14系统预防维修模型
预防性维修策略优化

预防性维修策略优化预防性维修策略优化预防性维修是一种预先采取措施来避免设备或系统故障的维修策略。
以下是一个优化预防性维修策略的步骤思考过程:第一步:了解设备或系统首先,我们需要对所涉及的设备或系统进行全面的了解。
这包括了解其工作原理、常见故障模式以及维修需求和周期。
只有了解了设备或系统的特点,我们才能更好地制定预防性维修策略。
第二步:收集数据接下来,我们需要收集相关的数据,以便更准确地分析设备或系统的维修需求和周期。
这可以通过记录设备的运行时间、故障记录和维修历史等方式来实现。
有了这些数据,我们可以更好地识别设备或系统的维修模式和趋势。
第三步:制定维修计划根据收集到的数据,我们可以开始制定预防性维修计划。
这包括确定维修的频率和时间点,以及所需的维修资源和材料。
通过维护计划,我们可以在设备或系统出现故障之前采取必要的维修措施,从而减少设备停机时间和维修成本。
第四步:实施预防性维修一旦维修计划制定好了,我们需要开始实施预防性维修措施。
这可能包括定期更换零部件、进行清洁和润滑、定期检查和测试等。
同时,我们还应该建立记录和报告系统,以便及时跟踪维修工作的进展和效果。
第五步:监测和评估实施预防性维修后,我们需要监测和评估其效果。
这可以通过收集维修后的数据和设备运行状况来实现。
通过分析这些数据,我们可以评估维修策略的效果,并进行必要的调整和改进。
第六步:持续改进预防性维修是一个持续的过程,需要不断改进和优化。
根据监测和评估的结果,我们可以发现新的维修需求和模式,并相应地调整维修计划和措施。
通过不断改进和优化,我们可以提高设备或系统的可靠性和可用性,降低维修成本和停机时间。
总结起来,预防性维修是一种优化维修策略的方法,可以帮助我们提前预防设备或系统的故障。
通过了解设备或系统、收集数据、制定维修计划、实施预防性维修、监测和评估以及持续改进,我们可以不断提高设备或系统的性能和可靠性,从而提高工作效率和降低维修成本。
预防性维修优化方案

预防性维修优化方案预防性维修优化方案预防性维修是一种旨在提前检测和修复设备故障的方法,以确保设备的正常运行和延长其使用寿命。
以下是一个逐步思考的预防性维修优化方案。
第一步:设备调查和问题识别首先,对设备进行全面的调查和检查,以确定可能存在的问题和潜在的故障点。
这可以通过检查设备的使用记录、观察设备的运行状况和与操作工人进行访谈来实现。
该步骤的目的是识别潜在的故障源,以便在早期阶段进行干预和修复。
第二步:设定维修计划和周期基于设备调查和问题识别的结果,制定维修计划和周期。
这包括确定每个设备需要进行维修的频率和时间点。
既要确保维修频率足够频繁以避免设备故障,又要确保维修时间不会对生产造成太大的干扰。
在设定维修计划和周期时,需要考虑设备的使用率、生产流程和维修资源的可用性。
第三步:设备监测和数据分析建立设备监测系统,定期监测设备的运行状况和性能数据。
这可以通过使用各种传感器和监测设备来实现,以实时收集设备的运行数据。
同时,将收集到的数据进行分析和比较,以识别任何异常或潜在的故障迹象。
这将帮助确定维修优化的重点和优先级。
第四步:实施预防性维修根据维修计划和周期,定期对设备进行预防性维修。
这包括定期更换易损件、清洁设备、检查并调整设备的各个部件等。
维修过程应由经过培训的技术人员执行,并采用标准化的维修程序和工具。
为了确保维修的及时性和质量,可以建立一个维修队伍,负责设备维修和维护工作。
第五步:维修记录和反馈对每次维修都应进行记录和反馈。
这包括记录维修日期、维修内容、使用的材料和工具、维修时间等。
同时,还应该记录设备在维修后的运行状况和性能。
这将有助于评估维修计划的有效性,并识别可能需要调整或改进的方面。
第六步:持续改进和优化根据维修记录和反馈,评估和分析维修计划的有效性。
识别维修过程中的瓶颈和改进的机会,并采取相应的措施进行持续改进和优化。
这可能包括改进维修程序、增加维修资源、优化维修时间等。
持续改进和优化是一个循环过程,需要定期进行评估和调整。
设备维护管理中的预防性维修策略优化

