统计过程控制简介 2014.11.12
统计过程控制(SPC)

第一节 统计过程控制概述
一、过程控制的基本概念
为实现产品生产过程质量而进行的有组 织、有系统的过程管理活动
主要内容
(1)对过程进行分析并建立控制标准 (2)对过程进行监控和评价 (3)对过程进行维护和改进
二、统计过程控制 应用统计技术对过程中的各个阶段进行评 估和监控,建立并保持过程处于可接受的 并且稳定的水平,从而保证产品与服务符 合规定的要求的一种质量管理技术。 内容 (1)利用控制图分析过程的稳定性,对 过程存在的异常原因进行预警; (2)计算过程能力指数分析稳定的过程 能力满足技术要求的程度,对过程质量进行 评价。-可接受性
2 K T/ 2 T
(0<K<1)
K: μ对M的偏移度,ε=|M-μ|
T 则:C pK 1 K C p 1 K 6
其中:ε——μ与公差中心M偏移量 T——公差带宽 T=TU—TL
(四)Cp和Cpk的比较与说明 Cp—— 反映过程加工的一致性,即 “质量能力”
或
1 5 n P P
P0 :给定标准值 P :未给定标准值 2. 计算样本不合格品率
3. 算P图的控制限
P 1 P UCLP P 3 n
CLP P
P1 P LCLP P 3 n
4. 样本不合格品率描点 5. 判稳/判异
6. 关于样本量ni的说明 ( 1 )若样本量 n 大小相等,则 P 图控制限为两条直线。 ( 2 )若样本量 ni 不全相等,则 P 图 控制限呈凹凸状。
分析过程若失控或异常,找出原因, 进行纠正,防止再发生。
7. 计算 X 图控制限并作图,判断状态。
8. 计算过程能力指数验证是否符合要求 9. 延长控制限,作控制用控制图,进行日 常管理
统计过程控制概述
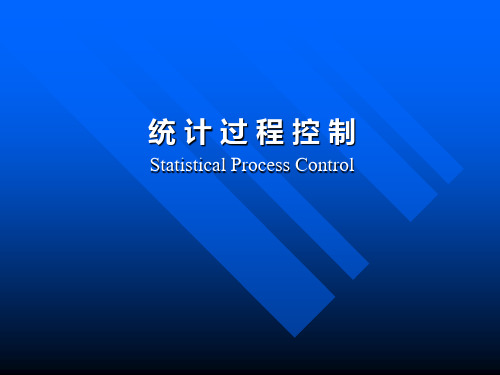
我们必须在失败中寻找胜利,在绝望中寻求希望
•
9、
。上 午4时14 分39秒 上午4 时14分0 4:14:39 20.11.3 0
控制图应用
步骤三、计算R图控制线
UCLR R 3 R D4 R CLR R R LCLR R 3 R D3 R
控制图应用
步骤四、计算 图控制线 X
UCLX X 3 X X A2 R CLX X X LCLX X 3 X X A2 R
控制图应用
步骤五、作R图 a、根据控制线作图 b、数据描点,判稳 c、不稳定则控制过程,回步骤二
贯彻预防原则 应用统计技术 保持过程稳定 保证产品质量
SPC的特点
强调全员参与 强调统计方法 强调过程、体系
二、控制图原理
控制图原理
控制图的结构:
样
UCL
本
统 计
CL
量
数 据
LCL
控制图
控制图原理
过程变差 偶然因素
过程固有 波动随机 对质量影响小
异常因素
非过程固有 对质量影响大
质量波动
•
1、
功的路 。20.11.3020.11.30Monday, November 30, 2020
成功源于不懈的努力,人生最大的敌人是自己怯懦
•
2、
。0 4:14:39 04:14:3 904:141 1/30/2 020 4:14:39 AM
每天只看目标,别老想障碍
•
3、
。20.1 1.3004: 14:390 4:14Nov -2030-Nov-20
控制图判异准则:
国标GB/T 4091-2001
UCL A B
CL C C B
统计过程控制(简称SPC)
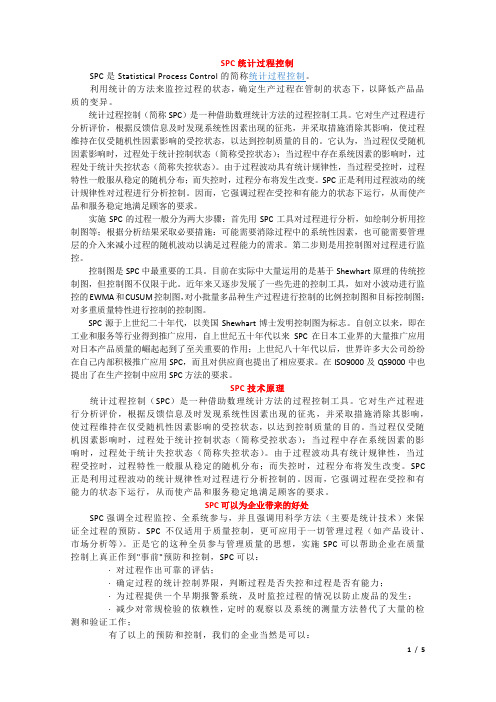
SPC统计过程控制SPC是Statistical Process Control的简称统计过程控制。
利用统计的方法来监控过程的状态,确定生产过程在管制的状态下,以降低产品品质的变异。
