模具系列3-模具镶件结构
注塑模具结构中的镶件设计

图 3 全 周 割 镶 件
F g3 Fufl t ns rs i l lwih i et i
图 5 活 动镶 件
Fi Ac ie i e g5 tv ns r t
( ) 当一套 模 具 需 要 生 产 多 种 型 号 的产 品 ,而 3
且 只是 局部结 构 有 所 不 同 时。可 使 用互 换 镶 件 ( 互
JA u ig C h n 。h n , HUAN e gh i I O R i n , HI e gz o g p C G N n u ( o ee f t a Si & E g er g aya nvr t o T cnl y aya 30 4 h a C l g e l c. l o Ma r i ni e n ,Ti nU i s y f eho g ,Ti n 0 2 ,C i ) n i u e i o u 0 n
具 的结构设计 中镶 件 问题 也是 一个 值 得 注意 的 问题 。 它不仅可 以节约钢料 、加工方便 ,而且 可 以增 加排气 有利于产 品的成型 ,缩短模具 制造周期 。
1 镶 件应 用 范 围 -1 2
镶件应用 范 围很广 ,不仅 在定模 、动模 中可 以应
用 ,在滑块 和斜顶 中也 有应用 。在实 际模具生 产 中主
法便 于后续 加工 ,而且可 以用来排气 ,便 于产品在较 深 的位置 不会 产 生 烧 焦现 象 ( 在产 品 的某 些 部位 产 生热 量过高 ,产 生像 被 烧 过 了一 样 的现 象 ) 或缺 胶 现象 ( 在产 品注 塑 冷 却 后 ,由于 不 能将 空 气及 时排 出 ,产 品在冷却后 收缩现象 ) 。
we e ald s rb d. r l e c ie
K y od :I et nm ud ne ;L cla o e w r s n c o o l;Isr oai t n j i t zi
冲压模具主流模具刀口镶件的设计标准和结构

冲压模具主流模具刀口镶件的设计标准和结
构
冲压模具是工业生产中常用的工具,在冲压过程中,模具刀口镶件的设计标准和结构是非常重要的因素。
以下是常见的设计标准和结构:
1.尺寸设计标准:刀口的长度、宽度、深度需要严格按照设计要求来进行控制,以确保压制出来的产品符合规格。
2.表面质量要求:因为刀口是直接接触产品的部分,所以它的表面质量要求很高。
在设计时需要确保刀口的表面光滑且平整,不能有毛刺和刮痕等瑕疵。
3.硬度要求:由于模具长时间使用时会受到挤压和磨损等影响,刀口镶件的硬度需要达到一定的标准。
通常使用淬火、高频淬火等工艺来提高其硬度。
4.结构设计:常用的刀口镶件结构有整体式、多块式和可调式等。
根据实际生产需求和成本预算,选择不同结构的刀口镶件。
5.材料选择:根据生产要求选择不同材质的刀口镶件,如钢、硬质合金等。
总之,刀口镶件的设计在冲压模具中是非常重要的环节。
合理的刀口设计可以提高生产效率,降低成本,保证产品品质。
模具镶拼式结构设计要点

模具镶拼式结构设计要点
模具镶拼式结构设计的要点包括以下几个方面:
1. 材料选择,在模具镶拼式结构设计中,首先要考虑选择合适
的材料。
模具的主体部分通常选用高强度、耐磨损的材料,如优质
合金钢或工程塑料。
而镶件部分则需要根据具体的使用要求选择不
同的材料,例如需要耐高温的部分可以选择耐热合金等材料。
2. 结构设计,模具镶拼式结构设计要考虑到镶件与主体的结合
