大型飞机制造中的关键数控技术及装备
机械加工技术在航空制造中的应用研究

机械加工技术在航空制造中的应用研究随着现代工业技术的不断进步,机械加工已经成为最基础和关键的工艺之一。
在航空制造领域,机械加工技术的应用也越来越成为制造高品质航空器的必要技能。
本文将探讨机械加工技术在航空制造中的应用研究,包括数控加工、高速切削等方面。
一、数控加工技术在航空制造中的应用数控加工技术是目前最先进的机械加工方式之一,其通过计算机控制机床自动进行机械加工,实现高效率、高精度、高稳定性的加工工艺。
在航空制造中,数控加工技术的应用非常广泛,包括机身外壳、发动机、座舱等各个领域。
在机身外壳的制造中,数控加工技术可以实现大型零部件的高精度加工,如滑动门、天窗、整流罩等,增加了飞机的性能和工艺水平。
而在发动机的制造中,数控加工技术可以实现复杂的轴类零件的加工,如转子、叶轮、轴套等,提高了制造工艺的可靠性和生产效率。
此外,在航空制造中,数控加工技术还可以与其他加工方式结合使用,如融合激光切割、熔化沉积等机械加工方式,实现多层次、复合型零件的制造,如结构用内部蜂窝板材、后来再用纤维增强塑料(FRP)等材料进行模具制造。
二、高速切削技术在航空制造中的应用高速切削技术是机械加工中的一种进阶形式,该技术可以極大提高加工效率、精度和表面质量,应用广泛,有能力满足航空制造领域高要求、高精度、高质量零部件的制造工艺。
在航空制造中,高速切削技术的应用范围也十分广泛。
例如航空发动机的涡轮叶片加工迫切需要高速切削的应用技术。
主流的涡轮叶片采用钢或镍基合金等材料材料制成,其加工精度和表面质量要求很高,而高速切削技术能够让叶片在高速加工过程中,发生少量松散或热膨胀,从而实现完美、高精度的加工过程。
高速切削技术在其他航空领域中的应用也十分广泛,例如中厚板材的高速切削、铝合金等轻金属材料的高速切削、复合材料的高速切削等方面,有利于提高零部件表面质量、机床有效利用、降低材料的加工成本等诸多因素。
三、机械加工技术在航空制造中的优势机械加工技术已成为现代制造业的主要技术之一,其在航空制造中的应用优势也十分明显。
数控技术在航空航天制造中的应用

数控技术在航空航天制造中的应用航空航天制造一直以来都是高度复杂和精密的领域。
为了满足航空航天工业对高质量、高效率和高精度的要求,数控技术在航空航天制造中得到了广泛应用。
本文将探讨数控技术在航空航天制造中的应用,并分析其优势和挑战。
首先,数控技术在航空航天制造中的应用广泛而深入。
在飞机制造过程中,数控机床可以用于加工各种零部件,如机身、发动机和翼面等。
数控机床可以根据设计要求进行自动化加工,保证零部件的精度和质量。
此外,数控机床还可以进行复杂的加工操作,如螺纹加工、曲面加工和孔加工等。
这些加工操作对于飞机的性能和安全至关重要。
其次,数控技术在航空航天制造中的应用提高了生产效率。
与传统的手工加工相比,数控机床可以实现自动化加工,减少了人工操作的时间和成本。
数控机床还可以进行多轴联动加工,提高了加工效率。
此外,数控机床还可以进行批量加工,提高了生产效率。
这些技术的应用使得航空航天制造能够更快速地满足市场需求。
然而,数控技术在航空航天制造中也面临着一些挑战。
首先,数控机床的运行需要高度的技术人员进行操作和维护。
这些技术人员需要具备深厚的机械和电子知识,以及丰富的实践经验。
其次,数控机床的运行需要高精度的控制系统和传感器。
这些控制系统和传感器需要具备高度的可靠性和稳定性,以确保加工过程的精度和质量。
最后,数控机床的维护和更新也需要大量的资金投入。
这些挑战需要航空航天制造企业进行技术创新和人才培养,以应对日益激烈的市场竞争。
总的来说,数控技术在航空航天制造中发挥着重要的作用。
它不仅提高了零部件的加工精度和质量,还提高了生产效率。
然而,数控技术的应用也面临着一些挑战,如技术人员的培养和控制系统的可靠性。
为了进一步推动数控技术在航空航天制造中的应用,航空航天制造企业需要加大技术创新和人才培养的力度。
只有这样,才能在航空航天制造领域取得更大的突破和发展。
综上所述,数控技术在航空航天制造中的应用是不可忽视的。
它为航空航天制造带来了高精度、高效率和高质量的加工手段。
数控机床技术在航空航天制造中的应用案例研究和发展趋势

数控机床技术在航空航天制造中的应用案例研究和发展趋势概述:航空航天制造是高技术、高精度、高要求的领域之一,对制造工艺和设备有极高的要求。
数控机床技术作为一种先进的制造技术手段,已经在航空航天制造中得到了广泛的应用。
本文将以案例研究的方式,深入探讨数控机床技术在航空航天制造中的实际应用,并分析其发展趋势。
案例研究一:数控机床在飞机结构零件加工中的应用数控机床技术在航空航天制造中的应用领域之一是飞机结构零件加工。
传统的加工方法通常需要多道工序,工艺复杂,易出现加工误差。
而数控机床技术的出现有效地解决了这一问题。
以某航空公司的飞机结构零件加工为例,通过数控机床的应用,在提高生产效率的同时,还能保证零件的高精度加工和一致性。
数控机床系统可以根据设计图纸自动调整刀具位置、切削速度和加工路径,实现精确的加工操作。
与传统机床相比,数控机床具有高速、高精度、高稳定性的特点,十分适合飞机结构零件的制造。
此外,数控机床还具备监控和检测功能,可以实时监测加工过程中的各项参数,并及时调整,确保加工质量。
发展趋势:随着航空航天工业的不断发展,对航空零部件的精度和质量要求越来越高。
数控机床技术在航空航天制造中的应用将会得到进一步的推广和发展。
首先,数控机床技术将更加智能化。
未来的数控机床将会具备更强大的自主判断和自适应能力,通过先进的算法和传感器技术,能够实现更准确、更高效的加工过程。
例如,机床可以通过扫描传感器实时检测切削力和温度,调整刀具参数,以避免因过热而引起的损伤。
其次,数控机床将追求更高的精度和稳定性。
随着科技的进步,新材料和新工艺将会被广泛应用在航空航天制造中,对机床的精度和稳定性提出了更高的要求。
未来的数控机床将会采用更精密的传感器和控制系统,以实现更高的加工精度和更小的误差。
再次,数控机床将更加灵活多样化。
航空航天制造中的零件类型繁多,需要不同的加工工艺和工具。
未来的数控机床将会具备更强大的灵活性,可以适应各种不同的零件加工需求。
航空制造智能化技术与装备的研究

航空制造智能化技术与装备的研究摘要:随着时代的发展,人工智能逐渐普及,智能化技术的应用成为制造行业的重点关注对象,为实现航空制造业的智能化,需要实现数字化才能达到自动化的标准,进而促进智能化的发展。