统计过程控制(简称SPC)是一种借助数理统计方法的过程控制工具。
它对生产过程进行分析评价,根据反馈信息及时发现系统性因素出现的征兆,并采取措施消除其影响,使过程维持在仅受随机性因素影响的受控状态,以达到控制质量的目的。
它认为,当过程仅受随机因素影响时,过程处于统计控制状态(简称受控状态);当过程中存在系统因素的影响时,过程处于统计失控状态(简称失控状态)。
由于过程波动具有统计规律性,当过程受控时,过程特性一般服从稳定的随机分布;而失控时,过程分布将发生改变。
SPC正是利用过程波动的统计规律性对过程进行分析控制。
因而,它强调过程在受控和有能力的状态下运行,从而使产品和服务稳定地满足顾客的要求。
实施SPC的过程一般分为两大步骤:首先用SPC工具对过程进行分析,如绘制分析用控制图等;根据分析结果采取必要措施:可能需要消除过程中的系统性因素,也可能需要管理层的介入来减小过程的随机波动以满足过程能力的需求。
第二步则是用控制图对过程进行监控。
控制图是SPC中最重要的工具。
目前在实际中大量运用的是基于Shewhart原理的传统控制图,但控制图不仅限于此。
近年来又逐步发展了一些先进的控制工具,如对小波动进行监控的EWMA和CUSUM控制图,对小批量多品种生产过程进行控制的比例控制图和目标控制图;对多重质量特性进行控制的控制图。
SPC源于上世纪二十年代,以美国Shewhart博士发明控制图为标志。
自创立以来,即在工业和服务等行业得到推广应用,自上世纪五十年代以来SPC在日本工业界的大量推广应用对日本产品质量的崛起起到了至关重要的作用;上世纪八十年代以后,世界许多大公司纷纷在自己内部积极推广应用SPC,而且对供应商也提出了相应要求。
在ISO9000及QS9000中也提出了在生产控制中应用SPC方法的要求。
统计过程控制简本

03
CATALOGUE
统计过程控制实施步骤
明确目标与范围
确定控制对象
明确需要控制的产品或过程特性,以 及相应的质量标准和要求。
制定控制计划
根据产品或过程特性,制定相应的统 计过程控制计划,包括采样方案、控 制图类型、异常处理流程等。
数据收集与整理
采集数据
按照控制计划的要求,定时或定量地采 集需要控制的产品或过程特性的数据。
应用领域与意义
应用领域
SPC可应用于制造业的各个领域,如机械加工、电子制造、汽车制造、航空航天等。同时,也可应用于服务业、 医疗、教育等非制造领域的过程控制。
意义
通过实施SPC,企业可以及时发现并消除生产过程中的异常因素,确保产品质量稳定可靠;降低生产成本,提高 生产效率;提升企业市场竞争力,实现可持续发展。同时,SPC还有助于推动企业质量管理水平的提升,促进企 业整体管理水平的提高。
正态分布与3σ原则
正态分布
在影响产品质量的众多因素中,当随机 因素占主导地位时,产品质量特性往往 服从正态分布。正态分布具有钟型曲线 特点,其概率密度函数关于均值对称。
3σ原则
正态分布的一个重要性质是,约有99.73%的数 据分布在均值的三倍标准差(3σ)范围内。因 此,在实际应用中,通常将均值加减三倍标准 差作为控制界限,超出此范围的数据视为异常 值。
目的
提高产品质量、降低生产成本、提升生产效率,最终实现企业经济效益的提升 。
发展历程及现状
发展历程
SPC起源于20世纪初的工业革命时期,随着生产规模的扩大 和产品质量要求的提高,逐渐发展成为一门独立的学科。经 历了手工绘图、机械化、自动化等发展阶段,目前正向智能 化、大数据等方向发展。
统计过程控制

统计过程控制统计过程控制(SPC)是一种基于数据分析的质量管理方法,旨在通过对过程的监测与控制,实现生产过程中的连续改进。
这种方法可以帮助提高产品质量,降低生产成本,提高客户满意度。
