12000船体焊接原则工艺
2船体焊接原则工艺规范
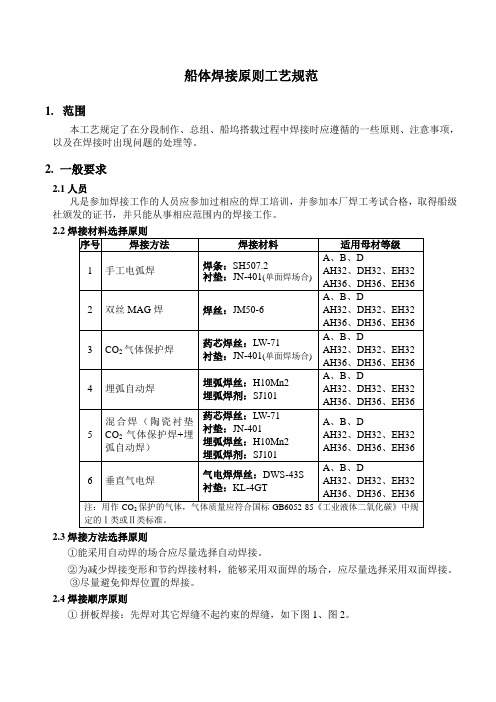
船体焊接原则工艺规范1.范围本工艺规定了在分段制作、总组、船坞搭载过程中焊接时应遵循的一些原则、注意事项,以及在焊接时出现问题的处理等。
2.一般要求2.1人员凡是参加焊接工作的人员应参加过相应的焊工培训,并参加本厂焊工考试合格,取得船级社颁发的证书,并只能从事相应范围内的焊接工作。
2.22.3焊接方法选择原则①能采用自动焊的场合应尽量选择自动焊接。
②为减少焊接变形和节约焊接材料,能够采用双面焊的场合,应尽量选择采用双面焊接。
③尽量避免仰焊位置的焊接。
2.4焊接顺序原则①拼板焊接:先焊对其它焊缝不起约束的焊缝,如下图1、图2。
⑦⑥⑤④③②①图 2图 1⑥⑤④③②①十字接缝的场合,应先焊横向对接缝,再焊纵向对接缝,如下图3。
图 3②①② 工艺孔封板焊接顺序,如下图4。
图 4③ 在构架和板缝相交的情况下,既有对接也有角接缝。
此时应先焊接对接缝,然后再焊角焊缝。
④ 当分段、总段焊接时,尽可能由双数焊工从分段中部逐渐向左右,前后对称地施焊,以保证结构件均匀地收缩。
⑤ 处在大接头同一端面的各种构件,应先焊大接头的对接焊缝,再焊其他构件的对接缝,后焊其它构件的角焊缝,以利于减少大接头中的残余应力。
2.5 环境为保证焊接质量,进行CO 2气体保护焊时当周围的风速大于2米/秒时应采取防风措施(如:加挡风板)。
雨雪天气或空气相对湿度大于80%时应采取相应的保护措施(如:挡雨棚或移至室内进行焊接工作。
)否则一律不得进行焊接。
在焊接时焊接人员应佩带相应的防护用品,(如:焊接面罩、口罩等)。
3. 焊接3.1 焊前准备3.1.1坡口加工零件边缘加工时,坡口应根据设计部绘制的《切割板图》进行切割,在焊接前,焊接人员应检查坡口是否符合《分段制作图》要求,对于坡口漏开或不符合图纸要求,应根据《分段制作图》进行补开坡口或坡口修正。
特殊情况下可根据《船体结构坡口形式选用规定》进行开坡口。
坡口加工可采用火焰切割、等离子切割,少量的坡口可采用碳弧气刨。
(完整版)建造船舶船体焊接工艺
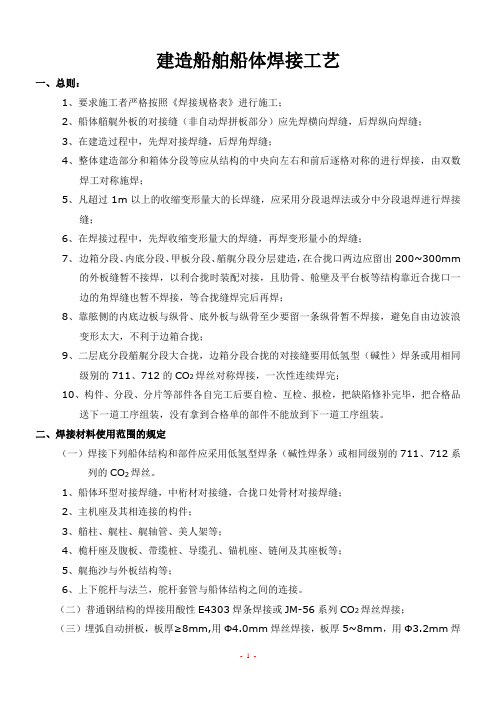
建造船舶船体焊接工艺一、总则:1、要求施工者严格按照《焊接规格表》进行施工;2、船体艏艉外板的对接缝(非自动焊拼板部分)应先焊横向焊缝,后焊纵向焊缝;3、在建造过程中,先焊对接焊缝,后焊角焊缝;4、整体建造部分和箱体分段等应从结构的中央向左右和前后逐格对称的进行焊接,由双数焊工对称施焊;5、凡超过1m以上的收缩变形量大的长焊缝,应采用分段退焊法或分中分段退焊进行焊接缝;6、在焊接过程中,先焊收缩变形量大的焊缝,再焊变形量小的焊缝;7、边箱分段、内底分段、甲板分段、艏艉分段分层建造,在合拢口两边应留出200~300mm的外板缝暂不接焊,以利合拢时装配对接,且肋骨、舱壁及平台板等结构靠近合拢口一边的角焊缝也暂不焊接,等合拢缝焊完后再焊;8、靠舷侧的内底边板与纵骨、底外板与纵骨至少要留一条纵骨暂不焊接,避免自由边波浪变形太大,不利于边箱合拢;9、二层底分段艏艉分段大合拢,边箱分段合拢的对接缝要用低氢型(碱性)焊条或用相同级别的711、712的CO2焊丝对称焊接,一次性连续焊完;10、构件、分段、分片等部件各自完工后要自检、互检、报检,把缺陷修补完毕,把合格品送下一道工序组装,没有拿到合格单的部件不能放到下一道工序组装。
二、焊接材料使用范围的规定(一)焊接下列船体结构和部件应采用低氢型焊条(碱性焊条)或相同级别的711、712系列的CO2焊丝。
1、船体环型对接焊缝,中桁材对接缝,合拢口处骨材对接焊缝;2、主机座及其相连接的构件;3、艏柱、艉柱、艉轴管、美人架等;4、桅杆座及腹板、带缆桩、导缆孔、锚机座、链闸及其座板等;5、艉拖沙与外板结构等;6、上下舵杆与法兰,舵杆套管与船体结构之间的连接。
(二)普通钢结构的焊接用酸性E4303焊条焊接或JM-56系列CO2焊丝焊接;(三)埋弧自动拼板,板厚≥8mm,用Ф4.0mm焊丝焊接,板厚5~8mm,用Ф3.2mm焊丝焊接;三、间断焊角接焊缝,局部加强焊的规定1)组合桁材、强横梁、强肋骨的腹板与面板的角焊接缝在肘板区域内应为双面连续焊;2)桁材、肋板、强横梁、强肋骨的端部加强焊长度应不小于腹板的高度,但间断的旁桁材端部可适当减小但要≥300mm;3)纵骨切断处端部的加强焊长度应不小于1个肋距;4)骨材端部削斜时,其加强焊长度不小于削斜长度,在肘板范围内应双面连续焊;5)用肘板连接的肋骨、横梁、扶强材的端部的加强焊,在肘板范围内应双面连续焊;6)各种构件的切口、切角、开孔(如流水孔、透气孔、通焊孔等)的两端应按下述长度进行包角焊;①当板厚>12mm时,包角焊长度≥75mm;②当板厚≤12mm时,包角焊长度≥50mm;7)各种构件对接接头的两侧应有一段对称的角焊缝其长度不小于75mm;四、其他的规定:1)锚机座、链闸、系缆桩底座、桅杆底座等受力部位的甲板与横梁、纵骨等是间断焊缝的应改为双面连续角缝。
船体结构焊接程序的基本原则
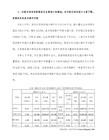
1、船体外板、甲板的对接焊缝,当是错开板缝时,先焊横向焊缝,后焊纵向焊缝;当是平列板逢时,则先焊纵向焊缝,后焊横向焊缝;
2、缝;
3、整体建造船舶或平面分段和立体分段建造时,应从结构的中央向左右和前后逐格对称的进行焊接;
8、肋骨、舱壁等结构靠近总段大接缝一边的角焊缝,以及双层底分段中内底边板与外板尚不角焊缝,一般应在大接缝焊后进行焊接;
9、应力较大的接缝,如总段的大接焊缝,焊接过程不应间断,要求连续完成;
10、分段建造中所产生的焊缝缺陷,应在上船台前修补完毕,不应集中在船台上进行。
4、具有对称中心线的构件,由双数焊工对称进行焊接;
