物料需求计划单
物料需求计划(MRP)
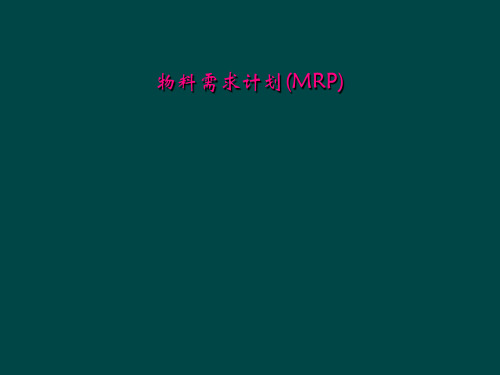
毛需求量
30
20
30
20
30
30
30
30
20
计划接受
量
40
预计可用
库存
5
15
5
5
5
5
5
5
5
5
30
30
20
计划产出 量
10
30
20
30
30
30
30
20
计划投入 量
10
30
20
30
30
30
30
20
思考题
1. 什么是MRP?它主要是解决什么问题? 2. 生成MRP一般有哪些方式?各有什么不同? 3. 请画出MRP的计算流程图? 4. MRP子系统与哪些子系统有关系?并绘图表示。 5. MRP的输出报表应有哪些? 6. 试着列举一个运算MRP的计算例子。
6.2 计算模型
A物料在X产品结构中的层次不同,则加工顺序就不同,因为产品是从最底层开始加工的,最后才组装 最上层的产品。A物料的MRP计算真正是从X产品的第二层才开始的。
0层
1层
A
X
B
C
2层
A
D
图6.4 物料A的MRP计算顺序示意图
6.2 计算模型
3. 确认MRP 生成MRP后,进行能力计划运算,要通过能力需求计划校验其可执行性
物料需求计划(MRP)
第6章 物料需求计划(MRP)
物料需求计划(Material Requirement Planning,简称为 MRP),与主生产计划一样处于ERP系 统计划层次的计划层,由MPS驱动MRP的运行。
6.1 定义与作用
物料需求计划是对主生产计划的各个项目所需的全部制造件和全部采购件的网络支持计划和时间 进度计划。主要解决以下五个问题:
物料需求计划

3、现有库存量(POH)
其概念与MPS中的概念相同,指每周需求被满足之后手头仍有的库存量。该记录随着每周 进货或出货的情况而更新,未来各周的POH则可计算的出
4、计划订货入库量 (PR)
含义是,计划订货或生产、但订单尚未发出的订货量。这个量的意义是要保持POH的量不 低于安全库存(在MPS中未考虑安全库存,保持POH非负即可)。对于某些不需要安全库
某办公家具公司,其两种主要产品(即企业要出厂的最终产品)是办公用椅A和B,其需 求大致稳定:产品A每周需30个,产品B每周需20个。这两种产品都需要用到一种支架部
件C。因此,对C的平均需求量是每周50个。A和B的装配期是1周
如右图示,在这种格式中,左上方通常要标出产品名称及其性质(如右图中,表明C是支 架部件),右上方表示计划因子,通常包括三项:生产批量、生产周期和安全库存量。 在本例中,C的批量是230个,生产周期为2周,安全库存量为50个。这些计划因子的量都 需要预先选定。当这些值发生变化以后,管理人员必须及时更新库存记录。下面首先来
存的中间物料,则如同MPS,其意义是要保持POH非负
在库存记录中所表示的PR量应包括这两种情况: 1)在POH出现短缺(或为负值或小于安全库存量)的当周制订一个PR量,其值的大小应是POH大于等于安全库存 2)继续计算其后各周的POH,当又出现短缺时,制订下一个PR量
5、计划发出订货量 (plannedorderreleas
基本计算模式
物料需求计划(MRP)的制定需要三个关键信息:MPS、BOM、库存记录
MPS
主生产计划
BOM
物料清单
库存记录
在MRP的制定过程中,库存记录的计算方法构成了MRP的基本计算模型
物料需求计划清单及其运算

工业工程本科课程设计〔论文〕学院〔系〕:专业:学生姓名:聂开政学号:指导教师:评阅教师:完成日期:目录一、课程设计任务书4二、物料需求定义5三、物料需求的特点5四、制定物料需求计划步骤61、绘出产品结构树72、计算第零层级物料X、Y、Z83、计算第一层级物料A94、计算第二层级物料B95、计算第三层级物料C106、计算第三层级物料D11六、物资需求计划实现的目标13七、课程设计总结13一、课程设计任务书产品物料清单如表1所示,各产品未来10周主生产计划如表2所示。
物料的提前期、现有库存量、安全库存量和已定未交量如表3所示。
制定未来10周详细的物料需求计划。
二、物料需求定义物资需求计划即〔Material Requirement Planning,MRP〕是指根据产品结构各层次物品的从属和数量关系,以每个物品为计划对象,以完工时期为时间基准倒排计划,按提前期长短区别各个物品下达计划时间的先后顺序,是一种工业制造企业物资计划管理模式。