以下是SPC的简介、使用方法、益处以及实现过程中可能存在的问题。
简介SPC的理念是“控制过程而不是修理产品”,它的核心是把质量管理的重点从检查和纠正缺陷转移到控制过程。
SPC主要应用于制造业,但也适用于服务业和医疗行业等其他领域。
通过数据收集、分析和监控,SPC可以帮助企业了解其生产过程并制定相应的改进计划,从而实现生产效率和产品质量的提高。
使用方法SPC主要包括数据的收集和分析两个阶段。
数据的收集通常是由受训人员通过抽样等方式获取,然后数据会被汇总到一个控制图表中。
控制图表是SPC最基本的工具,它可以反映生产过程中数据的变化情况,通过样本数据的变化来判断是否存在特殊因素,以及是否需要采取相应的措施来防止这些因素的再次出现。
在数据分析阶段,SPC通常使用各种统计方法来分析数据的规律性和变动性,从而确定过程的性能是否符合要求。
如果发现过程出现特殊的变化,就需要针对这些问题采取相应的措施。
然后,通过监控过程的稳定性和性能,来确保所采取的措施有效。
益处SPC的主要益处是提高质量和降低成本。
由于SPC持续地跟踪和分析数据,可以及时发现问题,并采取相应的措施。
这减少了产品缺陷率和因此而导致的重新工作或返工数量。
此外,SPC还可以提高生产效率,因为它可以减少生产中的浪费和停机时间,并优化制造工艺。
此外,SPC还可以增加生产过程的可持续性,使过程更加稳定,从而提高客户满意度。
实现过程中可能存在的问题尽管SPC被广泛运用于生产领域,但在实施过程中仍然存在一些问题。
例如,如果质量数据不正确或不完整,则无法有效地检测和纠正问题。
确保收集到正确和完整的数据非常重要。
另一个问题是寻找和培养高素质的SPC人才。
虽然有许多SPC工具和软件可以帮助质量控制人员更好地应用SPC,但必须确保员工已经得到了适当的培训,以确保他们理解SPC的基本概念和运用方法。
第四章 统计过程控制
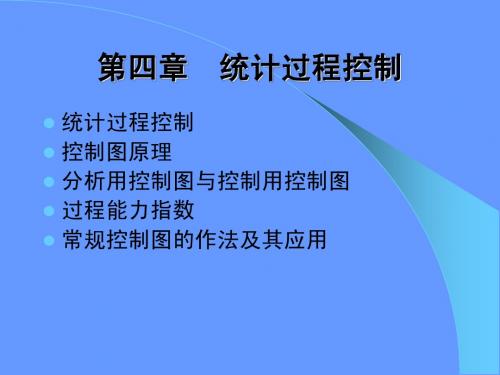
例:某零件的强度的屈服界限设计要求为4800— 5200㎏/㎝2,从100个样品中测得样本均值标准 偏差为62㎏/㎝2,求过程能力指数。 解:当过程处于稳定状态,而样本大小n=100也 足够大,可以用样本均值标准偏差估计σ,且 它的修正系数近似为1。过程能力指数为:
CP
5 2 0 0 4 8 0 0 6 62 1 .0 7 5
过程能力指数值的评价参考
Cp值的范围 级别
Cp ≥1.67 1.33≤ Cp <1.67 1.00≤ Cp <1.33 0.67≤ Cp <1.00 Cp <0.67
过程能力评价参考
过程能力过高(视具体情况而定)。 过程能力充分,表示技术管理能力已很好,应 继续维护。 过程能力充足,但技术管理能力较勉强,应设 法调整为Ⅱ级。 过程能力不足,表示技术管理能力已很差,应 采取措施立即改善。 过程能力严重不足,表示应采取紧急措施和全 面检查,必要时可停工整顿。
局部问题对策及系统改进
由异常原因造成的质量变异可由控制图发现,通 常由过程人员负责处理,称为局部问题的对策。 由偶然原因造成的质量变异可通过分析过程能力 发现,但改善往往耗费大量资金,需由高一级 管理人员决策,称为系统改进。
过程能力与过程能力指数
过程能力(process capability)是指过程处于 稳定状态下的实际的加工质量方面的能力。 “稳定生产状态”下的工序应该具备的条件: (1)原材料或上一道工序半成品按照标准要求 供应; (2)本工序按作业标准实施,并应在影响工序 质量各主要因素无异常的条件下进行; (3)工序完成后,产品检测按标准要求进行。
控制图名 称
统计过程控制(SPC)

解:
于是,过程能力指数为:
过程能力不够充分,从图2发现分布中心μ=0.1968与规范中心M=(TU+TL)/2=0.1720有偏离,应进行调整。调整后,Cp值会有所提高。
单侧规范情况的过程能力指数
01
只有上限要求,而对下限没有要求: 只适用于的范围:
02
只有下限要求,而对上限没有要求: 只适用于的范围:
4
3
6
5
判稳准则的分析 判稳准则的思路
打一个点未出界有两种可能性:
► 过程本来稳定 ► 漏报 (这里由于α小,所以β大),故打一个点子未出界不能立即判稳。
在点子随机排列的情况下,符合下列各点之一判稳:
01
► 连续25个点,界外点数d=0;
02
► 连续35个点,界外点数d<0;
03
► 连续100个点,界外点数d<2。
0.1821
0.1828
0.0086
18
0.1812
0.1585
0.1699
0.168
0.1694
0.0227
19
0.1700
0.1567
0.1694
0.1702
0.1666
0.0135
20
0.1698
0.1664
0.17
0.16
0.1666
0.01
图1
μ’
μ
图2-7 正态曲线随着标准差变化
σ=2.5
σ=1.0
σ=0.4
y
x
不论μ与σ取值为何,产品质量特性值落在[μ-3σ,μ+3σ]范围内的概率为99.73%。 图2-8 正态分布曲线下的面积
统计过程控制技术
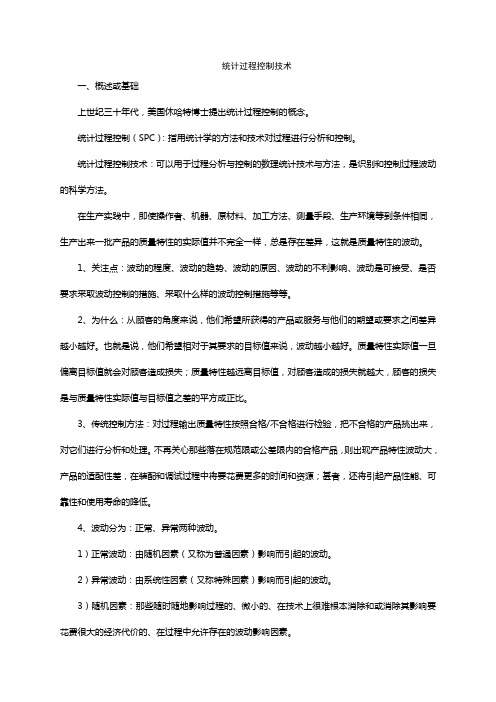
统计过程控制技术一、概述或基础上世纪三十年代,美国休哈特博士提出统计过程控制的概念。
统计过程控制(SPC):指用统计学的方法和技术对过程进行分析和控制。
统计过程控制技术:可以用于过程分析与控制的数理统计技术与方法,是识别和控制过程波动的科学方法。
在生产实践中,即使操作者、机器、原材料、加工方法、测量手段、生产环境等到条件相同,生产出来一批产品的质量特性的实际值并不完全一样,总是存在差异,这就是质量特性的波动。
1、关注点:波动的程度、波动的趋势、波动的原因、波动的不利影响、波动是可接受、是否要求采取波动控制的措施、采取什么样的波动控制措施等等。
2、为什么:从顾客的角度来说,他们希望所获得的产品或服务与他们的期望或要求之间差异越小越好。
也就是说,他们希望相对于其要求的目标值来说,波动越小越好。
质量特性实际值一旦偏离目标值就会对顾客造成损失;质量特性越远离目标值,对顾客造成的损失就越大,顾客的损失是与质量特性实际值与目标值之差的平方成正比。
3、传统控制方法:对过程输出质量特性按照合格/不合格进行检验,把不合格的产品挑出来,对它们进行分析和处理。
不再关心那些落在规范限或公差限内的合格产品,则出现产品特性波动大,产品的适配性差,在装配和调试过程中将要花费更多的时间和资源;甚者,还将引起产品性能、可靠性和使用寿命的降低。
4、波动分为:正常、异常两种波动。
1)正常波动:由随机因素(又称为普通因素)影响而引起的波动。
2)异常波动:由系统性因素(又称特殊因素)影响而引起的波动。
3)随机因素:那些随时随地影响过程的、微小的、在技术上很难根本消除和或消除其影响要花费很大的经济代价的、在过程中允许存在的波动影响因素。
特点:a)在过程中时刻存在着,对过程波动的影响力随时变化。
b)这类因素一般复杂繁多,要列举出所有的因素很困难。
c)所有随机因素的共同作用导致了过程的总波动。
d)很难通过对过程的控制来减小或消除随机因素的影响。
统计过程控制简介

1997年6月
JUNE 1997
• 经理看到从去年开始废品率持续下降
Manager has seen reduced scrap levels since the end of last year
• 教训:“严格的管理会出成效!”