5、手工电弧焊时,凡超过500mm的长焊缝,应采用分段退焊法或分中分段退焊法进行焊接;
6、构件中同时存在单层焊缝和多层焊缝时,先焊接收缩变形较大的多层焊缝,后焊单层焊缝;多层焊时,若条件允许,各层焊缝的焊接方向应相反,焊缝的街头互相错开;
7、分段或总段的外板纵向接缝以及纵向构件与外板的角接焊缝,其两端应留出200~300mm不焊,以利于船台装配时对接;
12000船体焊接原则工艺

1、概述本船为钢质、双底双壳、单甲板、混合骨架式、艉机型、具有艏艉楼的油船,航区为国内近海航区。
2、材料2.1、本船的船体材料为CCSA板、CCSB板及CCSD板,厚度为δ= 6`~26 mm。
船体结构所用的材料应符合《钢质海船入级规范》【CCS 2009】的要求并参照中国船级社《材料与焊接规范》中的规定。
所用焊接材料(包括焊条、焊丝、焊剂)应符合1998年《材料与焊接规范》第三篇第二章的有关规定,并应经船检认可,其级别应当与船体结构用钢的级别相对应。
2.2、当不同强度的母材焊接时,除去结构不连续处或应力集中区域应选较高强度等级的焊接材料外,一般选用与较低强度级别的母材相适应的焊接材料。
2.3、当母材的连接强度相同,韧性级别不同时,除结构受力情况复杂或施工条件恶劣外一般选用与较低韧性级别相适应的焊接材料。
2.4、焊接材料(包括焊条、焊丝、焊剂)的运输、储存、焊前处理和使用应符合焊接材料制造厂的使用说明要求。
2.5、本船结构采用T422钛钙型焊条,但下列部位应采用碱性低氢焊条施焊:1)船体大合拢时的环形对接缝和纵桁材对接缝;2)具有冰区加强的船舶,船体外板端接缝和边接缝;3)桅杆、吊货杆、吊艇架、系缆桩等承受强大载荷的舾装件及其所有承受高应力的零部件;4)要求具有较大刚度的构件,如首框架、尾框架、尾轴架等,及其与外板和船体骨架的接缝;5)主机基座及其相连接的构件。
6)对高强度钢或含碳量大于0.41%钢材的焊接,建议采用低氢焊接材料。
3、焊接方法与焊前准备3.1、焊接方法2)其余采用手工焊和CO2气体保护焊。
3.2、焊接前要求3.2.1、焊接前应去除油水和污垢,保证焊接面100%干燥清洁。
检查焊接材料和所开的焊接坡口尺寸,以及装配精度应符合CB/T3190-1997标准。
3.2.2、对接焊缝坡口要求:①、板厚在6~9mm的对接焊缝,在一面焊好后,另一面清根。
②、板厚在10~14mm的对接缝开单面坡口,焊后另一面清根。
船体焊接技术要求
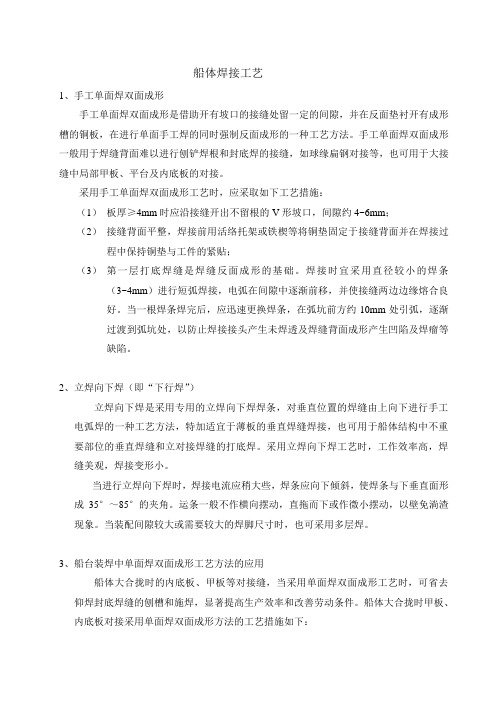
船体焊接工艺1、手工单面焊双面成形手工单面焊双面成形是借助开有坡口的接缝处留一定的间隙,并在反面垫衬开有成形槽的铜板,在进行单面手工焊的同时强制反面成形的一种工艺方法。
手工单面焊双面成形一般用于焊缝背面难以进行刨铲焊根和封底焊的接缝,如球缘扁钢对接等,也可用于大接缝中局部甲板、平台及内底板的对接。
采用手工单面焊双面成形工艺时,应采取如下工艺措施:(1)板厚≥4mm时应沿接缝开出不留根的V形坡口,间隙约4~6mm;(2)接缝背面平整,焊接前用活络托架或铁楔等将铜垫固定于接缝背面并在焊接过程中保持铜垫与工件的紧贴;(3)第一层打底焊缝是焊缝反面成形的基础。
焊接时宜采用直径较小的焊条(3~4mm)进行短弧焊接,电弧在间隙中逐渐前移,并使接缝两边边缘熔合良好。
当一根焊条焊完后,应迅速更换焊条,在弧坑前方约10mm处引弧,逐渐过渡到弧坑处,以防止焊接接头产生未焊透及焊缝背面成形产生凹陷及焊瘤等缺陷。
2、立焊向下焊(即“下行焊”)立焊向下焊是采用专用的立焊向下焊焊条,对垂直位置的焊缝由上向下进行手工电弧焊的一种工艺方法,特加适宜于薄板的垂直焊缝焊接,也可用于船体结构中不重要部位的垂直焊缝和立对接焊缝的打底焊。
采用立焊向下焊工艺时,工作效率高,焊缝美观,焊接变形小。
当进行立焊向下焊时,焊接电流应稍大些,焊条应向下倾斜,使焊条与下垂直面形成35°~85°的夹角。
运条一般不作横向摆动,直拖而下或作微小摆动,以壁免淌渣现象。
当装配间隙较大或需要较大的焊脚尺寸时,也可采用多层焊。
3、船台装焊中单面焊双面成形工艺方法的应用船体大合拢时的内底板、甲板等对接缝,当采用单面焊双面成形工艺时,可省去仰焊封底焊缝的刨槽和施焊,显著提高生产效率和改善劳动条件。
船体大合拢时甲板、内底板对接采用单面焊双面成形方法的工艺措施如下:(1)装配时按打底焊采用的不同焊接方法安装板缝。
当采用手工焊打底(陶质衬垫)时板缝开单边V形50°不留根坡口,间隙约4~6mm;当采用CO2气体保护半自动焊打底(软衬垫)时,板缝开单边V形40°不留根坡口,间隙约7~9mm。
大型船厂船体焊接原则工艺规范

大型船厂船体焊接原则工艺规范船厂船体焊接是造船过程中的重要环节,其质量直接影响到船舶的安全性和使用寿命。
为了保证船厂船体焊接的质量,制定了一系列的工艺规范和原则。
首先,船厂船体焊接应符合国家相关的法律法规以及行业标准,如《焊接工艺规范》、《焊工技能等级表》等。
同时,还需根据具体船体结构和船舶用途确定船体焊接的工艺参数,包括焊接方法、焊接材料、焊接电流和电压等。
其次,船厂船体焊接需要进行严格的质量控制。
焊工需要经过专业的培训和资质认证,并严格按照规范进行操作。
焊接过程中需要进行焊缝的准备和清理,确保焊接区域的干净和无杂质。
焊接操作需要控制焊接速度、焊接电流和电压等参数,以确保焊缝的质量和强度。
焊接完成后,还需要进行焊缝的无损检测,如X射线检测、超声波检测等,以排除焊接缺陷和隐患。
另外,船厂船体焊接应满足船舶设计和船级社的相关要求。
船体焊接需要符合船舶结构的强度要求,并满足船级社的要求。
例如,焊接工艺应符合船级社的检验和认证要求,焊缝应满足相关的级别和质量标准。
此外,还需要考虑船舶的航行环境和使用条件,确定合适的焊缝类型和焊接方法,以提高焊缝的抗腐蚀性能和使用寿命。
最后,船厂船体焊接还需要进行全过程的质量记录和追溯。
