塑胶射出成型的参数设定
射出工艺设定.

度
時
間
在噴嘴前端 蒸發的樹脂, 於通過射出 口時,降低 射出速度, 則可防止因 磨擦熱而産 生的燃燒及 銀條
多段射出的理念及應用
壓力
降低原圖 的成型品 之殘留應 力可使品 質較優良
壓
力 時 間
•冷卻凝固時, 保壓壓力下 降,防止過 度充填 •殘留應力減 低,品質向 上 •變形、熔合 線防止
多段射出的理念及應用
射出工藝條件設定
目
o 射出工艺主要参数说明 o 制程参数设定要领 o 多段射出五大要素说明 o 多段射出塑料流动原理
录
o 射出成型工艺条件设定的原则
o CDC-2000电脑界面的工艺条件设定
o 开锁模及顶出部分的参数设定原则
o 射出界面的设定
o 新产品试模试作步骤
射出工艺条件设定原则
条件设定三观念
多段射出的理念及應用
速度
減少成形 時間高速 射出
速 度
時 間
ห้องสมุดไป่ตู้
提高射出 速度,使 模變形以 防止偏內, 射出速度 提高,能 防止過刺
多段射出的理念及應用
速度
小的開模 力生産大 度 的産品 速
正確控制 保壓切換 的位置和 防止毛邊 發生
時
間
多段射出的理念及應用
速度
不良率的 速 減低 度 時 間
射出工艺品主要参数说明
合模參數
锁模力 F
在注射充模阶段和保压补缩阶段,模腔压力要产生使模具分 开的胀模力。
F=Am· Pv/1000
Am:模穴投影面积cm2 Pv:充填压力 kg/cm2
Pv的选择: 一般塑性材料150~350kg/cm2,流动性良好的取较 低值,流动性不佳取较高值; 工艺锁模力必须小于注塑机的额定锁模力,一般 取0.8~0.9倍的额定锁模力
射出成型参数设定方法

射出成型參數設定方法※成型前的物料干燥成型加工前,塑胶必须被充分的干燥。
含有水分的材料进入模腔后,会使制件的表面出现银绦状的瑕斑,甚至会在高温时发生加水分解的现象,致使材质劣化。
因此在成型加工前一定要对材料进行预处理,使得材料能保持合适的水分。
以下为几种塑料的烘料条件及成型时所能允许的适当水分:※模温的设定⑴模温影响成型周期及成形品质,在实际操作当中是由使用材质的最低适当模温开始设定,然后根据品质状况来适当调高。
⑵正确的说法,模温是指在成形被进行时的模腔表面的温度,在模具设计及成形工程的条件设定上,重要的是不仅维持适当的温度,还要能让其均匀的分布。
⑶不均匀的模温分布,会导致不均匀的收缩和内应力,因而使成型口易发生变形和翘曲。
⑷提高模温可获得以下效果;①加成形品结晶度及较均匀的结构。
②使成型收缩较充分,后收缩减小。
③提高成型品的强度和耐热性。
④减少内应力残留、分子配向及变形。
⑤减少充填时的流动阴抗,降低压力损失。
⑥使成形品外观较具光泽及良好。
⑦增加成型品发生毛边的机会。
⑧增加近浇口部位和减少远浇口部位凹陷的机会。
⑨减少结合线明显的程度⑩增加冷却时间。
※计量及可塑化⑴在成型加工法,射出量的控制(计量)以及塑料的均匀熔融(可塑化)是由射出机的可塑化机构(Plasticating unit来担任的①加热筒温度(Barrel Temperature)虽然塑料的熔融,大约有60~85%是因为螺杆的旋转所产生的热能,但是塑料的熔融状态仍然大受加热筒温度的影响,尤以靠近喷嘴前区的温度--前区的温度过高时易发生滴料及取出制件时牵丝的现象。
以下表格为几种塑料的适当料温、模温及成型收缩率等。
②螺杆转速(screw speed)A.塑料的熔融,大体是因螺杆的旋转所产生的热量,因此螺杆转速太快,则有下列影响:a.塑料的热分解。
b.玻纤(加纤塑料)减短。
c.螺杆或加热筒磨损加快。
B.转速的设定,可以其圆周速(circumferen-tial screw speed)的大小来衡量:圆周速=n(转速)*d(直径)*π(圆周率)通常,低粘度热安定性良好的塑料,其螺杆杆旋转的圆周速约可设定到1m/s上下,但热安定性差的塑料,则应低到0.1左右。
塑胶射出成型

收缩下陷 收缩下陷是成型品表面呈现凹陷的现象,主要原因是 熔融材料冷却固化时的体积收缩所致。收缩下陷易发生 于成型品肉厚较厚部位、肋、凸毂的背面、注道的背面 等肉不均的部份。因此为了防止收缩下陷,基本上,成 型品的设计要适切。 收缩下陷是成型品收缩所致,易见于PE、PP、PA等 成型收缩率大于结晶性塑料材料。反之,以玻璃纤维强 化的塑料或充填无机质的塑料材料之成型收缩率甚少, 故其收缩下陷可减至最小。
19
流痕 流痕是熔融材料流动的痕迹,以浇口为中心而呈现的 条纹模样。 流痕是最初流入成型空间(模穴)内的材料冷却过快,而 与其后流入的材料间形成界线所致。
银白纹 银条是在成型品表面或表面附近,沿材料流动方向, 呈现的银白色条纹。
20
烧焦 一般所谓的烧焦,包括成型品表面因材料遇热所致的 变色及成型品的锐角部位或谷部、肋的前端等材料焦黑 的现象。 烧焦是滞留在模穴内的空气,在熔融材料进入时未能 迅速排出,被压缩而显著升温,再将材料烧焦所致。 黑条 黑条是在成型品上有黑色条纹的现象,其发生的原因是 成型材料的热分解所致;常见于热安定性不良的材料。 有效防止黑条发生的对策是防止加热缸内的材料温度过 高,减慢射出速度
13