设备维护管理中的预防性维修策略优化随着科技的不断发展和工业生产的不断提高,设备维护管理在企业的运营中扮演着至关重要的角色。
而预防性维修策略是设备维护管理中的一个关键环节,它旨在通过定期检查和维护设备,来延长设备的寿命并减少故障率。
然而,如何优化预防性维修策略,仍然是一个值得关注和研究的问题。
本文将探讨设备维护管理中的预防性维修策略优化的方法和实施步骤。
第一步,了解设备运行状况和故障模式。
在优化预防性维修策略之前,我们首先需要了解设备的正常运行状况以及常见的故障模式。
这可以通过设备的历史维修记录和故障模式分析来获取。
通过了解设备的故障模式,我们可以针对性地制定预防性维修策略,将重点放在容易发生故障的部件或环节上。
第二步,制定适当的维修计划。
根据设备运行状态和故障模式的分析结果,我们可以制定适当的维修计划。
这包括计划维修的时间间隔、维修的内容和维修的方法等。
在制定维修计划时,我们需要考虑到设备的使用频率、工作环境以及设备制造商的建议,以确保维修计划的合理性和可行性。
第三步,利用预测性维修技术。
预测性维修是一种利用先进的监测和诊断技术来预测设备故障的方法。
通过监测设备的关键参数,如温度、压力等,我们可以及时发现设备的异常变化,并进行相应的维修工作。
预测性维修可以减少计划性维修的频率,提高维修效率,同时也能够避免由于设备故障造成的生产停工和生产损失。
第四步,利用信息化技术管理维修工作。
随着信息化技术的发展,现代企业可以利用计算机系统和软件来管理设备的维修工作。
通过建立设备维修管理系统,我们可以实现对设备维修工作的全面监控和管理,包括维修计划的制定、维修工作的安排、维修记录的管理等。
这样不仅可以提高维修工作的效率和准确性,还可以方便对维修工作进行分析和评估,从而更好地优化预防性维修策略。
第五步,培养设备维修团队的专业能力。
设备维修团队是设备维护管理中的关键环节。
只有具备一定的技术和专业知识,才能够对设备进行准确的诊断和维修。
预防性维修的机器学习模型与优化算法
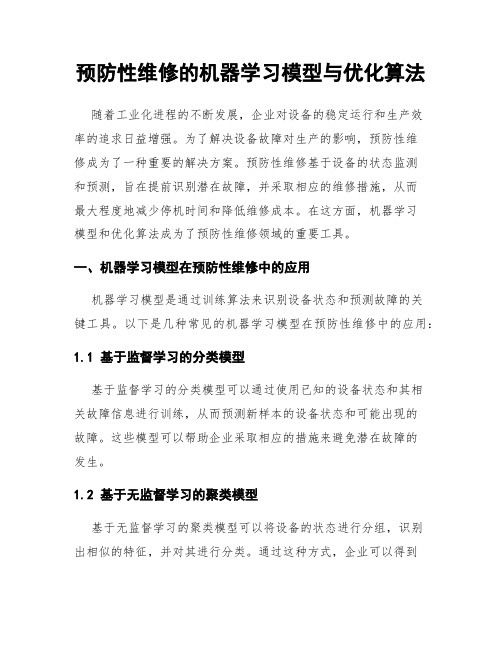
预防性维修的机器学习模型与优化算法随着工业化进程的不断发展,企业对设备的稳定运行和生产效率的追求日益增强。
为了解决设备故障对生产的影响,预防性维修成为了一种重要的解决方案。
预防性维修基于设备的状态监测和预测,旨在提前识别潜在故障,并采取相应的维修措施,从而最大程度地减少停机时间和降低维修成本。
在这方面,机器学习模型和优化算法成为了预防性维修领域的重要工具。
一、机器学习模型在预防性维修中的应用机器学习模型是通过训练算法来识别设备状态和预测故障的关键工具。
以下是几种常见的机器学习模型在预防性维修中的应用:1.1 基于监督学习的分类模型基于监督学习的分类模型可以通过使用已知的设备状态和其相关故障信息进行训练,从而预测新样本的设备状态和可能出现的故障。
这些模型可以帮助企业采取相应的措施来避免潜在故障的发生。
1.2 基于无监督学习的聚类模型基于无监督学习的聚类模型可以将设备的状态进行分组,识别出相似的特征,并对其进行分类。
通过这种方式,企业可以得到关于设备状态的更全面的认识,并根据这些分类结果来采取相应的维修措施。
1.3 深度学习模型深度学习模型是一种基于人工神经网络的机器学习模型,可以有效地处理大规模和复杂的数据。
在预防性维修中,深度学习模型可以通过学习大量的设备数据来发现潜在的故障因素,并提前预测出故障的可能性。
二、优化算法在预防性维修中的应用优化算法是将数学和统计技术应用于设备维修优化的关键工具。
以下是几种常见的优化算法在预防性维修中的应用:2.1 维修时间优化算法维修时间优化算法可以通过分析设备的历史数据和维修记录,识别出维修所需的时间分布模式,并根据设备状态的不同选择最佳的维修时间。
这样可以最大程度地减少停机时间,提高生产效率。
2.2 维修成本优化算法维修成本优化算法可以通过综合考虑设备维修成本、零部件和人工成本等因素,确定最经济的维修策略。
这可以帮助企业降低维修成本,并提高资金利用率。
2.3 调度优化算法调度优化算法可以通过优化设备维修的顺序和时间,使得维修工作能够最大限度地利用资源,并最大程度地减少停机时间。
设备预防维修和生产计划集成优化模型

...
z =1
f j (t ) = f (t + ∑ T − ∑ α z T ) = f (t + ∑ (1 − α z )T )
z =1 z =1 z =1
j −1
所以第 j 个维修周期内设备发生故障的次数为 :
λ j = ∫ f j (t )dt = ∫ f (t + ∑ (1 − α z )T )dt
1.2
f 3 (t ) = f (t + T − α 1T + T − α 2 T ) = f (t + ∑ (1 −α z )T )
2
参数说明
Cd : 设备进行一次预防维修所需费用 ; 设备进行一次故障维修所需费用 ; Cf : f (·): 设备的故障概率密度函数 ; F (·): 设备的故障分布函数 ; T: 第 j-1 次和第 j 次预防维修之间的时间间隔 ; 第 j 个周期的役龄回退因子,每个 Tj 结束后设 αj :
1
1.1
模型假设、参数说明和问题描述
模型假设
工程合同文书、变更事宜、合同费用演变等管理软件。 承包合同,二是严格履行合同条款。 作为国际项目的人员,更加要努力学习软件的应用,达 到国际项目的业务水平,为公司今后的发展提供更有力 的支持和帮助。 国际项目的顺利进行任重而道远,国际项目和国内 的项目还是有着很大的区别,我们目前所做的东西可能 还远远不满足不了国际项目的要求,在未来的日子里, 我们要对国际项目所涉及到的事宜要更进一步的分析和 学习,逐步的完善国际项目的顺利展开。
收稿日期: 2017-03-22 湖南省长沙雨花区香樟路16号博远大厦 通讯地址: A座1609 (410001)
5
按国际惯例解决项目承包中的争议问题
预防周期不同的最佳系统预防性维修优化模型
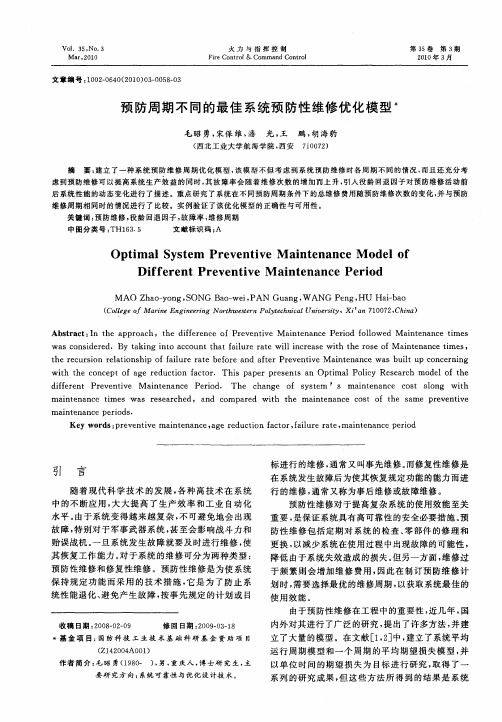
预 防周 期 不 同 的最佳 系统 预 防性 维修 优化模 型
毛 昭勇 , 宋保 维 , 潘 光, 王 鹏 , 海豹 胡
70 7) 10 2 ( 北 工 业 大 学航 海 学 院 , 安 西 西
摘 要 : 立 了一 种 系统 预 防 维 修 周 期 优 化 模 型 , 模 型 不 但 考 虑 到 系 统 预 防 维 修 时 各 周 期 不 同 的 情 况 , 且 还 充 分 考 建 该 而 虑到 预 防维 修 可 以提 高 系 统 生 产 效 益 的 同 时 , 故 障 率 会 随着 维修 次数 的增 加 而 上 升 , 入 役 龄 回 退 因 子 对 预 防维 修 活 动 前 其 引 后 系统 性 能 的动 态 变 化 进 行 了描 述 。重 点 研 究 了系 统 在 不 同 预 防 周 期 条 件 下 的 总维 修 费 用 随 预 防 维修 次 数 的 变化 , 与预 防 并 维修 周 期 相 同时 的 情 况 进 行 了 比较 。实 例 验证 了该 优 化 模 型 的正 确 性 与可 用 性 。 关 键 词 : 防维 修 , 龄 回退 因 子 , 障 率 , 修 周 期 预 役 故 维
m a n e a e p ro . i t n nc e ids
ቤተ መጻሕፍቲ ባይዱ
Ke r y wo ds: e e i i t n nc a e r du ton f c o f iu e r t ma n e n e p rod pr v ntve ma n e a e, g e c i a t r,a l r a e, i t na c e i
V0 . 3 。 . 1 5 No 3
Ma ,0 0 r2 1
火 力 与 指 挥 控 制
FieCo to r n r l& Co mma d Co to n n rI
构建预防性维修年龄维修策略模型

