橡胶硫化
橡胶硫化
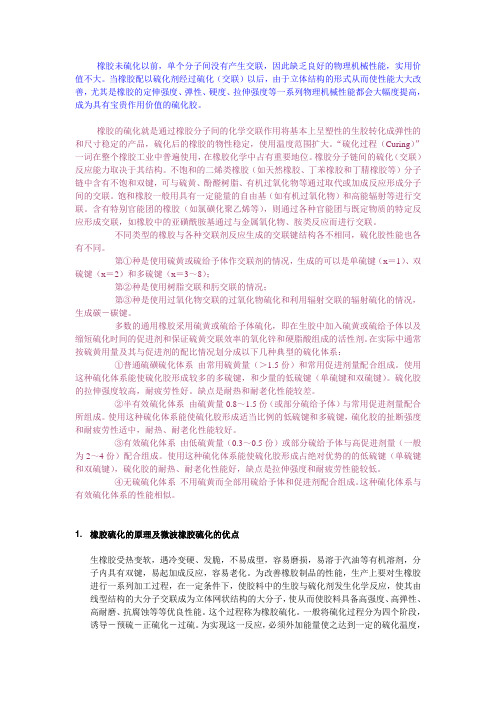
橡胶未硫化以前,单个分子间没有产生交联,因此缺乏良好的物理机械性能,实用价值不大。
当橡胶配以硫化剂经过硫化(交联)以后,由于立体结构的形式从而使性能大大改善,尤其是橡胶的定伸强度、弹性、硬度、拉伸强度等一系列物理机械性能都会大幅度提高,成为具有宝贵作用价值的硫化胶。
橡胶的硫化就是通过橡胶分子间的化学交联作用将基本上呈塑性的生胶转化成弹性的和尺寸稳定的产品,硫化后的橡胶的物性稳定,使用温度范围扩大。
“硫化过程(Curing)”一词在整个橡胶工业中普遍使用,在橡胶化学中占有重要地位。
橡胶分子链间的硫化(交联)反应能力取决于其结构。
不饱和的二烯类橡胶(如天然橡胶、丁苯橡胶和丁腈橡胶等)分子链中含有不饱和双键,可与硫黄、酚醛树脂、有机过氧化物等通过取代或加成反应形成分子间的交联。
饱和橡胶一般用具有一定能量的自由基(如有机过氧化物)和高能辐射等进行交联。
含有特别官能团的橡胶(如氯磺化聚乙烯等),则通过各种官能团与既定物质的特定反应形成交联,如橡胶中的亚磺酰胺基通过与金属氧化物、胺类反应而进行交联。
不同类型的橡胶与各种交联剂反应生成的交联键结构各不相同,硫化胶性能也各有不同。
第①种是使用硫黄或硫给予体作交联剂的情况,生成的可以是单硫键(x=1)、双硫键(x=2)和多硫键(x=3~8);第②种是使用树脂交联和肟交联的情况;第③种是使用过氧化物交联的过氧化物硫化和利用辐射交联的辐射硫化的情况,生成碳-碳键。
多数的通用橡胶采用硫黄或硫给予体硫化,即在生胶中加入硫黄或硫给予体以及缩短硫化时间的促进剂和保证硫黄交联效率的氧化锌和硬脂酸组成的活性剂。
在实际中通常按硫黄用量及其与促进剂的配比情况划分成以下几种典型的硫化体系:①普通硫磺硫化体系由常用硫黄量(>1.5份)和常用促进剂量配合组成。
使用这种硫化体系能使硫化胶形成较多的多硫键,和少量的低硫键(单硫键和双硫键)。
硫化胶的拉伸强度较高,耐疲劳性好。
缺点是耐热和耐老化性能较差。
橡胶硫化工艺
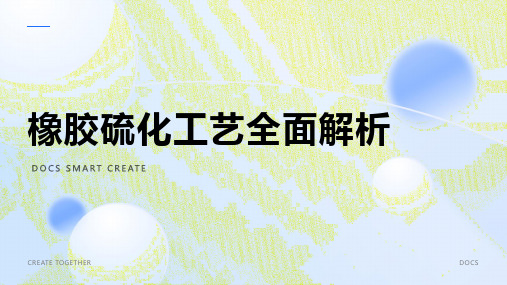
橡胶硫化工艺的未来发展趋势
智能化硫化工艺
• 利用物联网和大数据技术进行硫化工艺的监控和优化 • 提高硫化工艺的生产效率和产品质量
绿色硫化工艺
• 降低硫化工艺的能耗和污染排放 • 提高橡胶制品的环保性能
橡06胶硫化工艺在典型橡胶制品中的应用
实例
橡胶轮胎的硫化工艺与应用实例
橡胶轮胎的硫化工艺
• 热硫化工艺 • 压力硫化工艺
橡胶轮胎的应用实例
• 汽车轮胎 • 摩托车轮胎 • 飞机轮胎
橡胶密封件的硫化工艺与应用实例
橡胶密封件的硫化工艺
• 冷硫化工艺 • 压力硫化工艺
橡胶密封件的应用实例
• 汽车密封件 • 建筑密封件 • 航空航天密封件
橡胶输送带的硫化工艺与应用实例
• 热硫化工艺:加热橡胶材料进行硫化 • 冷硫化工艺:不加热橡胶材料进行硫化 • 压力硫化工艺:在压力条件下进行硫化
橡胶硫化工艺的特点
• 热硫化工艺:硫化效果好,生产效率较高 • 冷硫化工艺:适用于特殊场合,生产效率较低 • 压力硫化工艺:适用于大型橡胶制品,能提高制品的致密性
02
橡胶硫化工艺的主要方法及其原理
热硫化工艺及其原理
热硫化工艺
• 将橡胶材料加热至一定温度,加入硫化剂进行硫化 • 适用于大多数橡胶制品的硫化
热硫化工艺的原理
• 橡胶材料在加热过程中,分子链运动加剧,有利于硫化 剂的渗透 • 硫化剂与橡胶分子发生化学反应,形成交联结构,提高 橡胶制品的性能
冷硫化工艺及其原理
冷硫化工艺
• 在室温条件下,使用催化剂和硫化剂对橡胶材料进行硫 化 • 适用于特殊场合,如低温、高温或无法加热的场合
橡胶的硫化

四、伸长率和永久变形
与交联度关系 塑料工艺
塑料工艺
随交联度的增加而降低
五、弹性
与交联度关系
随交联度适当增加, 随交联度适当增加,弹性回复更为显著
1 − 2 2 W = ρRTM C1 (λ1 + λ2 + λ3 − 3) 2 2
W – 弹性 ρ- 橡胶密度 λ1,λ2,相邻交联键之间橡胶分子的平均分子量
只在一定交联度 范围内适用
塑料工艺
弹性体弹性 皮革态
硬质胶刚 体弹性
弹性
橡胶交联度与回弹性的关系
正硫化 交联度
3.2
塑料工艺
硫化过程的四个阶段
硫化曲线
胶料在硫化时, 胶料在硫化时,其性能随硫化时间变化而变化的曲线
塑料工艺
焦烧期
欠硫期
正硫
过硫
C 定伸强度 D A B 硫化时间 硫化过程的各阶段
硫化起步快的胶料; 有迟延特性的胶料; A - 硫化起步快的胶料; B - 有迟延特性的胶料; C - 过硫后定伸强度 继续上升的胶料; 继续上升的胶料; D - 有返原性的胶料
焦烧期or硫化诱导期 一、硫化起步阶段(焦烧期 硫化诱导期 硫化起步阶段 焦烧期 硫化诱导期)
1. 塑料工艺 硫化起步阶段
硫化时胶料开始变硬而后不能进行热塑性流动那一 点以前的硫化时间