毛边 熔融材料流入分模面或侧向滑板活动间隙时,会发生毛 边。 发生毛边的原因,基本上除了射出机对成型品的投影 面积无充分的合模(锁模)力之外,大都是模具与成型材料 所致。模具配件发生间隙或配件密着性不良的原因,是模 具设计制作不当或模具配件变形及磨损。模穴的熔融材料 流动性太好时,也会造成毛边,防止的方法是降低模具温 度、材料温度、射出压力及射出速度,但必须配合前项充 填不足问题,否则可能造成解决毛边问题而造成充填不足 的现象发生。
翘曲、扭曲 翘曲、弯曲都是从模具取出的成型品产生之变形,平 行边变形者称为翘曲。对角线方向的变形称为扭曲。 这些变形为成型时的各种内应力所致,原因大别如下: (1)脱摸时的内部应力所致。 (2)模具温度控制不充分或不均匀所致。 (3)材料或填充料的流动配向所致。 (4)成型条件不适当所致。 (5)成型品形状,肉厚等所致。
塑胶射出成型产品设计要领讲义

T
1998/4/30
塑膠射出成型產品設計要領
孔洞(Holes)
孔洞設計要項
裝配、組合 裝飾、通風
孔至孔及孔至 側壁之距離
d 2d
3d
孔洞附近需加 以補強
1998/4/30
塑膠射出成型產品設計要領
孔洞(Holes)
孔洞設計要項
對靠孔洞採不 同孔徑
d+0.5 d
盲孔附近壁厚
均一
L<2D
D
1998/4/30
塑膠射出成型產品設計要領
凸轂(Bosses)
凸轂設計通則
孔洞補強 裝配嵌合 局部增高
H D
d
W
D=diameter T=thickness L<2D better design L>2D add rib or gussets W=0.6-0.7T
H=3D d = not so close to the side
塑膠射出成型產品設計要領
組配(Assembly)
融接法 (Welding)
接合設計 振動破壞
1998/4/30
塑膠射出成型產品設計要領
結論
1998/4/30
SPP
檢驗品質
LKK
製造品質
CKS
設計品質
肉厚均勻 產模融合 看問學
塑膠射出成型產品設計要領
树立质量法制观念、提高全员质量意 识。20. 10.2920 .10.29 Thursday , October 29, 2020
专注今天,好好努力,剩下的交给时 间。20. 10.2920 .10.291 8:2818:28:311 8:28:31 Oct-20
牢记安全之责,善谋安全之策,力务 安全之 实。202 0年10 月29日 星期四6 时28分 31秒T hursday , October 29, 2020
注塑成型工艺参数说明
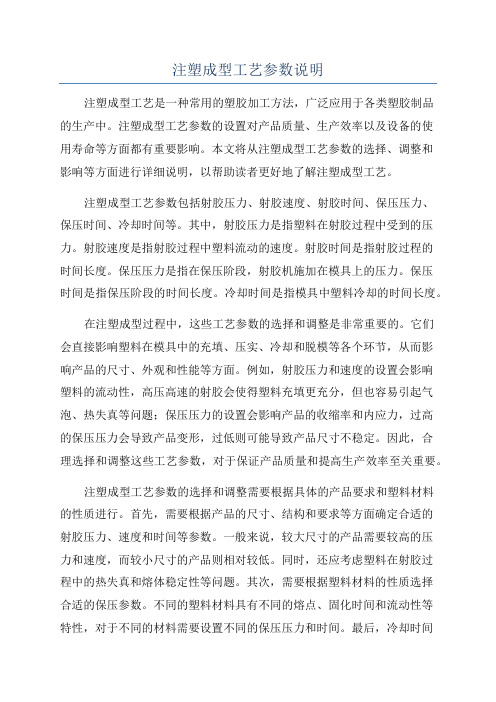
注塑成型工艺参数说明注塑成型工艺是一种常用的塑胶加工方法,广泛应用于各类塑胶制品的生产中。
注塑成型工艺参数的设置对产品质量、生产效率以及设备的使用寿命等方面都有重要影响。
本文将从注塑成型工艺参数的选择、调整和影响等方面进行详细说明,以帮助读者更好地了解注塑成型工艺。
注塑成型工艺参数包括射胶压力、射胶速度、射胶时间、保压压力、保压时间、冷却时间等。
其中,射胶压力是指塑料在射胶过程中受到的压力。
射胶速度是指射胶过程中塑料流动的速度。
射胶时间是指射胶过程的时间长度。
保压压力是指在保压阶段,射胶机施加在模具上的压力。
保压时间是指保压阶段的时间长度。
冷却时间是指模具中塑料冷却的时间长度。
在注塑成型过程中,这些工艺参数的选择和调整是非常重要的。
它们会直接影响塑料在模具中的充填、压实、冷却和脱模等各个环节,从而影响产品的尺寸、外观和性能等方面。
例如,射胶压力和速度的设置会影响塑料的流动性,高压高速的射胶会使得塑料充填更充分,但也容易引起气泡、热失真等问题;保压压力的设置会影响产品的收缩率和内应力,过高的保压压力会导致产品变形,过低则可能导致产品尺寸不稳定。
因此,合理选择和调整这些工艺参数,对于保证产品质量和提高生产效率至关重要。
注塑成型工艺参数的选择和调整需要根据具体的产品要求和塑料材料的性质进行。
首先,需要根据产品的尺寸、结构和要求等方面确定合适的射胶压力、速度和时间等参数。
一般来说,较大尺寸的产品需要较高的压力和速度,而较小尺寸的产品则相对较低。
同时,还应考虑塑料在射胶过程中的热失真和熔体稳定性等问题。
其次,需要根据塑料材料的性质选择合适的保压参数。
不同的塑料材料具有不同的熔点、固化时间和流动性等特性,对于不同的材料需要设置不同的保压压力和时间。
最后,冷却时间的设置也是十分重要的,它会直接影响产品的冷却速度和收缩率等方面。
冷却时间过短会导致产品尺寸不稳定,过长则会降低生产效率。
总之,注塑成型工艺参数的选择和调整对于产品质量和生产效率具有重要影响。
塑胶射出成型教程第一章预备参数设定(精)

塑胶射出成型教程第一章预备参数设定(1)材料干燥作业确认(2 模温,加热筒温度正确适当设定(3)开闭模及顶出设定确认(4)射出压力:无特殊原因先一段中低速设定(5)保压先设定为0(6)射出速度:无特殊原因先一段中低速设定(7)螺杆转速:一般设定为80RPM (8)背压:以0开始设定加至螺杆无法转动再提前为优先标准设定(9)射出时间:稍短设定(10)冷却时间:稍长设定(11)保压切换位置,计量长度及松退行程设定注意要点:1 先做短射品(有些产品第一次需注饱模,预防粘母模),慢慢调至饱模 2 顶出设定需严谨 3 螺杆参数设定要谨慎温度(1)料筒温度:与塑料的特性有关,最适合的温度范围在粘流態温度和热分解温度之间。