方式,通常有机械连接和焊接两种方式。
在设计时需要保证镶件与
主体的结合牢固、紧密,以及能够承受所需的工作载荷。
此外,还
需要考虑镶件的安装和更换便捷性,以提高模具的维护效率。
3. 冷却系统设计,在模具镶拼式结构中,冷却系统设计尤为重要。
合理的冷却系统设计能够有效地控制模具温度,提高生产效率,延长模具使用寿命。
因此,要点包括冷却水路的布置、冷却水路与
镶件的连接方式等。
4. 热处理工艺,针对不同的模具材料,需要进行相应的热处理
工艺,以提高材料的硬度、耐磨性和耐腐蚀性。
对于镶件部分也需
要考虑其热处理工艺,以保证其性能与主体匹配。
5. 结构稳定性,在模具使用过程中,要考虑模具镶拼结构的稳
定性,避免因为镶件与主体之间的松动或变形导致模具失效。
因此,在设计时需要充分考虑结构的稳定性,并在加工制造过程中严格控
制质量。
总的来说,模具镶拼式结构设计要点涉及材料选择、结构设计、冷却系统设计、热处理工艺和结构稳定性等方面,需要综合考虑各
个因素,以确保模具的性能和使用寿命达到预期要求。
模具设计之镶件设计

三星TV设计规范镶件设计目的:为了保证镶件设计的统一性,合理的加工工艺,和优良的模具品质。
镶拼原则:1.胶位尽量出在镶件上;2.镶件上没有尖角;3.从外观胶位面上装配的镶件,其底部应有8~10mm长的5度斜度;4.镶件上的T型挂台尺寸共两种;(T型挂台长度取镶件总长的三分之二)5.镶件上没有加工死角;6.同一镶件槽内的多个镶件应设计成一个部件;7.镶接线不影响产品外观;8.镶件有定位,防转设计;9.镶件有设计字码槽(30x6x1).一.后壳(back)1.定模镶件天线孔镶件三星电视机后壳天线孔形状共有俩种形式,A型和B型图示尺寸为标准化后的镶件尺寸。
B.警告牌镶件三星电视机后壳警告牌需做成镶件,镶接线为产品警告牌轮廓线。
镶件厚度以镶件表面到底部保证最小25MM., 其底部应有8~10mm长的5度斜度,便于装配。
C. A V端子孔镶件此镶件形式如图所示2. 动模镶件A. 搬运装配卡筋镶件此镶件要求卡筋胶位全部出在镶件上,且镶件上应该设计冷却水。
B.底座装配卡筋镶件此卡筋胶位一半出在镶件上,镶件靠挂台定位,z向锁螺钉。
C.A V端子孔镶件此镶件形式如图所示D. 警告牌镶件三星电视机后壳警告牌需做成镶件,镶接线为产品警告牌轮廓线。
镶件厚度以镶件表面到底部保证最小25MM..二.前壳(front)1. 定模镶件A.喇叭镶件喇叭镶件镶接线距网齿边0。
4mm,镶件上纵向通一条冷却水,六个固定螺钉非平衡设计,防止左右装错;定模板上应设计该镶件固定螺钉的过孔,便于在不拆定模板的情况下,可以拆出该镶件。
B.铭牌孔镶针铭牌槽内的孔设计成镶针。
2. 动模镶件A.喇叭镶件喇叭镶件根据需要设计成多块,用销钉定位,螺钉锁紧,且每两镶件之间应设计排气槽,底部应设计5度斜度便于装配,.动模板上应设计该镶件固定螺钉的过孔,便于在不拆动模板的情况下,可以拆出该镶件。
如下图示:B.排钮紧固螺丝柱镶件排钮紧固螺丝柱往往对排钮装配影响很大,经常需要调节,故此处应单独设计成一个镶件。
模具基本结构及分类

