乐泰SMT的工艺
SMT生产工艺
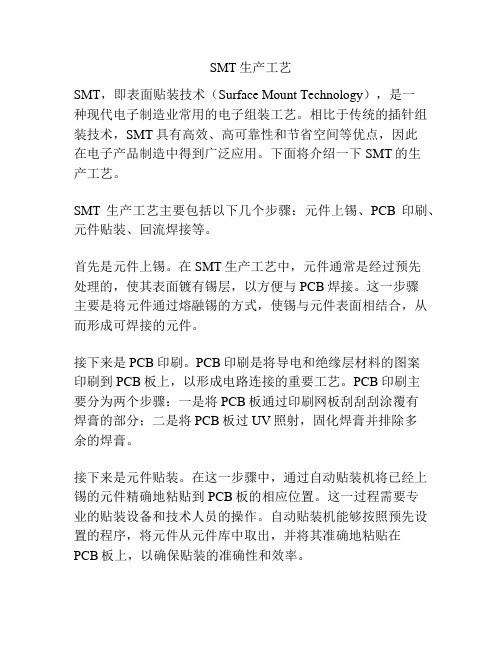
SMT生产工艺SMT,即表面贴装技术(Surface Mount Technology),是一种现代电子制造业常用的电子组装工艺。
相比于传统的插针组装技术,SMT具有高效、高可靠性和节省空间等优点,因此在电子产品制造中得到广泛应用。
下面将介绍一下SMT的生产工艺。
SMT生产工艺主要包括以下几个步骤:元件上锡、PCB印刷、元件贴装、回流焊接等。
首先是元件上锡。
在SMT生产工艺中,元件通常是经过预先处理的,使其表面镀有锡层,以方便与PCB焊接。
这一步骤主要是将元件通过熔融锡的方式,使锡与元件表面相结合,从而形成可焊接的元件。
接下来是PCB印刷。
PCB印刷是将导电和绝缘层材料的图案印刷到PCB板上,以形成电路连接的重要工艺。
PCB印刷主要分为两个步骤:一是将PCB板通过印刷网板刮刮刮涂覆有焊膏的部分;二是将PCB板过UV照射,固化焊膏并排除多余的焊膏。
接下来是元件贴装。
在这一步骤中,通过自动贴装机将已经上锡的元件精确地粘贴到PCB板的相应位置。
这一过程需要专业的贴装设备和技术人员的操作。
自动贴装机能够按照预先设置的程序,将元件从元件库中取出,并将其准确地粘贴在PCB板上,以确保贴装的准确性和效率。
最后是回流焊接。
回流焊接是将已粘贴好的元件通过高温热风或红外线加热,使焊膏熔化,与PCB板上的焊盘相结合。
在这一过程中,焊膏的熔化和冷却时间需要严格控制,以确保焊接质量。
回流焊接后,需要对焊接的质量进行检测,以确保焊接的可靠性。
除了以上的基本步骤之外,SMT生产工艺还包括一系列的辅助工艺。
例如,元件质量检查、元件的自动识别和补位等。
这些辅助工艺的目的是确保SMT生产过程中的质量和效率。
总的来说,SMT生产工艺是现代电子制造业中的重要工艺之一。
通过上锡、PCB印刷、元件贴装和回流焊接等步骤,可以实现高效、高质量的电子产品制造。
随着科技的不断发展,SMT生产工艺也在不断优化和改进,在提高生产效率的同时,也能够满足不同需求的产品质量要求。
smt车间生产工艺 流程
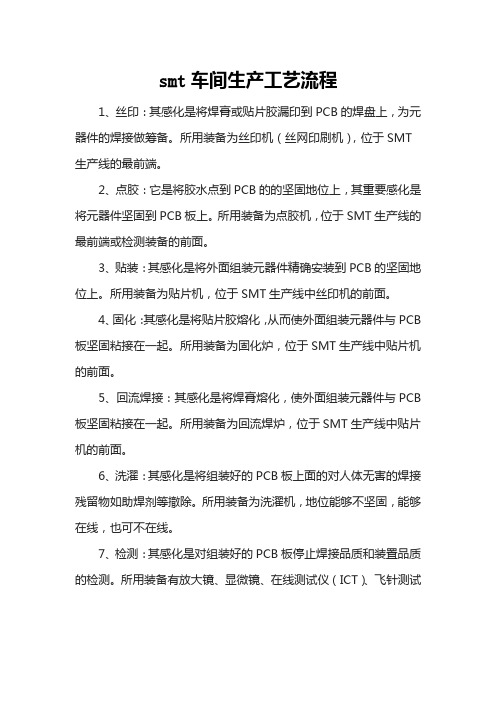
smt车间生产工艺流程
1、丝印:其感化是将焊膏或贴片胶漏印到PCB的焊盘上,为元器件的焊接做筹备。
所用装备为丝印机(丝网印刷机),位于SMT 生产线的最前端。
2、点胶:它是将胶水点到PCB的的坚固地位上,其重要感化是将元器件坚固到PCB板上。
所用装备为点胶机,位于SMT生产线的最前端或检测装备的前面。
3、贴装:其感化是将外面组装元器件精确安装到PCB的坚固地位上。
所用装备为贴片机,位于SMT生产线中丝印机的前面。
4、固化:其感化是将贴片胶熔化,从而使外面组装元器件与PCB 板坚固粘接在一起。
所用装备为固化炉,位于SMT生产线中贴片机的前面。
5、回流焊接:其感化是将焊膏熔化,使外面组装元器件与PCB 板坚固粘接在一起。
所用装备为回流焊炉,位于SMT生产线中贴片机的前面。
6、洗濯:其感化是将组装好的PCB板上面的对人体无害的焊接残留物如助焊剂等撤除。
所用装备为洗濯机,地位能够不坚固,能够在线,也可不在线。
7、检测:其感化是对组装好的PCB板停止焊接品质和装置品质的检测。
所用装备有放大镜、显微镜、在线测试仪(ICT)、飞针测试
仪、主动光学检测(AOI)、X-RAY检测系统、功效测试仪等。
地位依据检测的必要,能够配置在生产线适合的处所。
8、返修:其感化是对检测呈现毛病的PCB板停止返工。
所用对象为烙铁、返修工作站等。
配置在生产线中随意率性地位。
SMT的工艺
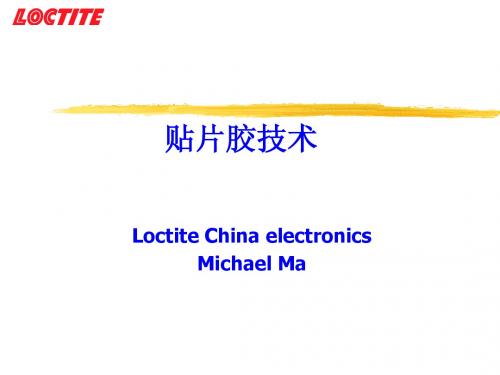
: 40mm/sec : 4N/cm2 : 1.0mm : 0.1mm/sec
点胶量
接着点 胶点 ADHESIVE DOT A
METALLIZATION
SMD
B
C
焊盘
C > A+B
- 80%焊盘之间的面积
-
胶点宽高比在 2:1--- 4:1
移印点胶
选择贴片胶考虑因素
1. 施胶方法 点胶/ 压力时间速度 ,印刷/压力速度 2. 固化 红外 3. 胶性能 流变性能,胶点形状,湿强度 4. 处理,修补性,耐高温性能 连接强度 5. 颜色
强度不足
温度曲线设置不当,固化不足 炉内温区不均匀,局部加热不足 阻焊膜附着强度不够 元件表面涂层附着不够 胶量不足 胶内有气泡 胶吸潮 胶设计强度偏低
气泡的产生
胶中混有气泡 PCB,元件和贴片胶均会吸潮 环境湿度过大,胶在空气中停留时间过长 控制胶在空气中停留时间 某些贴片胶固化时会有溶剂挥发(选择无溶剂的 贴片胶)
温度℃
时 间 (d s e c o n s )
固化温度曲线的测量
贴满元件的板 测量潜在的低温区 大元件PLCC或QFP附近 PCB边缘 每块PCB上测3-5个点, 定期检查
针筒点胶
时间压力点胶
P u i es r s T S m P IIN er mt se y R O E C S 时间压力系统e 精密调节
实现胶着强度
流变性改性剂
决定点胶性能和湿强度
颜料
与线路板有明显的对比度
填充料
接近线路板与元件的热膨胀
贴片胶的流变性
屈服值 Yield Point 点胶初始气压 湿强度 触变性 Thixotropy 点胶性 胶点形状
SMT工艺流程及各流程分析介绍
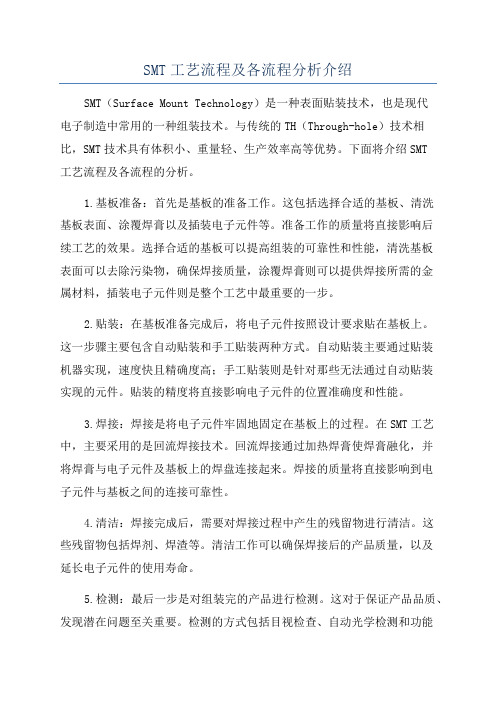
SMT工艺流程及各流程分析介绍SMT(Surface Mount Technology)是一种表面贴装技术,也是现代电子制造中常用的一种组装技术。
与传统的TH(Through-hole)技术相比,SMT技术具有体积小、重量轻、生产效率高等优势。
下面将介绍SMT工艺流程及各流程的分析。
1.基板准备:首先是基板的准备工作。
这包括选择合适的基板、清洗基板表面、涂覆焊膏以及插装电子元件等。
准备工作的质量将直接影响后续工艺的效果。
选择合适的基板可以提高组装的可靠性和性能,清洗基板表面可以去除污染物,确保焊接质量,涂覆焊膏则可以提供焊接所需的金属材料,插装电子元件则是整个工艺中最重要的一步。
2.贴装:在基板准备完成后,将电子元件按照设计要求贴在基板上。
这一步骤主要包含自动贴装和手工贴装两种方式。
自动贴装主要通过贴装机器实现,速度快且精确度高;手工贴装则是针对那些无法通过自动贴装实现的元件。
贴装的精度将直接影响电子元件的位置准确度和性能。
3.焊接:焊接是将电子元件牢固地固定在基板上的过程。
在SMT工艺中,主要采用的是回流焊接技术。
回流焊接通过加热焊膏使焊膏融化,并将焊膏与电子元件及基板上的焊盘连接起来。
