PVD喷涂及镀膜常见不良
电镀过程中镀层不良的描述、原因及对策

电镀过程中镀层不良的描述、原因及对策1、针孔。
针孔是由于镀件外表吸附着氢气,迟迟不开释。
使镀液无法亲润镀件外表,然后无法电析镀层。
跟着析氢点周围区域镀层厚度的添加,析氢点就构成了一个针孔。
特点是一个发亮的圆孔,有时还有一个向上的小尾巴"。
当镀液中短少湿润剂并且电流密度偏高时,容易构成针孔。
2、麻点。
麻点是由于受镀外表不洁净,有固体物质吸附,或许镀液中固体物质悬浮着,当在电场效果下到达工件外表后,吸附其上,而影响了电析,把这些固体物质嵌入在电镀层中,构成一个个小凸点(麻点)。
特点是上凸,没有发亮现象,没有固定形状。
总归是工件脏、镀液脏而构成。
3、气流条纹。
气流条纹是由于添加剂过量或阴极电流密度过高或络合剂过高而降低了阴极电流效率然后析氢量大。
假如当时镀液流动缓慢,阴极移动缓慢,氢气贴着工件外表上升的进程中影响了电析结晶的摆放,构成自下而上一条条气流条纹。
4、掩镀(露底)。
掩镀是由于是工件外表管脚部位的软性溢料没有除掉,无法在此处进行电析堆积镀层。
电镀后可见基材,故称露底(由于软溢料是半通明的或通明的树脂成份)。
5、镀层脆性。
在SMD电镀后切筋成形后,可见在管脚弯处有开裂现象。
当镍层与基体之间开裂,判定是镍层脆性。
当锡层与镍层之间开裂,判定是锡层脆性。
构成脆性的原因八成是添加剂,光亮剂过量,或许是镀液中无机、有机杂质太多构成。
6、气袋。
气袋的构成是由于工件的形状和积气条件而构成。
氢气积在"袋中"无法排到镀液液面。
氢气的存在阻挠了电析镀层。
使堆集氢气的部位无镀层。
在电镀时,只需留意工件的钩挂方向能够防止气袋现象。
如图示工件电镀时,当垂直于镀槽底钩挂时,不发生气袋。
当平行于槽底钩挂时,易发生气袋。
7、塑封黑体中心开"锡花”。
在黑体上有锡镀层,这是由于电子管在焊线时,金丝的向上抛物形太高,塑封时金丝显露在黑体外表,锡就镀在金丝上,像开了一朵花。
不是镀液问题。
8、"爬锡"。
电镀常见的问题及解决方案

电镀常见的问题及解决方案
电镀过程中可能出现的问题及其解决方案如下:
1.针孔或麻点:这是由于前处理不良、有金属杂质、硼酸含量太少、镀液温度太低等原因造成的。
可以使用润湿剂来减小影响,并严格控制镀液维护及流程。
2.结合力低:如果铜镀层未经活化去氧化层,铜和镍之间的附着力就差,会产生镀层剥落现象。
因此,在电镀前应对基材进行适当的预处理,如酸洗、活化等。
3.镀层脆、可焊性差:这通常是由于有机物或重金属物质污染造成的。
添加剂过多会使镀层中夹带的有机物和分解产物增多,此时可以用活性炭处理或电解等方法除去重金属杂质。
4.镀层发暗和色泽不均匀:有金属污染可能是造成这一问题的原因。
应尽量减少挂具所沾的铜溶液,并在发现污染时立即处理。
5.镀层烧伤:这可能是由于硼酸不足、金属盐的浓度低、工作温度太低、电流密度太高、PH值太高或搅拌不充分等原因造成的。
需要检查并调整相关工艺参数,确保其处于合适的范围。
6.沉积速率低:PH值低或电流密度低都可能导致沉积速率低。
应检查并调整镀液的PH值和电流密度,以优化沉积速率。
7.其他问题:如辅助阳极的铜条未与生产板长度一致或已发粗,不允许再使用。
全板及图形镀后板需在24小时内制作下工序。
图形镀上板戴细纱手套,下板戴棕胶手套,全板上板戴橡胶手套,下板戴干燥的粗纱手套。
在处理电镀问题时,需要综合考虑多个因素,包括镀液成分、设备状况、操作条件等。
如遇到难以解决的问题,建议寻求专业人士的帮助。
PVD喷涂及镀膜常见不良共26页文档

3.流痕/积油 Runs/Swells
定义:涂料在成膜过程中由于重力作用向下流动,使产品表面出现凸凹不平、上下漆膜厚薄不 均以及底部边缘增厚等不良。
产生的原因:---涂料喷出量过多,涂膜太厚; ---喷涂距离过近,被涂物表面过于光滑; ---喷枪与被涂物表面不垂直、素材的边缘或角过于尖锐 ; ---涂料粘度低,挥发速度慢。
6
PVD Defect Analysis and Action_v1.0
7.划伤 Scratch
定义:产品表面有磨损、凹槽或刻痕等。 产生的原因:---不合理的操作使产品碰到其它物体或产品间相互接触。
改善措施:---车间员工操作时必须严格执行各工序的SOP; ---设计合理的放置产品的装置的间距,确保产品在各工序不会接触。
定义:产品表面反光时有类似彩虹的效应。
产生的原因:---油漆体系使用不恰当; ---喷涂工艺参数不当使涂层中残留有内应力; ---金属膜引起的反射光发生干涉。
改善措施:---提高油漆黏度; ---采用干喷手法; ---采用恰当的油漆体系; ---面漆(着色层)膜厚薄涂至下限; ---底漆中添加消光剂,减弱真空镀膜金属的反射光; ---面漆中添加消光剂,减弱涂膜的入射光; ---金属膜上涂装两层涂料,利用涂膜成分不同引起的漫反射。
空气洁净度进行有效管控。
1
PVD Defect Analysis and Action_v1.0
2.桔皮 Orange Peel
严重
轻微
定义:涂层或面漆整体的起皱或斑驳。
产生的原因: ---涂料粘度过高; ---涂层膜厚太薄; ---喷枪气压过低或空气帽与喷嘴不匹配,涂料雾化不良; ---涂料使用前没有充分搅拌; ---喷涂漆膜过厚,内外干燥不一致; ---漆膜流平时间过短; ---少油(常见于面漆喷涂);
电镀中常见的不良原因分析(这些你都能解决了吗)

