注射模具设计一般常识(二)
塑胶模具(注射模)知识培训

謝謝!
11.产品粘贴模内 模具问题: ①由于注塑供胶不足造成,不要采用顶出机构。 去除倒切口,去除凿纹、刻痕及其它伤痕。② 增加脱模斜度,改善模具的光滑性。 ③增大有效的顶出面积,改善顶出机构。 ④在深抽芯模具中增强直空破坏及气压抽芯。 ⑤减少浇口尺寸,增设辅助浇口,重新安排浇口 位置。 ⑥克服设计模具致使成型周期反常。
塑胶模具(注射模)知识培训
IE內部培訓
模具结构图
一.在设计注塑模时应考虑以下几个方 面的问题。
1.塑胶件结构及技术要求,塑件的结构决 定了模具结构的复杂程度。塑件的技术 要求决定了模具制造及成型工艺的难易 程度。对于不符合塑料注射成型要求, 不合理结构形状均应提出改进,塑胶设 计的建议,否则会增加模具设计与制造 以及注射成型工艺的难度。
三.模具的构成部分
1.成型零件是构成模具型腔的零件,包括 有型芯、凹模、镶件等构成。 2.浇注系统:是将熔塑由注塑机射嘴引向 型腔的流道。包括有主流道、分流道及 浇口,冷料穴组成。
3.导向机构:通常是由导柱和导套组成。目 的是为了引导动定模正确闭合,保证其合 模的准确性。有些模具在动定模时两边分 别设置互相吻合的内外锥面,用来承受侧 向力,保证模具有足够的强度。有些在顶 针板上设有导向零件,增加中托司,目的 防止避免顶出过程中推板歪斜使推板平稳 运动。 4.侧向分型和抽芯机构,塑胶件上有侧孔侧 凹,需要在塑件未推出之前先抽出侧面型 芯,这样的机构称之为侧向分型。
9.产口翘曲与收缩 此原因通常是由于制品设计不善,浇口位置不好。 以及注塑成形条件所致,高应力取向也是因素。 模具问题: ①改变浇口尺寸及位置。 ②增加辅助浇口。 ③增加顶出面积。 ④保持顶出平衡。 ⑤要有足够的排气。 ⑥增加壁厚加强。 ⑦增加加强筋及圆角过渡。 ⑧校对模具脱模尺寸。
注塑模具设计基本知识

图3.1 单分型面注射模结构
一、单分型面注射模
3.单分型面注射模的工作过程
单分型面注射模的一般工作过程为:模具闭合—模具紧锁—注射— 保压—补塑—冷却—开模—推出塑件。下面以图3.1为例介绍单分型面 注射模的工作过程。 在导柱8和导套9的导向定位下,动模和定模闭合。型腔零件由定模 板2与动模板1和型芯7组成,并由注射机合模系统提供的锁模力锁紧; 然后注射机开始注射,塑料熔体经定模上的浇注系统进入型腔;待熔 体充满型腔并经过保压、补塑和冷却定型后开模,开模时,合模注射 机系统带动动模后退,模具从动模和定模分型面分开,塑件包在型芯7 上随动模一起后退,同时,拉料杆15将浇注系统的主流道凝料从浇口 套中拉出。当动模移动一定距离后,注射机的顶杆21接触推板13,推 出机构开始动作,使推杆18和拉料杆15分别将塑件及浇注系统凝料从 型芯7和冷料穴中推出,塑料与浇注系统凝料从模具中落下,至此完成 一次注射过程。合模时,推出机构靠复位拉杆复位,并准备下一次注 射。
按机构组成,单分型面注射模可由成形零部件、浇注系统、 导向系统、推出装置、温度调节系统和结构零部件组成。 单分型面注射模零件
成形零部件
模具中用于成形塑料制作的空腔部分称为模腔。 构成塑料模具模腔的零件统称为成形零部件。由于 模腔是直接成形塑料制作的部分,因此模腔的形状 应与塑件的形状一致,模腔一般由型腔零件、型芯 组成。图3.1所示的模具型腔是由型腔(定模板)2、 型芯7、动模板1和推杆18道称为浇注系 统,它分为主流道、分流道、浇口、冷料穴四个部 分。图3.1所示的模具浇注系统是由浇口套6、拉料 杆15和定模板2上的流道组成。
导向系统
为确保动模与定模合模时准确对中而设导向零件。 通常有导向柱、导向孔或在动模板模上分别设置互 相吻合的内外锥面。图3.1所示的模具导向系统由导 柱8和导套9组成。
注射成型及模具设计实用技术知识点总结

1、塑料是一种以树脂为主要成分,以添加剂(增塑剂、稳定剂、填充剂、增强剂、着色剂、润滑剂、特殊助剂、其他主要助剂)为辅助成分的高分子化合物。
增塑剂:为了改善聚合物成型时的流动性能和增进之间的柔顺性。
稳定剂:制止或者抑制聚合物因受外界因素影响所引起破坏作用。
填充剂:为了降低成本改善之间的某些使用性能,赋予材料新特性。
增强剂:使塑件力学性能得到补强。
着色剂:赋予塑料以色彩或特殊的光学性能。
润滑剂:改善塑料熔体的流动性能,减少、避免对成型设备的摩擦、磨损和粘附,改进制品表面粗糙度。
2、塑料的特性:相对分子质量大;在一定的温度和压力作用下有可塑性。
3、聚合物(树脂)通常有天然和合成两大类型。
对聚合物的选择主要是从分子量大小及分布、颗粒大小、结构以及与增塑剂、溶剂等相互作用的难易程度等诸方面考虑。
4、聚合物的作用:胶粘其他成分材料;赋予材料可塑性。
5、塑料的分类:根据来源:天然树脂、合成树脂。
根据制造树脂的化学反应类型:加聚型塑料、缩聚型塑料。
根据聚合物链之间在凝固后的结构形态:非结晶型、半结晶型、结晶型。
根据应用角度:通用塑料、工程塑料 根据化学结构及基本行为:热固性、热塑性塑料。
6、塑料的实用性能:轻巧美观、电气绝缘、热物理性能、力学性能、减震消音、防腐耐蚀。
7、塑料的技术指标:密度、比容、吸水率、拉伸强度、冲击强度、弯曲强度、弹性模量、马丁耐热、热变形温度等。
8、线性非结晶型聚合物在不同温度下所处的力学状态:g T T <聚合物处于玻璃态;处于高弹态f g T T T <<;f T T <粘流态。
9、玻璃态聚合物力学行为特点:内聚能大,弹性模量高,在外力作用下只能通过高分子主链键长、键角微笑改变发生变形。
10、高弹态聚合物力学行为特点:弹性模量与玻璃态相比显著降低,在外力作用下分子链段可发生运动11、黏流态聚合物力学行为特点:整个分子链的运动变为可能,在外力作用下,材料科发生持续性变形,变形主要是不可逆的黏流变形。
塑料注射模具设计的基本知识优秀课件

2021年2月24日
塑料成型工艺与模具设计
第一章 塑料注射模具设计的基本知识
二、注射成型分类:
➢普通注射成型:主要针对要求较低的热 塑性塑料和一些热固性塑料塑料制品成 型;
➢精密注射成型:可以成型要求较高的塑 料制品 ;
➢特种注射成型:共注射成型、结构发泡 注射成型等等。
2021年2月24日
塑料成型工艺与模具设计
2021年2月24日
塑料成型工艺与模具设计
第一章 塑料注射模具设计的基本知识
B、按注射装置分类:柱塞式注塑机和螺杆式注塑机 (1)柱塞式注塑机:以加热料筒、分流梭和柱塞 实现成型物料的塑化及注射。
2021年2月24日
塑料成型工艺与模具设计
第一章 塑料注射模具设计的基本知识
柱塞式注塑机存在的缺点: ①塑化不均:塑料靠料筒壁和分流梭传热,柱塞推动
➢ 锁模机构 :锁模机构的作用有三点:第一是锁紧模具; 第二是实现模具的开合动作;第三是开模时顶出模内制品。
➢ 液压传动和电气控制系统:液压传动和电气控制系统是保 证注射成型过程按照预定的工艺要求(压力、速度、时间、 温度)和动作程序能准确进行而设置的。
2021年2月24日
塑料成型工艺与模具设计
第一章 塑料注射模具设计的基本知识
以螺杆式注塑机为例:
2021年2月24日
塑料成型工艺与模具设计
第一章 塑料注射模具设计的基本知识
五、 注塑机基本参数
1.额定注射量
所需一次注射量:完成一次注射所需从料筒中注 射出的塑料熔体量,等于 (单个塑件质量×型腔个 数+浇注系统消耗质量)。
0.2mmax≤nm+m1≤0.8mmax mmax:注塑机额定最大注射量
2021年2月24日
塑料注射模具知识点总结

概述塑料注射模具是用于制造塑料制品的一种装置,由模具基板、模具芯、注射系统、冷却系统、脱模系统等部分组成。
塑料注射模具制造是一项相对复杂的工艺,需要对材料、工艺、设计、加工等方面具有深入的了解和掌握。
本文将从材料、设计、加工、维护等方面综合介绍塑料注射模具的知识点。
一、塑料注射模具的材料1.1 模具基板材料模具基板是塑料注射模具的主要承载部分,需要具有高强度、耐磨损、耐腐蚀等特性。
常见的模具基板材料有P20、718、2738等。
P20材料具有良好的硬度和耐磨损性能,适合制作中小型模具;718材料具有高强度和硬度,适合制作大型模具;2738材料具有高镍合金特性,适合制作高精度模具。
1.2 模具芯材料模具芯是用于塑料制品内部结构的部分,需要具有高硬度、高精度、耐磨损等特性。
常见的模具芯材料有SKD61、S136等。
SKD61材料具有良好的热稳定性和硬度,适合制作高品质的模具芯;S136材料具有良好的耐腐蚀性和耐磨损性,适合制作高精度的模具芯。
1.3 注射系统材料注射系统是用于将熔融塑料材料注入模具腔内的部分,需要具有耐高温、耐腐蚀、高流动性等特性。
常见的注射系统材料有H13、H13W等。
H13材料具有良好的耐热性和抗氧化性,适合制作注射系统组件;H13W材料具有更高的硬度和耐磨损性,适合制作高性能的注射系统组件。
1.4 冷却系统材料冷却系统是用于控制模具温度的部分,需要具有良好的传热性能、耐腐蚀、高耐压等特性。
常见的冷却系统材料有铜合金、铝合金、不锈钢等。
铜合金具有良好的导热性和抗腐蚀性,适合制作冷却系统管道;铝合金具有较轻的重量和较高的导热性,适合制作冷却系统散热器;不锈钢具有较高的耐腐蚀性和耐压性,适合制作高性能的冷却系统组件。
1.5 脱模系统材料脱模系统是用于将成型塑料制品从模具中脱离的部分,需要具有良好的脱模性能、耐磨损、易维护等特性。
常见的脱模系统材料有冷作钢、硬质合金等。
冷作钢具有良好的硬度和耐磨损性,适合制作脱模系统零部件;硬质合金具有更高的硬度和耐磨损性,适合制作高性能的脱模系统零部件。
模具毕业设计103注射模的结构设计

模具毕业设计103注射模的结构设计注射模具是工业制造过程中使用最广泛的一种模具,其设计结构直接影响到注射产品的质量和生产效率。
本文将详细介绍注射模具的结构设计,包括模具的结构要求、主要零件设计和结构优化。
一、模具的结构要求1.注射模具的结构要具有良好的刚性和稳定性,以确保模具在注射过程中不发生变形和振动,影响产品的精度和表面质量。
2.注射模具的结构要便于装卸、维修和保养,以提高模具的使用寿命和工作效率。
3.注射模具的结构要尽可能简单,以降低模具的制造成本和维修成本。
二、注射模具的主要零件设计1.模具基座:模具基座是支撑模具的主要部件,其结构要具有足够的刚性和稳定性。
为了方便模具的安装和调整,模具基座通常采用箱式结构,并设置有调整螺栓。
2.模板:模板是注射模具的主要部件,其上安装有注射模具的零件和导向机构。
模板的结构要求平整度高、刚性好,并配有合适的冷却系统,以确保注射过程中的热平衡。
3.滑块和导柱:滑块和导柱是注射模具中重要的导向和定位部件。
滑块通常用于实现中空或复杂形状的注射产品,其结构要求刚性好、耐磨损,并具有良好的导向性能。
导柱负责注射模具的下模板与上模板的定位,其结构要求尺寸精确、表面光洁,并配有合适的润滑系统。
4.模芯和模腔:模芯和模腔是注射模具成型部件的关键零部件,直接决定了注射产品的形状和尺寸。
模芯和模腔的设计要考虑到材料的选用、热处理和表面处理等因素,以提高模具的耐用性和工作精度。
三、注射模具的结构优化为了进一步提高注射模具的生产效率和产品质量,可以采取以下措施进行结构优化:1.采用优质材料:选择适当的模具材料,具有良好的强度和耐磨性,以提高模具的使用寿命和工作精度。
2.优化冷却系统:合理设置注射模具的冷却系统,以提高注射过程中的热平衡,减少产品变形和缩水现象。
3.降低模具重量:通过优化模具结构和采用轻量化材料,来减轻模具的重量,降低模具的惯性和振动,提高注射产品的精度和表面质量。
注塑常识及模具设计(二)
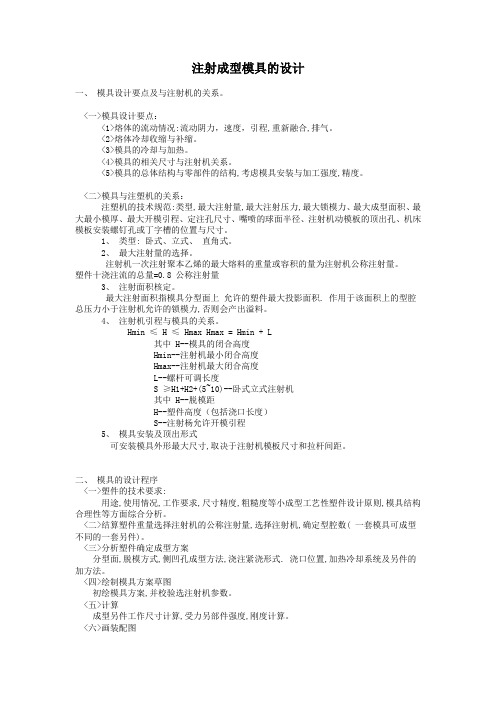
注射成型模具的设计一、模具设计要点及与注射机的关系。
<一>模具设计要点:<1>熔体的流动情况:流动阴力,速度,引程,重新融合,排气。
<2>熔体冷却收缩与补缩。
<3>模具的冷却与加热。
<4>模具的相关尺寸与注射机关系。
<5>模具的总体结构与零部件的结构,考虑模具安装与加工强度,精度。
<二>模具与注塑机的关系:注塑机的技术规范:类型,最大注射量,最大注射压力,最大锁模力、最大成型面积、最大最小模厚、最大开模引程、定注孔尺寸、嘴喷的球面半径、注射机动模板的顶出孔、机床模板安装螺钉孔或丁字槽的位置与尺寸。
1、类型: 卧式、立式、直角式。
2、最大注射量的选择。
注射机一次注射聚本乙烯的最大熔料的重量或容积的量为注射机公称注射量。
塑件十浇注流的总量=0.8 公称注射量3、注射面积核定。
最大注射面积指模具分型面上允许的塑件最大投影面积. 作用于该面积上的型腔总压力小于注射机允许的锁模力,否则会产出溢料。
4、注射机引程与模具的关系。
Hmin ≤ H ≤ Hmax Hmax = Hmin + L其中 H--模具的闭合高度Hmin--注射机最小闭合高度Hmax--注射机最大闭合高度L--螺杆可调长度S ≥H1+H2+(5~10)--卧式立式注射机其中 H--脱模距H--塑件高度(包括浇口长度)S--注射杨允许开模引程5、模具安装及顶出形式可安装模具外形最大尺寸,取决于注射机模板尺寸和拉杆间距。
二、模具的设计程序<一>塑件的技术要求:用途,使用情况,工作要求,尺寸精度,粗糙度等小成型工艺性塑件设计原则,模具结构合理性等方面综合分析。
<二>结算塑件重量选择注射机的公称注射量,选择注射机,确定型腔数( 一套模具可成型不同的一套另件)。
<三>分析塑件确定成型方案分型面,脱模方式,侧凹孔成型方法,浇注紧浇形式. 浇口位置,加热冷却系统及另件的加方法。
注塑模具设计知识点

注塑模具设计知识点注塑模具是在塑料制品生产中起关键作用的一种工具,它的设计质量直接影响着产品的质量和生产效率。
本文将介绍注塑模具设计的一些基本知识点,以及在设计中需要注意的事项。
一、模具结构注塑模具由模具板、芯轴、活塞、顶针等组成。
模具板承受注塑过程中的压力和冲击力,必须具备足够的强度和刚度。
芯轴用于形成注塑制品内部的空间形状,也要求具备较高的硬度和耐磨性。
活塞和顶针用于顶出注塑制品,其结构设计要考虑到顶出力的大小和顶出效果。
二、模具材料常用的模具材料有铝合金、钢材等。
铝合金模具具有质量轻、导热性好等优点,适用于小批量生产和快速开发新产品。
钢材模具则具有高强度、高硬度和耐磨性等特点,适用于大批量生产。
在选择模具材料时,需要根据生产要求、产品材料和使用寿命等方面综合考虑。
三、模具设计的重点1. 完整度:模具设计要保持产品的完整度,即保证产品的尺寸、形状和表面质量符合设计要求。