焊接过程中需要做好焊缝的记录,包括焊接材料、焊接参数、焊工资质等。
焊缝的检测和检验结果需要记录,以便后续的质量跟踪和追溯。
总之,大型船厂船体焊接的工艺规范和原则非常重要,它直接关系到船舶的安全性和使用寿命。
船体焊接需要符合国家相关的法律法规和行业标准,严格进行质量控制,满足船舶设计和船级社的要求,并做好全过程的质量记录和追溯。
只有这样,才能确保船体焊接的质量和可靠性。
典型船体结构的焊接工艺
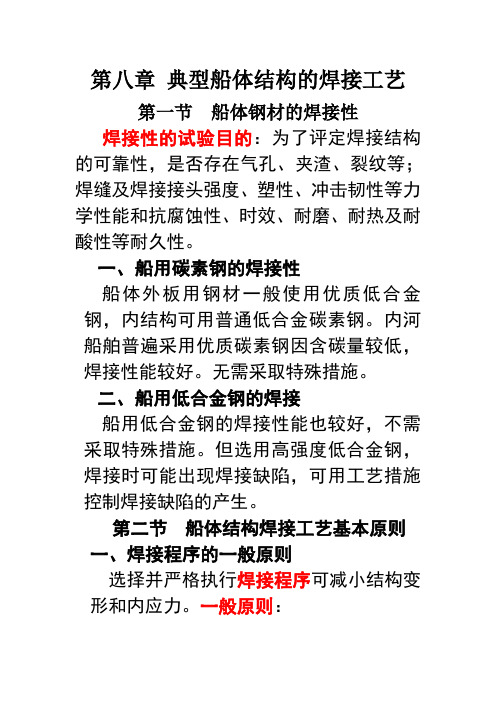
第八章典型船体结构的焊接工艺第一节船体钢材的焊接性焊接性的试验目的:为了评定焊接结构的可靠性,是否存在气孔、夹渣、裂纹等;焊缝及焊接接头强度、塑性、冲击韧性等力学性能和抗腐蚀性、时效、耐磨、耐热及耐酸性等耐久性。
一、船用碳素钢的焊接性船体外板用钢材一般使用优质低合金钢,内结构可用普通低合金碳素钢。
内河船舶普遍采用优质碳素钢因含碳量较低,焊接性能较好。
无需采取特殊措施。
二、船用低合金钢的焊接船用低合金钢的焊接性能也较好,不需采取特殊措施。
但选用高强度低合金钢,焊接时可能出现焊接缺陷,可用工艺措施控制焊接缺陷的产生。
第二节船体结构焊接工艺基本原则一、焊接程序的一般原则选择并严格执行焊接程序可减小结构变形和内应力。
一般原则:1、外板、甲板对接缝:○1错开板缝:先横向焊,后纵向焊;○2平列板缝:先纵向焊,后横向焊。
2、同时存在对接缝和角焊缝:先焊对接缝,后焊角焊缝。
3、整体或分段建造时:从结构中央向左右、前后对称焊接。
4、有对称中心线的构件:双数焊工对称焊。
5、手工电弧焊长缝:分段退焊或分中分段退焊。
6、同时存在单层焊缝和多层焊缝:先焊多层,后焊单层。
多层焊各层方向相反,接头错开。
7、分段或总段外板纵缝及纵向构件与外板的角焊缝两端200-300mm:先不焊,以利于船台装配时对接。
8、内结构靠近总段大接缝一边的角焊缝:在大接缝焊接后再焊。
9、应力较大的大接缝:焊接过程不能中断,应连续完成。
10、分段中的焊接缺陷应在上船台前修补,不应在船台上进行。
二、焊接材料使用范围的规定重要船体构件和部件应采用碱性低氢焊条(使用直流焊机):○1用低合金钢建造的所有船体焊缝;○2用碳素钢建造的船体大合拢环形对接焊缝和桁材对接焊缝;○3船壳冰带区的端接缝和边接缝;○4船长大于90m的舷顶列板与强力甲板在船中0.5L区域内的角接焊缝;○5桅杆、吊杆、吊艇架及其受力构件;○6拖钩架;○7主机座及其相连接的构件;○8艏柱、艉柱、艉轴架。
船体结构焊接顺序
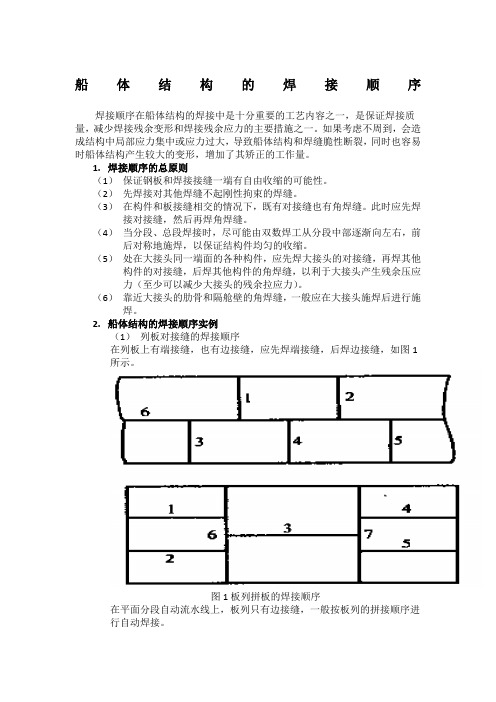
船体结构的焊接顺序焊接顺序在船体结构的焊接中是十分重要的工艺内容之一,是保证焊接质量,减少焊接残余变形和焊接残余应力的主要措施之一。
如果考虑不周到,会造成结构中局部应力集中或应力过大,导致船体结构和焊缝脆性断裂,同时也容易时船体结构产生较大的变形,增加了其矫正的工作量。
1.焊接顺序的总原则(1)保证钢板和焊接接缝一端有自由收缩的可能性。
(2)先焊接对其他焊缝不起刚性拘束的焊缝。
(3)在构件和板接缝相交的情况下,既有对接缝也有角焊缝。
此时应先焊接对接缝,然后再焊角焊缝。
(4)当分段、总段焊接时,尽可能由双数焊工从分段中部逐渐向左右,前后对称地施焊,以保证结构件均匀的收缩。
(5)处在大接头同一端面的各种构件,应先焊大接头的对接缝,再焊其他构件的对接缝,后焊其他构件的角焊缝,以利于大接头产生残余压应力(至少可以减少大接头的残余拉应力)。
(6)靠近大接头的肋骨和隔舱壁的角焊缝,一般应在大接头施焊后进行施焊。
2.船体结构的焊接顺序实例(1)列板对接缝的焊接顺序在列板上有端接缝,也有边接缝,应先焊端接缝,后焊边接缝,如图1所示。
图1板列拼板的焊接顺序在平面分段自动流水线上,板列只有边接缝,一般按板列的拼接顺序进行自动焊接。
(2)平直分段的焊接顺序①甲板分段它是由平面或稍有曲率的列板、横梁和纵桁材等零部件组成的分段。
一般情况下,板列已焊接结束,所以该分段主要焊缝为角焊缝,其焊接顺序先焊立角焊(图2-1所示),后平角焊(图2-2所示)图2甲板分段的构件角焊缝焊接顺序②纵向隔舱壁分段纵向隔舱壁分段没有船体中心线,施焊时不一定要左右对称施焊(舷侧分段亦是如此),舱壁按板列对接缝的焊接顺序进行焊接,加强材与隔舱壁的角焊缝可以按顺序进行焊接,当然可以用间跳法施焊更好,其焊接顺序如图3所示。
③横向隔舱壁分段横向隔舱壁的对接缝焊接顺序相同于板列顺序,横向隔舱壁板与加强材的角焊缝由双数焊工从中心线向左右对称地进行焊接,其焊接顺序如图4所示。
船体焊接工艺
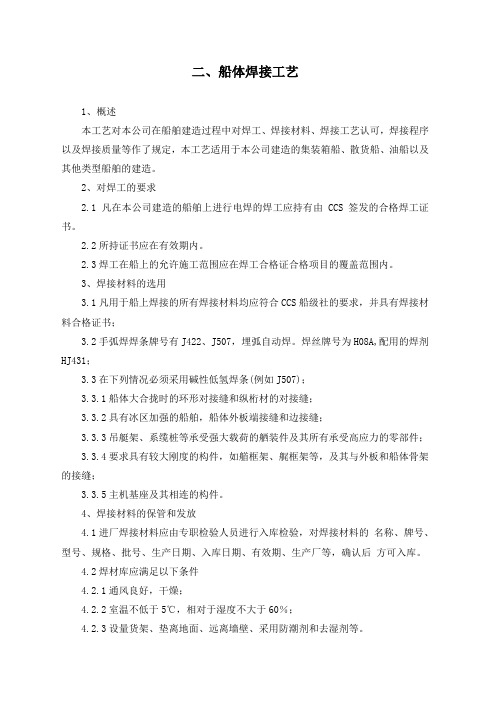
二、船体焊接工艺1、概述本工艺对本公司在船舶建造过程中对焊工、焊接材料、焊接工艺认可,焊接程序以及焊接质量等作了规定,本工艺适用于本公司建造的集装箱船、散货船、油船以及其他类型船舶的建造。
2、对焊工的要求2.1凡在本公司建造的船舶上进行电焊的焊工应持有由CCS签发的合格焊工证书。
2.2所持证书应在有效期内。
2.3焊工在船上的允许施工范围应在焊工合格证合格项目的覆盖范围内。
3、焊接材料的选用3.1凡用于船上焊接的所有焊接材料均应符合CCS船级社的要求,并具有焊接材料合格证书;3.2手弧焊焊条牌号有J422、J507,埋弧自动焊。
焊丝牌号为H08A,配用的焊剂HJ431;3.3在下列情况必须采用碱性低氢焊条(例如J507);3.3.1船体大合拢时的环形对接缝和纵桁材的对接缝;3.3.2具有冰区加强的船舶,船体外板端接缝和边接缝;3.3.3吊艇架、系缆桩等承受强大载荷的舾装件及其所有承受高应力的零部件;3.3.4要求具有较大刚度的构件,如艏框架、艉框架等,及其与外板和船体骨架的接缝;3.3.5主机基座及其相连的构件。