The Learning : “A tough management style gets results!”
客户需求上限
Upper “Customer” Requirement
这一方法导致何种管理行为?
This method causes what type of management behavior?
1996年4月
APRIL 1996
• 工厂废品率为年度最低的2%
The factory scrap level is at a year low of 2%
统计过程控制简介
本课件仅供大家学习学习 学习完毕请自觉删除
谢谢 本课件仅供大家学习学习
学习完毕请自觉删除 谢谢
Project Tracker
Project Hopper and Sponsor Role
Revision 5
Project Start Date:
Review 6 Sigma Databases
3
Scrap Level (%)废品率
2
Celebration Time
1 JFMA
1996
Derived from Understanding Variation: The Key To Managing Chaos, Donald J. Wheeler, SPC Press. 1993.
1996年6月
Scrap Level (%)废品率
统计过程控制(简本)
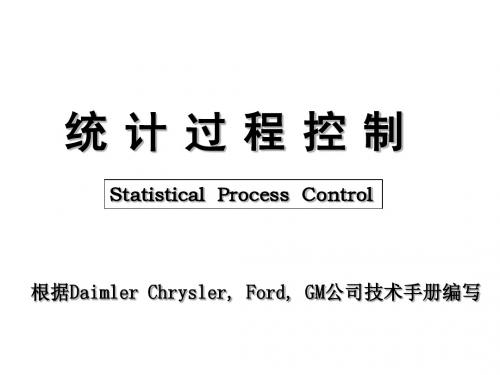
C p 1.00
C p 1.33
C p 1.67
-5 -4 -3 -2 -1
1.5
1.0
0.75
0.6
USL
0
1 2 3 4 5 P=4.45% p=0.27% p=60ppm p=0.6ppm
LSL
4.过程能力与过程性能
4.2 计算
Cp > 1.33, 可以 Cp = 1.00 – 1.33, 可以但須采取措施 Cp < 1.00, 不足
Incapable Borderline Capable
Cp = < 1.00
Cp = 1.00 – 1.33
Cp = > 1.33
4.过程能力与过程性能
数据: (1)计量值数据 计件 (2)计数值数据 计点 (3)数据的特征值 _ 平均值 X ~ 反映集中位置 中位数 X 极 差 R 反映分散程度 标准差 S
统计学术语和定义
平均值 - 总体或样本的平均值。 ^ 用x或来表示样本,用来表示总体。
x
=
1
n
n
xi ,
平均值的公式 在这里X1是样本的第一个点, Xn是样本的最后一个点。 .