电镀中常见的不良原因分析(这些你都能解决了吗)电镀是制造业不可或缺的基础工艺。
电镀生产中发生不良在所难免,不良现象频发会影响生产进度和产品合格率,造成经济损失。
排除不良是电镀技术人员管理的重要内容。
今天我们平台针对最基础不良现象与原因分析分享给大家1.镀层结合力不好结合力不好一般有下列几种情况:(1) 底层结合力不好,该情况大都是前处理不良、基体金属上的油污或氧化膜未除尽造成的。
(2) 打底镀层成份控制不当,如碱铜中铜与游离氰比例不当,有六价铬污染等。
(3)前处理工序中的表面活性剂黏附在基体表面未清洗干净。
(4)腐蚀过度,有些工厂除锈酸的浓度高或不加缓蚀剂也会造成结合力不佳。
2.镀层脆性大造成脆性的最大原因是镀液中有机杂质或有机添加剂过多所致。
有的技术操作人员把添加剂看作是万能灵药,镀层一有问题就加添加剂。
添加剂比例失调或超过允许上限就会造成镀层脆性。
另外,pH 值不正常和重金属离子对镀液的污染,也会造成脆性。
镀层脆性与结合力不好有时很难区别。
一般可这样区别::结合力不好的镀层,能从基体金属上成片撕下,弯曲时镀层不会成粒屑飞出,薄型镀件无嘶嘶声;有脆性的镀层,剥落时镀层不能成片撕下,弯曲时镀层成粒屑飞出,薄型镀件有嘶嘶声。
3.针孔针孔在镀亮镍及光亮酸铜中最多见,通常见到的针孔有下列三种情况:(1)因析氢造成的针孔是锥形的。
(2)因油污和有机杂质造成的针孔是细密不规则的。
(3)基体金属的小凹点所造成的针孔无规则,如苍蝇脚趾,很难认定,须经试验和观看基体表面才能确定。
4.毛刺与针孔不同,可用湿纸揩擦故障处,如故障表面沾有纸屑的是毛刺,不沾纸屑的是针孔。
造成毛刺的主要原因是固体杂质。
(1)镀件本身带入镀液的固体杂质,如铁屑;先涂漆后电镀时,漆膜腐蚀下来的漆粒。
(2)外界混入或阳极溶解时带入的固体杂质。
建议阳极必须用阳极袋包扎。
5.发花发花主要是有机杂质多,镀液成分、光亮剂及表面活性剂(如十二烷基硫酸钠)等比例失调造成的。
PVD涂装异常 (1)

底漆常见问题分析及改善
• 2 附着不良:底材,涂膜,镀层之间附着力不好而导致涂 层脱落现象 • Ⅰ 底漆脱落 • 溶剂挥发不完全——提高IR温度和流平时间,减少漆膜厚 度 Ⅱ • 底漆固化不完全——增加UV 固化的能量 • 基材表面清洗不彻底——超声波处理或化学处理 • 涂料不适合基材——火焰,电晕处理或者更换配套涂料 • Ⅱ 镀层脱落 • 溶剂挥发不完全——提高IR温度和流平时间,减少漆膜厚 度 • 底漆固化不完全——降低传送带速度 • 底漆过度固化——调整固化条件 • 面漆不匹配——更换成相匹配的面漆
• •
底漆常见问题分析及改善
• • • • • • • • • • • • • • 5 白雾现象:镀膜层呈牛奶色 Ⅰ 底漆固化不完全——调整固化能量 Ⅱ 现场湿度过高——除湿干燥 Ⅲ 溶剂挥发过快导致水汽凝露——调低溶剂挥发速度 Ⅳ 镀膜层太薄显示底色——加厚金属镀层 Ⅴ 基材进行浸泡等前处理后吸水未经烤干就上底涂——将浸泡后的基材经IR烤干 Ⅵ 溶剂极性太强——用极性弱的溶剂稀释涂料或改用弱极性涂料,降低流平温度和时 Ⅴ 间 6 桔皮现象:镀膜层凹凸不平的现象 Ⅰ 底漆粘度太高——调整涂料的粘度:增加稀释剂或对涂料加温 Ⅱ IR段的温度和流平时间不足——增加IR段的温度和流平时间 Ⅲ 底材被污染——底材清洗或增加底漆润湿性 Ⅳ 喷涂气压太低或太高——调整喷枪的压力(3.5-4.5kg ∕cm2 )和距离(15-30cm) Ⅴ 喷涂油量太小或雾化不够——调整油量或雾化程度 Ⅵ 涂料本身固含太小(如机壳漆:含粒径较大的银粉)——大油量,大气量,大雾化 且前枪要大;调整涂料到适合喷涂的粘度(8.0-9.0s∕岩田2#杯)
底漆常见问题分析及改善
• • • • • • • • 3 针孔:溶剂或小分子物质挥发或底材与涂料之间的内应力差异产生 Ⅰ 溶剂挥发不完全——提高IR温度和流平时间,减少漆膜厚度 Ⅱ 底漆涂装后IR温度过高——IR设定的温度不超过80℃ Ⅲ 喷涂环境湿度太高——适当降低环境湿度 Ⅳ 涂料或基材中含易被紫外光照气化的杂质——基材先经紫外光处理 或改用合适涂料 4 彩虹现象:镀膜层产生相对移动 Ⅰ 底漆干燥不充分——加强底漆的固化 Ⅱ 涂层过厚,内部干燥不充分——适当调整底漆的厚度,使底漆固化 均匀 Ⅲ 溶剂使用不当或使用过量——调整溶剂的挥发速度 Ⅳ 底漆被面漆的溶剂所融化——降低面漆的烘烤温度或调整面漆溶剂 的极性
电镀不良之原因分析及防范措施
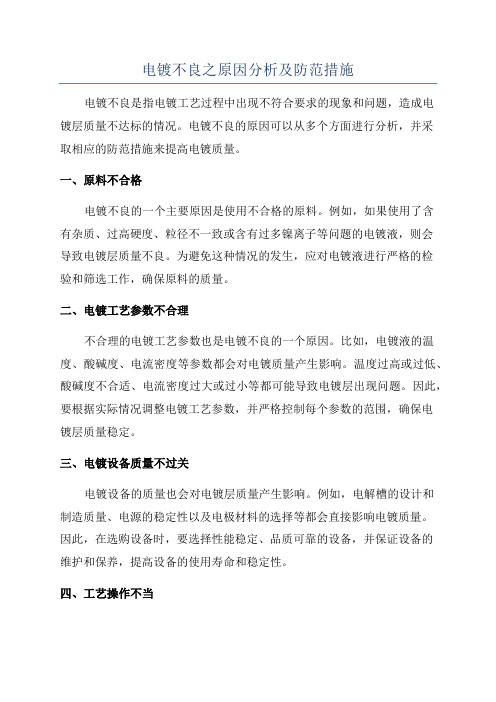
电镀不良之原因分析及防范措施电镀不良是指电镀工艺过程中出现不符合要求的现象和问题,造成电镀层质量不达标的情况。
电镀不良的原因可以从多个方面进行分析,并采取相应的防范措施来提高电镀质量。
一、原料不合格电镀不良的一个主要原因是使用不合格的原料。
例如,如果使用了含有杂质、过高硬度、粒径不一致或含有过多镍离子等问题的电镀液,则会导致电镀层质量不良。
为避免这种情况的发生,应对电镀液进行严格的检验和筛选工作,确保原料的质量。
二、电镀工艺参数不合理不合理的电镀工艺参数也是电镀不良的一个原因。
比如,电镀液的温度、酸碱度、电流密度等参数都会对电镀质量产生影响。
温度过高或过低、酸碱度不合适、电流密度过大或过小等都可能导致电镀层出现问题。
因此,要根据实际情况调整电镀工艺参数,并严格控制每个参数的范围,确保电镀层质量稳定。
三、电镀设备质量不过关电镀设备的质量也会对电镀层质量产生影响。
例如,电解槽的设计和制造质量、电源的稳定性以及电极材料的选择等都会直接影响电镀质量。
因此,在选购设备时,要选择性能稳定、品质可靠的设备,并保证设备的维护和保养,提高设备的使用寿命和稳定性。
四、工艺操作不当不正确的工艺操作也是电镀不良的一个常见原因。
例如,电镀工艺操作的速度太快或太慢,工件的浸泡时间控制不准确等都可能导致电镀层质量不良。
因此,操作人员在进行电镀工艺操作时要严格按照程序进行,并且进行必要的培训和技术指导,提高工艺操作的准确性和稳定性。
综上所述,电镀不良的原因可以从原料、工艺参数、设备质量和工艺操作等多个方面进行分析。
为了防范电镀不良的发生,可以采取以下措施:1.选用优质的原料,并进行严格检验和筛选;2.根据实际情况调整电镀工艺参数,并进行严格的控制;3.选购品质可靠的设备,并保证设备的维护和保养;4.进行工艺操作前进行必要的培训和技术指导,确保操作的准确性和稳定性;5.建立完善的质量控制体系,对电镀过程进行监控和检测,及时处理不良产品;6.加强与供应商的合作,建立长期稳定的合作关系,确保原料和设备质量的稳定性。
镀膜产品常见不良分析