【 关键词 】 定期维修 ; 可用度 ; 备维修 设 【 中图分类 号 】 TH7 7 【 文献标志码 】 A 【 文章编号 】0 7 5 0 20 )8 1 1 4 10 —7 1 (0 7 0 —0 0 —0
Es abls ng Age M a nt nanc t i hi i e e Polc o lf r t axi um i y M de o he M m Avaia lt e c lE qui l bi iy of M di a pm e nt
A h — ig, Z A i pn ̄ , O Qi  ̄ N Z i pnJ , H O L — ig一 A o n
( . u i n r l s ia o n h uAraC mma d Ur mq Xija g80 0 , ia 2 S aeKe b r tr r 1 Ur mq ea ptl f Ge Ho La z o e o n , u i nin 3 0 0 Chn ; . tt yLa o ao yf o
Ab t a t s r c :An l z s t e t a i i n lr g l r y m a nt na e mo e o a y e h r d to a e u a l i e nc d f me i a q i m e t d c le u p n .Ex e sv r i s f i i nt c s i e o n u fc e m a n i— t n n e e i t d e t h a nt n nc l n a r t e o e a i n tm e o h q i m e e a c x s u o t e m i e a e p a s pe h p r to i f t e e u p nt.St d e ,t e e o e,h w o r u is h r f r o t a — r n e t e p e e i n m a n e n e wo k r a o a l n p i i e t a nt na c r c s t e s h d a g h r v nto i t na c r e s n b y a d o tm z he m i e n e p o e s wih l a t s ut own tm e a — i c c r i g t he m a nt n nc h r c e i tc q i m e t o d n o t i e a e c a a t r s i sofe u p n .An u s f r r n a d p t o wa d a ge— m a n e a c o i y mo e t — i t n n e p l d lwi h e c
设备预防性维修优化模型及方法分析

设备预防性维修优化模型及方法分析一、引言在现代工业生产中,设备的正常运行对于企业的生产效率和竞争力至关重要。
然而,设备出现故障和停机时间是无法避免的。
为了降低设备故障和停机时间对企业造成的损失,预防性维修策略被广泛应用。
本文将分析设备预防性维修的优化模型和方法,以提供一种有效的解决方案。
二、设备预防性维修的概述设备预防性维修是在设备故障发生之前,通过定期维护和检修,以预防设备故障和提升设备的可靠性。
这种维修策略可以有效地减少设备故障次数、延长设备的寿命,并降低设备维修和停机时间所带来的成本。
三、设备预防性维修优化模型1. 维修决策模型维修决策模型是设备预防性维修优化的核心。
常见的维修决策模型包括确定维修时机和维修策略的模型。
- 维修时机模型:维修时机模型用于确定设备维修的最佳时间点。
根据设备的运行状态、维修成本和停机成本等因素,可以利用概率统计和数学模型来计算最佳维修时机。
- 维修策略模型:维修策略模型用于确定设备的维修策略。
常用的维修策略包括定期检修、故障检测和预防性更换等。
通过对设备的运行状态和维修历史数据进行分析,可以选择最适合的维修策略来减少维修成本和停机时间。
2. 故障预测模型故障预测模型是设备预防性维修优化的重要组成部分。
通过对设备的运行数据和维修历史数据进行分析,可以建立故障预测模型来预测设备的故障概率和剩余寿命。
常用的故障预测模型包括可靠性增长模型、故障模型和生存分析模型等。
这些模型可以根据设备的运行状态和维修历史数据来计算设备的故障概率和剩余寿命,从而提前采取维修措施。
3. 维修策略评估模型维修策略评估模型用于评估不同维修策略的效果和成本。
通过建立评估模型,可以比较不同维修策略的优缺点,并选择最佳的维修策略。
常用的维修策略评估模型包括成本效益分析模型和风险评估模型。
这些模型可以根据设备的维修成本、停机成本和故障风险等因素,计算不同维修策略的成本和风险,以帮助企业选择最合适的维修策略。
系统预防维护风险-成本优化模型的研究