2. 排气性能:模具内部注塑过程会产生大量气体,需要保证模具具有良好的排气性能,以避免空气被封闭在注塑制品中形成气泡。
3. 冷却系统:注塑过程中,需要通过冷却系统将塑料制品迅速冷却固化,以确保产品的尺寸稳定性。
因此,在模具设计中要合理布置冷却水道,以提高冷却效果。
4. 塑料流道设计:塑料从注塑机进入模具的路径称为塑料流道,其设计要遵循塑料的流动特性和产品的要求。
塑料流道的布置和尺寸直接影响着产品的充填状况和成型效果。
5. 分型面设计:注塑制品在模具中成形后需要顶出,因此需要合理设置分型面,以方便产品的顶出和模具的拆卸。
四、模具制造工艺模具的制造工艺包括数控加工、装配和调试等环节。
数控加工技术能够快速高效地完成模具的加工工序,提高模具的精度和质量。
在模具装配过程中,需要确保模具的各部件相互协调和配合良好。
调试环节是验证模具性能和调整参数的过程,确保模具能够正常运行。
注塑模具设计是一个综合性较强的工程,需要根据具体的产品要求和生产条件来进行设计。
模具设计重点知识(华航)
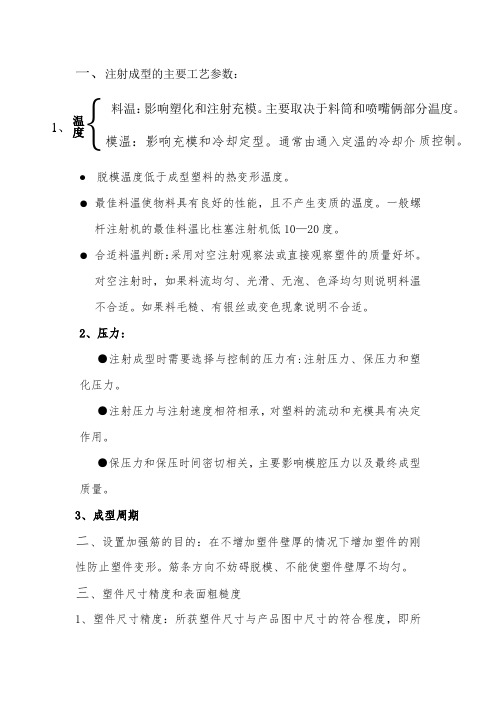
一、注射成型的主要工艺参数:{模温:影响充模和冷却定型。
通常由通入定温的冷却介 脱模温度低于成型塑料的热变形温度。
● 最佳料温使物料具有良好的性能,且不产生变质的温度。
一般螺杆注射机的最佳料温比柱塞注射机低10—20度。
● 合适料温判断:采用对空注射观察法或直接观察塑件的质量好坏。
对空注射时,如果料流均匀、光滑、无泡、色泽均匀则说明料温不合适。
如果料毛糙、有银丝或变色现象说明不合适。
2、压力:●注射成型时需要选择与控制的压力有:注射压力、保压力和塑化压力。
●注射压力与注射速度相符相承,对塑料的流动和充模具有决定作用。
●保压力和保压时间密切相关,主要影响模腔压力以及最终成型质量。
3、成型周期二、设置加强筋的目的:在不增加塑件壁厚的情况下增加塑件的刚性防止塑件变形。
筋条方向不妨碍脱模、不能使塑件壁厚不均匀。
三、塑件尺寸精度和表面粗糙度1、塑件尺寸精度:所获塑件尺寸与产品图中尺寸的符合程度,即所料温:影响塑化和注射充模。
主要取决于料筒和喷嘴俩部分温度。
质控制。
温度 1、得塑件的准确度。
{2、塑件比哦啊面粗糙度:塑件的外观要求越高,粗糙度越低。
成型时尽可能的从工艺上避免冷疤、云纹等缺陷产生除此之外主要取决于与型腔的粗糙度。
磨具比塑件精度高1-2级。
四、注射膜结构①成型零部件:是指动、定模部分中组成模腔零件。
(凸模或型芯、凹模、镶件等组成)决定塑件的尺寸形状。
②、浇注系统:熔融塑料从注射机喷嘴进入模腔所流经的通道。
(主/分流道、浇口、冷料穴)③、导向机构:分为动膜与定膜之间的导向机构和顶出的导向机构俩大类。
④、脱模机构:常见得有推杆、推板、推管脱模机构。
⑤侧面分型与抽芯机构:在塑件侧面有凹凸形状的孔或凸台时就要侧分型。
⑥加热和冷却系统 ⑦排气系统 ⑧支撑零部件●开模行程:是指动模固定板能够移动的最大行程。
模具是依靠动模固定板的移动实现合拢或打开,确定开模行程的需要量时,应以保证打开后顺利取出为度。
●影响因素:①磨具制造精度和磨损程度 ②塑料收缩率的波动以及成型时工艺参数的变化、塑件成型后时效变化和模具结构形状等。
注射模具基础培训
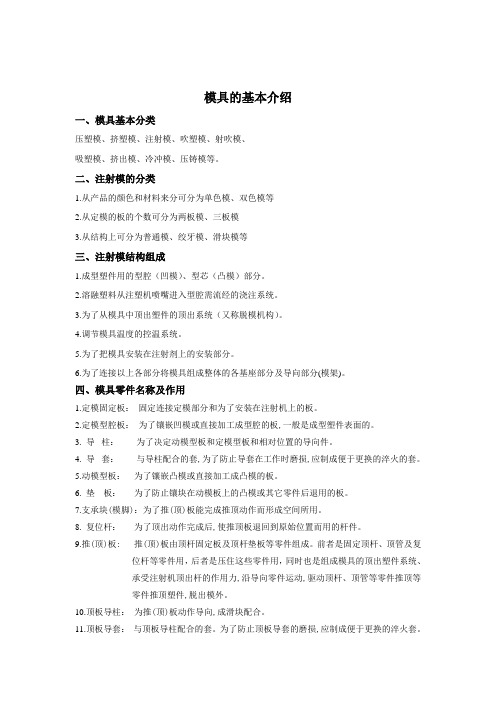
模具的基本介绍一、模具基本分类压塑模、挤塑模、注射模、吹塑模、射吹模、吸塑模、挤出模、冷冲模、压铸模等。
