制程检验作业规范1
模具制程检验作业指引

模具制程检验作业指引模具制程检验可太重要啦!这就好比我们做饭的时候,得时不时看看菜炒得怎么样,调料放得对不对,别等到出锅了才发现不对劲,那就晚喽!咱先来说说为啥要有模具制程检验这个事儿。
我给您讲个我亲身经历的事儿。
有一回啊,我们厂接了一个大单子,做一批精密模具。
大家一开始都干劲十足,想着赶紧完成任务。
结果呢,在制程中少了检验这一环,等到模具都快完工了,才发现尺寸有偏差,而且表面还有不少瑕疵。
这可把大家急坏了,重新修改费时费力不说,还差点耽误了交货时间,客户那边也很不满意。
从那以后,我们就知道了,模具制程检验那是万万不能少的!那模具制程检验到底要检些啥呢?首先得看看模具的原材料对不对,是不是符合要求的那种材质和规格。
这就好比盖房子,要是砖头质量不行,这房子能结实吗?然后呢,加工过程中得盯着那些工艺参数,像切削速度、进给量啥的,可不能乱来。
比如说有一次,一个师傅为了赶进度,把切削速度调得太快,结果模具表面都被刮花了,这可不行!还有啊,模具的各个零部件也得仔细瞅瞅。
尺寸精度那得用精密量具量一量,差一点儿都不行。
就像上次一个小零件,尺寸就差了那么一丢丢,装到模具里就不匹配,整个模具的性能都受影响啦。
在检验的时候,咱们得有一套标准的流程和方法。
比如说,先检什么后检什么,得安排得明明白白的。
不能东一榔头西一棒子,那样容易有疏漏。
而且啊,检验的工具也得选对,该用卡尺的时候用卡尺,该用千分尺的时候用千分尺,可不能瞎用。
检验人员也得有一双“火眼金睛”。
得经过专门的培训,知道怎么看,怎么判断。
不能模棱两可,差不多就行。
这可关系到模具的质量,一点儿都不能马虎。
说到这儿,您可能会问了,那检验出来有问题咋办?这就得赶紧采取措施啊。
小问题能当场解决的就当场解决,大问题就得停下生产线,好好研究研究,找出根源,彻底解决,可不能让问题留到后面。
总之啊,模具制程检验就像是模具生产的“守护神”,只有把这个工作做好了,才能做出高质量的模具,让客户满意,让咱们的工厂有好口碑。
FQC检验作业规范 (1)解析

主要缺陷:印字不清晰(或无印字) 、模糊、变形 2.方法[目视] 严重缺陷:表面是否破胶、露铜
主要缺陷:a.线身刮伤、污脏、起粒 b.印字内容错误 c.色差、杂色、混色、错色、不对板 次要缺陷:扎伤线、扎痕印深
C.注塑: 方法[目视]
主要缺陷:a.PVC颜料与线材统一 b.注塑类型 c.是否有冲胶、缺料、毛边等不良现象 3.规格: 方法[卷尺] 主要缺陷:总长 4.包装: 方法[目视] 主要缺陷:a.包装方式是否与生产计划单及作业指 导书规定相符
4.适用产品:V7类
1.检验项目 【外观】 2.合格判定基准:依生产计划单及作业指导书规定为基 准 A.水晶头: 方法[目视] 严重缺陷:水晶头卡位断裂或变形 主要缺点: a.水晶头线口为弧形或方口形 b.水晶头未压到位或压太深 B.线材:1.方法[擦试目视] 主要缺陷:印字不清晰(或无印字) 、模糊、变形 2.方法[目视] 严重缺陷:表面是否破胶、露铜
主要缺陷:a.线身刮伤、污脏、起粒 b.印字内容无“BELKIN”字样 c.色差、杂色、混色、错色、不对板 次要缺陷:扎伤线、扎痕印深
C.注塑: 方法[目视] 主要缺陷:a.PVC颜料与线材统一 b.注塑类型 c.是否有冲胶、缺料、毛边等不良现象 3.规格: 方法[卷尺] 主要缺陷:总长 4.包装: 方法[目视]
FQC成品检验作业规范
1.目 的:为确保成品出货质量,并降低检查费用而执行抽样检验,并使成 品检验有依可循。 2.定 义: 2.1.成品检验是指判定成品是否已完成客户订单之要求规范。 2.2.抽样检验是指送样批中,抽取若干样试验之,并将其结果与规范比较,以判断该批应 合收或拒收。 2.3.成品之抽检批量,经出货之数量为一批量,当FQC收到每批送检的成品时,按送检 的批量数进行抽检,所抽检出的成品检查数中,除各类产品的成品总长尺寸按每批 抽5PCS记录3PCS外,其它项目按抽查的成品数量进行全检,对所有抽检的成品, FQC记录时,尺寸项目记录3PCS数据,如有超出尺寸公差的,则必须记录超出公 差尺寸的数据,其它检验项目记录“OK”或“合格”字样即可,环保要求方面,依 客户环保要求及SGS核对,记录“OK”或“合格”字样即可。 2.4.每月初,品管部将对上个月FQC检验出的不良品项目,用《检查表》及《柏拉图》 形式统计出,并对柏拉图中前三项不良率最高项提交给责任单位作原因分析及改善 对策。 3.抽样标准 依据“GB/T2828.1-2003 正常检验一次抽样方案,一般Ⅱ级水平检验。
SOP标准作业程序与作业指导书

SOP标准作业程序与作业指导书.txt婚姻是键盘,太多秩序和规则;爱情是鼠标,一点就通。
男人自比主机,内存最重要;女人好似显示器,一切都看得出来。
标准作业程序与作业指导书我常常在咨询或者辅导企业的时候有人问到:“如何才能够增强执行力”,这个问题并不难;其实一个人先有了想法,才会有看法、说法和做法,您必须让执行作业的人,知道自己的岗位职责需要做哪一些事情?那就是想法;做好的标准那就是看法;执行业务的人能够很清楚地说出来以上要做的事流程、步骤、注意事项等等以及标准那就是说法,进一步现场去执行做好,那就是做法,从想法、看法、说法到做法,一个主管部门到底如何培育与培训员工?需要那一些资料?培训?工具呢?如何做好绩效考核?怎样才能够完善呢?我在之前写的博客有提到任何一个部门体系建立都需要建立在五个方面:1、制度标准化(System Standardization)、 2、专业手册化(Specialized handbook)、3、培训标准化(Training standardization)4、考核量化(Inspection quantification)5、完善工具化 (Perfect tool)。