Cne af l i d假设 系统进行 预防维护后会 减少操作应力 ,当系统在年 龄t 时经过维护后 ,将会恢复到年龄到 tT时的状态 。以后人们 —
针对许多涉及到改善 因子的维护优 化模 型进行 了研究 :Jybl aaaa n a dC ad u n hu h n,LeadC u ,S rs n h h 6 i n h n ueha dC a u 。多 数 是 对 n Ma k改善因子概念 的发展和延伸。纪冠 安受 Mak模型 的启发 , i l i l 提 出用以维护周期 、维护次数 、维护费用为参数 的改善因子函数
约束性条件 ,本文在满足最低可靠性 的条件下 ,针对三种维护方
式 ( 最小修复 、预 防性维护 和预防性更换 ) ,建立老化系统 的维 护成本的优化模型 ,同时考虑恢复因子 的影响因素。
三 、数 学 模 型
修复成本和停 机利润损失成本 ,建立优化模 型 ,目标 函数是一定 使用 时间内,在最低可靠性约束条件下 ,总的维护成本最小 。由
本文针对不能进行 自动预警的系统 ,参 照 Jyb l aa a n曾提 出 a
的简单预 防维护和预防性更换的概念 ,对系统进行不完全 的预 防 维护和纠正维护 ( 更换) ,即在达 到可靠性 水平 下限时 ,进行预 防性更换 ,而 在两次预 防性更 换之 间进 行预 防性 维护和 最小修 复 ,涉及到的维护成本有预防性更换成本 ,预防维护成本 ,最小
二 、 文献 回顾
系统维护管理 ,以其在生 产活动 中的运动链 和价值链 中关 键地位 越来越 受到关 注 , “ 护是对 未来 的投 资 ” “ 维 、 维护 是 制造业 的最后一、 维
维护工作重要性 的认识 。人们 对维护策 略 、维护模 式也做 了大 量的研究 ,将维护活 动从维护 时机上分 为预防维护 (r et e Pe n v v i
预防性维修

传统的预防性维修(定期维修)适用于故障多、难维修、费用高、需改善性能(特别是安全性)、延长使用 寿命的设备,如电梯、车辆、消防设备等,这种维修方式的局限性在于:
(1)即使进行预防性维修,也会发生某种程度的故障,而且不能保证实施预防性维修后实际故障率一定能下 降;
(2)维修周期由统计方式确定,所以常会造成维修过度,以致造成资源浪费的情况出现; (3)对于复杂机械设备维护效果差,适用于磨耗故障,而使设备的使用效率降低的情况; (4)因定期维修而造成的停产会对企业造成很大的经济损失。 由此可见,定期维修是按照一定的周期无条件进行修理、更换,虽然这样做简单而有效,但由于长期提前修 理、更换,增加了企业成本、降低了企业竞争力。为了适应企业竞争环境的变化,更高级的预防性维修被提出。
状态维修是对系统设备采取一些状态检测技术,例如:振动监测技术、滑油技术和孔探技术等,将系统设备 可能发生功能故障的各种物理信息进行周期性检测、分析、诊断,根据对物理信息的分析推断出系统设备当前所 处的运行状态,系统设备的运行状态的发展情况为依据安排必要的预防性维修计划。
由上可知状态维修是一种利用传感器、监测技术和故障诊断技术以分析、评估设备运行情况,并判断设备维 修需求的维修方式。状态维修有两种方式:点检状态维修和远程监测状态维修;前者由检测人员利用简易检测设 备定期检查,后者依靠设备中嵌入监测系统自动采集设备运行数据并对故障趋势进行分析。状态维修的要点在于 状态监测和故障识别,因此,其对设备的监测和诊断技术有较高要求。
主动维修是寻求系统设备故障产生的根源,例如:润滑介质理化性能的降低、油液污染度变大及环境温度的 变化等进行识别,主动采取一些事前的维修工作,将这些导致故障的因素控制在一个合理的水平或者强度W内,来 预防系统设备进一步的发生故障或者失效。
多产品生产系统的生产与预防维修综合计划优化模型

多产品生产系统的生产与预防维修综合计划优化模型刘昊;吕文元;刘勤明【摘要】生产与维修是制造业最重要的活动并共用企业设备资源,因此合理协调二者关系是企业控制成本的关键.使用时间延迟维修模型模拟设备老化和维修过程,将某一特定的计划周期等分成若干个生产阶段,考虑每个阶段的生产、库存、延期未交货、不合格产品成本、故障维修活动,以及周期性的预防维修活动,建立总成本模型.通过对案例进行分析阐明此模型,旨在求解出最佳预防维修间隔时间和各阶段各产品产量,得出最佳的生产和维修综合计划.%Production and maintenance are the most important activity in manufacturing and they share the enterprise's equipment, so coordinatingthe relationshipproperly between them is the key to controlling total costs.The aging and maintenance process of equipment is simulated by using delay-time model and the specific production horizon is divided to several periods.Considering the production, inventory, backorder costs, unqualified products costs, device failure maintenance and periodic preventive maintenance, the total costs model is established.An example using real data is presented to illustrate the model and the objective is to find the optimal number of production quantities of each product per period and the interval of preventive maintenance so that get the optimum comprehensive planning.【期刊名称】《科技和产业》【年(卷),期】2016(016)011【总页数】8页(P114-120,158)【关键词】生产计划;预防维修;时间延迟模型;停机时间【作者】刘昊;吕文元;刘勤明【作者单位】上海理工大学管理学院, 上海 200093;上海理工大学管理学院, 上海200093;上海理工大学管理学院, 上海 200093【正文语种】中文【中图分类】F273.4;TB472企业生产计划是指在一个特定的生产周期内,能够满足客户需求的同时,使得生产设备得到最充分的利用的计划。
以预知性为主的预防维修管理体系
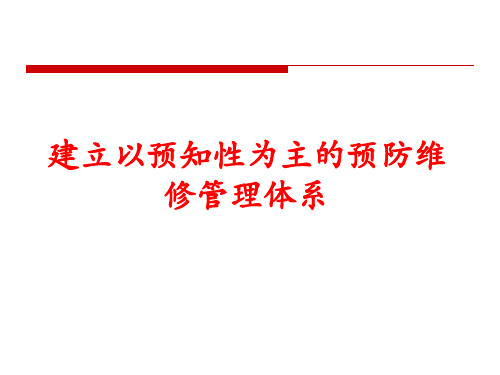
4、大修管理
大修准备、执行和重启 目标:
组织管理主机大修(窑、磨机等)并达到之前确定的所有 目标(安全、成本、时间进度表与技术目标) 严格遵守大修的十大黄金法则: (1)停窑日期必须至少要在3~4个月之前被确定 (2)实施的工作内容决定于日常的巡检活动,故障根本 原因分析的结果,检修的总结及改进提高的项目,根据下 次的生产运行的持续时间评估某些备件更换的需要。 (3)为了最大的优化检修持续时间及成本,应该限定计 划检修期间的工作范围。
如果你在某一段时期后进行恢复(预防性维修)
设备和组件 状况
零件更换
时间
预防性维修特点
特点: * 以时间为基础的、系统性的; * 计划、组织更好,减少了时间上的损失; * 绝大部分故障能在发生前进行处理: * 设备性能大大提高; * 预防性计划的编制有些要依赖于技术管理人员 的直觉与经验,依赖于设备的平均无故障时间。
1、 事后维修
事后维修也称故障性或纠正性维修,就是当设备发生故障 后所进行的维修,设备发生故障或性能降低后,通过恢复 性维修使设备能够暂时运行,并最终使设备恢复至正常状 态所进行的一种维修工作。 特点为: * 设备可靠性差 * 设备效率低 * 增加加班时间 * 需要的备件库存大 * 成本高 * 对产品质量产生负面影响
如果你等到机器出现故障才维修(事后维修)
设备和组件 状况
损失时间
零件更换
时间
维修的四种类型及特点
2、预防性维修 是一种系统性的、预先排定的检查、测验及监 控程序,目的在于防止早期故障、增加可靠性,同 时延长设备的经济寿命。 预防性维修有定时更换、修理的方式和定期检 查并根据检查结果来安排近期的检修计划的方式, 后者是我们常用的。
预防维修优化模型及其在数控设备维修中的运用