2. 配合剂对焦烧期的影响
超速促进剂,焦烧期比较短,胶料易发生焦烧,操作安 全性差; 迟效性促进剂,焦烧期长,操作安全
活性
的反应
离 子 反 应
另外ZnO与硬脂酸反应生成锌离子, 另外ZnO与硬脂酸反应生成锌离子,与多硫络合 ZnO与硬脂酸反应生成锌离子
塑料工艺
这说明有活性剂,交联键数目增加, 这说明有活性剂,交联键数目增加,交联键中硫原子数目 减小,硫化胶的耐热性提高。 减小,硫化胶的耐热性提高。
橡胶硫化原理

橡胶硫化原理
橡胶硫化是一种将天然橡胶或合成橡胶转化为具有较好弹性和耐磨性的过程。
它的原理是通过将硫元素添加到橡胶分子链中,从而形成交叉链结构。
硫化剂通常是硫或含有硫的化合物,如硫醇、硫含量较高的化合物和多硫化物。
在硫化过程中,硫与橡胶中的双键发生反应,使橡胶链之间形成交联。
这种交联结构能够增强橡胶的强度、耐磨性和耐老化性。
硫化反应需要在适当的温度和压力下进行。
通常,使用硫化机或硫化炉将橡胶制品置于高温和压力下进行硫化。
在硫化过程中,硫与橡胶中的双键发生加成反应,形成硫醇中间体,然后再与其他硫醇或橡胶分子链发生反应,形成交链结构。
交联结构的形成使橡胶变得坚固耐用。
交联结构可以限制橡胶分子链的自由运动,从而提高橡胶的强度和弹性。
另外,交联还能够使橡胶对温度、化学品和老化等外界环境的变化具有更好的耐性。
橡胶硫化是橡胶工业中一项重要的工艺,它使橡胶制品具有更广泛的应用。
硫化过程中的交联结构为橡胶制品提供了优良的性能,使其能够在汽车、轮胎、皮革制品、密封件和电气绝缘材料等领域发挥重要作用。
橡胶的硫化方式
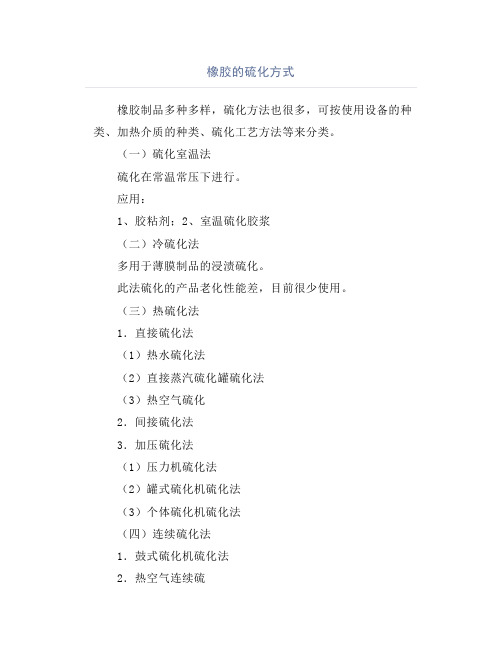
橡胶的硫化方式橡胶制品多种多样,硫化方法也很多,可按使用设备的种类、加热介质的种类、硫化工艺方法等来分类。
(一)硫化室温法硫化在常温常压下进行。
应用:1、胶粘剂;2、室温硫化胶浆(二)冷硫化法多用于薄膜制品的浸渍硫化。
此法硫化的产品老化性能差,目前很少使用。
(三)热硫化法1.直接硫化法(1)热水硫化法(2)直接蒸汽硫化罐硫化法(3)热空气硫化2.间接硫化法3.加压硫化法(1)压力机硫化法(2)罐式硫化机硫化法(3)个体硫化机硫化法(四)连续硫化法1.鼓式硫化机硫化法2.热空气连续硫是一种常压硫化方法,主要用于硫化雨布和胶乳制品。
特点:产品连续通过硫化室进行加热硫化。
硫化室分为三段,第一段为预热、升温,第二段为恒温硫化,第三段为降温冷却。
硫化室可用间接蒸汽加热或电热。
3.管道硫化法4.液体介质连续硫化法5.红外线硫化法红外线硫化是用红外线辐射硫化箱进行加热,使制品在红外线发热源之间通过二受到辐射加热。
红外线硫化适用于胶乳制品、雨布、密封条等薄壁制品。
6.沸腾床硫化法沸腾床的构造原理与液体硫化槽类似,床内贮存的是由固体、气体构成的悬浮系统。
沸腾床硫化的优点:热传递能力高;受热均匀;比液体介质的温度极限和化学惰性高;操作安全;不沾污成品和简化清洁工序等。
沸腾床除用于硫化橡胶制品外,还可用于金属、织物、坯料、模型的预热及原料的干燥等。
沸腾床硫化被广泛应用于无芯制品的连续硫化,如海绵条、门窗条、胶绳、胶条及异型压出制品、电线、电缆、纯胶管、薄膜制品等。
7.微波预热热空气硫化法微波预热热空气硫化法是压出制品先采用微波预热,接着让其进入热空气管道中进行硫化。
微波通常指频率在300~30000MHz之间的电磁波,只需要30~40s就可以使胶料的温度从90℃上升至190℃。
特点:微波预热热空气硫化法可以用于厚制品的硫化。
高频微波硫化法也可以用于厚制品的硫化。
具有频率高,占地少、制品清洁等优点,适用于各种尺寸和断面构型复杂的制品。
橡胶硫化—硫化工艺条件(橡胶加工课件)

一 硫化历程—硫化概念、原理与正硫化
二 硫化工艺条件—硫化三要素
三 硫化方法—工艺与设备 四 硫化质量分析—问题与对策
1.硫化工艺条件—温度
❖ 硫化工艺条件即硫化三要素—温度,时间和压力; ❖ 硫化温度是硫化反应的最基本条件。 ❖ 硫化温度高,硫化速度快,生产效率高;反之生产效率低 ❖ 硫化温度:电(硫化介质)间接加热,硫化介质直接加热或红
外、辐射能加热等。 硫化介质是传递热能的物质,如饱和蒸汽、过热水、热空气、
熔融盐、固体微粒等。
1.硫化工艺条件—温度
❖ 提高硫化温度会导致以下问题: ①引起橡胶分子链裂解和硫化返原,导致力学性能下降; ②使橡胶制品中的纺织物强度降低; ③导致胶料焦烧时间缩短,减少了充模时间,造成制品局
部缺胶; ④由于厚制品会增加制品的内外温差,导致硫化不均。
方程可计算出130℃和150℃时的等效硫化时间( K=2 )。
程度或胶料在一定温度下的硫化速度
t 100
I K 10
3.硫化工艺条件—硫化时间
例1:某制品正硫化条件为148℃×10min,K=2,问硫化温 度改为153℃、158℃、138℃时其等效硫化时间应分别是 多少?