建立体系需要的两个基本的概念与技术,那就是标准作业程序SOP与作业指导书,这两个工具与技术很简单,但是很多人不想去彻底做好它,所以导致执行力弱或者低下,当然做好之后的培训更是重要,让我们先看看看怎么做,下一篇文章再告诉大家怎样来培训与怎么做好执行力的培训?标准作业程序 SOP(Standard Operation Procedure)什么是SOP(标准作业程序)所谓SOP,是 Standard OperationProcedure三个单词中首字母的大写,即标准作业程序,就是将某一事件的标准操作步骤和要求以统一的格式描述出来,用来指导和规范日常的工作。
SOP的精髓,就是将细节进行量化,用更通俗的话来说,SOP就是对某一程序中的关键控制点进行细化和量化。
LED检验规范

LED检验规范版本:V100编辑:石冬,熊孜日期:2019/12/261,LED原材料检验(IQC)职责简介IQC(incoming quality control)意思是来料的品质控制,简称来料控制。
之所以在此谈IQC,而不是IPQC(制程品质控制),FQC(成品品质控制)等。
是因为各种假货,劣质产品在不断地侵蚀着我们,面对这些劣质产品,可能一个小小的失误就可能给我们造成巨大的财产损失或断送了前程。
所以处理好LED材料、原料的品质控制,对每个LED厂商来说,都已经是迫在眉睫。
只有材料好了,才可以制造出好的产品来。
LED进厂检验包括三个方面:a、库检:原材料品名规格、型号、数量等是否符合实际,一般由仓管人员完成。
b、质检:检验原材料物理,化学等特性是否符合相应原材料检验规定,一般采用抽检方式。
c、试检:取小批量试样进行生产,检查生产结果是否符合要求。
1 来料不合格的处理:a、标识:在外包装上标明“不合格”,堆置于“不合格区”或掛上“不合格”标识牌等。
b、处置:退货或调货或其他特采。
c、纠正措施:对供应商提供相关要求或建议防止批量不合格的再次出现。
2 紧急放行:2,LED检验参数和检验规范LED是英文Light Emitting Diode的简称,也是叫发光二极管。
1分类:1,按照LED功率来分:小功率LED,大功率LED2,按照封装类型来分:插件式(Lamp),贴片式(3812,3528,5050)3,按照发光角度来分:侧面发光(SideView),顶部发光(TopView)2 参数:1,正向电压(Vf)LED工作电压2,电流(If) LED工作电流,电流越大,亮度越高3,波长(nm)纳米;光的色彩强弱变化(可见光:380nm-780nm)4,光通量(lm)流明;光源每秒所发出的可见光量总和。
5,光强(mcd)亮度;光通量的空间密度,即单位立体角的光通量,叫发光强度6,色温(色坐标X,Y轴)如:x=0.35,y=0.353 宇宙物料规格认知:LED,WHITE,SMD4213,4.2*1.3*1.2mm,DSW-HSG-X1-J2,DOMINANT,1.178Grouping :X1J2=亮度BIN 和色度BIN 根LED 规格书区分代码标识(第4页有说明) X1是亮度等级,J2是色度坐标一切都是为了让我司产品亮度等处于平衡状态所采取的技术手段。
SMT制程检验作业指导书
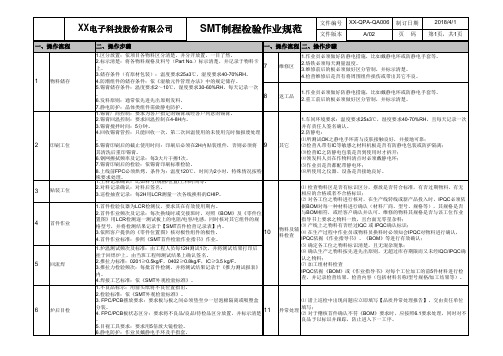
物料及辅 料检查
⑶ 产线上之物料有否经过IQC 或 IPQC确认标识; ⑷ 在生产过程中作业员或物料员换料时必须知会IPQC对物料进行确认, IPQC依据《作业指导书》、《BOM》等进行有效确认;
⑸ 确定各工位之物料标识清楚,且无混杂现象;
⑹ 确认生产之物料按先进先出原则,无超过库存期限而又未经IQC/IPQC确
10
4.首件作业标准:参照《SMT首件检验作业指书》作业。
1.炉温测试频次及标准:由工程人员每12H测试1次,并将测试结果打印后
挂于回焊炉上,由当班工程师测试结果上确认签名。
2.推拉力标准:0201≥0.5kg/F,0402≥0.8kg/F,IC≥3.5 kg/F。
3.推拉力检验频次:每批首件检测,并将测试结果记录于《推力测试报表》
其清洗后重印锡膏。
6.钢网擦拭频率及记录:每3大片干擦1次。
7.锡膏印刷后的检验:依锡膏印刷标准检验。
8.上线前FPC必须烘烤,条件为:温度120℃,时间为2小时,特殊情况按特
1殊.上要料求记处录理确。认:比如料号/规格/位置/上料时间等。
2.对料记录确认:对料后签名。
3.巡检抽查记录:每2H用LCR测量一次各线换料的CHIP。
6.静电防护:作业员戴静电手环及手指套。
维修区
1.作业员必须做好防静电措施,比如戴静电环或防静电手套等。 2.烙铁必须每天测量温度。 3.维修前后的板必须做好区分管制,并标示清楚。 4.检查维修后是否有将周围组件损伤或带出其它不良。
Байду номын сангаас返工品
1.作业员必须做好防静电措施,比如戴静电环或防静电手套等。 2.重工前后的板必须做好区分管制,并标示清楚。
1.首件检验仪器为LCR检测仪,要求其在有效使用期内。
WIPB-02成型抽验作业规范1.5版 2017.7.13修改(1)
