价值流图VSM绘图教程PPT课件
VSM价值流管理(PPT100页)名家精品课件

1.思維迷思 2.設計能力 3.計畫與
不足
管理不當
38
為何流動/快不起來?
思維迷思
-農耕心態 -追求利潤
最大化
設計能力 不足
-職能切割 -工程切割 -防坡堤設計 -分批-等待模式 -訂單/計畫的
不穩定 -轉換時間長 -物與情報
被切斷
計畫與管理 不當
-PMC中央管控 -預測式需求 -人為的不穩定 -不良多
• 傳統心理學研究: 找出不快樂的原因;給予消除
• 但,不滿足沒有不滿=/ 滿足 • 去除不滿足;並沒有得到滿足 • 因此,另外做不同的研究
46
如何才能快樂?
• 花25年對幾千人做研究 • 每人配帶call機 • 隨機響;就記下當時的作為與感受
• Flow:暢快;
順暢&爽快才能快樂
47
如何才能flow順暢?
11.開到 修理廠
消費時間:210分鐘
創造價值的時間:58分鐘
12.排隊、 描述問題
13.等候 借用車
14.委託 修理
創造價值的時間/總時間:28%
15分鍾
15.排除、 付款
20分鍾
16.駕車 回家
34
為何流動/快不起來 ?
35
價值流管理VSM
• 強調價值要快速流動
• 首先,要把沒有價值的去除: -以客戶角度定義價值 -給予價值最大化
• 搭配一個現場管理試驗,啟發思考 • 如何完成VSM的分析,不在此次課程
15
一.為何要做VSM 價值流管理?
常見老板的二大抱怨
• 交期長;又不準時 • 不要用的,一大堆; 要用的.卻沒有
17
為何要推動VSM?
1. 快速掌握企業經營系統 2. 全面瞭解企業的問題 3. 清析的瞭解瓶頸工程所在 4. 設備與人力配置研判 5. 日常管理執行與落實方向指引 6. 成為流程改善工具 7. 讓改善內容明確化與明確優先順序 8. 做為內外部的溝通工具
价值流程图 VSMppt课件

Tooling
Prepare tooling and testing fixture
Days: 2 CT: 0.25 day WIP: 5 FPY: 99% OTD: 90%
Doc Prepare the VA,WLB,Templetel
Days: 2 CT: 0.25 day WIP: 5 FPY: 99% OTD: 90% 0.25
0.25
Total L/T is too long, we need setup NAI L/T
standard for each kinds of material based on Location
2
0.25
2
30
Release PO to supplier take too
much time
IQC
3
Days: 1 1
Send the kit to production diectly
ห้องสมุดไป่ตู้
2
Production
Make the product
CT: 0.5 day WIP: 20 FPY: 95% OTD: 97% CO: 2H
IPQC
Check the finished goods
CT: 0.05 day WIP: 2 FPY: 99%
Planning
Run the ERP and Releases WO to Workshop
Measurements
· Working hours planned/released per Week · OTD of Documentation between ME / QA · Documentation/Information Released FPY. · OTD of Material Kit to Production. · Material Kit assembled FPY. · OTD of Tooling Kit to Production. · Tooling Kit assembled FPY. · NPI Project Book OTD Documentation.