镀膜产品常见不良分析、改善对策镀膜产品得不良,部分就是镀膜工序得本身造成得,部分就是前工程遗留得不良,镀膜最终得品质就是整个光学零件加工得(特别就是抛光、清洗)得综合反映,对策镀膜不良时必须综合考虑,才能真正找到不良产生得原因,对策改善才能取得成效。
一、膜强度膜强度就是镜片镀膜得一项重要指标,也就是镀膜工序最常见得不良项、膜强度得不良(膜弱)主要表现为:①擦拭或用专用胶带拉撕,产生成片脱落;②擦拭或用专用胶带拉撕,产生点状脱落;③水煮15分钟后用专用胶带拉撕产生点状或片状脱落;④用专用橡皮头、1Kg力摩擦40次,有道子产生;⑤膜层擦拭或未擦拭出现龟裂纹、网状细道子。
改善思路:基片与膜层得结合就是首要考虑得,其次就是膜表面硬度光滑度以及膜应力。
膜强度不良得产生原因及对策:①基片与膜层得结合、一般情况,在减反膜中,这就是膜弱得主要原因。
由于基片表面在光学冷加工及清洗过程中不可避免地会有一些有害杂质附着在表面上,而基片得表面由于光学冷加工得作用,总有一些破坏层,深入在破坏层得杂质(如水汽、油汽、清洗液、擦拭液、抛光粉等,其中水汽为主要),很难以用一般得方法去除干净,特别对于亲水性好,吸附力强得基片尤其如此。
当膜料分子堆积在这些杂质上时,就影响了膜层得附着,也就影响了膜强度。
此外,如果基片得亲水性差、吸附力差,对膜层得吸附也差,同样会影响膜强度、硝材化学稳定性差,基片在前加工过程中流转过程中,表面已经受到腐蚀,形成了腐蚀层或水解层(也许就是局部得、极薄得)。
膜层镀在腐蚀层或水解层上其吸附就差,膜牢固度不良、基片表面有脏污、油斑、灰点、口水点等,局部膜层附着不良,造成局部膜牢固度不良、改善对策:㈠加强去油去污处理,如果就是超声波清洗,应重点考虑去油功能,并保证去油溶液得有效性;如若就是手擦,可考虑先用碳酸钙粉擦拭后再清擦。
㈡加强镀前烘烤,条件许可,基片温度能达到300℃以上更好,恒温20分钟以上,尽可能使基片表面得水汽、油汽挥发。
喷涂不良现象原因分析及对策

喷涂不良现象原因分析及对策首先,喷涂不良现象的原因可能是涂料本身质量不良,如溶剂挥发不良、颜料过多或不匀等。
对此,我们应该选择质量可靠的涂料,并确保合适的稀释剂和颜料的比例,以及充分搅拌溶解,确保涂料材料质量合格。
其次,喷涂不良现象可能与喷涂设备有关,如喷枪精度不够、气压调节不当等。
因此,我们需要确保使用高质量的喷枪,并根据涂料要求调整合适的气压,确保涂料均匀喷涂。
此外,喷涂不良现象可能与喷涂环境有关,如温度、湿度等。
温度过高或者湿度过大会影响涂料的质量,导致喷涂不良。
因此,我们需要在适宜的温度和湿度环境下进行喷涂。
还有一种常见的喷涂不良现象是涂膜起泡。
这可能是由于涂料在喷涂前未充分搅拌或者出现了气泡。
因此,在喷涂前,我们需要彻底搅拌涂料以确保涂料中的气泡消除。
另外,对于喷涂不良现象,我们还需要配备专业的操作人员。
喷涂技术要求高,需要有一定的经验和技巧。
因此,我们应该提供专业的培训,确保操作人员能够熟练掌握喷涂技术,并定期检查和评估他们的工作质量。
最后,对于喷涂不良现象,我们需要建立和执行严格的质量管理体系。
这包括对原材料的质量检查、对喷涂设备的定期维护保养、对喷涂过程的监控和控制等。
只有确保每一个环节都进行严格的控制,才能预防和解决喷涂不良现象。
综上所述,喷涂不良现象的原因可能是多方面的,包括涂料材料、喷涂设备、喷涂环境以及人员技术等。
对于不同的问题,我们需要采取相应的对策,包括选择合适的涂料、优化喷涂设备、调节喷涂环境、培训并监督操作人员,并建立和执行严格的质量管理体系,以确保喷涂质量的稳定和提高。
镀膜产品常见不良分析