温度过高,冷却时间长,塑料易热分解;温度过低,流动性不好。
温度分布从料斗一侧(后端)起至喷嘴(前端)逐步升高。
以使塑料温度平稳上升达到塑料均匀塑化。
(2)喷嘴温度:一般略低于料筒的最高温度,以防止熔料在喷嘴处发生“流涎”现象。
喷嘴温度也不能过低,否则会造成熔料早凝将喷嘴堵死(3NH1喷嘴温度以不溢料为原则尽可能高温(4)H1主料温度第一段以不变黄为原则尽可能高温 (5H2-H3主料温度第2,3段温度按阶梯式下降(6)H4料温度后段以不发生搅碎声为原则尽可能低温第二章 . 多级注塑由于浇道系统及各部位几何形状不同,不同部位对于充模熔体的流动速度,压力提出要求,否则就要影响熔体在这一部位的流动性能或高分子的结晶定向作用,以及制品的表现质量。
在一个注射过程中,螺杆向模具推进熔体时,要求实现在不同位置上有不同注射速度和不同注射压力等等工艺参数的控制,这种注射过程称为多级注塑。
1 注射压力:是指螺杆头部对塑料熔体所施加的压力。
其作用是克服塑料熔体从料筒流向型腔的流动阻力。
塑化的塑料在螺杆的推挤作用下至料筒前端,经过喷嘴及模具的胶注系统进入模具型腔。
给予熔体一定的充填速率以及对熔体进行压制。
目前,大多数是注射速度进行多级控制注塑机,通常可以把注射全部行程分1个或1~5个区域,并把各区域设置成各自不同的适当注射速度。
射出成型条件的参数控制
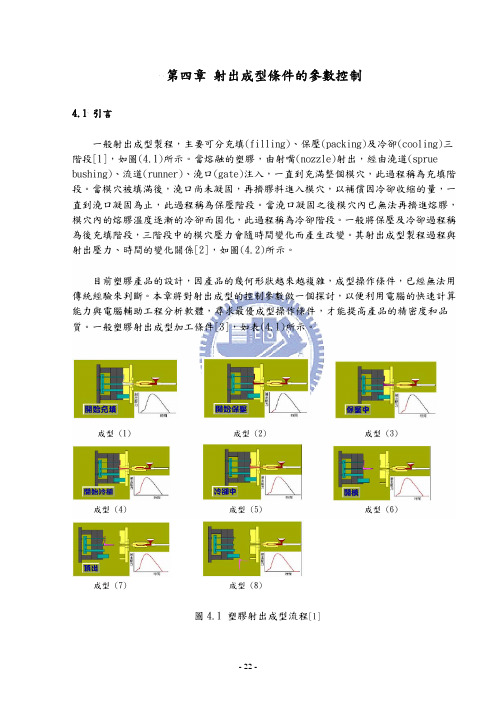
25 成品拔模角度
70~150rpm
26
行程效率
13
射膠量
採用理論射膠量
27
機台大小
的 70 % ~ 80 %
成型條件 射嘴 203~295℃ 前段 220~295℃ 中段 210~290℃ 後段 180~210℃
10~80℃ 30~60% 100~250kg/cm² 1.04~1.06g/cc 82~122℃ 0.4~0.8% 1.0~1.2 0.00006~0.00013/℃ 0.3~0.8% 66~113℃ 2~5 度 0.8 ~ 0.95 %
目前塑膠產品的設計,因產品的幾何形狀越來越複雜,成型操作條件,已經無法用 傳統經驗來判斷。本章將對射出成型的控制參數做一個探討,以便利用電腦的快速計算 能力與電腦輔助工程分析軟體,尋求最優成型操作條件,才能提高產品的精密度和品 質。一般塑膠射出成型加工條件[3],如表(4.1)所示。
成型 (1)
成型 (2)
佔機台料管總容量 的 50-70%
- 23 -
4.2 成型的控制參數
成型控制參數影響成品的品質,但要如何掌握成型作業的控制參數,才能讓成品的 品質符合客戶標準要求,且不需要用特別技術能力來進行作業,就可將成品順利成型。
由於射出成型條件的選擇,與實際現場認知上的不同,常見模流分析加工條件的錯 誤設定,尤其是發生在設定充填時間;而實際現場的充填時間為射出機台的輸出值,其 值除了包含充填所需的時間外,也可能包含保壓所需的時間;而模流分析的充填時間是 輸入值,與保壓時間分別設定,若直接輸入射出機台輸出的充填時間,則會造成充填時 間過長,而導致成品短射的問題;導致這個問題的主要原因在於,一般射出機台的設定 為螺桿行程控制,而充填時間只是螺桿行程結束時的輸出值。一般塑膠射出成型加工影 響品質的基本注意事項,有加工溫度、流動速度、體積收縮、冷卻速率、應力殘留、頂 出溫度等。
塑胶射出成型技术

塑胶射出成型技术塑胶射出成型技术设定注塑工艺时应考虑的塑料物性一收缩率影响热塑性塑料成型收缩的因素如下:1、塑料品种:热塑性塑料成型过程中由于存在结晶化形成的体积变化,内应力强,冻结在塑件内的残余应力大,分子取向性强等因素,因此热塑性塑料收缩率较大,收缩率范围宽、方向性明显,另外成型后的收缩、退火或调湿处理后的收缩率一般也比较大。
2、塑件特性:成型时熔融料与型腔表面接触外层立即冷却形成低密度的固态外壳。
由于塑料的导热性差,使塑件内层缓慢冷却而形成收缩大的高密度固态层。
所以壁厚、冷却慢、高密度层厚的则收缩大。
3、进料口形式、尺寸、分布这些因素直接影响料流方向、密度分布、保压补缩作用及成型时间。
4、成型条件:模具温度高,熔融料冷却慢、收缩大,尤其是结晶料因结晶度高,体积变化大,故收缩更大。
另外,保压压力及保压时间对收缩也影响较大,压力大、时间长的则收缩小但方向性大。
注塑压力高,熔融料粘度差小,层间剪切应力小,脱模后弹性回跳大,故收缩也会减小,料温高、收缩大,但方向性小。
因此在成型时调整模温、压力、注塑速度及冷却时间等诸多因素可适当改变塑件收缩情况。
二、流动性1、热塑性塑料流动性大小,一般可从分子量大小、熔融指数、表现粘度及流动比(流程长度/塑件壁厚)等一系列指数进行分析。
分子量小,分子量分布宽,分子结构规整性差,熔融指数高、流动长度长、表现粘度小,流动比大的则流动性就好。
常用塑料的流动性分为三类:1)流动性好PA、PE、PS、PP等;2)流动性中等聚苯乙烯系列树脂(如ABS、AS)、PMMA、POM;3)流动性差PC、硬质PVC。
2、各种塑料的流动性也因成型工艺条件而有所变化,主要影响的因素有如下几点:1)温度:料温高则流动性增大,但不同塑料也各有不同,PS (尤其耐冲击型)、PP、PA、PMMA、PC等塑料的流动性随温度变化较大所以在成型时宜调节温度来控制流动性。