本文从航空制造智能化的技术与装备出发,对航空制造智能化的发展提出相应的建议。
关键词:航空制造;智能化技术;智能化装备;建议;装备研究;技术研究引言:航空制造智能化的推进,带动了整个航空事业的发展,关系到国家安全以及科技发展,对国家整体发展都有着举足轻重的作用。
为实现航空制造智能化技术,需要进行车间的改造,创建数据采集分析系统,将大数据融入其中,通过智能化技术以及装备对航空制造进行关键性的研究,不断突破目前所有的智能化技术。
一、航空制造智能化的必要性智能化制造,是将信息技术及大数据融合在一起,结合最新的新型材料,分布到产品生产、设计以及管理等各个环节。
航空制造智能化能够精准把控相关信息,还可以对决策进行优化,是一个较为先进的制造系统,通过多功能的传感器,能够实现设备的自动化分析、感知以及进行决策等功能,不仅能够提升其效率,还能对产品信息进行及时反馈,有效提升航空制造行业的整体效率。
随着人们对航空产品要求的逐渐提高,对技术的要求也越来越高,相关的制造技术也随之发展,只有不断地对设备进行改进,并加入智能技术,同时能够自动化对机械的生产流程进行控制,这是我国航空制造业发展的必然方向。
二、航空制造中使用的智能化技术(一)使用APS系统进行自动排产APS系统,是一个针对生产规划与拍成系统的进阶式系统,采取最先进下技术,根据产品的实际情况生成相应的生产计划,通过对设备、工序、原料、员工、加工方式以及时间等进行模拟,得出最高效的计划,且对于所有工序都能够同步进行反馈,以及较强的约束力。
据实践表明,将生产设备、硬件和网络融入APS 系统后,将会以最大程度去发挥其功能。
(二)使用工艺组成技术优化生产通过对现有技术改革,加以计算机进行辅助,对零件的制造工艺不断进行优化,不断对生产工序的路径进行探索,以成组技术为基础,逐步组成一个规范的流程以及结构,最后实现航空制造中管理的多层控制,形成一个最优配置,不断贴合实际,让工艺更加实用。
四川省省级财政创新驱动发展专项资金(重大技术装备创新研制和产业化专项)题库
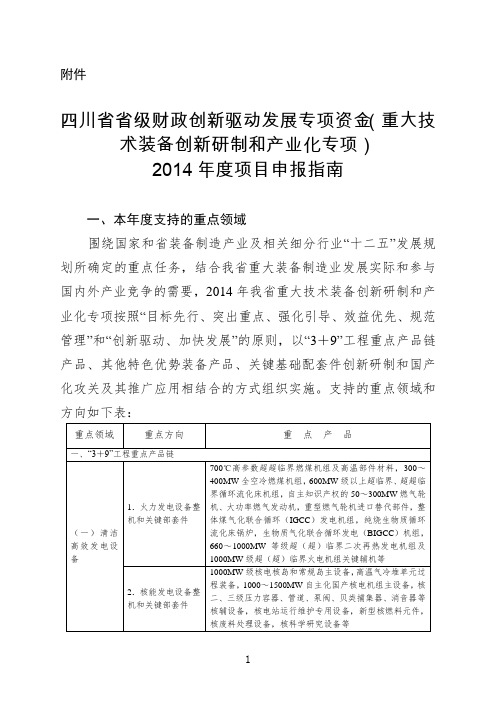
附件四川省省级财政创新驱动发展专项资金(重大技术装备创新研制和产业化专项)2014年度项目申报指南一、本年度支持的重点领域围绕国家和省装备制造产业及相关细分行业“十二五”发展规划所确定的重点任务,结合我省重大装备制造业发展实际和参与国内外产业竞争的需要,2014年我省重大技术装备创新研制和产业化专项按照“目标先行、突出重点、强化引导、效益优先、规范管理”和“创新驱动、加快发展”的原则,以“3+9”工程重点产品链产品、其他特色优势装备产品、关键基础配套件创新研制和国产化攻关及其推广应用相结合的方式组织实施。
支持的重点领域和方向如下表:二、申报条件(一)项目承担单位为规模以上企业,在我省登记注册、依法纳税、具有独立法人资格的企事业单位和央属企业集团在川纳税分公司,各项管理制度健全,具有较强的经济技术实力和创新能力,有专门的研究开发机构和人员,经济效益和社会效益较好,项目在本省范围内实施;(二)项目具有较高的技术水平,符合国家和省的产业政策,属于本年度支持的重点领域和方向;(三)项目符合本省装备制造产业结构调整方向,能够促进装备制造产业发展方式转变和提高装备制造产业配套能力,预期经济效益和社会效益较好;(四)项目总投资一般不低于1000万元;(五)项目具备相关实施条件,有资金投入保证,有实施场地,有相关资质条件或证明,有依托工程或用户合同支撑的优先支持;(六)产学研用联合攻关的重大项目可由主研单位牵头申报,牵头单位与联合申报单位之间应签定合作协议。
三、申报材料申报2014年四川省重大技术装备创新研制和产业化项目须提供以下材料:(一)四川省重大技术装备创新研制和产业化项目申报书;(二)企业营业执照和组织机构代码复印件;(三)四川省重大技术装备创新研制和产业化专项资金项目申请表;(四)2014年四川省重大技术装备创新研制和产业化项目汇总表;(五)项目承担单位近三年主要经济指标及创新能力一览表;(六)经会计师事务所审计的2013年的财务报表和审计报告;(七)项目投资备案、土地审批、环境评估、建设规划等政府审批文件复印件(产业化项目提供,研制项目不提供);(八)项目牵头单位与联合申报单位的合作协议(产学研用合作项目提供,其他项目不提供)(九)证明项目建设资金到位的企业银行存款、银行贷款和其他融资证明文件;(十)其他能证明项目承担单位经济实力和创新能力的材料。
机械工艺技术在航空制造中的应用案例
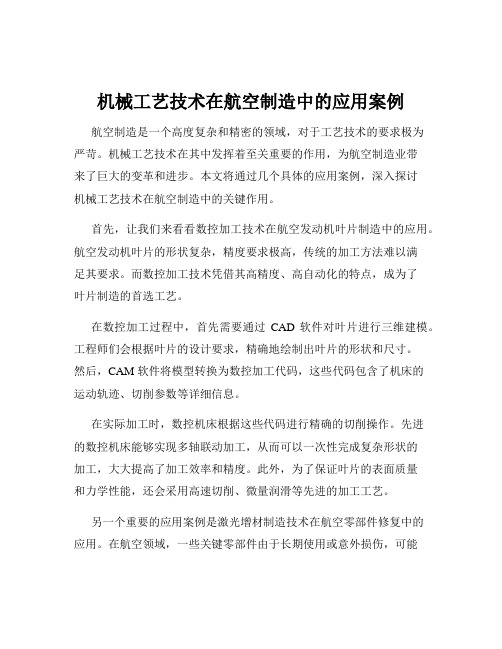
机械工艺技术在航空制造中的应用案例航空制造是一个高度复杂和精密的领域,对于工艺技术的要求极为严苛。
机械工艺技术在其中发挥着至关重要的作用,为航空制造业带来了巨大的变革和进步。
本文将通过几个具体的应用案例,深入探讨机械工艺技术在航空制造中的关键作用。
首先,让我们来看看数控加工技术在航空发动机叶片制造中的应用。
航空发动机叶片的形状复杂,精度要求极高,传统的加工方法难以满足其要求。
而数控加工技术凭借其高精度、高自动化的特点,成为了叶片制造的首选工艺。
在数控加工过程中,首先需要通过CAD 软件对叶片进行三维建模。
工程师们会根据叶片的设计要求,精确地绘制出叶片的形状和尺寸。
然后,CAM 软件将模型转换为数控加工代码,这些代码包含了机床的运动轨迹、切削参数等详细信息。
在实际加工时,数控机床根据这些代码进行精确的切削操作。
先进的数控机床能够实现多轴联动加工,从而可以一次性完成复杂形状的加工,大大提高了加工效率和精度。
此外,为了保证叶片的表面质量和力学性能,还会采用高速切削、微量润滑等先进的加工工艺。
另一个重要的应用案例是激光增材制造技术在航空零部件修复中的应用。
在航空领域,一些关键零部件由于长期使用或意外损伤,可能会出现局部的缺陷或磨损。
传统的修复方法往往需要更换整个零部件,成本高昂且周期长。
激光增材制造技术的出现为零部件修复提供了一种全新的解决方案。
该技术通过将金属粉末逐层熔化堆积,在受损部位精确地构建出新的材料,实现零部件的修复。
例如,对于飞机起落架上的某个关键承力部件,如果出现了局部的裂纹或磨损,可以使用激光增材制造技术在受损部位进行修复。
修复过程中,首先对受损部位进行清理和预处理,然后通过激光扫描精确确定修复区域和形状。
接着,将金属粉末输送到修复区域,在激光的作用下熔化并与基体材料融合,形成牢固的修复层。
与传统修复方法相比,激光增材制造技术不仅能够恢复零部件的尺寸和形状,还可以改善其力学性能,延长使用寿命。
大型飞机用发动机的特点及关键制造技术.