4、焊接材料的保管和发放4.1进厂焊接材料应由专职检验人员进行入库检验,对焊接材料的名称、牌号、型号、规格、批号、生产日期、入库日期、有效期、生产厂等,确认后方可入库。
4.2焊材库应满足以下条件4.2.1通风良好,干燥;4.2.2室温不低于5℃,相对于湿度不大于60%;4.2.3设量货架、垫离地面、远离墙壁、采用防潮剂和去湿剂等。
4.2.4对焊条的品种分类堆放,作好标识,以防发错。
5、焊接材料的发放和领用5.1焊条在使用前应经过烘干,烘干的要求如下:5.1.1 70~150℃烘焙一小时,如包装完好,未受潮的酸性焊条,可不必烘焙;5.1.2对于碱性焊条,使用前,必须经350℃烘焙2小时,后降为150℃保温1小时,随烘随用。
5.1.3烘焙时,焊条堆放一般为1~4层,不能太厚,防止焊条受热不均匀和便于潮气的排除。
船体焊接原则工艺规范

船体焊接原则工艺规范1. 引言船体焊接是造船过程中不可或缺的一项工艺,它影响着船舶结构的强度和密封性能。
为了确保船体焊接工艺的质量和安全性,制定了一系列的工艺规范。
本文将介绍船体焊接原则工艺规范的主要内容和要求。
2. 焊接材料选择在进行船体焊接前,需要选择合适的焊接材料。
船体焊接常用的材料有钢材和铝合金。
材料的选择应根据船舶的设计要求、工作环境和预期的使用寿命来确定,确保焊接后的船体具备足够的强度和耐腐蚀性。
3. 焊接设备选择船体焊接需要使用到相应的焊接设备,例如电弧焊机、气体保护焊机等。
选择焊接设备时,应根据焊接材料的类型和厚度、焊接位置的限制等因素进行合理选择。
同时,还需要确保焊接设备的性能稳定、操作简单,以保证焊接工艺的可靠性和高效性。
4. 焊接工艺参数船体焊接的工艺参数包括焊接电流、电压、焊接速度、预热温度等。
这些参数的选择应根据焊接材料的特性和船体结构的要求来确定。
一般情况下,要求焊缝牢固、均匀且没有明显的缺陷,同时也要考虑到焊接工艺的经济性。
5. 焊接工艺控制为了确保船体焊接的质量,需要对焊接工艺进行严格的控制。
控制措施包括焊接操作规程的制定、焊接工艺指导书的编制、焊工的培训和评定等。
此外,还需进行焊接过程中的质量检查和测试,及时发现和解决可能存在的问题,以确保焊接质量达到预期标准。
6. 焊接缺陷检测焊接过程中可能出现的缺陷包括焊缝裂纹、气孔、夹渣等。
为了及时发现这些缺陷并采取相应的措施加以修复,需要进行焊接缺陷的检测。
常用的检测方法包括可视检查、超声波检测、射线检测等。
7. 焊接质量评定焊接质量的评定是确保船体焊接工艺规范有效实施的重要环节。
评定标准一般包括焊缝外观质量、焊接强度和密封性能等方面的要求。
通过对焊接质量的评定,可以判断焊接工艺是否合格,提出改进建议,并为船体的后续加工和验收提供依据。
8. 结论本文介绍了船体焊接原则工艺规范的主要内容和要求。
船体焊接作为造船过程中的重要工艺,影响着船舶的结构强度和密封性能。
船体焊接原则工艺规范

船体焊接原则工艺规程1 目的为了保证船舶建造焊接质量,明确船舶建造过程中的焊接材料、焊接方法、焊接过程控制等要求。
2 范围本规程规定了船体建造过程中船体焊接的焊前准备、人员、工艺要求、工艺过程和检验。
本规程适用于船体结构建造焊接,其它钢结构及铁舾件等焊接可参照执行。
3 规程引用文件CB/T 3802-1997 船体焊缝表面质量检验要求CB/Z39-1987 焊接材料的存放、检查和使用CB/T3190-1997 船体结构焊接坡口型式尺寸CB/T3761-1996 船体结构焊缝缺陷修补技术要求Q/GLSG1402001-2008 船舶工程质量控制标准4 人员4.1 凡是参与焊接工作的焊工必须持有船级社颁发的考试合格证上岗,并只能从事与其考试相应等级范围内的焊缝焊接。
4.2 当验船师或船东驻厂代表要求查阅焊工合格证时,均应出示证件。
5 基本原则5.1 本规程所提供焊接材料、焊接方法、焊接接头的坡口型式和尺寸等方面的内容,均应取得国内外船级社认可。
5.2 应用CO2气体保护半自动和自动焊、埋弧自动焊、垂直气电焊等各类高效焊接方法,应在产品相关工艺文件和施工图中加以明确。
5.3 焊接坡口型式及加工尺寸应按《船体结构焊接坡口型式尺寸》进行。
安装精度应符合《船舶工程质量控制标准》要求。
5.4 焊接材料的焙烘、保管及使用要求5.4.1 一般焊接材料的焙烘、保管及使用,按照CB/Z39-1987《焊接材料的存放、检查和使用》执行。
5.4.2 特殊焊接材料的焙烘、保管及使用,应编制专用工艺文件。
5.5 焊接方法、焊接材料、钢种等级的选用原则,见下表1:6 工艺要求6.1 焊前清理6.1.2 焊前清理要求:焊工必须对焊接坡口及坡口两侧各宽20mm 范围内,角焊缝在焊接宽度方向两侧各宽20mm内,清除氧化物,水份,油污等。
6.1.3 当焊缝清理后未能及时焊接并因气候或其他原因影响而积水,受潮、生锈时,在焊接前应重新清理。
船舶焊接通用原则工艺

焊接原则工艺一、适用范围1.为保证船体焊接质量,提高焊接工作效率,降低工作劳动强度,特制定本焊接通用工艺,要求全体焊工在生产中贯彻执行。
2.本工艺在建造不同类型的船舶中,如有某些条文不适用或内容不完整,则可按所建船舶的实际情况与技术要求,另外制订补充条文,包括修改内容。
对于有特殊要求的焊接,可根据专门制定的焊接工艺进行。
二、工艺内容1焊接材料的选择1.1.船体板材的一般构件焊接均可采用J422焊条。
1.2.船体下列部分的焊接,需采用碱性低氢型焊条:1.2.1.船体大合拢时的环形对接缝和纵桁对接缝;1.2.2.船体外板的端接缝的边接缝;1.2.3.舷顶列板与主甲板在船舯0.5L内区域的焊接;1.2.4.桅杆、吊艇架、拖桩、系缆桩等承受强大载荷的舣装件及其所有承受高应力的零部件;1.2.5.要求具有较大刚度的构件,如首柱、舵浆座、首框架、尾框架、尾轴架等,及其与外板的船体骨架的接缝;1.2.6.主机座、辅机座、锚机座、绞机座、中间轴座等与其相连接的构件的焊接;1.2.7.蒸汽锅炉及受压容器。