MRP是根据市场需求预测和顾客订单制定产品的生产计划,然后基于产品生成进度计划,组成产品的材料结构表和库存状况,通过计算机计算所需物资的需求量和需求时间,从而确定材料的加工进度和订货日程的一种实用技术。
三、物料需求的特点1.需求的相关性:在流通企业中,各种需求往往是独立的。
而在生产系统中,需求具有相关性。
例如,根据订单确定了所需产品的数量之后,由新产品结构文件BOM即可推算出各种零部件和原材料的数量,这种根据逻辑关系推算出来的物料数量称为相关需求。
不但品种数量有相关性,需求时间与生产工艺过程的决定也是相关的。
2.需求确实定性:MRP的需求都是根据主产进度计划、产品结构文件和库存文件准确计算出来的,品种、数量和需求时间都有严格要求,不可改变。
3.计划的复杂性:MRP要根据主产品的生产计划、产品结构文件、库存文件、生产时间和采购时间,把主产品的所有零部件需要数量,时间,先后关系等准确计算出来.当产品结构复杂,零部件数量特别多时,其计算工作量非常庞大,人力根本不能胜任,必须依靠计算机实施这项工程。
物料需求计划例子

物料需求计划例子篇一:某工厂制作物料需求计划的案例16、某工厂制作物料需求计划的案例要生产成品就会有物料需求,其需求可以按照下面步骤进行:(1)分为季、月、周计划建立生产计划表。
计划表内应有生产单号码、品名、数量、生产日期等内容。
(2)计算标准用量将生产计划表内各品名、使用物料分析表,按照该品名的材料(BOM)的标准用料量进行备料。
(标准部门用料量×计划生产量)×(1+设定标准不良率)=标准用量。
也可以说生产某一产品的某项材料,生产部门按照生产计划的生产数所需要的材料标准领料。
(3)查库存数及调查该项材料,查出现有库存数及应发出还未发出的数量。
库存数-应发数≥标准需求,则表示此一材料,生产分析这张订单没问题,并记入物料分析表内。
库存数-应发数<标准需求,其差数要提出申购。
(4)查订购方式。
从材料目录表内查出此材料是存量管制的方式,还是按照订单的方式订购。
假如此材料属于按照“存量订购”则此材料按照存量订购的方式订购。
如果是按照订单购材料,则进入下步骤,提出申购单。
(5)材料采购采购按照申购单内的材料内容、数量及所要求日期,向供应商提出订购单,并按照申购者的要求,排定进货时间及数量,以配合已定的生产计划时间。
(6)进料控制采购人员及物料控制(MC)人员按照进料时间控制。
遇有迟延状况时最迟应于三天前通知生管,以方便变更生产计划。
(7)收料仓库管理部门使用收料单收料。
(8)生产备料仓库按照生产计划或备料单的日期,于领用前一天准备好所需的物料篇二:物料需求计划及其运算工业工程本科课程设计(论文)学院(系):专业:学生姓名:聂开政学号:指导教师:评阅教师:完成日期:目录一、课程设计任务书 (3)二、物料需求定义................................................. (3)三、物料需求的特点 (4)四、制定物料需求计划步骤 (4)1、绘出产品结构树 (5)2、计算第零层级物料X、Y、Z (6)3、计算第一层级物料A (7)4、计算第二层级物料B (7)5、计算第三层级物料C (8)6、计算第三层级物料D (8)六、物资需求计划实现的目标 (10)七、课程设计总结................................................. .. 10一、课程设计任务书产品物料清单如表1所示,各产品未来10周主生产计划如表2所示。
TOP GP物料需求计划

请购量 在采量 在外量 在制量 计划产量
取供给
需考虑是否属于被排除在外的单别(amri701)。 单据状态是否符合。 请购单:按asms260中设置,1、全部纳入;2、审核后纳 入;3、全部不纳入。如果纳入,取请购量-已转采购量, 如果小于0,取0。作废和结案请购单不纳入。
26
27
28
29
30
31
1
第一个时距日 第二个时距日 第三个时距日 第四个时距日 第五个时距日 第六个时距日 第七个时距日 第八个时距日
5月7日 5月8日 5月10日 5月13日 5月16日 5月19日 5月22日 5月28日
变动时距范例
50pcs
90pcs
时距设为3 时 时距设为 3天 天时
时距设为7 时 时距设为 7天 天时
纳入MDS需求 关系到apsi400中是否 参与运算。
纳入实际订单档资料 关系到销售订单是否参 与运算 纳入MDS需求与纳入实 际订单档资料不能同时 勾选。 纳入MPS计划(未开工 单)下阶料的备料需求 建议PLM料件生成下阶 料的备料需求
抓需求