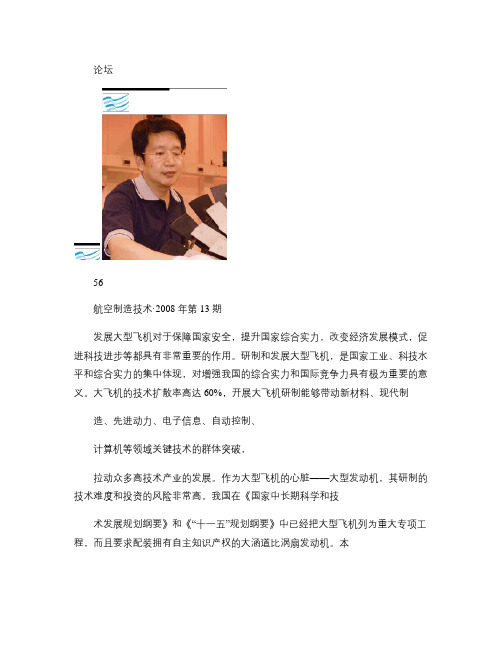
论坛56航空制造技术·2008 年第13 期发展大型飞机对于保障国家安全,提升国家综合实力,改变经济发展模式,促进科技进步等都具有非常重要的作用。
研制和发展大型飞机,是国家工业、科技水平和综合实力的集中体现,对增强我国的综合实力和国际竞争力具有极为重要的意义。
大飞机的技术扩散率高达60%,开展大飞机研制能够带动新材料、现代制造、先进动力、电子信息、自动控制、计算机等领域关键技术的群体突破,拉动众多高技术产业的发展。
作为大型飞机的心脏——大型发动机,其研制的技术难度和投资的风险非常高。
我国在《国家中长期科学和技术发展规划纲要》和《“十一五”规划纲要》中已经把大型飞机列为重大专项工程,而且要求配装拥有自主知识产权的大涵道比涡扇发动机。
本文结合大飞机用发动机的特点对其关键制造技术作了初步探讨和分析,并对我国研制和生产大飞机用发动机提出了几点参考建议。
大飞机用发动机的性能特点所谓大飞机,是指起飞总重量超过100t 的运输类飞机,包括军用和民用大型运输机,也包括150座以上的干线客机。
大飞机的发动机应该具备高可靠性、长寿命、节能环保以及低成本运行等基本要求,在发动机的结构上,具有大涵道比、零件整体化、轻量化等特点并尽可能多地采用复合材料。
与军用战斗机发动机相比,大飞机用发动机的主要特点具体表现为:(1)安全可靠性高。
安全性主要指低的空中停车率(现已降至0.002~0.005次/1000飞行小时)。
为满足这一要求,大飞机用发动机普遍采用了较大的核心机尺寸和较低的涡轮前工作温度。
大型飞机用发动机的特点及关键制造技术Characteristics of Aeroengine for Large Aircraft and Its ManufacturingTechnology西安航空发动机(集团)有限公司马建宁西北工业大学现代设计与集成制造技术教育部重点实验室张定华王增强李山吴宝海国外的成功经验和先进制造技术的发展表明,我国大飞机用航空发动机的研制必须将专业的制造技术与信息技术、管理技术进行有机地结合,并将计算机技术综合应用于设计、制造、检测、管理、销售、使用、服务等发动机研制的全过程。
数控系统在航空制造中的应用
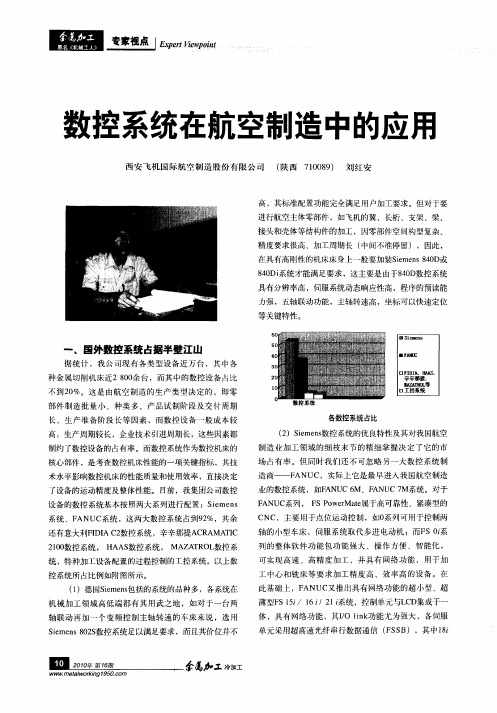
个原 因造成 的 :①国产数控 系统 的五轴 联动加工的软件 技术还 不十 分成熟 ,这就 限制 了它的应 用领域只能局限 在制造 业的 中低端 市场 ,而航 空制造 业大多涉 及5 标 坐 复杂轮廓 、曲面 的加 工 。②国产数控 系统的的软件功能
不够强大 ,如国外的数控系统嵌入AR I NC、OMA T SC T
设备 的数控系统基本按 照两大系列进行配 置 :Se e s im n 系统 、F N 系统 ,这两 大数控 系统 占:9 %,其余 A UC  ̄ 2 1 1
还 有意 大 ̄JI A C 数控系统 ,辛辛那提A R I DI 2 F C AMA I TC 2 0 数 控系统 , HA 数控 系统 , MA A R L 10 AS Z T O 数控 系 统 ,特 种加 工设备配置的过程控制的工控 系统 。以上数 控 系统 所 占比例如附 图所示 。 ( )德国Se n包括的 系统 的品种 多,各 系统在 1 i me s 机械加 工领 域高 低端 都有 其用 武之地 ,如 对于 一台两 轴联 动再加 一个 变频 控制 主轴 转速 的车床 来说 ,选 用
精度要 求很 高、加 工周期长 ( 中间不准停 留),因此 ,
在具有高 刚性 的机床 床身上一 般要加 装Se n 4 D或 i me s8 0 8 0 系统才能满足要 求 ,这主要是 由于 80 4 Di 4 D数控系统
具有分辨率 高 ,伺服 系统动态响应性高 ,程序的预读能
力强,五轴联动 功能 ,主轴转速高 ,坐标可以快速定位
等 刀具管理 、优化铣 削系统 ,主要是利 用他 们通过对数 控机床主轴切 削功率 载荷优化 ,提高现有数控 机床粗加 工效率 ;此 外像联 网组 态软 件 、D 功能等 涉及数 控 NC 系统技术前沿的软件 开发技术 。国产数控 系统距 离国际 流行数 控系统 还有一 定差距 。 ③ 国际上流行 的数控 系
数控技术在航空制造中的应用教程

数控技术在航空制造中的应用教程随着航空业的飞速发展,航空制造领域对精密加工的需求越来越大。
而数控技术作为一项先进的制造技术,已经在航空制造中发挥了重要的作用。
本文将为大家介绍数控技术在航空制造中的应用,并提供相应的教程。
一、数控技术简介数控技术(Computer Numerical Control)是一种利用计算机控制工具路径和动作的自动化加工方法。
它通过预先编制的程序来控制机床和工具,实现高精度、高效率的零件加工。
数控技术不仅提高了加工精度和效率,还减少了人为操作引起的误差,同时还能够实现复杂形状的加工。
二、数控技术在航空制造中的应用1. 零件加工航空制造中的许多零件都需要高精度的加工,例如飞机发动机、机翼等。
数控机床可以通过预先编写的程序来控制工具的路径和动作,实现对零件的精密加工。
数控技术不仅可以提高加工效率,还可以保证零件的一致性和精度,确保飞机的安全性和稳定性。
2. 车削加工和铣削加工在航空制造中,常常需要对金属材料进行车削和铣削加工。
数控车床和数控铣床可以通过编写不同的程序来实现对不同形状的零件进行加工。
相比于传统的手工车削和铣削,数控技术更加高效且具有更高的精度,可以大大提升生产效率。
3. 电火花加工电火花加工是利用电火花放电来加工金属材料的一种加工方法。
它主要用于加工硬度高、耐磨性强的材料,例如航空发动机的涡轮叶片。
数控电火花加工机床可以根据预先编写的程序,在金属材料表面产生放电,通过放电的热量将金属材料加工成需要的形状。
数控电火花加工可以提高加工精度和效率,同时还可以避免传统电火花加工中的人为操作误差。
4. 螺纹加工在航空制造中,常常需要对螺纹进行加工,例如螺旋桨、螺钉等。
数控螺纹加工可以通过编写程序来控制工具的运动轨迹,实现精准的螺纹加工。
相比于传统的手工螺纹加工,数控螺纹加工更加高效且精度更高,可以大大提升生产效率。
三、数控技术在航空制造中的应用教程1. 学习数控编程掌握数控编程是学习数控技术的第一步。
数控技术在飞机零件加工中的应用
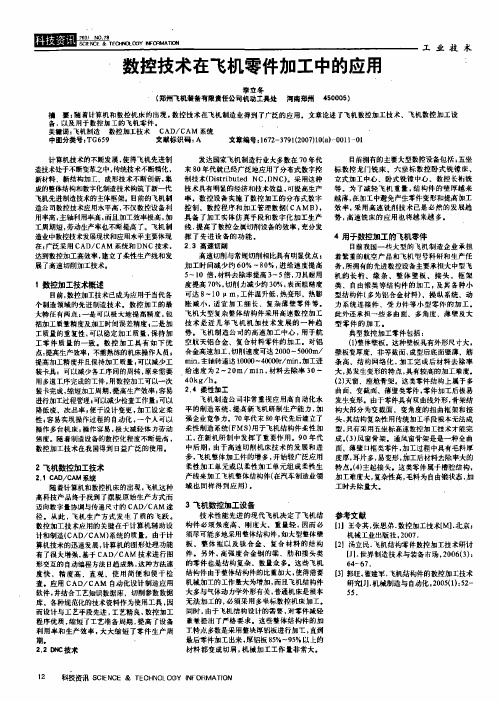
关健词:飞机制造 数控加工技术 CAD/ CAM 系统 中图分类号:TG6 59 文献标识码 : A 计算机技术的不断发展, 使得飞机先进制 造技术处于不断变革之中, 传统技术不断精化, 新材料、新结构加工,成形技术不断创新, 集 成的整体结构和教字化制造技术构筑了新一代 飞机先进制造技术的主体框架。目前的飞机制 造公司数控技术应用水平高, 不仅数控设备利 用率高, 主轴利用率高, 而且加工效串极高, 加 工周期短, 劳动生产率也不断提高了。飞机制 造业中数控技术发展现状和应用水平主要休现 在: 广泛采用CAD/ CAM 系统和DN C 技术, 达到数控加工高效率, 建立了柔性生产线和发
皿 路 粗
SiN&E aGC.zT, aEn e oE o
二 ,, 下
工 业 技 术
.Hale Waihona Puke 数 控 技 术 在 飞 机 零 件 加 工 中 的 应 用
李 立冬
( 郑州飞机装备有限贵任公司机动工具处