1.3.当不同强度的母材被连接时,一般可选用与较低强度级别相适应的焊接材料。
1.4.当焊接高强钢或钢材碳当量大于0.41%时,应采用低氢型焊接材料。
1.5.在无特殊要求的情况下,CO2气体保护焊可代替手工焊。
1.6.特种钢材的焊接材料应根据设计要求选用。
2.角焊缝连接形式及焊接要求角焊缝的连接形式分为连续角焊缝和间断角焊缝2.1.下列部位的角焊缝连接应采用双面连续焊:2.1.1.风雨密甲板和上层建筑外围壁边界的角焊缝,包括舱口围板、升降口和其他开口;2.1.2.液舱和水密舱室的周界;2.1.3.尾尖舱所有结构的角焊缝,包括舱壁扶强材的角焊缝;2.1.4.装载化学品和食用液体货舱内所有角焊缝;2.1.5.液舱内所有搭接焊缝;2.1.6.船艏0.25L区域内,主要构件和次要构件与船底板连接处的所有角焊缝;2.1.7.船体所有主、次要构件的端部和肘板的端部与板材的角焊缝;2.1.8.厨房、配膳房、洗衣房、浴室、厕所和蓄电池室等处的周界角焊缝;2.1.9.其他特殊结构或在高强度钢板上安装附件和连接件的角焊缝;2.1.10.T型角接中的竖板(如扶强材、纵骨等的腹板)厚度大于平列板(如舱壁板、外板)厚度时的角焊缝;2.1.11.机座和机器支承结构的连接处;2.1.12.中桁材与龙骨板的连接角焊缝;2.1.13.甲板等开口处四周的悬臂梁的角焊缝;2.1.14.焊缝长度在300mm以内的角焊缝。
船体焊接原则工艺规范

船体焊接原则工艺规范1 范围本规范规定了船体建造过程中船体焊接的焊接前准备、人员、工艺要求、工艺过程和检验。
本规范适用于船体建造焊接工艺。
编写其他各类焊接工艺文件时,亦可参照使用。
2 焊接前准备2.1 原则要求2.1.1 本规范所提供的焊接材料和焊接方法,均应取得国内外船级社认可。
2.1.2 应用CO2气体保护半自动和自动焊、重力焊、下行焊、垂直气电焊及各类衬垫单面焊双面成型等高效焊接方法,应在产品相关工艺文件和施工图中加以明确。
2.1.3 本规范所提供的船体各种规格的板厚,材料级别以及所应用的焊接方法,焊接材料,焊接接头的坡口型式和尺寸、焊接位置等方面的内容,均应获得船级社认可。
2.2 钢种等级与焊接材料的选配钢种等级与焊接材料的选配,见表1。
表1 钢材等级与焊接材料的选配序号焊接方法焊接材料钢材等级适用范围E4315.01 (SH427.01) A、B、DE5015.01 (SH507.01) 其它等效焊材AH32~DH36构架对接全位置角焊外板对接1 手工电弧焊E5015.02 (SH507.02) 其它等效焊材EH32、EH36外板对接构架全位置角焊焊丝:H08A焊剂:SHJ431其它等效焊材A、B、D2 埋弧自动双面焊焊丝/焊剂H10Mn2/HJ101(CHJ101)H10Mn2G/HJ331(SHJ331)其它等效焊材AH32 AH36DH32 DH36EH32 EH36拼板3 CO2气体保护半自动焊E71T-1 (DW-100)(2Y)E70T-1 (MX-200)E71T-1 (SM-1F)(2Y)E71T-1 (KFX-712C)E501T-1 (YJ-502)(Q)E71T-1 (TWE-711)其它等效焊材A、B、D、AH32AH36DH32DH36EH36外板及构架对接,构架与板平角,立角焊表1(续)钢材等级与焊接材料的选配序号焊接方法焊接材料钢材等级适用范围4 CO2气体保护单面焊焊丝:E71T-1 (TWE-711)E71T-1 (KFX-712C)衬垫:TC-1JN-4其它等效焊材A、B、D、AH32 AH36DH32 DH36EH32、E36中、大组立板材对接及总组立中合拢对接缝5 手工衬垫单面焊焊条:E5015.01(SH507.01)衬垫:JN-1其它等效焊材A、B、DAH32 AH36DH32 DH36中、大、总组立中板材对接及合拢对接缝E4313 (CJ421FeZ)其它等效焊材A、B、D6 高效铁粉重力焊E5024 (CJ501FeZ)其它等效焊材AH32 AH36DH32 DH36中、大组立中的构件平角焊缝7 手工下行焊E5015 (CJ507Fe)其它等效焊材A、B、DAH32 DH32船体构件合拢垂直角焊缝焊丝:EG70T-2 (DWS-43G)衬垫:KL-4GT其它等效焊材A、 BAH32、AH36DH32、DH368 垂直气电焊焊丝:EG70T-2 (DWS-43G)衬垫:JN-10其它等效焊材A、B、DAH32 DH32AH36 DH36总组立合拢旁板,纵、横舱壁的垂直对接焊9 FCB三丝埋弧自动单面焊焊丝:Y-A表面焊剂:NSH-50底面焊剂:NSH-IR其它等效焊材A、B、DAH32 DH32AH36 DH36平面分段流水线中板材的对接焊2.3 典型结构用焊接材料和焊接方法的规定:2.3.1 当采用手工电弧焊接时,下列结构的焊接必须选用低氢型焊条焊接。
典型船舶结构的焊

8).肋骨,仓壁等结构焊接时,应在大 接缝焊接后进行焊接.
9).应力较大的接缝,如总段的大接缝, 焊接过程不应间断,要求连续完成.
10).分段建造中所产生的焊接缺陷, 应在上船台前修补完毕,不应在船台上 进行.还应考虑到焊接施工的方便性.
3).整体建造船舶或平面分段和立体分 段建造时,应从结构的中央向左右和前 后逐格对称地焊地焊接.
5).手工电弧焊时,凡超过500毫米 的长焊缝,应采用分段退焊法或分中分 段退焊法.
6).构件同时存在单层焊缝和多层焊缝 时,先焊收缩变形较大的多层焊缝,后 焊单层焊缝
典型船舶结构的焊接工艺
船体钢材的焊接性 结构焊接工艺的基本原则 船体焊接工艺 船体结构的高效与高能束焊接 分段焊接工艺规程的编制
二.船体结构焊接工艺基本原则
1).船体外板,甲板的对接焊缝,如错 开板缝时,先焊横向焊缝,后焊纵向焊 缝;如平列板缝时,则先纵后横.
2).构件同时存在对接缝和角接时,先 对接后角接.