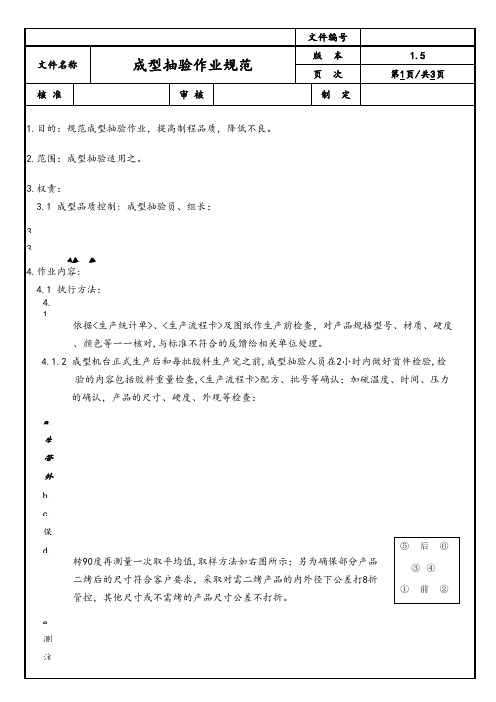
5.2.1 制程中抽验人员若发现外观、尺寸硬度、毛边有其中一项不符合时则生产判定为“不
文件编号 文件名称
成型抽验作业规范
版 页
本 次
1.5 第3页/共3页
可”,尺寸、硬度异常及外观不良率超出预估值的2倍以上时,由抽验员第一时间通 知制造技术员处理,制造部门在60分钟之内无法 处理降低不良,控制在预估不良 范围内时,由成型抽验员开具<品质异常处置单>,经抽验组长确认后交成型生技员(或组 长),由其进行原因分析和提出改善对策, 成型抽验人员负责追踪,抽验方法加严一倍抽 验,确认直至异常得到解决和处理,无法处理则联络工程课或材料课协助处理,抽验人员 对异常发生的时点、异常内容、发生率详细记录于<生产流程卡>的“过程栏”,并由相 关技术人员做异常处置记录,<品质异常处置单>保存以便日后品质追溯。 5.2.2 因二次加硫对产品尺寸有一定影响,对于需要做二次加硫的O-ring等制品,其尺寸公差 上限可放宽20%(上公差×1.2)。 5.2.3 对于花洒系列或者生产时自带撕边的制品,需冷冻拆边的产品因手工作业出现100%毛边, 对其毛边的撕边性不做判定,其他制品的撕边性不良不能超过10%;异常不良项目综合 不能超过15%的可判定放行生产。 5.2.4 对于送样尺寸不合格的规格,经客户确认接受并下单生产时,制程尺寸则按照送样实 测尺寸的范围来判定。 5.2.5 生产中对于难以改善的不良需要放行生产时,可由相关部门主管或品管人员在<生产流 程卡>的“异常处置”栏说明处置方案并签字放行,抽验员则对生产判定“可”并记录 于<成型抽验日报表>的记录栏。
5.1.2 产品厚度(或高度)测量选用仪器原则参见下表: 范围 30.01mm以上 游标卡尺
制袋制程及最终检验标准
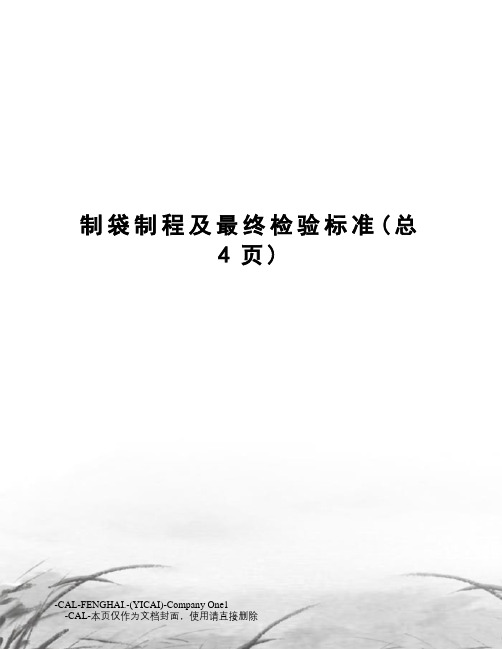
制袋制程及最终检验标准(总4页)-CAL-FENGHAI.-(YICAI)-Company One1-CAL-本页仅作为文档封面,使用请直接删除适用范围:本标准适用于制袋工序生产过程中生产人员对所生产产品的自检、质量控制及品管人员对制袋产品的制程检验和制袋成品包装缴库时的完工检验和出货前的出厂检验。
标准内容:1.抽取样本1.1依制袋机生产顺序,确定检验对象,在已确定的品种被制袋成型为成品状态的产品中随机抽样。
生产人员每一百只自检一次,制程检验人员每两小时抽查一次。
1.3成品包装缴库前进行完工检验。
产品出货前作出厂检验。
完工检验和出厂检验的抽样规格及数量执行以下标准:以产品个数抽样的抽样标准以产品包装件数抽样的抽样标准3.1上述指标全部合格则判定为合格;上述指标有一项不合格,则判定为不合格。
3.2首检合格才允许正式生产,制程检验发现不合格及时通知生产人员调整,必要时停机处理。
生产过程中意外停机或生产人员调整后须重复首件检验直至合格。
3.3制程检验发现的不合格品和出厂检验发现的不合格品,如果可以筛选或修复的由当班生产人员负责筛选或修复,无法筛选或修复的不合格品要开出《不合格产成品报告处理单》进行相应处理。
3.4 生产成品缴库前须由品管人员按计划缴库数量抽样作完工检验,完工检验不合格的产品不可缴库;库存产品出厂前须由仓库人员通知品管按照出货量进行抽检,作出厂检验。
4.记录与区分4.1分切和制袋制程检验及判定结果,分别填入《分切/制袋制程检验记录》,生产人员自检不做记录。
4.2产品缴库前的完工检验由品管记录检验数据和判定结果于《完工检验报告》上作为缴库依据;产品出厂前由品管人员作出厂检验,将出厂检验的数据和判定结果记录于《出厂检验报告》上,作为出厂放行的依据。
4.3对所有已检、未检产品作出明确、固定的标识,区分摆放。
已检合格的成品放入待包装区域。
4.4已检不合格产品可返工,重修的退还生产部门返工,若不合格又不能返工利用的,放入待处理品区域,同时填写《不合格产成品报告处理单》呈报公司批示后处理。
进货检验流程及规范
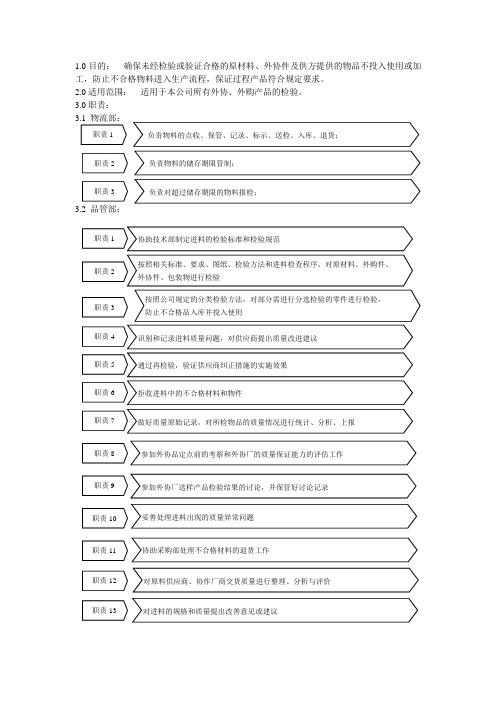
1.0目的:确保未经检验或验证合格的原材料、外协件及供方提供的物品不投入使用或加工,防止不合格物料进入生产流程,保证过程产品符合规定要求。
2.0适用范围:适用于本公司所有外协、外购产品的检验。
3.0职责:3.2 品管部:3.3采购部:3.4 生产部:5.1 入库送检:物流部在规定时间完成物料点收(含质量证明文件或检测报告)、标识,填写《送检单》,填写内容要求完整,物料到库半小时内送品管部报检。
5.2 进货检验流程: 5.2.1品管部收到《送捡单》(含质量证明文件或检测报告)半小时内回复检验及完成时间。
5.2.2 标准确认: 来料检验员根据具体来料标识卡、物流部报检单,查找相对应来料检验标准。
5.2.3抽样: 根据来料数量按《产品抽样检验管理办法》确定抽样方案并取样。
5.2.4测量/实验:5.2.4.1 进料检验进行来料标识确认:送货单位、产品名称、规格型号、日期、是否环保等内容标识完整;标识卡内容不完整或者无物流标识,物流部负责纠正,品管部进行跟踪验证。
5.2.4.2 检测实验报告及其他质量证明文件的确认、点收:确认无误按《文件控制程序》归档备查,如送货单位无检测实验报告及其他质量证明文件,内部联络采购部,依《不符合、纠正和预防措控制程序》处理。