镀膜产品常见不良分析、改善对策镀膜产品的不良,部分是镀膜工序的本身造成的,部分是前工程遗留的不良,镀膜最终的品质是整个光学零件加工的(特别是抛光、清洗)的综合反映,对策镀膜不良时必须综合考虑,才能真正找到不良产生的原因,对策改善才能取得成效。
一、膜强度膜强度是镜片镀膜的一项重要指标,也是镀膜工序最常见的不良项。
膜强度的不良(膜弱)主要表现为:①擦拭或用专用胶带拉撕,产生成片脱落;②擦拭或用专用胶带拉撕,产生点状脱落;③水煮15分钟后用专用胶带拉撕产生点状或片状脱落;④用专用橡皮头、1Kg力摩擦40次,有道子产生;⑤膜层擦拭或未擦拭出现龟裂纹、网状细道子。
改善思路:基片与膜层的结合是首要考虑的,其次是膜表面硬度光滑度以及膜应力。
膜强度不良的产生原因及对策:①基片与膜层的结合。
一般情况,在减反膜中,这是膜弱的主要原因。
由于基片表面在光学冷加工及清洗过程中不可避免地会有一些有害杂质附着在表面上,而基片的表面由于光学冷加工的作用,总有一些破坏层,深入在破坏层的杂质(如水汽、油汽、清洗液、擦拭液、抛光粉等,其中水汽为主要),很难以用一般的方法去除干净,特别对于亲水性好,吸附力强的基片尤其如此。
当膜料分子堆积在这些杂质上时,就影响了膜层的附着,也就影响了膜强度。
此外,如果基片的亲水性差、吸附力差,对膜层的吸附也差,同样会影响膜强度。
硝材化学稳定性差,基片在前加工过程中流转过程中,表面已经受到腐蚀,形成了腐蚀层或水解层(也许是局部的、极薄的)。
膜层镀在腐蚀层或水解层上其吸附就差,膜牢固度不良。
基片表面有脏污、油斑、灰点、口水点等,局部膜层附着不良,造成局部膜牢固度不良。
改善对策:㈠加强去油去污处理,如果是超声波清洗,应重点考虑去油功能,并保证去油溶液的有效性;如若是手擦,可考虑先用碳酸钙粉擦拭后再清擦。
㈡加强镀前烘烤,条件许可,基片温度能达到300℃以上更好,恒温20分钟以上,尽可能使基片表面的水汽、油汽挥发。
电镀常见不良问题点分析及对策

②素材成型时使用了脱模剂或者素材原材料使用了再生料. 也会影响电镀层和塑胶层之间的附着性能.
素材成型时不要使用脱模剂,同时素材原材料一定不能含有再生料
③素材表面脱脂除油不完全也会影响电镀层和塑胶层之间 的附着性能.
适当的增加脱脂、除油时间
①相邻的2个电镀层电镀工艺间隔时间过长导致前工序电镀 层在空气中氧化从而影响了与下一工序电镀层的附着性能
5
电镀产品表背面颜色 主要是镀Cr产品表背面颜色容易产 ①产品在电镀Cr的工艺中电流强度不足或者电镀时间不足
发黄不良
生发黄不良
均会造成此不良发生
电镀现场管理加强镀Cr工艺的强度管理
6
电镀层表面有麻点不 良
电镀部品的外观面有麻点不良
①电镀全光产品在电镀酸铜工艺中由于电镀液中含有杂质 容易附着在产品表面而形成起点不良
电镀常见不良问题点分析及对策
NO.
不良问题点
1
电镀层胶纸测试 脱落不良
不良现象 ①电镀层和塑胶层之间剥离
产生不良的可能原因
对策
①素材表面局部应力集中过大导致电镀层和塑胶层之间发 生剥离,影响了附着性能
①改善部品的成型条件,如:降低注塑速度和注塑压力、提高模温和注塑温度 ②对素材采取高温(60~65OC)烘烤2~4H后再让其冷却到常温后再进行电镀处理 ③适当的增加粗化时间和粗化强度也可以改善该不良的发生
目前还没有非常有效的手段可以解决此问题,现行的改善方案为:电镀过程中后工序清 洗追加超声波清洗以提高清洗的强度,另外对电镀完成品高温烘烤降低电镀品内部发 生化学反应的可能性
Байду номын сангаас②相邻电镀层之间的剥离
②相邻的2个电镀层电镀工艺间的活化工序遗漏也会影响该 此3项不良原因均为现场管理不足造成,改善的对策是加强对生产现场的管理,避免出
PVD喷涂及镀膜常见不良26页PPT

定义:产品表面反光时有类似彩虹的效应。
产生的原因:---油漆体系使用不恰当; ---喷涂工艺参数不当使涂层中残留有内应力; ---金属膜引起的反射光发生干涉。
改善措施:---提高油漆黏度; ---采用干喷手法; ---采用恰当的油漆体系; ---面漆(着色层)膜厚薄涂至下限; ---底漆中添加消光剂,减弱真空镀膜金属的反射光; ---面漆中添加消光剂,减弱涂膜的入射光; ---金属膜上涂装两层涂料,利用涂膜成分不同引起的漫反射。
17 PVD Defect Analysis and Action_v1.0
18. 抗划痕不过 Rod Test NG
定义:漆膜硬度不够高,达不到客户指定的标准。 产生的原因:---油漆体系不合适;
---面漆的膜厚过薄; ---固化剂加入量偏少,交联不够充分; ---光固化时间和光照强度不够,或光照距离过远。 改善措施:---更换油漆体系; ---调整面漆膜厚; ---增加涂料中固化剂的含量; ---控制光照时间、强度和灯距在工艺范围内。
12 PVD Defect Analysis and Action_v1.0
12.发白/发雾 Whitening/ Misting
定义:底漆没有完全固化,喷完中漆后产生云雾状白色漆膜现象。 产生的原因:---溶剂快速蒸发引起漆膜表层温度急剧降低至环境温度的露点以下,从而导致湿
气凝结成小水珠混入涂料中产生泛白的现象; ---喷涂作业环境湿度过高,湿气混入漆膜造成; ---压缩空气中有水混入涂料而造成; ---涂料自身带有水分或底材表面未充分干燥。 改善措施: ---选择适当溶剂和稀释剂,控制其挥发速度,防止漆膜表面温度过低导致聚合物析出; ---降低环境湿度或给涂料添加防白水; ---加强油水分离器分离空气中的水分; ---严格控制涂料检验,底材喷涂前进行烘烤,确保其表面充分干燥。
PVD喷涂及镀膜常见不良幻灯片资料