模具基本结构及分类:一、基本结构,根据部分起作用不同分类:〈一〉浇注系统将塑料由注射机喷嘴引向型腔的通道称浇注系统,其由主流道,分流道,内浇口,冷料穴等结构组成,由零件的浇注套,拉料杆等组成.〈二〉成型零件是直接构成塑料件形状及尺寸的各种零件,由型芯成型塑件内部形状,型腔成型塑料外部形状,成型杆,镶块等构成.〈三〉结构零件构成零件结构的各种零件,在模具中起安装,导向,机构动作及调温等作用.导向零件:导柱,导套.装配零件:定位隙,定模底板,定模板,动模板,动模垫板,模脚冷却加热系统主流道浇注系统内浇口分流道冷料穴注射型芯模成型零件型腔成型杆镶块导柱导向零件导套结构零件装配固定零件定位隙,定模底板,定模板,动模板,动模垫板,模脚冷却加热系统根据其运动特点均可分为两大部分:定模部分:一部份留于模具机座的定模板上,动模部分:随注射机动模板运动的部分定模部分与动模部分闭合则可形成型腔与浇注系统二、模具的分类〈一〉按注射机类型分:立式注射机,卧式注射机,直角式注射机上用的模具〈二〉按注射模具的总体结构特征分:1、单分型面模分流道位于分型面上,需切除流道凝料.2、点浇口脱出模具三板式模具3、带横向轴芯的分型模具4、自动卸螺纹注射成型模具注塑模基本组成注塑模具由动模和定模两部分组成,动模安装在注射成型机的移动模板上,定模安装在注射成型机的固定模板上.在注射成型时动模与定模闭合构成浇注系统和型腔,开模时动模和定模分离以便取出塑料制品.模具的结构虽然由于塑料品种和性能、塑料制品的形状和结构以及注射机的类型等不同而可能千变万化,但是基本结构是一致的.模具主要由浇注系统、调温系统、成型零件和结构零件组成.其中浇注系统和成型零件是与塑料直接接触部分,并随塑料和制品而变化,是塑模中最复杂,变化最大,要求加工光洁度和精度最高的部分.浇注系统是指塑料从射嘴进入型腔前的流道部分,包括主流道、冷料穴、分流道和浇口等.成型零件是指构成制品形状的各种零件,包括动模、定模和型腔、型芯、成型杆以及排气口等.典型塑模结构如图示.一.浇注系统浇注系统又称流道系统,它是将塑料熔体由注射机喷嘴引向型腔的一组进料通道,通常由主流道、分流道、浇口和冷料穴组成.它直接关系到塑料制品的成型质量和生产效率.1.主流道它是模具中连接注射机射嘴至分流道或型腔的一段通道.主流道顶部呈凹形以便与喷嘴衔接.主流道进口直径应略大于喷嘴直径O.8mm以避免溢料,并防止两者因衔接不准而发生的堵截.进口直径根据制品大小而定,一般为4-8mm.主流道直径应向内扩大呈3°到5°的角度,以便流道赘物的脱模.2.冷料穴它是设在主流道末端的一个空穴,用以捕集射嘴端部两次注射之间所产生的冷料,从而防止分流道或浇口的堵塞.如果冷料一旦混入型腔,则所制制品中就容易产生内应力.冷料穴的直径约8一lOmm,深度为6mm.为了便于脱模,其底部常由脱模杆承担.脱模杆的顶部宜设计成曲折钩形或设下陷沟槽,以便脱模时能顺利拉出主流道赘物.3.分流道它是多槽模中连接主流道和各个型腔的通道.为使熔料以等速度充满各型腔,分流道在塑模上的排列应成对称和等距离分布.分流道截面的形状和尺寸对塑料熔体的流动、制品脱模和模具制造的难易都有影响.如果按相等料量的流动来说,则以圆形截面的流道阻力最小.但因圆柱形流道的比表面小,对分流道赘物的冷却不利,而且这种分流道必须开设在两半模上,既费工又易对准.因此,经常采用的是梯形或半圆形截面的分流道,且开设在带有脱模杆的一半模具上.流道表面必须抛光以减少流动阻力提供较快的充模速度.流道的尺寸决定于塑料品种,制品的尺寸和厚度.对大多数热塑性塑料来说,分流道截面宽度均不超过8m,特大的可达10一12m,特小的2-3m.在满足需要的前提下应尽量减小截面积,以免增加分流道赘物和延长冷却时间.4.浇口它是接通主流道或分流道与型腔的通道.