纳入MRP运行的单据状态 独立需求:审核状态,开立、作废和结案状态不纳入。 销售订单:非合约订单,取未交量。单据需审核。开立、作 废、结案状态不纳入。 工单备料:工单开立即纳入,取应发量-已发量,如果小于0, 不纳入。作废、结案状态不纳入。试产工单不纳入。
abmi600 abmi710 abmi710 abmi604
axmr410 axmt800 axmp410 apmt540 apmt910 apmp551 aimi103 aimi103 apmt420 apmp451 aimi104 aimi104 asfp400 asfp401 asfi301
七、物料需求计划

第七讲物料需求计划1、物料需求计划的基本原理用料预算方法□用料预算第一条常备材料:由生产管理单位依生产及保养计划定期编制"材料预算及存量基准明细表"拟订用料预算。
第二条预备材料:由生产管理单位依生产及保养计划的材料耗用基准,按科别(产品表)定期编制"材料预算及存量基准明细表"拟订用料预算,其杂务用品直接依过去实际领用数量,并考虑库存情况,拟订次月用料预算。
第三条非常备材料:订货生产的用料,由生产管理单位依生产用料基准,逐批拟订产品用料预算,其他材料直接由使用单位定期拟订用料预算。
□存量管理第四条常备材料:物料管理单位依材料预算用量,交货所需时间、需用资金、仓储容量、变质速率及危险性等因素,选用适当管理方法以"材料预算及存量基准明细表"列示各项材料的管理点,连同设定资料呈主管核准后,作为存量管理的基准,并拟"常备材料控制表"进行存量管理作业,但材料存量基准设定因素变动足以影响管理点时,物料管理单位应即修正存量管理基准。
第五条预备材料:物料管理单位应考虑材料预算用量,在精简采购、仓储成本的原则下,酌情以"材料预算及存量基准明细表"设定存量管理基准加以管理,但材料存量基准设定因素变动时,物料管理单位必须修正其存量管理基准。
第六条非常备材料:由物料管理单位依据预算用量及库存情况实施管理(管理方法由各公司自订)。
□用料差异分析第七条材料预算用量与实际用量差异超过管理基准时,依下列规定办理:(一)常备材料:物料管理单位应于每月10日前就上月实际用量与预算用量比较(内购材料用)或前三个月累计实际用量与累计预算用量比较(外购材料用)其差异率在管理基准(各公司自订)以上者,需填制"材料使用量差异分析月报表"送生产管理单位分析原因,并提出改善对策。
(二)预备材料:物料管理单位以每月或每三个月一期,于次月10日前就最近一个月或三个月累计实际用量与累计预算用量比较,其差异率在管理基准(各公司自订)以上者按科别填制"材料使用量差异分析月报表",送生产管理单位分析原因,并提出改善对策。
物料需求计划计算举例
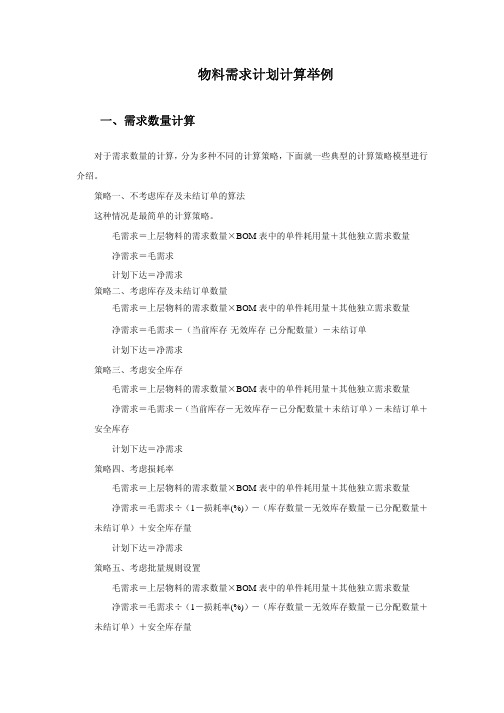
计划完工日期(调整后)=计划完工日期(调整前)+提前期余量
计划开工日期(调整后)=计划开工日期(调整前)+提前期余量
5、考虑工厂日历
如果计划开工日期和计划完工日期中间的时间段落在工厂日历的休息日,计划开工日期
和计划完工日期相应做顺延调整。
对于一些大型的企业,其组织结构可能还包括一些子公司、部门、生产车间等下级部门,
需要注意的是,如果物料的批量原则是 POQ 时,物料的订货周期(P)将影响到计划 完工日期。
2、计算物料的订货提前期 订货提前期=固定订货提前期+变动订货提前期 变动订货提前期=取大整数(变动订货提前期系数×订货批量÷变动提前期批量) 3、计算计划开工日期 计划开工日期=计划完工日期-订货提前期 物料需求计划在计算时,必须考虑工厂日历和提前期余量设置情况。 4、增加提前期余量调整
=2007 年 11 月 18 日 同时因为 2007 年 11 月 17 日和 2007 年 11 月 18 日为双休日,相应的计划开工日期再次 向前提前至工作日,计划完工日期为工作日,保持不变。 计划完工日期=2007 年 11 月 27 日 计划开工日期=2007 年 11 月 18 日-2 天
00
1
1
1
20
00
00
00
2
2
2
00
00
00
在策略二情况下,由于考虑了当前库存和未结订单的数量,塑料套的净需求发生了变化。 具体计算步骤如下:
毛需求=上层物料的需求数量×BOM 表中的单件耗用量+独立需求 =100×1×2+10 =210
净需求=毛需求-(当前库存-无效库存-已分配数量)-未结订单 =210-(10-4-3)-5 =202
=120 由于三脚架的批量增量为 120,所以本次最终的计划下达数量为 120.
