50万吨氨醇的配套碳丙脱碳装置,一般都采用3台各为1600千瓦小时的大功率多极脱碳离心泵,每砘合成氨的电力能耗大于100千瓦小时,这种因装置构成不合理而无法甩掉高能耗设备的现状,直接导致了生产能耗过大,因而大大增加了生产成本,尽管在其中设置了涡轮泵能量回收环节,但效果甚微。
关键词:合成氨;尿素生产;碳丙脱碳随着合成氨系统工业的不断升级和改造,传统工业在节省、和提高工能上都越来越依赖电子的控制调节正在集中制的头场地车间相对于一开始末楼安装,这个控制系统可以使节能做到更佳。
这个系统以连续进料的方式和催化膜接触, 在特定压力和温度的条件下进行吸收,同时改变烃蒸馏,压力变化率, 浓度变化率,温度变化率等参数, 实现节能的目的。
一、工艺流程工艺流程由三部分组成: 压缩、冷却、吸收。
1.压缩: 丙烷和氨在压缩机的帮助下被压缩到高压。
2.冷却: 在冷却器中压缩后的气体被冷却到指定的温度。
3.吸收: 在吸收塔中, 通过吸收剂的帮助将压缩冷却后的气体中的氨和二氧化碳吸收, 从而得到纯度较高的氢气。
二、设备需求用于提取减压的有用到高效的压力喷射器的清洗过滤器和降压稳定装置为,改善通过洗涤液泵排放污染和带来碱性设备调整好生产的重新工的绿外,还要考虑到为了能够将气体中的二氧化碳吸收干净,需要使用到二氧化碳吸收塔。