3.硫化工艺条件—硫化时间
例2 某胶料的硫化温度系数为2.17,当140℃时正硫化时 间为68min,求135℃下的硫化时间。
❖ 硫化温度选择应根据制品的类型、胶种、硫化体系及其他方
面综合考虑。
不同胶种的硫化温度
不同硫化体系的硫化温度
2.硫化工艺条件—压力
❖ 硫化压力:机械压力,硫化介质,包覆层(钢丝,包布,铅)提供; 有些制品常压。 ❖ 硫化压力作用:
(1) 防止气泡; (2)提高致密性; (3)流动,充模,花纹清晰; (4)提高附着力。 ❖ 硫化压力应根据胶料配方、可塑性及产品结构等决定。
橡胶硫化

橡胶硫化原理•橡胶受热变软,遇冷变硬、发脆,不易成型,容易磨损,易溶于汽油等有机溶剂,分子内具有双键,易起加成反应,容易老化。
•为改善橡胶制品的性能,生产上要对生橡胶进行一系列加工过程,在一定条件下,使胶料中的生胶与硫化剂发生化学反应,使其由线型结构的大分子交联成为立体网状结构的大分子,使从而使胶料具备高强度、高弹性、高耐磨、抗腐蚀等等优良性能。
这个过程称为橡胶硫化。
• 一般将硫化过程分为四个阶段,诱导-预硫-正硫化-过硫。
为实现这一反应,必须外加能量使之达到一定的硫化温度,然后让橡胶保温在该硫化温度范围内完成全部硫化反应。
橡胶硫化的来历硫化是胶料通过生胶分子间交联,形成三维网络结构,制备硫化胶的基本过程。
不同的硫化体系适用于不同的生胶。
以橡胶(生胶)为主体,加以多种辅助材料而成的合成体、(辅助材料有几大体系、填充补强、硫化、防护、增塑、特殊物质加入剂、)而硫化是包覆绝缘层或护套层以后的一种处理方法、其目的就是让辅助体系里的硫化体系发生作用,使橡胶永久交联、增加弹性、减少塑性。
硫化的名词是因最早时间是用硫磺使橡胶交联的故称硫化,沿用至今•橡胶硫化体系不饱和橡胶通常使用如下几类硫化体系•以硫黄,有机二硫化物及多硫化物、噻唑类、二苯胍类,氧化锌及硬脂酸为主的硫化剂。
这是最通用的硫化体系。
但所制得的硫化胶的耐热氧老化性能不高。
•烷基酚醛树脂。
•多卤化物(如用于聚丁二烯橡胶、丁苯橡胶及丁腈橡胶的六氯乙烷)、六氯-对二甲苯。
*双官能试剂[如醌类、二胺类、偶氮及苯基偶氮衍生物(用于丁基橡胶及乙丙橡胶)等]。
*双马来酰亚胺,双丙烯酸酯。
两价金属的丙烯酸酯(甲基丙烯酸酯)、预聚醚丙烯酸酯。
•用于硫化饱和橡胶的有机过氧化物。
饱和橡胶硫化不同种类的饱和橡胶时,可使用不同的硫化体系•硫化三元乙丙橡胶时,使用有机过氧化物与不饱和交联试剂,如三烯丙基异氰脲酸酯(硫化剂TAIC)。
・硫化硅橡胶时也可使用有机过氧化物。
乙烯基硅橡胶硫化时可在催化剂(Pt)参与条件下进行。
橡胶硫化

橡胶硫化摘要:“硫化”一词对初学者来说比较陌生;这次主要对其概念的解释以及硫化条件、过程等进行介绍,通过此次介绍主要是为了帮助初学者的硫化的认识,让更多的人去很快的认识它、熟悉它,为硫化的进一步发展奠定基础。
硫化是橡胶制品制造工艺的最后一个流程,也是最重要一个流程,它赋予橡胶各种宝贵的的物理机械性能,简单来说就是把一些胶料以及各种加强剂融合在一起,使得性能互补以及加强,以达到它橡胶在各个领域的使用性能。
1、硫化概念“硫化”一词主要来源于最初天然橡胶制品用硫磺作交联剂进行交联而得名。
简单来说,硫化就好比“架桥”把两岸连接起来,即把一些线型高分子通过交联(架桥)作用形成网状高分子的工艺工程。
再简单而言其实就是交联,把一些个体整合成整体的过程,其反应过程较复杂。
但是可以从蒸馒头这个事例中对其有个大致的了解,其主要是利用淀粉和水混合后利用其附着性使淀粉颗粒抱团,从而形成面团;利用酵母菌的无氧呼吸以及有氧呼吸产生二氧化硫在面团中“乱跑”,导致馒头形成疏松多孔的结构,因此面团变胖了并且不容易变散,达到了交联的作用。
橡胶硫化主要是产生化学键把其成分交联在一起。
形成大分子网状结构,使其性能大大提高。
2、硫化条件正如蒸馒头需要利用酵母菌的有氧呼吸及无氧呼吸似的,橡胶的硫化也需要借助一些条件使分子之间发生交联。
其主要影响因素包括以下三个:硫化压力、温度、时间,通常被称为“硫化三要素”。
硫化条件对其硫化工艺至关重要,而且不同制品的硫化其硫化条件也不尽相同。
2.1硫化压力硫化压力是指在硫化过程中橡胶制品所承受的单位压力。
所施加的压力通常情况下分常压和高压;施加压力的主要作用是排除橡胶制品在硫化过程中内部产生的气体,防止制品内部出现气泡,提高胶料的致密性;还能加速胶料的流动和充满模腔,达到提高制品的物理机械性能的目的。
因此对于一些薄壁制品施加常压就可以达到其目的,而对于一些后制品则需施加高压才能达到其目的。
2.2硫化温度硫化属于一种化学反应,是使得内部分子结构发生改变,因此它同其他一般化学反应一样都依赖温度,随着温度的升高,硫化反应的速率也不断升高,从而直接影响生产效率;但是并不能无限制的提高硫化温度,一般硫化温度越高,胶料的物理机械性能越低,过高的温度会引起香蕉分子链的破解和发生硫化返原现象,使性能下降并且工艺控制困难。
4橡胶工艺学第三章 橡胶的硫化工艺