摘 备 以及用 于数控 加 工的 飞机 零 件。
河南郑州
450005 )
要:防着计算机和数控机床的出现, 数控技术在飞机制造业得到了广泛的应用。文章论述了飞机数控加工技术、飞机数控加工设 文章编号:1672- 3791(2007)10(a卜0011- 0 1 目前拥有的主要大型数控设备包括: 五坐 标数控龙门铣床、六坐标数控卧式铣,t 床、 立式加工中心、卧式铣镬中心,数控长拓铣 等。为了减轻飞机重t , 结构件的壁厚越来 越薄, 在加工中避免产生零件变形和提高加工 效率, 采用高速铣削技术已是必然的发展趋 势, 高速铁床的应用也将越来越多。
发达国家飞机制造行业大多数在 70 年代 末8。 年代就已经广泛地应用了分布式数字控 制枝术(Dis trib uted N C,D NC) 。采用这种 技术具有明显的经济和技术效益, 可提高生产 率。数控设备实施了数控加工的分布式故字 控制、数控程序和加工管理数据( CA M B) , 具备了加工实体仿真手段和数字化加工生产 线, 提高了散控金属切削设备的效率 , 充分发 挥了先进设备的功能。 2 3 高速切削 高速切削与常规切削相比具有明显优点 : 展 了高速 切削 加工技术 。 加工时间减少约 6 0% 一 0% , 8 a 进给速度提高 5 一10 倍, 材料去除率提高3- 5 倍, 刀具耐用 ,数控加工技术概述 度提高 70%, 切削力减少约30%, 表面粗糙度 可达8 - 10 ”m , 工件温升低, 热变形、热膨 目前, 数控加工技术已成为应用干当代各 胀减小。 适宜加工细长、复杂薄壁零件等. 个制造领域的先进制造技术。数控加工的最 大特征有两点:一是可以极大地提高精度, 包 飞机大型复杂整体结构件采用高速数控加工 技术是近几年飞机 机加技术发展的一种趋 括加工质量精度及加工时间误差精度。 二是加 势。飞机制造公司的高速加工中心 , 用于航 工质且的重复性, 可以稳定加工质量, 保持加 空航天铝合金、复合材料零件的加工。对铝 工零件质量的一致. 数控加工具 有如下优 5000m/ 点 提高生产效率, 不需熟练的机床操作人员。 合金高速加工. 切削速度可达2000 一 mm, 主轴转速 达 10000- 40000r / mi n , 加工进 提高加工精度并且保持加工质盆; 可以减少工 给速度为2 一20 m/ min , 材料去除率 30 一 装卡具。可以减少各工序间的周转, 原来需要 4 0k g / h , 用多道工序完成的Z 件, 用数控加工可以一次 装卡完成, 缩短加工周期, 提高生产效率;容易 2 . 4 柔性 加工 飞机制造公司非常重视应用高自动化水 进行加工过程管理.可以减少检查工作盈.可以 加 降低废 次品串, 便于设计变更, 加工设定柔 平的制造系统 提高新飞机研制生产能力, 强企业竞争力。70 年代末 0 年代先后建立了 性。 容易实现操作过程的自动化, 一个人可以 柔性制造系统( F MS )用于飞机结构件柔性加 操作多合机床; 操作容易, 极大减轻体力劳动 工, 在新机研制中发挥了重要作用。9 0 年代 强度。随着制造设备的数控化程度不断提高. 数控加工技术在我国得到日益广泛的使用. 中后期, 由于高速切削机床技术的发展和进 步, 飞机整体加工件的增多, 开始较广泛应用 柔性加工单元或以柔性加工单元组成柔性生 2 飞机数控加工技术 产线来加工飞机整体结构件(在汽车制造业领 2.1 CA CAM系统 D/ 随着计算机和数控机床的出现, 飞机这种 城 也 同 样 得到 应用 ) 。 高科技产品终于找到了摆脱原始生产方式而 3 飞机数控加工设备 迈向 数字I 协调与传递尺寸的 CAD/ CAM 途 技术性能先进的现代飞机决定了飞机结 径。从此 , 飞机生产方式发生了质的 K跃。 构件必须强度高、刚度大,重量轻, 因而必 数控加工技术应用的关键在于计算机辅助设 须尽可能多地采用整体结构件, 如大型整体壁 计和制造(CA D/ C AM) 系统的质丘。由于计 板、整体框以及钦合金、复合材料的结构 算机技术的迅速发展, 计算机的图形处理功能 件。另外, 高强度合金俐的梁、肋和接头类 有了很大增强.基于CA D/ C AM 技术进行图 的零件也是结构复杂 数且众多。这些飞机 形交互的自动编程方法日趋成熟, 这种方法速 结构件由干整体结构件的比重加大, 使得需要 度快,精度高 、直观、使 用简便和便干检 机械加工的工作量大为增加, 而且飞机结构件 查。应用CA D/ CAM 自动化设计制造应用 大多与气体动力学外形有关, 普通机床是根本 软件, 并结合工艺知识数据库,切削参敖数据 无法加工的, 必须采用多坐标数控机床加工。 库、各种规范化的技术资料作为使用工具, 因 而设计与工艺手段先进, 工艺精良, 数控加工 同时 。 由于飞机结构设计的需要, 对零件减轻 程序优质, 缩短了工艺准备周期, 提高了设备 重最提出了严格要求. 这些整体结构件的加 利用率和生产效率 . 大大缩短了零件生产周 工特点多 是采用整块厚铝板进行加工 , 直到 期。 最后零件加工出来, 厚铝板85%- 95%以上的 材 料都 变 成切 屑 , 械加 工工 作 It 非常 大 。 机 2 , 【翻技术 2 ”二 科技资讯 S CI N 及 TECHN E CE OLOOY IN ORMATION F
精密制造技术在航空领域的应用

精密制造技术在航空领域的应用随着科技的不断发展,现代航空技术越来越成为人们日常生活的重要组成部分。
而精密制造技术正是实现航空技术突破的关键之一,它的应用范围不仅局限于飞机的制造,还包括发动机、仪表、螺旋桨等配件和设备的制造和维护。
本文将通过几个具体案例,探讨精密制造技术在航空领域的广泛应用。
一、精密制造技术在飞机制造中的应用现代喷气式飞机的制造十分复杂,需要使用高精度的制造设备和工艺,才能满足其复杂的结构和高性能的要求。
其中,钛合金材料及其加工工艺,是现代飞机制造中的重点和难点。
在现代喷气式飞机的制造中,钛合金是应用最为广泛的重要材料之一。
钛合金不仅具有良好的力学性能和耐腐蚀性,而且具有优异的重量比。
但是,由于钛合金具有高硬度和难加工的特点,必须使用高精度的加工设备和工艺才能进行加工。
精密制造技术在此时发挥了重要的作用。
例如,运用先进的数控铣削技术,可以实现复杂结构、高精度和高质量的零部件制造。
另外,与传统技术相比,激光焊接技术可以在焊接材料时减少不必要的再加热和变形,从而实现更高的精度和更高的质量。
二、精密制造技术在发动机制造中的应用发动机是航空技术的“心脏”,是保证航班安全的重要组成部分。
而现代发动机的制造过程中,涵盖了众多的精密制造技术。
例如,火花放电加工就是一种重要的精密制造工艺之一。
它可以直接将电极加工成工件表面所需的形状,精度高、效率高,适用于不同材料的加工。
火花加工的应用,可以帮助制造商开发更加锋利和高效的刀具,使得加工精度和效率大大提高,从而提高了发动机的性能。
另外,在制造高温合金材料的发动机叶轮时,精密铸造技术和数控制造技术也得到了广泛应用。
在数控制造技术中,采用了一些高精度的机床,例如五轴数控机、电火花生产线等,以实现更高精度和更大尺寸的制造。
这些技术的应用可提高加工效率,降低生产成本,同时还可以在功能和质量方面对发动机的性能进行额外增强。
三、精密制造技术在航空设备维修中的应用除了在飞机和发动机的制造中应用广泛外,精密制造技术在航空设备维修中同样也发挥了重要作用。