5.2.4.3 产品包装防护确认:目测检查产品包装外箱是否满足搬运、运输及储存要求,不符合要求,内部联络采购部,依《不符合、纠正和预防措控制程序》处理。
5.2.4.4外观检查:不允许有麻点,色差、锈迹、裂纹、油污、碰伤、字迹清楚、破损、缩水、水纹、变形等,按品管部检验标准执行。
5.2.4.5尺寸测量:按品管部图纸及检验标准执行。
5.2.4.6性能实验:按品管部图纸及检验标准执行。
5.2.4.7报告填写:依据来料标识及《报检单》填写《来料检验报告》抬头栏:供应商名称、来料日期、数量、客户名称、合同编号、检验员、检验日期及抽样方案Ac-----接收数Re------拒收数等。
制程检验规范(1)

规范文件
文件编号: 版次: 页次:
制程检验作业规范
6.7.1 良品退料:经过外观及性能检验合格,标识准确无误的良品物料,将贴上“良品退料” 的合格标贴后,IPQC员在生产线开具的《退料单》上确认签字后,予以良品退料。 6.7.2 不良品退料: 经过外观及性能检验不合格,标识准确无误的不良品物料,将贴上“不良 品退料”的不合格标贴标识清楚,不同供应商的不良品退料要用不同的外卡通包装,且 须分析其不良原因与《不良品退料单》上原因相符, 并判定准确无误后,IPQC员在生 产线开具的《退料单》上签字(有特殊原因的须在不良原因中作特别注明)后,予以 不良品退料。 6.8 数据分析及总结 6.8.1 IPQC员每天及时负责收集、整理、查核生产线《生产全检记录表》、《生产线老化 记录表》等品质记录报表, 经生产线管理人员签字确认后、送交品质主管审核后, 进行数据分析,以便考察目标合格率完成状况,然后予以存档。 6.8.2 及时将生产过程中所发生的各种品质状况记录于工作笔记中,并将信息传达于该产 品检验之相关人员知悉。 6.8.3 关闭、清点、整理检验所使用的仪器、设备,治、工、夹具,摆放在适当区域,做 好6S的维护工作。 7 记录表单 7.1 《首检记录表》 7.2 《巡检记录表》 7.3 《生产线老化记录表》 7.4 《品质异常处理单》
规范文件
文件编号: 版次2 巡回检查中的控制点依相关工序确定,所有控制点的检查项目及其检查结果必须记录 于相关制程巡检记录表内,呈品质组长签核。生产过程中因人员、场所变更时,需确 保操作人员能了解作业要求,同时对现场一些孤立的作业场所、孤立的作业人员, IPQC需作重点监控 6.4.3 生产过程中由于零件缺损或其他原因造成材料短缺而需补尾数时,须在生产拉不生产 其他产品的情况下进行补尾数作业,且其材料上线前须经由多能工实施全检,并通知 IPQC确认合格后方可投入生产,IPQC需对尾数的生产进行全程跟进,并在验证尾数合 格后签名确认。 6.4.4 巡回检查中如发现不合格品时需依《不合格品控制程序》处理,如发生品质异常时则 需开立《异常跟踪表》,要求相关部门解决。 6.4.5 对于检验中发现不合格且经品管判定需重工处理时,由生产单位进行返工,IPQC全程 跟进返工状况并对返工品进行复检。 6.4.5 巡回检查中IPQC需对生产单位作业指导书及相关测试标准之悬挂状况进行管控,并需 对操作人员之作业动作进行监督,对于违规作业者须及时提出纠正并视具体情况作其 他相应处理。 6.5 生产老化测试 6.5.1 在正常情况下,所有产品需进行老化测试(包括产出半品时和制成成品后)。 6.5.2 老化时间: 大功率产品老化时间最少为24小时,其中成品老化部分不小于8小时 小功率产品老化时间最少为18小时,其中成品老化部分不小于6小时 对于充电式产品可不全做老化测试,但应抽取10~20pcs作相应的完全充电和放电测试 开关冲击测试:可以不全做,但须抽10--20pcs做冲击测试(通45s关15s),不低 于1000次 若有客户特殊要求者,按客户要求进行相关老化。 6.6 异常处理 6.6.1 当在巡检过程中,若出现重大品质异常,不良率超过20%,导致大批量不良品或无法生 产时,IPQC员必须及时知会生产线现场管理人员和PE/QE工程师予以现场处理,并根据 实际情况,提出停拉申请, 并知会相关部门责任人员解决;待问题改善后,通知生产线 复产,并跟踪改善效果。 6.6.2 其它异常参照《不合格处理程序》执行。 6.7 退料检查
制程检验规范(含记录)
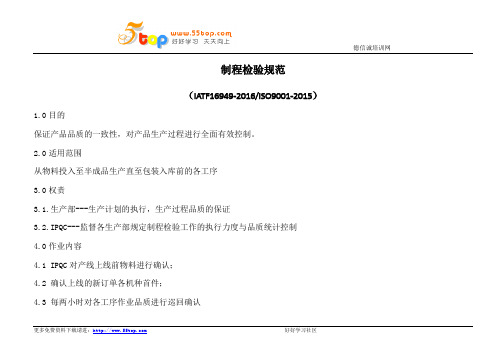
德信诚培训网制程检验规范(IATF16949-2016/ISO9001-2015)1.0目的保证产品品质的一致性,对产品生产过程进行全面有效控制。
2.0适用范围从物料投入至半成品生产直至包装入库前的各工序3.0权责3.1.生产部---生产计划的执行,生产过程品质的保证3.2.IPQC---监督各生产部规定制程检验工作的执行力度与品质统计控制4.0作业内容4.1 IPQC对产线上线前物料进行确认;4.2 确认上线的新订单各机种首件;4.3 每两小时对各工序作业品质进行巡回确认德信诚培训网4.4 单项外观不良率超过3%,电性不良率超过1%须立即开立品质异常联络单进行反馈4.5 对于由现场执行的改善措施进行跟踪并及时反馈上司。