244研究与探索Research and Exploration ·理论研究与实践中国设备工程 2020.12(上)预防维修优化模型及其在数控设备维修中的运用黄春武,张凤兰(江西志骋汽车有限责任公司,江西 九江 332005)摘要:本文主要以预防维修优化模型及其在数控设备维修中的运用为重点进行阐述,结合当下数控设备维修工作进行情况为依据,首先分析预防维修方式设定,其次介绍预防维修优化模型,再次深层次说明并探讨预防维修优化模型及其在数控设备维修中的运用思考,最后阐述数控设备维修发展方向,进而提高数控设备维修效果,凸显预防维修优化模式效用和价值,意在为相关研究提供参考资料。
关键词:预防维修;优化模型;数控设备;维修运用中图分类号:TH162 文献标识码:A 文章编号:1671-0711(2020)12(上)-0244-02科学的预防维修可以凭借最小的资源消耗维持设备自身运作能力,结合事前要求的方案或者技能标准加以维修,控制设备性能退化的情况出现,减少设备失效概率。
作用在出现故障会引发重大经济损失的场合中,数控设备可以理解是典型系统之一。
现阶段数控设备的维修管理依旧表现些许问题,包含维修手段单一化、无法保障设备故障维修的及时性或者设备运作效率低下等。
而延迟时间模型可妥善解决上述问题,形成完整的维修优化模型,明确确切的维修检查时间,保障单位时间内设备总停机时间期望数值实现最小化,最终落实维修决策设计。
针对预防维修优化模型及其在数控设备维修中的运用,如下是笔者给出的具体分析与建议。
1 预防维修方式设定针对预防维修,即将有可能引发设备故障与解决设备故障难度大的条件进行排除,基础化的维修手段是立足于运行时间实施定期维修与立足于系统运作状态实施监控维修。
现阶段企业针对设备时常采取预防维修的方式,一个因素是计划维修理念根深蒂固,各个企业均获取一定经验;其次是状态维修停留在维修发展过程,然实施不只是要引进专业技术人员的培训过程,还要思考到采集器等一系列昂贵仪器的采购,费用比较大,一般企业不能承担起经济负担;最后是因为预防维修能够提前设置在非生产时间阶段进行,控制停机带来的经济损失。
基于GA_PSO的系统预防性维修策略优化模型

科学技术创新2020.33基于GA_PSO 的系统预防性维修策略优化模型曹运龙郭文兵杨伟强(河南理工大学,河南焦作454003)1概述当前制造企业急需思考的一个问题,如何保证对复杂的制造系统进行维护时,以确保其可靠性、经济性和安全性。
目前,大多数维护都是在事后,当系统发生故障了才会去维护,这种方式暴露着效率低、成本高等问题。
与过去相比,可靠性现在是一个更加令人关注的问题,因为现代工程和制造系统的日益复杂性和自动化程度逐渐提升,已导致其对故障的敏感性急剧增加。
提升系统的可靠性方法有各组件可靠性的提升;并行安装冗余组件;将各组件和安装冗余组件结合;用可替换的组件进行替换。
如何快速建立竞争性质量体系是值得思考的问题。
这就要求企业必须以最快的生产速度、低生产成本、高质量产品来占据市场。
考虑到生产系统的复杂性和多变性,这就要求生产系统能够做到低维修次数,生产出高可靠性产品。
所以必须对生产系统做出预防性维修,为决策者提供优化策略。
预防性维护策略研究最先由M o r imu r a [1]提出,其最重要工作是需要对前N 个故障进行少量维修,并在N 次故障后进行等效更换。
对于预防性维护的研究中,有研究维护与设备的状态的联系、维修与维修成本的关系以及维修与决策的关系[2]。
对于维修与设备的关系一般用寿命的减少[3-5],失效概率减少和功能的退化方法概述[6-8]。
预防性维修策略由预防的类型和预防的次数共同决定的。
它也决定了系统在运行中的可靠性,因此合理的制定系统的预防性维修准则,直接影响系统的是否达到设计的经济性和可靠性。
综上所述,为了制定有效的预防性维修策略,从而避免系统因为反复的维修而降低可靠度和增加维修成本;在系统发生反复故障之前进行预防性的维修,由此来减少系统随时发生故障的次数。
本文旨在研究预防性维修活动与系统故障率与可靠度之间的关系,构建设计费用、维修费用、制造费用、待工费用函数,以系统故障维修成本最小为目标函数,以系统的可靠度为决策变量的模型,最后引入遗传-粒子群算法对模型进行优化求解。
预防维修周期的一种多目标最优化模型