5
PVD Defect Analysis and Action_v1.0
5.咬底/烧焦 Gnawing/Burning Marks
定义:底漆表面喷面漆时出现发黑、发皱、溶胀、起泡甚至脱落的现象。
产生的原因:---面漆溶解力太强,底漆耐溶剂性差; ---面漆喷涂太厚干燥慢,增强对底漆的腐蚀强度; ---底漆没有充分干透; ---面漆烘烤温度过高,产生酸性气体增强对底漆的腐蚀强度。
---素材表面不平整导致橘皮。
改善措施:---降低粘度或添加适量硅油;
---提高喷涂压力(充分雾化);
---更换合适的空气帽或喷嘴;
---严格按照工艺参数控制涂层厚度;
---加强喷涂前的搅拌;
---延长流平时间;
---调枪;
---注塑模具抛光。
3
PVD Defect Analysis and Action_v1.0
发生溶胀,溶剂挥发后表层体积收缩,产生应力;当塑料加工残余内应力与 外应力协同作用导致裂纹。 改善措施:---选择适当的涂料溶剂和稀释剂—溶剂的溶解力和挥发速度相互匹配; ---选择适当的涂料干燥方法和升温程序,减少干燥过程中产生的内应力; ---涂装前对塑料制品进行退火处理,消除塑料加工的残余应力。
7
PVD Defect Analysis and Action_v1.0
7.划伤 Scratch
定义:产品表面有磨损、凹槽或刻痕等。 产生的原因:---不合理的操作使产品碰到其它物体或产品间相互接触。
改善措施:---车间员工操作时必须严格执行各工序的SOP; ---设计合理的放置产品的装置的间距,确保产品在各工序不会接触。
---涂装前对塑料制品进行退火处理,消除塑料加工中产生的残余应力。 ---在上线之前确保素材表面清洁,无尘点、毛丝等杂质颗粒。
PVD喷涂及镀膜常见不良
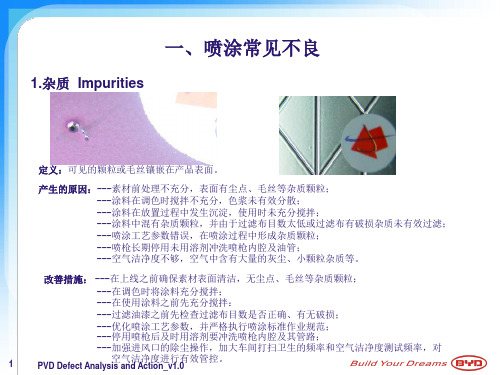
4
PVD Defect Analysis and Action_v1.0
5.咬底/烧焦 Gnawing/Burning Marks
定义:底漆表面喷面漆时出现发黑、发皱、溶胀、起泡甚至脱落的现象。 产生的原因:---面漆溶解力太强,底漆耐溶剂性差; ---面漆喷涂太厚干燥慢,增强对底漆的腐蚀强度; ---底漆没有充分干透; ---面漆烘烤温度过高,产生酸性气体增强对底漆的腐蚀强度。
改善措施:---减少涂料喷出量,严格控制膜厚; ---调整喷涂时产品与喷枪的距离,打磨被涂物表面使其变粗糙; ---调整喷枪与被涂物的垂直程度,改善素材边缘结构(将直角改为圆弧过渡); ---调整涂料粘度和挥发速度。
3
PVD Defect Analysis and Action_v1.0
4.彩虹纹 Rainbow
溶剂快速蒸发引起漆膜表层温度急剧降低至环境温度的露点以下从而导致湿气凝结成小水珠混入涂料中产生泛白的现象
一、喷涂常见不良
1.杂质 Impurities
定义:可见的颗粒或毛丝镶嵌在产品表面。 产生的原因:---素材前处理不充分,表面有尘点、毛丝等杂质颗粒; ---涂料在调色时搅拌不充分,色浆未有效分散; ---涂料在放置过程中发生沉淀,使用时未充分搅拌; ---涂料中混有杂质颗粒,并由于过滤布目数太低或过滤布有破损杂质未有效过滤; ---喷涂工艺参数错误,在喷涂过程中形成杂质颗粒; ---喷枪长期停用未用溶剂冲洗喷枪内腔及油管; ---空气洁净度不够,空气中含有大量的灰尘、小颗粒杂质等。 改善措施: ---在上线之前确保素材表面清洁,无尘点、毛丝等杂质颗粒; ---在调色时将涂料充分搅拌; ---在使用涂料之前先充分搅拌: ---过滤油漆之前先检查过滤布目数是否正确、有无破损; ---优化喷涂工艺参数,并严格执行喷涂标准作业规范; ---停用喷枪后及时用溶剂要冲洗喷枪内腔及其管路; ---加强进风口的除尘操作,加大车间打扫卫生的频率和空气洁净度测试频率,对 空气洁净度进行有效管控。
喷塑件表面常见缺陷及解决方法介绍

喷塑件表面常见缺陷及解决方法介绍一、工件表面塑层附着力不好。
1.前处理水洗不彻底造成工件上残留脱脂剂、铬化渣或者水洗槽被碱液污染而引起的附着力差。
解决方法是加强水洗,调整好脱脂工艺参数以及防止脱脂液进入磷化后的水洗槽。
2.磷化膜发黄、发花或者局部无磷化膜而引起的附着力差。
解决方法是调整好磷化槽液浓度和比例,提高磷化温度。
3.工件边角水分烘干不净而引起的附着力差。
解决方法是提高烘干温度4.固化温度不够而引起的涂层大面积附着力差。
解决方法是提高固化温度。
由于工件时在炉子里的固化温度和时间不够而造成的。
一般工件喷粉固化时间为20 分钟温度为180 度。
但是在实际生产中我们经常遇到的工件比较厚重,当板厚大于 3 毫米时时,应将工件在炉中温度适当调高到200度,工件的保温时间最少应在40 分钟。
对已经出现问题工件解决方法,再加热固化。
二、工件表面气泡、针孔、凹膜1.工件表面本身有气孔,固化时气孔内的气体膨胀冒出,在涂膜表面产生气泡或气孔。
2.工件原材料质量差。
3.工件表面有前处理的残留液,固化过程中残留液挥发或反应产生气泡。
4.粉末涂料受潮,含水量高,固化时水分溢出产生气泡。
5.喷涂时,喷枪电压高,涂层被击穿,固化涂层存在针孔。
6.涂层过厚,造成静电排斥。
7.压缩空气中含有油或水。
解决方法是加强粉末的保管,防潮,烘干工件的表面水份。
对压缩空气进行除油,除水。
对已经出现气泡工件,在气泡不太多情况下,可用刀片将气泡削平,然后用丙酮将粉调和后修补方可。
三、涂层流挂涂层太厚,升温太快,固化温度太高,烘烤固化前涂层不均匀四、涂层桔皮粉末颗粒大小分布状况也影响着涂膜的表面外观。
颗粒越小,由于其热容较大颗粒的低,因此其熔化时间比大颗粒的短,聚结也较快,形成涂膜的表面外观较好。
而大的粉末颗粒熔化时间比小颗粒的长,形成的涂膜就可能会产生桔皮效应。
粉末静电施工方法(电晕放电或摩擦放电)也是导致桔皮形成的一个因素。
实际工作中常使用流动促进剂或流平剂来改善涂膜外观,以消除桔皮、缩孔、针孔等表面缺陷。
电镀件常见不良原因分析ea