对PE、POM、则温度增减对其流动性影响较小,所以在成型时要通过增加注射压力来增加其流动性。
塑胶射出成型技术

塑胶射出成型技术射出成型技术射出理论1. 射出原理:乃利用塑料之热可塑性,2. 先将塑料原料经螺杆运转摩擦生热及料管电热之辅助而3. 溶解使成流体状态。
在经杜塞压力注入,4. 设计之模型穴内,5. 经冷却后取出而6. 成各种特殊形状之成形品。
7. 射出流程:锁模→射胶→熔胶→松退(冷却)→闭模→顶出成品认识塑胶:一般塑胶分类为两种(A)热固性(B)热可塑性,射出成型加工均使用热塑性塑胶。
热可塑性塑胶有两种区别分:结晶性塑胶及非结晶性塑胶一般结性塑胶在成型过程会结晶化成形收缩率较大,成型表面光泽良好。
1.结晶性塑胶有下列:PE PP PA PBT POM PPS PET非结晶性塑胶有下列:PS PBT POM PC PVC2.工程塑胶有下列:PA PBT POM PC NORYL(PPO)特殊工程塑胶有下列:PPS PET射出成型材料之成型条件成型时使原料恰当熔融所需之热量及温度;因为每种原料之熔融温度即比热不同而不同(此资料可由原料商提供)温度之设定可依照螺杆设计:进料段-低、压缩段-高、计量段-次之。
温度过低原料熔融不均、色泽不均、温度过高使原料分解变质。
射出成型条件之高设定1.锁模压力:锁模压力必许大於塑胶射入模内之总压力,过高塑料即可能由分模而溢出,锁模太大(过高)会损耗机器、模具及浪费电力,故适当的调整锁模。
是以成品射入模内分模面不出毛边为原则。
2.熔胶量之设定:首先找寻生产机器之最大射出量(PS)及螺杆之最大行程之资料最大射出量(PS)/螺杆最大行程=A(成品+夹头)重量/B=所需设定之熔胶A*生产原料之密度=B3.射出压力、速度、位置之设定:可利用分段射出,先设定一段之速度及压力位置后对照成品,再设定下一段之速度、压力位置以此类推、一般成型不管用几段射出,在完成之前一段必须调整到80%-90%,最后一段压力、速度均小,当保压用,位置用来控制毛边或缺料。
如果成品还是缩水可利用保压来补其不足。
塑胶射出成型条件与调整之基本概念
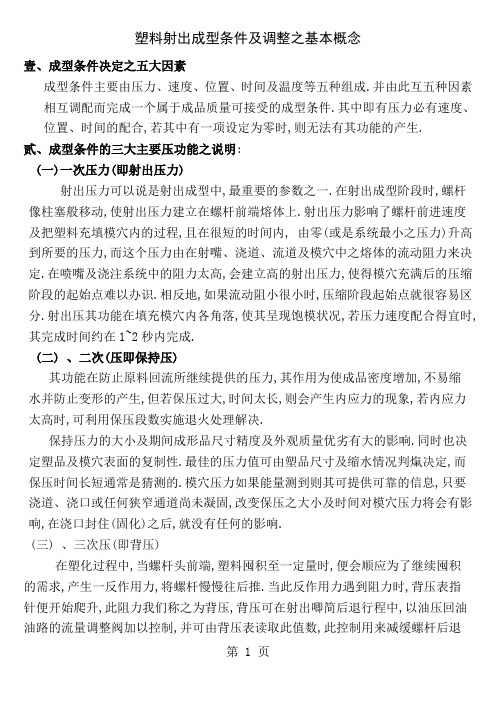
塑料射出成型条件及调整之基本概念壹、成型条件决定之五大因素成型条件主要由压力、速度、位置、时间及温度等五种组成.并由此互五种因素相互调配而完成一个属于成品质量可接受的成型条件.其中即有压力必有速度、位置、时间的配合,若其中有一项设定为零时,则无法有其功能的产生.贰、成型条件的三大主要压功能之说明:(一)一次压力(即射出压力)射出压力可以说是射出成型中,最重要的参数之一.在射出成型阶段时,螺杆像柱塞般移动,使射出压力建立在螺杆前端熔体上.射出压力影响了螺杆前进速度及把塑料充填模穴内的过程,且在很短的时间内, 由零(或是系统最小之压力)升高到所要的压力,而这个压力由在射嘴、浇道、流道及模穴中之熔体的流动阻力来决定.在喷嘴及浇注系统中的阻力太高,会建立高的射出压力,使得模穴充满后的压缩阶段的起始点难以办识.相反地,如果流动阻小很小时,压缩阶段起始点就很容易区分.射出压其功能在填充模穴内各角落,使其呈现饱模状况,若压力速度配合得宜时,其完成时间约在1~2秒内完成.(二) 、二次(压即保持压)其功能在防止原料回流所继续提供的压力,其作用为使成品密度增加,不易缩水并防止变形的产生,但若保压过大,时间太长,则会产生内应力的现象,若内应力太高时,可利用保压段数实施退火处理解决.保持压力的大小及期间成形品尺寸精度及外观质量优劣有大的影响.同时也决定塑品及模穴表面的复制性.最佳的压力值可由塑品尺寸及缩水情况判熂决定,而保压时间长短通常是猜测的.模穴压力如果能量测到则其可提供可靠的信息,只要浇道、浇口或任何狭窄通道尚未凝固,改变保压之大小及时间对模穴压力将会有影响,在浇口封住(固化)之后,就没有任何的影响.(三) 、三次压(即背压)在塑化过程中,当螺杆头前端,塑料囤积至一定量时,便会顺应为了继续囤积的需求,产生一反作用力,将螺杆慢慢往后推.当此反作用力遇到阻力时,背压表指针便开始爬升,此阻力我们称之为背压,背压可在射出唧简后退行程中,以油压回油油路的流量调整阀加以控制,并可由背压表读取此值数,此控制用来减缓螺杆后退之速度,并可测计量区的反作用力,如果当背压太大将会造成螺杆不退原地空转,迫使塑料从喷嘴流出,因此一般背压使用很少超过35kg/cm2背压的主要作用为:●增加背压,可增加螺杆对熔融树脂所做的功.●增加背压,可提高熔融温度及其均匀程度.●增加背压,可消除未熔的塑料颗粒.●增加背压,可增加料管内原料密度及其均匀程度.由以上可知背压的优点.不过增加背压却会降低螺杆的出力,而且也会破坏玻璃纤维的长度并且改变下班的特性,不得不注意.若依螺杆而言,在没有加阻料环的情况下,通常螺沟愈深,则输出量对射出压力詷整会相当敏感,背压的作用亦非常明显,反之深浅则输出量对射压调整并不明显,机械背压的感应也就罗不敏感.背压常被运用来提高料管理温度,其效果最为显著.