通道的截面积可以与主流道或分流道相等,但通常都是缩小的.所以它是整个流道系统中截面积最小的部分.浇口的形状和尺寸对制品质量影响很大.浇口的作用是:A、控制料流速度:.B、在注射中可因存于这部分的熔料早凝而防止倒流:C、使通过的熔料受到较强的剪切而升高温度,从而降低表观粘度以提高流动性:D、便于制品与流道系统分离.浇口形状、尺寸和位置的设计取决于塑料的性质、制品的大小和结构.一般浇口的截面形状为矩形或圆形,截面积宜小而长度宜短,这不仅基于上述作用,还因为小浇口变大较容易,而大浇口缩小则很困难.浇口位置一般应选在制品最厚而又不影响外观的地方.浇口尺寸的设计应考虑到塑料熔体的性质.型腔它是模具中成型塑料制品的空间.用作构成型腔的组件统称为成型零件.各个成型零件常有专用名称.构成制品外形的成型零件称为凹模又称阴模,构成制品内部形状如孔、槽等的称为型芯或凸模又称阳模.设计成型零件时首先要根据塑料的性能、制品的几何形状、尺寸公差和使用要求来确定型腔的总体结构.其次是根据确定的结构选择分型面、浇口和排气孔的位置以及脱模方式.最后则按控制品尺寸进行各零件的设计及确定各零件之间的组合方式.塑料熔体进入型腔时具有很高的压力,故成型零件要进行合理地选材及强度和刚度的校核.为保证塑料制品表面的光洁美观和容易脱模,凡与塑料接触的表面,其粗糙度Ra>0.32um,而且要耐腐蚀.成型零件一般都通过热处理来提高硬度,并选用耐腐蚀的钢材制造.2.调温系统为了满足注射工艺对模具温度的要求,需要有调温系统对模具的温度进行调节.对于热塑性塑料用注塑模,主要是设计冷却系统使模具冷却.模具冷却的常用办法是在模具内开设冷却水通道,利用循环流动的冷却水带走模具的热量;模具的加热除可利用冷却水通道热水或蒸汽外,还可在模具内部和周围安装电加热元件.3.成型部件成型部件由型芯和凹模组成.型芯形成制品的内表面,凹模形成制品的外表面形状.合模后型芯和型腔便构成了模具的型腔.按工艺和制造要求,有时型芯和凹模由若干拼块组合而成,有时做成整体,仅在易损坏、难加工的部位采用镶件.排气口它是在模具中开设的一种槽形出气口,用以排出原有的及熔料带入的气体.熔料注入型腔时,原存于型腔内的空气以及由熔体带入的气体必须在料流的尽头通过排气口向模外排出,否则将会使制品带有气孔、接不良、充模不满,甚至积存空气因受压缩产生高温而将制品烧伤.一般情况下,排气孔既可设在型腔内熔料流动的尽头,也可设在塑模的分型面上.后者是在凹模一侧开设深0.03-0.2mm,宽1.5-6mm的浅槽.注射中,排气孔不会有很多熔料渗出,因为熔料会在该处冷却固化将通道堵死.排气口的开设位置切勿对着操作人员,以防熔料意外喷出伤人.此外,亦可利用顶出杆与顶出孔的配合间隙,顶块和脱模板与型芯的配合间隙等来排气.4.结构零件它是指构成模具结构的各种零件,包括:导向、脱模、抽芯以及分型的各种零件.如前后夹板、前后扣模板、承压板、承压柱、导向柱、脱模板、脱模杆及回程杆等.1.导向部件为了确保动模和定模在合模时能准确对中,在模具中必须设置导向部件.在注塑模中通常采用四组导柱与导套来组成导向不见,有时还需在动模和定模上分别设置互相吻合的内、外锥面来辅助定位.2.推出机构在开模过程中,需要有推出机构将塑料制品及其在流道内的凝料推出或拉出.推出固定板和推板用以夹持推杆.在推杆中一般还固定有复位杆,复位杆在动、定模合模时使推板复位.3.侧抽芯机构有些带有侧凹或侧孔地塑料制品,在被推出以前必须先进行侧向分型,抽出侧向型芯后方能顺利脱模,此时需要在模具中设置侧抽芯机构.4.标准模架为了减少繁重的模具设计和制造工作量,注塑模大多采用了标准模架.设计方面1壁厚小,应加厚制件以免过早固化.2嵌件位置不当,应以调整.。