成本率最小和设备可用度最大的各维护周期最优预
防性 维护 时 间间 隔. 方 法 较 为 复杂 ; 该 杜凤 娥 , 立 刘 伟 [针对在 工 程实 际 中 往往 会 遇 到 在 给定 的造 价 、 7 ]
对于故障小修的周期维修策略l , 2 曹晋华 、 ] 程侃 讨论忽略小修和更换时间时的平均费用率和考虑小
p e e t e man e a c y l sd t r ie .Fial r v n i i tn n e c cewa ee m n d v nl y,ae a l sgv n t l sr t u e irt ft e x mp ewa ie o i u ta es p r i o h l o y
关键词 :故障小修 ;预 防维修周期 ;极小一 极大法;多目标最优化 中图分类号 : 1. ;O2 1 6 O2 3 2 2 . 文献标识码 :A
A mut ojcieo t z t nmo e f rvniemane a c y l l -bet p i ai d l ee t itn n ec ce i v mi o op v
rp i t n rv niema tn n et ,amut o jcieo t z t n mo e o rv n iemane e ar i a d pe e t i e a c i me v n me l— bet pi ai d l fp e e t it— i v mi o v
i dcs h n yu ig“ nma ”a po c ov emut o jcie pi zt nmo e,S a t i i .T e ,b s sn e n mi- x p r aht s le h l— bet t ai d l Ot t o t i v o mi o h a
预防性维修模型及其更换策略应用研究

预防性维修模型及其更换策略应用研究作者:焦健张雷张永军来源:《卷宗》2015年第02期摘要:企业高效、安全生产离不开设备的科技性和可靠性,而确保设备高度可靠性则依赖于设备管理和维护水平。
设备故障发生时间、失效类型、频率及其对设备效能造成的影响,是维修理论研究模型基础;对设备故障规律的研究和掌握是现代设备管理理论及实践的核心。
本文即是以局部失效或故障即可引起全系统停止运行的流程型生产系统为研究对象,在可靠性理论的指导下,对预防性维修优化模型及其更换策略的应用进行研究。
关键词:预防性维修;更换策略;体系优化;应用研究1. 引言设备管理,根据企业运营、生产目标,以设备为研究对象,确立最高目标为追求设备寿命周期费用最经济和设备OEE最高效,基于可靠性理论、维修理论、应用系统工程学、状态检测、故障诊断技术及管理学等理论,通过一系列技术、经济组织措施,对设备从规划、设计、制造、选型、采购、安装、运行、管理、维修、保养、改进、更新直至报废的全寿命周期进行管理[1]。
维护优化模型即致力于找寻维护成本和收益之间的最优平衡、且同时兼顾其它限制条件的数学模型[2]。
在企业维修过程中,常存在欠维修或过维修现象,这就需要运用科学管理对维修工作进行合理规划、安排、监督和优化。
维修理论研究的就是设备在整个寿命周期内的与维修相关的规律,包括维修性设计、维修技术、维修管理等。
其核心在于保持和恢复设备运行可靠性,兼具设备及其部件的可靠性状况,应用逻辑决策分析方法制定设备的维修大纲,确定所必需的维修内容及合理的维修类型、恰当的维修时间及维修方法,从而达到优化维修之目的。
在该理论指导下开展设备维修工作,既可以提高设备可靠性亦可降低维修成本,经多年生产实践检验,逐渐得到了广泛认可并且被付诸拓展。
2.几种典型的预防性维修和更换策略模型总系统的可靠性在很大程度上受其结构设计、质量和构成它的部件的可靠性影响,但系统的可用率除了受以上因素影响外,在某种程度上还取决于有效的维修保养和检测工作。
不完全预防维修的维修任务间隔优化方法的分析

不完全预防维修的维修任务间隔优化方法的分析作者:孙鹤来源:《科学与技术》 2019年第1期摘要:文章首先分析了主要的维修类型,包括预防性维修、事后维修和改进性维修等,随后文章介绍了维修任务可变间隔的优化设计,包括确定维修任务来源、问题描述、模型假设、明确维修改善因子、维修成本分析等,希望能给相关人士提供一些参考。
关键词:不完全预防;维修任务;间隔优化引言民航作为一种传统的交通领域,在现代化的经济发展形势下,能够发挥出巨大的引导作用,推动地区的产业发展升级,对于国家的发展也具有重要的影响。
同时在航空运输的引导下还能促进全球经济有机融合。
为了促进我国相关领域行业的竞争力与主导力的全面提升,应该进一步提高飞机的维修水平,促进民航的快速发展。
一、主要维修类型(一)预防性维修结合预防性维修的最终效果分析,我们可以将其划分成三种类型,分别是最小维修、不完全维修和完全维修。
其中最小维修就是对于系统部件中的改变状态几乎会和故障发生前一致,因此也被叫做修复如旧。
完全维修就是维修活动后,部件能够恢复到初始状态,也叫做修复如新。
不完全维修就是一种完全维修与最小维修之间的类型,符合维修设备的现实失效状况和老化特征,因此不完全维修的适用性也比较强,在现实民机维修过程中,占据较大比例的就是预防性维修。
(二)事后维修事后维修就是故障问题出现后实施的一系列维修行为,也可以叫做故障维修。
因为故障拥有一定的不可控性质,因此事后维修时间也是无法预知的,在设备发生问题后,或是故障影响设备运行时,应该立刻开始事后维修。
因为这种维修方式存在较大的不可控性,因此应该尽量避免这种故障问题的发生。
维修活动的增多在一定程度上也会对正常的经营活动和生产计划造成一定的影响。
(三)改进性维修改进性维修就是在结束设备维修工作后,为了提高设备安全性与可操作性等作用而进行的一系列改装活动,能够促进设备可靠性和使用性能的有效提升,其本质是修改产品设计。
二、维修任务可变间隔的优化设计(一)确定维修任务来源随着科技的发展,现代化的维修思想也不断创新,目前主要是一种可靠性思想和MSG-3维修思想相互融合的维修思想,是一种比较科学的现代化维修思想。
预防性维修培训PPT课件