参、射出至保压力的切换:A: B: C: D:↑从射出阶段到保压阶段无切换点的射出成形↑切换廷迟切换提早正确的切换,从射出至保压是平顺的转换模具卸料(材料回料管)↑用保压力充满模穴↑时间→时间→时间→时间→模穴内压曲线及影响的因素(a)轴赂移动速度(v) (b)模具温度(t)(c)浇口几何形状 (d)压力传感器及浇口的距离(g)由于有关模穴的内压力数据一般都不可靠,而使压压力切换点的选择经常是不正确的.列出四种基本的可能性:(a)没切换的射出(b)切换较迟的射出(c)切换较早的射出(d)较佳切换的射出如果最后压力越近于填充压力时,不用保压压力切换点的操作是可行的,这操作大部分发生于有小的浇口及有大的流向长/厚度比的塑品.即使浇口很大,相对地要求达到高的射出速度,而发生延迟切换的机会很大,其经常伴随着高度挤压的危险.除了对尺寸及毛边的不良影响,延迟切换是造成模穴边缘变形及夹模单元超负载的危险的主因.继而造成对系杆(大柱)的永久性伤害,甚至于长期运转后会继裂而报废.当从高的射出压力切换到较低的保压压力时,会造成熔体的回流,而在塑品内部形成不好的应力排列,若保压压力于浇口塑料固化前被切掉,也会有同样的状况.压力逆传的现象表示提早切换至保压压力,充填过程中的平衡,发生在偏低的保压压力状况,且因而降低射出速度.在切换瞬间,会造成短暂的流动停而使产品的表面产生令人压烦贩痕迹.从射出压力切换至保压压力的决定有三个主要方法,而其及后列三项有关:(1)时间、(2)位置、(3)模穴压力.(一)、利用时间切换此方法是从射出起始点开始计时,经过预定设定的时间,即送出一信号.此法不考虑在螺杆前端熔体的压缩性及其粘滞性、进料的准确性、射出速度变化、其中油压压力会造成螺杆位置偏移(进料结束点保压起始点)及其它相关的行程(进料行程、射出行程).最成结果是大变化性的质量规范,尤其是有关成型品的重量尺寸.因此,利用时间切换,原则上是不适当的,不用怀疑,它是所有方法里最糟的选择.(二)利用位置这种方法由证实是有用的且广泛被应用,切换信号是经由保压压力换位置的极限开关所送出.如果射出行程大部分维持固定,则切换点可视同每次皆在相同充填容积下发生.这种方法在保太行程很短的情况下会出问题,危险的是小的变化阻止每次的切换动作,在此情况下,最好还是完全不要有切换过程.此外包括进料行程的变化,极限开关的不准确,止逆阀的失效、不同的熔体粘度都会造成此方法出现问题.(三) 、利用模穴压力切换最近几年,利用压力切换的方法已被成功地使用,即使是在最糟的实际生产条件下.模穴压力在达预设之压力时,去作动切换功能其优点是有稳定可靠的切换信号,而此信号是基于绝对量的压力值所产生,使得切换更有效率.采用压力监视,可使螺杆行程和止逆阀功能的影响被排除.此种方法和两种方法一样不能对液压油、熔融塑料、模具等作温度变化补偿,或是射出速度的变化被赏.在压缩阶段压力快速上升用此种方法更具效率,因为在此状况下特别精密及适时的切换可强制性地避免压力峰的出现.在多种成形种类之中,此法特别适合用于那些分模面宽广及不允许毛边出现的情形,例如设备的平面盖板,其只有一点深度.肆、一般工程塑料成型不良原因及解决方法一、聚碳酸酯(PC)二、聚氧化二甲苯(变性PPO树脂)(MPPO)三、苯对苯二甲酸丁酸(PBT)第 11 页。
模具设计中的射出成型工艺参数优化

模具设计中的射出成型工艺参数优化射出成型是一种常用的塑料加工方法,广泛应用于各个行业。
在射出成型过程中,模具设计是至关重要的一环。
而射出成型工艺参数的优化则是确保产品质量和生产效率的关键。
本文将探讨模具设计中的射出成型工艺参数优化的重要性,并介绍一些常用的优化方法。
1. 工艺参数的选择在射出成型过程中,各种工艺参数的选择对产品的质量和性能有着直接的影响。
例如,射出速度、射压、射胶时间等参数的合理选择可以确保塑料熔体充填模具腔体的均匀性,避免产生缺陷。
此外,模具温度的控制也是非常重要的,过高或过低的温度都会导致产品的质量问题。
2. 塑料材料的选择在模具设计中,选择合适的塑料材料也是非常重要的。
不同的塑料材料具有不同的熔融温度、流动性和收缩率等特性,因此在选择塑料材料时需要考虑到产品的要求。
合理选择塑料材料可以减少产品的缩水、翘曲等问题,提高产品的质量。
3. 模具结构的设计模具结构的设计也是射出成型工艺参数优化的重要一环。
合理的模具结构可以确保塑料熔体在充填过程中的均匀性,避免产生气泡、短射等缺陷。
此外,模具的冷却系统设计也是非常重要的,合理的冷却系统可以提高产品的尺寸稳定性和表面质量。
4. 工艺参数优化方法在模具设计中,有很多方法可以用来优化射出成型的工艺参数。
其中一种常用的方法是通过数值模拟来预测和优化工艺参数。
数值模拟可以模拟射出成型过程中的流动、冷却等物理现象,从而帮助设计师选择合适的工艺参数。
此外,还可以通过试模来验证和优化工艺参数。
试模可以直观地观察到模具充填过程中的问题,并及时调整工艺参数。
5. 模具设计中的优化案例为了更好地理解模具设计中的射出成型工艺参数优化,我们可以看一个实际的案例。
假设我们需要设计一个塑料杯子的模具。
首先,我们需要选择合适的塑料材料,考虑到杯子的使用环境,我们选择了具有良好耐热性和耐冲击性的聚丙烯材料。
然后,我们需要设计合理的模具结构,确保塑料熔体在充填过程中的均匀性。
注塑射出成型参数表
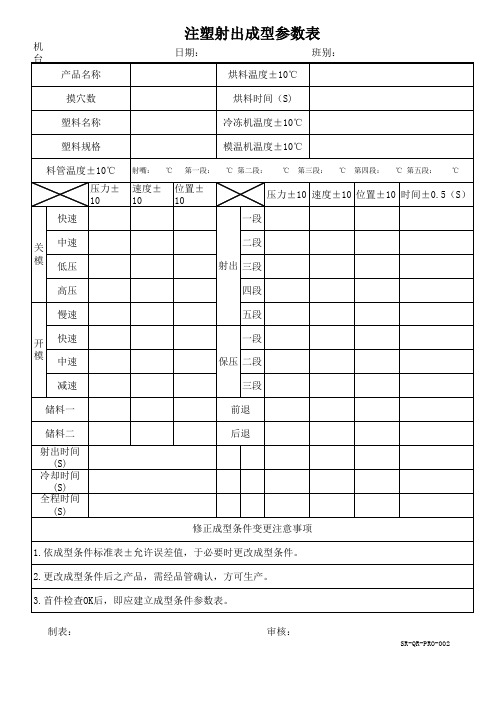
压力±10 速度±10 位置±10 时间±0.5(S)