焊接的质量将直接影响到电子元件与基板之间的连接可靠性。
4.清洁:焊接完成后,需要对焊接过程中产生的残留物进行清洁。
这些残留物包括焊剂、焊渣等。
清洁工作可以确保焊接后的产品质量,以及延长电子元件的使用寿命。
5.检测:最后一步是对组装完的产品进行检测。
这对于保证产品品质、发现潜在问题至关重要。
检测的方式包括目视检查、自动光学检测和功能性测试等。
通过检测可以及时发现问题并进行修复,避免对整个批量产品造成影响。
综上所述,SMT工艺流程包括基板准备、贴装、焊接、清洁和检测。
每个步骤都十分重要,对整个工艺流程的质量与效果有着直接影响。
合理的工艺流程可以提高生产效率、减少成本、提高产品质量,因此,企业在实施SMT工艺时应注重每个步骤的细节,确保每个环节的顺利进行。
SMT生产工艺流程

SMT生产工艺流程SMT(表面贴装技术)是一种电子元器件的组装技术,其生产工艺流程主要包括PCB制板、元器件采购、元器件贴装、回流焊接和测试等环节。
下面我将详细介绍SMT生产工艺流程。
首先,是PCB制板。
在SMT生产工艺中,先需要制作出一块贴片式电路板(PCB),PCB是一个带有电路图案的基础板,它上面有铜贴面,上面用来贴SMT元器件。
第二步是元器件采购。
在SMT生产过程中,必须准备和购买足够数量的元器件。
根据生产计划,根据元器件清单准备好所需的SMT元器件,确保元器件供应的及时和准确。
第三步是元器件贴装。
在这一步骤中,需要使用SMT贴装机将元器件贴到PCB上。
贴装机具有自动化功能,可以准确、高效地将元器件粘贴到PCB上。
第四步是回流焊接。
在SMT生产过程中,回流焊接是将元器件固定在PCB上的关键步骤。
通过回流焊接炉,使焊膏熔化,将元器件与PCB连接在一起。
第五步是测试。
测试是确保生产的电路板质量的重要步骤。
通常使用AOI(全自动光学检测)和ICT(嵌板测试)等设备进行测试,确保电路板无短路、无虚焊等质量问题。
最后,进行包装。
在电子产品组装完成之后,需要对其进行包装,以保护电子产品不受损坏。
常见的包装方式包括真空包装、防尘袋、纸箱等。
除了上述的基本流程外,SMT生产过程还需要考虑质量控制、工艺优化和设备维护等因素。
其中质量控制是确保生产质量和产品可靠性的关键,包括质量控制人员的专业要求、过程参数的控制和不断优化等方面。
综上所述,SMT生产工艺流程是一个复杂而又精细的过程,需要充分考虑生产计划、元器件采购、元器件贴装、回流焊接、测试和包装等环节,同时也需要重视质量控制、工艺优化和设备维护等因素。
通过合理优化和控制各个环节,可以提高生产效率、降低生产成本,提升产品质量和可靠性。
SMT 工艺流程介绍 (十个步骤)

SMT工艺流程介绍十个步骤目录第一步:制程设计 (3)第二步:测试设计 (8)第三步:焊锡材料 (14)第四步:印刷 (19)第五步:黏着剂/环氧基树脂和点胶 (23)第六步:组件着装 (29)第七步:焊接 (33)第八步:清洗 (38)第九步:测试与检验 (42)第十步:重工与整修 (48)第一步:制程设计表面黏着组装制程,特别是针对微小间距组件,需要不断的监视制程,及有系统的检视。
举例说明,在美国,焊锡接点质量标准是依据IPC-A-620及国家焊锡标准ANSI / J-STD-001。
了解这些准则及规范后,设计者才能研发出符合工业标准需求的产品。
量产设计量产设计包含了所有大量生产的制程、组装、可测性及可靠性,而且是以书面文件需求为起点。
一份完整且清晰的组装文件,对从设计到制造一系列转换而言,是绝对必要的也是成功的保证。
其相关文件及CAD数据清单包括材料清单(BOM)、合格厂商名单、组装细节、特殊组装指引、PC板制造细节及磁盘内含Gerber数据或是IPC-D-350程序。
在磁盘上的CAD数据对开发测试及制程冶具,及编写自动化组装设备程序等有极大的帮助。
其中包含了X-Y轴坐标位置、测试需求、概要图形、线路图及测试点的X-Y坐标。
PCB品质从每一批货中或某特定的批号中,抽取一样品来测试其焊锡性。
这PC板将先与制造厂所提供的产品数据及IPC上标定的质量规范相比对。
接下来就是将锡膏印到焊垫上回焊,如果是使用有机的助焊剂,则需要再加以清洗以去除残留物。
在评估焊点的质量的同时,也要一起评估PC板在经历回焊后外观及尺寸的反应。
同样的检验方式也可应用在波峰焊锡的制程上。
组装制程发展这一步骤包含了对每一机械动作,以肉眼及自动化视觉装置进行不间断的监控。
举例说明,建议使用雷射来扫描每一PC板面上所印的锡膏体积。
在将样本放上表面黏着组件(SMD) 并经过回焊后,品管及工程人员需一一检视每组件接脚上的吃锡状况,每一成员都需要详细纪录被动组件及多脚数组件的对位状况。
SMT工艺流程及各流程分析介绍

SMT工艺流程及各流程分析介绍摘要SMT(Surface Mounted Technology)是一项综合的系统工程技术,其涉及范围包括基板、设计、设备、元器件、组装工艺、生产辅料和管理等。
随着SMT 技术的产生、发展,SMT在90年代得到迅速普及,并成为电子装联技术的主流。
其密度化,高速化,标准化等特点在电路组装技术领域占了绝对的优势。
对于推动当代信息产业的发展起了重要的作用,并成为制造现代电子产品必不可少的技术之一。
本论文以具体实践岗位为基础,详细讨论了SMT技术的工艺流程以及各流程的分析等相关内容。
它大大节省了材料、能源、设备、人力、时间等,不仅降低了成本,还提高了产品性能和生产效率,还给人们的生活带来了越来越多的便捷和享受。
关键词:SMT技术工艺流程介绍分析AbstractSMT(Surface Mounted Technology)technology is a synthetic system .It involves ranges have substrate,devise,equipment,component, packaging technology, Production Auxiliary Materials and management .Along with the SMT technology generation and development, SMT obtains the news fast development and the popularization in the 90s, and becomes the electronic attire to unite technical the mainstream. Its density, the high speed, characteristics and so on standardization