物料需求计划
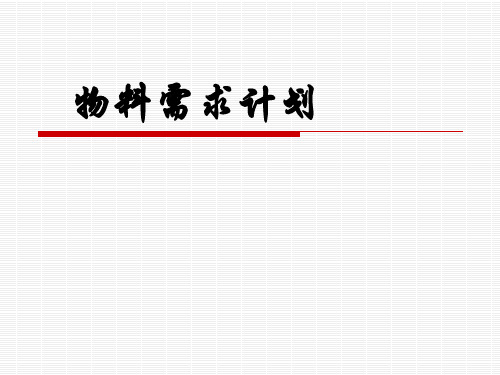
物料需求计划系统的输入输出
BOM MPS
库存文件
MRP
加工定单
采购定单
修改定单
MRP 的 逻 辑 流 程 图
市场要什么? 预测
1
潜在 客户 合同
卖什么? MPS
3 库存信息
(物料可用量)
主生产计划
2
产品信息
(物料清单) (工艺路线)
4 物料需求计划 MRP
买什么?
采购计划
做什么?
生产计划
MRP的相关概念
5
6 6
5
5
13
5
5
5
5
2
5
13
5
5
5
8 7 10
8
13 2 10
6
10 5 10
5
12 13 20
7
12 3 10
7
10 6 2
10 1
10 4
20 2
10 8
主生产计划的生产总量必须等于综合计划确 定的生产量 所确定的是最终物料项 主生产计划必须考虑企业能力、资源的约束 条件 主生产计划最终形成的计划在系统中运行前 要进行核实
O
时 段
毛 需 求 计划接收量 预计库存量 净 需 求 计划产出量 计划投入量
批量=40 现有量=10
1
2 20
9 10 11 12 10 0 10 40 0 30 10 40 40
CHEN.039 001
50 30 30 10 10 30 30 10 10
40
(2)MRP运算后生成的中间信息 毛需求:要生产什么?预测和订单组合(不是简单相加) 计划接收量:前期在制,也可理解为正在途中即将到达的物 料。 预计可用库存:已有了什么?即每个时区的期末库存余量 预计可用库存=前一时区末的可用库存 +本时区计划接收量-本 时区毛需求 +本时区计划产出量 净需求:还缺什么? 净需求=本时区毛需求-(前时区期末的可用库存+本时区计划 接收量) 计划产出量:为了满足净需求应生产量(考虑批量) 计划投入量:什么时间下达订单即投入生产或订货(考虑提 前期、废品率 )
物料需求计划【共49张PPT】
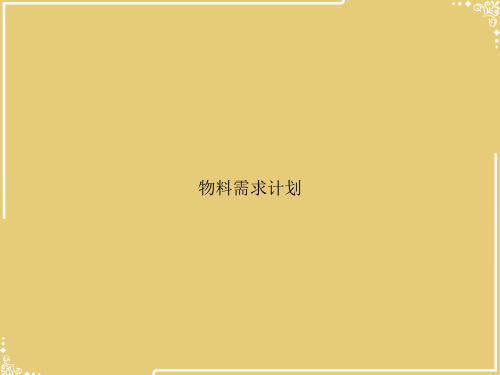
采购供应计划
每一项加工件的建议计划 • 需求数量 • 开始日期和完工日期
每一项采购件的建议计划 • 需求数量 • 订货日期和到货日期
MRP 的基本逻辑
四、MRPII的输入信息
MRP的输入有3个部分: • 主生产计划(产品出产计划MPS)
• 物料清单(产品结构文件,BOM) • 库存状态文件
物料清单(产品结构文件,BOM)
净需求=总需求—(预计到货量+现有量)+安全库存 于是,人们便思考:怎样才能在需要的时间,按需要的数量得到真正需用的物料?从而消除盲目性,实现低库存与高服务水平并存。 ERP是在MRP基础上发展起来的,以供应链思想为基础,融现代管理思想为一身,以现代化的计算机及网络通信技术为运行平台,集企业的各项管理功能为一身,并能对供应链上所有资源进行有效控 制的计算机管理系统。
件;要加工各种零件,就必须提前一定时间准备所需
数量的各种毛坯,直至提前一定时间准备各种原材料 。
其主要功能及运算依据为:
处 理 的 问 题 1. 生 产 什 么 ?生 产 多 少 ? 2. 要 用 到 什 么 ? 3. 已 具 备 什 么 ? 4. 还 缺 什 么 ? 何 时 需 要 ?