工序项目允收标准检验方法检验工具及附件判定基准类别内容MAJ MIN裁线外观印字清晰无油污,字体一致.印字内容与要求相同.目视工程图/样品△线材外被光滑无明显夹痕,无损伤,无色差. 目视样品/色板△印字方向每把线材印字头尾方向一致目视目视△裁线结构尺寸线材规格与工程图中线材规格标准一致量测千分尺△色序/排线与图面相符目视工程图/样品△分线分线长度与图面要求相符且无压伤量测/目视钢尺/工程图△总长度与图面要求相符量测尺/工程图△剥皮长度与工程图面相符量测钢尺/工程图△线芯无切伤/切断芯线及导体目视/ △端子压著外观端子型号/规格无变形、料带过长、损伤,端子型号规格均与图面相符.目视工程图/样品△线材无压伤、破损,规格、颜色符合图面要求. 目视工程图/样品△压着结构拉力依线材规格及端子型号确定拉力大小,须符合<<标准拉力表>>中要求量测拉力计△到位端子前脚两端均可见芯线且端子后脚间能看见绝缘皮目视/ △芯线不能有外露、压断铜丝、飞铜丝现象目视/ △全检端子外观除拉力外同端子压著工序目视放大镜△组装胶芯插端子规格Housing型号规格与工程图相符.颜色和塞孔正确.线材规格裁线长度正确,与工程图相符.量测尺/工程图△印字Housing和线材印字清晰,内容与颜色正确,不易脱落.目视工程图/样品△外观Housing无损伤,缺料,杂色等,线材无压伤,无端子变形,无单根受力,色序排列正确,无掉PIN,端子未插到位,漏插胶壳,飞丝,芯线掐伤,组合线无长短不一,套管到位烘紧无破损.目视工程图/样品△测试电气性能无开路,短路,错位,绝缘,耐压,接触不良测试测试机△焊接分线外观无分伤线,撕破外被,露铜,分线尺寸符合工程图要求.目视/量测钢尺/工程图△剥线尺寸剥头尺寸符合工程图面/SOP要求量测钢尺/工程图△外观无飞丝,剥断铜丝或伤芯线目视/ △焊接材料连接器规格型号与图纸一致,无用错规格目视工程图/样品△外观 焊点圆滑,饱满,无假焊,脱焊,漏焊,错位,烫伤零件及线材.目视 工程图/样品 △ 焊接接点焊点排位 焊点排位与图纸要求一致,无焊错位目视 工程图/样品 △ 温度铬铁温度 焊接温度是否符合作业要求,有无偏高或偏低.量测 温度计 △ 成型成型材料使用胶料材质颜色硬度等与图纸一致目视 工程图/样品△ 外观无缩水,流纹,毛边,冲胶,杂色,错模,变形,模印,气泡,缺料.目视 / △ 无压伤线材及零件目视 / △ 模具编号、LOGO 方向及图样与工程图相符目视 工程图/样品 △ 尺寸头部外露、SR 卡口等尺寸与工程图面相符量测 卡尺/工程图△ 吹 套 管外观 外观 套管缩紧,无烫伤,无破损.目视 / △ 尺寸规格 套管规格颜色正确,长度及烘烤位置符合工程图要求.量测 钢尺/工程图△ 脱 皮脱外皮外观脱皮口平齐,无刮伤芯线外被及铜丝,头尾方向正确目视 / △ 尺寸脱皮长度与工程图面相符.量测 钢尺/工程图△ 剥芯线外观无脱断/脱伤芯线及铜丝,铜丝保持整齐,无散乱.目视 / △ 尺寸脱皮尺寸符合工程图要求.量测钢尺/工程图△扭线扭铜丝外观无飞丝,打结,无漏扭及过松现象目视/ △尺寸各尺寸与工程图面相符. 量测钢尺/工程图△焊接温度铬铁温度焊接温度是否符合作业要求,有无偏高或偏低.量测温度计△材料锡丝规格锡丝是否为无铅环保锡丝,锡丝型号规格是否与工程图面要求符合目视/量测卡尺△产品外观焊点圆滑,饱满,无假焊,漏焊,错位,烫伤零件及线材.目视/量测测试机/工程图△沾锡参数锡炉温度锡炉温度是否符合作业要求,有无偏高或偏低.量测温度计△材料锡丝锡条规格锡条是否为无铅环保锡条,焊接头型号规格是否与工程图面要求符合,锡炉是否为环保专用锡炉目视/量测XRF环保测试仪△产品外观沾锡部分光亮,无连锡、大头、OD不符;沾锡不到位、烫伤线皮、线身沾锡渣、氧化发黑等目视工程图△绕扎线材料扎带规格扎带规格材质颜色等符合图纸要求目视工程图△尺寸扎线及头尾尺寸扎线中间主体尺寸及头尾留长尺寸与图纸一致量测钢尺△绕扎线外观外观扎带无破损、露铁芯;扎带扭转圈数正确,无松散;PET扎带有筋面是否朝上;线材是否刮伤;头/尾是否夹伤撞伤目视目视△功能测试治具测试治具测试治具使用是否正确,治具是否正常. 量测点检样品/工程图△参数设定测试参数测试机各项参数设定是否与工程图要求一致. 目视工程图△电气性能电性测试无开路,短路,错位,绝缘,耐压,打火,瞬间不良等.测试测试机△外观全检外观头部端子规格与图纸一致;无冲胶缺胶、缩水流纹料花、压伤线材五金头、五金头脏污氧化;外模鼓包变形;外模错模、合模线过大、外模开口凹坑、露内模锡点、LOGO方向正确;网尾裂缝等目视图纸/样品△线身线材印字内容与图纸一致,整把线材印字内容头尾方向须一致;线身无刮伤脏污颗粒,印字清晰可识别;目视图纸△尾部SR无变形,压线露铜,进料嘴过大手感明细目视目视△尺寸尺寸成品各尺寸符合图纸要求(端子外露、SR卡口、SR留长及锡尾留长等尺寸)量测卡尺/钢尺/卷尺△电测性能电性无短断路绝缘耐压不良等测量导通测试机△信耐性可靠性可靠性线材摇摆及头尾吊重及阻燃等级等可靠性符合图纸要求测量摇摆机/吊重仪/阻燃测试仪△包装外观包装方式包装方式符合图纸/SOP要求;外箱标签内容正确;标签内容与实物一致,无混料错料目视图纸/SOP △数量数量装箱数量符合要求,无短装多装量测电子磅△5.0参考文件制程检验程序6.0相关记录IPQC巡检记录IPQC巡检日报表(2).xls成品抽检台帐成品检验报告.docIQC进料检验报告德信诚培训网IQC进料检验报告.xls铬铁/锡炉温度点检表烙铁温度点检表.xls外观、电性全检日报表FAI检验报告记录表.xls。
机械(金属切削)加工检验标准及规范
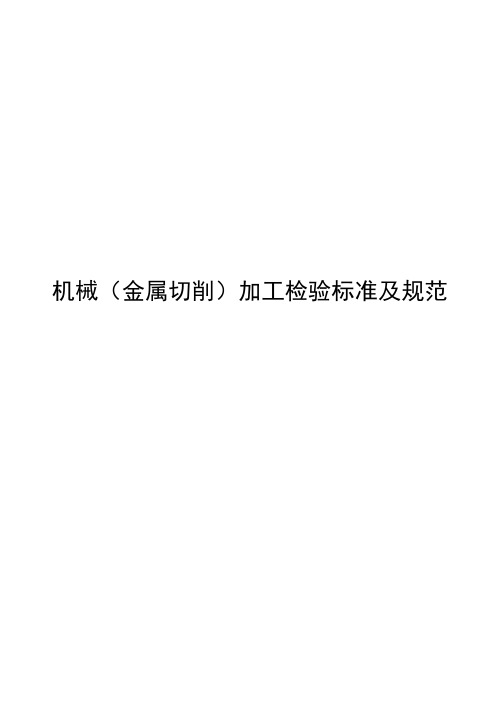
本标准适用于切削加工(包括外协、制程、出货过程)各检验特性的检验。在本标准中,切削加工指的是:车 削加工、铳削加工、磨削加工、镇削加工、刨削加工、孔加工、拉削加工和钳工作业等。
.