数控加工在航空航天领域的应用

数控加工在航空航天领域的应用随着科技的不断进步,航空航天领域对于制造工艺的要求也越来越高。
数控加工作为一种高精度、高效率的制造技术,在航空航天领域得到了广泛应用。
本文将就数控加工在航空航天领域的应用进行探讨,并分析其带来的优势和挑战。
一、数控加工简介数控加工,即Computer Numerical Control的缩写,通过计算机控制的加工方式,具有高精度、高效率、高稳定性等特点。
相比传统的手工操作和普通机械加工,数控加工具有更高的准确度和重复性,能够满足航空航天领域对于精度要求极高的零件加工。
二、数控加工在航空制造中的应用1. 零部件加工在航空航天领域,各种复杂、精密的零部件是飞机能够正常运行的基础。
传统的加工方式需要经过多次手工操作和磨削,对于复杂形状的零部件加工难度较大。
而数控加工可以通过预先编程的方式,实现对复杂形状零部件的高精度加工,大大提高了生产效率和零部件的质量。
2. 钛合金加工在航空航天领域,钛合金是一种重要的结构材料,具有优异的强度和耐腐蚀性能。
然而,钛合金非常难以加工,传统的方法需要大量的工时和能源。
数控加工可以根据钛合金的物理特性,通过优化的刀具和切削参数,实现高效、精确地加工,大幅提升了钛合金零部件的制造效率和质量。
3. 复合材料加工航空航天领域中,复合材料因其优异的性能成为重要的结构材料。
然而,复合材料的加工难度较大,传统的切削方法容易导致材料破损和纤维层分离。
而数控加工可以通过精确的控制和切削参数的优化,实现对复合材料的高效、准确加工,保证了结构的完整性和性能,满足了航空航天领域对于材料加工的要求。
三、数控加工的优势和挑战1. 优势(1)高精度:数控加工具有高精度的特点,能够满足航空航天领域对于零部件加工的高要求。
(2)高效率:数控加工通过预编程和自动控制,能够实现高效率的生产,提高了加工效率。
(3)高稳定性:数控加工具有稳定性高的特点,能够保证批量生产的一致性和稳定性。
数控技术和装备的应用与发展
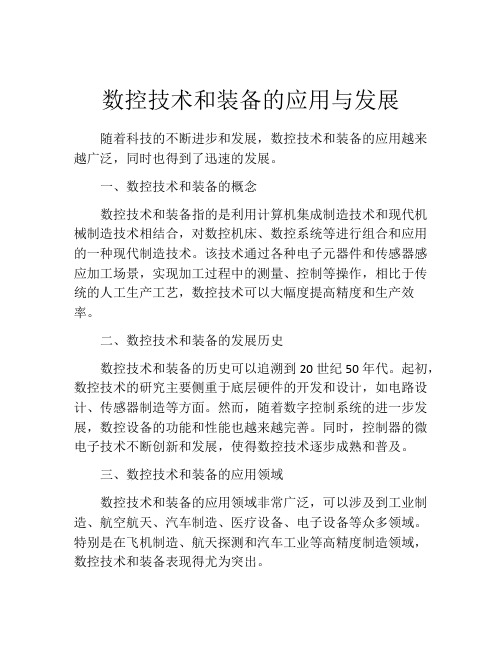
数控技术和装备的应用与发展随着科技的不断进步和发展,数控技术和装备的应用越来越广泛,同时也得到了迅速的发展。
一、数控技术和装备的概念数控技术和装备指的是利用计算机集成制造技术和现代机械制造技术相结合,对数控机床、数控系统等进行组合和应用的一种现代制造技术。
该技术通过各种电子元器件和传感器感应加工场景,实现加工过程中的测量、控制等操作,相比于传统的人工生产工艺,数控技术可以大幅度提高精度和生产效率。
二、数控技术和装备的发展历史数控技术和装备的历史可以追溯到20世纪50年代。
起初,数控技术的研究主要侧重于底层硬件的开发和设计,如电路设计、传感器制造等方面。
然而,随着数字控制系统的进一步发展,数控设备的功能和性能也越来越完善。
同时,控制器的微电子技术不断创新和发展,使得数控技术逐步成熟和普及。
三、数控技术和装备的应用领域数控技术和装备的应用领域非常广泛,可以涉及到工业制造、航空航天、汽车制造、医疗设备、电子设备等众多领域。
特别是在飞机制造、航天探测和汽车工业等高精度制造领域,数控技术和装备表现得尤为突出。
四、数控技术对制造业的影响数控技术的推广和应用,对制造业的影响是具有深远意义的。
首先,数控技术和装备可以提高生产效率和质量。
数控机床不仅能够提高工艺稳定性和加工精度,而且还具备高速度、高精度、高自动化的特点,可以大幅度降低生产成本和劳动强度。
其次,数控技术可以为制造企业带来源源不断的利润空间。
在竞争激烈的市场环境下,制造企业如果不能适应数控技术的趋势,很容易被其他更加先进的生产企业所取代,从而失去自己的市场份额和竞争优势。
最后,数控技术的普及可以推动工业高质量发展,加快制造业转型升级。
现代制造业的发展趋势是朝着高精密和高端的方向不断迈进,而数控技术的引入可以帮助企业更好地实现资源配置和生产组织调度,从而升级和提升企业自身能力。
五、数控技术未来发展趋势如今,随着全球制造业的转型加速,数控技术正成为一个十分热门的领域。
高端数控加工技术在国防航空产品制造中的应用

高端数控加工技术在国防航空产品制造中的应用随着国防科技的不断发展,高端数控加工技术在国防航空产品制造中的应用也越来越广泛。
数控机床是一种高精度、高效率、高稳定性的自动化加工设备,是现代制造业不可或缺的核心设备之一。
在国防领域中,数控机床已经成为生产各种精密零件、装备和武器系统的重要工具之一。
一、数控机床在国防航空产品制造中的重要作用在国防航空产品制造中,数控机床拥有不可替代的作用。
首先,数控机床可以实现高精度、高速度的加工,大大提高了航空产品的生产效率和质量。
其次,数控机床可以自动化进行加工操作,既提高了生产效率,也降低了生产成本,同时还减少了人为因素的干扰。
此外,数控机床的加工精度和稳定性也得到了保证,避免了人工加工中出现的误差和浪费。
二、数控技术在各类航空产品中的应用案例1. 气动结构件在航空领域中,气动结构件的制造对加工精度和质量要求非常高。
数控机床可以根据设计图纸自动进行加工处理,大大提高了加工精度和质量。
例如,在飞机航行过程中,轮子所受的力很大,需要采用高强度的材料,并通过精密加工技术来保证轮胎的完整性和稳定性。
数控技术可以很好地控制加工精度,确保零件的精度和质量。
2. 发动机零部件发动机是飞机最关键的部件之一,也是生产难度最大的部件之一。
通过数控技术可以确保发动机零部件的高精度加工,大大提高了发动机的性能和寿命。
例如,飞机发动机前部的叶片经常需要使用五轴数控机床进行加工,以确保零件内部的复杂结构和孔洞要求的加工精度。
3. 动力系统动力系统包括发动机、飞机乘员饰品等,也是航空产品中最重要的部件之一。
数控机床的应用可以提高动力系统的精度和质量,并且能够制造出复杂性能优越的零部件。
例如,在飞机降落时,需要使用高质量和高精度的制动系统,以确保飞机在地面上的安全行驶。
通过数控技术,可以制造出高精度、高耐久的制动系统,确保安全可靠性。
三、数控机床技术的发展趋势1. 越来越智能化随着人工智能技术的发展,数控机床也将越来越智能化。
航空制造中数控加工能力提上的有效措施
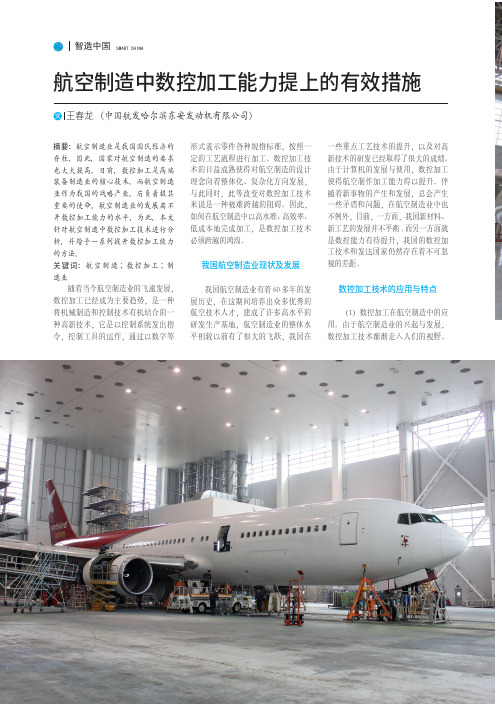
智造中国 SMART CHINA中国航班 CHINA FLIGHTS116航空制造中数控加工能力提上的有效措施文王春龙 (中国航发哈尔滨东安发动机有限公司)摘要:航空制造业是我国国民经济的脊柱,因此,国家对航空制造的要求也大大提高,目前,数控加工是高端装备制造业的核心技术,而航空制造业作为我国的战略产业,肩负着极其重要的使命。
航空制造业的发展离不开数控加工能力的水平,为此,本文针对航空制造中数控加工技术进行分析,并给予一系列提升数控加工能力的方法。
关键词:航空制造;数控加工;制造业随着当今航空制造业的飞速发展,数控加工已经成为主要趋势,是一种将机械制造和控制技术有机结合的一种高新技术,它是以控制系统发出指令,控制工具的运作,通过以数字等形式表示零件各种规格标准,按照一定的工艺流程进行加工。
数控加工技术的日益成熟使得对航空制造的设计理念向着整体化、复杂化方向发展,与此同时,此等改变对数控加工技术来说是一种极难跨越的阻碍。
因此,如何在航空制造中以高水准、高效率、低成本地完成加工,是数控加工技术必须跨越的鸿沟。