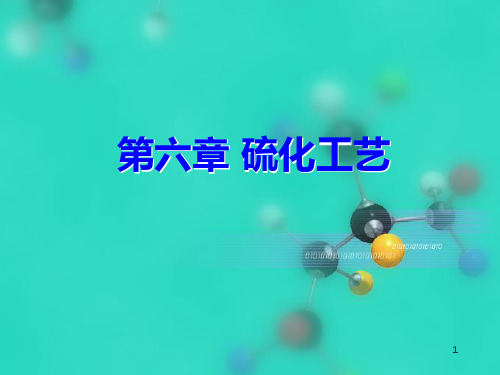
8
➢物理机械性能测定法
采用拉伸强度的最大值或 曲线的平坦区起始点对应 拉伸强度法 的时间为正硫化时间
物理机械性能法
压缩永久 变形法
综合物理机械性 能测试法
压缩永久变形-时间曲线的 转折点或拐点对应的时间即 为正硫化点对应时间 9
28
图13-6是热电偶测得的制品某部位在整个硫化过程 中的升温情况,t是时间的函数。该部位在硫化过 程中的硫化强度-时间曲线与横轴围成的面积即为 该部位胶料的硫化效应,如图13-7
29
30
有些橡胶制品的厚度较厚,在出模后温度不能很快的 降下来,因此会产生一定的后硫化效应,这在硫化工 艺中必须加以考虑,所以总的硫化效应应该是EA+EB, 如图13-8所示。
43
3.热空气:
介质环境干燥,可以硫化易水解的橡胶。但 其中的氧气易造成制品的氧化。常用于定型,再 通入蒸汽进行硫化。
44
4.过热蒸汽:
将饱和蒸汽进一步加热,可在相同压力下提 高40℃。
5.热水:
该介质传热比较均匀,制品变形较小。 但热水热含量低,热导率低,热损耗大,硫 化时间长,主要用于硫化薄的浸渍制品。
14
2.硫化方法和制品尺寸的影响:
不同的硫化方法影响硫化温度的选择。
硫化方法—— 注射,连续硫化两种工艺需要 的硫化温度较高;模压的较低。
尺寸—— 尺寸厚的大制件温度不宜过高,否 则表面过硫或内部欠硫。
15
二、硫化时间、等效硫化时间的确定和 等效硫化效应的仿真
1.硫化时间的确定
硫化时间是硫化化学反应必要条件。对于制品来说, 通常是指达到工程正硫化的时间,是由硫化温度、厚度、 制品形状、胶料自身的硫化特性决定的。胶料自身的硫化 特性取决于胶料配方,配方确定后,硫化温度和制品厚度 是决定硫化时间的主要因素。温度、制品厚度与硫化时间 的关系,可用等效硫化时间和等效硫化效应来确定。
橡胶的硫化

• 一.硫化发展概况
• 1839年,美国人Charles Goodyear发现橡胶和硫 黄一起加热可得到硫化胶;
• 1844年,Goodyear又发现无机金属氧化物(如 CaO、MgO、PbO)与硫黄并用能够加速橡胶的 硫化,缩短硫化时间;
• 1906年,使用了有机促进剂苯胺。Oenslager发 现在硫化性能最差的野生橡胶中添加苯胺后,可 使其性能接近最好的巴拉塔胶。
辐射硫化;70年代脲烷硫化体系;80年代提出了 平衡硫化体系。
• 橡胶硫化发展概况
大量硫黄 硫黄
100g胶
硫黄2-3份 促进剂0.6-1份
半有效硫黄硫化体系 有效硫黄硫化体系 平衡硫化体系(1979年)
1839年
1920年普通硫 黄硫化体系
1950年
•橡胶硫化体系主要由硫化剂、促进剂、活化剂组成。
• 这一阶段的长短取决于所用配合剂,特别 是促进剂的种类。
• 另外,不同的硫化方法和制品对焦烧时间 的长短亦有不同要求
二 .欠硫阶段(又称预硫阶段)
• 硫化起步与正硫化之间的阶段称为欠硫阶 段。
• 6.硫化返原:如果胶料再继续硫化就会使交联结 构产生降解,性能下降,这种现象就称为硫化返 原。
• 四.理想的硫化曲线
• 较为理想的橡胶硫化曲线应满足下列条件:
• 硫化诱导期要足够长,充分保证生产加工的安全 性;
• 硫化速度要快,提高生产效率,降低能耗;
• 硫化平坦期要长(以保证硫化加工中的安全性, 减少过硫危险,以及保证制品各部位硫化均匀一 致)。
(2)对某些需要塑炼的胶种,塑炼未达要求,可塑性太 低,胶质过硬,导致炼胶时急剧升温。炼胶机或其它 辊筒装置(如返炼机、压延机)辊温太高,冷却不够, 也可能导致现场焦烧。
橡胶硫化知识

橡胶硫化知识一1.硫化的定义硫化是胶料在一定条件下,橡胶大分子由线型结构转变为网状结构的胶联过程。
2.硫化历程2.1硫化反应过程硫化过程可以分三个阶段。
第一阶段为诱导阶段:先是硫磺分子和促进剂体系之间反应生成一种活性更大的中间化合物,然后进一步引发橡胶分子链,产生可交联的自由基或者离子。
第二阶段为交联反应阶段:可交联的自由基或者离子与橡胶分子链之间产生连锁反应,生成交联键。
第三阶段为网构形成阶段:此阶段的前期交联反应已趋于完成,产生的交联键发生重排和裂解反应,在此阶段的后期交联反应已基本停止,随之而发生的主要是交联键重排和热裂解的反应,最后得到网格稳定的硫化胶。
2.2硫化历程图扭矩MHMLA B C D硫化时间A:焦烧时间(TS2)B:热硫化(TS2+B Time =TC90)C:平坦硫化D:过硫化橡胶硫化历程可以分为四个阶段:2.2.1、图中A段是热硫化开始前的延迟作用时间,相当于硫化反应的诱导期,称作焦烧时间。
长短取决于胶料配方和加工条件,主要受促进剂影响。
包括操作焦烧时间和剩余焦烧时间;操作焦烧时间指加工过程中热积累效应所消耗的焦烧时间,取决于加工条件(混炼、挤出等)。
剩余焦烧时间是指胶料在模腔加热时保持流动性的时间。
2.2.2热硫化阶段图中B 段是硫化反应中的交联阶段。
逐渐产生网构,促使橡胶弹性和拉伸强度急剧上升。
热硫化时间的长短取决于胶料配方。