30/61
中国名牌产品
国家免检产品
如何润滑
设备润滑管理五定:
五定
内容
定点
确定每台设备的润滑部位和润滑点,实施定点给油。
定质
按照润滑规定的油脂用油,润滑材料。
定量
在保证良好润滑的基础上,实行日常耗油和定量换油。
定期 定人
按照润滑规定的周期加油、添油和清油。 确定润滑责任人。
31/61
中国名牌产品
国家免检产品
数量/台
安装部位
2
主传动箱(常备)
1
主传动箱(3-5年)
1
主传动箱(3-5年)
2
主传动箱(1年一换)
2
主传动箱(半年一换)
1
可堆焊
1
可堆焊
2
(半年一换)
2
(1年一换)
17/61
中国名牌产品
国家免检产品
制粒机之设备易损件
图号
定货号
名称
60
4-5043-00
吸振蝶型弹簧片
10.03 10.05 10.04 20.01 20.02 10.01 40 20 100.01
中国名牌产品
09.02.02.
抱箍 耐磨衫圈
08.12.20. 开裂补焊
09.01.22 (更换新的)
更换新的 (09.01.22)
16/61
中国名牌产品
制粒机之设备易损件
图号 定货号
名称
190 260 50.02 50.03 100.02 90 110 120 130
5-0915-10 安全销 5-5012-00 齿轴耐磨钢套 5-7347-03 主轴耐磨钢套 5-6512-00 压辊轴后铜衬套 0-1732-00 压辊轴前铜衬套 5-7288-02 内刮刀 0-3382-05 喂料外刮刀 5-1618-02 压辊调节螺丝 5-7099-06 压辊调隙轮
大型机械设备预防性维修模型构建

大型机械设备预防性维修模型构建一、引言随着工业化程度的不断提高,大型机械设备在生产中扮演着越来越重要的角色。
然而,这些设备的故障率极高,一旦发生故障,不仅会造成损失和停工,还会给工人的安全带来严重威胁。
因此,建立一套有效的大型机械设备预防性维修模型,成为了企业提高生产效率和降低成本的重要措施。
二、大型机械设备预防性维修概述1. 预防性维修的定义及优势预防性维修是指在机械设备运行良好的时候,按照制定的计划进行检修和维护,从而减少停机时间,延长机械设备使用寿命,增加设备的可靠性和安全性,提高生产效率和产品质量。
与其他维修模式相比,预防性维修具有以下优势:①能预测和避免故障的发生,从而保证生产的连续性和稳定性;②能减少机械设备损坏和停工对企业带来的经济损失;③能降低维修成本和延长机械设备的使用寿命;④能提高工人的安全保障,降低事故风险。
2. 大型机械设备预防性维修的策略大型机械设备预防性维修的策略主要有以下几种:①时间维修:按照一定的时间间隔进行检修和维护。
这种维修策略适用于设备运行正常的情况下。
②使用次数维修:按照设定的使用次数进行检修和维护。
这种维修策略适用于设备使用频繁的场合。
③状态维修:按照设备的运行状态进行检修和维护。
这种维修策略适用于设备运行环境比较恶劣的场合和对设备要求较高的场合。
三、大型机械设备预防性维修模型构建1. 预防性维修模型构建的意义大型机械设备预防性维修模型的构建,可以帮助企业科学、合理的制定维修计划,避免因维修不当而带来的额外损失。
同时,通过预测和评估机械设备的运行状态,可以实现设备的最大化利用,提高生产效率和产品质量。
2. 大型机械设备预防性维修模型构建的方法大型机械设备预防性维修模型的构建,主要包括以下几个方面:①数据采集与处理:采集机械设备相关的运行数据,如温度、压力、震动等,并进行处理和分析,形成完整的运行状态数据。
②运行状态预测:通过历史数据分析和数据模型计算,预测机械设备未来的运行状态和寿命。
多状态可修系统的最佳非完好预防维修策略