我国航空制造业现状及发展我国航空制造业有着60多年的发展历史,在这期间培养出众多优秀的航空技术人才,建成了许多高水平的研发生产基地,航空制造业的整体水平相较以前有了很大的飞跃,我国在一些重点工艺技术的提升,以及对高新技术的研发已经取得了很大的成绩。
由于计算机的发展与使用,数控加工使得航空制作加工能力得以提升。
伴随着新事物的产生和发展,总会产生一些矛盾和问题,在航空制造业中也不例外,目前,一方面,我国新材料、新工艺的发展并不平衡,而另一方面就是数控能力有待提升,我国的数控加工技术和发达国家仍然存在着不可忽视的差距。
数控加工技术的应用与特点(1)数控加工在航空制造中的应用。
由于航空制造业的兴起与发展,数控加工技术渐渐走入人们的视野。
智造中国SMART CHINACHINA FLIGHTS中国航班117最早的数控加工技术来起源于20世纪40年代末,它是由美国的一家直升机公司所提出的遐想,由此便产生了数控机床,到了1952年经过美国麻省理工学院不懈的研究,最终制得三坐标数控机床,这在50年代中期被广泛用于加工飞机零件。
大型航空结构件

大型航空结构件数控加工数控加工作为一种高效、精密的数字化切削加工技术,成为飞机复杂结构件机械加工的主要手段,飞机结构件50%以上的加工工作量由数控加工完成。
而随着航空工业的不断发展,飞机性能不断提升,飞机结构件日趋大型化、复杂化,对相应的数控加工装备及数控加工技术提出了更为苛刻的要求。
飞机结构件是构成飞机机体骨架和气动外形的主要组成部分,随着现代飞机为满足隐身、超声速巡航、超常规机动、高信息感知能力、长寿命、结构轻量化等方面的性能要求大量地采用新技术、新结构、新材料其结构件呈现出结构大型化的特点:相对于以往的小型结构件焊接、组装模式,采用大型整体结构件可大量减少结构件零件数量和装配焊接工序,并有效减轻飞机整机重量,提高零件强度和可靠性,使飞机的制造质量显著提高,如 F -22战机后机身整体框毛坯尺寸达到4000mm×2000mm。
随着材料技术、制造技术的发展以及飞机性能和结构的需要,在国内外先进主力战斗机的结构设计中,为满足飞机轻量化、长寿命、易维护等需求,机体零件结构向整体化、薄壁化、结构承载与功能综合化等方向发展,因此越来越多地采用了整体结构设计,其典型的代表就是整体框结构,将以前需要数个框段通过机械连接而成的框改为一个整体结构的大框,这样可以大幅减少零件数量,增加强度,减轻结构重量。
目前,发达国家设备精良,工艺技术先进,并针对飞机大型整体结构零件的特点进行了大量的工艺技术研究。
另外,通过对难加工材料的加工工艺方法进行研究,也大大提高了以钛合金为代表的难加工材料的加工效率。
但我国大型飞机整体结构件的数控加工仍然处于起步阶段,加工效率及质量方面都还明显落后于发达国家,这已成为制约整个飞机研制和生产的“瓶颈”之一。
航空结构件的上述发展趋势决定了其工艺特点:结构复杂,加工难度大——零件外形涉及机身外形、机翼外形及翼身融合区外形等复杂理论外形,且需与多个零件进行套合;切削加工量大——材料去除率达到90% 以上,部分零件甚至达到98%;加工精度高——装配协调面、交点孔等数量多,零件制造精度要求高;难加工材料比例大——以钛合金、复合材料为代表的难加工材料比重越来越大,对航空制造业提出了严峻的挑战。
大型飞机结构件数字化制造与成形技术

大型飞机结构件数字化制造与成形技术一、概述1. 大型飞机结构件制造技术的重要性随着航空产业的飞速发展,大型飞机的制造技术也得到了空前的发展。
而在飞机制造过程中,结构件的制造是至关重要的一环,其质量和精度直接影响着飞机的安全性和航空运输的效率。
数字化制造与成形技术在大型飞机结构件制造中发挥着至关重要的作用。
二、大型飞机结构件数字化制造技术2. 数字化设计技术数字化设计技术是大型飞机结构件制造的第一步,它通过计算机辅助设计软件,实现了对飞机结构件的设计、优化和改进。
相比传统设计方法,数字化设计技术具有设计周期短、效率高、精度高等优势,能够有效地提高飞机的设计质量和生产效率。
3. 数字化扫描技术数字化扫描技术是大型飞机结构件制造中的重要技术手段之一。
通过激光扫描仪等设备,可以实现对飞机结构件的快速、精准的三维扫描,将实体物体转化为数学模型,为后续的数字化制造提供了精确的数据基础。
4. 数控加工技术在大型飞机结构件的制造中,数控加工技术是不可或缺的一环。
通过数控机床、数控车床等设备,可以实现对结构件的高精度加工,保证了结构件的尺寸和形状的精准度。
5. 3D打印技术3D打印技术作为一种革命性的数字化制造技术,也在大型飞机结构件制造中得到了广泛应用。
通过3D打印技术,可以实现对复杂结构件的快速制造,大大缩短了制造周期和降低了制造成本。
三、大型飞机结构件成形技术6. 复合材料成形技术大型飞机结构件的重量和强度要求非常高,因此复合材料成形技术成为了制造这些结构件的重要手段。
通过真空成型、压缩成型等技术,可以实现对复合材料的成型,使其具备较高的力学性能和表面质量。
7. 热成形技术对于一些金属结构件来说,热成形技术是制造高强度、复杂形状结构件的有效方法。
通过加热和塑性变形,可以实现对金属材料的成形,提高其强度和塑性。
8. 精密成形技术大型飞机结构件的成形工艺要求非常高,需要保证结构件的尺寸精度和表面质量。
精密成形技术通过模具设计、成形工艺优化等手段,实现了对结构件的高精度成形,满足了飞机的使用要求。
机械工程中的数控加工技术在航空航天制造中的应用

机械工程中的数控加工技术在航空航天制造中的应用数控技术(数控加工技术)是指数字计算机控制设备和数控装置对机床进行数控运作的技术手段。
在现代航空航天制造业中,数控加工技术扮演着至关重要的角色。
本文将探讨机械工程中的数控加工技术在航空航天制造中的应用,并详细介绍其在不同领域的具体应用案例。
一、数控加工技术在航空航天制造中的重要性航空航天制造涉及到高精度、大型、复杂零部件的加工,而数控加工技术正是能够满足这些需求的重要技术之一。
相比传统的手工操作或非数控加工方式,数控加工技术具有以下优势:1. 提高加工精度和稳定性:数控加工技术采用计算机精确控制,能够实现精细的切削操作,从而提高零部件的加工精度和稳定性。
2. 提高加工效率:数控加工技术采用自动化控制,能够实现多种工序的无人化操作,提高了生产效率。
3. 降低人工成本:数控加工技术的自动化程度高,人工干预少,降低了人力成本。
4. 增强生产灵活性:数控加工技术可以根据产品的不同需求进行灵活调整和切换,提高了生产的灵活性。
二、数控加工技术在航空航天制造中的具体应用1. 航空发动机零部件加工:航空发动机是飞机的动力系统,其零部件的加工要求非常高。
数控加工技术在航空发动机零部件的加工中发挥着重要作用。
通过数控加工技术,可以实现对叶轮、叶片、燃烧室等复杂形状的加工,提高加工精度和一致性。
2. 飞行控制系统零部件加工:飞行控制系统是飞机飞行安全的关键之一。
该系统的零部件加工需要非常高的精度和稳定性。
数控加工技术可以实现对液压泵阀、油箱等零部件的高精度加工,确保其性能和可靠性。
3. 航天器结构部件制造:航天器的结构部件制造对加工精度和质量要求非常高。
数控加工技术能够实现对一些复杂形状的结构部件的加工,如航天器的外壳、载荷舱等。
4. 航空航天用材料加工:航空航天用材料往往具有较高的硬度和耐磨性,传统的加工方式难以满足对其加工的要求。
数控加工技术采用高速切削、精细控制等技术手段,能够实现对这些材料的高效加工。
飞机装配中的先进制孔技术与装备探究
