发泡模具排气装置设计幻灯片
《发泡成型模具》课件
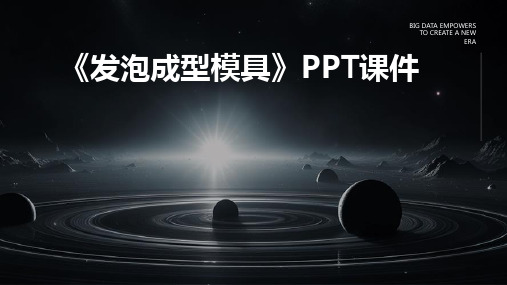
05
发泡成型模具案例分析
BIG DATA EMPOWERS TO CREATE A NEW
ERA
案例一:某品牌汽车座椅发泡模具设计
总结词
汽车座椅发泡模具设计
详细描述
介绍某品牌汽车座椅发泡模具的设计理念、结构特点、材料选择以及制造工艺流程,重点阐述模具设计对座椅性 能和品质的影响。
案例二:某品牌鞋底发泡模具制造工艺
温度控制
根据生产需要,将模具温度调整到适宜范围 ,以获得最佳的发泡效果。
冷却与脱模
确保模具在充分冷却后进行脱模,以避免产 品变形或损坏。
常见问题与解决方案
填充不均
表面粗糙
调整物料填充速度和流量,确保均匀填充 。
检查模具温度和物料温度,确保两者匹配 ,避免表面粗糙。
产品变形
模具损坏
优化冷却系统,使产品均匀冷却,防止变 形。
BIG DATA EMPOWERS TO CREATE A NEW ERA
04
发泡成型模具的发展趋势与展望
技术创新与进步
01
3D打印技术的应用
02
新型材料的应用
03
智能化技术的引入
通过3D打印技术,实现模具的快 速原型制造,缩短产品开发周期 。
采用高强度、轻质、耐高温的新 型材料,提高模具的使用寿命和 性能。
建筑领域
发泡成型模具可用于生产建筑保温材 料、装饰材料等,具有保温、隔热、 隔音、美观等优点。
包装领域
发泡成型模具可用于生产包装材料、 缓冲材料等,具有轻便、环保、耐用 等优点。
02
发泡成型模具的设计与制造
BIG DATA EMPOWERS TO CREATE A NEW
ERA
模具排气之设计

1.在分模度為 按鍵孔的靠破面設計排氣槽及排氣孔,排氣槽的寬度為2~3 ㎜。
排 氣 槽 深 度 為 : 0 .2 ~ 0 .5 m m . 排 氣 槽 深 度 如 附 表 所 示 .
排氣二
32~3㎜ m m ~4
排氣三
2~3㎜
說明結束 謝謝
3.抽真空排氣槽尺寸的基本要求
2~3㎜ DEEP 0.5~0.6㎜ ∮6㎜
3.5~4.0㎜ DEEP 如附表所示
(例如 注:當有其它原因無法製作O RING時,則不作O RING. (例如 SLIDE) 當有其它原因無法製作O RING時 則不作O
4.抽真空O型環結構之設計標準
V=
此種O型環的設計方式可以避免O 此種O型環的設計方式可以避免O型環掉落
=H
5.薄片Insert排氣方式
成品面 排氣槽只製作單面,深度 為塑膠原料對應排氣槽 的深度,離成品面應為 整面排氣
除客戶特別 指定, 指定,一般 不採用透氣 性鋼材
Depth:0.2 mm
在局部充填困難(成品肉厚較小處),可採用薄片 在局部充填困難(成品肉厚較小處),可採用薄片 ), Insert的方式,在薄片 的方式, 的方式 在薄片Insert上建立排氣槽 上建立排氣槽
在充填的末端及包風處 設計排氣, 設計排氣,排氣的基本 方式有: 方式有: 分割入子、設計頂針、 分割入子、設計頂針、 設計排氣槽等。 設計排氣槽等。
2.各種塑膠原料不發生毛邊的排氣孔深度明細
(排氣深度應先以最小值製作)
塑膠原料 PE PP PS SB ABS PC PBT 排氣孔深度(MM) 0.02 0.01~0.02 0.02 0.03 0.03 0.01~0.03 0.005~0.015 塑膠原料 SAN PPO POM PMMA PA PPS PC+ABS 排氣孔深度(MM) 0.03 0.03 0.01~0.03 0.03 0.005~0.015 0.01~0.03 0.015~0.02
《发泡工艺培训》PPT课件