本标准不适用于锻造、镀金、焊接后的检验,其检验标准另行制定。
本标准规定了尺寸检验的基本原则、对环境的要求、外观检验标准、线性尺寸公差要求、形位公差要求、表 面粗糙度的检验、螺纹的检验、检验计划和判定准则。
GB1804-2000不适用于下列尺寸:
a)其他一般公差标准涉及的线性和角度尺寸;
b)括号内的参考尺寸;
c)矩形框格内的理论正确尺寸。
参考尺寸和理论正确尺寸的公差要求另行规定。
表2 线性尺寸的极限偏差数值mm
公差等级
基本尺寸分段
0.5-3
》3~6
>6-30
>30-120
>120 〜40c
>400-1000
士5,
粗快c
±F30f
士
士3d
士15'
士10
最粗v
+3*
±2*
±r
±3«
士2G
9
基本要求
图纸上对形位公差有明确要求的,按照图纸要求进行检验。
图纸上对形位公差没有明确要求的,其形位公差由加工工艺保证,一般不做检验;对形位公差有怀疑时,需 进行检验。
k
客户另行要求的,以客户要求为准。
形状和位置公差要求
为了保证工件形位公差符合设计要求,在加工过程中,要求检测重要的形位公差要求,如回转性工件的同轴度 等。未明确要求的形位公差按照GB1184-1996的K级精度检脸。
直线度和平面度
表5绐出了直线度和平面度的未注公差值。在表7中选取公差值时,对于直线度应按其相应的长度选择;对 于平面度应按其表面的较长一侧或圆表面的直径选择。
IPQC作业规范

IPQC作业规范一、目的:通过IPQC首检和巡检预防生产线批量性品质事故发生,提高生产线品质水平。
二、适用范围:三、作业流程1.首件检查作业:1.1 首件检查作业时机:当新产品首次批量试产、老产品空拉下机、老产品机型转换、新材料试用、工程更改时,生产线应及时填写《转拉通知单》知会IPQC作首检,如有新材料、工程更改等需注明。
1.2IPQC首件检查项目:IPQC首件检查的项目包括工艺、材料、人员、仪器设备(夹具),IP QC接到《转拉通知单》后开始做首件检查工作。
针对要首件检查的机型,从下拉开始,检查每个工位的工艺、物料、特殊工位的人员、仪器设备是否符合要求。
产品流到哪里,IPQC就跟到哪里。
1.2.1 工艺核对:有无挂作业指导书,工序排位,操作是否符合作业指导书要求及有效《工程指导书》,对于关键工位需严格确认相关品质要求是否执行到位。
1.2. 2 物料核对:检验核对物料应尽可能提前,保证BOM清单,IQC PASS贴,实际物料三者一致。
对于部件需确认关的品质点,例如:原材料的生产厂家、塑胶组件是否放置2个小时以上,连板的版本号等,针对关键物料、特采物料需重点跟踪。
检查核对物料要在投产以前完成,如遇到急转拉,不能提前核对时就把BOM单(样板)等拿到线上一件一件核对,在核对物料时,严格以BOM清单为参照标准,如果BOM清单不是最新版本,需查相应的ECO和EIN更改。
部件加工组IPQC需要对辅料每周检查,确认辅料的有效期、规格、使用点。
同种物料外箱上标注的进料日期是否一致(或接近),如不一致要看是新进物料还是库存物料,如是仓库库存物料,则要特别注意过程中有无品质异常。
IPQC需对有机溶剂进行确认。
1.2.3 人员核对:特殊工位的员工是否具有《上岗实习证》或《上岗合格证》,关键工位的员工是否了解该工位的品质控制点。
1.2.4 样板仪器夹具核对:确认有合格的首件样板,当发生物料及工艺变更时,IPQC需对样板及时更新,IPQC在转拉时用首件样板核对工艺、物料,用首件样板核对插件方式,内部加工工艺,结构等与样板一致(此项适用于插件波峰项目)。
FFC
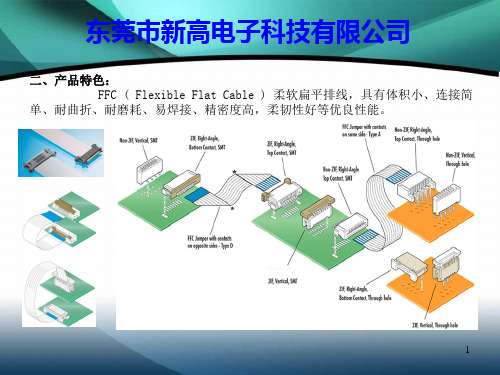
东莞市新高电子科技有限公司
十、检测实验仪器设备图; (机械特性)
11、自动插拔力机--延伸率测试: 确保产品的延伸率能达到行业标准要求。
30
东莞市新高电子科技有限公司
十、检测实验仪器设备图; (环境实验)
12、 耐高温性试验: 通过设定机器的温度和时间,来验证产品在指定的,
东莞市新高电子科技有限公司
二、产品特色: FFC ( Flexible Flat Cable ) 柔软扁平排线,具有体积小、连接简
单、耐曲折、耐磨耗、易焊接、精密度高,柔韧性好等优良性能。
1
东莞市新高电子科技有限公司
三、產品应用领域: 计算机、数码相机、打印机、复印机、扫描仪、影像机、
视听设备、通讯、MP3、显示器等各領域的电子产品。
四、生产规格: 有Pitch0.3mm、Pitch0.5mm、Pitch0.8mm、Pitch1.0mm、Pitch1.25mm、
Pitch1.5mm、Pitch 2.0mm、Pitch2.54mm,EMI导电铝箔、铜箔、聚酯胶带、折线、 LVDS、汽车安全气囊线等。
2
东莞市新高电子科技有限公司
五、FFC产品标准类型;
P 2.54±0.2
9
东莞市新高电子科技有限公司
七、产品标准公差(单位:mm);
4、常用导体规格
序号
导体规格
01
0.035 ╳ 0.30
02
0.035 ╳ 0.65
03
0.035 ╳ 0.70
04
0.035 ╳ 0.80
05
0.05 ╳ 0.30
06
0.05 ╳ 0.65
07
0.05 ╳ 0.70
实施权 责单位
制程作业流程及方法培训-IPQC培训1

变更事项、IPQC项目审核
记录保存
IPQICP检QC验检、I验P处Q、理C技检流能验程、、处处理理流流程程
朗驰欣创
首件异常处理
首件 异常
如生产单位对 IPQC判定有争 议请QE或品质 主管确认,依 QE确认为准
产品品质异常处理
出现有差异的 需复测一次
异常提出
核对样品及资料
将首件资料 及样品退回
朗驰欣创
IPQC 培训资料 品质部 houyuhui
IPQC检验、技能、处理流程
朗驰欣创
IPQC-制程品质检验
• I ---------- Inspect(检查、检验) • P --------- Process(过程、步骤) • Q --------- Quality(品质、质量) • C --------- Control(控制、管控)
IPQICP检QC验检、I验P处Q、理C技检流能验程、、处处理理流流程程
朗驰欣创
制程控制,是指产品从物料投入生产到产品最终包装 过程的品质控制。
• 2)巡回检验 巡回检验就是检验工人按一定的时间间隔和路线,依次到工作地或生产 现场,用抽查的形式,检查刚加工出来的产品是否符合图纸、工艺或检 验指导书中所规定的要求。在大批大量生产时,巡回检验一般与使用工 序控制图相结合,是对生产过程发生异常状态实行报警,防止成批出现 废品的重要措施。当巡回检验发现工序有问题时,应进行两项工作: 一、是寻找工序不正常的原因,并采取有效的纠正措施,以恢复其正常 状态; 二、是对上次巡检后到本次巡检前所生产的产品,全部进行重检和筛选 ,以防不合格品流入下道工序(或用户) 。 巡回检验是按生产过程的时间顺序进行的,因此有利于判断工序生产状 态随时间过程而发生的变化,这对保证整批加工产品的质量是极为有利 的。为此,工序加工出来的产品应按加工的时间顺序存放,这一点很重 要,但常被忽视 。
IPQC巡检规范1

IPQC巡检规范一. 目的:确保生产过程和过程中的检验符合产品规范要求,并受到合理的控制,以保障产品的质量,提高巡检员工的操作规范。
二. 使用范围:适用于飞安瑞公司所有的生产过程及过程中的检验。
三. 使用依据:《产品工艺外观检验标准》、《产品规格书》及国标GB-2828.1-2003。