常用模具拼镶方法
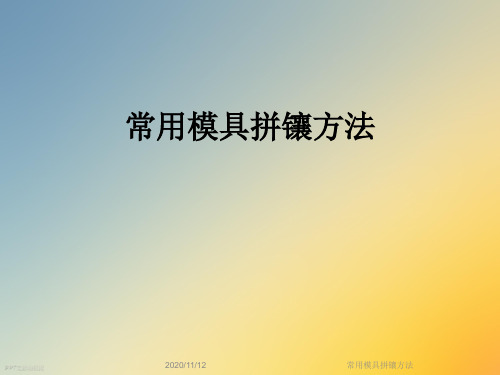
常用模具拼镶方法
设计思路的变更
§ 近几年来,通过日本模,工业模的设计和 制造,我们的设计思路和方向有了根本的 变化,其中最为典型的变化就是镶件的设 计和制作变等多了起来,所以我们在此大 概总结了一些镶拼镶
A、作用或优点:
▪ ①分散加工,缩短加工周 期。
PPT文档演模板
常用模具拼镶方法
2、通 镶
▪ A、作用或优点:
▪ ①利于加工,减少 EDM时间;利于抛光; 利于排气走料;方便 修改。
▪ ②利于控制尺寸精度。
▪ B、适应范围:
▪ 镶呵,镶骨,镶关尺 寸的柱、孔。
▪ C、固定方式:
▪ PPT文档演模板 底收螺丝,作管钉,
常用模具拼镶方法
通镶示意图(无EDM加工,抛光方便,排气好
PPT文档演模板
常用模具拼镶方法
窜镶示意图
PPT文档演模板
常用模具拼镶方法
7、侧 镶
▪ A、作用或优点: ▪ ①简化加工。 ▪ B、适应范围: ▪ 修改模
PPT文档演模板
常用模具拼镶方法
侧镶示意图
PPT文档演模板
常用模具拼镶方法
啤件内模侧面图
PPT文档演模板
常用模具拼镶方法
8、啤把镶(顺啤把反啤把)
PPT文档演模板
常用模具拼镶方法
搭底镶件方便加工(线割,不用EDM,
简化加工同时保证精度)
PPT文档演模板
常用模具拼镶方法
搭底镶件示意图(方便加工和排除真空
以利出模)
PPT文档演模板
常用模具拼镶方法
5、叠 镶
▪ A、作用或优点: ▪ ①利于加工,方便抛
光,可以处理倒扣加 工。例[2]: ▪ ②利于控制尺寸例[55]。 ▪ ③转移镶年痕的位置。 例:[5-3] ▪ B、适应范围: ▪ 倒扣位置
(02-06)模具镶件的技术规范

康佳精密模具公司技术文件技术文件康模技字(2003)第006号模具镶件的技术规范为了保证模具镶件在注塑过程中,保持牢固可靠,确保封胶,不露批锋,对镶件的镶入深度做以下规定。
1、镶件的镶入结构形式应该以保持镶件稳定牢固为原则。
2、在镶件镶入部分的底部应做出一段5mm的锥面(1°以下),对镶件起导入作用,防止损坏镶件槽的边缘,确保封胶。
3、1)细长类镶件(如孔芯类等)正镶:适合于浅孔(即孔深不大于孔径)的塑件。
镶件靠过盈配合H7/u6固定。
a、正镶镶件的镶嵌深度(配合部分)应15~20mm。
b、孔芯直径<3mm时,应加粗镶入部分的直径。
c、镶件应确保镶嵌到位,不可悬空。
特别注意:对于深孔类(孔深为孔径数倍的)镶件,考虑其稳定程度,镶入深度应为露出部分高度的1~1.5倍,背面用螺栓锁紧。
反镶:从模腔外向模腔内伸出的镶法,过渡配合H7/k6,H7/h6。
a、孔芯底部要做出肩台。
b、配合部分的长度为孔径的1~1.5倍。
2)平板(块)类镶件(如喇叭镶件等)a、基本采用正镶,背面用螺栓锁紧。
b、镶件的露出部分高度应小于镶入部分高度,以保证其稳定性。
c、镶件的镶入深度(配合部分高度)最小值为15mm,确保封胶。
d、镶件(如喇叭镶件)的镶入深度与镶件的最大尺寸有关:最大尺寸≤100mm,镶入深度≥20mm;最大尺寸>100mm,≤250mm,镶入深度≥25mm;最大尺寸>250mm,镶入深度≥35mm。