所 需 信 息 1. 切 实 可 行 的 主 生 产 计 划 ( M PS) 2. 准 确 的 物 料 清 单 ( BOM表 ) 3. 准 确 的 物 料 库 存 数 据 4. M RP的 计 算 结 果 ( 生 产 计 划 和 采 购 计 划 )
物料需求计划
本章学习目标
• 物料需求计划(MRP):
– Material Requirements Planning
• 制造资源计划(MRPⅡ ):
– Manufacturing Resource Planning
物料需求计划
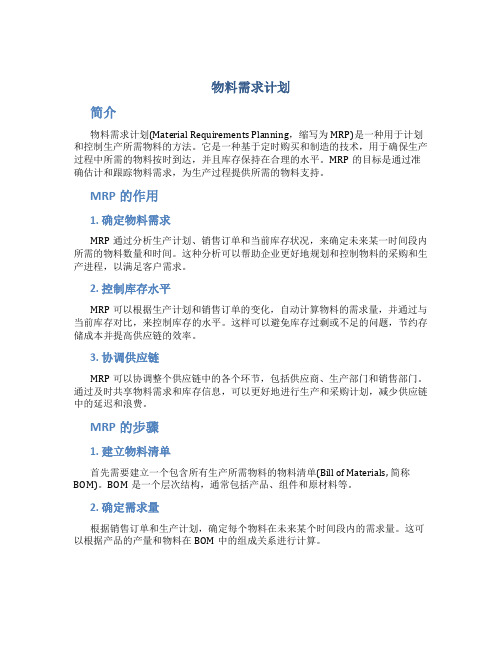
物料需求计划简介物料需求计划(Material Requirements Planning,缩写为MRP)是一种用于计划和控制生产所需物料的方法。
它是一种基于定时购买和制造的技术,用于确保生产过程中所需的物料按时到达,并且库存保持在合理的水平。
MRP的目标是通过准确估计和跟踪物料需求,为生产过程提供所需的物料支持。
MRP的作用1. 确定物料需求MRP通过分析生产计划、销售订单和当前库存状况,来确定未来某一时间段内所需的物料数量和时间。
这种分析可以帮助企业更好地规划和控制物料的采购和生产进程,以满足客户需求。
2. 控制库存水平MRP可以根据生产计划和销售订单的变化,自动计算物料的需求量,并通过与当前库存对比,来控制库存的水平。
这样可以避免库存过剩或不足的问题,节约存储成本并提高供应链的效率。
3. 协调供应链MRP可以协调整个供应链中的各个环节,包括供应商、生产部门和销售部门。
通过及时共享物料需求和库存信息,可以更好地进行生产和采购计划,减少供应链中的延迟和浪费。
MRP的步骤1. 建立物料清单首先需要建立一个包含所有生产所需物料的物料清单(Bill of Materials, 简称BOM)。
BOM是一个层次结构,通常包括产品、组件和原材料等。
2. 确定需求量根据销售订单和生产计划,确定每个物料在未来某个时间段内的需求量。
这可以根据产品的产量和物料在BOM中的组成关系进行计算。
3. 计算净需求量通过减去当前库存和已有采购订单的供应量,即可计算出每个物料的净需求量。
如果净需求量为负数,则表示库存中有过多的物料。
4. 制定采购和生产计划根据净需求量,制定物料的采购计划和生产计划。
采购计划包括物料的订购数量和交货时间,生产计划包括生产批次和交货时间。
5. 跟踪和更新根据实际生产和采购情况,不断跟踪和更新物料需求计划。
如果有变化,及时调整采购和生产计划,并与供应链中的其他环节进行沟通。
MRP的优势1. 提高准确性和可靠性MRP可以通过计算和分析数据,提高物料需求计划的准确性和可靠性。
第6章 物料需求计划(MRP)
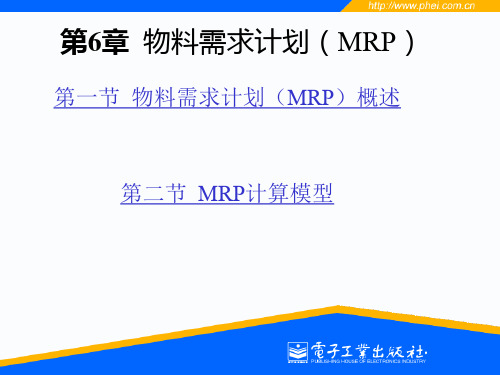
二、MRP计算步骤
• 2.物料需求计划计算具体步骤 • (1)计算物料毛需求量。考虑相关需求和低位码推算计划期全
部的毛需求。 • 项目毛需求量=项目独立需求+父项的相关需求 • 其中: • 父项的相关需求=父项的计划订单数量×项目用量因子 • (2)推算PAB初值。考虑毛需求推算特定时段的预计库存量。 • PAB初值=上期末预计可用库存量+计划接收量-毛需求量 • (3)计算净需求量。考虑安全库存推算特定时段的净需求量。 • 当PAB初值≥安全库存时,净需求=0 • 当PAB初值<安全库存时,净需求=安全库存-PAB初值
一、MRP概念及作用
• 2.MRP的基本依据 • MRP的基本依据是:① 主生产计划(
MPS);② 物料清单(BOM);③ 库存 信息。它们的逻辑流程关系如图6.1所示 。
一、MRP概念及作用
一、MRP概念及作用
• 3.MRP作用 • ① 要生产(含采购和制造)什么?生产(含采购和制造)多
少?(来自MPS) • ② 要用到什么?(根据BOM展开可知) • ③ 已经有了什么?(根据物料库存信息、即将到货的信息或
六、虚拟件
• 3.BOM中的虚拟件
• “虚拟件”最重要的作用就是简化产品结构的管理,以下用 图6.5的BOM进行说明。