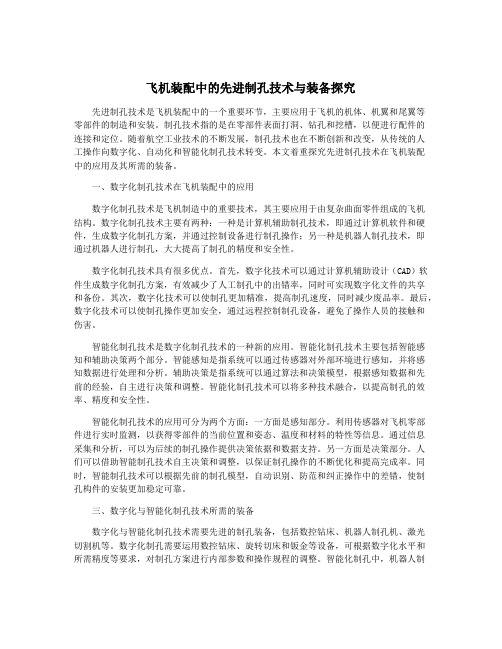
飞机装配中的先进制孔技术与装备探究先进制孔技术是飞机装配中的一个重要环节,主要应用于飞机的机体、机翼和尾翼等零部件的制造和安装。
制孔技术指的是在零部件表面打洞、钻孔和挖槽,以便进行配件的连接和定位。
随着航空工业技术的不断发展,制孔技术也在不断创新和改变,从传统的人工操作向数字化、自动化和智能化制孔技术转变。
本文着重探究先进制孔技术在飞机装配中的应用及其所需的装备。
一、数字化制孔技术在飞机装配中的应用数字化制孔技术是飞机制造中的重要技术,其主要应用于由复杂曲面零件组成的飞机结构。
数字化制孔技术主要有两种:一种是计算机辅助制孔技术,即通过计算机软件和硬件,生成数字化制孔方案,并通过控制设备进行制孔操作;另一种是机器人制孔技术,即通过机器人进行制孔,大大提高了制孔的精度和安全性。
数字化制孔技术具有很多优点。
首先,数字化技术可以通过计算机辅助设计(CAD)软件生成数字化制孔方案,有效减少了人工制孔中的出错率,同时可实现数字化文件的共享和备份。
其次,数字化技术可以使制孔更加精准,提高制孔速度,同时减少废品率。
最后,数字化技术可以使制孔操作更加安全,通过远程控制制孔设备,避免了操作人员的接触和伤害。
智能化制孔技术是数字化制孔技术的一种新的应用。
智能化制孔技术主要包括智能感知和辅助决策两个部分。
智能感知是指系统可以通过传感器对外部环境进行感知,并将感知数据进行处理和分析。
辅助决策是指系统可以通过算法和决策模型,根据感知数据和先前的经验,自主进行决策和调整。
智能化制孔技术可以将多种技术融合,以提高制孔的效率、精度和安全性。
智能化制孔技术的应用可分为两个方面:一方面是感知部分。
利用传感器对飞机零部件进行实时监测,以获得零部件的当前位置和姿态、温度和材料的特性等信息。
通过信息采集和分析,可以为后续的制孔操作提供决策依据和数据支持。
另一方面是决策部分。
人们可以借助智能制孔技术自主决策和调整,以保证制孔操作的不断优化和提高完成率。
飞机制造过程中的数控加工技术应用

飞机制造过程中的数控加工技术应用飞机制造是一个需要高精度、高性能加工技术的行业,而数控加工技术是现代制造业中不可或缺的一部分。
数控加工技术已经被广泛应用于飞机制造的每个环节,从飞机零部件的设计、加工到组装,都有数控加工技术的影子。
本文将从飞机制造中数控加工技术的应用入手,深入探究数控加工技术在飞机制造中的作用,包括其发展历程、应用范围及未来的发展趋势。
一、数控加工技术在飞机制造中的发展历程数控加工技术最初的应用是在20世纪60年代,当时的主要目的是提高加工效率和精度。
经过几十年的发展,随着工业自动化程度的提高,数控加工技术的应用范围越来越广泛,并且不断改善和升级。
而在飞机制造行业中,数控加工技术的应用也经过了一定的发展历程。
早期的飞机制造过程主要采用人工操作和传统的机械加工方式,色差、误差大、效率低下,难以满足飞机质量和生产效率的要求。
1970年代末,随着航空工业的发展和自动化水平的提高,数控加工技术被引入飞机制造中。
在数控机床上,只要将设计好的CAD图形转化为NC程序,数控机床就可以自动完成对工件的加工。
二、数控加工技术在飞机制造中的应用范围数控加工技术在飞机制造中的应用范围非常广泛,包括飞机零部件的制造、试验、组装等多个环节。
在飞机零部件的制造中,数控加工技术主要用于机翼、发动机舱壁、底盘等零部件的加工。
相比传统的机械加工方式,数控加工技术可以提高加工的精度和效率,缩短制造时间。
此外,在试验环节中,数控加工技术也可以用于飞机模型的制作和测试,为飞机设计提供更为准确的数据和参考。
在组装环节中,数控加工技术也有非常重要的应用。
为了确保飞机的结构安全和飞行性能,飞机的组装需要非常高的精度和可靠性。
数控加工技术可以实现高精度零部件的精确组装,大幅提高组装精度和效率,确保飞机的安全飞行。
三、数控加工技术在飞机制造中的未来发展趋势随着科技的进步和需求的不断变化,数控加工技术在飞机制造中的应用也在不断地发展和改进。
- 1、下载文档前请自行甄别文档内容的完整性,平台不提供额外的编辑、内容补充、找答案等附加服务。
- 2、"仅部分预览"的文档,不可在线预览部分如存在完整性等问题,可反馈申请退款(可完整预览的文档不适用该条件!)。
- 3、如文档侵犯您的权益,请联系客服反馈,我们会尽快为您处理(人工客服工作时间:9:00-18:30)。
大型飞机制造中的关键数控技术及装备刘强北京航空航天大学机械工程及自动化学院;国防科技工业高效数控加工技术研究应用中心大型飞机结构与材料的特点对数控加工技术及装备提出了很高的要求,主要表现为:(1)铝合金结构零件数控切削加工的高速化和高效化;(2)钛合金及结构钢零件数控切削加工大扭矩和高刚性要求;(3)复合材料铺放及加工的自动化和数控化;(4)数控加工工艺与装备技术解决方案的一体化。
以上4个方面的要求,使得面向大型飞机零件数控加工技术及装备的发展与应用呈现出新的特点。
本文就上述前2个方面,以飞机结构零件加工过程中涉及的一些关键数控加工技术及装备为重点,对大型飞机制造中的数控技术、装备以及相关的使能支撑技术的发展进行讨论。
波音787机身部件大量采用复合材料大型飞机选料和结构特点现代大型飞机在材料选择方面呈现出新的特点和趋势。
波音系列和空客系列飞机结构材料的选用最具代表性。
铝合金(包括铝锂合金)在大型飞机结构材料中所占比例较大,但在新的机型中铝合金的用量呈现出下降趋势,即由原来占结构重量的70%~80%下降为20%左右(B787和A350),而复合材料在飞机结构中的使用量则大幅度增长,原机型复合材料用量多在11%左右,到A380复合材料用量上升到22%,而A350和B787的复合材料用量比例高达52%和60%;钛合金和高强度结构钢的用量比例也呈增加的趋势,在B787、A380结构上增加到10%以上,而在A350上则高达21%。
大型飞机结构选用材料方面呈现的主要特点和趋势是:复合材料用量大幅度增加,钛合金和钢用量也有较大增加,铝合金用量明显减少。
复合材料加工也是国外航空航天制造技术研制的重点,这是辛辛那提公司正在用金刚石镀膜刀具进行发动机部件铣削加工飞机结构零件主要有壁板、梁、框、肋、缘条、长桁和接头及骨架等,由于高性能、轻量化和高可靠性的要求,在结构方面,这些零件采用整体结构和复杂型面结构的设计大大增加,从而使飞机结构零件呈现出几何尺寸大、加工精度高、型面复杂、工艺特征多、壁厚薄、切削加工过程材料去除量大、加工变形控制难度大等特点,对数控机床性能、加工精度、变形控制和加工效率提出了很高的要求。
机身机翼等结构零件数控加工技术与装备虽然B787、A350等最新型大型客机结构中复合材料的用量在增加,但大型飞机的机身、机翼、尾翼等结构多采用铝合金板材、型材等加工,近年来预拉伸铝合金板材在飞机整体结构件中的用量越来越大;机身承力框及加强框、机翼翼梁和加强肋等部件多采用高强度铝合金和合金钢锻造毛坯,经切削加工而成。
某铝合金整体结构机翼翼盒肋板的实际零件结构尺寸为3100mm³1600mm³100mm,材料去除量达95.5%,最小壁厚接近1mm。
数控切削加工是机身机翼等结构零件的主要制造工艺方法,实际应用中对于多坐标/高速/高刚性/大功率的数控龙门铣床、床身式立铣床、立式加工中心以及专用高速蜂窝铣床和长桁缘条铣床等数控加工设备的需求量大,这些设备主要用于整体构件(如机身、机翼、尾翼上的大型整体壁板/框等),钛合金、复合材料结构件以及其他高强度合金钢的梁、肋、接头类复杂结构零件等的数控加工中。