船体焊接原则工艺规范标准

A、B
AH32、
AH36
DH32、
DH36
总组立合拢
旁板,纵、
横舱壁的垂
直对接焊
焊
焊丝 :
EG70T-2 (DWS-43G)
衬垫 :
JN-10
其它等效焊材
A、B、D
AH32
DH32
AH36
DH369
FCB三丝
埋弧自动
单面焊
焊丝: Y -A
表面焊剂:
NSH-50
底面焊剂:
3.1.3本规所提供的船体各种规格的板厚,材料级别以及所应用
的焊接方法,焊接材料,焊接接头的坡口型式和尺寸、焊接位置等方
面的容,均应获得船级社认可。
3.2
钢种等级与焊接材料的选配
钢种等级与焊接材料的选配,见表 1。
表 1钢材等级与焊接材料的选配
序
焊接方
焊接材料
钢材等级
适用围
号
法
构架对接
E4315.01 (SH427.01)
全位置角
A、B、DE5015.01 Fra bibliotekSH507.01)
焊
AH32~DH36
其它等效焊材
手工电
外板对接
1
弧焊
EH32、EH36
外板对接
E5015.02 (SH507.02)
其它等效焊材
构架全位
置角焊
焊丝:H08A
焊剂:SHJ431
A、B、D
埋弧自
其它等效焊材
2
动
拼板
焊丝/焊剂
AH32 AH36
H10Mn2/HJ101(CHJ101)
DH32
{生产工艺技术}船体焊接原则工艺规范

{生产工艺技术}船体焊接原则工艺规范船体焊接是造船中至关重要的一部分,正确的焊接工艺可以确保船体的耐久性和强度。
下面是船体焊接的原则和工艺规范。
1.焊接工艺选择:根据船体的结构和材料的特点,选择适当的焊接工艺。
常用的船体焊接方法包括电弧焊、气体保护焊、电子束焊等。
2.焊接材料选择:根据船体的用途和特殊要求,选择适当的焊接材料。
一般情况下,船体焊接使用的材料需要具有良好的强度、韧性和耐腐蚀性。
3.焊接参数控制:在进行船体焊接时,需要控制好焊接电流、电压和焊接速度等参数,以确保焊接质量。
焊接参数的选择应综合考虑船体的材料、厚度和焊缝的类型等因素。
4.焊接工艺规范:船体焊接需要参照相关的工艺规范进行操作。
常见的船体焊接规范有船级社的规范和国际焊接工艺标准等。
5.固定和支撑:在进行船体焊接时,需要使用适当的夹具和支撑物,确保焊接件的位置和对齐度。
固定和支撑的方法应根据焊接位置和形状来选择,以确保焊接件的稳定和准确。
6.焊接质量检测:船体焊接完成后,需要进行焊缝的质量检测。
一般情况下,进行可视检查、超声波检测、射线检测等工艺来确保焊缝的质量和完整度。
7.焊接工艺参数记录:进行船体焊接时,需要记录焊接工艺参数和操作过程。
这些记录可用于追踪和分析焊接质量问题,并为日后的维修和改进提供参考。
8.焊接人员培训:进行船体焊接时,需要确保焊接人员具备足够的焊接技术和经验。
焊接人员需要经过专业的培训和认证,以确保焊接质量。
总之,船体焊接是船舶制造过程中不可或缺的一部分,正确的焊接工艺可以确保船体的耐久性和强度。
在进行船体焊接时,需要根据相关规范和工艺要求进行操作,并进行适当的焊接质量检测和记录。
通过严格的焊接工艺控制和培训,可以提高船体焊接的质量和效率。
12000DWT焊接原则工艺.doc

一.general1、DescriptionThe vessel is designed as a single screw , DO engine driving ,multipurpose container carrier with bulbous bow, raked stem and transom stern.Engine room aft and superstructure are arranged on fore ship.The vessel has two cargo hold, No. 2 hold is equipped with tween deck.For heavy load operations the vessel will be equipped with two heavy lift cranes with a capacity of abt. 400t each. Additionally the vessel will be equipped with one general cargo crane of a capacity of abt. 80t. Fuel oil tanks will be arranged in cargo area away from side shell, and in engine room, water ballast in double bottom, side tanks as well as in fore and aft peak tanks.2.Main DimensionsLength over all: appr. 153.80 mLength betw. perp. appr. 145.50 mBreath moulded: appr. 23.20 mDepth to main deck, mld. appr. 12.80 mScantling draught appr. 8.50 mDesign draught appr. 8.20 mFrame space:after~FR14: 600mmFR14~ FR54:650mmFR54~FR194:750mmFR194~FR212:600mm3.hull construction arrangementThe vessel is provided with forecastle and poop deck, main deck as free board deck.The engine room is located after, wheel house and superstructure at forecastle deck.The cargo hold is provided with wide opening and non-symmetrical portside and starboard side, width of portside is 9 m and starboard side 10m, total 19 m.Fore hold is 12.75 m long and after hold is long of 83.75 mm.二、Main technical requirements1. The vessel is built according to GL rules, welding of construction and fittings is to be supervised by GL.2. Standard of welding quality has to comply with requirement and drawings approved by GL.3.Size of all welding seams of construction and fittings has to be according to drawings and specification ofhull construction welding.4.All welder who work on this vessel, shall have GL approved qualified certificate, whose works shall notover the limitation of the cerfificate.三、Material and welding consumable1.materialSteel material of the vessel is normal and high tensile hull construction steel, the hull material includingforging and castings shall comply with GL rules.1.1 material quality of plate:GLA.GLE.GLD .GLAH36,GL DH36,GLEH36.GL DH40.1.2 material quality of profile:GL-A(bulb steel,flat bar), AH36(bulb steel, flat bar)1.3 pipes:20-Ⅰ.20-Ⅱ.20-Ⅲ seamless steel pipes2.Welding consumable2.1 All welding consumable shall have GL approval certificate.2.2 Electrode of manual welding:E4303 ,E4315, E5015, E4324, E5028 etc. with diameter of φ3.2~φ5mm.2.3 Core welding wire of CO2 shielding welding:YCJ501-1, KFX-712C etc. with diameter of φ1.2mm. Purityof CO2 ≥99.5%2.4 welding wire of automatic welding: H08A+HJ431,H10Mn2+ HJ350, diameter of φ3~φ5mm .2.5 stainless electrode:A132,special welding electrode:A302 , diameter of φ3.2~φ4mm.