二、注射模的分类1.从产品的颜色和材料来分可分为单色模、双色模等2.从定模的板的个数可分为两板模、三板模3.从结构上可分为普通模、绞牙模、滑块模等三、注射模结构组成1.成型塑件用的型腔(凹模)、型芯(凸模)部分。
2.溶融塑料从注塑机喷嘴进入型腔需流经的浇注系统。
3.为了从模具中顶出塑件的顶出系统(又称脱模机构)。
4.调节模具温度的控温系统。
5.为了把模具安装在注射剂上的安装部分。
6.为了连接以上各部分将模具组成整体的各基座部分及导向部分(模架)。
四、模具零件名称及作用1.定模固定板:固定连接定模部分和为了安装在注射机上的板。
2.定模型腔板:为了镶嵌凹模或直接加工成型腔的板,一般是成型塑件表面的。
3. 导柱:为了决定动模型板和定模型板和相对位置的导向件。
4. 导套:与导柱配合的套,为了防止导套在工作时磨损,应制成便于更换的淬火的套。
5.动模型板:为了镶嵌凸模或直接加工成凸模的板。
6. 垫板:为了防止镶块在动模板上的凸模或其它零件后退用的板。
7.支承块(模脚):为了推(顶)板能完成推顶动作而形成空间所用。
8. 复位杆:为了顶出动作完成后,使推顶板退回到原始位置而用的杆件。
9.推(顶)板: 推(顶)板由顶杆固定板及顶杆垫板等零件组成。
前者是固定顶杆、顶管及复位杆等零件用,后者是压住这些零件用,同时也是组成模具的顶出塑件系统、承受注射机顶出杆的作用力,沿导向零件运动,驱动顶杆、顶管等零件推顶等零件推顶塑件,脱出模外。
10.顶板导柱:为推(顶)板动作导向,成滑块配合。
11.顶板导套:与顶板导柱配合的套。
为了防止顶板导套的磨损,应制成便于更换的淬火套。
12. 支承钉:使推(顶)板和动模固定板之间形成空隙,便于调节推板的活动范围,并容清除料渣杂物。
13. 螺钉:用于连接各部位零件。
14.定位销:决定各部位零件的相对位置。
- 1、下载文档前请自行甄别文档内容的完整性,平台不提供额外的编辑、内容补充、找答案等附加服务。
- 2、"仅部分预览"的文档,不可在线预览部分如存在完整性等问题,可反馈申请退款(可完整预览的文档不适用该条件!)。
- 3、如文档侵犯您的权益,请联系客服反馈,我们会尽快为您处理(人工客服工作时间:9:00-18:30)。
奇瑞汽车乘用车研究一院
13
内外饰部
下盖模仁3D
奇瑞汽车乘用车研究一院
14
分型面设计的检查重点
• 在成型过程中,模板的定位 主要是靠四支导柱的定位。 但是当模座较大时,导柱的 公差也会随之增大,定位的 效果也会较差。为了帮助定 位效果,在模座的四周可以 安装导柱辅助器,协助模具 公母模板的开闭时的定位。 或者是利用分型面定位的设 计,让模具闭合的效果提高。
奇瑞汽车乘用车研究一院
41
喷流
喷流(Jetting)的定义: 自一受限区域(例如喷 嘴或是浇口),到一较 厚和开阔的区域,形成 的弯曲折迭似蛇的流痕。
胶口
奇瑞汽车乘用车研究一院
内外饰部
42
内外饰部
使用搭接浇口以避免喷流
奇瑞汽车乘用车研究一院
43
内外饰部
使用搭接浇口以避免喷流
奇瑞汽车乘用车研究一院
奇瑞汽车乘用车研究一院
47
内外饰部
冷却水路设计重点
• 冷却水路与模穴表面各处的距离最好相同。 也就是说,水路的排列与模穴的形状尽量相 吻合,如果产品形状允许,冷却水路与模穴 的距离,尽量不要小于10mm。
• 浇口附近加强冷却。 • 水路入口与出口的温差尽量降低。
奇瑞汽车乘用车研究一院
48
内外饰部
• 当产品造型设计不恰当时,排气问题会很难 解决。
奇瑞汽车乘用车研究一院
53
问题点
内外饰部
奇瑞汽车乘用车研究一院
54
模仁
内外饰部
奇瑞汽车乘用车研究一院
55
内外饰部
五、脱模机构