• 在图6.5中,如果对A产品BOM的定义采用图6.5(a)方式, 那么,子件B、C的BOM文件定义过程会重复引用到D、E与F 物料,加大了工作量,并且数据库的存储空间也会增加。而 采用图6.5(b)的定义方式,增加一个“虚拟件”物料K,并 定义K的BOM文件,则B、C的BOM中只需要加入一个子件K ,无须重复加入子件D、E与F物料,从而达到简化BOM的目 的,特别是在多个BOM中有大量的相同子件重复出现时,这 种定义方式的优越性就更加明显。另外,如果虚拟件的子件 发生工程改变,也只影响到虚拟件这一层,不会影响此虚拟 件以上的所有父项。
物料需求计划例子

物料需求计划例子篇一:某工厂制作物料需求计划的案例16、某工厂制作物料需求计划的案例要生产成品就会有物料需求,其需求可以按照下面步骤进行:(1)分为季、月、周计划建立生产计划表。
计划表内应有生产单号码、品名、数量、生产日期等内容。
(2)计算标准用量将生产计划表内各品名、使用物料分析表,按照该品名的材料(BOM)的标准用料量进行备料。
(标准部门用料量×计划生产量)×(1+设定标准不良率)=标准用量。
也可以说生产某一产品的某项材料,生产部门按照生产计划的生产数所需要的材料标准领料。
(3)查库存数及调查该项材料,查出现有库存数及应发出还未发出的数量。
库存数-应发数≥标准需求,则表示此一材料,生产分析这张订单没问题,并记入物料分析表内。
库存数-应发数<标准需求,其差数要提出申购。
(4)查订购方式。
从材料目录表内查出此材料是存量管制的方式,还是按照订单的方式订购。
假如此材料属于按照“存量订购”则此材料按照存量订购的方式订购。
如果是按照订单购材料,则进入下步骤,提出申购单。
(5)材料采购采购按照申购单内的材料内容、数量及所要求日期,向供应商提出订购单,并按照申购者的要求,排定进货时间及数量,以配合已定的生产计划时间。
(6)进料控制采购人员及物料控制(MC)人员按照进料时间控制。
遇有迟延状况时最迟应于三天前通知生管,以方便变更生产计划。
(7)收料仓库管理部门使用收料单收料。
(8)生产备料仓库按照生产计划或备料单的日期,于领用前一天准备好所需的物料篇二:物料需求计划及其运算工业工程本科课程设计(论文)学院(系):专业:学生姓名:聂开政学号:指导教师:评阅教师:完成日期:目录一、课程设计任务书 (3)二、物料需求定义................................................. (3)三、物料需求的特点 (4)四、制定物料需求计划步骤 (4)1、绘出产品结构树 (5)2、计算第零层级物料X、Y、Z (6)3、计算第一层级物料A (7)4、计算第二层级物料B (7)5、计算第三层级物料C (8)6、计算第三层级物料D (8)六、物资需求计划实现的目标 (10)七、课程设计总结................................................. .. 10一、课程设计任务书产品物料清单如表1所示,各产品未来10周主生产计划如表2所示。
物料需求计划

物料需求计划物料需求计划(Material Requirements Planning,简称MRP)是一种用于确定生产所需原材料和零部件数量的计划方法。
通过MRP系统,企业可以根据生产计划和销售订单,精确计算出所需的物料数量和采购时间,从而保证生产计划的顺利进行。
首先,物料需求计划的制定需要充分考虑市场需求和生产能力。
根据市场需求预测,结合企业的生产能力和资源情况,确定生产计划和销售订单。
在制定物料需求计划时,需要充分了解生产工艺和工序,明确每个物料在生产过程中的使用数量和时间,以便精确计算物料需求量。
其次,物料需求计划的制定需要充分考虑供应商的情况。
在确定物料需求计划时,需要与供应商进行充分沟通,了解供应商的生产能力、交货周期和库存情况,以便合理安排采购时间和数量。
同时,需要建立稳定的供应链关系,确保供应商能够及时提供所需的物料。
另外,物料需求计划的制定需要充分考虑库存管理和成本控制。
在确定物料需求计划时,需要综合考虑企业的库存情况和资金状况,避免因过多库存或者采购过多而造成资金占用过多的情况。
同时,需要合理安排采购时间和数量,以便降低采购成本和库存成本,提高资金利用效率。
最后,物料需求计划的执行需要进行及时跟踪和调整。
在执行物料需求计划时,需要及时跟踪物料的采购和使用情况,确保物料的及时供应和合理使用。