4、完全镶入的镶件,在结构允许的情况下,应采用T型槽结构(单边、双边)来增加强度,并用螺栓锁紧。
5、镶件装配的封胶面应确保紧密,不应存在可见间隙。
3159744.doc康佳精密模具公司技术文件技术文件康模技字(2003)第006号6、镶件的成型面应做出相应的脱模斜度(≥0.5°)。
7、须换款的镶件,如电视机后壳的端子镶件,应使用在注塑时便于换款的镶嵌方式。
批准:2003年1月1日。
模具镶件镶法课件

水平式镶法的缺点在于加工和更 换镶件比较困难,适用于大型模 具和高精度成型模具。
嵌入式镶法
嵌入式镶法是一种将镶件嵌入模具中 的镶法,其优点在于能够提高模具的 精度和使用寿命,同时减少模具的磨 损。
嵌入式镶法的缺点在于加工难度较大 ,需要高精度的加工设备和技术人员 。
03
模具镶件材料选择与 热处理
夹具选择
根据加工零件的特点,选择合适的夹具,确保工 件定位准确、固定牢固。
加工工艺流程与要点
01
02
03
04
流程概述
模具镶件加工主要包括模具设 计、备料、加工、装配等环节
。
备料
根据设计要求,准备合适的材 料,并进行必要的表面处理,
如除锈、粗加工等。
加工
在数控加工中心或铣床上进行 精确加工,包括钻孔、铣型等
根据模具材质和产品要求,选择合适的镶件材料 ,如耐磨性较好的硬质合金、碳化钨等,同时加 强设备的维护和保养。
案例三:利用镶件修复磨损严重的模具
01
总结词
利用镶件技术修复磨损严重的模具的情况。
02 03
详细描述
对于一些磨损较为严重的模具,可以利用镶件技术进行修复,如堆焊、 热处理等方法。这些方法能够有效地恢复模具的形状和尺寸,延长模具 的使用寿命。
解决方案
根据产品要求和复杂程度,设计合适的镶件结构和材质,同时加强生产过程中的质量控制 和维护保养。
THANKS
感谢观看
垂直式镶法是一种常用的模具镶件镶法,其特点是在模具垂直方向设置镶件,镶件 与型芯或型腔相配合,实现模具的加工和成型。
垂直式镶法的优点在于镶件容易更换、加工方便,适用于小型模具和成型小型零件 的模具。
垂直式镶法的缺点是镶件容易脱落,影响模具的精度和使用寿命。
模具镶件设计规范

镶件设计定义:镶件是镶嵌在内模钢料或是模板上的单独的用于成型胶位的模具配件称之为镶件。
一般除了镶针可以订购标准件外,其余均要按照模具的需要进行定做。
目的:在模具设计时,考虑到制件精度、排气冷却、加工工艺、模具强度、加工能力、节省材料、产品换款等因素,往往我们会设计为镶件结构。
应用场合:1.产品PL上有止口时,必须做镶件。
注意内模Core为整体镶件时,考虑强度及运水设计,尽量采用盲镶。
2.骨位深度超过3倍胶厚时,必须做镶件。
3.骨位根部厚度小于1.0mm时,必须做镶件。
4.与模腔内胶料流动方向垂直排列的骨位,必须做镶件。
5.产品结构为骨位阵列时,必须做镶件。
6.某处产品结构复杂,难以加工的也要设计为镶件结构。
7.产品上有6.0mm以下以及不规则碰穿孔时,必须做镶件。
8.产品上有文字及Logo或是版本号时,必须设计为镶件。
9.齿轮类产品前后模模腔都必须做镶件设计。
10.产品更改局部结构达到换款要求时,必须设计为镶件。
设计方式:1.止口位内模镶件设计形式如下图1.01图1.012.骨位深度超过胶位3-6倍胶厚时,采用如下图1.02方式设计镶件。
注意单边斜度做到浇口侧,以减小产品顶出时的收缩力。
图1.023.骨位深度超过6倍胶位厚度时,采用双边斜度。
如下图1.03所示。