修正成型条件变更注意事项 1.依成型条件标准表±允许误差值,于必要时更改成型条件。 2.更改成型条件后之产品,需经品管确认,方可生产。 3.首件检查OK后,即应建立成型条件参数表。 制表: 审核:
SR-QR-PRO-002
注塑射出成型参数表
机台号: 产品名称 摸穴数 塑料名称 塑料规格 料管温度±10℃
射嘴: ℃ 第一段:
日期: 烘料温度±10℃ 烘料时间(S) 冷冻机温度±10℃ 模温机温度±10℃
℃ 第二段: ℃
班别:
第三段:
℃第Leabharlann 段:℃ 第五段:℃
压力±10 速度±10 位置±10 快速 关 模 中速 低压 高压 慢速 开 模 快速 中速 减速 储料一 储料二 射出时间(S) 冷却时间(S) 全程时间(S) 一段 二段 射出 三段 四段 五段 一段 保压 二段 三段 前退 后退
射出机成形条件之设定
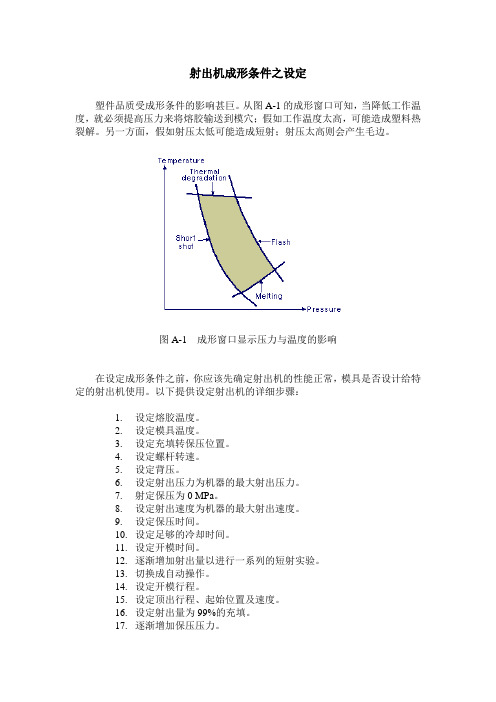
射出机成形条件之设定塑件品质受成形条件的影响甚巨。
从图A-1的成形窗口可知,当降低工作温度,就必须提高压力来将熔胶输送到模穴;假如工作温度太高,可能造成塑料热裂解。
另一方面,假如射压太低可能造成短射;射压太高则会产生毛边。
图A-1 成形窗口显示压力与温度的影响在设定成形条件之前,你应该先确定射出机的性能正常,模具是否设计给特定的射出机使用。
以下提供设定射出机的详细步骤:1.设定熔胶温度。
2.设定模具温度。
3.设定充填转保压位置。
4.设定螺杆转速。
5.设定背压。
6.设定射出压力为机器的最大射出压力。
7.射定保压为0 MPa。
8.设定射出速度为机器的最大射出速度。
9.设定保压时间。
10.设定足够的冷却时间。
11.设定开模时间。
12.逐渐增加射出量以进行一系列的短射实验。
13.切换成自动操作。
14.设定开模行程。
15.设定顶出行程、起始位置及速度。
16.设定射出量为99%的充填。
17.逐渐增加保压压力。
18.最小化保压时间。
19.最小化冷却时间。
步骤1. 设定熔胶温度熔胶温度是成形条件最重要的参数之一。
熔胶温度太低,使塑料无法完全熔化,或太黏而无法流动;熔胶温度太高,可能使塑料裂解,特别是POM或PVC 树脂更是如此。
熔胶与模具的建议温度可以请树脂供货商提供,或是使用表A-1的建议值。
大部份的树脂因为螺杆在料筒内旋转产生摩擦热而熔化。
料筒上通常会3~5组加热区域或加热片,主要功用是维持树脂在适当的温度。
设定加热片温度的规则为:●应该让温度从喷嘴到料斗附近逐渐降低。
●最接近料斗的加热片设定温度应该比计算之熔胶温度低40~50℃(72~80 °F),使塑料颗粒于塑化过程仍可以顺利地输送。
在喷嘴区的加热片应设定为计算之熔胶温度,并且保持均匀的温度。
设定不当的加热片温度会导致喷嘴处垂涎、塑料裂解或变色,特别是PA材料。
例如,C-mold软件建议使用235 ℃(455 °F)为PA材料的熔胶温度,则可以设定加热片的温度如下:●喷嘴区235 ℃(455 °F)●前段235 ℃(455 °F)●第一中段210 ℃(410 °F)●第二中段195 ℃(383 °F)●后段180 ℃(356 °F)因为旋转螺杆的摩擦热及背压对于熔胶的影响,真实的熔胶温度(或空射温度)通常比加热片的设定温度高。
塑胶射出成型进阶教程

*充填速度固定
彎 曲 點
0 60 65
70
75 80
充填速度(%)
最適當
85 90 95
35 成
34 形 品
33 重 量
32
31
30
29
塑膠射出成型進階教程 第二章 .安定成形的參數設定
P1
P2 P3 P4 保壓
(充填和壓縮)
0點 3
2 (螺杆鬆退)
1
保壓切換點
緩衝 cushion
射出前進最終點
塑膠射出成型進階教程 第三章.低壓成形技術概述
而引起這些缺點的原因,當和它的加工方法和原理息息相關,具體而言, 大概如下:
1.需要高壓高速的將塑料注射入模穴 2.因流動所引起的分子配向 3.注射後各位置密度及度的分佈差異 4.因流阻的壓力損失,使得必需以更高的壓力才能傳送塑料 5.因肉厚不均勻引起的收縮差異
2.工程概略
可 動 側
適當鎖模力關模
射出 模面寸開 保壓
壓縮
冷卻 開模
塑膠射出成型進階教程 第三章.低壓成形技術概述
3.原理概述 V
96 3
射出壓縮法
近澆口處:1 7 8 9
12
1
10
遠澆口處:10 11 12 8 9
4 11 7
8
傳統加工法
近澆口處:1 2 3
遠澆口處:4 5 6
5 2
期望比容積
塑膠射出成型進階教程 第二章 .安定成形的參數設定
2.手動運轉參數修正 (1).作業要領 確認各溫度設定是否已達正常 確認加熱筒內材料的可塑化程度 高壓閉鎖模具,射出座前進 以手動射出直螺杆完全停止,並注意其停止位置 待冷卻後,開模取出成形品 根據參數修正要領,重復第3~第5動作,直到滿意 (2).參數修正要領(-O-表螺杆最終停止位置)
注塑成型参数的调整的指南
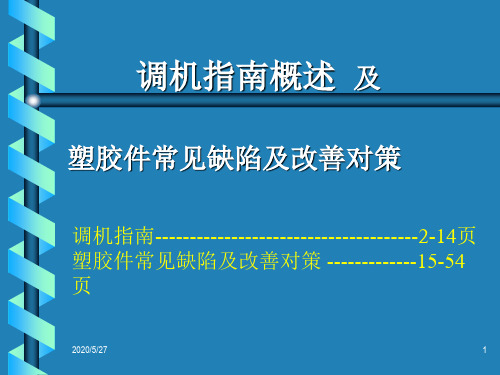
5.5 顶针速度(EJ SPEED): 顶针顶出胶件的速度称之为顶针速度。不同结构的胶
件其设置不同,一般采用中速。
六、时间参数(t):
6.1 局料时间:
不同的胶料所需的时间不同。
2019/9/18
13
调机指南概述