CPK与PPK的区别
过程固有变差—仅由于普通原因产生的那部份过程变差,可以从控制图 上通过R/d2来估计。 过程变差—由于普通和特殊两种原因所造成的变差,本变差可用样本标 准差S来估计:
S= σS=
n ∑ i=1
(Xi-X)2 n-1
Xi为单值读数
CPK与PPK的区别
CO2 Levels for 55 Time Points
SPC基本原理 基本原理: 过程波动 两类波动
第四章统计过程控制(1)统计过程控制概述

第四章统计过程控制(1)统计过程控制概述四、常规控制图的应用单选5-7题,多选7-9题,综合分析1-2题。
考查方式以理解题和计算题为主。
总分值35-45分。
总分170分。
一、统计过程控制概述1.掌握统计过程控制的含义(重点) 2.了解统计过程控制的作用和特点(重点)二、控制图原理1.掌握控制图的基本原理(重点)2.了解控制图的两种错误(难点)3.掌握常规的控制图分类。
(难点。
重点)三、分析用控制图和控制用控制图1.熟悉分析用控制图和控制用控制图的区别(难点)2.掌握过程改进策略3.掌握控制图的判异准(重点)四、常规控制图的应用1.掌握x—r 图、x—s 图和p 图的作用和使用方法(难点.重点)2.了解x—rs 图、me—r 图、c 图和u 图的作图和应用。
(难点.重点)五、过程能力与过程能力指数1.熟悉过程能力的定义 (重点) 2.了解过程性能指数的概念3.掌握过程能力指数c p 和cpk 的计算和评价(难点.重点)六、过程控制的实施1.熟悉过程控制的基本概(重点)2.掌握过程分析的基本步骤(难点)3.熟悉过程管理点的要求4.1统计过程控制概述4.1统计过程控制概述统计过程控制主要解决两个问题:一是过程运行状态是否稳定,二是过程能力是否充足。
前者可利用控制图这种统计工具进行测定,后者可通过过程能力分析来实现。
统计过程控制理论是从制造业中的加工过程开始的,但是目前其应用已扩展到各种过程,如设计过程、管理过程、服务过程等。
学习目标要求(含4.1;4.2;4.3;)1、掌握统计过程的含义2、了解统计过程的作用和特点(一)过程控制p991、概念。
过程控制是指为实现产品的生产过程质量而进行的有组织、有系统的过程管理活动。
目的在地为生产合格产品创造有利的生产条件和环境,从根本上预防和减少不合格品的产生。
2、过程控制的主要内容(1)过程分析,建立控制标准。
分析影响过程质量的主导因素,找出最佳水平,实现标准化。
统计过程控制知识大全

统计过程控制知识大全1、统计过程控制的基本知识1.1统计过程控制的基本概念统计过程控制(Stastistical Process Control简称SPC)是为了贯彻预防原则,应用统计方法对过程中的各个阶段进行评估和监控,建立并保持过程处于可接受的并且稳定的水平,从而保证产品与服务符合规定要求的一种技术。
SPC中的主要工具是控制图。
因此,要想推行SPC必须对控制图有一定深入的了解,否则就不可能通过SPC取得真正的实效。
对于来自现场的助理质量工程师而言,主要要求他们当好质量工程师的助手:(1)在现场能够较熟练地建立控制图;(2)在生产过程中对于控制图能够初步加以使用和判断;(3)能够针对出现的问题提出初步的解决措施。
大量实践证明,为了达到上述目的,单纯了解控制图理论公式的推导是行不通的,主要是需要掌握控制图的基本思路与基本概念,懂得各项操作的作用及其物理意义,并伴随以必要的练习与实践方能奏效。
1.2统计过程控制的作用(1)要想搞好质量管理首先应该明确下列两点:①贯彻预防原则是现代质量管理的核心与精髓。
②质量管理学科有一个十分重要的特点,即对于质量管理所提出的原则、方针、目标都要科学措施与科学方法来保证他们的实现。
这体现了质量管理学科的科学性。
第2 页(共12 页)为了保证预防原则的实现,20世纪20年代美国贝尔电话实验室成立了两个研究质量的课题组,一为过程控制组,学术领导人为休哈特;另一为产品控制组,学术领导人为道奇。
其后,休哈特提出了过程控制理论以及控制过程的具体工具——控制图。
道奇与罗米格则提出了抽样检验理论和抽样检验表。
这两个研究组的研究成果影响深远,在他们之后,虽然有数以千记的论文出现,但至今仍未能脱其左右。
休哈特与道奇是统计质量控制(SQC)奠基人。
1931年休哈特出版了他的代表作《加工产品质量的经济控制》这标志着统计过程控制时代的开始。
(2)“21世纪是质量的世纪”。
美国著名质量管理专家朱兰早在1994年的美国质量管理年会上即提出此论断,若干年来得到越来越多的人的认同。
- 1、下载文档前请自行甄别文档内容的完整性,平台不提供额外的编辑、内容补充、找答案等附加服务。
- 2、"仅部分预览"的文档,不可在线预览部分如存在完整性等问题,可反馈申请退款(可完整预览的文档不适用该条件!)。
- 3、如文档侵犯您的权益,请联系客服反馈,我们会尽快为您处理(人工客服工作时间:9:00-18:30)。
正态分布的密度曲线是一条关于μ对称的
钟形曲线.特点是“两头小,中间大,左右
对称”.