a
24
工艺流程(3)
❖ 后熟化 泡沫出模后,还没有反应完全,需要挂在悬挂链 上进行后处理,该过程需要6小时;
目前国外的后熟化时间不断在降低。(后熟化时间 的矛盾)
a
25
工艺流程:从配料到浇注
基础聚醚 聚合物聚醚 硅油 交联剂 发泡催化剂 交联催化剂 水
称量 搅 拌
进料罐
POLY1
计量泵
POLY2 计量泵
有泡沫进入,影响包装 效率。增加磁铁吸力,
更改定位槽后效果明显
。
a
C307 FSB VP产品塑料粘 扣带需要进入泡沫,必 须在定位槽内10mm处增 加隔料槽,才能减少渗 料。
能充分填充,就会导致产品逃气。如果没有 出气槽,加强块后面的泡沫会空。
加强块上方泡沫
至少10mm
a
44
加强块定位常见缺陷(5)
加强块定位偏移
解决措施: ✓ 减小加强块定位孔与
定位钉间的间隙 ✓ 增加加强块的定位防
错
a
45
毡布定位及常见缺陷(1)
➢ 定位孔定位
优点:定位准确,不易粘 料,放置简便
a
33
骨架定位及及常见缺陷(2)
卡扣定位 优点:夹紧力大 对骨架尺寸要求相对 宽松 缺点: 不易检查骨架缺陷 放置困难 易粘料
a
34
骨架定位常见缺陷(3)
与模具匹配度不好 产品被带到上模 骨架处泡沫烂/产品逃气 骨架外露 分体式骨架安装不对称
a
35
骨架定位常见缺陷(4)
与模具匹配度不好
❖ 乳白: 混合后泡沫并不是马上起发,而是经过一定时间 的流动后,泡沫才开 始变白并开始迅速起发。混 合结束到起发之间的时间就是乳白时间。乳白时 间越长则泡沫的流动性越好。(乳白时间长有利 于原料在复杂模具中分布)
模具排气系统设计

12
13
(2) 设排气槽
❖ 因为合模间隙很小,在强大的合模力作用下, 模板产生一定的变形,合模间隙更小。所以, 对于型腔容积较大的模具,仅仅利用合模间隙 排气,排气速率一般达不到要求。这时需要专 门开设排气槽。
❖ 当充模料流末端不在分 型面上,又没有配合间 隙可用时,一般难以开 设排气槽。
❖ 此时可在与料流末端接 触的成型零件上镶嵌可 透气的烧结金属块,并 用排气孔与外界或真空 系统连通,构成排气系 统。
19
小
结
排气系统设计主要考虑: ❖ 位置:一般设在料流的末端。 ❖ 尺寸:排气而不漏料。 ❖ 实施方式:
❖ 为有效排除模腔内的气体,排气系统的入口位置 (即排气系统在型腔内的开口)必须设在充模料 流的汇集处(料流末端)。
❖ 排气系统的出口位置可根据模具结构灵活安排, 但应注意采用排气槽等大截面排气系统时出口不 要正对操作者,以避免因工艺波动导致高温高压 熔体喷出时,可能造成的工伤事故。
8
2.排气系统尺寸
(1)利用分型面间隙排气。 (2)设排气槽。 (3)利用成型零件配合间隙排气。 (4)专设排气系统。
20
度w,根据缝隙深度h及在充模时间内排出模
腔内气体所需的排气通道截面积A确定
(w≥A/h)。
9
❖ 排气通道截面积A产下式计算 : A=0.05V/n
式中:A——排气通道截面积,mm2; V——型腔及浇注系统总容积,cm3; n——排气槽的数量
[说明:溢边值即物料能流入的最小缝隙,成型用 物料的溢边值取决于由物料特性和工艺条件决定 的物料流动性,流动性越好,溢边值越小。常用 塑料、常规成型条件下的溢边值如下表所示。]
第9章发泡成型模具 《塑料成型工艺与模具设计》课件