多状态可修系统的最佳非完好预防维修策略尹继东【摘要】针对多状态可修系统提出了一种预防性维修策略.假定系统存在多种状态,当系统每次的工作状态处于较差工作状态时,对系统进行预防维修,该预防维修视为"非完好维修",当预防维修次数达到N时,无论在下一个工作周期系统是否仍处于较差工作状态,系统将不再进行此预防维修.运用极大似然估计来估算系统元件的状态概率,借用通用生成函数的方法来获取系统各状态的概率值,将系统的工作时间描述为随机递减的几何过程,预防维修的时间描述为随机递增的几何过程,建立最优预防维修策略的数学模型,在确保系统单位时间内期望效益最大的条件下,给出最佳的预防维修策略值N?.【期刊名称】《机械研究与应用》【年(卷),期】2016(029)005【总页数】5页(P56-60)【关键词】多状态系统;极大似然估计;通用生成函数;几何过程【作者】尹继东【作者单位】西南交通大学数学学院,四川成都 611756【正文语种】中文【中图分类】O213.2;TB114.3在现代工业生产中,由于系统中元件的失效或性能的衰退而导致设备逐渐由性能高的状态转变到性能低的状态,同时系统会呈现非仅失效和正常工作的多状态特征,对于多状态系统,Tan等[1]以系统的状态和性能变化趋势来决定系统维修计划的制定,而不依赖系统中元件的状态,工业上也普遍采用Tan提出的这种方式,认为当系统的状态性能不能满足任务性能的需求时,定义系统处于失效状态,并对系统进行维修。
这类系统的相关维修策略的理论研究,有利于揭示系统衰退和维修措施对产品状态影响的潜在规律,从而具有重要的理论意义和经济价值。
然而,系统在工作过程中,为确保下个工作周期系统能顺利完成指定的任务,人们都会对系统采取不同程度的预防性维修措施。
在实际生产工作中,根据维修的程度和维修后系统状态性能恢复度,可分为最小维修“修复如旧”、完好维修“修复如新”以及非完好维修,即修复后系统的状态性能介于修复前的状态和全新状态之间。
- 1、下载文档前请自行甄别文档内容的完整性,平台不提供额外的编辑、内容补充、找答案等附加服务。
- 2、"仅部分预览"的文档,不可在线预览部分如存在完整性等问题,可反馈申请退款(可完整预览的文档不适用该条件!)。
- 3、如文档侵犯您的权益,请联系客服反馈,我们会尽快为您处理(人工客服工作时间:9:00-18:30)。
A()
1
1 ( c p )(t)
c p
2020/6/10
按有效度最大原则确定最佳间 隔期
当 c p ,而T=时,则
T
R(t)dt
A()
0 T
0 R(t)dt c
c p
也可将将式改写为
A() MUT1来自1MUT MDT 1 MDT / MUT 1
—维修系数
2020/6/10
2020/6/10
按有效度最大原则确定最佳间 隔期
若系统失效率函数为(t),则每一预防维修间隔期内平均 不能工作时间(Mean Down Time)为:
T
MDT p c 0 (t)dt
T
式中 (t)dt 为一个间隔期间故障发生的比例。 0
稳态有效度为:
A()
MUT MUT MDT
T
T
(t) R(t)dt [1 R(t)]
p
0
c p
移项后得:
T
(t) R(t)dt R(t)
p
1
c
0
c p
c p
2020/6/10
按有效度最大原则确定最佳间 隔期
由于上式左边为正值,因此,右边以及式应有 的条件,这正式损耗失效期的特征。因此,若失效率函 数(t)是t的递增函数,可按式子求得有效度最大的带有更 新事后维修的预防维修间隔期的最佳值T,将式代入式后 可得到有效度为
MUT
MUT
C p R(T )
T
Cc [1
R(T )]
0 R(t)dt
求解和前面一致。
2020/6/10
根据可靠性要求确定维修周期
根据可靠度要求确定维修周
可靠度R(t)是时间的递减函数,根据系统或元器件使用到一定时 间的可靠寿命要求确定其维修周期,即可靠寿命维修周期。
当寿命分布服从指数分布时,即 R(t) et ,若要求的可靠度 R(T)=r,则
2020/6/10
按总费用最小原则确定最佳间 隔期
带有更新型事后维修的预防维修间隔
在系统平均可能工作时间(MUT)内,要承担预防维修费用
Cp及事后维修费用Cc,而预防维修与事后维修的比率分
别为R(t)与[1-R(t)],因此,系统在单位工作时间内的平均、
费用为 CT C p R(T ) Cc[1 R(T )]
时刻t的可靠度值时,则可绘出可靠度曲线,平滑后其下
面的面积,则得到
T
0
R(t
)dt
的近似解,可列表计算,找出
与min对应的t值即是T的最佳值。
当(t)= =const时,
T et dt 1 eT
0
et
|T0
1 eT
0 p c p
即得 p 0 说明在偶然失效期或指数分布时,由于(t)=
=const,故不需维修。
按有效度最大原则确定最佳间 隔期
MDT MUT
R(T ) p [1 R(T )] c
T
R(t)dt
0
显然,是时间t的函数,由式可知,使为最小时A()为 最大,亦可由此求得带有更新型事后维修的预防维修间 隔期的最佳值T。
2020/6/10
按有效度最大原则确定最佳间 隔期
在实际解题中,若已知 c p 值,并测得系统在不同
T p c
T
(t )dt
0
2020/6/10
按有效度最大原则确定最佳间 隔期
为了求得A()为最大的最佳维修间隔时间T值,可采用微 分方法,取dA/dT=0,得
T(T ) T (t)dt p
0
c
因为
T(T )
T 0
(t )dt
[t (t )]T0
T
(t )dt
0
T
td(t)
MDT R(T ) p [1 R(T )] c
式中:R(T ) 为T小时的系统可靠度
稳定有效度为:
T
A() MUT MUT MDT
R(t )dt
0 T
0 R(t)dt R(t) p [1 R(t)] c
2020/6/10
按有效度最大原则确定最佳间 隔期
同样,令dA/dT=0,求得有效度最大的最佳维修间隔期T 应满足的条件为
R(t) et r
ln r T
预防维修间隔时间T。
2020/6/10
按有效度最大原则确定最佳间 隔期
带有更新型事后维修的预防维修间隔
T
p T1 c T
p
故障 更新
每一预防维修间隔期内的平均可能工作时间MUT为:
T
MUT 0 R(t)dt
2020/6/10
按有效度最大原则确定最佳间 隔期
平均不能工作时间MDT为 p 与 c 的加权和:
2020/6/10
按总费用最小原则确定最佳间 隔期
带有修理型事后维修的预防维修间隔 带有更新型事后维修的预防维修间隔
2020/6/10
按总费用最小原则确定最佳间 隔期
带有修理型事后维修的预防维修间隔
若将从预防维修到间隔期T结束为止的总费用记为CT,则 单位工作时间内的平均费用为
CT C p Cc
T t' (t)dt
0
0
2020/6/10
按有效度最大原则确定最佳间 隔期
故得
T t' (t)dt p
0
c
因为 p / c 是一个大于零的正值,故由上式可知,只有 当 ' (t) 为正值或 (t) 为递增型函数时才有解,由此
可见,只有当系统的失效是属于耗损型失效时,预防维
修才是有效的,并可由前面式子求得有效度最大的最佳
带有修理型事后维修的预防维修间隔
T
p T1 c T2 p
故障 修复
T — 预防维修间隔时间; p — 平均预防维修时间; c — 平均事后维修时间;
T1 —尚未满预防维修间隔期但发生故障的时间; T2 — 为修复后继续工作的时间; T1 T2 T(平均可能工作时间MUT, Mean Up Time)
T
(t )dt
T T T0
d 为了求得使CT/T 为最小的T值,可令 T
CT T
0
,则
得到最佳维修间隔期应满足的条件为:
2020/6/10
T(T ) T (t)dt Cp
0
Cc
按总费用最小原则确定最佳间 隔期
带有修理型事后维修的预防维修间隔
或
T t' (t)dt Cp
0
Cc
将以上两式分别与式及式比较,变可发现,若维修时间 与费用成比例,则两者的最佳解是一致的。但偶然损失 不一定与时间成比例。
系统预防维修间隔期的确定
2020/6/10
主要内容
按有效度最大原则确定最佳维修间隔期 按总费用最小原则确定最佳维修间隔期 根据可靠性要求确定维修周期
2020/6/10
按有效度最大原则确定最佳间 隔期
带有修理型事后维修的预防维修间隔 带有更新型事后维修的预防维修间隔
2020/6/10
按有效度最大原则确定最佳间 隔期