四、welding principle1、All welding materials including electrode, wire and solder shall be preheated and used according tospecification.2、Low hydrogen electrode E4315 or E5015 shall be used while welding the following structure:2.1 All butt seams, cycle seams during erection.2.2 Butt seams of all profile material and longitudinal girder.2.3 All seams of high tensile steel material.2.4 Seams of shell plate and stern post.2.5 Full penetration seams of side top plate and upper deck, seams of longitudinal bulkhead and upper deck.2.6 ME foundation, generator foundation, thruster bearing foundation, steering gear foundation, bollard and reinforcement etc.2.7 All welding seams of lifting eyes on blocks.3、The rule and procedure of manual arc welding see <<general workmanship of hull manual arc welding>>(G16-JZ49-01).4、The rule and procedure of automatic arc submerge welding see《general workmanship of arc submerge welding,semiautomatic fillet welding》.(G16-JZ50)5、When CO2 shielding welding is provided, erection welding shall not be taken for main engine foundation,welding seams between upper deck and tween deck, tightness of water tight bulkhead shall be guaranteed.6、Space between welding seams is stipulated in GL rule as following :A:space between two butt welding seams: min.100mm.B:space between corner welding and butt welding seams: min.50mm.C:space between two corner welding seams: min. 50mm.7、Should the difference of plate thickness is more than 3mm while butt welding,the thicker plate shall be sniped at the scale of 1:3 or according to the requirement of drawings.8、Web and top plate of “T” profile material are not allowed to butt welded in same section except erection joints, space between welding seams shall be more than 100mm.9、Plug welding holes shall be elliptical, min. width of the holes shall not less than twice the plate thickness, lengthof holes shall not be less than 75mm, pitch of holes shall not more than 150mm.10、Quality of tack welding shall be same as normal welding, diameter of electrode isφ3.2mm,tack welding seamswith defect shall be removed completely, surface of steel plate shall not be hurt while dismounting the assembling bars.11、Welding seams of all scallops and structure edges shall be around and smooth.12、Size of all fillet welding shall comply with requirement of drawings.13、During construction of blocks, welding shall start from middle of blocks towarding to fore and after, left andright symmetricly. Welding of deck blocks, side plate, double bottom blocks as well.14、Cycle welding of erection joints shall be executed symmetricly by dual welders, the welding shall be continuousand be completed as soon as possible.15、Special welding procedure for casting stern post, joints between stern post and shell plate shall be madeaccording to material quality of stern post. The welding shall be continuous. Smooth and levelness of cargo hold area shall be kept after welding, rigid welding procedure shall be constituted to avoid serious deformation after welding.。
10000吨散货轮焊接工艺

1 船体概述1.1船型及主要尺寸该船是一艘一万吨的散货轮,船体主要尺度如下:船长:160.8m型宽:20.8m吃水:8.4m1.2船体材料船体的主要材料以钢材为主,包括结构钢,铸钢,锻钢和铸铁等.2. 船体结构焊接的原则工艺2.1焊接顺序的基本原则在船体建造中,为了减小船体结构的变形和应力,正确选择和严格遵守焊接顺序,是保证船体焊接质量的重要措施。
由于船体结构复杂,各种类型的船体结构也不一样,因此焊接顺序也有所不相同。
船体结构焊接顺序的基本原则是:(1)船体外板、甲板的拼缝,一般应先焊横向焊缝(短焊缝),后焊纵向焊缝(长焊缝)。
(2)构件中如同时存在对接焊缝和角接焊缝时,则应先焊对接缝,后焊角焊缝。
如同时存在立焊缝和平焊缝,则应先焊立焊缝,后焊平焊缝。
(3)凡靠近总段和分段合拢处的对接缝和角焊缝应留出200~300毫米暂不焊,以利船台装配对接,待分段、总段合拢后再进行焊接。
否则,合拢时的装配质量就不能保证,焊接质量就会下降。
(4)手工焊时长度≤1000毫米可采用连续直通焊,≥1000毫米时采用分中逐步退焊法或分段逐步退焊法等方法。
(5)具有对称中心线的构件由双数焊工对称地焊接。
(6)在结构中同时存在厚板与薄板构件时,先焊收缩量大的厚板多层焊,后焊薄板单层焊缝。
多层焊时,各层的焊接方向最好要相反,各层焊缝的接头应互相错开。
因为该处由于焊接残余拉应力而非常容易产生裂纹,在此处若有焊缝接头会促使裂纹的产生。
(7)刚性较大的接缝,如立体分段的对接焊缝(俗称大接头),焊接过程不应间断,应力求迅速连续完成。
(8)船台大合拢时,先焊接总段中未焊接的外板、内底板、舷侧外板和甲板等的纵向焊缝。
同时焊接靠近大接头处的纵横构架的对接焊缝。
再焊接大接头环形对接焊缝,最后焊接构件与船体外板和甲板的连接角焊缝。
(9)整体建造船舶或平面分段和立体分段建造时,应从结构的中央向左右和前后逐格对称地进行焊接。
2.2焊接材料的使用要求造船规范中明确规定下列结构和构件必须使用低氢型焊条:(1)船体大合拢时的环形对接缝和纵桁材对接焊缝(2)具有冰区加强级的船舶,船体外板端接缝和边接缝。
- 1、下载文档前请自行甄别文档内容的完整性,平台不提供额外的编辑、内容补充、找答案等附加服务。
- 2、"仅部分预览"的文档,不可在线预览部分如存在完整性等问题,可反馈申请退款(可完整预览的文档不适用该条件!)。
- 3、如文档侵犯您的权益,请联系客服反馈,我们会尽快为您处理(人工客服工作时间:9:00-18:30)。
1、概述本船为钢质、双底双壳、单甲板、混合骨架式、艉机型、具有艏艉楼的油船,航区为国内近海航区。
2、材料2.1、本船的船体材料为CCSA板、CCSB板及CCSD板,厚度为δ= 6`~26 mm。
船体结构所用的材料应符合《钢质海船入级规范》【CCS 2009】的要求并参照中国船级社《材料与焊接规范》中的规定。
所用焊接材料(包括焊条、焊丝、焊剂)应符合1998年《材料与焊接规范》第三篇第二章的有关规定,并应经船检认可,其级别应当与船体结构用钢的级别相对应。
2.2、当不同强度的母材焊接时,除去结构不连续处或应力集中区域应选较高强度等级的焊接材料外,一般选用与较低强度级别的母材相适应的焊接材料。