四. 品管中英文表示:4.1 IPQC(In Process Quality Control)-制程巡检4.2 IQC( In Coming Quality Control)—进料检验4.3 FQC(Final Quality Control)—最终品质检验4.4 OQC(Outgoing Quality Control)--出货检验4.5 SQA(Supply Quality Audit)--供应商品质稽核4.6 QA(Quality Assurance)---品质保证4.7 QE(Quality Engineering)-----品质工程4.8 QCC(Quality Control Circle)---品管圈4.9 TQM(Total Quality Manage)---全面品质经营4.10 TQC(Total Quality Control)-----全面品质经营4.11 SPC(Statistics Process Control)----统计制程管制4.12 COQ(Cost Of Quality)----品质成本4.13 AQL(Accept Quality Control)---允收品质水准五. 职责:5.1 IPQC:每2小时巡检全部程序内容一次、跟踪问题,对产品的首件及产品的生产过程工艺负责,具体操作过程及作业内容如6作业内容;5.2 生产主管:处理的作业员工的违反操作、标识、物料摆放等问题;5.3产品工程师:负责处理作业指导书、流程、设备测试、校验、维护等一切与生产工艺有关的问题;5.4 品质工程主管:全面负责所有巡检内容有关问题的确认。
煮蛋器成品检验作业指导书

煮蛋器成品检验作业指导书煮蛋器成品检验作业指导书(第1篇)一、引言煮蛋器是一种常见的厨房电器,用于煮蛋。
为了确保煮蛋器的质量和安全性能,每一台煮蛋器出厂前都需要经过严格的检验。
本文将详细介绍煮蛋器成品检验的步骤和要求,以确保产品的质量和安全性。
二、检验环境和工具要求1.检验环境:检验环境应保持整洁,无杂物和其他干扰因素。
室温应在20-25摄氏度之间,相对湿度应控制在50%-70%之间。
2.检验工具:常用的检验工具包括电器测试仪器、计量仪器、外观检测工具等。
所选工具应与检验要求相匹配,并保证其精确度和可靠性。
三、外观检验1.检查外壳:检查煮蛋器的外壳是否完整、无损坏、无变形等情况。
2.检查控制面板:检查控制面板的按钮和指示灯是否正常、灵敏,无损坏和错位现象。
3.检查插座和电源线:检查插座和电源线是否完好无损,无暴露的电线和断裂现象。
4.检查其他外观件:检查煮蛋器的其他外观件,如锅、蛋架等,是否符合要求,无损坏和变形现象。
四、性能检验1.加热性能检验:(1)连接电源后,将适量水放入煮蛋器中,按下加热按钮,观察煮蛋器的加热情况。
正常情况下,煮蛋器应迅速加热,并保持水温在适宜范围内。
(2)使用温度计检测加热过程中的水温变化。
水温应在加热完成后迅速升高,保持在设定的温度范围内。
2.定时功能检验:(1)将煮蛋器设定为不同的时间模式,进行定时功能的检验。
时间模式设置应准确可靠。
(2)使用计时器检测定时过程的误差。
定时误差应在可接受的范围内。
3.安全性能检验:(1)接通电源后,检测煮蛋器的外壳、插座和电源线是否正常,无电击危险。
(2)检验煮蛋器的过热保护功能和断电保护功能,确保使用过程中的安全性。
五、记录和报告1.记录检验结果:将每台煮蛋器的检验结果记录在检验记录表中。
包括外观检验结果、性能检验结果、安全性检验结果等。
2.制作检验报告:根据检验记录,制作煮蛋器的检验报告。
报告应准确详实,包括检验日期、检验人员、检验结果等。
QC巡检&首件规范 (1)

深圳市XXX电子有限公司QC巡检&首件规范版本/版次:A/0总 页 数:共 8页文件编号 :生效日期 :区分制定审核核准发行印章签名修订记录二级文件生效日期制定/修订日期 修 订 内 容 摘 要 页次 版本/版次 总页数 2023-3-9 新制订 -- A/0 51、目的二级文件生效日期规范QC对制程的巡检过程,确保公司的生产制程过程,在有效的管制状态下稳定地进行,生产出满足品质要求及客户要求的产品。
2、适用范围本程序适用于与适用于公司制程全过程。
3、定义IPQC:(In-Process Quality Control)制造过程质量控制。
SOP:(Standard Operation Procedure)即标准作业程序。
4、工作程序4.1 QC每班必须对生产首件进行检查确认:4.1.1 QC每班必须按BOM核对物料的规格与描述使用是否正确;4.1.2 QC需确认机型的软件、配色、TAC是否正确;4.1.3 QC对于首件的过程与结果负责。
从物料、操作、QA的首件检测结果都属于QC的监察范围。
4.1.4 QC对点胶或热泥胶进行称重确认点胶的胶量和胶路是否合格.4.2 QC每天需要对产线的生产设备及ESD防护进行检查:4.2.1 QC每班需要对设备和静电环的点检记录进行核查,并将检查结果记录在《QC制程巡检表》中;4.2.2 QC每班需监督生产部对电烙铁温度和电批扭力的点检情况,并将检查结果记录在《QC制程巡检表》中;4.3 QC每天需要根据生产工艺文件中要求,依照生产工艺文件中细则对产线的工艺纪律进行考核,并将考核结果记录在《QC制程巡检表》中。
4.4 QC每班至少监察产线制程四次,检查各工位员工是否严格依照SOP要求进行操作,并将监察结果记录于《QC制程巡检表》。
4.5物料/产品的标识与摆放监察:4.5.1 物料摆放必须正确,叠放层数不能超出原包装叠放的层数,防止物料受压后导致损坏元器件;4.5.2 半成品摆放必须正确, 叠放层数不能超过8层(60pcs/箱),防止单机头受压后导致外观或功能故障;4.5.3 工位如出现堆机或有半成品,必须有状态标识来区分不同;4.5.4 焊接工位不能将PCBA摆放于电烙铁架与操作工位之间,预防电烙铁嘴的锡渣掉落于PCBA上;4.5.5 QC检测工位,必须对不合格品进行状态标识,并有专用的存放区域,防止因摆放混乱而导致未测试或不良品作为良品流入下一工序。
- 1、下载文档前请自行甄别文档内容的完整性,平台不提供额外的编辑、内容补充、找答案等附加服务。
- 2、"仅部分预览"的文档,不可在线预览部分如存在完整性等问题,可反馈申请退款(可完整预览的文档不适用该条件!)。
- 3、如文档侵犯您的权益,请联系客服反馈,我们会尽快为您处理(人工客服工作时间:9:00-18:30)。
c. 经QC抽检合格的产品,由生产部送往老化房进行老化,老化后再经全检QC进行外观、功能检验并将检查和测试结果填写在《QC制程检验报表》中。
d. 全检QC检查和测试合格产品送QA进行抽样检验,QA抽检不良时按照《QA出货检验作业规范》
c. 首件检验合格,品管部IPQC将其结果写在《首件检验报告》/《SMT首件确认表》上,将《首件检验报告》交工程部PE工程师或以上部门负责人进行确认审核,最后由品管主管或经理核准方可批量生产。
d. 品管部IPQC在合格首件上注明S字样(S代表Sample)并签名确认,并将合格首件置于生产现场QC工作台前首件盒中,并附上填写完整的《首件标签》,作为生产部生产和检验的重要依据.该生产工单完成后可作为合格品一同转入下一道工站或出货,不予保存。
高压不良
0
老化合格率
≥99.8%
全检组外观检验合格率
≥99.5%
全检组性能测试合格率
≥99.8%
成品QA抽检批次合格率
适配器≥99.8%电源板≥98.2%
d.当IPQC检验员在巡回检验中,发现不良率达到《制程品质异常停线管理规范》定义的制程警示不良时,则发出《异常矫正通知单》经品管部经理批准后转至工程部分析原因,责任部门回复改善措施,IPQC跟踪验证改善效果;开出《异常矫正通知单》后,生产部在回复2小时内还是没有改善,且达到停线定义不良率时,则开出《停线报告书》进行停线整顿,按照《制程品质异常停线管理规范》要求处理。
f.品管部QE召集生产、品管、PMC、工程等部门责任人员,对生产线的制程异常在生产例会上进行检讨,由责任部门提出改善方案,QE跟进改善结果,并进行结果通报。
5.2.3定点检验:
a. 品管部应按照作业指导书上规定要求,在生产过程中必须设置插件外观QC、补锡后焊外观QC、高压
测试QC和性能测试QC进行定点检查和测试,并将检查和测试结果记录在《QC制程检验报表》中。
2、范围
适用于生产过程中所有产品(在制品、半成品和成品)的检验和测试。
3、定义
IPQC—In-Process Quality Control 巡回检验(制程品质管控)。
4、职责
品管部: 负责对制程检验工作执行和监督,是制程检验的归属责任部门。
生产部: 确保按工艺文件(SOP)要求进行生产并及时对不良品的标识、隔离和处置。
要求处理.
5.2.4自检和互检:
a. 生产部的作业人员必须按照作业指导书进行作业,并依据相应的作业指导书上的品质要求,对自己的作业方法和产品进行检查。
b. 生产部的作业人员在自检的同时,还必须对上一道工序流下来的产品进行检查.确保合格的产品方可进入下一道工序。
c. 自检和互检时发现严重不良或同一问题连续出现3次, 生产部的作业人员应立即向生产线负责人或品管部IPQC报告,生产线负责人或工程部PE需及时去分析处理,并上报给生产部或品管部负责人。
□PMC部(PMC)
□市场中心
□PMC部(货仓)
□人力资源中心
□生产部(DIP车间)
□工程部
□生产部(SMT车间)
■品管部(品管)
3份
□生产部(磁电车间)
□品管部(体系)
□采购中心
【文件签收见“文件发放、回收登记表”】
受控发行印章:
重庆XX电子有限公司
文件编号
QAWI-A-003
版次/状态
B/7--受控
B/5
5
6.2.2增加SMT、磁电管控质量目标
B/6
3
修改5.2.2.C波峰焊焊点目标值和成品抽检批合格率按类别分定义
B/7
5
1.修改5.2.1对制程控制目标进行分解
2.对5.2.5超声产品巡检的要求进行细化
1、目的
为了规范制程检验作业过程,确保生产过程中产品的检验和测试得以有效控制,保证生产过程中产品质量符合相关的标准和要求。
c. 品管部IPQC根据各制程重点工序(外观检查、高压、超声和性能测试等)上的品质状况,增加对各个重点工序的巡检和抽检频次。
d.超声模具调好后,由工程技术人员提供2PCS合格品给IPQC做跌落试验,以验证超声产品的结构牢
固度,试验方法按照《超声产品单体跌落测试作业指导书》操作。
f.IPQC每二小时做一次跌落试验,将试验结果记录于《超声产品跌落测试记录表》中。跌落的产品要经IPQC确认,判定标准按《超声产品单体跌落测试作业指导书》要求执行,如有跌落异常的产品按《制程品质异常停线管理规范》要求处理;另外跌落品无起铜皮、脱胶松动、变形等不良,跌落的产品要进行报废处理。
b. 品管部IPQC依据生产实际状况,最少1次/每2小时对各工序的作业流程和生产的产品进行巡检,检验依据:按作业工位的SOP要求。
c. 品管部检验员在巡回检验中依以下“制程控制目标”进行管控,当发现不良率超出目标值但没到达到《制程品质异常停线管理规范》定义的制程警示时不良时,应第一时间口头通知该线拉长或生产部主管改善并跟踪确认其改善效果,生产部负责人须立即采取相应的措施予以纠正。制程控制目标如下:
制程控制项目
目标值
SMT直通率
≥99%
SMT抛料率
≤0.3%
SMT QA抽检批合格率
≥99%
磁电直通率
≥98%
磁电QA抽检批合格率
≥99%
插件外观目检合格率
≥99%
波峰焊焊点不良率
TOPOW≤4000PPM加工单≤8000PPM
后焊外观目检合格率
电源板≥96%适配器≥98%
DIP性能测试合格率目标
≥99%
5.2.5重点工序检验:
a. 品管部QC根据工艺文件上规定的工序控制点或质量控制点,对其进行重点管控,要求和方法可按工艺文件上规定执行.
b. 品管部QC在重点工序检验中发现工序的控制参数发生不正常的偏移或超差时,需及时通知生产部负责人或工程部PE工程师, 生产部负责人或工程部PE工程师根据情况作相应调整和改善。
文件名称
制程检验作业规范
生效日期
页码
1/5
修订记录
发行版本
页数
修订内容简述
制定/修订人
修订日期
A/1
3
首次发行
B/1Байду номын сангаас
4
增加修订页及内容修改
B/2
5
增加制程控制指标
B/3
5
增加制程控制目标值、增加超声和拆壳检验规定
B/4
5
1.增加SMT/DIP工序IPQC将PCB板贴片时间作为管控项目之一
2.增加SMT抛料率目标、全检验目标
重庆XX电子有限公司
制程检验作业规范
文件编号
QAWI-A-003
版次/状态
B/7--受控
文件归属部门
品管部
生效日期:
拟定:
职位:QE
签署:
日期:
审核:
职位:主管
签署:
日期:/
批准:
职位:品管部经理
签署:
日期:
文件分发/签收:
文件签收/发放部门:
部门/单位
份数
部门/单位
份数
电子档
纸档
电子档
纸档
□研发中心
5.3 生产过程检验与测试的所有使用的检测设备依据《监视与测量设备控制程序》规定执行作业。
5.4过程中产品检验状态标识具体依《产品标识与可追溯性控制程序》规定实施。
5.5记录保存
本规范发生的记录,其保存期限以《受控文件一览表》中规定的期限为准。
6、相关文件:
《纠正和预防措施控制程序》 TP-QP-807
5.2.1首件检验
a. 首件检验执行时机:
A、 每天开线时; B、 产品机型转换时;
C、 产品换线时; D、 产品变更(工艺或材料)时。
b. 在生产过程中,新产品生产部提前做好2PCS首件,旧产品生产部抽取最初过炉的2PCS产品作为首件,1PCS交品管部核对材料、工艺,1PCS交工程部检测性能,确保首件产品所使用的物料、工艺和测试方法的正确性。
e. 当首件检验不合格时,品管部IPQC将检验结果填写在《首件检验报告》上,并将不合格首件和《首件检验报告》交工程部PE工程师进行分析、确认,并开出《异常矫正通知单》最后由品管部主管或经理核准确认后,由责任部门回复纠正、预防措施,IPQC跟进异常回复处措施是否有效,并予以关闭结案。
f. 不合格首件由生产相关责任人确认后,生产部相关责任人需进行分析改善,品管部IPQC进行跟踪处理。生产部分析改善后需要重新送首件检验,直到首件检验合格后方可进行批量生产。
7、相关记录
《首件检验报告》 QAQR004
《SMT首件确认表》 QAQR006
《IPQC巡检报告》 QAQR003
《SMT IPQC稽核表》 QAQR005
《QC制程检验报表》 QAQR011
《异常矫正通知单》QAQR012
《超声产品跌落测试记录表》 QAQR047
《磁电部内部QC稽核确认表》 TDQR051
《产品的监视和测量控制程序》 TP-QP-803
《记录控制程序》TP-QP-402
《不合格品控制程序》 TP-QP-804
《产品标识与可追溯性控制程序》 TP-QP-709
《抽样计划规定》 QAWI-A-005
《适配器/主板QC工程图》 QAWI-A-043/046
《超声产品单体跌落测试作业指导书》 TPQASP0006
5.2.2巡回检验:
a. 品管部IPQC依据制程检验规范、物料清单(BOM)、工艺标准、产品工艺流程图、QC工程图等资料对生产过程中各工序作业方式和品质状况、生产现场物料、7S等状况巡回检验.并将巡回检验和测试结果记录在《IPQC巡检报告》/《SMT IPQC稽核表》中,SMT/DIP工序IPQC将PCB板贴片时间作为管控项目之一,时间要求如下:OSP板拆包后24H内必须打贴片过回流焊,贴片后 168H内必须过波峰炉,SMT QA抽检合格后在《成品标签》上注明检验合格时间,便于DIP进行时间管控.