VSM价值流程图(共75张PPT)
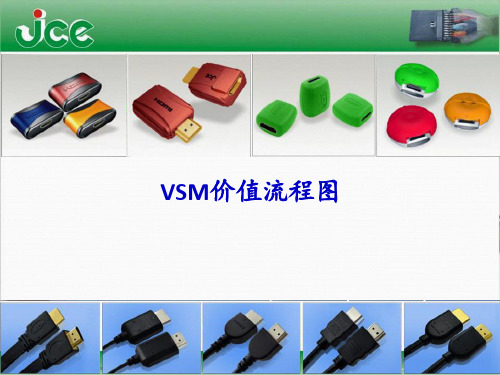
an unstable production process makes effective problem solving difficult, if not
impossible
*不稳定生产制程迫使危机管理取代了策略领导
an uncrisis management instead of strategic
5)How——简单说明价值流图析的应用方法。
价值流程图分析常见的七种工具
1.流程活动图(Process Activity Mapping)。 起源: 工业工程。 2.供应链反应矩阵(Supply Chain Response Matrix)。 起源: 时间加速与后勤学。 3.生产多样性漏斗(Production Variety Funnel)。 起源: 运营管理。 4.质量过滤图(Quality Filter Mapping)。 5.需求扩大图(Demand Amplification Mapping)。 起源: 系统动力学。 6.决策点分析(Decision Point Analysis)。 起源: 有效消费者反应/物流学。 7.物理结构图(Physical Structure Mapping)。
并有利于对生产流程进行指导,朝向理想化方向发展。
什么是价值流
所谓价值流,是当前产品通过其基本生产过程所要求的全部活动。这些活动包括 给产品增加价值
和不增加价值两部分,包括了从产品最基本的原材料阶段一直到产品 交付顾客的全部过程,如一辆汽车的制造, 包括了从顾客要求到概念设计、产品设计、 样车制造、试验、定型、投产到交付后的使用、信息反馈和回收过程,
➢ 顾客需求节拍应根据实际供货的历史加以修正。
➢ 顾客拉动和成品仓库发货拉动两种方式实际上都是由顾客需求拉动的,关键区别在 于是否
价值流图VSM绘图教程ppt课件

精益改善 线平衡 Line/Operator Balance
线平衡率 =
Σ(各工序作业时间) 瓶颈岗位时间 ∗ 人数
线平衡是指工程流动间或者工序流动间 负荷之差最小、流动顺畅、减少因时间差所造成的等待或滞留现象。
精益知识点 拉式生产、看板
物料员/水蜘蛛到上游超市取走需要的半成品, 提取生产看板,向上游工序发出生产指令,即生产拉动信号。
2. 连续流的多工序也可用一个工序表示
3. 物料流应按照工序从左向右绘制 而不是按照工厂的实际布局
4. 在车间沿物料流走一遍, 需要收集一些必要的、可以帮助 绘制未来状态图的数据, 并记录在数据箱中
• 周期时间 • 增值时间 • 设备开机率 • 工作时间 • 库存
• 员工数量 • 产品种类 • 良品率 • 换模时间 • 生产批次间隔(EPE)
感谢您的聆听
22
价值活动
任何增加市场或产品和服务的功能或市场形式的活动 (客户愿意为此付费的活动)
无增值活动
任何不增加市场或产品和服务的功能 (这些活动应当消除,简化,减少或合并)
优点: • 看到全流程,而不是单个工序 • 发现浪费并找到浪费的源头 • 同时体现信息流和物料流
• 材料入库 • 来料检查 • 库存 • 物料搬运
价值流图绘图教程
季正勇
目录
01
价值流图
02Leabharlann VSM图标03绘制现状图
04
绘制未来图
价值流图VSM
价值流程图(Value Stream Mapping,VSM)是丰田精益制 造(Lean Manufacturing)生产系统框架下的一种用来描述 物流和信息流的形象化工具。
VSM形象化地从系统层面观察生产过程中的物流和信息流, 发现浪费并制定相应的改善计划。
VSM价值流分析PPT课件
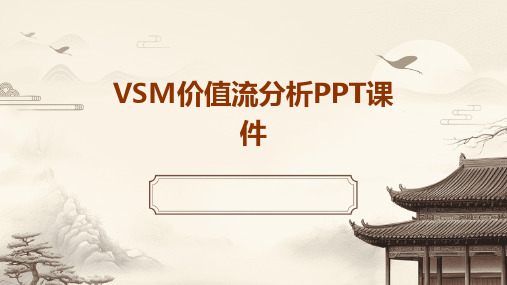
生产线平衡率计算
生产线平衡率 = 各工序时间总和 / ( 最长工序时间 * 工序数) * 100%。
提高设备利用率和员工工作效率,减 少在制品库存和等待时间,提高产品 质量和客户满意度。
生产线平衡方法
工序时间测定
通过秒表测时、预定时间标准等方法 ,准确测定各工序所需时间。
瓶颈工序识别
找出生产线上耗时最长的工序,即瓶 颈工序,进行重点改善。
02
收集数据
收集生产过程中的相关数据,如生产 周期、在制品数量、不良品率等。
01
03
绘制价值流图
使用标准的符号和工具绘制价值流图 ,包括流程图、数制定相应的改进计划, 包括优化生产布局、减少批量大小、 改进质量控制方法等。
05
04
分析浪费
在价值流图中标识出浪费的环节和原 因,如等待、运输、不良品等。