同时,需要根据实际情况对物料需求计划进行调整,及时应对市场变化和生产情况,保证生产计划的顺利进行。
综上所述,物料需求计划的制定和执行对企业的生产计划和供应链管理至关重要。
通过合理制定物料需求计划,企业可以有效控制物料采购成本和库存成本,提高生产效率和资金利用效率,从而保证生产计划的顺利进行,满足市场需求,提高企业的竞争力。
zpp011物料需求计划分析

zpp011物料需求计划分析总则1.1.制定目的标准物料分析作业,制定计算物料需求数量、交期的作业流程,使之有章可循。
1.2.适用范围本公司用于产品生产使用的原物料的分析,并提出需求方案的作业。
1.3.权责单位1)生管部负责本规章制定、修改、废止之起草工作。
2)2)总经理负责本规章制定、修改、废止之核准。
2.各部门工作职责2.1.配合部门1)业务部提供销售方案、客户订单资讯。
2)资材部提供成品、半成品、原物料库存状况报表。
3)生管部提供生产方案。
4)技术部提供产品用料明细表。
5)采购部提供采购前置期、经济订购量、最小订购量。
2.2.责任部门生管部物控人员为用料分析之责任人员,负责制订物料需求方案。
3.物料需求方案步骤3.1.决定产品总需求量业务部决定产品总需求量。
总需求量一般由三个来源整合而成:1)某期间(如一个月或一季度)的实际订单量。
2)该期间的预测订单量。
3)管理者决策改变前述数量(如为平衡淡旺季或调整产品线需要)。
3.2.决定产品实际需求量根据3.1获得的总需求量,再依据该产品的成品存量状况予以调整,即得:实际需求量=总需求量-库存数量。
一般由业务部或生管部确认。
3.3.确定生产方案生管部依实际需求量确定生产方案,一般需做下述工作:1)产能负荷分析。
2)产销平衡。
3)中日程生产方案与细部生产方案。
3.4.分解出物料清单生管部物控人员负责物料清单的分析。
物料需求量=某期间之产品实际需求量*每一产品使用该物料数量3.5.区分物料ABC项目1)物控人员根据物料状况区分ABC项目,一般作如下区分:占总金额60%~70%的物料为A类。
占总金额余下之30%~40%的物料为B类及C类物料。
2)A类物料作物料需求方案,B类、C类物料使用订货点方法采购。
物料需求计划编制流程
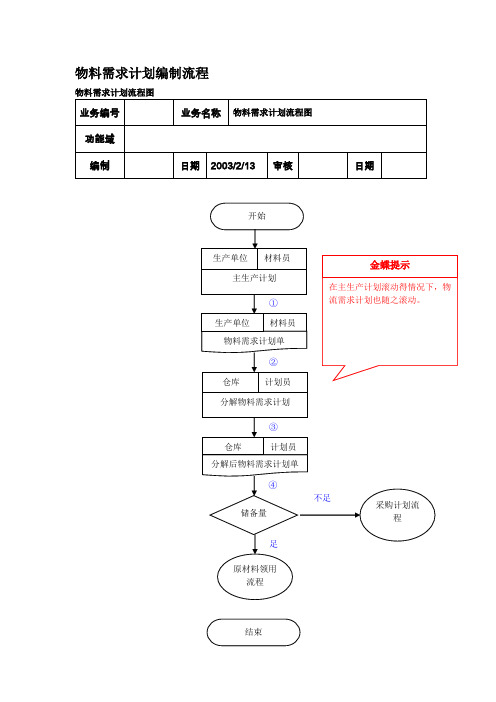
物料需求计划编制流程
物料需求计划流程图
业务编号
业务名称
物料需求计划流程图
功能域
编制
日期
2003/2/13
审核
日期
流程描述
1
生产需求部门材料员根据主生产计划填需求单
生产单位
材料员
2
仓库计划员分解物料需求计划
仓库
计划员
3
根据仓库储备量判断是否需要采购
仓库
计划员
4
进行采购或领料流程
第八讲 物料需求计划(MRP)的编制

右图示的产品BOM结构树中的
零件C分别处于产品结构树的l层
和2层,于是零件C的低位码就
是2,而其他零件的低位码数与
它们位于产品结构树的层次相同。
D(1)
精选2021版课件 LT=1
B(2) LT=2
A LT=1
C(2) LT=3
(这些数据MRP计算出结果获得)
• MRP是生产管理的核心,它将主生产计划排产的产品分 解成各自制零部件的生产计划和采购件的采购计划。
精选2021版课件
3
exit
MRP工作原理图
主生产计划 独立需求 物料清单 库存信息 其它因素
物料需求计划 (MRP)
采购定单 制造定单
精选2021版课件
4
8.2.2.1.1 主生产计划
– 零件废品系数是对订单数量的调整。零件废品系数是对项目
本身在采购或生产过程中出现的损耗而考虑的。
– 例如,产品A的零件废品系数为2%,在组装时的组装废品系
数为5%,针对该需求制定 MRP时,首先考虑2%的废品系数, 计算产品 A的计划订单数,计划订单数量要比计算的需要多2 %,如 A需求为100时,订单应为100+100×2%=102,然后 根据计划订单数量再考虑组装 A时的组装废品系数,在这种情 况下, A项目102的订单对玻璃管的毛需求量应为108(102+ 102×5%)。
C(1)
物料A 的毛需求计算表
周
1 2 3 4 5 6 7 8 9 10 11 12 13
X(lt=4)
25
30
15
Y(LT=6)
40
15
30
物料需求计划之毛需求 净需求