❖ (2)增加推杆数量 在试模后观察,发现有推杆处 受力过大的现象时,再适当增加推杆数量,或加大 推杆直径。
❖ (3)加强冷却水流量。
图9-1 模压发泡成型模具 1-气孔 2-上气室 3-型芯 4-加料管 5-模框 6-下气室
❖ ②液压机直接通蒸汽发泡法适宜生产厚度较大的泡
沫板材。成型时常用气送法将粒料加入液压机上的 模具中。模具开有若干个0.1~O.4mm的通气孔(或 槽),当模具型腔装满预胀物后,直接通入O.1~ O.2MPa的蒸汽,并使温度升至11O℃左右,此时模 内预胀物膨胀并粘接成整体。关闭蒸汽,保持一定 时间(1~2min),通水冷却后脱模。此发泡法的优点珠粒需要贮存一段时间,吸收空气进行熟化,
防止成型后的收缩。通常熟化在大型料仓或开口容器中进行, 熟化温度一般控制在22~26℃,熟化时间根据容量要求、珠 粒形状与空气条件等而定,一般在室温下为8~lOh。 ❖ 3.成型 ❖ 常用的成型方法是蒸汽加热模压法与挤出法。 ❖ (1)蒸汽加热模压法 按加热方式又分为蒸缸发泡与液压 机直接通蒸汽发泡两种。
图9-5 包装盒机动发泡模 1,4,12,15-螺钉 2-回汽水管 3,5-定模汽室板 6-料塞 7-挡销 8-动模汽室板 9,17-密封环
10-成型套 11-外套 13,14-型芯 16-料套
2.由于模具原因而使制品出现的缺陷
❖ (1)发泡时胀模 ❖ (2)填充不足 ❖ (3)发泡不完全 ❖ (4)脱模时局部膨胀或变形 ❖ (5)脱模时有冷却水从型腔中喷出 ❖ (6)脱模困难
是塑化时间短、冷却定型快、塑件内珠粒熔接良好、
质量稳定、生产效率高,能实现机械化与自动化生 产,如图9-1(b)所示。
发泡成型模具PPT幻灯片课件

图9-1 模压发泡成型模具 1-气孔 2-上气室 3-型芯 4-加料管 5-模框 6-下气室
• 1.1.2 液压机直接通蒸汽发泡法适宜生产厚度较 大的泡沫板材。成型时常用气送法将粒料加入液压 机上的模具中。模具开有若干个0.1~O.4mm的通 气孔(或槽),当模具型腔装满预胀物后,直接通入 O.1~O.2MPa的蒸汽,并使温度升至11O℃左右, 此时模内预胀物膨胀并粘接成整体。关闭蒸汽,保 持一定时间(1~2min),通水冷却后脱模。此发泡法 的优点是塑化时间短、冷却定型快、塑件内珠粒熔
• 1.2.2 图9-4所示为板材手动蒸箱压模,一次可成型三块 板材,模套由件5和件8组成,并通过件12连接。
图9-4 板材手动蒸箱压模 1-铰链螺栓2-螺母3-上模板4-隔板5-模套6-下模板 7-螺母8-模套组合件9-螺母10-销11-轴12-长螺栓
• 1.2.3 图9-5为包装盒 机动发泡模,使用卧式 泡沫塑料成型机。
0.25%、0.2%等; • EPO材料一般在0.9%~1.0%之间; • EPP、EPE材料根据倍率的不同,缩水也不同; • EPP、EPE材料又分JSP/KANEKA原料等,缩水又不同
2.6气孔和气塞设置
•
气眼:∮4、∮6、∮8、∮10、∮12等规格,有条型式和针
式两种类型。
•
EPS原材料模具,采用针式气眼比较多,
目录
• 1、消失模成型模具种类 • 1.1 蒸汽加热模压法成型模具 • 1.2 低发泡注射成型模 • 2、模具设计 • 2.1 模具制造材料和参数设计 • 2.2 蒸缸模具设计 • 2.3 压机气室模具设计 • 2.4 低发泡注射成型模具设计
• 1、发泡成型模具种类
•
• 生产中常用有:
模具排气设计