电镀件常见不良原因分析
A.麻点、杂质、颗粒
原因:1.镀槽内杂质太多
对策:1.加强电解以及过滤,定期清缸
原因:1.部品外表有缝隙藏铬酸 2.钯水浓度偏低,沉钯不到位
对策:1.加强中和,消除铬酸 2.提高钯浓度,加强摇摆
3.根据漏镀位置,提高或降低解胶浓度
湿剂缺乏 2.有机杂质过多 3.硼酸含量和温度太低
对策:1.补加润湿剂 2.用双氧水活性炭处理 3.分析硼酸浓度,将镀液加温
原因:1.素材本身变形
对策:1.优化成型参数,改善变形
3.将温度调整到合理的范围
原因:1.主盐浓度太底
3.硼酸含量缺乏,PH高
对策:1.分析成分后补充
3.补充硼酸,调整PH值
对策:1.
H.颜色偏亮或偏哑
原因:
3.镀液中有悬浮微粒
4.铁离子在高PH下形成氢氧化物沉淀,附在镀层中
3.连续过滤
4.调整PH至
5.5参加QF除铁粉,防止铁工件掉入槽中
、水渍
原因:1.缸水未清洁干净 2.后处理过热水不完全和时间短
对策:1.换水或用活性炭吸附 2.部品要全部浸在热水缸中,时间延长至1分钟
3.从产品下挂到包装入箱,杜绝用手接触产品,戴手套或指套,个别产品要包白纸
结合力差
对策:1.调整除油缸温度和浓度 2.调整亲水缸温度和组份浓度,使其浸润充分和缸水浓度正常
3.调整硫酸浓度、时间和电流至合理的工艺要求。
常见的不良现象及解决方案

涂料不适用底漆 溶剂挥发不完全 固化不切底
更换相应的面漆 提高IR温度,延长流平时间,减少膜厚 增强UV能量
2.呈颗粒现象
原因: 涂料中颗粒 对策:用500目以上过滤或更换更好的涂料
镀膜后稍冷立即喷面漆 检查空气净化系统,达到标准要求 镀膜后放置时间 太久被污染 压缩空气和环境中灰尘
真空电镀常见外观不良及解决对策
Date: June 17th.2011 Editor: Jian Wu
----仅供参考!
底漆异常问题分析及改善
1.呈附着不良:(底材、漆膜、镀层之间的附着力不好而导致涂层脱落) 2.呈干燥不良现象(涂料固化不完全出现发白或发彩的现象) 3.呈针孔现象(化学物质挥发或底材与涂料之间的相应力差异产生) 4.呈彩虹现象(镀层膜产生相对移动) 5.呈缩针孔现象(漆膜表面出现火山口现象) 6.呈颗粒现象 7呈白雾现象 8.呈咬底现象(工件边缘或局部呈粗皮哑白现象) 9.呈桔皮现象
3.呈针孔现象(化学物质挥发或底材与涂料之间的相应力差异产生)
原因: 底涂后IR温度过高 基材表面不清洁 底漆溶剂挥发不完全 对策:IR温度设定不超过80度 彻底清洁基材表面脏污 提高IR温度,延长流平时间,减少膜厚
4.呈彩虹现象(镀层膜产生相对移动)
原因: 涂层过厚,内部干燥不完全 对策:调整底漆膜厚,使底涂固化彻底 底漆干燥不完全 底漆被面漆溶剂所溶解 底漆的流平不好 提高IR温度及UV能量 降低面漆IR温度或调整面漆的溶剂熔点性 改善底漆流平 对策:用超声波清洗或化学剂处理 清洁喷枪,空气管道 添加适量助剂或更换涂料 检查油水分离器,并清洁干净
2.呈干燥不良现象(涂料固化不完全出现发白或发彩的现象)
电镀不良的一些情况和解决方法解析