have occupied the absolute superiority in the electric circuit packaging technique domain. Regarding the impetus message of today industry's development vital role, and became one of manufacture modern electronic products essential technologies. At present, it already soaked each profession, each domain, the application is very widespread.The present paper take the concrete practice post as a foundation, discussed the SMT technology technical process in detail and the process analysis and so on related content.It has saved the material, the energy, the equipment, the manpower, the time greatly and so on, not only reduced the cost, but also enhanced the product performance and the production efficiency, gave back to people's life to bring more and more convenient and enjoys.Key words:SMT technology,Technical process,introduce and analysis. (1).流程框图:(2).SMT流程介绍:由于SMA有单面安装和双面安装,元器件有全部表面安装及表面安装与通孔插装的混合安装;焊接方式可以是再流焊、波峰焊、或两种方法混合使用,目前采用的方式有几十种之多,下面仅介绍通常采用的几种形式。
SMT工艺流程报告
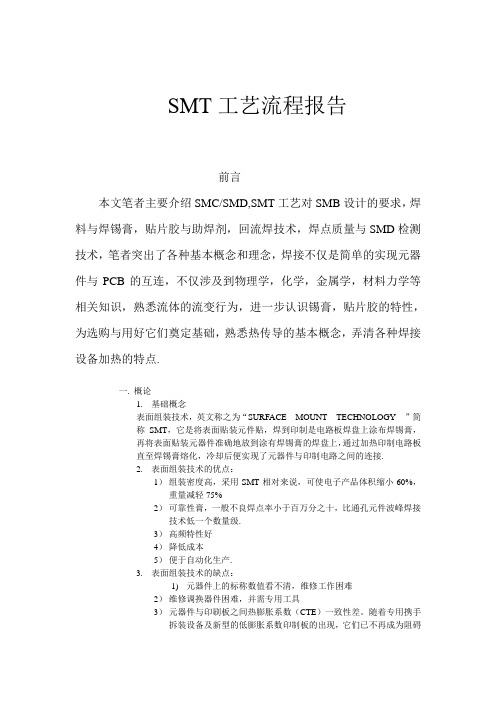
SMT工艺流程报告前言本文笔者主要介绍SMC/SMD,SMT工艺对SMB设计的要求,焊料与焊锡膏,贴片胶与助焊剂,回流焊技术,焊点质量与SMD检测技术,笔者突出了各种基本概念和理念,焊接不仅是简单的实现元器件与PCB的互连,不仅涉及到物理学,化学,金属学,材料力学等相关知识,熟悉流体的流变行为,进一步认识锡膏,贴片胶的特性,为选购与用好它们奠定基础,熟悉热传导的基本概念,弄清各种焊接设备加热的特点.一.概论1.基础概念表面组装技术,英文称之为“SURFACE MOUNT TECHNOLOGY”简称SMT,它是将表面贴装元件贴,焊到印制是电路板焊盘上涂布焊锡膏,再将表面贴装元器件准确地放到涂有焊锡膏的焊盘上,通过加热印制电路板直至焊锡膏熔化,冷却后便实现了元器件与印制电路之间的连接.2.表面组装技术的优点:1)组装密度高,采用SMT相对来说,可使电子产品体积缩小60%,重量减轻75%2)可靠性膏,一般不良焊点率小于百万分之十,比通孔元件波峰焊接技术低一个数量级.3)高频特性好4)降低成本5)便于自动化生产.3.表面组装技术的缺点:1)元器件上的标称数值看不清,维修工作困难2)维修调换器件困难,并需专用工具3)元器件与印刷板之间热膨胀系数(CTE)一致性差。
随着专用携手拆装设备及新型的低膨胀系数印制板的出现,它们已不再成为阻碍SMT深入发展的障碍.4.表面组装工艺流程:SMT工艺有两类最基本的工艺流程,一类为锡膏回流焊工艺,另一类是贴片—波峰焊工艺.在实际生产中,应根据所用元器件和生产装备的类型以及产品的需求选择不同的工艺流程,现将基本的工艺流程图示如下:1)锡膏—回流焊工艺,该工艺流程的特点是简单,快捷,有利于产品体积的减小.2)贴片-波峰焊工艺,该工艺流程的特点是利用双面板空间,电子产品的体积可以进一步减小,且仍使用通孔元件,价格低廉,但设备要求增多,波峰焊过程中缺陷较多,难以实现高密度组装。
3)混合安装,该工艺流程特点是充分利用PCB板双面空间,是实现安装面积最小化的方法之一,并仍保留通孔元件价低的特点.4)双面均采用锡膏—回流焊工艺,该工艺流程的特点能充分利用PCB空间,并实现安装面积最小化,工艺控制复杂,要求严格,常用于密集型或超小型电产品,移动电话是典型产品之一.我们知道,在新型材料方面,焊膏和胶水都是触变性质流体,它们引起的缺陷占SMT总缺陷的60%,训练掌握这些材料知识才能保证SMT质量.SMT还涉及多种装联工艺,如印刷工艺,点胶工艺,贴放工艺,固化工艺,只要其中任一环节工艺参数漂移,就会导致不良品产生,SMT工艺人员必须具有丰富的工艺知识,随时监视工艺状况,预测发展动向.二.焊锡膏与印刷技术1.焊锡膏是将焊料粉末与具有助焊功能的糊状焊剂混合而成的一种浆料,通常焊料粉末占90%以左右,其余是化学成分.它是一个复杂的物料系统,制造焊锡膏涉及流体力学,金属冶炼学,有机化学和物理学等综合知识,1)对于焊锡膏一类的流体,由于大分子的长链结构和缠绕,或触变剂的存在,它们的流动行为远比低分子流体复杂得多,这类流体受外力作用时,剪切力和剪切速率不再成比例,液体的黏度不再是常数,其流动行为不服从流变学方程,因此在工程上将这类流体称为非与顿流体.2)焊锡膏在外受力的增加,焊膏的黏度迅速下降,但下降到一定程度后又开始稳定下来.即焊膏在印刷时,受到刮刀的推力作用,其黏度下降,当到达模板窗口时,黏度达到最低,故能顺利通过窗口沉降到PCB焊盘上,随着外力的停止,焊锡膏黏度又尽速回来.3)焊锡膏是由焊球粉末和糊状焊剂组成,焊球粉末的粒度一般控制在25UM-45UM,过粗的粉未会导导致焊膏黏结性能变差,而在糊状焊剂中,通常含有一定量的松香或其他树脂,它一是起增黏作用,二是防止在焊接过程中成膜焊料的二次洋化.4)黏度与焊锡膏涂布方法:一种是金属模板印刷,另一类是通过点胶机滴涂,这两类方法需要不同黏度的锡膏,其黏度范围如下表:5)焊膏的印刷性能:SMT大生产中,首先要求焊膏能顺利地,不停地通过焊膏漏板或分配器转到PCB上,如果焊膏的印刷性能不好,就会堵死漏板的孔眼,导致生产不能正常进行,其原因是焊膏中缺少一种助印剂或用量不足而引起的,合金粉未的形状差,粒径分布不符合要求也会引起印刷性能下降..6)焊膏的黏结力:焊膏印刷后放置一段时间(8H)仍能保持足够的黏性是必需的.7)焊膏的塌落度:是描述焊膏印到PCB上并经一定膏温后是否仍保持良好形状的一种术语,这种现象往往会导致回流焊后出现“桥联,飞珠”2.