排气设计1.排气的必要性在射成成形中,当模具完全关闭时,模穴部与横浇道完全由空气所占有,因此若不排出这些空气,则所射出的溶融材料将此部分完全填充满。
必需以模具内的空气来换取溶融材料。
除了这种模具内空气排出的必要性以外,依成形材料处类而定。
有时候溶融时也会有气体或水蒸气竺挥发物质发生。
例如耐燃性塑胶在高温时某一部分会分解而产生腐蚀性气体。
除此之外,聚缩醛于成形时发生的挥发性物质会造成,而损及模具表面。
因此模穴所占的空气与成形时发生的挥发性物质必需迅速地由模穴排出,此排气通道的设计,在模具设计上是极重要的的注意事项。
所谓的排气,如前述不仅是排出空气而已,也需排出空气中的气体。
2排气设计不当时的问题。
一.烧焦当溶融材料填充速度比模穴内的排气速度快的话,模穴内的空气被压缩立刻达到高温(这种现象称为断热压缩),成形品与高温空气接角的部分产生烧焦,而成黑色。
二.由于在模穴内闭气阻力阻止了溶融材料的流动,减缓流速,造成填充不良现象。
另外闭铛于模穴内的气体量最后残留于模穴内,如果不会千百万烧焦也会造成填充不良的现象。
这种情形在吸湿性大的材料的预备干燥不完全时最容易发生。
三.溢料模穴内的空气与气体量,抑制了溶融材料的流动,使分割面扩充,造成与扩大投影面积相同效果,使分模面上浮,而产生溢料。
1.图2及图是其例子,如图所示的环状成形品中设置十字形进进浇口时,空气如图3所示,闭铛于中央部,虽然在周围设置排气沟,但模具分模面上浮而发生溢料,这种现象在薄肉制品的时候,特别容易发生。
四.其它问题如前所述发生的MOLD DEPOSIT,制品外观的损伤,小形精密形品也会发生尺寸不良的原因。
除此之外,排气不完全造成的成形不良不气泡,银线,喷嘴纹,外表污点等。
无如如何,模穴内空气或气体被闭锁于内的话,不仅阻碍溶融材料的流动,使速度下降,而且要采用较大的射出压力。
3.由模具分割面的排气法。
排气方法有很多种,任何方式皆是经验的积累,一般最常用采用的排气方法是在模具的分割面设置较浅的沟,图4是其例子,此图是在模具的分割面设置4个排气沟。
模具排气设计

圖18.6及18.7是疏氣鋼鑲件設計的參考方法:
序號
修訂內容
批準/日期
審核/日期
制訂/修訂
2.6盡可能用銑床加工,然后省去刀紋.因為用磨床加工,往往平位太長,使空氣不能直接排出
2.7排氣坑兩旁可做45斜邊及拋光(用#320沙紙)。
3.
4.水口的排氣
4.1水口的排氣深度
5.頂針及司筒排氣設計
5.1 “X”闊度為膠料排氣坑深度的1/2陪,排氣坑深度可參考表12.1
5.2哥針亦可用同樣排氣設計。
8.7.檢查疏氣的方法,可塗_少量液體如脫模劑在疏氣鋼工件表面上,再由出氣位吹入高
壓風,檢查泡沫湧起的情況便可知道疏氣性能的情度。
8.8.清潔阻塞疏氣孔的方法:
(i)加熱工件至500F,維時最少一小時。
(ii)冷卻至室溫後,浸入丙酮(acetone),維時最少十五分鐘。
(iii)取出工件,用高壓風從工件底部吹出阻塞物。
模具排氣設計
1.
作為一通道給型腔內的空氣及塑料被注射時所產生的氣體,在注塑時可流出型腔。
2.
2.1尺寸依膠料,不同膠料排氣尺寸不同.
2.2所有流道及冷膠位要加排氣.
2.3所有成品要加排氣,位置在入水對面.死角位.最后走到的.
2.4 CORE針及司筒有需要加排氣.
2.5排氣針要銑坑駁通模胚பைடு நூலகம்排氣,或駁通頂針孔.
8.2.疏氣鋼須疏氣的部份在幼加工時(膠位及底部)除電蝕外,不可作任何機械加工(磨床或
鑼床);粗加工時可作任何機械加工。
8.3.鑲件底要做疏氣坑。
8.4.疏氣鋼可直接修螺絲。
8.5.疏氣鋼如要開運水,運水孔要作鍍Dichtol處理。
发泡模具排气装置设计说明20页PPT