1 高速数控加工技术以高性能数控机床及先进刀具为基础的高速数控铣削加工技术为飞机主要结构件中的铝合金零件提供了高效率、高质量数控切削加工的解决方案。
该项技术已成为航空数控加工的一个发展方向,并开始从航空制造向其他制造领域推广应用。
此类数控加工技术与装备的特点及要求可概括为:(1)采用高速主轴系统,提供尽可能高的材料去除速率(Material Removal Rate,MRR),当前应用的高速主轴,转速可达42000r/min,甚至更高。
采用内冷、静压轴承、内装式力矩电机等技术的新型大功率电主轴在提供高转速的同时还可获得大的主轴功率,如Fisher 公司的MFW-2320/30 VC HSK-A63主轴系统的功率和转速可分别达到100kW、30000r/min。
米克朗HPM600U是高速铣的代表之一(2)采用高性能的进给系统,在加工中各种走刀路径获得很高的伺服动态特性,从而缩短切削加工时间。
高性能数控机床不仅有高的主轴转速和主轴功率,同时,进给系统的高速度、高加速度、高加速度变化率产生的各坐标轴走刀运动的高动态响应,可以大大缩短进给运动的动态加减速时间,直接缩短加工时间,同时还可以保持高的表面加工质量。
具有高加速度和高加速度变化率的高性能机床与传统机床在加工同一个型腔时同走刀路径对应的进给速度变化情况。
走刀加速过程很短,机床很快进入到给定的匀速进给切削阶段,从而可以获得好的切削性能和加工效率。
走刀加速过程长,机床不能快速进入匀速进给切削。
(3)高性能切削数控技术的应用,使得飞机铝合金结构件数控切削加工时的材料去除速率高达5000~7000cm3/min,当然,这里还有机床结构优化、刀具、主轴动平衡、控制系统等的贡献。
高速加工技术也对刀具设计制造带来了挑战2 新结构数控机床技术为适应飞机结构零件工件材料与结构的数控加工方面越来越高的效率和质量要求,一些新结构、新概念的数控机床的研制开发也受到人们的关注。
2007年汉诺威的欧洲机床展览会上,DS Technologie公司展出的ECOSPEED、ECOFORCE向人们展示了新颖的专用于航空航天数控切削加工技术和装备。
ECOSPEED和ECOFORCE系列机床采用并联结构SPRINT Z3主轴头,主轴采用卧式结构布局,全系列机床可进行完全的五轴联动加工,并具有高刚性、高阻尼特性、高加速度(9.81m/s2)等特点,可采用最小量润滑、刀具内喷冷却和普通冷却液等方式进行切削加工冷却润滑,工作台最大直线工作行程可达15800mm,最大快移速度达65m/min,摆角范围±40°\u65292X摆角,回转定位速度≥80°/s,角加速度达到685°/s2。
DS Technologie公司分别针对航空结构件2种不同类型的工件材料进行了相应的开发,ECOSPEED主要应用于铝合金材料的数控切削,主轴参数可选用功率为80kW,转矩为46N²m,转速为30000r/min或功率为75kW,转矩72N²m,转速为24000r/min;ECOFORCE 主要应用于钛合金难加工材料飞机零件的数控切削,采用低速大转矩主轴,进行三轴粗加工时,主轴参数可选用功率为60kW,转矩为4000N²m,转速2000r/min,而用于五轴精加工时,主轴参数可选用功率为50kW,转矩为1100N²m,转速为5000r/min。
DS Technologie新结构数控加工中心以其独特的设计理念及新颖的结构,为具有不同材料和不同结构特点的飞机结构零件加工提供了高效的解决方案。
A320客机铝合金翼肋零件加工实例表明,采用这种新结构的机床,可将零件加工时间由传统数控机床加工时的9.5h缩短到2.05h。
可以预见,未来还将出现一些专门针对大型飞机结构零件高效优质数控加工设计的新概念、新结构的机床。
3 高效专用数控机床及相关技术为了进一步提高加工效率,多主轴头、立卧转换(翻板)工作台、大型卧式主轴布局、柔性夹具等结构已成为大型飞机结构件加工用数控机床的重要特点。
多主轴头机床一般采用大型龙门结构,在一台机床上设计有2个甚至2个以上相同的主轴头,在同一个工作台上,多个主轴头可以同时加工多个相同的结构零件,从而使数控切削加工时间成倍缩短。
德国Zimmermann FZ42在欧洲VOLVO发动机工厂中的应用立卧转换(翻板)工作台是为方便飞机大型结构零件定位、装夹和切削过程排屑设计的一种多工作台形式,在使用时,先以立式工作台的形式进行零件的定位和装夹,零件定位装夹好以后,再将工作台自动转换到卧式加工位置,从而便于切削加工过程中大量切屑的快速排除。
立卧转换工作台多采用双工作台形式以节省工件装备时间,提高机床主轴的利用率。
大型卧式主轴布局主要是针对飞机大型结构零件尺寸大、加工中材料去除量大的特点设计的。
卧式主轴切削时形成的大量切屑,可以依靠自重自动掉落,避免了立式切削时必须采用人工或辅助工具清除切屑的麻烦。
柔性夹具采用数控多点可调支撑、真空吸咐或机械夹头的方式,实现对不同形状的大型结构件在机床上的柔性、快速的定位和装夹,非常适合单件或小批量大型结构零件以及大型复合材料构件数控加工时的装夹。
起落架零件数控加工技术与装备大型飞机起落架零件大多采用钛合金或超高强度钢锻件毛坯,如B777的主起落架载重梁采用Ti-10V-2Fe-3Al合金锻件,重3175kg,投影面积1.23m2;B747主起落架梁采用Ti-6Al-4V合金锻件,重1290kg,投影面积4m2,长6m,是迄今为止最长的钛合金锻件。
由于起落架零件材料的比强度高、弹性模量小、热导率低,采用锻件毛坯进行切削加工的方式,切削性差。
在零件几何结构方面,起落架零件的内外圆表面、凸台、孔等均需要进行数控加工,且几何和形位精度要求高,对数控机床精度、刚性的要求以及对刀具的要求都非常高,同时要求在一台数控机床上可实现多功能的复合加工,如车、铣、钻、镗等多种切削加工,以达到一次装夹完成全部加工的目的。
此外,采用车铣方式加工回转表面,还可获得变单刀连续车削为多刀非连续铣削,从而降低切削力,改善刀具散热条件,减小刀具磨损。
因此,高刚性多功能的复合加工数控技术及装备、新型涂层刀具材料及刀具结构设计已成为起落架零件切削加工的重要关注点。
高效数控加工使能技术如上所述,大型飞机制造中的数控加工过程,关键在于优质和高效。
真正地实现高效数控加工,机床、刀具等“硬件”条件是基础,同时,支持高效加工的“软件”使能技术和工具也必不可少,主要包括:高效智能化的数控程编系统、数控加工过程运动仿真软件、数控加工过程力学仿真软件、虚拟数控加工系统和数控加工切削参数数据库等。
数控程编系统和加工运动仿真软件已有较长的发展历史,并有大量成熟和商品化的工具软件,如CATIA、UG、Pro/E、Vericut、Delcam、EdgeCAM等。
数控切削加工过程中,“机床、刀具、工件”三者构成了一个具有动力学特性的加工工艺系统。
在数控加工过程中,除了各个控制轴坐标运动形成刀具与工件之间的相对几何运动关系之外,该加工工艺系统还会产生切削力变化,切削热、工件和刀具变形、振动等力学特性的变化。
这些变化直接影响到数控加工过程尤其是高速加工过程的质量、效率和成本。
因此,对数控加工过程特别是对高速加工进行力学仿真,获得不同切削参数条件下的动态切削力、刀具和工件的变形与振动状态、颤振稳定域、切削温度变化、已加工表面形貌等,可以为切削参数和刀具的选择和优化提供可靠依据。