这个阶段是衡量硫化反应速度的标志。
2.2.3平坦硫化阶段图中C 段相当于硫化反应中网状形成的前期。
这时,交联反应已趋完成,继而发生交联键的重排、裂解等反应,因而胶料的强度曲线出现平坦区,这段时间称为平坦硫化时间。
2.2.4过硫化阶段图中D 段以后的部分,相当于硫化反应中网构形成期的后期。
这阶段中,主要是交联键的重排作用,以及交联键和链段热裂解的反应,因此胶料的机械性能显著下降。
2.3硫化曲线的解说• ML ——最低转矩,N·m (kgf·cm )• MH ——到达规定时间之后仍然不出现平坦曲线或最高转矩的硫化曲线,所达到的最高转矩N·m (kgf·cm )•TS1——从实验开始到曲线由最低转矩上升0.1 N·m(kgf·cm)时所对应的时间,MIN•TS2——从实验开始到曲线由最低转矩上升0.2 N·m(kgf·cm)时所对应的时间,MIN•TC(x)——试样达到某一硫化程度所需要的时间,即试样转矩达到ML+X (MH-ML)时所对应的时间,MIN如X取值0.5,即TC50;X取0.9,即TC90)•硫检参数的意义:•ML:表示胶料的蠕变性,ML越低,蠕变性越好,反之,越差。
橡胶硫化

↑
定伸应力法
• 定伸应力法是根据不同硫化时间试片的300%定 伸应力绘出曲线,曲线在强度轴的转折点所对应 的时间即为正硫化时间。 • 由300%定伸应力所确定的正硫化时间基本上与 理论正硫化时间相一致。
↓↑
拉伸强度法
• 拉伸强度法与定伸强度法相似。通常,选择拉伸强度最 大值或比最大值略低(考虑到后硫化)时所对应的时间为 正硫化时间。 胶料的拉伸强度是随交密度的增加而增大,但达到最大 值后,便随交联密度的增加而降低。这是因为交联密度 的进一步增加,会使分子链的定向排列发生困难所致。 所以,由拉伸强度确定的正硫化时间为工艺正硫化时间。
②含骨架材料制品 进行等当量胶层厚度的换算
二、硫化工艺条件
例:制品的结构如图中所示,其胶料试片的正硫化时间为 142℃×8min,已知胶层的热扩散系数为1.32×10-3cm2/s,布 层的扩散系数为1.04×10-3cm2/s,求制品在142℃下的硫化时 间。
二、硫化工艺条件
3、硫化时间 硫化时间的调整
• 此法所测得的正硫化时间与理论正硫化时间应该 是一致的。
• 在硫化反应中消耗的硫黄并非全部构成有效的交 联键,不适于非硫黄硫化的胶料。
溶胀法
• 溶胀法是将不同硫化时间的试片,置于适当的溶剂(如苯、 汽油等)中,在恒温下,经一定时间达到溶胀平衡后,取出 试片进行称量,根据计算出的溶胀率绘成溶胀曲线。天然橡 胶的溶胀曲线呈“U”形,曲线最低点的对应时间即为正硫 化时间。合成橡胶的溶胀曲线类似于渐近线,其转折点即为 正硫化时间。
间的粘着力,改善硫化胶的物理性能(如耐屈挠性能)。
二、硫化工艺条件
2、硫化压力 • 一般来说,硫化压力的选取应根据产品类型、配方、可塑 性等因素决定。 • 原则上应遵循以下规律:可塑性大,压力宜小些;产品厚、
橡胶硫化处理

橡胶硫化处理摘要:1.橡胶硫化处理的概念和原理2.橡胶硫化处理的方法3.橡胶硫化处理的影响因素4.橡胶硫化处理的应用领域5.橡胶硫化处理的发展前景正文:一、橡胶硫化处理的概念和原理橡胶硫化处理是一种改善橡胶性能的重要工艺。
橡胶在经过硫化处理后,其物理、化学和机械性能都会得到显著提高,从而满足各种应用场景的需求。
橡胶硫化处理的原理是在一定的温度和压力下,使橡胶中的双键与硫磺发生反应,形成稳定的硫化橡胶。
二、橡胶硫化处理的方法橡胶硫化处理主要有以下几种方法:1.常规硫化:通过硫磺和促进剂的作用,使橡胶在一定温度下进行硫化。
这是最常用的硫化方法,适用于天然橡胶、合成橡胶等。
2.动态硫化:通过在橡胶中加入特殊的硫化剂,使橡胶在动态应力作用下进行硫化。
这种方法适用于生产轮胎等需要良好韧性和耐磨性的产品。
3.辐射硫化:通过放射线或紫外线照射橡胶,引发橡胶分子间的交联反应。
这种方法适用于医疗用品、食品包装等对硫化温度要求较高的领域。
三、橡胶硫化处理的影响因素橡胶硫化处理的效果受到以下因素的影响:1.硫磺用量:硫磺用量过多或过少都会影响硫化效果,需要根据具体情况进行调整。
2.促进剂:促进剂的种类和用量会影响硫化速度和效果。
不同种类的橡胶需要选用不同的促进剂。
3.硫化温度和时间:硫化温度和时间的选择要根据橡胶的种类和性能要求来确定。
4.橡胶的初始性能:橡胶的初始性能会影响硫化后的性能。
如橡胶的含胶量、含水量等都会对硫化效果产生影响。
四、橡胶硫化处理的应用领域橡胶硫化处理广泛应用于轮胎、胶带、胶管、密封件等橡胶制品的生产。
这些产品在经过硫化处理后,能够满足各种应用场景的需求,如耐磨、耐高温、耐油等。
五、橡胶硫化处理的发展前景随着科学技术的进步和环保理念的普及,橡胶硫化处理技术也在不断发展和创新。
橡胶硫化工艺
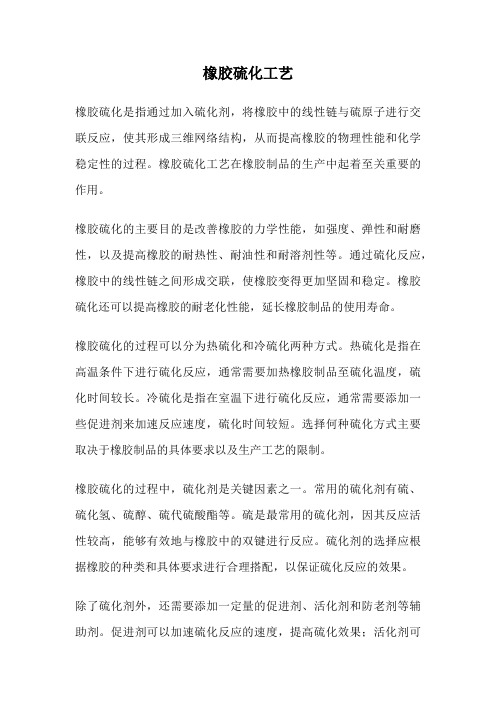
橡胶硫化工艺橡胶硫化是指通过加入硫化剂,将橡胶中的线性链与硫原子进行交联反应,使其形成三维网络结构,从而提高橡胶的物理性能和化学稳定性的过程。