6.2 射胶时间(INJ-HOLD TIME): 螺杆由S0移到S3所需的时间,其设定一定和螺杆位置移
求是在啤出合格胶件的前提下,越短越好。
2019/9/18
14
缺陷: 夹水纹
Defect: weld lines
夹水纹
2019/9/18
15
夹水纹改善对策
工艺:
1.提高注射速度 2.增加炮筒温度 3.增加保压压力
模具:
1. 提高模温 2.增大浇口及流道截面积 3. 改善模具的排气
压伤模面;调节时,使前后模面有一定的压力即可,一般 取80-100kg/cm2.(一般锁模全程状态:慢速 高速
低压低速 高压合模)。
4.6 顶针压力: 啤机施加于模具顶针板后面的顶出力,大小为能顶落
塑胶件为宜。
2019/9/18
10
调机指南概述
五、 速度参数:
5.1 射胶速度(V): 啤机在射胶时螺杆推动熔胶的移动速度。射胶速度主
具:
1.增大浇口及流道截面积 2.提高模腔表面温度 3.改善模具排气
2019/9/18
32
缺陷:披锋
Defect: flash
要受射胶压力、模具型腔对熔胶的阻力、熔胶本身具备的 粘度等因素的影响,射胶压力大于型腔阻力和熔胶粘度时, 设置的射胶速度才能得以充分的发挥。如:S0 S1为V1, 此时熔胶填充型腔,需要低速中压; S1 S2为V2,此时熔 胶填充型腔,需要高速高压; S2 S3为V3 ,熔胶填充胶件 周边,需要中速低压,而且射胶速度随着模腔的填满阻力
注塑射出成形的各阶段操作设定重点,收藏了

注塑射出成形的各阶段操作设定重点,收藏了注塑汇国内专注注塑业咨询培训服务,致力于注塑业的降本增效疫情以后,注塑行业向何处走?固体塑料的塑化阶段料缸温度及喷嘴温度(1)由第一段(入料处)到第三段(喷嘴前)逐渐升温,每段温度设定值约相差5~10℃,逐步将塑料加热到适当的加工温度,各种塑料有其不同的加工温度。
(2)对低黏度的塑料,为避免在机座后退时造成漏料,通常可将喷嘴温度设定成第三段温度或略低一些(约5℃),但太低将会造成冷料,在射出时易生流痕。
对高黏度的塑料,其设定值可高于第三段温度约5~10℃,射出时可用于将流道系统加热。
(3)熔胶因螺杆旋转而摩擦生热,常导致在第三段熔胶温度高于加热器的设定值,一般甚至可高出15~30℃,因此应避免温度设定太高产生热劣解。
螺杆背压螺杆背压一般约3~10kg/cm2,背压设定的目的主要是抵住螺杆,当进料时塑料输送到螺杆前端,产生熔胶压力而使螺杆缓慢后退。
若螺杆背压大,则塑料自入料口被输送到螺杆前端,所经历的时间较长,因此塑化程度较完全,气体较不易进入,但在螺杆前端产生的熔胶压力也较大,容易在机座后退时造成漏料。
反之!若螺杆背压小,则塑料自入料口被输送到螺杆前端,所经历的时间较短,因此塑化程度较不完全,且气体较易进入。
固体塑料的塑化阶段由于螺杆在进料过程中因熔胶室的增压而后退,因此后面进入的塑料所历经的螺杆长度将变短,对塑料的熔化能力将会发生不足的现象,若因此使未完全熔化的胶粒进入熔胶室而成悬浮状,将严重影响产品质量。
因此随着进料行程的进行,螺杆的后退速度应渐缓,且必须使后进的胶料能在螺沟内有足够的时间熔化。
为达此目的,螺杆背压应随着进料行程的进行而渐增,而螺杆转速应渐减。
螺杆转速•螺杆转速rpm快,则吃料量多,剪切热也较高,但若太快也可能造成塑料分子的剪断•参有玻纤的塑料,若螺杆转速太快,会将玻纤剪断,造成物性降低•随着进料行程的进行,为使后进的胶料能在螺沟内有足够的时间熔化,螺杆转速应渐减。
- 1、下载文档前请自行甄别文档内容的完整性,平台不提供额外的编辑、内容补充、找答案等附加服务。
- 2、"仅部分预览"的文档,不可在线预览部分如存在完整性等问题,可反馈申请退款(可完整预览的文档不适用该条件!)。
- 3、如文档侵犯您的权益,请联系客服反馈,我们会尽快为您处理(人工客服工作时间:9:00-18:30)。
成 品 重 量 凹 陷 保持壓力 最適保持壓ห้องสมุดไป่ตู้ 毛 邊
塑膠射出成型進階教程 第一章 .安定成形的參數設定 安定成形的參數設定
4.充填速度的修正 充填速度的修正 要領:在保壓切換前約 在保壓切換前約10mm前後將充填速度設定為 前後將充填速度設定為30%做為第二段 要領 在保壓切換前約 前後將充填速度設定為 做為第二段 速度,後將第一段速度上下調整 找出發生短射及毛邊的速度,以其中點 後將第一段速度上下調整,找出發生短射及毛邊的速度 速度 後將第一段速度上下調整 找出發生短射及毛邊的速度 以其中點 為最適當射速. 為最適當射速
1.0
(%)
塑膠射出成型進階教程 第一章 .安定成形的參數設定 安定成形的參數設定
1.8 1.6 充 填 1.4 時 間 1.2 秒 ( ) 0.8 彎 曲 點 0.6 0.4 0.2
0 60 65 70 75 80 85 90 95
*
定 35 34 品 重 量 33 32 31 30 29 形 成
塑膠射出成型教程
第一章 .安定成形的參數設定 安定成形的參數設定