作业改善
通过作业分析、动作研究等方法,对 瓶颈工序进行作业改善,提高生产效 率。
生产线调整
根据改善后的工序时间,对生产线进 行调整,使各工序时间与节拍相等或 成整数倍关系。
改善措施制定
目标设定
原因分析
根据生产线平衡率和企业实际情况,设定 合理的改善目标。
针对生产线不平衡的原因进行深入分析, 找出根本原因。
收集生产过程中的相关 数据,通过统计分析识
别浪费现象。
员工参与法
鼓励员工积极参与,提 出生产过程中的浪费问
题和改进建议。
改善机会挖掘
01
02
03
04
消除浪费环节
针对识别出的浪费现象,制定 相应的改善措施,消除浪费环
节。
优化生产流程
通过改进生产工艺、调整设备 布局等方式,优化生产流程,
价值流图分析(PPT 59张)

—查找和发现浪费的-mail:lgddyangwenku@
价值流图分析 VSM
目的
了解价值流分析的作用
掌握绘制价值流图的步骤 加深对精益思想的理解
价值流图分析 VSM
主要内容
第一部分 价值流分析基础知识 第二部分 价值流图的绘制步骤 第三部分 价值流分析的作用 作业
采用5W1H方法
1. Who——确定谁来做 需要一位了解产品价值流而且能推进其改进的人,这个人具有领导职责 (价值流经理),由他来领导一个小组进行价值流图析工作。 2. What——确定做哪些产品的价值流图析(正确选择确定物流) 通常我们首先按照80—20原则,对影响企业最大的产品进行图析。 3. When——确定何时做(正确选择确定物流) 应在实施改进之前对价值流进行分析,以确定应首先改进哪些过程。 4. Where——确定在哪里做(如何获取真实、正确的数据信息) 在现场!只有在现场收集的数据才能真正反映价值流的状况。 5.Why—为什么做价值流图析 明确价值,消除浪费 6、 How ——进行图析
价值流图分析 VSM
价值流图基本概述
价值流图分析 VSM
价值流图基本概述
价值流图与流程图区别
价值流图: • 让所有人看见整体 情况 • 根据真实数据 • 改善蓝图 • 持续改善 流程图: • 只能反映局部工艺 周期、流程 • 根据工程标准或旧 数据 • 一年一次的大计划
价值流图分析 VSM
价值流图析步骤
(以前的认识是我们创造了产品的价值,并且由此确定了其价值。)
总之,永远站在客户立场上看待我们的工作价 值。谁对我们的工作进行最终评判和衡量,谁就是 我们的客户。 客户—我们从事一切生产经营活动并进行改善的最根本的出发点和落脚点
2024版价值流程图VSM案例分析PPT课件

价值流程图VSM案例分析PPT课件目录•引言•案例分析:某制造企业生产流程优化•案例分析:某电商平台订单处理流程改进•案例分析:某医院患者就诊流程优化•总结与展望01引言提高生产效率降低成本提升产品质量目的和背景通过价值流程图VSM分析,识别生产过程中的浪费环节,优化生产流程,提高生产效率。
减少生产过程中的非增值活动,降低生产成本,提高企业竞争力。
通过价值流程图VSM分析,发现生产过程中的问题点,改进生产工艺,提升产品质量。
价值流程图VSM简介定义价值流程图VSM是一种可视化工具,用于描述产品或服务的整个价值流,包括从原材料到最终产品或服务的所有活动。
作用帮助企业识别生产过程中的浪费环节,优化生产流程,提高生产效率和质量。
适用范围适用于制造业、服务业等各个领域的企业。
02案例分析:某制造企业生产流程优化当前生产流程存在过多的环节和等待时间,导致生产效率低下。
生产流程繁琐资源浪费严重质量问题突出生产过程中的物料、人力和时间等资源未能得到充分利用,造成资源浪费。
产品质量不稳定,客户投诉率高,影响企业声誉和市场竞争力。
030201企业现状及问题分析深入企业生产现场,全面了解现有生产流程、设备、人员配置等情况。
流程调研收集生产过程中的关键数据,如生产周期、在制品数量、设备利用率等。
数据收集基于调研和收集的数据,绘制价值流程图VSM ,直观展示生产过程中的价值流动情况。
VSM 绘制价值流程图VSM 构建识别并消除生产过程中的浪费环节,如减少等待时间、降低库存等。
消除浪费优化生产流程,合并或取消不必要的环节,提高生产效率。
简化流程加强产品质量控制,采用先进的质量管理方法和技术手段,提高产品质量稳定性。
强化质量控制生产流程优化方案设计01020304生产效率提升资源利用率提高产品质量改善企业竞争力增强实施效果评估通过优化生产流程,提高生产效率,缩短生产周期。
充分利用物料、人力和时间等资源,降低生产成本。
通过生产流程优化,提高企业市场竞争力,实现可持续发展。
《VSM培训教材》课件

感谢您的观看。