橡胶硫化工艺在橡胶制品的生产中起着至关重要的作用。
橡胶硫化的主要目的是改善橡胶的力学性能,如强度、弹性和耐磨性,以及提高橡胶的耐热性、耐油性和耐溶剂性等。
通过硫化反应,橡胶中的线性链之间形成交联,使橡胶变得更加坚固和稳定。
橡胶硫化还可以提高橡胶的耐老化性能,延长橡胶制品的使用寿命。
橡胶硫化的过程可以分为热硫化和冷硫化两种方式。
热硫化是指在高温条件下进行硫化反应,通常需要加热橡胶制品至硫化温度,硫化时间较长。
冷硫化是指在室温下进行硫化反应,通常需要添加一些促进剂来加速反应速度,硫化时间较短。
选择何种硫化方式主要取决于橡胶制品的具体要求以及生产工艺的限制。
橡胶硫化的过程中,硫化剂是关键因素之一。
常用的硫化剂有硫、硫化氢、硫醇、硫代硫酸酯等。
硫是最常用的硫化剂,因其反应活性较高,能够有效地与橡胶中的双键进行反应。
硫化剂的选择应根据橡胶的种类和具体要求进行合理搭配,以保证硫化反应的效果。
除了硫化剂外,还需要添加一定量的促进剂、活化剂和防老剂等辅助剂。
促进剂可以加速硫化反应的速度,提高硫化效果;活化剂可以改善硫化剂的反应性能,增强硫化效果;防老剂可以提高橡胶制品的耐热性和耐氧化性。
辅助剂的添加量、种类和配比应根据具体要求进行合理调整,以确保橡胶硫化的效果。
橡胶硫化工艺的控制也是至关重要的。
硫化温度、硫化时间和硫化压力等因素都会对硫化效果产生影响。
硫化温度过高或过低都会导致硫化效果的下降,硫化时间过长或过短都会对橡胶的性能产生不利影响。
因此,在生产过程中需要对硫化条件进行精确控制,以确保橡胶制品的质量。
橡胶硫化工艺是橡胶制品生产中不可或缺的环节。
通过合理选择硫化剂、辅助剂和控制硫化条件,可以改善橡胶的力学性能、耐热性和耐化学性,提高橡胶制品的质量和使用寿命。
橡胶硫化工艺的研究和应用对于橡胶制品行业的发展具有重要意义。
橡胶硫化理论
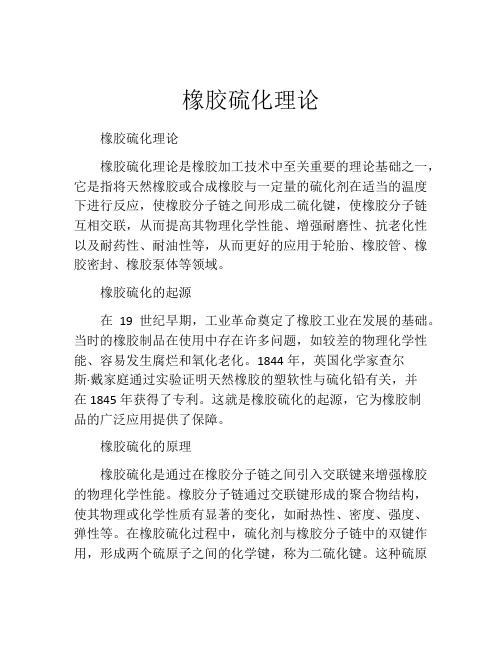
橡胶硫化理论橡胶硫化理论橡胶硫化理论是橡胶加工技术中至关重要的理论基础之一,它是指将天然橡胶或合成橡胶与一定量的硫化剂在适当的温度下进行反应,使橡胶分子链之间形成二硫化键,使橡胶分子链互相交联,从而提高其物理化学性能、增强耐磨性、抗老化性以及耐药性、耐油性等,从而更好的应用于轮胎、橡胶管、橡胶密封、橡胶泵体等领域。
橡胶硫化的起源在19世纪早期,工业革命奠定了橡胶工业在发展的基础。
当时的橡胶制品在使用中存在许多问题,如较差的物理化学性能、容易发生腐烂和氧化老化。
1844年,英国化学家查尔斯·戴家庭通过实验证明天然橡胶的塑软性与硫化铅有关,并在1845年获得了专利。
这就是橡胶硫化的起源,它为橡胶制品的广泛应用提供了保障。
橡胶硫化的原理橡胶硫化是通过在橡胶分子链之间引入交联键来增强橡胶的物理化学性能。
橡胶分子链通过交联键形成的聚合物结构,使其物理或化学性质有显著的变化,如耐热性、密度、强度、弹性等。
在橡胶硫化过程中,硫化剂与橡胶分子链中的双键作用,形成两个硫原子之间的化学键,称为二硫化键。
这种硫原子的交联使橡胶链成为一个结构复杂的网络,从而发生交联反应。
橡胶硫化的种类橡胶硫化可以分为热硫化和冷硫化两种。
热硫化是指在高温条件下,将硫化剂加入橡胶中,使其在特殊的压缩下形成交联键的过程。
热硫化可以分为高温硫化和低温硫化。
高温硫化一般在120°C到160°C之间进行,低温硫化一般在70°C到100°C之间进行。
冷硫化是指在常温下,将硫化剂加入橡胶中,使其通过紫外线、电子束等辐射,形成交联键的过程。
这种方式往往需要添加光敏剂加速反应速度。
橡胶硫化的影响因素橡胶硫化的影响因素主要有硫化剂种类、硫化剂用量、硫化温度和硫化时间。
硫化剂种类的不同,其加固效果也不同。
一般来说,活性硫化剂比惰性硫化剂反应活泼。
硫化剂用量的不同,其加固效果也不同。
但是硫化剂用量过量也会造成反效果,降低橡胶的性能。
- 1、下载文档前请自行甄别文档内容的完整性,平台不提供额外的编辑、内容补充、找答案等附加服务。
- 2、"仅部分预览"的文档,不可在线预览部分如存在完整性等问题,可反馈申请退款(可完整预览的文档不适用该条件!)。
- 3、如文档侵犯您的权益,请联系客服反馈,我们会尽快为您处理(人工客服工作时间:9:00-18:30)。
橡胶硫化工艺方法一、传统橡胶硫化工艺1、影响硫化工艺过程的主要因素:硫磺用量。
其用量越大,硫化速度越快,可以达到的硫化程度也越高。
硫磺在橡胶中的溶解度是有限的,过量的硫磺会由胶料表面析出,俗称“喷硫”。
为了减少喷硫现象,要求在尽可能低的温度下,或者至少在硫磺的熔点以下加硫。
根据橡胶制品的使用要求,硫磺在软质橡胶中的用量一般不超过3%,在半硬质胶中用量一般为20%左右,在硬质胶中的用量可高达40%以上。
硫化温度。
若温度高10℃,硫化时间约缩短一半。
由于橡胶是不良导热体,制品的硫化进程由于其各部位温度的差异而不同。