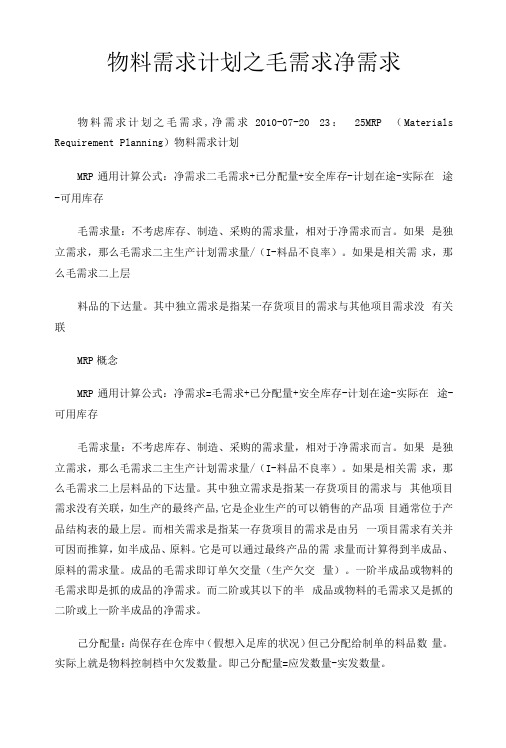
物料需求计划之毛需求净需求物料需求计划之毛需求,净需求2010-07-20 23:25MRP (Materials Requirement Planning)物料需求计划MRP通用计算公式:净需求二毛需求+已分配量+安全库存-计划在途-实际在途-可用库存毛需求量:不考虑库存、制造、采购的需求量,相对于净需求而言。
如果是独立需求,那么毛需求二主生产计划需求量/(I-料品不良率)。
如果是相关需求,那么毛需求二上层料品的下达量。
其中独立需求是指某一存货项目的需求与其他项目需求没有关联MRP概念MRP通用计算公式:净需求=毛需求+已分配量+安全库存-计划在途-实际在途-可用库存毛需求量:不考虑库存、制造、采购的需求量,相对于净需求而言。
如果是独立需求,那么毛需求二主生产计划需求量/(I-料品不良率)。
如果是相关需求,那么毛需求二上层料品的下达量。
其中独立需求是指某一存货项目的需求与其他项目需求没有关联,如生产的最终产品,它是企业生产的可以销售的产品项目通常位于产品结构表的最上层。
而相关需求是指某一存货项目的需求是由另一项目需求有关并可因而推算,如半成品、原料。
它是可以通过最终产品的需求量而计算得到半成品、原料的需求量。
成品的毛需求即订单欠交量(生产欠交量)。
一阶半成品或物料的毛需求即是抓的成品的净需求。
而二阶或其以下的半成品或物料的毛需求又是抓的二阶或上一阶半成品的净需求。
己分配量:尚保存在仓库中(假想入足库的状况)但己分配给制单的料品数量。
实际上就是物料控制档中欠发数量。
即己分配量=应发数量-实发数量。
安全库存量:为防止各种异常导致缺料从而特地额外增加的需求量,通常也可以理解为备品数量计划在途量:跑出MRP后从己生成了采购计划到生成采购单的中间过程的需采购数量实际在途量:分为采购在途和制造在途。
采购在途:己审核未结案的采购单的欠交数量。
制造在途:巳审核未结案的制造单的未入库数量可用库存量:一般是指所有仓别中可用的的良品实物库存数量(可用库存二库存量-安全存量.)但对于跑MRP时运算公式中的可用库存则是本次抓上一笔订单(制造单)的预计结存,是理论可用库存!其实假想有按日期先后顺序下的三个订单(制造单)A、B、C, A的预计结存就是B的可用库存,B的预计结存就是C的可用库存.依此类推下去就是本次跑MRP时的物料的可用库存就是用到或生产些物料的上一笔订单或制造单的预计结存量.预计结存量:预计结存量二下达量+可用库存+在途量+计划在途量-毛需求- 己分配量,是物料整体上的存量结算净需求量:依MRP计算公式计算出来的数量.逾期计划量:指在物料的需求日期之后总的的物料计划在途数量.逾期在途量:指在物料的需求日期之后的总的物料采购在途数量.下达量:指物料的实际下达量,通常就是净需求量实际下达的需求量,其数据来源为净需求量,但可能由于料品订货规则不同而和净需求量有一定的差异。
- 1、下载文档前请自行甄别文档内容的完整性,平台不提供额外的编辑、内容补充、找答案等附加服务。
- 2、"仅部分预览"的文档,不可在线预览部分如存在完整性等问题,可反馈申请退款(可完整预览的文档不适用该条件!)。
- 3、如文档侵犯您的权益,请联系客服反馈,我们会尽快为您处理(人工客服工作时间:9:00-18:30)。
物料需求计划单
定单号/物料采购计划单号: 生计填写计划 零部件名称 料 号 计划订 购数量 单位 计划到 货日期 计划到 货数量 客户定单号: 产品名称: 采购填写确认 计划到 货日期 采购定 单号
表单编号:QM-PU-405
下单日期: 仓库填写
①
供应商名 称
实际收 货日期
实际收货 数量
签 字
生 计 联 ② 采 购 联 ③ 仓 库 联
生
计:
采 购:
仓 库:
上海埃海迪机械有限公司
物料需求计划单
定单号/物料采购计划单号: 生计填写计划 零部件名称 料 号 计划订 购数量 单位 计划到 货日期 计划到 货数量 客户定单号: 产品名称: 采购填写确认 计划到 货日期 采购定 单号
表单编号:QM-PU-405 Nhomakorabea下单日期: 仓库填写
①
供应商名 称
实际收 货日期
实际收货 数量
签 字
生 计 联 ② 采 购 联 ③ 仓 库 联
生
计:
采 购:
仓 库: