8D工作方法
8d工作流程

8d工作流程8D工作流程是一种性质改善工具,通常被用于解决生产中的质量问题,特别是客户的不满意和产品缺陷。
这个工具以一种结构化的方式来提出问题、收集数据、诊断原因、制定和验证纠正措施,并对预防再次发生进行改进。
以下是8D工作流程的详细步骤:1. 确认问题:确保有清晰的理解本次问题,确认问题类型和问题状态。
问题类型可能包括产品缺陷、客户投诉、流程缺陷等。
问题状态应该根据事件的时间轴,有着明确的时间点描述。
2. 组建团队:团队负责收集和分析数据,制定并实施解决方案,持续监控解决的效果。
团队成员需要包括质量、工程、制造等相关部门的代表,以及实施现场的人员。
3. 限制损失(止血):起初要采取紧急的措施,以避免进一步的损失。
这部分是整个过程中最及时和关键的步骤。
4. 针对问题制定暂时性措施:在紧急措施落实后,需要采取一些暂时性的措施来控制质量问题。
5. 事件溯源:收集数据来分析问题的潜在原因。
采用5W1H方法,分析问题的何时、何地、何种情况下、何人、为什么和如何发生的原因,以确定深层次根本原因。
6. 制定永久性措施:主要是对基本原因进行根本解决,以预防问题再次发生。
制定并测试解决方案,以确保方案有效。
7. 实施对措施进行权衡的验证:实施解决方案,并测试验证解决方案是否有效。
如果没有满足预期和目标,需要重新改进和遵循8D流程的后续步骤。
8. 扩散和标准化:标准化和扩散有效的解决方案,以确保这些改进得到持续的应用。
最后制作报告,总结整个过程,从而为以后遇到类似问题的处理提供经验。
总之,8D工作流程是一个有条理的质量管理工具,可以帮助企业解决质量问题,提高顾客满意度。
该工具不断强调根本原因的发现和预防,提高了解决问题的效率和实效性。
在应对质量问题时,8D工作流程已经被证明是一种非常有效的解决方法。
8D (问题解决法)

何时
比较重大的制程品质问题
采用
8D
重复发生,一直没有解决的问题
第四部分
什么是8D. 为什么要推行8D. 什么时候采用8D. 8D工作方法.
8D改善案例分享.
8D工作方法
定义
D0
Define
建立小组
D1
Form the Team
D 2
问题描述 Describe the Problem
临时对策
D 3
Contain the Problem
原因分析 RCA
D4
确定可能原因
Identify the Root Cause
选择最可能原因
最有
NO
可能的原因
是否是根本
原因?
YES
确定根本原因
验证长期改善对策
D5
Formulate and Verify
Corrective Actions
改善并确定最终结果
D6
8D工作方法-D5验证长期对策
目的:在生产前测试方案,并对方案进行评审以确定所选的 校正措施能够解决客户问题,同时对其它过程不会有不良 影响。
关键要点: 重新审视小组成员资格;决策,选择最佳措施;重 新评估临时措施,如必要重新选择;验证;管理层承诺执行 永久纠正措施;控制计划
8D工作方法-D6确定最终结果
8D改善案例分享.
为什么要推行8D
● 提供问题有效解决的方法 ● 防止相同或类似问题的再发生。 ● 通过建立小组提高组织内部合作的技巧。 ● 提高顾客满意度,增强顾客的信心。
第三部分
什么是8D. 为什么要推行8D. 什么时候采用8D. 8D工作方法.
8D改善案例分享.
什么时候采用8D
福特-8D工作法

8D报告百科名片8D又称团队导向问题解决方法、8D问题求解法(8D Problem Solving)是福特公司处理问题的一种方法,亦适用于制程能力指数低於其应有值时有关问题的解决,它提供了一套符合逻辑的解决问题的方法,同时对於统计制程管制与实际的品质提升架起了一座桥梁。
简介8D最早是美国福特公司使用的经典质量问题分析手法。
二战期间,美国政府率先采用一种类似8D的流程——“军事标准1520”,又称之为“不合格品的修正行动及部署系统”。
1987年,福特汽车公司首次用书面记录下8D法,在其一份课程手册中这一方法被命名为“团队导向的问题解决法”(Team Oriented Problem Solving)。
当时,福特的动力系统部门正被一些经年累月、反复出现的生产问题搞得焦头烂额,因此其管理层提请福特集团提供指导课程,帮助解决难题。
问题解决8步法8D(8 Disciplines)问题解决8步法8D的原名叫做8 Disciplines,意思是8个人人皆知解决问题的固定步骤。
原始是由Ford公司,全球化品质管制及改善的特殊必备方法,之后已成为QS9000/ISO TS16949、福特公司的特殊要求。
凡是做FORD 的零件,必须采用8D 作为品质改善的工具,目前有些企业并非FORD的供应商或汽车业的合作伙伴,也很喜欢用这个方便而有效的方法解决品质问题,成为一个固定而有共识的标准化问题解决步骤。
Discipline 1. 成立改善小组(Form the Team):由议题之相关人员组成,通常是跨功能性的,说明团队成员间的彼此分工方式或担任的责任与角色。
Discipline 2. 描述问题(Describe the Problem):将问题尽可能量化而清楚地表达,并能解决中长期的问题而不是只有眼前的问题。
Discipline 3. 实施及确认暂时性的对策(Contain the Problem):对于解决D2 之立即而短期行动,避免问题扩大或持续恶化,包含清库存、缩短PM时间、加派人力等。
8D方法介绍
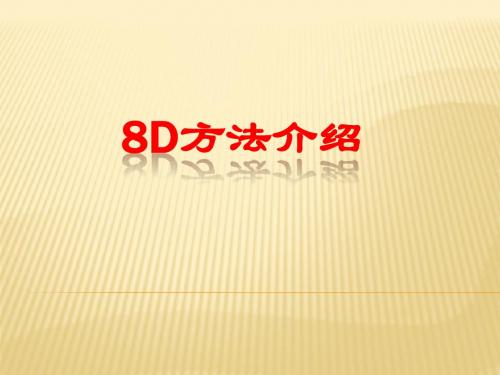
8D有哪几个步骤 8D有哪几个步骤
D0:征兆紧急反应措施 * D0:征兆紧急反应措施 D1:小组成立 * D1:小组成立 D2:问题说明 问题描述) 问题说明( * D2:问题说明(问题描述) D3:确定和实施临时措施 * D3:确定和实施临时措施 D4:寻找并确定根本原因 * D4:寻找并确定根本原因 D5:验证并确定永久纠正措施 纠正措施) 验证并确定永久纠正措施( * D5:验证并确定永久纠正措施(纠正措施) D6:实施永久纠正措施并验证 * D6:实施永久纠正措施并验证 D7:预防再发生 预防措施) 预防再发生( * D7:预防再发生(预防措施) D8:小组祝贺 肯定和激励) 小组祝贺( * D8:小组祝贺(肯定和激励)
D7-第七步骤: 预防再发生(预防措施) D7-第七步骤: 预防再发生(预防措施)
修改现有的管理系统、操作系统、工作惯例、 * 修改现有的管理系统、操作系统、工作惯例、设计与规程 以防止这一问题与所有类似问题重复发生。必要时, 以防止这一问题与所有类似问题重复发生。必要时,要提出 针对体系本身改善的建议。 针对体系本身改善的建议。 * 在同类产品或环节中推广应用这一永久措施。 在同类产品或环节中推广应用这一永久措施。 关键要点】 *【关键要点】 * 选择预防措施 * 验证有效性 * 决策 组织、人员、设备、环境、材料、 * 组织、人员、设备、环境、材料、文件重新确定
8D工作方法的运用 8D工作方法的运用 不合格的产品问题。 * 不合格的产品问题。 顾客投诉问题。 * 顾客投诉问题。 反复频发问题。 * 反复频发问题。 需要团队作业的问题。 * 需要团队作业的问题。
8D的目标 8D的目标
提高解决问题的效率,积累解决问题的经验; * 提高解决问题的效率,积累解决问题的经验; 杜绝或尽量减少重复问题出现; * 杜绝或尽量减少重复问题出现; 8D格式的原则上针对出现的问题 找出问题产生的根本原因, 格式的原则上针对出现的问题, * 8D格式的原则上针对出现的问题,找出问题产生的根本原因, 提出短期,中期和长期对策并采取相应行动措施; 提出短期,中期和长期对策并采取相应行动措施; 8D法可跨部门建立小组来加强部门间的协调 法可跨部门建立小组来加强部门间的协调, * 8D法可跨部门建立小组来加强部门间的协调,推进问题有效 解决,从而改进整个过程的质量, 解决,从而改进整个过程的质量,防止相同或类似问题的再发 以保证产品质量。 生,以保证产品质量。
8D和七步工作法

• D5:确定永久性纠正措施
在生产前测试方案,并对方案进行评 审以确定所选的校正措施能够解决客 户问题,同时对其它过程不会有不良 影响。
• 主要工具:因果图、FMEA
• 关键要点:重新审视小组成员资格;决策,选择最 佳措施;重新评估临时措施,如必要重新选择;验 证;管理层承诺执行永久纠正措施 。
是通用机型的故障还是专有机型的故障?
是否就措施方案的目的进行了针对性的试验验证?
是否充分收集并分析了典型的失效零件?
是否进行了符合设计标准的可靠性试验验证?
通过分析是否完全确定了失效故障模式?
是否进行过定点用户使用的验证?
识别的失效原因是否为根本原因?
验证数据是否对验证结论有充分的支持?
是否对相关的零件和过程进行了符合性的排查? 是否确定了小批投放(服务更换)的样本跟踪方案 ?
措施方案是否考虑了远近结合?
是否考虑了其它类似机型的采用问题?
是否考虑了在用、库存产品的临时措施?
是否确认了改进措施文件化的范围?
首先要分清楚什么是:
现象 问题 原因 什么是纠正措施 什么是临时措施 什么是长期措施
8D方法常用工具:
• 头脑风暴 • 推移图(目标达成情况、PPM) • 查检表 • 因果图(鱼刺图)、5why方法 • 帕累托图(排列图) • 控制图 • FMEA
Discipline 8
总结和激励
做好详细跟踪,趋势不理想,及时调整,重复上述过程
通过上述的工作过程回答: 1、问题是什么?(2D);2、问题如何解决?(3D~6D);3、将来该问题如何预防?(7D)
质量改进项目关键阶段控制评审内容
失效原因确认评审点
改进措施采用评审点
8D工作法标准版本时间
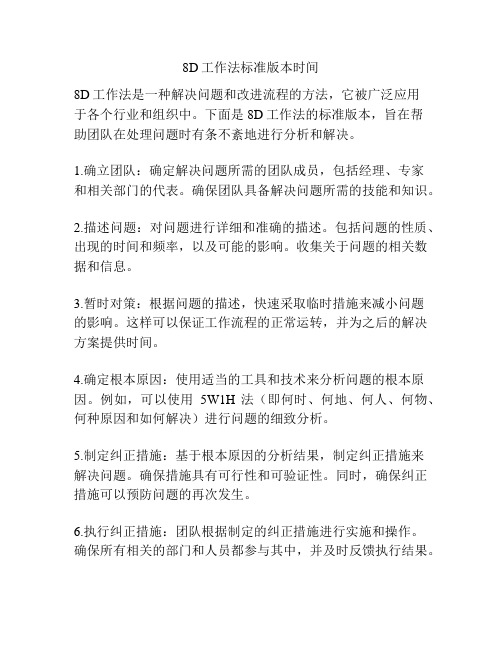
8D工作法标准版本时间8D工作法是一种解决问题和改进流程的方法,它被广泛应用于各个行业和组织中。
下面是8D工作法的标准版本,旨在帮助团队在处理问题时有条不紊地进行分析和解决。
1.确立团队:确定解决问题所需的团队成员,包括经理、专家和相关部门的代表。
确保团队具备解决问题所需的技能和知识。
2.描述问题:对问题进行详细和准确的描述。
包括问题的性质、出现的时间和频率,以及可能的影响。
收集关于问题的相关数据和信息。
3.暂时对策:根据问题的描述,快速采取临时措施来减小问题的影响。
这样可以保证工作流程的正常运转,并为之后的解决方案提供时间。
4.确定根本原因:使用适当的工具和技术来分析问题的根本原因。
例如,可以使用5W1H法(即何时、何地、何人、何物、何种原因和如何解决)进行问题的细致分析。
5.制定纠正措施:基于根本原因的分析结果,制定纠正措施来解决问题。
确保措施具有可行性和可验证性。
同时,确保纠正措施可以预防问题的再次发生。
6.执行纠正措施:团队根据制定的纠正措施进行实施和操作。
确保所有相关的部门和人员都参与其中,并及时反馈执行结果。
7.验证纠正效果:对纠正措施的执行结果进行验证。
可以采用实验、测试或观察的方法来评估纠正措施是否有效。
如果发现还有问题存在,需要重新制定纠正措施。
8.预防措施:基于之前的经验和结果,制定预防措施来防止同类问题的再次出现。
确保先前发现的根本原因得到解决,并且相关的流程和规范得到更新。
这是8D工作法的标准版本。
团队在解决问题时,可以根据该方法的步骤进行分析和决策。
通过逐步追踪问题,找出根本原因,并制定纠正和预防措施,可以有效地解决问题并改进工作流程。
同时,团队成员的协作和沟通也是成功应用8D工作法的关键因素。
继续写相关内容:9. 定期复审:定期回顾和复审已经实施的纠正措施和预防措施的效果。
确保问题的解决是可持续的,并跟踪潜在的新问题。
10. 持续改进:将学到的知识和经验应用于其他领域和流程中,实现持续改进的目标。
8D工作法

➢ 选取、验证、执行和确认紧急反应行动。 ➢ 确定是否需要8D来解决问题。
2022/3/23
Xu Ludong
17
四、过程介绍-D0准备8D
为什么要为8D过程作准备 ➢ 8D的过程是很精深的。可能涉及大量的时间、人员和 资源。当然也会浪费大量的时间、人员和资源,如果 全部问题都使用8D过程是不合适的。 ➢ 8D的使用标准帮助判别使用8D过程是合适的。如果不 使用8D的标准来判定是否使用8D,那么,您可能用精 深的过程来解决每一个单一的问题。 ➢ D0允许执行紧急反应行动(ERA)来保护顾客。 ➢ ERA也是保持顾客满意度和达到我们目标的重要部分。
2022/3/23
Xu Ludong
28
四、过程介绍- D2描述问题
怎样描述问题 ➢ 问题陈述 ➢ 问题描述
问题陈述 ➢ 问题陈述是确定未知原因引起的问题的对象和不合格的简 单、简明的陈述。 ➢ 怎样进行问题陈述 识别对象和不合格(问“什么出现了什么问题”) ✓“什么问题”是不合格 ✓“什么出了问题”是对象 ✓问‘什么出了什么问题’能够帮助小组以问题陈述 所需的两个基本要素为中心(对象和不合格)。
团队成员由保护与问题密切相关的 技术人员或管理人员、相关的质量 工程师组成;
质量部负责招集和组织团队的活动。
相关的QC工具
团队章程
业务个案
机遇陈述
目标陈述
项目范围
项目计划
团队人选
行动计划
TASKS TASKS
ACTIVITIES ACTIVITIES
RESP.
START
DUE
RESP.
START
DUE
Xu Ludong
25
四、过程介绍-D1成立8D小组
8D工作方法简介
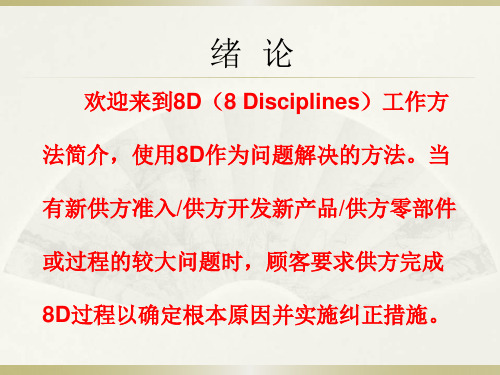
列出完成8D过程的工具(例如,试验设计DOE,统 计过程控制SPC, FMEA, 散点图, 检查单, 控制图等 等).
验证供方使用了适当的工具。 识别当评审8D报告时需询问的8D问题。 验证供方是否准确执行和文件化了8D过程。 确保供方通过启动和关闭问题已经验证了根本原 因。验证供方已经完成的所有材料包括所有可疑 材料,也包括已经在装配工厂、运输中、仓库 和过程中的零件。
D4: 定义和验证 根本原因和遗漏点(续)
常见性错误
声明的根本原因不是真正的根本原因, 操作者错误、准备的问题,或者是问题的 征兆或结果被作为根本原因给出。
质量工具
因果图 FMEA 是否分析 试验设计(DOE) 稳健设计
实例
S公司通过失效树(FTA)的方法验证根本 原因: 1、验证根本原因
根本原因1
问题
在AIM中顾客 项目的问题点
要求供方8D
供方在24小 时内以临时 纠正措施反应
在AIM 中标识
是 问题点
是供方的 职责吗?
否
在AIM 中关闭
问题的提出
下面的流程图显示了在现行生产中使用质量验收ຫໍສະໝຸດ 统(QR)导致问题的提出问题
QR中工 厂问题点
要求供方8D
供方在24小 时内以临时 纠正措施反应
到供方改 进矩阵
QR问题点
是 问题点
是供方的 职责吗?
否
顾客重新 确定职责
实例
S公司为顾客制造零件,见下图:
A
实例
根据顾客的工程规范,在零件A上必须镀银,否则顾客的 产品无法完成规定功能。有一天,他们收到顾客工厂发来 的问题点如下:
因为没有镀银造成产品缺陷,整批拒收。
质量管理方法:8D工作方法
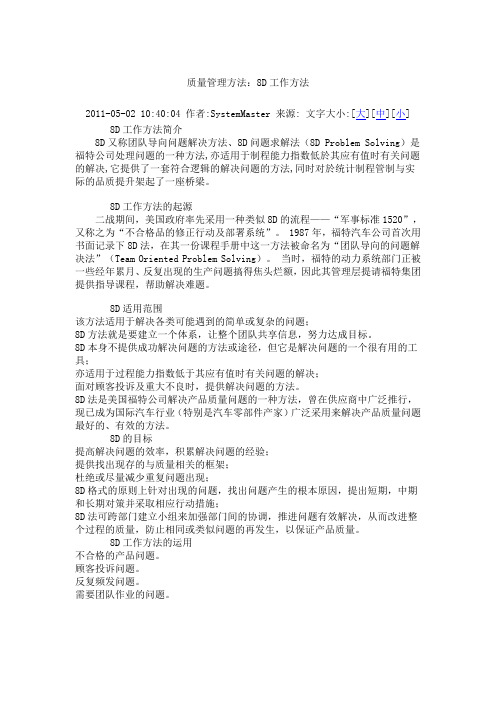
质量管理方法:8D工作方法2011-05-02 10:40:04 作者:SystemMaster 来源: 文字大小:[大][中][小]8D工作方法简介8D又称团队导向问题解决方法、8D问题求解法(8D Problem Solving)是福特公司处理问题的一种方法,亦适用于制程能力指数低於其应有值时有关问题的解决,它提供了一套符合逻辑的解决问题的方法,同时对於统计制程管制与实际的品质提升架起了一座桥梁。
8D工作方法的起源二战期间,美国政府率先采用一种类似8D的流程——“军事标准1520”,又称之为“不合格品的修正行动及部署系统”。
1987年,福特汽车公司首次用书面记录下8D法,在其一份课程手册中这一方法被命名为“团队导向的问题解决法”(Team Oriented Problem Solving)。
当时,福特的动力系统部门正被一些经年累月、反复出现的生产问题搞得焦头烂额,因此其管理层提请福特集团提供指导课程,帮助解决难题。
8D适用范围该方法适用于解决各类可能遇到的简单或复杂的问题;8D方法就是要建立一个体系,让整个团队共享信息,努力达成目标。
8D本身不提供成功解决问题的方法或途径,但它是解决问题的一个很有用的工具;亦适用于过程能力指数低于其应有值时有关问题的解决;面对顾客投诉及重大不良时,提供解决问题的方法。
8D法是美国福特公司解决产品质量问题的一种方法,曾在供应商中广泛推行,现已成为国际汽车行业(特别是汽车零部件产家)广泛采用来解决产品质量问题最好的、有效的方法。
8D的目标提高解决问题的效率,积累解决问题的经验;提供找出现存的与质量相关的框架;杜绝或尽量减少重复问题出现;8D格式的原则上针对出现的问题,找出问题产生的根本原因,提出短期,中期和长期对策并采取相应行动措施;8D法可跨部门建立小组来加强部门间的协调,推进问题有效解决,从而改进整个过程的质量,防止相同或类似问题的再发生,以保证产品质量。
8D工作方法的8个步骤
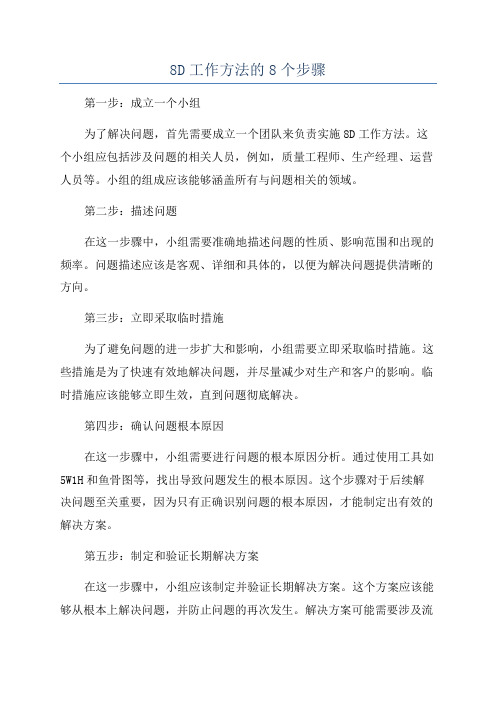
8D工作方法的8个步骤第一步:成立一个小组为了解决问题,首先需要成立一个团队来负责实施8D工作方法。
这个小组应包括涉及问题的相关人员,例如,质量工程师、生产经理、运营人员等。
小组的组成应该能够涵盖所有与问题相关的领域。
第二步:描述问题在这一步骤中,小组需要准确地描述问题的性质、影响范围和出现的频率。
问题描述应该是客观、详细和具体的,以便为解决问题提供清晰的方向。
第三步:立即采取临时措施为了避免问题的进一步扩大和影响,小组需要立即采取临时措施。
这些措施是为了快速有效地解决问题,并尽量减少对生产和客户的影响。
临时措施应该能够立即生效,直到问题彻底解决。
第四步:确认问题根本原因在这一步骤中,小组需要进行问题的根本原因分析。
通过使用工具如5W1H和鱼骨图等,找出导致问题发生的根本原因。
这个步骤对于后续解决问题至关重要,因为只有正确识别问题的根本原因,才能制定出有效的解决方案。
第五步:制定和验证长期解决方案在这一步骤中,小组应该制定并验证长期解决方案。
这个方案应该能够从根本上解决问题,并防止问题的再次发生。
解决方案可能需要涉及流程改进、设备升级、培训等多个方面。
解决方案制定后,需要进行验证,确保其可行性和有效性。
第六步:预防措施为了防止类似问题的再次发生,小组需要制定预防措施。
这些措施应该能够在一定程度上预防问题的发生,并提高质量水平。
预防措施可能包括改善标准操作程序、提高培训水平等。
第七步:应用控制措施在此步骤中,小组需要制定和应用控制措施,以确保解决方案的有效实施和问题的彻底解决。
这些控制措施可能包括质量检查、数据收集和监测等。
控制措施的目的是保持和改进质量水平。
第八步:总结和表彰最后一步是总结并对小组成员进行表彰。
小组应该总结并记录整个问题解决过程中的经验和教训,并将其用于未来的工作。
同时,对于那些为问题解决做出重要贡献的小组成员,应给予表彰和奖励,以表彰他们的努力和贡献。
以上是8D工作方法的八个步骤。
福特-8D工作法
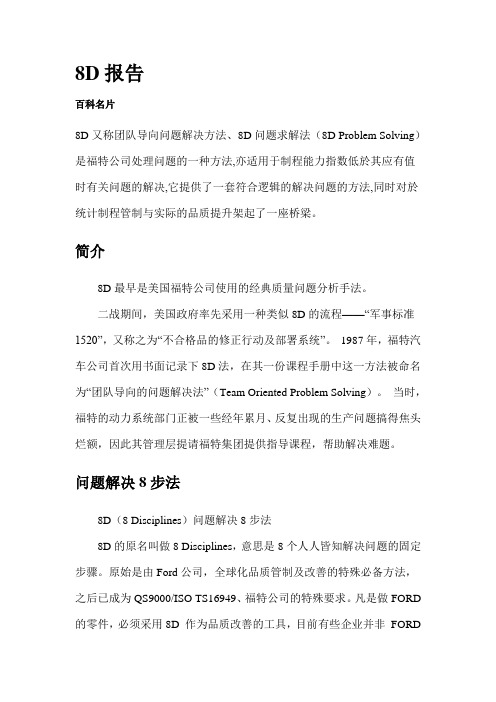
8D报告百科名片8D又称团队导向问题解决方法、8D问题求解法(8D Problem Solving)是福特公司处理问题的一种方法,亦适用于制程能力指数低於其应有值时有关问题的解决,它提供了一套符合逻辑的解决问题的方法,同时对於统计制程管制与实际的品质提升架起了一座桥梁。
简介8D最早是美国福特公司使用的经典质量问题分析手法。
二战期间,美国政府率先采用一种类似8D的流程——“军事标准1520”,又称之为“不合格品的修正行动及部署系统”。
1987年,福特汽车公司首次用书面记录下8D法,在其一份课程手册中这一方法被命名为“团队导向的问题解决法”(Team Oriented Problem Solving)。
当时,福特的动力系统部门正被一些经年累月、反复出现的生产问题搞得焦头烂额,因此其管理层提请福特集团提供指导课程,帮助解决难题。
问题解决8步法8D(8 Disciplines)问题解决8步法8D的原名叫做8 Disciplines,意思是8个人人皆知解决问题的固定步骤。
原始是由Ford公司,全球化品质管制及改善的特殊必备方法,之后已成为QS9000/ISO TS16949、福特公司的特殊要求。
凡是做FORD 的零件,必须采用8D 作为品质改善的工具,目前有些企业并非FORD的供应商或汽车业的合作伙伴,也很喜欢用这个方便而有效的方法解决品质问题,成为一个固定而有共识的标准化问题解决步骤。
Discipline 1. 成立改善小组(Form the Team):由议题之相关人员组成,通常是跨功能性的,说明团队成员间的彼此分工方式或担任的责任与角色。
Discipline 2. 描述问题(Describe the Problem):将问题尽可能量化而清楚地表达,并能解决中长期的问题而不是只有眼前的问题。
Discipline 3. 实施及确认暂时性的对策(Contain the Problem):对于解决D2 之立即而短期行动,避免问题扩大或持续恶化,包含清库存、缩短PM时间、加派人力等。
8D的工作方法及运用
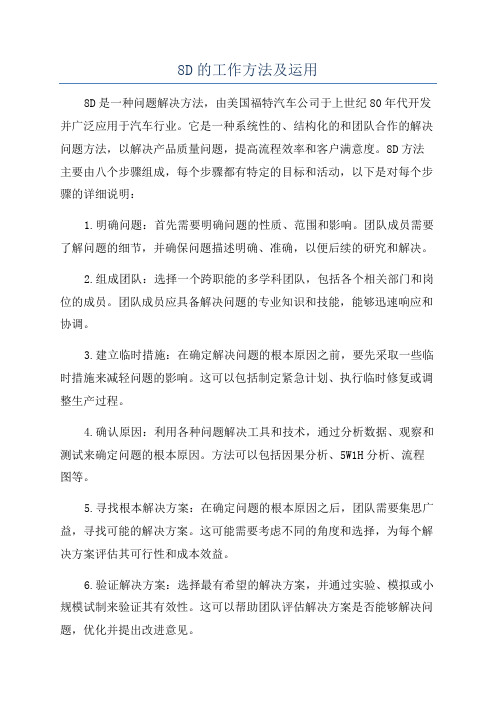
8D的工作方法及运用8D是一种问题解决方法,由美国福特汽车公司于上世纪80年代开发并广泛应用于汽车行业。
它是一种系统性的、结构化的和团队合作的解决问题方法,以解决产品质量问题,提高流程效率和客户满意度。
8D方法主要由八个步骤组成,每个步骤都有特定的目标和活动,以下是对每个步骤的详细说明:1.明确问题:首先需要明确问题的性质、范围和影响。
团队成员需要了解问题的细节,并确保问题描述明确、准确,以便后续的研究和解决。
2.组成团队:选择一个跨职能的多学科团队,包括各个相关部门和岗位的成员。
团队成员应具备解决问题的专业知识和技能,能够迅速响应和协调。
3.建立临时措施:在确定解决问题的根本原因之前,要先采取一些临时措施来减轻问题的影响。
这可以包括制定紧急计划、执行临时修复或调整生产过程。
4.确认原因:利用各种问题解决工具和技术,通过分析数据、观察和测试来确定问题的根本原因。
方法可以包括因果分析、5W1H分析、流程图等。
5.寻找根本解决方案:在确定问题的根本原因之后,团队需要集思广益,寻找可能的解决方案。
这可能需要考虑不同的角度和选择,为每个解决方案评估其可行性和成本效益。
6.验证解决方案:选择最有希望的解决方案,并通过实验、模拟或小规模试制来验证其有效性。
这可以帮助团队评估解决方案是否能够解决问题,优化并提出改进意见。
7.预防再次发生:一旦解决方案被证实有效,团队需要开发和实施预防措施,以防止类似问题再次发生。
这可以包括更新和修改流程、改善工艺和培训工作人员。
8.确认效果并提出奖励:在解决方案实施一段时间后,团队应评估解决效果,并将结果与原始问题相比较。
如果解决方案能够实现预期的效果,可以对团队成员进行表彰和奖励。
8D方法强调团队协作和持续改进,能够帮助组织有效地解决各种问题。
它具有结构化的步骤和工具,使团队能够系统地分析问题、找到根本原因并提出解决方案。
此外,8D还强调持续的改进和预防,为组织提供了一种改善流程和产品质量的方法。
8D工作方法的8个步骤
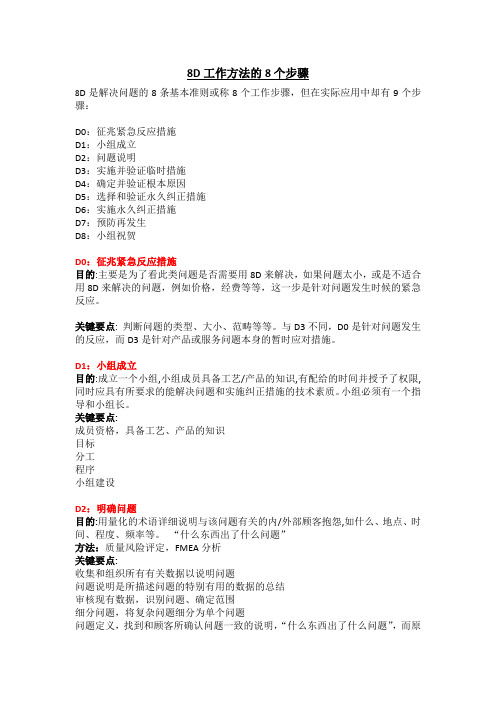
8D工作方法的8个步骤8D是解决问题的8条基本准则或称8个工作步骤,但在实际应用中却有9个步骤:D0:征兆紧急反应措施D1:小组成立D2:问题说明D3:实施并验证临时措施D4:确定并验证根本原因D5:选择和验证永久纠正措施D6:实施永久纠正措施D7:预防再发生D8:小组祝贺D0:征兆紧急反应措施目的:主要是为了看此类问题是否需要用8D来解决,如果问题太小,或是不适合用8D来解决的问题,例如价格,经费等等,这一步是针对问题发生时候的紧急反应。
关键要点: 判断问题的类型、大小、范畴等等。
与D3不同,D0是针对问题发生的反应,而D3是针对产品或服务问题本身的暂时应对措施。
D1:小组成立目的:成立一个小组,小组成员具备工艺/产品的知识,有配给的时间并授予了权限,同时应具有所要求的能解决问题和实施纠正措施的技术素质。
小组必须有一个指导和小组长。
关键要点:成员资格,具备工艺、产品的知识目标分工程序小组建设D2:明确问题目的:用量化的术语详细说明与该问题有关的内/外部顾客抱怨,如什么、地点、时间、程度、频率等。
“什么东西出了什么问题”方法:质量风险评定,FMEA分析关键要点:收集和组织所有有关数据以说明问题问题说明是所描述问题的特别有用的数据的总结审核现有数据,识别问题、确定范围细分问题,将复杂问题细分为单个问题问题定义,找到和顾客所确认问题一致的说明,“什么东西出了什么问题”,而原因又未知风险等级。
D3:实施并验证临时措施目的:保证在永久纠正措施实施前,将问题与内外部顾客隔离。
(原为唯一可选步骤,但发展至今都需采用)方法:FMEA、DOE、PPM关键要点:评价紧急响应措施找出和选择最佳“临时抑制措施”决策实施,并作好记录验证(DOE、PPM分析、控制图等)D4:确定并验证根本原因目的:用统计工具列出可以用来解释问题起因的所有潜在原因,将问题说明中提到的造成偏差的一系列事件或环境或原因相互隔离测试并确定产生问题的根本原因。
8d工作小组方案

8d工作小组方案
在企业管理中,8D工作小组是一种常用的问题解决方法。
它是一种系统化的
团队方法,旨在识别、解决和预防问题,以确保持续改进和高质量的产品或服务。
下面是一个具体的8D工作小组方案,以帮助团队有效地解决问题。
1. 确定问题描述:工作小组首先要明确问题的具体描述,包括问题出现的时间、地点以及影响。
2. 组建8D小组:选择合适的团队成员,包括相关专业知识和经验的人员,确
保多方面的参与。
3. 制定团队目标:明确问题解决的目标,如减少缺陷率、提高生产效率等。
4. 制定8D工作计划:确定解决问题的步骤和时间表,并为每个步骤指定负责人。
5. 采取紧急行动:在问题确认后,团队需要快速采取应急措施以减轻问题造成
的后果。
6. 根本原因分析:使用5W2H、鱼骨图、5 why等工具分析问题的根本原因,
找出问题发生的根本原因。
7. 制定纠正措施:根据根本原因分析结果,制定可行的纠正措施,并确保其全
面性、可持续性和有效性。
8. 实施纠正措施:将纠正措施落实到实际操作中,确保团队各成员按计划行动。
9. 核查效果:评估纠正措施的实施效果,通过数据分析和实地检查来验证问题
是否得到解决。
10. 预防措施:确定防止问题再次发生的预防措施,如培训、更新工艺流程等。
在整个8D工作小组过程中,团队应保持有效的沟通和协作,确保每个环节都得到适当的关注和执行。
通过8D工作小组方案,企业能够更好地解决问题,提高产品质量,增强市场竞争力。
8d工作方法在食品企业中的应用

8d工作方法在食品企业中的应用
8D工作方法是一种以消费者需求为导向的工作方法,在食品企业中可以应用于以下方面:
1. 产品开发:8D工作方法强调市场调研、产品创新和消费者反馈的重要性。
在食品企业中,可以运用8D工作方法来开发新产品,以满足消费者的需求。
例如,通过市场调研了解消费者对于某种口感、风味、包装等方面的需求,然后根据这些信息进行产品创新,并收集消费者的反馈以不断改进产品。
2. 质量控制:在食品企业中,质量控制是一个至关重要的问题。
8D工作方法可以帮助食品企业运用消费者反馈来改进质量控制,例如通过收集消费者对于食品安全、口感、香味等方面的反馈,改进产品的质量和口感。
3. 品牌管理:在食品企业中,品牌管理也是一个关键问题。
8D工作方法可以帮助食品企业运用消费者反馈来建立品牌声誉,例如通过收集消费者对品牌的认知、口感、安全性等方面的反馈,改善品牌形象和消费者信任度。
4. 供应链管理:在食品企业中,供应链管理也是一个关键问题。
8D工作方法可以帮助食品企业运用消费者反馈来优化供应链管理,例
如通过收集消费者对于物流、生产和销售等方面的反馈,优化供应链流程,提高生产效率和产品质量。
总之,8D工作方法可以帮助食品企业更好地了解消费者的需求,改进产品质量和口感,建立品牌形象和消费者信任度,优化供应链管理,从而提高企业的市场竞争力和盈利能力。
标准版8D报告教材
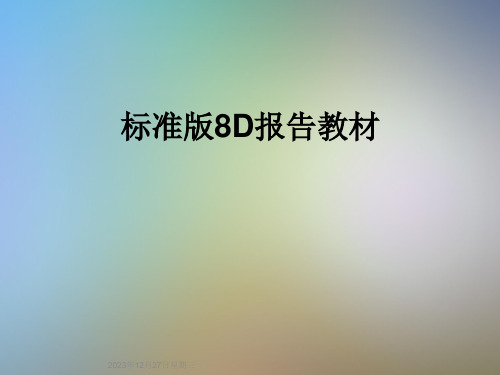
•
-1.推移圖
-2.管制圖
• 。以統計方法驗証效果的顯著與不顯著
• 。收集數據驗證改善措施的成效。(建議一至 二個月期間的資料收集)
•二. 8D工作方法的介绍
•D7:预防再发生
•目的: • 修改现有的管理系统、操作系统、
工作惯例、设计与规程以防止这一问题 与所有类似问题重复发生。
•二. 8D工作方法的介绍
被探测出但未被探测出的点
•
必要问题:
• 是否有鱼骨图分析? 是否 有是/不是分析?
• 是否确定了可接受的根本原因?
• 过程的根本原因是否被认可?
• 根本原因是否得到验证?
• “五个为什么”方法是否应用?
• 逃逸点是否确定?
• 现行控制系统是否有能力探测被确定的问题?
魚骨圖
•MAN(因1)
•因2 •ENVIRONMENT
MANY)的方法才能落實執行 • ∞執行過程中要確認效果相同的問題不再出現 •
•二. 8D工作方法的介绍
D4:原因分析及證實
• ∞以魚骨圖為架構,用腦力激盪的方式找出可能的原因 (POTENTIAL ROOT CAUSES)
• ∞以5WHYS深入追蹤直到分析出真正的原因(问题根源), 並追查出為何目前的系統無法顯驗出此異常
潤滑不足?
失靈了
• 。問4:為什麼潤滑泵 • 。答4:因為泵浦的輪
浦會失靈?
軸耗損了
• 。問5:為什麼潤滑泵 • 。答5:因為雜質跑到
浦的輪軸會耗損?
裡面去了
•二. 8D工作方法的介绍
•D4:原因分析及證實
•针对D2问题描述来测试每一个可能的原因,分析根本原因,
•
验证根本原因
•
8D模式(问题解决工作程序)

序号 1 2
主要原因
D6:实施并验证纠正措施 (略)
纠正措施
地点 完成时间 负责人
7
D7:制定巩固措施并实施 1)制定巩固措施
序号
巩固措施
1 修订 A 型号车轮控制计划,将××纳入其中。
2 修订 A 型号车轮车制作业指导书,将加工参数修订为××。
3 对 A 型号车轮加工人员进行培训(标准学习,技术操作培训)
action)。 制定纠正措施时,要注意纠正措施的有效性、经济成本、可操作性,不要把临时性和应
急性的措施作为纠正措施。纠正措施应考虑采用防错技术与控制图。
纠正措施实施前,要进行风险、可行性评审,必要时要试运行一下,要避免拔出萝卜带 出泥——旧问题解决了,新问题又出来了。
要形成纠正措施计划表。纠正措施计划表的内容包括:主要原因、纠正措施、负责人、 地点、预定完成时间等。参考本章 11.4 节中的(6)条款。
3
题对顾客或相关各方的影响,需采取临时措施 ICA(如挑拣、返工、修补、更换、停止发货 等)对问题进行处理。临时措施要执行到采取纠正措施为止。
临时措施 ICA 实施前,要进行可行性评审,避免拔出萝卜带出泥——旧问题解决了,新 问题又出来了。临时措施 ICA 实施过程中或实施后,要对其有效性进行验证。
5
案例 11-1:8D 报告格式
8D 报告
项目名称:解决 A 型号车轮装配困难问题
项目涉及的产品:
项目来源:
项目负责人:
项目开始日期:
பைடு நூலகம்D1:小组成立
1)小组目标:6 周内,解决车轮装配困难问题。
2)小组成员分工:
姓名
职务
组内职务
张三
质量部经理 组长
质量8D问题解决标准工作程序与效果评价规范
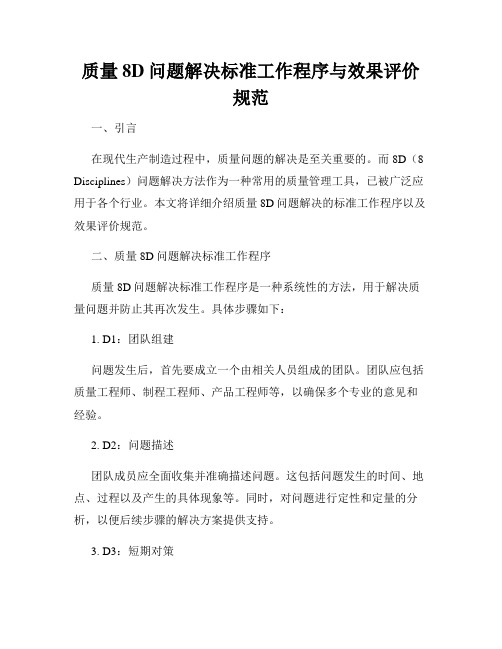
质量8D问题解决标准工作程序与效果评价规范一、引言在现代生产制造过程中,质量问题的解决是至关重要的。
而8D(8 Disciplines)问题解决方法作为一种常用的质量管理工具,已被广泛应用于各个行业。
本文将详细介绍质量8D问题解决的标准工作程序以及效果评价规范。
二、质量8D问题解决标准工作程序质量8D问题解决标准工作程序是一种系统性的方法,用于解决质量问题并防止其再次发生。
具体步骤如下:1. D1:团队组建问题发生后,首先要成立一个由相关人员组成的团队。
团队应包括质量工程师、制程工程师、产品工程师等,以确保多个专业的意见和经验。
2. D2:问题描述团队成员应全面收集并准确描述问题。
这包括问题发生的时间、地点、过程以及产生的具体现象等。
同时,对问题进行定性和定量的分析,以便后续步骤的解决方案提供支持。
3. D3:短期对策在确定问题的具体原因之前,可以通过采取一些短期对策来控制问题的扩散。
这些对策可以包括降低不良品数量、停止不良品流动等。
4. D4:根本原因分析团队应该通过使用5W1H的方法(即什么、为什么、何时、何地、谁、如何)来找出问题的根本原因。
采用鱼骨图、5W1H分析表等工具有助于决定问题根本原因。
5. D5:纠正措施当根本原因确定后,就需要制定纠正措施。
这些措施应着重于解决问题的根本原因,并确保将来不会再次发生类似的问题。
所有纠正措施都应该进行测试和验证。
6. D6:预防措施除了纠正措施外,还应该采取一些预防措施来避免类似的问题再次发生。
这些措施包括设立相应的工艺控制标准、培训相关人员等。
7. D7:效果验证纠正措施和预防措施实施后,应进行效果验证。
这可以通过对相关工艺和产品进行全面检查、检测和测试来完成。
8. D8:经验总结在解决问题后,团队应该进行经验总结和总结。
这样能够为以后类似问题的解决提供经验参考,并进一步提高质量管理水平。
三、效果评价规范为了评价质量8D问题解决方法的效果,可以采用以下几个方面进行评估:1. 解决时间评估解决问题所花费的时间。
- 1、下载文档前请自行甄别文档内容的完整性,平台不提供额外的编辑、内容补充、找答案等附加服务。
- 2、"仅部分预览"的文档,不可在线预览部分如存在完整性等问题,可反馈申请退款(可完整预览的文档不适用该条件!)。
- 3、如文档侵犯您的权益,请联系客服反馈,我们会尽快为您处理(人工客服工作时间:9:00-18:30)。
8D工作方法方式:1、疑惑:每人先提一个疑惑的问题,在过程中解答。
2、方式:讲评1个8D报告,每一部分先提问目的、信息、方法,再给出答案。
3、练习:按物料类分组各编写或改写1份8D---评讲【3-4份】,给每家以前出的问题各自完成一份8D交SQE检验合格后结束。
带合格8D回去培训一、8D 简介:8D方法又称团队导向问题解决步骤,是福特公司处理问题的一种方法。
已成为一个广泛使用的、有标准化步骤的、解决产品质量问题[非个人能解决]的最好的、有效的方法。
优点:1、提高解决问题的效率,积累解决问题的经验;2、杜绝或尽量减少重复问题出现;执行永久性矫正措施特点:是以团队运作为导向以事实为基础,避免个人主见的介入,使问题的解决能更具条理。
要建立一个体系,让整个团队共享信息,努力达成目标。
注意:让客户看得懂—不用专业术语[或做解释],多用图片展示[标出差异或变化],尽可能量化-用数字说话二、8D步骤基本信息:报告编号、组织名称、客户名称、标题、零件/过程名称、组织零件编码、客户零件号码、客户机型、开始时间、更新时间D0:紧急响应:目的:1、针对问题发生时候的紧急反应,使客户有良品使用和正常交付[质量合格/数量足够],不影响客户的正常生产/交付。
2、判断问题的类型、大小、范畴等等,是否需要用8D来解决,如果问题太小或不适合用8D来解决的问题,例如价格,经费等等。
步骤:1-控制可疑品:对所有可疑品实施停产-反馈-隔离-标识,遏住不合格再流出。
可疑品范围:向上/向下追溯-客户材料库存、客户在线品、客户已发货、组织材料库存、组织在线品、在途品、供应商。
要对现有的所有批次/相邻多个批次确认,不能仅仅控制反馈的批次。
2-紧急措施:和客户沟通,确认对可疑品实施换货、筛选、加工等方法使其合格,(针对描述的症状/失效后果)3-验证:不再出现客户陈述的症状。
内容:问题—量化工具【佩恩特图/趋势图/柏拉图】描述症状和问题。
现象、发现时间、发现地点/环节、发现者、故障件名称、故障部位、故障批号、生产日期;可疑数量、其他批次的确认、故障数、控制--措施方法、验证方法、有效性、实施日期、追溯标识、负责人、实施日期D1:小组成立要求:小组成员由议题之相关的、跨功能性的人员组成,并具有所要求的能解决问题和实施纠正措施的技术素质。
成员间有7种分工或担任的责任与角色[必须有小组长]。
使用头脑风暴方法工作。
关键要点:成员资格【具备工艺/产品的知识】,组成【组长/成员(多名)/客户/供方】,信息【部门/公司、姓名、电话】,分工;程序;目标;D2:问题说明概述:用量化的术语详细说明在具体环境中观察到的现象或问题造成的危险/影响【内/外部顾客抱怨】。
描述内容:故障现象和图片、合格标准、实际多少、偏差多少、故障比例/数量;发生地点/环节,什么东西出了什么问题;多用适当的图/表;5W2H-谁/什么/地点/时间/程度/频率/多少;尽可能量化;将复杂问题细分为单个问题。
受影响方、可能影响的产品有、信息反馈给(客户/操作工/检验员/供应商) 初步分析:是将症状转为缺陷,严重度/后果、出现的规律性、持续时间、生命周期的阶段、以前发生过吗、是异常波动吗;收集并审核现有数据识别问题,确定范围和可能原因,未被探测出来的环节和可能原因D3:临时措施的实施并验证目的:在真因没有找到/永久措施实施前,防止由此异常而影响顾客的措施。
只是对产品本身的纠正,保证组织处能有合格的产品生产使用和正常发货[质量合格/数量足够]。
立即而短期行动,避免问题扩大或持续恶化。
是围堵政策措施:基于问题描述中对问题的初步分析,临时措施要比以前改进了,检验方法要比以前内容/数量-控制力度加强了。
针对失效模式,治标不治本方法;1、已产品:范围--组织材料库存、组织在线品、在途品、客户材料库存、客户在线品、客户已发货方法---全检、返修、延迟交货、报废等2、客户处:告知客户收影响的批次数量SN等,和客户沟通是召回/退换货还是派人去处理。
3、再生产产品:方法--临时的管制措施、临时改进的工装等,临时的质量检查点,加强检验/加派人力,标识内容:临时措施(工艺上? 产品上? 检验上?)、追溯标识(产品上?包装上?)、实施日期、有效性验证、有效性% 副作用(导致其他质量、交货和生产能力问题)?、跟踪监控的效果【控制图、合格率等】验证:主要考虑消除或改变此原因后故障是否再现及再现多少,%有效率。
(DOE、PPM分析、控制图等)不再出现问题描述的问题。
用老的方法不能验出NG品,用改进的方法可以验出NG品D4:根本原因分析和验证及遗漏点目的:用统计/质量问题分析工具,列出/评估每个可能的原因可否使问题排除,验证,逐步缩小范围,找到发生问题的根源。
分析方法:造成偏差的一系列事件或环境或原因相互隔离测试,将他们会带来的结果与观察到的结果比较,原因/结果矩阵图可帮助选择优先考虑那个原因,并确定产生问题的根本原因。
故障件分析数据工具:用排列图、2-8原则、对比/比较分析、互换法等、FMEA、PPM、DOE、稳健设计(Robust Desig n)、控制图、5Why找出根本原因、过程流程图、因果图(鱼骨图)/4M1E定性、定量分析问题;识别问题的种类类型(设计、程序、制程、材料、人员技巧等)讨论的不同类型的原因1、鱼刺图:1-问题-主刺-分刺:人---1能力不够,2认识不够机[工具/设备]---- 1用错,2参数不合适料--1用错零件,2零件不良法--1流程不合理,2工艺不合理,3设计缺陷环--1大环境不良,2小环境不良测[遗漏点]--1测量方法,2测量条件2-对分刺分解多个小刺:2、5WHY:鱼刺图与5WHY的关系:WHYI:对鱼刺图中所有主刺原因分别验证,得出主因WHY2:对主因的主刺上的所有分刺分析验证,得出分刺的主因;WHY3:对主因的分刺上的所有小刺分析验证,得出小刺的主因;WHY4:对主因的小刺分析验证,得出过程控制的系统问题;WHY5:对过程控制的系统问题分析验证, 得出体系管理问题。
说明:1、每步推理之间都必须理由充分、逻辑性(都要问个为什么/能解释上一步);每步推理之间都是直接原因,直接原因的发生都基于出现了异常波动。
主因的差异要能够解释问题的现象。
2、每一次验证都必须理由充分、有逻辑性-使问题再现或消除,有效率%。
根本原因:对应永久措施的才是根因。
验证的根本原因:确定和认证问题逃出点:3、结论5Why:先简单说5WHY分析法是一种诊断性技术,是深度分析法,被用来识别和说明因果关系链,按层次逐步深入地系统的问“为什么?直到回答“没有好的理由”或直到一个新的故障模式被发现时才停止提问。
举一例如下:某工人加工的工件尺寸超差。
一问:为什么尺寸超差?——千分尺不准。
二问:为什么千分尺不准?——未按规定进行校准。
三问:为什么未按规定进行校准?——无校准规程。
四问:为什么无校准规程?——第一次使用指针式,采购部未移交有关资料。
五问:为什么采购部未移交有关资料?——无这方面的规定。
问题一:为什么机器停了?答案一:因为机器超载,保险丝烧断了。
问题二:为什么机器会超载?答案二:因为轴承的润滑不足。
问题三:为什么轴承会润滑不足?答案三:因为润滑帮浦失灵了。
问题四:为什么润滑帮浦会失灵?答案四:因为它的轮轴耗损了.问题五:为什么润滑帮浦的轮轴会耗损?答案五:因为杂质跑到里面去了。
使用时不限定只做“5次为什么的探讨”,主要是必须找到真正原因为止,有时可能只要3次,有时也许要10次。
追根究底的精神来发掘问失败例子:产品质量做的不好,要是问生产:为什么做不好?生产会说:材料不好。
问采购:为什么买的材料不好?采购一般会答:财务不让我们买贵的材料。
问财务:为什么一定要采购买便宜的材料?财务答:现在收到的货款少,资金紧张。
问业务:为什么货款少?业务答:经济危机定单量减少了,老板不给钱让我们去发展新业务。
,很多的问题大家最终都可以以老板不支持,“老板要求降低成本”,老板不给钱等等为答案,最终的结论就是:问题没法解决。
失败原因:大家不是在找原因,而是在找推卸自己责任、踢皮球。
真正的原因就很容易被掩盖。
应该:1、回答问题的人首先要尽可能找自身的原因,除非是在自身上找不到原因和改进的方法,才可以去从别的方面去找原因。
然后还要找可控的因素,可控因素才是我们能着眼去改进的因素,比如设备维修是我们内部可以做到的,而金融危机则是我们无法改变的现实,再比如说塞车,我们可控的是我们可以调整我们的出行时间,而交通拥堵则是我们无法控制的。
2、每个“为什么”的结论都可能是一个集思广益、头脑风暴的结果,是大家的意见的综合,对于每个结论都要有合理的理由或证据来证明其合理性,同时对于每个结论都要进行验证其结论的正确性,因为一个错误的结论必定会导致后面的“为什么”结论的准确性。
D5:永久纠正措施选择并验证区别:应急措施是针对问题发生的反应;临时措施是针对产品或服务问题本身的暂时纠正应对措施;永久措施是预防措施,使此类问题永远都不再出现。
关键要点:1、长久对策的要求:是针对所有失效的主因或盲点,从根本上解决的问题,可使同样的问题永远都不再发生【一般要求采用防错方法】,且无副作用【带来其他质量、交货和生产能力问题】。
2、长久对策描述:改进前方法?改进后的方法?---图片。
要达到的目标?目标实现时间?3、验证PCA :永久措施通过验证确认是否在实施后能提供一个合乎期望的结果。
长期措施改进的效果,用前后数据定量比较。
有效性的验证最终在于问题的发现环节。
4D6:永久纠正措施实施和确认1、实施:执行永久纠正措施,废除临时措施【终止时间】。
开始日期、批次、数量、故障统计。
2、确认:利用故障的可测量性【统计控制】,确认故障已经排除【问题是否重复出现】。
长期监督其效果【做控制点,定量统计说明故障降低的程度】。
产品改进的有效性的验证/确认最终是在问题的发现环节内部确认:控制图-附相关记录-分析,效果?副作用?外部确认:与客户确认原缺陷症状已消除D7:预防再发生目的:修改现有的管理系统、操作系统、工作惯例、设计与规程,以防止这一问题与所有类似问题重复发生。
关键要点:1、标准化:文件重新确定,修正与问题相关的管理系统/程序、设计与规程;FMEA、CP作业指导书[操作系统/工作惯例]等。
修改因素有:人机料法环测管。
D8:小组祝贺关键要点:1、经理层已对本8D作了审批?保留重要文档2、流览小组工作,将心得形成文件,分享经验教训?3、表扬小组和个人的贡献,对小组工作进行总结并祝贺;必要的物质、精神奖励。