XX试模报告
试块模具实验报告(3篇)

第1篇一、实验名称:试块模具实验二、实验目的1. 了解试块模具的结构及工作原理;2. 掌握试块模具的制作方法;3. 通过实验验证试块模具的性能;4. 提高对模具设计、制造和使用的认识。
三、实验原理试块模具是一种用于制作混凝土试块的装置,通过模具对混凝土试块进行成型和养护。
实验中,我们将按照一定的工艺要求,制作试块模具,并对模具进行性能测试。
四、实验仪器与材料1. 仪器:万能试验机、搅拌机、模具制作设备、电子秤、水平尺等;2. 材料:混凝土原材料、模具材料、密封胶等。
五、实验步骤1. 模具设计:根据实验要求,设计试块模具的结构和尺寸,绘制模具图纸;2. 模具制作:按照模具图纸,使用模具制作设备制作试块模具;3. 模具检验:对制作完成的试块模具进行检验,确保模具尺寸准确、表面平整、无变形;4. 混凝土制备:按照混凝土配合比,制备混凝土;5. 模具安装:将制作好的试块模具安装到万能试验机上;6. 混凝土浇筑:将制备好的混凝土浇筑到试块模具中,并使用水平尺调整混凝土表面平整;7. 养护:将浇筑好的混凝土试块进行养护;8. 模具拆模:养护完成后,拆下试块模具,观察试块质量;9. 性能测试:使用万能试验机对试块进行性能测试,如抗压强度、抗折强度等。
六、实验数据记录与分析1. 模具尺寸:长×宽×高=(mm);2. 模具重量:kg;3. 混凝土配合比:水泥:砂:石子:水=(kg/m³);4. 养护时间:天;5. 拆模后试块质量:kg;6. 抗压强度:MPa;7. 抗折强度:MPa。
根据实验数据,对试块模具的性能进行分析:1. 模具尺寸:实验中制作的试块模具尺寸准确,符合设计要求;2. 模具重量:实验中制作的试块模具重量适中,便于运输和使用;3. 混凝土配合比:实验中制备的混凝土配合比合理,满足实验要求;4. 养护时间:实验中试块养护时间充足,确保混凝土强度;5. 拆模后试块质量:实验中拆模后试块质量良好,表面平整,无变形;6. 性能测试:实验中试块抗压强度和抗折强度均达到设计要求。
压铸试模总结报告范文(3篇)

第1篇一、项目背景随着我国汽车、电子、电器等行业的发展,对精密金属制品的需求日益增加。
压铸作为一种高效、节能、环保的金属成型工艺,广泛应用于各类产品的制造中。
为了确保压铸件的质量和性能,试模环节至关重要。
本报告针对某型号压铸件进行试模,总结试模过程中的经验与教训,为后续生产提供参考。
二、试模目的1. 确保压铸件尺寸精度和表面质量;2. 优化模具结构,降低生产成本;3. 提高生产效率,缩短生产周期;4. 评估压铸工艺参数,为生产提供依据。
三、试模过程1. 模具设计:根据产品图纸,设计压铸模具,包括型腔、浇注系统、冷却系统等。
2. 模具加工:按照模具设计图纸,进行模具加工,确保模具精度和表面质量。
3. 模具装配:将加工好的模具零件进行装配,确保模具的刚性和密封性。
4. 工艺参数确定:通过实验,确定压铸工艺参数,如熔体温度、压射速度、保压压力、冷却时间等。
5. 压铸实验:在确定的工艺参数下,进行压铸实验,观察压铸件的尺寸精度、表面质量、内部缺陷等。
6. 数据分析:对实验数据进行整理和分析,评估压铸件的质量和性能。
四、试模结果1. 尺寸精度:压铸件尺寸精度达到产品图纸要求,无明显的尺寸偏差。
2. 表面质量:压铸件表面光滑,无明显的缺陷,如气孔、夹杂等。
3. 内部缺陷:压铸件内部无明显的缩松、冷隔等缺陷。
4. 生产成本:通过优化模具结构和工艺参数,降低了生产成本。
5. 生产效率:压铸实验证明,压铸件生产周期可缩短20%。
五、总结与建议1. 优化模具设计:在保证模具刚性和密封性的前提下,简化模具结构,降低生产成本。
2. 严格控制工艺参数:根据实验结果,确定合理的熔体温度、压射速度、保压压力、冷却时间等工艺参数。
3. 加强过程控制:在生产过程中,严格控制熔体温度、压射速度、保压压力等关键参数,确保压铸件质量。
4. 优化生产线:提高生产线自动化程度,降低人工成本,提高生产效率。