焊锡膏的印刷技术:焊锡膏的印刷是SMT中第一道工序,焊锡膏的印刷涉及到三项基本内容-----焊锡膏,模板和印刷机,三者之间合理组合,对膏质量地实现焊锡膏的定量分配是非常重要的.,焊锡膏前面已说过,现主要说明的是模块及印刷机.1)金属模板(stencils)的制造方法:A.化学腐蚀法,由于存在侧腐蚀,故窗口壁光洁度不够,对不锈钢材料效果较差,因此漏印效果也较差.B.激光切割法,它是利用微机控制CO2或Y AG激光发生器,像光绘一样直接在金属模板上切割窗口.C.电铸法:电铸法制造的模板价格显然是贵,适合在细间距器件焊接产品中使用.2)印刷机:说明全自动印刷机,通常有光学对准系统,通过对PCB 和模板上对准标志的识别,实现模反窗口与PCB焊盘的自动对准,印刷机精度达0.01MM,但印刷机的多种工艺参数,如刮刀速度,刮刀压力,脱模速度,模板与PCB板之间间隙仍需人工设定.3)影响印刷效果的因素:A.模板窗口的光滑度与径深比.B.锡膏触变性能的影响.4)焊膏印刷过程:A.焊膏准备:焊膏应放入冰箱冷藏(0—10度之间)。
smt各流程工艺要求和品质注意事项

smt各流程工艺要求和品质注意事项嘿,搞SMT的小伙伴们!今天咱们可得好好唠唠SMT各流程工艺要求和品质注意事项啦,这可太重要啦!首先呢,咱们来说说锡膏印刷这个流程。
锡膏就像是SMT的魔法胶水一样,那工艺要求可不能马虎。
锡膏的型号得选对喽,就像给不同的人穿合适的鞋子一样,选错了可不行。
印刷的时候,钢网要保证清洁干净,要是钢网上沾了脏东西,就好比在干净的画布上乱涂乱画,印出来的锡膏肯定不均匀。
压力也要适中呀,压力过大,锡膏就会被挤得到处都是,像调皮的小虫子乱跑;压力过小呢,锡膏又印不完整,这就糟糕啦。
在这个流程里,品质注意事项也很多呢。
要经常检查锡膏的厚度,这厚度要是不对,可能会导致焊接不良,那可就影响整个产品的品质啦,就像盖房子地基没打好,房子能稳吗?接着就是元件贴装啦。
哇,这一步就像是给电路板这个小世界安排居民一样。
贴片机的精度那得超高的,偏差一点点都不行。
元件的吸取和放置位置要精准无误,就像把棋子准确地放在棋盘格子里。
操作人员得时刻关注贴片机的运行状态,要是它出了点小毛病还不知道,那就像火车偏离了轨道一样危险。
对于品质方面,要检查元件有没有贴歪,有没有贴错型号的情况。
这要是贴错了,整个电路板就可能会像个乱了套的小社会,功能肯定不正常啦。
再然后就是回流焊接啦。
这个过程就像是给元件和电路板举办一场融合的派对。
回流焊的温度曲线要严格按照工艺要求来设置,这就像厨师做菜要按照菜谱的火候要求一样。
温度高了,元件可能会被烤坏,就像蛋糕在烤箱里烤焦了;温度低了呢,焊接就不牢固,就像胶水没粘牢东西一样。
在品质上,要检查焊接的效果,有没有虚焊、短路之类的问题。
虚焊就像两个人拉手没握紧,随时可能松开;短路就像电线乱搭,会引发大问题的。
还有检测环节呀。
这就像是给已经组装好的电路板做个体检。
检测设备要定期校准,不然就像秤不准了一样,量出来的数据都不可靠。
检测人员得认真仔细,不能放过任何一个小瑕疵。
对于发现的不良品,要及时标记和处理,可不能让有问题的产品混在好产品里面,这就像在一群健康的人里混进了生病的人一样,会传染的。
smt 工艺流程

smt 工艺流程SMT(Surface Mount Technology)是一种表面贴装技术,用于电子元件的精密贴装。
它通过将电子元件焊接在印刷电路板(PCB)表面,实现高速、高精度和高可靠性的电子装配。
以下是SMT工艺流程的简要介绍。
首先,需要准备好所需的材料和设备,包括印刷电路板、电子元件、焊膏、贴片机、回焊炉等。
印刷电路板需要经过PCB制作流程,包括切割、开孔、覆铜等步骤,以确保电路板的质量。
接下来是贴片过程。
首先,将印刷电路板放在贴片机的导引下,通过光学定位系统将电路板上的定位标记与贴片机程序进行匹配,以确保电路板上的元件能够准确地贴装。
然后,通过真空吸嘴将电子元件从进料盘中抓取,然后将其精确地放置在印刷电路板上的焊接区域,并且需要通过胶垫或者其他粘贴剂来保持元件的固定。
贴片完成后,需要进行自动焊接。
将贴装好的电子元件的焊脚与印刷电路板的焊盘相连接,通常使用热气流焊接或者波峰焊接。
热气流焊接是指通过传热系统向焊膏施加热量,使其熔化,然后将元件的焊脚与焊盘连接。
波峰焊接是将印刷电路板沿着焊盘与焊膏的共同路径移动,接触到熔化的焊膏,使元件的焊脚与焊盘连接。
这样,电子元件就与印刷电路板焊接在一起,形成牢固的连接。
焊接完成后,将印刷电路板送入冷却区域,使其快速冷却。
接下来进行组装和测试。
组装是指将电子元件的引脚与印刷电路板上的其他电路相连接,通常通过通孔连接或者焊接连接。
测试是对组装好的电路板进行全面的功能测试和质量检验,以确保电路板的功能正常,质量合格。
最后,进行清洗和包装。
清洗是为了去除表面残留的焊膏或其他污染物,以提高电路板的可靠性和稳定性。
包装是将组装和测试完成的电路板进行包装,以便于运输和存储。
整个SMT工艺流程是一个高度自动化和精密的过程,需要配备先进的设备和经验丰富的操作人员。
它极大地提高了电子元件的贴装速度和贴装精度,促进了电子行业的发展。
smt基本工艺流程
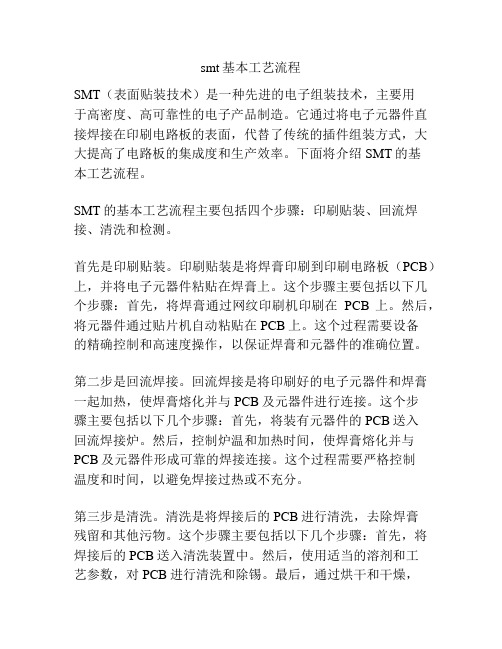
smt基本工艺流程SMT(表面贴装技术)是一种先进的电子组装技术,主要用于高密度、高可靠性的电子产品制造。
它通过将电子元器件直接焊接在印刷电路板的表面,代替了传统的插件组装方式,大大提高了电路板的集成度和生产效率。
下面将介绍SMT的基本工艺流程。
SMT的基本工艺流程主要包括四个步骤:印刷贴装、回流焊接、清洗和检测。
首先是印刷贴装。
印刷贴装是将焊膏印刷到印刷电路板(PCB)上,并将电子元器件粘贴在焊膏上。
这个步骤主要包括以下几个步骤:首先,将焊膏通过网纹印刷机印刷在PCB上。
然后,将元器件通过贴片机自动粘贴在PCB上。
这个过程需要设备的精确控制和高速度操作,以保证焊膏和元器件的准确位置。
第二步是回流焊接。
回流焊接是将印刷好的电子元器件和焊膏一起加热,使焊膏熔化并与PCB及元器件进行连接。
这个步骤主要包括以下几个步骤:首先,将装有元器件的PCB送入回流焊接炉。
然后,控制炉温和加热时间,使焊膏熔化并与PCB及元器件形成可靠的焊接连接。
这个过程需要严格控制温度和时间,以避免焊接过热或不充分。
第三步是清洗。
清洗是将焊接后的PCB进行清洗,去除焊膏残留和其他污物。
这个步骤主要包括以下几个步骤:首先,将焊接后的PCB送入清洗装置中。