• 在射出成型的每一个循环周期中,产品必 须准确无误的从模穴中脱出;让产品从模 穴中脱离的机构称为脱模机构。
• 脱模机构分类有多种方式,常见的脱模机 构有二: – 简单脱模机构(顶针、套筒) – 侧向脱模机构(滑块、斜销)
• 进行3D模仁设计时,必须注意分型面上是 否有尖角出现;因为如果分型面上出现尖 角,模具的寿命可能会缩短;可以与产品 设计人员讨论,检查是否可以修改产品造型。
奇瑞汽车乘用车研究一院
25
内外饰部
滑雪靴上压板
奇瑞汽车乘用车研究一院
26
模流分析
内外饰部
奇瑞汽车乘用车饰部
奇瑞汽车乘用车研究一院
• Fusible Core Injection Molding
• Mu Cell Molding 微泡射出成型
• Powder Injection Molding (金属、陶瓷)粉末射出成型
• LIM 液态硅胶射出成形
奇瑞汽车乘用车研究一院
4
内外饰部
塑料模具设计顺序
• 分型面设计 Parting Plane Design • 浇注系统设计 Filling System Design • 冷却系统设计Cooling SystemDesign • 排气系统设计Venting SystemDesign • 脱模机构设计 Ejecting System Design
内外饰部
模具设计及注塑工艺的培训(二)
模具设计合理化 Rationalization of MoldDesign
内外饰部:汪忠兴
日期:2008.5.24
奇瑞汽车乘用车研究一院
1
课程内容
• 设计合理化的目的 • 分型面 • 浇注系统 • 冷却系统 • 排气系统 • 脱模机构 • 总结与讨论
奇瑞汽车乘用车研究一院
• 分型面设计,需要检查的 重点有三个方面:
– 分型面的位置判断
– 分型面定位
– 分型面是否有尖角
分型面
内外饰部
奇瑞汽车乘用车研究一院
7
内外饰部
分型面的位置判断
• 分型面位置放置不当,有时候造成的成型问题而 无法解决。
• 通常分型面判断会出现问题者,多半是产品上有 两个以上的开模方向;一般产品设计者在进行设 计时,应考虑将行程较短侧做为滑块设计。
• 浇注系统的合理化,首重模穴配置与浇口设计。
奇瑞汽车乘用车研究一院
30
浇注系统
内外饰部
奇瑞汽车乘用车研究一院
31
内外饰部
浇注系统的重点
• 模穴布置尽量采用平衡配置,模穴与浇口的位置 力求平衡,以防止模具承受偏载,而产生溢料现 象。
• 流道末端必须设计冷料井,防止冷料随着流道系 统进入模穴。
• 结合线的位置,主要是由浇注系统的设计决定, 在产品上额外加上肉厚设计,可以在不调整浇口 位置的条件下,改变结合线的位置。
内外饰部
2
内外饰部
模具设计合理化的目的
• 最佳品质产品有四个主要关键:最佳产品设计、 最佳模具设计、合适塑料、最佳成型条件
• 随着机台加工精度的提升,现今模具厂的加工 技术都有水平之上。模具的好坏,设计人员与 钳工的水平成了决定因素。
• 在模具尚未加工前,如果能在设计图上按照顺 序检查出可能的问题,并且加以解决,模具的 问题自然减少。
冷却系统的合理化
• 模具的温度会直接影响到塑料产品的质量 与生产效率,所以模具上需要添加温度调 节系统,以达到理想的温度要求。
• 一般成型的塑料温度,大约在200℃左右, 而塑料件固化后,要从模具中取出的温度, 大约在60 ℃左右。热塑性塑料在成型后, 必须对模具有效的冷却,使融熔塑料的热 量必须很快的传给模具,以便使塑料冷却 后可迅速脱模。
• 模具温度控制常用方法:水和油。
奇瑞汽车乘用车研究一院
52
内外饰部
排气系统的合理化
• 成型的过程中,塑料进入模穴,模穴的空气 必须容易排出,塑料才能顺利充填。