为了保证比较均匀的硫化程度,厚橡胶制品一般采用逐步升温、低温长时间硫化。
2、硫化时间:这是硫化工艺的重要环节,时间过短,硫化程度不足(亦称欠硫)。
时间过长,硫化程度过高(俗称过硫)。
只有适宜的硫化程度(俗称正硫化),才能保证最佳的综合性能二、橡胶硫化工艺方法按硫化条件可分为冷硫化、室温硫化和热硫化三类。
1、冷硫化可用于薄膜制品的硫化,制品在含有2%~5%氯化硫的二硫化碳溶液中浸渍,然后洗净干燥即可。
2、室温硫化时,硫化过程在室温和常压下进行,如使用室温硫化胶浆(混炼胶溶液)进行自行车内胎接头、修补等。
3、热硫化是橡胶制品硫化的主要方法。
根据硫化介质及硫化方式的不同,热硫化又可分为直接硫化、间接硫化和混气硫化三种方法。
①直接硫化,将制品直接置入热水或蒸汽介质中硫化。
②间接硫化,制品置于热空气中硫化,此法一般用于某些外观要求严格的制品,如胶鞋等。
③混气硫化,先采用空气硫化,而后再改用直接蒸汽硫化。
此法既可以克服蒸汽硫化影响制品外观的缺点,也可以克服由于热空气传热慢,而硫化时间长和易老化的缺点。
三、橡胶硫化工艺:橡胶在未硫化之前,分子之间没有产生交联,因此缺乏良好的物理机械性能,实用价值不大。
当橡胶加入硫化剂以后,经热处理或其他方式能使橡胶分子之间产生交联,形成三维网状结构,从而使其性能大大改善,尤其是橡胶的定伸应力、弹性、硬度、拉伸强度等一系列物理机械性能都会大大提高。
橡胶大分子在加热下与交联剂硫磺发生化学反应,交联成为立体网状结构的过程。
经过硫化后的橡胶称硫化胶。
硫化是橡胶加工中的最后一个工序,可以得到定型的具有实用价值的橡胶制品。
四、注压成型硫化工艺:普通模压与注压最明显的区别在于前者胶料是以冷的状态充入模腔的,而后者则是将胶料加热混合,并在接近硫化温度下注入模腔。
因而,在注压过程中,加热模板所提供的热量仅仅只用于维持硫化,它能很快将胶料加热到190℃-220℃。
在模压过程中,由加热模板所提供的热量首先要用于预热胶料,由于橡胶的导热性能差,如果制品很厚,热量要传导到制品中心需要较长的时间。
采用高温硫化也可在一定程度上缩短操作时间,但往往导致靠近热板的制品边缘出现焦烧。
采用注压法硫化,可以缩短成型周期,实现自动化操作,这对大批量生产最为有利。
注压还具有以下优点:可以省去半成品准备、起模和制品修边等工序;可以生产出尺寸稳定、物理机械性能优异的高质量产品;减少硫化时间,提高生产效率,减少胶料用量,降低成本,减少废品,提高企业经济效益。
五、注压成型硫化工艺注意事项:采用合理的螺杆转速、背压,控制适当的注射机温度。
一般地,应保持出料口胶温和控制循环温度之差不大于30度为宜。
注射机螺杆的用途是在选定的和均匀的温度下为每一循环制备足够量的胶料;它明显地影响着注射机的产量。
背压是通过放慢注射缸中出油口的流量而产生的,并对注射机所射出胶料,对注射油缸的推挤作用进行限制。
实践中,背压只会稍微增加对胶料的剪切,而不会引起硫化制品物理性能的降低。
喷嘴的设计:喷嘴连接注射机头和模具,同时对热平衡有一定作用。
经过喷嘴的压力损失会经由注射而转换成为热量。
胶料绝不允许在这个部位硫化。
因此,选择合适的喷嘴直径非常重要,它影响着喷嘴部位的摩擦生热、胶料注射时所需要的压力和充模时间。
合适的模具温度,最佳的硫化条件。
在选择好胶料的最佳配合之后,重要的就是注射成型条件与硫化条件的相互配合。
注压成型与模压成型相比,由于模具表面、内部温度分布不同,要实现良好的硫化就必须对温度进行高精度控制,使模具表面、内部同时达到最佳硫化条件。
高温会增大橡胶的收缩率,但二者关系是线性的,在生产前应有充分的估计。
此外,就成型压力而言,高压成型是极为有利的,因为压力与收缩成反比关系。
安全合理的胶料配方设计。
对于进行注压硫化成型的胶料,要求其具有以下特性:胶料的门尼焦烧时间应当尽可能的长,以获得最大的安全性。
通常,门尼焦烧时间应比胶料在机筒中的停留时间长2倍。
硫化速度快,通过对不同胶料硫化体系的合理选择,添加合适的促进剂,使胶料在注压硫化时有令人满意的效率。
流动性良好,良好的流动性能减少胶料的停留时间,减少注压时间,并提高防焦烧能力。
六、氮气硫化工艺采用充氮气硫化的主要优点是节能和延长胶囊寿命,可节省蒸汽80%,胶囊使用寿命可延长1倍。
轮胎在硫化过程中要消耗大量热能和电能,因此开发和推广节能硫化工艺意义重大。
由于氮气分子量小、热容很小,氮气充入轮胎胶囊内腔时,不会吸热而引起温度降低,也不易造成胶囊氧化裂解破坏。
七、氮气硫化的工艺特点先通高温高压蒸汽,若干分钟后切换通入氮气,利用充氮硫化的“保压变温”工艺硫化至结束。
因为最初通入几分钟蒸汽的热量足够保持硫化一条轮胎,理论上只要在完成硫化之前温度不降到150℃以下即可。
但是,采用氮气硫化时,首先通入的是高温高压蒸汽,会造成上下胎侧的温差,要消除上下胎侧的硫化温差,必须合理布置硫化介质喷射的位置,改进密封和热工管路系统。
硫化用氮气的纯度要求达99.99%,最好达到99.999%,并建议企业自配制氮系统,以降低使用成本。
氮气纯度不够,会影响胶囊的使用寿命。