表示方法:N (μ, σ2 ) 概率分布 P(μ- Xμ+)=0.6827 P(μ-2Xμ+2)=0.9545 P(μ-3Xμ+3)=0.9973
21
测量系统分析
测量系统分析的目的和用途
n
版权不得擅用
• Geometric Mean(几何平均)
中心值
• G = (X1*X2*... Xn) • 调和平均 •H=
1 n
1
1 1 n [Σ x ]
• Median(中央值)
•X • Mid-Range(平均范围) • M = Xmax + Xmin 2
18
常用统计方法
散布(Dispersions )
课程内容
版权不得擅用
统计过程控制简介
(Statistical Process Control)
制作人:刚子 2014.11.12
1
课程目录
I. 统计过程控制(SPC)的基本概念 II. 常用的统计方法 III. 量测系统分析 IV. 建立 SPC 的步骤 V. 控制图(计量型、计数型 ) VI. 工程能力分析
版权不得擅用
预测 ??
Time
出现不可预测的变化
10
SPC的基本概念
过程受控的理解
偶然原因
•大量的微小原因所引起 •原料在一定范围内之微小变异 •机械之微小振动 •仪器测定时,不十分精确之做法 •依据作业标准执行作业的变化 •实际上,要除去过程上的偶然原因
版权不得擅用
特殊原因
•一个或少数几个较大原因所引起 •使用规格外的原物料 •新手之操作人员 •不完全之机械调整 •未依据作业标准执行作业 •所制订之作业标准不合理
4
SPC的基本概念
过程控制系统图示
版权不得擅用
5
SPC的基本概念
变异(Variance)的理解
版权不得擅用
-没有完全相同的两件产品
变异或变差是客观存在的,任何过程都存在许多引起变差的原因。
产品间的差距也许很大,也许小得无法测量,但这些差距总是存在。
6
SPC的基本概念
变异(Variance)的来源
● 测量系统应该是统计受控制的
这意味着在可重复条件下,测量系统的变差只能是由于普通原因而不是特殊 原因造成。这可称为统计稳定性且最好由图形法评价。
● 对于产品控制,测量系统的变异性与公差相比必须小
● 对于过程控制,测量系统的变异性应该显示有效的分辨率并且
与制造过程变差相比要小
24
测量系统分析
计量型测定分析结果(MINITAB)
通 常 用 来 消 除 变 差 的 特 殊 原 因 通常由与过程直接相关的人员实施
通 常 可 纠 正 大 约 1 5 % 的 过 程 问 题
12
SPC的基本概念
发生变异后采取什么措施
系統措施 → 改善機遇原因
共同原因的变异 通过职称能力分析可 以发现
版权不得擅用
如Ca,Cp, Cpk,及控 制图上点的 变化
25
版权不得擅用
测量系统引起的分散
VarComp 0.004437 0.001292 0.003146 0.000912 0.002234 0.037164 0.041602 %Contribution (of VarComp) 10.67 3.10 7.56 2.19 5.37 89.33 100.00
BIAS
为了明确流程变动的原因,首先应知道测 量系统的变动, 并且要把它与流程变动相 区分, 测量 Gage R&R分析将这样的变动 要因定量化
23
稳定性
线性度
测量系统分析
―好的”测量系统
● 足够的分辨率和灵敏度
版权不得擅用
为了测量的目的,相对于过程变差呀规范控制限,测量的增量应该很小。通 常所知的十进位或10-1法则,表明仪器的分辨率应把公差(过程变差)分为十份 或更多。这个规则是选择量具期望的实际最低起点。
(分再现性和反复性两类 )
样品引起的分散
总分散
%Tolerance (SV/Toler) 22.87 12.34 19.26 10.37 16.23 66.19 70.03
标准偏差的 构成
识别能力
测量系统分析
计量型Graph分析(MINITAB)
Gage R&R (ANOVA) for 螟沥蔼
管理人员参与及过程 人員合作去改善
系统改善对策
必 須 改 善 造 成 变 异 的 偶 然 原 因
经 常 需 要 管 理 阶 层 的 努 力 与 对 策
大 約 可 以 解 決 8 5 % 之 过 程 上 的 問 題
13
SPC的基本概念
过程改进循环及过程控制
1. • • • 分析过程 本过程应做什么? 会出现什么问题? 本过程正在做些什么?