斜度靠近线割边的一侧从高过骨位底部0.5-1mm的位置做一段直身位,以避免骨位底部封胶位因为加工精度原因出现披锋。
图1.034.井字形交叉的骨位,采用如图1.04的设计方式。
注意纵向骨位同胶料流动方向一致。
在镶件尺寸太小,不能做运水的情况下,可参考图1.04右图所示,大镶件套小镶件来设计。
图1.045.十字交叉的骨位,采用如下图所示方法6.不方便直接做镶拼结构(尺寸小于6mm或是边上会有薄钢)的地方或尺寸太小的十字骨位,可以采用托底镶。
如图1.06所示。
图1.067.对于日期章,Logo,等做盲镶的小镶件。
请注意必须在镶件底部做上取出工艺孔。
嵌入式铜件模具结构
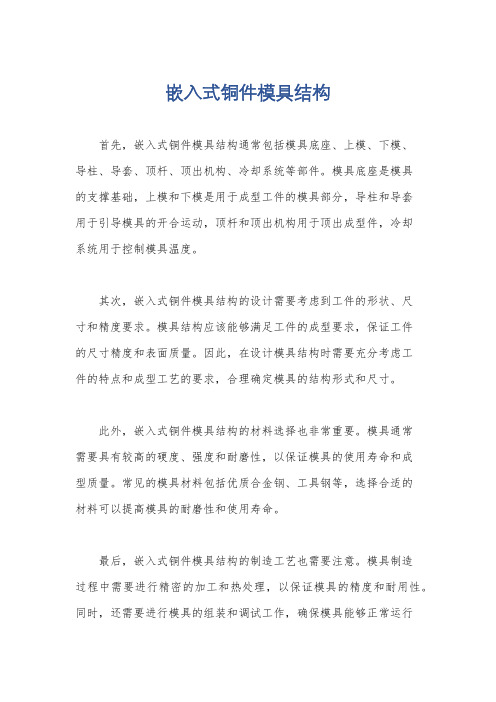
嵌入式铜件模具结构
首先,嵌入式铜件模具结构通常包括模具底座、上模、下模、
导柱、导套、顶杆、顶出机构、冷却系统等部件。
模具底座是模具
的支撑基础,上模和下模是用于成型工件的模具部分,导柱和导套
用于引导模具的开合运动,顶杆和顶出机构用于顶出成型件,冷却
系统用于控制模具温度。
其次,嵌入式铜件模具结构的设计需要考虑到工件的形状、尺
寸和精度要求。
模具结构应该能够满足工件的成型要求,保证工件
的尺寸精度和表面质量。
因此,在设计模具结构时需要充分考虑工
件的特点和成型工艺的要求,合理确定模具的结构形式和尺寸。
此外,嵌入式铜件模具结构的材料选择也非常重要。
模具通常
需要具有较高的硬度、强度和耐磨性,以保证模具的使用寿命和成
型质量。
常见的模具材料包括优质合金钢、工具钢等,选择合适的
材料可以提高模具的耐磨性和使用寿命。
最后,嵌入式铜件模具结构的制造工艺也需要注意。
模具制造
过程中需要进行精密的加工和热处理,以保证模具的精度和耐用性。
同时,还需要进行模具的组装和调试工作,确保模具能够正常运行
并达到预期的成型效果。
总的来说,嵌入式铜件模具结构的设计和制造涉及到多个方面
的因素,需要综合考虑工件要求、材料选择、制造工艺等多个方面,以确保模具能够满足工件的成型要求并具有良好的使用性能。
一种注塑模具的流道转水口镶件结构

一种注塑模具的流道转水口镶件结构
随着经济的发展,注塑模具的应用越来越广泛,在各行各业中都有广泛的应用。
在注塑模具的生产中,流道转水口镶件的结构设计是非常重要的,它可以为注塑模具的性能提供重要的保障。
本文就以“一种注塑模具的流道转水口镶件结构”为标题,简要介绍流道转水口镶件的结构,以及其性能优势。
流道转水口镶件是专为注塑模具设计的,主要用于注塑模具上的流道连接,将模具内的流动液体与外部流动液体连接起来,以保证模具中的液体不断地流动,从而提高模具性能。
此外,流道转水口镶件的结构设计非常复杂,包括芯轴、凸缘、垫圈等多种组件。
芯轴用于将外部液体与模具内液体连接起来,凸缘用于防止液体的泄漏,垫圈则有助于减少噪音和振动,减少模具对外界的影响。
由于流道转水口镶件的结构设计非常复杂,因此它能够为注塑模具提供很多优势。
首先,它能够提高模具的高速性能,提升模具加工的效率,有助于提高产品的产量。
其次,流道转水口镶件可以确保注塑模具正常工作,节约能源,降低企业的运营成本。
此外,流道转水口镶件结构设计非常合理,能够有效的降低注塑模具的磨损,提高模具的使用寿命。
综上所述,流道转水口镶件结构设计在注塑模具中具有重要的意义。
它不仅可以提高模具的加工性能,还可以提高模具的使用寿命,节约能源,降低企业的运营成本。