将氮气硫化的“保压变温”硫化原理应用于传统循环过热水硫化工艺的改造,人们又开发出了用高温高压蒸汽加过热水的硫化工艺取代常规的循环过热水硫化工艺。
硫化时,先通入高温高压蒸汽,若干分钟后切换通入循环过热水,再过若干分钟后关闭回水阀停止循环,直到利用潜热硫化至结束。
采用这种新的加热硫化方法,据理论计算,其能耗仅是传统硫化工艺方法的1/2。
八、变温硫化工艺变温硫化工艺过程的关键因素根据成品物理性能试验和生产经验,缩短硫化时间。
这在一定程度上减轻了过硫化程度。
采用高温硫化。
近年来小型轮胎硫化工艺逐渐向高温硫化方向发展,且考虑后硫化效应,硫化时间短,对减轻过硫和提高硫化程度的均匀性有一定作用。
进行硫化测温,找到制品中的最慢硫化点,以该点为依据来确定硫化时间,效果较前两种好。
利用该法可不同程度地提高硫化效率,改善硫化程度的均匀性。
但由于实际生产中只考察外温,轮胎各部位的实际温度并不确知,加上并不是每次温度固定不变,因此根据测温计算出的结果与实际硫化的结果有较大误差。
橡胶厚制品硫化过程温度场模拟仿真与预测表明,温度不均匀是造成轮胎外胎硫化程度不均匀的主要因素。
橡胶工业普遍认为外温恒定是保证质量的重要条件,从设备上要千方百计地实现恒温。
这对非厚橡胶制品来说是正确的,而对轮胎外胎等厚橡胶制品则不然。
轮胎在模型中加热硫化,热经由模型传到外胎各部位。
橡胶是热的不良导体,温升慢,加热早期外胎各部位存在明显的温度梯度,经过较长时间才能达到平衡。
介绍橡胶硫化介绍橡胶硫化“硫化过程(Curing)”一词在整个橡胶工业中普遍使用,在橡胶化学中占有重要地位。
橡胶的硫化就是通过橡胶分子间的化学交联作用将基本上呈塑性的生胶转化成弹性的和尺寸稳定的产品,硫化后的橡胶的物性稳定,使用温度范围扩大。
橡胶分子链间的硫化(交联)反应能力取决于其结构。
不饱和的二烯类橡胶(如天然橡胶、丁苯橡胶和丁腈橡胶等)分子链中含有不饱和双键,可与硫黄、酚醛树脂、有机过氧化物等通过取代或加成反应形成分子间的交联。
饱和橡胶一般用具有一定能量的自由基(如有机过氧化物)和高能辐射等进行交联。
含有特别官能团的橡胶(如氯磺化聚乙烯等),则通过各种官能团与既定物质的特定反应形成交联,如橡胶中的亚磺酰胺基通过与金属氧化物、胺类反应而进行交联。
橡胶硫化体系:多数的通用橡胶采用硫黄或硫给予体硫化,即在生胶中加入硫黄或硫给予体以及缩短硫化时间的促进剂和保证硫黄交联效率的氧化锌和硬脂酸组成的活性剂。
在实际中通常按硫黄用量及其与促进剂的配比情况划分成以下几种典型的硫化体系:普通硫磺硫化体系由常用硫黄量(>1.5份)和常用促进剂量配合组成。
使用这种硫化体系能使硫化胶形成较多的多硫键,和少量的低硫键(单硫键和双硫键)。
硫化胶的拉伸强度较高,耐疲劳性好。
缺点是耐热和耐老化性能较差。
半有效硫化体系由硫黄量0.8~1.5份(或部分硫给予体)与常用促进剂量配合所组成。
使用这种硫化体系能使硫化胶形成适当比例的低硫键和多硫键,硫化胶的扯断强度和耐疲劳性适中,耐热、耐老化性能较好。
有效硫化体系由低硫黄量(0.3~0.5份)或部分硫给予体与高促进剂量(一般为2~4份)配合组成。
使用这种硫化体系能使硫化胶形成占绝对优势的的低硫键(单硫键和双硫键),硫化胶的耐热、耐老化性能好,缺点是拉伸强度和耐疲劳性能较低。
无硫硫化体系不用硫黄而全部用硫给予体和促进剂配合组成。
这种硫化体系与有效硫化体系的性能相似。
橡胶交联键结构与硫化胶性能:使用硫黄或硫给予体作交联剂的情况,生成的可以是单硫键(x=1)、双硫键(x=2)和多硫键(x=3~8);使用树脂交联和肟交联的情况;使用过氧化物交联的过氧化物硫化和利用辐射交联的辐射硫化的情况,生成碳-碳键。
橡胶知识橡胶知识橡胶硫化原理橡胶受热变软,遇冷变硬、发脆,不易成型,容易磨损,易溶于汽油等有机溶剂,分子内具有双键,易起加成反应,容易老化。
为改善橡胶制品的性能,生产上要对生橡胶进行一系列加工过程,在一定条件下,使胶料中的生胶与硫化剂发生化学反应,使其由线型结构的大分子交联成为立体网状结构的大分子,使从而使胶料具备高强度、高弹性、高耐磨、抗腐蚀等等优良性能。
这个过程称为橡胶硫化。
一般将硫化过程分为四个阶段,诱导-预硫-正硫化-过硫。
为实现这一反应,必须外加能量使之达到一定的硫化温度,然后让橡胶保温在该硫化温度范围内完成全部硫化反应。
橡胶硫化的来历硫化是胶料通过生胶分子间交联,形成三维网络结构,制备硫化胶的基本过程。
不同的硫化体系适用于不同的生胶。
以橡胶(生胶)为主体,加以多种辅助材料而成的合成体、(辅助材料有几大体系、填充补强、硫化、防护、增塑、特殊物质加入剂、)而硫化是包覆绝缘层或护套层以后的一种处理方法、其目的就是让辅助体系里的硫化体系发生作用,使橡胶永久交联、增加弹性、减少塑性。
硫化的名词是因最早时间是用硫磺使橡胶交联的故称硫化,沿用至今.橡胶硫化体系不饱和橡胶通常使用如下几类硫化体系:以硫黄,有机二硫化物及多硫化物、噻唑类、二苯胍类,氧化锌及硬脂酸为主的硫化剂。