版权不得擅用
2
SPC的基本概念
SPC的定义
· Statistical - 利用统计方法(统计资料与分析技法) · Process · Control - 分析及把握工程的现象 - 使工程处于所希望的状态的管理技法
版权不得擅用
SPC是依据统计的逻辑, 来判断过程是否正常及是否 采取对策的一套控制系统。
,
是件非常不经济之处置
•非偶然原因之变异,不但可以找出其
原因,并且除去这些原因之处置,在 经济观点上来说 ,是正确的
11
SPC的基本概念
发生变异后采取什么措施
局部措施→改善因特殊原因导致的变异
非偶然原因的变异 通过简单的统计分析 就可以发现
版权不得擅用
如控制图
通 直接负责过程的人员 去改善 局部措施的改善对策
计方法』(Statistical Method from the point of Quality Control);
第二次世界大战前后,英、美两国将质量控制图的方法引进制造业; . 1950年日本邀请了戴明博士到日本演讲,介绍了SQC的技术观念;
为了纪念戴明博士的贡献,JUSE于1951年成立了戴明奖;
Percent
50
0 Gage R&R Repeat Reprod Part-to-Part
何前
1.1 1.0 0.9 0.8 0.7 0.6 0.5 0.4
1
2
3
4
5
6
7
8
9
10
R Chart by 累诀磊
0.15
1 2 3
By 累诀磊
UCL=0.1252
Sample Range
0.10 0.05 0.00 0
版权不得擅用
測量
结果
SQC-针对产品所做的 仍只是在做SQC
►检测——容忍浪费
►预防——避免浪费
15
SPC的基本概念
SPC的起源与发展
版权不得擅用
1924年修华特博士(W.A. Shewhart)在贝尔试验室发明了质量控制图; 1939年修华特博士与戴明博士(Deming)查品质
MSA
SPC/SQC TQM
22
DOE
测量系统分析
计量型测量系统变动的类型
观测到的流程变动
版权不得擅用
实际流程(制品)的变动
测量系统的变动
长期流程变动
短期流程变动
测量者造成的变 动
测量gage造成的 变动
再现性(Reproducibility)
反复性(Repeatability)
R=0.03833 LCL=0
累诀磊
1
2
3
Xbar Chart by 累诀磊
1.1 1.0 0.9 0.8 0.7 0.6 0.5 0.4 0.3 0
1 2 3
累诀磊*何前 Interaction
Average
UCL=0.8796 Mean=0.8075 LCL=0.7354 1.1 1.0 0.9 0.8 0.7 0.6 0.5 0.4
计划 实施 计划
版权不得擅用
2. 维护(控制)过程 • 监控过程性能 • 查找变异的特殊原因并 采取措施
实施
改善
研究
改善
研究
计划
实施
3.改進过程 ① 改变过程从而更好 ② 理解普然原因变异 减少偶然原因变差
改善
14
研究
SPC的基本概念
进行SPC的目的 SPC -针对过程的重要参数 进行控制管理 原物料 PROCESS
累诀磊
1 2 3
Sample Mean
1979年后SQC的理论是不足够的。单是在发生问题后,才去解决问 题,是一种浪费,所以进而发展出SPC; 美国汽车制造业,在QS9000中对SPC的使用提出了自己的要求, 推动了SPC的广泛应用.
16
常用统计方法
统计学中使用的基础术语
1) 总数和标本 ⊙ 总数(Population) : 成为所关心的对象的总的集合。
8
SPC的基本概念
过程受控的理解
受控的状态(偶然原因:不可避免)
- 安定的 - 管理状态 - 可预测的 - 只是偶然因素起作用
版权不得擅用
预 测
Time 没有不可预测的变化
9
SPC的基本概念
过程受控的理解
异常状态 (异常原因:可以避免的)
重要的变动 不安定的 管理状态以外的 不可预测的 发生了异常的原因
分散的构成
Gage R&R Source Total Gage R&R 反复性 再现性 测量者 测量者*产品 Part-To-Part Total Variation Gage R&R StdDev Study Var %Study Var Source (SD) (5.15*SD) (%SV) Total Gage R&R 0.066615 0.34306 32.66 Repeatability 0.035940 0.18509 17.62 Reproducibility 0.056088 0.28885 27.50 测量者 0.030200 0.15553 14.81 测量者*产品 0.047263 0.24340 23.17 Part-To-Part 0.192781 0.99282 94.52 Total Variation 0.203965 1.05042 100.00 Number of Distinct Categories (识别能力) = 4