《VSM培训教材》PPT课件
目录
VSM概述VSM的核心概念VSM实施步骤VSM实施案例VSM的未来发展
01
CHAPTER
VSM概述
01
02
它通过绘制产品从需求到交付的价值流图,帮助企业识别和消除浪费,提高生产效率和产品质量。
价值流图(Value Stream Mapping, VSM)是一种可视化工具,用于描述产品从概念到交付过程中所有活动和信息的流动。
服务业
02
CHAPTER
VSM的核心概念
价值流是指产品从原材料到最终成品的过程中,所有创造价值的活动和过程。
价值流定义
价值流识别
价值流分析
识别出产品在生产过程中的所有活动,包括原材料采购、生产、物流、销售等环节。
通过分析价值流,找出浪费和瓶颈,提高生产效率和降低成本。
03
02
01
价值流图是一种工具,用于可视化产品在生产过程中的所有活动和时间。
详细描述
05
CHAPTER
VSM的未来发展
数字化转型是当今企业发展的必然趋势,VSM作为价值流管理的工具,能够为企业提供全面的价值流视图,帮助企业更好地应对数字化转型的挑战。
VSM通过数字化技术,如大数据、云计算、物联网等,实现价值流信息的实时采集、分析和可视化,为企业决策提供有力支持。
VSM与数字化转型的结合,将进一步推动企业实现流程优化、降低成本、提高效率,提升企业的竞争力和市场地位。
制定改进措施
按照改进措施,逐步实施改进计划,并对实施过程进行监控和调整,确保改进计划的有效性。
实施改进计划
在改进计划实施后,持续监控价值流的运行情况,并根据实际情况进行优化和调整,以保持价值流的持续改进和高效运行。
VSM价值流程图精品PPT课件

VSM Tools 绘制价值流分析图所需工具
Manufacturing Process
Scrap
Kaizen闪光点/ 爆炸点
外部资源/ 客户
数据盒
I
库存
o oo
卡车运输
成品至客户
缓冲区/ 安全库存
手工的 信息流 Electronic Information Flow
Production Kanban
• Ties together lean concepts and techniques helps avoid cherry-picking 结合精益的概念与技术…避免“只挑容易的” 来改进
• Forms the basis of an implementation plan 形成实施计划的基础
• Describes what you are actually going to do to affect the quantitative data 描绘为了影响这些定量的数据,应该做些什么
两班生产
冲压
I
焊接 #1
焊接 #2
装配 #1
装配 #2
I
I
I
I
I
MCT =23.5 Days
VA = 188 Sec
信息收集—顾客信息:
➢发货频次 ➢发货量 ➢需求信息来源
➢发货方式 ➢顾客装配班次 ➢顾客休息日
信息收集—原材料/成品信息:
原材料信息 ➢ 库存量 ➢ 供应商性质 ➢ 采购周期 ➢ 信息交流方式 ➢ 发货方式 ➢ 发货量
价值流图 V alue Stream
M apping
防错 M istake P ro o fin g
全面设备维护 T o ta l
史上最好的价值流教程,VSM,一次91页PPT

史上最好的价值流教程,VSM,一次
11、获得的成功越大,就越令人高兴 。野心 是使人 勤奋的 原因, 节制使 人枯萎 。 12、不问收获,只问耕耘。如同种树 ,先有 根茎, 再有枝 叶,尔 后花实 ,好好 劳动, 不要想 太多, 那样只 会使人 胆孝懒 惰,因 为不实 践,甚 至不接 触社会 ,难道 你是野 人。(名 言网) 13、不怕,不悔(虽然只有四个字,但 常看常 新。 14、我在心里默默地为每一个人祝福 。我爱 自己, 我用清 洁与节 制来珍 惜我的 身体, 我用智 慧和知 识充实 我的头 脑。 15、这世上的一切都借希望而完成。 农夫不 会播下 一粒玉 米,如 果他不 曾希望 它长成 种籽; 单身汉 不会娶 妻,如 果他不 曾希望 有小孩 ;商人 或手艺 人不会 工作, 如果他 不曾希 望因此 而有收 益。-- 马钉路 德。
31、只有永远躺在泥坑里的人Fra bibliotek才不会再掉进坑里。——黑格尔 32、希望的灯一旦熄灭,生活刹那间变成了一片黑暗。——普列姆昌德 33、希望是人生的乳母。——科策布 34、形成天才的决定因素应该是勤奋。——郭沫若 35、学到很多东西的诀窍,就是一下子不要学很多。——洛克
如何绘制VSM-价值流分析图PPT课件

TT = 60 sec.
Daily Ship Schedule
18,400 pcs/mo -12,000 “L” -6,400 “R” Tray = 20 pcs
2 Shifts
1x daily
I
Coils 5 days
Stamp 200 t
MCT = 1 second C/O = 1 hour REJ = 3% U/T = 85% 27,600 sec. avail. EPE = 2 weeks
Data Box资料盒
OCT
= Time
MCT
= Time
D/R
= Time
PLT
= Time
BATCH = Pieces
PTP
= Time
REJ
=%
U/T
=%
C/O
= Time
EPE
= Time
PITCH = Time
NOTE:
Only place appropriate data in the data box. The list above may not be totally inclusive.
-
28
精益价值流的观念
➢ 第六Байду номын сангаас观念:只对价值流中的一个制程发出生产 排程
➢ 价值流中的信息流(information flow)可以简化,在 精益价值流中接受生产排程命令的程序称为引导 程序(pacemaker process)。引导点必须排除值流中 其他程序的产能限制,来安排全部上游程序的生 产步调。选定引导程序是非常重要的。
当顾客一天需要一部时,不要一星期一次给七部
1 Day
1 Day
Takt Time = 1 Day 客户需求时间 = 一天
2024版精益价值流程VSM培训PPT
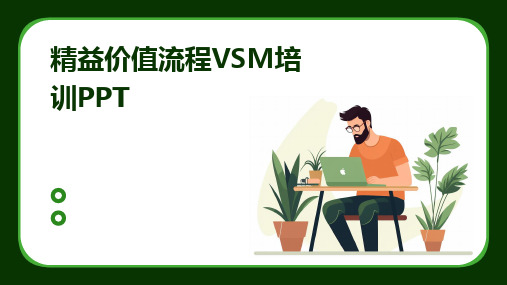
精益价值流程VSM培训PPT•精益价值流程VSM概述•精益价值流程VSM核心原理•精益价值流程VSM实施步骤•精益价值流程VSM在制造业应用案例目录•精益价值流程VSM在服务业应用案例•精益价值流程VSM培训总结与展望01精益价值流程VSM概述精益思想与VSM关系精益思想强调消除浪费,持续改进,追求卓越。
VSM 作为精益思想的重要工具,通过可视化价值流,识别浪费,推动流程优化。
精益思想与VSM相互补充,共同推动组织实现高效、灵活、优质的生产与服务。
VSM(Value Stream Mapping,价值流图)是一种可视化工具,用于描述产品或服务的整个价值流。
VSM通过识别价值流中的浪费,帮助组织优化流程,提高生产效率,降低成本。
VSM的作用包括:识别浪费、优化流程、提高生产效率、降低成本、增强组织竞争力。
VSM定义及作用010204 VSM发展历程VSM起源于丰田生产方式(TPS),是精益生产的重要工具之一。
随着精益生产的普及,VSM逐渐在制造业中得到广泛应用。
近年来,VSM的应用范围不断扩展,已经渗透到服务业、医疗、教育等领域。
未来,随着数字化、智能化技术的发展,VSM的应用将更加便捷、高效。
0302精益价值流程VSM核心原理选择具有代表性的产品族,明确其生产流程,包括从原材料到成品的所有环节。
确定产品族和生产流程收集数据绘制价值流图识别浪费收集各环节的生产数据,如生产周期、在制品数量、设备利用率等。
运用专业的绘图工具,将生产流程以图形化方式展现出来,包括物料流、信息流等。
在价值流图中标注出存在的浪费现象,如等待、运输、不良品等。
价值流图绘制方法识别浪费制定消除策略实施改进措施持续监控与改进浪费识别与消除策略持续改进文化培养树立持续改进观念建立改进机制培养员工能力营造改进氛围03精益价值流程VSM实施步骤现状调研与数据收集01020304明确调研目标收集现场数据了解客户需求分析现状价值流图绘制及分析确定价值流图的范围分析浪费和瓶颈A B C D绘制当前状态的价值流图制定改进目标改进方案制定与实施实施方案制定改进方案调整方案监控实施过程对实施过程进行监控,确保改进方案的顺利执行。
VSM(价值流图中文)ppt课件
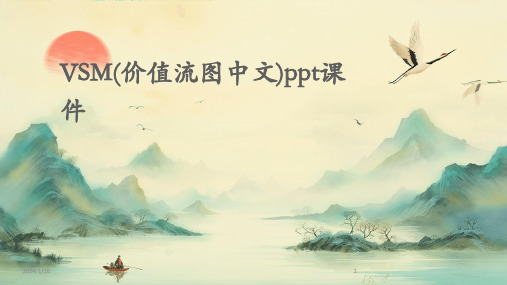
实施精益生产
引入精益生产理念和方法,通过持续改进和全员参与,不断优化生 产流程,降低生产成本。
18
供应链协同与整合
供应链可视化
通过价值流图将供应链各环节进行可视化展示,提高供应链透明度 和协同效率。
供应商选择与评估
利用价值流图对供应商进行全面评估,选择优质供应商并建立长期 合作关系。
5
价值流图发展历程
起源
价值流图起源于日本丰田汽车公司的 精益生产理念,旨在通过消除浪费来 提高生产效率。
发展
趋势
未来,随着数字化和智能化技术的发 展,价值流图将更加注重数据驱动和 实时性,实现更加精准和高效的流程 优化。
随着精益生产理念的普及,价值流图 逐渐被应用于其他行业和领域,成为 一种广泛使用的流程优化工具。
制定实施计划
制定改进方案的实施计划,包括 时间、资源、风险等方面的考虑
。
2024/1/26
16
04
价值流图在企业管理中应用实践
2024/1/26
17
生产流程优化与再造
2024/1/26
识别生产流程中的浪费环节
通过价值流图分析,发现生产过程中的无效等待、过度生产、不 必要的运输等浪费现象。
优化生产布局和设备配置
库存优化与物流管理
基于价值流图分析,合理规划库存和物流管理策略,降低库存成本和 运输成本。
2024/1/26
19
客户服务质量提升
2024/1/26
客户需求识别与响应
通过价值流图分析客户需求和反馈,及时响应并改进产品和服务 。
服务流程优化
优化客户服务流程,提高服务效率和质量,提升客户满意度。
价值流程图-VSMppt课件
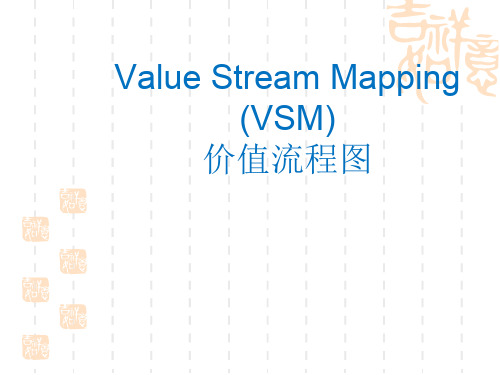
(VSM) 价值流程图
What’s Lean 什么是精益生产
Philosophy Thinking Toolkit Practice Journeys Life
NOT a program Not flavor Not a campaign
A Value Stream Map (VSM) is a hand-drawn map that helps people to see and understand process, material and information flow through a production process or value stream, from start to finish.
Avai lable tim e TAKT tim e
B Cycl e tim e RTY o r F TT
Scr ap r ate Up/Do wn t ime Star ve/Blo ck t ime EPE / Set up t ime
Avai lable tim e TAKT tim e
C Cycl e tonly adds time and cost, no value. 浪费只增加时间 和成本,不增加价值。
u Waste is the reason that product flow stops and is the cause for non competitiveness. 生产流动的停止是造成浪 费的原因,浪费是缺乏竞争性的根源。
Non-Value Added
Any activity that does not add market form or function or is not necessary. (These activities should be eliminated, simplified, reduced or integrated.)
价值流图VSM绘图教程PPT课件

3. 物料流应按照工序从左向右绘制 而不是按照工厂的实际布局
4. 在车间沿物料流走一遍, 需要收集一些必要的、可以帮助 绘制未来状态图的数据, 并记录在数据箱中
• 周期时间 • 增值时间 • 设备开机率 • 工作时间 • 库存
• 员工数量 • 产品种类 • 良品率 • 换模时间 • 生产批次间隔(EPE)
6
绘制VSM Step1 — 客户栏
.
1. 绘图从客户需求开始 改善最重要的是从客户的角度 来确认产品的价值
2. 用数据箱记录客户需求 需求量/交货频率/交货单位 最小批次量/工作时间
7
绘制VSM Step2 — 生产工
序
.
1. 用工序框代表不同的工序 物料从一个工序向另一个工序移动 流程不连续或材料中断时, 物料流自然停止
某些特殊情况,超市并不适用 如订制品、保质期短的材料、少量但高价的零件等。 可设置一个“顺序拉动”即先进先出FIFO来取代超市。
• 定拍工序按客户订单来控制生产
• 定拍工序往往是价值流中连续流的最后一个工序
• 定拍工序后面的流程按FIFO方式移动
.
16
精益均改衡生善产
D1
集中 生产
D2
D3
成品库存量大,原材料及在制品多,适应变化的灵活性差。
.
21
感谢您的聆听
.
22
价值流图绘图教程
季正勇
.
1
目录
01
价值流图
02
VSM图标
03
绘制现状图
04
绘制未来图
.
2
价值流图 VSM
价值流程图(Value Stream Mapping,VSM)是丰田精益制 造(Lean Manufacturing)生产系统框架下的一种用来描述 物流和信息流的形象化工具。
- 1、下载文档前请自行甄别文档内容的完整性,平台不提供额外的编辑、内容补充、找答案等附加服务。
- 2、"仅部分预览"的文档,不可在线预览部分如存在完整性等问题,可反馈申请退款(可完整预览的文档不适用该条件!)。
- 3、如文档侵犯您的权益,请联系客服反馈,我们会尽快为您处理(人工客服工作时间:9:00-18:30)。
8
绘制VSM Step3 — 绘制物料流图
1. 识别物料接收处
2. 确定选择的产品族的存货数量 每天/每班在手库存
3. 识别物料如何在过程中移动 推动或拉动
4. 记录观察到的库存量 以数量或时间为单位
5. 不同类型物料需要区分表示
.
9
绘制VSM Step4 — 添加信息流
1. 信息流在VSM的上半部,从右向左画 2. 需要区分电子信息和人工信息 3. 需要标注信息流的频率
价值活动
任何增加市场或产品和服务的功能或市场形式的活动
(客户愿意为此付费的活动)
无增值活动
任何不增加市场或产品和服务的功能
(这些活动应当消除,简化,减少或合并)
.
优点: • 看到全流程,而不是单个工序 • 发现浪费并找到浪费的源头 • 同时体现信息流和物料流
• 材料入库 • 来料检查 • 库存 • 物料搬运
.
21
感谢您的聆听
.
22
6
绘制VSM Step1 — 客户栏
.
1. 绘图从客户需求开始 改善最重要的是从客户的角度 来确认产品的价值
2. 用数据箱记录客户需求 需求量/交货频率/交货单位 最小批次量/工作时间
7
绘制VSM Step2 — 生产工
序
.
1. 用工序框代表不同的工序 物料从一个工序向另一个工序移动 流程不连续或材料中断时, 物料流自然停止
看板的两大功能:
下指令给一个工序进行生产的看板叫生产指令看板 指令物料员开始运送物料的叫物料提取看板
生产指令看板向上游工序发出生产一定数量的某个产品的指 令,以满足下游工序的需要。
物料提取看板发出向下游工序运送物料或零部件的指令,通 常有内部工序间的看板和供应商看板两种
.
15
精益知识点 先进先出、定拍工序
均衡 生产
均衡生产可能会增加一些工作,如较频繁的换模,产线旁暂存的不同零部件 均衡生产可以消除价值流中大量的浪费,缩短价值流的交付时间 有更大的能力,在小库存(上下游)、短交期条件下,应对不同的客户需求。
.
库存
库存
客户 每日 需求
17
绘制VSM未来图的准则
准则1: 按照节拍时间生产 准则2: 尽可能创建连续流 准则3: 在连续流无法向上游扩展时,建立一个超市来控制生产(拉动式、看板) 准则4: 下达订单到一个点 (定拍工序) 准则5: 在定拍工序,均衡地安排生产多种产品 准则6: 持续地向定拍工序下达小批量的生产指令 准则7: 在定拍工序上游工序,建立每天生产每种零件的能力
• 组装 • 配电 • 调试 • 包装
3
价值流图析的范围 和主要步骤
1 3
2
未来状态图
.
4
VSM图标
生产工序
推动箭头
数据箱
数据箱2
均衡生产
.
5
绘制VSM的主 要步骤
.
VSM绘制主要步骤:
Step1 — 客户栏 Step2 — 生产工序 Step3 — 绘制物料流图 Step4 — 添加信息流 Step5 — 添加时间线
.
10
绘制VSM Step5 — 添加时间线
1. 将物料流中各个工序生产周期 加上库存天数, 可以估计除生产线的交付期
2. 时间线上表示工序交付期 3. 时间线下表示增值时间
.
11
TWI工业公司VSM 现状图
.
12
精益 改善 流动 or 连续流、单件流 (One Piece Flow)
精益生产最重要的是在客户或下一道工序需要的时候才生产(JIT)。 将生产流程中所有的工序,从最终客户到原材料连起来,形成一个没有迂回的流程, 达到最短生产交付期、最高质量和最低成本的目的。
.
18
TWI工业公司VSM现 状图
10Min
.
19
TWI工业公司VSM未 来图
如何绘制未来图:
1. 使用拉式生产或者先进先出的 顺序拉动方式替代推动式生产
2. 降低换模时间,均衡生产减少库存
3. 计划部门只对定拍工序下达计划 增加发货频率,减少库存
.
20
绘图注意事项
• 应当独立作业去绘制整个价值流图 • 坚持用铅笔手工绘图 • 沿着物料流、信息流,快速地走上一圈 • 不断地收集需要的信息 • 不要依赖不是你亲自测量的标准工时或信息
2. 连续流的多工序也可用一个工序表示
3. 物料流应按照工序从左向右绘制 而不是按照工厂的实际布局
4. 在车间沿物料流走一遍, 需要收集一些必要的、可以帮助 绘制未来状态图的数据, 并记录在数据箱中
• 周期时间 • 增值时间 • 设备开机率 • 工作时间 • 库存
• 员工数量 • 产品种类 • 良品率 • 换模时间 • 生产批次间隔(EPE)
.
13
精益改善 线平衡 Line/Operator Balance
线平衡率 =
线平衡是指工程流动间或者工序流动间
负荷之差最小、流动顺畅、减少因时间差所造成的等待或滞留现象。
.
14
精益知识点 拉式生产、看板
物料员/水蜘蛛到上游超市取走需要的半成品, 提取生产看板,向上游工序发出生产指令,即生产拉动信号。
某些特殊情况,超市并不适用 如订制品、保质期短的材料、少量但高价的零件等。 可设置一个“顺序拉动”即先进先出FIFO来取代超市。
• 定中连续流的最后一个工序
• 定拍工序后面的流程按FIFO方式移动
.
16
精益均改衡生善产
D1
集中 生产
D2
D3
成品库存量大,原材料及在制品多,适应变化的灵活性差。
价值流图绘图教程
季正勇
.
1
目录
01
价值流图
02
VSM图标
03
绘制现状图
04
绘制未来图
.
2
价值流图 VSM
价值流程图(Value Stream Mapping,VSM)是丰田精益制 造(Lean Manufacturing)生产系统框架下的一种用来描述 物流和信息流的形象化工具。
VSM形象化地从系统层面观察生产过程中的物流和信息流, 发现浪费并制定相应的改善计划。