2.3、当母材的连接强度相同,韧性级别不同时,除结构受力情况复杂或施工条件恶劣外一般选用与较低韧性级别相适应的焊接材料。
2.4、焊接材料(包括焊条、焊丝、焊剂)的运输、储存、焊前处理和使用应符合焊接材料制造厂的使用说明要求。
2.5、本船结构采用T422钛钙型焊条,但下列部位应采用碱性低氢焊条施焊:1)船体大合拢时的环形对接缝和纵桁材对接缝;2)具有冰区加强的船舶,船体外板端接缝和边接缝;3)桅杆、吊货杆、吊艇架、系缆桩等承受强大载荷的舾装件及其所有承受高应力的零部件;4)要求具有较大刚度的构件,如首框架、尾框架、尾轴架等,及其与外板和船体骨架的接缝;5)主机基座及其相连接的构件。
6)对高强度钢或含碳量大于0.41%钢材的焊接,建议采用低氢焊接材料。
3、焊接方法与焊前准备3.1、焊接方法2)其余采用手工焊和CO2气体保护焊。
3.2、焊接前要求3.2.1、焊接前应去除油水和污垢,保证焊接面100%干燥清洁。
检查焊接材料和所开的焊接坡口尺寸,以及装配精度应符合CB/T3190-1997标准。
3.2.2、对接焊缝坡口要求:①、板厚在6~9mm的对接焊缝,在一面焊好后,另一面清根。
②、板厚在10~14mm的对接缝开单面坡口,焊后另一面清根。
③、板厚在14mm以上的对接缝必须开双面坡口,先焊一面,翻面清根再焊。
④、所有球扁钢、角钢、扁钢等型材允许对接,但必须按要求开坡口,全焊透。
⑤、主船体分段、分片的对接缝必须全焊透。
3.3、对接焊缝的要求3.3.1、船体外板、甲板、内底板及舱壁板之间的连接,均应采用对接焊缝。
下列板缝均采用双面连续焊缝:1)风雨密甲板和上层建筑外围壁边界的角焊缝,包括舱口围板、升降口和其他开口处;2)液体舱、水密舱室的周界;3)机座和机器支承结构的连接处;4)尾尖舱内所有结构(包括舱壁扶强材)的角焊缝;5)装载化学品和食用液体货舱内的所有角焊缝;6)散货船的货舱内主肋骨及其上下肘板与舷侧外板、上下边舱的斜板之间的所有角焊缝;7)液舱内所有搭接焊缝;8)船首0.25L区域内,主要构件和次要构件与船底板连接处的所有角焊缝;9)中桁材与龙骨板的连接角焊缝;10)厨房、配膳室、洗衣室、浴室、厕所和蓄电池室等处的周界角焊缝;部与板材连接的搭接焊缝;12)其他特殊结构、在高强度钢板上安装附件和连接件时的角接焊缝应特殊考虑;13)“T”型角接中的竖板(如扶强材、纵骨等的腹板)厚度大于15mm,且大于平列板(如舱壁板、外板或甲板)的厚度时,其角接焊缝应为双面连续焊。
3.3.2、船体构件的所有对接焊缝,均应有封底焊(双面成型者除外),当无法进行封底焊时,可采用加垫板的型式,但必须保证完全焊透。
3.3.3、板材厚度t≥6mm时,根据不同焊接方法,应采用单面或双面坡口的型式进行焊接,其坡口型式由船厂自定,但图样及技术方件中明确规定者除外。
3.3.4、对接板材厚度之差≥4mm时,应对厚板的边缘削斜均匀过渡,削斜的宽度应不小于厚度的4倍。
3.4、角接缝的要求:3.4.1、按焊接规格表的要求,凡规定全熔透或深熔焊的角接缝必须开坡口,留根在0~2mm之间,要符合GB985-88或CB/T3190-97标准,其焊脚高度要符合焊接规格表,如以下主要部位:主甲板与舷顶列板、主龙筋上下与内外底板、主副机座的复板与内底板和机座面的角接缝、横舱壁与舷壳板及内底板之间的周边角焊缝。
3.4.2、其余地方的角焊缝按焊接规格表要求,必须保证焊脚高度,如保证不了,那就必须开焊接坡口后再施焊。
3.4.3、当船体构件采用间断焊缝时,对下列部位在包角焊缝的规定长度内应采用双面连续角焊缝。
(1)肘板趾端的包角焊缝的长度不小于连接骨材的高度,且不小于75mm;(2)型钢端部,特别是短型钢的端部削斜时,其包角焊缝的长度应不小于型钢的高度且不小于削斜长度;(3)当各种构件的切口、切角和挖孔焊的端部处和所有相互垂直连接构件和垂直交叉处板厚大于12mm时,其包角焊缝的长度应不小于50mm。
3.4.4、当船体采用挖孔间断焊时,孔的两端应呈圆弧形并应光滑,但在下列位置处不准开孔。
1)在肘板趾端的应力集中区域内;2)与主支承构件相交时,其主肋骨、纵骨及扶强材等的相交处两侧至少各230mm区域内。
3.4.5、对接、搭接与塞焊(1)不同厚度钢板进行对接,其厚度差大于或等于4mm时,应将厚板的边缘削斜,使其均匀过渡,削斜的宽度应不小于厚度差的4倍。
若其厚度差小于4mm时,可在焊缝宽度内使焊缝的外形均匀地过渡;(2)若必需采用搭接焊缝时,两板的搭接宽度应为较薄板厚度的3~4倍,但不必大于50mm。
搭接表面应紧贴合。
搭接的两端应施以连续角焊;(3)若外板与其内侧的型材腹板无法直接采用角焊缝进行连接时,可采用扁钢衬垫于构件腹板与外板之间,扁钢与外边的连接可用连续熔透焊缝或长孔塞焊。
塞焊孔的长度应不小于90mm,孔的宽度应不小于板厚的2倍,孔的端部呈半圆形,孔的间距应不大于150mm。
长孔塞焊通常不必在孔内填满焊肉。
3.5、角焊缝与对接缝交叉时,应先焊对接缝,然后将角接缝处对接缝处的余高铲平,最后进行角焊接。
3.6、船体主要结构中的平行焊缝应保持一定的距离。
对接焊缝之间的平行距离应不小于100mm,且避免尖角相交,对接焊缝与角接焊缝之间的平行距离应不小于50mm。
3.7、强力甲板边板开单面坡口留根3mm,其坡口形式可按施工情况决定。
与主机座相连接的其它各构件及所有水密构件必须采用双面连续焊。
3.8、焊接区域的铁锈、氧化皮、油污、水分及其他污物必须消除干净。
3.9、焊接环境条件(如下雨、下雪、刮大风应停止施焊)应保证良3.10、焊机电流必须保持稳定电流、电压。
(先进行调试试验)。
3.11、自动焊丝不能生锈,焊剂不能受潮。
3.12、焊接构件或部件必须将其放置平整自然状态。
3.13、低氢焊条应按规定烘焙保温后才能使用,烘焙保温要求:将低氢焊条放在烘箱内先加温到350℃左右后保温2小时,然后再降到150℃保温,此时随用随取,重复烘焙不能超过两次。
4、焊接质量要求(1)焊缝均须进行外观检查,不应有咬边、溶瘤、浇穿、弧坑、表面夹缝及裂纹等缺陷。
(2)外板对接焊缝必须进行内部检查,可采用射线透视、超声波探伤或其它相应有效的方法进行。
如发现夹渣、未焊透、裂纹、密集气孔等缺陷应铲除重焊。
5、焊接工艺程序及注意要点5.1、焊接方向焊接方向是由里向外焊,左右对称焊,焊缝较长时应采用从中间向两端逐步退焊法和分段跳焊法,以减少构件变形和内应力。
5.2、焊接工艺程序先焊板材对接缝—→再焊型材对接缝—→再焊型材间角接缝—→最后焊板材与型材间的角接缝。
5.3、焊接要点5. 3 1、先焊接不致对其他焊缝形成刚性拘束的焊缝。
5.3.2、每条焊缝在焊接时应保持其一端能自由收缩。
5.3.3、手工焊时应先焊对称立角焊,焊立角焊时应采用逐步退焊法,跳焊法,交替法。
焊工人数尽量采用双数对称焊。
5. 3. 4、焊接工艺注意的问题5. 3. 4. 1 定位焊数量尽量减少,定位焊有一定的焊缝高度,定位焊应与施焊的质量相同,有缺陷的定位焊应在施焊前清除干净。
5. 3. 4. 2 焊缝未端收口处应填满孤坑,以防产生弧坑裂纹。
自动焊应使用引弧板,引弧板长度不少于100mm。
5. 3. 4. 3 进行多道焊时,应在下道焊前将前道焊的焊渣清除干5. 3. 4. 4 对要求焊透的焊缝在第二面焊缝前应进行清根,并开适当的坡口形式,以便进行封底焊。
若全焊透的对接焊缝无法进行封底焊时,允许加固定垫板进行对接焊,但此种接头的坡口形式及装配间隙应保证其在垫板上清能完全熔合。
5. 3. 4. 5 肘板的角接缝若迂上小夹角不能两面焊时,可在纯角位置的一面施焊,但肘板的趾端应有一定的包角焊缝。
5. 3. 4. 6 不同板厚进行对接,其厚度差大于或等于4mm时,应将厚板的边缘削斜,削斜宽度不小于板厚差的4倍。
5.3.5、分段安装焊接时,必须使之具有一定刚性方可开始焊接。
5.3.6、分段纵向大接缝的焊接:5.3.6.1 先焊横向构件的连接缝。
5.3.6.2 再焊板与板的舱内纵向大接缝—→再焊骨架与板材的角焊缝—→最后焊外板外壳面(批缝后)纵向大接缝。
5.3.7、分段横向大接缝的焊接5.3.7.1 先焊纵向构件的对接缝,然后进行环形接缝焊接。
最后焊接内部构件与船体外板、甲板、内底板角接缝。
5.3.7.2 环形焊缝在十字接头处应先焊纵向焊缝,后焊环形焊缝。
5.3.7.3 船体外板的对接缝应先焊有构件一侧的内面焊缝,先在外板外表面点焊,再在内侧批缝后再焊,否则板缝会错边。
焊完后再焊外表面(批缝后)焊缝。
6、焊接质量控制点6.1、焊接人员技术等级的控制6.1.1、焊工应进行考试考核,按船检认可的《焊工考试规则》进行考试,合格后方可上岗。
6.1.2、持有CCS船检颁发或认可的《焊工合格证书》的焊工方可从事与其证书同等级的焊接工作。
6.2、焊接材料及设备的控制6.2.1、采用低氢焊条必须使用直流焊机进行焊接。
6.2.2、采用H08Mn2si焊丝或H08Mn2siA焊丝应使用CO2气体6.2.3、采用08A焊丝及相配焊剂应使用半自动埋弧焊机进行焊接。
6.3、外板缝焊接外板缝按船舶有关标准进行刨坡口,先内后外。
刨坡口应根据焊接进度同步进行。
刨坡口后进行打磨,合格后速焊接,不允许坡口内有生锈及杂质存在。
6.4、焊接标准6.5.1、本船焊接规格,必须按《焊接规格明细表》要求执行。
6.5.2、所有构件的切口,切角和开的流水孔、通焊孔端部处所有相互垂直连续构件的交叉处应进行包角焊,包角焊必须填满、间断焊的构件两端部的包角焊的长度应在75mm~225mm之间。
7、焊接变形的控制7.1、首先检查装配间隙,应符合要求。
7.2、坡口尺寸必须符合CB*3190-97标准。
7.3、拼板厚度要平直,并在自然状态下拼焊。
7.4、掌握焊缝宽度及焊脚尺寸。
7.5、正确选择焊接程序。
7.6、适当采用刚性固定法施焊。
7.7、预留反变形量。
7.8、平直板缝采用自动焊接,自动焊的引弧板长度应不小于100mm。