因此,为保障注塑模具性能,企业必须重视流道转水口镶件的结构设计,使之达到高性能、高品质的要
求,从而提高企业的产品竞争力。
模具结构介绍

注塑模具的结构
注塑模具基本部件的名称
顶针底板
顶针面板
托板
B板
导柱 回针
型
型
腔
腔
拉 料 杆
顶 棍 孔
底板
方铁
顶针
运水
产品
水口
A板
面模
机咀 运水
合模、注塑
开模 分模線
成品頂出
取出成品
二板模剖视图
三板模剖视图
热流道模具
注塑模具的基本结构
主体部件 成型系统 浇注系统 冷却系统 顶出系统
圈、弹簧等。
※ 快速模:仅满足短期生产、极小批量生产的模具。
两板模模架
三板模模架
二、成型系统
指直接构成塑料件的形状及尺寸的各种零件 。
1、型芯:成型塑件内部形状。
2、型腔:成型塑料外部形状。
3、镶件、镶针等。
4、抽芯机构:塑件上有非脱模方向凹凸形状时采用的脱模前成型零件先行移开的一种机构。
一、主体部件
指在模具中起安装、导向、机构动作等作用的模架及其辅助零件。 1、定模部分:开模时留于注塑机定模板上的一部份模具。由A板、面板等零件构成。 2、动模部分:开模时随注塑机动模板运动的部分 。由B板、方铁、底板等零件构成。 3、辅助零件:导柱、导套、导套辅助器、压块、定位梢、耐磨块、平衡块、撑头、定位
C、浇口:指分流道与制品之间的塑料熔体流动通道。
2、冷料穴、拉料杆。
3、排气系统:注塑时排出型腔的气体或挥发物。
A、消除影响充填速度的反向压力。 B、防止因气体受压,体积缩小而温度上升,导致塑件局部碳化或烧焦(排气槽通常设置在熔体最后充满的地方)。 C、防止塑件卷入气泡、出现接缝、表面轮廓不清晰及充填缺料等成型缺陷(尤其是对于快速冲胶成型) 。
- 1、下载文档前请自行甄别文档内容的完整性,平台不提供额外的编辑、内容补充、找答案等附加服务。
- 2、"仅部分预览"的文档,不可在线预览部分如存在完整性等问题,可反馈申请退款(可完整预览的文档不适用该条件!)。
- 3、如文档侵犯您的权益,请联系客服反馈,我们会尽快为您处理(人工客服工作时间:9:00-18:30)。
目的:
1.方便加工(视厂加工能力定).
2.方便排气.
3.方便冷却.
4.节省时间及成本.
5.不能影响模具强度不能与冷却系统.锣丝等干涉.
6.方便线割省模及保证精度(磨).
位置:
1.产品周边有止口,镶通, 不镶通, 不镶通加R(大). (图01)
2.产品PL面是弧面,方便加工.(图02)
3.长型芯. (图03)
4.需换镶件位置.
5.深骨位(十字骨,叉骨,围骨等).
6.有插穿位置,尤其小插穿.
7.有标签地方或者要刻字地方.
8.模具某处特别难加工,单独镶出.
9.模具上有薄弱地方单独镶出方便维修更换.
10.齿轮产品枕底镶方便线割. (图04)
11.行位凸出部分做镶件节省材料及方便维修更换.
12.蕉型(牛角)入胶水口位置要镶.
13.满足客户夹线要求镶.
14.某些地方保证利角必须镶.
15.产品胶位特别薄做镶件排气.
16.呵精度高慢走丝镶.
17.某些地方走不了运水镶铍铜.
18.某些位于产品中间横竖走向并且高度一致的骨位可以镶出,镶件单独线割或磨出. (图05)
19.做截流阀或转水口时.(图06)
20.圆孔和圆柱位置.
21.局部镜面区域做镶件.
类型:
1.直身.
2.斜度. 3冬菇.
固定:
1.做托A.
2.穿针B.
3.斜度C .
4.锁镙丝D (大镶件,没镶通镶件, 冬菇镶件等).
5.枕底E.。