然后,使用适当的溶剂和工艺参数,对PCB进行清洗和除锡。
最后,通过烘干和干燥,将PCB完全清洁并保持干燥。
最后一步是检测。
检测是对焊接后的PCB进行质量检查,以确保电路板和焊接连接的可靠性和稳定性。
这个步骤主要包括以下几个步骤:首先,使用自动光学检测设备对PCB进行外观检查,检测焊接点的缺陷和偏差。
然后,使用测试仪器对电路板进行电气测试和功能测试,验证电路板的性能和可靠性。
最后,对不合格的PCB进行修复或重新制造。
综上所述,SMT的基本工艺流程包括印刷贴装、回流焊接、清洗和检测。
这些步骤的顺序和每个步骤的操作都需要严格控制和精确操作,以确保电子产品的质量和可靠性。
随着技术的不断发展,SMT技术将进一步提高电子产品的制造效率和质量水平。
SMT工艺流程概述

SMT工艺流程概述本文档旨在概述SMT(Surface Mount Technology,表面贴装技术)的工艺流程,以帮助读者了解SMT的基本原理和步骤。
1. 简介SMT是一种先进的电子组装技术,用于在电路板上安装电子元器件。
相比传统的插件式组装技术,SMT具有更高的速度和可靠性。
2. 工艺流程步骤2.1. 印刷- 首先,在电路板上涂覆一层粘合剂,这称为印刷。
- 印刷时使用的粘合剂是根据电路板上的元器件布局设计的。
2.2. 放置元器件- 在印刷区域上放置表面贴装元器件,这些元器件包括电阻、电容、芯片等。
- 放置元器件是通过自动设备完成的,可以提高生产效率。
2.3. 固化- 将电路板传送到固化炉中,进行固化。
- 固化的目的是使粘合剂在高温下变硬,以确保元器件牢固粘贴在电路板上。
2.4. 焊接- 进行焊接前,需要向元器件引脚添加焊膏。
- 焊接是将元器件与电路板连接的重要步骤。
- 通过传送电路板到热炉中,焊膏会熔化并形成电路板与元器件之间的焊点。
2.5. 检测- 检测是确保焊接质量和元器件安装正确的关键步骤。
- 检测可以使用光学、射频等方法进行。
- 如果检测发现问题,可以采取措施修复或重新制造。
2.6. 清洗- 清洗是为了去除焊接后残留的焊膏和其他不必要的物质。
- 清洗使用化学溶剂和水等方法进行。
2.7. 测试- 进行功能测试,验证SMT组装的电路板是否正常工作。
- 测试可以遵循特定的测试方案和标准。
3. 总结SMT工艺流程包括印刷、放置元器件、固化、焊接、检测、清洗和测试等步骤。
通过了解SMT工艺的流程,可以更好地理解和应用这种先进的电子组装技术。
以上是对SMT工艺流程的简要概述,希望对读者有所帮助!。
smt工艺流程

smt工艺流程SMT(Surface Mount Technology)是一种电子制造技术,根据电子元器件表面焊盘和贴片焊接设备粘合剂的粘合原理,将各种电子元件直接焊接在电路板表面上。
SMT工艺流程是一个非常重要的流程,它包含了多个步骤,接下来我将详细介绍一下SMT工艺流程。
SMT工艺流程的第一步是元件编码和分料。
在这个步骤中,首先需要根据工程师提供的元件清单,对每个元件进行编码,以方便后续的流程操作。
接着,将元件按照编码进行分料,按照电子元器件的类型和规格进行分类,以便后续的贴片工作。
第二步是人工检查和自动粘贴。
在这一步中,需要对分料后的元件进行人工检查,确保每个元件的质量和规格都符合要求。
然后,将元件放置在自动粘贴机上,并通过粘合剂将元件粘贴到电路板的表面。
自动贴片机可以根据电子元器件的尺寸和形状自动调整位置,并精确地将元件粘贴到预定位置。
第三步是回流焊接。
在这一步中,已经完成贴片的电路板需要进行回流焊接,将元件与电路板焊接在一起。
回流焊接是通过将电路板放入回流炉中,以高温和高压的环境下进行的。
在回流炉中,焊料被加热至熔点,然后冷却,将元件和电路板粘合在一起。
第四步是清洗。
在回流焊接后,电路板上可能留有焊接过程中产生的残留物。
为了确保电路板的质量和可靠性,需要对电路板进行清洗。
清洗的目的是去除电路板表面的残留物,以确保电路板的可靠性和稳定性。
第五步是AOI (Automated Optical Inspection) 检查。
在这一步中,使用自动光学检测设备对焊盘和贴片质量进行全面检查。
AOI系统通过光学方式对电路板进行扫描和分析,以检测焊盘和贴片上可能存在的缺陷和问题。
这样能够及时发现并纠正问题,提高产品质量。
第六步是功能测试。
在这一步中,已经完成的电路板需要进行功能测试,以确保它们能够正常工作。
功能测试一般包括对元件的基本性能和功能进行测试,以确保电路板的功能和性能能够满足要求。
功能测试可以通过自动测试设备完成。
smt主要工艺技术
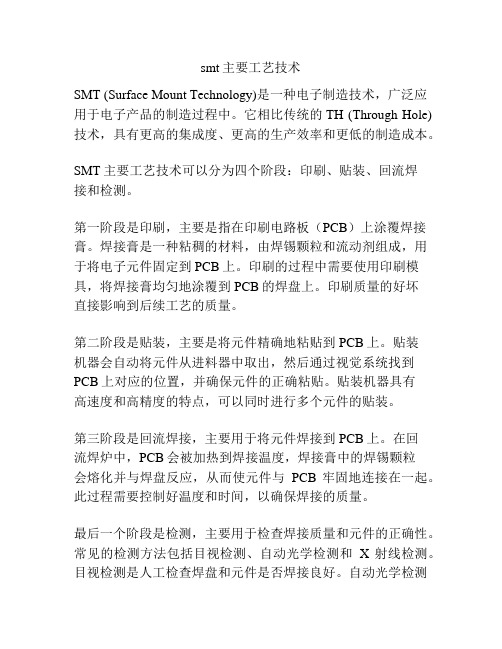
smt主要工艺技术SMT (Surface Mount Technology)是一种电子制造技术,广泛应用于电子产品的制造过程中。
它相比传统的TH (Through Hole)技术,具有更高的集成度、更高的生产效率和更低的制造成本。
SMT主要工艺技术可以分为四个阶段:印刷、贴装、回流焊接和检测。
第一阶段是印刷,主要是指在印刷电路板(PCB)上涂覆焊接膏。
焊接膏是一种粘稠的材料,由焊锡颗粒和流动剂组成,用于将电子元件固定到PCB上。
印刷的过程中需要使用印刷模具,将焊接膏均匀地涂覆到PCB的焊盘上。
印刷质量的好坏直接影响到后续工艺的质量。
第二阶段是贴装,主要是将元件精确地粘贴到PCB上。
贴装机器会自动将元件从进料器中取出,然后通过视觉系统找到PCB上对应的位置,并确保元件的正确粘贴。
贴装机器具有高速度和高精度的特点,可以同时进行多个元件的贴装。
第三阶段是回流焊接,主要用于将元件焊接到PCB上。
在回流焊炉中,PCB会被加热到焊接温度,焊接膏中的焊锡颗粒会熔化并与焊盘反应,从而使元件与PCB牢固地连接在一起。
此过程需要控制好温度和时间,以确保焊接的质量。
最后一个阶段是检测,主要用于检查焊接质量和元件的正确性。
常见的检测方法包括目视检测、自动光学检测和X射线检测。
目视检测是人工检查焊盘和元件是否焊接良好。
自动光学检测使用相机和图像处理算法,可以高速地检查焊盘的位置和焊接质量。
X射线检测可以检查焊点的内部结构,查看是否有缺陷。
SMT主要工艺技术的发展不仅提高了电子制造的效率和质量,还可以实现更小型化和更轻量化的产品设计。
它广泛应用于手机、电脑、电视等消费电子产品的制造过程中。
随着技术的发展,SMT工艺技术也在不断地改进和创新,使得电子产品的性能和质量得到了进一步的提升。
总之,SMT主要工艺技术的应用使得电子制造过程更加高效、精确和可靠,进一步推动了电子行业的发展。
随着科技的不断发展,相信SMT技术将会在未来的电子制造领域发挥越来越重要的作用。
SMT生产线工艺流程
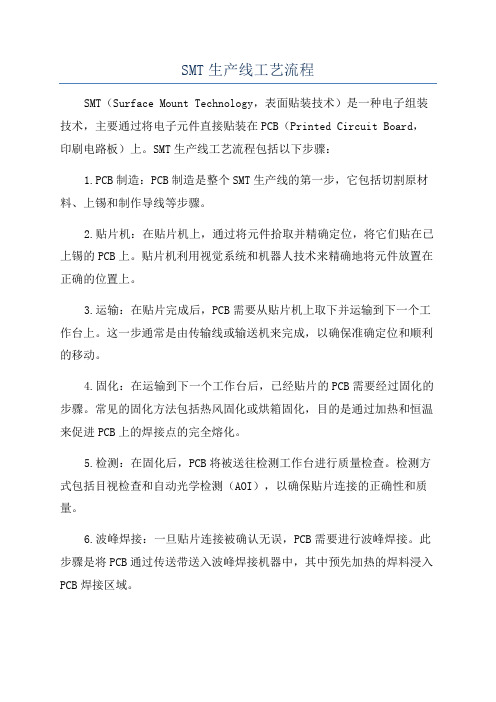
SMT生产线工艺流程SMT(Surface Mount Technology,表面贴装技术)是一种电子组装技术,主要通过将电子元件直接贴装在PCB(Printed Circuit Board,印刷电路板)上。
SMT生产线工艺流程包括以下步骤:1.PCB制造:PCB制造是整个SMT生产线的第一步,它包括切割原材料、上锡和制作导线等步骤。
2.贴片机:在贴片机上,通过将元件拾取并精确定位,将它们贴在已上锡的PCB上。
贴片机利用视觉系统和机器人技术来精确地将元件放置在正确的位置上。
3.运输:在贴片完成后,PCB需要从贴片机上取下并运输到下一个工作台上。
这一步通常是由传输线或输送机来完成,以确保准确定位和顺利的移动。
4.固化:在运输到下一个工作台后,已经贴片的PCB需要经过固化的步骤。
常见的固化方法包括热风固化或烘箱固化,目的是通过加热和恒温来促进PCB上的焊接点的完全熔化。
5.检测:在固化后,PCB将被送往检测工作台进行质量检查。
检测方式包括目视检查和自动光学检测(AOI),以确保贴片连接的正确性和质量。
6.波峰焊接:一旦贴片连接被确认无误,PCB需要进行波峰焊接。
此步骤是将PCB通过传送带送入波峰焊接机器中,其中预先加热的焊料浸入PCB焊接区域。
7.清洗:波峰焊接后,PCB需要经过清洗步骤以去除焊接过程中产生的残留物和通路上的污染物。
清洗可以使用溶剂、超声波或水等方式进行。
8.二次测量:清洗后的PCB需要再次进行测量和检测,以确保焊接质量的准确性和稳定性。
这可以通过光学检测、X射线检测等方式来实现。
9.包装和装箱:最后一步是将焊接完成的PCB进行包装和装箱。
根据需求,可以使用自动或手动包装设备将PCB放入保护袋中,然后装入适当的包装箱。
SMT生产线工艺流程涵盖了从PCB制造到最终产品包装的整个过程。
每个步骤都需要高度精确的控制和自动化,以确保质量和效率。
随着技术的不断发展,SMT生产线工艺流程也在不断演进,以适应市场需求和提高生产效率。
SMT整个工艺流程细则
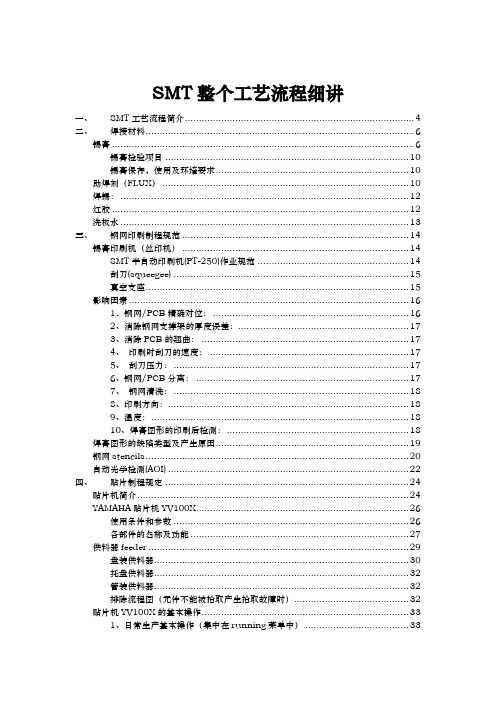
SMT整个工艺流程细讲一、SMT工艺流程简介 (4)二、焊接材料 (6)锡膏 (6)锡膏检验项目 (10)锡膏保存,使用及环境要求 (10)助焊剂(FLUX) (10)焊锡: (12)红胶 (12)洗板水 (13)三、钢网印刷制程规范 (14)锡膏印刷机(丝印机) (14)SMT半自动印刷机(PT-250)作业规范 (14)刮刀(squeegee) (15)真空支座 (15)影响因素 (16)1.钢网/PCB精确对位: (16)2、消除钢网支撑架的厚度误差: (17)3、消除PCB的翘曲: (17)4、印刷时刮刀的速度: (17)5、刮刀压力: (17)6、钢网/PCB分离: (17)7、钢网清洗: (18)8、印刷方向: (18)9、温度: (18)10、焊膏图形的印刷后检测: (18)焊膏图形的缺陷类型及产生原因 (19)钢网stencils (20)自动光学检测(AOI) (22)四、贴片制程规定 (24)贴片机简介 (24)YAMAHA贴片机YV100X (26)使用条件和参数 (26)各部件的名称及功能 (27)供料器feeder (29)盘装供料器 (30)托盘供料器 (32)管装供料器 (32)排除流程图(元件不能被拾取产生拾取故障时) (32)贴片机YV100X的基本操作 (33)1、日常生产基本操作(集中在running菜单中) (33)5、PCB生产完成 (34)6、关电源 (34)7、改变运输轨部件设置 (34)贴片机YV100X的高级操作 (35)1、创建新的PCB板 (35)找Mark (35)2、创建新的器件库(database) (35)3、生产信息查看 (35)4、打特定几个器件(补料) (36)YV100X贴片机常见故障及解决方法 (36)1、PCB传输故障: (36)2、丢料故障 (37)3、元件计数停止故障: (37)4、托盘供料器故障 (38)5、联锁故障: (39)6、暖机操作 (40)7、其它故障信息: (40)工艺分析 (41)A:元器件贴装偏移 (41)B:器件贴装角度偏移 (42)C:元件丢失: (43)D:取件不正常: (43)E:随机性不贴片(漏贴): (43)F:取件姿态不良: (44)贴片机抛料原因分析及对策 (45)五、回流焊 (47)回流焊炉 (47)回焊炉KWA-1225 Super EP8结构 (47)操作指导 (47)回流焊的保养 (48)锡膏的回流过程 (48)2.怎样设定锡膏回流温度曲线 (51)5.回焊之PROFILE量测 (54)6.标准有铅制程 (56)7.无铅焊接制程 (58)8.点胶制程 (62)回流焊接缺陷分析 (63)1.未焊满 (63)2断续润湿 (63)3低残留物 (64)4间隙 (64)5焊料成球 (64)6焊料结珠 (65)8竖碑(Tombstoning) (66)9、BGA成球不良 (66)10形成孔隙 (66)六、手工焊接制程以及手工标准 (67)4.1焊接操作的正确姿势 (68)4.2焊接操作的基本步骤 (68)4.3焊接温度与加热时间 (69)4.4焊接操作的具体手法 (69)4.5焊点质量及检查 (70)手工烙铁焊接技术 (74)4.3 焊接温度与加热时间 (75)4.4 焊接操作的具体手法 (75)4.5 焊点质量及检查 (76)五.静电简介 (80)七、波峰焊机 (81)波峰焊机组件日常维护要点 (82)八、其他SMT设备 (84)空压机 (84)空气压缩机操作指导 (84)螺杆式空气压缩机SA-350W操作指导 (84)冷冻式干燥机 (84)冷冻式干燥机GC-75/ GC-30/ GC-10操作指导 (84)水洗机 (85)九、运输、储存和生产环境 (86)十、料件的基本知识 (90)PCB(PrintedCircuitBoard)即印刷电路板 (90)2.2 元件基本知识 (91)2.2.1电阻器 (91)2.2.2 电容器 (91)2.2.3 表贴阻容元件的封装代号 (92)2.2.4 二极管 (93)2.2.5存储器 (93)2.2.6芯片: (94)2.2.7 BGA封装 (94)2.3 SMD元件的包装形式: (95)2.4 PCB及IC的方向 (95)十一、如何读懂BOM (98)贴片机料件知识 (99)十二、SMT设计(可生产性) (101)影响回流焊接缺陷的设计因素。
SMT基本工艺构成要素
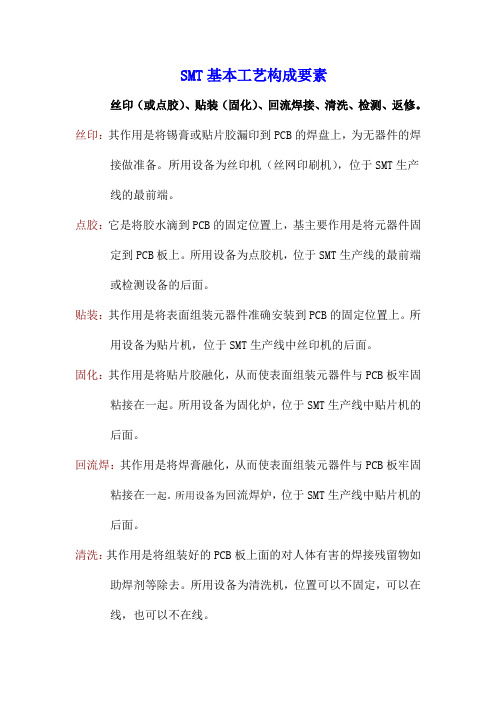
SMT基本工艺构成要素丝印(或点胶)、贴装(固化)、回流焊接、清洗、检测、返修。
丝印:其作用是将锡膏或贴片胶漏印到PCB的焊盘上,为无器件的焊接做准备。
所用设备为丝印机(丝网印刷机),位于SMT生产线的最前端。
点胶:它是将胶水滴到PCB的固定位置上,基主要作用是将元器件固定到PCB板上。
所用设备为点胶机,位于SMT生产线的最前端或检测设备的后面。
贴装:其作用是将表面组装元器件准确安装到PCB的固定位置上。
所用设备为贴片机,位于SMT生产线中丝印机的后面。
固化:其作用是将贴片胶融化,从而使表面组装元器件与PCB板牢固粘接在一起。
所用设备为固化炉,位于SMT生产线中贴片机的后面。
回流焊:其作用是将焊膏融化,从而使表面组装元器件与PCB板牢固粘接在一起。
所用设备为回流焊炉,位于SMT生产线中贴片机的后面。
清洗:其作用是将组装好的PCB板上面的对人体有害的焊接残留物如助焊剂等除去。
所用设备为清洗机,位置可以不固定,可以在线,也可以不在线。
检测:其作用是对组装好的PCB板进行焊接质量和装配质量的检测。
所用设备有放大镜、显微镜、在线测试仪(ICT)、飞针测试仪、自动光学检测(AOI)、X-RAY检测系统、功能测试仪等。
位置根据检测的需要,可以配置在生产线合适的地方。
返修:其作用是对检测出现故障的PCB板进行返工。
所用工具为烙铁、返修工作站等。
配置在生产线中任意位置。
随着表面组装技朮更广泛、更深入的应用于各个领域,SMT焊接质量问题引起人闪高度重视,SMT焊接质量与整个组装工艺流程各个环节密切相关,为了减少或避免止止述焊接缺陷的出现,不公要提高工艺人员判断和解决这些问题能力,另外还要注重提高工艺质量技朮。
完善工艺管理,制定出有效的控制方法,才能提高SMT焊接质量,保证电子产品的最终质量。
本文若有不对之处,请予以指正。
SMT焊接流程:发料单--SMT 排料--PCB 烘烤--印锡膏--目检锡膏点--SMT 贴装电阻,电容--SMT 贴装芯片--目检及修补--回流焊--QC 检查--手工插件--QC 检查--自动波峰焊--剪脚--修补--补件--短路测试--功能测试--成品。
威力泰SMT接设备解决方案三
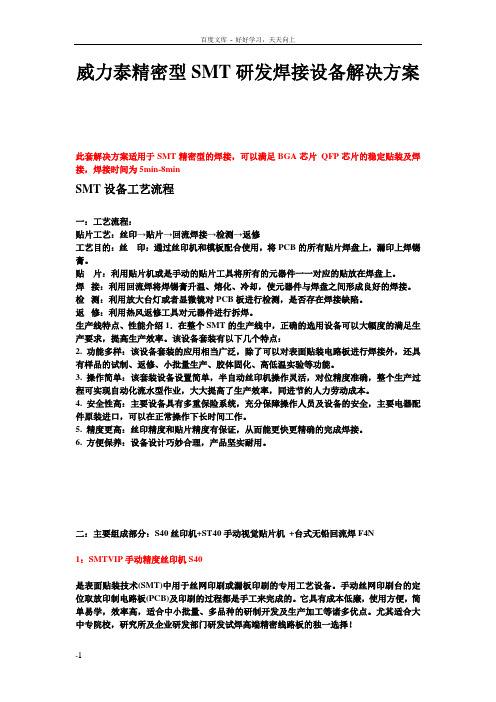
威力泰精密型SMT研发焊接设备解决方案此套解决方案适用于SMT精密型的焊接,可以满足BGA芯片QFP芯片的稳定贴装及焊接,焊接时间为5min-8minSMT设备工艺流程一:工艺流程:贴片工艺:丝印→贴片→回流焊接→检测→返修工艺目的:丝印:通过丝印机和模板配合使用,将PCB的所有贴片焊盘上,漏印上焊锡膏。
贴片:利用贴片机或是手动的贴片工具将所有的元器件一一对应的贴放在焊盘上。
焊接:利用回流焊将焊锡膏升温、熔化、冷却,使元器件与焊盘之间形成良好的焊接。
检测:利用放大台灯或者显微镜对PCB板进行检测,是否存在焊接缺陷。
返修:利用热风返修工具对元器件进行拆焊。
生产线特点、性能介绍1.在整个SMT的生产线中,正确的选用设备可以大幅度的满足生产要求,提高生产效率。
该设备套装有以下几个特点:2. 功能多样:该设备套装的应用相当广泛,除了可以对表面贴装电路板进行焊接外,还具有样品的试制、返修、小批量生产、胶体固化、高低温实验等功能。
3. 操作简单:该套装设备设置简单,半自动丝印机操作灵活,对位精度准确,整个生产过程可实现自动化流水型作业,大大提高了生产效率,同进节约人力劳动成本。
4. 安全性高:主要设备具有多重保险系统,充分保障操作人员及设备的安全,主要电器配件原装进口,可以在正常操作下长时间工作。
5. 精度更高:丝印精度和贴片精度有保证,从而能更快更精确的完成焊接。
6. 方便保养:设备设计巧妙合理,产品坚实耐用。
二:主要组成部分:S40丝印机+ST40手动视觉贴片机+台式无铅回流焊F4N1:SMTVIP手动精度丝印机S40是表面贴装技术(SMT)中用于丝网印刷或漏板印刷的专用工艺设备。
手动丝网印刷台的定位取放印制电路板(PCB)及印刷的过程都是手工来完成的。
它具有成本低廉,使用方便,简单易学,效率高,适合中小批量、多品种的研制开发及生产加工等诸多优点。
尤其适合大中专院校,研究所及企业研发部门研发试焊高端精密线路板的独一选择!技术参数:A.印刷尺寸:×300mmB.丝印粗调方式:带有对位刻度标尺C.丝印微调方式:精密丝杆调节,微调精度可达0.1mmD. 适用范围:丝网、钢网E.重量:20KgF.外形尺寸:700×600×350mm2:手动贴片机ST40产品特点:ST40 提供了一个能在X 轴向、Y 轴向、Z 轴向可调节的PCB 定位贴片平台,同时贴片头能够任意角度旋转,充分保证了对位的高度精确(精度可达到)。
SMT工艺概述
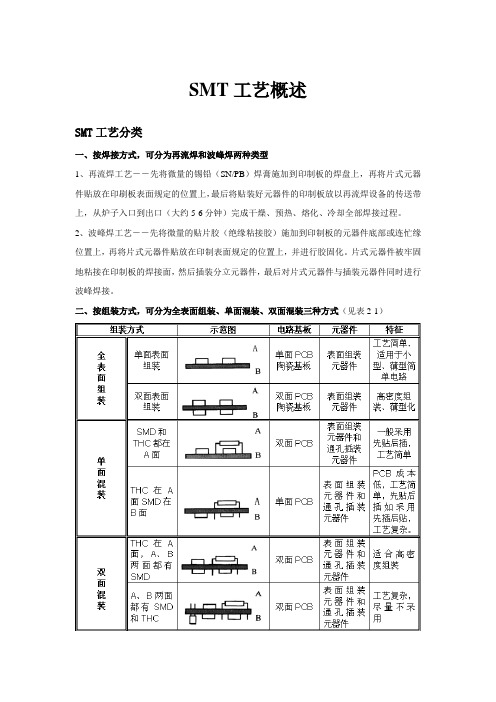
SMT工艺概述SMT工艺分类一、按焊接方式,可分为再流焊和波峰焊两种类型1、再流焊工艺――先将微量的锡铅(SN/PB)焊膏施加到印制板的焊盘上,再将片式元器件贴放在印刷板表面规定的位置上,最后将贴装好元器件的印制板放以再流焊设备的传送带上,从炉子入口到出口(大约5-6分钟)完成干燥、预热、熔化、冷却全部焊接过程。
2、波峰焊工艺――先将微量的贴片胶(绝缘粘接胶)施加到印制板的元器件底部或连忙缘位置上,再将片式元器件贴放在印制表面规定的位置上,并进行胶固化。
片式元器件被牢固地粘接在印制板的焊接面,然后插装分立元器件,最后对片式元器件与插装元器件同时进行波峰焊接。
二、按组装方式,可分为全表面组装、单面混装、双面混装三种方式(见表2-1)施加焊膏工艺一、工艺目的把适量的SN/PB焊膏均匀地施加在PCB焊盘上,以保证片式元器件与PCB相对应的焊盘达到良好的电气连接。
二、施加焊膏的要求1、要求施加的焊膏量均匀,一致性好。
焊膏图形要清晰,相邻的图形之间尽量不要粘连,焊膏图形与焊盘图形要一致,尽量不要错位。
2、一般情况下,焊盘上单位面积的焊膏量应为0.8mg/mm2左右,窄间距元器件应为0.5mg/mm2左右。
3、焊膏应覆盖每个焊盘的面积,应在75%以上;4、焊膏印刷后,应无严重塌落,边缘整齐,错位不大于0.2mm;对窄间距元器件焊盘,错位不大于0.1mm。
5、基板不允许被焊膏污染。
三、施加焊膏的方法施加焊膏的方法有三种:滴涂式(即注射式,滴除式又分为手工操作和机器制作)、丝网印刷和金属模板印刷。
各种方法的适用范围如下:1、手工滴涂法――用于极小批量生产,或新产品的模型样机和性能样机的研制阶段,以及生产过程中修补、更换元器件等。
2、丝网印刷――用于元器件焊盘间距较大,组装密度不高的中小批量生产中。
3、金属模板印刷――用于大批量生产以及组装密度大,有多引线窄间距元器件的产品。
金属模板印刷的质量比较好,模板使用寿命长,因此一般应优先采用金属模板印刷工艺。
- 1、下载文档前请自行甄别文档内容的完整性,平台不提供额外的编辑、内容补充、找答案等附加服务。
- 2、"仅部分预览"的文档,不可在线预览部分如存在完整性等问题,可反馈申请退款(可完整预览的文档不适用该条件!)。
- 3、如文档侵犯您的权益,请联系客服反馈,我们会尽快为您处理(人工客服工作时间:9:00-18:30)。
易于辨认
常见问题分析
点胶
拖尾 点胶不稳定(空点等 )
固化
强度不够 歪片
贴片
歪片 漏贴
波峰焊
掉片 立片
电器测试
短路 开路
拖尾
压力过高,点胶过快 点胶嘴与胶点不匹配 点胶温度过低 PCB板翘曲 有局部静电 点胶高度 回温不够(如果低温冷藏后使用) 胶的流变性不适合高速点胶机 胶变质
强度不足
温度曲线设置不当,固化不足 炉内温区不均匀,局部加热不足 阻焊膜附着强度不够 元件表面涂层附着不够 胶量不足 胶内有气泡 胶吸潮 胶设计强度偏低
气泡的产生
胶中混有气泡 PCB,元件和贴片胶均会吸潮 环境湿度过大,胶在空气中停留时间过长 控制胶在空气中停留时间 某些贴片胶固化时会有溶剂挥发(选择无溶剂的 贴片胶)
实现胶着强度
流变性改性剂
决定点胶性能和湿强度
颜料
与线路板有明显的对比度
填充料
接近线路板与元件的热膨胀
贴片胶的流变性
屈服值 Yield Point 点胶初始气压 湿强度 触变性 Thixotropy 点胶性 胶点形状
P C B 板 上 胶 点 胶 从 点 形 胶 成 头 过 程 中 挤 出
3616 / 3617
高速印刷
清洗剂
难粘表面
3618
3619
3620
低温固化
抗潮湿,低离子
3619
3621 3622
Ultra High 超高速 Speed
3 0 m l , Is w a h i t a
1 0 m l , Is w a h i t a
3 0 m l , Pr at n a s e
胶点不稳定一致
点胶参数不稳定 点胶压力过低 点胶温度过低 胶嘴堵塞 胶内有气泡 胶回温时间不足 胶变质
歪片、浮片
炉内有异物 贴片位置偏移 漏点 炉内预热升温过快 单胶点 胶内有气泡 胶固化膨胀量过大 胶量不足 胶湿强度不足 胶点位置偏移
立片
升温过快 PCB设计时,元件平行传送带方向,受热不 均 胶点偏位
Clinched Lead
Adhesive
- Stand-off 高度 - 胶嘴大小和间距
孔版印刷
刮板式印胶关键要素
刮板 (Stencil)
材质
钢板 网板
刮刀 (Squeegee)
材质
金属 硅橡胶 聚氨酯
厚度 开孔
控制胶量
角度: 45
刮板式印胶关键要素
参数设置
刮刀速度(squeegee speed) 刮刀压力(squeegee pressure) 脱模距离(Snap-off) 脱模速度(Down-release speed)
: 40mm/sec : 4N/cm2 : 1.0mm : 0.1mm/sec
点胶量
接着点 胶点 ADHESIVE DOT A
METALLIZATION
SMD
B
C
焊盘
C > A+B
- 80%焊盘之间的面积
-
胶点宽高比在 2:1--- 4:1
移印点胶
选择贴片胶考虑因素
1. 施胶方法 点胶/ 压力时间速度 ,印刷/压力速度 2. 固化 红外 3. 胶性能 流变性能,胶点形状,湿强度 4. 处理,修补性,耐高温性能 连接强度 5. 颜色
固化曲线
3- 固 化 4 10 固 8 5 秒秒 / -0 或 3 ℃ 6 0 化 1 9 9℃ 1 2 2 0 0 推 荐 的 时 间
典化 型曲 红线 外 加 热 炉 的 固
预~ 热2 段℃ 温/ 升 速 度 为 1 . 5 . 0 s 冷可 却 段 为 自 然 冷 却 即 强出 度烘 测箱 试5 推 钟 荐 后 在 进 P C B 分 行
粘度
切 固 定 剪 零 切 剪 速 率 速 率
时 间
胶点和屈服值
高 屈 服 值
低 屈 服 值
湿强度是... ... ...
贴片胶在未固化前固持元件的强度
胶的湿强度×面积 元件定粘结强度的因素
胶水本身 胶混合的均匀一致性 胶与PCB板和元件的表面“湿润”力 有否空气和湿汽的污染(气泡) 固化是否彻底 固化曲线是否相符
吸
潮
掉片——1
PCB 表面剥离
阻焊膜与PCB附着不良,会导致掉片
掉片——2
元件表面剥离
掉片——3
胶断裂
胶强度不足 胶点过小 固化不足 胶设计耐温性能不足 焊接时间过长 较大型的塑料元件,会被硅质脱模 剂污染
推力测试
电气测试
短路
元件失效 胶内有气泡或空穴,波 峰焊时过锡
开路
2 0 m l , Pr at n a s e
3 F 1E 1Gm m 0 D 0F 0 L lu l m l E m l D l T , j0 , m3F , , 0 i 1 M u s a s h i
Question and Answer
马朝胜 Michael Ma MP:13923461156 Tel:7785455 Fax:7789569 E-mail: michael.ma@
RL R EA GT UO A T AN II O H R MIE N C
进气
ST E UR BA ST SD T -F AO N F NL EE E D
基材
针
体积泵
P ep eu o D et m s 体积泵原理 n p i t il m i vs a c P s
点胶机参数
调节参数控制胶量: - 时间 - 压力 - 温度
PCB 或元件 胶污染焊盘 胶污染金属管脚
储存与回温
冷藏储存 ,保证有效期内质量 回温时间充足,>8 小时
解决问题的关键? 机器
PCB和元件
贴片胶
乐泰贴片胶
3611/3607 348
3612 / 3614
移针 /印刷
通用点胶
Varidot /印刷
3609 /3610
高速点胶
7360 3615
贴片胶技术
Loctite China electronics Michael Ma
乐泰贴片胶产品
SMT 和锡膏
回流
放件
锡膏
SMT 和贴片胶
点胶
放片
热固化
波峰焊
用 途
在 銲 接 過 程 前 及 進 行 中,暫 時 接 著 電 子 零 件 于 線 路 版 上
贴片胶的基本知识
贴片胶的组成
环氧树脂(丙稀酸脂)+硬化剂
温度℃
时 间 (d s e c o n s )
固化温度曲线的测量
贴满元件的板 测量潜在的低温区 大元件PLCC或QFP附近 PCB边缘 每块PCB上测3-5个点, 定期检查
针筒点胶
时间压力点胶
P u i es r s T S m P IIN er mt se y R O E C S 时间压力系统e 精密调节