5. 持续改进:针对试模过程中发现的问题,持续改进模具设计、工艺参数和生产工艺,提高产品质量。
压铸试模报告范文
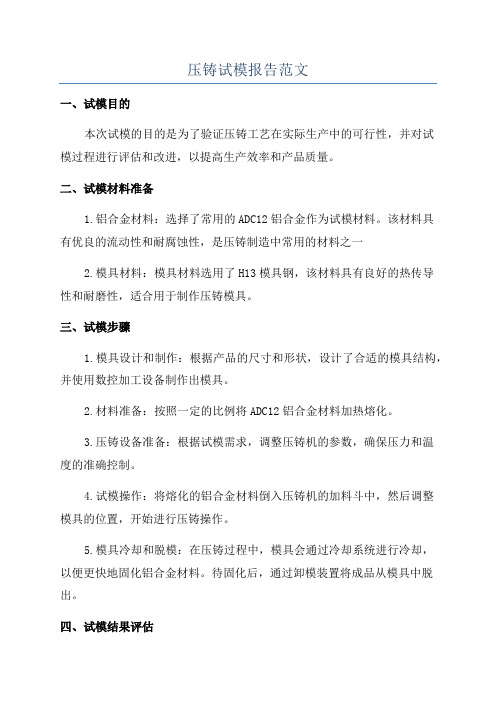
压铸试模报告范文一、试模目的本次试模的目的是为了验证压铸工艺在实际生产中的可行性,并对试模过程进行评估和改进,以提高生产效率和产品质量。
二、试模材料准备1.铝合金材料:选择了常用的ADC12铝合金作为试模材料。
该材料具有优良的流动性和耐腐蚀性,是压铸制造中常用的材料之一2.模具材料:模具材料选用了H13模具钢,该材料具有良好的热传导性和耐磨性,适合用于制作压铸模具。
三、试模步骤1.模具设计和制作:根据产品的尺寸和形状,设计了合适的模具结构,并使用数控加工设备制作出模具。
2.材料准备:按照一定的比例将ADC12铝合金材料加热熔化。
3.压铸设备准备:根据试模需求,调整压铸机的参数,确保压力和温度的准确控制。
4.试模操作:将熔化的铝合金材料倒入压铸机的加料斗中,然后调整模具的位置,开始进行压铸操作。
5.模具冷却和脱模:在压铸过程中,模具会通过冷却系统进行冷却,以便更快地固化铝合金材料。
待固化后,通过卸模装置将成品从模具中脱出。
四、试模结果评估1.成品质量:通过对试模得到的成品进行质量检测,包括尺寸测量和质量缺陷检查等。
结果表明,成品的尺寸和表面质量都满足设计要求,符合生产标准。
2.生产效率:根据试模过程中的数据记录,分析了生产周期、模具磨损、温度控制等因素对生产效率的影响。
提出了针对性的改进措施,以进一步提高生产效率。
3.模具寿命评估:通过对模具的磨损程度进行评估,结合试模过程中的观察和数据记录,估计了模具的寿命。
并提出了加强模具保养和维修的建议,以延长模具使用寿命。
五、试模结论和改进建议根据试模结果评估,可以得出以下结论和改进建议:1.压铸工艺在生产实践中具有很高的可行性,能够满足产品的质量要求。
2.需要进一步改进压铸工艺中的一些参数,以提高生产效率和降低生产成本。
3.模具在试模过程中表现出较高的耐磨性,但仍需加强模具的保养和维修工作,以延长模具的使用寿命。
综上所述,本次压铸试模取得了满意的成果,并为今后的生产提供了指导意见。
注塑模试模报告单
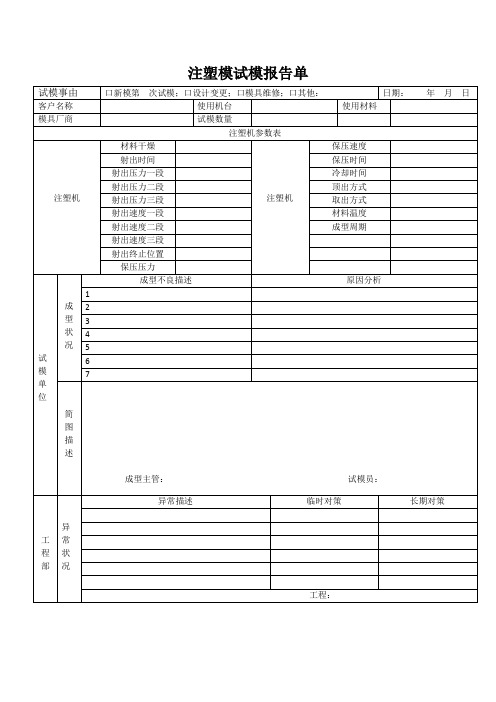
试模事由
口新模第次试模;口设计变更;口模具维修;口其他:
日期:年月日客户名称 Nhomakorabea使用机台
使用材料
模具厂商
试模数量
注塑机参数表
注塑机
材料干燥
注塑机
保压速度
射出时间
保压时间
射出压力一段
冷却时间
射出压力二段
顶出方式
射出压力三段
取出方式
射出速度一段
材料温度
射出速度二段
成型周期
射出速度三段
射出终止位置
保压压力
试模单位
成
型
状况
成型不良描述
原因分析
1
2
3
4
5
6
7
简图描述
成型主管:试模员:
工程部
异常状况
异常描述
临时对策
长期对策
工程:
注塑试模产品报告模板

注塑试模产品报告模板一、试模背景及目的本次试模的背景是为了测试某个注塑产品的生产工艺及模具可行性,并验证产品的质量符合要求。
试模的目的是通过实际注塑生产出的产品,评估其尺寸精度、表面质量以及材料流动性等性能。
二、试模过程及参数设置1. 模具选择:XXX型号模具;2. 原料选择:XXX材料;3. 注塑设备:XXX注塑机;4. 注塑参数设置:- 射出压力:XXX MPa;- 射速:XXX mm/s;- 射胶量:XXX g;- 螺杆转速:XXX rpm;- 模具温控温度:XXX ;- 冷却时间:XXX s。
三、试模结果分析1. 尺寸精度测量了注塑产品的尺寸,并与设计要求进行对比分析。
结果显示,产品的尺寸精度符合要求,各个关键尺寸的偏差在允许范围内。
2. 表面质量观察了注塑产品的表面质量,除了小部分产品存在一些细微的表面瑕疵外,整体表面质量良好,没有明显的气泡、划痕或色差。
3. 材料流动性通过观察产品的浇口、水口及排气情况,评估了材料在注塑过程中的流动性。
结果显示,材料流动性良好,浇口和水口处没有明显挤出现象,且排气通畅。
四、问题分析及解决方案根据试模结果,发现了一些问题,如单个产品出现略微尺寸偏差等。
经过分析,可能是以下原因导致:1. 模具加工精度不够,导致产品尺寸偏差;2. 注塑参数设置不合理,影响了产品的质量。
为了解决以上问题,采取了以下措施:1. 优化模具的制造工艺,提高精度,确保产品尺寸稳定;2. 调整注塑参数,如调整射胶量及温控温度等,以改善产品的质量。
五、本次试模总结本次试模结果显示,注塑产品在尺寸精度、表面质量和材料流动性等方面均符合要求。
通过问题分析和解决方案,确定了进一步优化模具和注塑参数的方向,以提高产品质量和生产效率。
未来将根据试模结果的反馈,继续进行改进和优化,以提高生产工艺的稳定性和产品的竞争力。
以上是本次注塑试模产品的报告模板,希望对您的工作有所帮助。
如有需要,请根据具体情况进行修改和补充。
模具试模验证报告
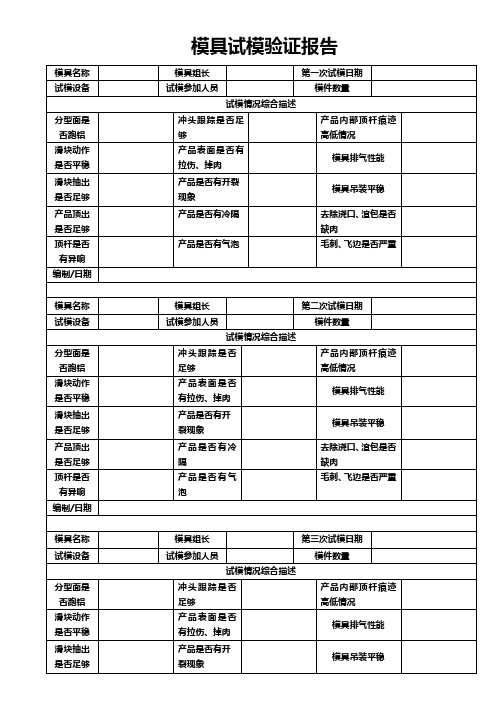
毛刺、飞边是否严重
编制/日期
模具名称
模具组长
第二次试模日期
试模设备
试模参加人员
模件数量
试模情况综合描述
分型面是否跑铝
冲头跟踪是否足够
产品内部顶杆痕迹高低情况
滑块动作是否平稳
产品表面是否有拉伤、掉肉
模具排气性能
滑块抽出是否足够
产品是否有开裂现象
模除浇口、渣包是否缺肉
去除浇口、渣包是否缺肉
顶杆是否有异响
产品是否有气泡
毛刺、飞边是否严重
编制/日期
模具试模验证报告
模具名称
模具组长
第一次试模日期
试模设备
试模参加人员
模件数量
试模情况综合描述
分型面是否跑铝
冲头跟踪是否足够
产品内部顶杆痕迹高低情况
滑块动作是否平稳
产品表面是否有拉伤、掉肉
模具排气性能
滑块抽出是否足够
产品是否有开裂现象
模具吊装平稳
产品顶出是否足够
产品是否有冷隔
去除浇口、渣包是否缺肉
顶杆是否有异响
顶杆是否有异响
产品是否有气泡
毛刺、飞边是否严重
编制/日期
模具名称
模具组长
第三次试模日期
试模设备
试模参加人员
模件数量
试模情况综合描述
分型面是否跑铝
冲头跟踪是否足够
产品内部顶杆痕迹高低情况
滑块动作是否平稳
产品表面是否有拉伤、掉肉
模具排气性能
滑块抽出是否足够
产品是否有开裂现象
模具吊装平稳
产品顶出是否足够
产品是否有冷隔
试模报告

试 模 报 告
项目 制模厂家 领料数量 打样数量 工序 工序名称 品 名 图 号 模 号 零件号 设计 试模 实际可用 机种/吨数 机种/吨位 机种/吨数 试模员 产品材质 剪口尺寸 厚度 宽度 步距 长度 开料尺寸 (卷料长度为C) 模具尺寸 (长*宽*高mm) 改模□ 试模责任人 设计人 完成日期 移模□ 新模□
气垫 试模后模具 问题点,建议修该项目及生产时 位置 注意事项,正常时填写正常。 压力
产பைடு நூலகம்简图
备注: 1、所有剪口模和连续模都要留1个料片,并注明模 号,零件号。 2、每工序都要留1至2个工序办并注明模号,零件号和 第几工序。 3、试模完成后,此表格必须交工程部存档。 审核:
验收 : 第一次试模合格/同意生产 修整后试模合格/同意生产 不合格/不同意生产 试模合格待确定
□ □ □ □
FORM:
工程部经理确认:
五金模试模报告

核准人 产品图号 模具名称 模具类型
生ቤተ መጻሕፍቲ ባይዱ部
试模部门
□合格 □不合格 说明:
□合格 □不合格 说明:
工程部判定意见说明
模具车间判定 意见说明
□合格 □不合格 说明:
最终判定 (必要时)
会签
生产部
备注
模具车间
试模人 工程部 模具车间
工程部
品质部
表单编号:FM-GC-018A
五金模试模报告
部门:模具部
日期
客户名称
申请人
材料名称
产品名称
样品数量
模具编号
试模次数 使用部门
使用机台
1、员工作业时是否安全? 2、员工作业是否顺畅、方便? 3、模具定位是否可靠、合理? 4、产品取出是否方便? 5、螺钉、销钉是否紧固好? 6、是否适合量产?
□合格 □不合格 说明:
□是 □否 □是 □否 □是 □否 □是 □否 □是 □否 □是 □否
试模总结报告范文(3篇)
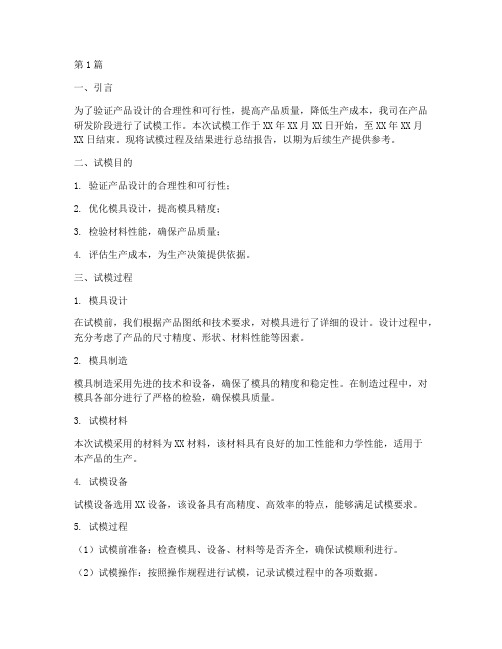
第1篇一、引言为了验证产品设计的合理性和可行性,提高产品质量,降低生产成本,我司在产品研发阶段进行了试模工作。
本次试模工作于XX年XX月XX日开始,至XX年XX月XX日结束。
现将试模过程及结果进行总结报告,以期为后续生产提供参考。
二、试模目的1. 验证产品设计的合理性和可行性;2. 优化模具设计,提高模具精度;3. 检验材料性能,确保产品质量;4. 评估生产成本,为生产决策提供依据。
三、试模过程1. 模具设计在试模前,我们根据产品图纸和技术要求,对模具进行了详细的设计。
设计过程中,充分考虑了产品的尺寸精度、形状、材料性能等因素。
2. 模具制造模具制造采用先进的技术和设备,确保了模具的精度和稳定性。
在制造过程中,对模具各部分进行了严格的检验,确保模具质量。
3. 试模材料本次试模采用的材料为XX材料,该材料具有良好的加工性能和力学性能,适用于本产品的生产。
4. 试模设备试模设备选用XX设备,该设备具有高精度、高效率的特点,能够满足试模要求。
5. 试模过程(1)试模前准备:检查模具、设备、材料等是否齐全,确保试模顺利进行。
(2)试模操作:按照操作规程进行试模,记录试模过程中的各项数据。
(3)试模结果分析:对试模结果进行分析,评估产品性能和模具质量。
四、试模结果及分析1. 产品性能(1)尺寸精度:产品尺寸精度达到设计要求,符合国家标准。
(2)形状:产品形状符合设计图纸,无明显变形。
(3)表面质量:产品表面光滑,无明显划痕、气泡等缺陷。
2. 模具质量(1)模具精度:模具精度达到设计要求,无明显磨损。
(2)模具稳定性:模具在试模过程中运行稳定,无异常现象。
3. 材料性能(1)力学性能:材料力学性能符合设计要求,具有较好的强度和韧性。
(2)加工性能:材料加工性能良好,易于加工。
4. 生产成本(1)模具成本:模具成本合理,符合预算。
(2)材料成本:材料成本合理,符合预算。
五、结论1. 产品设计合理,可行性高。
2. 模具设计精度高,稳定性好。
注塑部模具试模报告

注塑部模具试模报告1.实验目的本实验旨在通过注塑模具试模,了解注塑工艺过程、模具设计和注塑产品性能,并通过实验结果分析模具工艺参数对注塑产品质量的影响。
2.实验原理注塑模具试模是通过将塑料熔化后,注入模具中,经过冷却后得到所需形状的产品的过程。
注塑过程主要包括塑料熔融、注射、冷却和脱模等步骤。
3.实验设备和材料实验设备:注塑机、模具、冷却系统等。
实验材料:注塑塑料料粒、色料等。
4.实验步骤4.1模具安装与调试:根据模具图纸,将模具正确安装到注塑机上,并进行相关调试,保证模具工作正常。
4.2注塑机的操作设置:根据模具试模要求,设置注塑机的工艺参数,如射胶压力、保压时间、冷却时间等。
4.3材料的准备:将注塑塑料料粒与色料按照一定比例混合,并通过熔融设备将其熔化。
4.4模具上料:将熔化的塑料顺利注入到模具的进料口,并进行注塑过程。
4.5冷却脱模:根据注塑过程中设置的冷却时间,等待注塑产品冷却固化,并进行脱模操作。
4.6清理和分析:清理注塑产品和模具,对注塑产品进行外观、尺寸和性能等方面的分析和测试。
5.实验结果与分析通过模具试模实验,得到了一定数量的注塑产品,在清理和分析过程中,对注塑产品进行了外观、尺寸和性能等方面的分析。
5.1外观分析:通过外观观察发现,注塑产品表面光滑且没有明显的瑕疵和开裂现象,达到了预期的效果。
5.2尺寸分析:通过测量注塑产品的尺寸,发现其与设计图纸上的尺寸基本一致,满足了产品设计要求。
5.3性能分析:通过对注塑产品的质量、硬度、强度等性能参数进行测试,发现其满足了产品的使用要求。
6.实验总结通过本次注塑部模具试模实验,我们了解了注塑工艺过程和模具设计的重要性。
通过设置合适的注塑工艺参数,可以获得理想的注塑产品质量。
而模具的设计和制造则直接影响了产品的外观、尺寸和性能等方面。
实验过程中,我们遵循了规范的实验操作流程,并取得了预期的实验结果。
然而,在实验过程中也存在一些问题,如注塑产品的强度和耐用性等方面需要进一步改进和优化。
试模实习报告

一、实习单位及时间实习单位:XX科技有限公司实习时间:2023年X月X日至2023年X月X日二、实习目的本次试模实习旨在让我深入了解模具设计、制造及调试的全过程,提高我在模具设计、制造及调试方面的实践能力,为将来从事相关工作打下坚实基础。
三、实习内容1. 模具设计在实习期间,我参与了XX项目模具的设计工作。
首先,我学习了模具设计的基本原理和流程,了解了模具设计所需的软件和工具。
在导师的指导下,我独立完成了模具结构设计,包括型腔、冷却系统、导向系统等部分。
在设计过程中,我遵循了以下原则:(1)确保模具结构合理、强度高、耐磨性好;(2)便于模具的加工、装配和调试;(3)满足产品加工精度和表面质量要求。
2. 模具制造在模具设计完成后,我参与了模具制造过程。
首先,我将设计图纸转化为数控加工代码,交由加工中心进行加工。
在加工过程中,我负责检查加工精度,确保模具零件尺寸符合设计要求。
随后,我参与了模具的装配工作,按照装配图纸和工艺要求,将各零件组装成完整的模具。
3. 模具调试模具装配完成后,我参与了模具的调试工作。
首先,对模具进行试模,检查模具的加工精度和装配质量。
在调试过程中,我发现并解决了以下问题:(1)模具导向系统存在间隙,导致产品加工精度不高;(2)冷却系统设计不合理,导致模具温度过高,影响产品表面质量。
针对这些问题,我提出了相应的改进措施,并得到了导师的认可。
在导师的指导下,我对模具进行了改进,并成功完成了试模。
四、实习收获1. 提高了模具设计、制造及调试的实践能力;2. 了解了模具行业的发展趋势和市场需求;3. 学会了与团队成员沟通协作,提高了团队协作能力;4. 深入了解了模具设计、制造及调试过程中的关键技术,为今后从事相关工作奠定了基础。
五、实习体会通过本次试模实习,我深刻认识到模具设计、制造及调试的重要性。
在今后的工作中,我将继续努力学习,提高自己的专业技能,为我国模具行业的发展贡献自己的力量。
五金模具试模报告
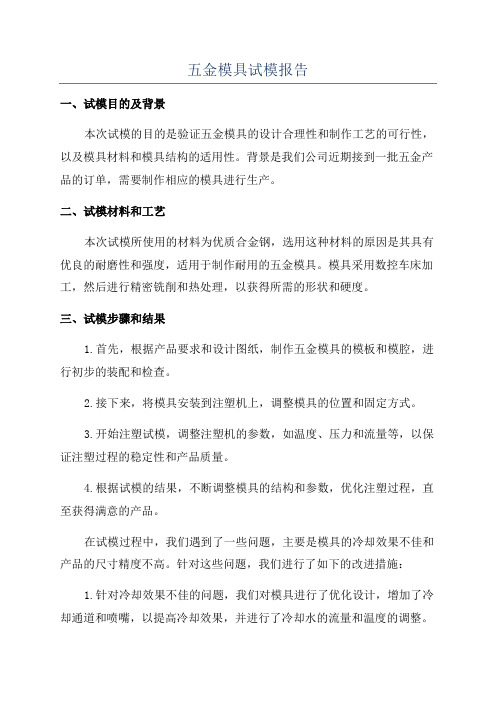
五金模具试模报告一、试模目的及背景本次试模的目的是验证五金模具的设计合理性和制作工艺的可行性,以及模具材料和模具结构的适用性。
背景是我们公司近期接到一批五金产品的订单,需要制作相应的模具进行生产。
二、试模材料和工艺本次试模所使用的材料为优质合金钢,选用这种材料的原因是其具有优良的耐磨性和强度,适用于制作耐用的五金模具。
模具采用数控车床加工,然后进行精密铣削和热处理,以获得所需的形状和硬度。
三、试模步骤和结果1.首先,根据产品要求和设计图纸,制作五金模具的模板和模腔,进行初步的装配和检查。
2.接下来,将模具安装到注塑机上,调整模具的位置和固定方式。
3.开始注塑试模,调整注塑机的参数,如温度、压力和流量等,以保证注塑过程的稳定性和产品质量。
4.根据试模的结果,不断调整模具的结构和参数,优化注塑过程,直至获得满意的产品。
在试模过程中,我们遇到了一些问题,主要是模具的冷却效果不佳和产品的尺寸精度不高。
针对这些问题,我们进行了如下的改进措施:1.针对冷却效果不佳的问题,我们对模具进行了优化设计,增加了冷却通道和喷嘴,以提高冷却效果,并进行了冷却水的流量和温度的调整。
2.针对产品尺寸精度不高的问题,我们对模具的结构进行了再设计,优化了尺寸控制和成型方式,同时对注塑机的参数进行了调整和优化。
经过多次试模和改进,我们最终获得了满意的试模结果。
产品尺寸精度达到了设计要求,并且注塑过程稳定,产品质量良好。
同时,模具的使用寿命也得到了有效延长。
四、试模总结和建议通过本次试模,我们对五金模具的设计和制作工艺有了更深入的了解,并验证了其可行性。
同时,也发现了一些存在的问题,并通过改进措施进行了解决。
综上所述,我们建议在今后的五金模具制作中,需要更加注重模具的冷却效果和产品尺寸精度控制,以提高产品质量和生产效率。
另外,还需要进一步研究材料选择、加工工艺和模具结构等方面的优化,以满足不同产品的需求。
以上就是本次五金模具试模报告的内容。
冲压试模报告

冲压试模报告
报告名称:冲压试模报告
报告编号:XXXXX
报告日期:XXXX年XX月XX日
目的:
本次冲压试模报告的主要目的是对XXX产品进行冲压性能试验并得出结论,为下一步开发、生产和销售提供参考。
试验方法:
试验设备:XXX冲床
试验模具:XXX模具
材料:XXX材料
试验过程:
1.按照试验要求,准备好材料和模具。
2.将材料放入模具,放置在冲床上。
3.设置好冲击力、冲程等参数,进行试验。
4.重复以上步骤,记录各个试验数据。
试验结果:
通过冲压试模试验得出以下结论:
1.材料的拉伸性能良好,成型效果优秀。
2.模具的使用寿命长,可以进行批量生产。
3.在不同的参数设置下,试验结果有所差异,在实际生产中需要根据具体情况进行调整。
建议:
1.根据试验结果,推荐确保材料的质量,以保证产品的成型效果。
2.需要对模具进行维护保养,延长其使用寿命。
3.在实际生产中需要进行参数调整,以保证产品质量和生产效率。
结论:
本次冲压试模试验结果表明,所使用的材料和模具均可用于批量生产,但需要根据实际情况进行参数调整,提高生产效率和产品质量。
附:本次试验结果详细数据表格。
试验编号材料厚度(mm) 冲剪孔直径(mm) 冲床冲程(mm) 力矩(kN.m) 成型结果
1 2 20 40 5 良好
2 2.5 25 45 7 优秀
3 3 30 50 10 良好
4 3.
5 35 55 13 一般
5 4 40 60 1
6 良好
以上数据仅供参考,具体情况还需要根据实际生产情况进行调整。
100模具试模报告

模具试模报告
模具厂商 订单号 需求 完成时间 冲压 模具规格 试制数量 拉深 其它 加工物料 作业类别 计划 完成时间 PMC部: 工序 项目 外观 冲压 尺寸 试装 加工工时 签署: 技术要求 日期: 判定 技术要求 检验结果 产品/名称 □新模具 冲压 拉深 □修(改)模 其它
技术部: 判定
备注
工序
项目 外观 尺寸 试装 加工工时
检验结果
备注
拉深
工序 其它
项目
签署: 技术要求
检验结果
日期: 判定
备注
签署: 试制结果: 是否移交: □合格 □移交 □不合格 □不移交
日期: (此项限新模具试制时填写)
试制不合格原因:
签Hale Waihona Puke : 处理方案: 签署: 备注:日期:
日期:
技术部
PMC部
生产部(模具仓)
品管部
试模总结报告模板
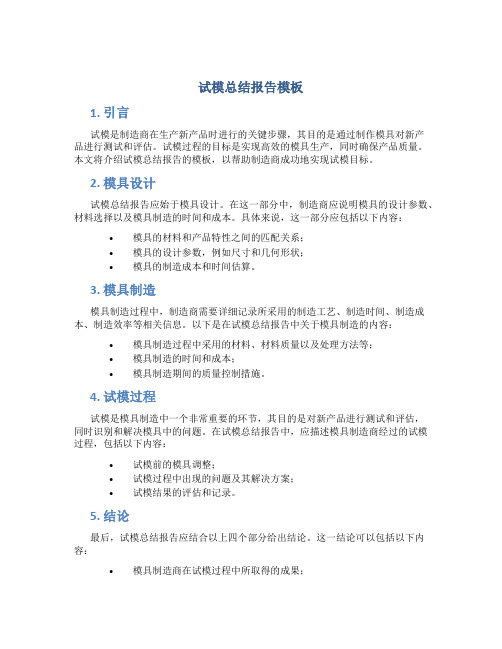
试模总结报告模板1. 引言试模是制造商在生产新产品时进行的关键步骤,其目的是通过制作模具对新产品进行测试和评估。
试模过程的目标是实现高效的模具生产,同时确保产品质量。
本文将介绍试模总结报告的模板,以帮助制造商成功地实现试模目标。
2. 模具设计试模总结报告应始于模具设计。
在这一部分中,制造商应说明模具的设计参数、材料选择以及模具制造的时间和成本。
具体来说,这一部分应包括以下内容:•模具的材料和产品特性之间的匹配关系;•模具的设计参数,例如尺寸和几何形状;•模具的制造成本和时间估算。
3. 模具制造模具制造过程中,制造商需要详细记录所采用的制造工艺、制造时间、制造成本、制造效率等相关信息。
以下是在试模总结报告中关于模具制造的内容:•模具制造过程中采用的材料、材料质量以及处理方法等;•模具制造的时间和成本;•模具制造期间的质量控制措施。
4. 试模过程试模是模具制造中一个非常重要的环节,其目的是对新产品进行测试和评估,同时识别和解决模具中的问题。
在试模总结报告中,应描述模具制造商经过的试模过程,包括以下内容:•试模前的模具调整;•试模过程中出现的问题及其解决方案;•试模结果的评估和记录。
5. 结论最后,试模总结报告应结合以上四个部分给出结论。
这一结论可以包括以下内容:•模具制造商在试模过程中所取得的成果;•发现的性能和生产问题;•解决问题和改进的方法建议。
6. 总结本文介绍了试模总结报告的模板,该模板包括模具设计、模具制造、试模过程和结论。
制造商可以根据该模板撰写试模总结报告,以便记录和评估新产品的性能和可靠性,并加以改进。
模具验收试模报告

模具验收试模报告一、引言二、试模背景1. 模具名称:xxx模具2. 试模时间:xxxx年xx月xx日3. 模具制造商:xxxxxx公司4. 模具设计师:xxxxx5. 模具加工厂家:xxxx公司三、试模目的通过对该模具的验收试模,评估其加工质量,确认其能否达到规定的技术要求,并为后续的模具使用和生产提供参考依据。
四、试模内容及评价1.模具结构设计评价该模具采用xxx结构设计,结构合理、布局合理,各零件之间配合紧密,方便拆装和护理。
模架刚度符合设计要求,对模具寿命和加工精度有良好的保障。
2.模具材料选用评价该模具的主要组成部分采用了xxx材料,具有良好的刚度、耐磨性和耐腐蚀性能,能够满足模具长时间使用的要求。
各部件加工后均经过热处理,材料硬度符合设计要求。
3.模具加工工艺评价模具零件加工精度高,零件尺寸符合设计要求。
加工表面光洁度高,无明显划痕和瑕疵。
模具各零部件装配紧密,无明显间隙和异响,能够正常使用。
4.试模过程评价试模过程中,模具操作简单,换模方便,模具使用寿命长。
试模过程中模具稳定性好,模具零件运动协调,模具动作精准可靠,模具生产效率高。
5.试模结果评价成功试模,产品尺寸精确,表面光洁平整,符合产品要求。
模具生产过程中无卡模、漏料等问题,模具的加工质量能够满足产品的使用要求。
六、模具验收结论该模具经过试模检验,各项指标符合设计要求,加工质量良好,能够满足产品生产的需要。
建议将该模具投入正式生产,并在使用过程中进行定期保养和维护,以延长模具寿命。
七、参考资料1.《模具设计和加工工艺》2.《模具质量验收标准》以上是对模具验收试模的报告,通过对模具结构设计、材料选用、加工工艺、试模过程和试模结果的评价,确认该模具的加工质量符合要求,并给出相应的使用建议。
模具验收试模的过程有助于提升模具加工质量和产品生产效率,为模具制造商和用户提供重要的参考依据。
6.试模报告模板
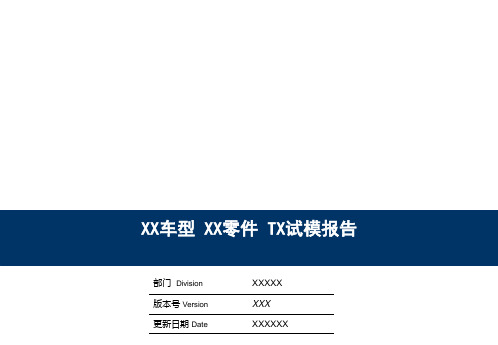
300000.00
0.58%
2
试模报告:XX车型 XX零件 TX试模
三 试模结论
模具本身问题:
• 浇注系统: 1.模具重点针对主框架地图袋分模线区域的脱模拉伤问题进行了优化,调整后零件状态较好;
• 冷却系统: 1.因为主框架本轮试模后需要腐蚀花纹,所以在试模过程中着重对与A面相关的问题进行了优化。除左后低配门板 地图袋区域、右后高配门灯区域断差线KW16需要研配后重新试模外,其他A面问题均已解决;
300000.00
0.58%
5
M120464
左后门板开 关盖板
8V4 959 527
深圳华益胜 佛山华翼
1
ABS 3616 Stlon
900T/900T
300000.00
0.58%
6
M120465
右后门板开 关盖板
8V4 959 528
深圳华益胜 佛山华翼
1
ABS 3616 Stlon
900T/900T
三 试模结论
以往问题关闭情况:
本次为T5次试模,模具重点针对主框架地图袋分模线区域的脱模拉伤问题进行了优化,调整后零件状态较好;
问题关闭情况
问题关闭率
T1问题关闭率 T2问题关闭率 T3问题关闭率 T4问题关闭率
70.00% 88.33% 98.39% 100.00%
5
试模报告:XX车型 XX零件 TX试模
XX车型 XX零件 TX试模报告
部门 Division 版本号 Version 更新日期 Date
XXXXX XXX XXXXXX
试模报告:XX车型 XX零件 TX试模
一 试模基本信息
模具供应商 昆山宏永盛
新模具试模报告

新模具试模报告摘要:本文是针对新模具的试模情况进行分析和总结的报告。
通过试模过程的详细记录和观察,对模具的设计和制造进行评估和优化,以提高模具的性能和效率。
本文将重点介绍试模背景、试模过程、试模结果和结论等内容。
一、试模背景模具是工业生产中常用的工具,用于制造各种产品,具有重要的作用。
随着技术的不断发展,新模具的设计和制造也不断创新和改进。
本次试模是为了验证并评估新模具的性能和可靠性,为后续的生产提供参考和依据。
二、试模过程1. 材料准备:选择合适的材料,并进行必要的加工和处理,以满足试模需求。
2. 模具装配:按照设计要求,将各个模具部件进行合理的组装调整,并进行必要的调试。
3. 试模准备:在试模前,对模具进行彻底的清洁和保养,确保模具表面的光洁度和平整度。
4. 试模操作:按照试模方案和工艺要求,对模具进行试模操作,包括开模、注塑、射出等过程。
5. 观察记录:在试模过程中,对模具的开模效果、产品的成型质量、模具的使用寿命等进行详细记录和观察。
三、试模结果通过试模过程的观察和记录,得到以下试模结果:1. 开模效果:新模具的开模效果较好,开合力均匀,无明显的卡滞和磨损。
2. 产品成型质量:新模具生产的产品尺寸精度高,表面光滑,没有明显的缺陷和瑕疵。
3. 模具寿命评估:经过一段时间的试模操作,模具表面仍保持较好的光洁度和平整度,表明模具的使用寿命较为稳定。
四、结论根据试模结果的评估和分析,可以得出以下结论:1. 新模具具有良好的开模效果,能够满足生产需求,并且平均使用寿命较长。
2. 新模具生产的产品成型质量较高,满足产品质量要求,有利于提高产品的竞争力和市场份额。
3. 在模具的制造和调试过程中,发现了一些细节问题和不足之处,需要进行优化和改进,以进一步提高模具的性能和效率。
综上所述,本次新模具的试模工作取得了较好的成果,对于提高产品质量和生产效率具有积极的促进作用。
在今后的工作中,我们将进一步优化和改进模具的设计和制造流程,不断提高模具的可靠性和稳定性,以满足不同客户和市场的需求。
- 1、下载文档前请自行甄别文档内容的完整性,平台不提供额外的编辑、内容补充、找答案等附加服务。
- 2、"仅部分预览"的文档,不可在线预览部分如存在完整性等问题,可反馈申请退款(可完整预览的文档不适用该条件!)。
- 3、如文档侵犯您的权益,请联系客服反馈,我们会尽快为您处理(人工客服工作时间:9:00-18:30)。
g 产品单重:1,
6,
TON 运转方式:□ 半自动 □ 六段 热流道℃ 设 定 值 实 际 值 开模设定 一段 二段 三段 四段 1 2
一段
顶出设定 五段 顶出 1 顶出 2 顶退 1 顶退 2 顶出模式 □前停 □多次 次 数: 延 时: 松退 计量背压: 冷却时间: 计量延时: 秒 秒 秒
射胶残量: mm S 保压切换条件: 时间+位置 □ 时间 □ 位置 □
文件编号 XXT1 试模报告
产品编号: 出模穴数: 胶料型号: 每模总重: 机 台 编 号 料管℃ 设定值 实际值 锁模设定 一段 二段 三段 低压 位置 压力 速度 射 出 一 >> 二 >> 三 >> 四 >> 五 >> 六 位置 压力 速度 时间 试模问题点: S S S S 保 压 一 >> 二 >> 三 >> 四 松退 一 计 量 二 三 高压
基本资料 试模参数 模具问题点 水路图
4
审批责任说明
栏位 制定 审核 批准 岗位 试模技术员 试模组长/试模工程师 / 备注
至终止
Rev: Rev:A.1
物料名称: 模具尺寸: 颜色编号:
模具编号: 定 位 圈: □ 有 水口配比: □ 无
试模日期:
年
月
日
射嘴要求:□ 标准 □ ℃ 烘料时间: 4, 5, 周期时间: 5 6 7
□ 加长
% 烘料温度:
2, 3, □ 全自动 3 4
H g
秒 8
g 水口重量:
号 : 锁 模 力: 二段 三段 四段 五段
前模温度: 后模温度:
行位温度: 水路图(请文字说明)
后 模
℃ □ 机水 ℃ □ 机水 ℃ □ 机水
□ 冻水 □ 冻水 □ 冻水
□ 水温机 □ 水温机 □ 水温机
□ 油温机 □ 油温机 □ 油温机
前 模
行 位 板 口
水
说明: 1.此参数必须在稳定情况下记录;
2.模具问题点一定要描述详细具体。
制定:
审核:
2
试模工程师 试模工程师/结构 工程师 模具项目工程师
3 4
3
各主要栏位 各主要栏位填写说明
栏位 填写说明 表格的前五行填写产品,模具,机械等基本内容。 包含料管温度,开锁模,顶出,射出,计量。 填写模具存在的所有问题点和要注意的事项,并且要清晰明了。 要简单的画清试模时运水的连接方法,必要时请文字说明。
批准:
文件编号 XXT1 试模报告使用说明
1 试模报告》 《XXT1 试模报告》的作用
Rev: Rev:A.1
《XXT1 试模报告》的作用是,作为每次试模结果及下次试模参考依据,明白模具存在的问题和注意事项。 2
序号 1
试模报告》 《XXT1 试模报告》的操作流程
操作流程描述 试模前准备:试模时条件稳定后记录,跟据接收的试模单,安 排合理的机台上模试模 上传系统:把《试模报告》扫描或拍照后上传 Windchill 发布 给相关人员[PLM] 组装开会:把《试模报告》中的问题提交到模具评审会议,参 会人员共同提出并确定解决方案 跟踪:跟据解决方案跟踪结果,修模后试模验证 责任岗位 试模技术员 备注