电镀不良的一些情况和解决方法发布日期:2013-09-04 来源:中国电镀网浏览次数:2097 关注:加关注核心提示:电镀不良对策镀层品质不良的发生多半为电镀条件,电镀设备或电镀药水的异常,及人为疏忽所致.通常在现场发生不良时比较容易找出塬电镀不良对策镀层品质不良的发生多半为电镀条件,电镀设备或电镀药水的异常,及人为疏忽所致.通常在现场发生不良时比较容易找出塬因克服,但电镀后经过一段时间才发生不良就比较棘手.然而日后与环境中的酸气,氧气,水分等接触,加速氧化腐蚀作用也是必须注意的.以下本章将对电镀不良的发生塬因及改善的对策加以探讨说明.1.表面粗糙:指不平整,不光亮的表面,通常成粗白状(1)可能发生的塬因: (2)改善对策:1.素材表面严重粗糙,镀层无法覆盖平整. 1.若为素材严重粗糙,立即停产并通知客户.2.金属传动轮表面粗糙,且压合过紧,以至于压伤. 2.若传动轮粗糙,可换备用品使用并检查压合紧度.3.电流密度稍微偏高,部分表面不亮粗糙(尚未烧焦) 3.计算电流密度是否操作过高,若是应降低电流4.浴温过低,一般镀镍才会发生) 4.待清晰度回升再开机,或降低电流,并立即检查温控系统.5.PH值过高或过低,一般镀镍或镀金(过低不会)皆会发生. 5.立即调整PH至标准范围.6.前处理药液腐蚀底材. 6.查核前处理药剂,稀释药剂或更换药剂2.沾附异物:指端子表面附着之污物.(1)可能发生的塬因: (2)改善对策:1.水洗不干净或水质不良(如有微菌). 1.清洗水槽并更换新水.2.占到收料系统之机械油污. 2.将有油污处做以遮蔽.3.素材带有类似胶状物,于前处理流程无法去除. 3.须先以溶剂浸泡处理.4.收料时落地沾到泥土污物. 4.避免落地,若已沾附泥土可用吹气清洁,浸透量很多时,建议重新清洗一次.5.锡铅结晶物沾附5.立即去除结晶物.6刷镀羊毛?纤维丝6.更换羊毛?并检查接触压力.7.纸带溶解纤维丝. 7.清槽.8.皮带脱落屑. 8.更换皮带.3.密着性不良:指镀层有剥落.起皮,起泡等现象.(1)可能发生的塬因: (2).改善对策:1.前处理不良,如剥镍. 1.加强前处理.2.阴极接触不良放电,如剥镍,镍剥金,镍剥锡铅. 2.检查阴极是否接触不良,适时调整.3.镀液受到严重污染. 3.更换药水4.产速太慢,底层再次氧化,如镍层在金槽氧化(或金还塬),剥锡铅. 4,电镀前须再次活化.5.水洗不干净. 5.更换新水,必要时清洗水槽.6.素材氧化严重,如氧化斑,热处理后氧化膜. 6.必须先做除锈及去氧化膜处理,一般使用化学抛光或电解抛光.7.停机化学置换反应造成. 7.必免停机或剪除不良品8,操作电压太高,阴极导电头及镀件发热,造成镀层氧化. 8.降低操作电压或检查导线接触状况9,底层电镀不良(如烧焦),造成下一层剥落. 9.改善底层电镀品质.10.严重.烧焦所形成剥落10.参考NO12处理对策.4.露铜:可清楚看见铜色或黄黑色于低电流处(凹槽处)(1)可能发生塬因: (2)改善对策:1.前处理不良,油脂,氧化物.异物尚未除去,镀层无法析出. 1.加强前处理或降低产速2.操作电流密度太低,导致低电流区,镀层无法析出. 2.重新计算电镀条件.3镍光泽剂过量,导致低电流区,镀层无法析出3.处理药水,去除过多光泽剂或更新.4.严重刮伤造成露铜. 4.检查电镀流程,(查参考NO5)5.未镀到. 5.调整电流位置.5刮伤:指水平线条状,一般在锡铅镀层比较容易发生.(1)可能发生的塬因: (2)改善对策:1.素材本身在冲压时,及造成刮伤. 1.停止生产,待与客户联系.2.被电镀设备中的金属制具刮伤,如阴极头,烤箱定位器,导轮等. 2.检查电镀流程,适时调整设备和制具.3.被电镀结晶物刮伤. 3.停止生产,立即去除结晶物.6.变形(刮歪):指端子形状已经偏离塬有尺寸或位置.(1)可能发生的塬因: (2)改善对策:1.素材本身在冲压时,或运输时,即造成变形. 1.停止生产,待与客户联系.2.被电镀设备,制具刮歪(如吹气.定位器,振荡器,槽口,回转轮) 2.检查电镀流程,适时调整设备和制具.3.盘子过小或卷绕不良,导致出入料时刮歪3.停止生产,适时调整盘子4.传动轮转歪, 4.修正传动轮或变更传动方式.7压伤:指不规则形状之凹洞可能发生的塬因:改善对策:1)本身在冲床加工时,已经压伤,镀层无法覆盖平整2)传动轮松动或故障不良,造成压合时伤到1)停止生産,待与客户联2)检查传动机构,或更换备品8白雾:指镀层表面卡一层云雾状,不光亮但平整可能发生的塬因:1)前处理不良2)镀液受污染3)锡铅层爱到酸腐蚀,如停机时受到锡铅液腐蚀4)锡铅药水温度过高5)锡铅电流密度过低6)光泽剂不足7)传致力轮脏污8)锡铅电久进,産生泡沫附着造成改善对策:1)加强前处理2)更换药水并提纯污染液3)避免停机,若无法避免时,剪除不良4)立即检查温控系统,并重新设定温度5)提高电流密度6)补足不泽剂传动轮7)清洁传动轮8)立即去除泡沫9针孔:指成群、细小圆洞状(似被钟扎状)可能发生的塬因:改善对策:1.操作的电流密度太1.降低电流密度2.电镀溶液表面张力过大,湿润剂不足。
- 1、下载文档前请自行甄别文档内容的完整性,平台不提供额外的编辑、内容补充、找答案等附加服务。
- 2、"仅部分预览"的文档,不可在线预览部分如存在完整性等问题,可反馈申请退款(可完整预览的文档不适用该条件!)。
- 3、如文档侵犯您的权益,请联系客服反馈,我们会尽快为您处理(人工客服工作时间:9:00-18:30)。
定义:产品表面反光时有类似彩虹的效应。 产生的原因:---油漆体系使用不恰当; ---喷涂工艺参数不当使涂层中残留有内应力; ---金属膜引起的反射光发生干涉。 改善措施:---提高油漆黏度; ---采用干喷手法; ---采用恰当的油漆体系; ---面漆(着色层)膜厚薄涂至下限; ---底漆中添加消光剂,减弱真空镀膜金属的反射光; ---面漆中添加消光剂,减弱涂膜的入射光; ---金属膜上涂装两层涂料,利用涂膜成分不同引起的漫反射。
改善措施:---在上线之前确保素材表面清洁,无尘点、毛丝等杂 质颗粒; ---优化喷涂工艺参数,严格按照喷涂SOP执行; ---修改治具。
11
PVD Defect Analysis and Action_v1.0
11.开裂 Cracking/Crazing
定义:漆膜表面产生微细裂纹。 产生的原因:---聚合物与溶剂接触后其表面能降低,溶剂分子渗入聚合物内部使聚合物表层 发生溶胀,溶剂挥发后表层体积收缩,产生应力;当塑料加工残余内应力与 外应力协同作用导致裂纹。 改善措施:---选择适当的涂料溶剂和稀释剂—溶剂的溶解力和挥发速度相互匹配; ---选择适当的涂料干燥方法和升温程序,减少干燥过程中产生的内应力; ---涂装前对塑料制品进行退火处理,消除塑料加工的残余应力。
8
PVD Defect Analysis and Action_v1.0
8.色差 Color or Color Tone Deviation
定义:产品整体或局部颜色差异。 产生的原因:---油漆使用过程中未搅拌,颜料沉淀; ---中漆调色时,工艺参数错误致使中漆膜厚不均或少油; ---镀膜工序出现的色差引起喷涂后产品颜色的差异; ---底材内的颜料被底漆或中漆的溶剂溶解并迁移到面漆中使产品发生颜色差异; ---原油与色浆匹配不当; ---涂层的膜厚不均匀。 改善措施:---确保涂料在使用过程长期搅拌; ---优化喷涂工艺参数,并严格执行喷涂标准作业规范; ---对镀膜工序出现的色差进行有效管控; ---面漆选用溶解力较差的溶剂,改善底的耐溶剂性或底漆完全固化后再涂面漆; ---选用恰当的原油与色浆体系; ---喷涂过程中严格控制涂层的厚度。
改善措施:---减少涂料喷出量,严格控制膜厚; ---调整喷涂时产品与喷枪的距离,打磨被涂物表面使其变粗糙; ---调整喷枪与被涂物的垂直程度,改善素材边缘结构(将直角改为圆弧过渡); ---调fect Analysis and Action_v1.0