一.預备參数设定 預备參数设定 (1).材料干燥作业确认 材料干燥作业确认. 材料干燥作业确认 (2).模溫、加热筒溫度正确适当設定 模溫、 模溫 (3).開閉模及頂出設定确认 開閉模及頂出設定确认. 開閉模及頂出設定确认 : (4).射出压力 据不同原料、不同产品設定 1.先做短射品(有些产品第 射出压力—据不同原料 射出压力 据不同原料、 先做短射品( 先做短射品 (5).保 先設定0 保 压—先設定 先設定 一次需注饱模, 一次需注饱模,预防粘母模)。 (6).射出速度 据不同原料、不同产品設定 慢慢调至饱模 射出速度--据不同原料 射出速度 据不同原料、 (7).螺杆转速 約80RPM設定 螺杆转速--約 螺杆转速 設定 2.顶出设定需严谨。 顶出设定需严谨。 顶出设定需严谨 2 (8).背 表压力)設定 背 压--約5-7kg/cm (表压力 設定 約 表压力 3.螺杆参数设定要谨慎。 螺杆参数设定要谨慎。 螺杆参数设定要谨慎 (9).射出時間 (9).射出時間--稍短設定 射出時間--稍短設定 (10).冷卻時間 稍長設定 冷卻時間--稍長設定 冷卻時間 (11).保压切換位置、計量長度及松退行程設定 保压切換位置、 保压切換位置
1.0
(%)
塑膠射出成型進階教程 第一章 .安定成形的參數設定 安定成形的參數設定
P1 P4 0點 點 3 P3 保壓 2 P2 (充填和壓縮 充填和壓縮) 充填和壓縮 (螺杆鬆退 螺杆鬆退) 螺杆鬆退 保壓切換點
緩衝 cushion
1
射出前進最終點
塑膠射出成型進階教程 第一章 .安定成形的參數設定 安定成形的參數設定
成 品 重 量
時間
射出時間
塑膠射出成型進階教程 第一章 .安定成形的參數設定 安定成形的參數設定
1.8 1.6 充 填 1.4 時 間 1.2 秒 ( ) 0.8 0.6 0.4 0.2
0 20 25 30 35 40 45 50 55
*
設定 99% 35 34 品 重 量 33 32 31 短 射 毛 邊 29 30 形 成
6.冷卻時間的修正 冷卻時間的修正 要領:調降冷卻時間 調降冷卻時間,直到下列條件滿足為止 要領 調降冷卻時間 直到下列條件滿足為止 1.成品被頂出 ,夾出 修整 包裝不會白化或變形 夾出,修整 成品被頂出 夾出 修整,包裝不會白化或變形 2.模溫能平衡而穩定 模溫能平衡而穩定 7.可塑化參數的修正 可塑化參數的修正 要領:依下列原則修正 依下列原則修正-要領 依下列原則修正 1. 背壓以 背壓以5~15kg/cm2,不發生銀條 加熱筒不發生過熱 不發生銀條,加熱筒不發生過熱 不發生銀條 加熱筒不發生過熱. 2. 調整螺杆轉速 使計量時間稍短於冷卻時間 調整螺杆轉速,使計量時間稍短於冷卻時間 使計量時間稍短於冷卻時間. 3. 鬆退行程以不滴料 流道不發生豬尾巴 不粘模及成品不發生氣痕為原則 鬆退行程以不滴料,流道不發生豬尾巴 不粘模及成品不發生氣痕為原則. 流道不發生豬尾巴,不粘模及成品不發生氣痕為原則 8.多段充填速度及多段保壓的活用 多段充填速度及多段保壓的活用 要領: 要領 1.多段速度 配合短射試驗對應成品外觀來設定 多段速度:配合短射試驗對應成品外觀來設定 多段速度 2.多段保壓 原則逐步下降 對應成品尺寸安定 凹陷程度及變形量來設定 多段保壓:原則逐步下降 對應成品尺寸安定,凹陷程度及變形量來設定 多段保壓 原則逐步下降,對應成品尺寸安定
P1=99%
PH
成 零 點 保 壓 切 換 點 品 重 量 毛 短 射 邊
SO
SO
計量行程
塑膠射出成型進階教程 第一章 .安定成形的參數設定 安定成形的參數設定
2.射出壓力的修正 射出壓力的修正 要領:將射出壓力由逐漸調降 記錄充填時間(一次壓時間 的變化, 將射出壓力由逐漸調降,記錄充填時間 一次壓時間)的變化 要領 將射出壓力由逐漸調降 記錄充填時間 一次壓時間 的變化 以其最接近产生毛边壓力時的狀況的較低射出壓力為適當. 以其最接近产生毛边壓力時的狀況的較低射出壓力為適當 3.保持壓力的修正 保持壓力的修正 要領:上下調整保持壓力 找出發生毛邊和凹陷的壓力,以其中間值為最 上下調整保持壓力,找出發生毛邊和凹陷的壓力 要領 上下調整保持壓力 找出發生毛邊和凹陷的壓力 以其中間值為最 適當. 適當
保持壓力 保壓時間 切換時機 120g 成 形 品 重 量 118g 116g 30s 114g 112g 110g 5s 25s 20s 15s 10s 53bar 35sec 遲 53bar 35sec 遲 53bar 35sec 早 39bar 25sec 早 53bar 變化 早
塑膠射出成型進階教程 第一章 .安定成形的參數設定 安定成形的參數設定
要点
零 點
10~20mm 松退行程 保压切換 計量行程
塑膠射出成型教程
第一章 .安定成形的參數設定 安定成形的參數設定
二.半自动运转參數修正 半自动运转參數修正 1.計量行程的修正 計量行程的修正 要領:將射出壓力增加 把計量行程縮短直到發生短射,再延 將射出壓力增加,把計量行程縮短直到發生短射 要領 將射出壓力增加 把計量行程縮短直到發生短射 再延 長直到發生毛邊
P1=99% PH V2=30%
零點 保壓切換
V1
SO
塑膠射出成型進階教程 第一章 .安定成形的參數設定 安定成形的參數設定
5.射出時間的修正 或保持時間 射出時間的修正(或保持時間 射出時間的修正 或保持時間) 要領:調升射出時間 直到成品重量明顯穩定為止. 調升射出時間,直到成品重量明顯穩定為止 要領 調升射出時間 直到成品重量明顯穩定為止