• 排气不良时,产品表面会有困气造成的气泡、 甚至是焦痕。
• 在成型过程中,最常遇到的情况,常常是因 为浇注系统设计的不恰当,造成排气问题。
奇瑞汽车乘用车研究一院
32
内外饰部
USB装饰板
奇瑞汽车乘用车研究一院
33
模穴布局
内外饰部
奇瑞汽车乘用车研究一院
34
模穴充填平衡分析
材料:ABS 射出成型机吨数:80 Ton
内外饰部
奇瑞汽车乘用车研究一院
35
液晶电视前框
材料:ABS 射出成型机吨数:80 Ton
内外饰部
奇瑞汽车乘用车研究一院
36
冷料井设计
内外饰部
奇瑞汽车乘用车研究一院
37
公模仁设计
内外饰部
奇瑞汽车乘用车研究一院
38
内外饰部
利用壁厚设计调整结合线位置
• 许多产品的进浇位置,其实都受限制 了。 然而,结合线的位置却因为浇口 位置的限制,而固定住了。
• 利用额外的肉厚设计,可以在固定的 浇口位置下,改变结合线的位置。
奇瑞汽车乘用车研究一院
• 滑块机构合模时能够提供的锁模力较小,若该方 向之产品投影面积较大,很容易会发生问题。应 在设计时充分考虑。
奇瑞汽车乘用车研究一院
8
笔筒
内外饰部
奇瑞汽车乘用车研究一院
9
设计一
内外饰部
奇瑞汽车乘用车研究一院
10
设计二
内外饰部
奇瑞汽车乘用车研究一院
11
USB
内外饰部
奇瑞汽车乘用车研究一院
12
内外饰部
奇瑞汽车乘用车研究一院
56
内外饰部
面壳-顶针顶出
奇瑞汽车乘用车研究一院
57
2D装配图
内外饰部
奇瑞汽车乘用车研究一院
58
滑块脱模
内外饰部
奇瑞汽车乘用车研究一院
59
内外饰部
总结与讨论
• 模具设计的合理化,其实就是模具机构设计 的合理化
• 掌握了基本的物理概念,配合适当的CAE分 析,就能够在模具制作前检查出模具可能发 生的问题;如此不但能够节省修模及试模的 时间,也能够更精确的掌握产品的开发过程 程。
奇瑞汽车乘用车研究一院
49
内外饰部
水路与模穴的外型尽量吻合
奇瑞汽车乘用车研究一院
50
2D装配图
内外饰部
奇瑞汽车乘用车研究一院
51
内外饰部
四、排气系统
• 注塑成型时,模具的温度直接影响到塑料的 填充与塑胶产品质量,也影响到注塑周期。 因此必须对模具进行有效的冷却,使模温控 制在一定的范围内。
• 要提交模具的热传导效率就应做好冷却水路 的设计。
奇瑞汽车乘用车研究一院
3
内外饰部
射出成型分类
• Traditional Injection Molding 传统射出成型
• Over (Multi-Material) Molding
多色(料)射出成型
• Insert Molding
嵌入射出
• IMD/IML 模内贴合射出
• Gas-Assisted Injection Molding
44
内外饰部
浇注系统设计检查点
• 充填模式是否平衡(可配合 CAE 软件进行 充填分析,检视模穴充填状况)
• 结合线位置是否恰当,有无可能利用改变 浇口位置,或者是增加局部肉厚,以避免 结合线出现在重要外观面上(可配合CAE 缓 体进行分析预测结合线位置)
• 浇口形式是否恰当(避免 Jetting 的发生)
28
模仁
内外饰部
奇瑞汽车乘用车研究一院
29
内外饰部
二、浇注系统
• 浇注系统是指模具中从射出机喷嘴起,到模穴入 口为止的塑料熔体的流通渠道,或者是在这个通 道内冷凝的固体塑料。
• 浇注系统分为普通流道系统(冷流道)以及热浇 道系统两大类,普通流道系统包括了流道(由主 流道、分流道,以及冷料井组成)和浇口。
气体辅助射出成型
• Co-Injection (Sandwich) Molding 共射(三明治)成型