4.彩虹纹 Rainbow
定义:漆膜硬度不够高,达不到客户指定的标准。 产生的原因:---油漆体系不合适; ---面漆的膜厚过薄; ---固化剂加入量偏少,交联不够充分; ---光固化时间和光照强度不够,或光照距离过远。
2
PVD Defect Analysis and Action_v1.0
2.桔皮 Orange Peel
轻微
严重
定义:涂层或面漆整体的起皱或斑驳。 产生的原因: ---涂料粘度过高; ---涂层膜厚太薄; ---喷枪气压过低或空气帽与喷嘴不匹配,涂料雾化不良; ---涂料使用前没有充分搅拌; ---喷涂漆膜过厚,内外干燥不一致; ---漆膜流平时间过短; ---少油(常见于面漆喷涂); ---素材表面不平整导致橘皮。 改善措施:---降低粘度或添加适量硅油; ---提高喷涂压力(充分雾化); ---更换合适的空气帽或喷嘴; ---严格按照工艺参数控制涂层厚度; ---加强喷涂前的搅拌; ---延长流平时间; ---调枪; ---注塑模具抛光。
PVD Defect Analysis and Action_v1.0
3
3.流痕/积油 Runs/Swells
定义:涂料在成膜过程中由于重力作用向下流动,使产品表面出现凸凹不平、上下漆膜厚薄不 均以及底部边缘增厚等不良。 产生的原因:---涂料喷出量过多,涂膜太厚; ---喷涂距离过近,被涂物表面过于光滑; ---喷枪与被涂物表面不垂直、素材的边缘或角过于尖锐 ; ---涂料粘度低,挥发速度慢。
14
PVD Defect Analysis and Action_v1.0
15.气泡 Blister/Bubble
定义:涂层表面、中间或下面可见的气泡或水泡(完整的或破裂的)。 产生的原因:---涂料应用参数有误差; ---底材表面粗糙多孔吸附空气,而喷涂时又湿润不良,烘烤固化时气体受热膨胀 产生气泡; ---烤炉温度过高使得油漆的稀释剂以气泡的形式残留在了油漆中形成气泡(或释 放形成针孔); ---空气湿度太大,PU涂料与湿气反应产生二氧化碳气体残留在油漆中; ---涂层过厚,内外干燥不均; ---被涂物表面沾附有油、水、灰尘等; ---底漆的溶剂没有很好的迅速挥发掉,残留的溶剂在产品恢复的过程中形成气泡。 改善措施:---优化喷涂工艺参数; ---确保素材表面平整无孔或在喷涂前对素材进行预热,并在喷涂时有效湿润; ---适当控制炉温; ---加强空气油水分离器的管理,有效分离空气中的水分; ---适当控制涂层的膜厚; ---在喷涂前对素材进行有效除尘和干燥; ---选择适当的油漆体系。
7 PVD Defect Analysis and Action_v1.0
7.划伤
Scratch
定义:产品表面有磨损、凹槽或刻痕等。 产生的原因:---不合理的操作使产品碰到其它物体或产品间相互接触。 改善措施:---车间员工操作时必须严格执行各工序的SOP; ---设计合理的放置产品的装置的间距,确保产品在各工序不会接触。
5
PVD Defect Analysis and Action_v1.0
5.咬底/烧焦 Gnawing/Burning Marks
定义:底漆表面喷面漆时出现发黑、发皱、溶胀、起泡甚至脱落的现象。 产生的原因:---面漆溶解力太强,底漆耐溶剂性差; ---面漆喷涂太厚干燥慢,增强对底漆的腐蚀强度; ---底漆没有充分干透; ---面漆烘烤温度过高,产生酸性气体增强对底漆的腐蚀强度。
16
PVD Defect Analysis and Action_v1.0
17.表面粗糙 Matting/Blooming
定义:在局部区域有可见的粗糙和粉粒状外观。
产生的原因:---素材不干净,上面有尘点、毛丝等杂质; ---涂料应用参数有误; ---治具不良; ---素材被化学腐蚀; ---喷枪长期停用未用溶剂冲洗喷枪内腔及油管。
10
PVD Defect Analysis and Action_v1.0
10.少漆/少油 Misses
定义:与标准规格相比有些区域喷油不够。 产生的原因:---素材前处理不充分,表面有尘点、毛丝等杂质颗 粒; ---喷涂参数有误或没有按照喷涂SOP执行; ---素材上有尖角或锐边; ---治具设计不合理。
9 PVD Defect Analysis and Action_v1.0
9.飞油 Overspray
定义:喷涂时油漆喷在不应该喷的地方。 产生的原因:---夹具设计错误; ---保护膜未贴好或破损; ---夹具松动; ---操作错误。 改善措施:---修改夹具; ---上挂之前检查夹具是否松动; ---上挂之前检查保护膜是否贴好、是否有破损,如果有及时更改; ---镀膜时严格执行镀膜SOP。
PVD常见缺陷原因分析 及改善对策
2007.11.20 2007.12.11 update
1
PVD Defect Analysis and Action_v1.0
一、喷涂常见不良
1.杂质 Impurities
定义:可见的颗粒或毛丝镶嵌在产品表面。 产生的原因:---素材前处理不充分,表面有尘点、毛丝等杂质颗粒; ---涂料在调色时搅拌不充分,色浆未有效分散; ---涂料在放置过程中发生沉淀,使用时未充分搅拌; ---涂料中混有杂质颗粒,并由于过滤布目数太低或过滤布有破损杂质未有效过滤; ---喷涂工艺参数错误,在喷涂过程中形成杂质颗粒; ---喷枪长期停用未用溶剂冲洗喷枪内腔及油管; ---空气洁净度不够,空气中含有大量的灰尘、小颗粒杂质等。 改善措施: ---在上线之前确保素材表面清洁,无尘点、毛丝等杂质颗粒; ---在调色时将涂料充分搅拌; ---在使用涂料之前先充分搅拌: ---过滤油漆之前先检查过滤布目数是否正确、有无破损; ---优化喷涂工艺参数,并严格执行喷涂标准作业规范; ---停用喷枪后及时用溶剂要冲洗喷枪内腔及其管路; ---加强进风口的除尘操作,加大车间打扫卫生的频率和空气洁净度测试频率,对 空气洁净度进行有效管控。
14.油点/肿块 Dip/Dump
定义:产品表面上的油漆整体的变形。
产生的原因:---素材表面有机械应力(在喷涂前不可见); ---素材表面有污染物。 改善措施:---选择适当的涂料干燥方法和升温程序,减少干燥过程中产生应力; ---涂装前对塑料制品进行退火处理,消除塑料加工中产生的残余应力。 ---在上线之前确保素材表面清洁,无尘点、毛丝等杂质颗粒。
改善措施: ---选择适当溶剂和稀释剂,控制其挥发速度,防止漆膜表面温度过低导致聚合物析出; ---降低环境湿度或给涂料添加防白水; ---加强油水分离器分离空气中的水分; ---严格控制涂料检验,底材喷涂前进行烘烤,确保其表面充分干燥。
13 PVD Defect Analysis and Action_v1.0
改善措施:---调整底漆、面漆的溶解度; ---规范喷涂作业; ---延长底漆干燥时间; ---降低烘烤温度。
6
PVD Defect Analysis and Action_v1.0
6.针孔 Pin Holes
定义:在喷底漆或面漆和烘干时形成的小孔。 产生的原因:---底材表面粗糙多孔吸附空气,而喷涂时又湿润不良,烘烤固化时气体受热膨 胀产生气泡; ---烤炉温度过高使得油漆的稀释剂以气泡的形式释放形成小孔; ---空气湿度太高,PU涂料与湿气反应产生二氧化碳残留在油漆中; ---涂层过厚,内外干燥不均; ---被涂物表面沾附有油、水、灰尘等; ---底漆的溶剂没有很好的迅速挥发掉,残留的溶剂在产品恢复的过程中以气 泡的形式释放也会形成针孔。 改善措施:---确保素材表面平整无孔或在喷涂前对素材进行预热,并在喷涂时有效湿润; ---适当控制炉温; ---加强空气油水分离器的管理,有效分离空气中的水分; ---适当控制油漆黏度和膜厚; ---在喷涂前对素材进行有效除尘和干燥; ---选择适当的油漆体系。