66、节制使快乐增加并使享受加强。 ——德 谟克利 特 67、今天应做的事没有做,明天再早也 是耽误 了。——裴斯 泰洛齐 68、决定一个人的一生,以及整个命运 的,只 是一瞬 之间。 ——歌 德 69、懒人无法享受休息之乐。——拉布 克 70、浪费时间是一桩大罪过。——卢梭
1、不要轻言放弃,否则对不起自己。
2、要冒一次险!整个生命就是一场冒险。走得最远的人,常是愿意 去做,并愿意去冒险的人。“稳妥”之船,从未能从岸边走远。-戴尔.卡耐基。
梦喝起来是苦涩的,回味起来却有 久久不会退去的余香。
发泡模具排气装置设计说明 4、守业的最好办法就是不断的发展。 5、当爱不能完美,我宁愿选择无悔,不管来生多么美丽,我不愿失 去今生对你的记忆,我不求天长地久的美景,我只要生生世世的轮 回里有你。
模具排气设计

1.在分模面設計排氣槽
排氣一
按鍵孔的靠破面設計排氣槽及排氣孔,排氣槽的寬度為2~3 ㎜。
排氣二
2~3㎜ 3~4mm
排氣三
2~3㎜
在充填的末端及包風處 設計排氣,排氣的基本 方式有: 分割入子、設計頂針、 設計排氣槽等。
2.各種塑膠原料不發生毛邊的排氣孔深度明細
(排氣深度應先以最小值製作)
PPS PC+ABS
0.01~0.03 0.015~0.02
3.抽真空排氣槽尺寸的基本要求
2~3㎜ DEEP 0.5~0.6㎜ ∮6㎜
3.5~4.0㎜ DEEP 如附表所示
注:當有其它原因無法製作O RING時,則不作O RING. (例如 SLIDE)
4.抽真空O型環結構之設計標準
V=
此種O型環的設計方式可以避免O型環掉落
=H
5.薄片Insert排氣方式
成品面 排氣槽只製作單面,深度 為塑膠原料對應排氣槽 的深度,離成品面應為 整面排氣
除客戶特別 指定,一般 不採用透氣 性鋼材
Depth:0.2 mm
在局部充填困難(成品肉厚較小處),可採用薄片 Insert的方式,在薄片Insert上建立排氣槽
說明結束
謝謝
塑膠原料 PE PP PS SB ABS 排氣孔深度(MM) 0.02 0.01~0.02 0.02 0.03 0.03 塑膠原料 SAN PPO POM PMMA PA 排氣孔深度(MM) 0.03 0.03 0.01~0.03 0.03 0.005~0.015
PC PBT
0.01~0.03 0.ห้องสมุดไป่ตู้05~0.015
模具排气

注塑模具的排气是模具设计中一个不可忽视的问题.排气不良,会造成众多问题.比如:气孔、空洞、烧焦、气泡、表面银纹、熔接线明显等。
模具内积集的气体主要有以下几个来源:
1.进料系统和型腔中存有的空气.
2.塑料含有的水分在高温下蒸发而生成的水蒸气.
3.塑料分解所产生的气体.
4.塑料中某些添加剂挥发或者化学反映所生成的气体
5.进料中夹杂的空气和水气!
基本的设计要点可以归纳如下:
1.排气要保证迅速、完全,排气速度要与充模速度相适应;
2.排气槽尽量开设在胶件较厚的成型部位;
3.排气槽应尽量开设在分型面上;
4.排气槽应尽量设在料流的终点和汇合处,如冷料井的尽端;
5.为了模具制造和清模方便,排气槽应尽量设在凹模一侧;
6.排气槽方向不应朝向操作面,防止注塑时漏料伤人;
7.排气槽不应有*角,防止积存冷料;
8.排气槽大小尺寸一定要合适(一般厚度在0.2-0.3mm左右),根据具体材料和产品要求进行选择加工,尽量避免造成飞边。
常见的排气形式有:
1.排气槽或孔排气2.分型面排气3.拼镶件缝隙排气
4.推杆或顶针间隙排气5.粉末烧结合金块排气6.设置排气杆强制排气。